
12 minute read
Blade Corner
10 Winter Sawing Tips
1. Lower blade hook angles work better in frozen and partially frozen logs. Consider running 9°, Turbo 7, Turbo 747, or 4° blades 2. Narrow blade widths can have less resistance and effectively clean out frozen sawdust.
Consider running 1-1/4" wide blades 3. Pay attention to partially frozen logs as the outside of the log freezes and thaws first 4. Keep feed rates up and consistent to reduce sawdust freezing on material 5. Monitor blade guides to ensure they are tight and level 6. Switch drive and idle side blade wheel belts 7. Check the blade guide arm to ensure it is tight 8. Use proper or slightly higher blade tension 9. Monitor drive belt tension to ensure it is tight 10. Use windshield washer fluid in blade water lubrication tank while sawing in 32° or below temperatures
NEW TURBO 747 HIGH-PERFORMANCE SAWMILL BLADES
Wood-Mizer introduces the Turbo 747 high-performance sawmill blade engineered for all band sawmill and resaw makes and models, horsepower ratings, and sawing applications. Available in SilverTip Carbon and DoubleHard High-Alloy steel material, Turbo 747 sawmill blades feature a deep capacity gullet for less sawdust on the board, extreme back angle for faster sawing speeds, and sharp penetrating points for increased sawing accuracy.
“The feed rate is quite a bit faster,” shares Luke Eames of Holland Timber Co. in New York who runs an LT70 super hydraulic portable sawmill.
“We can maintain faster feed rate through knots with minimal wave.”
Wood-Mizer Blades Sales Manager Randy Panko says, “After extensive
field testing, the new Turbo 747 blade has resulted in increased feed rate, accuracy, and sharp life in all horsepower levels and sawmill equipment models. With the blade’s steep sloped back angle and proven 7 degree hook angle, sawyers can take on even the most challenging sawing applications.”
The Wood-Mizer Turbo 747 sawmill blade is now available to order direct
at 800.522.5760, online at woodmizer.com, or through authorized dealers.
Turbo 747 Sawmill Blade Features
• Compatible with multiple makes and models of band sawmill equipment • Resharpen with precision CBN grinding wheel technology • SilverTip Carbon and DoubleHard High-Alloy steel material • Available in any length • 1-1/4", 1-1/2", 1-3/4", 2" widths • .042", .045", .055" thicknesses • 7/8" tooth spacing • Made in the USA

Tips from the Saw Filers Corner
If you are maintaining your own sawmill blades with Wood-Mizer blade sharpeners and tooth setters, here are a few tips from our ReSharp® blade sharpening specialists WINTER SAWING FAQ to ensure you receive consistent, sharp, and accurate blades with each sharpening.
First make sure your blade maintenance equipment is cleaned thoroughly and inspect all electrical cords for damage. Second, inspect the blade for any teeth damage and begin with as clean of blade as possible by lubricating the blade before removing from your sawmill equipment to eliminate any pitch build-up or wash the blade before installing on your maintenance equipment. HELPFUL BLADE MAINTENANCE TOOLS
Red Layout Dye (Part # 057791) is used to mark the profile of a blade on the tooth face, gullet, and back to ensure proper grinding depth and indexing while resharpening.
Blade Profile Gauge (Part # 109064) includes a total of 15 profiles to determine the correct blade profile before sharpening.
Tooth Setter Gauge (Part # 060490) is used to measure tooth set quickly and accurately for the best quality control. BMS250 OR BMS500 BLADE SHARPENING TIPS
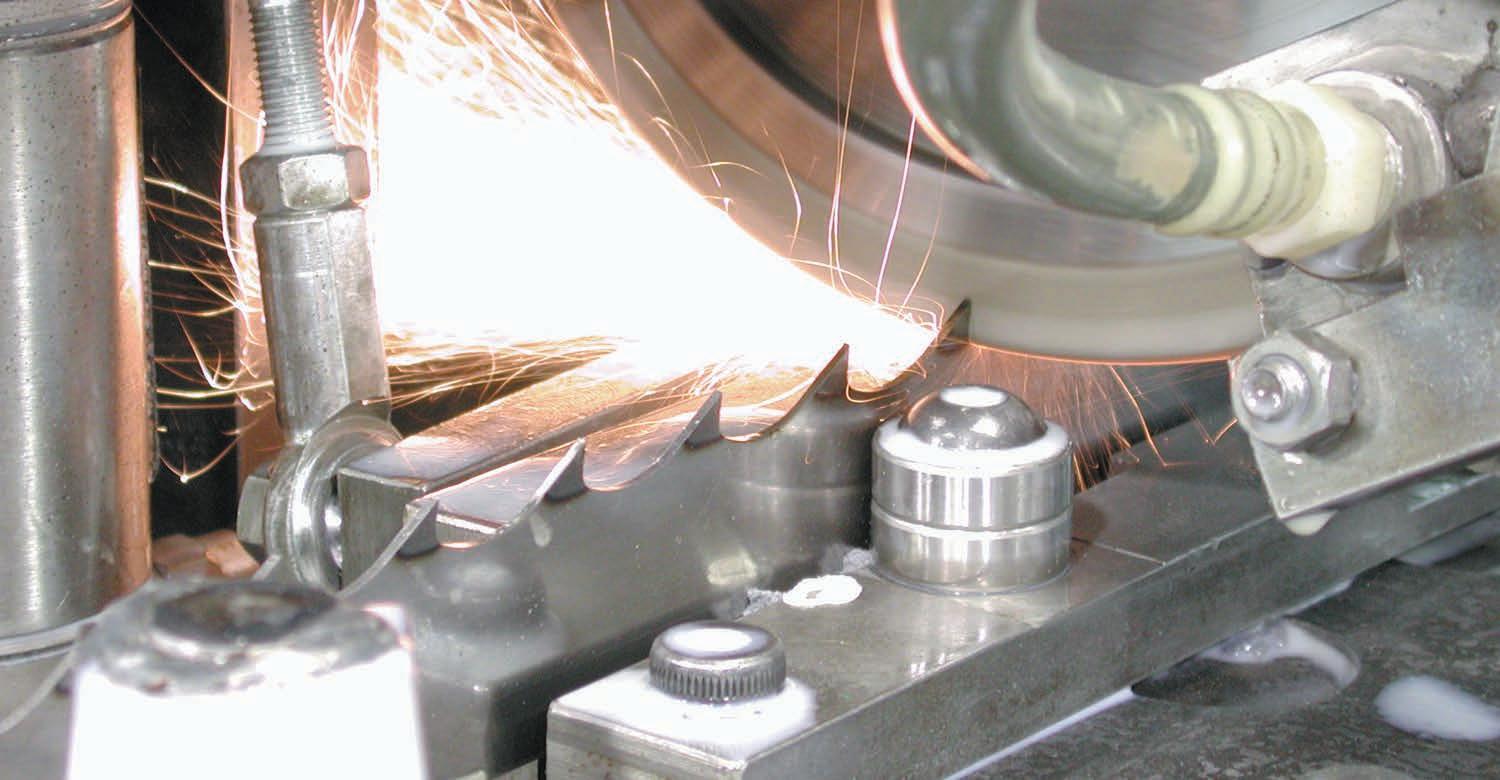
• Inspect clamp blocks for wear and replace if grooved for better clamping
• Check the index pivot arm bearings and replace if loose
• Inspect and replace wipers if worn
• Clean magnets on the BMS250 or clean the magnet tray on the BMS500
• Drain and clean oil trays and replace oil regularly
BMS500 BLADE SHARPENING TIPS
• Check pillow block bearings for wear and give them a reasonable amount of grease
• Check the mushroom bolt for wear and adjust for proper clearance to the clamp plate
TOOTH SETTER TIPS
• Check tooth pushers for excessive wear and replace if needed
• Check index pivot arm bearings and replace if loose
Steve Wilson – Clancy, Montana SAWMILL: LT40 HYDRAULIC SUPER BLADES: DOUBLEHARD
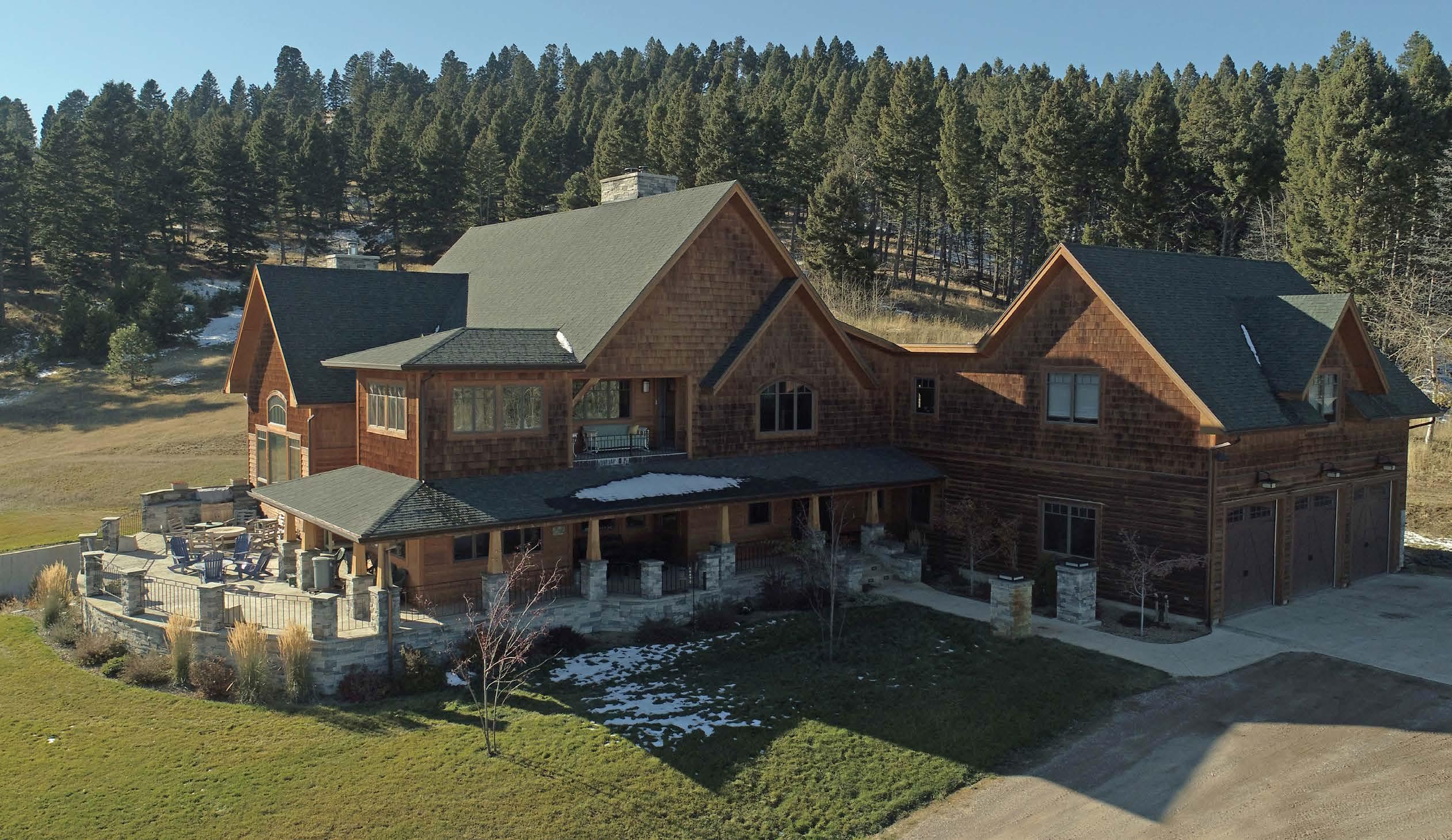
By The Numbers - 11,000 total square feet - 100 red oak trees produced 450+ beams - 6 years to complete - $50,000 saved
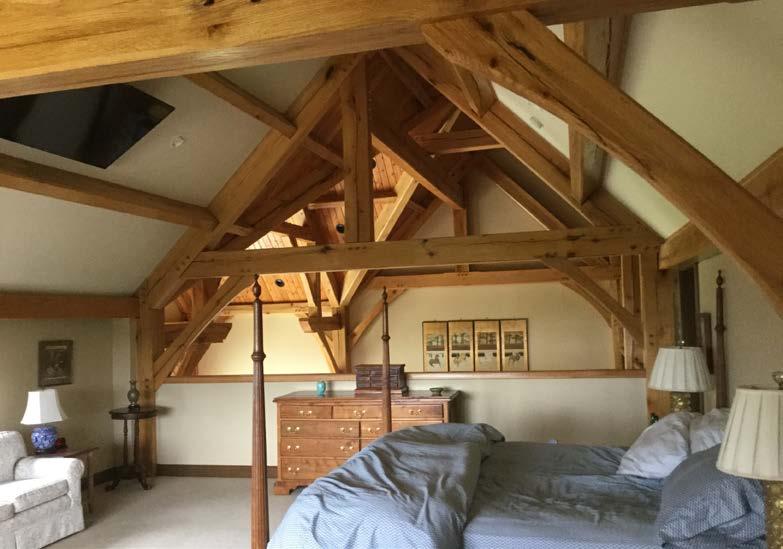
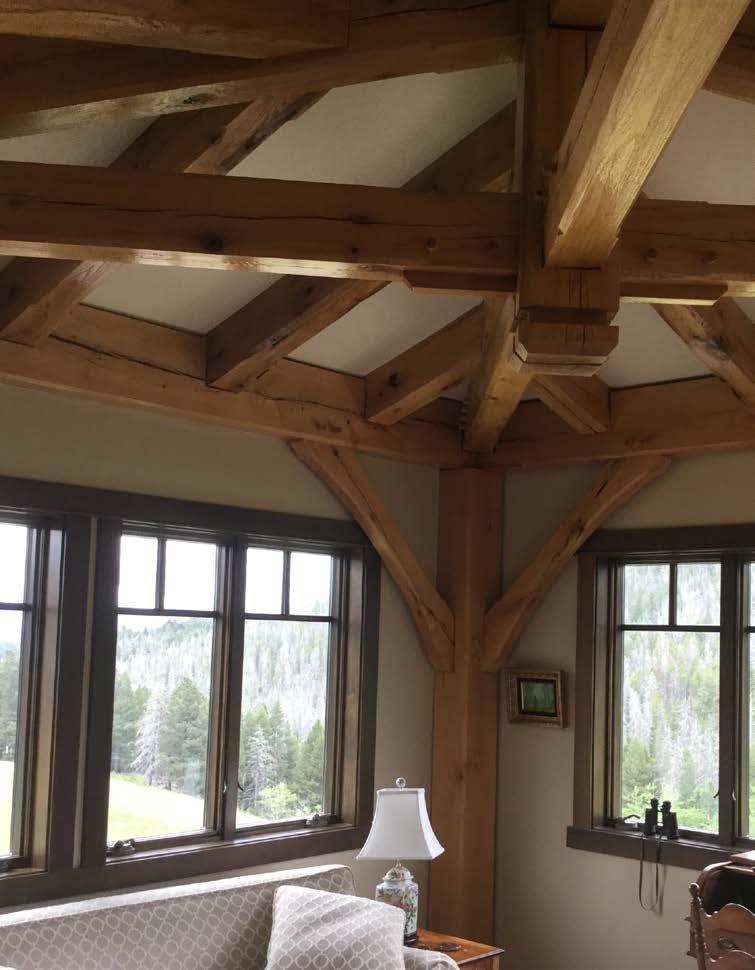

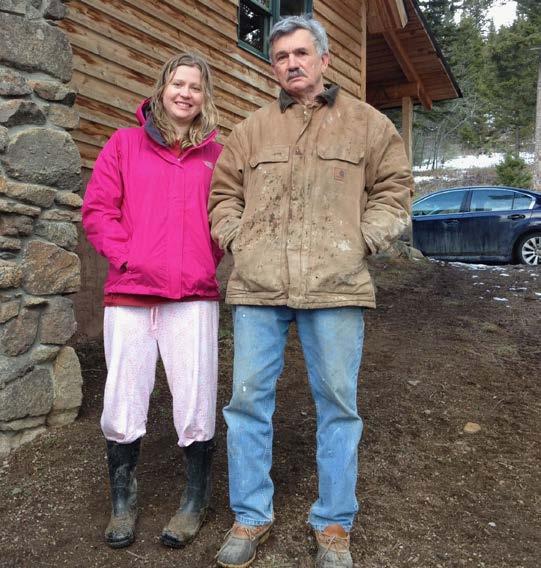
By Samantha Alexander
What started out as an idea, stemming from a magazine article, Steve Wilson felt that his persistence would get him to the final goal of a timber frame home. “After consultation with an architect, I started cutting trees,” said Steve. While the home stands tall in the mountains of Montana, the 450+ red oak beams were milled in North Carolina by Steve and his WoodMizer LT40 Super Hydraulic sawmill. Once cut, they were dried in a shed he built with the help of a friend. “After fabrication, the timbers were transported to western Montana and the frame erected to be dried over the next two years. It took about four flatbeds to move the timbers,” said Steve.
The timber frame home wasn’t the only thing on Steve’s mind while milling. He also cut a variety of hardwoods that he used to build furniture in North Carolina. “I also brought one flatbed of maple, cherry, walnut, oak, poplar & red cedar to Montana for my furniture making hobby,” said Steve. This caused a ripple effect that began the additions of more sheds, a shop and a sawmill shed at the Montana home to keep all of the transported hardwood. However, he was then able to fill his home with dozens of his own furniture creations using the lumber as well.
Steve used his Wood-Mizer for the milling process and said that the feature that assisted him the most during all of this was the hydraulic system. He was also able to save around $50,000 completing this project himself. “I had a more than full time job, so milling was primarily on the weekends,” said Steve. In a little more than five years, he was able to build what he now calls home.
“T he personal satisfaction of building a home for our family (wife and two kids), starting with zero building skills, is beyond measure. Every morning when I wake up to the wood that surrounds us I smile with pride. The LT15 was purchased because I could not find anyone to mill the logs for us and it is the perfect tool for us and our homestead. We use the sawdust for our compost toilets, give the slabs to locals for firewood and syruping wood, and use the mill for all of our outbuildings and continued interior projects. We could not have done any of this without it.” – Josh Wehrwein
Josh Wehrwein – Sedgwick, Maine SAWMILL: LT15 Project Description: Bill Coperthwaite designed three-story wooden tapered wall yurt
By The Numbers - 2,500 total square feet - 18,000 board feet of spruce and eastern white cedar - 85% of project completed with Wood-Mizer sawn lumber - 4 years to complete - $20,000 saved
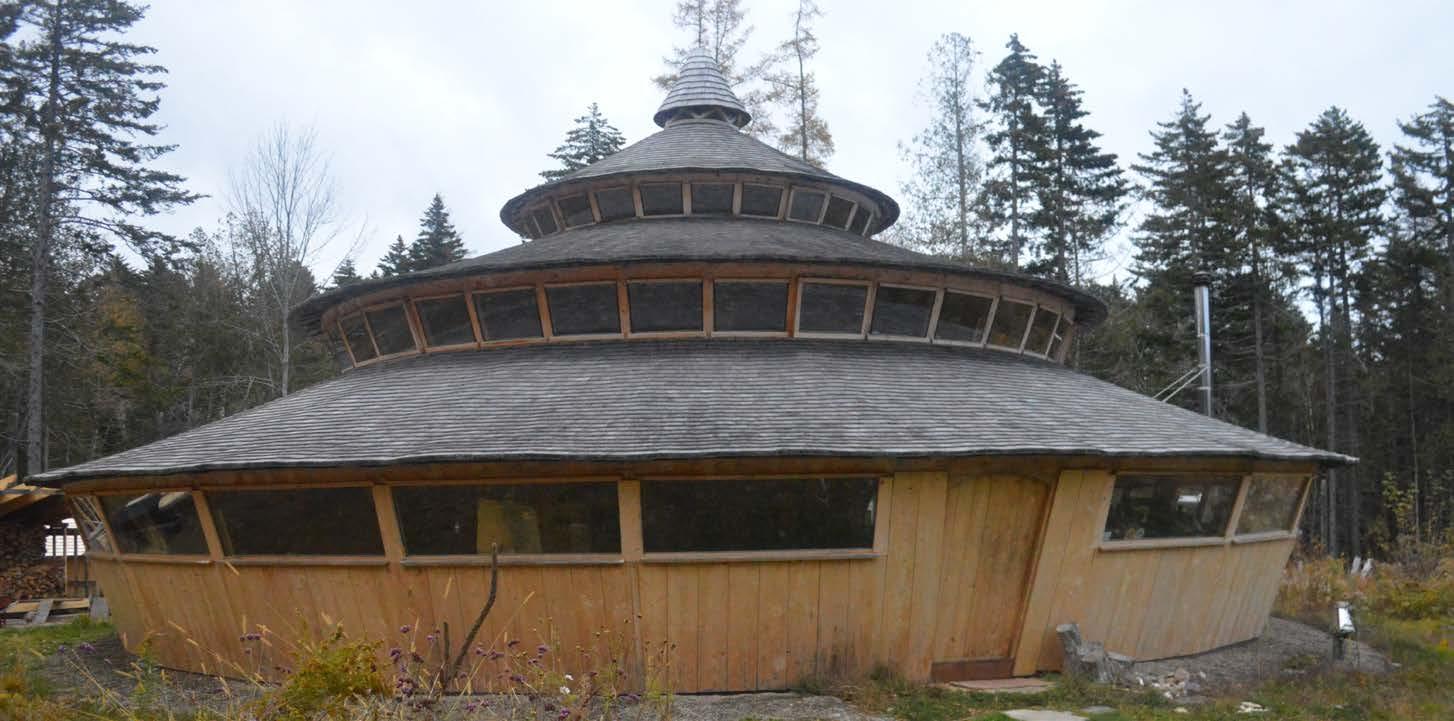
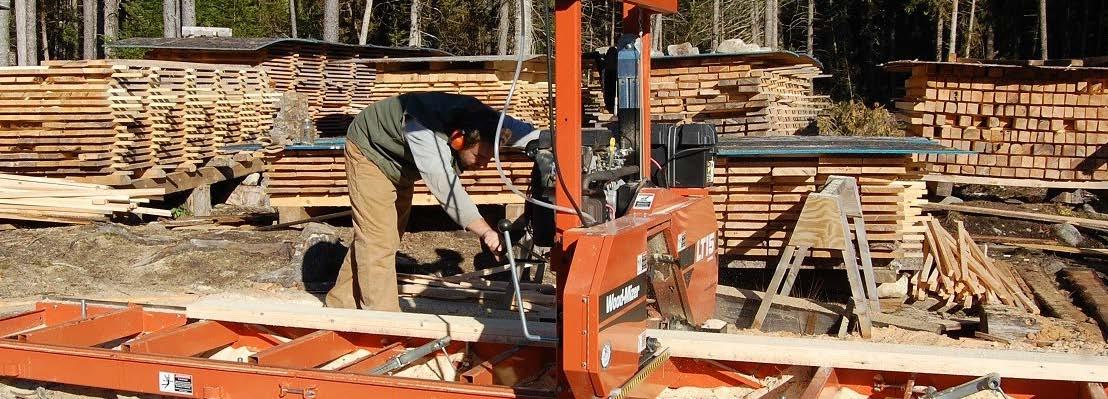
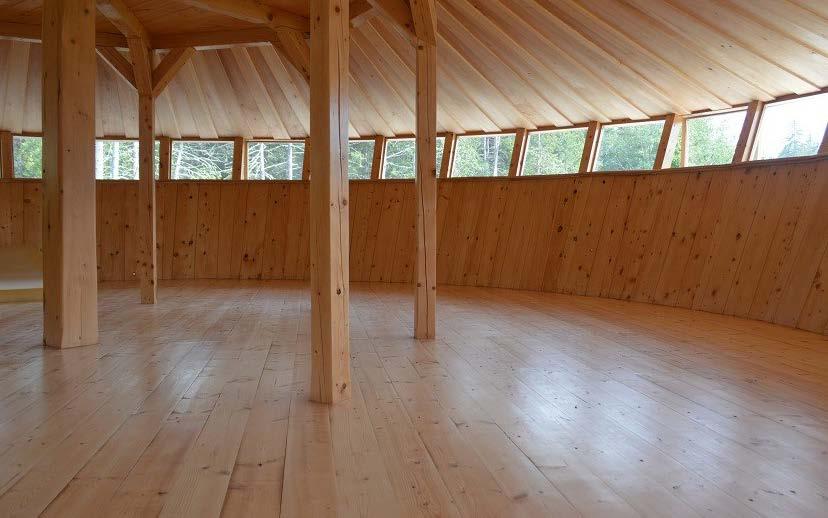
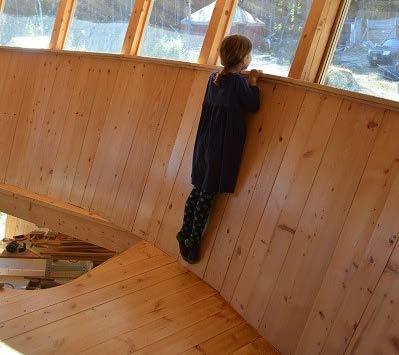
3RD PLACE Homes & Major Structures
e wanted to build our own custom dream home. Everyone is amazed at the quality of work and the overall appearance of the house. I was extremely satisfied and proud of all the hard work upon seeing the finished project!” – Wayne Quibell “W
Wayne Quibell – Wilberforce, Ontario SAWMILL: LT15 BLADES: RAZORTIP Project Description: Log home with a 26' timber trussed ceiling, handcrafted stone fireplace, and plenty of square feet to roam
By The Numbers - 2,280 total square feet - 20,000 board feet of pine - 85% of project completed with Wood-Mizer sawn lumber - 8 years to complete - $30,000 saved


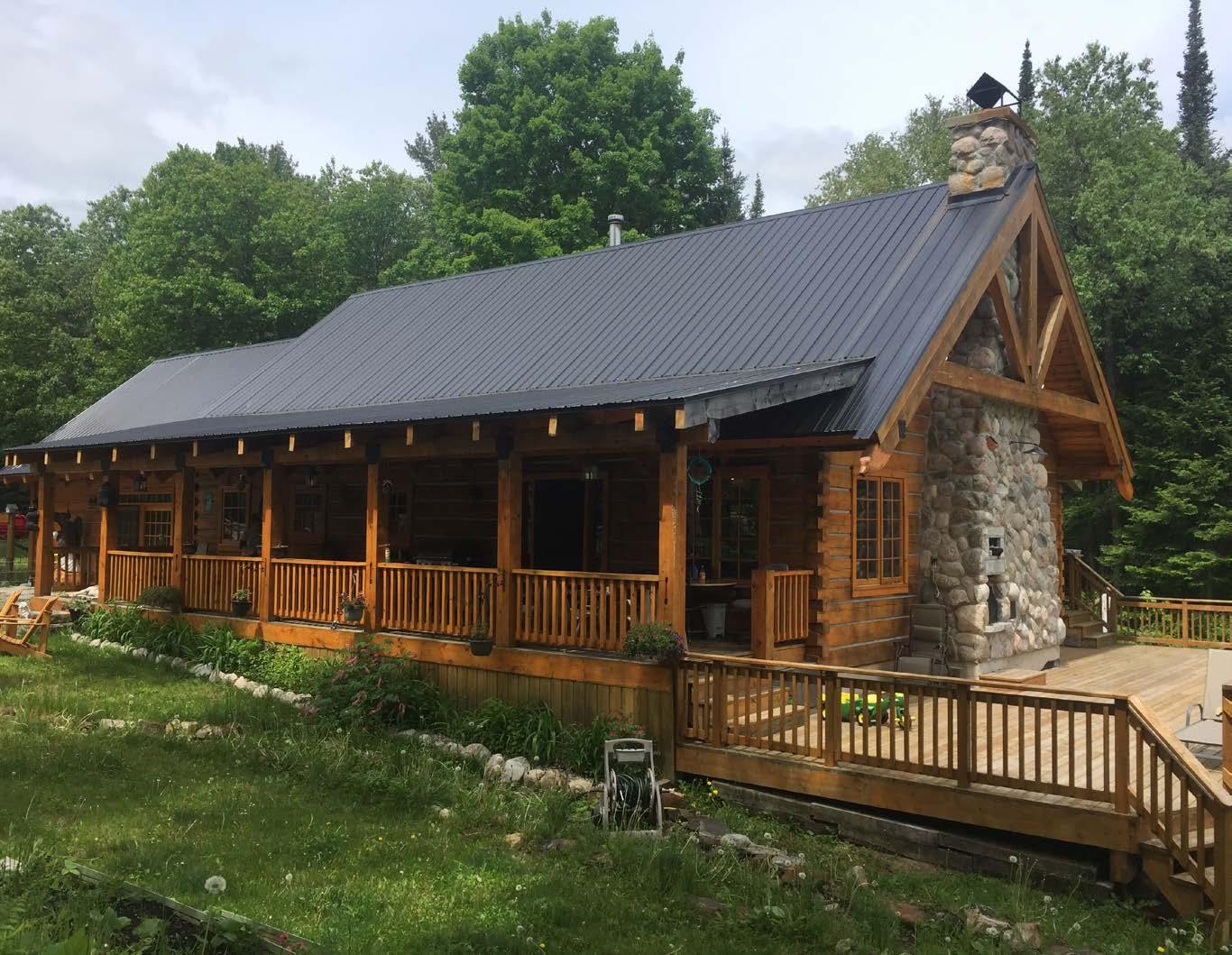
Russell Jacobs - York, Pennsylvania
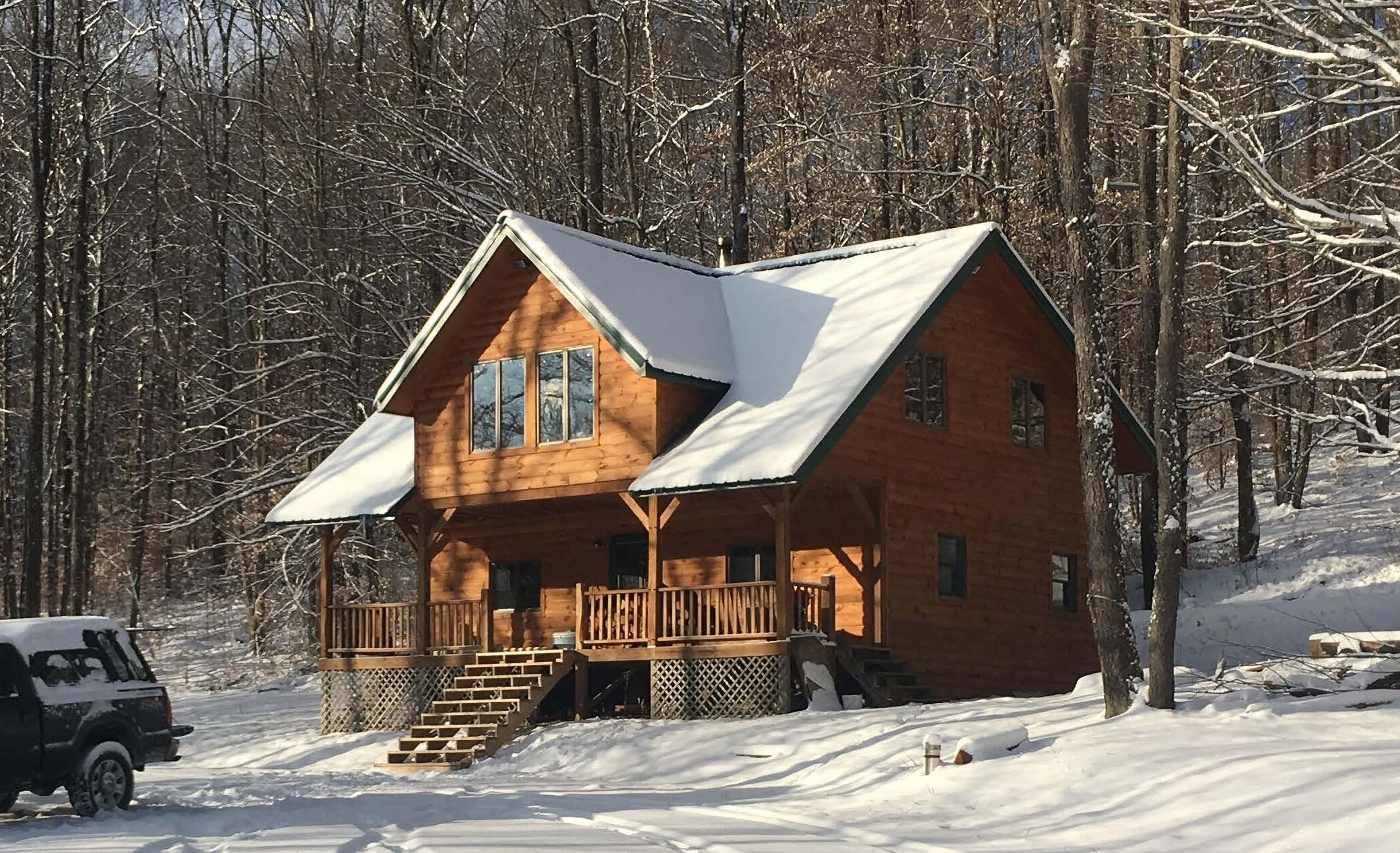
SAWMILL: LT40 BLADES: DOUBLEHARD
By The Numbers - 1,472 total square feet - 8,000 board feet of white pine, white oak and red oak - 99% of project completed with Wood-Mizer sawn lumber - 3 years to complete - $10,000 saved

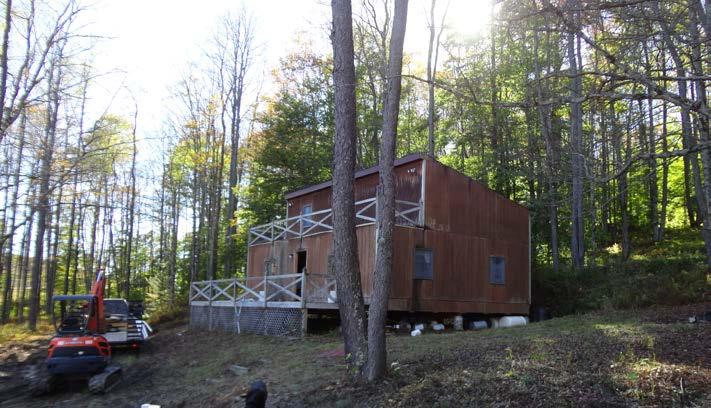
By Samantha Alexander

With an existing cabin already in place, Russell Jacobs used his expertise as an engineer, along with several helping hands from family and friends, to completely renovate his cabin. “My 80+ year old dad helped me make most of the flooring and shiplap siding in my home shop,” said Russell. He also had help from his sons who did the timber framing and his wife who kept the crew fed and lent her hand at installing the shiplap inside.
One of the amazing things about Russell’s cabin is the variety of wood used to complete the project. From the red oak floors and white pine shiplap walls to the white oak kitchen cabinets and the dawn redwood porch swing as an exterior accent piece, they all work together to give the cabin a unique, one of a kind look and feel.
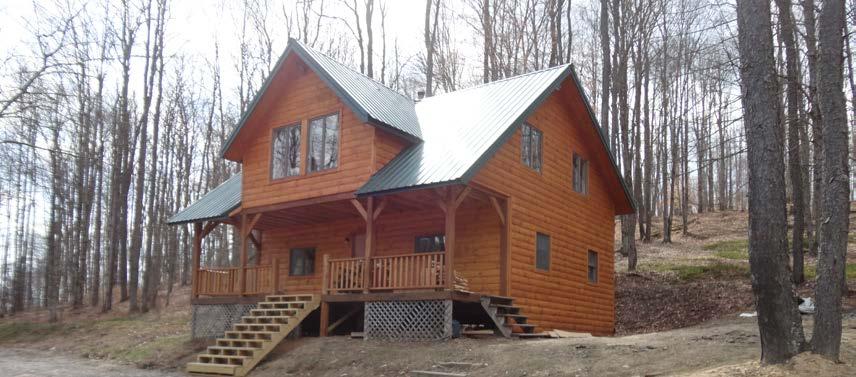
BEFORE AFTER
The cabin is also housing many of Russell’s furniture creations as well. “For furniture, last winter I made five of the exact same beds with five different woods. Cherry (cut on the property), white oak, white ash, shag bark hickory and pignut hickory,” said Russell.
Russell’s first portable sawmill, a 1988 LT40 model, was used for the majority of the project. However, Russell decided to upgrade to the LT40 WIDE portable sawmill a few years ago. “I enjoy building things,” said Russell. “I always wanted to build a cabin. I plan to timber frame a garage on site in the next year.” For now, he appreciates the positive comments he receives on his renovated cabin home.
“I n 2003, I saw a small timber framed structure in Branson, MO, and believed I could build one. Started cutting beams in 2004, resawing them in 2012. Being an encouragement to others to build their own timber frame kept the passion going. This project was only possible because of the Wood-Mizer mill. It truly is the best, most durable band mill on the market. I tell anyone who is looking for a mill that Wood-Mizer is the only mill to saw with.” – Bruce Politte
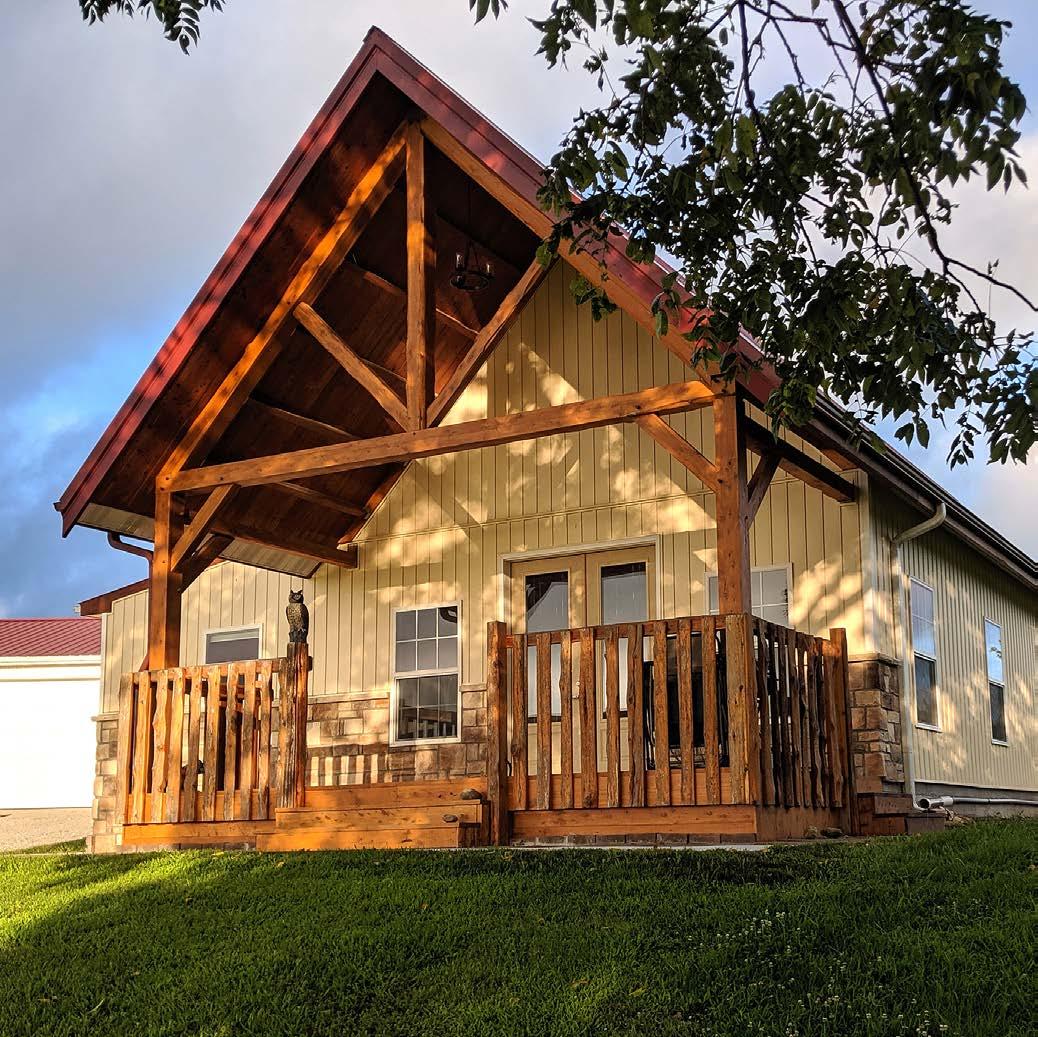

Bruce Politte – Forsyth, Missouri SAWMILL: LT40 HYDRAULIC BLADES: DOUBLEHARD Project Description: Timber framed ranch home built as a retirement project
By The Numbers - 1,664 total square feet - 11,500 board feet of red/white oak, eastern red cedar, and black walnut - 85% of project completed with
Wood-Mizer sawn lumber - 3 ½ years to complete - $35,000+ saved


3RD PLACE Small Homes & Cabins
“I n 2011, chasing a boyhood dream, I set out with little knowledge and a Wood-Mizer LT40. I watched every Wood-Mizer video and any cabin milling I could get my hands on. With the help of friends and family, we harvested all the pine timber from the 10 acre cabin parcel, and maple/oak for the cabinets on a second family woods. We worked weekends when time and funds allowed. Building the cabin without borrowing money took longer, but made it more satisfying in the end. My Wood-Mizer mill turned a dream into reality.” – John Stickel
John Stickel – China Township, Michigan SAWMILL: LT40 BLADES: DOUBLEHARD Project Description: Log cabin on the edge of Pigeon River Forest
By The Numbers - 1,260 total square feet - 27,000 board feet of red pine, maple, and oak - 95% of project completed with Wood-Mizer sawn lumber - 6 years to complete - $80,000 saved


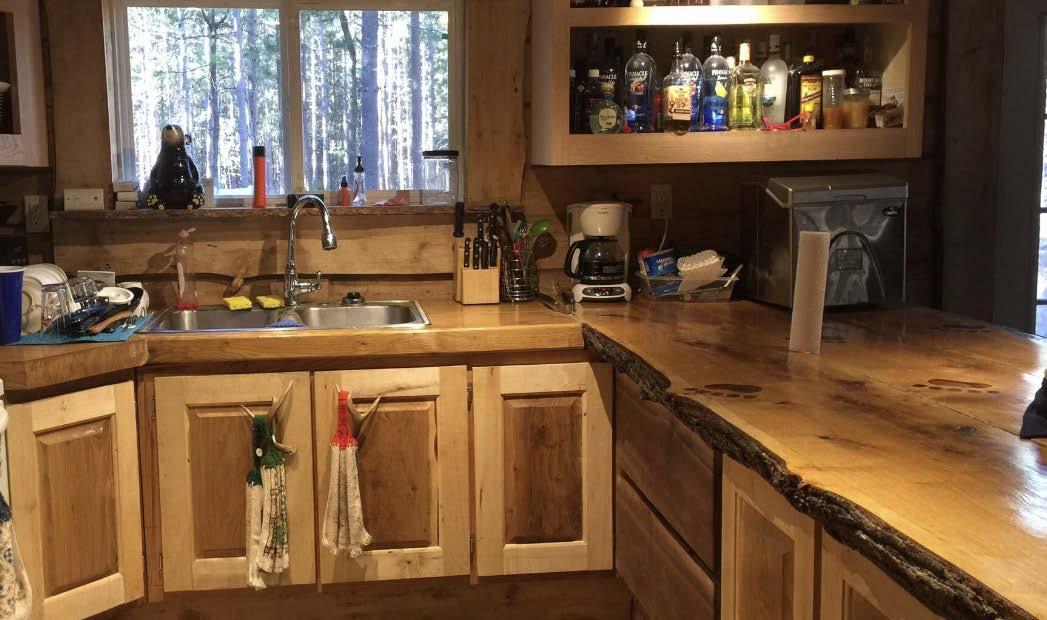
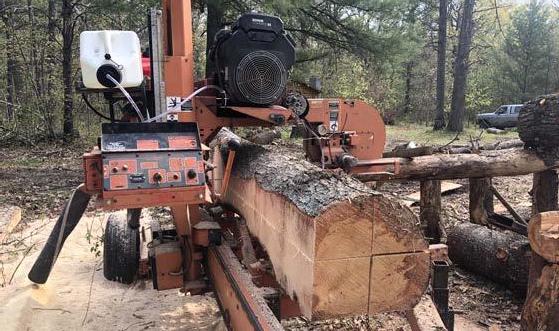
PROJECT SHOWCASE Homes & Major Structures
“V
ery satisfying to use timber off our own land and mill it ourselves for a family home. Our wood was just a small part of the overall project, the Net-Zero Energy use, mechanicals, concrete and steel work are main features.” – Daniel Guyer
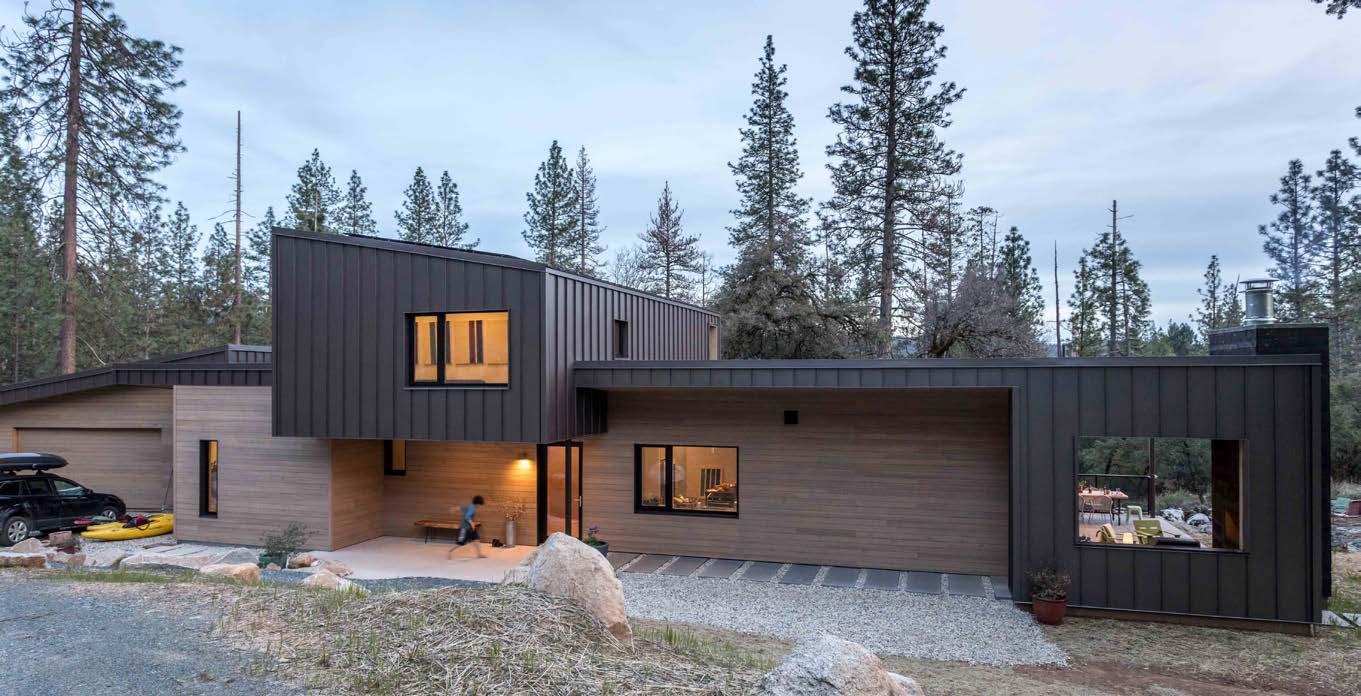
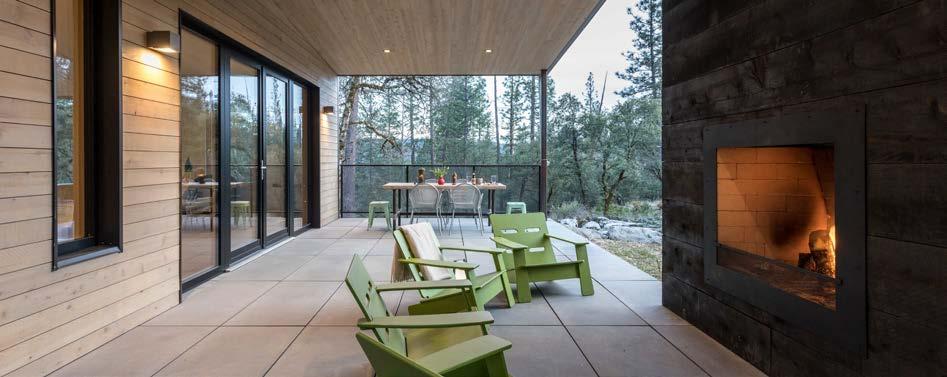
Daniel Guyer – Pike, California SAWMILL: LT40 HYDRAULIC BLADES: DOUBLEHARD Project Description: New energy-efficient home featured as the Fine Homebuilding Magazine 2018 House of the Year By The Numbers - 2,500 total square feet - 4,000 board feet of cedar, black oak, black walnut - Siding, soffits, balcony deck, kitchen cabinets completed with Wood-Mizer sawn lumber - 1 year to complete - $7,000 saved
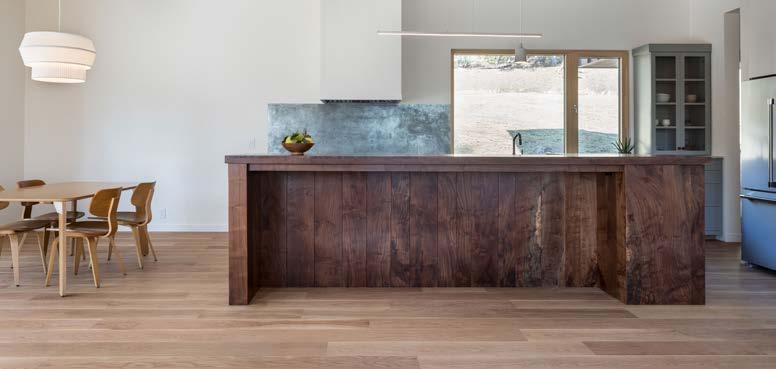
PROJECT SHOWCASE Small Homes & Cabins
“I
was looking for a room that I could complete using the trees that I had available to me. I really wanted a man cave, and it just seemed like the way to go. It has turned from my man cave to a community venue. I am ecstatic at having such a nice place.” –Andy Ard
Andy Ard – Pamplico, South Carolina
SAWMILL: LT70 BLADES: DOUBLEHARD Project Description: Former man cave has become a local venue for small weddings and parties By The Numbers - 1,200 total square feet - 18,000 board feet of white oak and walnut - 90% of project completed with Wood-Mizer sawn lumber - 1 year to complete - $50,000 saved


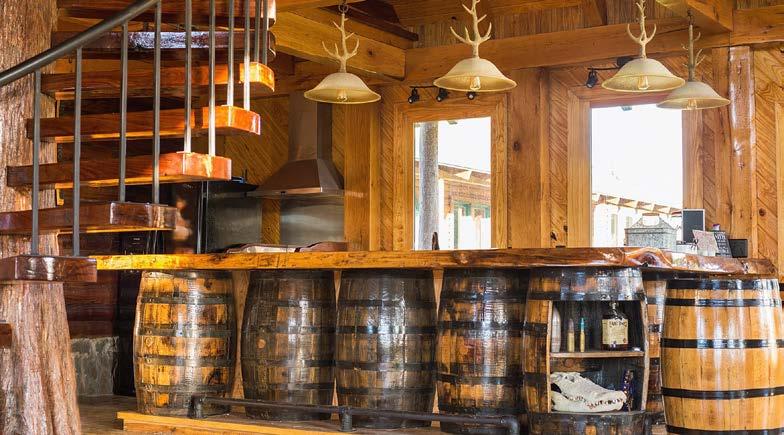