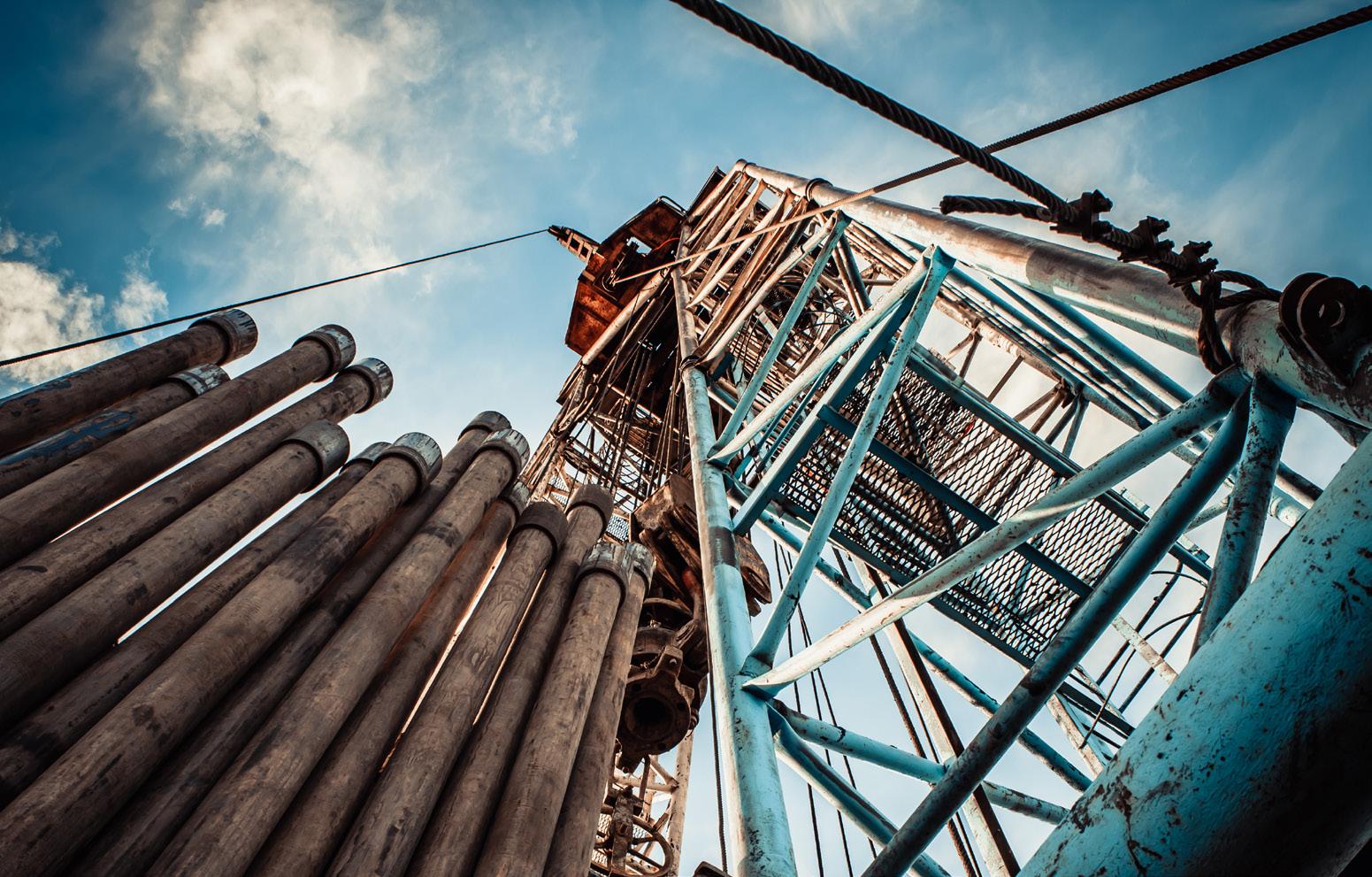
4 minute read
Enhancing Wellbore Integrity with Intelligent Deployment and Advanced Well Architecture
The problem with cement
Cementing wells comes with a set of risks. In deep well environments, achieving cement seal integrity is challenging for a multitude of reasons, including losses, a depleted reservoir, quality of cement, and equivalent circulating densities limitation. There is also a prohibitive cost to pay in terms of sustainability both from the cement itself – which is carbon intensive in production – and from the explosives used to perforate the casing. Due to the need for installation of an even smaller casing within the casing that has been cemented and perforated, the net result is a relatively small production area.
Advanced Well Architecture (AWA)
The completion concept of Advanced Well Architecture (AWA) drastically reduces risk and variability in operations by delivering flexibility to the number of zones, thus mitigating for reservoir uncertainties, and optimizing well construction through standardized structural design.
AWA is comprised of multiple components, with award-winning technologies like the Welltec Annular Barrier (WAB) at the heart of the concept. Instead of drilling an oversize hole to accommodate cement, a new wellbore can be drilled to the required dimension and the production casing then utilizes a WAB to ensure zonal isolation. Zones can then be controlled by opening and closing the flow valve which is mounted on the downhole actuator in the upper completion. This system provides full zonal isolation and zonal control, delivering a far simpler completion than could otherwise be achieved in a multizone cement scenario.
The architecture of the architecture
In addition to the industry proven WAB for zonal isolation, AWA is comprised of the Welltec Flow Valve (WFV) with Dual Position (DP) for inflow control, with the option for addition of a Downhole Actuator (DHA) onto the upper Intelligent Completion (IC) extended inner string, which engages with and mechanically shifts open the WFV-DP just prior to landing off the upper completion, providing flow access to the previously isolated zones.
The WFV is a full bore valve that can be used for both production and injection purposes within the lower completion, and its rugged design enables rotation during liner deployment. With specially designed inlets and sealing system, the WFV is qualified to open and close multiple times under differential pressure whilst maintaining flow, for both injection and production. The full bore design of the WAB provides high pressure zonal isolation and creates a completion which facilitates more efficient and smooth intervention in the future.
The DHA is a robust, bi-directional shifter, designed to be deployed on the tailpipe of the upper or intermediate completion to facilitate the mechanical opening and closing of the WFV. The DHA provides controlled access to multiple zones isolated during the safe deployment of the upper and intermediate completion. Run in combination across an open hole reservoir section, this system facilitates full bore, cementless, zonal isolation and control.
Tried and tested in the most challenging deepwater setting
The operational flexibility and equipment standardization provided by AWA has been a key factor in proving the concept’s worth in some of the most challenging environments. Of more than 50 completions made on behalf of multinational operator Petrobras, several AWA systems have been installed in the ultra-deepwater Brazilian pre-salt. Reservoir uncertainties and limited data can make it difficult to predict the number of zones required. Additionally, in the deepwater case, severe loss scenarios made it challenging for initial intelligent completion designs as they were not compatible with the managed pressure drilling (MPD) techniques being applied to drill the well.
Petrobras decided to design and implement a new intelligent completion design to reduce the time and cost per well. Usually, the well architecture associated with intelligent completion wells in pre-salt areas would preclude a separate run for perforation after cementing. AWA allows the steps of cemented then perforated casing to be skipped and facilitates a single operation for deployment of a simple and reliable full completion – this totally eliminates the cost of cementing the reservoir section.
Utilizing the AWA system, Petrobras was able to tailor their completion design as per their required specifications and gain several benefits. The open hole intelligent completion applied with the AWA system enabled operational flexibility and equipment standardization, meaning the same completion design could be adopted for either a single or multi-zone completion. This further allowed the operator to optimize and finalize the completion design based on reservoir data gathered during the drilling and logging phase, essentially at a much later stage than normal, thus giving them best production capability with full flexibility and minimal inventory.
In this case, a directional injection well was constructed in approximately 15 days less than the most recent configuration well (including drilling and completion). In a more complex five-phase well scenario, the savings would be in excess of 25 days.
Continued product development – Welltec Expandable Anchor (WEA)
Metal Expandable Packer (MEP) technology developed by Welltec has an established and proven track record across the globe. The forthcoming introduction of an all-metal Welltec Expandable Anchor (WEA) will assist operators at various stages of drilling and completion, offering a reliable, robust solution for application as a liner hanger, anchor, or tie-back.
With the modular addition of metal slips, the expandable anchor can be incorporated into designs to help overcome challenges with highly deviated wells, high-pressure-high-temperature conditions, challenging geometry of new or existing wells, enabling hang-off and anchoring of the liner or casing with a previous casing or open hole.
The high expansion capability of the new product helps cover a wide range of applications with one solution, covering different size casings. The WEA is qualified to API19LH and V0 high pressure and temperature standards, which can be used for injection and production wells with the possibility of modification to address specific requirements.