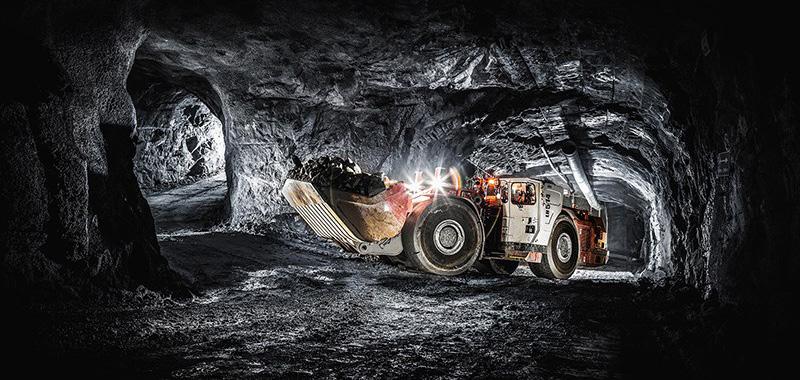
8 minute read
Updates
News
Blockchain can trace carbon emissions for mining
The World Economic Forum’s Mining and Metals Blockchain Initiative (MMBI), released a proof of concept that uses distributed ledger technology to track embedded greenhouse gas emissions. A collaboration between seven leading industry players and the World Economic Forum, the initiative has hit an important stage of development following its launch in October 2019. The successful completion of the proof of concept, named the COT, a Carbon Tracing Platform will be critical in helping to ensure traceability of emissions from mine to the final product. With a focus on end-to-end traceability, the COT platform uses distributed ledger technology to track CO2 emissions. The founding members of the MMBI – Anglo American, Antofagasta Minerals, Eurasian Resources Group, Glencore, Klöckner & Co, Minsur, and Tata Steel joined forces in October 2019 to design and explore blockchain solutions to accelerate responsible sourcing in the industry. By pooling resources and costs, the mining and metals companies aim to accelerate future adoption of a solution for supply chain visibility and ESG requirements. Developed in collaboration with industry experts, supported by the Dutch blockchain champion Kryha and Consortium Advisor Susan Joseph, it not only tests the technological feasibility of the solution, but also explores the complexities of the supply chain dynamics and sets requirements for future data utilization. In doing so, the proof of concept responds to demands from stakeholders to create “mine to market” visibility and accountability. “There is an increasing demand for metals and minerals, and an increasing demand for sustainable and responsible and traceable supply chains,” said Jörgen Sandström, Head of Mining and Metals Industry, World Economic Forum. “There is a potential to create a full value chain view with downstream visibility, and in partnering with regulators and aligning our work with robust ESG standards, sustainability certification schemes and assurance frameworks.” This work lays the foundation for the next phase of the development and reinforces comprehensive feedback sessions with stakeholders. It also supports the MMBI vision to enable emissions traceability throughout complex supply chains and to create “mine to market” visibility and accountability. “The distributed nature of blockchain technology enables cross-enterprise collaboration and makes it the ultimate networked technology, Nadia Hewett, Blockchain Project Lead, World Economic Forum, said. “This opens exciting new possibilities that organizations otherwise would not have the capability to deliver on their own.” Peter Whitcutt, Marketing CEO of Anglo American explained that they are committed to solving the physical challenges of mining and creating value for all stakeholders as defined in our sustainable mining plan. “By leveraging cross-industry collaboration and the increasingly important role played by technology innovation, MMBI’s Proof of Concept can help to unlock the potential of blockchain to support a greater level of reporting transparency and drive responsible sourcing,” he said.
News
MacKellar Group adds to T 264 fleet in Australia

Four Liebherr T 264 off-highway haul trucks will be added to Dawson Mine in Australia for customer MacKellar Mining. MacKellar Group has purchased four additional Liebherr T 264 240 t / 265 ton off-highway haul trucks, adding to the fleet of five commissioned in early 2020. All nine of the
T 264 fleet will work at Anglo American’s Dawson open cut metallurgical coal mine in Central Queensland, Australia. The four new T 264, manufactured in Liebherr Newport News, Co. facility in Virginia USA, will complete pre-assembly in Mackay before travelling inland to
Dawson Mine for final commissioning.
The trucks will join the working fleet in early 2021. MacKellar Group is a mining and civil earthmoving company, founded in Australia in 1966. Mackellar Group chose to continue with the T 264 trucks for their 240-tonne fleet, stating “the T 264 provides efficient productivity for our clients by offering a true 240 metric tonne payload, and superior speed on grade. The many operator comforts also makes the trucks well accepted on site.” The fleet of trucks at Dawson mine are supported by Liebherr-Australia’s Mackay branch and on site-Liebherr technicians, another area that assisted the purchase of the additional four units. “Liebherr-Australia’s support has been excellent, starting from the beginning with the provision of professional operator training, through to support from their experienced technicians,” concluded MacKellar Group.
News
Normet SmartDrive performing remarkably inside the Finnish bedrock Epiroc wins large mining equipment and service order from Codelco in Chile
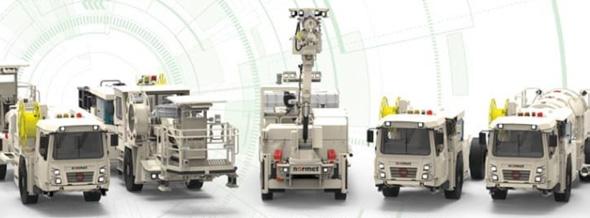
Normet’s new battery electric sprayer, the Spraymec 8100 VC SmartDrive performing remarkably inside the Finnish bedrock. The Blominmäki project is one of the biggest underground civil engineering construction projects up to date in Finland. It aims to construct a new wastewater treatment plant to serve more than 400,000 people and five cities and replace the old treatment plant in Suomenoja. The excavation project consists of circa 1,000,000 cubic meter caverns for water treatment processes, and 19 kilometres of water tunnels between the seacoast and the new plant. Normet’s battery electric sprayer, the Spraymec 8100 VC SmartDrive, was taking part in spraying the permanent sprayed concrete lining at one of the Blominmäki sites. The sprayer proved its worth in providing efficient, silent, and clean application process with low operating costs. “Air quality is extremely important when working underground” Pasi Hartikainen, who has been operating the Spraymec 8100 SmartDrive in Blominmäki, said. “It is one of the main benefits of having battery electric equipment that there are no diesel emissions”, Pasi describes his impressions on working with the new sprayer. In addition to battery electric drive, the new flag ship sprayer is equipped with automated boom control system SmartSpray, and concrete layer thickness optimization system SmartScan. “We have very demanding clients, and they will check through every layer of sprayed concrete,” Mikko Piirainen, Construction Manager for tunnelling contractor Kalliorakennus-Yhtiöt Oy, who’s sprayer fleet consists solely of Normet offering, added. “In the future, SmartScan will have a remarkable role in terms of providing best quality. Using SmartScan ensures the layer thickness is sufficient, and that there is no need to come back and spray again.”, Mikko adds. Codelco has ordered underground loaders, face drill rigs, rock bolting rigs and mine trucks, as well as several years of technical support and training, for use at the Chuquicamata underground mine project. Codelco, the world’s largest copper producer, opened the Chuquicamata underground mine in 2019. The company is transforming the century-old Chuquicamata copper and gold mine from being the world’s largest open-pit mine into a hightechnological underground operation. The transformation will extend the useful mine life by 40 years, according to Codelco. “We are proud to be a key partner of Codelco as it significantly extends the life of the Chuquicamata mine in the most productive, efficient and safe manner possible,” says Helena Hedblom, Epiroc’s President and CEO.
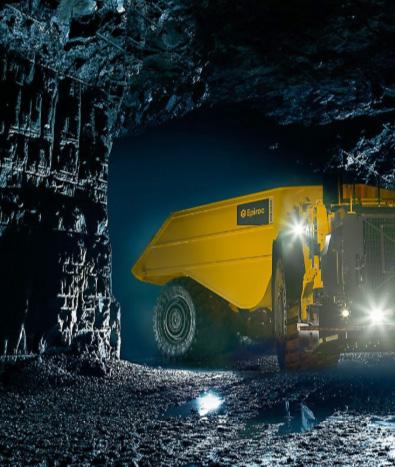
News
“Epiroc was chosen because it complied with all the technical, safety and performance requirements that Codelco demanded for the Chuquicamata Underground Mine Project, while being the supplier that provided the best economic proposal for all its equipment as a whole,” Juan Mariscal, sourcing category manager at Codelco, said. The order includes multiple units of the Scooptram ST1030 and ST18 loader, the Boomer S2 face drilling rig, the Boltec M bolting machine, and the Minetruck MT65, the highest payload capacity underground truck in the world. The machines will be equipped with 6th Sense solutions for automation, connectivity, and information management. The solutions include Epiroc’s Rig Control System, RCS, which makes the equipment ready for automation and remote control, and Epiroc’s Certiq system, which allows for intelligent monitoring of machine performance and productivity in realtime. Delivery of the equipment will take place later this year.
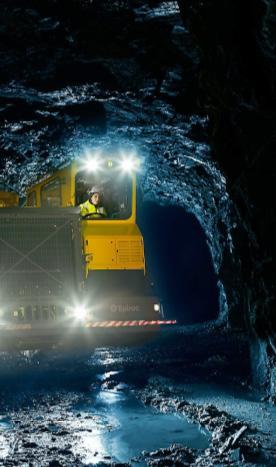
Next generation mining truck advances efficiency and productivity for lower costs
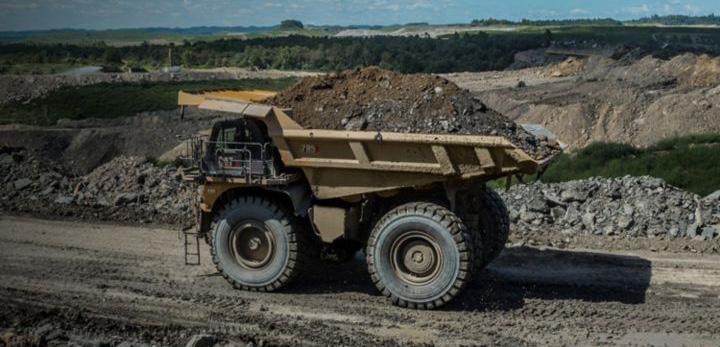
The Next Generation Cat 785 mining truck enhances operator safety and performance, provides more intuitive and predictable operation, delivers faster and easier access to data, and streamlines maintenance—to boost efficiency and lower costs. Leveraging the Next Generation concept, the new 150-ton class mining truck features an expandable technology platform, so it is future-ready. “The 785 was Caterpillar’s first large mining truck, introduced in 1985. It’s fitting that the first Next Generation Cat mining truck is the new 785—designed to enable mining operations to optimize productivity today and tomorrow,” David Rea, general manager of Cat Large Mining Trucks, said. “Cat Next Generation mining trucks feature a flexible technology platform and optional configurations that help each mining operation meet their goals.” Productive hauling begins with the operator, who sits in the new state-of-the-art cab, designed for efficiency, and equipped with features that automate functions. The Next Generation 785 offers a new integrated speed coaching feature to give feedback on how to operate the truck most productively. Truck responsiveness and controllability are enhanced through multiple upgrades such as the anti-lock brake system, dynamic stability control, enhanced traction control, machine speed limiting, hill start assist with anti-rollback, and cruise control. Additionally, new Auto Hoist control reduces dumping time and unburdens the operator. The improved payload monitoring system offers more accurate measurement and dipper counts as well as enhanced overload detection and carryback calculation and reporting—to inform operators and production managers. The 360-degree surround view camera delivers a full view of the working area to the operator. Inside the cab, guidance information, machine data and electronics controls are consolidated into two touch screens that eliminate clutter and promote efficiency. The spacious new cab features a walk-through sliding center console, increased legroom, and new cab air filtration system for operator comfort. The new deluxe seat boasts leather upholstery, air-adjustable bolsters, and lumbar support, heated and cooled cushions, dynamic dampening, and a 30-degree recline with thigh tilt and extension, so it comfortably accommodates operators of all sizes. The Next Gen 785 is powered by the proven Cat 3512E engine offering selectable power options, allowing operations to match the speed of the fleet or to speed up cycle times. Two tire options, 33R51 and 36R51 are available, to enable mines to optimize payload capacity. The larger tires allow a nominal payload of 142 tonnes (157 tons). The truck is available in multiple emissions configurations to meet different regulatory requirements around the world. The optional Tier 4 Final/Stage V emissions configuration has shown fuel efficiency improvements of as much as nine per cent. Advanced electronic powertrain controls deliver faster cycle times and acceleration, less spillage and reduced road maintenance in addition to improved engine and drivetrain life.