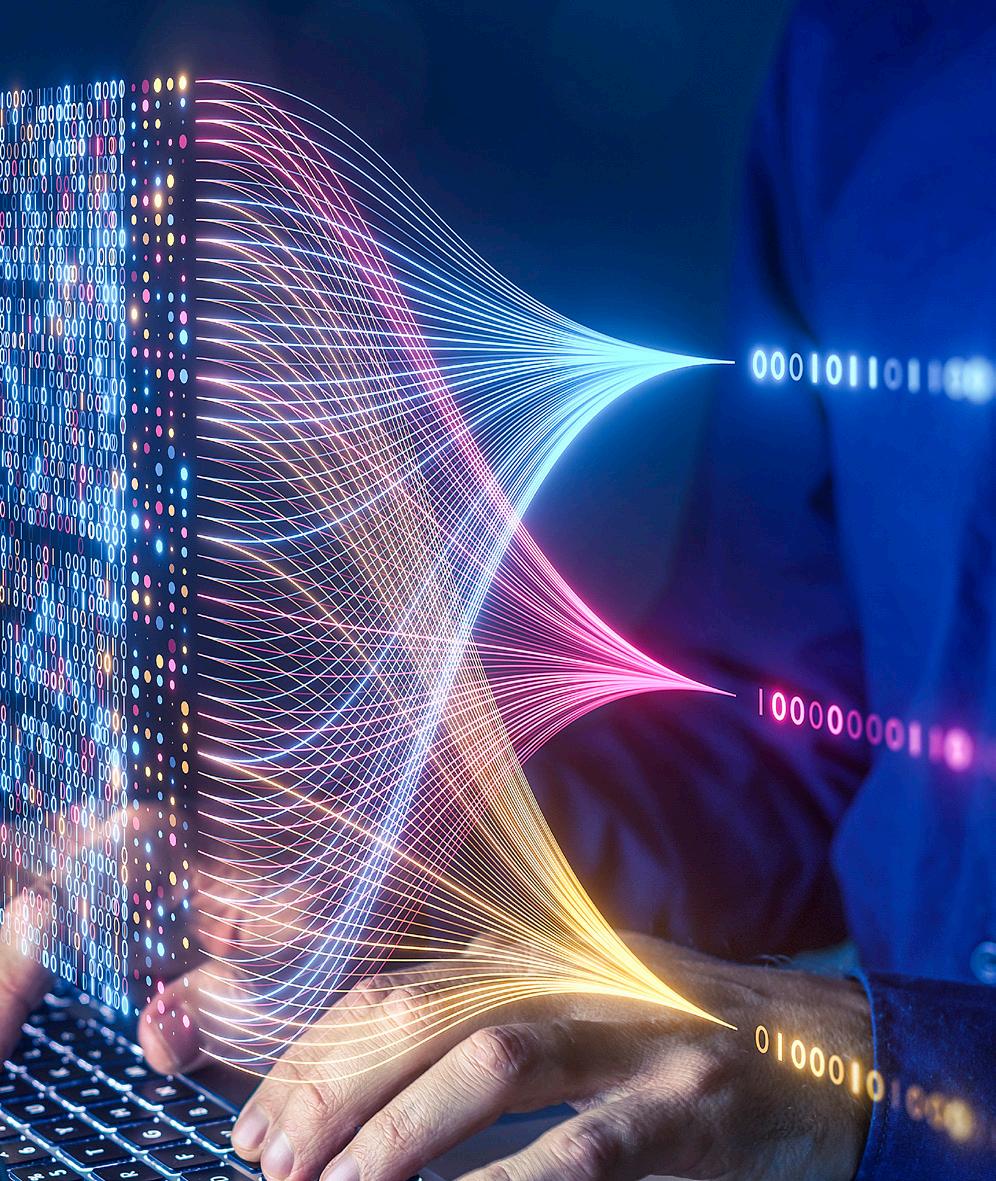
Interview with Dr. Aditya Gupta, COO, Supply Chain Management Centre, Indian Institute of Management, Bangalore (IIM-B)
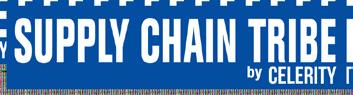
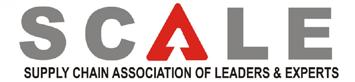








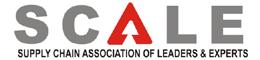
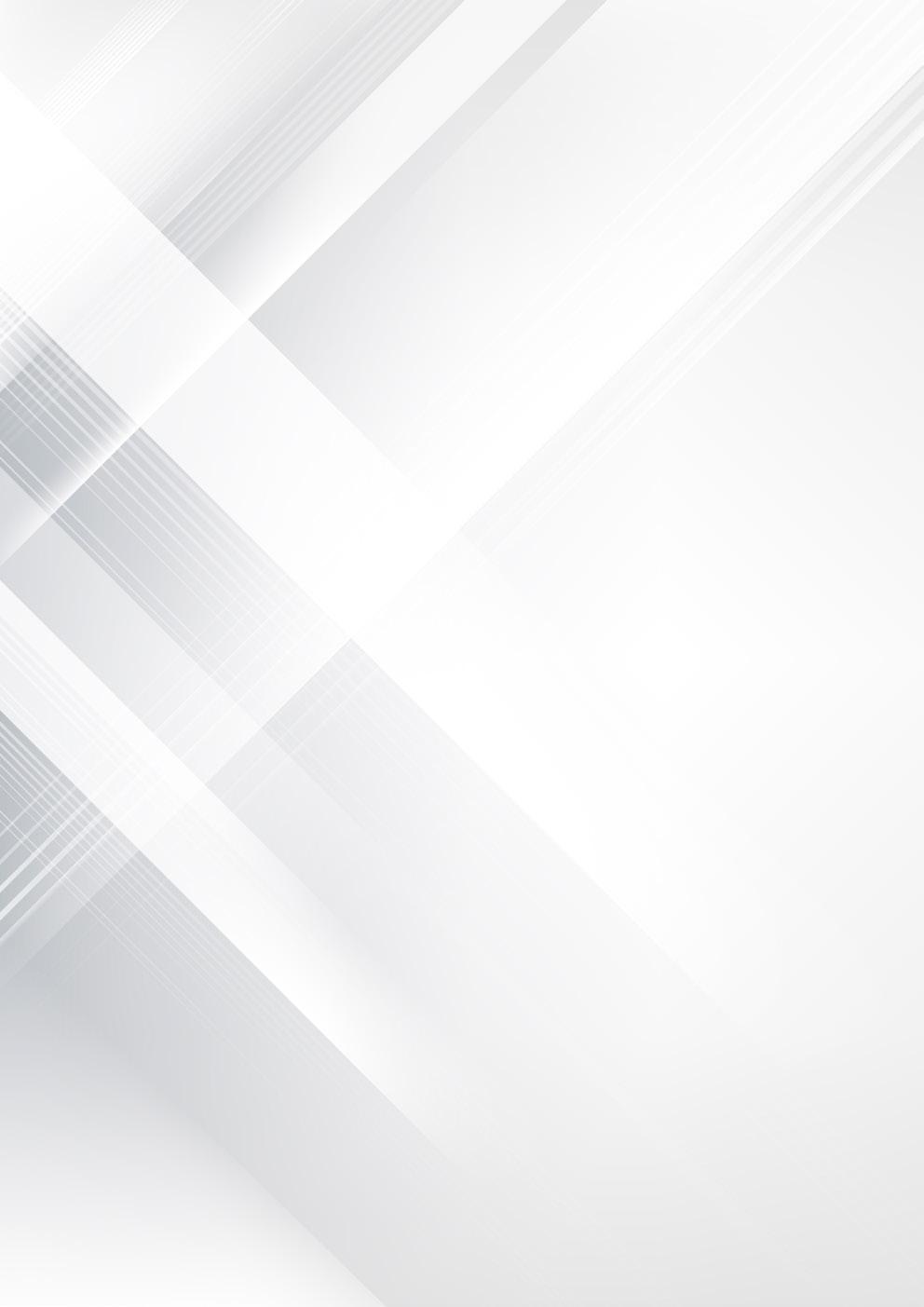









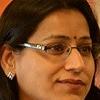































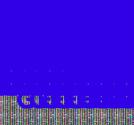

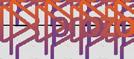
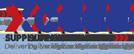
Interview with Dr. Aditya Gupta, COO, Supply Chain Management Centre, Indian Institute of Management, Bangalore (IIM-B)
Dear Readers,
The India Budget 2025 has reinforced the nation’s commitment to infrastructure development, a critical pillar for economic growth. With increased allocations to logistics corridors, multimodal connectivity, and digital infrastructure, the budget lays the foundation for a more seamless and efficient supply chain ecosystem. However, challenges such as execution delays and regulatory roadblocks remain key areas that demand urgent attention.
As we delve into this month’s cover story, Navigating the Future of Next-Generation Value Chains, we explore how industry leaders are addressing infrastructure bottlenecks, regulatory complexities, and the widening skills gap in emerging technologies. The supply chain of the future is not just about efficiency—it is about resilience, intelligence, and adaptability.
The transition towards sustainable supply chain practices is another crucial imperative. In our expert interview this month, we discuss the role of cleaner technologies in reducing transportation emissions. From electrification and alternative fuels to smart route optimization, industry pioneers are actively reshaping logistics for a lower-carbon future. However, achieving true sustainability is not just about adopting new technologies—it requires collaboration across the ecosystem. Companies must work closely with suppliers, customers, and regulators to build a supply chain that is not just efficient but also responsible and future-ready.
Additionally, our Special Report on Cold Chain takes a deep dive into how far the industry has come. From evolving cold chain infrastructure to groundbreaking technological advancements, the sector is undergoing a transformation that promises sustainable growth and enhanced efficiency.
As we stand at the intersection of rapid transformation, one thing is clear: The future belongs to those who embrace innovation while staying committed to sustainability. We hope this edition provides valuable insights and inspiration as you navigate your own journey towards next-generation value chains.
Let’s build the future, together!
Happy Reading!
Charulata Bansal Publisher Charulata.bansal@celerityin.com
www.supplychaintribe.com
Edited by: Prerna Lodaya e-mail: prerna.lodaya@celerityin.com
Designed by: Lakshminarayanan G e-mail: lakshdesign@gmail.com
Logistics Partner: Blue Dart Express Limited
“India is now poised to set global benchmarks for supply chain excellence in the 21st Century,” writes Sanjay Desai, General Manager – Asia, Supply Technologies.
Dr. Aditya Gupta, COO, Supply Chain Management Centre, Indian Institute of Management, Bangalore (IIM-B), highlights, “To achieve sustainable supply chain management, companies need to work closely with suppliers, customers, and other stakeholders.”
at the Helm:
Next-generation value chains are the epitome of innovation, weaving together Digital Technologies, Sustainability, and Resilience to create Agile, Intelligent Networks of Production and Distribution. India, poised on the cusp of transformation, is positioning itself as a dynamic player in these value chains. However, to truly flourish, India must overcome challenges such as infrastructure bottlenecks, regulatory hurdles, and a skills gap in emerging technologies. If navigated wisely, these hurdles could usher India into an era of unparalleled economic prominence, firmly embedding it in the core of nextgen global value chains. Our Cover Story unravels all these facets and more…
A collective and impassioned effort has been underway to foster innovation, elevate the cold chain sector’s competitiveness, and bring it on par with global standards. In this Special Report, we offer you a glimpse into expert insights on the evolving landscape of cold chain infrastructure, the groundbreaking technological strides, and the burgeoning promise of sustainable growth.
Capturing two of the latest events
• India @ Davos
• Key Takeaways from Union Budget 2025-26
all the care taken, errors or omissions may have crept inadvertently into this publication. The publisher shall be obliged if any such error or omission is brought to her notice for possible correction in the next edition. The views expressed here are solely those of the author in his private/professional capacity and do not in any way represent the views of the publisher. All trademarks, products, pictures, copyrights, registered marks, patents, logos, holograms and names belong to the respective owners. The publication will entertain no claims on the above. No part of this publication can be reproduced or transmitted in any form or by any means, without prior permission of the publisher. All disputes are subject to the exclusive jurisdiction of competent courts and forums in Mumbai only.
India is experiencing a remarkable shift in its supply chain footprint, driven by combination of advanced technology plus manufacturing growth, aided by a strong focus on ESG principles. With a strong foundation built over the last decades, India is now poised to set global benchmarks for supply chain excellence in the 21st Century. Building on these advancements, India’s supply chain leadership must push the nation beyond its current limits to meet its ambitious objectives. This visionary leadership will be instrumental in achieving India’s $6 trillion economic target and establishing it as a global manufacturing powerhouse, writes Sanjay Desai, General Manager – Asia, Supply Technologies.
THE ‘Make in India’ initiative has transformed the manufacturing landscape, attracted global players and fostered domestic innovation. These innovations have significantly enhanced efficiency, reduced costs, and strengthened resilience across networks. Simultaneously, the growing importance of ESG principles has steered businesses toward sustainable practices, ethical governance, and reducing carbon footprints. This shift reflects a broader economic strategy that aligns growth with environmental responsibility.
The last ten years have also witnessed the rise of green energy initiatives and digital platforms, underscoring India’s commitment to a balanced approach to industrial progress. These efforts have not only cemented India’s position as a global manufacturing hub but have also positioned it as a pioneer in sustainable supply chain practices. Let us take a quick
look at few major milestones in past decade which redefined India’s supply chain landscape.
Economic Growth: India's GDP surged from approx $1.67 trillion in 2010 to around $3.57 trillion in 2023, reflecting a robust annual growth rate. Our desire is to achieve a 6 to 7% YOY growth to reach 5.0++ trillion in the next five years. This growth will be fuelled by sectors
Sanjay Desai is an experienced commercial operation professional. Currently he is running Asia Commercial Vertical for Supply Technologies, USA as VP/GM based out of Singapore. In the past, he has been running profit & loss for over 500 million USD leading more than 2000 professionals located remotely across 30 international markets. He has led many Fortune100 multinationals in various segments like Pharma, FMCG, Oil & Gas, MedTech, IT/ Technology and Chemicals successfully for the last 40 years. Sanjay’s expertise lies in developing commercial & operational strategies, developing people’s skillset, and enabling market growth. He is a mentor for a couple of startup incubators. He sits as an advisory member on multiple startups and MSME organizations in SEA.
like petroleum, pharma, electronics & textiles, with increasing contributions from renewable energy, high-value manufacturing to US, UAE, China & European nations.
Manufacturing Sector: The ‘Make in India’ initiative has significantly accelerated manufacturing growth in India, transforming it into a global manufacturing hub. This growth is further complemented by the ProductionLinked Incentive (PLI) schemes, which have earmarked $26 billion to incentivize domestic production across sectors such as electronics, automotive, and pharmaceuticals. The manufacturing sector's contribution to GDP increased from 15.1% in 2014 to 17.4% in 2024, reflecting robust expansion driven by policy support and investments.
Exports touched record high: India’s total exports value touched 770-775 USD billion during FY 2024. Industry segments which contributed majorly are electronics, API/ pharmaceuticals, and engineering goods including Services. India signed significant new FTZ and FTAs especially in Asean region during the last couple of years have unlocked new markets. India’s IT sector accounts for over 55% of global outsourcing demand.
FDI as a percentage of GDP stood at 1.5% in 2024, reflecting sustained growth in foreign investment inflows. These are driven by India’s robust economic growth, market potential, and policy reforms. Sectors such as technology, manufacturing, e-commerce, and renewable energy have attracted significant investments. Notable
examples include Apple's expansion of manufacturing in Chennai, Amazon's investment of over $6.5 billion in Indian e-commerce, just to give you a few examples.
Technological Advancement: India’s IT and technological landscape has witnessed phenomenal growth over the last decade. In 2014, Indian IT sector was valued at approx. $118 billion, contributing around 7.5% to GDP. By 2024, the sector’s market size has surged to an estimated $245 billion, accounting for over 10% of GDP, with a consistent annual growth rate of over 9%. The export component has also expanded, with IT and ITES exports rising from $99 billion in 2014 to $190 billion in 2024, reflecting India's growing dominance in the global tech arena. Some key initiatives that propelled India on the Global format are Digital India Program (2015), Start-Up India (2016), National AI Strategy (2018), PLI Scheme for IT/ Electronic, etc.
Unified Payment Interface: India's Unified Payments Interface (UPI) has emerged as a frontrunner in the global digital payments landscape. With an impressive 46% of the global real-time payment transactions occurring in India, UPI has firmly established itself as a significant player in this sector. UPI number of transactions surged from 300 million in FY 2014-15 to 13.1 billion in FY 2023-24, marking a CAGR of 129%. The value of UPI transactions leapfrogged from ₹1 trillion in FY 2017-18 to ₹200 trillion in FY 2023-24. This rapid growth of UPI adoption underscores India's commitment to digital financial inclusion and the scalability of its payment infrastructure.
Ease of Doing Business: India made remarkable progress to improve its business environment, climbing from 142 number in 2014 to 63rd in the World
Bank’s Doing Business Report (DBR) 2020. This 79-rank jump over reflects the government’s sustained efforts to simplify regulations, reduce bureaucratic hurdles, and create a more businessfriendly environment, significantly boosting investor confidence to do business with India.
Logistics Performance index: Logistics costs in the India amount to almost USD 400 billion, or 14% of our GDP. A comparison with global peers shows that logistics costs amount to 8-10% of GDP in the US and Europe, and 9% in China. The global average is close to 8% of GDP. The 6% gap in our domestic logistics cost compared to global average cost - is about 180 billion USD. India ranked 44th in the World Bank Logistics Performance Index, far behind the US at 14 and China at 26. See below chart released last in 2018.
Foreign exchange reserves are assets held by the Reserve Bank of India in foreign currencies, gold, and India’s reserve position in the International
Monetary Fund (IMF). These reserves help stabilize Indian rupee, manage external debt & ensure liquidity during economic crisis or trade deficits. Our reserves have reached the highest point during year 2024 presently at 678 million USD.
The next five years hold immense promise for India as the nation accelerates its economic growth trajectory, driven by key initiatives and reforms. India is poised to consolidate its position as a global manufacturing hub, bolstered by the success of the ‘Make in India’ campaign and significant investment in infrastructure, digital transformation, and skill development. With GDP growth expected to remain robust, the focus will shift toward enhancing export
competitiveness, targeting diversified global markets, and scaling value-added manufacturing.
Building on these advancements, India’s supply chain leadership must push the nation beyond its current limits to meet its ambitious objectives. This visionary leadership will be instrumental in achieving India’s $6 trillion economic target and establishing it as a global manufacturing powerhouse. Let us examine key priorities that supply chain leaders must focus over the next five years…
Integrate ESG into core supply chain strategy: Global businesses must consider ESG risks when formulating growth strategy and executing business decisions. This includes regular training and audits on the ground with local partners, facilitating alignment with the more stringent Indian ESG disclosure requirements, and building sustainable supply chains.
Responsibility: CSR in India is mandated under Section 135 of the Companies Act, 2013. Companies meeting certain financial thresholds are required to spend at least 2% of their average net profits over three years on CSR activities. These activities typically focus on philanthropy, community development, and addressing social and environmental challenges.
Use Technology to drive supply chain architecture: In today’s world, digitalization is not an option, but
a necessity. The Indian supply chain needs to adopt and assimilate nextgen technology including Industry 4.0 applications to build tech-enabled smart supply chain networks. India needs to implement strategic technologies such as artificial intelligence, blockchain, and the IoT. Digitalization of supply chains architecture will foster an integrated platform, facilitating real-time information sharing among stakeholders and decision-makers at every stage of the value chain. These will contribute to reduce waste and cost out of business with the potential to reduce expenditure by 30-40%.
Integrate supply chain for end-toend visibility: Creating a flexible and agile supply chain necessitates platforms that seamlessly integrate processes, such as omni-channel supply chains, piggy-backing multiple lanes/ sources of supply. These integrated systems deliver a unified experience for consumers, regardless of the channel they choose. Supply chain visibility is a pivotal factor in determining responsiveness and operational efficiency. It empowers manufacturers, distribution centres, and retailers to seamlessly adapt to fluctuating consumer demand without additional labour or resources. Technologies like RFID and barcodes enable real-time visibility, enhancing forecasting accuracy and ensuring demand-supply alignment across the entire supply chain.
Build agility in the supply network: Establishing agility within supply networks necessitates creating a
flexible ecosystem with decentralized production hubs which are strategically located closer to consumer bases. This enables supply chains to adapt swiftly and operate seamlessly. Equally crucial is cultivating dynamic teams capable of quickly adjusting to external challenges. Prompt responses to disruptions can accelerate transformation while mitigating potential damages effectively.
Mindset shift from risk mitigation to risk management: Like in the past, organizations faced vulnerabilities within the supply chain as well as due to disruptions, often incurring significant financial losses. But these were considered as ‘unavoidable’. During last 5 years, it is becoming known that growing risks linked to factors such as limited supply chain transparency and data restrictions have hindered the ability to proactively evaluate the likelihood and impact of these risks. Transitioning from traditional risk mitigation to initiativetaking risk management necessitates addressing these gaps, thereby fostering greater resilience and adaptability.
Build logistics & warehousing infrastructure: India will aim to reduce its logistics cost to 7-8% of GDP, closing the USD 500 billion competitiveness gap with best-practice countries globally. For that to happen, companies need to improve their logistics infrastructure by benchmarking the logistics modal mix and emphasizing the use of electric vehicles (EVs) for last-mile deliveries. In warehousing, we need to improve out to expand
infrastructure
As technology reshapes the supply chain landscape, organizations need to re-prioritize skilling their workforce with advanced digital and analytical skills. Senior leaders must embrace AI, data analytics, and digital transformation to drive informed and agile decision-making. They must re-focus on upskilling employees in automation, IoT, and data-driven operations while fostering innovation through cross-functional teams. Attracting new talent and reskilling existing staff will ensure seamless integration of emerging technologies into supply chain processes, enabling faster and smarter operational outcomes.
to bridge the gap between required and available capacity and aim to reduce agricultural produce wastage to less than 10%.
Strengthen regulatory and policy support: Government involvement is unavoidable in strengthening India’s supply chain infrastructure. Investments in multimodal logistics networks and broadband connectivity are essential to extend physical and digital access to rural areas. Regulatory reforms, such as GST consolidation and the establishment of supply chain clusters, can transform the manufacturing landscape. Additionally, fostering a robust supply base through the development of MSMEs will drive growth, enhance local sourcing & create a skilled workforce that supports longterm supply chain efficiency.
Transition towards a green supply chain: Organizations are increasingly prioritizing sustainable supply chain practices to meet environmental goals and regulatory expectations. Reducing carbon emission is a key target, to be achieved through green logistics solutions. Adoption of EV (Electric vehicle) which can comprise a high % of number of the delivery fleet, will help reduce GHG consumption. Route optimization will improve transportation efficiency, at the same time moving to biodegradable or recyclable packaging will minimize waste. Companies need to adopt the ‘Reduce, Reuse, Recycle’ approach to create eco-friendly and future-ready supply chains.
Develop skills and talent for a techdriven supply chain: As technology reshapes the supply chain landscape,
organizations need to re-prioritize skilling their workforce with advanced digital and analytical skills. Senior leaders must embrace AI, data analytics, and digital transformation to drive informed and agile decision-making. They must re-focus on upskilling employees in automation, IoT, and data-driven operations while fostering innovation through crossfunctional teams. Attracting new talent and reskilling existing staff will ensure seamless integration of emerging technologies into supply chain processes, enabling faster and smarter operational outcomes.
MSME digitalization and growth:
Micro, Small, and Medium Enterprises (MSMEs) play a vital role in India’s supply chain, contributing over 30% to GDP and 45% to exports. Accelerating their growth through initiatives like Udyam Registration and governmentbacked e-marketplace (GeM) platforms will increase efficiency and market access. Access to affordable ERP solutions, cloud computing, and digital payment systems will enable MSMEs to integrate into global supply chains and compete internationally. The goal is to empower MSMEs to scale operations, enhance productivity, and contribute significantly to India’s $6 trillion economy aspiration by 2030.
Financial Inclusion and credit access: Expanding financial inclusion and ensuring easier access to credit are critical for the growth of India’s supply chain ecosystem, particularly for MSMEs and rural entrepreneurs. Initiatives such as the Pradhan Mantri MUDRA Yojana (PMMY) and Jan Dhan-AadhaarMobile (JAM) trinity have already
provided financial access to millions, but further enhancements are required. Digital lending platforms and fintech innovations can simplify loan approvals and offer customized financial products. Expanding trade credit insurance and invoice financing will enable businesses to manage cash flow more effectively. These measures will not only empower businesses but also ensure a financially robust and resilient supply chain to meet the demands of a growing economy.
India will be one of the top twenty countries in the World Bank Logistics Performance Index by 2030. The supply chain industry will be an optimized and automated logistics ecosystem, with a simplified distribution system and a sustainable, green, resilient, and flexible supply chain. It will be powered by next-gen technologies such as big data, AI, blockchain, and Internet of Things, backed by 21st-century infrastructure. It will be aligned with best practices across the world and stand on par with global standards. The reimagined supply chain will make India “Atmanirbhar” and strongly complement Make in India and Startup India, building a globally competitive supply chain across domestic and international markets!!!
Next-generation value chains are the epitome of innovation, weaving together Digital Technologies, Sustainability, and Resilience to create Agile, Intelligent Networks of Production and Distribution. India, poised on the cusp of transformation, is positioning itself as a dynamic player in these value chains. The country is rapidly embracing digital technologies, led by remarkable initiatives such as Digital India, while bolstering its manufacturing sector through the Make in India campaign. However, to truly flourish, India must overcome challenges such as infrastructure bottlenecks, regulatory hurdles, and a skills gap in emerging technologies. If navigated wisely, these hurdles could usher India into an era of unparalleled economic prominence, firmly embedding it in the core of next-gen global value chains. Our Cover Story unravels all these facets and more…
How has Make in India impacted technology adaption in manufacturing? How does it support India’s aim to be a global manufacturing hub?
Pratibha Nath, Director of Supply Chain – APAC, Alstom: The ‘Make in India’ initiative was launched nearly a decade ago with a focused approach to specific industries that the government identified as having the potential to transform the economy. Initially, it covered around 25 sectors, including automotive, textiles, electronics manufacturing, and renewable energy. Significant progress has been made since then, particularly in infrastructure development, such as railroads. This initiative presents a great opportunity to generate employment and enhance the Ease of Doing Business in India. Additionally, it aligns well with India’s vast pool of engineering talent— Bengaluru alone boasts over 100 engineering colleges. Emphasizing localization through such initiatives makes perfect sense.
From a supply chain perspective, having a localized ecosystem is highly beneficial. Ideally, suppliers should be in close proximity, allowing businesses to respond quickly to demand fluctuations. This flexibility is essential and Make in India facilitates this by fostering strong local partnerships for sourcing components. It also enables direct supplier evaluations to ensure quality standards are met. Various government schemes, such as the Production Linked Incentive (PLI) program and Customs Duty exemptions, further support businesses in achieving growth. It is up to each industry player to leverage these opportunities effectively.
Moreover, India is not just manufacturing for itself—it has established itself as a global manufacturing hub. With strong engineering capabilities, large-scale production, and a growing number of global capability centers, the country is well-positioned to serve international markets. The existing ecosystem provides a solid foundation to strengthen India’s role as a preferred global manufacturing destination. One crucial aspect that cannot be overlooked is the need for consistent quality. It is not enough to build a great prototype; maintaining high standards across production must be a priority. Ensuring reliability and excellence will be key to sustaining India’s reputation as a world-class manufacturing hub.
Nilanjan Das, VP & Head – SCM, Tata Hitachi Construction Machinery Co. Pvt. Ltd.: To make the ‘Make in India’ initiative a success, one has to deliver capabilities, in terms of producing goods of equivalent quality / durability and at lower cost. While cost advantage may naturally come to Indian manufacturers due to advantages in lower cost of labour, power, commodities, etc., they have to really scale up in terms of reliable and consistent quality in comparison to global best standards. To do this, Indian manufacturers have to adopt cutting edge automation to improve productivity and avoid human errors. It also helps shorten the learning curve. Hence, we see growing use of Cobots, articulated robots, AGVs, apart from advanced IT systems in manufacturing like Industry 4.0 and others. Poke yoke and failsafe methods of manufacturing are also
While manufacturers might be adopting the latest technology tools, but if their partners – the extended workforce including the suppliers, manufacturers, or the 3PLs aren’t onboarded, then that’s a big roadblock for end-to-end tech deployment. It’s high time that manufacturers convince and encourage the supporting partners in their ecosystem to start adopting those technologies and that’s when we would be able to realize the impact of such big bang transformation. You need to co-develop the tech infrastructure with your partners to not just share best practices but ensure that your partners also grow with you.
moving onto automated systems. Hence to shorten the journey on the road to reliable manufacturing, one has to rely on increased level of automation.
Hanuman Swami, Global Planning and Fulfilment Manager, ABB: The Make in India initiative has been instrumental in accelerating technology adoption in Indian manufacturing by emphasizing innovation, quality, and productivity. The policy incentivizes companies to invest in advanced technologies such as IoT, robotics, and automation, which are pivotal for enhancing operational efficiency and scalability. Additionally, government-led initiatives like the Production-Linked Incentive (PLI) schemes have made manufacturing sectors more competitive, aligning them with global standards. By fostering an environment conducive to innovation, Make in India enhances India’s positioning as a global manufacturing hub. The focus on infrastructure development, skill enhancement, and regulatory ease ensures that both domestic and foreign investors view India as a viable production destination. With an increasing emphasis on Industry 4.0 technologies, the initiative supports India’s goal of integrating into global supply chains, reducing import dependencies, and bolstering exports.
Gaurav Middha, Senior Manager –Procurement, ITC Ltd.: The ‘Make in India’ initiative has significantly impacted large food manufacturers by encouraging the adoption of cutting-edge technologies. Simplifying regulations and improving the ease of doing business
AI-driven solutions are unlocking new levels of efficiency. Predictive maintenance, powered by AI, can significantly reduce downtime by forecasting equipment failures. AI also optimizes production schedules and enhances quality control through realtime monitoring and defect detection. Over the next decade, the integration of AI and blockchain will enable Indian manufacturers to streamline operations, meet global standards, and strengthen their position in the international market. Collaborative ecosystems will emerge, driven by these technologies, to foster innovation and agility.
have made it more attractive for these companies to invest in modernizing their operations. Large food manufacturers have started integrating automation, AI, and IoT into their processes, which has resulted in increased productivity and efficiencies. However, challenges remain, especially for smaller companies that may struggle with the costs and need for workforce upskilling.
The initiative supports India’s goal of becoming a global manufacturing hub by creating an ecosystem that attracts foreign investments and fosters innovation. Special economic zones and policy reforms have encouraged both domestic and international companies to set up manufacturing bases in India. By emphasizing skill development, ‘Make in India’ also ensures a capable workforce equipped to handle advanced manufacturing technologies. As India’s food manufacturing sector continues to evolve, it strengthens the country’s position in the global supply chain, making it a formidable player on the world stage.
What are the biggest challenges in digital transformation for Indian manufacturers?
Pratibha Nath: One of the biggest challenges is data. While we have a vast amount of it, much of it is highly inconsistent. This inconsistency often leads to failures in digital initiatives. We tend to build front-end systems without giving enough attention to the back
end, only to realize later that the data is not delivering the expected results. At that point, it becomes clear that our data is out of sync. To ensure quality output, we must invest time in cleansing and organizing data before using it. Otherwise, it becomes a case of ‘Garbage In, Garbage Out’. In this context, data management is a fundamental part of digital transformation – something that needs to be addressed even before we begin digitizing operations. Despite the availability of numerous data analytics tools, challenges remain in data collection and interpretation. Many people hesitate to use these tools due to a lack of awareness or understanding of their necessity and impact. Overcoming these barriers is crucial to leveraging data effectively in digital transformation efforts.
Hanuman Swami: Digital transformation in Indian manufacturing faces several challenges. The first is the lack of uniform technological infrastructure, particularly among small and medium-sized enterprises (SMEs), which form the backbone of the industry. High initial investment costs and limited access to affordable digital tools deter widespread adoption.
Another significant hurdle is the skill gap. Employees often lack training in handling advanced technologies, leading to the underutilization of resources. Additionally, there’s resistance to change among traditional manufacturers who
are accustomed to legacy systems. Data management and cybersecurity also pose challenges. While transitioning to digital platforms, manufacturers must navigate concerns around data security and compliance, especially when working with international clients. Overcoming these challenges requires a collaborative approach involving government policies, industry partnerships, and workforce upskilling initiatives.
Vishal Pandey, Product Lead (Business Application) - Alphabet Supply Chain, Google: In my view, the biggest challenges and roadblocks for the digital transformation in India are legacy systems and mindset, resistance to change, lack of awareness, etc. Once we overcome these initial blockers, then the secondary barriers like integration challenge, lack of skills and cost would also need to be addressed.
Gaurav Middha: Indian food manufacturers, particularly large corporations, encounter significant challenges in their digital transformation efforts. One major obstacle is technology integration, as many still operate on outdated systems that require extensive modernization. Seamless data integration is also critical to ensuring consistency and reliability across operations. Additionally, these companies must strike a balance between automation and traditional processes while navigating stringent regulatory requirements and mounting
cybersecurity risks.
The struggle to attract skilled professionals further complicates the transition, as does managing the cultural shift among employees. Operational and market challenges add layers of complexity—supply chain transparency and optimization demand substantial investment in advanced technologies. Scaling digital initiatives while maintaining product quality amid shifting customer demands and the rising need for speed and customization requires continuous innovation. Sustainability is another pressing concern, with companies striving to implement ecofriendly practices without sacrificing efficiency.
Despite these hurdles, many manufacturers are already harnessing data analytics, AI, and automation to enhance supply chain efficiency, make data-driven decisions, and improve customer satisfaction. However, the road to full digital transformation remains a formidable journey.
How can Indian manufacturers stand out and become the top choice over other global manufacturing hubs?
Nilanjan Das: Over the last few decades, the manufacturing industry has gradually shifted from developed countries to developing ones, particularly the BRICS nations. The days when the US and Europe were the primary manufacturing hubs are long gone. Today, much of the production has moved to Asia and parts of South and Central America. To understand why this shift has occurred, we need to look at the key drivers behind it.
The primary factor is cost.
The supply chain is only as strong as its weakest link, and those links extend far beyond the primary supplier. With today’s complex supply chains, even the best technology in your factories won’t help if there are delays or inefficiencies at the tier II, III, or IV levels. To prevent this, it’s essential to not only have advanced systems within your own operations but also to understand and align with your suppliers’ capabilities, especially their IT infrastructure. Building resilience and efficiency requires digitizing the entire supply chain. If suppliers don’t have the right tools for forecasting, inventory management, or communication, smooth operations become nearly impossible. Supporting SMEs to improve their infrastructure is equally important, as they play a crucial role in the supply chain.
Manufacturing in developed countries has become too expensive due to high labor, material, and energy costs. One of India’s key advantages on the global stage is cost competitiveness. When positioning ourselves internationally, we need to focus on being a Cost Leader. India has many advantages over other countries in this area. A significant one is the competitive cost of raw materials. Every product begins with a raw material—be it iron ore, rubber, or bauxite—and India is rich in these resources, which are available at competitive prices.
In addition, India has efficient manufacturing facilities for many commodities like steel, rubber, and aluminium, which are crucial in producing machines and equipment. Being a cost leader in manufacturing is a crucial strategy for success.
Another significant advantage is India’s human capital. With a large, young, educated, and productive population, India has a distinct edge compared to many developed nations. For example, Japan is facing an aging workforce and struggles to attract younger generations to manufacturing jobs. In contrast, India boasts a large workforce, eager to work, skilled, and highly educated. This human capital advantage further strengthens India’s position.
However, India also faces several challenges. One major hurdle is the perception of low-quality manufacturing. Even Chinese companies sometimes view Indian products as inferior, which can be an unpleasant surprise. Overcoming this perception requires us to focus on improving quality and skill. We need to pursue tech transfers, form joint ventures with global companies, and
build stronger supply chains to elevate our manufacturing standards.
Finally, India faces a challenge in terms of market volume. The domestic market for certain products may not be large enough to achieve the economies of scale required for manufacturing. The solution lies in focusing on global exports. By producing for both the Indian and global markets, India can achieve the scale needed to compete effectively on cost in the global marketplace.
In summary, while India faces some significant challenges, it has a combination of cost advantages, a strong workforce, and abundant resources that can help it rise as a major global manufacturing player, provided it addresses its quality and volume challenges strategically.
How can India fit into the China plus one strategy and what all are the advantages we can focus on to succeed into that?
Nilanjan Das: Over the past several decades, manufacturing has gradually shifted from developed nations to emerging economies, with China emerging as a dominant force in the global production landscape. Despite ongoing geopolitical tensions, such as the strained relationship between the US and China, the US remains one of China’s largest importers, illustrating the significant dependence on China as a global manufacturing hub. However, recent geopolitical shifts and increasing political tensions have sparked a change in sentiment, especially regarding China. This is where India has a timely opportunity to step in, as the concept of ‘China Plus One’ has become a key strategy for many companies. Businesses across the US, Europe, and other regions
are considering alternative sourcing strategies, with even Japanese companies adopting this approach.
Over the past 10-20 years, many companies from the US and Europe have set up subsidiaries and relocated their manufacturing to China to capitalize on lower costs and economies of scale. These companies also shifted their supply chains to China to take advantage of the country’s competitive pricing. But now, with rising concerns about China’s political climate, trade restrictions, and shifting risk perceptions, many businesses are rethinking their dependence on China. This is India’s chance to capitalize on this change in sentiment, before the situation potentially stabilizes or reverses.
To seize this opportunity, India must focus on its competitive advantages— cost leadership, skilled human capital, and productivity. While China remains a stronger competitor in terms of sheer cost and workforce size, India can differentiate itself by focusing on the “Trust Factor.” Many global businesses view China with some degree of mistrust, even though not all Chinese companies share this reputation. India’s reputation as a trustworthy and stable partner could give it a significant edge in attracting global manufacturing.
When it comes to cost, China still leads the world in several key industries, such as steel production. Chinese steel is the least expensive globally, but Indian steel is the second most affordable. While the gap has traditionally been wide, it’s shrinking. Additionally, China’s steel industry has long been subsidized by the government, which has pressured banks to support Chinese manufacturers in
Upskilling the
order to secure global market share. However, with a growing reluctance from Chinese banks to continue these subsidies, prices for Chinese steel are beginning to rise, creating an opportunity for India to further close the cost gap. With strong government support, India’s steel prices could become even more competitive, and this dynamic extends to other commodities as well.
For India to truly take advantage of the global manufacturing shift, it must ensure that costs are aligned with, or even better than, China’s. As businesses increasingly consider relocating their production from China to other regions like India, Vietnam, Thailand, and Indonesia, this moment represents a high-potential opportunity. India must act now to capture this demand and position itself as the preferred global manufacturing hub.
How can we upskill the workforce for digital transformation?
Hanuman Swami: Upskilling the workforce is paramount for a successful digital transformation. The process begins with identifying skill gaps and designing targeted training programs that focus on emerging technologies like AI, IoT, and robotics. Collaboration between industry and academia can bridge the knowledge gap by integrating practical modules into educational curricula.
Government initiatives like Skill India and partnerships with global technology providers can further enhance these efforts. Companies must also foster a culture of continuous learning, where employees are encouraged to adapt and innovate. E-learning platforms and
workforce
is
hands-on workshops are effective in imparting practical skills.
Leadership plays a crucial role in guiding this transition. By clearly communicating the benefits of digital transformation and aligning it with individual career growth, leaders can mitigate resistance to change. Ultimately, upskilling the workforce ensures not just organizational growth but also creates a robust talent pool for the nation.
Vishal Pandey: Upskilling the workforce for digital transformation in Indian manufacturing is crucial. Here’s how it can be done:
Identify Skill Gaps:
Assess current skills: Use surveys, interviews, and skills assessments to understand the existing capabilities of the workforce.
Analyze future needs: Determine the skills required to operate new technologies and processes related to Industry 4.0, like AI, IoT, data analytics, and cybersecurity.
Prioritize key areas: Focus on upskilling in areas with the largest gaps and the greatest impact on the business.
Implement Targeted Training Programs:
Develop customized programs: Tailor training to address specific skill gaps and the needs of different roles within the organization.
Utilize diverse learning methods:
paramount for a successful digital transformation. The process begins with identifying skill gaps and designing targeted training programs that focus on emerging technologies like AI, IoT, and robotics. Collaboration between industry and academia can bridge the knowledge gap by integrating practical modules into educational curricula. Government initiatives like Skill India and partnerships with global technology providers can further enhance these efforts.
To make the ‘Make in India’ initiative a success, one has to deliver capabilities, in terms of producing goods of equivalent quality / durability and at lower cost. While cost advantage may naturally come to Indian manufacturers due to advantages in lower cost of labour, power, commodities, etc., they have to really scale up in terms of reliable and consistent quality in comparison to global best standards. To do this, Indian manufacturers have to adopt cutting edge automation to improve productivity and avoid human errors. It also helps shorten the learning curve. Hence, we see growing use of Cobots, articulated robots, AGVs, apart from advanced IT systems in manufacturing like Industry 4.0 and others. Poke yoke and failsafe methods of manufacturing are also moving on to automated systems. Hence to shorten the journey on the road to reliable manufacturing, one has to rely on increased level of automation.
Offer a mix of online courses, workshops, on-the-job training, simulations, and mentoring programs for holistic learning experience.
Leverage government initiatives: Take advantage of governmentsponsored programs like SAMARTH and NMCP that offer training and resources for Industry 4.0 adoption.
Partner with educational institutions: Collaborate with universities and technical institutes to develop specialized training programs and curricula.
Foster a Culture of Continuous Learning:
Encourage lifelong learning: Promote a mindset of continuous improvement and provide opportunities for employees to stay updated with the latest technologies.
Create a learning environment: Establish platforms for knowledge sharing, peer learning, and mentorship within the organization.
Reward learning and development: Recognize and reward employees who actively participate in upskilling initiatives.
Leverage Technology for Training:
Online learning platforms: Utilize online courses and resources to provide flexible and accessible training options.
Virtual and augmented reality: Use VR and AR simulations to provide immersive and engaging training experiences for complex tasks.
AI-powered personalized learning: Implement AI-driven platforms that adapt to individual learning styles and pace.
Address Challenges:
Time constraints: Offer flexible training schedules and microlearning modules to accommodate busy work schedules.
Financial constraints: Explore government grants, subsidies, and partnerships to reduce the cost of training.
Resistance to change: Communicate the benefits of upskilling and address concerns about job displacement through transparent communication and change management strategies. By investing in upskilling their workforce, Indian manufacturers can ensure they have the talent and expertise to thrive in the era of Industry 4.0. This will not only enhance their competitiveness but also contribute to the overall growth and development of the Indian manufacturing sector.
What support do manufacturers need from the government since we have fairly stable government in order to boost local manufacturing?
Nilanjan Das: To boost manufacturing, global exports, and the Make in India initiative, the government must focus on one critical element – the Ease of Doing Business. During recent panel discussions, I interacted with Industry Ministers from states like Karnataka, Tamil Nadu, and Andhra Pradesh, and it’s clear that states are fiercely competing for a larger share. This includes aspects like land acquisition, the efficiency and support in obtaining clearances, and how well they manage labor and political challenges. In India, the ease of doing business remains a significant challenge for business growth.
Another important aspect is ensuring that government incentives continue. The Production Linked Incentive (PLI) scheme is a prime example, but there are other incentives as well, such as the capital goods scheme. For those who don’t qualify for PLI, the capital goods scheme offers benefits for setting up and expanding factories. Additionally, there are export incentives, duty drawbacks, and other business-friendly policies that continue to encourage growth.
Finally, one recurring request I have made is for the government to address the rising cost of key commodities, which I believe could be a game changer. Having access to affordable oil, rubber, steel, and aluminium would provide a significant advantage. The government must work to control commodity prices and address the needs of industries like steel and oil, which face unique challenges and require specific safeguards. It’s essential to strike a balance between protecting these industries and ensuring we remain
competitive globally. Once commodity prices are stabilized, industries must focus on turning these raw materials into cost-effective finished products. The government is already making strides in this area, and there is potential for even greater impact with further action.
Vishal Pandey: The government has been taking a lot of initiatives on the technology front. I was amazed to know that many of the manufacturers, especially the smaller players, are not even aware of the initiatives. For instance, the government has launched some of the very fantastic initiatives such as SAMARTH (Smart Advanced Manufacturing and Rapid Transmission Hub). Similarly, there is the National Manufacturing Competitiveness Programme (NMCP). I firmly believe that awareness on the other side is equally important while we wait for the government initiatives to come up.
What role does sustainability play in Indian manufacturing, and how can technology help?
Hanuman Swami: Sustainability is a key driver for long-term success in Indian manufacturing. With rising environmental concerns and stricter regulatory norms, manufacturers are increasingly focusing on sustainable practices. Technology acts as an enabler by providing tools to minimize waste, optimize resource usage, and reduce carbon footprints. For instance, IoT-based sensors monitor energy consumption and identify inefficiencies, while AI algorithms optimize supply
chains to reduce emissions. Circular manufacturing models, supported by digital twins and blockchain, facilitate recycling and repurposing of materials, ensuring minimal waste.
Adopting green technologies like renewable energy and sustainable materials not only benefits the environment but also enhances brand reputation and profitability. Indian manufacturers embracing sustainability will not only comply with global standards but also gain a competitive edge in international markets.
Gaurav Middha: Sustainability isn’t just a passing trend—it’s a crucial necessity in today’s business world. By combining eco-friendly practices with cutting-edge digital technologies, we can create a balance that promotes both business growth and environmental responsibility. For many procurement managers, sustainability was once a topic they avoided. Over time, however, as our careers have evolved, we’ve come to realize that sustainability, while initially perceived as an additional cost, is now an essential and valuable part of the equation—much like a relationship that grows stronger with time, starting from a challenging beginning.
The driving forces behind this shift are rooted in several guiding principles and organizational commitments. The BRSR (Business Responsibility and Sustainability Reporting) framework is a perfect example of how companies in India are embracing sustainable practices. This framework covers critical aspects such as product development
and supply chain management (Scope 1, 2, 3), reflecting the changing preferences of consumers. Studies have shown that consumers are increasingly drawn to products that are fresh and sustainable, which is why businesses must evolve their product development strategies to meet these new expectations.
Furthermore, sustainability is now a mandate in many organizations, particularly around recyclability and the circular economy. Yet, there are still overlooked areas, like merchandising and point-of-sale materials, which could be shifted from plastic to sustainable alternatives, such as using cardboard instead of plastic for shelf strips.
At ITC, sustainability is a cornerstone of our business strategy. We prioritize sustainability through our strict adherence to our Code of Conduct, which includes ethical labor practices, human rights, and environmental protection. A notable project is in our agriculture division, where we focus on sourcing agricultural commodities in a sustainable way. Through our ITC Mars tool, we connect with farmers directly to guide them on best practices. This includes reducing waste, carbon emissions, and promoting sustainable farming practices right from the sowing phase. The goal is to make sustainability a part of the agricultural process from the ground up.
One recent initiative is our “farmto-fork” model, which ensures complete transparency and traceability in the supply chain. For instance, when we source potatoes for our Bingo chips, we track the journey of each potato from the field all the way to the consumer.
The Make in India initiative has been instrumental in accelerating technology adoption in Indian manufacturing by emphasizing innovation, quality, and productivity. Additionally, government-led initiatives like the Production-Linked Incentive (PLI) schemes have made manufacturing sectors more competitive, aligning them with global standards. By fostering an environment conducive to innovation, Make in India enhances India’s positioning as a global manufacturing hub. The focus on infrastructure development, skill enhancement, and regulatory ease ensures that both domestic and foreign investors view India as a viable production destination. With an increasing emphasis on Industry 4.0 technologies, the initiative supports India’s goal of integrating into global supply chains, reducing import dependencies, and bolstering exports.
At ITC, sustainability is a cornerstone of our business strategy. We prioritize sustainability through our strict adherence to our Code of Conduct, which includes ethical labor practices, human rights, and environmental protection. One recent initiative is our “farm-to-fork” model, which ensures complete transparency and traceability in the supply chain. For instance, when we source potatoes for our Bingo chips, we track the journey of each potato from the field all the way to the consumer. This digital traceability, supported by IoT and SCADA technologies, helps monitor the entire process—from farm to cold storage to processing units. The goal is to reduce food waste and enhance sustainability across the entire supply chain.
This digital traceability, supported by IoT and SCADA technologies, helps monitor the entire process—from farm to cold storage to processing units. The goal is to reduce food waste and enhance sustainability across the entire supply chain.
What strategies or technologies can help Indian manufacturers create more resilient supply chains amid global disruptions?
Pratibha Nath: The supply chain is only as strong as its weakest link, and those links extend far beyond the primary supplier. With today’s complex supply chains, even the best technology in your factories won’t help if there are delays or inefficiencies at the tier II, III, or IV levels. To prevent this, it’s essential to not only have advanced systems within your own operations but also to understand and align with your suppliers’ capabilities, especially their IT infrastructure.
Building resilience and efficiency requires digitizing the entire supply chain. If suppliers don’t have the right tools for forecasting, inventory management, or communication, smooth operations become nearly impossible. Supporting SMEs to improve their infrastructure is equally important, as they play a crucial role in the supply chain. Government initiatives to help them grow and connect with larger businesses can strengthen the overall ecosystem. It’s clear that optimizing your own operations isn’t enough—you need to ensure the entire supply chain is ready to scale alongside you.
Hanuman Swami: To build resilient supply chains, Indian manufacturers must adopt a multi-pronged approach.
Leveraging AI and machine learning for demand forecasting and inventory management can help mitigate disruptions caused by fluctuating demand. IoT-enabled systems provide real-time visibility into supply chain operations, ensuring timely identification of bottlenecks.
Diversifying supplier bases and fostering regional collaborations can reduce dependency on single sources. Blockchain ensures transparency and trust, particularly in multi-tier supply chains. Digital twins, which create virtual replicas of supply chains, allow manufacturers to simulate scenarios and devise contingency plans.
Additionally, fostering a collaborative ecosystem where manufacturers, suppliers, and logistics providers share data securely can improve agility and decision-making. With these strategies, Indian manufacturers can not only withstand disruptions but also thrive in an increasingly volatile global environment.
Vishal Pandey: There are no tailor-made technologies specifically for the Indian manufacturers. I believe the technology adoption criteria remain the same across the globe. One critical aspect I would like to address is that while manufacturers might be adopting the latest technology tools, but if their partners – the extended workforce including the suppliers, manufacturers, or the 3PLs aren’t onboarded, then that’s a big roadblock for end-to-end tech deployment. It’s high time that manufacturers convince and encourage the supporting partners in their ecosystem to start adopting those technologies and that’s when we would be able to realize the impact of such big
bang transformation. You need to codevelop the tech infrastructure with your partners to not just share best practices but ensure that your partners also grow with you.
Coming to technologies, there are no limitations and extent to which technological adoption can happen and this is an iterative and every evolving process to stay relevant. However, for starters, Indian manufacturers need to embrace several key technologies to maintain global competitiveness:
Automation and Robotics:
Increased Efficiency and Productivity: Automating tasks leads to faster production, reduced errors, and improved output.
Enhanced Quality: Robots can perform tasks with precision and consistency, leading to higher quality products.
Cost Reduction: Automation can lower labor costs and reduce material waste, making manufacturing more affordable
Artificial Intelligence (AI) and Machine Learning (ML):
Predictive Maintenance: AI and ML can analyze data from machines to predict potential failures, allowing for proactive maintenance and minimizing downtime.
Quality Control: AI-powered vision systems can detect defects in realtime, ensuring only high-quality products leave the factory.
Supply Chain Optimization: AI can optimize inventory management, logistics, and demand forecasting, improving efficiency and responsiveness.
Internet of Things (IoT):
Real-time Data Collection: IoT sensors can collect data on various parameters like temperature, pressure, and vibration, providing valuable insights into the manufacturing process.
Remote Monitoring and Control: IoT enables remote monitoring of equipment and processes, allowing for quick response to issues and improved overall efficiency.
Improved Traceability: IoT can track products throughout the supply chain, providing greater transparency and accountability.
Cloud Computing:
Scalability and Flexibility: Cloud computing allows manufacturers to scale their IT infrastructure up or down based on their needs, providing flexibility and cost-effectiveness.
Data Storage and Analysis: Cloud platforms offer vast storage capacity and powerful analytics tools, enabling manufacturers to gain insights from their data.
Collaboration and Communication: Cloud-based tools facilitate collaboration and communication between teams and partners, improving efficiency and responsiveness.
Gaurav Middha: I believe that digital transformation can play a crucial role in achieving our goals, particularly when it comes to risk management. We’ve made significant progress in diversifying our vendor base, especially in scenarios where we’ve had a single vendor. This has involved classifying these vendors and assessing their risks, categorizing them as low, medium, or high. From there, we’ve been able to develop contingency plans based on the specific risks identified. Additionally, we have tools
in place to track vendor inventories. We place great emphasis on building longterm relationships with our suppliers and fostering collaborative approaches to generate innovative ideas and improve cost management practices.
Which emerging blockchain or AI would have the biggest impact on Indian manufacturing over the next decade?
Pratibha Nath: We are entering the era of smart factories, where technologies like AI, machine learning, and cloud computing play a crucial role. However, to fully leverage these advancements, we must establish the necessary infrastructure within our systems. This ensures high-quality operations, minimizes machine downtime, and enables predictive maintenance. The integration of these technologies in smart factories will be a key driver of success moving forward.
Similarly, blockchain is transforming the logistics industry by enhancing transparency, efficiency, and security in supply chain operations. By providing all stakeholders with access to validated, immutable records, blockchain reduces errors and increases accountability. Secure digital documentation significantly cuts lead times but requires strong collaboration among freight forwarders, government customs organizations, and other key players.
This capability not only improves delivery accuracy but also optimizes overall supply chain efficiency through real-time updates and secure transaction records. While challenges remain—such as scalability, integration with existing systems, data privacy, regulations, and implementation costs, I am confident that we will overcome these hurdles. By embracing cutting-edge technology, we can shape the future of logistics and drive innovation across industries.
Hanuman Swami: Blockchain and AI hold transformative potential for Indian manufacturing. Blockchain, with its secure and transparent recordkeeping, can revolutionize supply chain management. It ensures traceability of raw materials and finished goods, minimizes fraud, and builds trust among stakeholders. This is especially
critical for sectors like pharmaceuticals and food processing, where compliance and quality assurance are paramount. On the other hand, AI-driven solutions are unlocking new levels of efficiency. Predictive maintenance, powered by AI, can significantly reduce downtime by forecasting equipment failures. AI also optimizes production schedules and enhances quality control through realtime monitoring and defect detection.
Over the next decade, the integration of AI and blockchain will enable Indian manufacturers to streamline operations, meet global standards, and strengthen their position in the international market. Collaborative ecosystems will emerge, driven by these technologies, to foster innovation and agility.
Gaurav Middha: Emerging technologies like blockchain and AI have the potential to revolutionize the food manufacturing industry in India over the next decade. Blockchain technology is poised to significantly impact large Indian food manufacturers by enhancing supply chain transparency and efficiency. It can provide a tamper-proof ledger for tracking the journey of food products from farm to fork, reducing fraud, and ensuring food safety. Blockchain can also help streamline processes like procurement, inventory management, and compliance with regulatory standards, ultimately lowering costs and increasing trust among consumers and partners.
On the other hand, AI can drive innovation and improve operational efficiency for large food manufacturers. AI-powered predictive maintenance can help identify and address equipment issues before they lead to costly downtime, ensuring smooth production processes. Moreover, AI can optimize production lines by monitoring and controlling factors such as temperature, humidity, and machinery performance. AI-driven analytics can also help manufacturers understand consumer preferences and forecast demand, allowing for more personalized and efficient production. In essence, both blockchain and AI will play crucial roles in making India’s food manufacturing sector more robust, transparent, and responsive to market needs, contributing to the country’s goal of becoming a global manufacturing hub.
“In India, the transportation sector is responsible for around 14% of the country’s total GHG emissions, with freight transportation accounting for nearly 40% of CO2 emissions within this sector. Without intervention or cleaner technologies, transportation emissions are projected to increase by 4-fold between 2016 & 2050, potentially reaching 1.17 billion tons of CO2 by 2050 and would increase the share of transport in total emissions to 19%. To achieve sustainable supply chain management, companies need to work closely with suppliers, customers, and other stakeholders. By working together, companies can create a more sustainable future for all,” emphasizes Dr. Aditya Gupta, COO, Supply Chain Management Centre, Indian Institute of Management, Bangalore (IIM-B), during this exclusive interaction…
Prior to his academic pursuits, Dr. Aditya Gupta gained extensive experience as a supply chain practitioner in the corporate sector, holding various positions of responsibility at organizations such as Tata Group, TVS Group, Jindal Group, Virgin Mobile, and Moser Baer, for a period of 23 years. He completed his PhD in 2019 and subsequently transitioned from a career in corporate to academia. Dr. Gupta is deeply passionate about sustainability and has developed tools like the Transportation Emission Measurement Tool and Carbon Accounting Tool to measure emissions.
How is sustainability going to impact supply chains and how can companies derive value from making the supply chains more sustainable?
Industry 4.0 or digitalization and sustainability are the two key megatrends which are impacting supply chains of today and tomorrow. There are several ways in which sustainability is reshaping supply chains of tomorrow. I would like to share four ways in which sustainability is impacting the supply chain. The first is decarbonization of supply chain. If we go by the recent news updates, most of the large corporates have declared to go Net Zero by 2040-50. This target just doesn’t include Scope 1 & 2 emissions, they go beyond and in fact focus more on Scope 3 emissions. Under Scope 3 emissions, the supply chain has a major role to play. There’s no escaping the fact that any company that envisions achieving Net Zero target, has to work on its supply chain emissions.
Another big trend that we are witnessing in this space is Circular Economy. We are witnessing shifting sands of change from Linear to Circular economy. In Linear, we talk about Take, Make, Use and Dispose. While in circular, we lay emphasis on closed loop system. There is an increasing pressure on supply chain or procurement officer not to procure virgin material and replace the entire virgin material with either recycled, modular, biodegradable or compostable materials.
The third big impact that we will see is with regards to regulations. There is a greater thrust by the government machinery on environment sustainability and that’s why we are witnessing formation of new policies and rules that mandate sustainability as part of business strategy. I would like to talk about one regulation which I believe will have a significant impact on supply chain – The Corporate Sustainability Due Diligence Directive (CSDDD). On 25 July 2024, the Directive on corporate sustainability due diligence entered into force in Europe. The aim of this Directive is to foster sustainable and responsible corporate behavior in companies’ operations and across their global value chains. The new rules will ensure that companies in scope identify and address adverse human rights and environmental impacts of
TCI-IIMB Supply Chain Sustainability (TCI-IIMB SCSL) Lab’s primary focus areas include the measurement, mitigation, and management of supply chain emissions. The crucial first step in this journey is measuring emissions, and we are developing tools for this purpose. For example, the Transportation Emissions Measurement Tool (TEMT) is already live and measures emissions from freight transportation across all modes. We have also developed a carbon accounting tool to measure scope 1, 2, and 3 emissions for the MSME sector. The next step involves mitigation, where we focus on solutions such as energy efficiency, decarbonization of transportation, the circular economy, green packaging, design for the environment, sustainable procurement, and more to mitigate emissions from supply chains. Lastly, we are concentrating on building and sustaining sustainability programs within organizations, providing training, and fostering a culture of sustainability.
their actions inside and outside Europe. It will become a law by 2026 in several European countries. This law is also called as Supply Chain Law. It mandates all the large corporates in Europe to perform due diligence of all their supply chain / value chain partners up to Nth level. Such a law is going to have a significant outcome on global supply chains.
The fourth major impact will be the physical risks arising from climate change. The frequency and intensity of extreme weather events are increasing, leading to significant supply chain disruptions. For instance, a supplier may fail to deliver due to a cyclone in their region, a company might struggle to fulfill orders because of warehouse flooding, or manufacturing could grind to a halt due to water scarcity caused by drought near a factory. These scenarios highlight the tangible risks businesses may face in the future as a result of climate change. To sum up, the impact of sustainability on Supply chains will be profound and pervasive.
How can we make transportation as a service sustainable without a lot of impact on cost?
When we talk about decarbonization of supply chain, decarbonization of transportation is the most important element. I hear a lot of supply chain managers discussing the lack of EVs available in the country for freight movement, and this being one of the major reasons for not being able to decarbonize. EV is one part of the solution. There are several other aspects that need to be dealt with when it comes to decarbonization of transportation. When you outsource this service to a transportation company, there are certain things which can be made efficient but are beyond your control. For instance, driver behavior can have a significant impact on fuel efficiency, but you can’t control that aspect. Hiring efficient vehicles can reduce emissions but not under your control. Route planning can again have an impact on fuel efficiency but still doesn’t fall under your control
purview because you have outsourced that service. Use of alternative fuels such as green hydrogen or LNG, also doesn’t come under your control.
There are six key logistics drivers that can be used to influence the environmental impact of logistics: Distance to be travelled, Mode of shipment, Transport Equipment being used, Fuel to power, Load Planning and Operation Execution.
By considering these drivers, it is possible to design greener logistics systems. Following are some of strategies which the companies may use to make their logistics greener:
Modal Shift: The first thing I would like to draw all the supply chain planners’ attention is towards modal shift. As a practice, we must switch to a more sustainable route of transport from air to road, from road to rail and from rail to water, wherever it is feasible.
Load Consolidation: The second important aspect is in terms of load consolidation. For instance, if you are sending two 10-ton trucks, instead of that, if you move a one 20-ton truck, then you are reducing your emissions by almost 30-40% upfront. By consolidating
cargo and shifting to higher payload vehicles, it is possible to significantly reduce emissions.
Vehicle Space Utilization: Maximizing the cube of the vehicle and utilizing every single inch of the vehicle for transportation is also one of the efficient ways to reduce emissions.
Network Redesigning: Another aspect that the supply chain professionals need to work towards is network redesign. The redesign of the distribution network to place distribution centers where demand is highest can help reduce the total weight-distance travelled, without compromising customer service.
As logistics professionals, we can influence the secondary packaging also. Minimizing the use of secondary packaging materials, light weighting them, using eco-friendly materials, and promoting the reuse and recycling of packaging materials.
Choosing Right LSP partners: As we do not directly influence the route, vehicle type and the driver behavior, it is essential to choose right transportation
partners who are making efforts to reduce their emissions.
EV in the last mile: EV options may not be easily available for the mid mile, but there are three and four-wheeler EV options available for last mile delivery. Companies must explore them to deliver to retail outlets or directly to customers.
Measurement: The first step in any improvement exercise is the Measurement. Companies must start measuring their emissions even if they are not able to reduce them to begin with.
Green Warehousing: Implementing energy-efficient lighting, insulation, and heating systems, using renewable energy sources, and reducing waste and water consumption.
If you don’t know that root cause of emissions, you can’t take the right measures to solve them. To achieve sustainable supply chain management, companies need to work closely with suppliers, customers, and other stakeholders. By working together, companies can create a more sustainable future for all.
Rather than focusing solely on the upfront cost of acquisition, companies should evaluate the total lifecycle cost of a product. This includes operating costs, maintenance costs, and end-of-life costs. For example, compare a diesel forklift with an electric forklift or a standard motor with a Variable Frequency Drive (VFD) motor. When lifecycle costs—including carbon costs— are considered, the sustainable option often provides better long-term value.
Are there any tools available to measure & report emissions?
In India, the transportation sector is responsible for around 14% of the country's total GHG emissions, with freight transportation accounting for nearly 40% of CO₂ emissions within this sector. Without intervention or cleaner technologies, transportation emissions are projected to increase by 4-fold between 2016 & 2050, potentially reaching 1.17 billion tons of CO₂ by 2050 and would increase the share of transport in total emissions to 19%.
Another important aspect is that the transportation emissions factors that are available in India are incomplete, dated, and limited. Accurate measurement is the critical first step toward mitigating these emissions. Organizations need robust tools to measure their emissions before they can take meaningful action to reduce them.
In response to the escalating call for decarbonization of value chains and the imperative to manage scope three emissions, IIM Bangalore has established the TCI-IIMB Supply Chain Sustainability (TCI-IIMB SCSL) Lab. This dedicated lab is designed to assist organizations in their journey towards achieving net-zero goals. The TCI-IIMB SCSL Lab represents a significant initiative aimed at propelling sustainability in logistics and supply chain management to the forefront.
We take pride in stating that the TCIIIMB Supply Chain Sustainability Lab has become the first organization in India to achieve ISO 14083 certification for its groundbreaking digital platform, the Transportation Emissions Measurement Tool (TEMT). ISO 14083, developed by the International Organization for Standardization (ISO), provides a global standard for quantifying GHG emissions from transport operations.
Applicable to road, rail, air, maritime, and inland waterway transport, it covers fuel combustion and electricity consumption. The standard outlines calculation methods, data requirements, and reporting guidelines, offering a standardized framework for tracking emissions and enabling organizations to make informed decisions on emissionreduction strategies.
The certification underscores the platform’s ability to accurately quantify and report greenhouse gas (GHG) emissions from freight transportation activities, helping organizations to measure, manage, and ultimately reduce their transportation-related emissions in line with regulatory requirements and sustainability goals. The emission factors API is now available on ULIP platform.
TEMT is a comprehensive online platform designed to measure emissions across all modes of transportation. TEMT, with its certified emissions factors across multiple transport modes, empowers organizations to quantify and report emissions accurately, setting the stage for effective emission-reduction strategies.
It integrates India-specific emission factors, validated through ISO 14083 certification, ensuring data accuracy and relevance. The tool allows users to calculate emissions for both past and future shipments and compare emissions between different transport modes for a given origin-destination pair. It also offers users the flexibility to build customized transportation chains, with all past entries securely stored in the cloud for easy monthly tracking and yearover-year comparison. The platform is commodity-agnostic, meaning it applies to all types of shipments, and outputs are available in PDF and CSV formats for ease of reporting and analysis.
How does the lab compare to global standards in terms of research, innovation, and implementation of sustainable supply chain practices?
The lab is still in its nascent stage and has just embarked on its journey. Since it was established at IIM Bangalore, our goal is to make it truly world-class. However, the lab’s focus is on the Indian perspective. We aim to make supply chains in India more sustainable. We have already developed tools with a wide reach and national impact. We are conducting research in collaboration with various government institutions. Our stakeholders include multiple government and private agencies, NGOs, educational institutions, and more. We are creating white papers and case studies to disseminate sustainable supply chain knowledge to the global community. While our standards align with global practices, our primary focus is on the national context.
The lab’s primary focus areas include the measurement, mitigation, and management of supply chain emissions. The crucial first step in this journey is measuring emissions, and we are developing tools for this purpose. For example, the Transportation Emissions Measurement Tool (TEMT) is already live and measures emissions from freight transportation across all modes. We have also developed a carbon accounting tool to measure scope 1, 2, and 3 emissions for the MSME sector. The next step involves mitigation, where we focus on solutions such as energy efficiency, decarbonization of transportation, the circular economy, green packaging, design for the environment, sustainable procurement, and more to mitigate emissions from supply chains. Lastly, we are concentrating on building and sustaining sustainability programs within organizations, providing training,
Companies may implement route optimization software to reduce fuel consumption, lower emissions, and improve delivery efficiency. They may invest in electric vehicles to minimize carbon emissions and enhance safety. They can now utilize digital freight marketplaces to optimize capacity utilization, reduce empty miles, and lower emissions. IoT devices can track vehicle performance, fuel consumption, and emissions in real-time, enabling data-driven decisions to optimize operations. AI-powered solutions maximize vehicle capacity utilization, reducing trips and emissions.
and fostering a culture of sustainability.
Would you like to cite a successful example of sustainability by Indian company?
While the examples are many going by the sustainability trends that are shaping up in the country, one of the first examples that comes to my mind is of Kalyani Steel – the company came up with the first green steel in India. Saarloha Advanced Materials Pvt. Ltd. (Saarloha), a Kalyani group company, launched first of its kind in India, green steel under the brand “KALYANI FeRRESTA”. This makes Saarloha the first supplier of Made in India green steel. KALYANI FeRRESTA steel products are manufactured in an Electric Arc Furnace using electricity from 100% of renewable energy sources and more than 70% recycled scrap material with zero GHG footprint. KALYANI FeRRESTA PLUS has Net Zero GHG emissions per ton of Crude steel whereas KALYANI FeRRESTA has very low GHG emission of <0.19 tCO2e per MT of Crude Steel. Added to that, customers purchasing
KALYANI FeRRESTA & KALYANI FeRRESTA PLUS steel products will get Green Steel certificates jointly issued by DNV Business Assurance India Pvt. Ltd. & Saarloha, which they can use to claim their Scope 3 emissions reduction.
Ethical & sustainable procurement is getting priority across the Indian companies and MNCs. What are your suggestions on making procurement sustainable?
When we talk about sustainability in procurement, it involves two key aspects: making the product more sustainable and making the supplier more sustainable.
Making the Product More Sustainable: When we refer to the "product," we mean the raw materials, components, or packaging that a company procures. This is the more challenging aspect of sustainable procurement. Identifying sustainable alternatives requires extensive research and development (R&D) and often involves significant trade-offs. For instance, replacing conventional steel
with green steel comes at a premium, creating cost implications. This is both an R&D and supply chain challenge. However, leading companies are investing heavily in finding innovative, low-carbon alternatives for materials, signalling that significant progress is being made in this area.
Making the Supplier More Sustainable: The second aspect, making suppliers more sustainable, is largely a supply chain management challenge. Companies can follow several actionable steps to address this:
Step 1: Implement a Supplier Code of Conduct: A supplier code of conduct sets clear expectations regarding environmental and social standards. Many leading companies already adopt this practice. A prime example is IKEA's IWAY Supplier Code of Conduct. Before supplying to IKEA, a supplier must meet specific baseline standards. Over the next 12 months, IKEA works with them to progress to higher levels, eventually reaching advanced sustainability
standards. This collaborative approach drives continuous improvement.
Step 2: Integrate Sustainability into Supplier Selection Criteria: Sustainability should be embedded into supplier evaluation processes alongside traditional metrics like Quality, Cost, and Delivery (Q, C, D). The new framework should emphasize Q, C, D, and S (Sustainability). This ensures that suppliers’ environmental and social performance becomes a critical consideration.
Step 3: Adopt Whole-Life Costing (Lifecycle Costing): Rather than focusing solely on the upfront cost of acquisition, companies should evaluate the total lifecycle cost of a product. This includes operating costs, maintenance costs, and end-of-life costs. For example, compare a diesel forklift with an electric forklift or a standard motor with a Variable Frequency Drive (VFD) motor. When lifecycle costs— including carbon costs—are considered, the sustainable option often provides better long-term value.
Step 4: Collaborate with Suppliers on Decarbonization: Supplier decarbonization is not a singles match; it’s a doubles game where the company and the supplier are on the same side, working together against carbon emissions and environmental challenges.
c Companies need to actively engage with suppliers to help them measure and reduce their emissions.
c Tools such as carbon accounting software can be shared with suppliers to enable accurate tracking.
c Providing technical support and sharing best practices on decarbonization creates a partnership-driven approach to sustainability.
Step 5: Build Internal Capabilities: To drive sustainable procurement, a company’s internal teams must be trained and empowered.
c Sustainability Key Result Areas (KRAs) should be embedded into their objectives.
c Teams must understand how to engage suppliers, evaluate lifecycle
costs, and implement decarbonization strategies effectively.
How is technology helping organizations in their sustainability journey?
I will only address the supply chain part of the sustainability journey. There are 5 facets of supply chain sustainability, and we will address use of technology in each of them – Procurement, Transportation, warehousing, Circular Economy and Packaging.
Procurement: Digital tools like SAP Ariba and EcoVadis help assess suppliers' environmental and social performance or ESG ratings, helping businesses make informed decisions and drive improvements. Blockchain technology can track products from origin to consumer, ensuring ethical sourcing, fair labor practices, and reduced environmental impact. Implement electronic contracts and documentation to minimize paper usage and streamline procurement processes. Leverage predictive analytics to forecast demand, reducing the need for carbon-intensive modes of shipments like Air.
Transportation: Companies may implement route optimization software to reduce fuel consumption, lower emissions, and improve delivery efficiency. They may invest in electric vehicles to minimize carbon emissions and enhance safety. They can now utilize digital freight marketplaces to optimize capacity utilization, reduce empty miles, and lower emissions. IoT devices can track vehicle performance, fuel consumption, and emissions in real-time, enabling datadriven decisions to optimize operations. AI-powered solutions maximize vehicle capacity utilization, reducing trips and emissions.
Warehousing: Companies may install energy-efficient lighting and material handling equipment to reduce energy consumption and lower emissions. Implement WMS to optimize inventory management, reduce waste, and improve operational efficiency. Though costly invest in AS/RS can minimize energy consumption, reduce labor costs, and enhance inventory accuracy.
Large warehouses may implement Energy Management Systems for realtime monitoring of warehouse energy consumption which optimizes HVAC, lighting, and equipment usage to lower emissions. Companies may install solar panels at roof tops to generate renewable energy and reduce overall carbon footprint.
Circular Economy: Companies may conduct a detailed Life Cycle Assessment using LCA tools to evaluate the environmental footprint of their products and then use it to design products for recyclability, reuse, and repair, extending product lifespans and reducing waste. Technology can streamline the process of collecting, sorting, and recycling used products, promoting a circular economy. Company may use sharing Platforms to facilitate product-sharing or reuse opportunities, extending product life cycles and reducing raw material needs. Digital Twins is another way to model product lifecycles to assess how materials can be reused or recycled efficiently.
Green Packaging: Companies may use design and simulation Software to design and simulate packaging with minimal material usage, recyclability, and biodegradability in mind. AI can analyze packaging data to identify opportunities for reducing material usage and improving efficiency. By embracing technology, businesses can significantly reduce their carbon footprint, improve resource efficiency, and build more sustainable supply chains.
Much like the eagerly awaited and wildly celebrated Coldplay concert, which has now resplendently concluded, the cold chain sector within our country has been basking in a similar spotlight of attention from all corners in recent years. Be it the guiding hands of government machinery, the dedicated service providers, the dynamic startup ecosystem, or the industrious user base, every sphere has been actively contributing to its growth. A collective and impassioned effort has been underway to foster innovation, elevate the sector’s competitiveness, and bring it on par with global standards. In this Special Report, we offer you a glimpse into expert insights on the evolving landscape of cold chain infrastructure, the groundbreaking technological strides, and the burgeoning promise of sustainable growth – all through an engaging Q&A format. Read on…
The last 5 years have been transformational for the cold chain segment in the country. What’s your view on this? What are some of the striking changes that you have witnessed in these years?
Chandramani Behera, Head –Transportation, Snowman Logistics Ltd.: The cold chain segment has experienced remarkable transformation over the last five years, largely driven by the following factors:
Technological Advancements: The integration of IOT, AI, and data analytics has significantly improved monitoring and control of temperature-sensitive goods, enabling real-time visibility and predictive capabilities that enhance operational efficiency.
Regulatory Compliance: Heightened regulatory standards, particularly in the pharmaceutical and food sectors, have necessitated stricter temperature controls and traceability, prompting advancements in compliance-driven technologies.
Expansion of Infrastructure: There has been substantial growth in both cold storage capacity and refrigerated transportation networks, allowing for more efficient handling of perishable goods across broader geographic areas.
Demand Surge: The rise in e-commerce and an increasing consumer preference for perishable and health-conscious products have directly elevated the demand for efficient and reliable cold chain solutions.
These drivers have collectively fostered greater efficiency, transparency, and scalability within the cold chain
industry, positioning it for sustained growth and innovation.
Soumalya Mukherjee, Co-founder, Tan90: The market of cold chain in India was unorganized a decade back, with major impact on pharmaceuticals and ice cream industries. Rise in urbanization and change in consumption pattern among urban population has led to the meteoric rise in quick commerce and D2C businesses. Their rise is fueled by faster delivery timelines, requiring a vast network of dark stores spread across a geography, requiring a robust cold chain infrastructure. The most searched for item on any quick commerce platform is either milk or ice cream, which both require cold chain management percolating down to the last mile movements. Scaling operations while maintaining no thermal breach along the supply chain require modern solute ions like passive cooling through Phase Change Materials (PCMs). PCMs also allow part-load movements in normal vehicles, thereby decreasing the cost of transportation per unit by 30% as compared to refrigerated trucks. This value proposition has enabled the quick commerce industry to learn about PCMs and apply them in their operations. There has been a surge of inclusion of technology in this space as well with blockchain based tracking, IoT based temperature logging, thereby increasing confidence among consumers about cold chain in India. Movement of chilled products by newly launched EV refrigerated vehicles can be a game changer as well and holds potential for serving tier II and III cities as well.
Kartik Jalan, Founder & CEO, Indicold: The biggest catalyst that transformed the cold chain segment was
COVID, giving it a push towards online in a big way. People lived a whole year if not months in certain communities on online ordered food, fresh vegetables and frozen/chilled foods. The industry since then has not only grown but is also changing the way the cold chain segment in the country will work going forward. Quick commerce is booming and so is the frozen food industry. This is impacting space requirements across the country. During this time, there has been a considerable push on sustainable infrastructure as well.
Indicold is playing its part in transforming the industry by installing two transformational cold storage automation projects in the country. Automation was earlier considered to be outside the domain of Indian cold chain company offerings. Now, Indicold is offering the same at competitive market rates. Further, Indicold is working towards creating net zero cold chain projects using geothermal and other renewable sources of energy.
What challenges persist in cold chain management? How can companies mitigate them?
Chandramani Behera: Despite significant advancements, several challenges remain in cold chain management:
Infrastructure Gaps: While urban areas have seen significant advancements in cold chain infrastructure, rural and remote regions still lack sufficient temperature-controlled facilities, which limits service coverage and operational efficiency.
Cost Pressures: The high operational costs associated with energy consumption,
Phase Change Materials (PCMs) are positioning themselves as a future in this vertical. Not only in transportation, PCMs also have a clear value add in storage and warehousing space. Cold storage warehouses rely on continuous power supply and with time-of-day tariffs in place, the operational costs for running cold storage often balloon up. Taking a cue from peak shift, PCMs can be used to maintain temperatures in cold storages during peak hours, keeping the compressors idle, while charging them during off-peaks. This is a proven concept in the US and European countries, where a savings of 20% is seen by implementing PCMs in cold storages, with provisions for application in both green (new) and grey fields (retrofitting in present cold storages).
Sustainability is a major factor shaping
consumer preferences. The growing demand for eco-friendly products and processes is pushing cold chain providers to adopt green technologies, improve transparency, and optimize efficiency. As expectations evolve, the industry must balance sustainability with maintaining product integrity and operational excellence.
maintaining temperature-controlled equipment, and logistics can impact profitability. These costs are particularly burdensome for smaller players in the market.
Temperature Variability and Risk: Unexpected disruptions—such as power outages, transit delays, or equipment failures—can lead to temperature deviations, which may compromise the integrity of the products, particularly in the pharmaceutical and food sectors.
To mitigate these challenges, companies can adopt the following strategies:
Investing in Advanced Technologies: Leveraging IoT-based monitoring systems, AI-driven predictive analytics, and real-time temperature tracking can help ensure operational continuity and minimize risks associated with temperature fluctuations.
Energy-Efficient Solutions: Transitioning to more energy-efficient refrigeration technologies, such as hydrocarbonbased systems or using renewable energy sources, can help reduce long-term operational costs.
Collaborative Infrastructure Development: By forming strategic partnerships with government agencies and other stakeholders, companies can work towards expanding infrastructure in underserved regions, improving overall supply chain efficiency. These strategies not only address existing challenges but also enhance the resilience and sustainability of cold chain operations in the long term.
Soumalya Mukherjee: A lot of work is still left in building infrastructure in the tier II and III cities, both in stationery and mobility applications. When it comes to cold chain logistics, using passive coolants, there are a lot of gaps in the awareness of Phase Change Materials (PCMs). This results in
industries using rudimentary solutions like gel packs for anything that requires temperature management. When used in pharmaceuticals, gels packs result in cold shocks and often fail on long term temperature retention. Chilled water is often used for maintaining temperatures between +18 to +22 degrees centigrade, which is not effective. PCM of +16 degrees Centigrade would be the correct choice for such applications, however high costs hinder its adoption.
Serial deliveries with frequent opening of doors, prevalent in the last mile movement of quick commerce industries, often poses a challenge with maintaining temperatures over a long period of time. This can be mitigated by using PCMs in discreet insulted boxes. However, the usage of PCMs often requires the need for specialized blast freezers, which are heavy on Capex. Working on this problem, Tan90 Thermal Solutions has pioneered a model along Cooling as a Service (CaaS), wherein they give the flexibility to clients to use pre-frozen panels without owning any capital-intensive freezers.
Coming to stationary applications, cold storage warehouses are energy intensive, and require a seamless power supply, which is still missing in remote areas. Use of renewable sources of energy for running cold storages is an interesting prospect. On that front, solar powered container based cold storages have come up, but are only limited to chilled products or FnV and cannot be used for frozen foods.
Kartik Jalan: India’s cold chain market is experiencing rapid expansion, fueled by increasing demand for fresh produce, pharmaceuticals, and frozen foods. However, challenges such as inadequate infrastructure, unreliable power supply, a shortage of skilled labor, and gaps in lastmile connectivity—particularly in rural areas—remain significant obstacles. These issues contribute to inefficiencies and substantial wastage of perishable goods.
To address these challenges, companies are investing in new infrastructure, incorporating palletized and automated solutions tailored to business needs. Solar-powered cold storage and other renewable energy alternatives are being explored to mitigate energy shortages and enhance sustainability. Strengthening last-mile delivery, especially through strategic partnerships and innovative models, is crucial for improving accessibility and efficiency.
Government support through incentives, subsidies, and skill-building programs can further accelerate progress. As the market grows, collaboration between stakeholders and adoption of advanced technologies will be critical in transforming India’s cold chain into a more resilient and efficient ecosystem.
Please enlighten us on the shifting demand patterns of consumers when it comes to cold chain.
Chandramani Behera: Consumer demands are increasingly influencing the evolution of cold chain logistics, particularly in the following areas:
Higher Expectations for Freshness and Quality: There is a growing preference for fresh, organic, and health-focused products that require stringent temperature control throughout the supply chain. This has driven the need for enhanced reliability in cold chain infrastructure, particularly for perishable goods.
Rapid Delivery Timelines: The rise in online grocery shopping and e-commerce has accelerated the need for quicker, more efficient delivery of temperaturesensitive products. Consumers now expect faster delivery times, often requiring solutions that support sameday or next-day delivery of perishable items.
Increased Focus on Transparency:
Consumers are becoming more aware of product sourcing and quality, demanding more transparency in the supply chain. Cold chain logistics providers must now offer real-time tracking and proof of compliance with temperature requirements, particularly for sensitive pharmaceuticals and food products.
In parallel, the pharmaceutical sector is experiencing a shift toward biopharmaceuticals and temperaturesensitive biologics, which require robust cold chain solutions to maintain efficacy and safety.
These shifts are driving the adoption of more advanced technologies, streamlined logistics networks, and enhanced tracking systems to meet the growing consumer expectations for faster, more reliable, and transparent cold chain services.
Kartik Jalan: We are now in a postCOVID era, where change has accelerated across industries. In the cold chain sector, consumer demand patterns are evolving rapidly, driven by shifting lifestyles, health-conscious choices, and the growing need for convenience. The rising demand for fresh produce, frozen meals, and ready-to-eat foods reflects a preference for quality and variety. At the same time, the pharmaceutical sector is driving increased reliance on temperature-controlled logistics, particularly for biopharmaceuticals and personalized medicine.
Additionally, hotter summers and shorter winters have heightened the need for temperature-controlled warehousing across industries, including food, pharmaceuticals, chemicals, and automotive. This transformation underscores the need for agile cold chain systems that can accommodate smaller, more frequent shipments — especially
Sustainability in cold chain logistics is no longer just an option — it’s essential for the industry’s growth. As the demand for temperature-sensitive goods increases, companies must balance operational efficiency with environmental responsibility. This involves investing in energy-efficient refrigeration systems with low-global-warming-potential (GWP) refrigerants, utilizing renewable energy sources like solar power, geothermal and deploying sensors for predictive maintenance and efficient running of the plant. Sustainable packaging solutions and smarter transportation planning are also vital in reducing emissions and operational costs.
for e-commerce and direct-to-consumer deliveries. Urban consumers prioritize speed and freshness, prompting investments in localized distribution hubs and advanced packaging solutions to enhance last-mile delivery.
Sustainability is also a major factor shaping consumer preferences. The growing demand for eco-friendly products and processes is pushing cold chain providers to adopt green technologies, improve transparency, and optimize efficiency. As expectations evolve, the industry must balance sustainability with maintaining product integrity and operational excellence.
What’s happening on the warehousing front as well in this regard? What are the packaging innovations shaping up in the cold chain segment?
Chandramani Behera: On the warehousing front, Snowman Logistics is investing heavily in automated temperature-controlled facilities that utilize advanced robotics and AI for inventory management, temperature monitoring, and overall operational efficiency. These facilities enable scalability, greater storage capacity, and compliance with increasingly stringent regulatory frameworks.
Advancements in both cold storage and packaging technologies play a pivotal role in enhancing the efficiency and sustainability of cold chain operations:
Cold Storage Innovations: The development of automated, temperature-controlled warehouses equipped with advanced robotics and AI-driven inventory management systems is enabling greater operational efficiency, improved scalability, and real-time monitoring. These innovations help meet the rising
demand for rapid order fulfilment, particularly in e-commerce and perishable goods sectors.
Packaging Solutions: Packaging technologies are becoming increasingly sophisticated, with innovations such as Phase Change Materials (PCMs) and active insulation materials ensuring that temperature-sensitive products maintain optimal conditions during transit, reducing the risk of spoilage. Additionally, sustainable packaging options, including recyclable and biodegradable materials, are gaining traction as part of the industry’s move towards greater environmental responsibility.
Smart Packaging: Integration of RFID tags and temperature-sensitive labels into packaging allows for better traceability and real-time condition monitoring, offering enhanced visibility throughout the cold chain and improving product safety.
These advancements in storage and packaging not only improve the operational integrity of cold chain systems but also help companies meet consumer demands for sustainability and transparency.
Soumalya Mukherjee: Temperature retention is influenced by three major factors: Cooling, Insulation Characteristics, and the Temperature Gradient between the product and the ambient environment. A lot of work has been done on insulation design, and its characteristics. Advanced materials like aerogel and vacuum insulated panels (VIPs) are picking up pace in this segment in niche segments like pharmaceuticals. Efforts are needed to establish manufacturing of these
specialized materials in India, and these are being imported from the European countries currently.
Radiative cooling finds a fit for space cooling applications, in which functional paints (in conjunction with insulating materials) are coated on surfaces, providing a temperature variation of 10 degrees Centigrade and above. Such solutions are retrofittable and require minimal upkeep, hence perfect fit for industrial applications. Using a hybrid power source to run cold storages (solar and grid) can be beneficial for their rural penetration. Presently, there are companies in India which provides AI powered services related to optimization, monitoring and controlling energy consumption in real time by cold storages and maximize their performances. Cooling as a Service (CaaS) is also available in this vertical, thereby preventing companies to invest upfront for the assets required for such monitoring.
Kartik Jalan: The cold chain segment in India is undergoing a remarkable transformation, with warehousing leading the charge. Indicold has pioneered this evolution by unveiling India’s first frozen Automated Storage and Retrieval System (ASRS) facility in Gujarat. This state-of-the-art facility exemplifies the shift toward automation, robotics, and energy-efficient refrigeration systems, making warehousing smarter, more efficient, and sustainable. Such advancements not only enhance storage capacity but also ensure precision and reliability in managing perishable goods.
Packaging innovations complement these efforts, focusing on preserving product integrity and minimizing environmental impact. Smart technologies like IoT and RFID provide real-time tracking, while temperature sensors maintain optimal conditions during transit. Sustainable solutions, including bioplastics, reusable packaging, and advanced insulation materials, ensure reduced waste without compromising quality.
Furthermore, packaging for even bulk storage, especially in automated systems, has become critical because the right quality of box will enable the material to be stored properly and retrieved properly.
Together, these advancements in warehousing and packaging are reshaping
India’s cold chain landscape, setting new benchmarks for efficiency, sustainability, and innovation.
What’s your take on government policy measures when it comes to harnessing cold chain? What’s your wish list from the government?
Chandramani Behera: The government has made commendable progress in supporting the cold chain industry through initiatives such as the Integrated Cold Chain Infrastructure Scheme, which aims to improve the capacity and efficiency of temperature-controlled logistics networks. However, further policy measures are needed to address ongoing challenges:
Standardization and Regulation: Clearer, more stringent standards for temperature control across industries, particularly pharmaceuticals, would ensure uniformity and reduce compliance complexities.
Tax Incentives: Enhanced tax relief for companies investing in energy-efficient cold chain technologies could stimulate the adoption of green practices.
Support for Sustainability: Providing incentives for energy-efficient refrigeration systems and green technologies could accelerate the transition towards more sustainable cold chain operations.
Public-Private Partnerships: Encouraging collaboration between the government and private players in underserved regions would help bridge infrastructure gaps, particularly in rural and remote areas.
R&D Funding: Increased government support for research and development in cold chain technologies, such as advanced refrigeration systems and sustainable packaging solutions, would drive further innovation and cost reduction in the sector.
These measures could provide long-term support for the cold chain industry’s growth, ensuring its ability to meet evolving market demands while contributing to environmental sustainability.
Soumalya Mukherjee: The Government has already taken substantial steps to
democratize cold chain infrastructure in the country, primarily opening up grants and subsidies through the Pradhan Mantri Kisan Sampada Yojana (PMKSY). Massive improvements in road infrastructure, policies to use green refrigerants in freezers have resulted in reducing carbon footprint considerably.
Promoting the use of solar energy to run cold storages would be a great step ahead. This can be realized through fostering public private partnerships which will eliminate the power issues faced in the remote areas, thereby penetrating more with world-class storage solutions. A shift in focus on cold storage warehouses, from fruit and vegetables to high value products like pharmaceuticals or frozen foods would be a welcome step.
Kartik Jalan: Government policies have significantly boosted India’s cold chain sector, with initiatives like the Pradhan Mantri Kisan SAMPADA Yojana and the Production-Linked Incentive (PLI) scheme paving the way for growth. These measures have enhanced infrastructure, reduced food wastage, and encouraged private sector participation. Subsidies for energy-efficient refrigeration and the GST reduction on cold storage equipment have also accelerated progress. However, there’s a pressing need to address specific gaps to unlock the sector’s full potential.
At Indicold, the vision is to see policies that foster a truly integrated ecosystem. Encouraging investments in advanced technologies, such as automation and AI, can redefine efficiency and sustainability. Government can encourage pilot projects or award existing innovations by encouraging support or grants. Simplifying land acquisition for building modern cold storage facilities, especially near consumption hubs, would ease urban storage constraints. Additionally, promoting renewable energy solutions like solar-powered refrigeration can align the sector with green goals.
The biggest expense is energy for cold storages. The government can help companies by removing peak charges for cold storages, by giving security deposit relief across cold chain facility electricity connections, by ensuring the land purchase or lease are stamp duty exemption for such critical infrastructure. These steps will go a long way in enabling the industry, as already the industry is capex heavy, and this will help without
hurting the exchequer.
With these steps, the government can empower India’s cold chain industry to not just meet domestic needs but also become a global leader in sustainable cold chain logistics.
What are the technological advancements shaping up in this segment? Kindly share with examples…
Chandramani Behera: Technological innovations are revolutionizing the cold chain industry, enhancing efficiency, reliability, and traceability in key areas:
Internet of Things (IoT) and Real-Time Monitoring: IoT-enabled sensors and monitoring systems are allowing for realtime tracking of temperature, humidity, and other environmental conditions across the supply chain. This continuous data flow enables immediate corrective actions in case of any deviations, ensuring product integrity and compliance with regulatory standards.
Block chain for Traceability: The integration of block chain technology provides an immutable ledger of data that enhances transparency and traceability, particularly for pharmaceuticals, where precise tracking from origin to final delivery is crucial to meet safety standards.
AI and Predictive Analytics: AI-powered platforms are enabling predictive analytics for route optimization, inventory management, and proactive maintenance of refrigeration systems, reducing operational costs and improving system reliability.
Automation in Storage and Handling: Automated cold storage systems, coupled with robotic process automation (RPA),
are increasing throughput and efficiency, reducing manual handling errors, and enabling scalable operations to meet growing demands.
These technological advances are driving the next generation of cold chain operations, ensuring greater control, reducing risks, and improving overall service reliability for clients across industries.
Soumalya Mukherjee: Phase Change Materials (PCMs) are positioning themselves as a future in this vertical. Not only in transportation, PCMs also have a clear value add in storage and warehousing space. Cold storage warehouses rely on continuous power supply and with time-of-day tariffs in place, the operational costs for running cold storage often balloon up. Taking a cue from peak shift, PCMs can be used to maintain temperatures in cold storages during peak hours, keeping the compressors idle, while charging them during off-peaks. This is a proven concept in the US and European countries, where a savings of 20% is seen by implementing PCMs in cold storages, with provisions for application in both green (new) and grey fields (retrofitting in present cold storages).
Working on the same principle, PCMs also have application in commercial freezers (ice cream chest freezers), making them more energy efficient, keeping performances intact even when there is a power cut. Such freezers can be of great importance when installed in rural areas.
Kartik Jalan: Technological advancements are driving significant change in the cold chain industry, improving efficiency, sustainability, and transparency. At Indicold, we are
embracing these innovations to enhance our operations. Through sensors, we monitor temperature-sensitive goods in real-time, ensuring that critical parameters like temperature and humidity are continuously tracked. This allows us to maintain and ensure the quality of goods.
Automation is also transforming our warehousing, as we have implemented Automated Storage and Retrieval Systems (ASRS) to streamline inventory management, reduce errors, and improve efficiency. In the future, we hope to incorporate AI and predictive analytics to help us optimize demand forecasting, route planning, and inventory control. By analyzing data from IoT sensors, we predict potential disruptions and take timely actions to prevent them.
Sustainability is a key focus as we adopt energy-efficient refrigeration solutions and explore renewable energy options like solar power. Additionally, the use of natural refrigerants and electric refrigerated vehicles helps reduce our environmental impact. These advancements are enabling Indicold in building a future ready sustainable cold supply chain.
What are the innovative services you are offering to your clients?
Chandramani Behera: Snowman Logistics offers a comprehensive suite of innovative cold chain services, including:
5PL Services: We’re the first in the country to offer 5PL services to our esteemed clients.
End-to-End Integrated Solutions: We offer fully integrated temperature-controlled logistics that span warehousing, transportation, and last-mile delivery, ensuring seamless operations and
The integration of blockchain technology provides an immutable ledger of data that enhances transparency and traceability, particularly for pharmaceuticals, where precise tracking from origin to final delivery is crucial to meet safety standards. Automated cold storage systems, coupled with robotic process automation (RPA), are increasing throughput and efficiency, reducing manual handling errors, and enabling scalable operations to meet growing demands. These technological advances are driving the next generation of cold chain operations, ensuring greater control, reducing risks, and improving overall service reliability for clients across industries.
product integrity across the supply chain.
Real-Time Monitoring and Analytics: Our advanced IoT-based monitoring systems provide continuous tracking of temperature, humidity, and other critical conditions, offering complete visibility and compliance with industry standards.
Predictive Analytics: By employing AI and machine learning algorithms, we can predict potential disruptions, such as equipment failures or supply chain bottlenecks, allowing us to proactively address these issues and ensure smooth operations.
Sustainability Integration: We focus on integrating eco-friendly technologies, such as energy-efficient refrigeration units and recyclable packaging, aligning our operations with global sustainability standards.
These innovations not only enhance operational efficiency but also provide our clients with greater control, transparency, and assurance of product quality throughout the cold chain.
Kartik Jalan: At Indicold, we believe in listening and delivering what the customer needs. We believe in delivering solutions and experiences which delight the customer. Our constant endeavor is to deliver beyond what the customer can imagine is possible.
In this endeavor, Indicold has delivered the First Frozen automated storage and retrieval system for our client. The facility is not only the first rack clad of the country but also has the first active fire prevention system installation of the country for such a facility. Our aim is to constantly CARE about the product, people and planet. At Indicold, we care about the environment, people, and the products we handle, delivering solutions that not only improve supply chain efficiency but also contribute to a greener, more sustainable future.
Do you see the cold chain sustainability combination working for the industry at large? If yes, how can companies work towards ensuring sustainable cold chain operations?
Chandramani Behera: Yes, the integration of sustainability into cold chain operations is not only possible but essential. Sustainability is becoming a critical focus in the cold chain industry
as companies face increasing pressure to reduce their environmental footprint while maintaining operational efficiency. Key considerations for promoting sustainable cold chain operations include:
Energy-Efficient Technologies: Companies can invest in energy-efficient refrigeration systems such as hydrocarbon-based cooling solutions that utilize natural refrigerants and optimize energy consumption, reducing both operational costs and environmental impact.
Green Warehousing Solutions: The transition to eco-friendly warehouses, utilizing renewable energy sources such as solar power and energy-efficient lighting and cooling systems, can significantly lower carbon footprints.
Sustainable Packaging: Emphasizing the use of biodegradable and recyclable packaging materials helps minimize waste while maintaining product integrity during transport.
Optimize Transport Logistics: Route optimization and better load consolidation can reduce fuel consumption and emissions, while the use of electric or hybrid vehicles for last-mile delivery can further reduce carbon footprints, which is a key area for environmental improvement in cold chain logistics.
Circular Economy Models: Implementing circular supply chain models—where resources such as packaging and containers are reused or recycled— can contribute to waste reduction and promote more sustainable practices.
By prioritizing these sustainable strategies, companies can reduce their carbon footprint, comply with global environmental standards, and meet the growing demand for environmentally responsible practices across industries. At Snowman Logistics, we are committed to embedding sustainability into every aspect of our operations, from reducing energy consumption to integrating eco-friendly packaging and logistics solutions.
Soumalya Mukherjee: Cold chain solution providers are investing massively in research and developing products that reduce the carbon footprint of cold transportation. Till now, cold chain solutions were energy hungry, running
on diesel fuels. The recent launch of refrigerated containers on EVs was an interesting step in this space, reducing dependency on fossil fuels, carbon footprint and opening opportunities for a possibly lower cold transportation cost. On the other hand, companies like Tan90 Thermal Solutions employ the concept of district cooling to freeze PCM cartridges on a bulk scale, thereby distributing energy costs, and providing customers pre-frozen –24-degree Centigrade PCM cartridges to transport ice cream and frozen desserts, using normal or electric vehicles. Large companies like CONCOR are also moving towards such solutions by integrating passive cooling solutions in their containers to move temperature sensitive products by railways. This proves that the industry, by large, is optimistic towards greener and sustainable solutions, and adoption has picked up pace in the last five years.
Kartik Jalan: Sustainability in cold chain logistics is no longer just an option—it’s essential for the industry’s growth. As the demand for temperaturesensitive goods increases, companies must balance operational efficiency with environmental responsibility. This involves investing in energy-efficient refrigeration systems with low-globalwarming-potential (GWP) refrigerants, utilizing renewable energy sources like solar power, geothermal and deploying sensors for predictive maintenance and efficient running of the plant. Sustainable packaging solutions and smarter transportation planning are also vital in reducing emissions and operational costs.
Indicold is embracing this shift by designing and building sustainable infrastructure ensuring all the above is met and more. Indicold is pioneer in Indian cold chain industry by being the first logistics company to setup a frozen ASRS in India. This infrastructure is more energy efficient and more compact than a traditional facility, hence contributing to the environment.
For the broader cold chain sector, prioritizing sustainable practices not only ensures long-term profitability and resilience but also reduces the environmental impact of the supply chain. As industry continues to evolve, adopting green technologies and practices will be crucial in building a future-ready cold chain that meets both operational and environmental goals.
The cold chain industry is experiencing significant growth and transformation as of 2025. Here are some key statistics and trends:
The global cold chain market is projected to expand from $405.02 billion in 2024 to $454.48 billion in 2025, reflecting a compound annual growth rate (CAGR) of 12.2%.
In the United Kingdom, the cold chain logistics market is estimated to be valued at $12.46 billion in 2025, with expectations to reach $18.44 billion by 2030, growing at a CAGR of 8.16% during this period.
The pharmaceutical sector’s reliance on cold chain solutions is anticipated to grow steadily, driven by an annual growth rate of 4.71% from 2024 to 2029, leading to a market volume of $1,454 billion by 2029.
The India cold chain logistics market is estimated at USD 12.77 billion in 2025 and is expected to reach USD 20.31 billion by 2030, growing at a compound annual growth rate (CAGR) of 9.72% during the forecast period.
Sustainability is becoming a focal point, with ongoing innovations in sustainable refrigeration technologies and energy-efficient systems shaping the future of the cold chain industry.
These developments underscore the critical role of the cold chain in ensuring the safe and efficient distribution of temperaturesensitive products across various sectors.
How do you foresee the prospects and possibilities of cold chain?
What are the upcoming trends that will shape the future of cold chain?
Chandramani Behera: The future of cold chain logistics is poised for significant transformation, with several emerging trends and opportunities set to shape the industry:
Pharmaceutical Sector Growth: The increasing demand for biologics, vaccines, and temperature-sensitive therapeutics will drive the need for highly specialized cold chain solutions, with an emphasis on precise temperature control and secure transportation. The rise of personalized medicine will further contribute to the demand for smaller, more flexible cold chain solutions.
Sustainability and Green Logistics: With growing environmental concerns, the cold chain industry is shifting towards more sustainable practices, including the adoption of energy-efficient refrigeration technologies and the use of renewable energy sources in warehouses and transportation. Eco-friendly packaging is also gaining traction as part of the drive toward a more sustainable supply chain.
Last-Mile Delivery Optimization: The surge in online grocery and food deliveries is leading to increased demand for rapid and reliable last-mile cold chain solutions. Technologies such as autonomous delivery systems and electric refrigerated vehicles are emerging as potential solutions for reducing delivery times while minimizing environmental impact.
Data-Driven Decision Making: The use of advanced analytics, AI, and machine learning will continue to grow, enabling cold chain providers to optimize routes, predict maintenance needs, and enhance demand forecasting, thereby improving efficiency and reducing costs.
Hyper-localized Warehousing: Smaller, decentralized warehouses closer to urban centres will emerge to support faster, more efficient delivery of temperaturesensitive goods, particularly in e-commerce.
These trends represent significant opportunities for innovation in cold chain logistics, providing new avenues for growth and enhancing the sector’s ability to meet evolving market demands.
Soumalya Mukherjee: Cold chain by railways, without grid power, is a dream that I envision. Railways have an extension network throughout the country and if plugged in properly, are faster than roadways. Creating an integrated ecosystem, end-to-end, from cold storages, pack houses, and logistics around railways would be highly beneficial for the country. This will not only be sustainable, but a faster turnaround for import and export transactions.
Kartik Jalan: India’s cold chain logistics market is poised for significant growth, projected to reach USD 12.77 billion in 2025 and USD 20.31 billion by 2030, growing at a CAGR of 9.72%.
Driven by the pharmaceutical and food sectors, industry is undergoing rapid transformation. India is the world’s largest provider of generic drugs, supplying over 50% of global vaccine demand, with pharmaceutical exports reaching USD 25.4 billion in FY23. In the food sector, India ranks as the largest producer of milk and the second-largest producer of fruits and vegetables.
Key trends shaping the industry include automation, sustainability, and enhanced supply chain visibility. A lot of new companies in IOT space across machine health, vehicle tracking etc., are ensuring transparency and visibility. Government initiatives, such as 20 mega food parks, 371 cold chain projects, and 68 agro-processing clusters, are strengthening infrastructure and driving value addition. The Ministry of Food Processing Industries (MoFPI) continues to play a crucial role in developing preservation infrastructure to support this growth.
As the industry adapts to geopolitical challenges and rising consumer demand for plant-based and organic products, upgraded cold storage facilities and strategically located distribution hubs will be essential for enhancing efficiency and resilience in both pharmaceutical and food logistics. I see that more private capital is slated to be deployed in the next 4-5 years than all years since independence. A lot of global interest in the Indian food industry will drive this demand.
Leaders at Davos highlighted key priorities for India's next growth phase, focusing on advancing services and service-driven manufacturing while harnessing the demographic dividend through investments in human capital.
“We are in one of the most complex and consequential moments in generations, when fast-changing geopolitical, geoeconomic and technological currents are shaping our societies and our industries and will do so for years to come,” said Børge Brende, President and CEO, World Economic Forum. “In this era of uncertainty, we must find ways of working together because force cannot replace discourse and conflict cannot replace compromise.”
BI-GLOBALIZATION, REGLOBALIZATION?
By some estimates, geopolitical bloc-based trade could cost the global economy up to $6.75 trillion. “There is no contradiction between economic fragmentation and the continuation of the increase in global trade – it’s just that you don’t trade with the same people,” said Gilles Moëc, AXA Group Chief Economist. “We have seen a lot of concentration of supply chains or manufacturing in certain sectors. We need to build resilience by something we call re-globalization,” said WTO Director General Ngozi Okonjo-Iweala. “The world needs to decentralize certain supply chains so that we can build resilience.” A new report by the Forum, in collaboration with IMD Business School
and Boston Consulting Group, suggests business sharpen their geopolitical radar. That means building capacity to track, assess and respond to geopolitical developments that might affect supply chains or the organization before they become full-blown crises.
The 55th World Economic Forum (WEF) Annual Meeting, held from January 2024, 2025, in Davos-Klosters, Switzerland, highlighted India's impressive progress. From advancements in AI and frontier technologies to expanding renewable energy and strengthening global partnerships, India’s strides align seamlessly with WEF 2025’s theme: "Collaboration for the Intelligent Age."
At Davos 2025, conversations on India's economic future highlighted its resilience amid global uncertainties and geopolitical tensions. Despite a temporary slowdown, the International Monetary Fund (IMF) maintains its 6.5% growth forecast for the year, with Deputy Managing Director Gita Gopinath stressing that India could accelerate progress by lowering tariffs and enhancing integration with global supply chains.
As WEF 2025 emphasizes five key
workstreams—Reimagining Growth, Investing in People, Rebuilding Trust, Industries in the Intelligent Age, and Safeguarding the Planet—India stands at the forefront of driving impactful solutions. With a strong focus on international collaboration and sustainable innovation, India's presence at this prestigious forum reaffirmed its commitment to shaping a more connected and sustainable future.
The Indian delegation presented a unified and compelling vision of the country’s growth as One Nation, One Voice, led by a high-level delegation comprising key ministers and representatives from the Centre and states. Regardless of political affiliations, Union ministers, Chief Ministers, and other state ministers came together at Davos to champion India's growth story. Despite their usual competition for investments and resources, they set aside rivalries and spoke with a united voice. "We may be different political parties, we are all one when we came to Davos. India first, our people first. That is our slogan,” Andhra Pradesh CM Chandrababu Naidu stressed.
Taking the thread forward, Maharashtra Chief Minister Devendra Fadnavis also echoed the 'Team India'
sentiment. "At Davos, we could see one India, and I think it's a great example of cooperative and competitive federalism whereby we are talking in one voice, but at the same time we are competing for business, we are competing for showcasing the abilities of our states, and I think that is what is contemplated in the cooperative and competitive federalism," he voiced at the press conference.
Addressing global leaders and industry captains, Shri Ashwini Vaishnaw, Union Minister of Information & Broadcasting, Railways, Electronics & IT, presented India's economic strategy as being built on “Four pillars: Public Investment In Social, Physical And Digital Infrastructure; Focus On Technology, Manufacturing And Innovation; Inclusive Growth; And Simplification.”
He highlighted the balanced approach to economic growth taken by India with both manufacturing and services driving nation’s development. “It cannot be manufacturing or services; it has to be manufacturing and services as both these sectors are integral to India’s economic trajectory.”
He emphasized India’s transformation from focusing solely on import substitution to adopting a “Make in India, Make for the World” approach. With 99% of mobile phones used domestically now manufactured in India, the growth strategy has shifted towards export-led growth across sectors such as pharmaceuticals, chemicals, and garments. With the prominent role of artificial intelligence (AI) in the services sector in shaping India’s future, driving
innovation and creating opportunities, the Union Minister also highlighted the need for laying special emphasis on training the talent pool in AI.
Emphasizing why global companies are increasingly gravitating towards India, the Union Minister highlighted the nation’s ‘unique advantage’ rooted in trust, abundant talent, and exceptional design capabilities. He credited India’s leadership under the Prime Minister of India for creating an environment of global trust, attracting companies to shift not just supply chains but also value chains to India. “With nearly 2,000 Global Capability Centers (GCCs) working on advanced designs, India is poised to be a major player in global manufacturing,” he stated.
The budget presents a bold strategy for industrial and logistics expansion, emphasizing infrastructure development.
BUILT on the vision of ‘Viksit Bharat’ and ‘Sabka Vikas’, the Union Budget 2025-2026 promises to continue Government’s efforts to accelerate growth, secure inclusive development, invigorate private sector investments, uplift household sentiments, and enhance spending power of India’s rising middle class. The Budget aims to initiate transformative reforms in Taxation, Power Sector, Urban Development, Mining, Financial Sector, and Regulatory Reforms to augment India’s growth potential and global competitiveness. It highlights that Agriculture, MSME, Investment, and Exports are engines in the journey to Viksit Bharat using reforms as fuel, guided by the spirit of inclusivity.
For long-term financing for the maritime industry, the Union Finance Minister Smt. Nirmala Sitharaman has proposed to set up a Maritime Development Fund with a corpus of Rs 25,000 crore. This corpus will be for distributed support and promoting competition in the maritime industry. The fund will have up to 49%
contribution by the Government, and the balance will be mobilized from ports and private sector.
The Finance Minister stated that the Shipbuilding Financial Assistance Policy will be revamped to address cost disadvantages, which will also include Credit Notes for shipbreaking in Indian yards to promote the circular economy. Further, the large ships above a specified size are also proposed to be included in the infrastructure harmonized master list (HML). The Union Budget also proposes to facilitate ‘Shipbuilding Clusters’ in order to increase the range, categories and capacity of ships. This will include additional infrastructure facilities, skilling and technology to develop the entire ecosystem. Acknowledging that the shipbuilding has a long gestation period, the Finance Minister proposed to continue the exemption of Basic Customs Duty on raw materials, components, consumables or parts for the manufacture of ships for another ten years. She further proposed the same dispensation for ship breaking to make it more competitive.
The government will facilitate upgradation of infrastructure and warehousing for air cargo including high value perishable horticulture produce. "Cargo screening and customs protocols will be streamlined and made user friendly," she added.
The Union Budget 2025-26 envisions to initiate transformative reforms in domestic manufacturing and integrating
India’s economy with global supply chains. A digital public infrastructure, ‘BharatTradeNet’ (BTN) for international trade has been proposed to be set-up as a unified platform for trade documentation and financing solutions. In the budget speech Smt. Sitharaman stated that, “BTN will complement the Unified Logistics Interface Platform and will be aligned with international practices”.
Support will be provided to develop domestic manufacturing capacities for integrating Indian economy with global supply chains. In this direction, the sectors will be identified based on an objective criterion. It is also proposed that facilitation groups with participation of senior officers and industry representatives be formed for select products and supply chains. Smt. Nirmala Sitharaman highlighted that the youth of India have both high skills and talent which are required for capitalizing on the opportunities related to Industry 4.0. “Our Government will support the domestic electronic equipment industry to leverage this opportunity for the benefit of the youth”, she added.
According to Neetu Vinayek, Partner and Tax leader- Infra, EY India, In her 8th budget, the Honourable Finance Minister presents a strategic vision to propel India's economic growth, with a strong focus on infrastructure as a catalyst for the Viksit Bharat @2047. Despite global economic headwinds, India maintains its position as the fastest-growing major economy, with a GDP growth forecast
between 6.3% and 6.8%, in line with IMF projections.”
“With the budgetary allocation of Rs. 11.21 lakh crore towards capital expenditure the government continues its promise of accelerated growth and inclusive development. Requirement of each infrastructure related ministry coming up with a three-year pipeline of projects to be implemented in PPP mode, an outlay of Rs. 1.5 lakh crore with interest free loan for 50 years to states for capex and incentives for reforms are initiatives which will invigorate private sector investments.”
“Allocation of Rs. 25,000 crore to the Maritime Development Fund with equal participation from private sector will facilitate long-term financing to the maritime sector. Revamping the shipbuilding financial assistance policy and inclusion of large ships in the harmonized list of infrastructure are positive measures towards ship building ecosystem. Tax measures such as granting benefit of tonnage tax schemes to inland vessels, extension of time limit to commence business in IFSC for ship and aircraft leasing will give further boost to sector. Additionally, the much expected extension of time limit up to 2030 for making investments by sovereign and pension funds will attract non-public capital investment in infrastructure projects. Setting up of an urban challenge fund of Rs. 1 lakh crore for economic and transit planning and redevelopment of peri-urban areas will help transform the cities as growth hubs,” Neetu Vinayek added.
Email: tech@celerityin.com | Mobile:
Website: www.supplychaintribe.com www.supplychaintribe.events