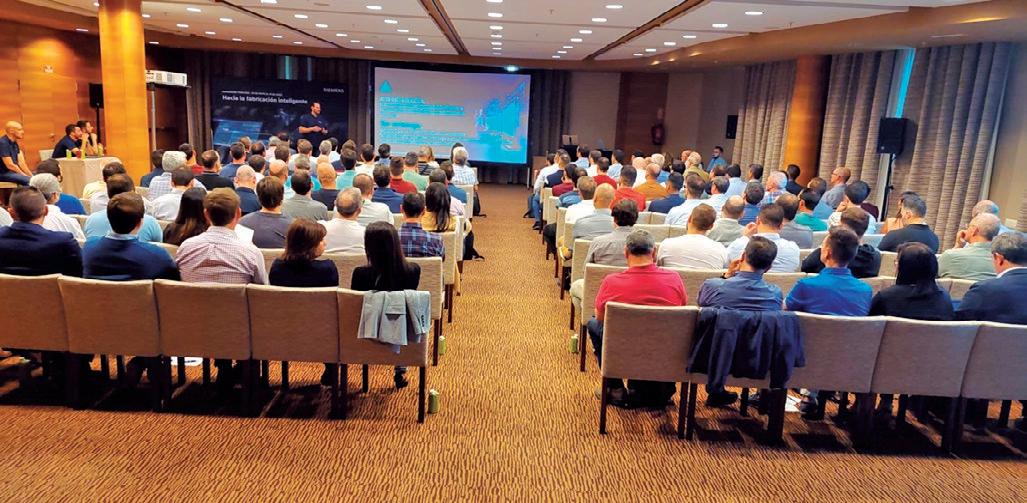
6 minute read
La fabricación inteligente, protagonista del Innovation Tour 2023 de Siemens
Siemens completó a mediados de junio su Innovation Tour 2023, un ciclo de jornadas con el que visitó doce ciudades españolas (Valencia, Bilbao, Gijón, Valladolid, Barcelona, Zaragoza, Sevilla, Santiago, Girona, Madrid, Santander y Granada). La finalidad de estas sesiones se centró en explicar la necesaria convivencia del mundo virtual y el operacional en el ámbito industrial y mostrar sus nuevas soluciones de digitalización a más de 1.200 clientes. Alberto de la Merced, responsable de campaña Innovation Tour 2023, resume los aspectos más destacados de esta iniciativa.
Siemens llevó a cabo un ciclo de jornadas que ha recorrido un total de doce ciudades españolas, desde el día 4 de mayo, en Valencia, hasta el pasado 14 de junio de 2023, cuando concluyó en Valencia.
El objetivo de esta iniciativa ha sido mostrar las nuevas soluciones de digitalización a más de 1.200 clientes.
Durante el recorrido, Siemens ha mostrado y explicado las últimas novedades en auto- matización, virtual commisioning, robótica, simulación y conectividad de los mundos IT (Information) y OT (Operation) de una manera cibersegura. La convivencia del mundo virtual y real y la óptima gestión de los datos son ya los grandes protagonistas del presente de la industria. Los contenidos de la gira se estructuraron en tres bloques:
Validación de la funcionalidad en máquina y/o línea y/o planta (Virtual Commissioning en tres niveles)
En este primer bloque, Siemens mostró las ventajas y oportunidades que brinda el enfoque de simulación holístico a lo largo de la cadena de valor; y no sólo para aspectos concretos, como probar el programa del PLC o la visualización.
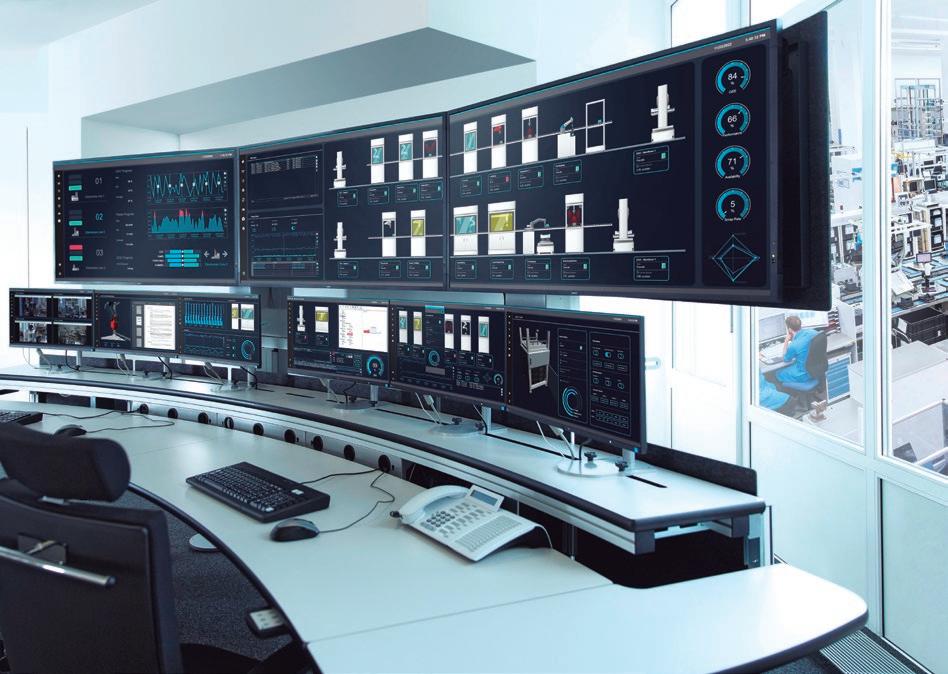
Durante la fase de oferta se va a poder utilizarar el gemelo digital como herramienta de marketing. Siemens es conscientes de la potencia a nivel de ventas dado que se puede mostrar ya en esta fase un modelo virtual de cómo va a quedar la máquina o instalación.
En la fase de diseño e ingeniería se pueden realizar todos los ensayos y validar el código sobre un entorno virtual; y se hace de una forma más sostenible al no necesitar utilizar prototipos físicos. Ya durante esta fase temprana se van a poder tomar decisiones, junto con el cliente final, para conseguir mejoras en la producción.
Al efectuar más pruebas en virtual, se va a reducir el riesgo y la duración de las prue- bas FAT (validación en fábrica) y puesta en marcha. Esto repercutirá en la consiguiente reducción de costes, al tener menos tiempo el personal desplazado en las instalaciones del cliente final.
Por último, con el sistema productivo en operación, el empleo de gemelos digitales permite validar las mejoras y modificaciones de una máquina o una planta sin necesidad de hacer pruebas en la instalación real.
El gemelo digital se va a poder alimentar con datos provenientes de Industrial Edge, Cloud computing o IA (Inteligencia Artificial) para conseguir propuestas de mejora basadas en datos, y así garantizar la viabilidad de la inversión. Además, el gemelo digital servirá como herramienta de formación para garantizar una rápida y eficiente incorporación de los nuevos empleados.
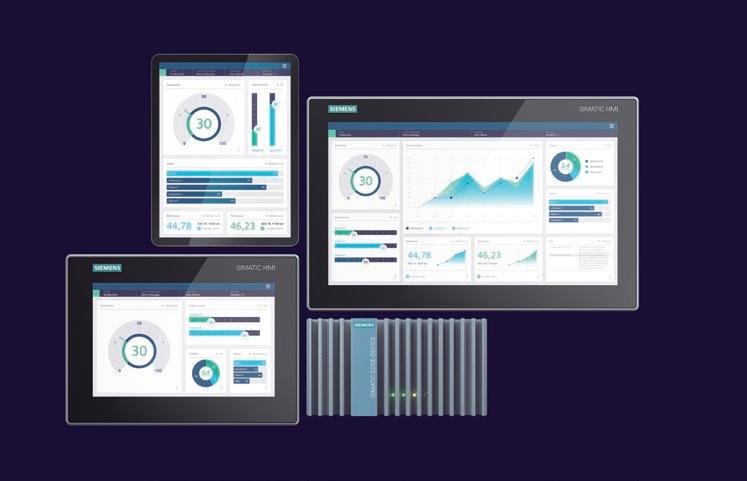
Existen diferentes casos de uso y referencias de clientes que ya utilizan esta tecnología. Se pueden destacar los siguientes:
◗ IMASD y el Instituto Tecnológico de Kalsruhe, que emplean el gemelo digital para validar nuevas funcionalidades en que supone una modernización de los antiguos sistemas de visualización. máquinas cada vez más complejas y con funcionalidades más sofisticadas.
◗ Ingemat, que llega a simular un 90 % del funcionamiento de las celdas de soldadura a través de los programas PLCSim Advanced y Process Simulate. Esto ha permitido a esta ingeniería, especializada en automatización robótica, reducir un 40 % los tiempos de depuración in situ y un 10 % los costes asociados al PEM (presupuesto de ejecución).
◗ Otras referencias de simulación a nivel de planta como son LM Group y Ferrero, ambos del sector intralogístico.
Dentro del Innovation Tour, se realizó también una demo donde se mostraba cómo, a través de la herramienta Simulation Model Generator (SMG), se puede generar de forma automática toda la simulación en el software SIMIT de los diferentes elementos que tenemos en el sistema de automatización, como pueden ser drives, seguridades, lectores RFID, etc.
Este primer bloque se finalizaba en las sesiones de este ciclo comprobando cómo las ventajas del gemelo digital y de realizar Virtual Commissioning pueden aplicarse también al sector de las infraestructuras, mostrando el gemelo digital de un túnel.
Convergencia OT/IT para la toma de decisiones anticipada y optimización Dentro del segundo bloque, en este tour se habló de uno de los retos más innovadores que se pueden encontrar en el mercado. Se debe aumentar la eficiencia de los procesos y ser más competitivos.
Convergencia OT e IT significa combinar el mundo real de la automatización con el mundo digital de las tecnologías de la información. Y, de esta manera, ayudar a las empresas a aumentar de modo significativo su rendimiento, productividad, flexibilidad y sostenibilidad.
Para hacer más tangibles y entendibles estos retos, Siemens presentó unos casos muy concretos de aplicación de esta convergencia donde se explica claramente en qué consiste, cómo implementar el caso de uso y los beneficios que obtendremos de ello.
También se detalló el procesamiento de órdenes para una operación global y sin papeles que permita una mayor transparencia de la información en todos los niveles. Se presentó asimismo la nueva versión de la herramienta WinCC V8, que puede representar uno de los pilares fundamentales es esa integración IT/OT gracias al conector REST API y MQTT. De la mano de sistemas como el SCADA WinCC ayudamos a armonizar la información y hacer una buena gestión de los datos.
El nuevo ecosistema abierto Industrial Edge plantea una nueva forma de crear valor añadido con herramientas IT en los entornos de producción OT. De esta manera, se pueden plantear casos de uso como mantenimiento predictivo, anomaly detection, optimización de los procesos ejecutando modelos de simulación en Edge y comparar, gracias a la app LiveTwin Edge, el sistema real con el modelo virtual.
También se mostraron varios casos de uso relacionados con el análisis de datos y la toma de decisiones, gracias a la transparencia vertical de los datos.
Tanto Simatic Industrial Edge como los sistemas SCADA WinCC son capaces de elaborar plantillas tipo business intelligence y conseguir datos específicos y preprocesados que permitan mejorar la eficiencia energética de una instalación, y tomar mejores decisiones gracias a las herramientas PM Analyze y Performance Insight
Durante todo este recorrido no hay que olvidarse de la importancia de la ciberseguridad. Digitalización, conectividad y ciberseguridad deben ir de la mano y no solo de una manera puntual, sino también en todo el ciclo de vida de la planta. Cumplir la norma IEC 62443 se hace indispensable en este nuevo modelo de convergencia OT e IT.
En resumen, los beneficios de la integración OT/IT se pueden expresar en muy pocas palabras, según Siemens: rapidez, operaciones sostenibles, incremento de la calidad, mayor flexibilidad y, por supuesto, mayor eficiencia. Es el momento de sacar el máximo partido a la fábrica combinando lo mejor de los mundos OT e IT.
Mayor rendimiento y disponibilidad
En el tercer y último bloque de estas jornadas, Siemens propuso a sus clientes cuatro retos que se encuentran de manera continua en su día a día en el campo de la automatización: Productividad, Alta Disponibilidad, Mercados no europeos y Modernización de las instalaciones.
Al principio de cada uno de estos retos, se plantearon a los clientes una serie de preguntas clave sobre el mismo, del tipo “¿Cómo puedo… incrementar número de piezas/hora, evitar paradas de producción, etc.?”, a lo que se añadía una reflexión so- bre lo que demandan los clientes de forma habitual. Una vez hecha esta composición de lugar, a continuación, se proponía la solución al reto aplicando los productos de automatización de Siemens.
El primero de esto retos, la Productividad, aborda como poder aumentarla gracias a los nuevos PLCs S7 1500 innovados, las nuevas soluciones de Motion Control, los nuevos drives Sinamics S210, así como con la integración de Robótica e Inteligencia Artificial con controladores SIMATIC que permite automatizar lo “desconocido”.
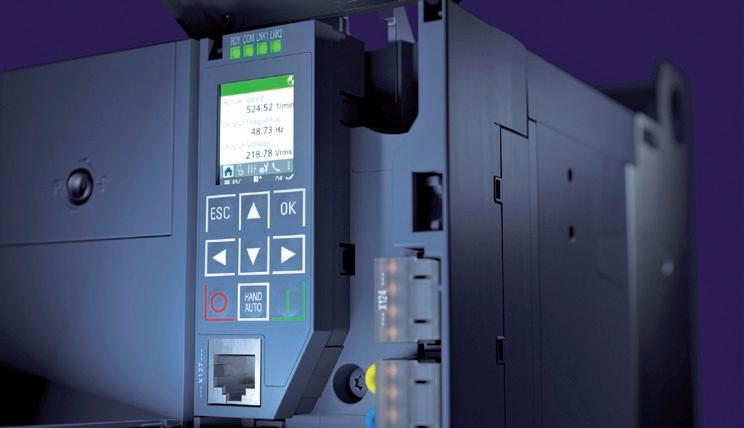
En el segundo de los retos, se trata como disponer de una alta disponibilidad en las instalaciones, evitando paradas de producción. Se describieron tres ejemplos de aplicativos de los PLCs redundantes S7 1500H.
Se explicó también cómo tener una redundancia total (red, controlador, periferia y E/S) en una estación depuradora de aguas; cómo abordar la alta disponibilidad en infraestructuras donde ya hay una red instalada (como en los túneles); y cómo mezclar arquitecturas redundantes y simples poniendo como ejemplo un barco.
También se dieron a conocer los nuevos drives SINAMICS G220, aptos para trabajar en sistemas redundantes sin olvidar la gama SITOP de sistemas SAI o UPS, que permiten asegurar el funcionamiento de instalaciones criticas ante una caída de tensión en las instalaciones.
El tercer reto, trata de cómo adaptar las soluciones a los mercados no europeos donde los requisitos de los clientes sobre buses de campo y comunicaciones son distintos a los que se utilizan habitualmente en el mercado nacional. Aquí se mostró la solución basada en periferia Multifieldbus, las posibilidades de comunicación con otros buses con los controladores SIMATIC, así como la amplia gama de pasarelas SIMATIC para cualquier comunicación.
Por último, en el cuarto reto se habla sobre cómo modernizar las instalaciones usando las nuevas pantallas Unified Comfort Panel. Se explicó tanto el valor añadido que se le dan a las instalaciones gracias a las nuevas funcionalidades de estas pantallas, así como la forma óptima de afrontar la modernización de los antiguos sistemas de visualización a la nueva familia
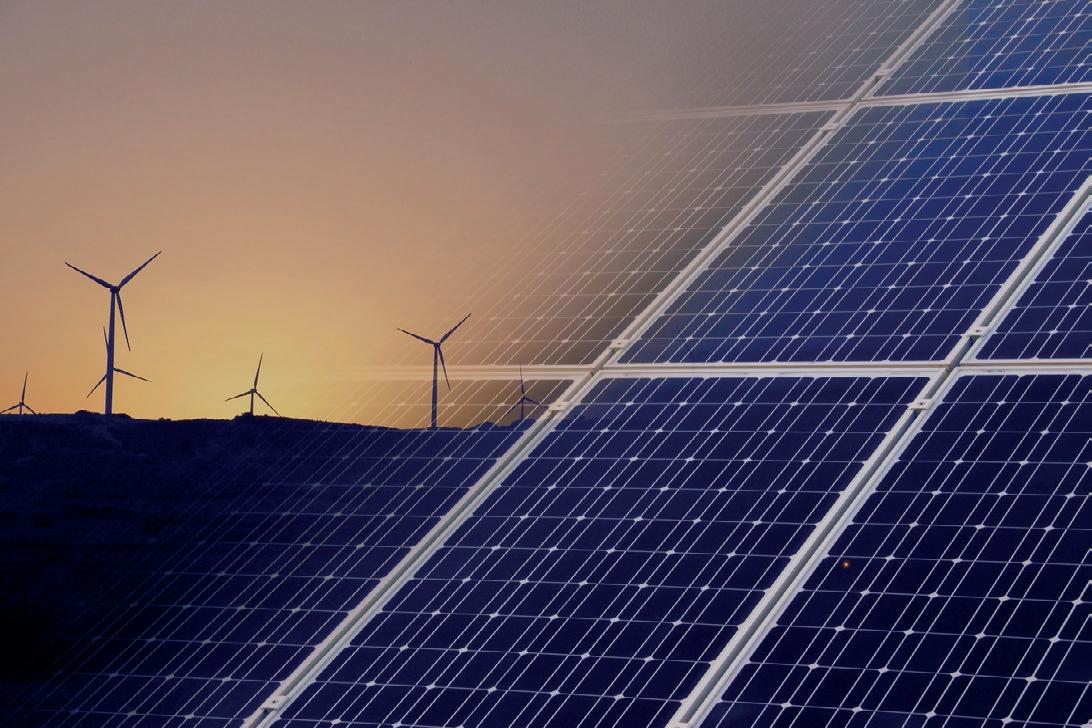