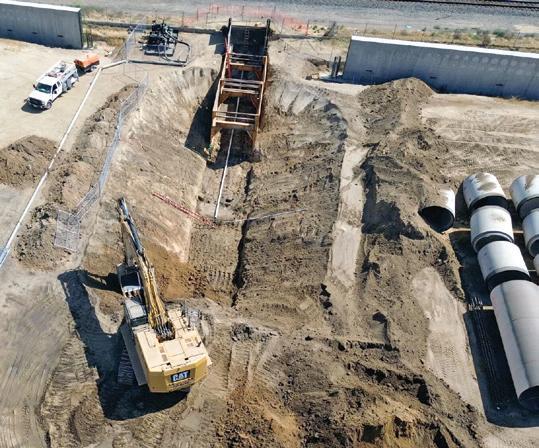
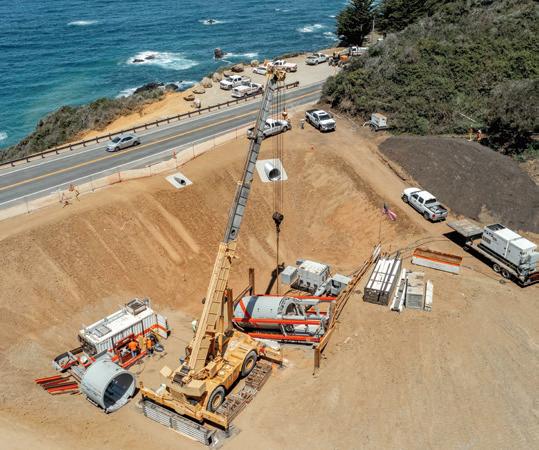
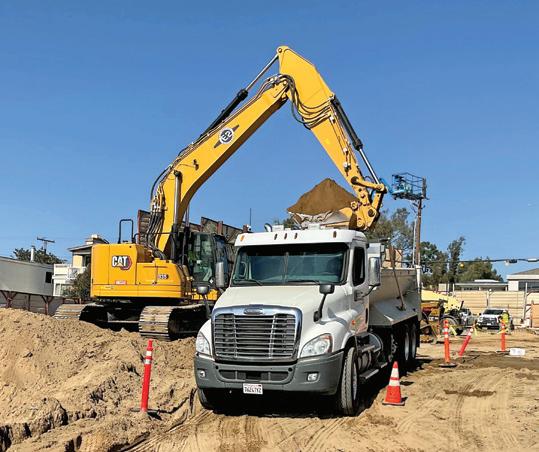
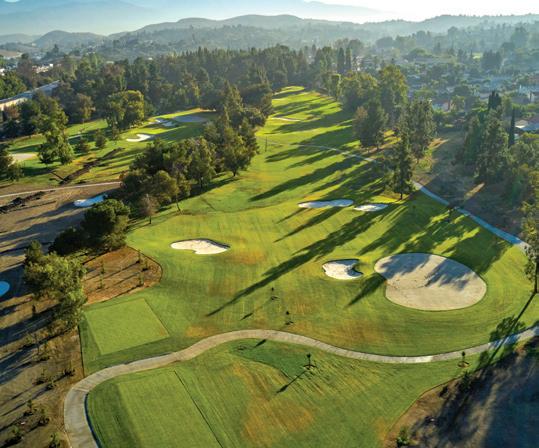

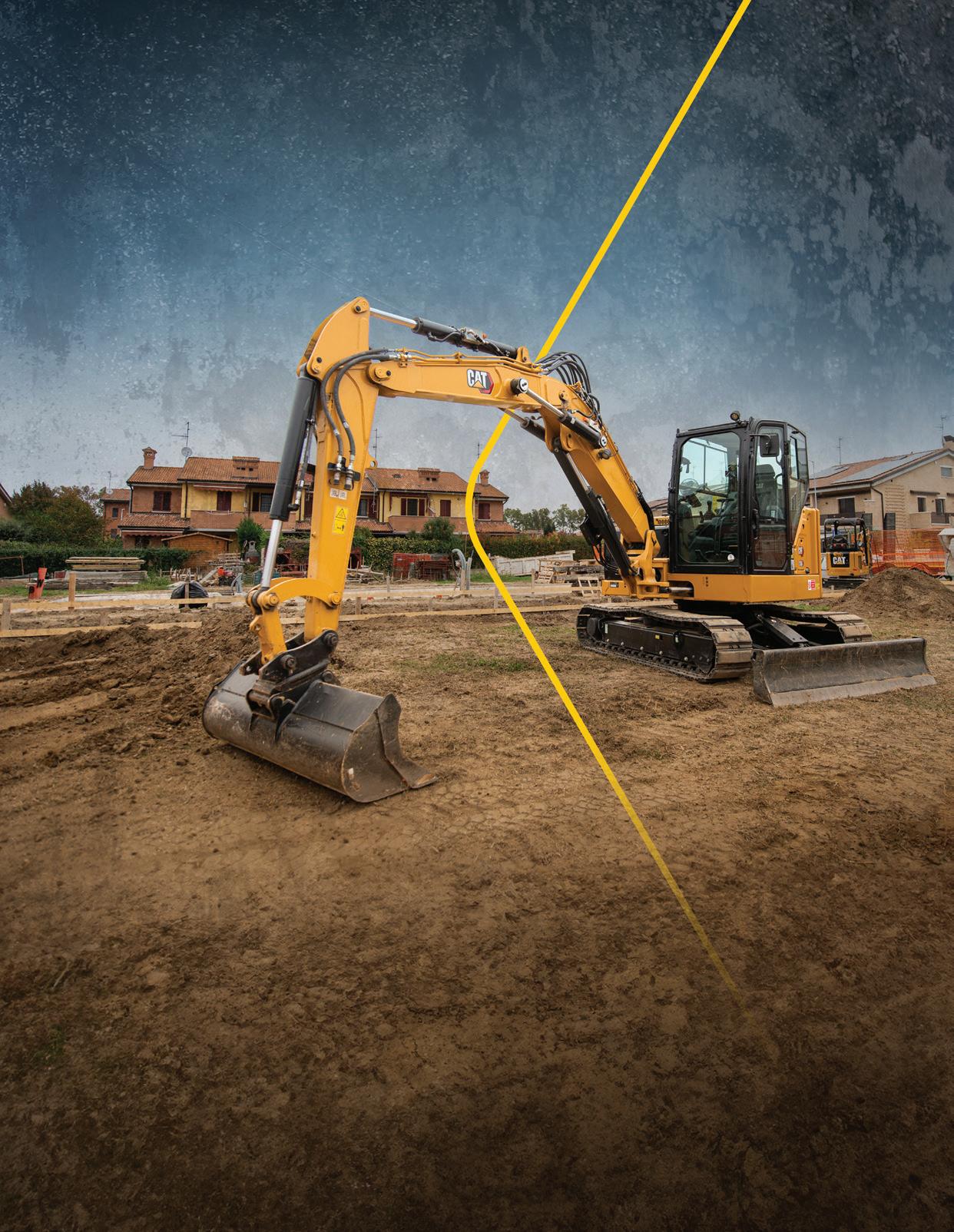
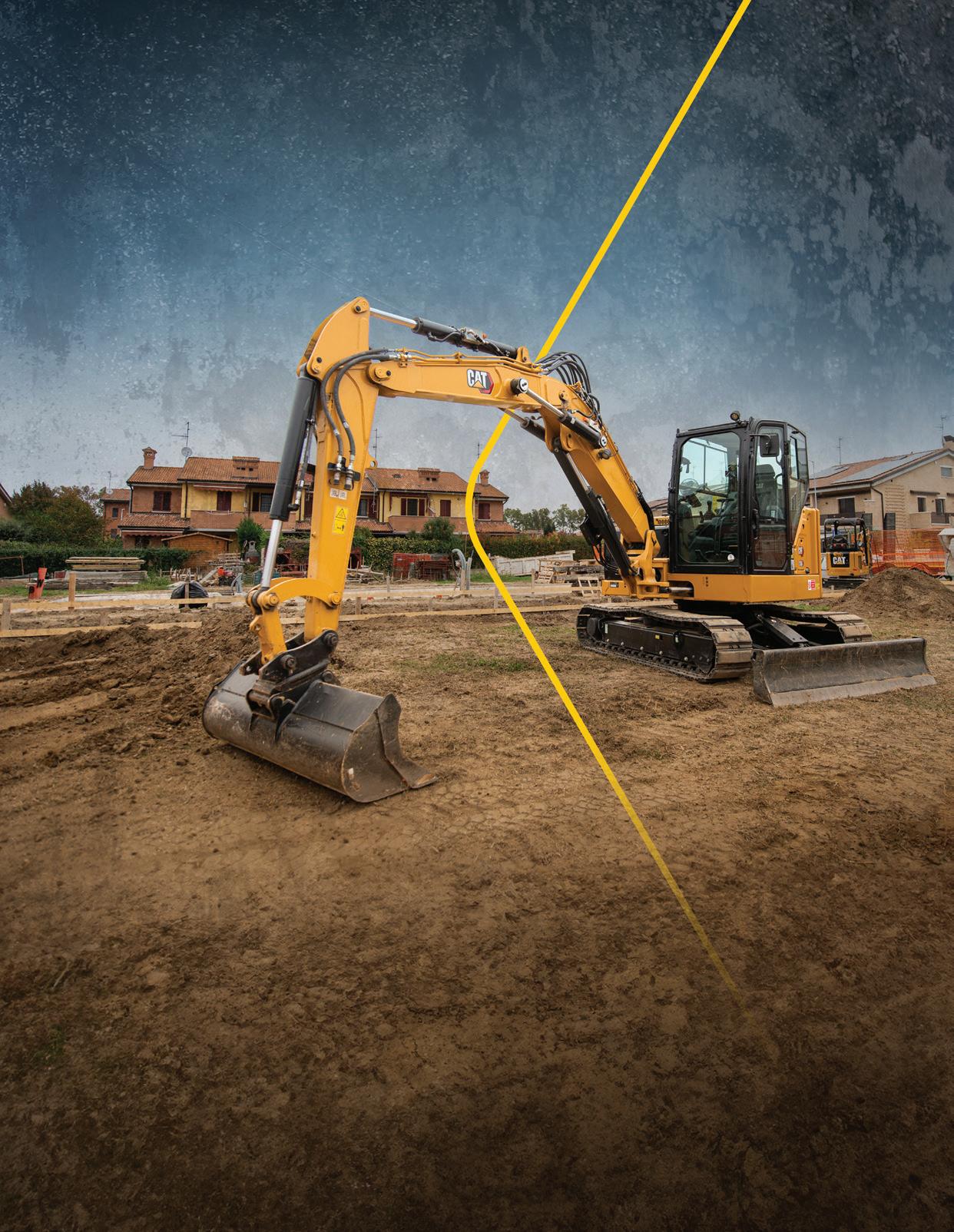

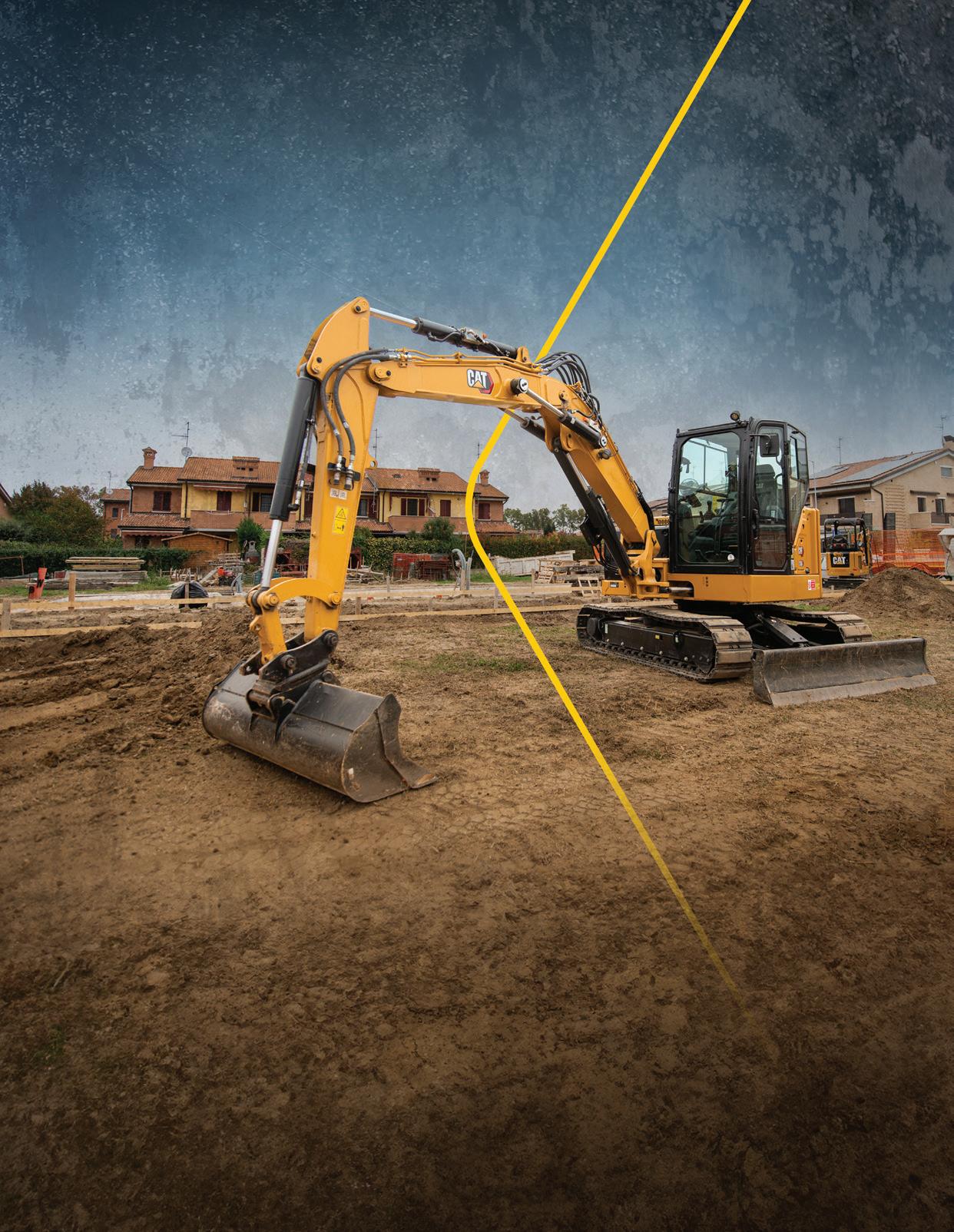
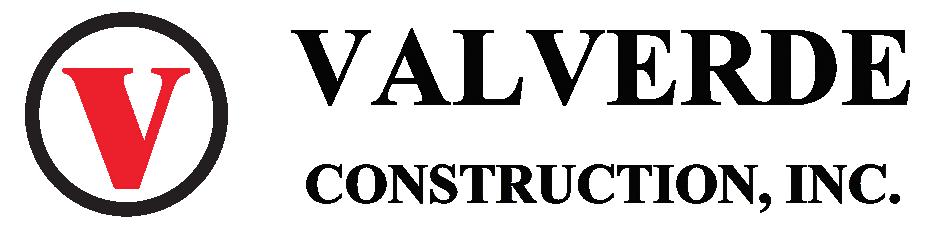
By Brian Hoover,
Valverde Construction, Inc. has built a reputation as one of California’s leading underground utility contractors, celebrating over five decades of excellence in the industry. Established in 1972 by Joe Valverde, the company is a family-run operation that has grown from humble beginnings into a powerhouse in the construction world. Today, Valverde Construction continues to thrive under the leadership of multiple generations, maintaining its commitment to quality, safety, and service.
Joe Valverde, now 88 years old and still actively working, founded the company after decades of experience in the construction equipment
industry. Joe began his career as a lowbed driver before transitioning to selling
equipment such as backhoes, dozers, and loaders in the 1950s. His interactions with contractors inspired him to take a bold leap into underground construction, despite having no prior experience in the field.
In 1972, Joe mortgaged his home to start Valverde Construction (Valverde) with the vision of providing top-tier underground utility services. At a time when there were few Hispanic or minority-owned construction companies in the industry, Joe faced significant challenges. However, his perseverance, resourcefulness, and ability to hire and train skilled workers laid the foundation for the company’s success.
Joe’s vision for a family-run, generational business inspired his sons—Mike, Ahron Sr., Edward and Chris to join the company and contribute to its growth. Each son brought unique expertise, from field operations to office management. Mike and Ahron Sr. gained hands-on experience in the field through the Operating Engineers’ apprenticeship program, while Edward and Chris transitioned into dispatch and estimating roles after studying at USC (University Southern California).
The family tradition continued with Ahron Jr., who joined the company in 2014 after earning a degree in business management from the University of San Francisco. Starting in the yard and working as a laborer for two years, he eventually moved into project management, focusing on time and materials (T&M) and change orders. Today, the
Left & Above: Valverde Construction crews perform conduit excavation on the LAX Metro Connector where they were subcontracted to perform water, sewer and storm drain utility relocations, along with duct bank construction.
company employs nearly 300 workers, including several Valverde cousins (Jonathan, Meghan and Steven), and is proud of its multi-generational workforce.
Valverde Construction specializes in underground utility construction, offering services for both wet and dry utilities, structural work, and restoration projects. The company handles everything from emergency water line repairs to large-scale utility relocation for high-profile infrastructure projects. The following represent just a few of the projects that Valverde Construction is currently working on.
Valverde is one of several leading construction firms that have been a part of Metro’s plan to construct a better transit
system. Metro’s efforts include connecting Los Angeles International Airport (LAX) with the Airport Metro Connector (AMC) at Aviation Blvd./96th Street, allowing for smoother transfers between LAX and Metro’s network.
Valverde was subcontracted to perform water, sewer and storm drain utility relocations, along with duct bank construction. They began their work in late 2021 and are expected to complete their contract in the first quarter of 2025. Part of Valverde’s contract includes the installation of 24”, 4” and 6” HDPE storm drain, 2”, 4”, 6”, 8” and 10” SDR35 sewer, 2” and 3” SCH 80 domestic water line, 6”, 10” & 12” C900 fire protection, and 4”, 6”, 10”, 12” C900 fire water line, and a new sewer pump station. Trench Shoring Company supplied aluminum panel shields and slide rail, along with other shoring for the project.
Valverde is part of the construction team extending the subway system through Beverly Hills and Century City, with Sections 2 and 3 slated for completion in 2026 and 2028, respectively. Metro’s plan for better transit includes extending the D Line from Miracle Mile through Beverly Hills and into Century City, one of LA County’s biggest job hubs. This project will add two new stations at Wilshire/Rodeo and Century City/ Constellation, increasing access to opportunities for the region.
Located in the heart of Beverly Hills, Section 2 of the D Line Subway Extension broke ground in February 2018, and is slated to open for service in 2026.
Section 2 includes the addition of a new Wilshire/Rodeo station box, located under Wilshire Blvd. from Beverly Dr. to Canon Drive, with the station entrance on the southwest corner of Wilshire Blvd. and Reeves Drive. Additionally, the Century City/ Constellation station box will be located under Constellation Blvd. between Century Park East and Solar Way (between Avenue for the Stars and Century Park West), with a station entrance at the northeast corner of Constellation Blvd. and Avenue of the Stars.
Section 3 of the Westside Metro Purple (D) Line Extension Subway Transit Project will add two new stations to better serve the city’s Westside region. This new station will provide access to the Westwood Medical Center, Hammer Museum, UCLA campus and Westwood Village.
The LA Metro Division 20 project includes widening the portal for Metro’s Red and Purple Lines maintenance yard
{ Continued on page 8 }
{ Continued from page 6 }
(Division 20 Rail Yard), along with a track reconfiguration, and utility relocations. The portal widening is generally bounded by the BNSF ROW to the east, Santa Fe Avenue and Center Street to the west, Commercial Street to the north, and 6th Street Bridge to the south. The project is expected to wrap up in 2026 with Valverde being subcontracted to perform the utility relocation work. The relocation included the installation of 300 linear feet of 8” sewer line, 5,400 linear of 4” to 6” ductile Iron, 6”, 8”, 10” & 12” ductile Iron fire water line, and 18”, 24” & 30” HDPE storm drain line.
The California High-Speed Rail Authority’s Construction Package 1 (CP1) is the first significant construction contract executed on the Initial Operating Section of the High-Speed Rail project in California’s Central Valley. The CP1 construction extends 32 miles between Avenue 19 in Madera County to East American
Avenue in Fresno County. The project also includes major work elements in downtown Fresno, in addition to 12 roadway / railroad grade separations, two mainline viaducts, one tunnel, realignments of existing railroad tracks, utility relocations, roadway relocations, two trench sections, and a major river crossing over the San Joaquin River.
The CP1 design-build contract was awarded to Tutor Perini / Zachry / Parsons (TPZP), a Joint Venture, and Valverde was subcontracted for the utility relocation work throughout the 32-mile stretch of high-speed rail line in Fresno County, set for completion in 2027.
As the construction industry evolves, Valverde Construction remains at the forefront by embracing new technologies and sustainable practices. “We are always pursuing excellence,” said Ahron Valverde Jr. “Our evolving culture focuses on
managing today’s workforce and creating an environment where employees feel valued and respected.”
The company is also committed to workforce training and retention. According to Ahron Valverde Jr., key figures in the organization include Tom Hutchins, who has led operations in Fresno for over a decade; Raul Luna, overseeing operations in Los Angeles; Marcus Gomez, managing Northern California projects; and Angel Acosta, serving as the Traffic Manager.
Valverde’s equipment fleet, consisting primarily of Caterpillar machinery, reflects its commitment to reliability and efficiency. The company enjoys strong partnerships with Quinn Cat and Trench Shoring Company, fostering long-standing relationships with suppliers and collaborators. “Our fleet is primarily Caterpillar, with the exception of a few John Deere machines. We have a great working relationship with Quinn Cat and our representative, Joe
Bonelli, who has done an excellent job meeting and exceeding all of our expectations,” says Ahron Valverde Sr. “We also have an incredible, longstanding relationship with Trench Shoring Company. It is a generational relationship where Tom Malloy and my father, Joe, have fostered a personal friendship and excellent working relationship that goes way back. Then there is the relationship with Kevin Malloy and our current leadership team. Finding and maintaining long-standing, honest relationships has always been a major component of our ongoing success.”
As the construction industry faces workforce shortages, Valverde Construction emphasizes training, retention, and fostering a culture of respect and innovation. Ahron Jr. is focused on integrating technology and modern management strategies to ensure sustainable growth while adapting to an evolving
workforce. “Our company culture continues to evolve as we pursue excellence and manage today’s new workforce,” Ahron Jr. said. “We’re committed to making employees feel valued and respected, which is crucial for retention and long-term success.”
As Valverde Construction looks to the future, the company remains grounded in the values instilled by its founder. Joe Valverde’s determination, risk-taking, and commitment to excellence continue to inspire the family and employees alike. With a strong focus on generational leadership, sustainable growth, and technological innovation, Valverde Construction is wellpositioned to remain a leader in underground utility construction for years to come. “As I reflect on my grandfather turning 88 a few days ago, I am reminded of his perseverance through challenging times, particularly in the early 2000s. He deserves immense recognition,” said
Ahron Valverde Jr. “We are all reaping the benefits of that hard work and determination today.” Headquartered in Santa Fe Springs, Valverde Construction is a certified Disabled Veteran Business Enterprise and holds multiple licenses, including General Engineering (A), Building (B), Electrical (C10), Fire Protection (C16), and Plumbing (C36). The company’s clients include public agencies, private developers, and major utility companies across California, particularly in the southern region. Valverde’s 24-hour emergency service center ensures that cities, counties, and water districts can rely on the company for urgent repairs. Long-term contracts with entities like the City of Los Angeles and the County of Los Angeles demonstrate Valverde’s trusted reputation in the industry. For more information on Valverde Construction, Inc., please visit www.valverde.webflow.io or call their Santa Fe Springs headquarters at (562) 906-1826. Cc
•
•
•
•
•
•
Founded in 1981, Pacific Boring, Inc. (Pacific Boring) has built a remarkable legacy in trenchless construction, but its story begins with three Central Valley men who turned a shared vision into one of the nation’s most respected tunneling contractors. David Cline, James Gardner, and Calistro "Cal" Terrasas combined grit, ingenuity, and determination to create a company that thrives on overcoming challenges and delivering innovative solutions.
David Cline was born in Selma, California, and attended Washington Union High School in Easton, where he met James Gardner, his future business partner. James, raised in Easton, also attended Washington Union High School, graduating with Gardner in 1962. In 1978, their paths crossed again when they began working together at a horizontal drilling company. During this time, they met Calistro Terrasas, a U.S. Army veteran and
Clovis native who had recently joined the company after returning home from his service. The three men quickly became a formidable team, united by their shared work ethic and vision for the future.
THE BIRTH OF PACIFIC
In 1981, Cal suggested to David and James that they start their own company. The idea resonated, and Pacific Boring was established. From humble beginnings, the three founders carved out a niche in trenchless construction, focusing on innovation, reliability, and
teamwork. David managed daily operations as president, James oversaw the auger-boring division, and Cal directed crews as general superintendent. Their combined expertise, leadership, and peoplefirst approach propelled Pacific Boring to success. Today, the company boasts the largest fleet of specialized tunneling and pipe-jacking equipment in the United States, having completed
thousands of projects within California and nationwide.
Steven Gallyer’s ascent to the presidency of Pacific Boring, Inc. is a compelling narrative of personal ambition intertwined with a company culture deeply rooted in mentorship and development.
Born and raised in Caruthers, California, Steven exemplifies how opportunities guided by meaningful mentorship can shape an individual’s career trajectory while strengthening the foundation of a business.
Steven’s journey began long before he joined Pacific Boring. As a student at Caruthers High School, he was profoundly influenced by a teacher who
recognized his potential and encouraged him to pursue construction as a career path. This teacher’s advice planted a seed of confidence in Steven, helping him see his future in an industry where innovation and leadership are critical. His teacher introduced Gallyer to Pacific Boring, and after graduating high school in 2002, Gallyer joined Pacific Boring as a shop laborer. His responsibilities at the time included sweeping floors, loading trucks, and assisting with equipment preparation.
Gallyer’s ambition and strong work ethic quickly set him apart. Recognizing this, company co-founder David Cline furthered Steven’s journey by urging him to consider a career in construction management.
Taking these words of encouragement to heart, Steven pursued a degree in construction management at Fresno State University. After earning his degree in 2007, Steven returned to Pacific Boring full-time, stepping into the role of project engineer, and eventually advancing to
project manager. The company’s commitment to fostering internal talent created an environment where Steven could grow, flourish, and prepare for the next phase of his career. In 2021, Steven was named president of Pacific Boring. In his new role, Steven has embraced the responsibility of continuing the company’s legacy while mentoring the next generation of talent.
Over the years, Pacific Boring has tackled some of the most complex trenchless construction projects in the industry. Their work spans utility tunnels, culvert installations, and large-scale public works projects across the United States.
Pacific Boring also played a pivotal role in the emergency reconstruction of Highway 1 near Big Sur after a massive landslide in 2021 washed a section of the highway into the Pacific Ocean.
Papich Construction contracted with Pacific Boring to install a new 10-foot diameter culvert. Reopening Highway 1 was a priority for Caltrans, so trenchless installation was selected to allow work to be performed after the highway section was completed and reopened to traffic. “The slope was designed at 30.56 percent downhill with nearly 80-feet of fall over the 250-foot bore. The tunneling began within a depressed basin, so it was not necessary to excavate a jacking pit. Soldier piles were installed at the front of the pit to assist in holding back the 800ton capacity jacking frame.”
Currently, Pacific Boring is working on a high-speed rail project in Fresno County. This involves installing twin 96-inch casing under BNSF railroad tracks
{ Continued on page 16 }
Above
An earth pressure balance machine (EPBM) was used to pave the way for the new system and install 3,000 linear feet of 96-inch reinforced concrete pipe (RCP) in two drives of 1,300 Linear Feet and 1,700 Linear Feet.
{ Continued from page 14 }
and relocating a Fresno irrigation ditch. The project required 24/7 operations due to strict regulations in Zone A of the railroad, with drilling crews working during the day and welders at night. Utilizing an Akkerman Tunnel Boring Machine (TBM) and a 100-ton Grove crane, the team executed a precise operation to ensure the project met its deadlines.
According to Gallyer, the High-Speed Rail project began for Pacific boring in September, 2024 and just recently wrapped up in mid-November. “We used one of our 96-inch TBMs to implement two 144-foot bores, 12-feet deep to the top of the pipe. We also worked within an open cut area where we ran 360 feet of steel
casing, while pushing another 480 feet of 72-inch RCP (reinforced concrete pipe),” says Gallyer.
“Working under live railroad tracks was perhaps our biggest challenge, because we were working within what BNSF Railroad considers Zone A. Our crews were required to work 24/7 until all of the bores were complete. Our drilling crew would work the day shift, while the welders worked at night.”
In October 2024, Pacific Boring completed a challenging project on Highway 46 between Templeton and Cambria for Caltrans. Subcontracted by John Madonna Construction, the team installed 280 feet of 48-inch welded steel
pipe on a 14% downhill grade. The steep terrain required innovative setup and meticulous planning, showcasing the company’s adaptability and problem-solving skills. “We were subcontracted by John Madonna Construction to perform a bore to replace a failed culvert,” says Gallyer. “Our crew began the bore on October 14, 2024 and finished on October 28. We setup in a steep position to bore under Highway 46, alleviating the need for a bore pit.”
Headquartered in Caruthers, California, Pacific Boring operates as a union-signatory subcontractor, specializing in public works
projects. The company maintains a close relationship with the local community, recruiting talent from many sources, including Caruthers High School’s agriculture mechanics program, and Future Farmers of America (FFA).
The Pacific Boring team is known for its expertise, with most training conducted in-house due to the highly specialized nature of the work. “We have worked hard to hire and train intelligent, hardworking individuals that give their all out on the jobsite every day. I would like to take a moment to thank everyone here at Pacific Boring, and recognize two individual leaders who play a critical role in the success of our company,”
says Gallyer. “Ted Miller handles all of our estimating and has done an amazing job. Richard Cisneros oversees our yard and dispatch operations and keeps everything running smoothly.”
Pacific Boring operates six boring crews annually and boasts a full workload, recently s ecuring a Caltrans project in Napa that involves 4,500 feet of 42-inch RCP across 10 bores, set to begin in early 2025.
Now in its fourth decade, Pacific Boring remains committed to innovation, quality, and safety. With Dallas Cline and Brad Gardner, the next generation of ownership continues to build on the
foundation laid by their fathers. Under the leadership of Steven Gallyer and a dedicated team, Pacific Boring is poised to tackle future challenges and expand its legacy in trenchless construction.
From its inception in 1981 as a bold idea shared by three m en, Pacific Boring has grown into an industry leader through determination, teamwork, and a commitment to excellence. As it looks to the future, the company remains steadfast in its mission to deliver reliable, innovative s olutions for complex tunneling projects across the nation. For more information, please visit www.pacificboring.com or call their Caruthers headquarters at (559) 86 4-9444. Cc
The WORKMASTER™ 25S sub-compact tractor is the perfect “first step” tractor for homeowners and AG-lifestylers who need a hard-working, versatile small tractor to handle the chores a garden tractor just can’t. it’s ready to take on your yard, landscape, gardening and property maintenance jobs. Its compact size makes it easy to operate and maneuver around obstacles and in confined spaces
Precision Detection technology is available in smoke and combination alarms and meets the latest industry standards.
Same Wiring Harness
No extra parts needed for an easy installation
Available in Photoelectric & Ionization Sensing Technologies
10-Year Battery options available to eliminate battery changes for the life of the alarm
Less Nuisance
Distinguishes between cooking smoke or steam and a fire emergency to reduce nuisance alarms
Early Warning
Provides an early warning because today’s home furnishing and materials burn hotter and faster
By Brian Hoover, Editor / Photos supplied by E2 Contracting, Inc.
Established in 2018, E2 Contracting, Inc. was born from a unique convergence of military discipline, lifelong friendships, and complementary expertise. The name “E2” reflects the first plane Navy veteran and company co-founder Erik “Reno” Franzen, CDR USN Ret., flew during his 26-year service: the E-2 Hawkeye, a twin-turboprop aircraft used for airborne early warning missions. Beyond its aviation roots, the name also symbolizes the company’s focus on engineering and earthwork, two cornerstones of its operations.
Erik Franzen’s career as a Navy pilot introduced him to construction during his final years of service. As his aviation career wound down, Erik transitioned into installation management, overseeing naval
bases and construction projects as the Commanding Officer of NAF El Central and the Executive Officer at Naval Weapons Station Seal Beach. These experiences laid the groundwork for his post-military venture into the construction industry.
It was a chance meeting at a bar with longtime friends Steve Arthur and Robert Lagsdin during an Ohio State versus USC football game that sparked the idea for E2 Contracting. Erik mentioned his post-retirement boredom, and Robert suggested starting a Disabled Veteran Business Enterprise (DVBE). After a follow-up meeting, Erik, Robert, and Steve decided to join forces and establish a construction business. Today’s ownership and leadership team consists of Erik Franzen, who serves as President and Chief Compliance Officer, Robert Lagsdin, Vice President and Senior Estimator, Steven Arthur, Vice President of Business Operations, and
Michael Lewis as Director of Operations and Federal Projects Program Manager.
The trio brought a wealth of knowledge to their venture. Erik leveraged his military leadership and organizational management experience, Robert contributed over 25 years in the earthwork industry, and Steve offered a logistics background. Later, Michael Lewis, a geologist and college rugby teammate of Steve, joined as Director of Operations and Federal Projects Program Manager. Together, they assembled a team with complementary skill sets, which has been key to the company’s growth. “We’ve known each other since childhood or college,” Erik explains. “That level of trust and shared history helps us operate smoothly and make decisions confidently.”
E2 Contracting began modestly with a $67,000 grading project for a General Contractor at a Utility Companies training facility. Over time, the company built a reputation for quality work, reliability, and its ability to meet DVBE requirements for general contractors. Early introductions to General Contractors at veteran-focused networking events helped E2 land critical subcontracting opportunities. Today, the company specializes in grading, mass excavations, and general earthwork, primarily throughout Southern California.
E2 Contracting has tackled notable projects, including work on the SEGS Boron Solar Farm Project, where its team operated scrapers for months to prepare 60 acres of land. Another milestone was the Warner Bros. Ranch redevelopment in Burbank, a $500-million project that will add soundstages, offices, and parking to the historic studio lot.
Currently, E2 is working on a multi-faceted project at Beverly Hills High School, which includes demolition, grading, and excavation for a new athletic building and pool complex. Additionally, the company is contributing to the
LA Purple Line extension as a subcontractor, constructing a parking lot and parking structure on the VA campus.
Erik often draws parallels between his time on an aircraft carrier and the construction industry. “Working on a flight deck is one of the most dangerous jobs in the world. You have to keep your head on a swivel. Construction sites are similar—there’s heavy equipment everywhere, and safety must always be a priority,” he says. E2 prioritizes safety and professionalism,
consistently exceeding client expectations and maintaining clear communication to ensure projects are completed on time and within budget.
E2 Contracting has grown significantly since its inception, increasing annual revenue more than 300% since its’ initial years. A key component of the company’s success is its strategic approach to equipment.
E2 maintains a fleet primarily composed of Caterpillar equipment, including excavators, loaders and a Cat 150 motor grader with Trimble GPS technology.
While owning equipment offers long-term cost advantages, E2 recognizes the importance of flexibility and efficiency through equipment rentals. Partnering with Savala Equipment Rentals, the company accesses top-tier machinery and operators to meet the specific needs of each project. Savala’s reliable service
and high-quality equipment have allowed E2 to adapt to varying project demands while keeping overhead costs manageable.
Steve Arthur, Vice President of Business Operations, elaborates: “Our partnership with Savala Equipment Rentals has been instrumental to our success. It ensures we always have access to experienced operators and the latest machinery, allowing us to scale up or down as projects require.
{ Continued on page 24 }
{ Continued from page 22 }
This adaptability is especially crucial in today’s market, where timelines and budgets are tighter than ever.”
E2 aims to own 60–70% of its equipment fleet, strategically renting the remainder to remain nimble during economic downturns or peak project loads. This balance allows the company to maintain a lean operational model while delivering high-quality results.
In addition to General Contracting Earthwork Division, E2 also offers Environmental Remediation and Operated Equipment Rental services. The company’s SDVOSB (ServiceDisabled Veteran-Owned Small
Business) certification has been instrumental in securing federal contracts, including several projects on the VA Wilshire campus. “We have three revenue streams so that if any one of them slows down the others will sustain the business. We have a subcontracting side which is our earthwork and demolition services, a general contracting side where we do environmental remediation, and oil well abandonment, and then an equipment rental division,” says Erik. “We are proud to offer our operated equipment rental to our customers to help them easily fulfill their DVBE (Disabled Veteran Business Enterprise) or SDVOSB (Service-Disabled Veteran-Owned Small Business) credit requirements.”
E2 Contracting’s leadership remains committed to sustainable growth. “We’ve grown faster than we ever imagined,” says Erik. “Now, we’re focused on maintaining a sustainable, manageable size, ensuring we have the resources and personnel to deliver exceptional results.”
With a solid backlog of projects, a reliable fleet bolstered by strong rental partnerships, and an expanding client base, E2 Contracting stands as a testament to the power of teamwork, adaptability, and unwavering commitment to excellence. For more information, please visit www.E2Contracting.net or call their Orange headquarters at (949) 247-DIRT. Cc
The completion of Phase 1 of the State Route 57/60 Confluence Chokepoint Relief Program marks a significant milestone in addressing one of the most congested and hazardous freeway segments in California. The $50 million Diamond Bar Golf Course Renovation Project, initiated on July 16, 2021, and completed on November 30, 2023, represents a decadelong collaborative effort to enhance commuter safety, reduce traffic congestion, and promote sustainability. This extensive project, combining transportation enhancement, environmental stewardship, and public recreation modernization, highlights a decade of collaborative effort and innovation.
The SR 57/60 interchange, located in eastern Los Angeles County at the confluence of Diamond Bar and the City of Industry, has long posed challenges for commuters. Identified by the American Transportation Research Institute as the seventh-worst traffic chokepoint in the United States, the interchange is notorious for its two-mile stretch of severe congestion and hazardous weaving movements.
The project was initiated under Los Angeles County's Measure M Traffic Improvement Plan, which provides funding for critical infrastructure upgrades. Delegated to the San Gabriel Valley Council of Governments (SGVCOG) by the Los Angeles County Metropolitan Transportation Authority (Metro), the program focuses on reducing congestion and enhancing safety. Phase 1, the Diamond Bar Golf Course Renovation, was an essential precursor to the larger freeway-widening initiative.
Landscape Division Manager, Luis Cervantes, has been with Griffith Company for 12 years and served as Project Manager overseeing all aspects of the project. “In return for the land to perform the roadway widening,” Cervantes explained, “the State committed to significant improvements at the Diamond Bar Golf Course. This unique partnership balanced infrastructure upgrades with recreational enhancements for the community.”
The Diamond Bar Golf Course Renovation Project required significant modifications by to accommodate freeway expansion while preserving its reputation as a premier public golf facility. The redesign reduced the golf course’s acreage from 171.3 to 161.9 acres,
with adjustments made to six of the course’s 18 holes (Nos. 1, 2, 3, 8, 9, and 11). These changes preserved the course's par 72 status and maintained its overall yardage of 6,807 yards.
Key components of the renovation included:
• Extensive Grading and Drainage Improvements: Over 300,000 cubic yards of grading were performed, alongside the installation of three biofiltration systems (1,100 square feet each) and a 12,000-square-foot infiltration basin.
• Modernized Utilities and Stormwater Systems: The project involved the installation of over 9,200 linear feet of domestic and fire water lines, 16,000 linear feet of storm drains, and a realignment of 660 linear feet of a 120-inch reinforced concrete pipe.
• Cart Paths and Course Features: A total of 130,000 square feet of new concrete cart paths were installed, along with reconstructed fairways, sand bunkers, tee boxes, and green complexes.
To ensure safety along the freeway-adjacent portions of the course, the project included the installation of 1,500 linear feet of 60- to 100-foot-tall protective netting and poles.
Sustainability was a guiding principle of the project, with numerous innovative strategies employed to reduce its environmental impact:
• Water Conservation: Turf reduction across 33.43 acres allowed for a significant decrease in water consumption, saving approximately 28 million gallons of water annually. The project incorporated droughttolerant ground covers such as mulch in areas previously covered by turf.
• Recycling and Reuse: All green waste, hardscape materials, and netting poles removed during the project were recycled or repurposed.
• Sustainable Bridge Construction: A new cart bridge on Hole 11 was constructed using weathering steel, which naturally resists corrosion and requires minimal maintenance, reducing longterm environmental impacts.
By integrating low-impact development principles, the project enhanced stormwater management through bioswales and native vegetation, fostering an ecologically balanced site. Over 1,000 plants and several mature trees were added to the course, further
Below: Processing and stockpiling crushed miscellaneous base (CMB) for reuse in the construction of cart paths and roads.
contributing to environmental sustainability. “We had a crusher onsite and recycled all of the cart path concrete to create Class II Aggregate Base (CMB) for the maintenance road and new cart paths,” Cervantes noted. “There were several trade subcontractors who greatly contributed to the success of this project. American Landscape, Judge Netting for specialized golf course netting, and Ferreira who performed the Edison infrastructure work. Between Griffith Company and its subcontractors, there were more than 100 individuals working onsite each day, helping to bring the vision to life.”
The project coincided with one of California's wettest years in recent history, which brought extraordinary weather challenges, including 31 atmospheric river storms and Tropical Storm Hilary. These conditions resulted in persistent flooding and soggy terrain.
To address these challenges, the Griffith Company project team developed an innovative water diversion plan. This plan included:
• High-density polyethylene pipes and pumps to redirect water.
• Gravel bags to mitigate erosion and sediment displacement.
• Continuous maintenance and inspections of Best Management Practices (BMPs) to ensure compliance with environmental regulations.
Despite the adverse weather, the project stayed on schedule, a testament to the team’s proactive planning and adaptability.
Collaboration among key stakeholders was central to the project's success. Regular partnering meetings emphasized transparency, professionalism, and respect. This spirit of teamwork allowed the project to overcome challenges and deliver exceptional results, finishing on time and within budget.
One standout innovation was the integration of a water conservation plan that reduced both maintenance { Continued on page 30 }
{ Continued from page 28 }
costs and environmental impacts. These efforts, coordinated with golf course architects, ensured that water savings were achieved without compromising the course’s playability.
Christian Montes was the Senior Project Engineer overseeing the Diamond Bar Golf Course Transformation Project and he highlights the importance of synergy: “The partnership between the contractor, the owner, and the construction manager made this challenging project much more manageable,” Montes said. “The camaraderie and team bonding meant that everyone worked toward the same goal. I worked with the subcontractors and was involved in overseeing the construction of the maintenance building structure. This involved numerous challenges and details, especially for the underground utilities to the building. Subcontractor, J-Squared Contractors, did an incredible job and played a pivotal role in the building construction. We all did our part and worked as a team to deliver the best possible finished project.”
Luis Cervantes echoed this sentiment, emphasizing that teamwork minimized the difficulties often associated with large-scale construction. “In today’s construction environment, everything becomes more challenging without a team atmosphere,” he said. “From the start, we all worked together to reopen the golf course to local and surrounding residents. The project featured innovative solutions like turf reduction, which offered lowrisk, high-reward outcomes that benefited everyone involved while reducing closure time.”
The Diamond Bar Golf Course Renovation Project not only helped to enable critical freeway improvements, the upgraded course now provides a sustainable recreational space for the community. It stands as a model for how public works projects can balance transportation needs with ecological responsibility and community benefit.
As Phase 1 of the broader SR 57/60 Confluence Chokepoint Relief Program, this project sets the stage for continued progress in addressing one of California’s
most pressing transportation challenges. With modernized facilities, reduced water consumption, and enhanced infrastructure, the Diamond Bar Golf Course now serves as a testament to innovative, forward-thinking design that meets the needs of both people and the environment. Completion of this transformative project underscores the power of collaboration, innovation, and a steadfast commitment to excellence in shaping a more sustainable future for Southern California.
“This wasn’t just another project,” Cervantes reflected. “Not every day do you have the opportunity to work on a golf course. Making the course better than it was while helping rehabilitate a freeway made this project special. It was important, especially post-COVID, to reopen this course for the community. We worked as partners with all stakeholders to minimize construction time and maximize community benefits.”
For more information on Griffith Company, please visit www.griffithcompany.net or contact Eric Viado, Business Development Manager, at eviado@griffithcompany.net Cc
and ef ciency in a
with a hybrid excavator designed to reduce fuel consumption while driving performance. When swinging, all available hydraulic power is sent to the boom, arm and bucket for improved cycle time and increased production.
Experience the difference CASE machines make in your construction endeavors.
Our diverse range of equipment is engineered to meet the demands of any project with precision and power.
Digging, Grading, Landscaping, Demolition, CASE manufactures a full line of solutions for commercial and residential.
SONSRAY HAS MACHINES THAT GET THE JOB DONE.
St ow & Go Jib W inc h
Stows in plat for m and requires no as sembly. 50 0 lb. capacit y in all posit ions eliminates gues swork
180 Degree Platform Rotation
Maximizes acces s for each set up.
Heav y Dut y Structural Components
Robust subf rame, t ur ret, bear ing, out r iggers and boom for smoot h r ide and except ionally long usef ul life.
Main Boom Material Handling
2,00 0 lb capacit y for added f unc t ionalit y
• 87’ Wor king height, 7 7’ side reach on 25,999 lb. chas sis
• Mater ial handling on main boom and in wor k plat for m
• 30” x 54” E ZR wor k plat for m wit h 750 lb capacit y
• 180 Degree plat for m rotat ion
• Full lengt h steel subf rame for excellent stabilit y and long chas sis life