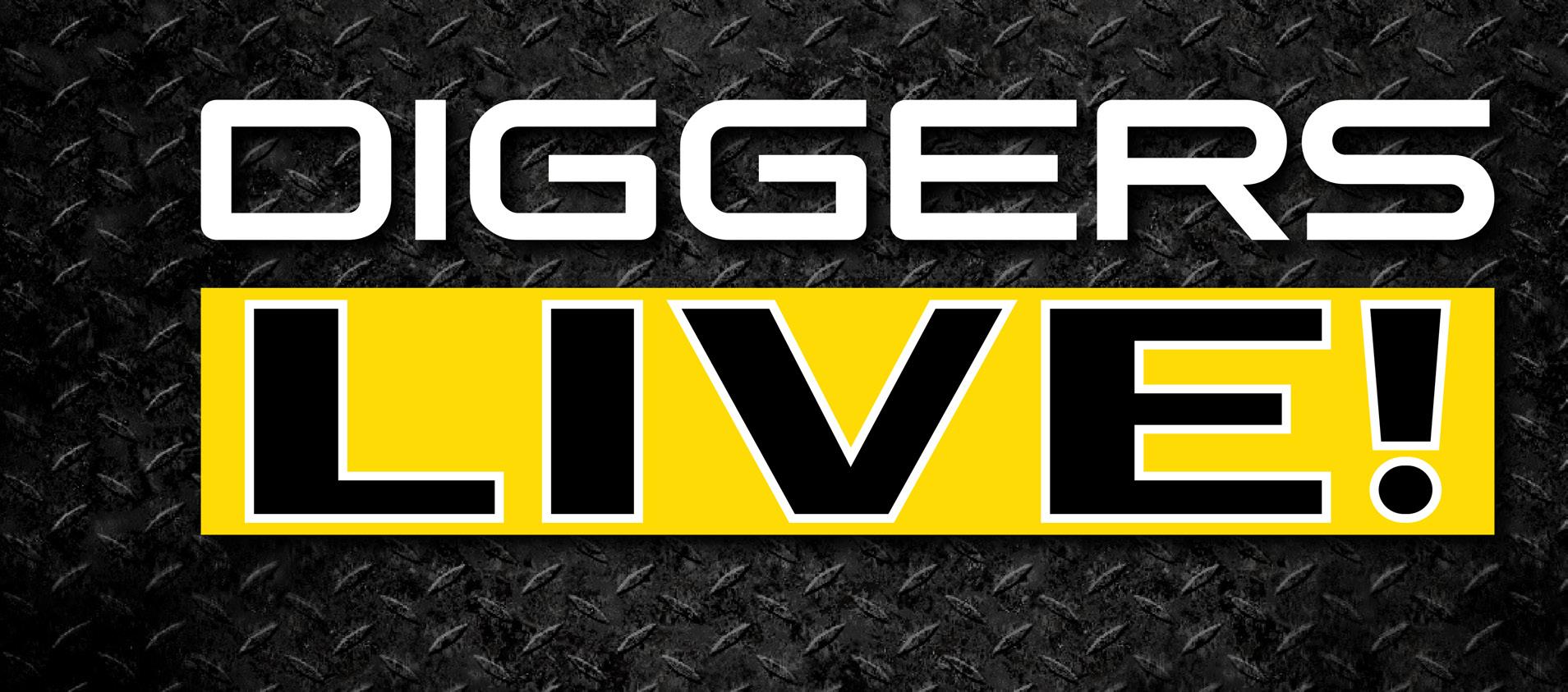






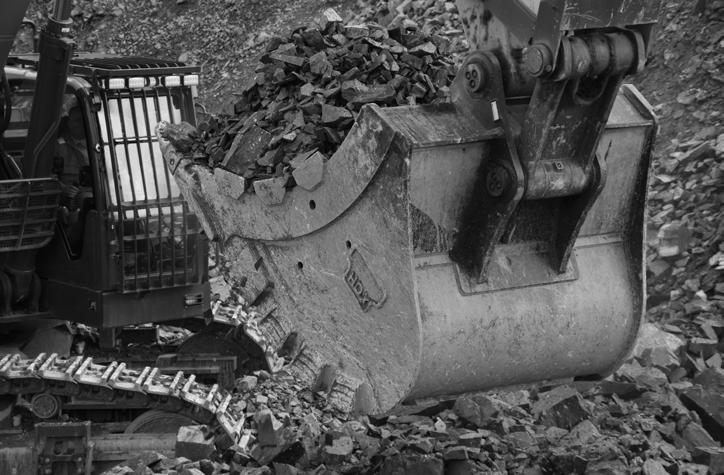
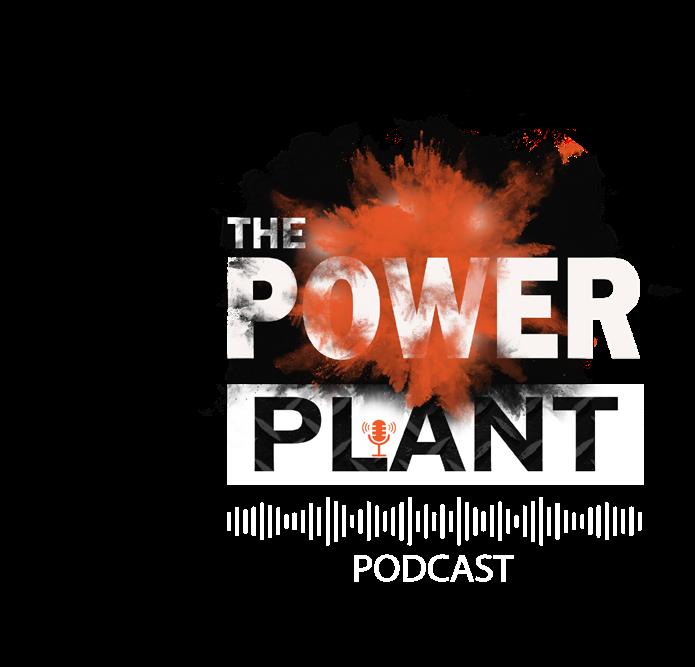
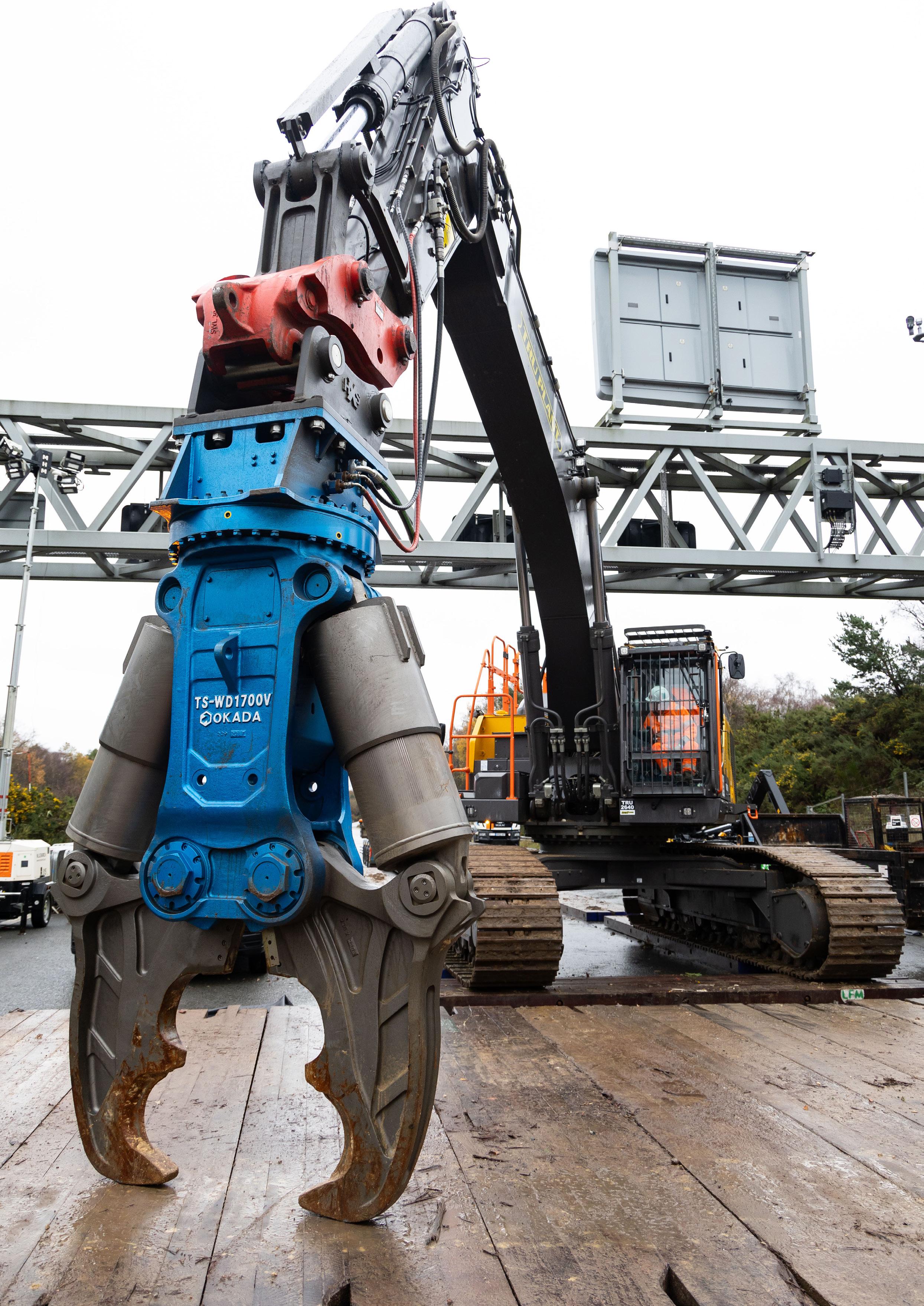

FROM 1.8 TO 95 TONNES THE ALL NEW F-SERIES BREAKS THE MOULD.
As we kick off September, a little later than usual, we’re still buzzing from the success of this year’s British Demolition Awards. Many of you joined us in London, and I hope you’ll forgive the slight delay.
It’s hard to believe how fast time flies. Four years ago, we were just about to launch Diggers LIVE!, a global construction industry magazine that now reaches readers every other month—those who buy, supply, and use construction equipment.
Before the launch, we were already deeply entrenched in the industry, but the team and I wanted more. We craved the freedom to innovate in real time as trends emerged, to promote the industry and its brands in a more meaningful way, and to offer something just a bit different, a bit better.
As many of you know, I rarely stay put for long. I’d hate to calculate the air, land, and sea miles I’ve racked up over the past four years. But being out there, injecting a bit of personality into the industry, reporting on new innovations and technology, and making a few friends along the way, doesn’t feel much like work.
Now, as we enter our fifth year producing Diggers LIVE!, we do so with a few more friends, a solid reputation for being where the action is, and a proven track record over 25 issues of promoting this incredible industry.
As I look ahead to the first event of 2025 in Vegas, I want you to know you’re in good hands. Here’s to the next four years of promoting your success!
In this milestone 25th issue, we’re thrilled to feature Owen Buttle, National Sales Manager at Merlo, in our regular Equipment Engagement interview. He shares insights into Merlo’s history and the company’s vision for the future (and yes, one day I’ll stop spelling it like the wine!).
We also have a Business Insider interview with Scott Freeman, Business Development Manager at EPG Global, who discusses how he builds relationships across agriculture, construction, and industrial sectors.
Along with our popular attachment feature, we’ve packed in a hiring spotlight and a wealth of industry updates.
With just one more issue left in 2024, set to drop in early November, I can’t help but ask again: Where does the time go?
Ben Chambers, Publisher
PUBLISHER
Ben Chambers ben@chambers.media
EDITOR
Toby Wilsdon toby@chambers.media DESIGNERS
Nicki Chambers nic@chambers.media Joe Bers joe@chambers.media
GENERAL ENQUIRIES info@chambers.media 01903 952 640
Ben Chambers ben@chambers.media 01903 952 648
PRODUCED & PUBLISHED BY Demolition Hub Ltd
Suite 5 & 6 Chapel House 1-6 Chapel Road, Worthing West Sussex BN11 1EX ben@chambers.media 01903 952 640
Diggers LIVE! is published six times a year by Demolition Hub Ltd
Articles and information contained in this publication are the copyright of Demolition Hub Ltd and may not be reproduced in any form without the written permission of the publishers.
The publishers cannot accept responsibility for loss of, or damage to, uncommissioned photographs or manuscripts.
6
EQUIPMENT ENGAGEMENT
With Owen Buttle, National Sales Manager of Merlo
With Scott Freeman, Business Development Manager at EPG Global, part of Shepherd Global Ltd
16 EVENTS
RESOURCE & WASTE MANAGEMENT EXPO (RWM)
UK’s largest resource and recycling expo ready to go
20
ALTERNATIVE POWER FEATURE
• A New Era in sustainable power: HVO and the path to a low-carbon futurE
• Bobcat RogueX2 autonomous loader
• CEA
• Energy expert busts common renewable diesel myths
• JCB hydrogen generator debut paves way for zero carbon future
• DEVELON
• SANY
32
Diggers LIVE! and Kicking – Ben and the team out promoting the industry between issues
36
• BMC Buckets
• BPH Attachments
• Hill Engineering
• Miller UK
• Malaguti Plury range supplied by Robustrack
• Ulrich Attachments
• CAM attachments by TVH
• Speakers and topics confirmed for Construction Planthire Association conference
• Mount Machinery
• Mutley Plant Service
• Tru7 Group
• Warwick Ward (machinery) Ltd 36
Tru7 group invests in huge JCB X series fleet
Prolec opens state-of-the-art technology hub in Southampton
ECL strengthens fleet with £10m investment in Komatsu plant
Gearing up for Vertikal Days 2024
Ignoring this crucial safety tool could put your entire operation at risk
CASE Construction Equipment launches D-Series graders
JLG Industries acquires AUSA
Hitachi and Xwatch – a winning formula for safety
Waste not, want not: CDE encourages quarries to reappraise waste by-products
Construction software platform partners with ethical consultancy to deliver lived experience modern slavery assessments
James King (Plant) adds to HD Hyundai excavator fleet
Paul Lyons – focusing on market insights as independent consultant
Interviewee:
Owen Buttle
Role:
National Sales Manager
Company: Merlo
QTell us about the history and culture of Merlo and the development of Merlo UK
The company was founded by Amilcare Merlo in 1964. Merlo quickly established itself as a pioneer in the design and manufacture of telescopic handlers. The company’s design principles revolve around user-centric innovation, safety and sustainability.
Over the years, Merlo has significantly expanded its product range. While telescopic handlers remain at the core of its offerings, the company now produces a variety of specialised machines, including roto telehandlers with 360° rotation, heavyduty tool carrier tractors and even tracked carriers.
Merlo UK was established 31 years ago to strengthen the company’s presence in one of its key European markets. The UK branch has played a crucial role in expanding Merlo’s market share, providing direct access to British customers and ensuring that they receive the high level of service and support that Merlo is known for.
QTell us about Merlo’s key innovations and awards
Merlo has been at the forefront of technological advancement in the construction and agricultural machinery sectors. Some of the most notable innovations include:
• Hydrostatic transmission
Merlo was a pioneer in integrating hydrostatic transmission into its machinery, offering operators greater control, precision and efficiency. This technology has become a hallmark of Merlo’s telehandlers and other machines, setting an industry standard.
• Rotating telehandlers (Roto Series)
The Roto telehandlers revolutionised the market with their 360° rotating capabilities. This innovation allows for greater flexibility and versatility in confined spaces, making the Roto series a game-changer for construction and industrial applications.
• Merlo ASCS (Adaptive Stability Control System)
The Merlo ASCS is an advanced safety feature that plays a critical
role in ensuring the stability and safe operation of Merlo telehandlers. This system is designed to monitor and manage the machine’s stability dynamically, adapting to changing conditions in real time to prevent accidents and enhance operator confidence. The ASCS continuously monitors various parameters of the telehandler, including load weight, boom extension, boom angle and the machine’s overall stability. By processing this data in real time, the system can assess the current stability of the telehandler.
• Hybrid and electric technology
In response to growing environmental concerns, Merlo has invested in hybrid and electricpowered machinery, reducing carbon emissions and fuel consumption. This move towards sustainability has positioned Merlo as a forwardthinking leader in eco-friendly machinery. In 2021 the eWorker EW25.5 was launched, a fully electric telehandler built from the ground up specifically to run from battery
power. We have since introduced the electric tracked dumper, Cingo, adding to the Generation Zero range of electric machinery.
We have been recognised with numerous awards in recent years, which is testament to Merlo’s innovations and commitment to excellence. These include EIMA Innovation Award, Machine of the Year Awards, Innovation in Safety Award, Sustainable Machinery Award.
QTell us about your team and the working culture
At Merlo our staff are the backbone of our success. We believe that our people are our greatest asset and we have an environment that encourages collaboration, creativity and continuous learning.
The sales and aftersales teams place a strong emphasis on being present and actively engaged with our customers. Our customer focus mentality is integral to our approach, ensuring that we deliver not just high-quality machinery, but also exceptional service and support throughout the customer journey. Our sales teams are not just sales
representatives – they are experts in our products and the industries we serve. They work closely with our dealer partners and customers to provide insightful advice, demonstrate machine capabilities and ensure that each customer receives the attention and assistance they need.
QWhat can a customer expect when they buy from Merlo?
With a comprehensive network of local dealerships, Merlo ensures that customers have easy access to sales, service and support. This localised presence allows for prompt assistance and a deep understanding of regional needs. Building long term relationships with our customers is a core value at Merlo. We aim to be more than just a supplier; we strive to be a trusted partner in our customers’ success. This commitment to relationship building is reflected in our ongoing support and dedication to meeting their evolving needs.
QTell us about any trainee schemes Merlo has
The Merlo Academy represents a significant investment in our commitment to developing talent and providing career opportunities within our production line. Launched at the group level, the Academy is designed to cultivate the next generation of skilled professionals by offering comprehensive training and career development programmes. The Academy also aims to create clear career pathways within Merlo’s production line. Through structured training programmes, participants can progress from entry level positions to more advanced roles, supporting their long term career growth and development.
Merlo UK, on the other hand, works closely with a variety of industry organisations and trade associations to promote career opportunities in the machinery sector. These partnerships help bridge the gap between education and industry, ensuring that students and job seekers are well-informed about career paths and opportunities.
Q
How about ongoing training for existing staff?
At Merlo UK, we prioritise the continuous development of our staff by investing in comprehensive training programmes. Our commitment to employee growth is reflected in the resources and time
we dedicate to enhancing skills and ensuring that our team remains at the forefront of industry standards. We also focus on developing soft skills such as communication, leadership and problemsolving. These skills are crucial for effective teamwork, customer interactions and overall professional development. Training programmes empower staff by enhancing their skills and confidence. When employees see that the company is willing to invest in their growth, it gives a sense of appreciation and motivates them to excel in their roles.
Q How do you see the outlook for the plant industry and Merlo in the medium term?
The plant industry is expected to continue evolving with rapid technological advancements. Innovations such as electric and hybrid machinery, automation and advanced telematics will drive efficiency and sustainability. These technologies are likely to become more integrated into standard operations, offering new opportunities for growth and development. Merlo will continue to lead in innovation and safety by integrating
advanced technologies into our product range. We are committed to developing and offering machinery that meets the evolving demands for efficiency, sustainability and performance.
QAnd how do you see the medium term future for Merlo’s product development?
Innovation is at the heart of Merlo’s strategy. We are constantly exploring new technologies and advancements to enhance our product range. Our commitment to being at the forefront of technological development ensures that we offer cutting-edge solutions that improve performance, efficiency and safety. We are excited to be introducing Merlo Mobility to the UK market in the next few months, our advanced telematics solution designed to revolutionise how users interact with their equipment. This technology provides real time data and insights into machine performance, usage and maintenance needs as well as tracking and geofencing.
QWhat are the biggest developments you have seen in the industry and what do you envisage will be the future game changers?
When I first entered the construction industry 22 years ago, the focus was predominantly on traditional machinery powered by diesel engines. The technology was centred around maximising power
and efficiency in a more conventional framework, with little to no emphasis on alternative energy sources.
At that time, the idea of selling electric-powered telehandlers was not on the horizon. Embracing electric technology has required a shift in mindset and approach. It’s been fascinating to witness the growing acceptance and demand for electric machinery as companies and industries prioritise sustainability and seek to reduce their carbon footprints. Looking forward,
it’s clear that the industry will continue to evolve with further technological advancements and a stronger emphasis on sustainability. The rise of electric telehandlers is just one example of how the industry is adapting to new challenges and opportunities.
QWhat is Merlo doing with regard to sustainability?
We have made significant strides towards sustainability by investing in a significant solar panel array at our UK depot. This on-site renewable energy solution helps us generate clean electricity, reducing our reliance on non-renewable energy and lowering our carbon footprint. The solar panels contribute to powering our facilities and twelve electric car chargers that we had installed.
We have strategically replaced many of our company vehicles with petrol hybrid models. Merlo UK has also started a significant shift from traditional road haulage to electric rail transport for shipping our machines from Italy to the UK. Rail transport offers a more efficient eco-friendly alternative, significantly reducing the carbon emissions associated with end to end road transportation.
At our Italian factory, we have installed solar panels wherever feasible and have partnered with a fully renewable energy provider. This partnership ensures that the remaining energy needs of our factory are met through 100% renewable sources.
QTell us about one of your key products
The Roto series is one of Merlo’s flagship product lines, featuring telehandlers with a rotating upper structure. This allows for 360° operation, making them incredibly versatile and efficient for tasks that require multiple positioning without moving the base of the machine.
Q Outline the key specifications of the product
The Roto 50.35 boasts a maximum lifting capacity of 5,000 kg, making it suitable for the most demanding lifting tasks on construction sites and industrial projects; a maximum lifting height of 34.7 metres; and a forward reach of up to 30 metres, providing substantial vertical and horizontal reach for a wide range of applications. The 360° rotating turret allows for uninterrupted rotation, enabling the operator to position the load anywhere around the machine without needing to reposition the base. This feature significantly improves efficiency, especially in confined or restricted spaces.
The 50.35 is equipped with four independent stabilisers, which can be adjusted to ensure maximum stability on uneven or sloped terrain. The system automatically adjusts the stabilisers and levels the machine, ensuring a stable working platform even in challenging conditions. Safety is paramount and the Roto 50.35 is equipped with Merlo’s ASCS, which continuously monitors load conditions and machine stability. The Roto 50.35 includes an Eco Mode that optimises engine performance for fuel efficiency. In this mode, the machine reduces the RPM when full power is not required, significantly cutting fuel use.
Q How is this product critical for potential users?
The Merlo Roto 50.35 features a dual hydraulic load-sensing flow sharing pump, which is a critical component for enhancing fuel efficiency. The dual hydraulic pump automatically adjusts the hydraulic flow and pressure based on the specific demands of the task at hand. This means that the machine only uses the necessary amount of hydraulic power, preventing wasteful energy consumption and reducing
the load on the engine. By efficiently managing hydraulic power, the machine can perform a wide range of tasks at lower engine RPMs. The load-sensing system provides smoother and more responsive control, which not only enhances operator comfort but also productivity of the job in hand. The fuel-saving features and advanced technologies in the Merlo Roto 50.35 significantly reduce both the total cost of ownership and operating costs.
QCan you quantify any of these benefits?
Customer feedback indicates a noticeable difference in both performance and fuel savings with the Merlo Roto 50.35. Users appreciate the improvements in efficiency and operational effectiveness that the
machine offers. In the most demanding applications, calculations show that the typical RPM reduces by 25%.
QTell us about the development of this particular product
The Roto market in the UK has been steadily growing, driven by the increasing awareness and versatility of machines like the Merlo Roto 50.35. As these become more recognised for their capabilities, they have evolved to be used in a broader range of applications. With each new attachment we develop, the Roto 50.35 becomes more versatile, opening up opportunities for it to be used in applications that were previously not possible. This adaptability is a key factor in the product’s ongoing development and success.
QHow long have you been in the plant industry and how did you start out?
I’ve been involved in the construction and plant industry for 22 years and my journey began thanks to an opportunity given to me by a family friend. From that point on I never looked back. Over the years, I’ve had the privilege of working for two global manufacturers, gaining valuable experience in parts, marketing and sales.
QWhat attracted you to the industry?
I’ve always had a passion for machinery and I take pride in being knowledgeable about the products I work with. This enthusiasm has helped me build
strong relationships with colleagues, dealers and customers alike. I particularly enjoy the face-to-face interactions as they allow me to connect on a more personal level.
QWhat do you find most rewarding in work?
I’m passionate about working closely with our sales staff and dealers, supporting them in achieving their goals. Being involved in the sales process keeps me connected to the core of the business and allows me to continue doing what I love. Even though I’ve progressed into a management role, I still enjoy the sales element of the job – there’s nothing quite like getting a deal over the line.
What would you be in an alternative life?
I could see myself as a pilot. The thrill of being in control of a powerful machine and the precision and attention to detail required in aviation align with my passion for machinery. The freedom of flying would be incredibly appealing, it would be an exciting way to combine my love for engineering with a sense of adventure.
Describe yourself in three adjectives Driven, approachable and knowledgeable
What do you do for fun?
For my sins, I’m a Southampton FC fan. I really enjoy going to watch them with my daughter when she’s not busy playing football herself. Otherwise, I spend my weekends enjoying quality time with the family, which is always a highlight for me.
Who do you most admire?
Lewis Hamilton. His relentless pursuit of excellence on and off the track is truly inspiring. Hamilton’s ability to consistently perform at the highest level, his focus and his resilience in the face of challenges set him apart as one of the greatest athletes of all time. Beyond his racing achievements,
QWhat kind of projects would you like to be involved with before retirement?
Before I retire, I’d love to be involved in projects that push the boundaries of innovation in the construction and plant industry. Being part of initiatives that introduce groundbreaking technologies or significantly improve sustainability would be incredibly fulfilling. I also aim to mentor and develop the next generation of industry leaders, ensuring that the knowledge and experience I’ve gained over the years are passed on. Ultimately, I want to leave a lasting impact on the industry and see the teams I’ve worked with achieve success.
I also respect his commitment to using his platform to advocate for diversity, equality and positive change, which adds another layer to his legacy.
When and where are you happiest?
Spending quality time with my family, especially during moments that involve simple joys like a weekend outing or a relaxed evening at home. These times create memories and reinforce the strong connections we share. Additionally, I find immense satisfaction in achieving milestones at work or successfully tackling challenges, knowing that my efforts contribute to both personal fulfilment and the wellbeing of those around me.
What’s the most expensive non-essential you’ve ever bought?
A robot lawnmower. It’s a luxury that adds convenience and efficiency to maintaining the lawn, allowing me to enjoy more time with the family.
What’s your bucket list activity?
To explore New Zealand. I’d love to experience the breathtaking landscapes and volcanic terrains of Tongariro National Park.
What’s your favourite cuisine?
Italian. I’m not just saying this because I work for an Italian company, I love the rich flavours of dishes like pasta, pizza and risotto. The emphasis on fresh, high-quality ingredients and the variety of flavours never fails.
Interviewee: Scott Freeman
Role: Business Development Manager at EPG Global, part of Shepherd Global Ltd
Sector: Extended warranty
Employees: 75
Current brands: Machine Guard
Related companies: A trading name of Shepherd Compello
Geographic reach: Global
Established: 2003
Prior roles in career: Sales and Marketing Administrator, Parts Development Manager at Case International, Business Manager UK and Ireland CNH UK, Business Director UK and Ireland CNH UK
QHow do you fit into EPG Global? I am responsible for business development within the company, my prime role being to develop business with both current and new clients across the agriculture and construction industries and industrial sectors globally.
QTell us about your career progression. Was it a natural progression based on your skills, interests and experience or involving some unexpected tangents?
I started my career as management trainee back in 1990 in Doncaster with Case International, as it was then, better known today as CNH Industrial. I enjoyed a full 26 years within the CNH organisation and worked in both the agriculture and construction sectors during my time there. I touched most areas of the commercial business on machines and aftersales, always interfacing with the dealerships and also end users which was one of the most enjoyable parts of all the roles I have done historically.
An opportunity came along to work with EPG, a great forwardthinking, family-owned business, which would enable me to reach out to all manufacturers and dealers within the sector. I knew the company’s products and services very well and respected that.
Their appetite for growth and development was a key factor in my decision, and if I could be part of that growth and development, then that could only be a good thing, so I decided to take on the challenge.
I am comfortable in the environment of manufacturers and their distributors, I understand the processes involved and more importantly the necessary tools to assist in the selling of machinery and the need to provide a good service to their customers for client retention.
Warranty packages are important for customers and of course one size does not fit all so we need to be flexible and responsive and know our business.
QHow has what you do developed during your career and how has EPG developed in the time you have been there?
The most important thing is to be responsive to your clients as usually they require answers quickly.
Machinery packages have developed
continuously over the past few years, cost of ownership being a key driver. There is constant development in technology in all types of machinery and this of course comes at a cost. Extended warranty is one key product to help avoid any unnecessary expense in relation to mechanical defects. Customers are asking for longer warranty terms when they are investing in machinery and that’s where we can help both manufacturers and dealers.
EPG’s development over the years has been consistent. Our global client base requires us to provide multilingual support, and we have a team of talented, responsive people on board to carry out this service for us globally.
I always remember from many years ago the phrase, “The sales team sell the first machine but the aftersales and service levels will sell the next one.” This remains true in most cases.
Additionally, there has been a growing requirement to put extended warranties on used machinery, allowing the dealers to replicate similar packages they would sell on new machines. This model is great for customers investing in used machinery
Q
and gives them peace of mind. EPG has developed products for used equipment and this part of the business is growing consistently on both agriculture and construction products.
We offer our clients up to two years of cover on units under seven years old or 7,000 hours and all ranges of construction machinery are applicable.
QWhat is it about your role that attracts you? What are the skills required for your job?
The industry is great, full of great people – not many people leave the industry once they’re in it. I enjoy the cycles of the
Tell us about EPG Global, its history and development
EPG Global has been providing extended warranties, administration services and other insurance-backed products to clients including manufacturers, dealers, auction houses and leasing companies of new and used machinery on a worldwide basis for more than 30 years. EPG Global is uniquely positioned to support clients in the agricultural, construction, commercial vehicle, grounds care and marine industries as its team is steeped in experience of working for world-leading companies in these sectors.
Q
Tell us about its growth path up until now – and perhaps the future
I’ll start with our CEO John Shepherd. John has forged a long and successful career over 40 years growing businesses and developing innovative insurance and warranty products across the world. He is a well-known and respected figure within the Lloyd’s marketplace. John established EPG Insurance Services, as it was then known, in 2003.
Our Managing Director Holly Shepherd, who is John’s daughter, joined the business in 2006 and has spearheaded the international expansion of EPG Global to become the preeminent provider of machinery extended warranties. Holly is also the Managing Director of Lloyd’s broker and coverholder Shepherd Compello and sits on BIBA’s International and Wholesale Brokers’ Advisory Board. In recognition of her contribution to the insurance and warranty industries, Holly
business, the technological developments on machinery and I do like to visit clients in their own environment.
The main skills for me are to understand what the customer wants, listen to their needs and deliver a solution. Relationships are a key driver for me, and this really is the best part of the job.
QHow do you think your colleagues see you (or you would like them to)?
I would hope they would say reliable and always available to help when needed. These things are important in both one’s professional and personal life.
has been awarded International Businesswoman of the Year at the International Women’s Day Awards, Young Broker of the Year award at both the Insurance Insider Honours and the London Market Awards, and is listed as both one of Insurance UK’s Elite Women and Business Insurance’s Women to Watch.
EPG and its related companies continue to expand geographically and widen its expertise consistently to provide solutions to many parts of the industry including, transportation, property, cyber and other speciality classes of insurance-related products. Future ambitions remain to grow and provide a solid foundation for its employees and customers.
QExplain what EPG Global does, in particular for our construction plant user readers in Diggers LIVE!
EPG Global has built its reputation as a valued partner to agricultural and construction machinery manufacturers and dealerships through a combination of market-leading equipment coverage, superior service levels and a highly skilled team. Our team brings a wealth of technical and commercial knowledge gained from decades of experience gained between them of working in the agricultural and construction sectors.
Our client base includes many of the world’s top 10 largest agricultural and construction machinery manufacturers, with whom we have built long-standing relationships. We are particularly proud of these enduring partnerships where we have provided extended warranty programmes on behalf of agricultural and construction clients over many years and on a multi-jurisdictional basis.
Our extended warranty programme covers the full spectrum of construction machinery including crushers/screeners, wheel loaders, telehandlers, excavators, dozers, loaders, ADT attachments and many others.
We offer three levels of cover to protect the major powertrain, hydraulic and electronic components, which can be adapted to accommodate any specific coverage requirements for machinery and equipment. We have more than 60 detailed that set out the detailed coverage available for every type of machine or equipment in our warranty programmes.
With some manufacturers’ factory warranties on new machinery commonly expiring at 12 months, and at just three months for used machinery, customers run the risk of significant financial loss over the lifetime of their machine or equipment in the event of outage or failure.
Available from dealerships worldwide, the Machine Guard extended warranty offers bespoke coverage options for the core drive train and hydraulic components, with additional protection available for the chassis/main frame and electrical elements, amongst many other component coverages.
Our extended warranty is transferable to subsequent owners, making it the ideal solution to protect assets over the long term and, at the same time, add resale value to your machinery.
QTell us about the EPG Global service
Our people have many years of experience in the construction industry, either with dealers or manufacturers, so knowing the product is our speciality. What’s refreshing for me is when a manufacturer says it’s nice to talk to a company that understands the business, and the different options required by country and by product type.
Our dedicated support and administration team is multilingual and has a high energy for delivering customer
satisfaction, and it’s important to do this quickly as machinerydown situations are usually time critical.
So, from a sales, service and administration support point of view, we deliver a great product that is good value for money.
QWhat are the company’s USPs in relationship to the broader insurance market?
Product expertise – all our engineers are from the industry and talk the same language, and our administration platform is effective and simple to use for our dealer clients.
With more than 60 coverage sheets, we really do know the machinery we are covering. With other providers this may not be so clear in terms of component coverage. The clearer the better for all parties.
Dealerships rely on servicing and parts to generate the lion’s share of their income. Our warranty programme positively impacts their absorption rate, helping them exceed the common benchmark figure of 85%.
Firstly, we reimburse dealerships at the full RRP on all genuine manufacturer parts bought under our warranty programme.
Secondly, we reimburse labour at their full retail charge out rate, helping to offset lower rates on internal work and discounts.
Thirdly, the dealership can tie in servicing and repair work for the lifetime of the warranty. The longer the warranty, the more they benefit.
Our extended warranties are available at a fraction of the cost of common component breakdown repairs, with an extended warranty typically available at well under €1/£1 on a cost per operating hour basis.
There are no deductibles with our warranties, which are so often a cause of irritation and disappointment for customers with other providers. But with us it’s all covered from the first €1/£1.
QHow can these USPs benefit customers? How do they improve the bottom line?
1. Productivity
• Fixed cost of ownership: the customer can rely on the guarantee that in case of breakdown their machine will be quickly repaired without any additional cost,
• Uptime: the smooth claims process maximises the uptime of the machine, reducing loss of productivity,
• No excess/deductible: There is no excess or deductibles with our warranties. This is so often a cause of irritation and disappointment for customers with other providers.
2. Safety and security
• The machine will be maintained according to the manufacturer’s requirements,
• The repairs will be done using original spare parts.
3. Improved residual value of the machine
• In the event of the sale of the machine, the protection will follow the machine,
• The new owner will have the guarantee that the machine has been fully maintained and repaired with original spare parts.
QHow do the needs of end users and OEMs for warranties differ worldwide? What is relevant in different markets?
Different markets can be driven by many things – climate, application and length of ownership. What is for sure is that the demand for extended warranty continues to increase across all markets and we can see this generally in what the manufacturers are offering to their clients. Technological developments and high value components will continue and clients will look for safety blankets to protect them from unforeseen expenditure all around the world.
QTell us about your working culture. How do you source new talent and keep skills up to date?
At EPG, we very much work as a family, collaborating for our partners and with our teams within the organisation. We are always on the lookout for individuals
who want to be part of an organisation that our staff see as a long-term home that offers support and harnesses talent and progression. We attend many trade shows and events with industry leaders all over the world, focusing on new technologies and machineries to ensure our expertise meets the growing needs of our partners.
Our four core values are:
1. Partnership
• Building long-term relationships with our customers and business partners,
• Working as a team to ensure all stakeholders achieve their objectives,
• Collaborative behaviour, attitude and environment.
2. Innovation
• Challenging the norm and proposing new ideas,
• Open-minded and forwardthinking,
• Embracing and welcoming change.
3. Passion
• Drive to perform your role to the best of your abilities,
• Having the energy and enthusiasm to get things done,
• Demonstrable commitment to the company’s core values.
4. Integrity
• Reliable, honest and true to our word,
• Strong moral principles and ethical conduct,
• Treating everyone with respect.
QWhat is the company doing in regard to sustainability and the net zero agenda?
EPG is moving with the times. Most manufacturers now have or are developing more eco-friendly solutions via electric power. We are heavily involved with the electric machinery industry as it moves forward providing solutions to different sectors including auto and commercial vehicles as well as construction.
Q
How about broader involvement in the community and CSR?
The Shepherd Global group of companies has been a proud partner of charities including Great Ormond Street Charitable Trust, Build Africa, Designability and Whizz-kids. Each year we support our staff to fundraise for their
chosen charities through staff events. We also support our partners at fundraisers and event throughout the year.
QHow do you see EPG Global in five or ten years?
Our purpose is to deliver tailor-made products, dedicated claims handling and full-service administration to our customers and business providers worldwide. With our unique experience, expertise and knowledge in safeguarding our customers’ assets and business interests, our vision is to grow as a global provider for warranty solutions across multiple sectors. We are already expanding from agriculture and construction into trucking and auto, and embracing advances in technology, not only in electric vehicles and machinery, but also in how it can enhance our data and services.
QAnd how about yourself?
I would like to think I would be a good contributor to the success of the growth of the business over the next 5 to 10 years. Then maybe I will be able to afford to retire! Let’s see.
Who is your favourite artist? Ian Brown from the Stone Roses
What would be your desert island (exile) luxury? A comfy bed
What gets you out of bed in the morning?
A passion for the industry and a growing family
What do you do for fun? Golf and socialising
When are you happiest? When I can see all the growing family together
What’s your ideal weekend? Golf, and seeing kids and grandkids.
What’s your favourite cuisine? Chinese
What’s your tipple of choice? I’ll take what’s on offer at the time, I’m not fussy.
The countdown to the Resource and Waste Management Expo (RWM Expo) is on. As the UK’s largest gathering of resource, waste management and recycling professionals, RWM Expo takes place on 11 and 12 September at the Birmingham NEC.
The show offers an incredible opportunity for professionals across the entire resource spectrum to connect with the industry’s biggest players, learn from the sector’s brightest minds and drive positive environmental change via discourse on sustainable resource management.
The event is free to attend for the first 20,000 registrants, so secure your free place at the forefront of environmental innovation, solutions and knowledge exchange here: www.ess-expo.co.uk/rwm.
RWM Expo is at the forefront of resource, waste management and recycling, addressing critical issues such as resource scarcity, plastic pollution and sustainable materials use. Attendees can expect
to discover innovative solutions and technologies that promote recycling, waste reduction and the circular economy, ensuring both ecological balance and long-term economic growth in the resource sector.
Expect to see cutting-edge solutions from leading waste management suppliers, including waste service providers and operators; plant and machinery; sorting technologies; waste collections and transport; recyclers and reprocessors; material handling; skips and bins; and professional services and consultants.
RWM is spread across three halls and includes a massive 10,000-m 2 outside area featuring spectacular displays of industryleading machinery, live demonstrations of waste processing equipment, refuse collection vehicles and street sweepers. The outdoor section of the show is the place to see apparatus in its natural environment as well as to relax, enjoy food and drink and hear live music in the sunshine at the Inn on the Green.
RWM Expo is part of the broader Environmental Services and Solutions
Expo (ESS Expo). This event combines multiple shows, addressing key areas such as waste management; recycling; energy from waste; decarbonisation; water resource management; contamination; land development and air quality control in a comprehensive platform under one roof.
With more than 12,000 visitors, the combined ESS Expo forms the UK’s largest environmental event. This unique format allows attendees to seamlessly explore a wide array of sectors and industries, all focused on addressing the most pressing environmental challenges of our time.
With free entry and access to all co-located shows through a single ticket, the RWM Expo provides an unparalleled opportunity for networking, learning and collaboration across the entire environmental spectrum.
The five shows that make up ESS Expo are:
Resource and Waste Management (RWM) Expo – focusing on critical waste and resource management, innovative green technologies and solutions to the sector’s most pressing challenges in line with the principles of the circular economy.
Energy, Fuels and Decarbonisation (EFD) Expo – dedicated to sustainable energy generation, energy from waste, bioenergy, alternative fuels, energy management and decarbonisation. It covers a broad spectrum of topics, including carbon capture, hydrogen technologies and clean energy systems.
Water Resource Management (WRM) Expo – focusing on water scarcity, flood and drought cycles, wastewater management and water quality issues, WRM dives into wastewater treatment, point source treatment and sustainable practices to ensure safe and accessible water resources.
Contamination and Land Remediation (CLR) Expo – CLR addresses the remediation of contaminated sites; soils and materials; brownfield regeneration and greenfield development; geotechnical engineering and technologies; biodiversity and natural capital; and the management of hazardous substances.
Air Pollution Control (APC) Expo – focusing on air quality management, emission reduction, stack monitoring, noise prevention, dust and odour control.
Why attend?
ESS attracts over 12,000 international visitors, uniting industry pioneers, visionary entrepreneurs and eco-driven professionals to collaborate, learn and inspire one another to move towards a greener future.
From government to Europe’s largest environmental services contractors and big brands, RWM welcomes industry leaders from up and down the supply chain. Whether you are a business planning your net-zero strategy, a council looking to hear the latest regulatory updates or an equipment manufacturer launching a new piece of equipment, this is your platform to collaborate, network and learn with the people shaping the future of the resource sector.
Numbers that speak for themselves
12,000+ attendees
86% hold buying power
6,000+ companies
64 countries
26,000+ leads generated 17,000+ meetings
Free to visit: The first 20,000 tickets are free, making it an accessible event for all professionals interested in environmental services and solutions.
Comprehensive visitor experience
As part of five shows in one, attendees get to explore the full environmental spectrum under one roof, gaining access to a wealth of knowledge and innovations. One free ticket gets you access to all five shows, as well as the outside areas, which you can freely walk between.
Influential brands and suppliers
RWM hosts the most influential
brands and world-class suppliers in the environmental sector, providing a platform to discover new products and services from its 550+ exhibitors.
Unrivalled networking opportunities
With numerous opportunities to connect with peers, suppliers and potential clients, attendees can engage in private meetings, tutorials, member networking events, industry-specific forums, award presentations and breakfast briefings. Socials around the central bar, Inn on the Green, and at the ESS Live Stage featuring live bands and DJs, provide a more informal networking opportunity.
From high-level government discussions and cutting-edge technical sessions to interactive presentations and vibrant entertainment, ESS Expo’s 17 stages offer something for everyone.
Stages include the Net Zero Summit Theatre, which acts as the foundation for high-level discussions on environmental policies, strategies and innovations; the Green Skills and Future Talent Hub, which aims to nurture and develop the next wave of environmental professionals; and sector-specific technical theatres.
The expert-led conference programme includes interactive speaker presentations, lively panel discussions, workshops and Q&A sessions. Attendees will have the chance to learn from industry leaders and gain insights into the latest trends and innovations across the entire resource and recycling spectrum.
Current headliners include Chris Packham MBE (one of the UK’s leading wildlife presenters and conservationists) and Mike Gunton, an icon of wildlife broadcasting as BBC Studios’ Creative
Director and Executive Producer of record-breaking series, Planet Earth III.
The full agenda includes the likes of Sony, EY, Biffa, Virgin Media O2, the Environmental Services Association, WRAP, Grant Thorton, Veolia, the Environment Agency, BT Group, SLR Consulting, Plasticseurope, enfinium, Grundon Waste Management and more.
Live demonstrations and workshops
Live demonstrations of vehicles, equipment and machinery provide a hands-on experience with the latest technologies working in their intended environments. Workshops and talks will cover a range of topics, offering practical insights and solutions for everyday challenges in the environmental sector.
Award schemes and initiatives
RWM Expo features a variety of award schemes and initiatives that celebrate the achievements and contributions of outstanding individuals and organisations within the environmental sector.
The 35 Under 35 Awards identifies the trailblazers in the environmental sector who are striving for professional excellence, promoting industry innovation and giving back to their company or community. This programme invites individuals from waste and recycling, water management, energy, construction and anyone connected to managing sustainability within their organisation to join an exclusive group of professionals under the age of 35.
The Environment 100 recognition scheme recognises environmental leaders and sustainability champions, shining a light on the trailblazers and visionaries driving environmental sustainability in the UK.
A New Era in sustainable power: HVO and the path to a low-
As the construction industry advances towards a more sustainable future, the spotlight has increasingly turned to alternative fuels that promise to reduce carbon emissions while maintaining efficiency and reliability. For New Era, a leader in innovative sustainability solutions, the shift
towards alternative power sources is not just a trend – it’s a commitment to creating a more sustainable world. In this context, Hydrotreated Vegetable Oil (HVO) emerges as a key player in the quest for reducing carbon footprints, making it a natural fit for New Era’s vision.
The construction industry is one of the largest contributors to global carbon emissions, with traditional diesel fuels being a significant part of the problem. As environmental regulations tighten and the demand for greener solutions grows, there is a pressing need to find alternatives that not only meet the performance standards of traditional fuels but also contribute to the reduction of greenhouse gases. HVO is currently a viable solution.
Hydrotreated Vegetable Oil (HVO) is a renewable diesel alternative produced from vegetable oils, waste fats and residues. Unlike conventional biodiesel, HVO undergoes a hydrotreatment process that enhances its properties, making it a high-quality fuel that closely mirrors the chemical structure of fossil diesel. This allows HVO to be used in existing diesel engines without modification, offering a seamless transition.
The benefits of HVO
For companies like New Era, HVO offers several compelling advantages:
1. Significant carbon reduction: HVO can reduce greenhouse gas emissions by up to 90% compared to conventional diesel. This dramatic reduction is a game-changer for industries like construction, where cutting emissions is both a regulatory requirement and a moral imperative.
2. Enhanced performance: HVO delivers comparable, if not superior, performance to traditional diesel. It has a higher cetane number, which translates to better combustion, smoother engine operation and lower engine noise. For construction machinery that operates in demanding environments, these benefits are crucial.
3. Improved air quality: In addition to reducing CO2 emissions, HVO produces fewer particulates and nitrogen oxides (NOx). This contributes to better air quality on job sites, which is particularly important in urban areas where construction activities are often closely monitored.
4. Versatility and compatibility: One of the most attractive
features of HVO is its drop-in compatibility with existing diesel engines. This means that fleets can switch to HVO without the need for expensive retrofitting or new equipment investments, making it an economically viable option for companies looking to transition to greener alternatives.
In the near term, HVO provides a practical and impactful solution for reducing carbon emissions across New Era’s operations. By integrating HVO into its fleet, New Era is not only taking a significant step towards sustainability but also setting a benchmark for the industry to follow. As technology evolves, so too will the opportunities to further reduce environmental impact, ensuring that the construction industry can continue to grow while respecting the planet’s finite resources.
New Era’s embrace of HVO and other alternative fuels represents more than just an operational shift – it’s a pledge to lead the industry into a sustainable future, where innovation and environmental stewardship go hand in hand.
The RogueX2 loader has been developed from the RogueX concept presented at the Conexpo show in Las Vegas in 2023. RogueX2 is an all-electric and autonomous concept machine that produces zero emissions and features a lithium-ion battery, electric drive system and electric actuated lift and tilt kinematics with no hydraulics.
Specifically designed and built without a cab, the RogueX2 and RogueX concept
machines address the challenges of workforce shortages by eliminating the need for an operator. They also provide the blueprint for how work machines of the future can be designed and optimised for new technologies and enable an entirely new work experience.
In RogueX2, the internal combustion engine is replaced with an electric powertrain for power and drive. This machine also eliminates 100% of the
hydraulics, including all connectors, hoses, tubelines and fittings that are common failure points. The absence of hydraulics and fluids in its design not only reduces emissions but also minimises noise pollution and the risk of all environmental pollution.
The original RogueX was designed with tracks and it uses advanced workgroup kinematics to offer unique functionality that combines verticalpath, radial-path and variable-path lift capabilities in one machine. In contrast, RogueX2 is designed with wheels instead of tracks to optimise the electric battery run time. It also features axial flux motors, which give the machine incredible tractive effort. The machine delivers greater power output for demanding applications like grading, digging or powering attachments for heavy duty work.
Together, the RogueX and RogueX2 concept loaders have garnered many new patents pending. “These patents represent more than new features on a machine –they signify how we are breaking rules to define a new work experience,” said Joel Honeyman, Doosan Bobcat Vice President of Global Innovation.
We have the largest central stockholding in the UK, which is supported by a finely tuned stock control program, a highly organised warehousing system and carefully selected logistics partners. This allows Astrak to have the undercarriage parts that you need available when you need them, minimising machine downtime.
Once it’s on the machine, our extended warranty is the most comprehensive in the market place. Each of our rubber tracks come with an extended 24 month warranty as standard.
All of our undercarriage and wear parts are manufactured in IS0 9001 and OEM approved production facilities with rigorous quality control procedures.
Place your order prior to 4.30pm and it will be despatched for delivery on the next working day.
Our wide range of heavy-duty components will keep your excavators, dozers and tracked machinery working harder, for longer. Every hour of machine downtime incurs avoidable costs! This is why you need a reliable partner you can rely on. Stocking the widest range from bucket teeth, cutting edges and OEM quality undercarriage components through to custom made wear parts. Astrak providing you complete undercarriage and wear part solutions. The right part, to the right place, at the right time!
United Kingdom regulations allow hydrogen-fuelled cars, trucks and buses to circulate on public roads, but as things stand hydrogen-fuelled NRMM is not allowed on the roads. This disparity needs to be addressed with some urgency since many CEA members are developing construction equipment powered by a hydrogen-fuelled internal combustion engine. The way the law is currently written, these machines would be legally allowed to operate on a construction site. Still, they would not be permitted to circulate on public roads, putting them at a disadvantage compared to their traditionally fuelled counterparts.
The CEA was therefore very keen to respond to a recent DfT open consultation titled “Enabling road use of hydrogen-powered non-road mobile machinery,” which sought stakeholder views on whether hydrogen-fuelled NRMM should be allowed on roads and asked for feedback on DfT’s proposal on the means to demonstrate compliance with safety requirements.
After consulting with the wider CEA membership, our views were established and fed back to DfT. We very much welcome that hydrogen-fuelled NRMM should be allowed to go on the road, but we have some significant issues with the proposed route to demonstrate safety compliance. However, rather than raise our concerns, we supplemented our response with a counter-proposal offering a more reasoned compliance mechanism that will ultimately lead to safer machinery circulating on the road. We also believed that approval should not be granted for machinery initially sold with a diesel-fuelled engine, which was subsequently retrofitted with a hydrogen-fuel system in the aftermarket.
We await the outcome of the consultation and will advise members as soon as there is something further to report.
by Niki Holt, Head of Commercial at Certas Energy
With the UK government setting the net zero target of decarbonisation by 2050 for all sectors, many industries are seeking a replacement for traditional fossil fuels to help meet these requirements. One such option is renewable diesel and Hydrotreated Vegetable Oil (HVO fuel), alternatives that are gathering speed in popularity, with Zemo estimating that as many as 4,000 HGVs are now running on renewable diesel. Despite this growing use, many myths circulate about the fuel and how well it can perform compared to other alternative fuels and traditional fossil fuels.
Myth #1 – Electricity is the only choice for net zero
Integrating more electrification into vehicles and machinery will be vital to meeting net zero targets, but concerns are holding it back in the commercial space. These key concerns tend to focus on insufficient battery range and a lack of robust and accessible charging infrastructure. Plus, while the vehicles and equipment don’t directly produce emissions, there will always be by-products when generating the power, and establishing charging networks can still rely on fossil fuels. This is where alternatives can provide a solution, as HVO offers
significantly lower emissions than traditional fossil fuels and can act as an intermediary between traditional fossil fuels and emission-free electric. While it isn’t completely net zero, it’s an important step for businesses to re-evaluate their carbon footprint.
Myth #2 – HVO and renewable diesel isn’t cost-effective
As a premium fuel with benefits over and above standard fossil products, the cost per litre of HVO fuel is currently not the same as standard diesel, although the price gap is expected to reduce as momentum accelerates to achieve greenhouse gas emission reductions and governments consider additional incentives for renewable fuels. It’s also worth noting that there are no switch costs for changing to HVO from standard diesel. Unlike the often-considerable upfront cost of switching to some other alternative energy options, HVO is a straight drop-in fuel.
Myth #3 – There’s no value in making the transition yet, as it will disrupt my business
Despite the government’s plan for a carbon-neutral future, many businesses may not see any reasonable benefit in making the switch before it’s a necessity. But we’ve already seen legislative changes being passed, such as Ultra Low Emission Zones (ULEZ) and clean air zones (CAZ) around the country to encourage the
incorporation of alternative fuels and help push towards better air quality.
This represents only the beginning and it’s likely we’ll see more changes and restrictions being introduced that will force a much faster adoption of alternative fuels like HVO. HVO is an attractive alternative to standard diesel and it’s expected that as more restrictions come into play to support plugging the gap to net zero, getting ahead of the curve and building relationships with supply partners will help businesses to mitigate risks.
is beginning to be seen by an increasing number of businesses across wide range of industries, including haulage and logistics, construction, public sector, utilities and marine to name a few.
This is made easier by the fact that modifications to machinery, vehicles, equipment or engines are not required –meaning less disruption or downtime in operations, as well as zero or minimal cost to switch, giving businesses a smooth transition between fuels and enabling productivity.
Myth #4 – It’s not reliable enough
Reliability is a factor that many businesses deem crucial to making commitments to a newer technology. This is why many may see fit to stick with traditional fuels like diesel, due to the stability of the offers despite its emissions. However, positive adoption of renewable diesel alternatives
This shows that investing in alternatives like HVO can help fuel innovation and push forward as a true renewable option in the future. At Certas Energy alone, there’s an extensive national network of around 900 tankers, 130 local depots and a growing network of HVO-stocked high-speed HGV refuelling sites, all supporting a reliable, assured, convenient and competitive supply of HVO to UK businesses.
Myth #5 – It’s not suitable for my business due to warranties and OEM approvals
While HVO is a suitable fuelling solution for vehicles capable of all terrains, as well as plant and machinery, a common myth is that it’s not compatible with popular OEMs. This is far from the truth, as most OEMs already have confirmed their approvals of HVO fuel.
JCB has taken another major step forward in the process of evaluating hydrogen as a fuel of the future, with the first showing of a generator powered by the net zero fuel.
The company is investing more than £100 million in pioneering hydrogen as a fuel solution for construction and agricultural machines and has already produced 115 evaluation engines, which are powering backhoe loaders and loadall telescopic handlers.
A new concept was unveiled in June at the Hillhead Show – a generator powered by a JCB hydrogen combustion engine. The G60RS H genset offers a glimpse into the future of zero carbon worksites and highlights how the JCB
hydrogen generator delivers the same power, performance and efficiency as its diesel equivalent – but without the carbon.
JCB showcased how a hydrogen generator works in tandem with JCB’s three-phase Powerpack to create on-site microgrids – utilising both battery-electric and hydrogen combustion technology. With energy supplied to the Powerpack from renewable sources, the generator, powered by hydrogen, effectively becomes a battery charger, only running for short periods when the battery needs topping up, or at peak load points. This reduces fuel consumption and offers long periods of silent or quiet hours operation.
JCB’s Group Director of Special
Projects, Tim Burnhope, said: “Hydrogen generators coupled with battery boxes really are the future, paving the way for the formation of on-site microgrids. Construction sites today rely on diesel power because there are insufficient or inaccessible grid connections, but because diesel is incompatible with net zero targets, customers are rightly seeking alternatives.
“A hydrogen generator offers that alternative, providing clean power on site. It delivers zero carbon power to the worksite for anything from welfare units to lighting towers. It also works in the same way as its diesel counterpart, ensuring familiar operation, installation, maintenance and servicing.”
BMC MAKE ALL TYPES
LARGE STOCK OF 1 - 22 TON BUCKETS AVAILABLE FOR NEXT
First shown on the company’s stand at Intermat 2024, the prototype DL250 FCEV (Fuel Cell Electric Vehicle) from DEVELON has a versatile, single platform design that allows it to be equipped with a fuel cell powerpack running on hydrogen, but offers the ability to transition to a BEV (Battery Electric Vehicle) by installing a battery pack.
The design of the DL250 FCEV prototype offers solutions to some of the key challenges in operating zero emission vehicles such as battery cost, battery charging time, the infrastructure for rapid battery charging and the hydrogen refuelling infrastructure. These challenges vary across regions, hence a strategy that can cater to various electric power systems, such as BEV and FCEV using a single platform is essential. Despite being designed based around the FCEV system, the DL250 FCEV wheel loader allows easy expansion to the BEV system.
Electric drive with flexible platform
The electric solution in the DL250 FCEV is based around segmenting the machine into two primary areas: the Function Area, responsible for the operation of equipment with a smaller battery capacity, and the Power Source Area, serving as the equipment’s main power hub. This unique design allows the Power Source Area to be versatile – when equipped with a fuel cell Powerpack, the equipment operates as an FCEV system running on hydrogen, but when installed with a battery, it transitions into a BEV system. This means from a singular platform, it is possible to implement a diverse range of electric power systems. In the DL250 FCEV, saltered by fitting a battery to transform it into a BEV system. A challenge that arises, especially in equipment similar to electric vehicles with large battery capacities, is the extended charging time relative to equipment operation.
However, the DEVELON solution lies in the modularity of the Power Source Area. Unlike the fixed Function Area, the Power Source
Area is designed for easy replacement, thereby addressing the charging time issue with a battery swap method, ensuring equipment remains at the forefront of efficiency and adaptability.
The DL250 FCEV, when compared to traditional internal combustion engine wheel loaders of equivalent weight and performance, has a more substantial rear size. This enlargement results from the replacement of spaces previously occupied by the engine and fuel tank with the Powerpack, which can potentially hinder visibility in the equipment’s operation due to the increased size of the Power Source Area.
To mitigate this visibility issue, DEVELON has equipped the machine with cameras to enhance rearward sightlines. This ensures that regardless of the size of the Powerpack installed in the Power Source Area, operators experience no significant obstructions to their field of view.
Additionally, anticipating the possibility of Power Source Area replacements, DEVELON has integrated a Dual Camera System. This design ensures unobstructed rear visibility even when components from this area are removed, further enhancing the equipment’s userfriendliness and safety.
Both the front operations and driving tasks of the wheel loader have been equipped with electrically driven systems: the e-Working system and the e-Travel system. The e-Working system ensures performance equal to or better than existing internal combustion engine equipment. As for the e-Travel system, it leverages regenerative driving to enhance efficiency. It also offers rapid responsiveness compared to conventional combustion engines, enabling users to execute tasks more swiftly.
The DL250 FCEV, which currently uses hydrogen as its power source, can operate for more than eight hours on a full charge. Should it be converted to use a battery as its power source, transitioning into a BEV system, it still maintains the equivalent performance, testifying to the versatility and efficiency of DEVELON’s design.
In 2023, SANY launched its first electric mini excavator to the UK plant and tool hire market with Charles Wilson Plant amongst the first of leading rental companies to invest in these electric machines.
With the fully electric SY19E, SANY sees the advantages that high voltage can give in terms of efficiency and performance. Unlike other manufacturers, SANY has successfully designed the technology, which is normally only seen in large machines into this small twotonne machine. This technology offers industry changing benefits and a number of environmental benefits too.
Automotive standard component configuration
Automotive standard components meet the highest safety requirements and regulations, the performance is much greater than comparable industrial components and they are more readily available to purchase which effects the total cost of ownership for plant hirers. The CCS2 charging socket of the SY19E is also automotive standard, therefore the SY19E can be charged at any public charging station, including fast chargers, which helps to support the charging infrastructure being developed by the government and companies within the UK.
State-of-the-art lithium iron phosphate battery
The 100% electric SY19E is powered by a state-of-the-art lithium iron phosphate battery, exceeding SANY’s objectives to provide the best solution to both customer and operator alike. Lithium iron phosphate batteries not only have superior operating characteristics compared to lead-acid batteries, they’re also far less toxic to produce and recycle. They do not contain any toxic/hazardous chemicals or rare metals like cobalt, nickel or lead and are made of more common elements like graphite, iron and copper instead, eliminating the biggest environmental impact factor in standard lithium ion batteries and improving recyclability.
The lithium iron phosphate battery, equipped with a 11-kW onboard charger offers customer three different methods to recharge the machine. Fast charging in 1.5 hours, or AC charging in 2.5 hours from a battery level of 0 to 100%. Unlike other batteries, the depth of discharge behaviours will not affect the overall life of the battery. This allows the customer to tailor the charging needs to each day and different site/ job being undertaken, minimising logistics and maximising business efficiency.
Lithium iron phosphate batteries also offer lifetime periods (up to 3,500 full charge cycles), which will cover the machine for more than the standard lifetime. This reduces environmental impact compared to other batteries, which will need to be changed throughout the machine life.
The SY19E excavators are produced within a light house factory company (as recognised by the World Economic Forum) so material waste, energy and greenhouse gas emissions are hugely reduced throughout the
production and manufacturing process, minimising the environmental impact compared to standard manufacturing processes.
The SY19E’s high voltage system and automotive standard components offer state of the art design and easily available changeable parts. The high voltage reduces energy loss and increases the energy capacity, ultimately offering the best environmental benefit, performance and economy in the market.
Ben and the team out promoting the industry between issues
by Wayne Ridings
There has been a positive upturn in our sales of bespoke products within the UK marketplace since the start of the year. There are several reasons for this but, I believe the tilt and turn couplers have played a significant role in this upturn. Our clients seem more willing to invest in the correct product for the intended project these days.
A lot of money has been invested in the tilting products and for many, they have proven their worth, highlighting the benefits of bespoke in general. Adding the extra weight of a tilty to the machine presents its own problems when choosing suitable attachments to accompany them, increasing the quantity of bespoke buckets required even further.
Using the correct tool for the machine is a vital long-term investment that will pay dividends both in productivity and maintenance. It makes sense to shift the maximum load within the machine’s capabilities ensuring operator safety and the best possible returns economically. Bespoke applies with or without a tilting mechanism or quick coupler – when you want maximum effectiveness, one size does not fit all.
For instance, our popular 4 in 1 bucket must be made to measure because, due to replaceable wear parts, rams and general heavy build to provide a strong grab function, a slightly smaller capacity bucket will be produced. These buckets are truly heavy duty with a remarkably impressive gape and grabbing force that suits excavators from 1 to 20 tonnes. The feedback on these buckets has always been positive, the best of its kind I have seen in my time.
While we endeavour to manufacture all our bespoke products ourselves, we have been unable to supply our customers with products suitable for machines over 70 tonnes. With this in mind, we are presently in the process of forming an alliance with a first-class company based in Italy to remedy this, allowing BMC to offer our customers another alternative in the bigger end of the market. We are looking to supply the specialised products in the mining and quarrying divisions including dozer and loader products giving bespoke opportunities throughout all markets. So watch this space guys, this will be happening in the very near future.
Small radius ditch cleaning buckets are proving very popular this year, usually supplied longer than standard with a closed smaller profile allowing the operator to work from one side of the ditch, for instance 2.4m long is regular for a 13-tonne machine. Again, there are similar versions of these to suit each category of weight excavators you require.
BMC rock buckets will always sell because they are all built to customer spec. They can be supplied full of replaceable armour or can be constructed fully from Hardox materials to control weight and preserve capacity.
When it comes to buying an excavator attachment it can seem daunting when looking at the prices. You may be questioning why would I pay this price when there are cheaper options available? An important place to start, is asking what are excavator attachments and what are they going to be used for?
Often our customers are offering more than one service to their clients. It used to be that you would have a specialist contractor to carry out the demolition work and then another to a carry out the remediation etc. Now you see the demolition company completing up to and sometimes including the groundwork stage before handing over a site to a client.
Excavator attachments are highly specialised tools which attach to an excavator to perform different tasks in various industries. With the vast range of types of attachments available, it’s important to consider the purpose:
• Hydraulic hammer/breaker – Used in the construction, demolition and quarrying industries. Its primary purpose is to break down concrete, rock and other hard surfaces.
• Selector grabs – A very versatile attachment in the waste recycling, demolition, construction and land clearance industries. Great for lifting and moving materials or pulling down buildings in demolition.
• Rotating pulveriser – These attachments are used for primary and secondary demolition, concrete pulverising and material processing.
• Screening buckets – To screen and separate materials while on site for various purposes such as reuse and salvaging.
From these examples it’s clear that they need to be strong, reliable and up for the demanding work that is required of them. Even high quality and well-made attachments become worn down over time and require maintenance to keep them running smoothly. On the other hand, cheaply made attachments are often more
likely to break down, less efficient and may be harder to find replacement parts for. This can result in them becoming rather expensive, not to mention the cost of downtime.
With that in mind it’s clear that buying an attachment for you excavator isn’t a decision that should be taken lightly. It requires you to do your research to make sure that you are getting an attachment that is going to serve you and your business well. Is it worth saving money initially and going for a cheaper option that may only last a short time before having to buy another one? Or do you make the investment and go with a brand that is built around quality and reliability?
If you decide to make the investment it can have a significant impact on your operations and how productive and efficient they are. Choosing quality made attachments comes with the peace of mind that they are built to last and get the job done effectively. This can have positive knock-on effects for your business such as increased customer satisfaction and customer loyalty.
Another added benefit of buying a high-quality attachment is that the supplier will offer a much longer warranty. At BPH Attachments we go beyond a warranty and offer you constant support and care should an issue arise.
BPH Attachments, the Excavator Attachment Specialists, provides the right attachment for the operator to get the best performance. PRODEM Attachments, which BPH exclusively imports to the UK, are the choice for strength and durability. They have long been a force to be reckoned with in the hydraulic attachments market. Since 2003, PRODEM Attachments has become synonymous with durability, reliability and cost effectiveness – the trilogy of key desirable characteristics in excavator attachments.
BPH is a family-run business with over 50 years’ experience in the construction industry. This means we have the knowledge and experience to advise and support you. We also like to think we’re great folk to do business with. We’re quick, our products are reliable and we are there with support when you need us – known for providing high-quality products that are right for the customer.
Our vision is to continue developing BPH Attachments based on our company’s foundations. We will never lose sight of what sets us apart (quality products coupled with exceptional customer service). As a leading supplier of excavator attachments for sale, hire or repairs, we cover the whole of the UK and offer next day delivery for in stock products.
For the last 30 years, we at Hill Engineering have pioneered the design and manufacture of hydraulic quick couplers for excavators. During this time, we’ve constantly looked for ways we can improve our products, researching and developing new products to add to our industry leading range, meeting stringent safety standards and delivering exceptional quality, synonymous with the foremost manufacturer in our industry.
Setting standards through quality, innovation, reliability and safety
We’re uncompromising, both in our exceptional production standards and our quest for new innovations. Like our customers, we demand perfection at every stage from the materials we use to every person involved. We’re fully committed to not only delivering world class products but also to maintaining new levels of safety and compliance, born out of our unquestionable and comprehensive knowledge of our industry.
Hardworking couplers that are big on durability
We’re the global leaders in excavator attachments, supplying leading manufacturer brands including Hitachi, JCB, Komatsu, Takeuchi, Volvo and Caterpillar, and our products have won many awards around the world. We also supply direct to businesses in construction, civil engineering and demolition, with our TEFRA range of fully automatic quick couplers to suit excavators ranging from 2 to 120 tonnes.
Complementing TEFRA is our TITAN bucket range, which is reliable and long lasting for increased earth moving performance. Built with high strength steel, our buckets feature a double radius design, which gives superior digging performance due to the low drag factor. This also means that they fill quickly, meaning more productive digging and loading operations. Our Titan buckets have an enviable reputation for build quality, excellent digging performance and long service life.
They are designed and manufactured
in the UK to conform to OEMs’ dimensions and have the option of fixed pin or bossed attachment points.
All our products are manufactured at our purpose-built facility in Northern Ireland and sold to a global customer base via a distributor and support network around the world.
Since the launch in 2009 we have sold over 130,000 TEFRA couplers. Today we have five options in the TEFRA Range:
• The excavator coupler for machines in the >10-tonne weight class
• The BHL coupler
• Mini excavator coupler for machines <10-tonne weight class
• TEFRA Tilt available for excavators from 2 to 22 tonne-weight class
• TEFRA Connect
Each is manufactured to the same exacting quality standards and each features our unique dual locking system to meet enhanced safety standards.
The primary safety system consists of a uniquely designed set of hooks powered by a single high specification hydraulic cylinder. The cylinder works together with a dedicated solenoid valve, locking the attachment securely into place.
The intrinsic feature of the hooks is their shape – they are designed to hold the attachment pins against the body of the coupler. This secure and failsafe retention means the attachment stays in place in all orientations and operating conditions.
Our Active Protection System (Hill APS) consists of two separate powerful springs that apply pressure to the hooks to ensure attachment retention at all times.
A single leaf spring applies constant pressure to the front hook. This compact and durable spring ensures the hook stays in place at all times.
A coil spring serves exactly the same function in relation to the rear hook. Both springs are individually rated far in excess of any strength and safety requirements and have undergone stringent testing to ensure durability and reliability in the field.
Miller UK, the United Kingdom’s largest bucket and coupler manufacturer, has invested in five new state-of-the-art welding robots, significantly increasing welding speed, delivering 100% weld consistencies and improving the safety of its workforce.
The new robots, already in full operation, were developed by industry leaders in welding and automation, CLOOS and include two different model ranges. The QRC 410-2.0 range is ideal for welding attachments for machines up to 45 tonnes and the QRC 350-E models are capable of handling attachments for machines up to 100 tonnes. The introduction of the larger machines doubles the company’s production capabilities.
Miller first invested in welding robots in 2018, with the installation of the smaller robots. Recognising the value of these machines, it has now installed the latest range of these models. The business believes it is the first of its type in the world to have such advanced robotic welding machinery, capable of producing buckets up to 3.2-m wide and able to hold up to 4.5 tonnes of material.
Speaking about the investment, James Ross, Commercial Director at Miller said: “Manufacturing technology has always been a priority and it is very important that Miller continues to invest in the next generation of welding equipment and robotic automation, which can transform the quality to consistent market leading levels. This will be recognised by our customers in terms of product durability and performance in the field.
“With minimal production downtime required and the ability to operate for extended periods of time, this has significantly increased our manufacturing capabilities –particularly to produce much larger buckets for extreme applications to meet demand and significantly reduce lead times for customers. As such, this allows Miller to have a real competitive advantage in our marketplace.”
The QRC 350-E robot boasts a range of smart features. Comprising 12 axis movement, including the robot arm, the machine is designed to allow for more manipulation of parts, which increases its versatility and ability to reach more difficult areas on a workpiece. This allows Miller to weld more, while reducing the manual labour required once the robot process has been completed.
The tandem and single torch of the machine operate in conjunction with each other with the tandem torch being used for long straight run welds while the single torch completes trickier, harder to reach radius parts. Not only does this increase the speed of the process, it also reduces heat input decreasing distortion of the workpiece.
Gregg Hudson, Global Manufacturing Leader said: “The new robot really does step our production capabilities up to the next level. The weld finish achieved
from this machine is exceptional and like nothing else you will see on the market as we continue to drive our quality standards, which is what we are known for. This is showcased with our demo units at Miller HQ where customers can inspect first-hand the quality they will receive.
“It is an exciting time at Miller for our staff on the shop floor to work with the new machinery and learn the next generation of pre-programming welding automation techniques to operate the equipment, while continually developing
their manual skills. We have significantly invested in upskilling our workforce with complex technical knowhow to operate our suite of robots and have a dedicated team for collaborative automated production.”
Increasing the safety of its workforce, the robot has an extensive range of safety features, including mechanical barriers when the robot is in use, which will trigger an emergency stop if opened.
Established in 1978, Miller supplies its
trusted products to leading earthmoving manufacturers, including Komatsu, Hitachi, Volvo, SANY, LiuGong, Kubota, Case, Cat and JCB, as well as an established independent global distributor network and end users worldwide.
The new Plury range from Malaguti offers a new and innovative solution to excavator attachments. Featuring a range of accessories that can be added to the main vibration body, the Plury allows you to compact, pre-drill, drive piles and cut with a single machine.
This versatile attachment comes in 10 models and is suitable for excavators from 1 to 40 tonnes. This updated compact and pile range from Malaguti allows for more effective working with
multiple jobs being covered by one machine. Accessories include cup, sheet pile clamp, grapple, various plates, pre-drill bit, asphalt cutter and compaction wheels.
The Plury range is ideal for construction, agricultural and other applications for trench work, ground compaction, photovoltaic systems, fencing and post driving and sheet piling. Malaguti has also developed a quick coupling system as an optional extra so that accessories can be swapped over without leaving the cab.
Puts safety first ENGINE 115 LIFT HEIGHT 12.5 LIFT CAPACITY 4.0 t
The featured image is a P40.13 with 12.5m lift and 4t capacity with built in attachment recognition. Merlo’s Adaptive Stability Control System adapts load charts and safety limits to guarantee maximum performance in total safety at all times.
The Bristol Port Company’s buyer for plant equipment may have inherited Ulrich Attachments as a supplier from her predecessor but the relationship has gone from strength to strength, to such an extent that this year could be a record one for the partnership.
Lucy Ellis, Project Engineer (Procurement) and her colleagues at The Bristol Port Company have purchased 24 attachments from British manufacturer Ulrich in the past 10 years. Most of the buckets are the High Tip high-discharge buckets designed for light material or stone re-handling into high sided trucks and hoppers. Ulrich has been at the forefront of the development of these and at Bristol Port, they are complemented by a pusher blade designed to reduce
areas where grain may become trapped or lost, ensuring the maximum grain stays in the store.
Four of the Ulrich attachments have been purchased since Easter – two 3.3m 3 and one 5.3m 3 High Tip as well as a 6.3m 3 High Tip that was custom-designed for the port, which has existed since Roman times.
Lucy Ellis said: “The bucket was designed to allow maximum capacity with good visibility over the top. It was an adjustment from an original design sent and has performed well, with no issues.”
Three more stone buckets are now on order.
Ulrich’s attachments are typically used across a range of front-end loaders on the company’s Avonmouth and Royal Portbury docks, which opened in 1877 and 1977 respectively, for bulk materials such as animal feed, stone and gypsum.
Lucy added: “I have continued to purchase Ulrich Attachments as we have had good performance from them and the price is competitive. I have also had good support technically and from the sales personnel.
“We have used a mix of suppliers in the past and we do tender out work and review costs and design before making a decision. But our service contact at Ulrich, Drew, is very helpful and we have had a positive experience overhaul with them.”
Ulrich National Sales Manager Emma Pierce said: “We redesigned the 6.3m 3 bucket for them to better suit the application and the material they are working with. The material is a finely ground maize powder and they were finding they were losing a lot of material over the sides of the bucket.
“We looked at the design and went back with a solution but they needed to see the leading edge of the bucket for health and safety reasons. So our design team worked closely with Lucy and myself to come up with a new design to meet these needs and they ordered the bucket based on this new design.”
The Bristol Port Company was formed in 1991 when entrepreneurs Terence Mordaunt and David Ord purchased the Port of Bristol from Bristol City Council. Since privatisation, more than £600 million has been invested to create a modern, thriving business offering the full range of shipping, distribution and logistics services.
Ulrich has been a leading UK manufacturer of front-end attachments and supplier to all the major OEMs for more than 25 years.
As well as its flagship High Tip buckets, it also manufactures general purpose, side-dump and refuse clamp buckets; rock, grain and coal buckets; hydraulic quick couplers, long-reach boom and dipper arms, and fork attachments.
A proud member of Made in Britain, it offers a wide range of standard and bespoke options for plant machinery ranging from telehandlers, wheeled loaders and excavators to tractors and military equipment.
Ulrich exclusively offers up to five years extended warranty on all its telehandler and wheeled loader attachments, and specialises in wheeled loader bucket and loader arm refurbishments at its Hull factory or with its team of highly-skilled service engineers on site.
The business started following a management buyout from Boughtons,
the then premium producer of buckets and winches. Ulrich has since revised and perfected designs, introduced new products such as tree cutters, hydraulic steps and excavator booms, and thanks to sole production in the UK, has probably the shortest lead times in the industry.
The highly experienced team have chalked up more than 100 years’ industry expertise between them and comprises world-class designers, sales and support staff, and a manufacturing team whose attention to detail is unsurpassed.
At CAM attachments, a house brand of TVH, innovation, efficiency and safety are top priorities. That is why CAM attachments is proud to unveil its latest family of fork positioners, featuring the advanced PK-TS model. This attachment is designed to improve operational efficiency and set new standards in productivity, ergonomics and safety.
Want to increase productivity while ensuring operational safety? How about improving ergonomics and reducing damage? Fork positioners used correctly can achieve all these objectives, making them the preferred choice material handling machines such as forklifts.
The hydraulic adjustment of the distance between the forks is a key feature of fork positioners. This innovation offers several significant benefits:
• Operator comfort and reduced fatigue: Drivers no longer have to leave their cab to manually adjust the forks,
• Improved accuracy: The forks can be adjusted while the load is up,
so there is no need to lower the forks and mast for adjustments,
• Prevention of injury: Manual adjustment of forks carries the risk of back strain and pinched fingers.
The use of hydraulic fork positioning saves time and enables faster load cycles. This allows drivers to spend more time on their core task – handling goods. Uptime increases, boosting productivity and creating more value.
The PK-TS embodies the many advantages of a fork positioner and is the cream of the crop in terms of safety, ergonomics and productivity. The PK-TS comes as a hook-on version with carriers to mount standard forks (ISO 2328:2011).
One of the striking features of the PK-TS is its hydraulic fork adjustment system. The operator can adjust fork distances without leaving their seat. This eliminates the need for manual adjustments and speeds up loading cycles, saving you valuable time.
The main feature of the PK-TS is its
fork positioning system. However, it also has a sideshift function, allowing the load to move sideways. This adds even more flexibility and value for money to this attachment. This dual function reduces cycle time and improves driver safety and comfort.
The precision of the PK-TS is second to none, with precise fork positioning and sideshifting capabilities. These hydraulic features provide the flexibility needed for seamless load handling and optimal placement, making work easier and more efficient.
When it comes to durability, the PK-TS does not disappoint. It is robust and designed for easy maintenance, with a long service life thanks to reinforced frame corners that absorb shocks and easily accessible lubrication points.
Thanks to its powder coating, the PK-TS is more resistant to stains and scratches. This durable coating ensures the attachment remains impeccable looking and functioning, no matter how tough the job.
Designed with a low over-height, the PK-TS gives operators better visibility. In addition, the compact design makes it easier to handle loads under ceilings and in confined spaces.
Don’t miss out on transforming your operations with the PK-TS fork positioner. Contact TVH today to learn more and discover for yourself how the PK-TS can take your material handling efficiency and safety to new heights.
The Construction Plant-hire Association (CPA) has confirmed the panel speakers and topics for the CPA Conference on Thursday 7 November 2024 at the Heart of England Conference and Events Centre in Meriden near Coventry.
The theme of the one-day conference is Shaping the Future: Insights for the Plant-hire Sector and the event will be co-hosted by Merryn Myatt – a former television presenter, newsreader and journalist who previously worked with
the BBC, ITV and Channel 4 – and Peter Haddock who is well known throughout the plant-hire industry as a content, social media and PR specialist, journalist and vlogger.
The CPA Conference 2024 will bring together a number of panel speakers discussing how organisations can shape the future of the plant-hire sector. Merryn and Peter will lead a number of interactive panel debates discussing key topics including innovation, decarbonisation, digitalisation, skills, business growth, succession planning and mental health and wellbeing in the construction sector. CPA Chief Executive Steven Mulholland will welcome attendees and deliver a keynote speech at the event. The panel speakers taking part in the conference are Andrew Egglesden, Group Equipment Deputy Director at Soletanche Bachy; Beth Doel, Advanced Technical Trainer at Reaseheath College; Brian Jones, President of the CPA; Carl Hassell, Group Director of Skills at NOCN Group; Chris Cassley, Policy Manager at the CPA; Chris Harvey, co-founder of the Hire Exchange; Dani Saveker, CEO and founder at Glas Method; David Graham, co-founder of the Hire Exchange; Deborah Madden, Engagement Director at CITB; Ian McMillan, Head of Business Development at Thomas Group; Jamie Charles, Lead Economist at Oxford Economics; Jamie Morris, Technical and Managing Director at Gaia; Katie Kelleher, Technical and Development Officer at the CPA; Kathryn Adams, Commercial Director at Prolectric; and Steve Kerslake, Trustee and founder at Construction Sport.
Delegate tickets can be booked online at www.cpa.uk.net/events/cpaconference-2024 and CPA members can take advantage of a 50% discount on the standard ticket price of £80 plus VAT by emailing enquiries@cpa.uk.net for the discount code.
Last year’s CPA Conference theme was Facing the Challenges and the CPA Conference 2024 has moved on to discussing how attendees can help shape the future of the industry and provide solutions. There will be a total of five panel debates throughout the day, notably:
• Panel Session 1: The plant-hire sector in 2024 – Where the industry currently sits in the wider economic and political context
• Panel Session 2: The innovative plant-hire company – Insights into current and future developments and innovations in the sector
• Panel Session 3: Expanding the skills base – Where do we stand in the battle for skills, what progress is being made in attracting new people to the industry, especially women?
• Panel Session 4: Growing your business – What next? The challenge of growth and succession planning
• Panel Session 5: Focus on mental health and wellbeing in the construction sector
The CPA Conference 2024 will run alongside a small, targeted exhibition. Confirmed exhibitors at the event so far include headline sponsor MHM Group, plus ACOP Group, Acrow Bridge, CESAR Powered by Datatag, CITB, Capja, Conquip, GGR Group, Explore Plant and Transport Solutions, Genquip Groundhog, Parksafe Group, Plantworx, Point of
Rental Software, Prolectric, Record360, Rouse Services, Scottish Qualifications Authority (SQA), Spartan Solutions, Thomas Group, VUE Group and WOLFF Onsite.
A limited number of exhibition spaces are still available. For further information, please contact Lisa Collins on 07968 840 390 or email: lisa@lisacollinscommunications.co.uk.
Based in Leeds, Mount Machinery has made a name for itself as a supplier of services and attachments for excavators in a range of sectors. Following its acquisition by CID Group last year, the business has grown within the excavator attachment market.
This family-run company, which has been in operation for more than 20 years, provides a wide selection of hydraulic breakers, crusher buckets, screening buckets and other products to the recycling, civil engineering and demolition industries. Whether
you’re shopping for new or refurbished machinery attachments, or just want to hire one to test it out, Mount Machinery makes sure the appropriate item is delivered to the job site in a timely manner.
Mount Machinery is recognised for its extensive inventory, available for both hire and sale. Products include attachments from top manufacturers like 4TÉ, Socomec, PRODEM, and Cangini, known for their reliability and innovation. As well as the attachments, the workshop holds a large stock of parts and consumables which are often available for same day collection/ next day delivery.
One of the standout products is the FSB screening bucket, which is unique in that it is hydraulically adjustable in seconds. The two drums, one inside the other, are controlled from inside the cab. These are currently available to purchase.
The hire fleet is rapidly growing with new equipment arriving frequently. If you need reassurance that the item you are looking to buy is really what you want, the team recommend hiring to get a feel for its performance before you make the purchase. Because the wide range of breakers and saddles fits excavators ranging from 1.5 to 40 T, they are highly accessible.
Mount Machinery makes certain that every component of the excavator and attachment setup is configured for optimal performance. This covers operator assistance and training in addition to mechanical modifications.
Mount Machinery’s 5% price match promise, which guarantees consumers receive the best value for their investment, demonstrates its devotion to quality. The company’s fully stocked workshop, manned by skilled experts, can handle anything from simple fixes to intricate diagnostics and Mount Machinery is now the preferred supplier for many in the
excavation and construction industries thanks to its unwavering commitment to quality.
The Mount Machinery workshop is fully equipped to handle all your repair and servicing needs. Services range from breaker re-gassing to large overhauls using the most advanced diagnostic equipment available to quickly and precisely pinpoint problems. Because of the team’s experience, they can make repairs that both meet and frequently surpass industry requirements. In addition to repairs, Mount Machinery provides speciality servicing such as hydraulic testing,
calibration and help setting up new attachments. They are aware that in order to function at its best, every attachment needs to be flawlessly connected with the excavator. Their professionals not only install the machinery but also train personnel on site so they are well aware of its safety procedures and operational features.
Whether you’re looking to hire, purchase, or service equipment, Mount Machinery has the expertise and resources to meet your needs.
In the world of construction and excavation, the right equipment can make all the difference between a project that runs smoothly and one that faces constant setbacks. Mutley Plant Service understands this critical need and has dedicated itself to providing top-tier excavator rental attachments.
At Mutley Plant Service, we believe that every project, big or small, deserves the best equipment. Our extensive range of excavator attachments are designed to enhance the versatility and efficiency of your machinery, enabling you to tackle diverse tasks with ease.
Some of our hire attachments include concrete crushers, hydraulic breakers, sorting grapples, clamshells, multi-processors, shears, pulverisers and hydraulic magnets. We can offer fitment sizes from 1 to 100 tonnes all over the UK.
What sets us apart in the competitive landscape of equipment rental is our unwavering commitment to quality, support, and value.
Quality equipment: We partner with reputable manufacturers to provide attachments that are built to last and perform under the toughest conditions. Each piece of equipment is thoroughly inspected and maintained to ensure it meets our high standards of reliability and efficiency.
Expert support: Our team of professionals is always on hand to offer expert advice and support. Whether you need help selecting the right attachment or require technical assistance, we are here to help.
Competitive rates: We understand the financial constraints of projects, which is why we offer flexible hire options at competitive rates. Our goal is to make it affordable for you to access the best tools without compromising on quality.
Maintenance and service: Downtime can be costly, so we ensure all our equipment is regularly serviced and well-maintained. This proactive approach minimises the risk of breakdowns and maximises the efficiency of your operations.
We believe that we are more than just
an equipment rental company, we are your partners in demolition, construction, recycling and excavation. By providing a wide range of high-quality excavator attachments, we would like you to take on any challenge with confidence and efficiency. Whether you are breaking ground on a new project or tackling a complex demolition, trust Mutley Plant Service to provide the tools you need to get the job done right.
Tru7 Group is a Suffolk based family business with a history spanning over 60 years. Combining new and existing services, owner and CEO, Guy Nicholls rebranded the family’s group of businesses ‘Tru7’ and started a refreshed entrepreneurial journey.
Today Tru7 Group is comprised of various divisions, providing a holistic range of services including nationwide self-drive or operated plant hire and plant sales, commercial vehicle hire and sales, earthworks and demolition contractors, ready-mix concrete, recycling, aggregates, and muck away.
As the group continues to diversify and expand, it maintains its traditional approach to business, as Guy Nicholls says: “While the brands may have changed, our values haven’t. At Tru7, we put service and quality first.” This sentiment rings true across its full scope of services, as the group is renowned for investing heavily in its range of low emissions machinery and equipment, maintaining one of the youngest fleets nationwide.
Tru7 Group is also fiercely loyal to its East Anglian roots. The team has raised significant funds for local organisations, including St Elizabeth Hospice, the Motor Neurone Disease Association and East Coast Hospice. Tru7 is also the proud sponsor of the Ipswich Witches and Sheffield Tigers Speedway teams, both sporting Tru7 Group branding.
The group also employs more than
300 people, with the majority living locally to the headquarters at Sinks Pit, Kesgrave.
Guy’s son and Group Managing Director Jake Nicholls is eager to maintain the group’s momentum to become the leading brand across construction, demolition and agriculture, recognised for quality, supporting its people and local communities and as the supplier of choice.
“My ambitions for this business are to keep evolving,” Jake said. “Plant hire is still the mothership, but our fleet is large and consists of thousands of plant, lorries and commercial vehicles. There is scope to cross-sell across the different areas of our business and there are ways to keep growing while remaining here, in the heart of Suffolk.
“I’m third generation so all the pressure is on me. They say less than 10% of third generation businesses survive, but for me, this is just another driver.”
Tru7 Group is dedicated to maximising your plant hire experience, while also focusing on sustainability. That’s why through Tru Plant, it continuously invests in state-of-theart machinery, helping its clients to be more ecological, cost effective and time efficient without compromising on performance.
In recent years, Tru Plant has been bolstering its hire fleet with specialist offerings, including Volvo’s EWR130Es, EWR170Es, ECR355Es and EC550ELs.
Its unbeatably compact form makes this versatile machine perfect for working in tight spaces, with the ability to quickly manoeuvre through infrastructure projects and urban spaces, while boasting a light enough footprint for landscaping.
Its Steelwrist Tiltrotator allows operators to maximise productivity by rotating 360° and tilting up to 45° in each direction, giving Tru Plant’s clients industry leading precision and controllability.
With one of the shortest tail swings on the market, powerful engine, intelligent technology, as well as height and slew restrictors, Tru Plant’s EWR170Es are a favourite among our clients looking to operate with efficiency and control.
Both models boast two-piece boom configurations, increasing versatility and performance when lifting close to the machine.
A new addition to Tru Plant’s everexpanding fleet, our all new 40-tonne Volvo ECR355ELs offer both mono and twopiece boom configurations with blades. Its zero tail swing dimensions allow it to work in confined areas with more than impressive lifting capabilities, making it ideal for pipelaying, trench-box installation and utility works. Rely on top performance from Tru Plant’s ECR355Es, featuring a powerful Volvo D8 engine for fast and efficient operation, with the option to boost fuel efficiency by up to 10% with ECO mode.
Tru Plant’s EC550ELs provide the levels of durability and performance more commonly expected from a 60-tonne machine, making them the perfect choice for heavy-duty digging, mass excavation and demanding demolition projects.
Prioritising operator comfort while remaining efficient and complemented by new generation electro-hydraulics, a 20% increase in productivity and 25% improvement in fuel efficiency – it is obvious why the Volvo EC550EL is considered a flagship in Tru Plant’s fleet of excavators.
Tru Plant’s expansive offering allows its clients to benefit from the latest high specification machinery available on the market. Providing holistic plant hire solutions across construction, demolition and agriculture, self-drive or operated.
Warwick Ward (machinery) Ltd has a long history of selling earthmoving machinery to the construction industry. Over the years, we’ve earned a reputation for providing reliable equipment that our customers can depend on. As the demand for flexible machinery solutions grew, we saw an opportunity to expand our services. This led us to branch out into plant hire, offering the same high standards of quality and service that our customers had come to expect from our sales department.
The plant hire side of Warwick Ward has developed naturally over many years, evolving to meet the needs of our customers. The main idea behind our plant hire service is to provide strong support to our clients, especially when they need a temporary replacement for machines that are out of action due to repairs or maintenance. This ensures that their work can continue smoothly, even when their own equipment is unavailable.
The majority of our fleet comprises CASE construction wheel loaders, which are renowned for their exceptional performance, reliability and versatility on job sites. These machines are engineered to handle a wide range of tasks, from heavy material handling to precision work in tight spaces.
CASE loaders are equipped with powerful engines that deliver high torque and fuel efficiency, making them ideal for demanding construction environments. The advanced hydraulics ensure smooth and responsive operation, while the comfortable cab design enhances operator productivity by reducing fatigue during long shifts. Additionally, CASE wheel loaders are known for their durability, with robust frames and components that stand up to the toughest conditions, offering long-term value and reduced maintenance costs.
Another area of our plant hire business that has been steadily growing year after year is our recycling equipment sector. We’ve seen a rising demand in this field
and to meet it we offer a comprehensive range of solutions. This includes waste shredders, trommel screens and material and scrap handlers, all of which are available through our trusted Terex Ecotec range. These machines are designed to handle the toughest recycling tasks, ensuring efficient processing and handling of materials, whether it’s reducing waste volume or sorting through recyclable materials.
In addition to our recycling equipment, we also provide a full lineup of crushing and screening equipment. This area of our plant hire service has become increasingly popular. Our crushing and screening offerings come from the Keestrack product range, known for their durability, efficiency, and precision. Whether you need to crush large rocks or screen various types of materials, our Keestrack crushers and screens are up to the task, providing reliable performance fuel efficiency.
With these additions to our plant hire portfolio, we’re able to offer complete solutions that cater to the diverse needs of our clients, whether they’re working in recycling, construction or other industries that require heavy-duty processing equipment. Our goal is to provide the
tools that help our customers get the job done efficiently and effectively, no matter the challenge.
Ashley Ward, Executive Chairman of Warwick Ward said: “Our aim isn’t to compete with our customers in the retail market; instead, it’s to support and collaborate with them. We focus on strengthening partnerships and working together to achieve shared success.
“This commitment to building strong relationships is evident in the loyalty of our clients, many of whom have been with us for years. Their continued trust and satisfaction are the best proof that we’re doing a great job. The emphasis as always at Warwick Ward is offering complementary products and services, the plant hire side of our business is no different.
“Right now, we’re planning to enhance our plant hire offerings by including some of our other product ranges. This will soon feature Faresin telehandlers, Ausa forklift trucks and a selection of small to medium-sized dump trucks. These additions are part of our ongoing commitment to providing our customers with a broader array of equipment to meet their diverse needs.”
At Warwick Ward, we know our success depends on our clients’ success. That’s why we focus on building lasting partnerships. We’re not just here to supply machinery; we’re here to be a trusted partner in your journey.
Tru7 Group has invested in a fleet of 20 new JCB 140X tracked excavators – much to the delight of the company’s operators.
The major Ipswich-based construction group has bought the JCB X Series models to operate on general construction and housebuilding sites as well as working on high-profile energy contracts across the UK.
Supplied by dealer Watling JCB, they join existing JCB Loadall telescopic handlers and backhoe loaders in the Tru7 Group fleet.
Tru7 Group CEO and owner, Guy Nicholls said: “Our family has a long history of buying JCB machinery, especially its telescopic handlers. One of our previous businesses operated by far the largest fleet in Europe at the time.
“We kept hearing how good the JCB 140X model was and felt it was time we tried some. So we ordered 20 models to test out within our operations. The machines have proved to be very good, and the drivers love them. The modern
styling, excellent driver environment and tough build quality make them ideal for our work.
“For many years we have been fortunate to have Watling JCB as our dealer. It is without doubt an outstanding company from the top down – and the team really are a pleasure to deal with.”
A Suffolk-based family-run business, Tru7 Group has a rich history spanning over 60 years. Under the leadership of Guy Nicholls and now his son, Jake Nicholls, the company has continued to expand its services and capabilities. It now operates van, truck and plant sales and rental businesses alongside its demolition and remediation, earthworks, asbestos removal, concrete and aggregates divisions.
Across this range of services, Tru7 Group has built a high profile client list including Suffolk Highways, HS2, Morgan Sindall, Balfour Beatty, RG Carter, Barnes Construction and Suffolk County Council.
“It is without doubt an outstanding company from the top down – and the team really are a pleasure to deal with”
Prolec, a leader in innovative safety technology solutions, has proudly announced the grand opening of its new cutting-edge facility, the Prolec Technology Hub, in Southampton. This milestone represents a significant expansion for Prolec, underscoring its commitment to driving technological advancement in the world of on-site safety as well as offering a training and testing facility for its global distributor network, customers and other partners.
Established in 1982, Prolec, a member of the Kinshofer Group, is recognised not only as a leader in providing innovative safety solutions but also as a thought leader committed to advancing on-site safety today and creating a safer future through technology. Using virtual barriers, Prolec’s technology stops collisions with hazards such as overhead power cables, ground obstacles and people or objects getting too close, by limiting machine
movement making it easier for the operator to focus on the job at hand and giving those responsible for site safety the confidence they need.
The Prolec Technology Hub, designed to be a centre of excellence, features an advanced research and development lab, where the Prolec team of engineers can develop and test safety critical systems. A key element of the hub is the inclusion of a field and excavator, essential for enabling comprehensive testing and development with real hazards to give that real-life scenario.
Nigel Shaw, Prolec’s Managing Director, said: “Demand for our safety systems for the construction equipment industry continues to grow, the new Technology Hub enables us to walk outside the office, get to the field and test our software and hardware in real world with an array of deliberate physical hazards – overhead, at the sides and underground.”
Prolec recently launched an allin-one screen for operators of plant machinery cabins, encompassing safety, with proximity sensors and automatic stop features for unsafe height, slew and loads, and productivity for guidance so optimal digging accuracy can be achieved without wastage.
Nigel said: “We often hear construction staff asking machine operators, ‘Do you have your Prolec on?’ Our name has become part of everyday language, much like people say ‘Hoover’ instead of ‘vacuum cleaner.’
With over 16,000 excavators and other plant machines equipped with Prolec’s virtual barriers and the growing emphasis on on-site safety, we anticipate increasing demand for our products. We are continually innovating to provide solutions that make the work environment as safe and straightforward as possible for everyone involved.”
UK-based ECL Civil Engineering has deepened its relationship with MarubeniKomatsu through a new six-figure plant deal.
Steve Tysoe, Managing Director at ECL Civil Engineering Ltd and Brian Graham, Managing Director at Marubeni-Komatsu, have agreed to a 90-machine deal with a range of crawler excavators, including 40 Komatsu PC55s, three Komatsu PW148s, 24 Komatsu PC138s, 10 Komatsu PC210 excavators and two 19-tonne D61 class leading dozers.
Steve Tysoe said: “Our primary goal with this latest investment is to extend and replenish our fleet with the best equipment available in the market to ensure the safety and efficiency of our fleet operatives. Additionally, we aim to minimise CO2 emissions and continue to commit to greener construction practices.
“We have a longstanding relationship with the Marubeni-Komatsu team, built on their unwavering reliability and the quality of their products, making them the right supplier for our business.”
ECL continues to experience increased demand for its groundworks and civil services. This growth is particularly evident in its support for significant strategic developments with a vested interest in sustainable, low-carbon construction.
ECL’s new Komatsu machines are powerful and environmentally friendly and lead the industry in fuel efficiency. Access to Marubeni-Komatsu’s specialist technology division will ensure that carbon reduction opportunities are maximised.
Brian Graham said: “We are extremely excited to partner with ECL with this latest purchase in Komatsu cutting-edge technology. We will support ECL in
maximising the return on their investment through proactive machine and fleet support while delivering solutions to enhance the productivity of these machines. We see this as the next stage of a positive long-term relationship and we look forward to hearing the many success stories of the projects these machines will help deliver. ECL is enthusiastic about using Komatsu’s technical advances in low-carbon machinery to benefit its projects and achieve its carbon-zero ambition.”
Europe’s largest lifting equipment event opens at Newark showground on Wednesday 11 September and SANY UK
double folding jib and will travel with 13-t counterweight within UK STGO regulations.
proving very successful and this will be another fantastic platform to showcase the machine, highlighting key features and
entire operation at risk
A Rated Capacity Indicator (RCI) is a crucial tool in industries that involve lifting and heavy machinery operations, such as construction, manufacturing and logistics. There are several reasons why an RCI is essential.
At Xwatch we are often asked: “Why do we need an RCI?” Jemma DycerHopkins, Xwatch Sales and Operations Manager explains: “Excavators, though primarily designed for digging, are very versatile machines frequently used for lifting operations. When an excavator is utilised this way, it effectively becomes a crane and is subject to the LOLER (Lifting Operations and Lifting Equipment Regulations). This is why having an RCI is crucial – it ensures compliance with these regulations and enhances safety during lifting operations.”
Jemma added: “For example, the RCI Lite, a key product in Xwatch’s safety suite, is designed to offer clear, simple and reliable performance while meeting all current industry standards. It’s versatile enough to be configured for any hydraulic excavator, providing essential overload protection and optional motion control to ensure safe operation
without compromising the machine’s full capacity. RCI Lite is the cost-effective choice for general civil lifting tasks.”
Xwatch RCIs provide real-time monitoring of load weight, boom length, radius and other critical parameters. This helps ensure that lifting operations remain within safe limits, preventing overloading and potential accidents. The system offers both visual and auditory alerts if the equipment approaches or exceeds the maximum rated capacity, allowing operators to take immediate corrective action.
The RCI from Xwatch features an intuitive and easy-to-use interface, making it simple for operators to monitor all the necessary data. This reduces the chances of human error and ensures that
are followed effectively. Xwatch Safety Solutions’ RCI systems can be customised to fit the specific needs of different types of machinery and operations. This flexibility makes it a versatile choice for various construction and industrial environments.
Xwatch’s RCI can be integrated with
provided by the company, such as height and slew restrictors, to create a comprehensive safety system. This integration enhances overall site safety and ensures all aspects of the lifting operation are monitored. Xwatch RCIs are designed to comply with industry safety standards and regulations, making it easier for companies to meet their legal obligations and avoid penalties.
Their products are also approved by various regulatory bodies, ensuring reliability and trustworthiness.
The XW RCI system, specifically the XW2 and XW5 models, has advanced features that can slow down the machine gradually and bring it to a stop before it reaches its operational limits. This prevents abrupt stops or potential damage.
In contrast, the RCI Lite model does not have this capability. It only has an ON/OFF function and lacks the proportional valve control needed for gradual slowing. Additionally, the RCI Lite cannot manage operational limits in the same way that the XW2 and XW5 RCI models can.
The RCI systems automatically log data related to lifting operations, which can be used for reporting, analysis and
audits. This feature is particularly useful for post-operation reviews and continuous improvement of safety practices. Xwatch Safety Solutions’ RCIs are designed to improve safety and operational efficiency in lifting operations. They offer real-time monitoring, customisable settings, and integration with other safety systems, making them a valuable tool for ensuring compliance and protecting workers and equipment. If safety and efficiency are priorities on your site, an RCI from Xwatch is definitely worth considering.
An Xwatch RCI is essential to safe, efficient, and compliant lifting operations. Whether you aim to protect your workforce, ensure compliance with industry standards, or prevent costly equipment damage, an RCI plays a vital role in maintaining safety and operational integrity on any site where lifting operations are performed.
CASE Construction Equipment is building upon the success of its motor grader heritage with the introduction of the new D-series: 836D and 856D. Boasting many of the operator comfort and productivity benefits launched with the previous C-Series machines, the D-Series models take the operator’s cabin to a new level of comfort, with precision, intuitive moldboard control, powerful Dual Power engines and a comprehensive range of after-sales solutions.
The D-Series graders feature a low-profile ROPS/FOPS cab, delivering unbeaten visibility and a reduced overall height facilitates easier transportation between job sites. Full width tinted glazing and a commanding view to the front and at the moldboard ensure optimum control, whatever the task.
There is a new touchscreen display for all machine and maintenance info and to provide a monitor for the rearview camera. This customisable screen is located on top of a redesigned front console. A second console to the righthand side of the cab incorporates the ignition key, the new electronic hand throttle, a cup holder and USB charging ports. On the left-hand side of the cab there is a spacious storage compartment,
which features a rubber strap and net.
The new grader comes in both electro-hydraulic joystick controls and mechanical levers, which means the driver has the ability to choose depending on their preference. Both machines come as standard with a heated and air-suspended seat. The electro-hydraulic system uses highly precise, three-axis joysticks, which are built into multi-adjustable armrests for maximum operating comfort. The joysticks are equipped with multiple roller switches and buttons, to control various machine functions.
These joysticks also provide accurate control of all moldboard operation, comfort steering options and TwinLift control, which allows the operator to control both lift cylinders from a single joystick.
Powered by a Stage V six-cylinder FPT diesel engine, with Hi-eSCR2 emissions technology, the CASE D-Series graders deliver a dual power curve, with automatic switching as higher transmission ratios are reached. This ensures maximum power is available as travel speed increase, boosting productivity.
Compliant with HVO and other XTL synthetic fuels, the 6.7-litre diesel engine features a maintenance-free Diesel
Oxidation Catalyst (DOC) with Selective Catalytic Reduction (SCRoF) exhaust after-treatment system. An Ergopower transmission automatically delivers smooth shifting between gears, with allwheel drive models having a creep mode for compaction work, reducing the need for additional machines on site. Both the two and four-wheel drive models are available with optional 24-inch tyres, ideal for uneven ground conditions.
D-Series graders can be tailored to the application with a choice of different moldboard widths, moldboard extensions, an overload clutch, a five-tooth ripper, additional counterweights and LED working lights. An A-shaped frame and central saddle provide maximum stability and versatility for the cutting edge.
The CASE moldboard design, on a roller-mounted encapsulated slewing ring, avoids any backlash and reduces wear, while supporting high mechanical torque for maximum control. With fewer greasing points, maintenance is reduced, boosting uptime and ensuring increased profitability for the customer. The D-Series graders come ready to easily install a range of the most popular plug-and-play machine control systems to further boost productivity.
A range of connected and non-connected after-sales solutions ensures that your machine is working without unexpected maintenance costs and downtime.
Graders come with a CASE SiteWatch subscription – a tracking and fleet management tool, allowing customers to remotely monitor their equipment in use. Fleet managers can use geofencing to increase security and monitor unauthorised equipment use. With CASE SiteConnect this telematic transfer is enhanced by directly alerting dealers about machine performance and operating conditions, allowing proactive maintenance, quicker repairs as well as preventive service.
New D-series Graders benefit from CASE Care, a planned maintenance programme with genuine parts and lubricants that allows for certainty on the total cost of maintenance without any hidden surprises.
In addition, there are a range of services such as CASE Protect extended warranty and CASE Fluid Analysis to protect CASE construction equipment and ensure uptime with extended warranty and other preventive programmes aimed at avoiding unexpected operating costs and optimising profitability.
JLG Industries, an Oshkosh Corporation company and leading manufacturer of mobile elevating work platforms and telehandlers, has completed the acquisition of Spanish manufacturer AUSA, adding the market-leading brand’s compact all-terrain transportation and material handling machines to the company’s range.
Following the acquisition of Hinowa in 2023, the AUSA brand further supports Oshkosh’s accelerated growth strategy and strengthens the JLG equipment portfolio.
Established in 1956, AUSA specialises in designing, manufacturing and selling wheeled dumpers, rough terrain forklifts and compact telehandlers for the residential, civil and road construction industry and the transportation and handling of industrial and agricultural materials. The acquisition included AUSA’s 23,000 m 2 manufacturing facility in Barcelona, approximately 350 team members and access to 200 dealers worldwide.
Mahesh Narang, President of JLG, said: “AUSA’s culture of innovation and
quality matches the same standards we hold and our shared core values around safety, productivity and sustainability position us well for the future. Together we will work diligently, as both companies always have, to meet the needs of our customers.”
JLG and AUSA have collaborated since 2020, bringing the SkyTrak 3013 to market together. With the acquisition, AUSA products will enhance JLG’s line of telehandlers and complement Hinowa’s line of tracked dumpers and forklifts. Both acquisitions help accelerate JLG’s growth into the speciality equipment, agriculture and landscaping markets while providing its construction and materials handling customers with an even broader array of products – all backed by JLG’s robust training, support and service infrastructure.
“Our combined capabilities, market leadership positions and complementary product offerings provide a more comprehensive solution to address market needs, expand our operational footprint and unlock growth opportunities worldwide. The acquisitions of AUSA and Hinowa help JLG create an organisation that can better serve customers globally,” finishes Narang.
“AUSA’s culture of innovation and quality matches the same standards we hold and our shared core values around safety, productivity and sustainability”
Hitachi Construction Machinery UK (HCMUK) has established itself as a key specifier of Xwatch Safety Solutions, playing a significant role in the widespread adoption of advanced safety systems across the construction industry. This partnership highlights the growing emphasis on integrating innovative safety technologies in response to the increasing complexity of construction projects.
Stephen Creaser, Hitachi Director of Product Support, says, “Hitachi Construction Machinery UK (HCMUK) is proud to be leading the way with Xwatch by installing the market-leading XW4 and XW5 systems at our Hitachi Connected Technology (HCT) facility in Newcastle.
The market demand for Xwatch Safety Solutions is rapidly growing as key clients and blue chip construction organisations are starting to mandate Xwatch as their preferred height, slew and RCI control solution on hydraulic excavators working on their projects. HCT is committed to enhancing the safety of our equipment and we have seen this increase in demand first-hand with over 80 systems installed and calibrated at Newcastle in the last three months.
HCMUK are also leading the way with real time telematics by providing
remote real time monitoring of the Xwatch system, via our CTFleet Link® mixed fleet management solution. CTFleet Link enables live direct access to key Xwatch safety metrics alongside the machine’s operation data while the machine is in operation.”
Since partnering with Xwatch in 2021, HCMUK has installed more than 350 Xwatch Safety Systems, including the XW4 and XW5 units, designed to meet and exceed client expectations for hydraulic excavator safety.
Jemma Dycer Hopkins, Xwatch Sales and Operations Manager, highlighted the significance of this partnership in the company’s growth: “We are approaching the milestone of 5,000 Xwatch systems installed since our start-up in 2019, a testament to the industry’s trust in our solutions. The support of major OEMs like Hitachi has been crucial in helping us reach this point. Their confidence in Xwatch has enabled us to expand rapidly and set new standards for safety across construction sites. HCMUK’s proactive approach in specifying and integrating our systems demonstrates a shared commitment to raising safety standards industry-wide.”
As the rate of global resource extraction continues to accelerate, finite natural materials continue to deplete and barriers to gain approval for new mineral extraction sites mount, CDE is encouraging materials producers to reappraise their waste streams to get more value from their operations.
Sand and aggregates are among the most important resources for everyday life. They’re needed for the construction of the roads and pathways we travel on, the buildings we live and work in, the microchips powering our technology and so much more. They are indispensable resources for modern living, yet they are finite and require careful resource management.
In 2018 mineral wastes and soils accounted for 63% of total waste generation in the UK, meanwhile the latest Global Resources Outlook report published by the United Nations Environment Programme suggests resource extraction could rise by 60% to 160 billion tonnes over the next three decades.
William Melanophy, Head of Business Development for the UK and Ireland
“Too often these masses are categorised as waste or low value material when in reality they possess significant potential to quarry operators”
Uncovering buried profits
Mining and quarrying operations generate significant volumes of waste byproduct as part of their process but within these waste streams there is opportunity to repurpose the overburden, scalpings, and crushed rock fines that come as part of the mining and quarrying process.
Where overburden concerns the clay-bound top layers of soil and subsoil above bedrock that are removed as quarries and mines expand, scalpings are the contaminated stones removed during primary screening in dry processing plants, and crushed rock fines are a byproduct of the dry rock crushing process, which typically produces a low-value product with very high fines content.
Old materials, new opportunities
The traditional approach to managing waste by-product such as overburden, scalpings, and crushed rock fines is to stockpile them on site, which is generally symptomatic of the limitations of the technology employed on site at the time.
CDE’s patented washing and processing allows quarry operators to
transform unwanted waste materials that may have been sent to landfill into highvalue sand and aggregate products that can be sold straight off the belt.
Longcliffe Quarries, based in Derbyshire, had historically discarded its clay-bound limestone scalpings, but feasibility studies and material testing found a market for products recovered from this waste stream. Powered by a 220 tonnes per hour (tph) state-of-theart CDE wet processing plant, up to six different products are being extracted from clay-contaminated material, which is creating new, high-value revenue streams and helping reduce net emissions on site.
Conventional dry processing equipment has its drawbacks with quarry waste by-products, which typically have high clay and fines content, but advances in washing technology is shown to overcome these challenges to produce high-quality sand and aggregates and maximise product yield from quarry waste.
Recently, CDE designed and engineered such a solution to support
Peter Fitzpatrick Ltd, a quarrying and contracting company based in Northern Ireland, to reprocess excess crushed rock fines and blinding material at its quarry in Newry. Processing up to 130 tph of quarry waste overburden per hour, the CDE wash plant is enabling the firm to produce five saleable outputs, including concrete sand, 6 mm grit, 10 mm, 20 mm, and +20 mm aggregates.
Commenting on the value of repurposing waste streams, CDE’s William Melanophy, Head of Business Development for the UK and Ireland, says: “Too often these masses are categorised as waste or low value material when in reality they possess significant potential to quarry operators. When processed with the right technology, most of these seemingly low-quality by-products can be marketed quite profitably.
“It is crucial we start to maximise the available reserves and tackle more complex material. CDE is committed to providing solutions which address the industry’s waste burden in a bid to meet the everyday needs of our customers.”
Construction software platform Compliance Chain and ethical consultancy Align Ltd, have partnered to improve ethical labour practices by offering on site “lived experience” modern slavery assessments.
Align Ltd specialises in ensuring ethical practices and a transparent supply chain for social impact-driven businesses, not-for-profit organisations and public entities; while Compliance Chain supports public and private sector clients to track, monitor and deliver effective social value plans.
Lived experience assessments, provided by Align, are conducted by lived experience consultants who have been exploited previously. Lived experience consultants are vital to the assessments, providing an important perspective and experience in what could be a challenging and delicate situation for workers.
The partnership offers a unique take on modern slavery assessments, by harnessing digital tools that enhance transparency and active prevention within
construction projects. Clients who use this service through the Compliance Chain platform will also gain access to the Just Good Work app, ensuring organisations have an ongoing picture of what is happening on site.
Just Good Work is an interactive mobile platform, powered by FiftyEight, a certified B-Corp that helps individuals make good choices for better work abroad.
The platform is free for workers and enables them to understand their rights and responsibilities throughout the process alongside good advice on safe recruitment, migration and employment in their new workplace.
As modern slavery remains a serious global issue infiltrating the construction industry, Compliance Chain, Align and FiftyEight offer a unique partnership in combating unethical practices and exploitation.
Whilst Align conducts lived experience, honest assessments of the activities on site, Compliance Chain can provide practical advice to companies
on the steps they should take to protect workers and a digital tool that allows them to track their social value delivery.
Before, during and after the assessment has concluded, companies can access the Just Good Work app, which offers workers protection and advice while providing companies with live worker feedback, giving real-time insights across their supply chains that fill in the gaps between audits.
This offering is exclusive to clients who use Compliance Chain to track their social value delivery and can be requested through the platform.
Adam Cochrane, Head of Operations at Compliance Chain said: “We are honoured to be working in partnership with Align and FiftyEight to deliver practical and meaningful modern slavery assessments to our clients.
“Our Modern Slavery assessments protect workers at its core. Lived experience assessors and ongoing monitoring through digital solutions ensure that companies can access practical
advice and detailed steps they should implement to protect workers.
“Companies that currently track and measure their social value using Compliance Chain can easily request a modern slavery assessment through the platform, with the added reassurance that they will be able to access real-time insights between audits.”
Phillip Clayton, Chief Executive Officer at Align Ltd added: “We are proud to partner with Compliance Chain and FiftyEight to offer this innovative approach to the construction sector.
We believe that any approach that does not include those with lived experience will lack robust outcomes. The
most effective prevention methods come from the meaningful inclusion of those with lived experience. They are uniquely placed to assess risks on site; having experienced exploitation, they know what the signs and symptoms are and can bring unique insight to prevention and risk mitigation.
With companies looking to go “beyond audit” this method alloys prevention technology and lived experience insight in an end-to-end site risk management process delivering tangible results and evaluation side by side. We hope this will set a new standard in the construction space.”
Quintin Lake, Executive Director
at FiftyEight said: “Our aim with Just Good Work is to get it into the hands of as many workers who can benefit from it as possible and this partnership helps accelerate that for the construction sector.
As workers better understand what is okay and what isn’t through information in their own language, real-time insights about their experience can help shine a light on both good practices and where improvements are needed to proactively prevent modern slavery for workers and companies alike.”
Northamptonshire-based earthworks contractor James King (Plant) has added two HD Hyundai HX220A L and two HX140A L crawler excavators to its growing fleet of equipment. The company, which is approaching 50 years in business, operates 53 major pieces of plant, including 10 HD Hyundai excavators. In the past this has extended to 42 and 50-tonne machines, to meet the needs of a diverse range of customers.
“When we started purchasing new machines we went with Hyundai. We like Tony Wilcox at Willowbrook Plant and the back-up service that they provide, which is very good,” said Plant Manager Gary Follen.
“The Hyundai reliability is superb. We don’t have to put many spanners on them. Generally, we don’t get any problems once they are up and running.”
All of the HD Hyundai machines have been delivered to local dealer Willowbrook Plant’s in-house specification, with standard hydraulic breaker lines, HD Hyundai’s All Around Vision Monitor (AAVM) 360 ° camera system and a full boxing ring of safety handrails on the upper structure.
The machines also benefit from an impressive standard trim, both under
the engine canopy and within the operator’s cab.
“We have also added GPS preparation for our Trimble machine control system on the 22-tonne machines,” said Director Patrick King.
A third-generation family business, James King (Plant) was founded in 1975 in Blisworth, Northamptonshire, by Patrick’s father James. The company has become well known and respected as a specialist earthmoving sub-contractor, working with many of the UK’s leading house builders and commercial property developers, throughout the Northamptonshire area and further afield.
“We do a lot of moving muck for the housebuilders,” said Mr King. “We don’t seek nationwide work, but we will go anywhere to provide a service to our customers. Mostly we are within 50-60 miles of our base location.”
The company dedicates one operator to each machine, with many of its staff having been with the firm for multiple years. The business has had a positive start to 2024 and is looking for continued growth going forwards, as it looks to meet the changing needs of its customer base.
“We’ve been busy so far this year, but it’s been difficult, due to the weather
conditions. We’re looking for slow and steady growth,” said Mr King.
“We’ve got a very loyal workforce and we treat them well. They really like the Hyundai excavators.”
HD Hyundai’s HX220A L is a 22-tonne crawler machine powered by a 129-kW version of the Stage V compliant Cummins B6.7 diesel engine. Equipped with Electronic Pump Flow Control (EPFC) hydraulics, the machine boasts a maximum digging depth of up to 7,720 mm and a bucket breakout force of 152-165kN.
The smaller HX140A L is a conventional tailswing 14.4-tonne tracked machine. Powered by a 100-kW Stage V Cummins F3.8 diesel, the machine is built for the toughest conditions, with robust upper and lower frames, highgrade hoses, side protectors and a durable cooling module.
Willowbrook Plant was founded in 2008, delivering a range of construction equipment to customers across central England. The company has been the HD Hyundai dealer for Northamptonshire, Leicestershire and Cambridgeshire since July 2011 and added Lincolnshire, Derbyshire and Nottinghamshire to its sales area in 2020.
The Construction Equipment Association (CEA) is delighted to announce that CEA Market Information manager, Paul Lyons is embarking on an exciting new chapter in his career as an independent consultant. Paul has been instrumental in establishing and developing our market insights service and we are thrilled that he will continue to focus on this crucial area as part of his new role.
Paul’s work in providing market insights has been invaluable to our members, offering regular updates on the UK market for construction equipment. His detailed reporting includes monthly sales (from Systematics International), quarterly imports and exports, as well as insights into end-use markets across the UK. Additionally, Paul monitors overseas equipment markets through collaborations with industry partners such as Off-Highway Research.
Viki Bell, CEA’s Director of Operations, commented on Paul’s transition: “Paul has been invaluable in
providing market insights since joining ASL, our admin partners, in 2016. His deep understanding of the industry and his ability to translate complex data into actionable insights have been crucial for our members. We are looking forward to continuing working with Paul as an independent consultant, leveraging his experience within the industry to further enhance our market insights service.”
Paul Lyons also shared his thoughts on this new chapter: “I am excited to be focusing on the market insights service for the CEA as my key role in future. I have enjoyed supporting the association in other areas, but I am pleased to be focusing now on my key area of expertise. With the construction equipment sector undergoing significant changes, particularly in the areas of decarbonisation and technological advancement, I look forward to applying my experience to help members navigate these developments. This new role allows me to focus even more on delivering
valuable insights that support the strategic decisions of our members. Additionally, I am also looking forward to exploring new opportunities outside of the CEA, broadening my reach and impact within the industry.”
One of the key areas Paul will be focusing on is the progressive decarbonisation of equipment in the UK market – a significant development in our sector. This transition, starting with the electrification of compact and medium-sized machines via battery power and extending to future technologies like hydrogen power, is crucial for the industry’s contribution to net-zero targets. Paul will be liaising with Systematics International, who run the construction equipment data exchange and are collecting the data relevant to these changes within the industry.
As Paul transitions into his new role, his responsibilities for the CESAR Scheme will be handed over to Amy Gavin, the CEA’s executive assistant. Viki Bell will oversee new member recruitment, while ongoing support will be managed by Beth Abbott, CEA’s Head of Marketing and Communications. Together, they will ensure that new members are fully integrated and supported in their engagement with the CEA.
The CEA looks forward to continuing its work with Paul in this new capacity and is excited about the enhanced focus on market insights that his independent consultant role will bring.