
37 minute read
SEL 019 Obsolete as of April 8th 2016 (Temporary Work Platform
Document Identification Document Creation Date
SEL 019
January 1, 2013 Page Number 1 of 1
Implementation Date
January 1, 2013
Document Obsolete as of April 8th 2016.

WORKING AT HEIGHTS & LADDER SAFETY
Document Identification SEL 020 Page Number 1 of 10
Document Creation Date May 2, 2015 Implementation Date on Revised Document May 15, 2015
1.0 INTRODUCTION
1.1 SCOPE
This document establishes the safe work practices to be followed while working in elevated areas and aerial platforms. It shall be adhered to by all employees including contractors who work, or who could potentially be working at heights and elevated areas at / for Belterra
1.2 PURPOSE
This procedure is intended to protect Belterra employees from the hazards of working at heights and prevent injuries.
2.0 POLICY
It is the policy of Belterra Corporation to provide a safe work environment for all employees while working in aerial environments. As part of this policy, no one will be required or permitted at any time to expose him/herself to elevated areas without some form of required protection or the strict adherence to approved work procedures.
3.0 DEFINITION
Aerial Platform: workplace that is located mid-air or is airborne in nature.
4.0 RESPONSIBILITIES
4.1 BRANCH MANAGERS
It is the responsibility of the branch manager to ensure that the appropriate standards are put into practice and are being adhered to. The branch manager must ensure that all protective equipment is available and utilized in the prescribed manner.
The branch manager shall ensure that all fall protection equipment including ladders meet the regulatory requirements including CSA standards
4.2 SUPERVISORS/SAFETY OFFICERS/DESIGNATE
Supervisors /Safety Officers or designates must be familiar with all aspects of the Working at Heights Standards. Before workers are allowed into a location where a risk of falling exists, the supervisor / safety officer/designate must discuss the appropriate fall protection plan for the job. They will ensure
Document Identification SEL 018 Page Number Document Creation Date January 1, 2013 Implementation Date on Revised
Document
May 15, 2015
4.3 WORKERS
Employees have the responsibility to ensure that they are adhering to the safe work practices. Employees must not work under hazardous conditions and that attention is being paid to each details including protective equipment.
5.0 SAFETY PRACTICES
5.1 IDENTIFYING FALL PROTECTION REQUIREMENTS
Supervisors / safety officers or designate will ensure that a fall protection system is used when work is being performed in these hazardous situations: From which 3 metres (10 feet) or more may occur, including when working off a ladder or; Where a fall from a lesser height may result in an unusual risk of injury; for e.g. from a fall when working over operating machinery.
The supervisor must identify : The fall hazard expected in each work area; The fall protection method to be used in each area; The correct method to assemble, maintain, inspect, use, and disassemble the fall protection system; and Rescue procedures from elevated work areas.
The choice of fall protection should depend on the practicability of using it to the hazards it creates.
A Job Hazard Analysis to identify the hazards and mitigation plans must be conducted and established for areas identified as posing potential falling from height risks prior to conducting any Working at Height jobs.
5.2 FALL PROTECTION
All fall protection systems shall confirm to appropriate WCB regulations or be certified by a professional engineer.
5.2.1 FALL RESTRAINT
Fall restraint normally means a fall protection system arranged such that a worker cannot fall lower than the surface on which the worker was supported before the fall started. For example, a personal fall restraint system for a worker on a elevated flat surface would be arranged so the worker could go up to the edge of the work surface, but not beyond the edge in the event of a slip or fall. The system, in the
Document Identification SEL 020 Page Number Document Creation Date May 2, 2015 Implementation Date on Revised
Document
May 15, 2015
event of a slip or fall, would result in the worker landing on the work surface and not going over the edge.
When practicable for the work process, management will ensure that guardrails, barriers, or other similar means of fall restraint are used. When the use of a fall restraint system is not practicable or the equipment cannot be arranged to limit the vertical drop to 30 cm (1 foot), the supervisor will ensure that a fall arrest system is used.
5.2.2 GUARDRAILS
Guardrails must meet the design requirements of the WCB regulations. Any work platform where there is risk of falling more than 4 feet (1.2 m) must have guardrails. Opening in floors, walkways or roofs that are accessible to workers must be adequately covered or guarded to protect the worker.
Note: When a guardrail must be removed to accommodate work, only that portion of the guardrail necessary to allow the work to be done may be removed. The guardrail must be replaced if the work area is left unattended or after the work is completed if the circumstances still require the guardrail.
5.2.3 FALL ARREST All employees must wear a full body harness when using a personal fall protection system for fall arrest. A full body harness must conform with the Canadian Standards Association, or other standards acceptable to WBC. A full body harness and lanyard must be available for use any time there is a potential for a worker falling 10 feet or more. Before using any fall arrest device, each person must be familiar with: Inspection procedures; Correct method of wearing; How to install anchors; How to connect and use the harness in different situations. When a fall arrest system is not practical, or will result in hazards that are greater than if the system were not used, the supervisor will ensure that: A safety monitor system with a control zone is used; or A risk assessment is completed to devise a procedure that would be compliant with WCB Regulations.
5.2.4 FALL ARREST EQUIPMENT INSPECTION, MAINTENANCE & STORAGE
Safety belts, harnesses, lanyards, lifelines, anchors, and other similar devices must be: Inspected by a person before each use; kept free from substances and conditions that could contribute to their deterioration;
Document Identification SEL 020 Page Number Document Creation Date May 2, 2015 Implementation Date on Revised
Document
May 15, 2015
Anchor points shall, when at all possible, be able the work area. The distance of fall vs. distance of fall arrest travel, needs to be calculated; Maintained in good working order in accordance with manufacturers’ instructions; A device or part that is defective in condition or function must be removed from service.
After any personal fall protection equipment has arrested the fall of an employee, it must:
Be removed from service, tagged; and Not be returned to service until it has been inspected and re-certified for use by the manufacturer or its authorized agent, or by a structural engineer. Fall protection equipment must be stored in a clean dry environment.
5.2.5 FALL ARREST ANCHORS
All lifelines as well as lanyards used without lifelines, must be secured to anchors. An anchor plate with multiple eyes designed to support combinations of suspension lines, tie-back lines and lifelines must be designed by a structural engineer. A temporary anchor (such as a metal l-beam and lifeline combination) can be devised using other than engineered anchor points.
A supervisor/safety officer or designate must be responsible for performing a risk assessment confirming its adequacy for load bearing before work commences. Temporary anchors must be part of the fall protection plan.
5.2.6 ELEVATING EQUIPMENT
Guardrails and toe boards for elevating work levels 3 meters (10 feet) or more above the ground or floor: Shall meet minimum regulatory requirements. Shall require a pre-use inspection prior to any usage of the scaffold. Use extreme caution when using elevating equipment around power lines. A minimum distance of 10 feet should be maintained unless approved by the supervisor.
6.0 SCAFFOLDING
Scaffolding must meet the requirements of the CSA Standard CAN/CSA-S269.2-M87 (R2003) Access Scaffolding for Construction Purposes, and any other WCB Occupational Health and Safety Regulations. There are a number of scaffold types and the WCB Regulations should be reviewed carefully for special requirements that apply to each type. The footing or anchorage for scaffolds shall be sound, rigid and capable of carrying the maximum intended load without settling or displacement. Unstable objects, such as barrels, boxes, loose brick, or concrete blocks shall not be used to support scaffolds or planks.
Document Identification SEL 020 Page Number Document Creation Date May 2, 2015 Implementation Date on Revised
Document
May 15, 2015
Scaffolds and their components shall be capable of supporting at least four times the maximum intended load. Scaffolds shall be maintained in a safe condition and shall not be altered or moved horizontally while the yare in use or occupied. Scaffolds must be secured to ensure stability during use. Platform wheels must be locked if used. Scaffold platforms must meet the requirements of WCB regulations. Damaged or weakened scaffolds shall not be used. A safe means must be provided to gain access to the working platform level through the use of a ladder, ramp, etc. Overhead protection must be provided for personnel on a scaffold exposed to overhead hazards. Guardrails, mid-rails and toe boards must be installed on all open sides and ends of platforms more than 10 feet above the ground or floor. Mesh must be installed between the toe board and the guardrail along the entire opening, where persons are required to work or pass under the scaffolds. Employees shall nto work on scaffolds during storms or high winds or when covered with ice or snow.
7.0 ELEVATING WORK PLATFORMS
Elevating work platforms must meet the requirements of WCB Regulations. Any personnel operating an Elevating Work Platform (e.g. JLG) must be trained and a holder of a valid certificate. The equipment must be inspected by the operator prior to use, using an inspection form designed for that particular piece of equipment. If deficiencies are found during the inspection, the equipment is to be tagged “Out Of Service” and the deficiency pointed out to the heavy duty mechanics immediately.
Operators shall also: Follow the safe work practices; Follow all warning instructions on the equipment; Conduct pre-use inspection on the equipment; Use all available protective and safety devices; Use caution when fueling; Cleanup the work site; Check the work area; Plan your work; Check for overhead clearance to obstructions and power lines; Use the fall arrest harness at all times; Be knowledgeable of the safe load for the work platform; Travel at speeds safe for the area; Place hi-vis safety cones to warn others.
Document Identification SEL 020 Page Number Document Creation Date May 2, 2015 Implementation Date on Revised
Document
May 15, 2015
8.0 WORK PLATFORM (SUSPENEDED BY LIFT TRUCK)
Manually Propelled ladder stands and scaffolds must meet the requirements of WCB Regulation. A work platform must only be used in conditions where it is not feasible or practical to use another means - when all other reasonable options have been exhausted. The work platform used to lift personnel must be certified by a structural engineer. The lift truck forms must be inspected annually. The rated capacity of any lift truck must be clearly visible and sufficient to handle, without tipping, work platforms mounted the weight of the platform and its occupants and their contents (work tools). All work platforms must be secured by a device of adequate strength (chain) to the lift truck to prevent accidental dislodgment of the work platform from the lift truck. Inspection records must be kept for all inspections and repairs. A structural engineer must approve all alterations/repairs to a work platform. Approved hand signals must be used for communications by personnel in the work platform (radio communication is a suitable substitute for this). Only a designated worker may give signals, this will be determined prior to the start the task. No one may ride in a work platform mounted on a forklift while the lift truck is in motion. A pre-lift meeting must be held for all personnel that are involved in the lift prior to the actual lift commencing. The area surrounding the work platform must be identified by the use of hi-vis safety cones.
9.0 LADDERS
Ladders must meet the requirements of WCB Regulations and meet CSA Standards.
Proper use of ladders is essential in preventing accidents. Even a good ladder can be a serious safety hazard when used by workers incorrectly. Ladders shall be inspected before each use and those which have developed defects shall be withdrawn from service for repair or destruction and tagged or marked as “Dangerous, Do Not Use”. Use both hands when climbing or descending ladders - do not carry heavy or bulky objects that make climbing unsafe; a three point contact must be maintained with the ladder at all times. The worker shall always face the ladder when climbing up or down. Metal ladders shall never be used near electrical equipment; only non-conductive ladders must be used. Only one person should be on a ladder at a time and no work is to be done from the top three rungs of single or extension ladders, or from the top two steps of step ladders. Fall protection is required when the ladder is positioned near an edge or floor opening that significantly increases the fall hazard.
Document Identification SEL 020 Page Number Document Creation Date May 2, 2015 Implementation Date on Revised
Document
May 15, 2015
9.1 PORTABLE LADDERS
The various types of portable ladders include: Stepladder – A self-supporting portable ladder, non-adjustable in length, having flat steps and hinged back. Single Ladder – A non-self-supporting portable ladder, nonadjustable in length, consisting of but one section. Its size is designed by overall length of the side rail. Extension Ladder – A non-self-supporting portable ladder adjustable in length.
Portable Ladder Safety Precautions:
Ladders shall be placed with a secure footing, and they shall be tied at the top, or held in position when the ladder is being used to facilitate work.
Ladders used to gain access to a roof or other elevated work areas shall extend at least one meter above the point or support. The foot of a ladder shall be used at such a pitch that the horizontal distance from the top support to the foot of the ladder is one-quarter of the working length of the ladder (the length along the ladder between the foot and the support) i.e. the 4:1 rule should be applied (for every four feet of height, the ladder must be one foot away from the vertical structure). Ladders shall never be used in the horizontal position as scaffolds or work platforms. The top 3 of a portable stepladder shall not be used as a step. It is permissible to work off a ladder for a short period of time (less than 15 minutes) without the need to hook on if 3 point contact is maintained – i.e. Replacing a light bulb where your 2 feet and one hand (3 point contact) is maintained.
9.2 FIXED LADDERS
A fixed ladder is a ladder permanently attached to a structure, building or equipment. Fixed ladders, with a length of more than 20 feet to a maximum unbroken length of 30 feet shall be equipped with cages fastened to the side rails of the fixed ladder or to the structure to encircle the climbing space. A fixed ladder less than 20’ if used only for access does not need to be caged.
9.3 RESPONSIBILITES – PORTABLE LADDERS
Safety officers / supervisors or lead hands, or others in authority shall: Identify situations where the use of portable ladders is required; Determine the type of portable ladder required for the task as per the requirements; Provide employees with the appropriate portable ladder; Ensure that workers are informed of the proper use, care and maintenance of portable ladders; and Ensure that workers use the appropriate portable ladder.
Document Identification SEL 020 Page Number Document Creation Date May 2, 2015 Implementation Date on revised
Document
May 15, 2015
Workers shall:
Use portable ladders in a manner consistent with their training at all times; Maintain portable ladders in good condition; Inspect ladders upon receipt and before each use; and Ensure ladders are stored safely after each use. Not use or step on the top three rungs of the portable stepladder at any time.
Note: Persons who tire easily, are subject to fainting spells, are taking medication or have a physical disability which would prevent them from using a ladder in a safe manner should not use ladders.
9.4 SELF SUPPORTING LADDERS – STEP AND TRESTLE
Ladders used as self-supporting units shall have the legs fully spread and locked open; step ladders shall never be used in the unfolded position; No person shall sit or stand on the top two steps/rungs of the ladder; Never stand on the top step or pail shelf; The extension section of a trestle ladder shall be locked according to the manufacturer’s specifications.
9.5 STORAGE
Never rest a ladder on any of its rungs; ladders must rest on their side rails. When hanging a ladder on its side rails, place the rack at 2 m (6ft) intervals for supports; If storing a ladder vertically, secure the ladder by using a chain or bungee cord to prevent it from falling; During transport, do not pile other materials on top of the ladder. Ladders should be “top freight.” Store ladders in a cool and dry area
9.6 LADDER INSPECTION
Ensure that all rungs, side rails and non-skid feet are present and in good condition; Ensure that all rivets, joints, nuts and bolts are tight; and feet, steps and rungs are secure; Ensure that all moveable parts operate freely without binding or excessive play; Ensure that non-skid feet are checked for wear and free of imbedded materials. Swivel feet should display proper pivot action; For extension ladders, ensure that the ladder extension locks and feet are functioning (if necessary lubricate); and that the rope is properly affixed and in good condition; For step ladders, ensure that the spreader and pail shelf function proper; Wooden ladders should never be painted because that hide signs of deterioration. They may have a clear non-toxic coating or clear varnish; Ensure that ladders/rungs are clean and free of wet paint, mud, snow, grease, oil and other slippery materials; Ensure that clean shoes with dry soles and good grip are used. Leather soles should not be used;
Document Identification SEL 020 Page Number Document Creation Date May 2, 2015 Implementation Date on Revised
Document
May 15, 2015
Ensure replacement parts are made of appropriate/similar materials (i.e. inferior materials should not be used); Ensure that al working parts are in good working order before the ladder is used.
10.0 TRAINING
All employees using fall protection equipment including ladders must be trained in the following aspects: Identification of fall protection hazards Fall protection equipment available on site Correct size and positioning of belt and harness Correct procedures for tying off Inspection of equipment General requirement of regulations Proper use of elevating equipment & ladders
11.0 DEFINITIONS
“Anchor” means a secure point of attachment for a lifeline or lanyard; “Fall arrest system” means a system that will stop a worker’s fall before the worker hits the surface below; "Fall protection system" means o a fall restraint system, o a fall arrest system, or o work procedures that are acceptable to the Board and minimize the risk of injury to a worker from a fall; "Fall restraint system" means a system to prevent a worker from falling from a work position, or from travelling to an unguarded edge from which the worker could fall; "Full body harness" means a body support device consisting of connected straps designed to distribute the force resulting from a fall over at least the thigh, shoulders and pelvis, with provision for attaching a lanyard, lifeline or other components; "Horizontal lifeline system" means a system composed of a synthetic or wire rope, installed horizontally between 2 anchors, to which a worker attaches a personal fall protection system; "Lanyard" means a flexible line of webbing, or synthetic or wire rope, that is used to secure a safety belt or full body harness to a lifeline or anchor; "Lifeline" means a synthetic or wire rope, rigged from one or more anchors, to which a worker's lanyard or other part of a personal fall protection system is attached; "Personal fall protection system" means a worker’s fall restraint system or fall arrest system composed of a safety belt or full body harness, and a lanyard, lifeline and any other connecting equipment individual to the worker that is used to secure the worker to an individual point of anchorage or to a horizontal lifeline system;
Document Identification SEL 020 Page Number Document Creation Date May 2, 2015 Implementation Date on Revised
Document
May 15, 2015
"Safety belt" means a body support device consisting of a strap with a means for securing it about the waist and attaching it to other components; "Boom-supported" means supported by an elevating device that telescopes, articulates, rotates or extends relative to the machine base or vehicle, so that the platform can be positioned completely beyond the base; "Boatswain's chair", also known as a bosun's chair, means a seat attached to a suspended rope designed to accommodate one person in a sitting position; "Elevating work platform" means a movable work platform that self-elevates to overhead work locations; "Movable work platform" means a work platform that can be re-positioned during the course of the work; "Permanent powered platform" means a movable work platform that is permanently installed on or attached to a building or structure; “Portable powered platform” means a movable work platform that is raised or lowered by other than manual means, and is not permanently installed on or attached to a building or structure; “Scaffold” means any temporary elevated work platform and its supporting structure used for supporting workers, materials or equipment; “Self-propelled” means the capability of an elevating work platform to travel under power with the primary controls on the work platform; “Swing stage” means a work platform that is raised and lowered by manual or powered hoisting equipment, supported by 2 or more suspension lines; “Work platform” means an elevated or suspended temporary work surface used for supporting workers and includes a scaffold and boatswain’s chair.
o CORRESPONDING DOCUMENTS & FORMS
o CHSM - SEL 005 – WORKPLACE HAZARD ASSESSMENT & CONTROL
o CHSM – FRM 003 – JOB HAZARD ASSESSMENT TEMPLATE
o CHSM – FRM 050 – FALL PROTECTION PLAN TEMPLATE

Document Identification SEL 021 Page Number 1 of 7
Document Creation Date May 10, 2011 Implementation Date on Revised Document Feb 2, 2016
1.0 PURPOSE
The purpose of this program is to ensure employees are informed about hazardous materials used in the workplace so they can use that information to protect themselves from accidents, injuries and illnesses.
This hazard communication is accomplished through the three main components of WHMIS:
Labels: Containers of controlled products are required to be labeled Safety Data Sheets: Technical sheets that provide detailed hazard and precautionary information about the hazardous material. Education: To ensure employees understand the contents and significance of labels and material safety data sheets and apply that knowledge to work safely with hazardous materials
2.0 SCOPE
This program applies to all Belterra employees and contractors who are exposed to or likely to be exposed to hazardous materials used in the workplace.
3.0 RESPONSBILITIES
3.1 SUPPLIERS OF HAZARDOUS MATERIALS ARE RESPONSIBLE FOR
Determining whether their products are considered “controlled products” under the Controlled
Products Regulations and classifying the material into the appropriate hazard class(es); Preparing a safety data sheet for their products and providing copies of the SDS to purchasers; Labeling containers of controlled products or providing a supplier label to purchasers.
3.2 SUPERVISORS ARE RESPONSIBLE FOR
Ensuring containers of controlled products used in the workplace are properly labeled or identified; Ensuring that the safety data sheets are up to date (less than 3 years old) and readily available for employees to review; Maintaining an inventory of hazardous materials used in the workplace; Ensuring employees who work with or in close proximity to hazardous materials complete WHMIS training and an annual review quiz; Ensuring employees use the required equipment and protective measures and work safely with hazardous materials; Ensure hazardous waste is disposed properly in accordance with provincial regulatory requirements.
Document Identification SEL 021 Page Number Document Creation Date May 10, 2011 Implementation Date on Revised
Document
February 2, 2016
3.3 EMPLOYEES ARE RESPONSIBLE FOR
Applying their WHMIS training to work safely with hazardous materials used in the workplace; Reviewing the Safety Data Sheets for hazardous materials used in the workplace prior to using them; Following safe procedures and using required equipment when handling hazardous materials; Reporting hazardous or unsafe chemical incidents or exposures to their supervisor.
3.4 CONSTRUCTION SAFETY OFFICERS AND SAFETY REPRESENTATIVES ARE RESPONSIBLE FOR
Reviewing the WHMIS program with the Joint Health & Safety Committee and informing corporate
H&S of any updates as required. Program review must be done annually; Act as Subject Matter Expert to all levels of employees at branch level
3.5 CORPORATE HEALTH & SAFETY IS RESPONSIBLE FOR
Develop the WHMIS program and ensure it meets the regulatory compliances; Responding to or providing advice in the event of a chemical emergency where necessary; Assist branch management, safety representatives and CSO’s as and when required.
3.6 CONTRACTORS ARE RESPONSIBLE FOR
Ensuring containers of controlled products that may be brought to Belterra or customer sites are labelled properly; Maintaining SDS for controlled products used at Belterra and customer sites; Ensuring workers are trained in WHMIS; Informing the CSO or branch manager of any WHMIS or other health and safety related problems.
4.0 TRAINING
WHMIS training is required for employees who are exposed to or likely to be exposed to hazardous materials in the workplace. There are two levels of WHMIS training based on an employee’s degree of exposure to hazardous materials.
Employees, in consultation with their supervisor, are responsible for determining which WHMIS program is required. Construction Safety Officers or Corporate H&S can also be contacted for further information.
Document Identification SEL 021 Page Number Document Creation Date May 10, 2011 Implementation Date on Revised
Document
February 2, 2016
4.1 BASIC LEVEL WHMIS
Intended for employees who are not likely to be exposed to hazardous materials in the course of their work, but as part of awareness only. Examples include - Inside sales, operations manager, HR department etc., and employees working in areas that do not store or use hazardous materials.
4.2 ADVANCED LEVEL WHMIS
Intended for employees who work with or are in close proximity to hazardous materials or who supervise such employees. Examples include field technicians, shipper receiver, supervisors, outside sales, ISO coordinators & H&S representatives etc.
4.3 TRAINING FREQUENCY
WHMIS training is required every three years or more frequently when there are changes to an employee’s degree of handling hazardous materials. An annual refresher quiz is required to ensure the level of understanding of WHMIS stays current.
5.0 LABELS
Containers of controlled products are required to have labels applied to them in order to alert users to the potential hazard(s) of the products, and any safe handling precautions necessary to protect themselves while using the product.
Labels also refer users to the SDS for more detailed information regarding the product.
There are two types of WHMIS labels:
5.1 SUPPLIER LABELS
Suppliers are responsible for labeling containers of controlled products (or providing proper labels).
5.2 WORKPLACE LABELS
A workplace label is a label that Belterra will prepare to identify controlled products under the following conditions: - To replace a damaged, missing or unreadable supplier label; - To label a controlled product that has been transferred into another container from the suppliers container; - To label a controlled product provided in the workplace.
Document Identification SEL 021 Page Number Document Creation Date May 10, 2011 Implementation Date on Revised
Document
February 2, 2016
5.3 WHMIS WORKPLACE LABEL CONTENT
Workplace labels do not require borders, hazard symbols or specific wordings, but must contain a minimum of the following information:
Product identifier (product name) Information for safe handling of the product (e.g. wear suitable gloves, avoid breathing vapors, avoid skin contact Statement that a SDS is available
6.0 EMERGENCY PROCEDURES – CHEMICAL SPILLS
Chemical spills must be cleaned up promptly to protect life, property and the environment. There are two types of spills:
Minor Spill: Minor spills involve quantities small enough such that the emergency spill kit materials available are sufficient to contain and clean-up the spill.
Major Spill: Major spills involve quantities that cannot be contained safely with the emergency spill kit materials on site and/or threaten the building or the environment. Depending on the materials involved, major spills may pose significant fire, health or environmental hazards and must be promptly cleaned-up by a trained emergency response team such as a company specializing in hazardous materials spill response.
6.1 EMERGENCY PROCEDURE – MINOR SPILLS
Notify the spill response coordinator or the person responsible for the area. Promptly stop or shut off the source of the spill if possible and safe to do so. Eliminate any sources of ignition (e.g. electrical equipment, smoking, sparks, flames etc.). Ventilate the area using natural or mechanical ventilation (open doors, windows etc.) Contain the liquid by placing a dam around it using absorbent socks or inert absorbent material.
Prevent material from entering drains or contaminating other materials.
Place absorbent or neutralizing material on the liquid (refer to SDS for proper procedure). Pick up the material with a scoop or shovel made of non-sparking and non-reactive material and place in a compatible container for disposal. Contact your local spill disposal company for proper disposal. If a fire should result, follow the procedure for fire emergencies.
Document Identification SEL 021 Page Number Document Creation Date May 10, 2011 Implementation Date on Revised
Document
February 2, 2016
6.2 EMERGENCY PROCEDURE – MAJOR SPILLS
Promptly stop or shut off the source of the spill if possible and safe to do so. Evacuate the area and restrict further access. Notify branch manager or designate will notify or make arrangement to notify the Environmental &
Spill Emergency department within the province of occurrence.
6.3 EMERGENCY TELEPHONE NUMBERS
Fire Department: 9-1-1 Environmental & Spill Emergencies: o BC- 1-800-663-6456 o ON- 1-800-268-6060 o MB- 1-204-944-4888 (collect calls accepted within province) o SK- 1-800-667-7525 o AB- 1-800-222-6514 o AC- 1-866-283-2333 CANUTEC: (For dangerous goods incidents during transportation) 1-888-226-883
7.0 WHMIS CLASSES AND HAZARD SYMBOLS
The flame pictogram is used for the following classes and categories:
Flammable gases (Category 1) Flammable aerosols (Category 1 and 2) Flammable liquids (Category 1, 2 and 3) Flammable solids (Category 1 and 2) Pyrophoric liquids (Category 1) Pyrophoric solids (Category 1) Pyrophoric gases (Category 1) Self-heating substances and mixtures (Category 1 and 2) Substances and mixtures which, in contact with water, emit flammable gases (Category 1, 2 and 3) Self-reactive substances and mixtures (Types B*, C, D, E and F)
Organic peroxides (Types B*, C, D, E and F) The gas cylinder pictogram is used for the following classes and categories:
Gases under pressure (Compressed gas, Liquefied gas, Refrigerated liquefied gas, and Dissolved gas)
Document Identification SEL 021 Page Number Document Creation Date May 10, 2011 Implementation Date on Revised
Document
February 2, 2016
The corrosion pictogram is used for the following classes and categories:
Corrosive to metals (Category 1) Skin corrosion/irritation - Skin corrosion (Category 1, 1A, 1B and 1C) Serious eye damage/eye irritation - Serious eye damage ( Category 1)
The exploding bomb pictogram is used for the following classes and categories:
Self-reactive substances and mixtures (Types A and B*) Organic peroxides (Types A and B*)
The skull and crossbones pictogram is used for the following classes and categories:
Acute toxicity o Oral (Category 1, 2 and 3) o Dermal (Category 1, 2 and 3)
Inhalation (Category 1, 2 and 3) The health hazard pictogram is used for the following classes and categories:
Respiratory or skin sensitization - Respiratory sensitizer (Category 1, 1A and 1B) Germ cell mutagenicity (Category 1, 1A, 1B and 2) Carcinogenicity (Category 1, 1A, 1B, and 2) Reproductive toxicity (Category 1, 1A, 1B and 2) Specific Target Organ Toxicity - Single exposure (Category 1 and 2) Specific Target Organ Toxicity - Repeated exposure (Category 1 and 2)
Aspiration hazard (Category 1) The exclamation mark pictogram is used for the following classes and categories:
Acute toxicity - Oral, Dermal, Inhalation (Category 4) Skin corrosion/irritation - Skin irritation (Category 2) Serious eye damage/eye irritation - Eye irritation (Category 2 and 2A) Respiratory or skin sensitization - Skin sensitizer (Category 1, 1A and 1B)
Specific target organ toxicity - Single exposure (Category 3) The biohazardous infectious materials pictogram is used for the following classes and categories:
Biohazardous Infectious Materials (Category 1)
* Both the Flame and Explosive pictogram are used for Self-reactive
Document Identification SEL 021 Page Number Document Creation Date May 10, 2011 Implementation Date on Revised
Document
February 2, 2016
substances and mixtures (Type B) and Organic peroxides (Type B)
NOTE: Physical Hazards Not Otherwise Classified and Health Hazards Not Otherwise Classified classes are required to have a GHS pictogram that is appropriate to the hazard identified.

HEARING CONSERVATION AND CONTROLS
Document Identification SEL 022 Page Number 1 of 7
Document 1st Created January 1, 2013 Implementation Date on Revised
Document
Jan 20, 2017
1.0 SCOPE AND APPLICATION
This program applies to all employees who work in noise hazard areas or who have the potential to develop noise-induced hearing loss as a result of their occupation. Nuisance noise, which may be irritating or annoying to some people, but which is not loud enough to be associated with noise-induced hearing loss does not fall under this program.
2.0 CRITERIA FOR NOISE EXPOSURE
2.1 Individual Exposure: An individual is considered noise exposed if he/she has the potential to develop occupational noise-induced hearing loss. Regular exposure to noise levels greater than a time-weighted average of 85 dB(A) or an “equivalent” noise exposure as listed in Table 1, is associated with the development of noise-induced hearing loss
The level of 85 dB(A) is not a fine line between safe and hazardous noise exposures. Some individuals may be more susceptible to the effects of noise and may be at risk of developing noise-induced hearing loss when regularly exposed to sound levels between 80 and 85 dB(A).
Although the risk between 80 and 85 dB (A) is lower than that associated with regular exposure to noise levels greater than 85 dB(A), employees who work in such situations shall be informed and offered appropriate hearing protection.
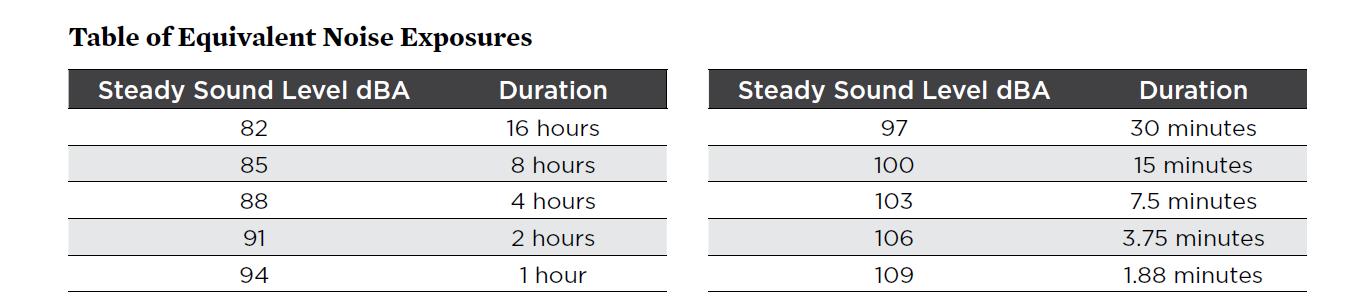

Document Identification SEL 022 Page Number Document Creation Date May 10, 2011 Implementation Date on Revised
Document
February 2, 2016
2.2 Noise Areas: An area or location is considered a noise hazard if sound levels are regularly at or above 85 dB(A).
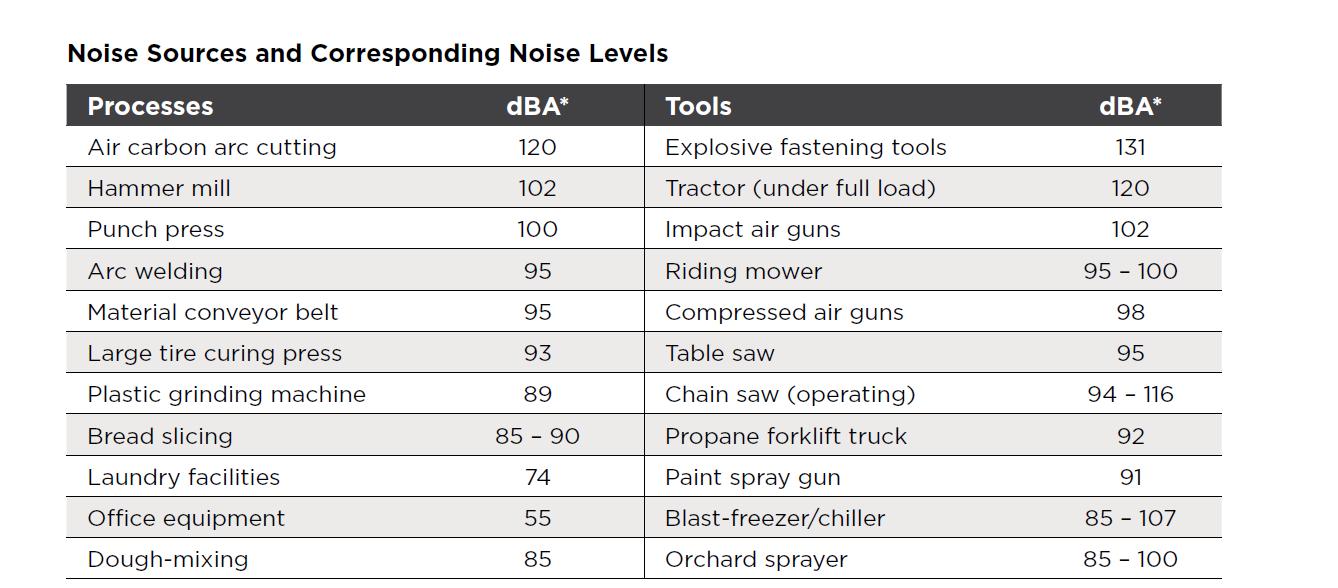
3.0 PROGRAM ELEMENTS
o 3.1 Noise Hazard Assessment:
Noise hazard areas and noise exposed workers will be identified by the appropriate manager or supervisor in conjunction with the health and safety representative and the safety committee. No employee shall be exposed to a sound level greater than 85dBA without proper training and appropriate hearing protection to reduce the sound level to less than or equal to 85dBA. The safety representative or supervisor will arrange for a survey of noise levels and personal noise dosimetry in noise hazard areas.
The safety representative will maintain a list of noise hazard areas and conduct periodic resurveys. If workplace conditions potentially change noise levels at any time, the supervisor of the area should contact the branch manager for a re-survey of the area.
3.2 Engineering Controls: In any noise hazard area, the feasibility of instituting engineering controls to reduce noise levels shall be the first consideration where practicable. This is best done at the design stage and when purchasing new equipment. When new equipment is purchased, the noise specifications should be checked and
consideration given to applying engineering controls to reduce noise levels to below 85 dB(A) if possible.
Document Identification SEL 022 Page Number Document Creation Date May 10, 2011 Implementation Date on Revised
Document
3 of 7
February 2, 2016
Depending on the circumstances, possible engineering controls could include barriers, vibration damping, source isolation and sound absorbing enclosures.
3.2 Administrative Controls:
Where engineering controls are not practical or feasible, or unable to reduce noise levels below 85 dB(A), administrative controls such as changes in work procedures, rescheduling of noisy activity or decreasing the duration of exposure should be considered. Clearly visible warning signs must be posted at the approaches to an area where sound levels regularly exceed 85 dB(A).
These warning signs must clearly indicate that the use of hearing protection is mandatory or provide the maximum exposure time from Table 1 where an individual may be in the area without hearing protection. In situations where a piece of equipment or machinery presents a noise hazard, a sign must be affixed to the equipment, in a clearly visible location, indicating that the operator must wear appropriate hearing protection.
3.4 Hearing Protection: Where other hierarchy of controls is not practicable, hearing protection must be worn by workers where noise exposures could exceed the levels given in Table 1. Regardless of the limits in Table 1, hearing protection should be available to workers on request where noise levels exceed 80 dB (A).
3.3 Education and Training:
All noise-exposed workers who are required to wear hearing protection must attend a training session with the health and safety coordinator. This training session will cover: 3.3.1 Hazards of excessive noise
3.3.2 Results of noise surveys in the work area 3.3.3 Noise control strategies 3.3.4 The proper selection and use of hearing protection
Document Identification SEL 022 Page Number Document Creation Date May 10, 2011 Implementation Date on Revised
Document
4 of 7
February 2, 2016
4 NOISE EXPOSURE STANDARDS:
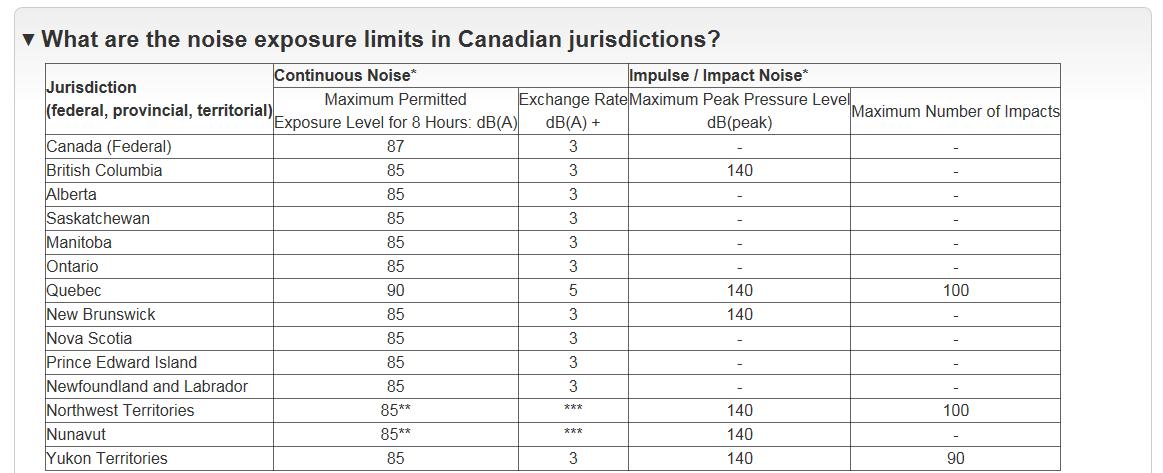
5 SELECTION OF HEARING PROTECTION
Noise-induced hearing loss may be prevented through the effective use of appropriate hearing protection. Hearing protection must protect against the level of noise hazard, provide a comfortable fit, and comply with CSA Standard Z94.2-M1984, Hearing Protectors.
It is also important that workers receive appropriate training prior to the initial use of hearing protection. There are two general categories of hearing protection devices – earmuffs and earplugs.
5.1 Earmuffs:
Earmuffs are external hearing protection devices consisting of a headband and ear cups. The ear cups are cushioned and are intended to fit snugly against the side of the head. The ear cup must completely encircle the ear in order to provide a good seal and protect the inner ear. Earmuff fit can be compromised by the use of other safety equipment such as glasses, goggles and hard hats so care must be taken to ensure a proper fit. Earmuffs must comply with CSA Standard Z94.2-M1984. Earmuffs must be regularly inspected and maintained in good condition. Ear cup cushions which are cracked, hardened must be replaced. The headband must maintain adequate tension against the ear or it must be replaced.
Document Identification SEL 022 Page Number Document Creation Date May 10, 2011 Implementation Date on Revised
Document
5 of 7
February 2, 2016
5.2 Earplugs
Earplugs are hearing protection devices which are inserted into the ear canal. Earplugs must fit snugly and seal the ear canal to provide adequate noise attenuation to protect the inner ear. Earplugs must comply with CSA Standard Z94.2-M1984. There are a variety of different earplugs available but the most common types are expandable foam or preformed plugs with flanges. To get the best fit, the ear should be pulled back with the opposite hand to straighten the ear canal and the earplug inserted with clean hands. Earplugs can work loose through the day and therefore should be reseated periodically. Earplugs are either disposable (used only once) or reusable. With proper care the latter can be used for up to six months. Reusable earplugs must be regularly inspected and cleaned (washed with mild soap and allowed to dry in a clean environment). If the earplug becomes hard or is not able to provide a good seal, the earplugs must be replaced.
5.3 Classes of Hearing Protection
Hearing protectors are classified as Class A, B or C based on the minimum noise attenuation at various assigned frequencies. Class A provides the highest level of attenuation across the test frequencies, Class B provides the next highest level of attenuation and Class C provides the least attenuation.
6 CSA RECOMMENDED CLASS OF HEARING PROTECTION
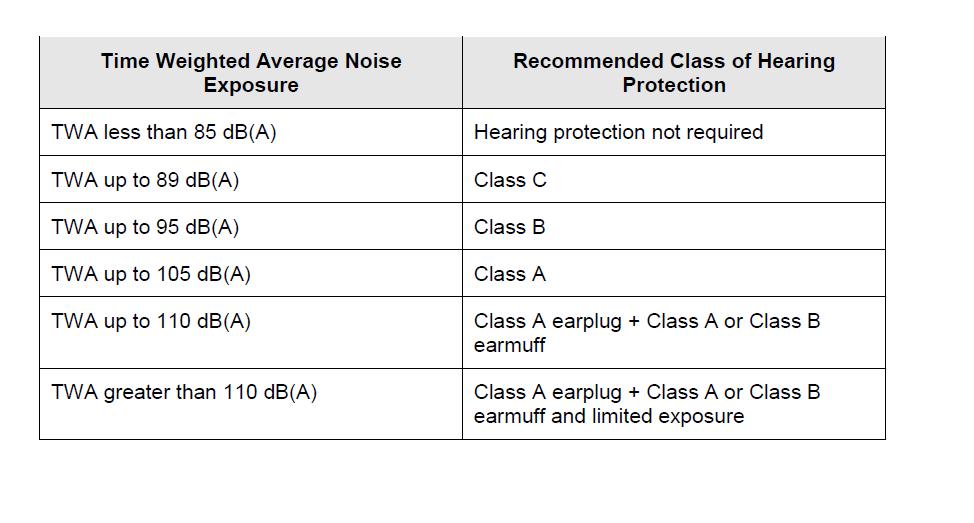
Document Identification SEL 022 Page Number 6 of 7
Document Creation Date May 10, 2011 Implementation Date on Revised
Document
February 2, 2016
7 ANNUAL HEARING TESTS
Occupational hearing loss is one of the leading causes of work-related disorders. Because occupational hearing loss happens gradually overtime, workers often fail to notice changes in their hearing ability until a relatively large change occurs. By comparing audiometric tests from year to year, early changes can be detected and appropriate protective measures implemented to prevent further damage
PROVINCE
FREQUENCY OF AUDIOMETRIC TESTING’S
AB Where a worker is or may be exposed to excess noise, the worker shall have a baseline audiogram as soon as practicable, but no later than six months after the start of employment. Additional tests are required 12 months after the baseline test, and every two years thereafter.
BC Where workers are exposed to noise that exceeds noise exposure limits initial hearing test must be given as soon as practicable after employment starts, but not later than 6 months after the start of employment. Audiometric testing must be conducted at least once every 12 months after the initial test. ON Hearing test should take place annually unless workers are exposed to very high noise in exposure of 105 dB and greater. In this case, hearing tests should be conducted once every 6 months. SK Employers shall arrange to have hearing tests be available to workers who are
exposed to a daily noise level equal to, or greater than, 85 dB(A), regularly work in areas where noise levels are equal to or greater than 90 dB(A) once every 2 years MB Baseline audiometric testing’s shall be conducted within the first 70 days of hire for all individuals that are exposed to average noise levels in excess of 85dBA throughout their workday. Thereafter audiometric tests shall be conducted on annual basis QC Hearing Test shall be conducted on annual basis
8.0 BELTERRA’S REQUIREMENTS ON CUSTOM MOULDED HEARING PLUGS
Studies have shown that custom molded earplugs offer a far superior protection than foam disposable earplugs. These earplugs also offer the option for connectivity to cell-phones and two-way radios.
The use of hearing protection is mandatory at Belterra for all employees while in the shop, at customer sites and any other work area where noise level exceeds 85 dBA.
Document Identification SEL 022 Page Number Document Creation Date May 10, 2011 Implementation Date on Revised
Document
7 of 7
February 2, 2016
Molded ear plugs are designed to last a minimum of 5 years. Belterra will provide to all employees one pair free of charge, every four years after completion of the probationary term.
Where an employee has to replace their molded earplugs prior to four years, the employer will pay the prorated amount, and the employee will shoulder the rest of the balance e.g. if an employee requires replacement after one year, the Company will pay 25%, after 2 years 50% , and after 3 years 75% etc.