
31 minute read
SEL 017A Workplace Bullying,& Harassment Policy
WORKPLACE BULLYING & HARASSMENT POLICY
Document Identification SEL 017A Page Number 1 of 1
Document Creation Date June 1, 2010 Implementation Date June 1, 2010
POLICY
Every employee is entitled to employment free of harassment. The management of Belterra Corporation is committed to making every reasonable practicable effort to ensure that no worker is subjected to harassment.
This policy applies to all Belterra employees, including permanent, temporary or casual employees, as well as independent contractors. This policy applies wherever Belterra’s business or work-related activities are conducted (including washrooms, lunchrooms, or company vehicles), and includes work-related social functions, conferences and training, and work assignments outside of Belterra’s premises. This policy also applies to conduct by employees outside of the workplace when one or more of Belterra’s employees are the target of bullying and harassment (i.e. cyber-bullying).
Bullying and harassment is defined as including but not limited to:
any inappropriate conduct, comment, display, action or gesture by a person that: is made on the basis of race, creed, religion, color, sex, sexual orientation, marital status, family status, disability, physical size or weight, age, nationality, ancestry or place of origin; or adversely affects the worker’s psychological or physical well-being and that the person knows or ought reasonably to know would cause a worker to be humiliated or intimidated (sometimes referred to as personal harassment); and constitutes a threat to the health or safety of the worker.
Sexual harassment, which is conduct, comment, gesture or contact of a sexual nature that is offensive, unsolicited or unwelcome, is also prohibited.
Bullying and harassment excludes any reasonable action taken by an employer or supervisor relating to the management and direction of workers or the place of employment Employees must: not engage in the bullying and harassment of other employees, in person or on social media/email; report if bullying and harassment is observed or experienced; and comply with Belterra’s policies and procedures on bullying and harassment
There is a Workplace Violence, Bullying & Harassment Program that implements this policy. It includes a process for workers to report incidents, or raise concerns, and information about how incidents and complaints will be investigated and/or dealt with. Any employee or independent contractor who engages in workplace bullying and harassment shall be subject to discipline, up to and including termination of employment or contract.
The Company’s Workplace Bullying & Harassment Policy will be reviewed every year.

June 30 - 2017
-----------------------------------------Janice Stasiuk – Chief Executive Officer -------------------DATE

WORKPLACE VIOLENCE, BULLYING & HARASSMENT PROGRAM
Document Identification SEL 017B Page Number 1 of 7
Document Creation Date January 1, 2013 Implementation Date July 1, 2012
1.0 PURPOSE
Belterra Corporation is committed to a work environment that is free of violence, bullying and harassment, and one in which all individuals are treated with respect and dignity. This Workplace Violence, Bullying and Harassment Program has been established to provide a clear statement on
(a) the definition of workplace violence, and what does and what does not constitute bullying and harassment
(b) roles and responsibilities of Belterra’s supervisors and employees in addressing and preventing workplace violence, bullying and harassment,
(c) the process for reporting violence, bullying and harassment; and
(d) the process for responding to and investigating reports of violence, bullying and harassment.
2.0 DEFINITIONS
2.1 WORKPLACE VIOLENCE
Workplace violence is defined as: the exercise of physical force by a person against a worker, in a workplace, that causes or could cause physical injury to the worker; an attempt to exercise physical force against a worker, in a workplace, that could cause physical injury to a worker; a statement or behavior that is reasonable for a worker to interpret as a threat to exercise physical force against the worker, in a workplace, that could cause physical injury to the worker.
2.2 BULLYING AND HARASSMENT
Bullying and harassment is defined as including but not limited to: (a) any inappropriate conduct or comment by a person towards a worker that the person knew or reasonably ought to have known would cause that worker to be humiliated or intimidated, but (b) excluding any reasonable action taken by an employer or supervisor relating to the management and direction of workers or the place of employment.
Document Creation Date January 1, 2013 Page Number 2 of 7 Implementation Date July 1, 2012
Examples of bullying and harassment include, but are not limited to:
o verbal aggression (including yelling and insults) o personal attacks, name calling o harmful hazing or initiation practices o vandalizing personal belongings o spreading malicious rumors o other intimidating or humiliating behavior Workplace bullying and harassment usually consists of repeated incidents or a pattern of behavior that is intended to intimidate, offend, belittle or humiliate a particular person or group of people. Lack of intent is not an excuse if the bully ought to have known the behavior would cause the victim to be humiliated or intimidated. Bullying and harassment can also consist of a single traumatic incident
Workplace bullying and harassment does not include the exercise of management rights to assign additional work, to hold employees accountable for their performance through performance improvement or corrective action plans, and impose justifiable discipline. Also, not every instance of workplace conflict or differences of opinion is bullying and harassment.
2.3 SEXUAL HARASSMENT
Workplace harassment also includes sexual harassment. Sexual harassment is defined to mean any "unwelcome conduct of a sexual nature that detrimentally affects the work environment or leads to adverse job related consequences for the victims of the harassment. By requiring an employee, male or female, to contend with unwelcome sexual actions or explicit sexual demands, sexual harassment in the workplace attacks the dignity and self-respect of the victim both as an employee and as a human being."
2.4 COMPLAINANT
The Complainant is the individual making a complaint of violence, bullying and/or harassment against another individual who the Complainant believes has engaged in, or is currently engaging in, violent, and/or bullying and harassing behaviors against the Complainant.
2.5 RESPONDENT
The Respondent is the individual that the Complainant has made a complaint against.
Document Creation Date January 1, 2013 Page Number 3 of 7 Implementation Date July 1, 2012
3.0 WORKPLACE VIOLENCE RISK ASSESMENTS
Belterra employees perform a number of activities that may increase the risk of workplace violence. These include: o Use of a vehicle (mobile workplace) o Working alone or with just a few people o Working late at night or early in the morning o Working in remote or unknown areas
Belterra Corp. proactively assesses the risk of workplace violence in all workplace environments and will re-assess as often as necessary to protect employees from workplace violence. Assessments for workplaces include the nature of the workplace, the type of work or the conditions of work.
4.0 PROCEDURES TO CONTROL RISKS OF WORKPLACE VIOLENCE
4.1 COMMUNICATION DEVICES, TELEPHONE, OR PORTABLE CELL PHONE
Your workplace may include a land-line telephone, portable cell phone or other mobile device that is used to communicate. You must be familiar with the communications system available and ensure that you know the number to call for emergency assistance.
5.0 PROCEDURES WHEN VIOLENCE IS IMMINENT OR IN PROGRESS
5.1 WHEN A VIOLENT SITUATION OCCURS OR IS IMMINENT
Call 911 for emergency situations. Police or emergency responders will assist immediately. Call your immediate manager or supervisor if feasible after calling 911. If you are at risk, remain calm, try to withdraw from the violent individual and seek an immediate safe location.
Any violent actions committed by Belterra employees, employees of the client, or members of the public will be prosecuted under the Criminal Code of Canada or as appropriate. Belterra intends to use reasonable legal, managerial, administrative, and disciplinary procedures to secure the workplace from violence and to reasonably protect employees and members of the public.
Document Creation Date January 1, 2013 Page Number 4 of 7 Implementation Date July 1, 2012
6.0 VIOLENCE, BULLYING AND HARASSMENT REPORTING PROCEDURE
6.1 WHAT TO DO IF YOU OBSERVE, OR BELIEVE YOU ARE THE VICTIM OF VIOLENCE, BULLYING AND HARASSMENT
If you believe that you are the victim of violence, bullying and/or harassment, including sexual harassment, the first thing you should do is tell the person to stop. Do so as soon as you receive any unwelcome comments or conduct. If violence is imminent or in progress, please follow section 5.0 Procedures When Violence is Imminent or in Progress. Some of the things you can say that might stop the behavior include: o “Please stop doing or saying…” o “It makes me uncomfortable when you…” o “I don’t find it funny when you…” If your attempts to stop the behavior have not been successful and/or if you fear reprisal, then you should report the incident(s).
Employees who become aware of situations where violence, bullying and harassment may be occurring should report the suspected violence, bullying and harassment.
6.2 HOW TO REPORT ALLEGED OR SUSPECTED VIOLENCE, BULLYING AND HARASSMENT
Reports of alleged or suspected violence, bullying and harassment may be made verbally or in writing using the Workplace Violence, Bullying and Harassment Complaint Form (FRM 038). Belterra expects that workers will keep written accounts of incidents to submit with any complaints; the written accounts must include a description of the incident(s), where and when the incident(s) occurred, the persons involved and the names of witnesses, if any. You will be asked to provide any other evidence or information that you believe are relevant to the complaint, such as emails, handwritten notes, text messages, and photographs, if available.
Reports should be made to the employee’s immediate supervisor or manager. If the immediate supervisor or manager is alleged to be involved in the bullying and harassment, then reports can be made to the employee’s RVP, or to the Human
Resources Department located at the Corporate Head Office. If you make a complaint in good faith and without malice, regardless of the outcome of the investigation, you will not be subject to any form of discipline. Belterra Corp. will, however, discipline or terminate anyone who brings forward a false and malicious complaint.
Document Creation Date January 1, 2013 Page Number 5 of 7 Implementation Date July 1, 2012
Any employee who retaliates against someone who has made a complaint in good faith is subject to disciplinary action up to and including dismissal.
6.3 CONFIDENTIALITY
All reports of complaints will be handled in a confidential manner. Information concerning a complaint, or action taken as a result of the investigation, will only be released as necessary to conduct a proper investigation, to take disciplinary measures, or where required by law.
7.0 BULLYING AND HARASSMENT INVESTIGATION PROCEDURE
7.1 WHEN AND HOW INVESTIGATIONS WILL BE CONDUCTED
All complaints and reports of alleged violence, bullying and harassment will be assessed thoroughly and an investigation will be conducted if deemed necessary. Most investigations will be conducted internally, however in complex or sensitive situations, an external investigator may be hired. The investigation process will involve interviews of the Complainant, the Respondent and any witnesses named by either. If the Complainant and the Respondent agree on what happened in the incident, the Company will not investigate further and will determine what corrective action to take, if necessary.
Investigations will be: o undertaken promptly and diligently; o focused on finding facts and evidence, including interviews of the Complainant, Respondent and any witnesses; o sensitive to the interests of all parties involved; and o fair and impartial.
The investigation will include: o interviewing the Complainant and the Respondent to ascertain all of the facts and circumstances relevant to the complaint, including dates and locations; o interviewing witnesses, if any; o reviewing any related documentation and evidence; o making detailed notes of the investigation and maintaining them in a confidential file. Once the investigation is complete, a report of the investigation results will be kept on record and a summary of the findings will be provided to the Complainant and Respondent.
Document Creation Date January 1, 2013 Page Number 6 of 7 Implementation Date July 1, 2012
7.2 EMPLOYEE ROLES AND RESPONSBILITIES
All employees are expected to report suspected violence, bullying and harassment and to cooperate with those responsible for investigating any complaints. Belterra has a responsibility to prevent any violence, bullying and harassment in the Workplace therefore if any supervisor or manager fails to report incidents of violence, bullying and harassment, or fails to take appropriate corrective action, he or she will be subject to disciplinary action, up to and including termination.
7.3 FOLLOW-UP
The Complainant and Respondent will be advised of the findings of the investigation within a reasonable timeframe. Belterra will keep a written record of investigations, including the findings. Regardless of the outcome of any violence, bullying and harassment complaint made in good faith, the employee lodging a complaint or reporting suspected violence, bullying and harassment, as well as anyone providing information regarding the complaint, will be protected from any form of retaliation by either co-workers or supervisors.
8.0 CORRECTIVE MEASURES
If disciplinary actions are deemed necessary, they will be taken within a reasonable timeframe, however the nature or details of the disciplinary actions will not be shared with the Complainant or anyone else unauthorized to receive the information due to the confidential nature of disciplinary actions.
Management will determine what action should be taken as a result of the investigation and inform the Complainant and Respondent of the findings of the investigation; based on the outcome of the investigation, the following corrective measures will be taken, if necessary: o disciplinary action, up to and including termination; o referral for counseling, anger management training or attendance at educational programs on workplace respect;
If there is not enough evidence to substantiate the complaint, corrective measures will not be taken.
9.0 TRAINING
All managers, supervisors, and employees are required to take violence, bullying and harassment prevention training.
Document Creation Date January 1, 2013 Page Number 7 of 7 Implementation Date July 1, 2012
The training will include workplace violence, bullying and harassment prevention strategies including complaint resolution, listening and communications skills, identifying problematic behavior characteristics, anger management and any other topics that may be deemed necessary. New employees will take part in mandatory internal violence, bullying and harassment training as part of their orientation. Re-fresher training will be required on an annual basis.

Document Identification SEL 018 Page Number 1 of 19
Document Creation Date January 1, 2013 Implementation Date January 1, 2013
1.0 PURPOSE
The purpose of this program is to ensure the protection of all Belterra employees from the hazards associated with confined space energy. This document contains requirements for practices and procedures to protect employees from those hazards of entry into, and work within permit required confined spaces.
It is the policy of Belterra Corporation to reduce the need for confined space entry, and to eliminate whenever possible, all confined space hazards. When confined space entry is necessary, all provisions of the Confined Space Entry Program must be followed. Belterra Corporation does not have Confined Space’s in any one of their branches. Our workers however come into contact with confined spaces when performing tasks at customer sites. For all Confined space entry/entries at a customer site, employees must follow customer specific Confined Space Entry Program(s).
Belterra’s SEL 018 will only be utilized when there are no customer-specific Confined Space Entry Programs available. The program requirements must then be carried out under the supervision of a trained, certified, experienced and competent Safety officer
2.0 SCOPE
The Confined Space Entry Work Standard applies to all Belterra employees who manage, specify, design, work in, and /or carry out emergency rescues in confined space.
3.0 DEFINITION OF A CONFINED SPACE
A confined space means a space that: is large enough and so configured that an employee can bodily enter and perform assigned work; has limited or restricted means for entry or exit; and Is not designed for continuous human occupancy. Examples of confined spaces include but are not limited to storage tanks, process vessels, bins, silos, boilers, ventilation or exhaust ducts, sewers, pipe chassis, underground utility vaults, tunnels, and pipelines.
A permit-required confined space means a confined space that either: contains or has the potential to contain a hazardous atmosphere, contains a material that has the potential for engulfing an entrant, has an internal configuration such that an entrant could be trapped or asphyxiated by inwardly converging walls or by a floor which slopes downward and tapers to a smaller cross-section, or Contains any other serious safety or health hazard.
Document Identification SEL 018 Page Number Document Creation Date January 1, 2013 Implementation Date on Revised
Document
April 26 2016
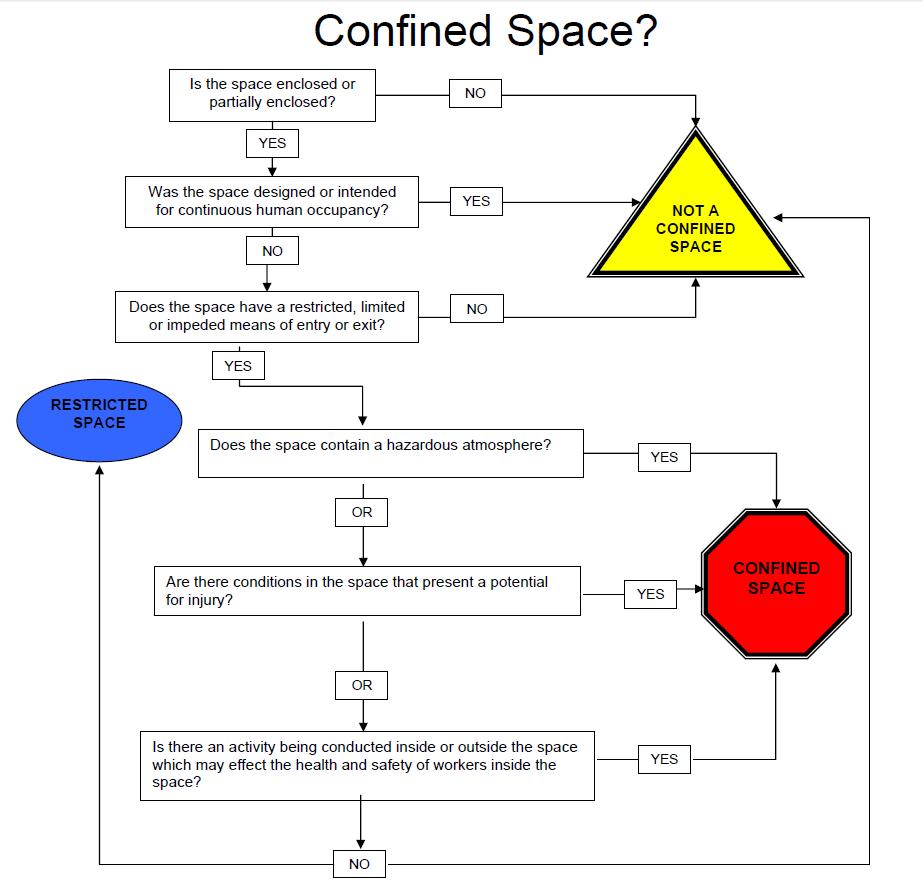
Document Identification SEL 018 Page Number Document Creation Date January 1, 2013 Implementation Date on Revised
Document
April 26 2016
4.0 DEFINITIONS
Barricade – A physical obstruction created with tapes, screens or cones to warn of and limit access to a hazardous area.
Confined Space Code of Practice – A written set of procedures developed to eliminate or control the hazards anticipated in a confined space entry.
Entry – Any action that breaks the plane of the confined space (i.e., complete or partial entry, such as entry of only the employee’s head).
Hazardous Atmosphere – An atmosphere that is oxygen-deficient and/or contains explosive gases or toxic contaminants in a concentration that may exceed permissible exposure limits.
Hot Work – Any work involving the use of a flame or a potential source of ignition, including:
• Cutting, welding, burning, air gouging, riveting, heat shrinking, drilling, grinding, chipping, working with explosive actuated tools; • The use of non-classified electrical equipment; • The introduction of a combustion engine to a work process; and • Any other work where a flame is used or sparks are produced.
LEL (lower explosive limit) – The minimum concentration of gas, vapour or dust (or any combination of these) in air at ambient temperatures at which flame propagation will occur in the presence of a source of ignition. Monitoring – Continuous or periodic testing of an atmosphere in a confined space.
OEL (occupational exposure limit) – The maximum airborne concentration of substances that workers may be exposed to for specific lengths of time, as defined by the Alberta Occupational Health and Safety Code.
Rescue – The process of a person or persons removing an employee from a hazardous environment while protecting their own safety and notifying authorities of an emergency situation.
STEL (short term exposure limit) – The maximum concentration of substances that workers may be exposed to for 15 minutes continuously
Tending Worker – Employee(s) required to stand by, outside a confined space and remain in constant communication with employee(s) inside the confined space.
Testing – Atmospheric inspection of a confined space before entry by means of approved visual, sensory or instrument monitoring.
Document Identification SEL 018 Page Number Document Creation Date January 1, 2013 Implementation Date on Revised
Document
April 26 2016
TWA (time-weighted average) – The time-weighted average concentration of substances that workers may be exposed to in a normal eight-hour workday
Vault – An enclosure above or below the ground which employees may enter for the purposes of installing, constructing, operating or maintaining electrical equipment or cable(s).
Ventilation – The circulation or exhaust of air into or out of a confined space with sufficient flow to remove fumes, vapours or other toxic contaminants. Mechanical ventilation refers to the process of forcing fresh air into the confined space while work is being carried out.
5.0 RESPONSIBILITIES
5.1 Managers Responsibilities The manager is responsible to: Make sure the Confined Space Code of Practice (Section 7.0) and an Entry Permit system is in place for each confined space; Ensure that the supervisor and the lead hands are appropriately trained and educated to enter and carry out their responsibilities of overlooking the Confined Spaces.
5.2 Supervisors Responsibilities The supervisor is responsible to: Make sure the worker-in-charge reviews the Confined Space Code of Practice for each confined space, working with other employees, contractors (at all customer sites), and our customers in its review; Ensure that a hazard assessment is completed and the Code of Practice meets the requirements. Ensure that all employees required to enter a confined space have received training specific to the type of confined space they will enter; When required, contract with knowledgeable third party to provide confined space entry and emergency response services; Provide all equipment necessary for confined space entry; Maintain all records of confined space entry for three years.
5.3 Worker– In – Charge Responsibilities The Worker-In-Charge (WIC) is responsible to: Review the Confined Space Code of Practice and make sure all requirements are met before work begins; Develop and review the Entry Permit (Appendix A); Identify any required changes to the Confined Space Code of Practice, and /or inabilities to manage the hazards identified, and postpone work until the revisions have been completed and approved by the supervisor; Prior to entry, communicate the Confined Space Code of Practice and Entry to all employees and post the Entry Permit at the main entrance to the confined space.
Document Identification SEL 018 Page Number Document Creation Date January 1, 2013 Implementation Date on Revised
Document
5.4 Workers Responsibilities: Workers may enter a confined space only if they: Have completed confined space entry training; Wear a rescue harness; and Comply with the Confined Space Code of Practice and Entry Permit. April 26 2016
6.0 ENTRY PERMIT
6.1 Completing the Entry Permit: An Entry Permit must be completed before any employee can enter a confined space. It must: Identify the confined space and the purpose of entry; Specify the time period for which it is valid; Verify that all entry requirements have been met.
6.2 Verifying Entry Requirements: The Confined Space Code of Practice and Entry Permit must be reviewed and accessible at the work site prior to entry to verify that all requirements have been met.
If changes are required to the Code of Practice due to site conditions or for any other reason, entry is not
permitted.
The Code of Practice must be updated by the WIC before proceeding.
All written records relating to confined space entry must be retained for at least three years.
7.0 CONFINED SPACE CODE OF PRACTICE
7.1 Scope: This Code of Practice applies to all Belterra Employees for entry into all confined spaces.
7.2 Responsibilities: All employees participating in the confined space entry are required to become familiar with and understand this Code of Practice.
The Worker-In-Charge (WIC) is required to review this Code of Practice and the Entry Permit prior to entry into the confined space.
7.3 Hazard Identification: Written work procedures, based on the Hazard Assessment, must be created for all confined spaces that require entry. Thee work procedures must specify the means to eliminate or minimize the hazards
Document Creation Date January 1, 2013 Implementation Date on Revised
Document
April 26 2016
outlined in the hazard assessment including those that could be created by the work being performed in the space.
The written procedures must be prepared by a qualified person and must address, where applicable:
Identification and entry permits, Lockout and isolation, Verification and testing, Cleaning, purging, venting or inerting, Ventilation, Standby persons, Rescue, Lifelines, harnesses and lifting equipment, Personal protective equipment and other precautions, and Coordination of work activities.
Work procedures must be updated upon any changes to the Hazard Assessment.
Complete the Confined Space hazards Assessment Work Sheet as per Appendix B.
The following table identifies the types of hazards that may be encountered during a confined space entry. Refer to the barriers and ensure they are in place prior to entry.
HAZARD BARRIER(S)
Difficult Access or Egress Wear full body harness with tag line on D-ring. Ensure sufficient length of tag line. Have rescue equipment available, such as tripod, rope blocks with anchor point (i.e. boom truck) Ensure employees are trained in rescue techniques and confined space entry. Have third person on site as part of the rescue team; Complete Entry Permit Atmospheric Hazards Where atmospheric hazards are suspected (e.g., LEL, CO, H2S, O2), use an approved four-head monitor to sample air conditions (see Appendix C). Attach a sample pump to the monitor to ensure accuracy. Use ventilation equipment as indicated by the test results. Test periodically, as required. Record readings on the Entry Permit. Identify any other atmospheric hazards on the Entry Permit. Ensure employees are trained to use the monitors and equipment Dust and Biological Hazards Assess if the confined space needs to be cleaned prior to entry. Wear appropriate respiratory protection and personal protective equipment. Use cleaning solutions to wet and dilute the contaminated area. Electrical System Isolate and ground if required. Maintain Limits of Approach. Follow Lock Out/Tag Out (LO/TO) Work Standard. – SEL 039 and SWP 010 Include topic in tool box meeting
Sharp Objects
Extreme Temperatures (Hot and Cold)
Welding, Cutting, Grinding (Fumes and Gases)
Gravity Fall from heights Falling objects
Vehicle Fumes
Traffic Hazards Wear appropriate gloves or personal protective equipment.
Follow Safety Standards –SEL 006 for personal protective equipment, warm clothing, proper nutrition, etc.
Wear a respirator as required. Follow procedures from SEL 006 Complete a detailed tool box meeting
Wear a harness. Keep the work area clean (i.e., housekeeping). Use barricades to prevent the public from entering the work area.
Shut off vehicles in the immediate area.
Use barricades/signs as required. Include in the tool box meeting
7.4 Training: The Worker-in-Charge must ensure that all employees participating in the confined space entry have appropriate training as following: Recognition and identification of potential hazards associated with the confined spaces that will be entered. Evaluation and control procedures for the identified or potential hazards. All equipment such as ventilation equipment (blowers), harnesses and air quality monitors (e.g. Oxygen / combustible meters) that will be used while in the confined space. All personal protective equipment (e.g. respirators0 that the worker will be using while in the confined space. All procedures for entering the confined space as outlined in the Hazard Assessment and Work Procedures. Procedures to follow in the event of a situation developing that could present additional risk to the worker or an emergency. The specific work to be done while in the confined space.
7.5 Entry Permit System: Before work begins, the WIC must develop a Confined Space Entry Permit that identifies any sitespecific conditions or hazards outside the scope of this Code of Practice.
The conditions identified on the Entry Permit must be reviewed and signed to indicate understanding by all individuals prior to entry.
7.6 Personal Protective Equipment Requirements: Follow CHSM – SEL 006 in regards to the selection and use of personal protective equipment.
7.7 Hazardous Atmosphere Testing: Test all existing vaults prior to entry. New construction requires testing only when a hazardous atmosphere is suspected (e.g., oil/gas facility).
Use an approved four-head monitor to sample air conditions.
Document Creation Date January 1, 2013 Implementation Date on Revised
Document
April 26 2016
Test the atmosphere prior to entry. Record the test results on the Entry Permit. Periodic testing may be required in some confined spaces, as determined at the site, and must be included on the Entry Permit and tool box meeting.
If exposures above Occupational Health and Safety limits (OEL) are encountered, immediately exit the area. In consultation with the supervisor, identify the source of the hazard and determine a method to eliminate or reduce the hazard prior to re-entry.
7.8 Ventilation: If a hazardous atmosphere is detected or is likely to exist, the confined space must be ventilated and air conditions re-tested before entry. If purging is necessary, external resources can provide the knowledge and equipment required for safe entry.
7.9 Communication: Have a second employee on-site to maintain ongoing communication with an employee entering a confined space.
Utilize handheld radios when entering confined spaces where voice audibility may be reduced.
7.10 Emergency Response Plan:
It is the responsibility of the branch manager or the safety officer to ensure that an emergency response plan has been developed (or exits) by a qualified and competent individual at a customer site, prior to entering the confined space in case there’s an accident or other emergency. The rescue plan must include provisions for –on-site rescue procedures or safe work procedures to address rescue.
The plan should include procedures in place to evacuate the confined or restricted area immediately in the following circumstanced:
When an alarm is activated; If the concentration of oxygen inside the confined space drops below 19.5% by volume or exceeds 23% by volume; or If there is a significant change in the amount of hazardous substances inside the confined space.
The rescue plan must be tested to ensure quick rescue of all workers performing work in a confined space. It must cover the necessary rescue equipment, team of rescuers, evacuation plan, alarms and communications, PPE, safety harnesses and lifelines, first aid kit and equipment and recovery equipment.
8.0 GAS DETECTION EQUIPMENT (MONITOR) STANDARDS
8.1 Bump test : A bump test is required each day, before use of the monitor. A bump test involves applying a known concentration of calibration gas to the monitor, according to the manufacturer’s recommendations.
Document Identification SEL 018 Page Number Document Creation Date January 1, 2013 Implementation Date on Revised
Document
April 26 2016
If the monitor responds appropriately, the bump test is complete. The bump test tells the user only that the monitor is responding as it should.
8.2 Calibration: Calibration involves applying specific amounts of calibration gas to the monitor to adjust the sensors, so they read properly according to the set-points.
Calibration should also be done whenever a bump test fails.
The set-points are previously configured by the factory. All of the set-points match provincial OHS as there is no ceiling exposure limit for CO, the high alarm set-point should remain at 200 ppm.
Note: LEL is read in % LEL mode rather than as percentage of total air volume. % LEL is safer and preferred.
9.0 ATMOSPHERIC HAZARDS IN CONFINED SPACE
Atmospheric hazards in a confined space are those that expose entrants to a risk such as death, entrapment, injury, or acute illness from one or more of the following causes:
9.1 Oxygen: An atmospheric oxygen concentration below 19.5 (oxygen deficiency), or above 23.5 (oxygen enrichment)

Document Identification SEL 018 Page Number Document Creation Date January 1, 2013 Implementation Date on Revised
Document
April 26 2016
9.2 Combustible Gases: A flammable gas or vapor in excess of 10% of its lower explosive limit (LEL) yet still remaining below the upper explosive limit (UEL).
9.3 Toxic Gases: An atmospheric concentration of any toxic compound above the permissible exposure limit established by NIOSH or ACGIH is classified as Toxic Gas. Examples of common toxic gases found in a confined space.

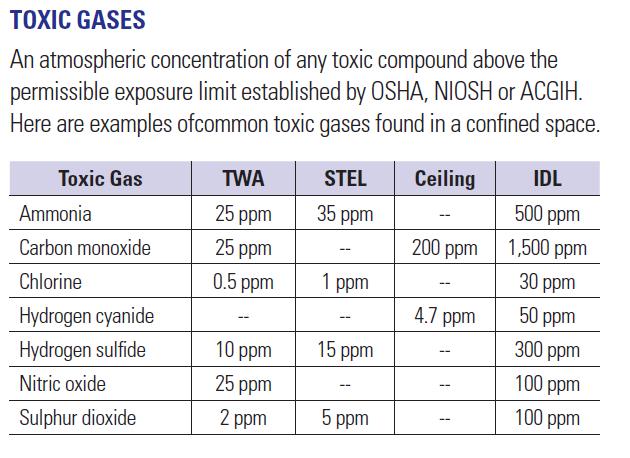
Document Identification SEL 018 Page Number Document Creation Date January 1, 2013 Implementation Date on Revised
Document
April 26 2016
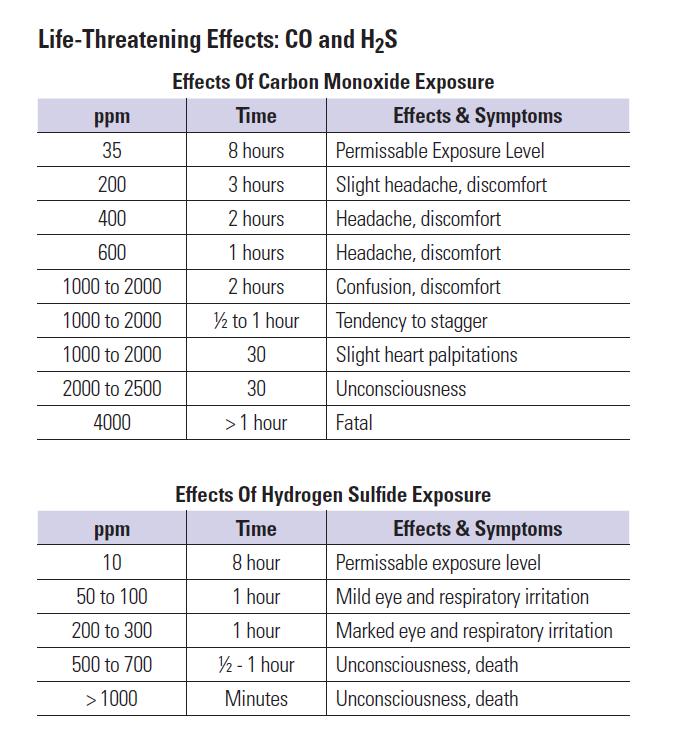
Document Identification SEL 018 Page Number Document Creation Date January 1, 2013 Implementation Date on Revised
Document
April 26 2016
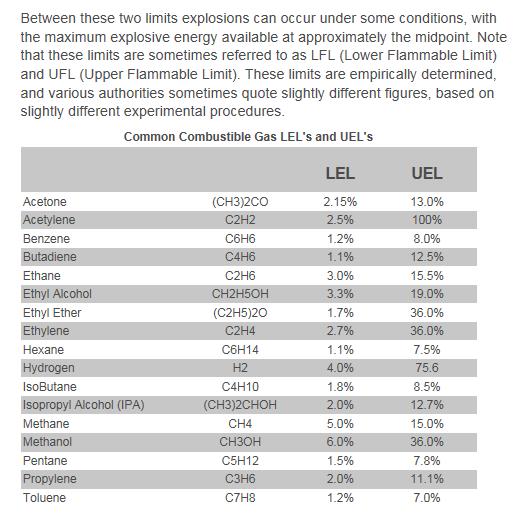
10.0 DOCUMENTATION
All documentation that is related to the training and instruction must be maintained for a minimum of 3 years. All confined space hazard assessments and work procedures will be maintained at branch level by the safety representatives for a minimum of 3 years following the creation of updated documents.
11.0 PROGRAM REVIEW
The Confined Space Entry Program must be reviewed annually for the following: The effectiveness of the program as it applies to ensuring employees and contractor safety Document control.
The annual review will be done in consultation with the Joint Occupational Health & Safety Committee with a minimum of 5 branch committee members participating in the review process.
Document Identification SEL 018 Page Number Document Creation Date January 1, 2013 Implementation Date on Revised
Document
12.0 APPENDIX A: CONFINED SPACE ENTRY PERMIT FORM
April 26 2016
CONFINED SPACE ENTRY PERMIT Permit Number:
Location and Description of Confined Space(s) Purpose of Entry: Date of Entry:
Scheduled Start Date:
Scheduled Time of Entry: AM PM
Worker(s) in charge of entry (Entrants) Scheduled End Date:
Scheduled Time of Exit: AM PM
Attendants:
Pre-Entry Authorization (Check those items below which are applicable to your confined space entry permit)
�� Oxygen-Deficient Atmosphere �� Oxygen-Enriched Atmosphere �� Welding/cutting �� Flammable Atmosphere �� Toxic Atmosphere �� Engulfment �� Energized Electric Equipment �� Entrapment �� Hazardous Chemical
Safety Precautions
�� Self-Contained Breathing Apparatus ��Ventilation �� Protective Gloves �� Air-Line Respirator �� Line-lines �� Respirators �� Flame Resistant Clothing �� Fire Extinguishers ��Barricade Job Area �� Lockout / Tagout ��Signs Posted ��Clearance Secured ��Lighting ��Ground Fault Interrupter
Environmental Conditions
Tests To Be Taken Date / Time Oxygen % Lower Explosive Limit % Toxic Atmosphere Instruments Used Worker conducting safety checks signature: Re-Testing Oxygen % Lower Explosive Limit % Toxic Atmosphere Instruments Used Date / Time
Remarks on the overall condition of the confined space
�� ENTRY AUTHORIZATION - All actions and / or conditions for safe entry have been performed
Person in charge of the entry: _____________________________________________________(Please Print)
�� ENTRY CANCELLATION – Entry has been completed and all entrants have left the space.
Person in charge of the entry: _____________________________________________________(Please Print)
Document Identification SEL 018 Page Number Document Creation Date January 1, 2013 Implementation Date on Revised
Document
April 26 2016
13.0 APPENDIX B: CONFINED SPACE HAZARD ASSESSMENT WORKSHEET
Location Of Work: CONFINED SPACE HAZARD ASSESSMENT WORK SHEET
Description of Tasks To Be Carried Out:
Entry Date:
Atmospheric Hazards
Explosive atmosphere (gases, vapors, fine dusts)
Oxygen deficiency
Oxygen enrichment
Toxic gases or vapors
Dusts, mists, fumes
Smoke
Biological agents
Other
If yes to 1 or more of the above, specify atmospheric hazards
Yes No
Document Identification SEL 018 Page Number Document Creation Date January 1, 2013 Implementation Date on Revised
Document
Safety Hazards
Exit / Entry: Small / narrow openings Steep openings Entry / Exit at height Angled openings Exits into traffic or machinery Machinery / mechanical equipment Piping and distribution systems Residual chemicals or materials Pressure systems Electrical hazards Poor visibility Physical obstacles Walking and working surfaces Temperature extremes Heat stress Cold stress Humidity Noise Vibration Radiation Type: Other Type:
Work Related Hazards
Hot Work Type: Sandblasting Bond Operations Grinding Cutting Use of solvents, corrosive chemicals or cleaners Use of paint / spray painting Repairs If yes, describe
Installation If yes, describe: Inspection If yes, describe Emergency rescue procedures / first aid Other Type:
Human Factors
Comments: April 26 2016
Yes No
Yes No
Document Identification SEL 018 Page Number Document Creation Date January 1, 2013 Implementation Date on Revised
Document
April 26 2016
14.0 APPENDIX C – CODE OF PRACTICE WORK SHEET
Date: Company Name:
Work Site: Confined Space Identification Number:
Confined Space Location:
Code of Practice Prepared By (Name & Designation): Telephone Number:
Description of Confined Space
Tasks to be Completed in the Confined Space:
Description of Hazards:
Atmospheric:
Safety:
Work Procedures:
Human Factors:
Worker Training Requirements
How many workers are required to complete the work:
Describe worker training requirements / courses:
Entry Permit: (Attach Sample Form)
Work Procedures:
Testing the atmosphere: Test for:
Equipment:
Document Identification SEL 018 Page Number Document Creation Date January 1, 2013 Implementation Date on Revised
Document
Equipment calibration:
Task Frequency: Before Entry:
After Entry:
Other:
Entry Into Confined Space: Who is authorized to enter?
Entry / Exit Procedures:
April 26 2016
List of Required Tools and Equipment
Required Personal Protective Equipment
Description of PPE Respiratory Protective Equipment Yes No Type
Protective Clothing
Footwear
Head wear
Protective Eyewear
Gloves
Other:
If other, describe:
Document Creation Date January 1, 2013 Implementation Date on Revised
Document
April 26 2016
Traffic Hazards
Are there any traffic hazards related to this confined space entry Yes No
If yes, describe controls:
Ventilation, Purging, Inerting, isolation
VENTILATION: If yes, describe procedures to be used.
PURGING: If yes, describe procedures to be used.
INERTING: If yes, describe procedures to be used. Yes No
Yes No
Yes No
ISOLATION: If yes, describe procedures to be used. Yes No
Tending Worker
Is a tending worker required to be physically present? Yes No If no, who has the responsibility to be in communication with the workers in the confined space? What are the duties of the tending worker(s)? What actions do the tending worker(s) take in an emergency? Describe communication procedures:
Document Identification SEL 018 Page Number Document Creation Date January 1, 2013 Implementation Date on Revised
Document
Emergency Response Procedures:
Emergency Contact Numbers:
Describe emergency procedures:
List of rescue equipment (include personal protective equipment for rescue workers)
Required training and recordkeeping procedures: April 26 2016
Record Keeping
Code of Practice Reviewed By:
Code of Practice update Frequency:
When is the confined space entry done?
What is the frequency of entering this confined space entry: Describe incidents that have occurred in connection with this confined space entry:
Has emergency rescue been required during an entry?
Actions taken to prevent future incidents:
Other comments: