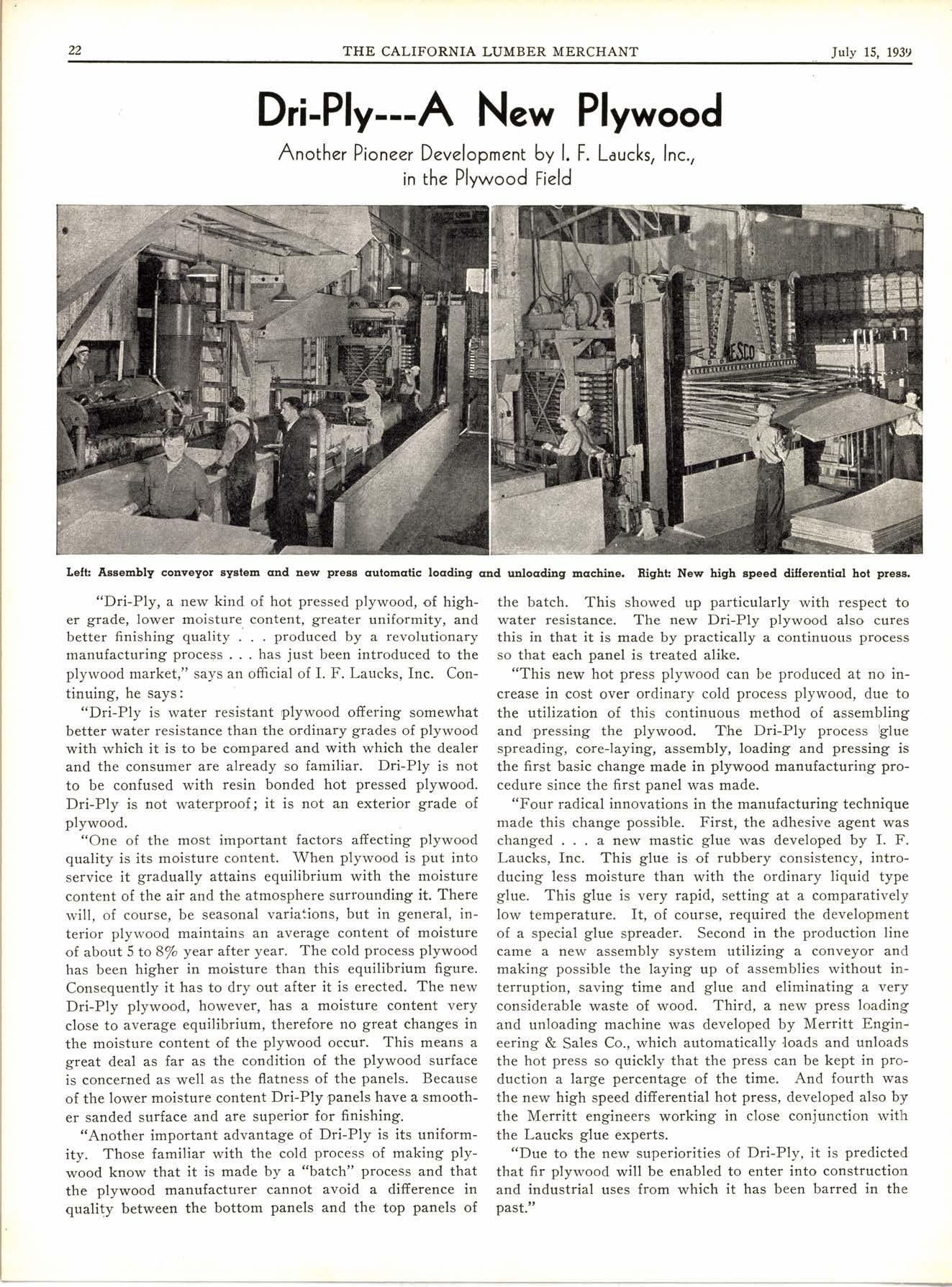
2 minute read
Dri-Ply---A New Plywood
Another Pioneer Development by l. F. Laucks, Inc., in the Plywood Field
"Dri-Ply, a ,new kind of hot pressed plywood, of higher grade, lower moisture, content, greater uniformity, and better finishing quality produced by a revolutionary manufacturing process has just been introduced to the plywood market," says an official of I. F. Laucks, Inc. Continuing, he says:
"Dri-Ply is rvater resistant plywood offering somewhat better water resistance than the ordinary grades of plywood with which it is to be compared and with which the dealer and the consumer are already so familiar. Dri-Ply is not to be confused with resin bonded hot pressed plywood. Dri-Ply is not waterproof ; it is not an exterior grade of plywood.
"One of the most important factors affecting plywood quality is its moisture content. Wh.en plywood is put into service it gradually attains equilibrium with the moisture content of the air and the atmosphere surrounding it. There will, of course, be seasonal variations, but in general, interior plywood maintains an average content of moisture of about 5 to8/o year after year. The cold process plywood has been higher in moisture than this equilibrium figure. Consequently it has to dry out after it is erected. The new Dri-Ply plywood, however, has a moisture content very close to average equilibrium, therefore no great changes in the moisture content of the plywood occur. This means a great deal as far as the condition of the plywood surface is concerned as well as the flatness of the panels. Because of the lower moisture content Dri-Ply panels have a smoother sanded surface and are superior for finishing.
"Another important advantage of Dri-Ply is its uniformity. Those familiar with the cold process of making plywood know that it is made by a "batch" process and that the plywood manufacturer iannot avoid a difference in quality between the bottom panels and the top panels of the batch. This showed up particularly with respect to water resistance. The new Dri-Ply plywood also cures this in that it is made by practically a continuous process so that each panel is treated alike.
"This new hot press plywood can be produced at no increase in cost over ordinary cold process plywood, due to the utilization of this continuous method of assembling and 'pressing the plywood. The Dri-Ply process lglue spreading, core-laying, assembly, loading and pressing is the first basic change made in plywood manufacturing procedure since the first panel was made.
"Four radical innovatio.ns in the manufacturing technique made this change possible. First, the adhesive agent was changed a new mastic glue was developed by L F. Laucks, Inc. This glue is of rubbery consistency, introducing less moisture than with the ordinary liquid type glue. This glue is very rapid, setting at a comparatively low temperature. It, of course, required the developme.nt of a special glue spreader. Second in the production line came a new assembly system utilizing a conveyor and making possible the laying up of assemblies without interruption, saving time and glue a,nd eliminating a very considerable waste of wood. Third, a new press loading and unloading machine was developed by Merritt Engineering & Sales Co., which automatically .loads and unloads the hot press so quickly that the press can be kept in production a large percentage of the time. And fourth was the new high speed differential hot press, developed also by the Merritt engineers working in close conju,nction with the Laucks glue experts.
"Due to the new superiorities of Dri-Ply, it is predicted that fir plywood will be enabled to enter into construction and industrial uses from which it has been barred in the past."