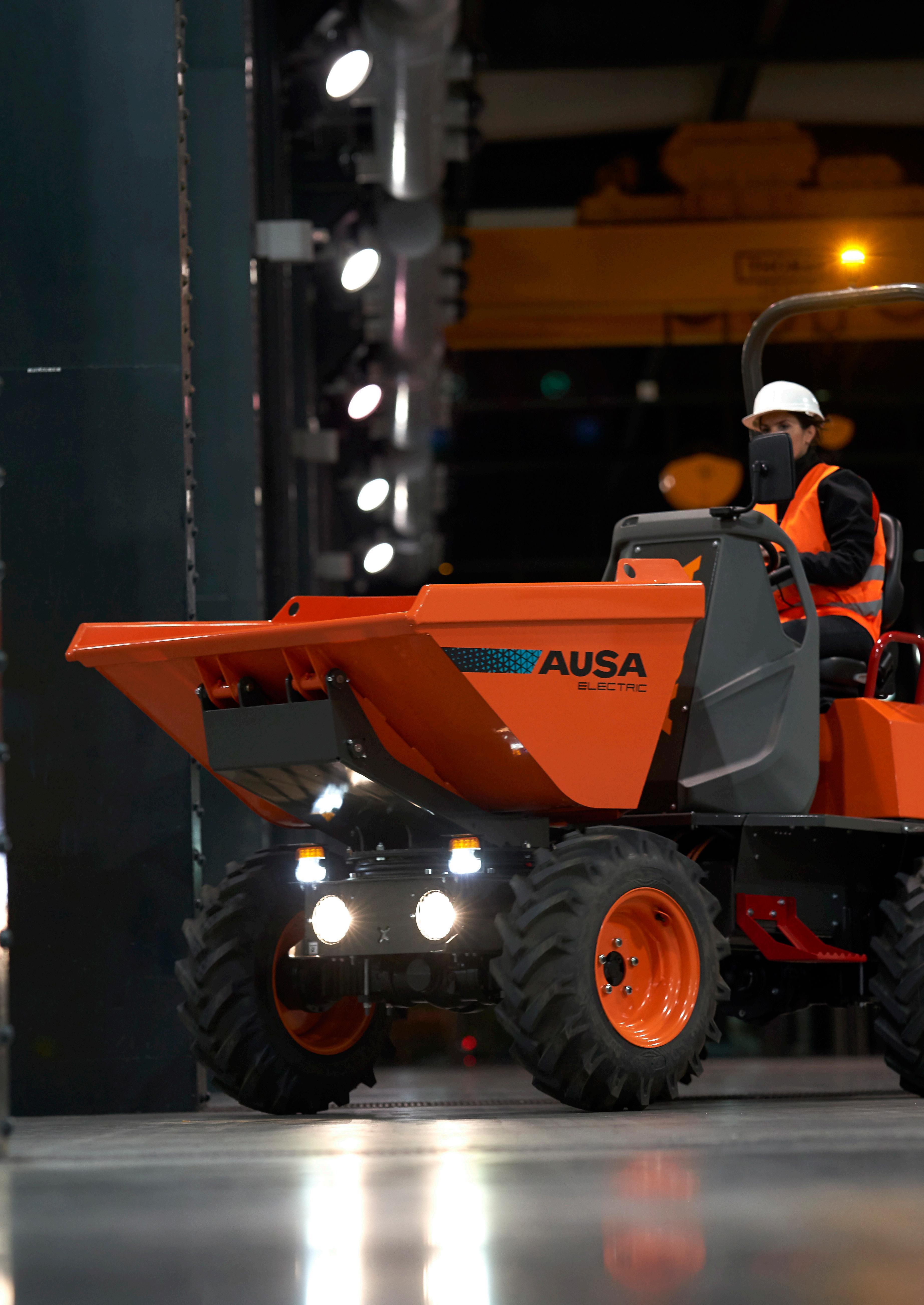
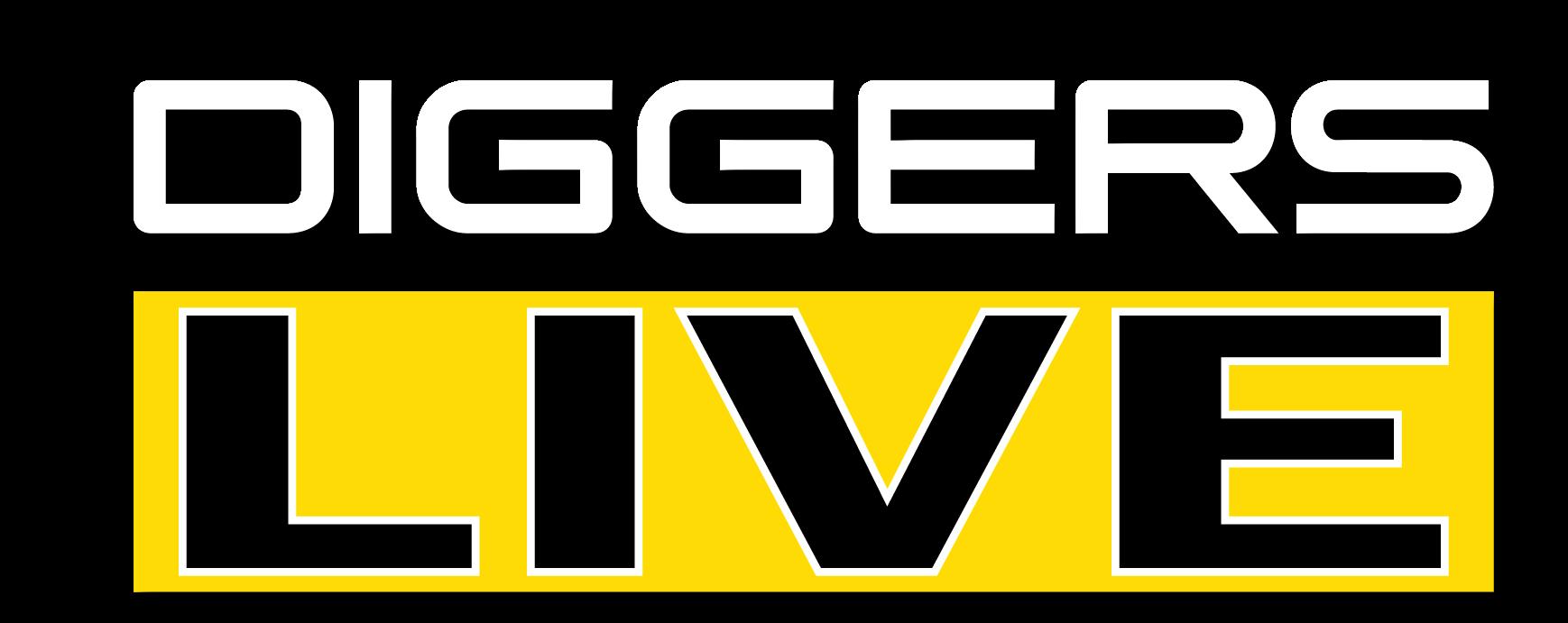

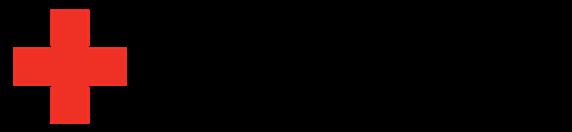
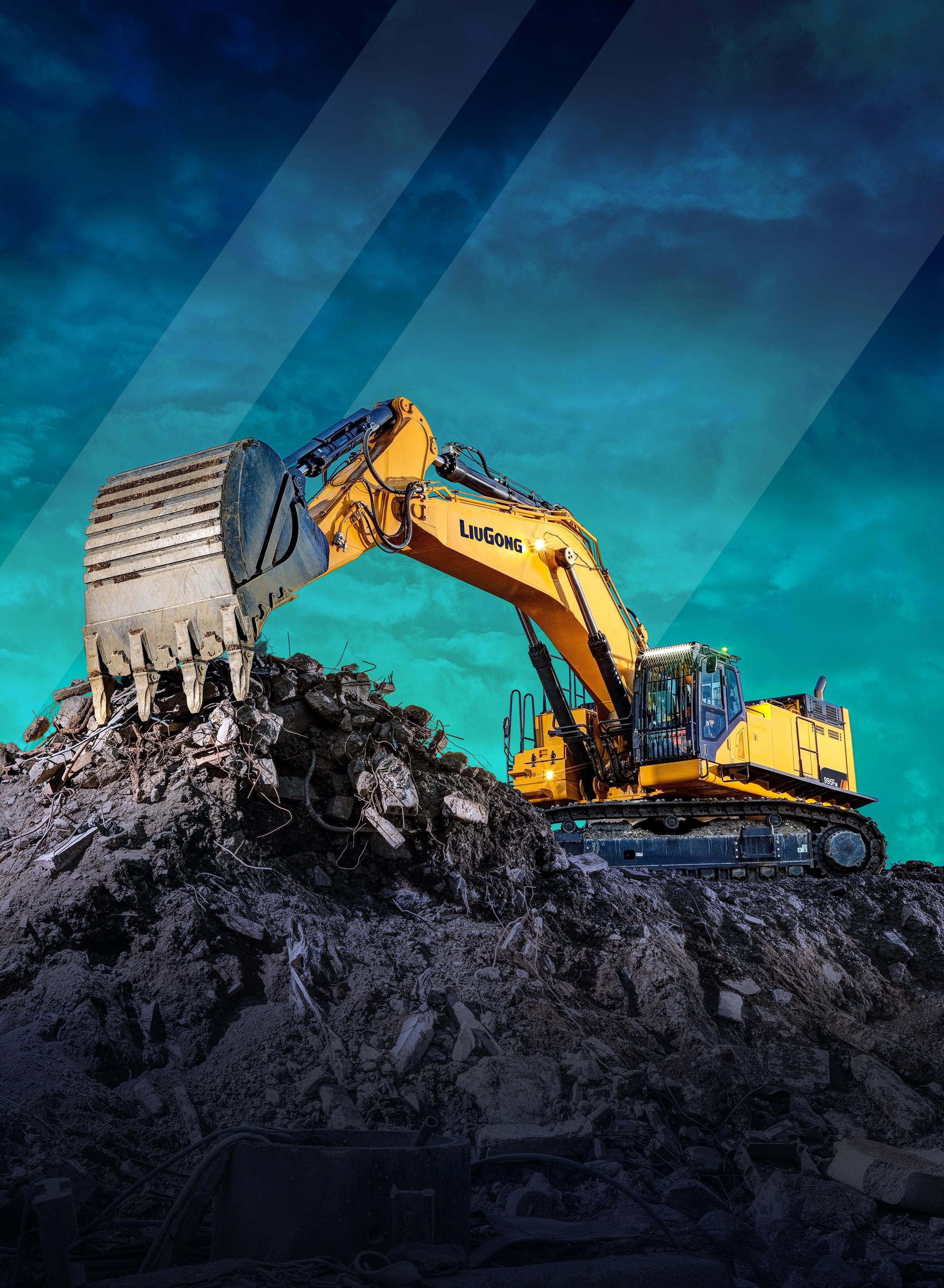

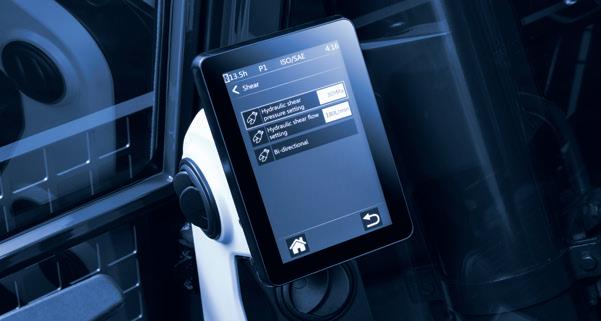
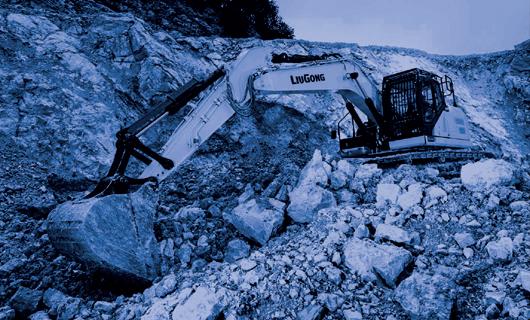
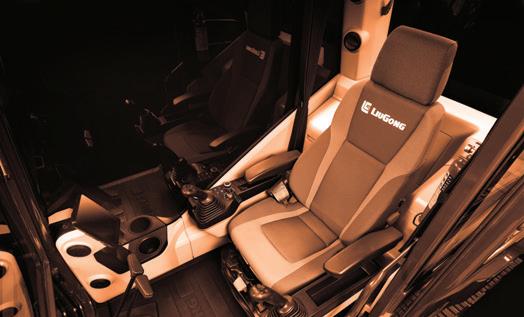
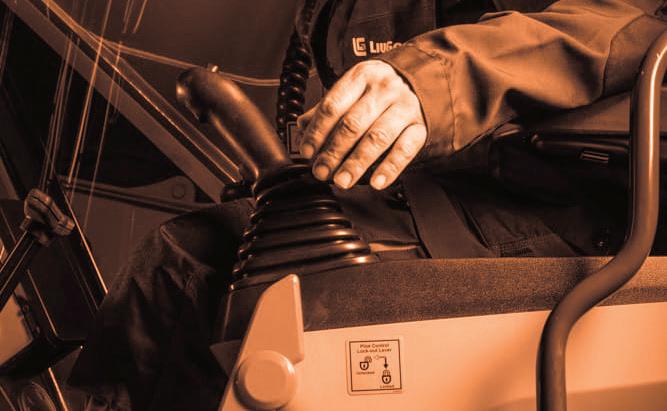
Having spent the last week of January in Las Vegas for the 49th World of Concrete, I had a brief interlude in the UK, and have now just returned once again from North America following the National Demolition Association’s four-day annual conference, Demolition Phoenix.
While networking, education, industry awards and social activities were an important part of the conference, the key occasion for me was the Live DEMOlition Event™, a showcase of excavator mastery paired with a variety of job improving attachments.
It’s far too late in the day to get any of this into Diggers LIVE #16, so this is where I put in a rare mention of one of our other home publications Demolition Hub. All will be in there in about a month – let me know if you want a copy.
With these shows as fresh as today’s jet lag, you’d think that I would’ve had enough of transatlantic travels and big machinery… Well, I haven’t. In fact our third US trip is very much on the horizon and today I am going through the plethora of invitations I have had from a variety of manufacturers who wanted to showcase launches, demonstrations and everything construction machinery to our readers, all to be presented at the triennial CONEXPOCON/AGG event in Las Vegas.
We will be there as an official publication to the event and bring you all the action in May’s issue as well as on our socials and YouTube channel.
Domestically, I attended Executive Hire Show in Coventry last month and we have a post-show rundown in this issue.
Our EQUIPMENT ENGAGEMENT feature is with Roy Haaker, Sales Director at Yanmar Compact Equipment and the BUSINESS INSIDER interview is with Andrew Scheer, Marketing Director of Pathfindr, both compelling Q&As, I am sure you will agree.
It’s busy couple of months ahead for us and indeed the industry, so I’m looking forward to spending some of it with you.
If you want to get involved – ben@globalnews.media.
Ben Chambers ben@chambers.media
toby@chambers.media
DESIGNERS
Nicki Chambers nic@chambers.media
Joe Bers joe@globalnews.media
Alex Jarrett
GENERAL ENQUIRIES info@chambers.media
01903 952 640
SALES
Luke Chaplin luke@globalnews.media
01903 952 643
Nathan Sandford nathan@globalnews.media
01903 952 642
PRODUCED & PUBLISHED BY Global News Media Ltd
Suite 5 & 6 Chapel House 1-6 Chapel Road, Worthing West Sussex BN11 1EX ben@chambers.media
01903 952 640
Diggers LIVE is published six times a year by Global News Media Ltd
Articles and information contained in this publication are the copyright of Global News Media Ltd and may not be reproduced in any form without the written permission of the publishers.
The publishers cannot accept responsibility for loss of, or damage to, uncommissioned photographs or manuscripts.
TradeGraft, by CEO, Chris Walker
Doosan Bobcat donates $1m in equipment for Turkey earthquake relief and recovery
XCMG launches emergency rescue after devastating earthquake in Turkey and Syria
JCB engine breakthrough proves hydrogen has wider appeal
CPA urges Treasury to work with the construction planthire sector
Bronze medal for TVH’s sustainability efforts
Rental industry appeal targets 10,000 generators for Ukraine
16
With Roy Haaker, Sales Director of Yanmar Compact Equipment EMEA
Asset finance – your next option for plant funding by Anton Nebbe of Close Brothers
MySMT now available nationwide
Electric dumpers product feature:
Andrew Scheer, Marketing Director of Pathfindr 81
• Florian Jud, Product Manager Dumper Line, Wacker Neuson
• Mark Royse, Head of Sales, Mecalac Construction Equipment UK
• Albert Hidalgo, R&D Director, AUSA
Executive Hire Show 2023 review featuring:
• Hydroscand
• JCB
• SANY debuts new electric mini at Exec Hire Show
• Pinnacle Platforms
• Nightsearcher
• Thwaites
CONEXPO 2023 preview featuring:
• Rokbak
• Goldhofer
• Leibherr
• Rammer
• Caterpillar
• Global Operator Challenge
Plantworx
CPA Conference
• Andrew Little, Sales Manager, Rototilt
• Karl Serneberg, VP OEM Sales and Marketing Steelwrist
• BMC Buckets – Scandinavian Grader S60 and S70
• MB Crusher BF60.1 provided by Chippindale Plant
• Robustrack Concrete Mixing Buckets
• MB BF60 Crushing Bucket provided by Worsley Plant
• Worsley Plant couples up with OilQuick
• Tesab 700ie hybrid electric jaw crusher
• Powerscreen Premiertrak 330 crusher provided by Blue Machinery
• Rubble Master RM120X provided by Red Knight 6 Ltd
• Keestrack B5e jaw crusher provided by Warwick Ward (machinery) Ltd
• Anaconda J12 tracked jaw crusher provided by Global Machinery Solutions
• Evoquip Cobra 230R
MDS expands with £1.1m JCB deal
Kier works with Lighthouse Club to provide mental health support for thousands of construction workers
Lighthouse Construction Industry Charity launches free E-learning programme
CRS NI Ltd and Agg Pro announce new UK Partnership
Dean Ashton joins the Agg Pro team as Environmental Product Line Manager
Bobcat one-stop shop provides increased financing flexibility
Finning takes leading role in diversity drive
Skipway upgrades to new Hyundai A-Series loaders
TVH expands range of spare parts for backhoe loaders
Goldhofer PST/SL-E 8 heavy duty module in action for Kiel Canal Waterways and Shipping Authority
CAM attachments known for high-quality products with pin-type forks no exception
Volvo Construction Equipment invests in battery pack production at excavator plant
Rokbak RA30s prove vital to largest pipe installation of its kind in Utah, America
FCC Environment gives green light for UK’s first Cat® Certified Machine Rebuild
Doosan Bobcat will provide equipment worth around $1m (£825m) for relief and recovery activities in the earthquakestricken areas of Turkey.
Construction equipment will be delivered promptly through Doosan Bobcat’s dealer network to be of practical help in lifesaving activities in affected areas and to help restore critical infrastructure such as collapsed buildings and roads. The equipment being supplied includes skid-steer loaders and excavators to remove and clean debris, and portable generators and lighting towers to be used at sites with power supply issues.
By providing equipment that can be used immediately for relief and recovery efforts, Doosan Bobcat hopes to help residents of the affected areas in Turkey to begin to recover their daily lives as soon as possible.
The donation will be financed in cooperation with Doosan Bobcat’s mother company, Doosan Group, which has supported previous major disasters with equipment and donations, such as hurricanes and earthquakes in the US, China, Haiti, Japan and Nepal over the past 20-plus years.
At 04:17 and 13:17 local time on 6 February, two 7.8-magnitude earthquakes with a focal depth of 20 km occurred in Turkey. This was the largest earthquake that Turkey has suffered since 1939, and many buildings were razed to the ground.
A mild tremor was felt in Ankara, where XCMG Turkey is based, about 700 km from the epicentre.
Upon learning of the disaster, XCMG quickly established an emergency rescue working group headed by Liu Jiansen, Vice President of XCMG and general manager of XCMG Import and Export, to keep close contact with the front of Turkey and command and dispatch onsite rescue in real time round-the-clock.
According to preliminary statistics, XCMG has about 600 excavators in Turkey. XCMG Turkey quickly launched the emergency response mechanism. While reporting the local situation to XCMG headquarters, it quickly coordinated and deployed three XCMG
excavators under construction near Gaziantep to the disaster area.
At 12:30 local time on 6 February, as a series of orders were issued quickly, all XCMG Turkey employees were mobilised. Based on the principle of proximity and speed, employees of XCMG Turkey carried out multi-party communication, rallied 12 sets of emergency equipment, such as excavators and loaders of various tonnages to be on standby, and actively responded to the call of the Chinese Embassy in Turkey and the General Chamber of Commerce of Chinese Enterprises in Turkey to coordinate resources to provide necessary assistance.
At 14:00 on the same day, XCMG completed the purchase of the first batch of relief supplies, exceeding 50,000 Lira (£2,200), including blankets, baby products and hygiene products, and immediately shipped them to the disaster area. Follow-up relief supplies are being raised urgently.
A spokesperson for XCMG Turkey said: “We have also joined the Turkish Construction Machinery Association. We will first register with the government and then send the machine to the area instructed by the government to carry out the rescue. We are still waiting for the government to give instructions.
“The Turkish government has requisitioned all available means of transport. The equipment from XCMG has arrived in the disaster area and is being put into rescue. We are also working with our agents to coordinate with our clients in other parts of Turkey to get involved quickly.
“We are members of the Chinese Enterprises Association, and its president has built a group, including the Blue Sky Rescue, where everyone actively offers advice and suggestions, such as organising air tickets, arranging accommodation and daily supplies, and reminding of Turkish cultural taboos, etc. In short, everyone in the group will help each other.”
It is understood that the supply of materials in Ankara is normal at present, while daily freight is basically suspended. The government is mobilising the whole country to deliver relief materials to the disaster-stricken areas and all sectors of society are actively donating materials to participate in blood donation.
At the same time, several Chinese rescue teams have gone to Turkey to participate in the earthquake rescue work. Through urgent coordination with local customers and distributors, many XCMG excavators, cranes, loaders and other equipment and operators have responded to the unified deployment of
relevant Turkish government agencies and rushed to the disaster area.
XCMG has dispatched nearly 100 people, including Chinese and foreign personnel of XCMG Turkey and employees of four dealers and secondary agents in Turkey to participate in the emergency rescue work.
JCB has made a major breakthrough in proving the wider appeal of hydrogen combustion technology by installing one of its super-efficient hydrogen engines into a 7.5 t Mercedes truck.
The retrofit was completed in just days and one of the truck’s first test drivers was JCB Chairman Anthony Bamford, who has been spearheading the company’s £100m hydrogen project.
The internal combustion engine used in the truck is the same as those already
powering JCB prototype construction and agricultural machines.
Lord Bamford said: “This is a giant leap forward for JCB and the rest of the world because we all have one goal: to reduce emissions. The hydrogen engine we have installed in the truck is the same as those already powering prototype JCB machines, so there is no reason we should not see hydrogen combustion engines in vehicles used on the roads in the future, including cars.”
JCB has already manufactured 50 hydrogen internal combustion engines in a project involving 150 engineers and they now power prototype JCB backhoe loader and loadall telescopic handler machines. The truck at the centre of the latest project was formerly diesel-powered and the switch to hydrogen is a breakthrough that underlines that this form of power could represent a much quicker way to reach global carbon dioxide emissions targets.
JCB was the developer of the world’s first working hydrogen-powered construction and agricultural machines. Last year JCB revealed another industry first – a mobile hydrogen refueller which provides a quick and straightforward way to refuel machines on site. JCB’s hydrogen internal combustion engines are manufactured at JCB Power Systems in Derbyshire.
Ahead of the spring budget in March, the Construction Plant-hire Association (CPA) has written to the chancellor, Jeremy Hunt, to urge the Treasury to work with the construction plant-hire sector to address concerns and focus on the issues that matter to the industry.
The letter to Mr Hunt states: “The CPA continues to have very real concerns over the challenges facing our members which have continued to mount over the course of the last year. The removal of the red diesel rebate in April last year coincided with the unprecedented rise in fuel prices due in part, to the war in Ukraine. While prices have stabilised to a degree, high levels of inflation and wider economic uncertainty have all contributed to a challenging year for our members.”
The CPA is the largest trade association for the plant-hire sector in the UK, representing over 1,800 companies who are responsible for 85% of the construction plant used in the UK.
The government has recently formed three new departments – the Department for Energy Security and Net Zero; the Department for Science, Innovation and Technology; and the Department for Business and Trade. CPA Chief Executive
Kevin Minton believes that the creation of these new government departments provides a fresh opportunity to focus on the issues that matter to the plant-hire industry.
Mr Minton said: “We welcome the creation of these three new government departments as they provide opportunities to focus on key issues for the planthire sector – namely competitiveness, decarbonisation and the ability to invest in new machinery and technology.
“With the economy narrowly avoiding recession according to the latest figures, it is vital the government works with our members and the wider construction industry to create the conditions needed to drive growth and secure our economic future. These new departments must be at the core of this process – action is needed now.”
In the letter to Mr Hunt, Kevin Minton urges the Treasury to consider five key areas ahead of the budget on 15 March:
• With the replacement of the Super Deduction Allowance (SDA) due to expire at the end of March, we urge the Treasury to introduce a replacement that includes the plant-
hire industry. Encouraging and incentivising businesses to invest will be key to avoiding a prolonged recession,
• A rebate for Hydrogenated Vegetable Oil (HVO) should be introduced for the construction sector, to help companies offset the price rises witnessed over the course of the last twelve months, while simultaneously incentivising companies to move away from fossil fuel powered construction plant,
• The Treasury should keep in place the 2022 cut in fuel duty and resist calls to raise it back to its previous level. Historically, fuel prices remain high, with inflation still set to remain high for the large part of 2023,
• Construction is a key driver of economic growth. In a challenging economic environment, where confidence remains fragile and business investment levels low, it is vital the government remains committed both to HS2, but also further planned infrastructure projects such as Hinkley Point C. Failure to do so will undermine confidence in the construction sector and place doubt on future government plans,
• The government should publish its response and act on the findings of the Chris Skidmore Net-Zero review as soon as possible. The review has clear recommendations and actions needed, for the UK to take advantage in building the green economy of the future. With industry already working towards a range of targets set by government, time is running out for further action.
Parts specialist TVH has been awarded the EcoVadis Bronze Medal in recognition of its sustainability efforts in 2022. It is the first time that TVH has been honoured by EcoVadis, one of the most important rating organisations for sustainability worldwide.
TVH was presented with the Bronze
Medal because it ranks in the top 20% of the best-rated companies in its industry, according to EcoVadis benchmarks. The parts specialist scores especially high in the field of ethics – the company secured a spot in the top 8%, thanks to its efforts in setting up compliance policies (e.g. fraud, conflict of interest, corruption).
New milestone for TVH
EcoVadis is the world’s largest and most trusted provider of business sustainability ratings, with a network of more than 100,000 companies rated. The organisation rates all member companies in multiple areas, including environment, labour and human rights, ethics and sustainable procurement.
Anton Theunynck, Head of Sustainability at TVH, says sustainability is of strategic importance for TVH: “A lot of people worked hard last year to achieve progress on multiple fronts. It is thanks to their efforts that we were able to achieve this medal. Surely, this recognition is a new milestone in our sustainability performance and we look forward to achieving even better results in the future.”
bitterly cold weather, but just imagine going through that with no power for heating. It doesn’t bear thinking about.
“Working with Rotary International, we’re appealing to colleagues across the UK and around the world to join us to help reach this ambitious target of 10,000 generators.”
As freezing winter temperatures grip eastern Europe, the humanitarian need in Ukraine is more urgent than ever. In response, following several highly successful campaigns in 2022, the Plant and Hire Aid Alliance has launched its latest appeal, Power to Ukraine, in association with Rotary International. The ambitious appeal aims to send no less than 10,000 desperately needed generators to Ukraine.
Following repeated attacks on the power grid and other critical infrastructure, many Ukrainians get just three hours of electricity per day, not nearly enough to combat temperatures that rarely rise above freezing. Winter temperatures in the capital, Kyiv, can reach as low as -4°C in the daytime and -11°C at night, putting thousands of lives at risk.
Ukraine’s President Zelensky said that generators had become “as important as armour in helping Ukraine to survive this winter”. In an impassioned plea to an emergency conference in Paris, Zelensky described the latest Russian bombardment as “blackout and energy terror”, creating a desperate situation that has left as many as
12 million Ukrainians without power to heat their homes in the depths of winter. Generators are already saving lives Ninety-five generators have already been sent directly from the factory to Ukraine as part of the Alliance Christmas appeal. This was thanks to a very generous donation of £25,000 from Gary McArdle, President of Rail Services in the US. These generators are already saving lives at the main hospital in Kharkiv in north-east Ukraine. They have been put to use in the Institutes of Neurology, Psychiatry and Narcology, where dedicated staff treat both military and civilian casualties from the war.
By donating to the Power to Ukraine appeal, you or your company can make a real difference, providing life saving winter heating to a desperate Ukrainian family, or essential power to a medical facility like those above.
“A donation of £270 is enough to buy and send a generator to Ukraine, to help keep these families warm,” said Jeremy Fish, the CEO of Ardent Hire, which set up the Alliance. “This includes the elderly, as well as small children and babies, who are at serious risk from the cold. We have all recently experienced the misery of
To ensure that the generators reach those in the greatest need, the Alliance is working with the 69 Rotary Clubs across Ukraine, which will help distribute the generators and confirm that they have only been provided directly to those intended. “This not only maximises the impact of the campaign, but also gives our generous donors the reassurance that their contribution is making a real difference,” said Jeremy Fish.
The alliance has also created a website where the aid workers will register each recipient including the details of the family or group, along with a declaration that the generator is being used as intended.
The people of Ukraine need all the help they can get to stay warm this winter. If you would like to help, either as an individual or as a company, you can rest assured that every penny of your donation will go directly towards generator orders for immediate dispatch. There are no paid staff and no overheads or other such costs. If you are located in the UK, Gift Aid will add a further 25% to your donation at no extra cost to you.
The Ukrainian people are literally freezing to death right now, so your donation, however large or small, will genuinely save lives.
To find out more, and to make your donation, please visit aid-alliance.com, email ukraine@ardenthire.com or donate by visiting: www.justgiving.com/fundraising/ ukraine-gensets.
AUSA’s new electric 1,500 kg (3,300 lb) payload dumper gives you a more environmentally friendly and silent machine. Thanks to its minimal noise emissions, it can be used in more applications than a traditional dumper, as well as in works to be carried out at night. With the machine’s integrated charging cable, you can connect directly to the mains via a 110 V or 230 V socket, or via 415 V socket with a fast charger.
1,500 kg / 3,300 lb Payload
Swivel Skip 7.6 kW / 10.2 hp Power
130 Nm Peak torque
15 km/h / 9.3 mph Maximum speed
Up to 12,3 kWh Battery capacity
One intense shift Battery range
Lithium-Ion Battery type
2 hours Charging from 20 to 80% (230V)
On-board Charger
Interviewee: Roy Haaker
Role: Sales Director
Company: Yanmar Compact Equipment EMEA
Standing still is not an option – which is fine by me. I’m happy in the sweet spot between machine innovation and strategy and management. Customer demands, market forces and new legislation and technologies are driving continual change and, in my role as Sales Director of EMEA at Yanmar Compact Equipment, I actively search for ways to challenge the status quo, pushing for innovations in product, providing solutions and customer experience
1912: Foundation of Yanmar
1933: HB Model diesel engine
1968: First mini excavator
1984: First imports of Yanmar machines in Europe
1989: Creation of Ammann Yanmar S.A.
1993: Launch of the ViO Series
2010: Creation of Yanmar Construction Equipment Europe S.A.S.
2012: 100 years of Yanmar
2014: Launch of the SV26
2016: Acquisition of Yanmar Compact Germany GmbH
Yanmar Compact Equipment EMEA is part of the Yanmar Group, a Japanese business renowned for its engineering excellence in construction, marine, agriculture and energy systems.
The company has two main construction sites in Europe: Saint-Dizier in north-east France and Crailsheim in central southern Germany. Each of these has been awarded ISO 9001: 2015 certification. This means that they have been independently recognised as consistently providing products and services that meet customer and applicable statutory and regulatory requirements and enhance customer satisfaction. In addition, both sites follow lean manufacturing processes, minimising waste while maximising productivity.
As a global brand, Yanmar Compact Equipment EMEA works with more than 170 dealers in 37 countries. This multi-national approach ensures that we maintain a close relationship with our customers, a deep understanding of market idiosyncrasies and an on-theground approach to sales and support.
So when we say that we’re closer to you, we don’t just mean geographically. It’s the closer relationships we have with our dealers and with you that mean we can offer you the very best in products, providing solutions and service support. Our promise to customers is simple – providing the best performance and to always be by their side. Customers can rely on us to offer high quality products and services through our extensive network of more than 170 dealers across Europe. We pride ourselves on sharing the philosophy of the Yanmar Group, which includes respecting people, communities and the environment, using a sustainable approach and the latest technologies to help meet the challenges of tomorrow.
Yanmar as a global group offers a broad variety of different schemes, depending on regions, countries and local legal obligations and needs. In the EMEA region, apprenticeships vary from two to four years and we offer dual studies and trainee programmes in order to create the talent pipeline we need for our organisation to thrive in the future.
Our philosophy is simple: to understand the daily challenges our customers face, exceed their expectations and deliver excellence in everything we do.
Yanmar CE and its dealers always adhere to Yanmar values. Whether it’s in proximity, speed, reliability or service quality, you’ll find that our dealers are always ready to help and will make a real difference.
We offer, via our dealers, financing, leasing, warranties and maintenance contracts, as well as access to preowned machines through our used equipment division. In addition, our dealers are trained on the use and effective maintenance and repairs of Yanmar machines by our skilled Yanmar instructors.
Our values in Yanmar CE in EMEA include:
Reliability : The high quality of our products, comprehensive services and extensive partner network means that Yanmar is a brand customers can always count on.
Proximity: We are reassuringly close to our customers, thanks to our wideranging network of dealers and close relationships with our end customers.
Performance: Yanmar is known for our advanced technology, with products we pioneered, such as zero tail swing machines (VIO), now industry standards.
We offer a range of internal mobility opportunities across regions, countries and business units, including secondments where we welcome Japanese colleagues to EMEA, and vice-versa, giving our colleagues the opportunity to experience the organisation and culture in Japan.
We live in a tight labour market, where finding – and retaining – the right talent is a constant challenge. Schemes like those described above make us a more attractive employer. Only with a vibrant internal talent pipeline we can cover our needs for the growth we are planning.
As mentioned in the previous answer, the continuous development of our people is key to our success. Our HR Strategy reflects this, and includes organisational efficiency, talent management incl. sourcing/training and development/succession planning, employee engagement and HR excellence. Training initiatives include a range of training courses, including intercultural,
As a global brand, Yanmar Compact Equipment EMEA works with more than 170 dealers in 37 countries
technical, and leadership training. In all of these areas we can clearly state that continuous development is key. We know the strengths and weaknesses of our talent, where we need to develop further and where we need to source talent externally. We also are lead by our culture of HANASAKA. What does it mean? It means let the people and the future bloom. It comes along with new beginnings, a new generation, with new possibilities. We will nurture young talent to create an unprecedented level of wonder and joy in the world.
QWhat can we do to attract young people into the plant industry?
Construction equipment needs to improve its image and become a desired career destination for young talent. It is a cool industry at the cutting edge of electrification, connectivity, autonomy
and sustainability – we need to start spreading the word about what life in construction equipment is like at a young age. Promoting the sector in schools and supporting students in the required subjects through bursaries, scholarships and vacation work placements will all help. We also need to target women to consider the sector and cast the net as wide as possible, to encourage a greater diversity of talent to join the industry.
QHow do you see the outlook for the plant industry and Yanmar post-COVID?
The ramifications of COVID are still being felt, in logistics and supply chain constraints, especially component shortages and increased shipping costs. We will continue our strategy of making a higher proportion of sourcing and manufacturing as close to our major markets as practicable.
QAnd how do you see the medium term future for Yanmar’s product development? We will continue to refine and improve our internal combustion engine (ICE) products, but the medium term focus will increasingly be the path of electrification. There are still lots of challenges to overcome to make the energy transition from ICE, but Yanmar is committed to being at the forefront of this change.
The move from ICE to electric power is exciting and will undoubtedly have the most profound impact on the construction equipment industry. The transition has already begun with compact equipment, for which it is well suited. Having electric power opens up new opportunities in terms of telematics, connectivity, machine control systems and even the electrification of other systems on the machines, for example control of the boom/arm.
QWhat is Yanmar doing with regard to sustainability? What new technologies are you embracing?
At the Yanmar Group our corporate mission since 2012 has been ‘A sustainable future’. This is not just to please our ESG investors, it is truly our passion, our purpose and our dream.
Even now that we are a decade into our ‘Green Challenge’ we still forecast that it will take a further 27 years to achieve our zero environmental impact goal. By 2050 we will be totally free of greenhouse gas emissions in our business activities, circulate all resources and support our customers so that they can achieve the same greenhouse goals as us.
Of course, we would like to achieve our climate/societal goals faster, but we must be realistic as to the scale of the challenge. In 2019 we calculated that we caused 224,000 tonnes of CO2 to enter the atmosphere from our business activities, while a further two million tonnes came from our supply chain –and a staggering 80 million tonnes of CO2 was released from customers using our machines.
Changing this is going to take time. Our machines are made from steel, plastics, rubber etc. and many of these components currently have no (or limited) green options. But we are committed to using them as they become available. In the meantime, we will source green energy and create our own, using solar panels on factory roofs. It will be a stepby-step approach, and different countries and customers will move at different speeds. This is much more than a Yanmar challenge – going green is as much a societal challenge as a technical one.
Electrifying our machines will be vital in achieving our zero carbon ambitions. And it is going to happen. But this is not as simple as in the car business and many hurdles to adoption remain. The charging infrastructure needs to develop and battery machines need to be proven in the harsh work environments of construction. People won’t buy electric machines to save the planet; they will buy them because they make economic sense.
Fortunately, as costs fall, the total cost of benefit of using electric machines will make them the compelling option. As with the new range of electric machines we launched at bauma, they are simpler, more comfortable, with low vibrations and noise, and lower running costs.
We are starting on the energy transition with battery electric powered smaller machines, but by the end of the decade we will introduce hydrogen power in our larger equipment. All the major components of electrification are on a sharp development curve that will continually make them better. It’s a step-by-step approach to the green future we seek.
At just 980 mm wide, Yanmar’s SV15 mini crawler excavator is slim and weighs in at 2,330 kg. Designed for agriculture, construction, civil engineering and landscaping duties, the well made and rental-tough SV15 can be transported on a small trailer or light vehicle. Available with a cabin or a canopy, it is a compact and a powerful machine.
Dependable, reliable and tough, the SV15VT delivers class-leading productivity
in a highly compact package. A powerful engine and double gear pump hydraulic system ensures impressive performance, while compact dimensions make the mini excavator perfect for job sites where space comes at a premium. Innovative design and a light transport weight makes the SV15VT it easy to move between sites, while best-inclass maintenance accessibility makes daily checks quick and simple.
QHow will it improve their offering or bottom line?
Efficient and lightweight, the SV15VT is the perfect earthmoving solution for job sites where space comes at a premium. A short turning radius at the front and rear, combined with a wide boom swing amplitude to the left, make the machine perfect for trenching and landscaping work in tight urban areas or at residential properties. Compact dimensions and low transport weight mean the SV15VT can be easily towed between work sites, along with buckets and a light work tool, on a standard 2.5-tonne GVW trailer. Four tiedown points on the track frames (standard) and four on the turning frame (optional) make transport preparation simple.
As with every model in the Yanmar range, the SV15VT has been designed with reliability, comfort and durability firmly in mind. The upper position of the boom cylinder, alongside hydraulic hoses routed inside the boom itself, provide class-leading protection. The SV15VT comes equipped with blade
fingertip efficiency. A track frame layout, featuring three bottom rollers, ensures a comfortable and stable ride for the operator.
The easy-access cabin is the perfect combination of stylish design and efficient technology. With a fullyadjustable seat as standard, alongside ergonomically-designed control pedals, levers, switch boards and a state-of-the-art interface, operators are guaranteed maximum comfort and practicality. Thanks to innovative design and clever cab arrangement, the SV15VT provides unmatched visibility of the working area, alongside the added benefit of excellent air circulation.
The SV15VT provides unmatched visibility of the working area, alongside the added benefit of excellent air circulation
seat, the machine features standard powerful LED work light and an orange seatbelt. Optional seatbelt sensor, additional work lights, flashing orange/ green beacons, travel alarms and a polycarbonate protective shield (for the canopy) offer unbeatable operator protection. Depending on specific job site requirements, customers can fully customise their machine. Flexibility and versatility – designed for you.
cylinder protection as standard, while optional bucket and arm cylinder guards can be specified to offer even greater machine protection. Collectively, these features ensure optimum efficiency, minimal downtime and low total cost of ownership.
Thanks to long/short arm and blade configurations, the SV15VT is versatile and adaptable to a wide range of applications. The wide boom swing amplitude distribution further extends the working range of the excavator, ensuring efficiency and performance for the operator.
The extendable undercarriage improves flexibility and stability, the SV15VT is designed with shaped steel profiles and reduced clearance between sliding parts, to prevent soil build-up – yet another low maintenance design benefit. The SV15VT features a double gear pump hydraulic system, with 28 L/min and 205 bar maximum flow and pressure. The machine comes fitted with a standard auxiliary hydraulic line to power breakers or augers, delivering a flow of 29 L/min at a pressure of 120 bar.
Operators benefit from a digging force of 7.4/12.9 kN (short arm/bucket), traction force of 13.3/8 kN (first/second speed) and two travelling speeds – either 1.9 or 3.7 km/h with a selector on the blade operation lever, providing
Safety is considered pivotal in the design and development of every Yanmar machine. The SV15VT is no different, featuring a whole host of safety-critical technologies to keep the operator safe on site and drive increased productivity. Alongside 360° visibility from the operator
Thanks to best-in-class maintenance accessibility, operators can carry out daily checks, seamlessly. The wide engine compartment hood offers easy access to the powertrain, while the side panels and cabin floor are straightforward to disassemble, providing instant access to hydraulic components, the fuel/hydraulic tanks and the radiator. The battery and fuse box are located in a lockable compartment under the operator’s seat, thus maximising safety. Collectively, these design features minimise the time taken to deliver daily checks and scheduled maintenance.
We offer the world‘s best-selling quick coupler system with over 45,000 systems sold worldwide. We have decades of experience and testing behind us. Our solutions work and you get an outstanding combination of quality, performance and safety.
• Lightning fast change of hydraulic, electrical and mechanical attachments from inside the cab.
• Always the right attachment for the job.
• Distributes oil, grease, water and electricity.
• No staff around the machine during tool changes.
• Improved safety.
• Meets and exceeds safety standards globally.
• Increased productivity.
• Increased profitability.
• Reduce the number of machines on the site.
• Reduced transport costs.
• Eliminates oil spills.
• Protected hose run.
• Less dirt in the cab.
• For machines 1-120 tonnes.
It’s September 2020. My girlfriend and I had parted ways right at the beginning of the pandemic and for the duration I have been stuck in a flat with a cat called Gary. Gary has an appalling attitude.
I get a call from a friend of mine, Lee, a brute of a man who helped me renovate my house when I moved to Dumfries from London. He’s a local lad, ex-army like me, who cut his teeth as an agricultural contractor before moving on to excavators and other heavy plant.
He was sleeping on his parents’ sofa at the time, so I offered him my spare room.
Although our professional lives are now a million miles away from what we did in the army, the brotherhood and bond still shine through. I work as a project manager on large-scale IT transformation projects while Lee is a selfemployed plant operator.
Over breakfast one morning I started asking him about the construction industry. He seemed to move frequently and was always on the phone with someone or other, securing future work. It became apparent very quickly that agencies and social media pages are the go-to places to find work. Additionally, there weren’t any digital tools – for example an intelligent digital wallet or CV builder – explicitly designed for the construction industry. Lastly, everything was done via email or faceto-face office visits.
So, as the UK population was standing on their doorsteps clapping for heroes, learning Mandarin or getting buff with Joe Wicks, I started doing some discovery work on what was already out there and how I might be able to tidy up my mate Lee’s work life.
My focus was clear: could I build a digital solution using automation
to validate a construction worker’s qualifications while, in parallel, building them a CV and introducing them to training providers who could help them upskill, all with a minimum amount of input and computer literacy?
Why? So employers could search for validated cardholders with the correct experience and within a specific geography; and workers could manage their own careers by finding appropriate, competitively priced, training.
I convinced a few friends – Euan, Max and Phil – to climb aboard and help me build a prototype. Now they are my co-directors and form the meat of the Tradegraft team.
Over thirty card schemes govern the construction industry, so we had to pick one. Plant was the obvious starting point due to having direct insights from Lee. Next, we had to find an accrediting body. At the time we didn’t have a preference, but NOCN were the first to respond and hear our transformative vision.
Gareth Cutts at NOCN got it, immediately seeing the value of connecting employers and employees, validating certifications in real time and, at the same time, suggesting training establishments
“Have I told you the one about two veterans who lived together through a global pandemic? It ends a little differently from how you may expect…”
to both cohorts in the background. This meant that for the first time, employers were being offered assurance that the people they might want to employ were indeed holders of the qualifications they said they held.
Things moved quite quickly after that. NOCN signed a five-year partnership with us. We became a CSCS technical partner, too. All the time, in the background, we were building version one of Tradegraft.
Fast forward to December 2022, we are ready to go and we secure our first production trial when Flannery Plant Hire contact us for a working demo –with actual data and real accounts.
It went well. Flannery posted five jobs, we delivered at least one applicant for each role, with a total of twelve applicants in all. So Tradegraft had now been tested, jobs responded to and we had proved our solution worked.
Now it’s fair to say at this point that the numbers coming back weren’t going to set the world on fire, but we had data and could refine our product over the Christmas break. Most importantly, we learned a lot from the experience.
Revisiting Flannery in January, we gave it another go. Again five jobs in five distinct locations across the country. The jobs were posted on www.tradegraft.com on Wednesday afternoon and by 17:00 on Thursday had over fifty applicants. By the following Monday it was eighty-six and consistently rising daily.
All these applicants filled in a single simple form that takes no more than 30 seconds.
So
When an employer like Flannery posts a job with us, our bespoke automation is able to identify card numbers like location, category, endorsement and experience that match the job role specifics. During this process no personally identifying information is shared with us, the employer or NOCN.
We then send these card numbers
back to NOCN and ask them to contact the cardholder regarding the job to see if they may be interested, via the Tradegraft platform. This process is entirely automated.
If any of the contacted operators are interested they can follow the link, create an account and apply. The whole process only takes a couple of minutes the first time, after that it’s a couple of clicks.
This all assumes everyone registered with NOCN is always actively seeking employment, so what if they aren’t?
As I said at the start, the whole reason Tradegraft came into existence in the first place was to make life easier for people like Lee who move between short term contracts on different sites. But if the cardholder is happy with their current situation we do two things:
• Offer them the option to opt out of any other communications concerning job placements from NOCN or,
• Create an account and provide a very clearly marked toggle switch, which, once activated, lets us know they are not looking for work at the moment, but would still like an account for future use.
Sounds simple, right? There are of course some risks and believe me, having heard some industry feedback loud and clear, we are taking them seriously. The main one though is: “This sounds great, but how do I stop my competitor from poaching my standing workforce via Tradegraft?”
The answer is: “You can’t, entirely.” In the same way you can’t stop people from using LinkedIn, Facebook or posting their
CV on Indeed, creating a digital solution will always increase possibilities. But this works both ways. Employees might find a better job, but employers will almost certainly find a better employee.
That said, we can filter outbound messaging sent from NOCN. It requires a little effort from both parties, but that is part of a collaborative attitude towards the digitisation of job brokering and an understanding that it is the employee’s choice to be contacted or not.
So what’s the cost of all this? We are free to operators. Forever. We see the social value of our platform and if nothing else you should give it a go just to see how easy building an online CV is. We aim to make this feature downloadable by summer 2023.
To employers, agencies and recruiters the price is £10 for a seven-day job posting. It will take you 30 seconds to enter the specifics of the role you are advertising for. Then just sit back and wait for applicants to drop into your portal. No more Facebook, Indeed or LinkedIn. And the increasingly opaque pricing structures (if you have tried, you will know already) being employed by most platforms. Instead, use a transparent, construction-dedicated, solution to manage all of your positions via one easy-to-use web portal.
It’s probably worth mentioning that you only pay when you start to review applicants, which is decidedly uncommon. We also show you how many card holders match your advert before you even publish it, offering you the assurance you need that you’re not looking for a unicorn.
What does that mean in real terms? Tradegraft can contact almost 300,000 CPCS card holders covering 750,000 individual categories and endorsements. The efficiencies to the recruitment process for an employer go far beyond that of time saving. Tradegraft’s ability to allow employers to separate where its employees and contractors are working via
projects allows a quick view of workforce utilisation at specific sites, delivering complementary workforce management capability for free.
For employees we say “Let the jobs come to you.” It’s the simplest and easiest market solution to ensure you can be found and offered relevant jobs that meet your qualifications.
As an employer, if you’re interested in seeing how many people match a specific search for example, we have a great free tool called The Plant Operator Locator, which you can find on the tradegraft.com website.
The most significant achievement for us is to see Tradegraft in use and working, and we hope that it positively impacts people’s lives. We encourage feedback and industry engagement and, over time, will be adding features led by your insights.
Our next milestone is attending the Scottish Ex-Forces in Business Awards 2023, where we are shortlisted as a finalist under the innovation category. Feel free to wish us luck.
For any further details about Tradegraft please don’t hesitate to get in touch via our website or to hear more in person from Chris: Chris@tradegraft.com. We would love to hear from you all.
The Rototilt® tiltrotator transforms your excavator into a flexible tool carrier. This opens the way for new types of jobs, and maximise both safety and productivity. The whole tiltrotator family is packed with innovative technologies and ingenious design solutions that make your work safer, easier and more profitable. With Rototilt® you get a tiltrotator that fits your specific need, whether you require dexterity and precision, or muscles and capacity. Rototilt® makes it possible.
Open-S
The open industry standard for fully automatic quick couplers. Read more at www.opens.org
Our tiltrotators
• R1 | 1.5-3.5 tonnes
• R2 | 3–6.5 tonnes
• R3 | 6-12 tonnes
• R4 | 10-16 tonnes
• R5 | 14-19 tonnes
• R6 | 15-24 tonnes
• R8 | 23-32 tonnes
Interviewee: Andrew Scheer
Company: Pathfindr
Role: Marketing Director
Sector: Technology
Turnover: Group turnover
£72m
Employees: 25
Current brands: Zonr, Pathfindr
Geographic reach: Global
Established: 2016
Prior roles in career: Product Manager, CMO
Andrew has considerable experience leading and developing high-performance product and marketing teams within blue-chip and entrepreneurial SME environments. These include Sony and Barclays through to tech startup Pathfindr and MarTech platform provider Coniq
QHow do you fit in to Pathfindr? Sitting in the leadership team.
QHow did you first come to be in your role?
I joined PF in the midst of the COVID crisis in June 2021. PF was looking to bolster its marketing effort by bringing in its first Marketing Director
QTell us about your career progression
I have accumulated a wealth of experience in technology, having started my career in financial services. Starting as a product manager looking after retail financial service products I moved to
Sony, ultimately developing, launching and managing its non-core propositions. Through several technology businesses, I landed at PF in 2021.
QHow has Pathfindr developed in that time?
Since I arrived, we have developed and launched the Zonr plant proximity safety solution as well as significantly built momentum in our core IIoT business.
QHow about the balance between your product expertise and your business role
My mix of experience, skills and
expertise helps when adapting to new markets and propositions. The breadth allows for cross-fertilisation of ideas, speeding up problem solving and delivery.
QWhat is it about your role that attracts you?
The team as well as the variety of the work; from digital to face to face, IIoT to safety solutions.
QHow do you think your colleagues see you (or you would like them to)?
I’ll leave them to answer that.
QTell us about Pathfindr, its history and development
PF is a team of technology experts who specialise in asset intelligence, i.e. using connectivity-enabled location tracking to identify the whereabouts of assets –wherever they may be in the world – and highlight potential inefficiencies that can save firms millions. But what many people
don’t know is that our story began in a very different place.
PF was established in 2016, but it started out life as a small team of technology experimenters, at krow (formerly bigdog), a creative agency within MISSION, and set up an innovation task force to explore technologies that could support clients’ objectives to drive sales.
We challenged ourselves to develop a new indoor wayfinding method to allow for indoor navigation to help shoppers find products more quickly in supermarkets.
The primary focus of the tech was to help customers to find what they were looking for in the store, based on research that found that customers are likely to spend more money if things are easier to locate. Another aim was to improve the efficiency around online orders, as they were unable to build bigger warehouses and so wanted to see if they could optimise the picking of products.
PF published a blog about our new approach to wayfinding, which led to an inquiry from BBC producers who wanted to explore how the same tech could work in a completely different way – to track and explore the behaviour of domestic cats, for BBC Horizon TV documentary The Secret Life of the Cat.
The team adapted the solution to include optical cameras in the house, accompanied by different infrared signals coming from the cats’ collars, allowing the cats’ movement and behaviour to be tracked 24/7 – providing data that was then analysed by animal behaviour experts.
Involvement in the BBC programme gave our team the profile it needed to secure the major client that would help to further progress the development of our solution, and ultimately establish a business dedicated to asset location. A senior leader from Rolls Royce happened to watch the show, and wanted to explore how the tech could help them monitor their assets, to provide operational efficiencies.
While the team had been looking at asset tracking and real-time location systems for a while, they were considered challenging to implement, expensive, and not without their limitations. The team took a fresh approach and combined the product from the retail application and BBC documentary, using Bluetooth
technology instead of the optical, camerabased approach. The Pathfindr product available today was born and has since been expanded, improved and evolved for different uses in aerospace, manufacturing and other environments and sectors across the world.
During COVID, the team developed and launched a social distancing device. This was sold in large numbers (c40,000) and was intended to keep workers safe. This evolution led to the development of Zonr using the tried and tested technology of our core IIoT as well as the SDA.
QTell us about its growth path
COVID made traditional growth difficult with on-site visits impossible. Since the return of face-to-face meeting on-site or at expos, interest in our core product has grown significantly. Rolls Royce remains our biggest customer, but many others have now joined them to leverage the value that the IIoT technology can bring
QExplain what Zonr does, in particular for our readers in Diggers LIVE
Every year too many workers are killed or injured through unnecessary contact with plant and machinery on construction sites and beyond. Zonr Plant Proximity Solution provides a dynamic virtual barrier intended to warn workers and plant operators of incursion into safety exclusion zones.
Our products use BLE, UWB, cellular and GPS technology to improve visibility to reduce waste (time, money, materials etc.) as well as lives. The products monitor their environments to make data available to either better manage processes or warn workers if they are in the wrong place.
QWhat are Pathfindr and its products’ USPs?
We build all our solutions to be as simple for the user as possible. Yet we seek to solve challenges that others can’t even understand. It is the agility, simplicity and power that make our solutions different
QHow can these benefit customers? PF solutions give users visibility and access to data for areas that are often hidden in plain sight. Tools lost, materials mishandled, machines not managed effectively. PF core solution helps engineering, manufacturing and logistics organisations improve their effectiveness; saving time, money and the planet, by shining a light on (digitally) hidden processes. We call this Real-time Asset Intelligence.
Zonr simply aims to save life and injury by warning plant operators and operatives about unauthorised incursions into safety or red zones around dangerous plant and vehicles. It is very simple and quick to set up and very easy to use
QTell us about your team and working culture
The team work closely together knowing the importance of the problems they solve and the benefits they bring. From the engineers to the customer sales and
support teams they all have one focus – delivering the best possible solutions that we can whether this is for our manufacturing, logistic or construction customers.
QTell us about any apprenticeships Pathfindr has
We have apprentices who join us to help them on their journey within technology. This could be looking at existing or new technologies such as blockchain and their application with our business.
QIs there a good pool of potential new recruits?
Finding good people is always tough, never more so than now. That said, the interest in our sector has meant we have been able to continue to build the team as demand grows.
QWhat can we do to attract young people into the industry?
Speak to what interests and excites them; the planet, their community and their future career path.
QDoes Pathfindr undertake any training or Continuous Professional Development? How do you bring new talent on board? Yes. And we have a group talent acquisition team who help us navigate the path of talent onboarding.
QHow do you see Pathfindr in five or ten years?
A business firmly embedded in the fields of RTLS/IIoT as well as PPI safety.
QAnd how about yourself? Helping the business continue to grow towards financial and cultural (team) success.
What gets you out of bed in the morning? Kids
What do you do for fun? Watch rugby
When are you happiest? Watch win at rugby
Autumn, winter, spring or summer? Spring
What’s your tipple of choice? Beer
Be or do – which one best represents you? Do
Asset finance is, for many firms in the construction sector, a form of funding they have used for many years. Yet still, for others, it’s not something they know much about. In this article we take a closer look at the different products and understand why it could be the perfect option when considering your next purchase.
In short, asset finance is an alternative form of funding used by businesses to obtain the equipment they need to grow
or access much-needed cash. It makes the otherwise unaffordable affordable because it gives businesses access to the equipment they need without incurring the cashflow disadvantage of an outright purchase.
Agreements can also be customised to the business’s needs, with flexibility on both the term and repayment schedule.
There are various products that come under the broad umbrella of asset finance, with one of the key ones being refinancing
or capital release as it’s also known. This is a proven way to make your assets work for you and release cash back into the business.
It works by the finance company purchasing the asset and financing it back to you, with repayments calculated in line with the income the asset is expected to generate. At the end of the refinance term, you own the asset.
This offers several benefits to a business
that just needs a cash injection, whether it’s for investment in additional business critical assets or to use in other areas of the business, including unexpected bills and invoices, salaries, VAT payments, diversification – the uses are almost endless. Funders can also look to take over a finance agreement with another provider and extend the term, ultimately reducing monthly payments and easing the pressure on cash flow.
• Hire Purchase (HP): This allows you to buy equipment on credit. The finance company purchases the asset on your behalf and owns the asset until the final instalment is paid, at which point you are given the option to buy it,
• Finance lease: The full value of the equipment is repaid to the finance company, plus interest, over the lease period. At the end of the term, you can choose to continue to use the asset by entering a secondary rental period; sell the asset and keep a portion of the income from the sale or return it,
• Operating lease: Similar to a finance lease, an operating lease allows you to rent the asset from the asset funder while you need it. The key difference between the two is that an operating lease is only for part of the asset’s useful life. This means you pay a reduced rental because the cost is based on the difference between the asset’s original purchase price and its residual value at the end of the agreement.
Close brothers is the largest, most successful and longest-established asset finance funder in the UK, with over 30 years’ experience working with SMEs through all economic cycles. Its team of construction finance
specialists, many of whom have transport industry background themselves, work with businesses across the UK to provide funding for both new and used construction equipment. As sector experts, they understand how vital it is that you have the right tools at your disposal, whether you are looking to expand or replace your diggers and other key assets.
MySMT also provides customers with their own ability to create multiple staff user accounts based on varying levels of access and visibility options. This ensures that all staff responsible for the monitoring and administration of their fleet benefit from MySMT, and that key decision making processes are preserved within the original arrangements of the customer’s management structure.
Commercial Solution Manager Jack Kenny said: “In a nutshell, MySMT provides a wide range of user roles to ensure managing or administrating a machine fleet from simple, user-friendly and secure portal.
“Thanks to MySMT, you no longer have to remember how and where to access every piece of information required to keep your fleet running. You can simply sign in to the secure, web-based MySMT portal and have every piece of information relating to your fleet readily available right at your fingertips and through tailored notifications.
Following a meticulous design and testing process, SMT GB’s brand new one-stop information, service and online parts ordering portal is now available nationwide.
One of the core customer areas of feedback when it comes to fleet management is requiring access to multiple online or app-based portals and platforms, which turns effectively monitoring and managing a machine fleet into an administrative nightmare.
To alleviate this burden, MySMT offers SMT GB’s customers a single point of access solution for modern fleet management.
Thanks to the secure, web-based portal, customers can quickly and easily access, monitor and act on multiple aspects of fleet management both from the office or on the move.
Making sure that all of the
information stored on MySMT is easily accessible, the platform is divided into the three distinct areas: Company, Fleet and Parts.
“Company” provides customers with visibility of financial transactions with SMT GB, all active CSA and warranty contracts, oil sampling reports, ProCare recommendations and Service Inspection Reports.
“Fleet” provides customers with access to current fleet details, including location, operating hours, information of fuel consumption, productivity data, CO2 emissions and visibility of repair and maintenance data on all machines within a customer’s fleet.
“Parts” provides access to the newly launched SMT online parts store, allowing customers to look up and order all genuine Volvo parts 24/7, with access to technical drawings if required.
“By combining information and the ability to take action instantly from a single, universally-accessible platform, staff responsible for fleet management and administration are offered the peace of mind from knowing that they are taking the best possible proactive steps to keep their fleet and operations running smoothly, all thanks to MySMT.
“SMT are committed to bringing customer information into the digital age and will continue to develop MySMT with our customers’ needs at the forefront of any new development.”
MySMT is freely available for all SMT GB customers.
Name: Florian Jud
Job title: Product Manager Dumper Line
Role: Managing the product roadmap, developments and market launches based on customer needs and wishes
Time spent at Wacker Neuson: One year
Previous experience: Industrial manufacturing as product manager and international sales manager
Any relevant qualifications: Environmental studies and lean production
I had the pleasure to take over the responsibility for the strong Wacker Neuson Dumper portfolio one year ago. For us, the focus is on customer needs and wishes. Aligned with this, this means for me to manage and optimise the product roadmap as well as the development of the dumpers with this in mind. I am also responsible for planning the market launches for the dumpers internationally so that we can offer the right solution for every customer in every region.
Product name: DW15e
Key features/advantages: Electric drive system, no direct exhaust emissions, minimal noise, compact, intuitive operation
Date released: 2019
Development time: Three years
Brief specifications:
• Payload: 1,500 kg,
• Travel speed: 15 km/h,
• Effective power: 15 kW.
Wacker Neuson is known for its wide range of zero emission solutions. One of them is the battery-driven wheel dumper DW15e. Based on our experienced and reliable 1.5-t dumper 1501 we developed an electrical drive dumper. The DW15e is the perfect solution for every typical inner-city construction site as well as for applications indoors, in urban environments, gardens, golf courses, and in many other sectors. It fits perfectly into the range with the well known
intuitive operation of our compact 1 to 1.5-t dumpers.
The dumper DW15e offers many additional application uses. The clearly laid-out display with charge level display and separate motors for the drive system and hydraulics ensure maximum efficiency and operating comfort. Charged overnight, it can be used again immediately the next workday, fully ready for operation without performance restrictions as compared with conventional wheel dumpers. 100%
emission-free work protects the environment and the operator alike. Customers also benefit from the high service intervals and maintenancefree battery for the perfect costbenefit ratio.
At Wacker Neuson we can offer the whole portfolio of electric driven machines and equipment for the zero emission construction site. In addition to the DW15e wheel dumper, this also includes track dumpers, excavators, wheel loaders, rammers, vibratory plates and an internal vibrator system for concrete compaction. Furthermore, they are ideal for areas with a sensitive environmental as for example at night, in nature reserve or indoor applications. Therefore, the compact dumper DW15e offers a great alternative to the conventional machines. Regarding future sustainable development, the DW15e is very important to reduce emissions along the whole construction sites. Since we introduced the machine to the market in 2019, it has proven itself many times over. It works reliably and is just as powerful as the conventional alternative, the runtime is sufficient for a typical workday and it can be recharged easily.
For the future, we continue to further develop our zero emissions portfolio, which includes the development of electric dumpers. We see that our customers are convinced by the E-machine and its performance, with reliability, power and durability.
Name: Mark Royse
Job title: Head of Sales, Mecalac Construction
Equipment UK
Role at Mecalac: As Head of Sales, my key responsibilities are to lead Mecalac’s sales strategy in the UK, manage the commercial team, build and maintain strong relationships with key customers and drive the future direction of our major product lines
Time spent at Mecalac: 22 years
Any relevant qualifications: (BEng) Mechanical Engineering, University of Durham. (MSc) Engineering and Manufacturing Management, Coventry University
Around the world, political leaders are facing a climate crisis – an emissions gap that continues to widen, greenhouse gases rising on a daily basis and an increasing population demanding ever greater energy requirements. While, at its peak the construction industry was said to be responsible for around 20% of global emissions, the sector is quickly decarbonising, with businesses investing millions in developing environmentally friendly solutions for the industry of tomorrow.
At Mecalac, we continue to operate at the forefront of sustainability. With a strategic commitment to reducing our carbon footprint, as well as cutting the emissions created through the operation of our market-leading compact machinery, we’ve embraced countless innovations to help our customers – and ourselves – along the journey towards net zero.
We’re delighted to have launched the sector’s first zero-emissions range
Product name: Mecalac six-tonne electric site dumper
Key features/advantages: As Mecalac’s first ever plug-in dumper, its sixtonne model aims to set the standard in performance, capability and low carbon operation for operators all over the world. The culmination of extensive R&D into electrification, the innovative model offers a futureproof earthmoving solution with zero tailpipe emissions – perfect for urban jobsites and low emission zones.
Its stylish cab, inspired by Mecalac’s highly acclaimed MDX range, offers unmatched safety on site, while a wide range of first-to-market incab technologies, impressive functionality and ergonomic design features guarantee comfort, ease of operation and maximum user productivity.
Date released: Launched October 2022, full production to commence later in 2023
Development time: 48 months
Brief specifications:
• 6-t working payload,
• Full-integrated cab with 360° views of the jobsite,
• State-of-the-art safety credentials, including ‘Mecalac Shield’ as standard,
• Plug-in electric powertrain with zero tailpipe emissions,
• Compatible with Mecalac Powerpack, a 300 kWh portable battery power supply.
Job title: R&D
DirectorRole at AUSA: Managing AUSA new product development to meet and exceed customer expectations and company profitability goals, implementing new digitalisation activities and tracking technology trends and relevant legislation in company products and services
Time spent at AUSA: 19 years
Previous experience: Urban Range Business Unit Director at AUSA, Project Manager for HVAC systems at NISSAN Technical Center Europe and responsible for the quality certifications at Behr
Any relevant qualifications: Before being the AUSA R&D Director, my role was Urban Range Business Unit Director, where I successfully oversaw the start-up and initial development of this new product division and developed and implemented specific strategies to create the Business Unit.
It also included managing new sales team in order to fulfil the Business Unit targets and being responsible for sales, pricing strategies, product development, manufacturing, delivery and service.
The D151AEG dumper is the first 1,500-kg payload dumper available on the market that is equipped with a LiIon battery power unit, batteries that are known for their reliability and durability. In the case of this dumper, it features a pack with up to 12.4 kWh capacity, enough for at least one full day’s work with this type of equipment.
It also gives you more environmentally friendly and quieter options. The Li-Ion battery pack is managed electronically to smoothly offer maximum power and match diesel vehicles in all-terrain conditions.
Its 7.6 kW batteries and peaks of up to 17.3 kW are managed electronically to smoothly offer optimal power and with all-terrain capabilities that are equal to diesel vehicles. Additionally, when the accelerator is released, the electric motor instantly reduces the speed while energy is regenerated, ensuring an increased range.
Product name: D151AEG electric dumper. 1,500 kg payload, Li-Ion batteries
Key features/advantages: As this vehicle generates zero emissions and emits virtually no noise, it is the perfect tool for working in pollution-free spaces such as greenhouses, municipal works carried out at night, enclosed spaces, etc.
Release date: October 2022
Development time: 30 months
Brief specifications:
• Up to 12.4 kWh battery capacity, enough for at least one intense shift
• Only two hours to charge from 20% to 80% (at 230 V)
• It can be connected directly to the mains via a 110 V or 230 V socket, or via 415 V socket with a fast charger.
• 50% reduced TCO compared to a dieselpowered machine with similar features.
• The cost of electric charging compared to fuel fill ups is a 75% lower.
The 16th annual Executive Hire Show took place on 8 and 9 February at the Coventry Building Society Arena. This year’s event comprised 150 exhibitors, with 32 companies making their show debuts. The show also boasted a record number of visitors, with a bullish feel to the event on both days.
The EHS team is delighted to report that the unique visitor numbers, who were validated hirers, totalled 2,045 over the two-day show – smashing last year’s record.
Chris Moore, Publishing and Events Director for the Executive Hire Show said: “After scrutinising the visitor list with a fine-tooth comb, we are delighted to confirm that the 2023 show attracted 2,045 visitors – a recordbreaking number of relevant hire industry professionals that is 119 greater than the 2022 event. All hire industry visitors were from national and independent operations, which is consistent with previous years. This reconfirms the pivotal role of the show and its continued ability to attract relevant, quality hire professionals.”
Visitors from the hire sector attended the event to expand their fleets, with new products to discover, the latest innovations and launches from a diverse range of exhibitors at the show. There was a real buzz among both exhibitors and visitors, all of whom were eager to do business. The main hall and the atrium areas were packed on both days of the show. Numerous deals done during the two-day event and many hands were shaken. Professional alliances were forged and trade was most certainly brisk throughout.
Speedy and generator supplier
Shindaiwa UK announced a spectacular deal, whereby Speedy invested £1m in ECO 165 petrol-powered and ECO 200/300 amp diesel-driven welder generators – the ECO 200/300 welder generators are HVO compatible.
Shindaiwa also sold 10 of its Stage V PowerCenter 15 diesel generators to Aberdeen-based Genny Hire, in a deal worth over £100,000.
SANY UK and Ireland sold the first of its fully electric drive mini excavators – the SY19E to Gary Plant, Managing Director of G Plant (Midlands) Ltd
Altrad Belle also did a mega deal with Bradfords Building Supplies, which was the first hire company in the south-west to invest in the brand new Minimix 150E+ battery-powered cement mixers. They sealed the deal for 24 units.
Elvington Plant Hire reported that the hire firm had a ‘fantastic trip’
to the show and made many purchases to bolster its hire fleet, including Prop Pal, which is a state-of-the-art new needle support system for the domestic construction trade.
The show also attracted attention from a number of influencers from the construction sector. Ollie Gunns is a successful vlogger with thousands of followers on YouTube, LinkedIn, Instagram and other social media platforms. This was Ollie’s first visit to the show and he was impressed. Reporting there was lots to see he also said that the ratio of reps and visitors was refreshing. Ollie also negotiated some deals for his own contractor business. You can check out his review of the show on his YouTube channel –Olliegunns
There was a record number of new product launches at the show, with a strong focus on environmental solutions.
New exhibitor Lifos launched its ‘Fort’ product range, which is specifically
designed for the hire industry. Fort is a complete battery-based power system in a box, making it easily transportable and quickly deployed. The Fort range can also be fitted with solar panels.
Tufftruk introduced the new allelectric BENDie EB800 mini dumper, which provides maximum versatility and light touch operation. This adaptable, battery-powered machine also has an 800 kg payload.
Wirtgen showcased one of its subsidiary, Hamm AG’s first fully electric battery-driven tandem rollers – the HD12eVO with vibration and oscillation, which forms part of the HD CompactLine series and is the world’s first e-combination roller.
Ammann introduced its prototype eAPX 68/95 3D Vibratory Compactor, which attracted plenty of interest from hirers. The Ammann eAPX 68/95 is the first vibratory plate on the market that can move in an arc or circle – or turn on the spot.
Those products that explored new power options or introduced technologies that improved safety, security and productivity in the workplace were celebrated on the Innovation Trail.
Hilti Great Britain showcased the new 22 V Nuron Power Tool range, which continues to expand beyond 70 power tool products. The Nuron system also benefits from a range of battery sizes, online asset management options and fast charging.
Wirtgen made the trail with its electric Hamm E-Power roller range. The HD 12e VV model has a 23.4 kWh battery with a 120 size roller. The machine weighs 2.7 tonnes and is fully electric, with three points of articulation. Running times are from four to six hours, depending on the application.
The new Duro Yokota ‘dust free’ core drilling complete solution for the hire industry was also on the Trail. It features two drill sizes and a vacuum which sucks dust directly from the cutting edge, thus removing harmful particles from the drilling site.
Elite GSS Ltd lit up the Innovation Trail with its new High-Vis Ballast Block. This simple and effective innovation is already reducing carbon emissions, due
to the recyclable materials used in its construction and its lightweight, waterfilled design.
MHM Group showcased its Ultra Silent 10 kVA generator on the trail. This ‘UK first’ model reduces noise emissions to as low as 50 dBa at seven metres. This pink-coloured machine also features a Stage V, HVO-ready Yanmar engine, and is fully bunded to prevent fuel leaks and spillages.
Thwaites showcased its three-tonne electric dumper prototype, which is the first of its class in the industry and will be made in the UK. With up to eight hours of standard operating capability from the 23 kWh battery, the machine is designed for the applications dumpers are typically used for, but with the added extra of being able to be used indoors. It will also be a popular choice for low emissions zones and areas where noise pollution can be an issue.
Genquip Groundhog launched its new energy-efficient ‘i’ range of welfare units on the Innovation Trail – new i360 and i550 mobile cabins. Hot on the heels of the show, Genquip also won yet another green award.
The new Faresin 17 m electric telehandler, from UK dealer GGR Group, was awarded a place on this
year’s Innovation Trail. Sadly, the new machine could not be delivered in time, but its smaller sibling – the Faresin 6.25 – was a compelling substitute. GGR Group has already received significant orders for the 6.25 from the likes of Flannery, Explore and Lynch. The hire companies have also placed back orders for the 17 m electric machine.
Pro Pal was also selected for the Innovation Trail. This innovative needle system helps builders to safely and effectively support domestic buildings during structural alterations. The product is so successful that it’s now available in a new, longer length, as well as from high profile independent and national level hire companies.
Metal and Modular showcased its innovative Navigator scissor lift range. The Navigator is the UK’s only manually-powered scissor lift to attain a working height of six metres, and the company used the Innovation Trail to introduce a new 4.5-metre model. The novel equipment can be used 24/7, thanks to free ‘hand power’ and reduced maintenance requirements. No diesel or charging is required, and the Navigator is simple and safe to use. This is a gamechanger for hire fleets and it’s made in the UK.
Last but not least were this year’s Passionate Hirer Awards, which were presented by Publishing and Event Director Chris Moore at the networking event on the first evening of the show. Sponsored by the Hire Exchange, our congratulations go to Marley Hire and
Sales for winning in the Outstanding Single Depot category, while Drogheda Hire achieved the Outstanding Multi Depot accolade. Chris said: “Well done to both companies on your very welldeserved win and for your continued support of the Executive Hire Show.”
Building on the success of the 2023 event, the dates have now been confirmed for the 2024 Executive Hire Show, which will return to the Coventry Building Society Arena on Wednesday 14 and Thursday 15 February 2024.
As a provider of fluid transfer solutions, Hydroscand supports many businesses in the construction, plant hire and civil engineering industries. From the moment we arrived, it was clear that the show was well attended by relevant exhibitors and visitors. It was evident that the organisers had put in the effort to create a space that was both inviting and professional, with a layout that made it easy to navigate the exhibits.
Our primary focus was promoting our full range of products and services, including hoses and fittings and mobile hose replacement, with the stand having a particular emphasis on our hose assembly machines. Nigel Townsend, Product Manager, gave several demonstrations throughout the day, which caught the attention of many visitors. People were impressed with the machines’ capabilities and how easy they are to use.
Throughout the day, there was a steady flow of people who were genuinely interested in our stand. They took their time to ask questions and learn more about our products and services. We found that the quality of conversation we had with visitors was exceptional and we were impressed with the level of interest they showed in what we had to offer.
Nigel Townsend, Product Manager said: “It was a good two days and we gained some good quality leads. We were promoting our crimping machines including our new lightweight range; hose and fittings and our 24/7 mobile hose service.”
What we appreciated most about the show was the genuine interest and enthusiasm displayed by the visitors. They weren’t just browsing or killing time – they were actively seeking out information about our products and services. We explored ways to reduce expensive downtime with owners and managers of businesses. We understand the costs associated with machine failure and stoppages. We are always happy to work with customers to find solutions that work for them.
Michael Sines, Area Sales Manager said: “We got to meet a lot of people who showed a great deal of interest in our many different crimping machines. We got a chance to discuss our fluid power side of the business from hose and the fittings to making people aware of the mobile breakdown service we offer.”
Since the show, we have already made sales of two such machines and have several more conversations ongoing. This is a clear indication that the show was a success for us and that our efforts in exhibiting paid off. Overall, we were pleased with the show’s organisation, the quality of attendees, and the outcomes we achieved.
Rebecca Galley, Managing Directorsaid: “The Executive Hire Show brought many companies together from the construction, plant hire and civil engineering industries, gathering to share innovation and best practice.
“We had lots of interesting conversations. It’s great to make new connections and talk with customers about their challenges and opportunities. It’s also a pleasure to see people we are already working with and learn about their latest projects and ideas.
“A great deal of work goes into preparing for, taking part in, and following up an exhibition but it is always worthwhile. Thank you to everyone who made this a success, it was a brilliant team effort.”
JCB is a proud supporter of the Executive Hire Show and once again exhibited on its traditional stand space at the entrance to the event. The show provided the ideal opportunity for the JCB team to network with a wide variety of its customers and potential customers in the UK plant hire market, from decision makers at SMEs through to executive board level members at JCB’s key national accounts.
The company showcased the extensive range of JCB machines for the rental sector, including the first public showing of the brand new 514-40 compact telescopic handler.
Stand visitors could also learn more about how JCB is playing a leading role in developing alternative fuel technology, such as hydrogen and
electric, pioneering the move towards a cleaner, low-emission future for the construction industry and rental market. JCB representatives discussed how they can support customers on their own road to zero journeys.
The JCB 514-40 loadall telescopic handler
The 514-40 is JCB’s smallest loadall telescopic handler to date, with a cab height of just 1.8 m and a width of 1.56 m. However, the compact machine has the largest operator’s cab in the class, sharing its core DNA with the world’s number one telehandler range.
• Low maintenance 19 kW diesel engine requires no DPF or DEF to meet Stage V,
• 82% shared JCB componentry ensures quality, ease of maintenance and maximum uptime,
• Full width cab is up to 200 mm wider than competitors, delivering more operator space,
• Best-in-class lift capacity at full height is 12% higher than competitors,
• 17% increase in power-to-weight ratio over the previous generation 516-40
• Increased manoeuvrability for the tightest working sites.
JCB’s new 514-40 loadall telescopic handler brings together more than 45 years of telehandler development to create the smallest overall package, with
big machine comfort and capabilities. The 514-40 has been designed to access the most confined sites.
The telehandler is powered by a low maintenance 18.4 kW diesel engine that meets the EU Stage V emissions standard without the need for a complex Diesel Particulate Filter (DPF) or any diesel exhaust fluid, reducing operating costs for customers and simplifying operation.
With a maximum travel speed of 15 km/h and permanent four-wheel drive and four-wheel steering, the 51440 offers the all-terrain capabilities synonymous with JCB’s market-leading loadall range.
The maximum lift capacity is 1,400 kg, while maximum lift height is set at 4.0 m, making this an ideal machine for numerous industry sectors. Lift capacity at full reach is set at 525 kg. With an unladen weight of 2,695 kg, the machine has a 17% higher powerto-weight ratio than the previous 516-40 loadall. However, the 514-40 can be
transported on a lightweight 3.5-t trailer behind a 4x4 or a light commercial vehicle, making it easier, quicker and less expensive to deliver to site.
The full width operator’s cab is 20% larger than the previous 51640 and a full 200 mm wider than competitor models. This provides the operator with a comfortable working environment and the extensive glazing delivers excellent visibility to all four corners. The cab will be instantly familiar to operators of other loadall models, with JCB’s intuitive ergonomic controls making the 514-40 one of the easiest machines to operate.
The JCB E-TECH range Also on display were a small selection of JCB’s extensive range of E-TECH electric machinery, including the 19C1E mini excavator, the S1930 electric battery-powered scissor lift and the E-TECH single-phase power packs which offer a zero-emissions solution to varying on-site electrical demands.
The world’s first electric mini excavator, the JCB 19C-1E has zero emissions at point of use and is considerably quieter than a standard machine. The pioneering model has been a huge success, with JCB celebrating production of its 1,000th model in December 2022. Four lithium-ion batteries provide 20 kWh storage –enough for full working shift for the majority of mini excavator customers on a single charge.
JCB’s E-TECH power pack range provides a zero-emissions solution to varying on-site electrical demand, creating no noise or vibrations at the point of use and allowing longer operation of electrical tools and machinery in urban and emissionssensitive areas. The power packs are a further demonstration of JCB’s leading role in the move towards a cleaner, low-emission future for construction equipment, building upon the growing range of JCB E-TECH electric machinery available to customers.
SANY UK and Ireland returned to the Executive Hire Show, following its extremely successful debut at the event in 2022.
Similarly to last year, the heavy machinery manufacturer found its stand to be well attended on both days of the event, with its new 2-t electric mini excavator, the SY19E, taking centre stage as it was unveiled to the UK market for the first time.
As well as zero emissions, the compact and innovatively designed SY19E with fully electric drive is equipped with a lithium iron phosphate (cobalt free) battery. This allows for faster, safer and more efficient charging as well as a significantly longer battery life (up to 3,500 full charge cycles) to reduce total cost of ownership.
Featuring a single automotive standard charging socket, the machine offers a fully flexible charging solution that includes a fast charge of 1.5 hours
and without the need to purchase any additional equipment. Significantly lower noise levels (66 dB(A)) for improved operator comfort and reduced noise pollution also makes for cleaner, more sustainable working.
The saving potential of the electric excavator is also very high. Compared to machines with combustion engines, electric operation reduces power costs by around 30%. The savings are even more significant in maintenance costs, which are around 80% lower.
SANY also presented two other popular machines on the stand, the SY26U with Stage V Yanmar engine and load sensing hydraulics and the 8.8-t SY80U compact excavator, which impresses with its compact design, low fuel consumption and outstanding operator comfort. Both machines have proved to be a huge hit with plant hirers and owner operators alike.
All excavators come with SANY’s industry leading five-year / 3,000-hour warranty as standard for complete peace of mind.
Leigh Harris, Business DevelopmentDirector for the UK and Ireland said: “It’s been terrific to kick off our 2023 events calendar. Following our success at the show last year, we had high hopes for this year’s event and it hasn’t disappointed us.
“It’s been the perfect springboard to unveil our brand new electric excavator to the UK market and it’s been great to see the amount of interest the electric SY19E and the other machines on our stand have generated.”
Pinnacle Platforms is the sole GB distributor for Sinoboom Aerial Work Platforms. Founded just two and a half years ago, the rapidly growing company is headed by Access Rental seniors Tim White and Wayne Lawson, both of
and providing customer solutions and satisfaction.
The company was pleased to attend and participate at its second consecutive Executive Hire Show.
Tim White said: “The past two years have been very pleasing. More pleasing, however, is that every single customer became a repeat customer, with the quality of the equipment and service feedback as the abiding factors. We like that, as we work hard to support customers with availability, warranty, service and on time deliveries.
“The business has been fortunate to have the supply of plentiful stock to match the growing demand. This has been achieved through our agreement with Sinoboom at both a global and
European level, with what can only be described as outstanding logistics from Sinoboom BV in Holland.”
Pinnacle Platforms has been prominent on the UK exhibition scene. After a highly successful Vertikal Days and successive Executive Hire Shows, the business believes in showing its products with the aim of introducing the brand to potential customers, allowing the build quality and product functionality to do the talking.
At this year’s Executive Hire Show Pinnacle Platforms, showed three products ideal for the rental market. There is an increasing demand for vertical mast lift products in applications calling for compact machines capable of operating in congested industrial,
manufacturing sites, warehouses and retail settings. The ML340EJ (ML10EJ), with its 10.3 m working height, offers a zero-tail swing with ‘up-and-over’ outreach –just the solution UK hirers are looking for.
Battery autonomy is critically important on high duty-cycle applications. This Sinoboom ML10EJ has a highly efficient electric drive, which greatly improves run times, a feature much appreciated by contractors working extended shifts.
The machine is fully electric and powered by four 6 V, maintenance free, AGM batteries, delivering zero emissions, a quick charge and long run life.
To complete the array, Pinnacle Platforms showed two championship contenders in the competitive 19-foot (5.8 m) scissor lift category – the 1932SE and 1932ME. Pound for pound, both machines punch above their weight, providing knockout results for UK hirers.
The 1932SE is a little more compact and 365 kg lighter than the 1932ME, providing greater manoeuvrability and flexibility on site, in addition to being nimbler when being loaded and transported. With all the efficiencies hirers will recognise when additional machines can be transported, reducing hefty fuel bills and improving rental margins.
Sinoboom has worked hard to ensure that the machines that enter UK hire fleets will stay looking good for longer. A quality electrophoretic paint finish gives a high hardness impact, reducing body wear and corrosion; fork pockets ensure safe and impact free loading and the Sinoboom bumper rail protects bodywork, paint work and decals. All this delivers improved utilisation, protecting hirers’ reputation and increasing rental earnings while delivering best in class residuals.
Pinacle Platforms’ Operations Supervisor Harry McLoughlin in ML340EJ BasketHaving previously attended the Executive Hire Show, expectations were high for meeting connections old and new and launching UK designed and manufactured rechargeable site lighting. We were not disappointed.
There was a steady stream of attendees visiting the stand and being dazzled by the new StratoStar, a rechargeable 115,000-lumen tower light with up to 12 hours of runtime. Visitors were keen to get details of the Pulsar Navstar, an innovative set of 10 rechargeable sequential lights that have extensive uses, from hazardous demarcation to magnetically attaching to booms and other plant hire equipment. With a runtime of 72 hours, colour plus flashing modes options and being highly visible from over a kilometre away, these definitely caught the prospect’s attention.
Conversations this year were driven towards sustainability, focusing on GenZero, our new range of battery powered generators. With an overnight charge, these compact units provide zero emissions or noise pollution, a portable solution to sites for tools, lighting and welfare units. Many sites are moving to battery only tools, so this resonated with both procurement and site
managers when looking for futureproof options. Available in three output sizes and optional 110 V or 240 V, customers were eager to place orders.
Attendees were also drawn to our new LunarStar high-performance and energy-efficient site lighting range, which is available in 110V or 240V options. These mains or generatorpowered multi-directional lights are ideal for lighting up any work site or large area, they are economical to run, quick to set up and easy to maintain.
Also high on the agenda was NexSun solar powered lighting range. We have many options from small ambient lighting to powerful 5,000 lumens floodlighting. Discussions were had with health and safety in mind for providing
night site lighting with no associated running costs.
The emphasis of Nightsearcher is developing robust and industry specific lighting, working in collaboration with both construction and hire to research and develop new products.
All products come with a three-year warranty that is extendable to five years when registered on the company website. Along with being a UK manufacturer, this gives peace of mind when investing in products for both site use and hire.
The exhibition organisation and facilities were excellent, providing a great boast to opening new doors in the industry.
Every year too many workers are killed or injured through unnecessary contact with plant and machinery on construction sites and beyond.
Zonr plant proximity solution has been designed and built using Pathfindr’s technology expertise in collaboration with construction safety experts. It uses Ultra-Wideband (UWB) signals to create a virtual barrier around dangerous plant and equipment.
• Super simple and quick to deploy.
• Base easily transferable between vehicles.
• Logs and locates all identified incursions.
• No hard wiring for exterior equipment.
For a free, no obligation demo go to Zonr.com
Thwaites is a stalwart supporter of the Executive Hire Show, exhibiting at every show since the event was launched back in 2007.
Thwaites designed and built the world’s first ever site dumper back in 1951, a major product innovation of the day that remains an on-site essential 72 years later.
This year Thwaites presented visitors with an exclusive look at an all new, all electric, 3-t dumper. Designed specifically for the hire and contractor market, the machine has been manufactured to offer the same build quality, robust design and engineering excellence that is ubiquitous across the Thwaites range. The latest product to enter the dumper range was, as ever, built at the company’s Leamington Spa factory.
The 3-t electric machine displayed was an advanced concept machine, with the go to market version being available later in 2023.
Four maintenance free, longlife, lithium-ion (dry-cell) batteries, operating at 48 V, are fitted. Each
battery is rated at 5.75 kWh, providing the power to drive the machine, with two highly efficient electric motors giving the operator the control and manoeuvrability expected from a Thwaites dumper.
The electric drive dumper has a similar unladen weight to the diesel/ hydrostatic version. The main battery pack and driveline components now sit low in the rear chassis, lowering the centre of gravity, further improving stability.
Critically, the battery pack will complete a full eight-hour shift of ‘normal site operation’ from a single charge.
The standard on-board 3.4 kW battery charger can charge the pack
from 0-100% in eight hours. Optional off-board chargers rated at 7 kW (singlephase) and 22 kW (three-phase) have charge times of four hours and two hours respectively.
Thwaites General Sales Manager, Andy Sabin said: “We were delighted to showcase the new, all electric dumper, as the demand for cleaner alternative fuel sources grows, we are keen to ensure we offer a quality product that delivers for our customers, their clients and the environment.” The machine, which was positioned as the Thwaites centrepiece, was flanked by the hirer’s favourite onetonne hi-tip dumper.
In addition, on day one of the show Thwaites introduced a unique artist in residence, Ian Cook of Popbang Colour Studios. Ian, who employs many artistic methodologies, impressed visitors to the stand with his continual line drawings of the 1-t machine.
On day one of the show a deal for 50 x 1-t Hi-Tip machines was signed by Thwaites distributor, BTE Plant Sales and leading UK rental company Hirebase.
Andy Sabin concluded “We are delighted to be able to offer this all electric three-tonne dumper for consideration at this year’s Executive Hire Show.
“The machine will provide for the rental market, a cleaner, quieter, alternative, giving contractors options to use the machine in more urban refurbishment settings. In addition, the new, all electric dumper is compliant with the growing number of authorities and bodies that operate low emission zones.”
Rokbak is bringing a pair of its haulers and a strong team to CONEXPO in Las Vegas to show exactly how the brand has become a major mover in both the US and global market. Rokbak haulers will be on display for the first time ever at a North American tradeshow when the RA30 and RA40 arrive at CONEXPO 2023 in Las Vegas, Nevada, from 14 to 18 March.
The Scottish articulated hauler manufacturer is bringing both models to the largest construction show in North America, providing attendees with the chance to get up close and personal with the earth-moving machines and demonstrate exactly how they can offer grounded ‘Roksolid’ performance stateside.
Paul Douglas, Managing Director of Rokbak said: “We cannot wait to get back to CONEXPO and give the RA30 and RA40 pride of place on our stand. We’re looking forward to getting as many attendees interacting with what we’ve got lined up as possible, as well as introducing people to our knowledgeable team who are keen to show off our robust and hardworking haulers. Rokbak will be there to show customers first-hand the quality our machines and why we’ve become known as one of the most reliable and trusted articulated hauler manufacturers in the market.”
The strength of the Volvo Group
Rokbak will be located at Booth F8926 in the Festival Grounds, together with fellow Volvo Group companies Volvo Construction Equipment and Volvo Penta. CONEXPO will be the perfect opportunity to highlight the machines’ abilities to benefit construction projects, talk to customers about how the haulers deliver new benchmarks in both performance and total cost of ownership, and reinforce the company’s commitment to sustainability and journey to net-zero as part of the Volvo Group.
With sustainability in mind, the Rokbak event booth materials are all recycled or reusable. Two 40 ft (12 m) customised shipping containers, adorned in the recognisable Rokbak
aesthetic, will be used for meeting rooms and product information displays. Following the event, these will be shipped back to Motherwell for reuse at future events.
Product experts will be ready and waiting to discuss the technical capabilities and key aspects of the haulers, welcoming everyone to the booth where there will be merchandise giveaways and competition prizes up for grabs throughout the event – as well as plenty of refreshments.
Robert Franklin, Rokbak’s Director of Sales – Americas said: “The US is leading articulated hauler demand globally Rokbak is seeing huge demand for its RA30 and RA40 articulated haulers in the US, with huge infrastructure spend. There is a lot of construction activity at the moment around house and road building, so we are keen to meet with customers and potential customers at CONEXPO and discuss how the RA30 and RA40 can help with these projects.”
It was to the USA that Motherwell based Rokbak’s first sand-coloured machines were delivered following the rebrand in September 2021. A pair of RA30s were sold to earthmoving, utility and clearing company Linco Construction of Houston, Texas, via Easton Sales and Rentals, to assist with earthworks, underground utility and clearing work. Most US dealers went on to confirm orders within the first few months.
Outdoor stand D2239
Goldhofer is setting new benchmarks in innovation at the upcoming CONEXPOCON/AGG
At CONEXPO-CON/AGG
Goldhofer is presenting no fewer than four highlights for the American market. An STZ-VL4 (3+1) lowboy trailer with flip axle and deck inserts, the P12 PLUS highway trailer recently introduced specifically for the US market, and an ADDRIVE 2.0 combined with the FTV 850, the global leading wind turbine blade carrier built by Goldhofer.
Time is key in the gruelling everyday world of road transportation. In this context Goldhofer’s STZ-VL double drop semitrailers are a convincing choice in all respects. They are designed for fast and easy front-end loading and, in spite of their low deadweight, will reliably handle very high payloads. An additional pin-on flip axle brings greater flexibility and payload as well as the adaptability to operate across state lines with differences in heavy haul regulations.
The Goldhofer P12 PLUS
The ultimate in flexibility for a wide range of transportation operations – that is the new P12 PLUS highway trailer. It offers decisive advantages for successful
operations with a modern fleet. The vehicle can be adapted to handle the various loads that go with everyday heavy haul operations and thus ensures optimum fleet capacity utilisation. In the 12-axle version, the P12 PLUS offers a maximum payload of up to 127 t, with a 12-t axle load. It also has the flexibility to be operated in a nine or six axle version. The vehicle’s universal character is underscored by an extensive range of accessories including loading decks and turntables for transporting long and heavy loads using the steerable dolly.
Jerry Rothwell, Director of Sales –North America says: “A wide range of jobs with just one vehicle – Goldhofer’s P12 PLUS – represents our wealth of experience with the successful THP series transferred to the highway transportation market. Thanks to its variability, heavy haul companies can now ensure punctual delivery of diverse special and everyday loads across state lines with just one vehicle.”
The ADDRIVE 2.0 is an intelligent solution that combines the advantages of a towed heavy-duty module with those of a self-propelled module. With its enormous driving force, it can support the tractor up to a speed of 50 km/h (31 mph). The drive unit then disconnects automatically and can be reconnected at lower speeds without stopping. With the ADDRIVE 2.0 it is possible to switch from the supporting function for road transportation to off-road operation as a self-propelled vehicle. This means savings in terms of time and costs and greater efficiency and flexibility for every fleet.
Jerry Rothwell says: “With its various travel modes, it can be towed, used to deliver additional power to the tractor unit on the road and also operated independently as a hydrostatically
powered self-propelled transporter. In countless combinations worldwide, more than 60 units are providing outstanding service for our customers, enabling transports that would otherwise have been much more complicated at a higher cost to complete.”
The FTV 850 blade carrier
Goldhofer has been a pioneer in the field of wind turbine blade carriers since 2013. The FTV 850 is designed for maximum safety and stability for wind turbine transports.
This incredible success story began with the FTV 300. Today more than 60 units in different versions are in operation around the world, helping to make power generation increasingly sustainable. This is thanks to an intelligent design concept that makes light work of difficult routes and minimises the need to make changes to the roadside infrastructure. As a result, narrow passages in built-up areas, forests and winding roads present no problems to this manoeuvrable combination. The largest blade carrier to date can be used not only in the basic width of 3 m but also in split combinations with a width of up to over 4 m. Depending on the configuration, the latest generation of wind turbine blades requiring a load moment of up to 850 metre-tonnes can be picked up and transported on a highly flexible basis.
The Liebherr booths at CONEXPO 2023 offer space for more than 30 exhibits on a total exhibition area of almost 5,600 m². The area was enlarged by approximately 670 m² due to the addition of a demo area, where Liebherr will show its machines in action for the first time. Numerous new products and developments from the areas of construction machines, cranes and material handling technology are on display. In addition, Liebherr presents the latest innovations from its components product segment in the South Hall.
The TA 230 Litronic from the new generation of articulated dump trucks has been redeveloped from scratch. The machine was unveiled to the US market during Liebherr USA’s Customer Day event in May 2022 and is now introduced to the rest of the North American market at CONEXPO 2023.
With the two material handling machines, the LH 30 M Industry Litronic and the LH 60 M Industry Litronic, Liebherr will present two models specifically designed for scrap handling. The handling of scrap steel and other metals is one of the toughest applications in industrial material handling which requires high-performance and economical material handlers.
The railroad excavator on display, the A 924, represents an example for maximum efficiency with very high flexibility. The machine, which is making its North American debut, is a dualpurpose machine that can be used both
on the road and on tracks. The rail undercarriage is mounted on both sides of the undercarriage. With an operating weight of 21,800 to 25,000 kg, the A 924 Rail Litronic combines aboveaverage performance with high economy and meets the requirements of Tier 4f emissions.
Likewise, Liebherr’s Generation 8 crawler excavators have proven as top performers since their market launch in the USA at CONEXPO 2020: The machines with proven technology have fully established themselves on the US market. The R 924 and R 945A feature higher engine power, a larger counterweight in conjunction with higher bucket capacities and increased digging and pulling forces – special characteristics of the Generation 8 crawler excavators compared to their predecessors.
The PR 766 G8 is also premiering in the US. The crawler dozer model, which further expands Liebherr’s Generation 8 fleet, comes with an operating weight of up to 54,300 kg and High Drive, the proven and tested undercarriage for heavy mining applications. As the only crawler dozer with hydrostatic drive in the 50-t class, the PR 766 offers maximum efficiency, productivity and safety.
The new 36 XXT truck mounted concrete pump comes equipped with the advantages of a new five-part folding boom with the Powerbloc drive unit and the semi-closed oil circuit. The 36 XXT is a versatile machine including multiple comfort and safety enhancing factors, such as ergonomic access steps and simplified accessibility. An extremely compact assembly with no
boom overhang at the rear ensures high manoeuvrability in confined spaces. A major highlight of the new 36 XXT is Liebherr’s newly developed “Powerbloc” pump drive unit that is characterised by the fact that all hydraulic switching and measuring elements are fully integrated.
Liebherr´s mobile and crawler cranes will present the new LR 1400 SX, extending its range of crawler cranes. For CONEXPO, the LR 1400 SX is fitted with a 41 m main boom and a 44 m luffing jib. With the compact transport weight of 46 t, the complete crane can be transported easily between jobsites. Whether expanding the infrastructure with bridges or tunnels, constructing stadiums or factories with steel or precast concrete elements, working in the energy sector or lifting work on high buildings –this versatile and highly efficient machine is useful in the most diverse work applications.
The LTM 1100-5.3 is a mobile crane that takes mobility, economy and performance to a new level. It offers a powerful 62 m telescopic boom and carries up to 16.9 t of ballast with a 12 t axle load on public roads. The new crane also provides economical mobility worldwide as it can travel with an axle load of only 9 t.
Flexibility and economical worldwide transport also characterise the LRT 1130-2.1. As the most powerful twoaxle rough-terrain crane with longest telescopic boom on the market, this crane is especially adapted to the needs of the US-market. The LRT 1130-2.1 has a maximum lifting capacity of 130 t and extends Liebherr’s range of rough-
terrain cranes at the top end of this segment.
For the first time at a trade show in North America the product segment tower cranes will present the 470 EC-B, its largest flat-top crane in steel rope design. The top-slewing crane excels with a maximum lifting capacity of 16 t or 20 t. From transport through assembly to operation on site: this Liebherr crane meets all the demands of a modern fleet.
This also applies to the 125 K from the K crane series. The fast-erecting crane offers maximum lifting capacity with minimum space requirements. With a radius of 55 m and a hook height of up to approximately 66 m, the Liebherr 125 K is currently the largest fast-erecting crane on the market. A well-thought-out assembly system and low logistical costs make the Liebherr fast-erecting cranes particularly useful for shorter projects.
From the deep foundation machines segment, visitors will be able to experience the LRB 23 piling and drilling rig and the LB 30 unplugged drilling rig at the trade show. These two machines are characterised by maximum reliability and safety thanks to digital assistance systems. Ground Pressure Visualisation, for example, calculates the machine’s current ground pressure in real time and compares it with the specified safety limits. The Kelly Visualisation makes locking the telescopic rails of the Kelly bar much easier. The drilling assistant enables automated drilling during the concreting process. Automatic obstacle recognition and remote control are used to recognise attachments as well as simplify the loading process during transport and assembly. All of these systems contribute to time savings and higher machine availability as well as a significant increase in safety during operation.
Liebherr Tower Cranes is presenting its new digital service portfolio for the first time in North America. Liebherr supports customers with its “Plan and Analyse” concept for comprehensive planning and spot-on analysis. The dimension “Plan” covers the digital planning of construction sites, including the digital design and selection of crane models based on crane information models. These then form the basis for a precisely fitting crane selection that best meets the requirements of the respective construction site. Liebherr’s digital Site Monitoring enables efficient
“Analysing” processes as: relevant crane data can be easily recorded, displayed and analysed. This information also gives site managers and construction planners a reliable overview of efficiency and construction progress.
The product range of Liebherr attachments is specifically designed and customised for the respective application and optimally configured for the machine size. During CONEXPO, a range of Liebherr´s attachments will be demonstrated on both, the R 914 Compact Litronic and A 924
Rail Litronic excavators. Liebherr will demonstrate its fully automatic quick coupling system Solidlink during live shows in a dedicated demo area. Solidlink, formerly known as LIKFUIX, is a hydraulic quick coupler combined with an automatic hydraulic coupling system developed by Liebherr. Here, Liebherr will demonstrate how Solidlink allows both mechanical and hydraulic attachments to be changed quickly, efficiently and safely from the operator’s cab. Application possibilities and utilisation of the machines can
be increased by up to 90 % with this solution.
Liebherr is presenting its new medium-sized wheel loaders, equipped with a wide range of digital assistance systems. With a significant increase in performance compared to the previous models, the new machines are prepared for demanding applications in various industries such as mining, recycling or the timber industry. The portfolio of intelligent assistance systems for maximum reliability and safety includes, for example, active person detection with brake assist or the revised Skyview 360° camera system for an optimal all-round view even in poor visibility conditions. Moreover, Liebherr shows several large wheel loaders of the XPower® series at the booth. Thanks to their power-split driveline, these wheel loaders are known for their tremendous fuel efficiency.
The components product segment will also be presenting its digital bearing clearance monitoring (BCM) for slewing bearings. The integrated wear measurement system enables optimum remote monitoring of the slewing bearings in various applications such as mining and material handling or maritime applications. The BCM system can be used to measure bearing wear in axial and radial directions, as well as tilting clearance. These diagnostics ensure flexibility in measurement, reduced downtime and lower costs in maintenance.
As a globally active family-run company, Liebherr bears a great responsibility towards society and the environment. That is why Liebherr is working on the continuous improvement of work safety.
This includes, for example, comprehensive work on modern assistance systems for earthmoving machines and cranes, which relieve
the machine operator and thus make a significant contribution to work safety on the construction site. Under the slogan “Safety first” the mobile and crawler crane segment will be demonstrating the latest safety equipment and assistance systems that set new standards, using its LRT 1130-2.1 on display as an example.
One of the highlights is the VarioBase® variable outrigger base developed by Liebherr, which is used as standard on all Liebherr-LRT-cranes. With VarioBase®, each individual crane jib can be extended to any length. Crane operation is controlled by a load moment limiter, which calculates the maximum lifting capacities precisely for the current situation.
Liebherr is working to continuously reduce the ecological footprint of its products throughout their life cycle, from development to disposal. The group already offers its customers numerous ecologically optimised products, some of which operate with zero local emissions. Visitors will be able to experience the LB 30 unplugged from the deep foundation machines product segment. For battery operation and thus local zero emission, the charging cable only has to be unplugged and reconnected to the construction power supply for unrestricted operation. The battery is designed for an operating time of four hours in Kelly mode. Whether in battery or socket operation, the drilling performance remains unchanged.
Liebherr Components will present a prototype of its hydrogen engine, the H964, employing a direct hydrogen injection developed by Liebherr. This technology is particularly well suited for dynamic heavy-duty applications, since it offers high power density. Durable against dust, dirt and vibrations, as well as other harsh environmental conditions, the direct injection is comparable to the diesel engine in terms of performance and durability.
Rammer, the world-renowned hydraulic hammer brand, is excited to announce its participation at this year’s CONEXPO exhibition. As a leading manufacturer of rock-breaking machines, Rammer has been providing reliable, productive, and durable solutions for carriers of all sizes, ranging from 0.6 to 120 t-operating weight class. The company’s dedication to quality and safety has been a top priority, and this year’s show promises to deliver on that promise with the unveiling of its highly anticipated demolition tool product line.
The Rammer team will be located at booth 20439 in the central hall, where they will showcase their new product line. The demolition tool product line consists of several powerful tools, such as pulverisers, shears, grapples and more. With Rammer’s long-standing reputation for quality and safety, visitors to the booth can expect the same level of excellence and peace of mind that they’ve come to expect from Rammer products.
As a leading hydraulic hammer brand, Rammer has established itself as a top choice for construction equipment dealers and operators alike. This year’s show promises to be no different as Rammer introduces its latest product line and product upgrades that aligns with its 45 years of hammer expertise, quality and customer support. The company’s commitment to providing a smooth and reliable purchase experience is evident in its demolition tools, which are designed to be easy to use, durable and built to last.
Visitors to the Rammer booth can expect to see another new addition –
its smallest hammer range, the RAMI hammer line. This year’s show is a great opportunity for construction equipment dealers who seek a one-stop partner for demolition and recycling tools. Rammer’s attachment tools are the premium solution that enables dealers to simplify their daily operations and provide their customers with the best possible experience.
Rammer’s participation at this year’s CONEXPO exhibition is an exciting opportunity for attendees to learn more about the company’s highly anticipated demolition tool product line. With a reputation for quality, safety and reliability, visitors can expect to see a wide range of powerful
and durable tools that are built to last. Make sure to stop by booth 20439 in the central hall to learn more about Rammer’s latest products and innovations and discover why it is the hydraulic hammer brand of choice for dealers and operators around the world.
The stage is set for Caterpillar’s largest exhibit to date at CONEXPO-CON/ AGG, where the company will highlight its latest products, services and technologies while paying tribute to those who build the world’s infrastructure. The company’s 6,500 m2 outdoor demonstration arena will anchor the massive display known as Operator Stadium in the expo’s Festival Lot.
New Caterpillar Technology, Services and Sustainability hubs provide visitors the opportunity to look beyond the iron for ways to increase operating efficiencies and improve machine uptime. Visitors will find new and current models and battery-electric machine prototypes at the show.
The latest equipment
The extensive Cat® equipment display in the Festival Lot includes more than 30
machines, including model unveilings and battery-electric model prototypes with charging stations. Visitors will see two main equipment demonstrations each day; one focused on the latest Cat Technology, and one that will spotlight the company’s full equipment lineup. Caterpillar will also be providing unique daily spotlight demonstrations that will take a deep dive into key industry topics including improving fuel efficiency and jobsite efficiency, the evolution of technology and convenient, scalable solutions.
The new Cat 50 medium wheel loader on display offers premium performance and simple-to-use technologies to help boost operator efficiency and increase productivity, while extended service intervals help lower maintenance costs. Visitors will be treated to a preview of the Next Generation Cat 926, 930 and
938 small wheel loaders – slated for production in late 2023 – which feature new technologies designed to make work easier, a reimagined operator environment and extended service intervals.
For paving contractors, the halflane Cat PM822 cold planer features integrated Cat Grade technology and the latest System K rotor options that deliver performance, productivity and cutting precision. With its compact size, exceptional mobility and easy transport, the Cat AP455 Mobil-trac™ asphalt paver offers great features for both large and small contactors when paving urban streets, parking lots and rural roads. Furthermore, an exciting new market disrupting three-dimensional screed plate with modular fastening system improves mat density and smoothness while reducing screed plate change time by up to 80%.
latest power Caterpillar Industrial Power Systems Division will exhibit a wide and rapidly growing portfolio of high-efficiency Cat industrial power solutions in booth S84329 in the South Hall. The exhibit includes the unveiling of a new high power internal combustion engine, as well as the leading-edge lithium-ion battery technologies under development. Engines on display, such as the C3.6 IPU, C7.1 and C9.3B, meet EU Stage V, US EPA Tier 4 Final emission standards and are compatible with biodiesel up to B20 and hydrotreated vegetable oil (HVO) to EN15940, to help customers power a better, more sustainable world.
The booth will also showcase Caterpillar’s technical services and market expertise leveraged by the global Cat dealer network to maximise the efficiency and extend the lifecycles of off-highway equipment, including Cat remanufactured and service replacement engines.
Caterpillar offers a range of service options that are easy, convenient, flexible and sustainable. The new Cat Central app is the latest tool for convenient access to genuine Cat parts and support. This on-the-go experience makes it easy for customers to find and order Cat parts, scan and shop a specific asset instantly and find answers to maintenance and support questions. Another new service-related solution is the new Cat SIS2GO app, which takes the guesswork out of maintaining, troubleshooting and repairing Cat equipment. Both apps are available on Windows, iOS and Android platforms.
The Services Hub is located in the Festival Lot and will include Caterpillar subject matter experts (SME) who will help guide attendees through several maintenance options for Cat equipment. Customer Value Agreement (CVA) options offer easy ownership plans customised to fit a customer’s business needs to extend equipment life and maximise the investment. Cat Certified Rebuild programmes return end-of-life machines, systems and components to like new condition. Cat Reman products bring new life to assets with like-new performance at a fraction of the cost of buying new. Cat Self-Service Options deliver convenient, simple parts ordering and machine repair support for those who prefer to do their own service.
Team members from Cat Financial will be available to discuss the latest leasing and financing programs, including Cat Card, as well as extended protection packages to help secure customers’ investments. Whether they are looking for new or used Cat machines or for repair/rebuild options to keep their current machines operational, Cat Financial experts will help customers make the right decision to support their business – no matter how large or small.
The Caterpillar Technology Hub in the Festival Lot will offer attendees the ability to experience a range of new and existing Cat technologies – VisionLink, Cat Command, VisionLink Productivity, Cat Detect, Cat Grade and Cat Payload. Caterpillar SMEs will be on hand to assist each customer in finding a scalable solution designed to fit the business’s needs and budget. Its centrepiece exhibit, the “Looking Glass” cube, displays and interactively showcases the five key capabilities of the new Cat VisionLink® application – Geofence and Location, Fuel Theft Alerts, Diagnostics, Idle Time/Fuel Burn, and Maintenance. An interactive wall
invites visitors to explore the full suite of VisionLink capabilities for both Cat and non-Cat equipment and non-machine assets. The hub’s multiple Cat Command stations allow attendees to remotely operate Cat machines located more than 400 miles away at the Tinaja Hills Demonstration and Learning Center. They are positioned to allow attendees to better experience and learn more about the Command for Dozing, Excavating and Loading technologies. One of the Command stations allows visitors to try the “Strike Pay Dirt Challenge,” where participants remotely control an excavator to win a prize.
The Caterpillar Sustainability Hub in the Festival Lot will spotlight fuel efficiency and alternative power sources; technologies to fit every operation and budget; and parts and service designed to make uptime fast and easy. Customers will also learn about sustainability benefits they can choose today and plan for tomorrow.
Outside the Sustainability Hub, exhibit attendees can view components of Caterpillar’s
total site solution for the energy transition, including four batteryelectric machine prototypes – the Cat 301.9 mini excavator, 320 medium excavator, 950 GC medium wheel loader and 906 compact wheel loader – in addition to AC and DC charging solutions. The Caterpillardesigned batteries powering these battery-electric machines are built on lithium-ion Cat technology with a modular design that offers flexible configurations across multiple applications.
In a quest to prove that they are the best, more than 10,000 operators representing more than 32 countries around the world registered to compete in the 20222023 Global Operator Challenge. From 3,500 participants in the first round of local competitions to 84 reaching the regional semifinals, nine of the world’s best equipment operators will demonstrate their advanced skill, precision and stamina in hopes of being named the Global Operator Challenge Champion. The nine finalists competing in Operator Stadium at CONEXPO are:
• Pontus Eriksson, representing Zeppelin Sweden,
• Sebastian Behr, representing Zeppelin Germany,
• Łukasz Mokrzyński, representing Bergerat Monnoyeur Poland,
• John Schiedeck, representing Holt Cat (USA),
• Matt Ferris, representing Empire Cat (USA),
• Fernando do Nascimento, representing PESA (Brazil),
• Masato Imai, representing Nippon Caterpillar (Japan),
• Patrick Doheny, representing William Adams (Australia),
• Nick Thompson, representing CavPower (Australia).
The finals kick off on Tuesday morning, 14 March, immediately following the expo’s grand opening ceremonies. Throughout the competition, the skills of the finalists will be put to the test in three identical challenges – excavating, loading and hauling/manoeuvring the equipment through a variety of obstacles. The champion is set to be crowned on the afternoon of the same day.
All CONEXPO-CON/AGG attendees are encouraged to attend the Global Operator Challenge Finals to see first-hand the new equipment, technologies and services on display in Festival Lot exhibit, F9127. The Finals will also be broadcast live on cat.com.
Plantworx 2023 will provide a platform for startups engineering the future, connecting them to some of the UK’s most influential companies, potential investors and media. The BIG Ideas Zone will be a showcase and forum for smaller companies (SMEs) with BIG Ideas.
Plantworx wants companies with products, technologies, or services new to the construction industry that can make a Big IMPACT on the sector, offerings that can improve efficiency, sustainability, safety, or security.
The BIG Ideas package comprises:
• An exhibition pod under the BIG Ideas banner close to the main entrance of the show,
• Participation in the VIP preview event, with trade press and invited contractors, specifiers, influencers and opinion formers (on 12 June),
• Starred listing on the Plantworx website and in the Plantworx App,
• Invite and tickets to the CEA Conference and Awards evening (30 March), providing excellent networking opportunities with key decision makers.
The selection process Plantworx organisers will determine which companies have products, technologies or services appropriate to the Big IDEAS
promotion. For further infomation, contact rob.oliver@plantworx.co.uk or louise.carney@plantworx.co.uk in the first instance.
CEE (Construction Equipment Events) Director Rob Oliver said: “We are looking for startup companies with products, technologies or services new to the construction industry that can make a Big IMPACT on the sector, improving efficiency, sustainability, safety or security. We are encouraging companies who think they fit the criteria to get in touch to discuss the discounted package.”
The package is being made available to Big IDEAS companies for £395 plus VAT (the package is worth in the region of £4K plus VAT).
About Plantworx
Plantworx 2023 will be the show where emerging and disruptive technologies will feature alongside construction equipment, innovation, technology products and services. The show remains the UK’s biennial showcase for the
construction sector – and will lead visitors into the future of construction.
With a combination of live demonstrations and the latest in machine technology and support products, Plantworx offers a valuable experience for construction sector professionals.
Over 350 exhibitors are expected to be present at the show with around 15,000 visitors over the three days of the show. Confirmed exhibitors include Caterpillar, Hitachi, JCB, Hidromek, SMT (Volvo), Takeuchi, SANY, Sunward Europe, Yanmar, Liugong, Mecalac, John Deere, Avant, Kubota, Doosan and Bobcat and BOMAG. You can also expect to see attachment specialists Auger Torque and BPH Attachments and leading tiltrotator companies including Engcon and Steelwrist.
Handling and lifting specialists Manitou and Merlo have also confirmed, alongside remote control demolition experts, Brokk, which will be at the event showing the company’s latest demolition robots. The full exhibitor list can be found on the Plantworx website.
DEMOLITION/CRUSHING/MIXING/WASHING/ SCREENING/RECYCLING/SEPARATION
To hire, buy or arrange a demo:
The Construction Plant-hire Association (CPA) has announced that the CPA Conference 2023 will be hosted on Thursday 9 November and the theme will be Facing the Challenges in the Plant-hire Sector. The one-day event will be held at the Heart of England Conference and Events Centre in Fillongley near Coventry.
The CPA Conference is organised by the CPA, the longest established trade association for the plant-hire sector in the UK. The CPA has more than 1,800 members, who supply 85% of hired plant to the construction industry. Delegate tickets can be booked online at www.cpa.uk.net/ events/cpa-conference-2023. Tickets can be purchased for the advance delegate booking rate of £50 plus VAT (reduced from £75 plus VAT) until 31 March 2023 by entering the discount code TS2023.
CPA Chief Executive Kevin Minton said: “We felt that this year’s conference should address the core issues that are of
importance right now to CPA members and the wider construction industry, such as the rising cost of fuel and energy, critical supply chain shortages and the difficulties of attracting new recruits to the industry. We’re in the process of devising a packed, topical agenda with panel debates and case studies to allow delegates to come away with a deeper understanding as to how they can tackle some of the challenges they currently face.”
The CPA Conference 2023 will be the eighth CPA Conference. Over the years, the conference has become an essential event for senior figures in the plant-hire sector, with speakers from organisations such as Costain, the then Department for Business, Energy and Industrial Strategy (BEIS), the European Rental Association
(CRA), GAP Group, HS2, Highways England, JCB and Sunbelt Rentals.
This year’s panel debates will be steered by event convenor Merryn Myatt, a former BBC news presenter and journalist who has hosted previous CPA Conferences to great success.
As well as attending the conference, delegates will also have the opportunity to visit exhibitors from many of the UK’s leading construction plant equipment manufacturers, suppliers and construction services providers.
Peter Beach, Sales and Marketing Manager at Genquip Groundhog said: “As a business, we have attended and exhibited at the CPA Conference for several years and found it to be a great networking opportunity with attendance from senior figures in the plant-hire sector. The panel discussions are relevant and engaging and I was pleased to be able to contribute to one of the debates last year which discussed ESG (Environmental, Social and Governance) in the construction and planthire sector.”
Exhibition space has proved so popular at previous CPA conferences that it has been a sell-out. To exhibit at the CPA Conference 2023, please call Lisa Collins on 07968 840 390 or email: lisa@lisacollinscommunications.co.uk
Name: Andrew Little
Job title: Sales Manager
Role: UK Sales
Time served at Rototilt: Two years
Previous experience: A number of years in aftermarket, product management and sales at companies including JCB, Liebherr, Terex, Kinshofer
A tiltrotator creates opportunities for your excavator and allows you to take on new applications while requiring fewer machine movements. We have a wide range of tiltrotators for excavators weighing between 1.5 to 43 tonnes from the R1, which combines technology with strength normally only found in higher weight classes, to our largest model, the RC9.
The RC Series maximises energy efficiency and improves your operating experience. With the RC™ System control system and the SecureLock™ safety lock, you have a highly adaptable productive tool.
Ergonomic design
When developing RC™ Joysticks, we considered ergonomics and operating experience down to the smallest detail. We kept different hand sizes in mind with the help of modelling, 3D printing and extensive field tests with actual machine operators.
Premium materials give the handles an effective grip and excellent surface quality. The patented 360° angle adjustment, optional FNR and adjustable palm rests ensure you get through long working days without unnecessary strain on your hands, wrists, arms, and shoulders. The angle and position of the buttons and rollers have been calculated to ensure comfortable access when working, without the need to adjust your grip. The handles are tailored to your machine, to provide the optimum operating experience and ergonomics.
Pressure-compensated hydraulics
Tiltrotators in the RC™ series have newly developed pressure-compensated hydraulics. This allows the tiltrotator’s various functions to work independently of each other to provide precise control of tilt and rotation, even if you want to operate these at different speeds. This becomes even
clearer when you are using both functions at the same time. When the tilt function is operating in the maximum position, rotation can continue at the same speed as before. As a result, tiltrotators in the RC™ series provide you with optimum parallel operation, as you do not need to take the speed of rotation and tilt into account. Your operating experience becomes smoother and your movements more controlled, allowing greater precision and better results in all your tasks.
The choice of control system can be one of the most important decisions you make to ensure that your investment will achieve the desired result. Our latest control system, RC™ System, has been developed to transform your excavator and your day-to-day work. This is particularly true alongside our options and system solutions, such as the awardwinning SecureLock™ safety system, the RPS™ positioning solution, as well as the High-Flow Swivel (HFS) and the patented High Flow Controller (HFC) for greater flexibility when operating tools that require a high flow.
Oil has properties that are particularly beneficial for tiltrotators. The worm gear in a tiltrotator operates with significant internal friction, which generates heat. This heat is dissipated by the oil to the entire rotor housing, which is something that does not occur with grease.
One of the secrets behind our technological development is Rototilt’s unique test lab, which we use to evaluate technical solutions. With the help of the test lab, we are well advanced in tribology, or the study of interaction of surfaces in relative motion. One of our latest advances is that we can ensure all preceding production stages have been performed correctly in our high-tech final testing, meaning even better-quality assurance.
Rototilt offers a wide range of options when it comes to elevating your tiltrotator system to new heights. Its load-holding valve (LHV) keeps your load secured, even if the hydraulic system loses pressure, for example in the event of a hose rupture. LHV comes as standard on all tiltrotator models. Our high-flow swivel (HFS) provides even greater flexibility when operating tools that require a high flow. There is also the option of combining with
an electric swivel. Rototilt’s Innovative Lubrication System (ILS) facilitates lubrication and rapidly distributes the correct amount of grease to the right places. Our RPS solution means that, together with an excavation system, you can easily measure and check your work from the cab, resulting in faster decisions, fewer manoeuvres and better results.
Part of Rototilt® QuickChange™
With QuickChange™, part of the Open-S, you can change hydraulic tools automatically without leaving the cab. When you work with QuickChange™ in both the attachment frame at the top and the quick coupler at the bottom, you can disconnect and connect the tiltrotator or switch between different hydraulic tools quickly, easily and safely, depending on which task you have in front of you. You can also mount your tiltrotator directly on the machine and get QuickChange™ functionality for the quick coupler for rapid hydraulic tool changes. The SecureLock™ safety solution is also always included. With a tiltrotator from the RC series, you can always choose to upgrade to QuickChange™ at a later stage.
What is driving reason for the growth of both tiltrotators and fully automatic quick couplers?
First of all, customers are increasingly demanding safer coupling solutions and the demand is coming from all over the world. Parallel to this, legislators are raising the bar for what is considered to be safe. When we launched the Front Pin Lock technology in 2012, we wanted operator and ground personnel to feel safe during work tool changes, as the operator could see when the work tool was in a safe position. Thanks to that, Steelwrist couplers are not sensor dependant and our solutions work equally well with all types of excavators regardless of whether they are small, large, new or used. Today, with thousands of couplers in the field, the result has been a higher safety level and a robust solution cast in steel.
Secondly customer want to increase the efficiency and versatility of their investment and this drives the continuously increased penetration for tiltrotators. The core of the Steelwrist product offering includes quick couplers, tilt couplers and tiltrotators that together with the control system make up the foundation for higher excavator efficiency. This then drives development of new work tools (powered work tools and non-powered work tools) that makes the excavator become a true tool carrier.
Looking into the future, the
Job title: VP OEM Sales and Marketing
Role: Overall responsibility for developing relationships and sales with major excavator OEMs. Overall responsibility for marketing within Steelwrist
Time served at Steelwrist: Less than one year
Previous experience: Close to 20 years with Volvo Construction Equipment. Previous two roles as Marketing Director for Volvo Construction Equipment EMEA Sales Region and before that as Director for Volvo Construction Equipment’s Global Attachment business. I have also worked for the forklift manufacture Linde Material Handling as the Country Manager for the Swedish sales and service organisation
Any relevant qualifications: I was part of the project within Volvo Construction Equipment that prepared and launched the very first factory fit solution for tiltrotators. With this project Volvo Construction Equipment was the first major OEM that offered a factory fit solution for tiltrotators. During this time I gained a lot of experience and knowledge around both various types of quick coupler solutions across the world and overall understanding of the attachment / work-tools business
penetration of tiltrotators will only continue to increase globally, alongside the demand for fully automatic quick couplers. These are the two most significant trends we see and both these solutions are fundamental to drive excavator efficiency. The expansion of MCS (Machine Control Systems) allows for increased automation together with the tiltrotator.
Some facts about quick couplers and the Steelwrist SQ fully automatic quick couplers
A job needs a work tool, and a work tool needs an excavator – not the other way around. That’s the starting point when we think about how to increase your excavator efficiency.
Let’s focus on quick couplers. What is first and foremost crucial with a quick coupler is that you can change the work tool in a safe manner. The demand for productivity is constantly rising and in many applications the need for quick change of work tool is almost continuous, meaning the importance of quick couplers is also increasing.
All Steelwrist quick couplers are based on the S-Type (symmetrical) standard, which is by far the fastest growing standard with increasing penetration across the world. The compact design, lightweight and robustness of the S-type couplers and the fact that they are based on an open standard are some reasons for this.
Unlike so-called “pin-grabbers” there is no risk of picking up a work tool that is not designed for the specific coupler, thus increasing safety. Add to this that the total height of the S-Type coupler is significantly lower than the pin-grabber.
The requirement to be able to change hydraulic powered work tools without leaving the cab is increasing and this is why the demand for fully automatic quick couplers is increasing fast. With Steelwrist SQ technology you can change between hydraulic powered work tools such as breakers, crushers, shears, grapples as well as mechanical work tools in seconds – all without leaving the cab.
Steelwrist Qplus™ is the label we have put on all the improvements we have developed compared to competitor solutions. Higher flow, more uptime and improved serviceability are the main benefits for the operator. With Steelwrist Qplus™ the flow area measures up to 37% more compared to competitor products (depending on coupling size). Steelwrist Qplus™ sealing technology is completely new and significantly more durable compared to competitor products. This will give you more hours in operation before sealings have to be changed. Changing seals in Steelwrist Qplus™ couplings is done fast and easy without need for proprietary and complicated tools.
We believe strongly in open standard
Product name: Steelwrist SQ couplers
Key features: With Steelwrist SQ technology you can change between hydraulic powered work tools such as breakers, crushers, shears and grapples as well as mechanical work tools in seconds
Date released: 2017
Development period: Development of the SQ fully automatic quick coupler began in 2014
Brief specifications:
• Steel cast,
• Best in class hydraulic flow characteristics,
• Locked front pin – maintains the work tool in a safe position,
• Positive lock indicator – green indicates when work tool is in a safe position,
• Negative lock indicator – red indicates when the coupler is open,
• Steelwrist SQ fully automatic quick couplers build on the Open-S standard, making it able to connect to other brands using the same type of oil connection system.
interfaces, so the Steelwrist SQ system is designed to be able to connect with other brands using the same type of oil connection systems, the Open-S standard. With an open standard for quick couplers, machine operators and contractors can more easily choose quick couplers, tiltrotators and work tools from different manufacturers and be confident that they will function together.
How is Open-S contributing to development within the industry?
Let’s compare with recent EU legislation regarding the USB-C standard. The goal here is to give the consumer the freedom to buy solutions with different
brands all sharing the same interface. The legislation also says that the charger should be optional to buy when you by a new device with the USB-C port. Why? If you already have the chargers you need, it is not mandatory to add another one.
With the Open-S alliance we strive to give machine operators and contractors around the world the freedom to combine quick couplers, tiltrotators and work tools from different manufacturers that are following the standard. With a common standard it is easier for industry manufacturers to continue competing with
performance and functionality while still offering customers compatibility. The standard also means that dealers can provide clearer information about which products fit together.
Steelwrist fully automatic SQ quick coupler is designed to be able to connect to other brands following the Open-S standard – the Open-S alliance is a good for both the machine owner and the industry as a whole.
The popularity of these tilty products has grown significantly in recent years, to the extent of Scandinavian style buckets coming off the bespoke category. The most popular and instantly recognisable bucket is the grading bucket.
Everyone carries one of these very versatile tools to cover many different aspects on site. The grader has been shaped to enable it to revolve within the trench it is cutting, allowing more
freedom for the driver to achieve the desired result.
The grader is not as wide as your standard grader, relying on its agility rather than capacity to shift earth. It has no centre bracing and its tapered sides allows it to empty its contents more easily with each load. The cutting edge must be of a very good standard because anything else will be distorted from the stresses.
The bucket becomes a fabulous
shaping tool and is of an optimal length to fill dumpers etc when required. There are many products available to complement the tilty but a few stand out apart from the ever-ready grader. Both the concrete pouring bucket and the pallet forks are massive additions to the tilty. They are ideal for working in confined spaces or working from a static position, in the scenario of mass footings or offloading building materials roadside etc.
The BF60.1 bucket is a patented top-of-the-range attachment from crushing experts and industry leaders, MB Crusher. It’s the perfect tool for crushing on site and is a one-of-a-kind piece of equipment designed to pick up and process material easily while guaranteeing quality and increased production rates.
It’s also packed full of extra features, including an AAA+ advanced hydraulic cooling system, vibration-eliminating
design and it allows you to specify the output size of your material with precision. On top of all of that, for its weight, it also has the widest mouth opening of any crusher on the market –working quicker and saving you time.
This crusher bucket is ideal for a range of applications, including demolition, general recycling, requalification of industrial and urban areas, processing of excavation materials from earth movement sectors,
road works, quarries and mines, environmental reclamation and more.
So whether you have a specific project in mind or are looking to save on-site clearance costs by monetising your on-site rubble, concrete or rock, this MB Crusher bucket has you covered.
Available to hire today from Chippindale Plant’s Excavator Attachment Division with quick delivery, fit and calibration included.
With the flexibility of having concrete wherever it is needed, including areas that are hard to reach and usually inaccessible with a pan mixer, concrete mixing buckets are becoming an increasingly popular alternative to more traditional methods. As you control the volumes and consistency of what is mixed, they are a far more economical option, especially when considering how much downtime there can be waiting for concrete deliveries.
Suitable for excavators, telehandlers, skidsteers and mini loaders we can supply with a mounting bracket to suit your machine. Recently, a popular choice on a TS50 has been to incorporate a 13-t excavator bracket with a Q-fit bracket for JCB telehandlers so that the attachment can be used on both machines.
With a mixing bucket attachment on your excavator you can load, mix and use concrete all without the use of another machine. Sizing of our mixing buckets is largely determined by the weight and lifting capacity of your excavator, skidsteer or telehandler.
Concrete is mixed more evenly and consistently than other traditional on-site methods thanks to the design of the auger, which allows you to push concrete across the bucket width and back by reversing the rotation on the auger. Once mixed, the concrete can then be distributed either directly from tipping the bucket or through the discharge chute underneath. This can be hydraulically operated by an electric control from the cab.
For accuracy into the footings, post holes etc, a pipe that can be attached to the chute to direct flow is supplied. The Hardox paddles of our concrete mixing buckets are replaceable so that when they are worn the operator can grind them off the main shaft and weld new paddles into place.
Perfect for on-site crushing of inert materials and the first of its kind on the market, the MB Crusher Bucket works by taking advantage of the hydraulic system of the excavators, skid loaders, loaders and backhoe loaders to which it is fitted. It has many applications; from building demolitions in general, to the requalification of former industrial and urban areas to the processing of excavation materials, from the earth movement sector to road works, from quarries to mines, from environmental reclamation to applications on rocky soil.
MB crushing buckets are designed to turn your machine into a real crusher. They offer the world’s widest range of crusher attachments with more than 90% market share.
The BF60.1 crusher bucket, despite its compact size and reduced weight, is sturdy and resistant. Agile and powerful, it is MB’s solution for small-scale sites. Its reduced weight and ease of installation allow for access to problematic and difficult-toreach sites such as those in historical urban centres or in high altitude mountain areas.
Key features:
• Crushes all types of inert waste material,
• Crushes materials directly on site,
• Reduces the use of mechanical equipment,
• Avoids disposing of demolition materials by taking them to a dump,
• Eliminates leasing costs,
• Cuts down transportation and management costs,
• Comfortable, simple to use and fast,
• Suited for small and large worksites,
• Allows materials to be recycled, resulting in significant savings.
Worsley Plant starts off 2023 by widening its product offering and strengthening its reputation as the UK’s attachment specialist – your one-stop-shop for all your attachment sales and hires
The company is delighted to announce that it is now an official UK dealer for OilQuick. Its fully automatic quick coupler system means hydraulic attachments can be changed directly from the driver’s cab in just 10 seconds and is ideal for use in the demolition, construction, quarrying industries. The use of innovative highperformance technology in product design and manufacturing, makes OilQuick quick couplers an efficient and reliable choice for customers around the globe.
OilQuick’s first quick coupler for backhoe loaders was launched in spring 1993. By 2021 the Swedish manufacturer had supplied more than 40,000 OilQuick systems to satisfied machine operators worldwide.
OilQuick is an automatic quick coupler system that allows hydraulic work tools to be connected and disconnected from the driver’s cab of excavators from one to 120 tonnes within a few seconds. These could include hydraulic hammers,
pulverisers or shears, sorting grabs, hydraulic magnets, compactors, crushing buckets or tilt buckets.
Operations Director Adrian Nixon said: “We are delighted to have added Oilquick to our range. We already offer the Lehnhoff range of fully automatic quick couplers and will continue to support and sell these throughout the UK.
“However, we appreciated that our customers have a choice, as there are two big players in the quick coupler
marketplace. We needed to offer both brands to complement our growing range of hydraulic attachments.
“We recognise that we need to offer the fullest range for our customers so that they have a one-stop-shop for all their attachment needs, whether they want to buy or hire, available UK wide.
“We predict exciting times ahead for both parties involved in this dealership arrangement and are see this as an extremely positive start to 2023.”
Worsley Plant already offers crushing and screening buckets from REMU and MB, as well as demolition attachments from ROTAR – including grabs, shears and pulverisers. It also offers magnets from Dynaset and more recently added Montabert breakers to its range.
Based on the proven 700i, the new Tesab 700ie hybrid is up to 33% more fuel efficient and reduces operating costs by as much as 70%, while at up to 350 tph, still produces the tonnages of its diesel equivalent.
The 700ie comes complete with an efficient all electric drive that requires less than 20 litres of fuel per hour, with the option to work on mains electricity for even lower running costs.
Packed with new features, the robust 700ie includes reverse crusher operation, custom panel enclosure with integrated air conditioning and 10-inch display control panel with mobile app and remote access. The 700ie can be operated as a standalone unit fed by an excavator or integrated into the Tesab range of secondary crushers and screeners.
Specifications:
• Production rate: 350 tph*
• Max feed size: 700 mm
• Reduction ratio: Up to 4:1
• Engine size: C7.1 Stage 5 with Genset
• Pre-screen: Yes
• Transport height: 3,400 mm
• Transport width: 2,940 mm
• Transport length: 14,300 mm
• Working width: 5,590 mm
• Working length: 16,080 mm
• Working weight: 47,500 kg
*Dependingonmaterialdensityandsetup
Blue Machinery supplies the industry leading range of Powerscreen crushers and screeners throughout the UK. This includes the high-performance Premiertrak 330 (PT330). The PT330 boasts a
two-piece grizzly feeder for better material flow towards the chamber, with the second section angled. Track mobility gives a quick set-up time and variable crusher speed allows the operator to fine tune the machine and maximise output. A hydrostatic drive system offers versatility and allows the crusher to be operated in reverse, which is
of particular benefit in recycling applications. The PT330 has a large under jaw clearance with hydraulically lowered conveyor and optional radio control for clearing blockages. The large fixed hopper is manufactured from 8 mm wear plate and the bypass chute has an adjustable deflector plate to switch between product and dirt conveyor. The unit’s engine speed and hydraulic system are optimised to reduce losses and maximise fuel efficiency and a dust suppression system provides an improved working and site environment.
Specifications:
• Weight: 34,860 kg
• Transport width: 2.6 m
• Transport length: 15.7 m
• Transport height: 3.4 m
• Working width: 4.6 m
• Working length: 15.5 m
• Working height: 3.9 m
• Throughput: up to 280 tph
Austrian based Rubble Master is leading the impact crushing world with its range of RM crushers, available from UK distributor Red Knight 6. The range is led by the recently available 42-t RM120X, delivering maximum efficiency and simplicity for use in a wide range of applications.
The RM120X features a range of solutions to make the life of the operator easier and safer, while delivering cost benefits to the business through intelligent management of the machine, based on the amount and type of material to be crushed.
The RM Operations Assist and RM GO! SMART functions enable the operator to keep track of the machine’s performance from the excavator cab, with live updates on engine performance, fuel consumption and performance all clearly visible via a lighting system on the outside of the machine. Rubble Master machines are highly mobile, versatile and powerful, ideal for crushing natural rock (riverbed material, basalt, limestone, gypsum, granite) and for recycling rubble, asphalt, concrete, glass and production waste.
RK6 offers five Rubble Master products in the UK, starting with the hook lift, 12-t RM60 with an output of up to 80 tph, through to the RM 120GO! with output of 350 tph. All machines in the range are highly mobile, easy to transport and have low running costs due to the hybrid electric hydraulic design.
Equipped with a fully automatic feed system, hydraulic adjustment and user-friendly controls with great maintenance access and replacement of wear parts, the B5 Jaw Crusher technology is ideal for applications such as granite, basalt and most medium hard stone, concrete and landfill recycling, primary crushing, quarrying, construction waste, demolition, gravel and coal.
The B5 Jaw Crusher is designed with a large independent double-deck vibrating pre-screen, reducing wear and tear on the crushing chamber by removing fines from the material before entering the crusher and ultimately extending the lifespan of the machine.
Available with a low emission diesel engine coupled with loadsensing hydraulics that reduces fuel consumption by up to 25%, or a hybrid diesel/electric e-drive with demountable engine power pack with the added ability to plug-in to mains power whenever available.
Keestrack also offers state-of-theart plug-in, all electric e-drive, with zero emissions, reduced maintenance, reduced noise levels and significantly reduced operating costs. With such tangible benefits and savings, it’s no surprise that more than 30% of Keestrack’s global production is in e-drive.
Keestrack’s innovative fuel saving technology and electric
drive systems are the cornerstone for sustainable processing in all crushing and screening applications. Its interconnective electric and hybrid drive models offer both efficient and effective possibilities to protect resources, without loss of performance. By continuously advancing its products, it is prepared for tomorrow’s requirements as well as for the changing needs of its clients. The full range of Keestrack crushing and screening equipment is available from your UK national dealer – Warwick Ward (machinery) Ltd.
www.warwick-ward.com/ keestrackfootprint
In June 2022, Global Machinery Solutions was appointed Anaconda distributor across England. Anaconda Equipment manufactures and supplies a diverse range of products for the material processing industry.
Anaconda’s J12 tracked jaw crusher is the latest in its series of mobile crushing solutions and is taking the industry by storm. The machine is fitted with a 1,100 mm x 700 mm direct hydraulic drive Universal Crusher Jaw Chamber. This is the heaviest chamber in its class and really packs a punch.
This powerful crushing solution has a proven ability to deal with the most strenuous crushing conditions. Its versatility allows the crusher to deal with hard and abrasive rock such as basalt and granite. Whether processing soft or hard rock, often keeping fines to an absolute minimum is key and this is why the J12 can be effortlessly run at different speeds.
Global Machinery Solutions recently took the J12 on a demonstration roadshow across the
country. The crusher faced several uncrushable items that would have caused damage to other makes of crusher. Without any fuss or thought, the chamber released and reset itself without any damage or downtime to the machine.
Crushing asphalt isn’t an issue for the J12 as the jaw can be run in reverse and has an unblock feature, in case of uncrushables getting lodged.
The uncrushable feature provides operators and owners with the peace of mind that should something enter the chamber that cannot be crushed, they will not be faced with an expensive repair bill or the need to stop work to replace the toggle plate.
Reduced crusher downtime and reduced repair bills are key to why customers choose this crusher. The release system automatically resets, giving the J12 its advantage over other models. A large toggle plate and hydraulic cylinders keep the closed side setting (CSS) constant, keeping downtime to a minimum. The hydraulic setting of the CSS can be adjusted on the fly, saving time.
Speed is key to the machine, with an impressive set up and go time of 20 minutes. This makes the J12 ideal for contractors and site use, where time is of the essence.
As well as ease of use and productivity, the J12 offers users low running costs, without compromising on quality. This makes the crusher a fantastic option for all customers.
The demonstration roadshow feedback was impressive, with customers especially commenting on the robustness of the chamber. One customer said, “It’s the best chamber I’ve seen in over 30 years.”
There are more than 10,000 Universal Crusher Jaw Chambers in operation around the world, with some chambers having been run for in excess of 30,000 hours.
The robustness, quality, low running cost and time saving aspects of the J12 set the machine apart from the rest.
For further information, visit the website or call the sales office on: 01476 568 384, option 1.
www.globalmachinerysolutions.co.uk
The Cobra 230R is a versatile and easy to use small impact crusher that can operate in the most demanding of applications such as reinforced concrete, recycled asphalt, construction and demolition waste and natural rock. The integrated afterscreen system on the Cobra 230R ensures the required product specification is achieved with oversized material either being recirculated back to the crusher or else stockpiled.
Despite its compact size the Cobra 230R packs a punch by producing up to 250 tph, depending on the application. It achieves optimal material flow with a widening material path and two independent hydraulic aprons.
The Cobra 230R is ideal for urban use thanks to its low feed in height and ease of transportation. Coming in at 23.7 t, it maintains the same level of robustness that users have come to expect with EvoQuip.
EvoQuip’s engineers have developed a number of features that make this impact crusher
easier to service and easier to use. The intuitive control system, launched using the two button start up, allows users to adjust the crushers settings with no tools.
On top of this the Cobra 230R can be moved without stopping the crusher. With serviceability in mind a hinged radiator pack, excellent ground level access and a product conveyor that can be moved for
maintenance are just some of the features that have been developed for the Cobra 230R.
See the Cobra 230R up close at Con-Expo 2023 on the EvoQuip stand, Silver Lot Booth S5435.
A leading groundworks and civils contractor has invested in a fleet of new JCB equipment in a deal worth more than £1.1m.
Essex-based MDS Civil Engineering has taken delivery of 21 new machines including JCB’s 10 and 14-t tracked excavator models, three, six and nine-tonne site dumpers plus Loadall telescopic handlers, skid steers and Teletruks. The new models have been put straight to work on the company’s groundwork and civil engineering projects at major new build developments across Essex.
MDS Civil Engineering’s Plant and Transport Manager, Patrick Delaney said: “JCB equipment is well designed, cost-effective to run and delivers strong residual values. The huge investment
JCB made in the development of the X-Series excavator range has genuinely paid off. They are extremely powerful and the cabs have been praised by our operators.
“We have been a JCB customer for over 20 years and JCB has played a major role in our fleet ever since. It is a very forward-thinking company and through its dealer Greenshields JCB, it provides excellent aftersales care. The investment Greenshields JCB has made in its business in our region gives us further confidence to continue with JCB as a major supply partner.”
Established in 2000, MDS Civil Engineering Ltd is a specialist groundworks and civil engineering contractor that works predominantly in Essex and the surrounding counties.
Did you know that in the UK two construction workers take their own life every working day and over 20% of work-related absence is caused by stress, anxiety, or depression?
One life is too many, and that’s why Kier is putting its support behind the Lighthouse Construction Industry Charity (Lighthouse Club), the only charity that provides independent emotional, physical and financial wellbeing support to construction workers and their families.
All colleagues at Kier will benefit from Kier becoming an annual Company Supporter of the Lighthouse Club, so it can continue to provide vital support.
Due to this partnership, support provided by the Lighthouse Club is also more accessible to people working within Kier’s wider supply chain, meaning thousands more people will have access to support when they need it.
The construction industry is made up of a diverse and multinational population and one of the unique services the Lighthouse Club offers is a 24/7 confidential helpline with free translation for any language, meaning that anyone can access help when they need it without a language barrier. For those who aren’t comfortable reaching out for help on the telephone the charity also offers a free text support service.
The Lighthouse Club also has a network of over 350 Lighthouse Beacons, which use existing support groups to offer a safe space to share and socialise with like-minded people face to face. The beacons are facilitated by individuals with lived experiences who are able to encourage those struggling with life’s problems to share their issues and if necessary, signpost to additional support.
Kier Group’s health, safety, wellbeing and sustainability director Chris Lilley said: “We want to ensure our people and supply chain go home safely every day. By looking after the wellbeing of our people and those from our valued supply chain, we’re supporting them to bring their best selves to work and encouraging them to make safe decisions.
“By supporting the construction charity, the Lighthouse Club, we’re ensuring our people and supply chain have direct and immediate access to support that is adapted to their needs,
tackling issues they may be facing and giving them the best support possible. This includes access to mental, physical, financial and emotional wellbeing support 24/7 through the Lighthouse Club. We’re delivering joint webinars and toolbox talks alongside the Lighthouse Club for our operative and management colleagues, to help raise awareness of the support available.
“At Kier, we prioritise wellbeing in the same way as health and safety. We currently provide mental health support through a network of over 500 mental health first aiders and our employee assistance programme. This charity support is the latest way we’re supporting our people and our supply chain.”
Bill Hill, CEO of the Lighthouse Club said: “We’re absolutely delighted to have Kier on board as a Company Supporter. It’s vital that every level of our construction community knows that we have a huge variety of free and easily-accessible wellbeing support, and we are really looking forward to working together to help improve our workforce wellbeing.”
Additional support the charity offers includes a variety of free constructionfocused training programmes ranging from self-paced e-learning, tutor led online masterclasses and MHFA England accredited Mental Health First Aider courses.
The Lighthouse Construction Industry Charity is launching its new e-learning programme to help spread some extra love and support within the construction industry.
The charity’s Wellbeing Academy already offers online tutor led masterclasses, seminars and on-site training and this latest addition is aimed at equipping workers with the soft skills they need to navigate today’s challenges and uncertain times.
The free self paced e-learning modules form the foundations of the Wellbeing Academy and courses include Bang on Budget, Banter vs Bullying, Managing Stress, Resolving Conflict, Understanding Anxiety and Work-Life Balance.
Each of the e-learning modules are delivered at two levels. Foundation Level 1 provides learners with an introduction to each subject, the key topic areas and an understanding of the language used in the next level. Foundation Level 2
presents scenarios where learners need to demonstrate their understanding of the subject, apply the skills learned and use logical reasoning to engage and master a variety of problems much like in real life.
With one simple registration, learners can access all of the e-learning modules on any device and at any time. This allows learning at a pace that suits the individual and the ability to pause and return to a module at a later date and time gives complete flexibility around hectic work and home lives.
An easy to navigate dashboard shows the learner’s progress through the modules and reminds them of partially completed courses.
Sarah Bolton, Director of Charitable Services for the charity said: “We are constantly augmenting our charitable services to ensure that we meet the needs of our workforce. The very nature of our industry means that fitting a set training schedule around work and home life
commitments doesn’t work for everyone and our self paced e-learning addresses that problem. Studies also show that this style of learning means people are more likely to retain knowledge on new subjects and therefore will feel more confident in applying those skills in real life.
“We also know that to support a positive wellbeing culture, we need to develop our workforce’s soft skills to help them negotiate the challenges of everyday life and working in what can be a very stressful environment.
“Our self paced e-learning modules do exactly that and they are relevant to every person in our industry. Whether you’re a self employed tradesperson, a site operative, project manager or office based, everyone will benefit from developing their soft skills and everyone needs to play their part.”
To register for e-learning modules and find out more about the training available, visit www.lighthouseclub.org.
CRS NI Ltd and Agg Pro, leading supplier of equipment for the quarrying and recycling industries, have recently announced a new partnership.
Agg Pro will become the exclusive dealer for CRS NI Ltd across England and Wales for its range of mobile and static recycling machines.
As the momentum for households and businesses taking on the challenges of recycling continues to grow, so does the need for more recycling solutions and increased capacity.
CRS’s new range of mobile and static solutions more than meets that challenge. Facilitated through its new partner Agg Pro, it will push out innovative solutions across the UK.
Speaking about the partnership Sean Conlon, Company Director at
CRS NI Ltd said: “As CRS NI Ltd continues to expand its presence around the globe and reach new markets, we are delighted to announce our partnership with Agg Pro to cover the English and Welsh markets.
“CRS are known for our innovative and reliable world-class systems and we will continue to push our research and development to always keep us one step ahead.
“We look forward to working with the Agg Pro team, a longstanding recycling equipment dealer with a wealth of knowledge and experience in the game.”
Commenting on the new dealership, Dean Ashton, Product Line Manager at Agg Pro said: “We are very proud and immensely excited to bring CRS NI Ltd to the UK market.
“The recycling market is growing exponentially and we want to ensure our customers are in a position to exploit any opportunities that come their way.
“CRS are known for offering quality, cutting-edge recycling systems that stand the test of time. Put simply, that’s exactly what we want to supply our customers with.
“Along with the Agg Pro service support, it’s a strong collaboration.”
Agg Pro is delighted to announce the appointment of Dean Ashton as Product Line Manager for the environmental division of its business.
Dean has more than 40 years of experience in engineering and business development in the recycling, waste-toenergy and manufacturing industries.
Dean’s appointment, along with Agg Pro’s McCloskey Environmental dealership and the recent announcement of a partnership with CSR NI Ltd, serve to further emphasise the focus Agg Pro has in growing environmentally sustainable recycling and waste management solutions for its customers.
Commenting on his new role, Dean said: “I can’t wait to get started, I really can’t. Agg Pro is a company renowned for the quality of the service they provide, they just seem to be a notch above anyone else and I want to help further enhance that reputation.
“The exclusive dealership agreements with McCloskey Environmental and CRS NI Ltd show Agg Pro’s dedication and passion for promoting environmentally friendly solutions, a passion I share.”
Steve Peterson, Agg Pro’s Commercial Director added: “We are really pleased to have Dean on board. His experience speaks for itself and I’m sure he will prove to be an invaluable addition to the Agg Pro family.
“We had a fantastic 2022 and this appointment shows our ambition to go even further in enhancing the depth and breadth of our offering in 2023.
“Welcome to the team, Dean.”
In the face of rapidly changing prices and market conditions, Bobcat is now offering customers a new one-stop shop selection of attractive hire purchase financing options for buying new Bobcat products. The range of finance schemes covers not only traditional Bobcat products such as loaders, mini-excavators, telehandlers and attachments but also the light compaction, compact wheel loader, small articulated loader and compact tractor ranges added in the last two to three years.
Hayley Quinn, Finance Manager, UK, Ireland, Baltics and Scandinavia for Doosan Bobcat EMEA, said: “We have added to our roster of finance products available through our dealer network to provide more for new and existing Bobcat customers looking to develop and maintain their businesses, especially in these difficult times. Our finance range has been developed with care with our customers in mind, to provide the solutions and flexibility to suit their business needs.”
Aimed at customers in all markets, including construction, rental, agriculture, horticulture, waste, recycling and landscaping, the selection of finance options now includes:
• Rental with service,
• 0% for two years,
• 0.99% for three years,
• Half price rentals in the first year,
• Up to 180-day deferral,
• Annual payments,
• Seasonal payments,
• Agility.
All details and applications for the finance schemes are available via Authorised Bobcat Dealers in the UK.
Inclusion in lease financing can also be part of the new national version of the company’s successful BobCARE Planned Maintenance (PM) programme for customer machines in the UK, the first of its type in Europe. The new BobCARE plan ensures that costs are fully predictable – the price is final and clearly stated right at the start of the contract. This means that maintenance costs are completely resistant to inflation.
Nowadays, a service contract is a natural part of the machine sales process – the current market trend is to perceive service packages as a machine option. Therefore, Bobcat’s lease partner is fully supporting the company’s service offerings and will support an ‘all-in-one approach’ where the machine, attachments, Protection Plus, BobCARE and financing are all covered by a monthly fee so that customers can focus solely on developing their own businesses.
“The breadth of our finance offering is meant to make these tough times easier”
John Christofides, Regional Sales Director for Bobcat EMEA, said: “The breadth of our finance offering is meant to make these tough times easier. They will provide the help our customers are looking for to combat the current climate, market changes, fuel price increases and so on. As well as weathering tough market conditions, our finance plans also help customers meet increased demand.”
Finning UK and Ireland, the world’s largest dealer of Cat® machines and equipment, is taking a leading role in driving equality, diversity and inclusion by signing up as a partner for the 2023 Inspiring Women in Construction and Engineering programme.
A collaboration with Construction News and New Civil Engineer, the Inspiring Women in Construction and Engineering initiative brings together people across the sector to champion the role of women. It aims to provide an open forum for women – and men – to share their experiences of overcoming challenges and to inspire others. It also provides an insight into the policies and practices already being implemented that are helping to drive better equality, diversity and inclusion across the sector.
on the Inspiring Women in Construction and Engineering awards, recognising those across the industry who are inspiring others, overcoming adversity and achieving success in an industry where women continue to play a supporting role.
The programme culminates in an annual conference, which takes place in October, and brings together keynote speakers from trailblazing organisations and individuals to share experiences and empower others.
Rachel See, Director of Aftermarket and Marketing took part in last year’s event, leading a panel discussion on the topic of overcoming challenging behaviour in the workplace. She said signing up to be a partner for the 2023 programme was a natural fit for Finning.
the industries we work in, which is fundamentally at the heart of everything we do here at Finning.
“Being a partner in the Inspiring Women in Construction and Engineering programme enables us to ensure we embed diversity of thought and action across everything we do – from our interactions with our own colleagues and customers through to helping to shape a more open future for the construction and engineering sectors.
“It’s a real honour to be part of such a progressive and inspirational group of companies. We’re looking forward to learning about the impactful work others are doing to drive diversity, and in sharing our own experiences and future, to continue to reinforce the importance of equality and of having a secure and inclusive environment for our colleagues and customers.
“We are working hard to attract more women into engineering and the construction industry because we understand the value of a diverse workforce and fundamentally want the best talent in our team.
“Giving female and male employees flexibility to manage their hours, for example, enabling them to achieve a better balance with family commitments or professional development has successfully driven our retention rates and means we deliver the best service experience for our customers.
“Events such as this one have a key role to play in breaking down people’s perceptions of our industry.”
This is the second year Finning has been a partner in the Inspiring Women event, which runs from March to October. This year’s event kicks off with the publication of an annual survey and webinar that focuses on the role that flexible working plays in opening more opportunities for women in the industry.
A big part of the programme focuses
The company has recently launched two development programmes to support employees to become successful leaders, while also endorsing a better work/life balance through measures including flexible and hybrid working.
She said: “We are extremely proud to play a leading role in driving equality, diversity and inclusion across
The webinar, “Unlocking the potential for flexible working” takes place on 8 March, which is also the launch date for the entries to the Women in Construction and Engineering Awards. For more information about the award categories and the conference go to www.inspiring.constructionnews.co.uk
“We are working hard to attract more women into engineering and the construction industry because we understand the value of a diverse workforce and fundamentally want the best talent in our team”
One of Northern Ireland’s leading waste firms, Skipway Waste Management and Recycling, has celebrated a 25-year history with Hyundai Construction Equipment Europe with the purchase of two brand-new A-series wheel loaders.
Belfast-based Skipway briefed its trusted dealer, Northern Lift Trucks, to source machines that would be durable, with a focus on good fuel economy and operator comfort. The machine that stood out as perfect for the job was the HL960A – and Skipway swiftly ordered two of them.
Matthew Heatrick, Systems Manager of Skipway, said: “We’ve only ever used Hyundais here at Skipway, mostly 770 models over the years, so we knew that we liked and trusted the brand and wanted to stick with them for our next purchase. Already we’re seeing the benefits of upgrading to the new A-series machines. Their fuel economy is so much better, they’re using half the diesel of the previous ones which obviously makes a huge difference to our finances.”
The two machines have been earmarked and specified for different uses. One of the HL960As will be based at a materials recovery site in Belfast and used for the heavy-duty tasks of stockpiling waste and loading rubble and timber. This machine has been fitted with longer arms and supplied with different bucket attachments to ensure the HL960A can tackle any load, terrain and material in its path.
The second HL960A will be used for waste transportation at a second Skipway site in Newtownards, where flexible and robust machines are the key to running an efficient operation.
Matthew continued: “A typical day on one of our sites is long and complex, so we need machines that can live up to the challenge. The A-series has been above and beyond what we expected and our operators have been extremely complimentary about them.
“The main feedback has been about how comfortable they are – the joystick controls are really easy to use and the visibility is much better than any machine they’ve used before.
“From our side, the camera system gives us peace of mind that the machines will be operated safely and the fuel economy is obviously a big plus. We are very impressed with the new A-Series and these first machines definitely won’t be our last.”
Acquired by the R Heatrick Group in 2012, Skipway Waste Management and
Recycling provides demolition, aggregate, haulage and skip hire services throughout Northern Ireland. With a focus on sustainability, Skipway’s current waste recycling rate is 92%, equating to over 45,000 tonnes, helping the company to deliver on its promise of building a more sustainable future for Northern Ireland.
Supplied by Hyundai Construction Equipment dealer, Northern Lift Trucks, the HL960A Wheel Loader is part of Hyundai’s flagship A-series – a fresh generation of construction equipment that complies with European emission levels. This Stage V machine was awarded the SaMoTer Technical Innovation Award in the Medium Wheel Loaders category and is suitable for general construction applications and heavyduty work on industrial, mining and quarrying projects.
BMC MAKE ALL TYPES OF BUCKETS, GRAPLES, CRUSHERS, RIPPERS ETC FOR EXCAVATORS FROM 0.7 UP TO 55-TON ALL HERE IN THE UK. GIVE US A CALL OR SEND US AN EMAIL WITH YOUR REQUIREMENTS.
BMC MAKE ALL TYPES OF BUCKETS, GRAPLES, CRUSHERS, RIPPERS ETC FOR EXCAVATORS FROM 0.7 UP TO 55-TON ALL HERE IN THE UK. GIVE US A CALL OR SEND US AN EMAIL WITH YOUR REQUIREMENTS. 4 IN 1 BUCKET CONCRETE POURING COMPACTION WHEEL SLAB ROCK SLUDGE / SLURRY TRAPEZOIDAL
LARGE STOCK OF 1 - 22 TON BUCKETS
TEL: 01291 630 073
EMAIL: SALES@BMC-BUCKETS.CO.UK
AVAILABLE FOR NEXT DAY DELIVERY
Parts specialist TVH has announced it is further expanding its range of products for small earthmoving equipment (SEM). TVH already offered parts and accessories for three types of small earthmoving machines (up to 10 t): mini excavators, skid steer loaders and compact track loaders. To this it now adds parts for
earthmoving equipment sector. But our customers’ needs and expectations always come first. That is why we now also offer parts and accessories for backhoe loaders.”
Over 4m known references Backhoe loaders are equipped with a bucket on the front and a backhoe
offer more than 4m known references for the SEM market. The company processes more than 300,000 orders for the small earthmoving market every year.
backhoe loaders. This move enables TVH to further enter the new adjacent market of small earthmoving equipment.
Joris Tijtgat, Market Management Specialist for SEM at TVH said: “We are continuously expanding our product range, especially within small earthmoving machinery, whether that is with new parts, new brands or new equipment. Our in-house experts keep a close eye on the market and respond to all trends and developments in the small
on the rear. That makes this vehicle a very versatile machine. They are suitable for all kinds of earthmoving jobs in demanding environments. Joris explained: “With one and the same machine you can perform different tasks and therefore backhoe loaders can be used everywhere, such as in public administrations, in roadworks, in (agricultural and garden) construction etc.”
By adding parts and accessories for backhoe loaders to its range, TVH can
Most parts available from stock Joris added: “The focus for the development of the range of parts for backhoe loaders will initially lie on the machine makes JCB, CASE, Caterpillar, John Deere, Volvo, Bobcat and Kubota. We proactively search for the best parts and accessories for those makes. As a result, most of these parts are already in stock, even before there is demand for them, and we can deliver very quickly. But when a customer needs a part from another make like New Holland, Komatsu, Terex ... our in-house experts will of course help them quickly with that too.”
“We are continuously expanding our product range, especially within small earthmoving machinery, whether that is with new parts, new brands or new equipment”
Ferries themselves have to be transported at regular intervals. This was recently the case for the Kiel Canal Waterways and Shipping Authority at the Yard in Rendsburg, where a new procedure was implemented for the first time as a faster and more practicable method of moving vessels ashore for inspection purposes.
Previously the vessels, weighing up to 130 t, were manoeuvred onto a shiplift consisting of a lower and upper cradle, which was winched ashore and along the rails leading to the shipbuilding hall.
With the introduction of heavier hybrid ferries (approximately 180 t) and on the basis of an economic assessment for upcoming refurbishment measures on the approach to the shipbuilding hall, it was decided that a wheel-based transportation system on a level surface would be preferable to replacing the rails.
The plan was to use a heavy duty vehicle to pull the vessel ashore, pick it up and transport it between the shiplift, the wash yard and the shipbuilding hall, and set it down there. After a thorough study of the options available, the Waterways and Shipping Authority chose a heavy-duty selfpropelled eight-axle module manufactured by Goldhofer.
The self-propelled transporter also features electronic multiway steering, which makes it possible to manoeuvre the vessel in the confined space of the shipyard and set it down with pinpoint accuracy. The only adjustment required to the ship was a modification of the upper cradle of the shiplift to permit the self-propelled module to be positioned beneath it so as to pick up the load with the help of the hydraulic axle compensation.
The Nobiskrug drop-ramp inland ferry, which can carry up to 45 t, was the first vessel to be handled using the new system. The ferry has a total length of 32 m and a total width of 9.8 m and weighs around 130 t. It was brought to the Rendsburg shipyard to undergo maintenance and a basic overhaul following a regular inspection.
The ferry was positioned on the shiplift and brought ashore on the slipway using the Goldhofer PST/SL-E self-propelled transporter as a tow tractor. The selfpropelled transporter was then positioned under two upper cradles and picked up the ferry using the transporter’s hydraulic axle stroke and moved to the shipbuilding hall for the inspection and maintenance work.
Ideal for telehandlers carrying heavy loads, PIN-type forks are often found on construction sites. Each fork has an eye at the top of the back of the fork. This slides over an axle on the machine to securely mount the attachment. Made from high-quality chrome-manganese steel, these PIN forks offer superior mechanical strength and are expertly crafted with a smooth and attractive finish.
A trusted brand
Available exclusively at TVH, every product from CAM attachments is infused with decades of expertise and experience.
By using high-quality material and precise engineering, these products offer exceptional strength and durability. Moreover, they are easy to install
and replace, increasing efficiency and productivity.
CAM attachments is well known for extensive knowledge, high quality standards, and unmatched reliability. The products have gained huge popularity in western European countries such as Italy, France, the UK, Portugal, Germany, Spain and Belgium.
Dedication to quality and reliability
CAM attachments is committed to providing customers with the highest level of quality and reliability. Its rigorous adoption process ensures that only the most capable attachments are included in the range. CAM attachments remains at the forefront of market and product innovation and subjects its products to extensive testing before they are
made available for sale. Thanks to this commitment to performance, durability, and customer satisfaction, many of the CAM attachments have been in use for a decade or more.
If you are looking for a product that will make your work easier, more efficient and productive, CAM attachments’ pin-type forks or other attachments such as clamps, rotators, skips, positioners and many other products are the right choice.
Key Features:
• Maximum care to component quality standards,
• Technical awareness,
• Durability,
• Standard testing,
• Certification.
D E A L I N G W I T H W A S T E
W A T E R O N S I T E ?
K E L L Y T A N K S P R O V I D E S
C O N C R E T E
W A S H O U T &
W A T E R
T R E A T M E N T
S Y S T E M S
S O T H A T Y O U
C A N E A S I L Y
R E - U S E O R
S A F E L Y
D I S C H A R G E
Y O U R O N S I T E
W A S T E W A T E R
Volvo Construction Equipment (Volvo CE) has announced an investment into battery pack production at its excavator plant in Changwon, South Korea, signalling once again its ambition to drive industry transformation with sustainable solutions.
The Changwon plant in South Korea specialises in the production of excavators and is the biggest excavator production site in Volvo CE. The SEK 80m (£6m) investment will enable the plant to begin manufacturing a wide range of battery pack solutions. This is
another important step forward towards the company’s Science Based Targets commitments and its ambitions to be fossil free, with 35% of machine sales to be electric by 2030.
With the investment from Volvo Group, a new production facility and equipment will be built at the Changwon plant, which at around 1.1m square metres is the largest excavator production site in Volvo CE, producing around 55% of its total excavator volumes.
The new facility at the Changwon plant will produce a wide range of
common electric storage solutions (battery packs) for Volvo Group and become a core competence centre for electric excavators. This will enable Volvo Group to offer more sustainable solutions to its APAC markets in a more flexible, cost-effective and agile way and will include supply chain, manufacturing and logistics.
Andy Knight, Head of Operations
Excavator and Managing Director of Volvo Group Korea, said: “As the largest plant in Volvo CE and the core site for excavator development and production, Changwon is at the forefront of our shift to a sustainable future.
“This investment is an important milestone in our electrification roadmap and supports our recent investments in production facilities for electric excavators. Changwon is ideally located close to battery module supply partners and other key suppliers in South Korea to meet the needs of customers in the future. We are also home to a highly skilled and motivated workforce who are fully committed to meeting our future environmental targets.”
The new production facility will be built inside the current component workshop at Changwon without disruption to the existing operation. Once complete, the facility will be approximately 2,500 m 2 including assembly and logistics areas. The building work will begin in April 2023, with battery pack production expected to commence in June 2024.
Coming soon after an announcement to invest in the production of electric wheel loaders at its plant in Arvika, Sweden, and electric haulers from the company’s production facility in Braås, Sweden, this is another sign that Volvo CE is committed to becoming completely fossil free by 2040, in line with the Paris Agreement and as laid out in its Science Based Target goals. And it is taking another step forward in its ambition to transform the industry through electromobility and other more sustainable solutions.
Volvo CE has already successfully introduced compact electric excavators to the global market with the ECR25 Electric, ECR18 Electric, EC18 Electric and the mid-size EC230 Electric excavators. Together with its compact electric wheel loaders, Volvo CE has one of the largest electric ranges on the market.
When Utah-based contractor BHI was awarded low bid on a threemile stretch of canal essential to the irrigation around the largest city in Uintah County, in the north-eastern part of the state, it knew that extensive excavation and backfill would be on the cards and that it would require the most robust and reliable equipment
BHI has been tasked by Uintah Water Conservancy District to enclose a two-metre High-Density Polyethylene (HDPE) pipe across a vast portion of the Steinaker Service Canal near the city of Vernal. Owing to a water shortage over the past several years, the Uintah Water Conservancy District has been working to improve provision to the surrounding area, with the Steinaker Service Canal Enclosure Project.
The existing channel is being converted into a pressurised pipeline to provide a firm water supply to land in the surrounding Ashley Valley, with the aim of minimising and even eliminating loss of water through seepage and evaporation, maximising the amount of water available for irrigation purposes. Upon completion, the canal enclosure will be the largest diameter HDPE pipe installation in the United States of America.
BHI is self-performing the entire scope of the project, which includes site preparations, excavation, pipe installation, backfill and restoration of the canal. To handle the large-scale earthmoving, BHI needed articulated haulers that would be up to the challenge, day after day, in an intense six-month timeline.
Rokbak dealer Rasmussen Equipment, of Salt Lake City, supplied two RA30s to BHI on a rental-purchase option in September 2022. The haulers were received so positively on site that the purchase was completed before the end of the year.
The RA30s are tasked with transporting rock and rubble to excavate the area in order to install the pipe and later they will support with the subsequent backfill. With the capacity to transport a payload of up to 28 t, a maximum engine power of 276 kW, a heaped capacity of 17.5 m 3, and a maximum torque of 1,880 Nm at 1,400 rpm, the Rokbak RA30 can be relied upon to all-weatheroperate, transporting loads effectively and efficiently, with optimal traction in difficult terrain and combating steep inclines with ease.
It’s not hard to see why. Cushioned bump stops on the steering cylinders reduce strain on the operator over an extensive shift and a 45° steering angle at either side creates a turning radius of just 8,470 mm, resulting in superior manoeuvrability. There is a spacious, ROPS/FOPS-compliant, pressurised cab. Smoother gear shifting accentuates these levels of comfort, alongside other benefits like faster cycle times, lower fuel consumption and reduced carbon emissions.
Exceeding expectations
“The RA30 is a top-performing machine,” says BHI operator Reese Shultz, who has already clocked up over 2,000 hours alongside colleague Dustin Gardner in the two RA30s since work commenced in September. “It’s fuel efficient, powerful and with features like the tailgate helping to maximise load retainage as well as multiple reverse gears enabling quick cycle times, it’s been designed for productivity. It also has excellent mobility, it’s relatively narrow (3,224 mm at its maximum width), which is hugely beneficial in confined job site spaces.”
“One of the first things I noticed when I started using the RA30 was that it has proper visibility, from a comfy seat, in a quiet cab and the HVAC (Heating, Ventilation and Air conditioning) system works really well,” explains Dustin. “It’s a real solid ride and it’s comfortable to operate over various ground conditions.”
Rasmussen Equipment has provided Utah contractors with equipment solutions for over 75 years. That wealth of experience combined with the RA30’s capabilities for taking on the toughest tasks and terrain has proven to be an ideal combination.
“It’s always easy to work with BHI because of the professionalism and knowledge throughout the organisation,” says Rasmussen Equipment’s Sales Representative Brandon Dorney, who has worked closely with BHI for many years and facilitates the equipment support provided by Rasmussen Equipment. “We enjoy keeping up with the demands of BHI and coming up with solutions to individual projects. When BHI outlined this particular job with its challenging earthmoving aspects, we knew they needed Rokbak haulers.”
With the Steinaker Service Canal Enclosure Project due to run until April 2023 and a huge amount of groundwork still to be done, BHI expects to put the RA30s through their paces for a good while yet.
One of the UK’s leading recycling and waste management companies has given Finning the green light to complete the UK’s first Certified Machine Rebuild (CMR) on a 15-year-old Cat 836 landfill compactor to give it a new lease of life ensuring that it can continue operating for another 15 years.
FCC Environment owns and operates over 200 recycling, treatment, and disposal facilities across the UK, managing more than 8.5m tonnes of waste for its customers, which include over 72 local authorities across North Yorkshire, Suffolk and Essex.
FCC’s waste processing fleet alone comprises 500 machines including landfill compactors, wheeled excavators, track type loaders and articulated dump trucks, with Cat equipment making up almost half.
One of these machines, a Cat 836 landfill compactor, was purchased from Finning in 2007 with a full repair and maintenance programme, which proved instrumental in keeping the machine operating effectively for around 15 years while minimising downtime.
However, when the machine’s transmission failed in late 2022, FCC Group Plant Manager, Bill Stone, began discussions with the Finning team on the best solution for a replacement machine package. This included looking at buying another new machine as well as considering the option to carry out a full CMR, which is the highest-level Cat certified rebuild available.
Adam Walker, engine and drivetrain product manager at Finning is overseeing the project. He said: “Sustainability is now at the forefront of the waste
industry, so we’ve seen a shift in demand towards companies requesting remanufactured or reconditioned parts for their machines, or for the entire machine to be rebuilt.
“This is the first machine rebuild that FCC has commissioned, but the company now plans for this approach to become an integral part of their fleet management succession plan because it enables them to demonstrate a clear commitment to improving the environmental impact of their operations and reducing emissions in the drive to net-zero.
“Rebuilding a machine instead of buying new requires 85% less energy, uses 86% less water and generates around 61% fewer greenhouse gases. Plus, we recover and recycle over 65% of the original machine, so it’s ready to be used as a replacement part in another machine.
“Not only that, but customers choosing a rebuild machine option will typically save around 50-60% on the cost compared with buying a new machine. While remanufactured parts, of which there are more than 8,000 Cat certified ones available, can be up to 60% less than the cost of a brand new one.”
Bill Stone said: “We have a commitment to run our operation in an environmentally and socially responsible way, and by choosing to rebuild and give our assets a second life rather than buy new, we are helping to meet that commitment.
“Our mobile plant fleet is key to our operation, so it is essential these assets are managed effectively, and Finning plays a vital part in that.
“It is because of their record of strong aftermarket support and our collaborative relationship with the team at Finning that we have complete confidence in the effectiveness and efficiency of their rebuilds and they will play a crucial part in our succession planning moving forward.”
Once complete, the Cat 836 will be ‘as new’, so will offer the same machine lifespan as a new machine.
Machine rebuilds are fast becoming a recommended approach for firms’ fleet management, providing a sustainable and commercial option alongside investment in new machines. Finning has seen its number of machines rebuilds double year on year, with its specialist rebuild engineers completing hundreds over the last three years.
As an SMT customer, you can quickly and easily access and manage all your administrative documents alongside fleet information, reporting, parts ordering, and repair and maintenance information related to your account.
Get 24/7 access to all of your SMT GB documents in one place whenever you need them through our new online portal. Manage your information and receive relevant product suggestions for your fleet.