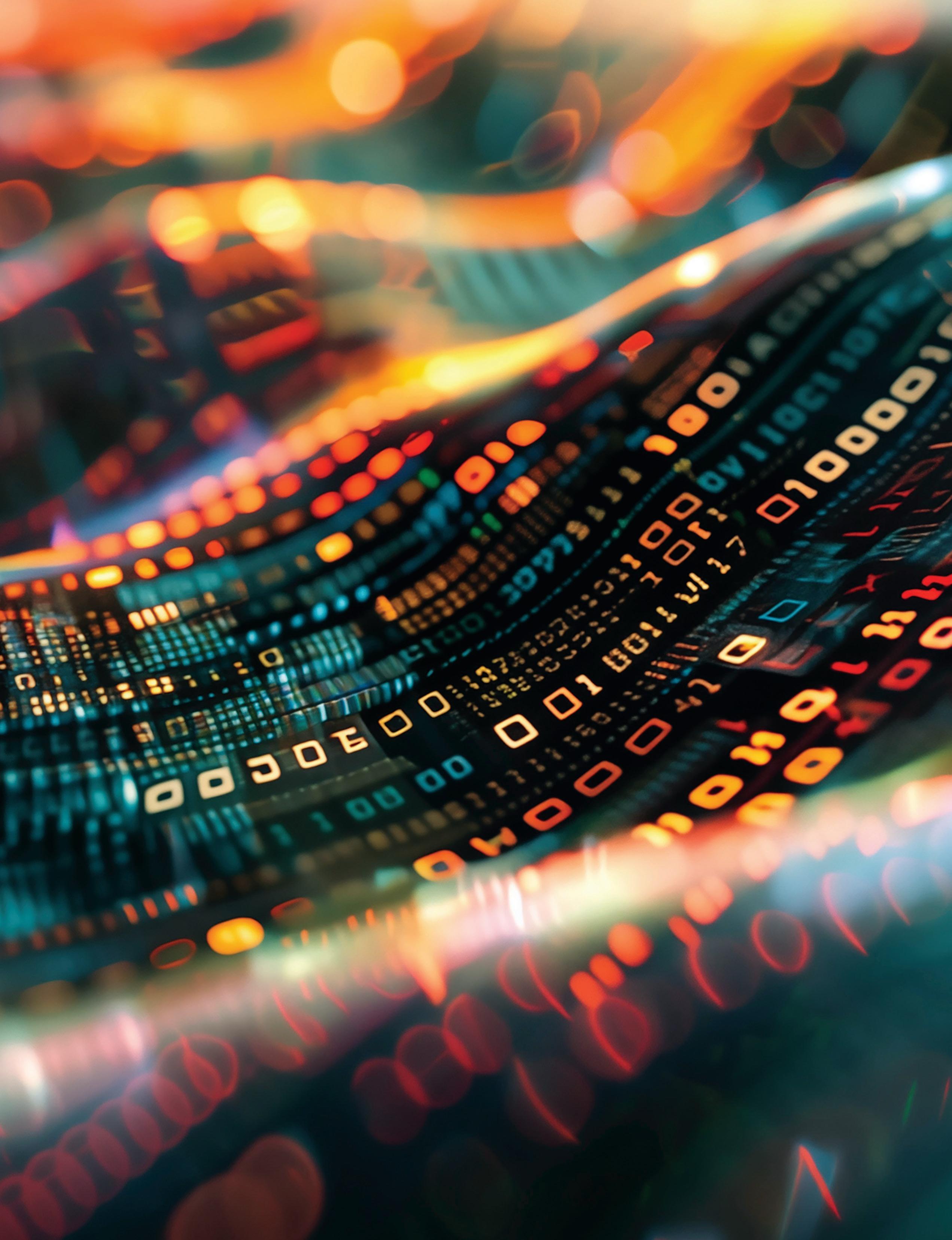
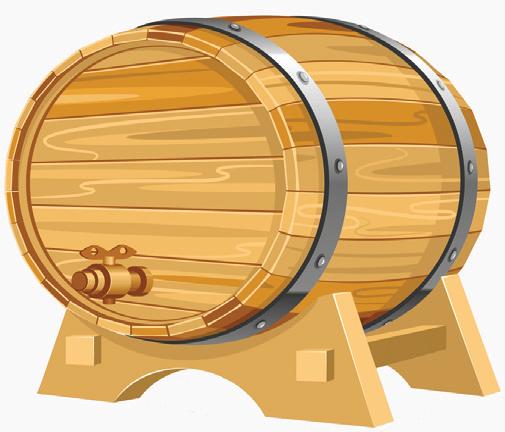
Alyssa Ochs
Craft Beverage Practice
Jake Ahles - Morel Creative
David Delorenzo - Bar & Restaurant Insurance PMMI
Loan Mantra Distillery Now Consulting LLC
Bricker Publishing Division of: Bricker Group, LLC 1409 13th Street North Humboldt, IA 50548
E-mail: editor@BrickerPublishing.com
Website: www.BrickerPublishing.com
BEVERAGE MASTER targets the Craft Beverage market and located in Fort Dodge, Iowa. BEVERAGE MASTER is printed bi-monthly and distributed to the most qualified buyers. Opinions expressed in BEVERAGE MASTER are not necessarily those of the publication personnel, but of the writers who contribute stories to BEVERAGE MASTER.
ERROR RESPONSIBILITY: BEVERAGE MASTER is responsible only for the cost of the ad for the first incorrect insertion of the ad. Each insertion of an advertisement is proof of publication and it is the responsibility of the advertiser to check the correctness of each insertion. The publisher shall not be liable for slight aesthetic changes or typographical errors that do not lessen the intent of the ad. No adjustment can be made for advertisements not published. In the event of any error in an ad for which the publisher is liable, the liability is limited to adjusting that portion occupied by the error in relationship to the entire value of the advertisement. No adjustments will be made 30 days after initial insertion date. All contents of BEVERAGE MASTER are Copyright © by Bricker Group, LLC CHANGE OF ADDRESS: Please send new address and phone number along with “BEVERAGE MASTER” mailing label or email changes to editor@brickerpublishing.com
By: Gerald Dlubala
ometimes, sitting around a bonfire enjoying a craft brew can be the best thinktank in the world. Such was the case for Joleen and Brian Durham, founders and owners of Piney River Brewing Company, an award-winning, family-owned brewery in the Missouri Ozarks. While enjoying a bottle of Ommegang's Three Philosophers, an idea sparked that gave birth to Piney River Brewing Company, humbly nestled in
the Missouri Ozarks. The Durhams began beef cattle farming in 1998. Thoughts turned introspective when they wanted to invest in themselves, their land and their property to bring additional value to their rural community.
“We were homebrewers, and we loved and homebrewed craft beer,” said Joleen. “As far back as the early 2000s, whenever we would travel, we always looked for local beer options to sample and maybe have with a meal. Craft beer wasn’t as big then.
There weren’t nearly the number of taprooms associated with craft brewing, but given the opportunity, we visited those as well, and I think doing that kind of sparked us to do it. We always believed that craft beer is about place, and at the time, we knew we lived in a unique place. The Ozarks are a place people recognize as a vacation destination full of nature, so we thought we should make a craft beer that carries the Ozarks as a theme and reflects those qualities."
Piney River Brewing Company offers beers with names like Missouri Mule, Old Tom Porter, Black Walnut, Float Trip Ale, Bronzeback Pale Ale, Low Water Bridge and more. Their beers are brewed using limestone-filtered well water from a natural spring on their property. In 2010, a deeper well was dug on their property to tap into their natural water supply more efficiently.
"We make no changes to our natural water profile at all," said Joleen. “We have a very large aquifer in the area. We have to test our water regularly, and the tests on the water profiles from our wells and the natural springs on our property yield the same results, so that's pretty cool. We're pulling water out of our limestone-filtered spring, which plays a key role in our brewing.”
“Our Black Walnut Beer is our most popular and has become synonymous with our brewery,” she said. “It’s an American-style, dark wheat beer made with the meat of locally sourced black walnuts. It was one of our earliest beers because we looked for an ingredient that the Ozarks is known for, and black walnut is that flavor of the Ozarks. It can remind you of your grandma’s cookies, a black walnut ice cream or just eating them while growing up. The Ozarks grow the most walnuts in the country; we're proud of that. We don't use the hull, only the black walnut nut meat in our brewing. The way we utilize them in our brewing process removes the natural tannins in the nuts and, instead, creates a subtle fruitiness. You get this very nice aroma of black walnut when you pour a glass, and then you get a black walnut finish, but it's not sharp or abrasive in any way. Brian chose to use a wheat beer to highlight the flavor, and the dark wheat is a play on the black walnut name. It has a smooth, light drinkability with a lot of body and flavor that has turned out to be a gateway beer for those who thought or said they don’t like or
wouldn’t drink dark beers.”
Joleen said their original plan was to make great craft beer for distribution that reminds people of good times spent in nature. As the majority of their beer is still canned for distribution purposes, the evolution of Piney River Brewing Company has resulted in a very vibrant, on-site brewery and taproom.
The 1940s-era barn was meticulously cleaned and decluttered to become the "BARn," which opened in 2011 and was home to the first official brewery for Piney River Brewing Company. It featured a 10-gallon Sabco Brew Magic Brewhouse to brew the Durhams' original homebrew recipes for public consumption. When demand quickly outpaced production, and Piney River got its first distributor, the Durhams purchased a used seven-barrel brewhouse and other equipment, including a two-head canning unit for 16-ounce cans.
Piney River Brewing Company became the first microbrewery in Missouri to can their beer on-site at the brewery. The accolades and demand continued, and by 2014, thoughts of expansion were again on the table. Ground was broken for a larger barn in December 2014, and with a $1.3 million investment in a new 15-barrel brewhouse and eight-head canning line, Piney River Brewing's roots were firmly set.
The original “BARn” is a booming taproom that welcomes guests every weekend. The brewery regularly draws customers from up to a 90-mile radius.
They also welcome those passing through the Ozark region, including people from all over the world who come to their farm to enjoy their property and craft beer. They continue to grow as a destination craft brewery by offering new beer releases and popular live music to also draw craft beer lovers like themselves to their brewery.
Brian and Joleen's son Andy was in elementary school when the Durhams started putting in the long hours and effort to get Piney River Brewing up and running, whether brewing, canning or running the taproom on weekends. Joleen said that Andy was always nearby, reading a book or visiting with customers at their picnic tables. He wanted to be involved somehow, so his parents let him pick out the root beer syrup of his choice to keg, and they named it Andy's Root Beer.
“It wasn’t long before he wanted to scale up,” said Joleen. “He noticed we were canning everything except his root beer. He was probably all of 12 years old at this time. We sent him to a kids’ busi-
ness camp, and wouldn’t you know it, he won the junior division’s business pitch contest, pitching his root beer canning idea. Andy’s Root Beer has now taken on a life of its own. It has won a couple of awards through the U.S. Open Beer Championship, and it is also sold in the taproom. Some folks like to have a shot of Andy’s Root Beer with their pint of Old Tom Porter. We started canning his root beer after he won the awards, and now you can find it around the area in cans and on draught. Andy gets the proceeds after expenses, which helped him buy everything from band equipment to a car, and now provides him with money to spend while he's in college.”
Speaking of awards, there are no shortages when it comes to Piney River Brewing Company and recognition. Just recently, Piney River Brewing Company’s Old Tom Porter took home the bronze medal during this year's Great American Beer Festival competition, with 1869 entrants representing all 50 states plus Washington, D.C. and Puerto Rico. There are too many prior awards to mention individually, including gold, silver and bronze medals for nearly all of their brews over the years. Additionally, Piney River Brewing Company
was named Best Microbrewery, People's or Editor's Choice four times over the last 10 years in the U.S. Open Beer Championships and has received accolades from the World Beer Cup, Great American Beer Festival, The Best of Craft Beer Awards and from Rural Missouri Magazine.
“Well, we are full-time beef cattle farmers, so you’ll pass through a couple of cattle guards along the two-mile gravel road on the way here,” said Joleen. “But then, you’ll see this brewery in the middle of nowhere. The taproom is open on the weekends, with live music. Handmade pizzas and pretzels are available, and outside food can also be brought in to enjoy while visiting."
Piney River Brewing Company sits on the Durhams' original 80-acre farm. When a nearby property became available, they took the opportunity to buy that and enhance the Piney River experience.
“Back in 2020, our area was hit with a devastating hailstorm right about the same time as COVID hit,” said Joleen. “Prior to that, in 2019, a farm on our same road came up for sale, and the family contacted us to see if we were interested. It contained an old, severely neglected house that got absolutely shredded from the baseball-sized hailstones, taking out windows and everything.”
“We ended up utilizing our staff, who weren't doing anything due to COVID, to gut the house and turn it into an extension of the Piney River experience,” she said. “Now, it's a little weekend getaway that we call our Bed and Brewery. It's on the same road as the brewery, also in the middle of nowhere. The Bed and Brewery is a really cool extension of our brewery for those who like to come in on Friday and stay through Sunday. Along with a brewery tour, they get a place to stay with a huge front porch, fire pit and a fully stocked beer fridge to make it the ultimate escape. It’s all those things about enjoying nature, watching the stars and just getting away from it all without seeing any cars, light pollution or other people for the most part. It is a very unique and enjoyable property for those who want to extend their stay and visit surrounding areas for tourism.”
“As others can tell you, it's challenging times for many craft breweries,” said Joleen. “For us, that means that we must continue to focus on brewing the best craft beer here in the Ozarks and remain consistent with our distribution throughout Missouri and Arkansas. We want to be known for what we do and do well right here because the freshest beer is the beer brewed closest to home.”
“We continue to work with our distributors to ensure that what we put out there is the absolute best representation of what we do and of our location,” she said. “We want to continue providing an enjoyable and fun experience for guests of all ages, whether regulars or first-time visitors. Believe it or not, there are still people out there who have never had or been exposed to craft beer, so we want to be that gateway into the craft beer experience for those people. It seems weird to say in this day and age, but it's really true that there are still areas of the country where craft beer isn't the norm. We want to make craft beer a great experience for those people while providing a place that is welcome for everyone, including pets.”
Joleen continued, “We also want to provide an example of a thriving small business located on a farm in the Ozarks. Many believe those conditions to be considerable odds, but we're proud to be a successful family farm business. The brewery is important to us, but it's also something we do alongside raising beef cattle and being good stewards for our land."
Piney River Brewing is located in Bucyrus, Missouri, in the Missouri Ozarks. Call or check out their website for more information, to plan a visit, or to book a stay at their Bed and Brewery.
Piney River Brewing Company
15194 Walnut Grove Bucyrus, MO 65444 417-967-4001
https://pineyriverbrewing.com/
By: Alyssa L. Ochs
enerally speaking, a conveyor is a mechanical system that automatically transports materials within a designated area. They are helpful in many different industries, including craft beverage production, to increase efficiency and productivity while maintaining food-grade safety standards and reducing manual labor.
Conveyors serve various functions in breweries and distilleries, including grain transportation to and from silos, moving malt within a small area and transferring bottles between packaging and labeling machinery. Fortunately, there are various conveyor options available to breweries and distilleries today.
Here are some insights about how conveyors help producers of craft beverages and tips for choosing the right one for your operations.
Various types of conveyor technology are used in craft beverage production to handle malt. Flexible screw conveyors are an excellent option for this purpose because they don't require extensive cleaning or maintenance. The spiral is the only moving part in a flexible screw conveyor, making it ideal for low throughput and avoiding cross-contamination. Aeromechanical conveyors work well for microbreweries with a small footprint. They
incorporate polyurethane discs evenly spaced in an air stream to handle malt for greater throughput and energy efficiency.
Conveyors also move cans and bottles between different pieces of machinery during bottling and packaging. This process requires regular cleaning and maintenance to keep the moving parts working properly.
Chain disk conveyors are used to transfer grain and are effective in gently and quickly moving grain while improving yield. This type of conveyor pulls segmented disks through a tube for grain transfer. Meanwhile, pneumatic conveyors, which utilize compressed air, are preferred by large breweries. It is also possible to customize conveyors to achieve tailored solutions for breweries and distilleries and integrate them alongside existing systems and processes.
Breweries and distilleries have numerous choices about the types and sizes of conveyors they implement. Yet ultimately, the goal is to improve production efficiency and maintain the quality of beverages as materials move across conveyor lines.
It is common to choose mass-flow conveyors for canning and bottling purposes whenever you need to move items vertically in mass quantities. With this conveyor, you can move products up or down in a mass or single flow at a rate of up to 2,000 units per minute with consistent movement.
Reflow conveyors temporarily accumulate products moving down a conveyor line and provide necessary time between machines used for different purposes at different stages of the production process. For example, a reflow conveyor may be used during the transitions of moving products between labeling stations and packing equipment. Example configurations include in-line, serpentine, alpine, bidirectional and spiral options.
Another option is the single-lane accumulation conveyor, which provides a downstream buffer zone where products can accumulate during processing. This conveyor helps prevent congestion and product damage as they move through the system. You might consider using one of these conveyors in your packaging line so that bottles and cans
can be held in place temporarily while awaiting the next processing phase.
Bucket lift conveyors are made of carbon steel and have plastic buckets on the belt to lift material in a high-efficiency lower hopper. After use, this conveyor can leave substantial residual material under the hopper and become moldy if not cleaned properly.
Craft beverage producers can try shafted or shaftless screw conveyors but should be aware of their pros and cons. Shafted screw conveyors are more efficient, but shaftless options are more flexible and can change direction. It's essential to check for residual material at the bottom and be mindful of the potential for loud noise due to the high speeds of the shaftless option.
Producers can process grain through wind conveyors and rely on suction generated by a large fan to transport grain to its intended destination. This low-noise option can transport materials long-distance, but it generates some dust and isn't necessarily the most efficient option.
Another idea to consider is the pipe chain conveyor, which has roots in the livestock breeding industry but is now used in craft brewing. This type of conveyor system is expensive, but you'll enjoy low noise benefits, multi-angle transportation and efficient transportation for your investment.
Certain companies specialize in conveyor systems for the craft beverage market, including, Spiroflo, which offers flexible screw conveyors and aeromechanical conveyors. Spiroflo's flexible screw conveyors are recommended for conveying malt in breweries and distilleries because they are easy to clean and maintain. There's only one moving part, the spiral, and it comes with quick-release flanges that can be easily cleaned to prevent cross-contamination. If you have higher throughput, Spiroflo's aeromechanical conveyors gently move products in an air stream and work well with malt to avoid product degradation while boosting energy efficiency.
Another company, Floveyor, offers a tubular drag conveyor that manages complex routes and controls infeed and dosing with multiple discharge out-
lets in the process line. It incorporates food-grade conveying technology in a single machine to handle powders, granules and multiple grains. Floveyor invented the aeromechanical method of conveying and has been in this industry for over 65 years. Its conveyors are made from stainless steel, have fully enclosed tubing, offer a compact size and are easy to clean and maintain for added long-term value.
Globaltek is another company that works in this space and offers a wide range of packaging, bottle handling, filling and labeling solutions. Its industrial conveyor system minimizes bacteria so craft beverage products can safely transfer and meet all stability and sanitation requirements. Globaltek offers brewery-specific, custom-made conveyors that are adjustable, reliable, efficient and easy to clean. Its product line includes a bottomless side belt transfer conveyor and accumulating tables.
Meanwhile, UniTrak offers a Powderflight aeromechanical conveyor with a small equipment footprint yet a high throughput rate of up to 1,440 cubic feet per hour. These machines can convey products from angles of zero to 90 degrees and have portable bases so you can move them easily
for processing. In breweries, they are used to transport malt to the mash tun so it can be mixed with hot water to form mash. UniTrak also offers flexible screw conveyors with lower throughput rates as an economical solution. These conveyors are fed manually with sacks of ingredients and can convey materials at 650 cubic feet per hour. The company has been in business for over 45 years and helps customers address their material conveying challenges worldwide.
Aside from buying the actual conveyor system itself, it’s crucial to understand how to properly clean and maintain your conveyor to protect your long-term investment.
Yujin Anderson, the owner & CEO of Steamericas, Inc., told Beverage Master Magazine how cleaning with steam eliminates the labor-intensive process of removing conveyor parts to rinse and wash them. She explained that you can’t use too much pressure or water when cleaning a conveyor because these modern pieces of equipment have delicate sensors and electronics. Yet, cleaning man-
ually is very time-consuming because conveyors’ many nooks and crannies.
This is where steam comes in to address those problems. Once water boils and becomes a gas, it acts more like air than water to get to all those tiny areas. The naturally high temperature is able to replace chemicals as the heat melts off debris and is naturally sanitizing.
Anderson shared that using steam to clean a conveyor utilizes less water than traditional methods – more like a 10 ounce cup of water per minute instead of five gallons. Steam doesn’t expose brewery and distillery employees to harmful chemicals, promoting better worker safety and wellbeing. It also keeps employees safe because it reduces the risks of finger pinches and amputations in conveyor systems.
Craft beverage producers often call Steamericas for steam solutions to sterilize barrels or to sanitize tanks and keg lines. However, the exact same product used for these purposes, the Optima Steamer, can also be used to clean conveyors. Therefore, this cost-effective solution is beneficial for small operations with limited budgets. The steamer is a multi-purpose product that can save you money on overall equipment investments, make your equipment last longer because it’s well-maintained, and streamline employee training with just one product to use.
Many established breweries and distilleries already have conveyor systems that satisfy their needs. But if you run a new business or are experiencing rapid growth, you might look to buy new machinery or upgrade your current setup.
One of the most important things to consider is how much space you have for a conveyor so that the model you choose fits where you need it to be. You'll also want to consider the prices of comparable models, their ease of use and their cleaning requirements. You can buy new or used conveyors depending on your budget, or consider leasing a conveyor if that fits better into your production's financial plan. The installation process, ongoing maintenance and energy consumption are other considerations that factor into a decision about a getting new conveyor.
Furthermore, you will want to explore the belt types, size and weight of the product, speed needed to move the product and the direction of the conveyor (either incline or decline). There are conveyors that you may need to wipe down dry or can wash down with soap and water, as well as various design types that include pivot, Z-frame, pacing and vacuum conveyors. It's also essential to think about conveyor-related accessories that you may need, such as diverters, gates, side tables, pushers and control-stop safety devices.
Looking to the future, some recent innovations and trends to watch in the conveyor industry may interest craft beverage producers. For example, artificial intelligence (AI) technology is revolutionizing conveyors and equipping them with sensors, cameras and real-time data to identify potential issues and inform users about upcoming maintenance needs. Researchers have been using 3D printing to produce custom conveyor parts for greater durability and design to tailor systems to producers' unique needs.
Sustainability is a significant concern among craft beverage producers today, so conveyor manufacturers are focusing on energy-efficient drives and brake systems. It is also becoming possible for robotic systems to collaborate with human users to handle sorting, packing and quality check tasks for greater efficiency and accuracy during the conveying process.
If your brewery or distillery has yet to consider conveyor technology for your operations, perhaps now is the time to learn about the options available and their potential benefits. Staying ahead of the curve and embracing the spirit of innovation can go a long way in helping a beverage business thrive while boosting productivity, saving money and conserving resources.
By: Hanifa Sekandi
Authenticity wins the day. This is a cliche saying that rings true in today's complex marketing landscape. People are not easily fooled by inauthentic brands. They prefer brands that convey truthful marketing strategies and products that support their claims. Your consumer desires connection. They desire to be valued and respected. The money they spend on your beverage is money hard-earned. Brands should move from the notion that their consumer is just a commodity that lines their pockets. Your consumer is your lifeline. They keep the doors open and keep you relevant.
This does not mean that you cannot devise overthe-top marketing campaigns. Of course, draw your consumers in with out-of-the-box marketing campaigns. It illustrates that you believe in your product and care about your consumers buying choices – so much so that you will go above and beyond to maintain their brand loyalty while keeping them entertained. A good example of this is popular comic book films. There is a loyal consumer who loves the books and anticipates a big-screen release. A creative ad campaign or movie trailer excites loyal fans. However, things can go wrong quickly if the marketing strategy deviates from
what is expected. Die-hard fans prefer familiarity and authenticity. They do not take well to brand reinventions that are gimmicky or inauthentic.
So, how do you become an authentic marketing expert? How do you win as a beverage brand with authentic marketing?
There is a lot of competition. Keep your eye on the prize, your consumer. Every brand should have an ideal consumer profile. This archetype needs to be well-researched. Keep in mind that it is not your job to tell your consumers what they need; your goal is to show them that you are a brand that understands their needs. Your beverage is the missing piece to the puzzle. For example, Chill House Ale is the beverage that adds to a warm-cooked meal or Sunday night football.
The simple answer is research. But the most honest answer is a good marketing strategy. Research is everything in the beginning stages of brand development, but it will not be enough with a subpar marketing strategy. Yes, an in-depth understanding of your audience is essential. But, it will not help you connect with your audience or increase brand awareness if you do not know how to turn heads. Give people something to talk about. One could argue that there are a lot of great beverage brands no one knows about that are better than many popular legacy beverage brands. Why? Brands underestimate their marketing spend. They spend a lot of money on packaging and branding, forgetting that a great label is a good start but will not solely sell your brand.
So, now you have your branding in place. In your mind, your beverage is of great quality and packaged well. Where do you go from here? Chase your consumer. Yes, that is right. Go to where they hang out. Become your consumer so you can understand their buying decisions. Do you need to start local? Get your beverage distributed at local bars and restaurants. Is your consumer an adventurist who loves the outdoors? Go to the places and spaces where your consumer finds joy and comfort. Build relationships with businesses that have built a relationship with your consumer. If your consumer likes to ski and loves colder weather activities, host a night at a popular bar in Whistler or Vail.
Would you like to attract football fans? Have you ever thought about tailgating with the fans? Join in on the festivities. Show your consumers that you are like them and you enjoy the activities that they do. Make sure your approach is authentic. Tailgating culture is about a community of sports fans sharing their love of the game. Are you the quintessential football beverage brand? If you are the new kid on the block, you will benefit from spending time with your consumer. This will help you make better marketing decisions. Get honest feedback about your packaging or flavor profile. Everyone on your team should participate in field marketing, even the CEO. To be authentic, remember you need to show up more than once. Commit to tailgating with football fans as much as possible. Be the familiar brand that shows up rain or shine because you love the game and want to be a part of the community.
Simply put, you attract your consumer by acting like your consumer – by embodying who they are and what they desire.
Connecting is easier than you think. Be who you say you are, nothing less and nothing more. Imagine buying a beverage for many years; you love this brand because it is consistent – same great taste and quality. Then, one day, you take a sip, and something is off. You read the label and realize they added in another ingredient. It is a slight deviation from the previous beverage you loved, but it is not the same. You give it another try but realize it no longer meets your expectations, so you decide to move on to another beverage you like or a brand that always stays consistent.
Just like all relationships in life, being consistent builds authentic relationships. Are you a beverage brand that stays true to your mission statement? Your consumer promise? Or do you cut corners when there are higher gains at stake? Are you driven by popularity and the short wins that happen when you chase social media trends? Authentic connections take time to build and seconds to break. This is where a lot of brands struggle. It is enticing to jump on the viral bandwagon. It pays off for some brands, but it does not work out quite well for others. New brands can benefit from viral trends since they are still in the audience-building stages. Brands with an existing audience they
worked hard to captivate can fall short if they jump on a trend that could alienate their consumer.
Are you struggling to build a loyal consumer base? Ask yourself, would you buy this product if you saw it in the store? Are you compelled to buy this beverage when you see a social media post or ad? If your marketing strategy does not excite you and your team, it will not excite your targeted consumer. Remember, the first consumer of your beverage is you. Consider the time you spend perfecting the taste, sourcing quality ingredients and finding the right bottle and label. The love of the product must occur during these stages. Amongst other beverage brands, you should see your product as the diamond in the rough – the beverage you would reach for on a busy liquor store shelf where the choices are endless. There are so many beverages to choose from, but it is the winner every time.
Belief in your product shows in every detail. Fortunately, brands can reach their audience without paying millions for traditional marketing. Out-of-home marketing is not affordable for everyone. The online landscape allows brands to create authentic ads. Each day, a brand can seize the moment and create a timeless video that best illustrates what it represents and how this beverage was made with pure heart and dedication – a beverage brand for the people. These are people who look for connection, work hard and want to know that you care. This product is more about them than it is about you. As a brand, if you can demonstrate this, people will believe you.
It is okay to go back to the drawing board and start again. Many brands refresh their websites and social media channels. If there is room in your budget, hire a brand strategist who can give you a 360-degree view of your brand and what it needs to capture an audience. Be sure to hire someone or an agency with a track record within the beverage industry. Every penny spent should be well earned, so choose wisely. For some brands, it is beneficial to hire a marketing strategist who will work exclusively with your company. It may take some time before you make headway. Meanwhile, having someone in-house will allow for more room to grow organically and authentically.
By: Jake Ahles, Morel Creative
In today’s competitive market, visual storytelling has shifted from a “nice-to-have” to an essential tool in brand building. Many brands, especially emerging ones, view cohesive visual storytelling as unachievable or reserved for big players with larger budgets. Instead, they focus on updating Instagram or TikTok sporadically, hoping this will carry them from the fringes to the forefront of their industry. However, effective visual storytelling is no longer a luxury limited to the big brands. A cohesive, clear, and consistent storytelling strategy can be the key to scalable, sustainable growth for any brand willing to invest the time and effort - with tangible ROI.
It’s the brands that devote meaningful time and resources to visual storytelling that rise above the
noise. This doesn’t mean investing millions in a Super Bowl commercial. Nor does it mean posting on social media multiple times a day - or even daily. It means understanding and showcasing what makes your brand unique—those elements that form your brand’s DNA and resonate deeply with your target audience. Successful brands know that product facts aren't enough. They must connect with their audience's aspirations and solve their pain points.
Your brand lives in the minds of your customers. Effective storytelling allows you to shape how they perceive you instead of leaving it to chance. Storytelling is your brand’s superpower, making your product not just visible, but irresistible. Here’s the hard truth: your customers don’t care about
Fillmore Packaging Solutions provides affordable beverage packaging for small and aspiring craft beverage makers.
Our machines are uniquely engineered to provide you with the bottling, canning and keg washing support you need for success!
your product. They care about what your product does for them—how it makes them feel, how it alleviates a problem, or helps them reach a goal.
Many brands avoid visual storytelling. They worry about its time, effort, and measurability. Let’s address these challenges directly.
1. Time: A structured, strategic plan can save time in creating visual content. A defined storytelling framework avoids last-minute content scrambles. Instead, you’re building a library of assets that can be reused and repurposed, saving time in the long run. Also, a good storytelling strategy lets brands produce 3+ months of content from a single production.
2. Effort: Crafting a visual storytelling program is undoubtedly a commitment, but the rewards are proportional. By putting in the effort to build a cohesive visual story, you’re setting the stage for long-term brand loyalty, engagement, and differentiation. A stage that meets your B2B
goals and B2C needs for sustainable, scalable growth.
3. Measurability: Brand growth and storytelling don’t always have short-term sales metrics. But, that doesn't mean they lack value. Brands that implement consistent visual storytelling and brand-building practices are often the ones that attract investors, raise capital, or get acquired. Longevity is what investors are after, not a flash-in-the-pan ‘viral video’. Brands with strong storytelling have gained trust and emotional connections with their audience. This is vital for long-term growth and market leadership.
To build a visual storytelling program that showcases how your product can solve customer pains and help them reach aspirational goals, focus on these four key principles.
1. Cohesion: A cohesive video and photo content program works together to tell a unified story.
Every piece of content, from social media to packaging, must capture your brand's essence and story. Cohesion reinforces recognition, trust, and loyalty among your audience.
2. Clarity: A clear brand story differentiates your offerings in a crowded market. When your audience easily understands what sets you apart, they’re more likely to engage, trust, and remain loyal to your brand.
3. Consistency: Consistent messaging reinforces your unique selling proposition (USP) and builds trust. By consistently communicating what makes your brand special, you create a dependable, recognizable image, fostering long-term relationships with consumers.
4. Connection: Emotional connection is crucial for brand loyalty. Addressing your audience's pain points and hopes makes your content personal. It drives engagement and advocacy, improving brand perception and sales.
Defining Your Unique Selling Proposition (USP): By clearly defining your USP with the F.E.E.E.D. ingredients we discussed in a previous article and implementing the 4Cs, you position your brand to stand out and rise to market leadership. Defining your brand's core ingredients and values—the "story" that makes you different—is essential to cutting through market noise. A solid USP, when done well, boosts your value to your audience and potential investors. It makes your brand more attractive for acquisition or investment.
Positioning as a Premium or Trusted Choice: Intentional, professional visual content helps position your brand as high-quality and trustworthy. In a market where consumers are increasingly discerning, the quality of your visual storytelling can be a powerful signal of your brand’s reliability and value. Premium content boosts your brand's image. It makes you a top choice as a craft brewery, distillery, or kombucha maker.
Driving Engagement and Loyalty: Great storytelling keeps your customers engaged over time, encouraging loyalty and repeat purchases. Instead of pushing your product on every platform, focus on
building a relationship. Show your brand's personality. Share behind-the-scenes glimpses. Showcase the faces behind the product. When your audience feels connected to your brand, they’re not just buyers—they’re advocates.
Creating Share-Worthy Moments: In today’s digital age, shareable content is a key driver of organic growth. When your content resonates, it invites your audience to share it, amplifying your brand's reach. Create shareable moments. It could be a beautiful bottle, a relatable brand message, or an impactful video. Let your audience become your brand ambassadors.
To start building a visual storytelling strategy, think benefits first, then features. Begin by listing out the core facts and features of your brand and product. Next, identify ways to use these features to educate, engage, and connect with your audience emotionally. Ask yourself:
• How does my product solve a problem for
my customer?
• How does my brand help my audience reach an aspiration?
Combine the facts and features that engage, educate, and connect with your audience emotionally. This forms the foundation of your brand’s story and a true differentiating factor—a Unique Selling Proposition that resonates.
This process allows you to plant the story of your brand in the minds of your target customers. It’s no longer just a product; it’s an experience, a solution, a part of their lives.
By addressing the perceived obstacles of time, effort, and measurability, and focusing on the 4Cs, craft beverage brands can use visual storytelling as a vehicle for growth. When your brand's visuals show not just what you offer but why it matters, you invite customers to be part of your story.
Embrace storytelling: Let it turn your brand into a compelling choice that customers are proud to support and share.
By: David DeLorenzo
s the year comes to a close and a new one begins, many bars and restaurants are in their high season. The combination of outof-towners as well as families and friends gathering to celebrate the holidays can lead to a successful season for those in the hospitality industry. But it can also bring additional safety concerns for business owners. While the holidays are for celebrating and good times, they are no time to get lackadaisical on important safety protocols. Here are some tips and reminders to minimize loss control throughout the holiday hustle bustle:
Train employees properly — Your staff members are the gateway to your success. Many custom-
ers will chose an establishment for the customer service. So hiring friendly, welcoming staff is key. However, it’s also important that those employees not only know how to treat the customer, but that they are well-trained in the safety protocols of your business. This extends to interaction with the customer as well as safety protocols in the kitchen. Staff members should be highly trained on not only their area of service (bartender, server, cook, dishwasher and host, for example), but the entire restaurant’s. Ensuring this can help you run a tight ship — and keep everyone safe.
It's highly researched and proven that people overconsume more during the holidays, with some
sources stating December through March as the range in which alcohol consumption spikes. This is great for business if you are a bar and restaurant owner. However, it can also bring unwelcome consequences if you and your staff are not carefully abiding by the laws and maintaining your own protocols when it comes to serving alcohol.
Maintain camera footage — Having timestamped video footage can truly be a lifesaver in the case of an incident involving customers or staff. Think of video surveillance as a safety net for your business — one that you need to maintain. I highly recommended holding onto camera footage for longer than 30 days, even if you don’t think there was any incident during that time. This can be one of the most persuasive pieces of evidence in the case of a lawsuit and you won’t regret having it if that time ever comes.
Check IDs (and check them twice) — It’s better to be over cautious than under cautious, particularly at this time of year. Overserving is one thing, but overserving a minor is quite another. Make sure servers always check IDs and don’t be hesitant to have another staff member give it a look or ask for a secondary form of ID if there is any question about validity.
Security isn’t seasonal — Depending on the type of establishment you run, consider heightening security during holiday and high seasons. When overconsumption increases, this can lead to poor decisions and aggression. Having added security to support double-checking those IDs and for ensuring no one enters your establishment that has already been drinking in excess can help save your business. It’s also beneficial to hire someone that has a background or experience in security. This role requires brains and brawns.
The bottom line is that just one claim, at any time of the year, can result in a 50% to 100% increase in your insurance rate for the next year, at least. And for the most part, this is avoidable by taking these simple precautions.
Stay on top of your premiums payments — As the holidays come to a close, it’s important that your businesses finances are kept up to date and that
you’re making timely payments on your premiums. They are the bedrock of your coverage — not just to keep your policy active, but to ensure that when the unexpected happens, your policy stands strong, ready to protect your establishment. If you keep up to speed on your premiums payments you won’t have to worry about any gaps in coverage that could sneak up on you in the new year.
Have, and be able to access, documentation — It’s also important to make sure your documentation and certifications are in order (and easily accessible) in the event of an audit. It’s crucial to understand that audits are not just about numbers but about ensuring your coverage reflects your reality. This will safeguard your establishment against the unexpected.
Speaking of documentation and certifications, they are the tapestry of the hospitality industry and the shield of protection for your business. It’s not only important to have them but be able to access them when needed. When looking ahead to 2025, consider upgrading your organization systems. For example, you can invest in an app that allows you to consolidate your documentation and certifica-
tion into one easily accessible format that you can get to at a moment’s notice. It’s not just about having the proper documentation and certifications, it’s about proving that you have them.
Work with a trusted specialist — End of year is a good time to review your policy, which should be done annually. When doing so, make sure you meet with an experienced specialist that is well-versed in the intricacies of your industry. At the end of the day, the rate is the rate. Unfortunately, this is the result of the amount of lawsuits that occur.
However, if you find a specialist who works with businesses in your industry, you’re paying for the expertise that they can bring when advising you on your policy. This is invaluable, especially if you ever do get into the unfortunate instance in which a claim is filed against you, a staff member or your company as a whole.
An experienced and knowledgeable insurance broker can review your current policy to ensure the documents are accurate and that they truly represent your coverage. They can also advise you on the importance of life insurance and buy-sell agreements. For many restaurateurs, these can seem like investments for the future. However, they are actually the lifelines of today, to make sure that your business not only survives, but thrives, even in the case of the unexpected.
Consider your broker your partner in your thriving business. They will help you through the good times and bad. More than simply selling you a policy, a trusted insurance partner will be able to provide you with peace of mind, assurance, and a shared vision for the future of your business.
So as you head into 2025, make a list — of the things you need to do in the new year to ensure the safety and protection of your business and your staff members — and check it twice.
Out of his passion for serving the restaurant and hospitality industry, David DeLorenzo created the Bar and Restaurant Insurance niche division of his father’s company The Ambassador Group, which he purchased in 2009. For more than 20 years, he has been dedicated to helping protect and connect the hospitality industry in Arizona. For more information visit barandrestaurantinsurance.com.
By:
In late September, 2024, Hurricane Helene ripped through the Southeast U.S. with what President Biden called “history-making” effects. With a rising death toll and billions of dollars in damages, the impact on families and communities is devastating. With a federal major disaster declaration for counties in Florida, the Carolinas, Tennessee and parts of Georgia some financial relief was provided. Unfortunately, small businesses face significant challenges after a natural or unexpected disaster like Hurricane Helene. While the impact may vary based on location, industry and disaster level, there are a few key steps that beverage businesses can do to lessen the economic impacts of natural disaster and acquire disaster loans.
Impact: Buildings, inventory, and equipment can be damaged or destroyed by high winds, floods, and debris associated with natural disaster. Likewise, businesses can often face delays or denials in their insurance claims, which delays cost repair or stretches the timeline for repairs.
Recovery Tip: Assess the damage quickly and file insurance claims for your small business immediately. Sometimes it can be difficult to remain level-
headed after disaster, but remember to take many photographs, keep records of the damage, and work with reputable contractors to get estimates for repairs or replacements.
Impact: Forced closures during and after a disaster can result in a significant loss of revenue, especially for beverage businesses that rely on daily sales cycles like bars/pubs, brewers, distributors and service-based companies. Transportation and logistics networks may be disrupted, making it difficult for businesses to receive supplies. And in dire cases of emergency, customers may leave the area temporarily or permanently, reducing demand for services.
Recovery Tip: Apply for SBA disaster loans or local assistance programs to cover lost income and operational costs while your business is closed. Consider moving some operations online or offering limited services to keep cash flow going and to maintain your sense of the customer base during unexpected times.
Impact: Weather disaster can disrupt the transportation of goods and supplies, causing delays or shortages.
Recovery Tip: Diversify suppliers if you feel you are relying on a single source for one good or product. Establish backup agreements with alternative vendors and explore local suppliers who may have the ability to provide more in the circumstances.
Impact: Power outages can disrupt business operations, including online orders, point-of-sale systems, and production.
Recovery Tip: Invest in backup power solutions, such as generators, to keep critical operations running during outages. Also, cloud-based services can allow for remote access to accounts, files and programs as needed.
Impact: Employees may be physically unable to report to work due to displacement from their homes or several transportation challenges. Most small businesses see an uptick of employee absenteeism during times of disaster.
Recovery Tip: Create an emergency communication plan to stay in touch with employees. As is possible, offer flexibility, including remote work options, or temporary paid leave to keep your workforce intact and loyal.
Impact: Your customer base may be financially impacted by the disaster, leading to reduced demand for your products or services.
Recovery Tip: Adapt your marketing strategy to target new or existing customers online. Consider offering discounts or flexible payment options for loyal customers during the recovery phase.
Impact: Repairing damage, replacing equipment and restocking inventory can significantly increase operational costs after a hurricane.
Recovery Tip: Seek financial assistance, such as SBA disaster loans, FEMA grants, or state and local programs. These can help cover recovery expenses without straining your cash reserves.
Impact: If your business is unable to fulfill orders or provide services, customers may turn to competitors, damaging your brand.
Recovery Tip: Communicate with your customers about the status of your business. Be transparent about delays or issues and provide regular updates to maintain trust and customer loyalty. Remember, it’s best to be genuine when communicating about challenges. Recognize that many of your customers may be dealing with similar negative effects.
Impact: The emotional toll of dealing with the aftermath of a disaster, combined with financial uncertainty, can be overwhelming for business owners.
Recovery Tip: Beverage business owners may have invested personal savings into their business, and the destruction or disruption caused by natural disaster could be devastating for their personal finances. In any instance, beverage owners should seek support from local business networks, recovery organizations and mental health resources.
Impact: While disaster loans and grants are available, the application process can take time, and many businesses may face immediate cash flow problems while awaiting assistance. Likewise, it can be daunting to navigate the complex paperwork required for disaster loans, insurance claims or government aid.
Recovery Tip: Reach out to a trusted financial advisor to help you sort through complex paperwork or claims. Financial experts, such as Loan Mantra, can help you determine the best economic recovery strategies and help you find assistance. Similarly, many nonprofits or other professionals are available to help small businesses get disaster loans and aid.
After a natural disaster like Hurricane Helene, small businesses can access various disaster loans
through the U.S. Small Business Administration (SBA). The SBA offers disaster assistance in the form of low-interest loans designed to help businesses repair or replace real estate, inventory, equipment, and other assets damaged or destroyed. Businesses of all sizes, private nonprofits, and homeowners or renters (depending on the loan type) may apply.
Applications are typically available through the SBA website or local disaster recovery centers. Businesses will need to provide financial statements, tax returns, and other documents to prove damage and financial loss.
Here are the primary types of disaster loans available:
Business Physical Disaster Loan: Available to businesses of all sizes to repair or replace real estate, equipment, inventory, and other business assets damaged during a disaster.
Loan Terms: Up to $2 million with terms as long as 30 years, depending on your ability to repay. Interest rates for businesses without credit elsewhere are low (around 4%) and slightly higher for businesses with credit elsewhere.
Economic Injury Disaster Loan (EIDL): This loan provides small businesses with working capital to meet necessary financial obligations that they could have met if the disaster had not occurred. It's designed to help businesses recover from the economic impact of a disaster, such as revenue loss.
Loan Terms: Up to $2 million at interest rates around 4% or lower for businesses without credit elsewhere, with a term of up to 30 years. These loans are only for essential needs, such as payroll, rent, or operating expenses.
Military Reservist Economic Injury Disaster Loan (MREIDL): For small businesses whose employees are essential to the operations of the business but are called to active duty. It helps the business meet operating costs until the employee returns.
State and Local Loan Programs:
State and Local Relief Programs: Some state and local governments offer disaster relief programs, which may include low-interest loans, grants, or temporary tax relief.
Non-SBA Lenders: Some banks and credit unions may offer special disaster recovery loans for businesses, often at low or no interest. Additionally, businesses can look for grants from nonprofit organizations or industry-specific programs.
Federal Assistance through FEMA:
FEMA Grants and Assistance: While FEMA generally helps homeowners and individuals more than businesses, it can aid some small businesses, particularly agricultural enterprises or non-profits, as well as provide information on SBA disaster loans.
The worst time to get documents in order needed for financial assistance is after a disaster happens. By then, important paperwork, vital records and electronic files may be destroyed or in-accessible. Uploading these files to a safe place can ease the process and put you first in line for assistance. Companies like Loan Mantra offer free accounts to house financial documents that are needed to apply for grants and loans in a secure digital format.
Hurricanes like Helene, or any other natural disaster, can hit beverage businesses hard, but with the right recovery strategies, you can minimize the damage. By securing financial assistance, communicating with employees and customers and preparing for future disasters, your beverage business can better weather the storm.
Raj Tulshan is the founder and managing member of Loan Mantra, a one-stop FinTech business portal that democratizes the loan process by providing corporate sized services and access to entrepreneurs, small and medium sized businesses. Connect with Raj and Team Loan Mantra at 1.855. 700.BLUE (2583) or info@loanmantra.com.
By: Earl E. Sullivan
n the hospitality industry employees come and go. If you are lucky, you will have them for several years. Employees staying in the hospitality sector can often bounce from place to place making training more difficult as well as more important. With new employees their training is your opportunity to break any bad habits from previous employers and set the standard at the very start of your new relationship. How your employees treat your customers, their team mates and the business will be a direct reflection on the business and corelate directly to profits. With that, employee training starts at the interview.
First, are you on time? It sets the expectations that they should be on time. If you do not set the standard, how will they know the true measure
of your expectations. Are you prepared? If you are not, why would they try to be prepared in the future? Are you professionally dressed? I fully understand that sometimes you have a new hire come in to interview after you just finished with some hard work and you are a little on the purple side. Take them in the back and show them where you were working and why your attire is relevant to the job you are doing and important for the role that they are seeking.
Next, all the same questions apply to the candidate. Are they on time? There are reasons why people can be late. New location that is unfamiliar, traffic or general lack of attention to detail. For us, late is a red flag. It indicates that the person did not think through the details of the job interview
beforehand and that you are just another job and not a sought-out destination to work. Are they prepared? Again, is this just a job or are they passionate about wine or your brand or the industry? Have they looked at the website? Do they know what type of beverage you produce? Do they know some of the common events you do or traits of your business, like being pet friendly? Did they visit your space prior to the interview to see how your business operates.
With social media and websites, it is not unreasonable to expect that a candidate would come in knowing something about your business. It is hard to find the right person but putting the wrong person into the culture with both your existing staff and your customers is worse than being shorthanded. Someone should want to know where they are interviewing, come prepared and be able to see if it is as much a fit for them as for you. Unprepared equals not invited back at our facility. Finally, are they dressed appropriate for your brand.
Every brand has a style - some are casual, some are edgy, some are old-school. Trying to fit someone into your brand that does not naturally fit will
be a long-term problem for both your team and your customers. They do not have to have on the trendiest clothes in the business or the most expensive shoes. However, if you are an edgy brand and they show up in khakis and a button down, you might want to ask some additional questions.
When you are first looking at candidates, you will get a sense of how well versed they are in customer service and in the trade. But you will also be setting the standards that your company will have if you conduct the interview with the same attention to detail that you provide your customers during service. In addition, how you treat the prospective employees as well as your main staff will determine how they treat the customers. They learn by seeing and experiencing the way the current team works. If you or your team do not smile, do not greet guests, or do not take an interest - why should they?
In our business, once we pass the interview stage we put the prospective employee into a trial shift. This allows them to see the pace of the workplace, engage with the team and see what type of clientele we have. Many a candidate have not made
it past the trial shift because of lack of empathy, unwillingness, or inability to pitch in, (even if they are new) or just a general attitude that does not mesh with the team. You never want to throw a curveball at your team with personalities unless they are looking for something to add to their current group dynamic. It is an easy, safe, and cost-effective way to see if this person is going to be a good fit for your team.
The next step in how you conduct your training is what you type of benefits you provide to the new staff member. Remember, it takes time and money to train someone. You want them to stay with you for as long as they can, and to do that they need the prospect for a living wage.
Food insecurity and housing insecurity are the two biggest issues facing employees in the hospitality sector. When they walk into your tasting room or bar and see that it is not busy, they instantly wonder if they will be able to pay rent or buy food. If they do this enough, they will either need to leave to find more secure wages or get a second or third job. When an employee has multiple jobs, by nature, they will be split on their loyalties and
focus. Lack of passion for what you are doing or not attending to the details of service lead to compounding problems with the guests.
Not everyone can afford full time or salaried employees but what can you do as an owner or manager to make sure that when things are slow the employee has an opportunity to earn or when things are busy, they can bank a little extra money to tide them over during the lean times? In our facility, our employees have full benefits which come with additional responsibilities. Not every facility is the same but the cost of training employees and the cost of losing customers from poorly trained employees is real across the board.
The right employee can make or break you. It is your responsibility to set the tone from the beginning. Invest time in bringing people on so that you add the right dynamic and personality to your team and your brand. You can train wine; you cannot train attitude. And it all starts with you at the interview. So, take it seriously and use the time wisely.
Rockville Pike, Nov. 12, 2024 (GLOBE NEWSWIRE) -- According to a newly published research report by Fact.MR, a market research and competitive intelligence provider, the global bio-tech flavor market is analyzed to reach a size of US$ 34.44 billion in 2024 and is further forecasted to expand at a noteworthy CAGR of 7.2% over the next ten years. The continuous developments in biotechnology, particularly in the fields of fermentation, microbial engineering, enzymes, and other technologies, are revolutionizing the manufacturing of natural flavors.
These techniques are essential because they enable the efficient and regulated synthesis of taste molecules from enzymes and microorganisms, producing bio-tech flavors of superior quality.
Moreover, these approaches require less money than resource-intensive conventional extraction methods. Because of these ongoing advancements, leading food and beverage producers are embracing bio-tech tastes on a large scale. Bio-tech flavor makers are also increasing their manufacturing capacity and focusing on supplying them at budget-friendly pricing by scaling up these biotechnological processes.
Request a Sample of this Report for Additional Market Insights https://www.factmr.com/connectus/sample?flag=S&rep_id=10427
North America's strong demand for natural and clean-label products is contributing to the market
growth in the region. Because the region is home to biotechnology enterprises, the market is growing at a noteworthy rate. Owing to the rising demand for flavored foods and beverages, the East Asian market is estimated to provide several lucrative opportunities in the coming years.
The worldwide market for bio-tech flavors is forecasted to reach a size of US$ 69.03 billion by 2034-end. The North American region is estimated to lead with a 23.9% portion of the global market in 2024.
The market in East Asia is approximated to reach a valuation of US$ 15.95 billion by the end of 2034. The application of bio-tech flavors in beverages is evaluated to increase at 7.2% CAGR through 2034.
Demand for bio-tech flavors in South Korea is projected to rise at 8% CAGR from 2024 to 2034. By flavor type, the microbial produced flavor segment is analyzed to generate revenue worth US$ 19.05 billion by 2034.
“Prominent bio-tech flavor companies are investing in R&D activities to generate new and advanced microbial flavors that enhance product offerings and meet evolving customer expectations for distinctive flavors and health benefits,” says a Fact.MR analyst.
Some of the leading providers of bio-tech flavor market are Givaudan S.A; International Flavors & Fragrances Inc.; Firmenich SA; Symrise AG;
Takasago International Corporation; Sensient Technologies Corporation; Kerry Group; Frutarom Industries Ltd.; BASF SE; Bell Flavors and Fragrances Inc.; Fab Flavour; Janiel Biotech; Garden Flavours Co. Pvt. Ltd.
The biotech company Cultimate Foods, based in Berlin's Biocube and Hannover (Institut für Technische Chemie, Leibniz Universität Hannover), successfully concluded its €2.3 million seed investment in April 2024. The business intends to expand its operations, business alliances, and manufacturing procedures.
In 2024, BASF Aroma Ingredients launches a new natural product under the Isobionics brand into the taste market. Isobionics Natural beta-Caryophyllene 80, a new product in the Isobionics brand, exemplifies the company's commitment to developing natural tastes that are impacted by consumer desire.
With reputable biotechnology companies and academic institutions establishing the benchmark for the development of biotech tastes, the US is renowned for its technical innovation. These advancements are improving fermentation and microbial engineering techniques, enabling the production of high-quality, efficient natural flavors.
Get a Custom Analysis for Targeted Research Solutions https://www.factmr.com/connectus/sample?flag=RC&rep_id=10427
By increasing the scalability and cost-effectiveness of bio-tech flavor manufacturing, advancements are encouraging food and beverage industries to use bio-tech tastes as an alternative to synthetic or traditional natural flavors. By ensuring consistent flavor quality and reducing manufacturing costs, this technological breakthrough is also contributing to a rise in industry adoption in the United States.
A high number of beverage producers are switch-
ing from artificial flavors to biotech alternatives derived from plants. The growing demand for natural solutions by consumers is the cause of this shift. Beyond their actual flavor characteristics, bio-tech tastes meet consumer desire for clean-label products free of artificial ingredients.
Biotechnology is enabling the production of unique and complex taste compounds that enhance beverages' sensory characteristics and appeal to a wider range of customers. The need for bio-tech flavors is also driven by the growing popularity of functional beverages, which frequently include bio-active ingredients for health advantages.
Fact.MR, in its new offering, presents an unbiased analysis of the bio-tech flavor market, presenting historical demand data (2019 to 2023) and forecast statistics for 2024 to 2034.
The study divulges essential insights into the market based on form (powder, liquid, paste), flavor type (vanilla & vanillin, fruity, microbial produced, essential oils), and application (food, beverages, nutraceuticals), across seven major regions of the world (North America, Western Europe, Eastern Europe, East Asia, Latin America, South Asia & Pacific, and MEA).
Discover Additional Market Insight from Fact.MR Research:
Flavor enhancers market is estimated to be valued at US$ 3.66 billion in 2023. The global demand
is set to reach a market value of US$ 6.08 billion by 2033.
Food ingredient market size is estimated to reach $35.15 Bn in 2024 and is projected to grow at a CAGR of 4.9% to end up at US$ 56.79 billion by 2034
Natural flavor carrier market is projected to grow at a steady CAGR rate during 2018-2028. Clean Label products augur the growth of natural flavor carriers.
Gamma-decalactone market is expected to grow steadily during the forecast period. The market is projected to exhibit faster expansion in North America.
Natural and organic flavor market is projected to be valued at US$ 9.99 Bn in 2024 and is projected to rise at 5.7% CAGR to ascend to $17.39 Bn by 2034
Fact.MR is a distinguished market research company renowned for its comprehensive market reports and invaluable business insights. As a prominent player in business intelligence, we deliver deep analysis, uncovering market trends, growth paths, and competitive landscapes. Renowned for its commitment to accuracy and reliability, we empower businesses with crucial data and strategic recommendations, facilitating informed decision-making and enhancing market positioning. With its unwavering dedication to providing reliable market intelligence, FACT.MR continues to assist companies in navigating dynamic market challenges with confidence and achieving longterm success. With a global presence and a team of experienced analysts, FACT.MR ensures its clients receive actionable insights to capitalize on emerging opportunities and stay ahead in the competitive landscape.
US Sales Office: 11140 Rockville Pike • Suite 400 Rockville, MD 20852
Tel: +1 (628) 251-1583
n an era dominated by digital transformation, the packaging and processing industries increasingly rely on big data to streamline operations and enhance efficiency. Central to this revolution is the concept of the "data lake"—a vast, dynamic repository that stores and secures colossal amounts of raw data. PMMI's white paper, Transforming Packaging and Processing Operations, offers a deep dive into the challenges and opportunities associated with data lakes, revealing how industry leaders leverage this resource to gain a competitive edge.
A data lake serves as a central point where businesses can store unstructured data across various
sources until needed. One of the unique features of a data lake–and this distinguishes them from data warehouses–is that they are not schema-in. This means they can take in raw data in its native format without changing any of the data attributes from the source. They only apply schema to the data on the actionable side of the data lake once it has been processed for analytics, making it schema-out. Data warehouses, on the other hand, are schema-in, meaning the data must be structured before coming in.
Data lakes are helping manufacturers solve concrete problems. With the schema-out structure of data lakes, manufacturers organize what information they need when they need it. This flexibility makes it an invaluable tool for machine learning,
analytics, and real-time reporting, helping companies to react swiftly to market changes and internal demands. On the other hand, manufacturers must define their data needs with a schema-in structure before using it. And in most cases, they only end up using a fraction of the data.
The packaging and processing industry is increasingly seeing the potential value of data as an asset. It is being used to measure and enhance business performance and operations, with applications including:
• Measuring performance and downtime
• Developing and tracking KPIs
• Driving operational improvements
• Performance opportunities
• Analyzing equipment
• Processing performance vs. expectations
• Tracking quality and production metrics
• Analyzing business operations
• Driving, planning, safety, BOMs, specs, and operations improvements.
For example, a quality problem—whether it is beverage contamination or a delivery that doesn’t meet specifications—can mean a dreaded slog through uncontextualized (or even paper) data to find out what happened. Moving to a data lake turns this process into a much simpler query that can be done in minutes. Proactively creating traceability reports means that manufacturers can quickly identify the underlying issue and pinpoint just the affected units, keeping products on the shelves and ultimately protecting consumers and the bottom line.
Finally, predictive maintenance is often considered the pinnacle of data-driven manufacturing. According to another report by PMMI, Trends in Remote Monitoring, the ability to use predictive maintenance was seen as either somewhat or very important by 83% of end-users. Reduced machine downtime is a major factor in end-users specifically investing in predictive and preventative maintenance, with 92% of end-users citing machine downtime as a very or somewhat important factor. Data is the foundation and requires a combination of people, process, and technology expertise. Without
enough data and the right data architecture, it will remain elusive.
Data lakes are the foundation to process and analyze immense amounts of sensor data in real time and then visualize it to enable pattern recognition. This opens the door to testing and training machine learning models on historical sensor data to identify the precursors to machine failure. As manufacturers and their technology partners fine-tune these models, they become increasingly adept at predicting machine failure far enough in advance to perform necessary maintenance to prevent failure.
However, the Transforming Packaging and Processing Operations white paper shows that while data lakes are widely acknowledged for their potential, many companies in the packaging and processing sectors are not fully tapping into this potential. End-users and OEMs alike admit that there is significant room for improvement in how they utilize data to enhance operational efficiencies and drive business growth.
One of the primary challenges in managing a data lake is ensuring the quality and consistency of the collected data. PMMI's findings indicate that data management practices vary widely, from manual data entry to sophisticated AI-driven analytics platforms. This inconsistency can lead to data reliability and usefulness issues, potentially turning a data lake into a "data swamp."
Security is another critical concern. As companies move more of their operations to the cloud, they must protect data against breaches and theft. According to the PMMI white paper, data governance and security challenges emphasize the need for robust strategies to manage and protect the vast amounts of data collected and stored in data lakes. This includes concerns about interoperability and sharing data across different platforms and stakeholders while ensuring data security and privacy.
One end-user participant in PMMI’s research pointed to the importance of storing data in the cloud so that it can be shared across organizations and noted, “the more data you have, the more value you’ll create at the data lake” and “the more people who have access to the data, the more that
value can actually be realized.”
However, data security and confidentiality concerns can prevent data from being shared and fully leveraged. These are often the most common threats within IT teams in factories and can lead to tension between IT and OT teams. The white paper suggests that action is needed to bring IT and OT leaders together and to involve IT specialists more in discussions about data analytics. Although the technology to leverage data offers “tremendous economic benefits,” very real risks can be “profoundly expensive to the organizations if any of these security vulnerabilities get exploited.”
Artificial Intelligence (AI) and machine learning are playing increasingly critical roles in navigating the complex data landscapes of the packaging and processing sectors. The rise of artificial intelligence and advanced analytics has transformed the potential of data lakes. These technologies allow companies to predict trends, automate decision-making processes, and optimize operations in ways previously unimaginable. For instance, as previously noted,
AI-driven predictive maintenance can anticipate equipment failures before they occur, minimizing downtime and maintenance costs.
The integration of AI extends beyond maintenance. It's also transforming operational processes by enabling the analysis of vast data sets to identify inefficiencies and optimize production lines. AI's potential to offer predictive insights can lead to significant improvements in both productivity and operational reliability.
The Transforming Packaging and Processing Operations white paper underscores the varying degrees of AI integration across the industry, with some companies at the forefront of innovation and others just beginning to explore the possibilities. The common thread, however, is a clear recognition of the need to invest in these technologies to stay competitive.
PMMI’s white paper stresses the importance of collaboration and standardization to maximize the
benefits of data lakes. By sharing data and analytics tools, companies can gain insights that would be unattainable in isolation. Standardizing data formats and analytics processes can also facilitate a more seamless integration of new technologies across the industry.
The PMMI white paper highlighted several collaborative initiatives, such as the Vision 2030 series and the OpX Leadership Network, which are focused on developing industry guidelines and best practices. These efforts are essential in fostering a more integrated and efficient data management and utilization approach.
Looking forward, the report suggests that embracing data-driven strategies will be crucial for the packaging and processing industries. PACK EXPO Southeast (March 10-12, 2025; Georgia World Congress Center, Atlanta) offers numerous resources, such as Innovation Stage presentations and networking opportunities, to aid in this transition. These gatherings allow industry leaders to share best practices, explore new technologies, and form partnerships that can help them navigate the complexities of data management.
The three-day event comes on the heels of a successful PACK EXPO International, the largest packaging and processing trade show this year. PMMI forecasts a convergence of 7,000 attendees to Atlanta from consumer-packaged goods and life sciences companies based in the Southeast to witness innovation in action, learn about the latest industry trends and topics, and network for brand and professional growth. PACK EXPO Southeast will feature 400 exhibitors displaying the latest solutions and technologies for 40+ vertical markets over 100,000 net square feet of exhibit space, making it a perfectly sized show where attendees can explore many solutions yet have a personalized experience and meaningful interactions to address their specific needs.
As the packaging and processing industries continue to evolve, the role of data lakes will become increasingly central. By addressing the challenges of data management, harnessing the power of AI, and fostering industry-wide collaboration, companies
can unlock the full potential of their data to drive innovation and efficiency. The insights from PMMI’s report and the resources provided at PACK EXPO Southeast are invaluable tools in this ongoing journey, helping businesses stay afloat in the vast data lake and thrive in these turbulent digital waters.
Dive into the innovation epicenter and discover answers to your packaging and processing challenges at PACK EXPO Southeast. Taking place in one of the U.S.’s most vibrant manufacturing hubs comes the new PACK EXPO Southeast (March 10-12, 2025; Georgia World Congress Center, Atlanta). Discover the future of packaging and processing at the most comprehensive show in the region offering crossover solutions for any of today’s biggest manufacturing needs to 40+ vertical markets. Brands will find the Atlanta location, a manufacturing hub of the region, convenient and easy to access for teams to attend, assess the latest technologies, learn from leading industry experts, and make valuable connections to meet current or upcoming projects. For more information and to register, visit packexposoutheast.com
By: Kris Bohm: Owner of Distillery Now Consulting LLC.
Ask a distiller this question and you will hear different answers from every person you talk to. Spend some time in Kentucky and you will hear that good bourbon is only made on continuous column stills. Step foot into a modern craft distillery and the distiller running the place may tell you that the best type of still is a hybrid batch still. Ask a distiller who distills using old world methods and their equipment of choice is often a pot still. Why this topic is eternally debated among distillers is that all three of these opinions are correct. What makes it so tough to sort out this debate is that just as great whiskey can be made on all types of stills. It is important to note that not so tasty whiskey can also be made on all 3 types of
stills when not produced properly. Let's weigh the pros and cons of each type of still and look at a few respected distilleries who are utilizing their preferred distillation method to produce world class whiskey.
How each type of still functions is an excellent starting point to unpack the debate. The design of a still plays a strong role in the profile and character of spirit it will produce. Each type of still utilizes a different design to extract the alcohol from the distillers beer. The difference is how the alcohol is distilled from the beer and rectified plays a strong role in the character of the spirit. This pronounced difference is subtle to the average person but the
difference is distinct to a trained palette. This difference is so distinct that if a distiller were to take two identical batches of beer and distill it on two different types of still the difference in flavor can be remarkable.
Pot stills are the oldest and well known style of distillation equipment. Pot stills, while effective, are not very efficient at separating the chemical components of a distiller's beer. When a beer is distilled in a pot still the spirit that is produced from the first distillation is known as low wines. These low wines are an unsavory spirit that is normally around 40% ABV and not suitable to be drunk nor barrel aged. To fully distill a whiskey on a pot still the low wines must be redistilled to fully separate the unwanted components from the spirit. During the second distillation the distiller makes their cuts to separate the heads, hearts and tails. The hearts which can be anywhere from 55 to 70% ABV are
kept and then diluted a bit before being put into a barrel to age. When a distiller is working with a pot still they will typically double distill the spirits. When distilling using this type of equipment the decision of the distiller when to make their cuts plays a critical role in the overall profile of the spirit. Spirits that are pot distilled are often described as heavier, oily and more flavorful when compared to spirits distilled in other ways.
Hybrid batch stills share many similarities to pot stills in that both pots and hybrids are batch distillation systems in which a single batch of beer is distilled all at one time. A hybrid still differs from a pot still in that there are internal components in a hybrid still that increase rectification, which in turn increase the alcohol concentration that is produced by the still. Because of this design in hybrid stills they are operated by doing a single distillation to produce a spirit that is ready to be barreled. During
this single distillation the distiller makes a heads and tails cut. The ABV of spirits from a Hybrid still is normally a bit higher than spirits from a pot still. This is due to the rectification that occurs on the plates of a hybrid still. The spirit that comes off a hybrid still tends to be a bit cleaner and more neutral when compared to pot distilled spirits.
Continuous Column stills are drastically different in operation and theory when compared to pot or hybrid stills. A continuous column still distills alcohol from a beer by continually injecting beer into a plated column that strips the alcohol from the beer and then continually rectifies the spirit while also removing a portion of the spirit which is referred to as the hearts. Continuous columns are known to produce spirits that are lighter in flavor and less oily when compared to pot distilled spirits. Continuous columns also have a very high output when compared to pot or hybrid stills. There is considerable rectification that occurs within a continuous column and as a result the spirit is noticeably different when compared to pot distilled spirits.
A wonderful example of all styles of distilled bourbon coming together is happening right in the heart ofTexas. The great folks who run the Milam and Greene Distillery in Blanco Texas have found a unique balance between pot distilled bourbon and column distilled bourbon. At their distillery the bourbon is being distilled using the old world method of double distillation utilizing a pair of Vendome Copper stills. The whiskey distilled by Milam and Greene is a bourbon that is rich and full of character emphasizing the grains in the spirit that stand out. While distilling flavor forward bourbon in house on pot stills Milam and Greene also brings in whiskey from other distilleries to blend. This outside bourbon comes from a distillery that runs a continuous column still, thus there is a distinct difference in the two types of bourbon that can be found aging in the Milam and Greene barrel warehouse. One of the popular and unique products offered at the distillery is their Triple Cask Bourbon. This creative whiskey is a blend of pot distilled bourbon from their own distillery that is blended with spirits from two other distilleries. The spirit is rich in character and stands proudly as a heavily awarded bourbon among its peers in Kentucky and Texas.
When it comes to selecting the best still for making whiskey there are many factors to consider.
Output of the equipment and budget are two of the most important. Pot stills and hybrid stills such as those found in many craft distilleries have a smaller capacity to produce. Small still can only produce a few dozen barrels of whiskey per year. In comparison continuous column stills typically produce thousands of barrels per year. The cost to produce thousands of barrels annually can be beyond the budget of goals for many start ups. Which leads to the decision to do pot or hybrid distillation. If you are trying to make the decision on which still is right for you, drop us a line and we can help you make that decision. In the meantime have a sip of good bourbon and savor the years of hard work it took to make that spirit.
Kris Bohm of Distillery Now Consulting. When Kris is not debating the merit of distillation methods you can find him traveling the world by bicycle.