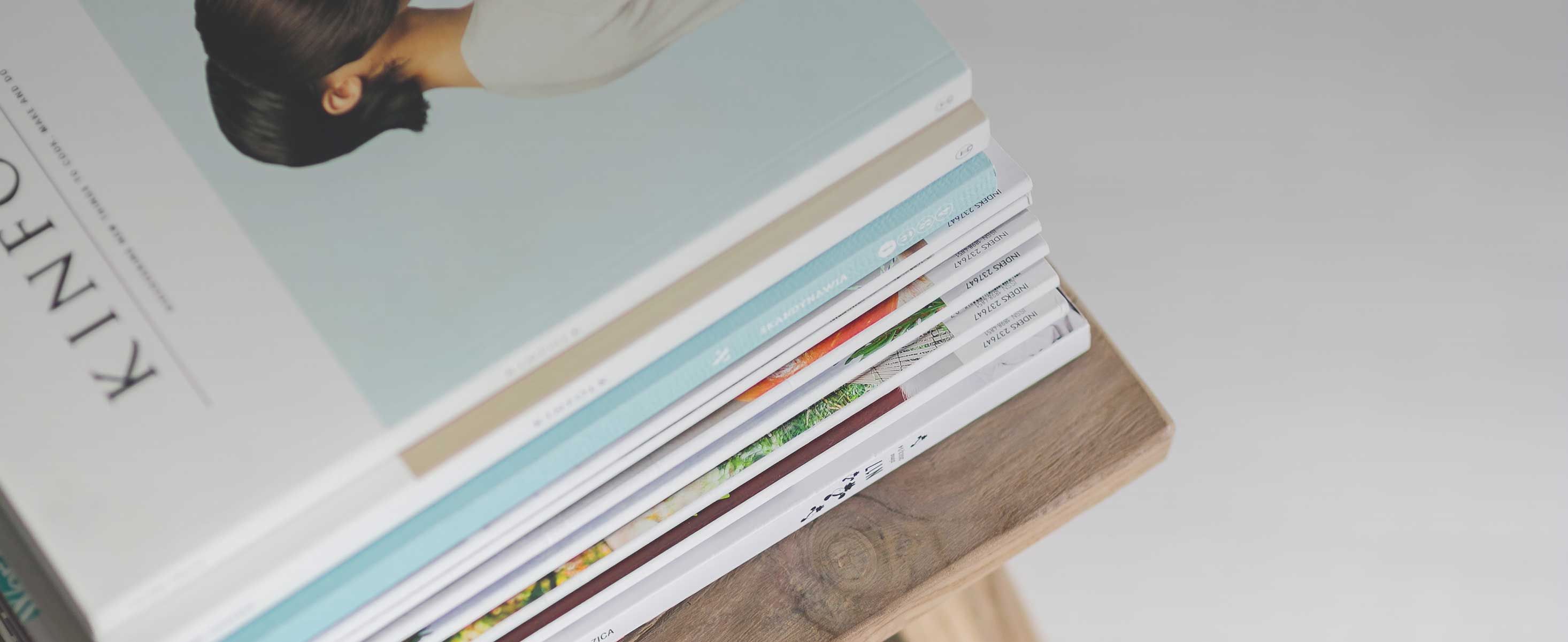
2 minute read
Greening the black gold with digital twins
MachineMax, explains
The oil and gas industry is a dynamic sector driven by the imperative for enhanced productivity and performance. Amidst its digital transformation, the adoption of technologies like artificial intelligence (AI) and the Industrial Internet of Things (IIoT) is central to this evolution. Digital twin technology, an innovative advancement from IIoT, is revolutionising how the industry manages assets, optimises operations, and reduces both costs and unplanned downtime.
In today’s competitive landscape, oil and gas companies are focused on transforming their operations to improve the reliability of assets while reducing costs and emissions. The move towards carbon neutrality is crucial, and digital twin technology offers a promising pathway to addressing these challenges by significantly enhancing operational efficiencies. These technologies include smart sensors, mobile connectivity devices, cloud computing and AI, which collectively enable a robust integration of operation technologies with information technologies.
Digital twins provide a comprehensive digital representation of physical assets, capturing essential data like machine performance and environmental conditions. This virtual testing ground facilitates real-time adjustments and improved decision-making, enabling facility operators to simulate various operational scenarios without halting production. This is particularly effective for minimising environmental impacts while maintaining costeffective operations.
For instance, digital twins can model the effects of adjusting pump speeds to alter flow rates in pipelines or optimise compressor operations to reduce energy consumption without affecting output. Another key application is in leak detection, where digital twins simulate pipeline systems to identify potential failure points, preventing environmental contamination.
Meanwhile, digital twins can also test emission control technologies, such as carbon capture and storage, helping to choose the most effective method to reduce greenhouse gas emissions. They can also support resource management, like water recycling in hydraulic fracturing or minimising chemical use to reduce waste.
This proactive approach enables the identification and refinement of the best possible strategies to implement sustainable practices. However, the deployment of digital twins is not without challenges. Siloed information systems are still a significant barrier. With intelligent sensor technology, advanced telematics and collaborative cloud management, seamless integration and real-time data processing across platforms are achievable. These technologies enhance the granularity of data necessary to model and simulate complex operational scenarios while making a single source of data accessible to a variety of stakeholders, thereby enabling real-time interventions.
Looking ahead, the strategic deployment of digital twin technology holds immense potential for transforming the oil and gas industry. Beyond immediate operational improvements, digital twins are pivotal for long-term planning and strategic decision-making. They allow companies to simulate future scenarios, evaluate the impact of operational changes and plan technological upgrades. This not only bolsters sustainability but also secures a competitive advantage in an increasingly environmentally conscious market.
Offering more precise control over emissions and a unified platform for continuous improvement, digital twin technology will play a pivotal role in the industry’s future, transforming challenges today into opportunities for sustainable growth tomorrow.