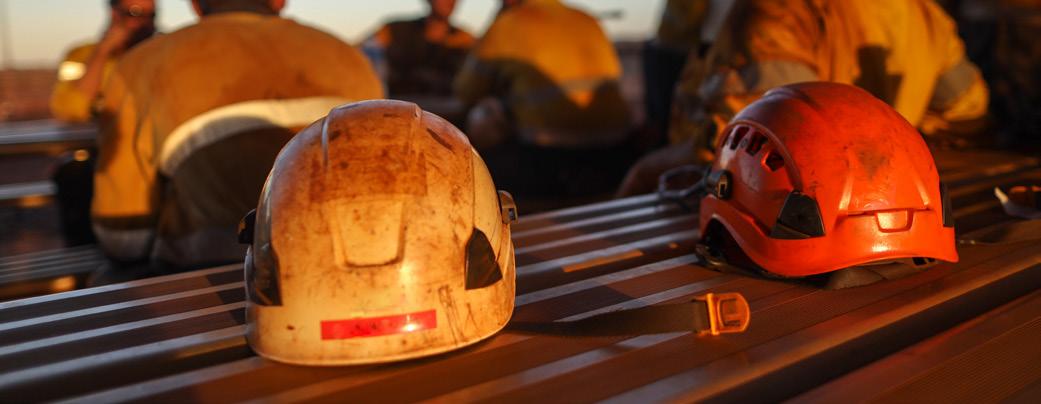
4 minute read
The era of Smart Mines
Safety
Zero is the only number
Underground mining has always been associated with higher risks that are different from those in other sectors.
Let us dive deep into some interesting statistics taken from different industries and find out if this is the case. The number of fatalities in the trucking industry, for instance, grew 6.6 per cent from last year taking the number from a mind-boggling 786 in 2016 to 840 in 2017. Trucking as a profession had a fatal injury rate of 26.8 deaths per 100,000 full-time equivalent workers, compared with 3.5 per 100,000 full-time equivalent workers for all professions. The fishing industry had a fatal injury rate of 99.8 per 100,000 full-time equivalent workers, the highest rate of any occupation. “Zero” is the only acceptable number when it comes to fatalities, but it is also important to see that number in a wider context. This includes having policies, training, and engineering controls in place to address the major causes of fatalities and injuries. Focusing our attention back to the underground mining industry, some hazards, such as ground instability, are inherent in the underground environment, while others may arise due to the complexity of mining processes and activities. If these risks are not managed properly, they can result in fatalities and serious injuries. According to International Council on Mining & Metals (ICMM), the highest number of fatalities in 2018 was attributed to mobile equipment and transportation, overtaking the fall of ground category that had consistently been the number one killer in past years. With advances in technology, some of these risks can be mitigated. The advent of Artificial Intelligence, Machine Learning, and Autonomy provides an opportunity to manufacture smarter machines that can improve safety by reducing exposure of workers to hazardous conditions. Major mining equipment manufacturers are excited and have started embracing these technologies with a strong emphasis on improving safety and productivity. Mining companies are adopting these technologies at a slow pace, but as is always the case, there are a few early adopters that set the benchmark for the industry. MacLean Engineering is one such company that quickly focused its efforts towards building a team of engineers dedicated to conceptualizing, designing, and implementing these technologies in the underground mining context. To illustrate an example, the MacLean Vehicle Monitoring System enables operators to monitor the health of critical systems and provides diagnostics delivering significant benefits to productivity, operating costs, and safety. Another example is the role MacLean Bolters have played in Ontario’s improved fall-ofground safety over the past three decades. With the first MacLean bolter entering the market in 1984, and over 500 units sold globally, the company has been able to replicate the Ontario experience in other hard rock mining jurisdictions, with the appropriate training program and safety culture backdrop. The key innovation with the MacLean bolter was in fact not one, single feature, but instead a series of design elements that work together to deliver accuracy, speed, versatility, and, most importantly, a safer application environment for operators. Last but not least, MacLean has been working on its fleet electrification program for the past three years and we are now able to offer mining companies the option to reduce their carbon footprint by switching to battery powered fleets with zero emissions, low noise and low heat operations. Workplace health and safety are also big benefits. These are exciting times for the mining industry, and the onus is on the mining fraternity (equipment suppliers and mining companies) to make the best use of the technologies available and provide a safer underground environment to the workers.
FOR TOUGH JOBS
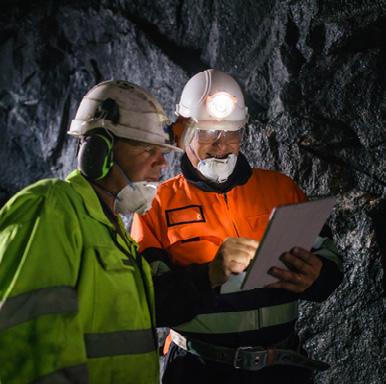
Normet is virtually exclusively focused on the disciplines of underground mining, tunnelling and civil construction. We live in your world on a day-to-day basis. We come from the industries; we speak your language; we understand your objectives. We understand HSQE, engineering, development, production cost/ productivity drivers and management. Your challenge is our challenge.
ABOUT OUR EXPERTISE We understand that development cycle time and production effectiveness are important to you. We work with you to optimise these. We believe that Total Value of Ownership/Partnership is a very important metric. Normet brings process expertise to bear which has been amassed over thousands of mines and projects all over (and under) the globe. This broad perspective means that we’ve seen, and learned, a lot about what should and should not be done to achieve the optimum results. We improve underground mining and tunnelling processes with knowledge and technology. We translate process expertise into actions and results which you can measure financially.
ABOUT OUR PROCESSES Normet, more importantly, has a wealth of expertise and experience (over 55 years) in your pertinent, specialized processes such as Ground Support, Explosives Charging, Equipment Life Cycle management, TBM operations and other innovative applications. This boils down to understanding your processes in which our technologies are employed, and improving the overall processes to your benefit.
ABOUT OUR PEOPLE AND ORGANIZATION Normet is both local and truly global with respect to our customers’ operations; we operate in all relevant markets around the world, from 43 locations, interacting directly with our customers. Over our lifetime, we have delivered over 11,000 built-for-purpose underground machines. We also service machines and support the rest of our offering with our range of Normet services. For many processes, we are a “one stop shop”. We nurture inspiration in our employees and they have a passion for doing “big” things for Normet and for the industries we serve. We travel; we go to your project wherever it may be; we go underground; we get our hands dirty. We spend the time with our customers and we invite our customers to be an integral part of our Research and Development processes.