
9 minute read
Working Hard and Honoring Family Values are at the Heart of American Wrecking, Inc.
By Brian Hoover, Senior Editor
Photos provided by Tara Garner, Under Construction Photography and American Wrecking, Inc.
Founded in 1961, American Wrecking was later acquired in 1986 by brothers Pepe and Jerry Galaviz. Now in its third generation, American Wrecking has built upon its stellar reputation as specialists in the art of demolition, environmental remediation, asbestos abatement and hazardous material removal. Headquartered in South El Monte, American Wrecking utilizes a fleet of over 100 machines to perform an average of 175 projects each year. The company proudly serves Southern California with a 100% success rate for implosions and a 93% average recycling rate.
Sheila Street Demolition Project – Commerce, CA
Jerry Gutierrez Jr. Gutierrez now serves the 60-year-old construction firm as estimator and project manager. The following is just a quick snapshot of two of the jobs Gutierrez is currently managing for American Wrecking.
American Wrecking began demolition of 5200 Sheila Street in Commerce April 5, 2021. The project started with abatement of the roof penetration and floor tile. The next step was to perform the soft demolition of everything from drywall and partitions to the remaining flooring, bathroom fixtures and other non-structural elements. The project called for the complete demolition and removal of the 104,888 square foot office building, 8,065 square foot cafeteria building and surrounding parking lots. The 5.6- acre site will be redeveloped with a modern one-story, 41-foot tall, 114,898 square foot speculative warehouse building. “Our soft demolition phase included the removal of non-ferrous metals, including 80 to 90-tons of copper and aluminum. We processed another 800-tons of heavy-gauge metal, half of which was rebar,” says Gutierrez. “We crushed all of the 15,800-tons of concrete onsite with a final recycling rate of 94%.”
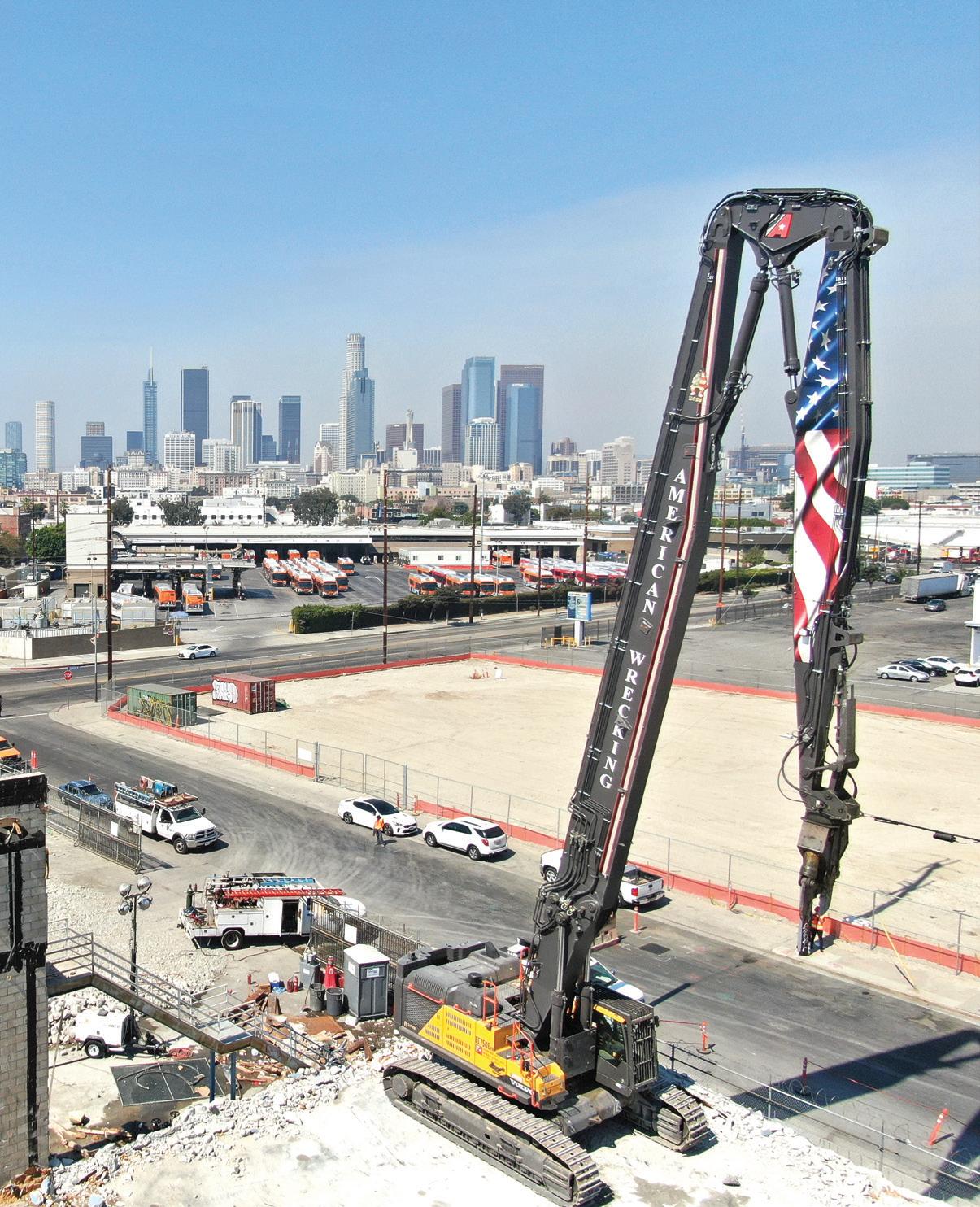
American Wrecking, Inc. performed the demolition of a cold storage facility located at 668 South Alameda Street in the AVA Arts District of Los Angeles.
The structural hard-demolition of the 4-floor structure was made much easier using American Wrecking’s new Volvo EC750EHR Tier 4 Final-compliant high-reach demolition excavator. The Volvo EC750EHR was also equipped with a LaBounty UPX 950 universal processor. “Our crews demoed in 3-bay sections, 40-feet at a time, bringing down the structure one story at a time,” says Gutierrez. “We hit every column on the perimeter of each level, collapsing, lowering, and processing the walls in the process.” In addition to the Volvo EC750EHR, American Wrecking also utilized a Volvo wheel loader and five additional Volvo excavators equipped with munchers, breakers, buckets and grapples. “We used our Volvo EC350E, EC480E, and EC250E excavators to size the concrete to 2-foot-minus sections, before processing to 2-inch-minus with our mobile crushing unit. All of the crushed material was left onsite as fill and base material for future construction,” continues Gutierrez. “All of the demolition was complete by the end of June, and the credit is due to our owner Pepe Galaviz and his crew for a job well done.” According to Gutierrez, American Wrecking also removed the concrete pads and footings to 5 feet below grade. In addition, 2,586-tons of asphalt was also milled off the parking areas and left onsite for future base material.
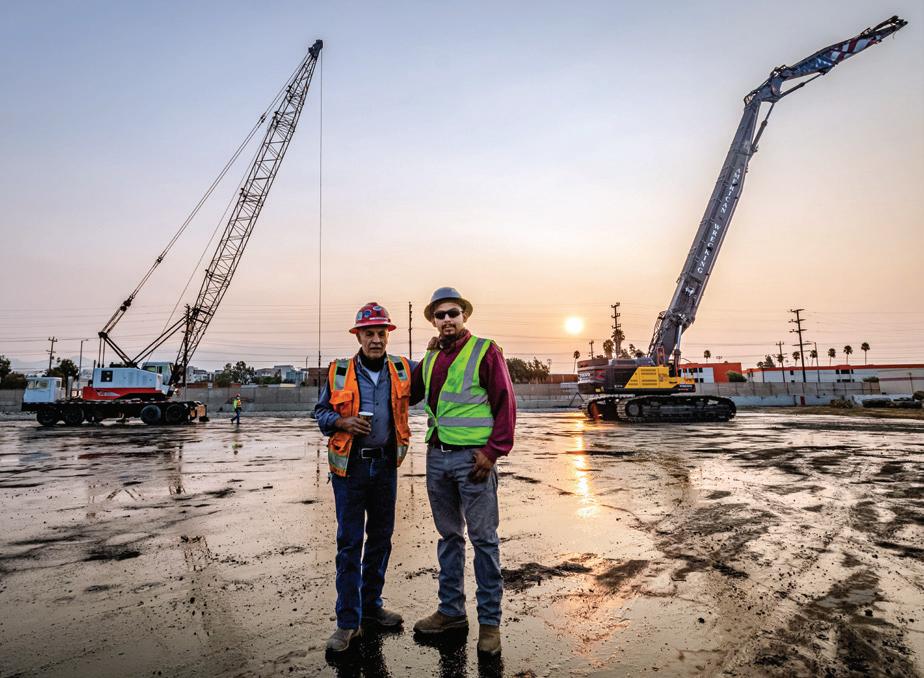
Old school meets new school, as American Wrecking, Inc. owner, Pepe Galaviz (left), stands in front of the type of crane that used to be the only way to perform demo work. Ricardo Arana (foreman), stands in front of a new Volvo EC750EHR highreach excavator, representing the new and improved way to do demo.
Alameda Street Cold Storage Facility Demolition – Los Angeles, CA
Gutierrez was also the project manager for the demolition of a cold storage facility located at 668 South Alameda Street in the AVA Arts District of Los Angeles. The existing 135,000 square foot building was demolished to make room for a new 7-story podiumtype building consisting of 475 live/work units and just under 50,000 square feet of ground-floor retail space. American Wrecking began demolition in Sept. 2020 and completed its work in Dec. “Although this former cold storage facility was only one-story, it also had 57-feet high walls that needed to come down within a minimal footprint. We had Industrial Street on the north side, Alameda on the west side, a restaurant and school on the south side of the property, and other buildings on the east side. Space was limited, and safety was the number one concern on this compact site,” says Gutierrez. “We positioned debris nets in the school and restaurant area and used innovative techniques to bring down the tilt-up structure panel by panel.”

American Wrecking, Inc. used their Volvo EC750EHR high-reach excavator with LaBounty UPX950 universal processor to complete a project at 5200 Sheila Street in Commerce. The project consisted of the demolition and removal of the 104,888 square foot office building, 8,065 square foot cafeteria building and surrounding parking lots.
According to Gutierrez, the job began with asbestos abatement on the roof mastic and some of the tile flooring. American Wrecking then moved on to the soft demolition phase before once again deploying their Volvo EC750EHR high-reach excavator to bring down the 57-foot and 45-foot wall sections. “Half of the work was done at night due to the special measures used to bring down the walls,” says Gutierrez. “We broke the taller walls at the bottom and created holes at the top to attach cables that were used to pull the sections inward. We had our Volvo 350s and 480s on site to pull the walls down and separate and process the concrete panels, footings and slab. We removed 24,200 tons of concrete, 650 tons of metal including rebar and 500 tons of asphalt. We were able to achieve an overall recycling rate of 92%. Even with the space constraints, our crews, led by owner Jerry Galaviz, did another outstanding job.”
Goodman Commerce Center Demolition - Los Angeles
Glenn Bell is the chief estimator and senior project manager at American Wrecking and has been with the company since 1995, working his way up from his initial position as a $5 an hour intern. Glenn meets and listens to the client’s needs and advises them on available value engineering methods. Bell then manages the work from that point to completion. Bell was the project manager on the Goodman Commerce Center (GCC LA) project at 4841 West San Fernando Road in Los Angeles. “We started this three-phase demolition and rehabilitation project in April 2020, and after remobilizing at least 10 times, we finished our portion of the work in September,” says Bell. “The first phase was to completely gut Building 1, which had previously been used as a distribution center for a well-known grocery store chain. We started by doing the soft demolition, which required removing vast amounts of racking and then basically stripped down the interior to just four walls and a roof. Next, we cut openings for the new rollup doors and sawcut and removed slabs to make room for new elevators and stairs.”
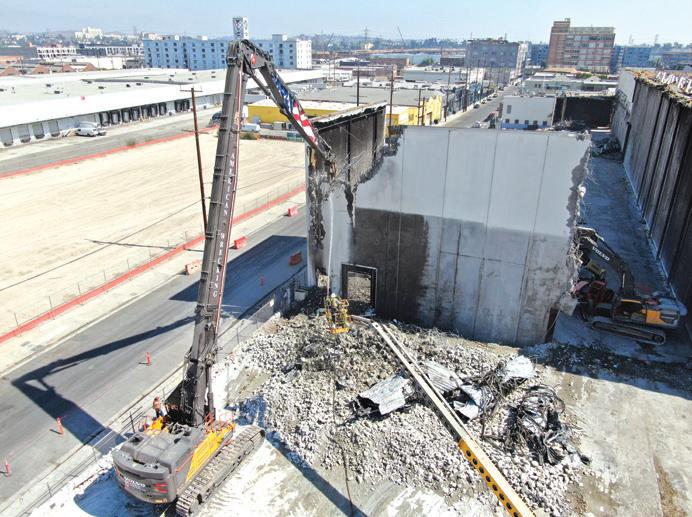
American Wrecking, Inc. uses their Volvo EC750EHR high-reach excavator for the demolition of the Alameda Street cold storage facility in Los Angeles.
Bell points out that Phase 2 was the real meat and potatoes of the project. “We were contracted to remove around 250,000 square feet of a 102-feet-tall rack supported structure and loading dock system. The entire section was built with a specialized racking system with a roof and unique skin on the outside,” says Bell. “This 5,000-ton, tube steel, rack supported structure is one of many built back in the 80s but represented the first time our company had ever brought one down.” According to Bell, this particular rack-supported structure was more extensive and taller than other similar buildings. “At the time of bidding on this project, there was not a high-reach excavator available that could reach 102 feet in height. We were prepared to use hand wrecking methods where we would cut the roof open and use cables to pull over each section of racking,” continues Bell. “However, we decided instead to make a huge capital investment in the new Volvo EC750EHR high-reach demolition excavator that had just become available. The EC750 is the largest production, high-reach excavator available in North America right now, and we accepted delivery just as we were starting this project.”
Bell says that the contract required American Wrecking to deliver the site’s north end in 65 working days. “Meeting the tight schedule was a challenge but our crew, led by foreman, Ricardo Arana, did an exceptional job under pressure,” says Bell. “At the project’s height, we had two foremen working separate portions of the job, along with eight heavy equipment operators and 10 laborers. In all, we demoed and crushed 65,000 tons of concrete to 1-inch minus. We achieved a 97% recycling rate and left the crushed material onsite for future construction use.” Bell says that they performed minimal abatement of floor tile and drywall joint compound. We also removed and recycled steel, reusable lumber and non-ferrous metals like aluminum and a substantial amount of copper. American Wrecking maintained the salvage rights on this project, where the scrap value represented a portion of their pay. “We took a gamble and decided not to sell the copper right away, which turned out to be a smart decision. Copper prices are up almost 100% from this time last year, and we still have not yet sold,” continues Bell. “On the flip side, steel prices went down significantly at the beginning of this project but came back up to acceptable levels before the end of the job.”

Above & Below: American Wrecking, Inc. uses their Volvo EC750EHR high-reach excavator on a three-phase demolition project at the Goodman Commerce Center located at 4841 West San Fernando Road in Los Angeles.
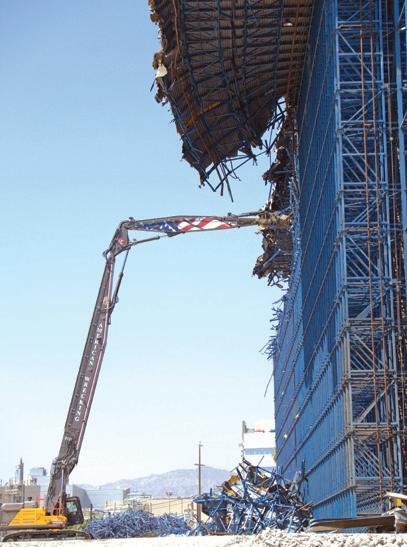
After the entire rack-supported structure was brought down, American Wrecking moved on to the third phase, where they went after the sturdy foundation. “Most buildings have perimeter footings and column foundations. The weight is distributed differently on this particular type of structure and because of this, the building had a mat foundation,” says Bell. “So, a 40-foot band of concrete going inward included 36 inches of double mat rebar, while the center was 30-inches thick with a single mat rebar.” Bell explains that they attacked the mat foundation with their 1967 Lima conventional crane, equipped with an 8,000pound wrecking ball. “We used the crane to lift the wrecking ball to 25 or 35 feet and just let it freefall. This weakened the mat by creating fissures or cracks so that the excavators could come in and segregate the rebar from the concrete, minimizing the use of hydraulic hammers,” continues Bell.
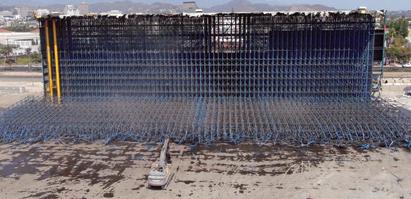
According to Bell, the eastern side of the building was right up against San Fernando Boulevard with high voltage lines only 10 feet away. “We do all the necessary planning with our engineers and follow the plan, but always anticipate potential safety risks. The last section of racking was not as stable, and it was difficult to keep it standing on its own,” says Bell. “We cut the racking at 90-feet, tied six and a quarter-inch cables to these sections, and used six of our excavators to pull them inward, away from the high-voltage lines.” Bell also points out that there was lots of torching going on, particularly at the bottom of the racking system so it would pull over easier. “95% of the work was done with our Volvo EC750 high-reach excavator. We used this amazing demolition machine to trim the roof section back to create access to what I refer to as the next slice of bread or section of support racking,” continues Bell. “We are phasing out our other units as they reach the end of their lifecycle in favor of Volvo machines. Volvo is putting out a great product. They got smart about the way they manufactured their demolition machines. We had to armor our units, upgrade the pumps, and install new hydraulic lines in the past. Volvo went after the demolition market with excavators that are ready to go right off the production line, saving us both time and money.”
Working hard and honoring family are at the heart of American Wrecking. Now in its 60th year, the company has more than 100 employees, including several family members. For more information on American Wrecking, visit www.americawreckinginc.com or call their South El Monte headquarters at (626) 350-8303. Cc