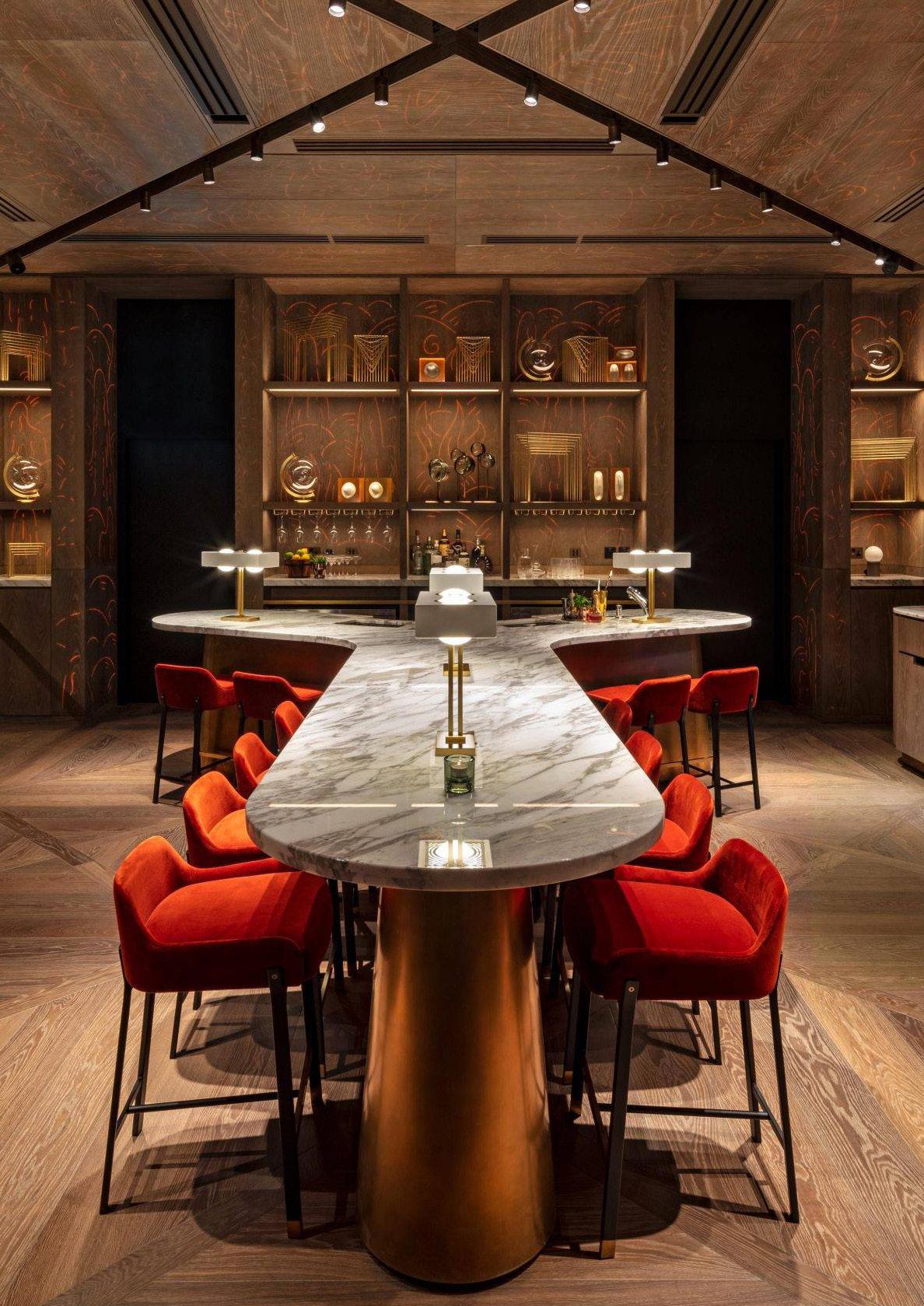
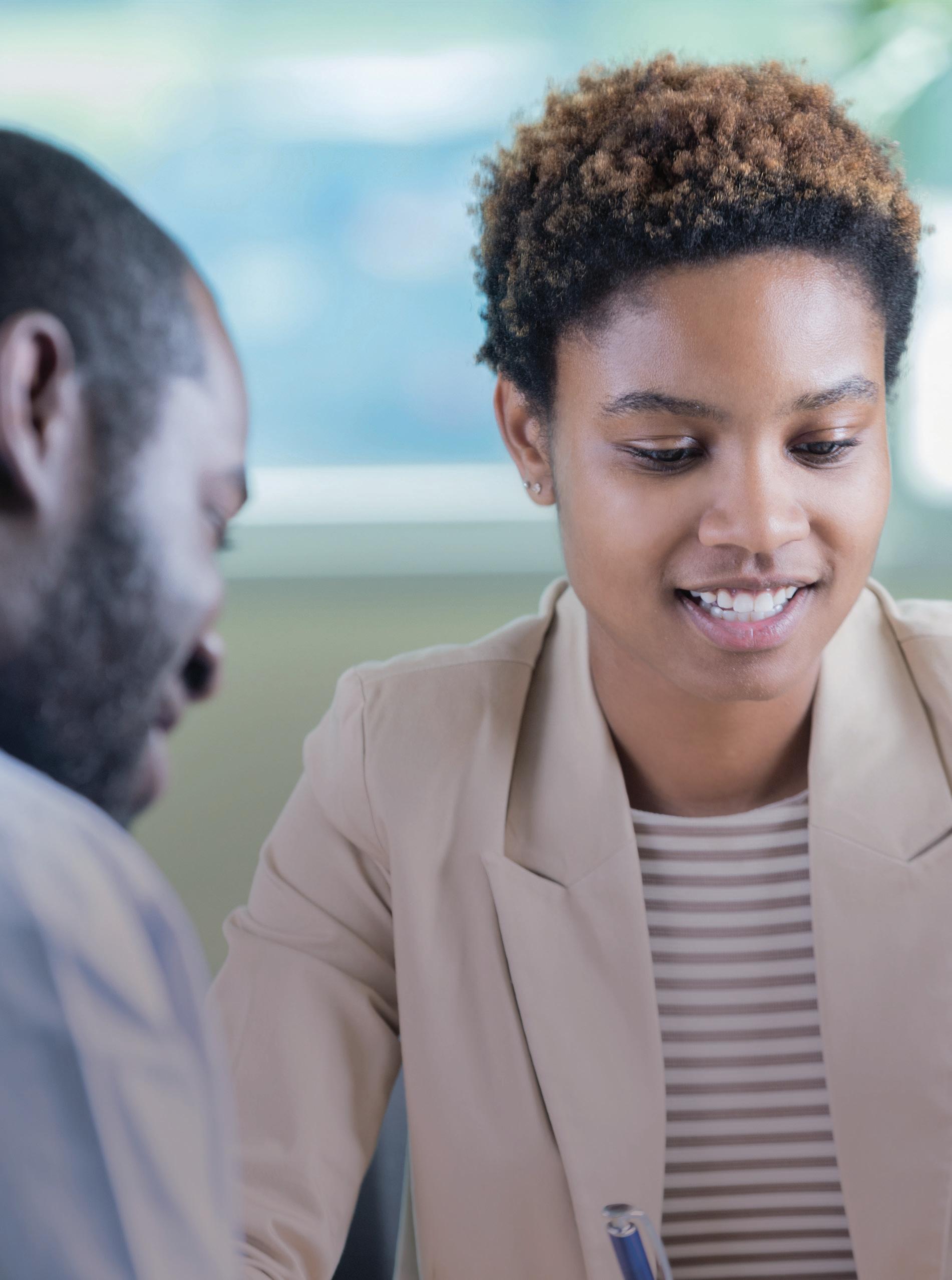
That’s how we help.
Switching your business is one of the most important decisions you’ll ever make. This is why we proactively manage the transition for you, to ensure minimal disruption to your business. We take end-to-end accountability until your business is fully banked, and a Business Banker is in play to look after the day-to-day relationship. It takes a bank that does more to help you start, run and grow your business.
For more information, contact:
Fathima Rahman
Email: frahman@fnb.co.za I Call: 087 328 0280
Eloise Heyduczek
Email: eloise.heyduczek@fnb.co.za I Call: 087 335 6859
Global Business Pursuit
Published and Distributed by Business Industry Publishing Ltd
For any enquires contact info@business-pursuit.net
Production
Donnie Rust Editor donnie@business-pursuit.net
Charles Brown Business Development Manager charles@business-pursuit.net
James Smith Operations Manager james@business-pursuit.net
Harry Lewis Accounts Manager harry@business-pursuit.net
Simon Poulton Project Manager Simon@business-pursuit.net
Design Felix Baldwin Design Assistant felix@business-pursuit.net
Harvey Tarlton Graphic Design harveytarlton.co.uk www.business-pursuit.net
If you would like more information about ways in which Business Industry Publishing can promote your business please call +44 (0)20 32878 795 or email | charles@business-pursuit.net. Business Industry Publishing does not accept responsibility for omissions or errors. The points of view expressed in articles by attributing writers and/or in advertisements included in this magazine do not necessarily represent those of the publisher. Any resemblance to real persons, living or dead is purely coincidental. Whilst every effort is made to ensure the accuracy of the information contained within this magazine, no legal responsibility will be accepted by the publishers for loss arising from use of information published. All rights reserved. No part of this publication may be reproduced or stored in a retrievable system or transmitted in any form or by any means without the prior written consent of the publisher.
© Business Industry Publishing Ltd 2024
As the year ends, the December edition of Business Pursuit brings inspiring stories of resilience, innovation, and determination. This month’s theme highlights the power of attitude and adaptability in achieving success.
Our lead story, Attitude Makes the Difference, explores the philosophy of E.E. Smith, showing how a positive mindset and commitment to excellence can turn challenges into opportunities.
In Stolle Machinery Company: Can They Make It? Yes, They Can., we see how a global leader overcomes supply chain disruptions through agility and relentless pursuit of quality.
Finally, Bluewing Midstream: Alacrity in Energy Infrastructure highlights how bold, efficient strategies are shaping the future of energy, addressing industry demands while modeling sustainable growth.
These stories remind us that challenges—whether personal or global— can be met with vision, perseverance, and action. Thank you for making us part of your journey this year. Here’s to a 2024 filled with success and new opportunities.
Donnie Rust
Global Business Pursuit
EE Smith
Donnie Rust
It has to be said that having the right kind of attitude stands for a lot. A reputation for style, confidence and a “must-do” approach are what the business world has always run on. Donnie Rust explores EE Smith.
The company, EE Smith was founded in 1897 by Edward Elijah Smith who ran his business from a small shop on Canning Street, Leicester. The self-proclaimed, ‘Master Craftsman’ was skilled as a plumber, gas and bar fitter and supplied and repaired gas stoves and gas chandeliers, proclaiming with understated professional pride, that all kinds of repairs would be ‘neatly executed’.
During these early years, EESmith took on a number of young apprentices to aid his flourishing business and as the business
prospered, it moved to new premises in 1937. In the same year, 14-year-old Basil Richardson was taken on as an apprentice, making pewter basins.
Although many of EE Smith’s apprentices who fought in the Second World War did not come home, following his wartime service in the Royal Navy, Basil Richardson returned to Leicester to find Edward Elijah Smith in poor health and the business in decline. At the age of 24, Basil became EE Smith Contracts’ Managing Director, foreman and entire workforce. However, in an age of heroes he did not wilt under the challenge but grabbed and ran with it.
Since then, the company has had the
opportunity to shift and change with markets and ride on the momentum of just getting things done. After turning down interest from market leaders, 2016 began an exciting new era when a management buy-out saw four of the long serving team take over the ownership of the business, with Neil Bottrill at the helm as the new Managing Director.
The £11.1 million buyout was made possible thanks to funding from Maven Capital Partners, an investment that reflected the confidence in Bottrill’s leadership qualities.
Bottrill, who has been with the firm since 1990 in a variety of estimating and commercial management roles, joined the board of directors in 2008 as commercial director. Even after becoming MD in 2016 following the buyout, he has continued the company’s spirit of driving hard into the future and always leading by example.
Having climbed up through the ranks and firmly established himself as the leader of the company, Bottrill reveals that EE Smith, still one of the UK’s leading privately owned specialist interior fit-out contractors, have been setting the industry standard for over 100 years.
“We are experts in fitting out some of the world’s most prestigious hotels, commercial interiors and private residences,” he says, “Our interior solutions are engineered to the finest tolerances, ensuring the finished product perfectly matches the designer’s vision.”
Further to this, EE Smith Contracts is also one of the UK’s leaders in training apprentice joiners and cabinet makers, taking on new applicants every year, and have seen over 200 apprentices successfully pass through their programme. Bottrill explains that it is this marriage of technology and tradition that allows his company to deliver highquality solutions to design briefs without compromising on aesthetic requirements.
“Our outstanding level of project
We are experts in fitting out some of the world’s most
management is one of the key elements which sets us apart within the saturated industry,” he says, “ With an in-house team of directly employed design managers, technical services managers and preconstruction coordinators, we are able to seamlessly take a project from tender stage to completion, whilst providing a consistent project management team to the c lient.”
And according to him, it is this ethos that is the core to their success and one of the many reasons they have such a longstanding rapport with their repeat clients. This close control over every detail makes them proud to be one of the UK’s very few contractors with a turnkey offering.
Regardless of circumstances, EE Smith has a reputation for being outstanding, for example in 2022 when many companies were still struggling to recover from the ripples of Covid, they posted the highest annual revenues in the company’s history, with an additional £60 million of secured work for the new financial year.
It was fitting as they also celebrated their 125th birthday in 2022. Bottrill explains that the record-breaking activity was secured partly by working on multiple prestigious developments including the luxurious Peninsula London hotel overlooking Hyde Park Corner and the completion of 15 super-prime apartments in Knightsbridge in London. Profits have bounced back strongly following Covid-19 and are forecast to exceed pre-pandemic levels for the year ahead.
Generally working with around £60 million worth of secured work, EE Smith Contracts enters 2025 with their usage aplomb and confidence. But have gone a step further as pioneers in their business
EE Smith Contracts has a long history of training youngsters, and a significant number of our current employees are former apprenticeships
with a focus on sustainability.
The business, which employs 285 staff, has reduced carbon emissions by over 20 per cent in the last year despite the growth in activity at its sites in Leicester and London by investing in a new £125,000 extraction system. There is also continued growth in long-established apprenticeship programmes, with 35 new apprenticeships having been recruited since the outbreak of Covid-19.
Neil Simpson, Finance Director, says, “EE Smith Contracts has a long history of training youngsters, and a significant number of our current employees are former apprenticeships who have stayed with us because it is a family environment. We have established great links with London colleges and have thirty apprentices on our sites in London learning from among the finest craftspeople in the country. The London labour market is very dynamic and we’re building the EE Smith Contracts family environment on those sites as well to retain our apprentices and provide a pathway for their career. Further reductions are forecast in our carbon emissions following significant investment in carbon saving technology in the last six months because this is an area which is really important to us.”
Stolle Machinery Company
Donnie Rust
Stolle is the foremost provider of machinery for manufacturing two-piece cans and can ends in the canmaking sector globally. Renowned for their highspeed capabilities, Stolle’s machines serve as the cornerstone of canmaking operations worldwide, renowned for their demonstrated productivity and unwavering reliability.
Offering comprehensive solutions at every scale, whether individual machines, line modules, or swift service with OEM parts, to the conception, construction, and initiation of entire facilities, Stolle’s technical expertise ensures clients consistently receive equipment featuring cutting-edge engineering advancements and enhancements. Canmakers globally rely on Stolle to bolster their productivity and profitability with many acknowledging the company’s unwavering support.
Stolle Machinery takes its name from Ralph J. Stolle, the founder of the predecessor company, The Stolle Corporation, established in Sidney, Ohio, in 1961. Mr. Stolle notably refined the high-speed production method for easy-open (pop-top) beverage ends, alongside other significant technical accomplishments. He also established a business philosophy that has steered the company through
more than six decades. This philosophy is straightforward: to develop and deliver the most dependable solutions and cutting-edge technologies to enhance the functionality and aesthetics of metal, particularly aluminium, packaging for their customers.
The utilization of aluminium in can manufacturing was a paramount development for several reasons. Firstly, aluminium is exceptionally lightweight, contributing to reduced transportation costs and energy consumption. Secondly, its corrosionresistant properties ensure prolonged shelf life and product integrity. Thirdly, aluminium’s recyclability makes it an environmentally sustainable choice, with recycled aluminium requiring significantly less energy for production compared to virgin aluminium. Additionally, aluminium’s malleability allows for intricate designs and easy shaping, enhancing branding opportunities. Lastly, aluminium cans are impermeable to light and oxygen, safeguarding the contents from deterioration, thereby preserving flavour and freshness.
Powered by innovation and guided by experience, Stolle has maintained it’s leading position in technology by delivering high-speed, precise, and safe packaging solutions. Such solutions that promote the brand experience through sustainability,
colour, shape, texture, and ease of use and by “Serving the world” by being seen as a local provider in each market.
“Along with the principles of good business and service, the values of the group are simple but applicable and festooned within the company’s core,” says Michael Larson, Chief Operations Officer for Stolle, “Safety, quality, sustainability, technology and customer happiness.”
Leadership
Over the last six decades it has been seen repeatedly that good leadership makes all the difference and often what makes or breaks a brand is who is out front. At the centre of their roadmap for the next century is how to find the right people for the job and provide them the right tools.
Now, at the heart of the company is the Stolle management team who offer a collective experience reaching across both industry and globe. From previous experience in managing global relationships, technology, and finance, they are well positioned to help continue the leadership of Stolle internally as well as internationally. With a focus on technology and a dedication to continuing Stolle’s globalization, each team member brings an invaluable perspective to the company. These experiences blend seamlessly into a vision for
The partnership excites us particularly because of Rockwell’s deep knowledge in the food and beverage industry
the future that include the highest levels of customer satisfaction and the development of revolutionary new technologies that will advance the industry.
As their yellow “wave of innovation” has indicated for years, Stolle is committed to advancing metal packaging through a constant flow of sustainable innovations and technology that will benefit customers. From some of the strongest and most metal-efficient tab designs available, to brilliant new equipment upgrades, to revolutionary new equipment poised to impact the next generation of can making, Stolle continues to make significant investments of personnel and funding to R&D in every area of can making. Stolle’s global technical centres are dedicated facilities that develop the advanced software and hardware that future industry leaders can come to rely on while producing the sustainable machinery features that today’s customers expect.
As if to prove this point, Stolle has been designated a Platinum OEM Partner by Rockwell Automation. Companies at this level have met the product design, marketing, and business relationship criteria of Rockwell Automation technology across their entire company. Having occurred in 2022, Rockwell’s strategic partnership will further help Stolle to develop innovations in advanced software and hardware across their product line. Rockwell Automation evolved its OEM Partner Program globally, establishing levels of participation based on need and output. As a Platinum OEM Partner, Stolle Machinery takes advantage of a true partnership approach with Rockwell Automation with executive-level engagements and alignment with strategic
growth opportunities along with various services for digital transformation.
“Rockwell Automation is pleased to welcome Stolle Machinery as a Platinum OEM Partner to our growing OEM Partner Program,” said Johannes zu Eltz, Vice President of Global Market Access, “Not only does this Platinum designation help Rockwell Automation partner with Stolle on initiatives, but it also adds diversity to our stable of partners, delivering unrivalled co-marketing opportunities, coordinated market planning with our sales force, and improved customer engagement with co-managed objectives.”
With its expanded range, which facilitates greater market access, streamlines processes, and standardizes product integration for manufacturers, the enhanced offering empowers stakeholders to maximize the benefits of Rockwell Automation technology. Anticipating an influx of platinum level partners, alongside numerous gold, silver, and bronze members, the company foresees the program becoming a premier opportunity for original equipment manufacturers on a global scale.
“The partnership excites us particularly because of Rockwell’s deep knowledge in the food and beverage industry,” said Michael Larson, Chief Operations Officer for Stolle. “With a long history of innovation, we’ll partner with Rockwell Automation to develop new machinery and technology to make production faster and more efficient for our customers.”
Stolle is committed to advancing their customer needs through ongoing innovation and technological advancement, backed by substantial investments in resources and personnel. Expert engineering teams collaborate with seasoned technicians at the company’s R&D Technical Centres to explore new ideas and concepts, integrating cutting-edge technology and materials as they become available in the market. Often, teams initiate projects from scratch, devising equipment that addresses industry demands for functionality, speed, and efficiency, even if it requires pioneering solutions. The Stolle R&D Technical Centres afford the company the flexibility to experiment and validate new concepts during their developmental stages. Strategically located within several assembly facilities worldwide, these centres facilitate seamless collaboration. Additionally, Stolle collaborates with various independent engineering firms to access specialized expertise when necessary.
Bluewing Midstream
Foylan Rhodes
Founded in July 2015 and headquartered in Houston, Texas, Bluewing Midstream LLC has rapidly emerged as a key player in the energy infrastructure sector along the U.S. Gulf Coast. Specializing in the acquisition, development, and operation of bulk liquid terminals, their keen strategic initiatives have enhanced the logistics and storage capabilities for their petroleum product customers while providing workable solutions to industry problems in the region.
With terminal assets strategically situated in Texas, at the Port of Brownsville, Bluewing’s location serves as a critical gateway to South Texas, Mexico, and other international markets. Supporting this, the company’s facilities offer a comprehensive suite of services, including bulk storage, blending, heating, and transloading of various bulk liquid commodities such as diesel, gasoline, base oil, wax, jet fuel, LPGs, and ethanol. Seen as an innovative infrastructure company by their various customers, CEO Todd Reid explains that they are guided by four pillars: Safety, Technology, Service and Communication, which have been essential in their ongoing expansion plans.
He explains that, in response to growing customer demands, Bluewing commenced construction on its Phase II Expansion Project in May 2019 and began operations later the
same year. This expansion added 300,000 barrels of new liquids storage capacity, capable of handling gasoline, diesel, jet fuel, and other petroleum products. Combined with existing assets, this brought the total storage capacity to approximately 1.1 million barrels.
“We were very excited to break ground on our Phase II expansion project and continue to build upon our existing operations,” Reid says, “Phase II allowed us to advance our strategic organic development vision while continuing to provide flexible and efficient terminal and logistics solutions to our customers.”
Phase III of the project includes the addition of four modes of transportation with tanks configured to ship and receive product by truck, railcar, barge or pipeline. This is expected to result in an additional 1.8MM Bbls of bulk-liquid storage capacity with 41 tanks ranging in capacity from 36,000 Bbls to 88,000 Bbls. Supported by 85 railcar spots with 40 automated loading positions.
A distinguishing feature of Bluewing’s operations is their commitment to technological innovation, particularly in automation. The company has implemented advanced systems that automate processes from scheduling to loading, significantly enhancing efficiency
and transparency. Customers can log into the terminal automation system at any time to monitor their product’s status, providing realtime insights into loading and transportation activities.
Vice President of Engineering and Construction, Danny Malone, highlighted the benefits of automation in a recent interview, saying, “Everything is automated from the time the driver comes into the time he leaves, and this seamless integration of technology not only streamlines operations but also sets Bluewing apart from competitors that still rely on manual processes.”
According to Reid, Bluewing has always placed a strong emphasis on environmental responsibility and the company utilizes nextgeneration, advanced vapor combustion systems to prevent emissions during terminal loading operations. These systems are designed to be super-clean and superefficient, ensuring that pollutants are not released into the atmosphere. He continues that understanding the relevance of their impact on the environment is an offshoot of the leadership team’s experience.
Combined with this, is a clear vision for the company’s growth. Chief exec Todd Reid, who leads the company with his 28
At Celerity Engineering, we believe every project has the potential to be truly special. We specialize in structural design, heavy industrial facilities, marine facilities, architectural engineering, and civil structures. We have the expertise and technology to complete your project, on time and on-point.
Whether it is a conceptto-completion project or a renovation, Celerity will partner with you to make it successful.
(plus) years in the energy industry, and has been instrumental in steering the company’s strategic direction, is supported by Vice President of Commercial Operations, Amanda Luckey, and Vice President of Engineering and Construction, Danny Malone, who contribute their expertise in commercial operations and engineering.
Bluewing Midstream addresses the unique logistical hurdles of operating in the Gulf of Mexico through targeted strategies focused on resilience, regulatory compliance, environmental safety, infrastructure investment, workforce training, and advanced cybersecurity measures. We were keen to take a deeper look at their approach and were able to highlight specific areas that make a difference.
Reid advocates preparedness, and Bluewing Midstream is well aware of the Gulf’s weather volatility and has fortified their facilities to withstand adverse conditions. This includes developing comprehensive contingency plans to ensure the safety and continuity of its operations during hurricane season, such as emergency storage solutions and implementing alternative shipping routes to mitigate the risk of supply chain disruption.
Additionally, recognizing that adverse weather can delay shipments and drive-up costs, Bluewing has integrated supply chain risk management strategies into its logistics planning. By leveraging its strategic location at the Port of Brownsville, Bluewing can offer flexibility in distribution channels and is equipped to reroute shipments as necessary to ensure continuity.
Navigating regulations is an important but time-consuming practice. Operating across multiple jurisdictions, Bluewing has invested in a compliance framework aligning with federal, state, and local regulations. This framework is particularly crucial given the port’s crossborder operations with Mexico, “Our in-house team regularly reviews regulatory changes to stay up-to-date and minimize operational delays,” says Reid.
This includes navigating the regional infrastructure limitations, such as port congestion. Although this is a challenge at
This involves prioritising safety training which is integral to our operational philosophy
major Gulf ports, Bluewing’s location at the Port of Brownsville, a less congested site than ports like Houston, allows it to avoid frequent delays. This tactical positioning provides a useful advantage in meeting delivery schedules and minimizing wait times for loading and unloading, which has led to further investment in infrastructure.
Bluewing is committed to modernizing and maintaining its infrastructure to ensure reliable operations. For instance, its Phase II expansion project, completed in 2019, added substantial storage capacity. Such investments enable Bluewing to manage operational disruptions while keeping capital expenditures in check.
Even a company as automated as Bluewing, still relies on skilled labour and they proactively invest in recruiting and retaining skilled professionals, focusing on attracting talent with specialized experience in energy and logistics. Additionally, Bluewing partners with local training organizations to cultivate a talent pool equipped with the required technical skills, particularly for terminal and storage operations.
“This involves prioritising safety training which is integral to our operational philosophy,” Reid says, “Employees undergo regular training sessions that comply with OSHA standards, ensuring they are wellprepared to handle the challenges of a highrisk environment. This ongoing commitment helps prevent accidents and maintain a high safety standard.”
Donnie Rust
EnerMech is a global engineering services company that provides integrated solutions for the energy and infrastructure sectors. Specialising in offering services such as cranes and lifting, hydraulics, equipment rental, training, and asset management. Their expertise ensures safe and efficient operations across various industries worldwide.
A standout business that offers clients a simple yet powerful approach consisting of nine key services, EnerMech was founded in 2008 and has made a significant impact for a company so young. Part of this is their holistic delivery approach, which ensures that their customers benefit from fewer contract personnel on site, improved safety, and reduced complexity.
With experts around the globe, they have the right capabilities and vision to serve the ever-changing needs of their industry with an extensive portfolio. As the company’s CEO Chris Brown points out, EnerMech does not generalize, it specializes, “We’ve successfully grown over the last fifteen years through a mixture of acquisitions and organic strategies,” he says, “Considering that we began as a small business from Aberdeen, we now have a presence in twenty-three countries and a workforce of over four thousand people.”
Employee focussed perfect days. Running a safe, profitable, and socially responsible business that drives innovation, enhances well-being, and contributes positively to the environments in which they operate is non-negotiable for EnerMech and this includes the safeguarding of their staff. This sustainable approach underpins and supports all core operations and means that they will protect the customer’s long-term interests, act responsibly and manage risks effectively to minimize the impact on the environment.
To this end, the company sets their goals on “Perfect Days.” A Perfect Day is one in which all employees return home safely and the environment remains unharmed. The goal, therefore, is to have a Perfect Day every day. This is supported by ENERGISE, their safety hallmark, which provides the training, tools, and support to give every member of the Enermech family a sturdy foundation in and understanding of their safety values.
This unfaltering commitment to QHSE drives their culture of honesty and transparency and results in a happier workplace where their colleagues feel safe, valued, and stimulated.
“Our people are at the centre of everything we do,” says Chris, “We have a talented team working at EnerMech and we promote diversity
and internal career development to ensure we build a workforce capable of meeting any challenge and as varied as the customers and regions we serve. This inclusive environment is an essential part of our culture and creates multi layers of stability which strengthens our foundations.”
As he says, by putting people first Enermech leads innovation and improving standards across a range of disciplines empowers their people to find integrated solutions to complex challenges, delivering sustainable support to better serve the customer’s needs. A business’ reputation for finding solutions to complex challenges and actioning them quickly is entirely dependent on the quality and sharpness of its team.
Bespoke. Tailored Solutions.
The company’s values are at the heart of everything they do, guiding decisionmaking, behaviours, and team management culture. Basic adherence to the simplest core approach is crucial, with regards to working safely, with integrity and respect for others. Focussing on quality and being a solution orientated organisation is how they stay at the bleeding edge of their industry.
Since launching into the market, a decade and a half ago, they have forged a reputation for rapid growth and innovative thinking. Through
Our people are at the centre of everything we do
judicious acquisitions, their customers benefit from more than 40 years of rich heritage in the industry. It is this combination of the energy of youth and the wisdom of experience that has helped them emerge as one of the major players in the global energy and infrastructure markets.
Recently, EnerMech won a five-year multimillion contract by TotalEnergies EP Congo for crane and lifting maintenance at a new facility at Pointe-Noire, the second largest city in the Congo.
The work scope will include specific maintenance of crane and lifting equipment, and onshore and offshore parts supply for three offshore sectors which include Likouf and Nkossa. The agreement also includes riser pulling systems, mooring, and tensioning systems.
EnerMech has established a new entity, EnerMech Congo, to conduct the work and has sub-contracted a local Congolese company, Congo Services, to assist in the delivery. The company is recruiting local Congolese personnel in onshore contract support roles with experienced local maintenance crew personnel provided by the sub-contractor. The new facility at Pointe-Noire will benefit the area through the establishment of an additional lasting technical provision and local employment opportunities.
EnerMech has previously worked with TotalEnergies SE on projects across the African continent and has also worked in Congo, on contract to Technip on the Moho Nord project.
“We have a well-established relationship with TotalEnergies which goes back many years,” says Steve Swanson, Vice President, Africa for EnerMech, “We are pleased that they continue to see the value of the trusted and experienced service that we provide and chose EnerMech to collaborate with them on this new project in Congo.”
We have a wellestablished relationship with TotalEnergies which goes back many years
To this, the Regional Director for Africa, Middle East & Caspian, Paul Cockerill adds, “EnerMech has been successful in securing new and retaining existing cranes, and lifting operations and maintenance contracts, as well as extending existing frame agreements, in a number of locations in Europe, Africa, Middle East, Caspian and Asia.”
He goes on to explain that this is due to a number of factors including delivery of well thought out execution plans, with a highly detailed focus on solution delivery and, more importantly their safety culture. Additionally, their highly qualified project management who bring their own expertise and many years of industry experience.
“We are committed to not only adhering to, but exceeding local content requirements through engagement of our global network of subject matter experts with minimal ex-pat project resourcing and we have a successful, proactive regional employee training and development plan,” Paul says, “Where possible, as is the case here with Congo Services, we engage incountry subcontractors and utilize local supply chains.”
Foylan Rhodes
Expocrete, a division of Oldcastle APG Canada West, are a leading manufacturer and distributor of highquality concrete products across Western Canada. Their extensive product line includes concrete pavers, retaining walls, masonry units, and industrial precast solutions that cater to residential, commercial, and municipal projects while offering much needed solutions to the cracks in the industry.
Offering a diverse range of products designed to meet various construction needs, including standard and architectural masonry units, including the beautiful terrazzo, a functional selection of sidewalks, walkways and rooftop patios that ensure durability and visual appeal, and their powerful retaining wall solutions that are engineered for stability and designed to complement diverse landscapes, providing both functionality and aesthetic enhancement.
With operations spanning multiple locations in Western Canada, indicating a substantial workforce dedicated to manufacturing, distribution, and customer support, the company has in recent years, focused on innovation and sustainability. Undoubtedly however, it is Expocrete’s commitment to quality and innovation that has positioned them as a trusted partner in
the construction industry and their approach to continually evolving to meet the demands of modern building and landscaping projects.
The landscaping and building industries in Canada, are important to the country’s economic growth and urban development but face a unique set of challenges shaped by environmental concerns, labour shortages, and rising material costs. As the nation, new and old customers alike, push for more sustainable practices and efficient construction, the companies that work within these sectors are under growing pressure to adapt to evolving regulations, technological demands, and consumer expectations.
One of the most prominent issues worth discussing is the shortage of skilled labour. With an aging workforce and a lack of new talent entering these fields, companies are struggling to find qualified workers for both technical and operational roles. This shortage is particularly pronounced in specialized trades such as masonry, plumbing, and electrical work, where despite government efforts to increase immigration and attract skilled labour, many companies report difficulty in filling positions, leading to delays in project completion and increased labour costs.
In the landscaping sector, this shortage impacts not only the speed at which projects can be completed but also the quality and precision of work. The demand for eco-friendly designs, like native plant gardens and watersaving irrigation systems, requires skilled professionals who understand sustainable practices, which is an area where expertise remains limited.
Supply chain issues, exacerbated by the COVID-19 pandemic and ongoing global uncertainties, continue to affect the availability and cost of materials. Prices for essential building materials, such as lumber, steel, and concrete, have risen significantly over recent years, impacting both small projects and large-scale developments. These price fluctuations make it difficult for contractors and developers to estimate project costs accurately, leading to budget overruns and potential disputes with clients.
The landscaping industry faces similar challenges, particularly with materials like soil, gravel, and plants, which can be affected by transportation costs and seasonal availability. Import restrictions and tariffs have further complicated sourcing, forcing companies to seek local or alternative materials that may
not always meet the same quality or durability standards.
As Canada strengthens its commitment to reducing greenhouse gas emissions, building and landscaping industries are under increasing pressure to adopt sustainable practices. New regulations aimed at reducing environmental impact require construction companies to consider energy-efficient designs, use eco-friendly materials, and reduce waste. While these regulations are essential for addressing climate change, they add further complexity to project planning and execution, creating more opportunities for error.
Landscapers are also facing greater demand for environmentally conscious solutions, such as xeriscaping and rainwater harvesting systems, to create resilient, lowmaintenance green spaces that minimize water usage. Additionally, developers are being asked to incorporate green building certifications, like LEED and WELL, into new constructions. These inclusions necessitate compliance with strict standards and often requires higher upfront costs, of which clients are usually reluctant to pay.
The issue with customers and clients expecting the latest services without accruing additional costs is an issue. As it stands, keeping pace with technological advancement is an expected challenge, as companies must constantly adapt to new tools, software, and machinery to remain competitive. In both sectors, technologies like Building Information Modelling (BIM), 3D printing, and advanced project management software have reshaped how projects are designed and executed. Other innovations such as robotic mowers, drone mapping for site surveys, and smart irrigation systems offer immense benefits but require a workforce skilled in these technologies. Embracing these tools is crucial to meeting client expectations for modern, data-driven designs, yet the associated costs and learning curve can be prohibitive with companies facing the bills themselves.
Weather Beaten
Canada’s diverse climate adds another layer of complexity that Expocrete have had to answer to. With projects needing to withstand extreme weather conditions, from harsh winters in the north to wet coastal environments, the company has found
that materials and designs need to endure temperature fluctuations, heavy snowfall, and flooding. With the frequency of severe weather events on the rise, resilience has become a top priority, driving demand for innovative materials and designs that can handle these challenges.
Increasingly, Expocrete’s clients are increasingly tasked with creating climateresilient landscapes that can tolerate drought, heavy rains, and even wildfires. This shift calls for expertise in native plants, soil health, and water management, which are areas where traditional landscaping techniques have fallen short in the past.
Expocrete’s products are not the only value that they offer customers. Their personalised services also includes navigating the complex web of permits, inspections, and regulations which poses a constant challenge for builders and landscapers alike. In Canada, each province has its own requirements, often adding time and cost to projects. In urban areas, additional considerations, like zoning restrictions and neighbourhood associations, can create obstacles, slowing down development timelines.
Furthermore, the rise of environmental, social, and governance (ESG) standards also impacts the building industry, with developers needing to demonstrate a commitment to social responsibility, which may involve hiring diverse suppliers, minimizing environmental impact, or ensuring fair labour practices. Expocrete’s assistance in meeting these standards has proven to be crucial for securing financing and maintaining a positive reputation but adds further complexity to project management.
The Canadian landscaping and building industries are navigating a period of profound change, driven by labour shortages, environmental demands, rising costs, and rapid technological advancement. Fortunately, these are the sort of challenges where Expocrete have been able to excel and they see these changes as opportunities for innovation, sustainability, and growth. By investing in skilled labour, embracing sustainable practices, and adopting new technologies, the industries are poised to continue shaping Canada’s urban and natural landscapes in resilient and impactful ways.
Based out of Norwood, Massachusetts, Gaston Electrical has provided expert electrical, low-voltage and fire alarm services to a range of industries since 1934. With services and products that are valued in many different sectors, they’ve worked in commercial, institutional, life-sciences, hospitality, and retail markets across New England. Daemon Sands reports.
Working within their signatory area of IBEW Local 103 Boston, Local 223 Brockton, and Local 96 Worcester, what really makes the company stand out is the level of pride they take in their workmanship. This combined with the team of highly skilled and extensively trained professionals is what makes up the guts of Gaston. They are a company striving to rise above the standards of their industry, but after almost nine decades, their influence on those same standards must be tangible.
Gaston Electrical has the infrastructure, leadership, workforce, and technology systems to deliver innovative solutions for large and highly complex projects throughout New England. With a team of over 275 field electricians and technicians, utilising a full fleet of service vehicles, providing important services to a hefty range of industries from life sciences to condominiums to restaurants
and hotels, the company, who are in their third generation of family ownership, work hard to keep up with the latest developments. But they have an advantage.
It is often said that one shouldn’t make business personal, however, the family have a legacy of creating reliable products and offering much-needed services in important industries, and conduct and professionalism is something they do take personally. As company president Michael Webber says, “Professionalism is personal and that’s what our clients have come to expect from us. We take business personally.”
According to Michael, the Northeast construction market has seen a slowdown in 2024 compared to the robust activity of the past five years. For the most part, new developer projects remain on pause due to limited large-tenant activity and movement. Broader economic factors, including elevated vacancy rates, the presidential election, and increasing construction costs, are also contributing to the sluggish pace of commercial construction starts. On the other hand, the Medical sectors continue to expand their facilities, and venture capital funding appears to be re-entering the market with targeted investments in smaller life science
projects.
“While cautiously optimistic,” he says, “We see early signs of momentum returning to the commercial construction sector.”
He goes on to reveal that long lead times for large switchgear packages and generators remain a significant hurdle for the construction industry in Greater Boston and beyond. These extended delays in procuring critical electrical equipment have persisted since the pandemic, straining project timelines.
Furthermore, the Northeast construction market has decelerated over the past year. With limited exceptions, new developer projects are largely paused due to minimal large-tenant activity. Broader macroeconomic challenges, such as rising interest rates, elevated vacancy rates, and climbing construction costs, are also contributing to the slowdown. However, there are bright spots, University and Academic sectors continue to invest in their facilities and infrastructure.
Many contractors maintain healthy backlogs, new commercial starts have slowed, and backlogs are transitioning into earned revenue without large-scale projects filling the pipeline. Macroeconomic factors, including high interest rates, inflation, record national urban vacancy rates (23.7%), and limited tenant movement, have left many sectors stagnant.
EMCOR’s core values of safety, integrity, transparency, trust, mutual respect, discipline, and teamwork are lived by the Gaston team every day
Gaston Electrical is somewhat protected from industry fluctuations since they were acquired in August 2022 by EMCOR Group, Inc. acquired Gaston Electrical Co., LLC. At the time Gaston Electrical had estimated revenues of approximately $140 million and still to be completed performance obligations of about $120 million.
EMCOR Group, Inc. is a Fortune 500 company specializing in mechanical and electrical construction services, industrial and energy infrastructure, and building services. They design, install, and maintain complex systems such as HVAC, electrical, lighting, air conditioning, heating, security, fire protection, and power generation across various sectors, including commercial, industrial, healthcare, and government. Additionally, EMCOR provides facilities management services, ensuring the efficient operation and maintenance of buildings and infrastructure
Quite clearly, the acquisition aimed to strengthen EMCOR’s specialty construction services in the Greater Boston area, enhancing its capabilities in key markets such as life sciences facilities and data centers. The addition of Gaston Electrical is expected to
continue to broaden and enhance the service offerings EMCOR provides to its customers in the region as well as adding additional clients and long-term partners to the mix.
While specific post-acquisition performance metrics for Gaston Electrical are not publicly disclosed, EMCOR’s overall financial performance has been strong. In the second quarter of 2024, EMCOR reported earnings per share of $5.25, surpassing analysts’ estimates of $3.68, with revenues reaching $3.67 billion.
This suggests that the integration of Gaston Electrical has contributed positively to EMCOR’s operations, aligning with the strategic goals outlined during the acquisition.
“EMCOR’s core values of safety, integrity, transparency, trust, mutual respect, discipline, and teamwork are lived by the Gaston team every day,” says Bill Weber, CEO of Gaston, “We are excited about our future prospects as a part of EMCOR.”
Dan Fitzgibbons, President and CEO of EMCOR’s Electrical Construction Services Segment added that they were pleased to expand their footprint in the Northeast with the addition of the Gaston team. This group brings important capability and expertise in servicing many of EMCOR’s core end markets, including life sciences facilities and data centers. With one of the most experienced executive and field management teams in the electrical construction industry, Gaston will further broaden and enhance the service offerings EMCOR provides to its customers in the Greater Boston area.
Weber added that they were delighted to join EMCOR, a company that has the same culture and commitment to excellence as themselves, “EMCOR’s core values of safety, integrity, transparency, trust, mutual respect, discipline, and teamwork are lived by the Gaston team every day. We are excited about our future prospects as a part of EMCOR. Principles and approaches aligned well with the two businesses ensuring that a solid undercurrent of professional could continue.”
Operating under the unified IMI brand as IMI Process Automation, the company formerly known as IMI Critical Engineering, is a legacy global engineering company headquartered in Birmingham, England. Founded in 1862 by Scottish entrepreneur George Kynoch, who established a percussion cap factory in Witton, West Midlands, the company over time diversified into various industries, where it applied its automation approach and underwent several mergers and acquisitions, eventually becoming fully independent in 1978.
Taking this time to evolve to suit the needs of their diverse client range, today, IMI Process Automation specializes in designing, manufacturing, and servicing highly engineered flow control solutions for critical applications. Catering to industries such as power generation, oil and gas, pharmaceuticals, and naval sectors, the company offers a range of products, including control valves, safety valves, isolation valves, and actuators, designed to withstand harsh environments and meet the needs of energy and production processes.
As of 2024, the company employs approximately 10,000 people worldwide,
with IMI Process Automation contributing a significant portion of this workforce.
Supported by their highly trained staff, the company operates manufacturing facilities in over 20 countries, emphasizing a culture of engagement and empowerment among their employees.
Roby Buyung, President of Process Automation at IMI tells us, “IMI is committed to building an inclusive organization, encouraging curiosity, ambition, and an entrepreneurial growth mindset.”
Strategic Decisions
Buyung goes on to add that in recent years, IMI has focused on strategic acquisitions to expand its capabilities and market presence.
Notably, in November 2022, IMI announced the proposed acquisition of Heatmiser, a leading UK smart thermostatic control manufacturer who’s philosophies on business and their project management aligned perfectly with IMI’s strategy to accelerate growth in smart building technologies.
Earlier the same year in June, the company completed the acquisition of Bahr Modultechnik, a provider of modular electric linear motion systems which was how they were able to further enhance their offerings in automation-driven markets.
“These strategic moves reflect our
commitment to innovation and growth,” says Buyung, “Positioning ourselves to address evolving industry challenges and deliver advanced engineering solutions across the company’s key markets.”
Breakthrough Technology
A perfect example of this is MI Truflo Marine, the marine valve specialist subsidiary of IMI, a prominent supplier of specialised, high-performance valves tailored to naval requirements who are delivering an innovative technology to the global defence market while addressing a long-term conundrum that has affected vessel owners and operators since maritime exploration began.
Biofouling, or biological fouling, is the accumulation of microorganisms, plants, algae, or crustaceans on wet surfaces that have a mechanical function, causing structural or other functional deficiencies. Left unchecked, the resulting build-up can cause corrosion and impact operational efficiency. A heavily fouled ship hull can result in powering penalties of up to 86% at cruising speed and even relatively light fouling by diatom ‘slimes can generate a 10–16% penalty.
IMI’s naval marine valves play a vital role in various applications, including weapons handling, where precise control and reliability are paramount. Preventing biofouling will
Unlike biocidal coatings and impressedcurrent systems, this low-power solution is a low-cost, lowmaintenance, and non-toxic solution to marine growth and fouling
help increase fleet availability while reducing maintenance and operational costs and ensuring seawater mechanical systems operate without impedance.
Buyung points out that IMI has a long history of developing technological advancements and, in this case, having worked with technology partner Sonihull, the company is able to offer a commercially proven solution to tackle biofouling for the naval marine market, both in dock and during operations. With over 30,000 antifouling solutions from Sonihull already installed on commercial ships, the secret at play here is the ultrasound-induced non-inertial agitation solution that disrupts the biofouling process and actively prevents barnacle and mussel attachment. The system is an ideal alternative to harmful biocides, which are increasingly being restricted by new environmental legislation as explains Mike SemensFlanagan, Global President of Marine at IMI.
“IMI Truflo Marine is proud to introduce a biocide-free system, particularly as legislation increasingly restricts the use of metallic biocides in existing antifouling systems.”
Semens-Flanagan explains that submarines are especially prone to biofouling, especially when undergoing maintenance or refits in dockyards, where stagnant water often accelerates the build-up and ingestion of biomaterial into ballast and cooling systems. Surface ships experience similar issues, with the US Navy estimating that biofouling costs US$56M per year for the entire DDG-51 class or US$1B over 15 years.
He says, “Sonihull’s ultrasonic antifouling solution, coupled with IMI’s deep domain understanding and qualification capabilities for the naval marine market, is designed for fit-
and-forget ease, and is suitable for any solid surface exposed to raw seawater,” he adds, “Unlike biocidal coatings and impressedcurrent systems, this low-power solution is a low-cost, low-maintenance, and non-toxic solution to marine growth and fouling.”
In October 2024, IMI Plc announced the acquisition of TWTG Group B.V. (TWTG), a leading Industrial Internet of Things (IIoT) specialist based in the Netherlands. TWTG will become part of IMI’s Process Automation sector, and it is expected that this strategic acquisition will further strengthen their position as an innovator in digital transformation and process automation, broadening their capabilities in wireless IoT solutions.
TWTG, renowned for its cuttingedge wireless products and LoRaWANenabled devices, offers solutions that enhance operational efficiency, safety, and sustainability across industries including energy, utilities, and heavy manufacturing. With this acquisition, IMI aims to leverage TWTG’s expertise to accelerate its growth in the fast-evolving IIoT market, providing customers with state-of-the-art digitalisation solutions.
The acquisition of TWTG aligns perfectly with our strategy to deliver innovative solutions that help our customers make smarter, more efficient, and sustainable decisions,” says Buyung, “TWTG’s unique technology and deep expertise in the Industrial IoT space will enhance our existing asset monitoring portfolio and help us deliver next-generation wireless automation solutions to our customers.”
Commenting on the acquisition, TWTG CEO, Nadine Herrwerth, revealed that they were humbled and excited to become part of IMI, adding, “This partnership provides us with a global platform to scale our innovative solutions, accelerate the growth of TWTG, and enhance IMI’s offering to its valued customer base. We see great potential in our joint future path.”
IMI and TWTG will collaborate closely to integrate their solutions and ensure a seamless experience for customers and channel partners. The acquisition is expected to bolster IMI’s expanding portfolio of IoT-enabled products, allowing it to better serve the growing demand for digital transformation across key end markets in process industries.
Klarius Products
Cassidy Banks
In the realm of automotive aftermarket solutions, Klarius Products Ltd stands out as a leader, specializing in emission control products. Based in Cheadle, Staffordshire, the UK-based company has a reputation for delivering product performance with a commitment to quality, an innovative approach to development and a sense of environmental responsibility that has earned them not only the trust of consumers but the respect of businesses.
Klarius Approach to Quality and Compliance
At the core of Klarius’s is a commitment to quality. With the automotive industry’s evolving emission standards and performance expectations, Klarius ensures that each product aligns with the stringent guidelines required for safety and environmental standards. To achieve this, they employ a dedicated in-house research and development team who’s entire focus is on crafting products that are both efficient and durable.
And, in order to bolster this, Klarius’s manufacturing processes are precise and reliable with every product rigorously tested, ensuring that it meets European standards and regulations, such as those defined by the Vehicle Certification Agency (VCA). This level of strict compliance underscores Klarius’s
dedication to reducing environmental impact, a stance that aligns well with the increasing focus on eco-conscious practices across the globe.
Quality is its own standard and in a 2021 interview, Klarius Products Ltd CEO Mark Brickhill emphasized the company’s unwavering commitment to it by revealing that they choose to approve and certify all of their exhaust systems with the UK Vehicle Certification Agency (VCA), adding, “Now, that is not a legal requirement, but we continue to do it anyway to have the high standards of our products independently confirmed.”
He further highlighted the company’s dedication to customer satisfaction, saying, “For us, it is about constantly looking for new ways to delight customers with our service, which ultimately translates into new sales and a growing business that continues to create British manufacturing jobs.”
Talk is cheap, and Klarius’ range of products need to stand on their own, because if you will excuse a minor adjustment to the old adage, “The proof is in the product,”. By all measurements, the company’s impressive catalogue of products cater to a diverse range of vehicles with the key areas including exhaust systems, catalytic converters, diesel
In 2024, NC Lancaster proudly marks 25 years in business, a milestone built on trust, reliability, and unwavering customer support. For over 15 years, we’ve been a key supplier to Klarius, delivering excellence through a commitment to availability and next-day delivery.
At NC Lancaster, our mission is clear: to help our customers streamline their operations with confidence. Our comprehensive stockholding and logistics services are designed to reduce your stockholding while ensuring you always have what you need, when you need it.
Your success is our priority. By fostering long-term relationships, we aim to be the partner you can rely on today, tomorrow, and for years to come.
particulate filters and mounting kits and accessories.
Whether it is the exhaust systems which make a big difference in fuel efficiency and engine optimisation, or catalytic converters which are essential for reducing harmful emissions, or diesel particulate filters that reduce particulate matter emissions, or mounting kits for accessories that drivers may find necessary, each of these product lines have to meet Klarius’ specific standards before being allowed off the line.
Cutting edge research and development is the only way to keep ahead of your competitors in terms of knowing which areas of your business to invest in. Klarius’ focus on R&D is how they stay ahead of market needs and regulatory changes. Their investment allows them to adapt quickly to advancements in automotive technology and evolving environmental standards. For example, Klarius focuses on creating lightweight, highperformance products that can reduce overall vehicle weight, contributing to improved fuel efficiency and reduced CO2 emissions. Their state-of-the-art testing facility also plays a pivotal role in maintaining their position as a market leader. This facility, combined with an agile manufacturing process, enables
Klarius to bring new products to market faster than many competitors. The company’s swift turnaround time is particularly beneficial in the automotive aftermarket, where there is often an urgent need for replacement parts that meet specific regulatory standards.
“Our research and development ethos has definitely provided more than one pivot point for the business,” says Brickhill.
As the world seems to be scrutinizing every aspect of the automotive industry under a microscope, Klarius has capitalised on their long-term sustainability practices. And, in today’s environmentally conscious world, Klarius’s dedication to sustainability is noteworthy.
“Our entire production process is guided by sustainable practices, from sourcing raw materials to energy-efficient manufacturing processes,” says Brickhill, adding, “By aligning with stringent European environmental regulations, we have helped reduce harmful emissions and foster a cleaner environment.”
Their commitment to eco-friendly practices extends beyond product development. In fact, Klarius actively engages in initiatives aimed at reducing carbon footprints and waste, further solidifying their role as a responsible corporate entity within the automotive sector. Proactive stances like this, that do not wait for the trend to catch up, appeal to an increasingly eco-aware consumer base and is destined to become ever more important for businesses that are thriving in the future.
The most important factor in any business is not their focus on sustainability but their relationship with clients and customers. Klarius Products Ltd has built a robust distribution network that covers the UK and parts of Europe, ensuring that products reach customers quickly and efficiently. Their strategically located distribution hubs are designed to minimize downtime, which is crucial in the aftermarket sector, where timely availability can be the difference between a satisfied and frustrated customer.
Birkhill highlights that the company’s strong focus on customer service has also contributed to its growth. Not only do they provide top-tier products but they also back it up with responsive support and technical guidance, helping clients and partners address any challenges during installation or use.
While Klarius is primarily focused on the UK and European markets, the company’s standards and practices resonate on a global scale. By offering high-quality, emissioncompliant products, Klarius has positioned itself as a company that could expand beyond its current borders, especially as more countries adopt strict emission control
As a pioneering brand we’re used to working ahead of the crowd and relying on our own research and the relationship with our clients
measures. With its robust approach to R&D and sustainability, Klarius has the potential to tap into new markets, including North America and Asia, where demand for aftermarket emission solutions is on the rise.
More than just an aftermarket component supplier, Klarius Products Ltd represents a forward-thinking approach to emission control and sustainability, an area that continues to gain importance worldwide. Their focus on high-quality products, coupled with a commitment to meeting and exceeding emission standards, positions Klarius as a pivotal player in the automotive aftermarket.
As the automotive industry transitions to more sustainable practices, Klarius Products Ltd will likely continue to lead in this space, adapting to new challenges and innovating solutions that contribute to a cleaner, more sustainable future.
Birkhill adds, “As a pioneering brand we’re used to working ahead of the crowd and relying on our own research and the relationship with our clients. With an eye on emerging global trends and our finger on the pulse, we plan to continue making big steps into the future.”
Meinhardt Group Asia
Don Campbell
Aleading global engineering, infrastructure, and project management consultancy, Meinhardt Group Asia have shaped urban landscapes across Asia and beyond. Established in 1955 in Melbourne, Australia, the firm expanded its footprint to Singapore in 1974, marking the beginning of its significant influence in the region. Over the decades since the company has evolved from a modest 10-person operation into a global powerhouse with over 6,000 employees across 61 offices worldwide.
Such impressive growth has to be credited to the leadership team of Meinhardt Group Asia which comprises of the industry’s most seasoned professionals dedicated to driving innovation and excellence. Bringing a wealth of experience and strategic vision to the organisation, Dr. S. Nasim serves as the Executive Chairman while in May 2023, Mr. Go Yang San was appointed as the Managing Director of Meinhardt Singapore and a Global Board Member.
As a hands-on leader, providing over 35 years in the industry, Mr. Go has been pivotal in planning, designing, and managing major civil, structural, and infrastructure projects across Singapore and the region. His prior roles include leading Meinhardt Infrastructure
Singapore and serving as Managing Director of Aurecon’s consulting business in Singapore.
Mr. Go explains that Meinhardt places a strong emphasis on nurturing its staff, recognizing that their expertise and dedication are central to the firm’s success, saying that the company fosters a culture of innovation and continuous learning, offering employees opportunities to work on complex projects that challenge and expand their skill sets, “This commitment to staff development has cemented our reputation as a preferred employer in the engineering consultancy sector,” he says.
In September this year (2024), Meinhardt Singapore celebrated its golden anniversary, a milestone of fifty years that underscores the firm’s enduring impact on Singapore’s built environment. Reflecting on this achievement, Dr. Nasim stated, “This is a significant milestone marking half a century of Meinhardt’s engineering achievements and dedication to shaping the future of cities,” He added, “We have been privileged to play a significant role in shaping Singapore’s built environment and are excited to continue this journey as we expand our global presence and embrace new opportunities in digitalisation and sustainability.”
Of course, Dr. Nasim and Mr. Go emphasize that just because a business is fifty years old, is no reason to rest on their laurels and 2024 has been a year of activity for the business where they have demonstrated their commitment to growth and innovation. In June, they announced major expansion plans for Malaysia where the firm aims to double their presence in the country to 600 specialized staff by 2025.
Further showcasing their dedication to technological advancement, Meinhardt Japan celebrated its third anniversary in October 2024 with strategic announcements focused on leveraging artificial intelligence to redefine the consulting landscape.
“This initiative aims to address various challenges faced by project delivery teams, creating a more connected and intuitive consulting environment,” says Dr. Nasim.
Meinhardt Group Asia’s rich history of robust leadership, staff development, and unwavering commitment to innovation have solidified their reputation as a leader in the engineering consultancy industry. As the firm continues to expand and adapt to emerging technologies, it remains poised to shape the future of urban development across Asia and the globe.
At Azbil, it has always been our goal to create comfortable and safe work environments. This aspiration has motivated us to perfect our measurement and control technology for more than 100 years, just as it defines our future. Together with our customers, we strive to do more than add value—we are shaping a more secure and sustainable society for all.
As we celebrate our Golden Jubilee, we recognise the immense contribution of our dedicated staff, valued clients and partners who have been instrumental in our success
The power of the company cannot be understated, with international projects valued at an estimated US$30 billion annually, the company is a champion at managing some of the industry’s (read: the world’s) largest and most complex building and infrastructure projects. Today, it is one of the most awarded engineering consultancy firms in Singapore, and the largest privately held design and engineering firm in Asia.
“As we celebrate our Golden Jubilee, we recognise the immense contribution of our dedicated staff, valued clients and partners who have been instrumental in our success,” adds Dr. Nasim, “This anniversary is more than just a celebration of time. It signifies our commitment to technological advancement, innovation, sustainability, and industryleading urban development and professional consultancy services. The event will not only highlight our past successes but also underscore our future aspirations as we continue to shape the cities of tomorrow. We have been privileged to play a significant role in shaping Singapore’s built environment and are excited to continue this journey
as we expand our global presence and embrace new opportunities in digitalisation and sustainability,”
And what does the new year look like for the powerhouse company? With more projects on the way there are already a handful of developments in Asia slated for 2025.
Dulwich College International School, Bangkok, is a new campus, set to open in 2025 that will feature facilities for early years and junior school students, including sports and aquatic centres, with a total estimated gross floor area of 31,000 square meters. Several other projects are also expected to be completed including the FTB Tower, Royal Group Central and the Sathapana Tower in Phnom Penh. These projects are all entering their final stages and should be opened and operational in 2025.
Kellanova’s Newest Plant, Chonburi, Thailand: Formerly known as the Kellogg Company, Kellanova is constructing a new plant equipped with cutting-edge equipment to produce Pringles® for distribution throughout the Asia Pacific region. The groundbreaking ceremony took place on October 19, 2023, with completion expected by 2025.
The landscaping and construction industry in Asia, with Singapore at its forefront, is set to redefine urban living and sustainability in the coming decades. As rapid urbanization drives demand for innovative housing and infrastructure, Singapore leads the charge with vertical green cities and eco-friendly designs that integrate nature seamlessly into urban spaces. Sustainability is at the core, with green building standards, carbonneutral goals, and advanced technologies like prefabrication and smart construction reshaping the industry.
Beyond aesthetics, landscaping enhances resilience against climate change through flood mitigation and urban cooling, while boosting livability with green recreational spaces. Economically, Singapore’s expertise in sustainable urban planning positions it as a regional hub, exporting innovation across Asia and supporting projects like the Belt and Road Initiative. This pivotal industry is poised to balance economic growth with environmental stewardship, shaping a greener, more liveable future.
OceanaGold Corp
Foylan Rhodes
Under the leadership of Gerard Bond, company Chief Executive, OceanaGold Corp have set themselves the task of mining gold for a better future. The gold, copper, and silver they produce are essential to the renewable energy and transport sectors, life-saving medical devices and technology which connects communities around the world. The modern era of digitalisation, connectivity and prosperity we find ourselves in would be impossible without the mining industry. But as OceanaGold is proving, there are areas where improvements can still be made.
“Our activities contribute to economic growth and improved health and education outcomes in the regions where we operate,” Gerard tells us, “In fact, we provide direct employment for over 3,700 people and indirect employment for many more.”
A company whose success can be attributed to their attention to staff as much as shareholders, OceanaGold Corp fosters a work atmosphere where a combination of care, respect, integrity, performance and teamwork emboldens them to make changes to their industry. As a growing intermediate gold and copper producer the company is able to maximise the generation of Free Cash Flow from their operations and deliver strong returns through their portfolio of four
operating mines: the Haile Gold Mine in the United States of America; Didipio Mine in the Philippines; and the Macraes and Waihi operations in New Zealand.
Founded on the principles of responsible mining and sustainable practices, OceanaGold Corporation has evolved into a prominent player in the global gold mining industry.
Originating in New Zealand, the company has grown its operations and influence worldwide, carving out a name not only as a gold producer but also as an organization deeply committed to environmental stewardship and community engagement.
The Roots
Established in 1989, OceanaGold traces their roots back to New Zealand’s historic mining industry. The founders envisioned a company that would blend traditional mining methods with emerging environmental and social governance (ESG) standards. Initially, OceanaGold focused on projects within New Zealand, primarily the Macraes Goldfield in Otago, which remains a cornerstone of their operations and the largest gold-producing mine in the country.
The founders’ ethos emphasized mining responsibly and sustainably and from the outset, they prioritized protecting New Zealand’s pristine landscapes while
delivering economic value. As Gerard says, “This philosophy has guided our expansion into other regions, including the Philippines and the United States and has cemented OceanaGold’s reputation as a leader in sustainable mining. But our most defining feature remains our loyalty to staff.”
One of OceanaGold’s defining features is their commitment to their workforce and Gerard emphasises the pride in being to create a safe and empowering workplace, where employees are encouraged to develop their skills and advance their careers. He details how OceanaGold emphasizes robust training programs, career progression opportunities, and a company culture that prioritizes safety and well-being.
“In recent years, we have introduced several mental health and wellness programs aimed at supporting employees and their families,” he says, “This holistic approach to workforce management has not only bolstered staff retention but also strengthened OceanaGold’s reputation as an employer of choice in the mining industry.”
Gerard Bond brings extensive experience in global finance and the resources industry
We are wellpositioned to meet the evolving demands of the mining industry
to OceanaGold Corporation. Prior to his appointment as President and Chief Executive Officer in April 2022, he served as Finance Director and Chief Financial Officer at Newcrest Mining Limited from January 2012 to January 2022, a period marked by significant operational, financial, and growth transformation. Before joining Newcrest, Gerard spent over 14 years at BHP, a position that provided him with a comprehensive understanding of corporate finance, mergers and acquisitions, treasury, and human resources across North America, Europe, and Australia.
With experience encompassing gold, copper, nickel, and aluminium, his appointment as the leader of OceanaGold Corp was based on his proven track record of driving performance and delivering on business potential. It also put OceanaGold Corp into a position of benefitting from his understanding of all levels of the business and what it takes to achieve their ultimate goals which are centred around sustainability and responsible mining.
As a long-time advocate and leader in responsible mining practices, the company has developed and implemented advanced environmental management systems to reduce their footprint, particularly in terms of water and energy use. Gerard reveals that these efforts align with their “zero-harm” environmental policy, aimed at preventing negative ecological impacts in the areas where they operate. Additionally, the company’s commitment to responsible mining also extends to its community engagement efforts.
“OceanaGold has invested significantly in local communities,” Gerard elaborates, “Where we have created job opportunities, improved
infrastructure, and funded education initiatives.”
In the Philippines, for example, their Didipio Mine has become a model for community involvement, providing jobs and supporting local development while maintaining high environmental standards.
As of 2024, OceanaGold is making strides in several key areas. The company has continued to push boundaries in technological innovation, focusing on digitalization and automation to optimize mining efficiency and safety. A highlight of their recent technological initiatives is the integration of artificial intelligence to enhance ore processing and reduce waste, contributing to both cost efficiency and environmental goals.
OceanaGold is also expanding its North American footprint, with new exploration projects in Nevada, USA. These projects signal a strategic move to capitalize on the region’s rich resources while adhering to stringent U.S. environmental standards. The new developments are poised to boost the company’s output, further strengthening its position in the gold mining industry.
In alignment with global climate goals, OceanaGold continues to invest in renewable energy projects to power their operations. At their Macraes site in New Zealand, for instance, the company has recently completed the construction of a large-scale solar farm designed to meet a substantial portion of the mine’s electricity needs. This initiative is part of OceanaGold’s ambitious target to achieve net-zero carbon emissions by 2050.
While OceanaGold Corp stands as a testament to the mining industry’s potential for positive impact, Gerard is aware that more can and should be done. However, through their forward-thinking approach to environmental management, community development, and employee welfare, the company is set to push these positive developments further than many competitors and have set a benchmark for others to follow. As they expand into new markets and explore innovative technologies, OceanaGold continues to demonstrate that mining can be both profitable and sustainable.
“We are well-positioned to meet the evolving demands of the mining industry,” says Gerard, “And we continue to embody a bold legacy that prioritizes people, planet, and above all progress.”
Daemon Sands
As one of the leading providers of towage services in the Americas, SAAM Towage has carved a niche as a powerhouse in maritime logistics and operations. Founded as part of the Chilebased multinational SAAM (Sudamericana Agencias Aéreas y Marítimas), the towage division has expanded its influence from Chile to multiple countries across the Americas. Through diligent hard work and consistently towing the line over the years, SAAM Towage has evolved from a regional service provider to a key player in the maritime and logistics sector. And as such, have contributed to the stability and efficiency of numerous ports along the continent’s Pacific and Atlantic coasts.
Led by an adept executive team, SAAM Towage has steered the company’s growth through innovation and strategic acquisitions. Key figures include the CEO of SAAM Towage, Macario Valdés, who has brought decades of experience in the towage and port logistics industries. Having previously held the role of General Manager of SAAM, Valdés, has played a pivotal role in aligning SAAM Towage’s strategies with broader corporate objectives. Together with a dynamic board, the executive team has consistently
emphasized operational excellence, safety, and environmental sustainability as part of their growth model.
Indeed, under Valdés leadership, SAAM Towage has focused on optimizing their fleet and investing in advanced technology to improve towage operations and safety, he adds, “This has not only ensured reliable services but has also reinforced the company’s reputation as a maritime partner that values accountability and expertise.”
An outstanding feature of the company that SAAM Towage is known for, is their dedication to their people. Through a robust safety culture, the company focusses heavily on training, career and personal development. Towage is a demanding industry that requires skilled teams who are well-versed in both technical and safety procedures, while these sorts of individuals, possessing of the right mind frame and approach can be sourced, it is best that they are trained, nurtured and developed into their roles. Therefore, SAAM Towage prioritizes rigorous training and provides opportunities for continuous skill development. The company’s workforce, ranging from tug captains to support staff, benefit from programmes designed to enhance professional growth and
technical expertise. According to Valdés, safety remains a cornerstone of SAAM Towage’s culture. To ensure their staff are protected, the company has introduced stringent safety measures and training protocols that not only meet but exceed industry standards. This focus on safety is a key reason why SAAM Towage has successfully maintained its high performance across multiple countries, with crews who are well-equipped to handle various conditions and challenges in port and offshore environments.
In order to reduce their carbon footprint and bring themselves up to parr in terms of green processes, SAAM Towage have expanding their operations and fleet alongside integrating green technology. Coupled with recent acquisitions and strategic partnerships this approach has allowed SAAM Towage to broaden their presence, particularly in markets where demand for towage services is rising due to increased shipping volumes.
In the past few years, the company has grown its fleet with state-of-the-art tugboats, some of which are equipped with hybrid technology to reduce fuel consumption and emissions. A milestone that aligns with the global maritime industry’s shift toward more
In an industry defined by tides of change, success is for those who are able to ride the current and maintain their own standards of excellence.”
environmentally sustainable practices.
In 2023, SAAM Towage announced the addition of advanced tugboats to its fleet in Ecuador and Panama, aiming to support the growing demand for reliable towage services at some of the busiest ports in the region. These vessels are equipped with technology that enhance manoeuvrability and fuel efficiency, underscoring SAAM Towage’s commitment to operational efficiency and environmental responsibility.
Moreover, as Valdés highlights, SAAM Towage has invested in technology-driven solutions for fleet management, such as real-time monitoring systems that improve operational oversight and support predictive maintenance. This approach minimizes downtime, maximizes fleet efficiency, and, importantly, ensures that services remain punctual and reliable, a critical requirement in today’s fast-paced maritime industry.
Speaking about technology-driven solutions, the inclusion of the SAAM Itzá to their fleet deserves a mention. The SAAM Itzá is a powerful tugboat that serves the key ports of Puerto Quetzal and San José in Guatemala. Built in 2019 by Med Marine, a prominent Turkish based company who, since 1995, have specialised in shipbuilding and maritime services. Boasting a robust design by Robert Allan Ltd, the vessel clocks in at a length of 23 meters, a beam of 10.9 meters, and a bollard pull of 60 tons. The boat is powered
by Caterpillar 3512C engines and Rolls Royce US205 FP azimuth thrusters and can achieve speeds of up to 12 knots, making it highly effective in confined port environments.
It replaced the Amazonas I tug to boost berthing and deberthing efficiency, exemplifying SAAM Towage’s focus on fleet modernization and optimized port operations. Currently registered under the Guatemalan flag with the IMO number 9854777, the SAAM Itzá continues to play a vital role in Guatemala’s maritime logistics, stationed most recently at Puerto Quetzal.
The Path Forward
SAAM Towage’s commitment to service excellence, environmental responsibility, and safety has positioned it as a leader in the towage sector across the Americas. With continued investments in technology and people, and a leadership team valuing innovation and sustainable growth, the company is poised to navigate the challenges of an evolving maritime landscape.
Continuing to approach challenges and new developments alike with resilience and agility, Valdés reveals that as the company charts their future, their focus on sustainable practices, staff well-being, and operational excellence will be key drivers in maintaining its industry-leading status.
“In an industry defined by tides of change,” he says, “Success is for those who are able to ride the current and maintain their own standards of excellence.”
Cassidy Banks
An integrated insurance holding company with a speciality for personal residential insurance, Universal Insurance Holdings headquartered in Fort Lauderdale Florida works hard to live up to their name. Established in 1990, the company has developed, underwritten and marketed a range of insurance products that have come to benefit those that own homes and properties and those who live in them. But it is not only their diverse product range that has made them stand out in the crowd for almost thirty-five years, but rather their singular approach to customer service.
Step One. Reach And Responsibility
Operating primarily through their main subsidiaries, namely the highly effective but very wordy “Universal Property & Casualty Insurance Company” and the “American Platinum Property and Casualty Insurance
Company”, Universal provides insurance services across various states in the U.S. through a well-established network that relies on their reach and responsibility. One of the biggest hurdles in this industry and certainly one that has to be overcome before substantial growth can be achieved is customer trust.
To achieve this, the company makes sure to combine a comprehensive approach encompassing a full range of products including risk management, claims management, and distribution with a diverse and highly trained staff contingent of approximately 1200. These highly skilled team members ensure a robust presence in the property and casualty insurance sector and financial markets while helping customers and clients navigate the bureaucracy of the insurance industry. While the insurance sector is an industry known for its wordiness, it’s terms, loopholes and pitfalls,
Founding partners Scott Link and Kara Link bring over 60 years of combined experience in commercial civil litigation and appeals. We pride ourselves on blending fierce advocacy, constant professionalism, and strategic planning to ensure that every case is meticulously prepared and postured should an appeal be required. Whether you are facing a trial or considering an appeal, trust our team to advocate for you and preserve your rights.
Universal have set themselves up as the guide.
Step Two. Sustained Focus.
W hile the company’s strategic focus remains on expanding their footprint in the personal residential insurance market, Stephen J. Donaghy the company CEO is insistent that this happens while maintaining a strong emphasis on customer service and operational efficiency. This, he believes is essential to create a sustainable future for everything to enjoy.
“At Universal Insurance Holdings,” he says, “We are committed to creating a sustainable future that extends far beyond our business operations, to our society, our environment, and our people. Being a responsible corporate citizen is part of our DNA, and I am tremendously proud of the environmental, social and governance efforts that Universal is undertaking.”
Step Three. Build A Better World.
As Donaghy explains, Universal Insurance Holdings is committed to creating a sustainable workplace for their employees, society, and their planet. As a property and casualty insurance group, they are keenly aware of the risks posed by increased climate change and issues that affect society at large. By leading with their values, their company focuses on ways we can drive positive change by promoting the benefits of sustainability, reducing their environmental footprint, encouraging employee education and involvement, and monitoring progress.
Donaghy believes that active leadership in environmental issues and sustainability is paramount to the well-being of the planet, let alone the industry where they thrive. Climate change has been linked to an increase in natural disasters that affect the insurance and assurance markets. As such it is their goal to support their communities when natural disasters strike and to create a sustainable workplaces to preserve the environment for
future generations by establishing worthwhile habits today.
Almost as if to prove a point, the company’s quarterly results were a real-time reflection on the effect of hurricanes.
Universal Insurance Holdings, Inc. reported its third-quarter 2024 financial results recently which showcased a mix of revenue growth and expanded net losses compared to the same period in 2023. Total revenue rose to $387.6 million, a 7.6% increase over last year’s $360 million, while direct premiums written climbed 8.0% to $574.4 million. Despite these gains, the company saw a significant rise in its net loss, reporting $16.2 million, compared to a $5.9 million loss in Q3 2023. Loss per share deepened from $0.20 last year to $0.57, and the combined ratio jumped to 116.9%, up from 110.7% in Q3 2023. This reflects heightened underwriting losses, primarily from increased claims due to recent hurricane activity which resulted in a great loss of property value and far worse, a loss of life.
Looking at a more positive note, Donaghy explains that Universal’s book value per share rose impressively by 37%, reaching $14.15, which he believes underscores the company’s focus on asset growth even amid adverse conditions. Through hardships like this he does emphasise that knowing where you’re going is crucial to battling the storms and that dealing with difficult industries is nothing new for a company of their size. He adds, “Unlike many of our closest competitors, we are taking tangible steps to evolve our company to drive sustainable change, particularly with how our business affects the environment.”
According to him, their ESG approach builds on setting more definitive goals where they are able to measure their challenges and take stock of their successes and implement best
This is a journey that we have worked diligently to ensure it becomes an essential part of our culture and company strategy
practices to ensure they remain good stewards on behalf of their key stakeholders which include employees, customers, shareholders, agents, and communities.
“Living up to that commitment means staying true to the values that have defined our organization for many years,” he says, “And only by harnessing the full power of our businesses and our people can we help solve society’s toughest challenges.”
And Donaghy is also keen to involve all of their staff and their team in their ongoing plans and enlightening all onto what they are achieving. As CEO he is delighted to share their recent progress across these priorities and to underline their vision for what lies ahead in Environmental, Social and Governance.
“This is a journey that we have worked diligently to ensure it becomes an essential part of our culture and company strategy,” he says, “And it is this deep commitment and focus on sustainability allow us to maintain our leadership position and will support our longterm success.”
Foylan Rhodes
As the world pivots towards sustainable energy, few companies have captured attention like Wind Estate, a leader in wind power generation. Founded on the principles of renewable energy and sustainability, Wind Estate has carved out a significant niche by offering clean energy solutions benefitting communities, businesses, and the environment alike. The Danish-based company is known for transforming rural landscapes into powerhouses of renewable energy, harnessing wind’s power to meet rising energy demands without harming the planet.
Wind Estate owns and operates more than 400 wind turbines in Denmark and is also significantly involved in project development in Denmark and the United Kingdom. This makes Wind Estate one of the largest wind developers and operators in Denmark. Wind Estate was founded in 2001 and is active in onshore and offshore wind, solar, hydrogen, and battery solutions.
The Wind Estate Model Wind Estate operates with a unique business model that prioritizes environmental stewardship while fostering economic development. It is deeply integrated into the communities where it establishes wind farms, often entering into partnerships with local
landowners. This inclusive approach not only generates clean energy but also stimulates local economies by creating jobs, generating income for rural communities, and increasing property values.
Through a combination of private funding and strategic partnerships with government agencies, Wind Estate has been able to expand its operations rapidly. Its wind farms, primarily located in Denmark and other parts of Europe, have contributed significantly to meeting national renewable energy goals. Each wind turbine installed is part of a broader mission to reduce greenhouse gas emissions, decrease dependency on fossil fuels, and drive forward the EU’s ambitious target of becoming carbon-neutral by 2050.
Partnering with other, like-minded businesses has proven to be crucial for the long-term possibilities or the industries. Recently, Wind Estate formed a partnership with Eurowind that is set to do just this.
As Ane Mette Lysbech-Kleis, CEO of Wind Estate explains, one of the reasons that their company has been so successful is their dedication to technological innovation, “Wind energy is an evolving field, with advancements constantly being made to improve efficiency,
capacity, and sustainability,” Ane says, “Wind Estate has invested heavily in state-of-theart turbine technology that maximizes energy output while minimizing the environmental impact. Its turbines are designed for longevity and efficiency, which translates into lower maintenance costs and increased profitability.”
Wind Estate’s commitment to R&D has enabled it to stay ahead of the competition. By continually analyzing wind patterns, refining turbine placement, and implementing predictive maintenance, Wind Estate ensures optimal performance across its portfolio of wind farms. These innovations not only drive down costs but also contribute to the overall viability of wind energy as a sustainable solution.
Financially, Wind Estate are positioned as a stable, long-term investment in the energy sector. The demand for renewable energy is growing exponentially, and wind energy plays a critical role in this shift. Wind Estate’s diversified portfolio and geographical reach provide a steady revenue stream, while longterm agreements with government agencies and private buyers guarantee demand for its power output.
Moreover, Wind Estate has a robust plan for expansion. With increasing interest in renewable energy from investors and governments worldwide, the company has laid the groundwork to expand into new markets, especially across Europe and North America. Its financial model relies on a mix of private investment, public funding, and corporate partnerships, allowing it to scale efficiently and minimize risk.
For Wind Estate, sustainability is more than a buzzword; it’s a core value. The company is dedicated to creating a cleaner, greener world by reducing carbon emissions and preserving natural resources. Its wind farms are designed with the environment in mind, ensuring minimal disruption to local ecosystems. By prioritizing sustainability, Wind Estate aligns itself with global efforts to combat climate change, reinforcing its commitment to future generations.
Additionally, Wind Estate’s practices extend beyond mere power generation. The company has initiatives in place to educate communities about renewable energy, promote environmental awareness, and support local development projects. These efforts have not only helped Wind Estate foster goodwill but also strengthened its position as a responsible leader in the energy sector.
As the global energy landscape shifts, Wind Estate’s role in the transition towards renewable energy becomes even more significant. The International Energy Agency projects that wind energy could provide up to 30% of global power needs by 2050, and companies like Wind Estate are crucial to achieving this vision. With its expertise, commitment to innovation, and focus on sustainability, Wind Estate is well-positioned to shape the future of energy.
In a world increasingly affected by the consequences of climate change, the need for clean energy has never been greater. Wind Estate is more than just a company, it’s a movement towards a sustainable future. By empowering communities, leveraging advanced technology, and making a steadfast commitment to environmental responsibility, Wind Estate stands as a beacon of what is possible when business and sustainability intersect. As the demand for renewable energy surges, Wind Estate’s approach provides a roadmap for success that other companies would do well to follow.
“Our story is one of growth, innovation, and positive impact,” says Ane Mette LysbechKleis, “Providing a model for businesses aiming to thrive in an eco-conscious world.”
Denmark’s renewable energy landscape is
It makes sense to explore how we can jointly optimize the operation and further develop the area.
witnessing a groundbreaking partnership as Eurowind Energy and Wind Estate unite to form K/S Blue Holding, a jointly owned company set to dominate the sector. With a transaction exceeding three billion Danish kroner, the partnership brings together 186.3 MW of operational capacity, including Denmark’s largest onshore wind park, Overgaard Wind Park, which boasts 146.7 MW, nearly double the size of its nearest competitor. The new company will see Eurowind Energy contribute 39 turbines across two sites, while Wind Estate adds 16 turbines and compensates Eurowind with an undisclosed payment.
This collaboration underscores the two companies’ commitment to expanding Denmark’s renewable energy potential. Eurowind Energy, established in 2006, operates across 16 markets and employs over 600 people, while Wind Estate has long been a trusted partner in the sector. Together, they are set to redefine Denmark’s onshore wind capabilities.
Ane explains that they have historically had a strong collaboration with Eurowind, based on a good relationship, integrity, and mutual trust. Adding, “It is, therefore, a natural next step to formalize this partnership and harvest synergies across our businesses, benefiting both the local area and both companies. The collaboration opens up opportunities that neither of us could achieve alone. And when the turbines stand side by side, as in Overgaard, it makes sense to explore how we can jointly optimize the operation and further develop the area.”
CEO of Eurowind Energy, Jens Rasmussen echoed these sentiments by adding, ““We are pleased that we can elevate our cooperation to a new level for the benefit of all. By consolidating all the turbines in Denmark’s largest wind park, we maximize the value of the park. The collaboration benefits both companies, but also the landowners, shareholders, and the local community. We have several other joint interests, so it is certainly possible that we will further enhance our cooperation with Wind Estate, both in Denmark and abroad.”
Daemon Sands
The maritime industry, crucial for global trade and commerce, faces a multitude of complex challenges that impact its operational efficiency and sustainability. These include stringent environmental regulations, escalating fuel costs, labour shortages, and the need for digital transformation to enhance logistics and fleet management. Safety concerns are also paramount, with vessels and personnel facing risks from piracy, weather extremes, and operational hazards. Additionally, maritime companies must maintain strict compliance with international standards, often demanding high-quality maintenance, repairs, and certified technical support to ensure smooth operations.
In this demanding landscape, the Worldwide Industrial & Marine Association (WIMA) offer valuable solutions through their network of certified, maritime-oriented companies. By providing integrated services covering a wide array of industry needs, WIMA facilitates a cohesive approach to maritime operations, ensuring that high-quality resources and expertise are readily accessible. The association fosters collaboration among its members, driving innovation in response to emerging challenges, such as environmental regulations and technological advancements. With a
commitment to stringent quality standards and global reach, WIMA helps maritime companies navigate regulatory requirements, optimize their operations, and enhance safety measures, ultimately contributing to a more resilient and sustainable maritime industry.
WIMA’s primary mission is to support and promote the activities of the over fifty global members that work with them. This is achieved on a regular basis by creating a cohesive network that allows their members to effectively cover diverse requirements across all sectors of the shipping industry. This collaborative approach ensures that clients receive reliable, high-quality services without the complexities of sourcing multiple suppliers.
This simplification of the industry from a client perspective is invaluable considering the constantly evolving landscape of the maritime industry. Through this network, processing changes can be managed and political issues navigated, while members work together in a cohesive net to make sure that none of the client needs fall through. Of course, to achieve this requires strong leadership and in April this year, WIMA held elections to appoint a new Board of Directors, reflecting their commitment to dynamic leadership
“We keep your vessels trading so you keep the world turning”
and strategic growth. The newly elected board emphasized presenting and promoting the capabilities of its members to shipping companies, organizations, and conferences both domestically and internationally. A key focus was placed on collaborating with shipbuilding and repair units while leveraging new European and national programs announced by the government.
And, in a sector as crowded as the maritime industry, there is a tangible value in being part of a larger network as a certified member. Not only do the members benefit from the legitimacy of the certifications which holds them to a different standard to their many competitors, they also gain the trust and confidence to make important decisions that are informed. WIMA has become a symbol of the power of collaboration and the importance of teamwork, showing that when we work together, we achieve better things than if we work alone.
This year, the maritime industry has faced multifaceted challenges, including environmental regulations, technological advancements, and economic fluctuations. These changes, largely out of control of the companies working in the sector, have affected the WIMA in particular, especially in
This year, the maritime industry has faced multifaceted challenges, including environmental regulations,
the industry’s push towards decarbonization which has necessitated investments in sustainable technologies and compliance with stringent environmental standards.
At the same time, the global economic climate has introduced uncertainties affecting trade volumes and shipping demand. In order to address these challenges, WIMA has been proactive in facilitating knowledge exchange and fostering innovation among their members.
Following a belief that in-person networking and relationship-building develops the best results, they organisation organizes regular workshops, seminars, and collaborative projects. Through these muchanticipated events the association aims to equip its members with the tools and insights needed to navigate the evolving maritime landscape as well as develop and maintain relationships between their members.
Recognizing that a skilled workforce is essential to overcoming industry challenges, WIMA have gone to great lengths to employ a range of staff training and development programmes that shows their significant emphasis on the development of the people factor in the industry. The association collaborates with educational institutions and training centres to provide their members with access to the specialized programmes needed to enhance technical skills and industry knowledge.
This commitment to professional development ensures that WIMA members remain competitive and capable of delivering high-quality services. By investing in their
workforce, member companies can adapt to technological advancements and regulatory changes more effectively.
Back in November 2022, WIMA signed a Memorandum of Cooperation with the Municipality of Piraeus, aiming to strengthen and support innovative development in the blue economy sector. This partnership underscores WIMA’s dedication to fostering entrepreneurship and innovation within the maritime industry.
Piraeus, located near Athens, Greece, is strategically positioned at the intersection of Europe, Asia, and Africa, making it an essential hub in the Mediterranean for the maritime industry. An enviable proximity to the Suez Canal provides an efficient route for ships from Asia, Africa, and the Middle East, that reduces travel times and fuel costs as vessels transition to European waters. As Greece’s largest port, Piraeus offers seamless connections to European markets through extensive road and rail networks, enabling swift distribution from the harbour to inland destinations.
One of the port’s competitive advantages lies in its deep-water harbour, capable of accommodating large container ships, cruise liners, and oil tankers, positioning it favourably against other regional ports. Recent significant investments, particularly from China’s COSCO Shipping, have upgraded Piraeus’s infrastructure, increased its cargohandling capacity and made it an attractive option for global shipping companies. Additionally, Piraeus’s role as a primary ferry and cruise departure point for the Greek islands contributes to its financial strength, with consistent passenger traffic driven by Greece’s robust tourism industry as well as a current influx of maritime talent.
As the maritime industry continues to evolve, WIMA remains steadfast in its mission to support its members through collaboration, innovation, and professional development. By addressing current challenges and seizing new opportunities, the association plays a crucial role in shaping a resilient and sustainable future for the maritime sector. Further to this, across the timeline of 2025, the importance of their continued work in actually promoting and showcasing their members to the industry should not be overlooked.
Aliya's Foods
Cassidy Banks
Celebrating their 25th anniversary and named after the founders’ youngest daughter, the company Aliya’s Food Ltd, brings the taste of India to North America and the chances are if you’ve ever eaten a ready-to-go samosa anywhere near Edmonton, it was probably one of Anis and Noorudin Jiwani’s. Business Pursuit explores.
Today, Aliya’s Foods Ltd, serves a diverse customer base across North America, offering authentic Indian cuisine through its Chef Bombay brand. With their products being available in major supermarket chains throughout Canada and the United States, they are a staple in many a kitchen, restaurant and bachelor pad.
Like many a good story, the husband and wife team launched their business twentyfive years ago in a modest 3,000-square-foot facility. Definitely a humble start considering that today, Aliya’s Chef Bombay brand is sold in most major grocery outlets in North America and the company has transitioned their headquarters into a bustling 100,000-squarefoot facility where they make in excess of 100 million samosas a year, along with other Indian staples like butter chicken and pakoras.
In addition to the above, in order to meet demand, they also operate an 80,000-square-
foot plant in New Mexico, USA. Together, these facilities adhere to rigorous standards, holding certifications such as SQF, HACCP, CFIA, and USDA, ensuring the highest levels of food safety and quality.
“Samosas were our first item entry into the market. What French fries are to McCain, samosas are to us,” says Mr. Jiwani. “And by the way, we do supply samosas to McCain.”
Jiwani explains that Aliya’s products are sold in retail packaging, club packaging and as white-label products for supermarket brands. These include Loblaws, Sobeys-Safeway, Walmart, M&M Meats and Federated Calgary Co-ops in Canada. In the United States, which represents 85 per cent of their business, they sell through Trader Joe’s, Albertsons, H-E-B, Aldi, Walmart and Kroger.
The growth in their North American sales, put the company in the 315th spot on The Globe and Mail’s Top Growing Companies list for 2021 with three-year revenue growth of 101 per cent. And all of this began due to what Jiwani describes as a mid-life crisis.
“We were both living in Toronto,” he explains, “Both of us had good jobs, I worked at an actuarial consulting firm and Noorudinas was a dietician consultant. During a long drive from Toronto to Vancouver, we were chatting
about what we would do if we started a business.”
The idea took hold and when they returned, Mr. Jiwani wrote to the governments of Alberta, B.C. and Ontario to ask about agrifood business development opportunities, however, only Alberta responded. At which point they decided to move to Edmonton and see what they could do, adding, “We just left our jobs and decided to take a year to try it.”
With daughters in Grade 4 and Grade 5, they journeyed west to their new frontier.
Supported by Alberta’s Food Processing Development Centre in Leduc, Ms. Jiwani was able to refine her recipes for large-scale production, and with additional help from the province’s Agriculture Financial Services Corp., they transformed her cherished family recipes, beloved among friends and relatives, into a widely recognized North American staple.
Today, annual revenues are about $50-million, and the company has grown from five employees to just under two hundred and fifty. Quickly outgrowing five plants, in 2021 they moved to their current facility and soon after opened the additional space, which Jiwani says should provide plenty of room for future growth.
“Scaling production to meet the growth
Crawling Valley Plastics has been in operation since 2007. Throughout this time we have produced packaging for large industry, retail and small businesses. We are committed to producing plastic film products for food and industrial-grade packaging.
We’ve seen people grow from within. That’s been our strength: the people behind the office walls
of the company has been a challenge,” he admits, “But it is a good problem to have.”
He jokes about losing his hair over the years, but one thing the Jiwanis have held onto is their roots. Both immigrated to Canada, Mr. Jiwani arrived with his family as a child from Kenya, and Ms. Jiwani came as a refugee from Uganda. As such, the team at Aliya’s Foods reflects the diversity of Canadian society.
”We never question anybody if they’ve had Canadian experience, because my father went through that a lot when he migrated to Canada,” Jiwani says, “The first question people would ask is, ‘What Canadian experience do you have?” he says. “So, one belief that we put into this business was nobody’s ever going to be asked, ‘Where do you come from?’”
This has paid off, as the company has a relatively low turnover of staff and Jiwani credits their team, and of course his wife’s delicious recipes, for the company’s success. Of the five people on staff when they launched the company in December 1999, two have retired and three are now in senior management positions. Their current accountant once worked in their shipping and receiving warehouse.
“Staff development is the key to business growth,” Jiwani believes, “For example, today somebody who was operating a machine when they first started with us does the purchasing of goods worth $18 million to $20 million a year!”
He adds, “We’ve seen people grow from within. That’s been our strength: the people behind the office walls.”
In order to further enhance opportunities, the Jiwanis arranged English classes in the boardroom when a handful of employees expressed interest. Their staff reflects various waves of migration, and today the company has a large contingent of Afghan migrants. About twenty of their former staff now run their own businesses, a testament to their growth.
“This provided them with a strong foundation. They secured their homes, got
This expansion was the thought process of creating more capacity so that we could grow into more clients
their children into school, and eventually started their own businesses,” he says with pride. “For me, the real satisfaction comes from seeing their success, it’s not always about the money.”
While Mr. Jiwani has no plans to fully retire soon, he takes pride in seeing the next generation take charge of the company he and his wife built. Their daughters and nephew have now become part of the business.
The new manufacturing facility was designed for growth, and once travel is safe again, Mr. Jiwani plans to explore Europe, a promising market for Chef Bombay. He continues to oversee finances, while his wife manages research and development, but he says the next generation has largely assumed responsibility for daily operations.
”This expansion was the thought process of creating more capacity so that we could grow into more clients,” he says. “The new generation stepping in clearly has more energy and drive, with a real fire in their belly to determine the next direction.”
Foylan Rhodes
Operating as a subsidiary of Pressure Technologies plc, an AIM Stock Exchange listed company, Chesterfield Special Cylinders brings over 125 years of industry knowledge and expertise to their field and is considered a world-leading provider of bespoke, high-pressure gas containment solutions and services with a wide range of client bases that reflect their legacy reputation for accuracy and reliability. BP explores.
CSC’s high-pressure cylinders play a vital role in diverse applications, ranging from high-pressure systems in naval submarines and surface ships to oxygen cylinders for fighter jets. They are also integral to the bulk storage of industrial gases, air pressure systems in motion compensation on floating oil platforms, and, more recently, hydrogen transport, refuelling, and energy storage solutions.
In focus
Chesterfield Special Cylinders is a trusted partner for the global energy and defence sectors, offering comprehensive services such as systems design, cylinder manufacturing, re-testing, refurbishment, and bespoke solutions. As a leading supplier to the growing hydrogen market, the company provides complete storage solutions and
asset management services.
A key focus is the continued development of its unique Integrity Management Team, regarded as the strongest service team in the industry. Backed by over a century of expertise, Chesterfield Special Cylinders ensures customers receive unparalleled service and support.
Leadership and management
Chesterfield Special Cylinders’ Integrity Management team operates globally, providing faster, safer, and more cost-effective inspection and testing of high-pressure cylinders. Specializing in acoustic emission (AE) testing, the team adheres to BS 8562 and EN 16753 standards, the latter being the new benchmark for inspecting and testing hard-toreach or immovable gas tubes.
High-pressure cylinders often degrade from both inside and outside, but historically, inaccessible cylinders have undergone less rigorous safety tests than transportable ones, leading to significant safety, cost, and downtime challenges. Chesterfield Special Cylinders is uniquely equipped to deliver this strict testing regime worldwide, offering bespoke facilities and equipment. This through-life Integrity Management service is particularly valuable to the hydrogen sector, enabling a true design-to-operation gas
storage solution.
What is EN16753?
EN 16753 represents the latest standard for inspecting and testing hard-to-reach or immovable gas tubes and forms the foundation of Chesterfield Special Cylinders’ Integrity Management service. Central to this standard is acoustic emission (AE) testing, widely regarded as the future for seamless cylinder assessment.
Both EN 16753 and its predecessor, BS 8562, are non-destructive in situ testing standards, ideal for high-pressure tubes in hazardous or inaccessible locations, such as offshore oil installations, or where downtime for removal would disrupt critical operations, including power generation, hospitals, research facilities, and marine installations like heave compensation systems on drilling rigs. AE testing, endorsed by leading authorities such as DNV-GL, offers a faster, safer, and more cost-effective approach. EN 16753 builds on BS 8562, co-developed with the CSC IM team, which set a benchmark for testing cylinders that cannot be removed after installation.
These standards address industry safety concerns by providing precise requalification methods equivalent to national and international standards such as BS EN
1968:2002 and ISO 6406:2005, significantly reducing costs and downtime by allowing full in situ testing.
Hydrogen is one of their major focusses and the company designs, manufactures and maintains hydrogen storage across a wide range of pressures.
As managing director Mick Pinder says, “We are supporting the adoption and future growth of hydrogen energy with innovative and cost-effective storage solutions using Type One steel cylinders,” adding, “We design, manufacture and maintain hydrogen storage across a wide range of pressures for applications such as hydrogen refuelling stations, green hydrogen and industrial decarbonisation.”
He goes on to add that Chesterfield Special Cylinders are trusted for their outstanding reputation and have a longstanding history of working with gas majors to design, manufacture, and service cylinder fleets. All of their cylinders are manufactured to meet international quality and safety standards and allow for modular expansion to meet future energy demand in a highly demanding market.
With out a doubt, Chesterfield Special Cylinders is a partner of choice for hydrogen solutions, providing optimised plans for efficient storage and making use of the fewest cylinders which are seamless, accurate and made to order.
“Highest quality standards,” says Pinder, “Means longer life.”
Understanding that since the refuelling process for hydrogen vehicles requires higher pressure, the company have developed a 500-bar hydrogen trailer. One of the advantages of this trailer is that it also facilitates the transportation of two hundred bar hydrogen cylinders. This makes their trailer a leading player within the sector of future fuel transportation, and they also offer various other solutions for the transportation of alternative fuels.
Storing hydrogen under high pressure and within the confinement of a small footprint such as a refuelling station, requires a highly technical solution. At Chesterfield Special Cylinders they work closely with their customers to identify the best and cost-effective solutions for hydrogen refuelling stations around the world and support companies at the forefront of developing systems for this embryonic and growing industry.
“Our bespoke solutions reflect the size and pressure of our customers’ requirements,” Pinder says, “And in regard to safety devices, the experience of Chesterfield Special Cylinders hydrogen solutions world-wide, has helped to make systems as safe as possible.”
The efficiency of renewable plants is of major importance, especially in the storage of hydrogen or CNG (Biomethane). Whether you’re in need of a buffer system, a storage system or if you simply need to secure gas
This strategic move allows the group to focus on the growth of CSC in defence and hydrogen energy markets
availability for process purposes, CSC has designed and installed various compatible projects all over the world.
“Even if the project is at an early stage,” he adds, “We can use our experience to support you.”
This year has been a busy one for Chesterfield Special Cylinders, which on reflection is a clear example of the range of work they are involved with.
In March 2024, CSC secured a major contract to supply air pressure vessels for the Royal Australian Navy’s Hunter-class frigate program. This agreement, covering the first batch of three frigates, underscores CSC’s ongoing collaboration with BAE Systems and highlights its specialized engineering capabilities. Manufacturing milestones are set to commence later this year, with deliveries expected over the next three years.
The company was awarded a contract to provide high-pressure steel cylinder packages to Cheesecake Energy Ltd (CEL) for a pilot project funded by the UK’s Department for Energy Security & Net Zero. These cylinders will facilitate the storage of surplus energy from a dedicated solar power plant, promoting sustainable energy solutions.
To boost manufacturing efficiency, they invested in advanced equipment, including the installation of a DMG four-axis horizontal milling machine. Pinder believes that this upgrade enhances CSC’s capacity to meet growing demand across various sectors.
Then, in September past, their parent company Pressure Technologies announced the sale of its Precision Machined Components (PMC) division to Raghu Vamsi Machine Tools for an initial enterprise value of £6.2 million.
“This strategic move allows the group to focus on the growth of CSC in defence and hydrogen energy markets,” Pinder explains, “Where we see a great deal of potential in the future for our services, products and reputation for excellence.”
Our fully compliant, temperature-controlled vehicles provide secure and reliable distribution of medical and pharmaceutical deliveries, including time-sensitive cold chain parcels. With over 40 hubs across South Africa, our state-of-the-art and fully integrated technology and logistics infrastructure solutions makes us the perfect partner for the medical and pharmaceutical industry. Paperless, secure and timeous, our online track and trace system also makes it easy to follow your vital parcel journey from start to finish.