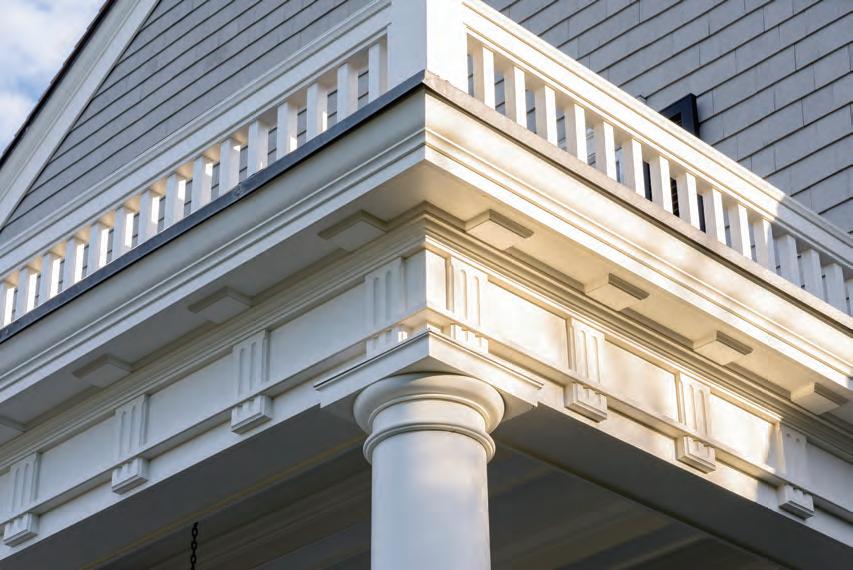
7 minute read
InduStry trendS
A WEALTH of traditional design elements, carried out in workable, dimensionally stable PVC, is calculated to stay crisp and unmarred with no more maintenance than an occasional power-washing. This home faces the water in Suffolk County, Long Island, N.Y. Contractor/fabricator: Seifert Construction; architect: Bruce Nagel + Partners
PVC architectural trim evolves to meet heightened demands
Withstanding what used to be once-a-century storms. Endowing luxury homes with bold, distinctive personalities. Empowering owners to spend more time enjoying—and fewer resources maintaining—their coastal retreats. All of these prospects, and more, stem from the continuing reinvention of PVC architectural trim products, an outlier category just a couple of decades ago.
Then things changed. Many architects, builders and homeowners had clung to the notion that natural wood was the only appropriate trim material for high-end residences. But, by the early 2000s, it was clear that both aesthetics and materials had reached their tipping points.
Younger homeowners (and quite a few of their elders) were elevating “zero maintenance” to a mantra for gracious living. And builders were mourning the bygone strength and durability of available solid-wood products. Old-growth stocks had vanished, and they were eager to get their hands on materials that would work as easily as wood but last more than a couple of seasons.
In stepped a few visionary manufacturers convinced that a new, “green,” manmade material could make life easier for owners and contractors alike. The innovation they had in mind was high-quality cellular PVC, which derives largely from plentiful natural gas and can be engineered to resist anything weather and climate can throw at it. Yet it yields finished results that replicate or even improve on the traditional painted or stained wood forms dear to architects and homeowners.
These manufacturers didn’t invent PVC; they reinvented it, dramatically enhancing its physical properties, creative potential and curb appeal. They’ve even introduced realistic, long-lasting wood-tone laminates for contrast with customary all-white trim designs.
This summer, I asked a few professionals who design or build high-end homes in demanding coastal environments about their experiences with the continually evolving possibilities of PVC trim products.
“Building homes on the Jersey Shore is uniquely challenging,” says
Cathy Van Duyne, of Van Duyne Builders, Inc., in Ventnor City, N.J. “PVC has become almost indispensable for us, especially because it’s waterproof and resists the extreme changes in climate and local conditions.
“If you look at some of the houses we’ve built recently, you can see why the owners are so happy with it,” Cathy says. “If the millwork had been done in wood, they’d have to repaint it every three or four years. That means a lot of money and disruption when there’s only a narrow window of time to use the house. The best time to paint is during nice weather in summer and fall, just when you don’t want scaffolds full of painters around your home.
“There’s been an explosion of advancements in homebuilding technology, from smart homes to sophisticated adhesives and fastening systems, to new building materials,” she says. “What we’re seeing with PVC trim, including smarter techniques for using it and specialized new products and tools, is a system that’s part of that overall revolution.”
Another builder, John Seifert of Long Island-based Seifert Construction, told us that continuing refinements in premium PVC means he can produce higher-quality results with each succeeding project. One reason he’s dedicated to a certain brand is that it keeps introducing an expanding range of profiles, sizes and features that extend his range of options.
“We tried them all,” he says, “and landed on one company for its quality, which was clearly superior. Then we saw we were gaining more flexibility, too. One example: We had to build an arch that normally would have taken two pieces of traditional, 8-foot-long sheet material. We realized we could use one sheet of PVC in a new, 10foot length—and finish the job with no seams! Small innovations come along on every single job, thanks to the big innovation that’s wrapped up in this material.”
He says his team finds ways to innovate in the fabrication shop, as well. “We had to fabricate an elaborate portico that called for dozens of small pieces, including a row of pilasters with a water table running right through it. Some of the components were only a couple of inches square. Making them out of modern pine was out of the question. If they didn’t break in fabrication, they’d fall apart in a year; we’re not getting the same wood my grandfather was us-
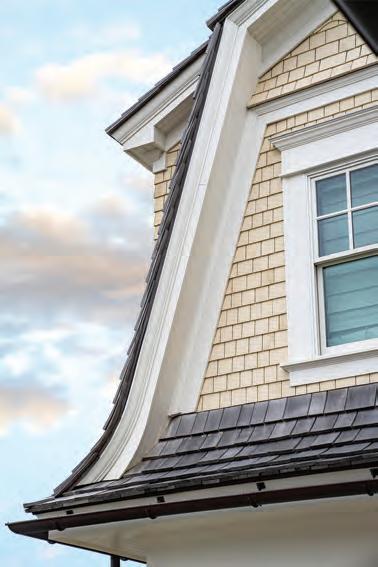
CONTINUOUS SWEEPING curves with fewer joints, realized in long PVC mouldings, distinguish a shingle-style coastal home. Tongueand-groove soffit and other PVC millwork will withstand harsh waterside conditions for decades, requiring little or no homeowner attention. Contractor/fabricator: VanDuyne Builders, Inc.; architect: S.J. Fenwick Associates.
sanTa FE sPrings, Ca • WWW.huFFLumBEr.nET (800) 347-4833
EWP • Big TimBErs/Long LEngThs • DisTrEssED WooD • D-BLazE® FrTW
Wholesale distributor of a Wide range of engineered Wood Products, including

PaCiFiC WooDTECh i-JoisTs
• PWi-20 • PWi-45 • PWi-60 • PWi-70 • PWi-77 • PWi-90
LVL BEam & hEaDEr
• beam/header • rim board • lvl studs • lvl columns
lengths from 8’ – 66’
rosBoro gLuLams & X-BEams
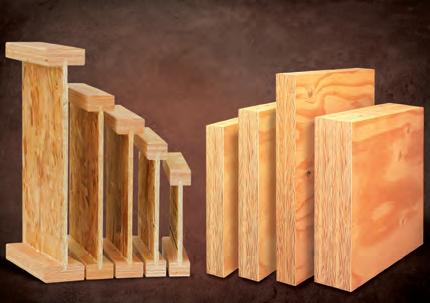
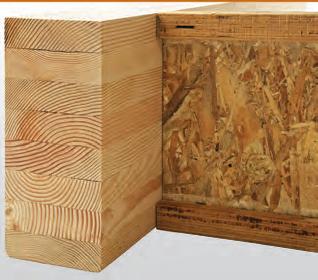
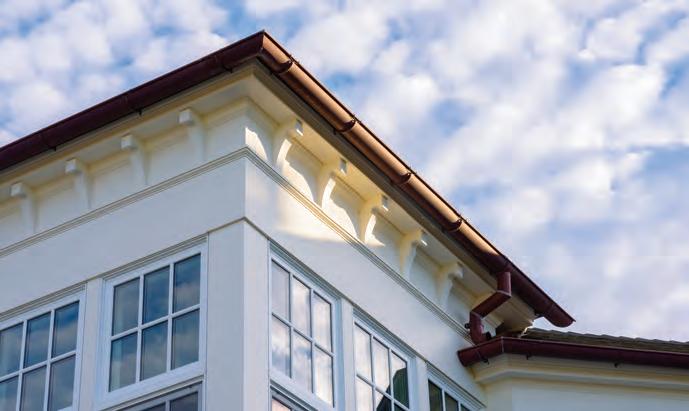
DECORATIVE BRACKETS, custom-fabricated from solid PVC stock, harmonize with sharply detailed standard PVC mouldings and trimboards. Premium PVC brings the luxury of complex architectural personality within reach, without the drawbacks of weather damage or upkeep. Contractor/fabricator: Seifert Construction; architect: Bruce Nagel + Partners.

A 270º ROOF, sheltering an upper-story porch, illustrates the range of challenging curves achievable in frieze boards, soffit and crown mouldings thanks to increasing lengths and enhanced workability of PVC trim components. Contractor/fabricator: VanDuyne Builders; architect: S.J. Fenwick Associates.

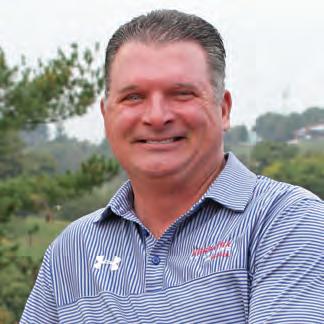
WEATHER-RESISTANT millwork characterizing this South Jersey region home can withstand extreme storms as well as day-to-day sunlight and spray, in part because advances in installation techniques, fastening systems, and adhesives have kept pace with PVC formulations. Credit: VanDuyne; Fenwick. ing. Instead, we brought the architect’s vision to life partly in custom-carved PVC, and partly in sharply detailed, stock PVC profiles from the same manufacturer, like crown mouldings and standard five-and-a-quarter boards.”
“One development worth mentioning: the amazing progress they’ve made in eliminating any hint of a “plastic” look and feel. Once you could spot manmade trim from a mile away. The material we use today comes across as authentic and substantial at any distance. Even historical districts that used to be strictly wood-only for restoration projects are looking at the expense of painting and maintenance, and starting to come around.”
Bill McConville, of Fenwick Architects in Linwood, N.J., is on the same page. “Take something like a decorative, painted wooden bracket,” he says. “If they’d had cellular PVC in 1901, they would have used it, because then they wouldn’t have had to scrape it and paint it every few years. Now that the technology has come into its own, homeowners accept PVC without giving it a thought. And now even preservationists are willing to consider it. We love to use it. From the architect’s standpoint, it holds up, looks good, and makes sense.”
We live in a world where homeowners show more knowledge about design and construction—and less patience with maintenance—than ever before; where exterior building materials take an increasingly heavy beating from the environment; and where a fresh idea can be your strongest competitive advantage.
My colleagues and I are convinced that this is a world where an evolving spectrum of building products, including premium PVC, have a major role to play. And we’re pretty sure today’s builders, architects, and clients are ready for new waves of possibility.
– Rick Kapres is vice president of sales for VERSATEX Building Products (www. versatex.com).
No shimming, planing, twisting, or warping.
The world’s rst manufacturer-treated LVL with protection through every layer using innovative TRU-CORE® technology.
PWT Treated saves you time and materials because it’s straight, stable, and uniform-sized. Plus, it’s stiffer and stronger, allowing for better views with longer spans—and it’s stainable! But wait, there’s more— it’s backed by a 25-year warranty against damage caused by fungal rot, decay, and wood-destroying insects.
Find out how this premium, preferred framing system can be built into your next project: sales@paci cwoodtech.com.
By
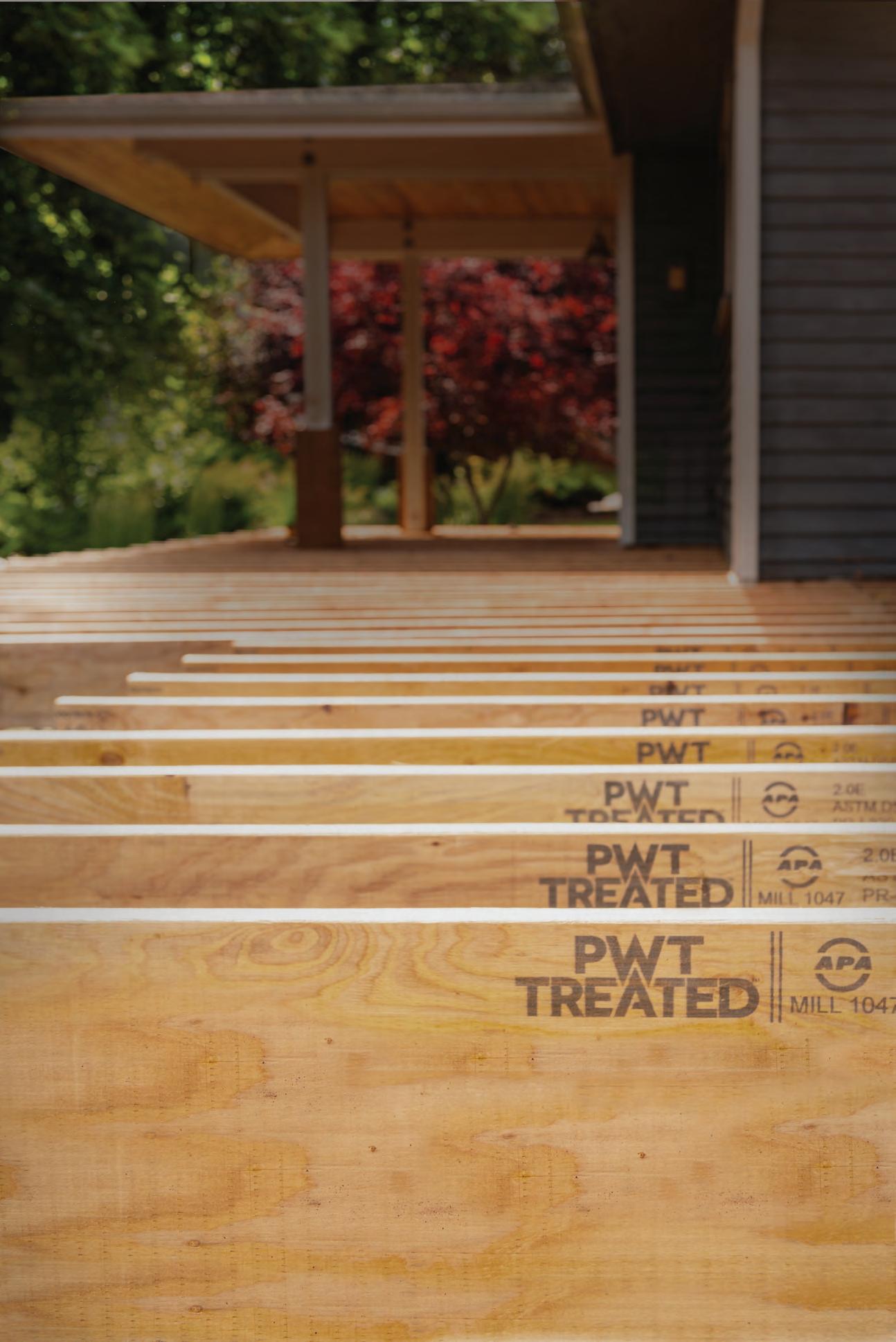