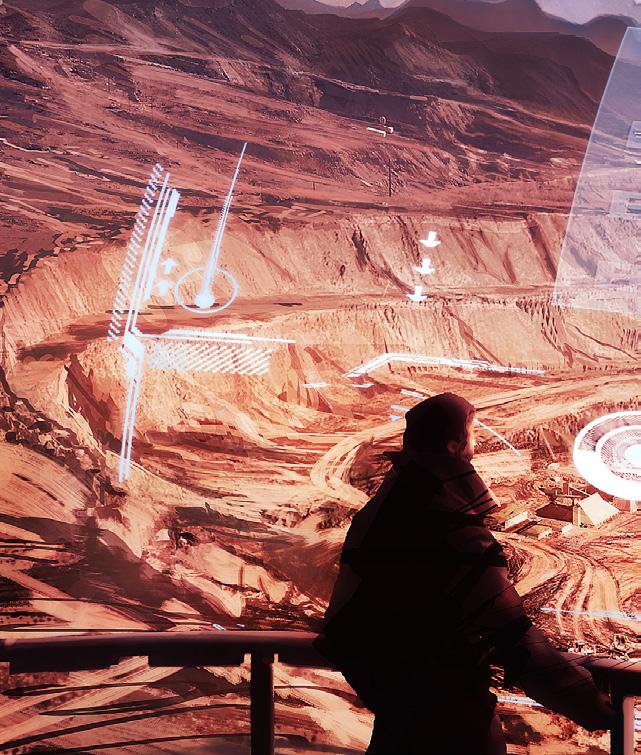
11 minute read
Four trends for tomorrow’s success
Future of Mining
are currently using driverless haulers and automated drill extractors to move metals with proven results in efficiency and productivity. Robotics and automation in mining is a particularly exciting proposition since it connects directly to innovation with AI and machine learning technology. In a recent poll conducted by Mining IQ, 77 percent of mining professionals view automation as a top priority. Fully 40 percent say automation is “more important than ever.” Robotics can be particularly advantageous in replacing traditional shovel and extraction processes used by humans. The concept of a continuous robotic mining system will evolve as technology replaces manual processes and computer-controlled and powerful machines extract the most minerals in the shortest amount of time. “Smart” automated conveyor systems are already being used for speedy material transport. Like drones, mine robots can also be used to replace humans in performing radiological, inspection, and survey tasks, especially in small areas or an inhospitable environment, such as abandoned mines. Soon, abandoned mines with previously inaccessible minerals can be reopened with robots successfully doing extraction that just was not possible before. “Automation at new scales – much smaller than today’s – will allow us to operate swarms of small and low-cost autonomous equipment in mines designed only for machinery, thus allowing new deposits to be mined,” Yeates adds. “Hydro-metallurgical techniques and nanotechnology will get us closer to in situ mining, a much smaller environmental footprint, and lower energy, capital and operating costs.”
Environment accords, like the Paris Climate Agreement, along with an increasingly global awareness of the value of our natural resources is putting more and more pressure on mining companies to address sustainability. Fortunately, many of the technological innovations we have already discussed reduce fuel consumption, emissions, waste, and water use in mining operations. Even the rehabilitation of mining sites through new biological and chemical solutions for environmentally friendly waste management and acid mine drainage can allow ecosystems to recover. But being green is not just a piecemeal effort for the industry or a trendy marketing campaign. Going forward, the onus will be on mining operations to change their entire business model and adhere to the concept of Corporate Social Responsibility (CSR). “What I’m most excited about for the future is the prospect of mining companies embracing the role of being a responsible steward of the environment,” Dr Priscilla P Nelson, dept. head and professor, department of mining engineering, Colorado School of Mines, adds. “We have to find a way of participating in the circular economy and identifying creative solutions for reducing raw materials in mining operations by reusing resources and recycling water and materials. This could change the public perception of mining and put the whole industry in a more positive light.” Today’s shift toward CSR sets the stage for concepts like green mines or zero-waste mining to become increasingly popular. The goal of greening mining is to reduce the environmental impact of mineral and metal extraction and processing, with a focus on new technologies, smarter mining operations and processes, and sustainability best practices. The good news for mining companies is that “going green” can have its financial benefits. The Green Mining Initiative cites one project in Ontario, Canada that resulted in a 40 per cent reduction of energy consumption with an annual savings of up to $4 million. “Tailings are going to be an issue with lower grades of ore,” says Dr. Nelson. “If you go from an ore that has ten percent of the metal mines are looking for to one-tenth of a percent, that means that tailings are going to increase by a factor of ten, which is pretty significant. This will drive mines to use more advanced technology, like spectroscopy, to decide what to take out of a mine and what to leave down there. The retooling of processing to be more flexible with different grade of ore will also be needed.”
New frontiers of deep sea, space, and rediscovery
As the industry looks further into the future for tomorrow’s opportunities, several key areas emerge as the front runners. In Twenty Thousand Leagues Under the Sea, Jules Verne predicted the future when he described mining operation on the ocean floor. Now that vision is starting to come true. Deep sea mining is a relatively new concept in mining, and undersea technologies are just beginning to scratch the surface of what is possible.
Future of Mining

The prospect for significant extraction opportunities lies right on sea floors, especially considering that we have only explored five per cent of the deep ocean. The deep sea has created formation with highly valued metals that can be mined. Polymetallic modules — softballsized formations that litter the seabed — are rich sources of nickel, cobalt, copper, and magnesium. Polymetallic sulphides form when hot water from the earth’s crust meets cold water, resulting in smokestack formations rich in iron, silver, and gold. Underwater crust formations and mountains (mostly in the Pacific) are rich in rare earth metals, like cobalt, vanadium, molybdenum, platinum, and tellurium. Space mining might seem like something out of science fiction, but it is a future frontier that may not be too far off. Some experts contend that asteroid mining may be a reality by 2025. Why asteroids and not Mars first? Beside containing valuable minerals like platinum and palladium, reaching an asteroid that is near to earth requires far less energy than reaching a far-away planet like Mars. NASA and advocates of space mining have noodled on the many ways that asteroids could be mined, with most ideas focused on launching an interconnected army of robotic devices and crewless mining spaceships to extract minerals and send them back to earth. Some say that human could soon follow, but the low surface gravity of asteroids offers some serious obstacles. Even though Mars is a much further destination, the red planet is estimated to be rich in ore and other valuable minerals. Also, if colonization is the end goal, mining activities on a planet like Mars may allow colonies to be self-sustainable. NASA continues to tap into fresh minds in academia in brainstorming new mining robotics designed for celestial surfaces like Mars.
The future of mining looks bright
There is no doubt the mining industry faces some significant challenges. The increasing demand for minerals and metals coupled with the pressure to increase output cost-effectively puts many mining operations in a tough spot. Fortunately, digital transformation and new technologies offer mining companies golden opportunities to become more efficient, boost production, and cut costs while making the work environment safer. And, although the push for sustainability and environmentalism may have headwinds, mining operations are becoming increasingly green and also benefiting from the push for materials to build electric cars and renewable fuel sources of energy. Finally, future opportunities for mining in the deep sea, space, and abandoned mines mean the industry has more frontiers to conquer.
Digitalisation
Practical applications of digitalisation in mining, minerals, and metals business
According to World Economic Forum, digitalisation in the mining, minerals, and metals industries has the potential to deliver over $425 billion in shareholder, customer, and environmental value by 2025. Mo Ahmed, global segment solutions metals at Schneider Electrics explains
Much of this value will come in the form of operational effectiveness, increased productivity, faster decision-making, and enhanced safety. However, cashing in on the digitalization opportunity will require strategic planning, strong partnerships, the realignment of the employee culture, and appropriate digitalisation technologies. Companies are looking to modernise operations to remain competitive. These operators are faced with the issue of working within silos. Many workers are in separate departments working on spreadsheets, highly customised applications, and out-of-date solutions with no real ability to share the data they produce. Such a siloed mode of operation leads to inefficiencies that propagate mistakes and that prevent streamlining of processes. The challenge is how to best get started down the digitalisation path. Today, open architectures are accessible to enable digitalisation by providing tightly coupled linkages with a cybersecure envelope across the smart device, edge control, and apps and analytics layers of mining, minerals, and metals enterprises. This approach increases field to enterprise transparency and enhances value chain visibility and efficiency all along the asset life cycle. The nature of digitalisation is evolution and not revolution. Embracing a gradual, scalable approach, enables the measured introduction of modernisation in the form of production, maintenance, operator enablement, and workforce building blocks. These days, competitive advantages in the mining, minerals, and metals industries rely heavily on an ability to gain holistic insight of operations, an Integrated Operations Management approach, from design to maintenance.
Digitalisation life cycle impact
1 Efficiency starts in the design phase Such a holistic view, enabled by an open architecture, provides new linkages and deeper integrations across core power and process systems. On the design and engineering front, for instance, hybrid DCS (HDCS) and PLC’s can integrate seamlessly with configuration, analytics and digital optimization technologies that would have been impossible or extraordinarily complex to implement in the recent past. Engineers can now configure and operate an entire automation system based on the distributed control system, with gains such as engineering time and cost reduction, minimized downtime, new testing capabilities, scalability, or rich access to asset information. Also consider the example of digital twin. According to Gartner, 50 per cent of large industries will use digital twins by 2021. These software simulation tools provide mining, minerals, and metals operators with virtual models for both the engineering and design phases of a project and for refinement of operations. A digital twin’s power is that it allows engineers to observe the physical asset’s behaviour without spending money to build it, and then improves the overall design by iterating through different operating conditions. 2. Drive production management efficiencies Improving productivity across the value chain is critical for maintaining competitiveness. This can be achieved by addressing in an integrated way, different aspects that impact production activity – from planning, when a Unified Supply Chain Management help achieving agile and collaborative decisions between multiple sites in the value chain network for better scheduling; to execution by enabling process stabilisation and optimisation and providing operator support in helping to drive machine productivity closer to process limits. Continuous operations are the key to solving many production issues and to improve. MMG, a mining
Digitalisation
company that operates globally, has emerged as a reference in delay accounting, the measure of lost time when operating assets or processing. By using a standard approach MMG has increased asset utilisation by at least 10 per cent across multiple global sites. EcoStruxure Advisors, are a specialised suite of smart manufacturing apps and digital services that also provide collect, measure, and analyse cloud-based and plant-wide data and recommend cost effective actions to take for continuous improvement. Some of these advisors use machine learning techniques to better tune mining, minerals, and metals processing plants. Specific plant parameters are set such as speed, and how much chemical is added, for example, to achieve an optimal operating point. 3. Tighter management of energy to reduce costs and guarantee uptime, while fostering sustainable operation Despite efforts, overall energy usage is rising. Demand for electrical energy in the copper industry, for instance, is forecast to grow at four per cent (CAGR) through 2026. Better control of these costs using digital solutions in now possible. Energy is one of the top five expenses for Saint-Gobain. They have saved millions of dollars in energy costs working out their energy planning and improving stages using cloud-based energy management tools like EcoStruxure Resource Advisor. By being focused on buying energy smarter and using it efficiently, and centralising energy procurement, resources are also freed up to deliver leading-edge, sustainable solutions. Through use of digitised technologies, plant operators can now track, and control energy use based on the time of day, and trim consumption when grid-wide use and prices peak. During execution, in many remote sites, microgrids are beginning to play a more important role in maintaining business continuity. The newest generation of microgrids has become much smarter due to the integration of digitalised, predictive technologies. Cloud-based solutions like EcoStruxure Microgrid Advisor, for example, serve multiple roles such as providing a Human Machine Interface (HMI) for site managers, processing demand / response requests, optimizing output decisions based on energy tariff rates and weather forecast predictions, and factoring in user / customer constraints. As a result, energy bills can be minimized, and carbon footprint decreased. 4. Digitalised asset management to efficiently extend asset life Within the mining, minerals, and metals industry, 40 per cent of OPEX is generated through maintenance activities. In fact, most asset maintenance costs will far exceed capital costs over the life of the asset. In some mining operations, more than 60 per cent the total site workforce is exclusively dedicated to maintenance. During planning, comprehensive Enterprise Asset Performance Management (APM) improves asset performance by integrating risk and asset criticality into an overall asset performance management strategy. The software generates optimised maintenance and spare parts strategies by first looking at the company’s business strategy and objectives, and then prioritising actions down to an individual asset level to maximise return on asset investment, establishing recommendations to choose from reactive, preventive, or predictive maintenance. Good example on preventive maintenance is EcoStruxure Asset Advisor, cloud-based maintenance solution that brings a proactive approach to managing power assets, addressing issues before they become critical incidents. During execution, augmented reality is beginning to change the way maintenance in remote sites is being performed. It provides maintenance technicians with tablet-driven graphical views of the inside of machines, without ever having to open a panel, which greatly enhances worker safety. Instant access to real-time information speed ups identification of the issue and visually displays the proper procedures for applying a fix. This helps to reduce the human error commonly associated with traditional maintenance procedures.
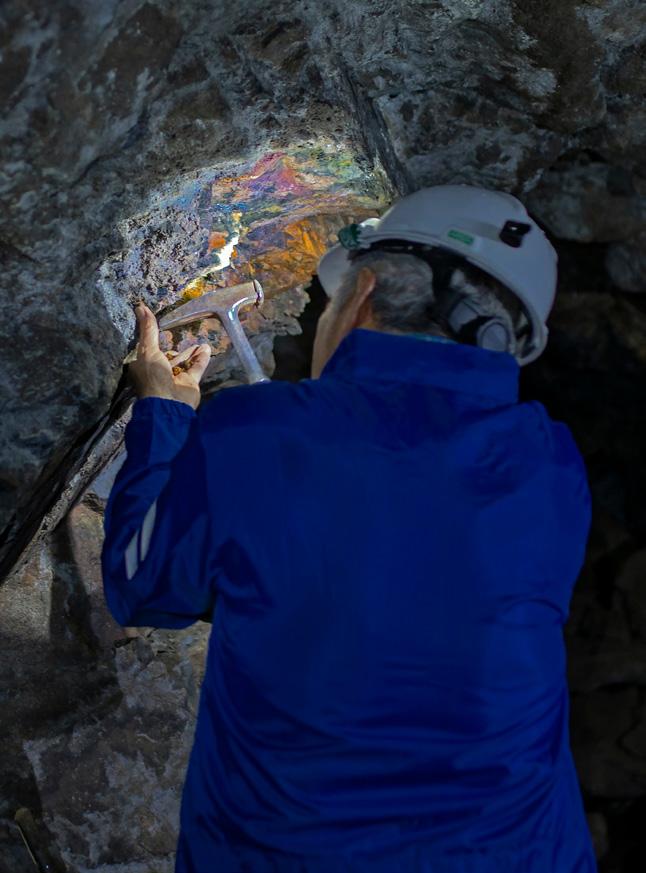