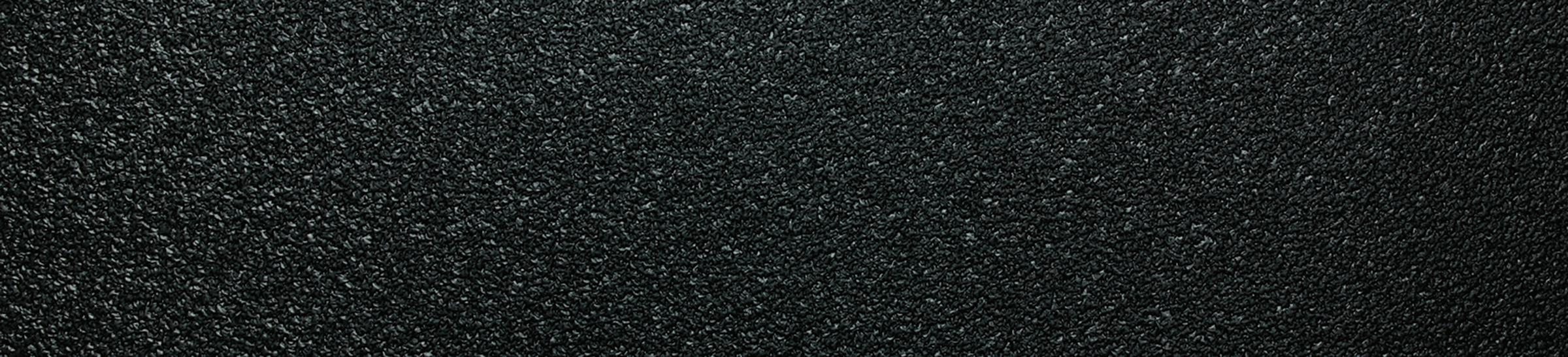

Influencers
Cat® SDX
The Cat® SDX Screed Plate System is changing the standard for asphalt screeds. It is designed to create smoother surfaces, higher densities, faster screed plate changes and increased wear properties when compared to standard screed plates.
Contractors utilizing the Cat SDX Screed Plates have experienced higher and more consistent densities across the width of the mat. Contractors have also realized improvements in International Roughness Index (IRI) scores.
Machines equipped with the Cat SDX Screed Plate System utilize a hardware-free locking system that enables replacement in as little as 4 hours. This unique design minimizes the need for scheduled downtime.
Contact your local California Cat Dealer for more information.
The Cat SDX Screed Plates are designed with cast chromium-alloy materials that provide consistent properties throughout the plates to increase wear life when compared to standard screed plate designs.
Regular readers of this publication no doubt notice that we have a fondness for quality. Most years, we devote an entire issue to the subject, and have done extensive reports on research and best practices on how we can make asphalt pavements of the highest quality possible.
Back in 2012, we profiled Bruce W. Woolpert, former CEO of Graniterock, winner of the Malcolm Baldrige National Quality Award. In the same issue we interviewed the chief of the Caltrans Office of Roadway Materials Testing, Joe Peterson, who discussed the department’s approach to quality.
In 2013 we focused on the quality work on the asphalt placed on the new San Francisco-Oakland Bay Bridge. In 2014 we did a deep dive on a national movement to improve ride quality through technology, measurement and incentives. In our special leadership issue in 2016 we profiled Larry Bonine, former Arizona DOT director and “Zen Master” of quality and mentor to many. In 2017 we were back examining pavement quality and durability through the lens of using higher percentages of Reclaimed Asphalt Pavements (RAP).
Jumping ahead to 2019, the innovative Caltrans-industry Joint Training & Certification Program made the cover of the magazine, spotlighting how collaboration can result in quality and consistency in testing construction materials. Our 2020 quality issue highlighted new and exacting Federal Aviation Administration airfield specifications, and the importance of precision when measuring pavement smoothness.
In 2021, we took a humorous take on quality pavements, thanks to Steve Marvin, president of LaBelleMarvin, who brought his unique take on “politically correct” pavements. By 2022 we were spotlighting innovative Caltrans design strategy for long-life (perpetual) asphalt pavements, which earned the department and the contractors who worked on the projects national recognition by the Asphalt Pavement Alliance.
Sometimes just posing the right questions can elicit new insights. On the cover of our 2022 equipment issue, we posed a simple but powerful question: “How do you know?” The issue also profiled our recently launched Quality Certificate Program, the gold standard for excellence in the asphalt paving industry in California. Last year we took a look at how we define quality, and added some famous quotes from W. Edwards Deming, Winston Churchill and others. A popular one, variously attributed to John Ruskin and William A. Foster, defines quality this way: “Quality is never an accident; it’s always the result of high intention, sincere effort; intelligent direction and skillful execution; it represents the wise choice of many alternatives.”
By now you get the idea: quality never goes out of style. That’s why we’re back on the subject with this issue, focusing on perspectives from influential experts on the subject. Our Q&A with Buzz Powell, in particular, draws upon his many years of experience for the Alabama Department of Transportation, in private industry, and managing the Pavement Test Track operated by the National Center for Asphalt Technology at Auburn University. He is currently technical director of the CalAPA-supported Asphalt Pavement Alliance.
I have my own bias since I put the word “quality” in my company name when I founded it. But I think you’ll agree that quality is here to stay, and the members of the California Asphalt Pavement Association will always place quality at the forefront of everything we do.
Chris Gerber President G3 Quality
Q&A with Buzz Powell, Ph.D., P.E.
Technical
CalAPA-supported asphalt technology workshop at CSU Chico proves popular
Member spotlight: From source to surface, Talley Oil Inc. continues their 75 year legacy of innovation and
HEADQUARTERS: P.O. Box 981300 • West Sacramento • CA 95798 (Mailing Address) 1550 Harbor Blvd., Suite 120 • West Sacramento • CA 95691 • (916) 791-5044
EXECUTIVE DIRECTOR: Russell W. Snyder, CAE, rsnyder@calapa.net
TECHNICAL DIRECTOR: Brandon M. Milar, P.E., bmilar@calapa.net
MEMBER SERVICES MANAGER: Sophie You, syou@calapa.net
MEMBER SERVICE COORDINATOR: Jackie Henry, jhenry@calapa.net
GUEST PUBLISHER: Chris Gerber, G3 Quality
PUBLISHED BY: Construction Marketing Services, LLC • (909) 772-3121 P.O. Box 892977 • Temecula • CA 92589
GRAPHIC DESIGN: Aldo Myftari
CONTRIBUTING WRITERS: Russell W. Snyder, CAE, CalAPA and Brian Hoover, CMS
ADVERTISING SALES: Kerry Hoover, CMS, (909) 772-3121
Over 100 di erent asphalt products and grades of material available
Rigorous in-house testing procedures ensure consistent quality
Value-added service at every step, from product selection to application
Full-service transportation solutions across the Paci c Northwest
A proactive approach to safety and environmental protection
Technical Director, Asphalt Pavement Alliance
By Russell W. Snyder
Editor’s Note: Buzz Powell is well-known nationally and in California in the asphalt pavement industry and academic circles. Since November of 2023 he has been the Technical Director of the Asphalt Pavement Alliance, which is supported by the National Asphalt Pavement Association, the Asphalt Institute and State Asphalt Pavement Associations, Inc., including CalAPA. He retired in 2023 as an associate director of the National Center for Asphalt Technology (NCAT) and a research professor at Auburn University after a 24 year career. For much of that time he was in charge of research related to the NCAT Pavement Test Track, where many different types of asphalt pavements and treatments have been field tested under simulated real-world conditions, providing important new knowledge for an industry committed to innovation. Located on a 309-acre site, the NCAT Pavement Test Track is a 1.7 mile closed-loop oval comprised of 46 200-foot test sections that undergo controlled heavy truck traffic equivalent to 10 million equivalent single-axle loads (ESALs). From 1986 to 1997 Powell worked for the Alabama Department of Transportation, last holding the position of assistant testing engineer. Powell has a Ph.D in Civil Engineering from Auburn University. Earlier this year he was a featured speaker at the CalAPA Spring Asphalt Pavement Conference & Equipment Expo in Ontario, and his remarks were very well received by both industry and
agency personnel in attendance. Many attendees said they appreciated his expertise and perspective, as well as his passion for quality asphalt pavements. He sat down recently with California Asphalt magazine to share the insights he has gleaned over his long career working in academia, public works and private industry.
California Asphalt Magazine: Thank you for making time to speak with us.
Buzz Powell: I’m very excited to do this interview, and really appreciate the opportunity.
CAM: We’ve been talking to lots of prominent people in our world about what quality means to them. We’d like get your thoughts on that as well. Because you are so well known from your time at the NCAT Pavement Test Track, perhaps we could start there.
BP: It was a huge blessing to me to be at the track for as long as I was. The fun thing for me about it was, prior to that, I was with the Alabama DOT for 12 years, and I wrote and enforced specifications. And I also worked in the private sector for a few years doing consulting work before I came to NCAT. I really thought I understood our world, our asphalt world, prior to my time coming to NCAT. But when I came to NCAT I realized rather quickly that I didn’t know what I thought I knew. I was dealing with aggregates and mixes and specifications from all over
the country for the large variety of test sections that we built for that first research cycle. All of a sudden I’m living like a contractor, and I’m dealing with stuff from all over the country that I’ve never seen before. In three months in the trenches, when we built that first track with 46 test sections, I learned more than I did in the whole rest of my career to that point. I thought I knew what I was doing, but I quickly realized that I didn’t, and I had to fight my way through it and learn as I went. I developed an instinct to change hats. When I’m looking at any technology, or any method or any specification, I think, “If I’m an agency, can I write and enforce a specification and create a level playing field for bidding and building purposes using this?” And at the same time, if I’m wearing a contractor’s hat, I’m thinking, “Am I confident that I can bid and build
a successful project with this? And how much risk do I need to build into my prices to protect myself?” And so I found myself in a really interesting mindset because I constantly bounced back and forth between those two worlds. And I still think that way when people ask me questions about new technologies. It’s really instinctive for me to say, “If I’m an agency, this is what I think about that.” And then, “If I’m in industry, this is what I think about that.” It is an interesting perspective.
CAM: So you’re a “Spec Whisperer,” right?
BP: I don’t know about that (laughs). But I think I understand what contractors go though, and the whole concept of risk, the essence of risk in our projects. Agencies are risk-averse. They instinctively want to avoid risk, and when they encounter it, they want to push as much risk as possible over to the contractor. And I certainly understand that. But I think sometimes what the agencies don’t grasp is that if I’m a contractor, and you push risk on to me, that risk is going to have to be translated into higher bid prices. That’s because I just can’t assume risk without compensating for it in the way I plan and cost out
Buzz Powell,
Technical Director
of the Asphalt Pavement Alliance, was a featured speaker at the 2024 CalAPA Spring Asphalt Pavement Conference in Ontario.
my project. That was one of the things I did not understand as an agency person, but I really get it now, because the NCAT Pavement Test Track is a non-profit research business. We don’t have unlimited money to do things. We have budgets that we have to work with. I 100% get it.
CAM: Contractors live in that world every day.
BP: Right. An easy example that is very relevant to the market in California is the whole issue of granulated tire rubber. My mentor within ALDOT had a mindset of, when I get a tanker full of binder, it needs to have everything in it that is going to be required to run that mix because I don’t want to run the risk that any ingredient is not accounted for during production. So that is how we wrote and enforced our specifications. That would require, then, a terminally blended ground tire rubber modified binder. So as an agency person, I was taught that way. But now if I’m a contractor, I really understand it – if I’m going to run ground tire rubber, my preference is a dry additive because if I add it at the plant as a dry additive then I can keep ground tire rubber out of my tank, out of my plumbing system. It’s not something I have
to account for because of my perceived risk of the negative impact that it may have on me. And so that’s just a really easy example of understanding both perspectives that I never had before. And it’s because we’ve done such a large variety of technologies through the years when I worked at the NCAT Pavement Test Track.
CAM: In California, particularly in the industry’s discussions with the California Department of Transportation on specification language and contract requirements, there has traditionally been baked-in friction on this point. Sometimes it seems like the Department wants to push all the risk, which generally revolves around unknowns, to the contractor, while the contractor wants to have it reside with the owner. In recent years there has been a greater appreciation by each party of the point of view of the other, and this has helped to reduce some of this conflict and arrive at specifications and contract language that represent a true compromise that will work for all parties. This is no easy task, but the joint industry and agency commitment to partnering principles seems to have helped tremendously in this regard. Everything is in service of a successful project, which is in the best interests of our ultimate customer, the taxpayer and transportation system user.
BP: That’s exactly right. The way we need to do it is we need to be partners, and find the most product-oriented way that we can share the risk, because that’s going to give the taxpayers the best deal, I think.
CAM: That is the magnetic north, if you will. Ultimately, the taxpayer will be the one benefiting from the final product, and we all need to be mindful of that. At least in the case of the DOT-industry relationship in
recent years, at least in California, it seems to be trending upward in this regard. That’s not to say it isn’t without its hiccups, and there is always the potential to backslide, but there does appear to be a recognition and respect from all parties about the point of view of the other.
BP: That sounds good.
CAM: In the purest sense, entities such as NCAT explore gaps in our knowledge and attempt to fill them with practical research. Here in California this is also done by, among others, the University of California Pavement Research Center and the Pavement Preservation Center at California State University, Chico. And there is a recognition that, in an Information Age when we are awash in data, rigorous research that is practical, peer-reviewed and field tested, really stands out from the crowd and helps everyone understand the product better and make better decisions.
BP: Yes, and that gets into the subject of controlled experiments. You’ve got to have controlled experiments so outcomes are not biased. An easy example of that is you can take a good asphalt, and put it on a bad road, and it might not perform well. But that would not be a reflection of the quality of the asphalt. And the flip side of that is also true. You can put a bad asphalt on a good foundation and it might look better than it really is. It is a simple illustration of why it is so important to do controlled experiments where all the things that can possibly confound your results can be controlled. I was with ALDOT when we implemented SuperPave, and we had several field projects scattered all over the state. I wasn’t supposed to be there when the projects were built, but I was supposed to pull the QC (Quality Control) data, and look at
field performance, and try to make sense of it. I wasn’t there, so I didn’t know how good the data was, or how much the materials varied, from south Alabama to north Alabama. We had no idea what the traffic levels actually were. And then if I wanted to go out there to do a good “boots on the ground” assessment of performance I ran the risk of being run over by live traffic. So now when I came to the NCAT Pavement Test Track, I built all the test sections. Construction was precisely controlled and documented. The climate was identical for every section. The traffic was precisely monitored. And then we could shut the fleet down every Monday and collect all the performance data we wanted without any risk of being hit by a truck. So all the factors that could potentially confound the experiment out in the real world, all of those factors were normalized and controlled at the track.
CAM: Those types of controlled experiments really came in handy with NCAT’s research into the use of Reclaimed Asphalt Pavements (RAP), right?
BP: Right. We started building high RAP test sections in 2006. The first test sections were 45% RAP, and the next test sections were 50% RAP. I came out of that experience with the perspective that you can do this. You can build pavements that are half recycled or reclaimed materials. You have to have performance specifications to do that, I believe. I concluded that, if I’m a regulator, I should be comfortable writing a specification around this. The cautionary tale is for contractors because, yes, you can do this, you can hit the quality targets. But you must do special things in your yard. You can’t treat high-RAP mixes like you treat low-RAP mixes because you must have more respect for RAP piles than you do for virgin piles,
because they are going to hit you on the gradation side of the mix as well as the AC (liquid asphalt binder) and the volumetrics sides of the mix. So fractionization and Quality Control testing, statistical understanding of RAP, that’s a good example of experimental control and the real-world stuff that you learn that is really useful for agencies for new specification development and implementation. And also for contractors, who shouldn’t go into these jobs thinking they’re not going to make investments in their operation and change some things. You can do this, but it’s going to take some extra effort. It’s a necessity to have controlled experiments so you can come out of it with that kind of meaning.
CAM: That’s an astute observation about RAP, and how using more if it will require changes on the part of the contractor. We have also seen that in California with rubber mixes. The properties are different than conventional Hot Mix Asphalt, and they also perform differently on laydown. Contractors need to be aware of those differences, and respond accordingly, for them to achieve an optimum performance in the field.
BP: Exactly. And when you have problems when you’re a contractor and quality is bad, you’re also going to hemorrhage money. You want to build a high-quality job, and you want to do it in a profitable way, so you have to understand the technology that you’re working with going into it or you’re not going to be able to satisfy both of those objectives.
CAM: Sticking with the higher RAP issue for a moment, we have done a lot of engagement with the state DOT and others on increasing the percentage of RAP in mixes, but there continues to be a reluctance
[ Continued on page 12 ]
[ Continued from page 10 ] on the part of some owners to move in this direction even though it is clearly sustainable and should be popular with their constituents. We even published a cover story in this magazine titled, “Who Killed High RAP?” highlighting the fits and starts on this front. What do you attribute the reluctance on the part of agencies to embrace high RAP?
BP: I think the risk-aversion and institutional resistance is always a challenge for innovation to overcome. But, in my opinion, the big resistance to higher RAP is related to binder content. Mix performance is about the quantity and the quality of the effective binder content. Legacy volumetrics only address the quantity of the effective binder content, and not the quality. We’re not comfortable loosening our grip on the basic volumetric principles that we grew up understanding. But I think it is going to take Balanced Mix Design, or at least relaxing our grip on volumetrics and having an open mind about volumetrics in order to really innovate with high RAP. It’s super important in a market like California where the availability of virgin materials is finite. It’s not just about pursuing a green concept and saving money. It’s about the reality of limited resources. It has to happen. And we need to do it and deliver the best possible product for the taxpayer. If we have half of a new mix that is aged binder, legacy volumetrics are really not going to tell us what we need to know about the quality of that effective binder content. We are going to have to use Balanced Mix Design testing, which I am personally an advocate of, and be able to think outside the box with traditional volumetrics. In other words, let air voids go really low, lower than we are traditionally comfortable with, because we have confidence in a rutting test and a
cracking test that will tell us what mix quality is. Or, the alternate method is to use the corrected optimum asphalt content (COAC) principal that more states are adopting now, which still requires you to relax volumetrics. So whether you are using mix testing, or whether you are using something like a modified volumetric approach, you must loosen your grip on legacy volumetrics. Whatever approach the agency wants to take, it’s up to them. But we need to have quantity and quality of effective binder content. We have an aversion to loosening our grip on those basic mix principles that we grew up with — mixes produced with virgin aggregates and neat asphalt — because the numbers don’t mean the same with polymer and high polymer binder and with higher percentages of reclaimed and recycled materials.
CAM: Interesting.
BP: We have the tests. We have the knowledge. We have to overcome the institutional riskaversion toward doing something different.
CAM: On the subject of Balanced Mix Design, which certainly seems in our future, what is your assessment of where we are on that
right now? How long will it take for BMD to be fully implemented?
BP: Too long. That’s my assessment (laughs). And I say that as a regulator. If I was writing specifications, I would want to implement it now. Let’s start like we did with SuperPave. We implemented SuperPave, and then we modified our practices as we learned more about it.
CAM: For our younger readers, Superpave mix design was developed as part of the Strategic Highway Research Program from 1987 to 1993, which had a goal of developing a performance-based asphalt binder specification as well as a performance-based asphalt mixture specification and a mixdesign system. It ushered in major changes to asphalt specifications, procedures and test methods.
BP: Right. So for Balanced Mix Design, let’s implement it and we can modify it as we work our way through it. The longer we wait, the more millions of tons of asphalt we produce that may not be providing us with the performance that the taxpayers have invested in and have trusted us with. I’m an advocate of implementing sooner rather than later because I believe that we know enough about Balanced Mix Design to
do a better job with it. As proof of that, we did a project where we helped some counties in Alabama to come up with a really simple BMD specification. It’s all about just testing the material as it comes out of the plant, and making sure it meets an IDEALCT requirement and a Hot IDT requirement. There’s an AM test and a PM test. It’s really simple, but the counties are extremely pleased with the product that came out of that. The allowable RAP content almost doubled in the mixes, as long as you could ensure mix quality. Everybody won. The counties got a better product. The taxpayers got better performance. The contractors got to use more RAP and they got to innovate. I don’t want to wait five years so we can do more research projects to learn more nuances. We tend to go down rabbit holes, and that’s part of my bias. I’ve worked a lot in the academic world, but one of the problems we have is academia creates a divergence of thought. The funnel is shaped the wrong way. You can’t get a Ph.D by studying something someone else did. You have to create some new knowledge, so it creates divergence. We end up with a whole bunch of different approaches, when really the funnel should be the other way and we should all be working toward the best possible solution. That’s part of our problem. We do too many academic research projects, and we end up going down rabbit holes. What really matters is mix performance. As agencies, let’s specify mix performance, which BMD does, and let industry respond to that by innovating. That’s what we need: our specifications that give the taxpayers what they’ve invested in, but the process needs to be open enough to allow contractors to innovate. Legacy volumetric specifications are much more like recipe specifications.
Contractors’ hands are tied –they can’t innovate. We need to ensure quality at the same time we facilitate innovation. I believe that Balanced Mix Design is the way that we do that.
CAM: We’d like to get your perspective in the perpetual pavement design concept, also known in California as longlife asphalt pavement, a design strategy where asphalt pavements will last 40 years or longer with minimal maintenance. It was a little slow to catch on in California, but after a successful project on the 710 Freeway in Los Angeles County, and lots of evaluations by the University of California Pavement Research Center and others, Caltrans has now embraced the concept, and several other projects have been constructed on Interstate 5, Interstate 80, and the concept was recently included in the Caltrans Highway Design Manual. The Asphalt Pavement Alliance, which has a perpetual pavement award program, recently presented an award to Caltrans for implementing these projects. How do you view this pavement design strategy nationally?
BP: Perpetual pavements are something that I am especially excited about. We have a perpetual pavement conference coming up later this year, and I wrote a paper for that conference to describe the large variety of the perpetual pavements that we have built and tested and observed at the NCAT Pavement Test Track. When you talk about perpetual pavements, many people instinctively think you’re talking about a really thick pavement. In simple terms, yes, you build a thicker pavement, and it is thick enough that it never cracks at the bottom and we just preserve the surface, renew the surface, and the foundation lasts forever. And that’s true. But we can compartmentalize it when
we think of it that way when we say, OK, strain-tolerant bottom, thick strain-resistant middle and then a durable surface. But that’s not the whole story. We did research at the NCAT Pavement Test Track on mix and materials, pavement thickness and pavement preservation. Perpetual pavement is a fun topic because it involves all three of those things. You want to strategically use the right mix and materials, depending on where you are within the structure. You don’t want to waste any thickness. You want enough thickness so that you’re isolating the distresses to the surface, and then you want to preserve it in the most costeffective way. But instead of thinking like really thick three-layer systems, you can get around that, for example, by doing something we did at the track in building a two-layer perpetual pavement. It was 8 inches of thick high-mod binder dense-graded mix and then a half-inch thick, dense-graded 4.75 MM surface mix. So it was a two-layer perpetual pavement. We built a “forever pavement” with two paver passes, in two lifts. The first lift was 8-inches thick, high-mod binder running Warm Mix Asphalt technology, at 275 degrees. We cut full-depth cores and sliced it up into pieces to look at the density profile. The density was really good in the top middle, and bottom. It was a good, healthy mix. So there you have a perpetual pavement that is not like the concept we think of inside the box. But that’s a pavement that’s going to last forever. All you have to do is preserve the surface.
CAM: As one Caltrans construction engineer once told us, the department likes the concept of “Get in, get out and stay out.”
BP: Right. I love the idea of perpetual pavements because you can innovate to get to that pavement that just has to be
preserved. The easy button is the traditional three-layer concept, really thick, but the rest of the story is that if I’m a designer at an agency, or if this is a design-build alternate bid, we need to leave room for innovation in there on the design side and the designbuild side so that we can really take advantage of technologies that create that system where the pavement will last forever. I think using technology like highly modified binder, and innovation, I think you can build a concrete pavement or an asphalt pavement at exactly the same thickness, but with rapid construction on the asphalt side, and now you have a system that is more economical and just has to be preserved forever. It’s hard to beat a pavement like that. And that’s really fun innovation where the taxpayer wins. It’s a great topic, and it’s something I’m very excited about. A big focus of the Asphalt Pavement Alliance is acknowledging perpetual pavements.
CAM: It was great that Caltrans, as well as the contractors, got that recognition from the APA. A lot of people put in a lot of work to refine that design strategy so that it is not something that is exotic but rather just another tool in the designer’s toolbox.
BP: I’ve been blessed, since I’ve been with the APA, to present some of those awards, and the fun part about that is it takes really well thought-out designs, it takes really good construction, and then it takes generations of maintenance and preservation. You look at the engineers that are in that history. We give out one award, but there’s multiple generations of engineers who contributed to the success of that return on investment for the taxpayers. It doesn’t get any better than that. I love to go give an award for a pavement that might
have been built in the 1960s, and it was a good design, and good construction. And I think, “How many engineers were involved in maintaining that structure since it was built in the 1960s?” That’s a huge success story. We need to give out a whole bunch of those trophies to everyone who was involved in that process.
CAM: Let’s talk about trends. You benefit from lots of different perspectives in your long and successful career. What trends to you see in the future that either industry or agency personnel should be aware of?
BP: That’s a great question, and some of it depends on how we embrace innovation on both sides of the contract. Especially in the California market, we talked about diminishing virgin resources. We have got to get on board with higher percentages of reclaimed and recycled materials in specification systems. But in
order for us to be successful with that, industry has got to embrace the idea that we’ve got to step up our game in the way we handle these materials. We can do that. For example, look at how safety has evolved over the last three decades in our business. We have the capacity to change. We have the capacity to make life better, and we’ve got to do that on the quality side and in our technical practices side. We’ve got to up our game. Agencies need to be willing to accept that, OK, we’ve got to open the door to innovation. We’ve got to protect the taxpayers, of course. We’ve got to have a good specification package that is something that’s enforceable, that contractors can bid and contractors can build. And industry has to embrace the idea that, yes, we can do these things, but it’s imperative that we deliver the quality that the taxpayers require. Contractors have to play the short game and the long game all the time. You survive in bidding cycles. If you can’t survive in bidding cycles, then what happens five years from now really doesn’t matter. You have to survive in the short term, but you also need to be looking long-term, and anticipating the long game so you can survive today and thrive tomorrow. I think that’s the perspective you have to have in industry, and that way you can be a successful business from bid month to bid month and you can keep our industry competitive out there in the pavement-type selection process and the preservation option selection process so that we can be as competitive as we really want to be in those areas.
CAM: That’s one of the most important responsibilities of our association, to understand what is happening today, but to look over the horizon to see what is coming, and prepare our membership so [ Continued on page 16 ]
For over 30 years, we’ve been one of Southern California’s leading seal coat manufacturers and service providers. We’re here to support your business with exceptional products and lasting value.
SUB CONTR AC TIN G
(High Per formance Seal) – No Track Tack
U IP M EN T REN TA L
6000 Gal Job Site Tank Drop Deliveries
600 Gal Seal Tank Trailers SS1h Tank Trailers
OverKote® Asphalt Pavement Sealer
SS-1h Emulsion Paving Fabric Rolls
Petrotac and Geo Textiles
Hot Soup Buckets Oil Flo & Oil Spot Sealer Latex Additives
when that eventuality arrives we are ready for it. That also includes the duty to influence those far-off issues so that they are beneficial, or at least not harmful, to our industry when they arrive. A big part of that is education –educating stakeholders, regulators, elected officials, agencies and other project owners, about our product and our processes. It is playing the ultimate long game. It’s hard work, but important.
BP: Absolutely. Just take sustainability. We use that word a lot, but industry has to be sustainable to meet infrastructure needs in the future, so it’s not just about material sustainability or environmental sustainability. It’s people, planet, profit, right? We have to work in the overlap of the Venn diagram, because that creates a sustainable infrastructure for the future. That’s imperative. It’s essential that’s where we stay. It’s a challenge for spec writers. I was writing specifications before I was out on construction jobs with the DOT, and I didn’t have the right perspective. I didn’t begin to develop the right perspective until I was out on active projects having to solve problems on a daily basis, and observe what the contractor was going through, and what the project team was going through. And then I came to the NCAT Pavement Test Track later and had a whole new world view based on what I experienced there. We have a lot of young people at our agencies who have a very limited view of the construction world that we live in, and the more we can do to foster good fellowship between industry and agency the more everyone will understand we all want to do the right thing. Let’s work together to achieve that.
CAM: The CalAPA strategic plan, in fact, has these concepts woven throughout, helping owners
succeed. We educate industry and agency personnel, side-by-side, so that everyone has access to the same information. I know the APA also has a robust program to educate industry and project owners about key concepts, design strategies and other disciplines so they can design and execute successful asphalt pavement projects. Our association appreciates coordinating with the APA, NAPA the Asphalt Institute and other partners to achieve this common level of understanding, even as our industry continues to go through many changes.
BP: That sounds great. The Asphalt Pavement Alliance’s mission is in alignment with that.
CAM: So, how would you compare your time at the APA to your previous jobs? I know the APA is doing a bit of a self-assessment, and we and other stakeholders have been called upon to provide input. What is your perspective?
BP: My last three years at NCAT I was responsible for the Pavement Test Track research program, but a primary responsibility for me was promoting implementation of track findings. The commonality is that’s what I’m really doing now – promoting implementation of the things that I have learned. I’m really enjoying that part of the work that I’m doing with the APA because it’s very connected to the experience that I was blessed to have at the NCAT Pavement Test Track all those years. So all of that experience informs me in the implementation promotion mission, moving the needle in the marketplace in a healthy way. I want to encourage agencies to make the right kind of change so that everybody wins. With the right kind of innovation, everybody wins. The agency wins, the taxpayers win, and the contractors win. That really is my
mindset going into this. Our three funding partners are NAPA, the Asphalt Institute and the state asphalt pavement associations, and those three entities have slightly different priorities. Their missions are different. I think I had a healthy understanding of that going into my job, but I have a growing appreciation for that as time passes. NAPA has its national mission, the SAPAs have a very much state-focused mission, and the Asphalt Institute has a very much product-focused mission with hot liquid asphalt and emulsions. I imagine that as another Venn diagram, and the overlap of those three things is the easy place to work. The hard place is where they don’t overlap. I have a respect for what that is, and promoting the right kind of implementation with a healthy understanding of what the market looks like.
CAM: You came out earlier this year to speak at the Spring Asphalt Pavement Conference in Ontario, and your remarks were very wellreceived by the audience. What were your impressions from your visit to California?
BP: I love going into states where it strikes me that there is a great partnership between industry and agency. I have not had a lot of time to spend in California, but what time I have been there I feel like there is a really good partnership. I think I saw it at that meeting. No one put any boundaries on what I was asked to talk about. I was asked to speak about national issues that I believed would be important to California, and so I put that presentation together, and did a demonstration of the “Hey NAPA” AI-powered tool. My topics, I think, were very well received, and there was a very good exchange afterwards, and I observed that good partnership afterward,
which was very refreshing. I like to go into markets and talk about national issues and regional issues when those partnerships exist.
CAM: Any final thoughts?
BP: I guess my final thought is if you are a contractor, and you are trying to work through a problem, or trying to accomplish an objective, put on the agency hat and look at it from the other side. And the same thing is true for agencies. If you are an agency person, and you’re looking at a new specification or you’re trying to work through a dispute or something, put on a contractor’s hat. Try to understand what is happening on the other side. If you can do that, that’s how we really solve problems. What I tell young engineers with agencies, when you’re writing specifications, when you think you have it in a
final form, put on the contractor’s hat and say, “Now I’m going to bid this job. What does this specification mean to me?” Do a thought experiment and ask yourself that.
CAM: Or better yet, solicit input directly from the contracting community. That’s what we do in the joint Caltrans-industry Pavement & Materials Partnering Committee. The process takes a little longer, but better and more realistic specifications are the result. The model has proven to be very successful.
BP: I think specifications would roll out looking a little differently if we all did that. I wish I could go back and re-do that part of my career with that mindset, because I think it is a really healthy perspective to have. We can get to a better place from an innovation
point of view if we can try to develop that type of mindset. It’s about safe mobility at the lowest possible lifecycle cost, and to do that what we need is quality asphalt pavement. That is achievable when you write the right specifications and deliver the right product. The taxpayers win when we do that. CA
Russell W. Snyder, CAE, is executive director of the California Asphalt Pavement Association (CalAPA).
Snyder, R. & Milar, B. (2017) “Who Killed high RAP?” California Asphalt, Journal of the California Asphalt Pavement Association, 2017 Quality Issue (PP 8-22)
Crafco Mastic One is your answer for fast, durable pavement repairs. Mastic One seals wide cracks and large distresses, and is load-bearing while remaining flexible to protect the surrounding pavement. Make your repairs quickly with Mastic One and open to traffic within hours, not days. Visit Crafco.com/Mastic-One to see how you can get more done.
Editor’s Note: What follows are selected perspectives from noted asphalt experts contacted by California Asphalt magazine on the subject of quality.
I view quality in the context of the project, and prefer the phrase ‘an appropriate level of quality.’ The quality characteristics need to appropriately address the project needs, but do not need to exceed them, or to address characteristics that do not materially affect project value or performance. Thus, quality is as much, if not more, a design consideration, than a construction consideration.”
the public never notices it. The public doesn’t see the frantic concert of engineers, technicians, surveyors, inspectors, and construction crews that work with that quality in mind to construct the road they drive on. Only when some part of the construction fails to meet that high quality does the public notice. But even then, that concert of professionals starts again to ensure that the road is fixed and that quality is met. This is not done for the fame or accolades, but for the desire to construct quality roads deserving of the taxpayer’s monies.”
Blaine Thomann Laboratory Manager, County of Orange
Mike Robinson, P.E. Consulting
Engineer,
Wyoming (& CalAPA trainer)
The easy definition would be that quality is the standard to which something is assessed. However, instead of the word standard, I prefer the word excellence. Quality is the level of excellence to which a product performs. I started to say that it is the level of excellence in which it satisfies the purchasers' requirements. However, after some thought, I strongly believe that is not the case. What if a purchaser has a poor standard? What if they are ok with buying something that is cheap? You would not that quality just because it met the purchaser's expectations. Quality has to be tied to delivering performance in the asphalt industry”
Richard Willis, PhD Vice President, Engineering, Research & Technology
National Asphalt Pavement Association
“As an agency, we want high quality asphalt concrete in the public roads, so the taxpayers realize smooth roads that last their design life. To achieve that final quality means holding higher standards at all levels of the project: design, materials, inspection, and construction. It’s a performance where all the people in these aspects of the project must perform their part with that final quality in mind. When our industry does its job well and produces this high-quality asphalt concrete,
“Quality in asphalt pavement means ensuring long-lasting, durable, resilient, and sustainable roads that meet both performance and safety standards. It reflects the balance between materials, construction techniques, and design, aimed at achieving optimal performance under traffic and environmental conditions.”
Jhony Habbouche, PhD, P.E.
Western U.S. Regional Engineer Asphalt Institute
"Quality is a measurement tool we use to compare one item or service to similar items or services. We celebrate the ability to achieve our goals with different strategies and different tools. As a result, the quality measure tells us more than the acceptability of an item. Quality provides insight to the focus, passion, commitment, and craftsmanship of those that provide the item or service. Whether we are buying a new pair of shoes, a new car, or building an asphalt roadway, we identify our values and our quality measurement tools. With these in hand, we can move forward with our decisions on how to make or select an item or service."
Brandon Milar, P.E. Director of Technical Services
California Asphalt Pavement Association (CalAPA)
By Russell W. Snyder
An American Public Works Association, Sacramento Chapter sponsored asphalt technology workshop held at Cal State Chico gave college-age students a hands-on view of how asphalt pavement mixes are designed, tested and evaluated.
The fourth annual event was also supported by CalAPA and CalAPA member Knife River. CalAPA Technical Director Brandon Milar, P.E., delivered one of the presentations on asphalt pavements, and CalAPA sponsored one of the lunches at the May 29-31 event attended by about 20 students from various Northern California colleges and universities. CalAPA member Knife River also hosted a lunch and tour of its Chico asphalt plant complex.
CSU Chico Associate Professor Kun Zhang, Ph.D., one of the organizers of the event, said he "very much enjoyed talking and working with" the attendees and various subject matter experts who contributed to the program, including Caltrans Office of Asphalt Pavement Chief Cathrina Barros and Brendan Ottoboni representing the City of Chico.
Mason Richardson with Knife River helped conduct the tour of the Knife River facility May 31. "It went really well," Richardson said. "They definitely asked a lot of interesting questions. I think they were interested in our industry."
CalAPA's support of the event is in alignment with its workforce recruitment and development
mission as envisioned by its newly established charitable arm, the California Asphalt Research & Education (CARE) Foundation. CalAPA's Milar, who also has helped with foundation work, said he was pleased to support such a high-quality workshop at CSU Chico.
“What was noteworthy was being able to provide university students with a hands-on experience with asphalt materials, in the lab and also in the field, combined with a plant tour,” Milar said. “That hands-on experience is a huge plus in this event. There are a lot of university-level civil engineering programs that don’t provide this level of asphalt focus, and the hands-on experience.”
Milar said the event reminded him of a similar workshop he attended early in his engineering career that sparked an interest in asphalt pavements. At that
workshop he met legendary professors Carl Monismith with UC Berkeley, and Peter Sabaaly with the University of NevadaReno, cementing what would become a lifelong collaboration in advancing knowledge and best practices about asphalt pavements.
“It is one thing to sit in a class and have someone talking to you,” Milar said. “It is very different when you get into the lab and do the hands-on activities. That’s what I would really like to see more of, the hands-on focus, in
educating those who our headed into our industry.”
Other participants had similar sentiments.
“It has been a great opportunity to learn more about how asphalt is made and how it comes together, and how I can better aid that process,’ said Keith Gramcko, Design Engineer with Kenco Engineering, a CalAPA associate member and manufacturer of wear parts for the construction industry.
Rick Liptak, representing the APWA Sacramento Chapter, said, “This event is a very rare opportunity for civil engineers, and anybody in the industry, to
learn about asphalt pavement. This will really set apart those students who participated in this workshop because they’re going to learn things that other people in our industry do not know.”
The agency perspective was provided by Barros, who oversees asphalt projects for Caltrans, the largest consumer of asphalt in the state.
“One of the things I shared is, we have over 50,000 lane-miles of road, and 75% of them are made of asphalt,” she said. “And our replacement value for pavement, if we had to take it all out and do it all over again, it would cost us $64 billion, so the asphalt
pavement on the road, it means something. It is valuable.”
One of the students who participated in the workshop, Bryan Saucedo from Butte College, said he also appreciated the hands-on approach to learning.
“It was pretty interesting,” Saucedo said, “going out into the street, laying out the asphalt, making sure it is clean beforehand, obviously, and then padding it down, smashing it with the compactor, and after that, covering it with the dirt to make sure it doesn’t stick to the tires of the vehicles driving by.”
Left: One of the 10 modules of the workshop involved filling potholes with asphalt patching material.
Below Left: Workshop participants also got to tour the Knife River Construction Materials Lab at their Chicoarea plant.
Below Right: CalAPA member Knife River hosted a tour of its Chico-area asphalt plant and materials laboratory for the workshop participants May 29.
Looking at potential future technologies also was highlighted at the workshop. Chris Wacinski, CTO and founder of Driven Plastics, delivered a presentation on those emerging technologies.
“The first third was talking about sustainability, what is sustainability? Wacinski said of his presentation. “The second part we talked about is what I’m looking in to, plastics in asphalt, how that is done, when they are evaluating new materials, how to consider performance additives, things like that. And the third material we talked about was a
plant-based rejuvenator that we are bringing into the market.”
Another summer workshop on asphalt technology with be held at CSU Chico in 2025, Zhang says. CA
Russell W. Snyder, CAE, is executive director of the California Asphalt Pavement Association (CalAPA). Content provided by Cal State Chico College of EDD TV was included in this report.
When it comes to building roads, you want to do it as quickly and efficiently as possible. That’s why you choose Volvo. The hard-hitting rollers from Volvo offer greater uptime and higher performance, helping your productivity stay in the fast lane. Find the right equipment for your road-building projects with Volvo Construction Equipment & Services.
By upcycling end-of-life tires and leveraging their performance properties, SigmaBond extends the life of roads while meeting California's sustainability goals.
• Designed to meet the latest Caltrans and Greenbook specifications for terminal blend PG-TR and MAC 15/10
• Only terminal blend PG-TR and ARHM that routinely uses more than 15% RAP
• Reduces surface wearing course thickness without sacrificing performance
• Enhances pavement marking contrast due to coloration of carbon black
By Brian Hoover
O. W. (Oscar) Talley started hauling livestock right after returning from serving his country in World War II in the 1940s, under the name Talley Transportation. The livestock trucking business grew as Oscar began adding several more trucks. However, things changed with the advent of refrigeration and packaged meat, so Oscar and his son, Ken Sr., began hauling liquid asphalt and fuel oil in insulated tankers. This business continued to grow and is still owned and operated by Ken Talley Sr. today, managed by his son, Marty Talley.
As the Talley family trucking business evolved, the family decided to get into other ventures such as ready-mix and the sand and gravel business, eventually choosing to go back to what they knew best—trucking. Ken Talley Jr. (Talley) graduated from Cal Poly San Luis Obispo in 1998, and he and his father, Ken Sr., began discussing his immediate future. “Dad and I bumped heads for a while, so I went to work for the Reed family out of Modesto. I worked for Greg Reed and Mark Bertsch for three years, and this was a great experience for me. This is where I first learned about asphalt emulsions, asphalt rubber, chip seal, pavement maintenance, and other solutions available on the construction side. This is also where
I got to meet many of the people I work with everyday,” says Talley. “I eventually decided that it was time to go home and work things out with my dad, who gave me a job driving distributor trucks and tankers. Then, in 2004, my brother and I, Marty, sold the home left to us by our grandfather and purchased an emulsion mill and some used storage tanks, and set up on an old pecan orchard in Madera owned by our father. We had three distributor trucks, four asphalt tankers, and the emulsion mill and tanks, but nothing else. So, we ended up going on eBay to purchase pumps, motor drives,
and other plant components. We could not afford a brand-new plant, so this is how we built our first emulsion plant.”
The Talley brothers started making some money off of their plant, and so they decided to build a hot mix plant at the same site in Madera. Unfortunately—or fortunately, depending on how you look at it—the decision to go into the hot mix asphalt business was severely stifled by the fallout of the Great Recession. “The recession hit us hard, and we made the move to lean more on the trucking business once again,” explains Talley. “As fate would have it, things worked out as we put an agreement together with Vulcan Materials, selling them the plant itself and leasing the property, while also maintaining the inbound trucking contracts. The plant would have taken us 10 years to pay off, but by making the move to work with Vulcan Materials, we were able to free up our capital for other ventures.”
The decision was made to invest in new trucks, new distributors, and a new chip seal machine. Then, in 2020, an opportunity presented
itself in Taft, California. “We decided to purchase a prototype asphalt production facility in Taft. It took some time to figure it all out. We made the move to now focus on the asphalt emulsion production side of the business. After completing construction of a new emulsion plant, we started purchasing asphalt from third parties and began manufacturing emulsions,” says Talley. “Our plan was to go back to the existing part of the facility and start manufacturing our own asphalt from the crude oil we were going to be purchasing from the Central Coast area. After a lot of hard work, we got it done and began taking possession of crude oil from the Santa Maria area. We haul the oil in our trucks to the Taft facility where we process the crude oil into asphalt and a light gas oil that we sell to third parties.”
Now that Talley was manufacturing their own asphalt in Taft they were able to supply themselves there for emulsions and they would haul the asphalt for use at their original asphalt emulsion plant in Madera. In Madera, the company then utilizes its own construction crews to place the material for customers throughout the Central Valley, from Bakersfield to Sacramento. “We haul the asphalt emulsions to customers who put down the material with
their own distributor trucks, or we do it for them with our own in-house fleet of Bearcat computer-controlled distributor trucks. To highlight our new, almost fully vertically integrated offerings, we coined the phrase, ‘From Source to Surface,’” continues Talley. “With the exception of the production of the crude oil itself, we now control the entire process. We use our own materials on our own construction projects and also sell our slurry, chip seal, and all of our other asphalt emulsions to thirdparty users.”
Talley Oil Inc. now operates through three separate divisions. The transportation division is made up of crude oil trucks, asphalt tankers, and asphalt distributor trucks. The materials division is responsible for manufacturing asphalt and asphalt emulsions, while the construction division bids and performs work for Caltrans, cities, counties, and other agencies, along with ongoing private jobs. “As of late we have grown quickly and are now focusing on quality and company culture. Our transportation and manufacturing divisions serve all of California, while our construction division is localized within the Central Valley. We are fully licensed throughout the states of California and Nevada, but we purposely remain local to keep our people home at night with
their families,” says Talley. “Being strategically positioned is also important in the emulsion business to better serve customers. Because we are ‘Source to Surface,’ the buck stops with us. No excuses. We have a lot of pride in what we do and are extremely customeroriented. If there is an issue, we get to the bottom of it immediately and make it right. It is always about the customer getting the best product and the best service.”
In order to better serve their customers, Talley Oil leverages automation in the manufacturing process. “I believe that our automated systems on the manufacturing side will trump anything out there right now. We are able to process more material with fewer people while always providing a consistent, high-quality product,” continues Talley. “We are often asked to build emulsion plants for others, as we learned this business from the ground up and continue to design and implement our own manufacturing systems. We believe in an old-school work ethic, supported by the latest technology and systems.
Talley says that his family-owned and operated business will eventually expand into new locations, expanding their reach and territory. However, Talley says that growth will come slowly and organically.
“Our customers are also many times our competitors. This is just the way it is in our business, and everyone tries to get along and helps one another out whenever needed,” continues Talley. “Our trucks work primarily for our own interests, but also for others when needed. We sell materials direct to our competitors at the same price as we would to ourselves. We don’t need every job, but we would like a piece of as many projects as possible through the supply of materials and/or trucking.”
Ken Talley Jr. served as president of the California Chip Seal Association (now Western Regional Association for Pavement Preservation) and has been recognized with awards like the AEMA (Asphalt Emulsion Manufacturing Association) Excellence in Manufacturing Award in recognition of their Taft facility. Talley Oil also became a member of the California Asphalt Pavement Association (CalAPA) four years ago, and Talley says the decision has helped them to remain on the cutting edge. “I felt like we had grown to a size where we needed
to be continually informed on what was going on in the asphalt industry. For example, we rely on CalAPA for information on things like the upcoming Environmental Product Declarations (EPDs). We are now well-prepared for implementation and documentation. By sourcing local crude materials for our asphalt and maintaining high efficiency in both transportation and manufacturing, we expect to offer significant market advantages to our customers, explains Talley. “Our customers are members of CalAPA, and that is where the knowledge base is to stay informed on what is going on in the asphalt industry in California. CalAPA remains a valuable asset for all of our divisions.”
What began as a livestock hauling business 75 years ago has now become an industry-leading trucking, manufacturing, and construction business today. Talley Transportation paved the way for Talley Oil, a company that is now a fully integrated trucking, manufacturing, and construction enterprise. “My father comes into work every day and is very involved
in the trucking business. None of this would have been possible without all of our very hard working people and of course my father, grandfather, and grandmother (Elaine Talley). My grandparents lived and began their livestock trucking business from their home in Maricopa. Now, 75 years later, we are hauling crude oil right through the same town.”
Talley Oil manufactures various asphalt emulsions, road oils, and dust palliatives that are applied throughout California and other states, such as Oregon and Nevada. Their construction division offers chip seal, crack fill, fog seal, Reclamite, and dust control for vineyards, dairies, contractors, numerous government agencies, and other public and private entities. For more information on Talley Oil Inc., please visit www.talleyoil.com or call their Madera headquarters at (559) 673-9011. CA
Brian Hoover is co-owner of Construction Marketing Services, LLC, and editor of CalContractor Magazine.
CalAPA members and their guests gathered on July 27 for another festive "Day at the Races" at Del Mar fairgrounds, proving once again that a work-life balance can be fun and exciting at the same time.
The Women of Asphalt California Branch volunteers added a colorful flair to the event with a "Derby Day" hat contest and other activities that
helped keep things lively between thoroughbred racing action. In the CalAPA-sponsored third race, Without Borders with Diego Herrera aboard, coming in at 8-1 odds, led the pack and claimed the $40,000 purse, paying $14.80 on a $2 bet. Queens Code came in second and Phosphorescense was not far behind in third. Sadly, a horse named "Beer Money" finished out of the money.
The setting was the fabled Del Mar Fairgrounds, where cool ocean
breezes and a spectacular view from a luxury skybox above the finish line afforded attendees ample opportunities to cheer on their favorite horses, network and just have a good time.
Special thanks go out to the event sponsors: Ergon Asphalt & Emulsions, Inc., Martin Marietta, Pavement Recycling Systems, Sully-Miller Contracting Co. and Valero Energy. Additional photos will be posted on CalAPA's various social media feeds. CA
Participants of the hat contest.
Mission
Hardy & Harper’s group: (Standing) Monique Beyle (left) Dennis Beyle, Ruby Lemus, Tony Lemus, Jose Mora, Jon Dooley (PRS), John Godinho, Jennifer Godinho, Anne Bolanos. (Seated) Maura Reed, Justin Dooley and Rigo Bolanos.
Jessie Ponce (left) and Alan Arredondo, Diversified Asphalt.
Steve Ward PRS (left), Chis Albright, DIII, Maxwell Hobbs, Martin Marietta, Taylor Schmidt, Surface-Tech and John Cress, Martin Marietta
home second place at the
Susie Muniz guest of Sully-Miller Contracting won a Hermes scarf in honor of the 2024 Paris Olympics.
to
By Russell W. Snyder
Family, friends, co-workers and other well-wishers gathered in Los Gatos recently for a "celebration of life" for longtime industry figure Gerald R. "Gerry" Graham Jr. of San Jose-based Reed & Graham Inc., who passed away on Sept. 1 at the age of 78.
Graham, born on June 5, 1946, was the son of Gerald R. Graham Sr., who while working in the construction industry in the 1940s helped guide the business into asphalt, and in 1955 joined forces with the C.E. Reed Co. to become Reed & Graham. Graham Sr. passed away in 2017.
A Navy veteran who served two tours in Vietnam, Graham joined the company in the 1970s and performed nearly every job at an asphalt plant, including driving loaders. He started his own contracting business in 1976, Graham Contractors Inc., which he owned and operated for over 30 years before selling it to his son, David Graham, in 2018.
In the mid-1980s, while still running his own business, he returned to Reed & Graham to assist in managing the company. He was named president and CEO in 1996.
In the 1980s the company began marketing OverKote, a seal-coat product. The company also moved aggressively in the recycling area, and also added a Geosynthetics Division. Among his many accomplishments as CEO, he helped direct a major refurbishment of the company's San Jose hot mix asphalt plant in 2010.
At a packed memorial service held Sept. 18 at the La Rinconada Country Club in Los Gatos, family and coworkers shared fond memories of Graham as a tough but fair and loyal boss, father and mentor to many.
At the event it was announced that for his lifetime of contributions to the asphalt pavement industry, Graham will be inducted into the CalAPA "Hall of Fame" at the association's annual dinner Jan. 16 in Los Angeles.
Graham is survived by his children, Eric Graham and his wife Lucresia and their daughters Aurora and Miranda; David Graham and his wife Kristen and their children Nolan, McKinlay and Wyatt; Melissa Graham and her daughter Olivia; stepdaughter Stacey Rando and her husband Jim and their son Tyler and daughter Jacquelyn, as well as great-granddaughters Giuliana and Kynzee; stepson David McLean and his son Dawson; Gerry’s sisters Nan Graham and her wife Carol, Jane Graham; and sister-in-law Mary Ellen Graham,
as well as numerous nieces and nephews.
Graham was preceded in death by his parents Gerald Graham, Sr., Anna Jane Reed and stepmother Allene Graham, his brother Stephen Reed Graham, Sr., his first wife Nancy Graham, and his grandson Joseph Rando. In lieu of flowers, the family requested that donations be made in Graham's name to Bellarmine College Preparatory school in San Jose, or to the charity of your choice.
The Reed & Graham team also mourned the loss of longtime employee Eugene "Gene" George Guido. Born in San Jose on May 3, 1934, he attended local schools and later worked in the family's business, S.A. Guido Paving. He later hired on with Reed & Graham, where he worked for 47 years. For 30 of those years he was sales manager, representing the company. His son, Sal, also works for Reed & Graham.
Guido passed away on Aug. 30. He is survived by his wife, Rosemarie, and his children Michael (Lisa) Guido, Cheryl (Bruce) Maes, Sal (Dia) Guido and Marc (Becky) Guido, six grandchildren and five great-grandchildren. Services for Guido were held on Thursday, Sept. 19 at St. Lucy's Church in Campbell, followed by a Celebration of Life event at Orchard City Banquet Hall in Campbell. CA
Russell W. Snyder, CAE, is executive director of the California Asphalt Pavement Association (CalAPA).
Diamond Green Diesel
Valero’s Diamond Green Diesel joint venture is the world's second-largest producer of sustainable renewable diesel. Using recycled animal fats, used cooking oil and distiller's corn oil, we produce a low-carbon fuel that reduces life cycle greenhouse gas emissions up to 80% compared with traditional diesel.
Energy-saving
Emission-free,
Sustainable,
Combination
HAMMTRONIC
Low maintenance