
7 minute read
RAMCO – Where the Highest Standards of Safety, Quality, Service and Integrity Ensure Total Customer Satisfaction
By Brian Hoover, Senior Editor Photos provided by Dallas Jones and CMS
Recycled Aggregate Materials Company, Inc. (RAMCO) is a third-generation family-owned leader in the construction materials recycling industry. For nearly 75 years, RAMCO has supplied quality and competitively priced recycled aggregate materials to the Southern California construction marketplace. Founder, Ralph Newman started in 1947 operating Newman & Sons, Inc., one of the largest and most successful grading and paving enterprises in greater Los Angeles. Ralph’s son, Dennis, eventually took over the reins of the business and began pursuing his interest in recycled concrete and asphalt. Although the Newman family still maintains their paving and grading license, they made the move to the aggregate recycling and production business in 1976.

Above: Ramco’s Rialto facility provides 24/7 dump and material services. They offer many different recycled aggregate materials for the construction industry, as well as concrete slurry recycling.
RAMCO is now led by third generation family member President and CEO, Ken Newman. With Ken at the helm, the company has soared to new heights and continues to meet and exceed tonnage goals with each passing year. On average, the company will recycle close to 1-million tons of material each year through its four facilities in Sun Valley, Rialto, Beaumont, and Escondido. They receive their concrete, asphalt and other materials from contractors and agencies like Caltrans, City of L.A., and a small percentage from homeowners. The demoed material comes into RAMCO yards from several types of jobsites, including the removal of curbs, gutters, concrete foundations, patios, sidewalks, and concrete pools, to entire buildings, highways, bridges, roads and airports. RAMCO crushes and sizes the material into several road base product offerings, including Class 2, CMB, PMB, Class 3, RCA #3 (1” minus), RCA #4 (3/8” rock), RCA 3” Minus Rock, and Fill Sand. RAMCO also offers Concrete Slurry Water Recycling services. They use a filter press to take slurry water and produce a filtrate completely free of suspended solids. The water is then used onsite for dust control, while the cement solids are turned into a very low-moisture cake that is added into the recycled aggregate products.
Dallas Jones is the vice president of operations at RAMCO, and he oversees all four aggregate facilities from the company’s headquarters in Simi Valley. “This business is somewhat of a balancing act where we are consistently managing how much material is coming into our facilities versus how much we are selling,” says Jones. “Space constraints at some locations are also a daily concern. There is only so much space, and I can tell you it is never big enough. As removals are coming in and product is going out, one pile may be bigger than another. The balancing act is with keeping the flow going at all times and not running out or having too much material on one end or the other.”
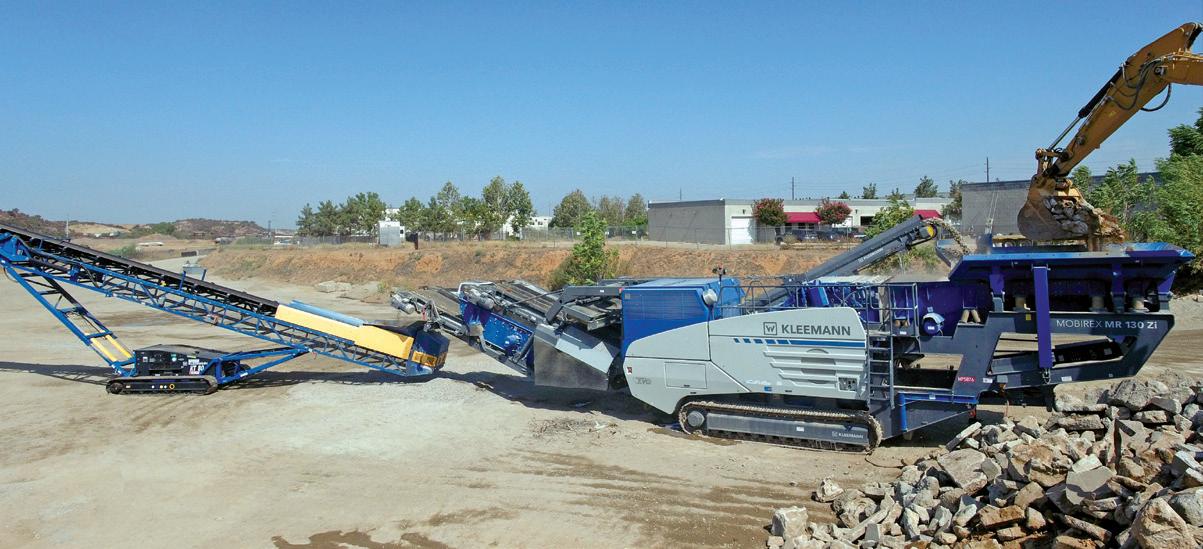
Above: Ramco’s new Kleemann MR 130i EVO 2 mobile impact crusher with KT80 stacker can be deployed universally as an all-rounder and produces first-class final grain quality.
According to Jones, RAMCO’s high-quality product and tremendous emphasis on excellent customer service set them apart. “We get them in and back out to their jobsite as quickly and safely as possible. No one likes to wait around to get loaded and we are ever respectful of our customer’s time and bottom line. From dispatch and billing to loading and unloading services, our clients know they can always expect the same, prompt, friendly, professional service.”
Dump trucks, ten-wheelers, roll-offs, and trailers constantly enter through RAMCO’s gates to unload their asphalt and concrete. RAMCO also accepts sand and rebar for an additional charge. Crushing huge chunks of concrete and asphalt requires robust and durable equipment, and RAMCO relies on only the highest quality heavy equipment at their recycling facilities. Mike Anselmo is the general manager of the Rialto location, where they take in more than 250,000 tons of material every year. “As our volume continued to increase, we found ourselves in the market for a new mobile crusher that we could move between facilities to keep the process moving smoothly,” says Anselmo. “We looked at several makes and models and finally decided to go with the Kleemann MR 130i EVO 2 mobile impact crusher.”
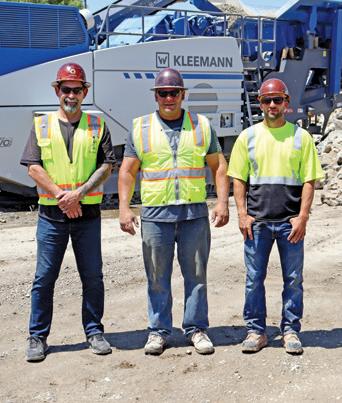
Dallas Jones, VP of Operations (left), Mike Anselmo, General Manager and Darrel Bourghs, Utility Operator.
Anselmo was afforded the incredible opportunity of touring the Wirtgen America manufacturing facility in Nashville, where Kleemann crushers and other Wirtgen Group products are assembled. “I was impressed with just how many Kleemann machines they had in stock, ready for delivery. I was fortunate to meet one of the senior mechanics, and he gave me an indepth inside tour,” continues Anselmo. “I got a closeup and personal look at the cones and the jaws as they were breaking down the machines. I was just so impressed with the heavy-duty quality of every component and the innovative details that go into these amazing crushing units.”
RAMCO utilizes crushers, conveyors, screening equipment, and heavy construction machines to keep the manufacturing process moving forward. Every RAMCO location has at least two Cat (988 or 980) wheel loaders to load the material into the hoppers, move it into piles, and then load out trucks as they enter the facility. “We run 24/7 here in Rialto, and that means that our equipment sees an extraordinary amount of use. We demoed and took a close look at several different units, and the Kleemann was the best built machine,” says Anselmo. “The setup and maintenance are so much easier than other machines. It is just extremely easy to use, and things like changing out bearings or changing screens can be done with ease, compared to the tight access problems that some of the other manufactures seem to have.”
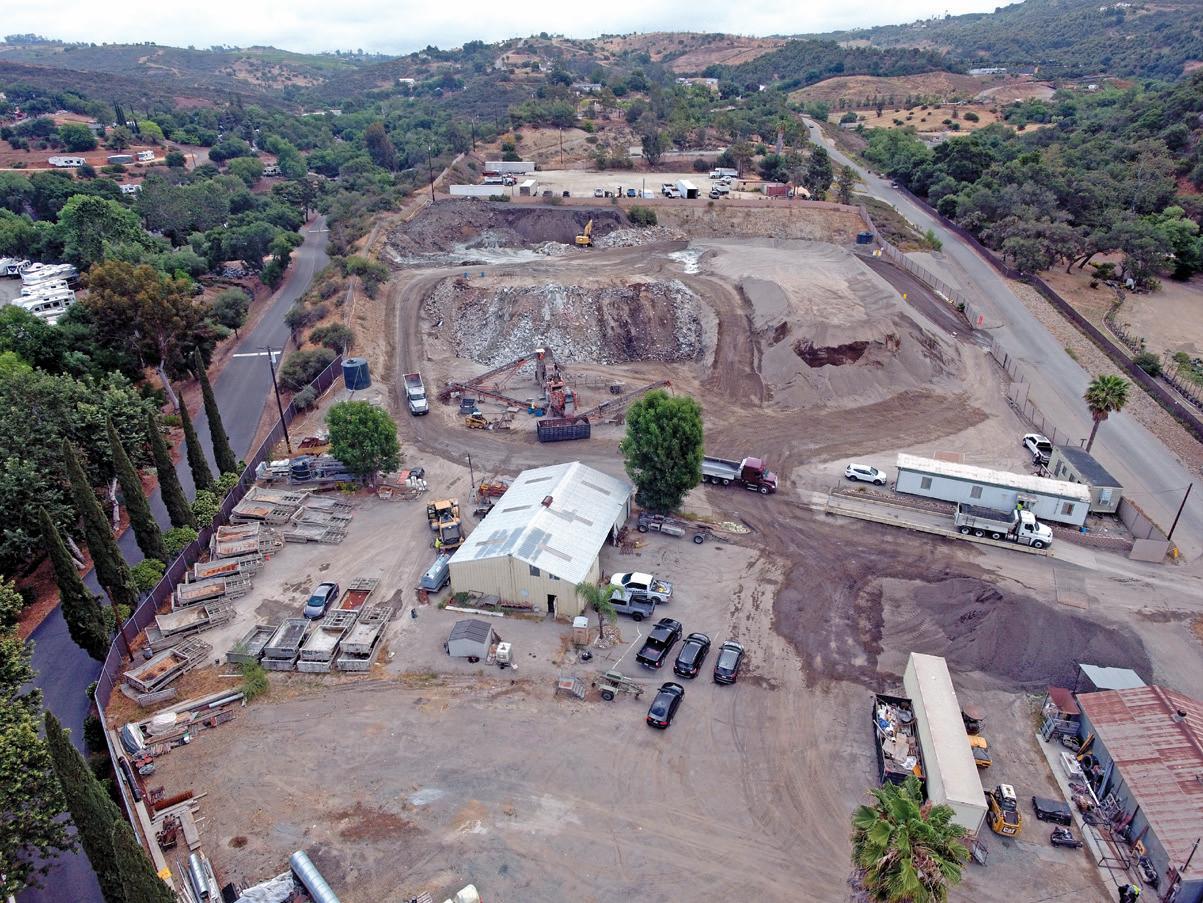
Ramco Escondido prides itself on being #1 in customer service, quality and core principles.
VP of Operations, Dallas Jones, is also very impressed with the Kleemann product line. “Kleemann is a new addition to our crusher capabilities, and it will surely help us grow as we utilize it in several new areas. The MR 130i is a portable unit and puts out more than I have witnessed with other portable crushing plants of the size,” says Jones. “I have to say that I am impressed with the volume our new Kleemann puts out as a portable machine. We will use it to float between locations where it is needed most and would like to add another Kleemann crusher to our fleet soon.”
RAMCO purchased their Kleemann MOBIREX MR 130i EVO2 impact crusher from NixonEgli Equipment Co. Jones explains the decision-making process in more detail. “Chris Doring (a representative from Nixon-Egli) came around a while back and took the time to introduce me to the entire Kleemann line of products. I remember thinking that a Kleemann crusher would be nice to add to our fleet someday,” says Jones. “Well that day finally arrived as we met with our new Nixon-Egli representative, Shari Sendejo, who was extremely knowledgeable and knew the product line inside and out. This was our first purchase from Nixon-Egli, but when the time comes to expand our operations even further, Kleemann and Nixon-Egli will be a big part of that transition.”
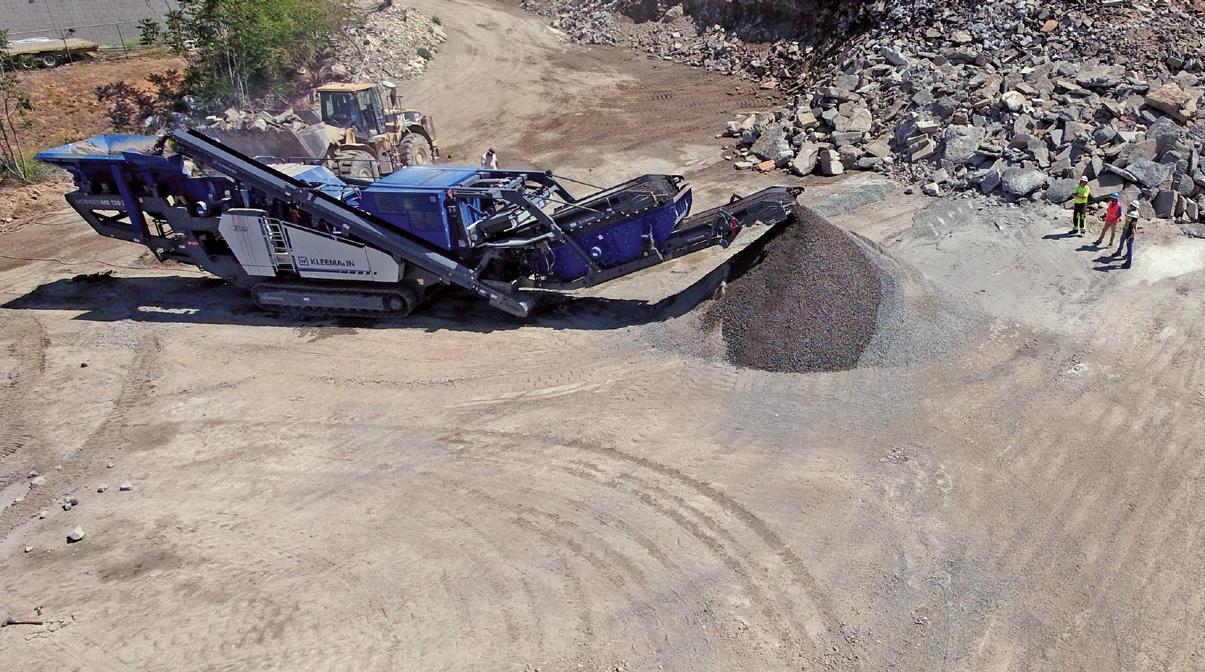
Above & Below: Ramco’s new Kleemann MR 130i EVO 2 mobile impact crusher includes a high-performance secondary screening unit and innovative c-shape rotor ledges. Ramco is impressed with the volume the new Kleemann puts out as a portable machine. It will float between facilities for now.
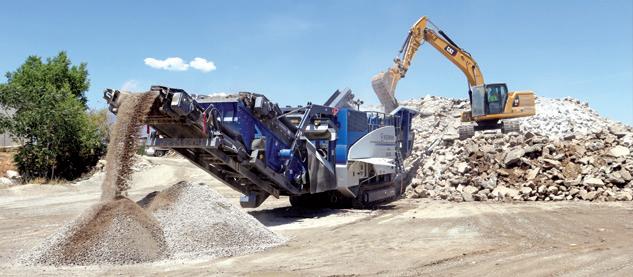
Jones and Anselmo both agree that purchasing a Kleemann crusher is a lot like buying an elite high-end vehicle. “The best is always a little more expensive, but as they say, “you get what you pay for,” continues Jones. “Nixon-Egli arranged for speedy and seamless delivery, and we put our new Kleemann crusher to work right away. We immediately noticed how great it was to have the continuous feed system. We also appreciate the large feeding unit, the double-deck prescreen, and the SPECTIVE control system that is so simple and intuitive to operate.” Other exceptional features of the Kleemann MR 130i EVO 2 mobile impact crusher include a high-performance secondary screening unit and innovative c-shape rotor ledges. The Kleemann also has a turning device for simple and safe rotor positioning, a return conveyor for closed material circuit, in addition to fast and simple Quick Track operating mode, and a crusher inlet width of 1300 mm.
Kleemann manufactures mobile jaw crushers, cone crushers, impact crushers, screening plants and stockpile conveyors. For information on any of the Kleemann products, please visit www.nixonegli.com or call their Kleemann specialist, Shari Sendejo, at (909) 938-1021.
For more information on RAMCO and their recycled aggregate materials, visit www.ramco.us.com or call their Simi Valley headquarters at (805) 522-1646. Cc