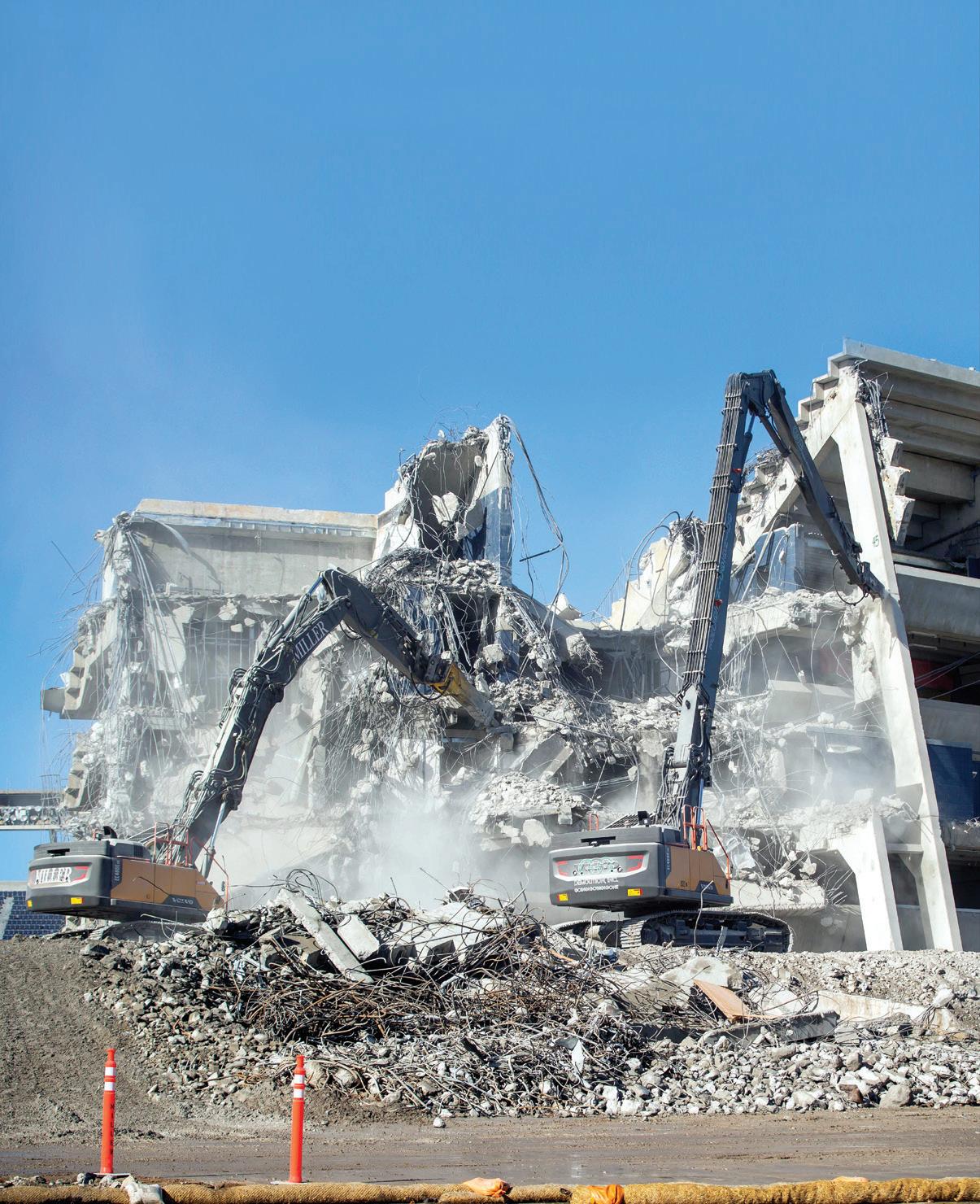
14 minute read
MILLER ENVIRONMENTAL, INC. AND GGG DEMOLITION, INC.
Husband and Wife Team Provide Industry-Leading Full Demolition, Remediation and Recycling Services Throughout Southern California
By Brian Hoover, Senior Editor Photos provided by Miller Environmental, Inc./GGG Demolition, Inc.
Miller Environmental, Inc.
Miller Environmental, Inc. (Miller Environmental) incorporated in 1999 and quickly grew to become a leader in the Southern California demolition and remediation industry. Gregg Miller started Miller Environmental after first going to work straight out of college at the University of North Carolina to work for an asbestos removal firm in Orange. Miller remembers learning all about asbestos remediation as it had just become regulated a few years earlier. After giving the company his all for 10 years, Miller was put into a position to move on and see what he could do with his own demolition and abatement construction business. Miller Environmental’s first job began in 2000 and it has a fascinating backstory. “My first job was a good one where a large national company was proposing to renovate a 10-story office building in Los Angeles,” says Miller. “I still remember walking into the interview when eight impressive gentlemen from a very large demolition company, dressed to the nines, came walking out.” Miller was by himself, and shortly after sitting down, they asked him the million-dollar question. “Looks like you just literally started your company yesterday. Why should we hire you?” Miller presented them with an intelligent proposal and a fair price. The interview must of went well because a few weeks later, Miller was notified that he had been awarded the entire interior soft demolition and asbestos abatement contract.
One steppingstone led to another and soon Miller was bidding his next project, which was even more interesting than the first. This large demolition project was to remove a portion of the Hughes Aircraft plant in Culver City that became known as Playa Vista. “We were selected for the project and moved on to the bonding phase,” says Miller. “I soon learned that the project was over our bonding limit as they told me that I would need to provide collateral if I wanted to move forward.” Undaunted, Miller moved on to another bonding company, and a few days later, he had his $3 million bond. “This job turned out to be very important to our newly formed demolition enterprise, as this single project turned into $35 million of more work over the next eight years,” says Miller. What a learning experience for a new company as the team began to form around this project.
GGG Demolition, Inc.
GGG Demolition, Inc. (GGG) is a fully licensed and insured, certified woman-owned business led by majority owner and company president Celin Miller. As a Woman Business Enterprise (WBE), GGG provides additional benefits to clients with WBE requirements. “I met my wife while she was working for a demolition company in San Diego. One of my buddies called me Triple G because of the three Gs in my first name (Gregg). I always liked the nickname, and so we incorporated GGG Demolition, Inc. as a joke in 2012. Celin was ready to get back into the abatement and demolition business and GGG began officially offering demolition, hazardous waste, and remediation services in 2014 on her first job at Los Angeles City College. GGG focuses on federal, commercial, educational and industrial public works projects.”
Both Miller Environmental and GGG Demolition have been involved in a wide range of construction projects over the past 21 years. These include everything from tenant improvements, hazardous material abatement projects, and the demolition of a long list of structures in various industries to complete plant closures and contaminated soil remediation jobs. Together, both companies have performed more than $1 billion in contracts since their inceptions.
Qualcomm Stadium Demolition – GGG Demolition, Inc.
This landmark stadium has gone by many names over its 53 years of existence. The stadium was officially opened to the public in 1967 under the name San Diego Stadium. From 1981 to 1997, it went by Jack Murphy Stadium, and then the naming rights went to Qualcomm until 2017. San Diego County Credit Union purchased the naming rights in Sept. 2017, and it remained that way until it closed for good in March 2020. Many still refer to the 70,000plus seat structure as Qualcomm Stadium. The 135-acre site it sat on for decades will soon become the home to SDSU’s new Aztec Stadium. Before that stadium could go up, however, the old one had to come down.
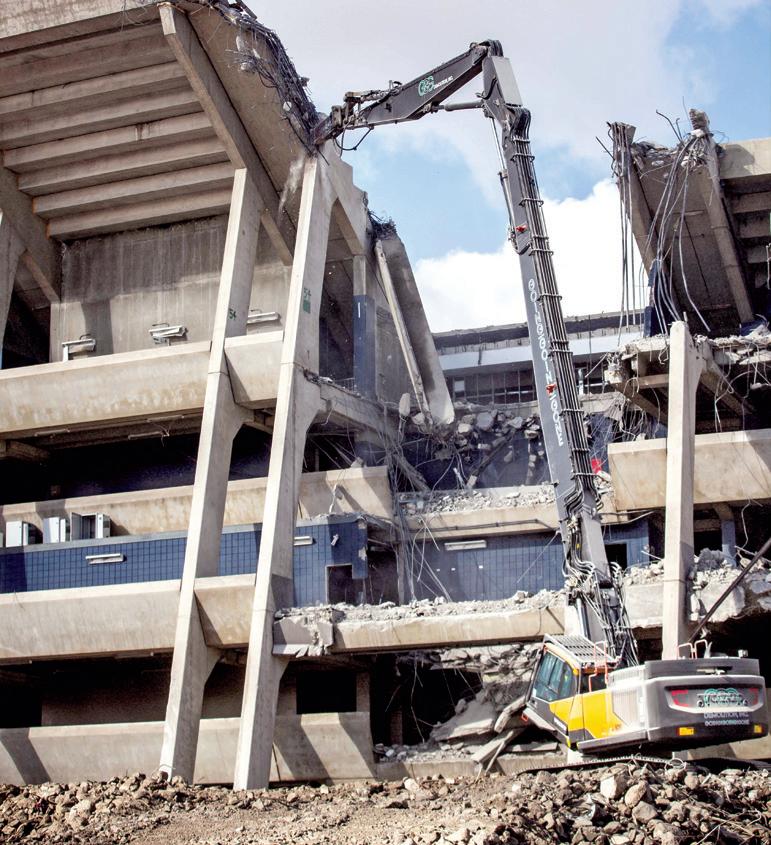
Above: GGG Demolition, Inc. using their Volvo EC490EHR high-reach excavator to bring down Qualcomm Stadium.
Clark Construction has historically performed a great deal of work for San Diego State (SDSU) over the years and they are the prime contractor overseeing the construction of the new SDSU Aztec Stadium. Clark Construction chose GGG Demolition, Inc. to perform all of the abatement, demolition and crushing work on the old stadium structure. Due to COVID-19, the demolition duties were moved up a year and began in Nov. 2020. “We had to make some quick adjustments to meet our client’s needs,” says Miller. “We were given 9-months to complete the job, and we will be just about finished here in July.” GGG’s first phase of work included removing the enormous number of furnishings and fixtures left behind. After this was complete, GGG moved on to the abatement phase, where they removed any small amounts of asbestos and other hazardous materials from the structure. Next came the universal waste removal to include light tubes, ballasts, exit signs, and more. The soft demolition came next, where GGG began removing things like drywall, ceiling tiles, floor coverings, and bathroom fixtures. After all of this was complete, GGG personnel could finally start the structural or hard demolition phase. “We utilized two crews that began working the schedule from the scoreboard inward. Then our Volvo high-reach excavators went to work at the upper-level bleachers to demo from the top down,” continues Miller. “We initially entertained implosion, but regulations and the potential for Air Pollution Control District dust control violations pushed us back into the more conventional methods.”
During the height of hard and soft demolition, GGG had a crew of around 100 onsite and 26 pieces of operated equipment. “We started the hard demo with two Volvo high-reach excavators along with numerous other conventional excavators at the ground level for separating the rebar from the concrete materials. We processed around 210,000 tons of concrete using shears, grapples, processors, and a lot of large 10,000 lb., 12,000 lb. and 15,000 lb. breakers,” says Miller. “We also made use of several off-road trucks, track loaders, and skid steer loaders throughout the jobsite.” According to Miller, the concrete was sized to 2-foot by 2-foot sections and then crushed to 1-inch minus. “We subbed the crushing to Griffith Company, and the final product will be left onsite to be used as fill and base material for future projects like the paving of parking lots during new construction.”
According to Miller, his vice president, Rob Schaefer, personally oversaw all operations on the stadium’s demolition. “Rob moved his life down to San Diego for the entire work weeks, and he and his crews have done an amazing job on this high-profile project,” says Miller. Schaefer points out that his crews started by taking down the most challenging portion of the stadium first. “The 1996 addition to the stadium was located on the eastside by the scoreboard. This area made up around 25% of the entire project area and was very different from the remainder that was originally built in 1967,” says Schaefer. “Building codes were much different in the 60’s and did not call for as much rebar usage. As a result, the new section was full of rebar, and things were slow going at first. However, once we got through this area on each side of the scoreboard, the demo process began to speed up exponentially.”
Miller says that the next big challenge was getting to that highest ring of upper deck bleachers. “We had to create pad benches out of the rubble to put our Volvo high-reach excavators on so that we could reach the highest sections,” continues Miller. “We removed and separated 10,000 tons of rebar, 4,000 tons of steel piles and 180 tons of copper, aluminum and other non-ferrous metals.” Miller says that they surpassed all LEED requirements with an overall recycling percentage of 98%. He also says that most of the rebar was exported to SA Recycling on Terminal Island and the other non-ferrous metals went to other various vendors.
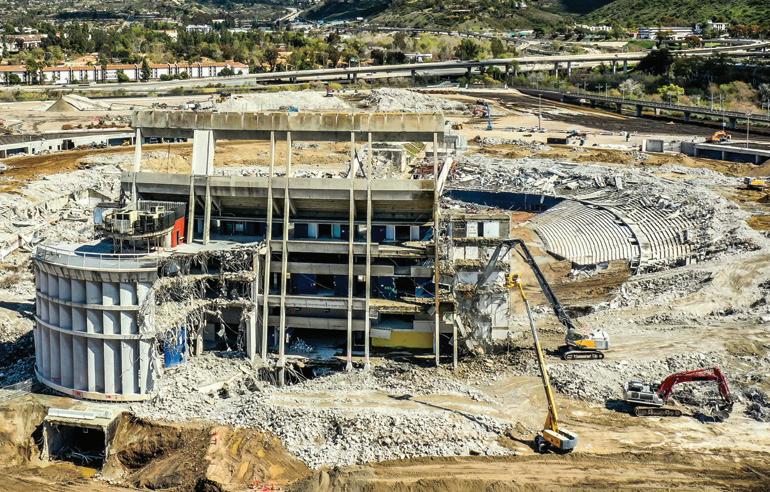
Above: GGG Demolition, Inc. crews complete the demo and processing on the western side of Qualcomm Stadium in San Diego.
Schaefer points to the 1,400 steel piles installed before the stadium’s original construction as another significant challenge and time-consuming phase of demolition. “The initial extraction process for these piles was to use a vibratory rig, and in some cases a crane, to vibrate the beams out of place and then pull them up from the depths. We were able to remove around 400 piles entirely, but 1,000 remained solidified into the sediment layer and could not be excised from the earth,” says Schaefer. “These beams were anywhere from 36 to 100 feet in depth. The owner and general contractor decided to excavate down and torch the beams off at around 46-feet, and then survey them. This was deep enough to not interfere with future construction efforts.”
The Old Riverside Cement Plant – Miller Environmental, Inc.
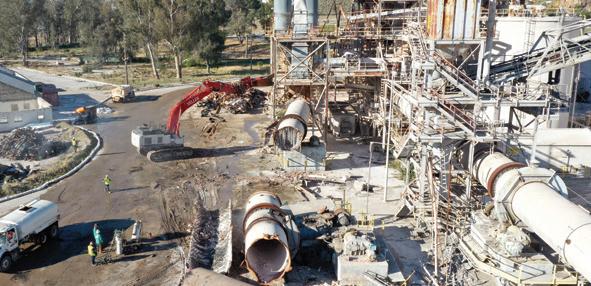
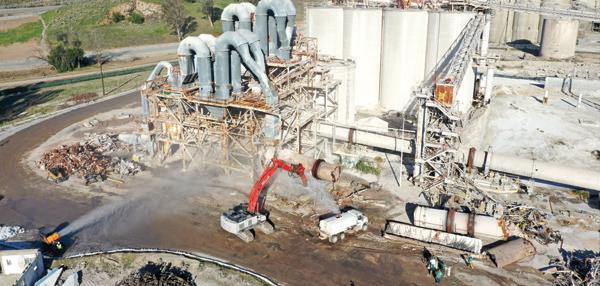
Above : Miller Environmental, Inc. crews demolishing the kiln area at the old Riverside Cement Plant.

ECCO Equipment provided the rentals of a John Deere 470G excavator and a Cat 740B rock truck, which were used for processing and transport.
The former Riverside Cement Plant facility needed to come down to make room for the new Agua Mansa Commerce Park in the City of Jurupa Valley. The site was used previously by Riverside Concrete for cement production and mining until its closing in 2014. Miller Environmental was selected to do the complete abatement and demolition of all onsite structures. This included steel and concrete structures, storage silos, empty tanks, conveyor belts, utility tunnels, a cement bagging building, various cement production lines, and a control center and administration building. Miller began demolition in Jan. 2021 and is scheduled to have everything wrapped up by Oct. 2021, even after a significant delay caused by nesting birds. “The Riverside Cement Plant had been around for 100 years and sat on nearly 200 acres. We are demolishing the complete site so five new buildings can be constructed that will encompass around 4.5 million square feet of warehouse space,” says Miller. “There were also 47 silos, ranging in height from 40 to 130 feet, and more than 30 structures onsite. In all, I think there were around 150,000 sq. ft. of large vertical steel structures.”
Miller says that there were conveyors everywhere, and the Miller Environmental team removed more than 6,000 tons of steel and rebar. In addition, Miller Environmental processed around 200,000 tons of concrete, crushed onsite by subcontractor, North American Recycling and Crushing. “Our professional crews utilized several excavators equipped with breakers and shears, in addition to our Volvo high-reach excavator. We also went to the wrecking ball to remove the numerous silos onsite.,” continues Miller. “There were 50-acres of columns, footings, and drying beds on the north side and massive, 5-footthick retaining walls that were connected to the conveyor system. We also removed more than 2,500 trees and turned the bulk of them into firewood. We are working for prime contractor KPRS Construction on this project, and Berner Leon and his team continue to do an outstanding job.”
LAC+USC Medical Center – GGG Demolition, Inc.
Demolition is now underway at the LAC+USC Medical Center’s Women’s and Children’s Hospital located in East Los Angeles on the USC Medical Center Campus. GGG Demolition began clearing the way for a new health care campus in Jan. 2021. The hospital being demolished is on the campus of the long-running television soap opera General Hospital. It had been vacant for the past 10-years due to not meeting current building codes. The structure required extensive retrofitting, so the decision was made to demo and construct the new Restorative Village Psychiatric Hospital in its place. The job began with GGG performing hazardous substance mitigation, followed by the demolition of approximately 440,000 square feet of hospital space and surrounding vacated structures.

GGG Demolition, Inc. at LAC+USC Medical Center where crews are demoing a 9-story wing on the south side.
According to Miller, the old hospital included two 9-story wings and two 7-story wings. The heavyduty165-foot tall structure also had two levels of underground mechanical and basement, and is said to have been built like a bunker. GGG Demolition started the $11.5 million demolition operation in Jan. 2021, which began with the abatement of asbestos and other hazardous materials. “Most of the soft demolition was already completed through a separate contract. Typically, we would consider doing a project like this as a floor by floor where we crane small excavators up to the top level and bring the structure down, floor by floor. We decided against that approach, in favor of the high-reach excavator, wrecking ball combo,” says Miller. “The penthouse was up at 165’ and we used the old-style wrecking ball to bring down part of that area. This was a safe and efficient alternative, and the client has been pleased with our progress. They have also awarded us additional work across the street that begins next month.”
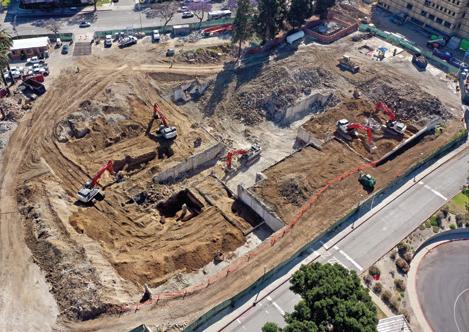
Crews performing foundation demolition at LAC+USC Medical Center.
Miller points out that his 12-person team used six large excavators and one Volvo EC490EHR high-reach machine to bring down and process most of the building. “The client wanted the basement excavation area graded but left open for future building and backfill operations,” says Miller. Dave Anderson is our project manager on this project, and Humberto Garcia is the superintendent. They have done a great job demoing and processing around 41,000 tons of concrete and 3,200 tons of rebar and other metals on this project.
Equipment Fleet and Use of Operated Equipment Rental
Miller Environmental and GGG Demolition share a fleet of more than 100 pieces of heavy equipment. Their combined fleet consists of several dozen excavators, from 4,000 to 180,000 lb. capacities that can be equipped with 40 or so different attachments. They also own and operate 45 skids steers, a track loader, Volvo articulated trucks and Brokk demolition robots. “We used operated equipment rental companies exclusively for several years. It wasn’t until 2007 that we purchased our first two 100,000 lb. excavators. We had them delivered directly to our Cal State Long Beach job where we took down a 3-story, 100,000 square foot classroom building,” says Miller. “We now have our own large fleet of heavy construction machines, but we still utilize operated equipment rental regularly. The issue is often not the equipment, but rather qualified operators to put on our machines. We have enjoyed working with rental companies such as Savala Equipment Rental and recently started renting operated machines from ECCO Equipment.”
Miller explains that they have been so busy over the past year where they had around 54 operating engineers working for them at any given time. “I started working with Vince Castellanos from ECCO Equipment in February. ECCO has been a big help, offering great machines and service at a fair price. Our entire operations team has enjoyed working with the folks at ECCO,” says Miller. “We rented six off-highway trucks from ECCO on the Riverside Cement Plant demolition but used our own operators. We also rented several excavators from 50,000 to 180,000 lb. capacities.” In addition, Miller says that his company also utilized ECCO’s services on the Qualcomm Stadium demolition project. “We rented two rock trucks with operators, five operated excavators and a D8T dozer for a period of time at the peak,” continues Miller. It is all about having the best possible operators and laborers on every job that we take on. Working with operated equipment rental companies like ECCO helps us to accomplish that goal.”
Together, Miller Environmental and GGG Demolition billed $99 million in 2020, making that the best year in the combined companies history. The companies, owners and employees feel very fortunate to have been deemed an essential industry during the COVID-19 pandemic. The husband-and-wife team has quickly risen to become one of the largest and most trusted demolition and environmental firms in all of Southern California. Their full-time staff exceeds 380 team members, as both companies continue to take on the most challenging projects. “I am very proud of our dedicated and experienced team members. Everyone has done such an outstanding job taking us to the top of our industry these past 21 years. I want to thank our office staff, estimators, operators, laborers, mechanics, foremen, superintendents, and everyone at Miller Environmental and GGG Demolition. None of this would have been possible without these individual efforts, and I want them to know that Celin and I both appreciate them very much.” For more information on Miller Environmental, please visit www.millerenvironmental.com or call their Orange headquarters at (714) 385-0099. You may also visit GGG Demolition at www.gggdemo.com or call (714) 699-9350. Cc