
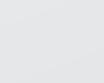

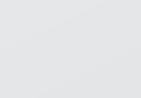
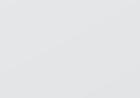
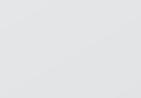
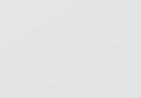

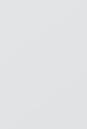
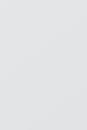
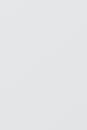
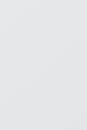
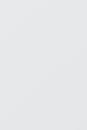
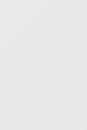
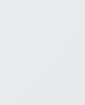


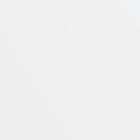
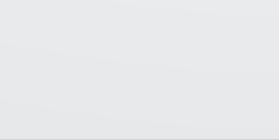
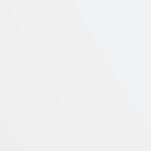
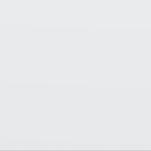
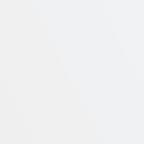
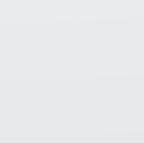
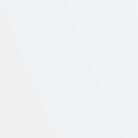

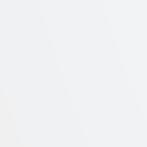
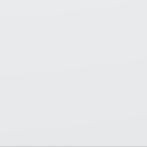
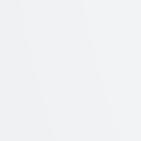



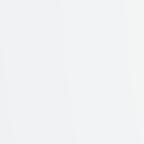
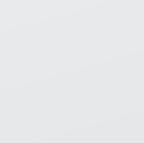
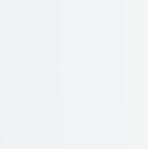
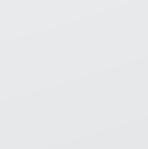

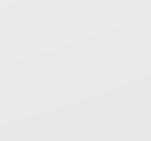











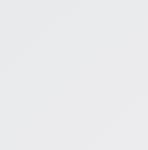
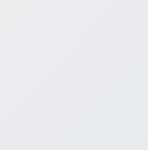
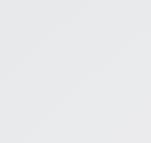
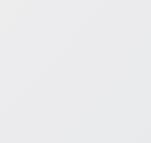
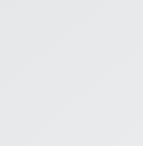

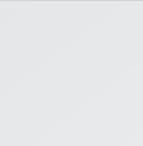

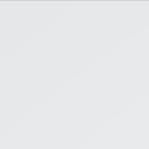
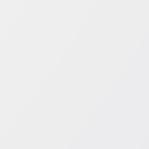

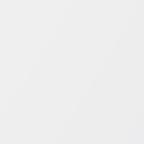
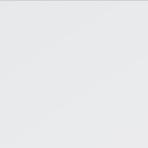
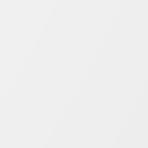
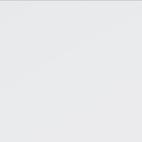
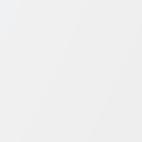
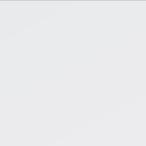
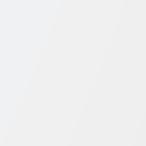
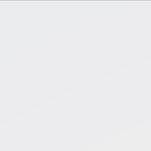


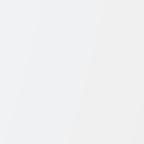
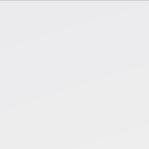
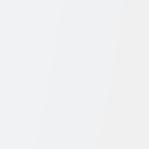
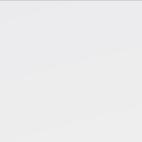

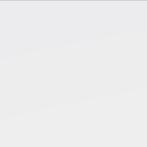
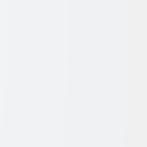
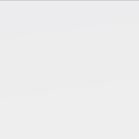
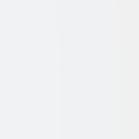
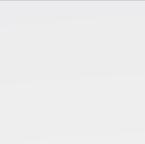

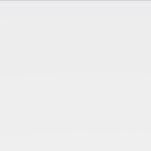
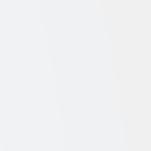
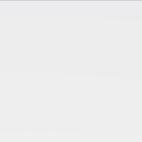
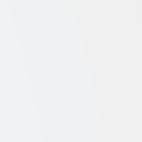
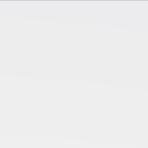
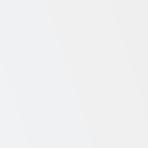

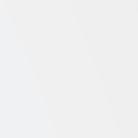
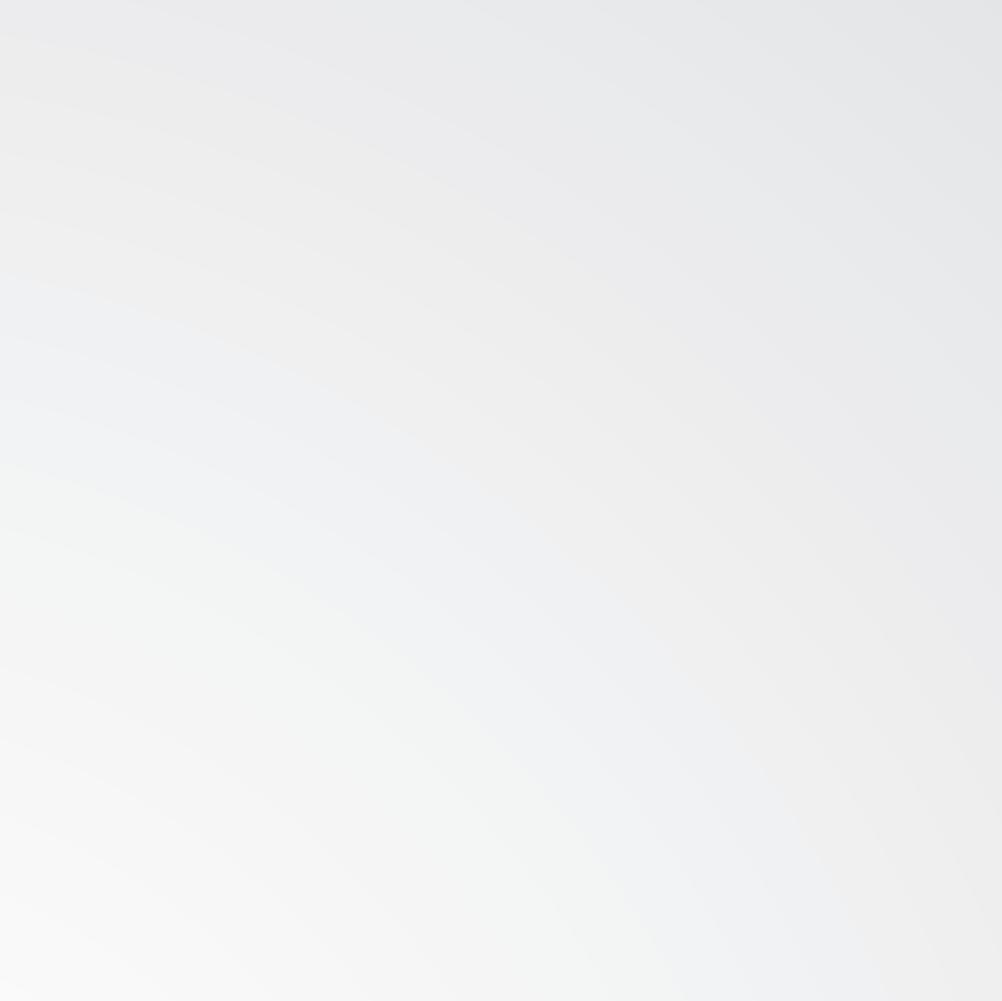
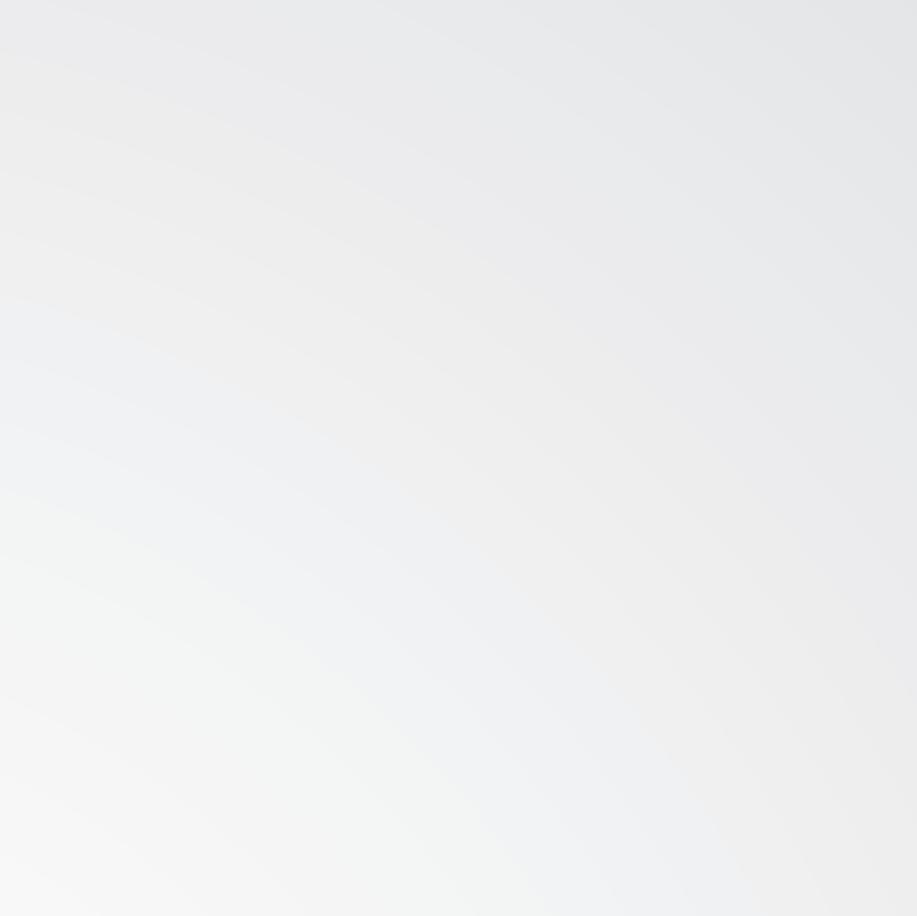

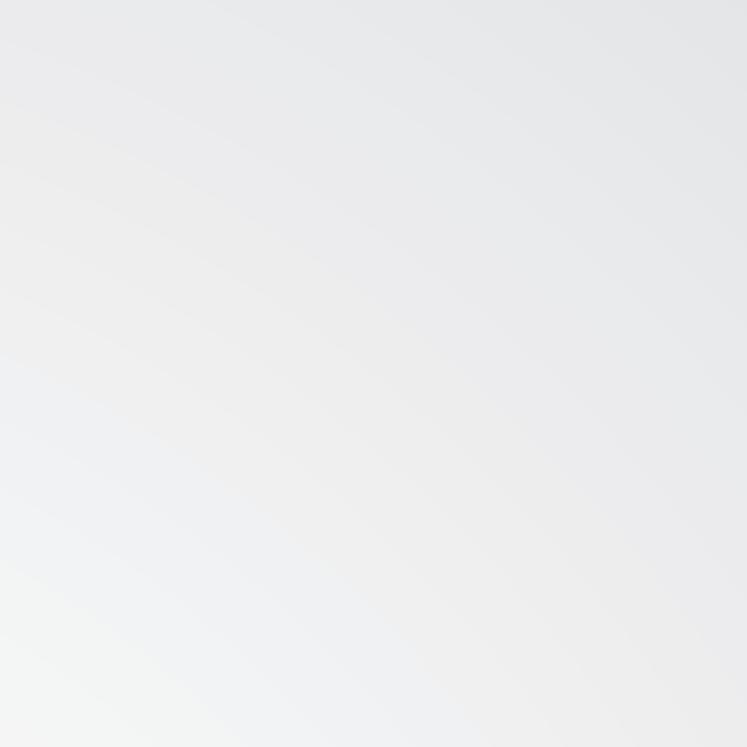
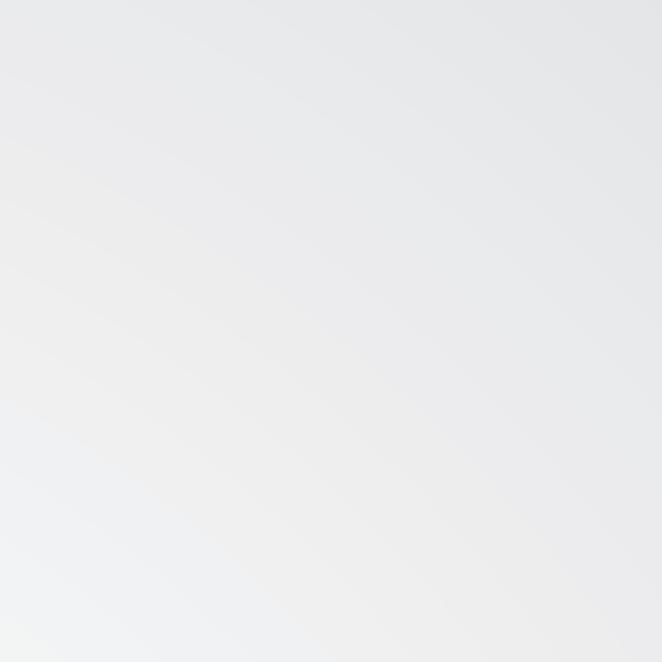
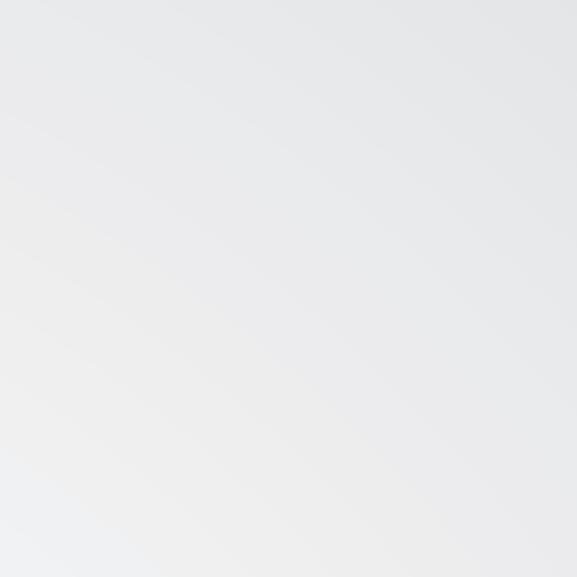

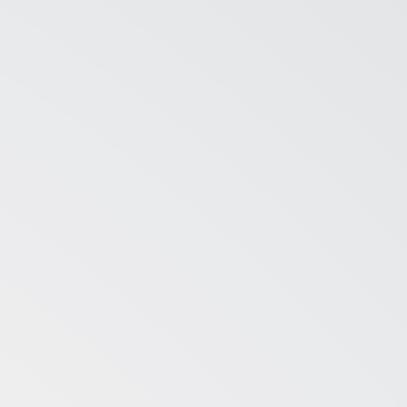

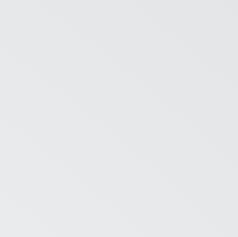
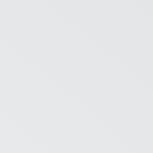









































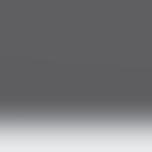
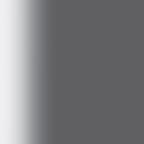


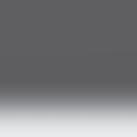
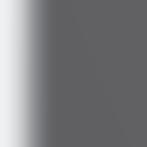
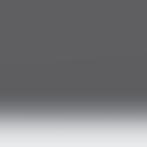
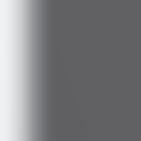


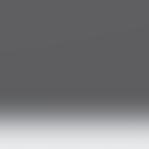
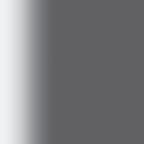
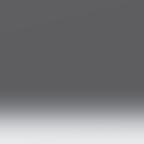
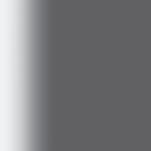
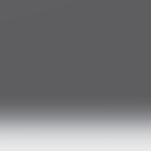
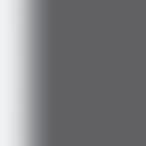
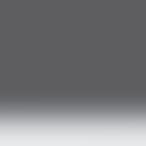
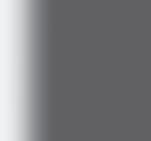
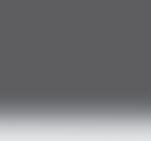































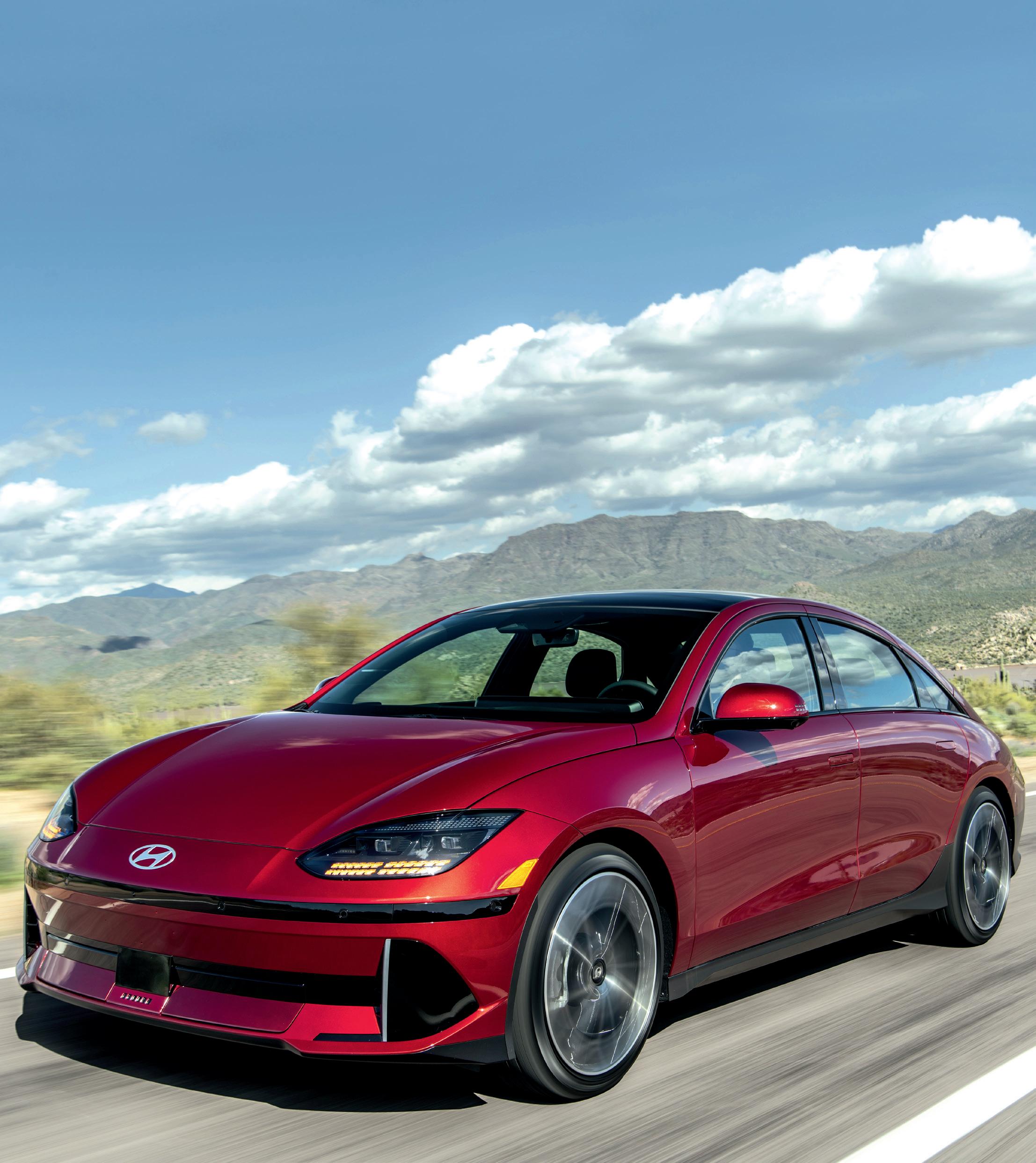
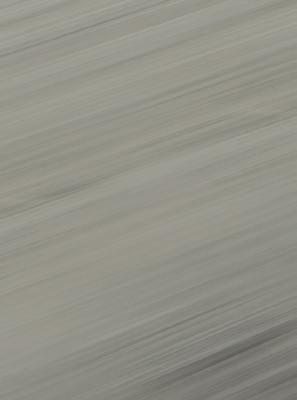
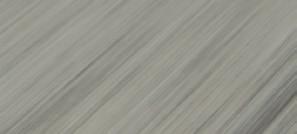


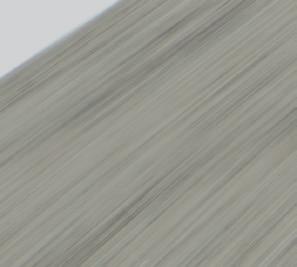
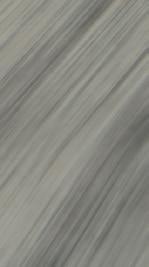
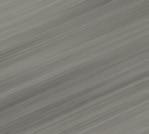
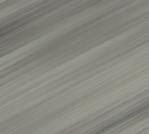
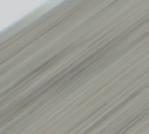
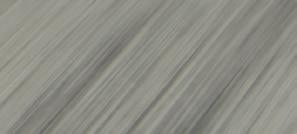



















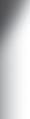




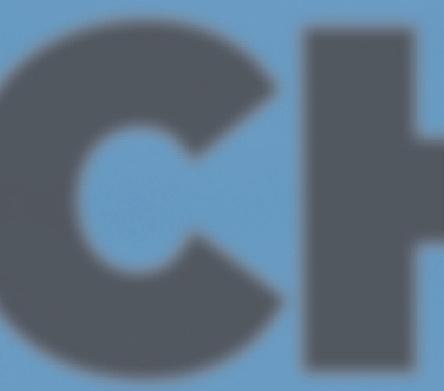
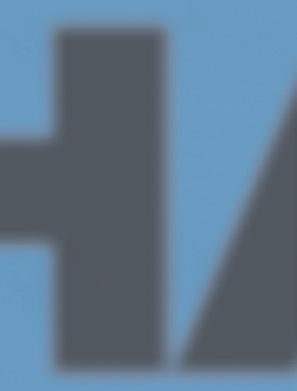



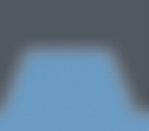
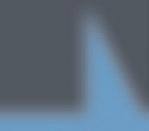

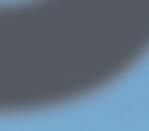





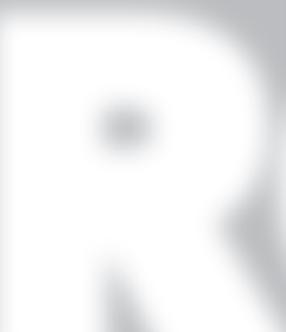
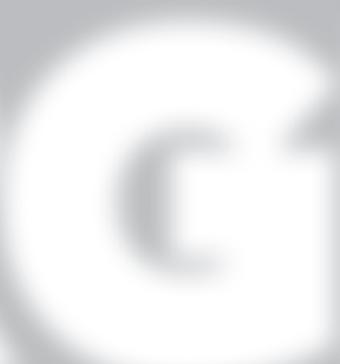



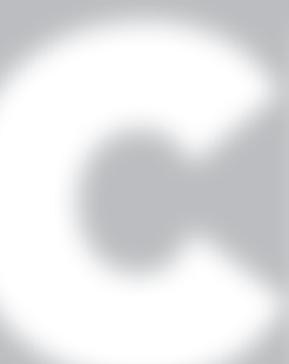


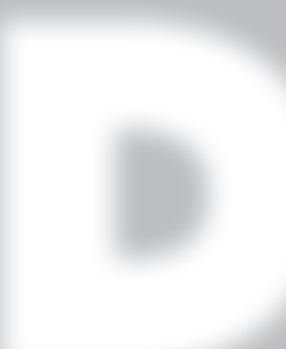

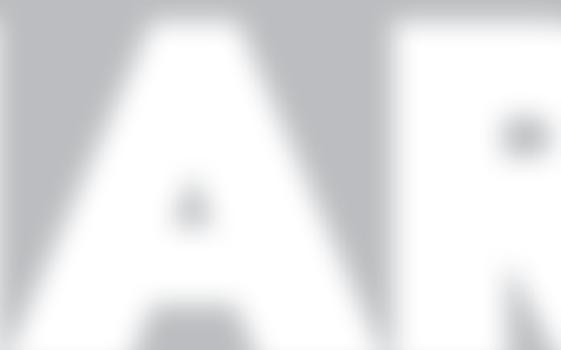
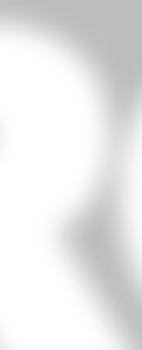


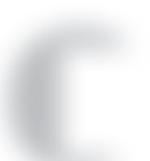
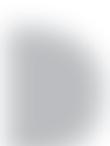

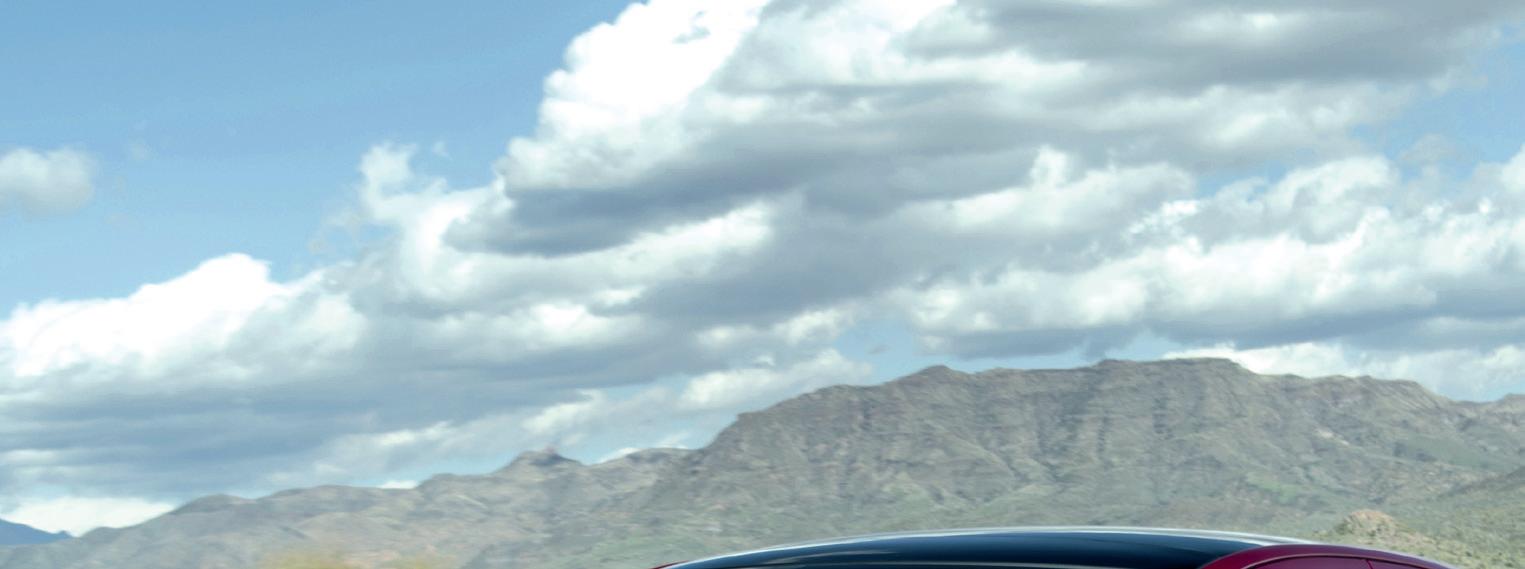
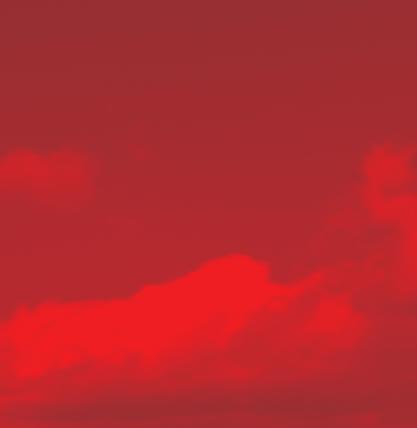
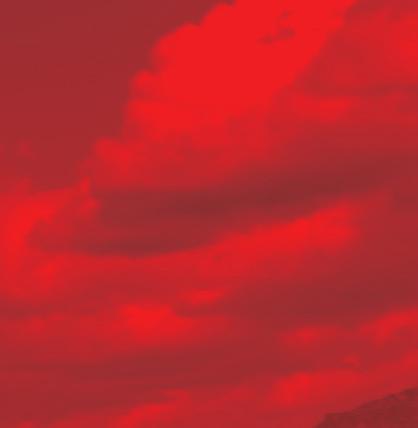
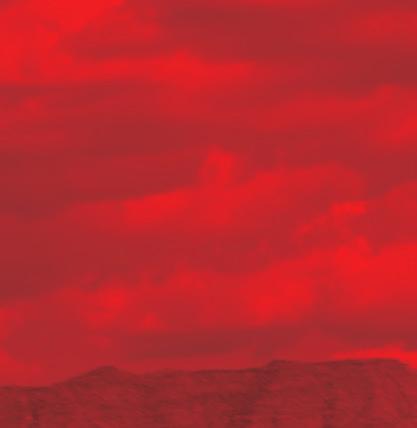
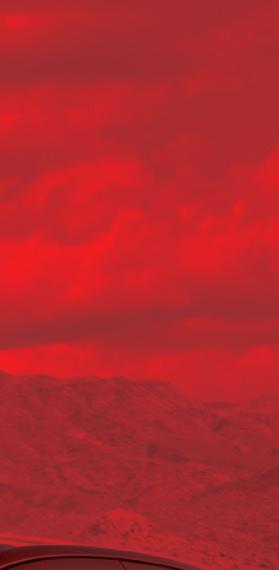
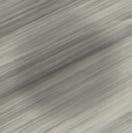
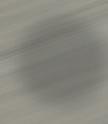

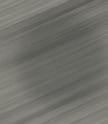

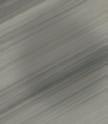

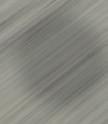

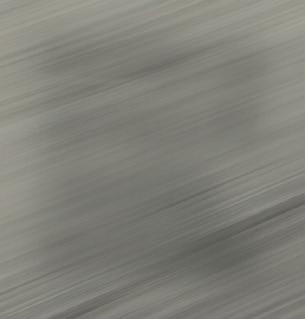

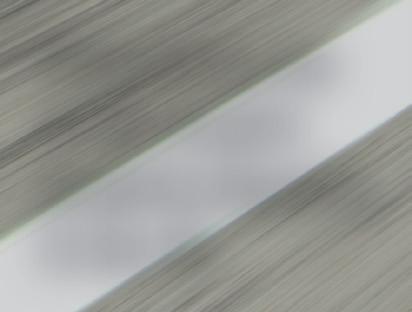

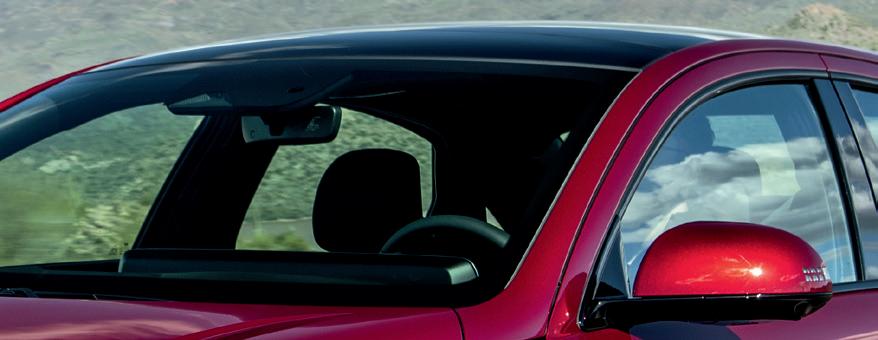
FLEXIBLE, HIGH PRECISION SOLUTIONS FROM R&D TO END OF LINE
Battery cell, module and pack level charge/discharge cycle testing solutions designed to provide high accuracy measurement with advanced features. Regenerative systems recycle energy sourced by the battery back to the channels in the system or to the grid.
Battery simulation for testing battery connected devices in all applications to confirm if the device under test in performing as intended. Battery state is simulated which eliminates waiting for the charge/discharge of an actual battery. Real time test results include voltage, current, power, SOC%, charge/discharge state and capacity.
To learn more about our Battery Test Solutions visit chromausa.com
Eaton continues e-mobility expansion in Europe
Metis Engineering releases Cell Guard for battery health monitoring in EVs
Rincon Power’s new RXC15 contactor offers 250 amps continuous up to 1,000 VDC
Bitrode launches new generation of battery cyclers
Delta-Q Technologies mass-produces its 3.3 kW EV battery charger
INFICON releases ELT3000 PLUS electrolyte leak detector for batteries
Aspen Aerogels opens Advanced Thermal Barrier Center in US
Henkel’s new injectable thermally conductive adhesive for EV battery systems
Ford signs lithium and nickel deals to secure IRA-compliant supply
LG Energy to build a $5.5-billion battery manufacturing complex in Arizona
Pre-Switch includes remote update and analysis in Pre-Flex controller for SoC
Huber’s new Unimotive offers precise temperature control for battery tests
NI’s Software-Defined Battery Lab is designed for continuous improvement
Vitesco Technologies presents new electric drive without rare earths
Piedmont and Sayona to provide lithium from Quebec mines to LG Chem and Tesla
Schaltbau introduces 800-volt contactors
SK Signet opens Texas-based EV charger manufacturing facility
Electrify Commercial to install 80 DC fast charger at 20 sites in Utah
SolarEdge introduces bidirectional DC-coupled EV charger
Versinetic releases ISO 15118-compliant EV charging software stack
New York City to deploy up to 13 fast EV charging hubs at municipal parking lots
Cummins and Heliox to offer EV charging solutions for fleet customers
Volvo invests in bidirectional EV charging startup dcbel
ABB E-mobility and Scania successfully test Megawatt Charging System
Legrand launches Level 2 EV charger for commercial use
Schneider opens large electric truck charging depot in Southern California
InCharge Energy launches suite of bidirectional charging solutions for EV fleets
Wattzilla introduces UL-listed J3068 3-phase EV chargers
Our flexible printed circuits do more than link battery cells to EV electronics. They flex during charging cycles, creating a sleeker, lighter solution that boosts miles per charge.
Put our long history of technical knowledge and consultation to work for you. From engineered materials to innovative circuitry, our vertically integrated solutions are uniquely created to help your concepts take shape.
sheldahl.com
Publisher
Christian Ruoff
Contributing Writers
Jeffrey Jenkins
Charles Morris
For Letters to the Editor, Article Submissions, & Advertising Inquiries Contact: Info@ChargedEVs.com
Associate Publisher
Laurel Zimmer
Christian Ruoff
John Voelcker
Senior Editor
Charles Morris
Cover Image Courtesy of
Hyundai Motor America
Account Executives
Jeremy Ewald
Special Thanks to
Kelly Ruoff
Technology Editor
Graphic Designers
Jeffrey Jenkins
Tomislav Vrdoljak
Sebastien Bourgeois
ETHICS STATEMENT AND COVERAGE POLICY AS THE LEADING EV INDUSTRY PUBLICATION, CHARGED ELECTRIC VEHICLES MAGAZINE OFTEN COVERS, AND ACCEPTS CONTRIBUTIONS FROM, COMPANIES THAT ADVERTISE IN OUR MEDIA PORTFOLIO. HOWEVER, THE CONTENT WE CHOOSE TO PUBLISH PASSES ONLY TWO TESTS: (1) TO THE BEST OF OUR KNOWLEDGE THE INFORMATION IS ACCURATE, AND (2) IT MEETS THE INTERESTS OF OUR READERSHIP. WE DO NOT ACCEPT PAYMENT FOR EDITORIAL CONTENT, AND THE OPINIONS EXPRESSED BY OUR EDITORS AND WRITERS ARE IN NO WAY AFFECTED BY A COMPANY’S PAST, CURRENT, OR POTENTIAL ADVERTISEMENTS. FURTHERMORE, WE OFTEN ACCEPT ARTICLES AUTHORED BY “INDUSTRY INSIDERS,” IN WHICH CASE THE AUTHOR’S CURRENT EMPLOYMENT, OR RELATIONSHIP TO THE EV INDUSTRY, IS CLEARLY CITED. IF YOU DISAGREE WITH ANY OPINION EXPRESSED IN THE CHARGED MEDIA PORTFOLIO AND/OR WISH TO WRITE ABOUT YOUR PARTICULAR VIEW OF THE INDUSTRY, PLEASE CONTACT US AT CONTENT@CHARGEDEVS.COM. REPRINTING IN WHOLE OR PART IS FORBIDDEN EXPECT BY PERMISSION OF CHARGED ELECTRIC VEHICLES MAGAZINE.
Choosing a topic for the Publisher’s Note is not always easy, but this time around it was a slam-dunk. e surprising news that Ford would hitch its wagon to Tesla’s charging plug set o an avalanche—at this writing GM, Rivian and Volvo have joined the party, along with a plethora of EVSE makers and charging network operators.
Yes, it’s a very big deal in the EV industry, and on the whole it seems like good news. It’s spectacularly good news for Tesla, which has scored a massive publicity coup and opened up potentially large new revenue streams in the future (reselling electrons will probably never be a great business, but there are other opportunities if you get creative). It’s great news for drivers, who will have more—and hopefully better—places to charge.
Techies can debate the relative merits of CCS vs NACS, but all that is beside the point. e other automakers made this move for the sole reason of being able to promise a better customer experience. For potential EV drivers, charging is the #1 concern (for actual EV owners, it’s a minor issue at most), and while public charging in general su ers from unnecessary complexity and abysmal reliability, Supercharger users report an easy-to-use, dependable charging experience.
e legacy automakers are spinning this as good news for them, but we’re not so sure. e move to Telsa’s NACS is an admission of defeat—the upstart has beaten the Old Guard (who had 11 years to raise their game), and everyone knows it. at’s not a great look. On the other hand, if more access to charging helps sell more EVs in general, then let the rising tide li all cars.
Reaction to the news has been almost universally positive—even usually Tesla-skeptical pundits are hailing the convergence single plug standard, and predicting a good riddance to CSS. Standards body CharIN was one of the few dissenting voices, but along with fellow standards body SAE, it has announced that it will cooperate with the new overlords.
We hope things work out the way everyone thinks they will. More and better charging—what’s not to like? However, all of North America’s public chargers aren’t going to become Superchargers overnight. We strongly suspect that the main reason Superchargers work much better is that they’re designed and operated by one company for one small set of vehicles, and that’s going to change. Every new vehicle, adapter and charge point operator that signs on will compound interoperability issues, and it’s going to be up to Tesla—a company with a less-than-perfect record of keeping its promises—to straighten it all out.
e Tesla takeover is far from the only news shaking up the EV world this year. President Biden’s IRA and BIL are (so far) succeeding beyond the most optimistic predictions. Companies are investing billions to bring supply chains to the US, creating lots of good jobs and building political support in the process. See this issue’s feature article on Westwater Resources, page 34, which is building a huge graphite processing facility in Alabama.
California is poised to start requiring new EVs to support bidirectional charging—a technology that promises to revolutionize both the transport and utility industries. Read our interview with the CEO of Nuvve, page 72.
e incentives included in the IRA and the promise of V2X are both drivers of another important trend: the long-awaited rise of electric trucking. Few know more about this red-hot eld than Rustam Kocher, who gives us an indepth look at the current state of the commercial EV scene, page 64.
Power management company Eaton is continuing to expand its European e-mobility business operations, adding new production, o ce and research facilities at several sites.
Eaton has invested in a new production facility for power electronics components in Montrottier, France.
e new plant will produce high-voltage power components including traction inverters and DC-DC converters. High-volume production is scheduled to begin in mid-2023.
Eaton has also expanded a current site in Tczew, Poland, to include electri ed vehicle capabilities.
Eaton’s electrical engineering design and testing facility in Bonn, Germany will increase its focus on EV systems, including the company’s Breaktor circuit protection technology.
Last year, Eaton established a new o ce and laboratory facility in Karlsruhe, Germany, near major manufacturers and suppliers. Here the company will add a lab for the testing of power electronics and power distribution products.
Eaton is also expanding e-mobility production in Gummersbach, Germany and Györ, Hungary.
“ e electri cation of automotive and commercial vehicle markets requires new capabilities to meet the changing industry,” said Mark Schneider, President, E-mobility, Eaton. “We are seeing increasing global demand for electri ed vehicle solutions that are designed and produced in our European locations.”
UK-based Metis Engineering has launched Cell Guard, a battery safety sensor, to detect lithium-ion battery cell venting and monitor battery health in EVs and energy storage systems.
Cell Guard monitors volatile organic compounds (VOCs), pressure change, humidity, dew point, shock duration and shock loads (up to 24 G), unlike other battery cell monitoring systems (BMS) that only monitor temperature and voltage. is data can be compared to cell temperatures and pressure spikes to detect cell venting and alert the driver within minutes.
e sensor sends data to a control unit like the vehicle’s ECU through a customizable CAN interface, which can also interrupt the battery pack’s circuit to prevent thermal runaway. Cell Guard monitors the battery pack dew point and provides an alert before condensation falls on the battery contacts, which can cause shorting and thermal events. ere is also a threshold-triggered programmable pin to control relays. If a threshold is achieved, the sensor transmits warnings via CAN and wakes the vehicle if a problem is identi ed.
“As cells age, the chance of one in a pack of hundreds or thousands having a fault increases signi cantly. e early detection of cell venting is vital to the safety of the vehicle’s passengers and everything in proximity,” said Metis Engineering’s MD Joe Holdsworth. “Cell Guard provides consumers with valuable and detailed information on used EV battery condition.”
As companies develop new battery chemistries and new hardware and so ware algorithms to improve the utilization and safety of batteries, advanced battery testing equipment is gaining importance.
Bitrode has more than 65 years of experience in the design and development of battery cyclers and battery testing equipment. e Bitrode line of products includes cell, module and pack testers along with battery formation equipment. In recent years, Bitrode Corporation has been investing heavily in a new product development team, and the team’s activities have been ampli ed since September 2022 when Bitrode was acquired by the Schuler Group.
e Bitrode Digital Cycler, which was launched at the recent Battery Show Europe, is designed to meet the current and future demands of the battery industry for testing high-capacity battery cells.
Battery cyclers enable characterization and modeling of batteries in di erent stages of battery design and development, such as inspection, validation, end-of-line testing, pack assembly and battery management system design.
Electronic parts manufacturer Rincon Power is expanding its chassis-mount series of contactors by introducing the new ceramically-sealed RXC15 unit, which is capable of isolating high-voltage systems in a compact and robust package, according to the company.
e RXC15 o ers 250 amps of continuous duty for applications up to 1,000 VDC. e single-pole, single-throw (SPST) relay features optional auxiliary contacts that can be used as part of a high-voltage safety circuit, for status feedback or weld detection. e hermetic seal allows the unit to be operated in virtually any environment and minimizes contact oxidation over the life of the switch, the company said. e contactor can be installed in any orientation, even upside-down, providing needed installation exibility.
“ e RXC15 is ideal for those seeking high performance in a small package,” said Brian Munari, Business Development Manager at Rincon Power. “ e chassis-mount terminals make it easy for busbar connections or for routing large-diameter cables. ere’s also a PCB version available for those seeking an even more compact solution. e generous over-current capability makes this a ne choice for medium-duty loads with high inrush without oversizing the contactor.”
Canadian EV charger producer Delta-Q Technologies has begun mass production of its mid-power battery charger, the XV3300, for o -road mobile machinery.
e charging system’s 3-in-1 IP67-rated design includes a 3.3 kW battery charger, a 500 W DC-DC converter for auxiliary loads such as AC, lights and navigation, and an EV charging station interface. e XV3300 charges at nominal voltages from 48 V to 120 V. OEMs can stack up to three 3.3 kW chargers for power levels up to 10 kW with the 58.8, 65 and 120 V DC versions.
e XV3300 can charge at typical AC charging stations in North America and Europe using SAE J1772 (Levels 1 and 2) and IEC 61851 (Modes 2 and 3) connectors.
“No other 3.3 kW charger on the market also includes a DC-DC converter for auxiliary DC loads and an EVSE charging interface in such a compact size,” said Mourad Chergui, Senior Product Manager at Delta-Q. “As we start full-scale production, we can begin to ful ll the substantial demand we received since we rst announced the initial development.”
INFICON, a leak-testing device and instrument manufacturer, has released an upgraded electrolyte leak detector for in-line leak testing of batteries.
e ELT3000 PLUS directly detects electrolyte solvent leakage into a vacuum chamber to test ready- lled lithium-ion and sodium-ion batteries in all cell formats. It has manual and automatic in-line leak detection modes for fast cycle times and high throughput in series manufacturing, and can simultaneously test multiple cells. INFICON says its method identi es leaks with all cell formats, including prismatic, round or button cells and so pouch cells.
With its automated calibration capability, the ELT3000 PLUS can monitor di erent electrolyte leakages in 30 seconds and transfer all test results to each plant’s quality system in real time. e ELT3000 PLUS can evaluate leaks a few micrometers in diameter at 5.10-7 mbar.I/s (helium equivalent leak rate), reducing the risk of battery failure from water or humidity. e smallest detectable leak rate of its predecessor, the ELT3000, was 1.10-6 mbar.l/s.
“With its high throughput and accuracy, integrating the ELT3000 PLUS into the production line will add only seconds to cell production, and it can save millions in costly recalls from malfunctioning lithium-ion battery cells,” said omas Parker, an INFICON Sales Manager. “ e ELT3000 PLUS operates to ISO standards and can easily integrate into a battery cell production line.”
Aspen Aerogels, an aerogel-based electri cation company, has opened new engineering and rapid prototyping facilities in Marlborough, Massachusetts.
Aspen’s 59,000-square-foot Advanced ermal Barrier Center (ATBC) will create Pyro in cell-to-cell barriers to optimize battery pack safety and performance for the e-mobility and energy storage system sectors. e Pyro in barriers prevent thermal runaway propagation and are optimized based on the manufacturer’s performance and critical safety requirements. Global manufacturers can use ATBC’s quick prototyping and real-time engineering collaboration to develop thermal mechanical
barrier technologies. is center aims to commercialize next-generation thermal runaway technologies for EVs while also providing customer-facing technical services.
“Our strategy is to leverage our Aerogel Technology Platform into large important markets, especially those with sustainability and electri cation themes,” said Don Young, President and CEO. “ e ATBC is designed to be the center of our customer-facing work.”
This Inverter offers a modular electrical and mechanical integration of a 3-phase 1200V/340A-550A SiC MOSFET Intelligent Power Module from CISSOID with OLEA® T222 FPCU control board and application software from Silicon Mobility. This unique hardware and software supports the rapid development of e-motor drives up to 350kW/850V, setting new levels in terms of power density and efficiency.
• Up to 350kW/850V
• Modular SiC power module
• Low-ESL DC-Link capacitor
• 900V/400A EMI filter
• Liquid cooling
• Robust SiC gate driver
• OLEA® T222 FPCU controller
• DC & phase current sensors
• Advanced control algorithms
• SVPWM or DPWM up to 50kHz
Powered by CISSOID SiC Intelligent Power Module & Silicon Mobility OLEA® T222 FCPU & OLEA® APP INVERTER Software. www.cissoid.com
Image courtesy of Aspen AerogelsHenkel Adhesive Technologies has extended its portfolio of solutions for EV battery systems with a new injectable thermally conductive adhesive. e new adhesive, Loctite TLB 9300 APSi, provides both structural bonding and thermal conductivity in the battery system. Henkel says the new product has already been adopted by a major EV battery manufacturer.
Designed for applications such as bonding battery cells to modules, or bonding cells directly to cooling systems, Loctite TLB 9300 APSi is a two-component polyurethane thermally conductive adhesive with a high thermal conductivity of 3 W/mK, moderate viscosity, and self-levelling characteristics. In addition to its heat management properties, it’s designed to deliver a combination of good electrical insulation with high bonding performance to a variety of substrates. It’s a solvent-free solution that cures at room temperature without the need for additional energy consumption.
“Loctite TLB 9300 APSi is a testament to Henkel’s continued e orts to innovate new e-mobility solutions tailored to solve today’s battery manufacturing challenges and enable the next-generation designs of tomorrow,” said Holger Schuh, Global Senior Manager ermal Technologies at Henkel. “Its immediate adoption by a major battery manufacturer demonstrates our close partnership with key players in the e-mobility industry.”
Ford appears to be working to build the supply chain it will need to reach its goal of producing two million IRA-compliant EVs per year by 2026. e automaker recently signed lithium supply agreements with ve producers, and Benchmark Minerals predicts that, with these deals and a nickel supply agreement, Ford has secured more than 90% of the lithium and nickel it will require to meet its two-million-vehicle target.
According to Lisa Drake, VP of EV Industrialization at Ford, supply agreements with two major lithium providers have “signi cantly de-risked” the automaker’s expansion plans. Albemarle will supply 100,000 tonnes of lithium hydroxide between 2026 and 2030, and Chilean producer SQM will deliver an unspeci ed amount of lithium carbonate and lithium hydroxide.
Ford is also investing in lithium projects still under development, which Drake says supports the “need to continue exploring reserves and development extraction technologies” in order to “further diversify the industry.”
Ford says it will become the rst customer of Nemaska Lithium, which is developing a mine and processing facility in Québec. Nemaska will supply Ford with spodumene concentrate from its existing Whabouchi mine, and will supply up to 13,000 tonnes per year of lithium hydroxide from its Bécancour plant for 11 years once that facility comes online.
EnergySource Minerals will supply an unspeci ed amount of lithium hydroxide from a 20,000-tonne-peryear brine project in Imperial Valley, California, which is expected to start operating in 2025.
Compass Minerals will provide Ford with up to 40% of the lithium carbonate from its Utah brine project for 5 years once it starts producing. e facility is to enter production in 2025 with an initial nameplate capacity of 11,000 tpa of lithium carbonate.
Last year, Ford signed an o ake agreement with Ioneer, which is developing a lithium mine in Nevada.
Drake says one Ford battery plant will have access to a supply of IRA-compliant nickel sulphate intermediate MHP, under a 2022 deal with Brazilian miner Vale.
South Korean battery manufacturer LG Energy Solution will invest approximately $5.5 billion to construct a battery manufacturing complex in Queen Creek, Arizona. e complex will consist of two manufacturing facilities—one for cylindrical batteries for EVs and another for lithium iron phosphate (LFP) pouch-type batteries for energy storage systems (ESS).
e company plans to invest $3.2 billion in building the EV battery manufacturing facility which will have a capacity of 27 GWh and $2.3 billion in the LFP pouchtype battery facility which will have a capacity of 16 GWh. LG plans to break ground on both plants this year.
LG aims to begin mass production at the cylindrical battery plant in 2025 with an initial capacity of 2,170 cells per year, mainly for EV makers in North America.
e ESS facility, meanwhile, is slated to start production in 2026.
“Our decision to invest in Arizona demonstrates our strategic initiative to continue expanding our global production network to further advance our products in scale and with speed,” said Youngsoo Kwon, CEO of LG Energy Solution.
We offer process solutions for bonding battery cells, sealing or potting battery packs and modules, applying thermal materials, with plasma pre-treatment worldwide. As well as machines for joining electronic components with heat staking.
www.bdtronic.com
Pre-Switch, a producer of AI-based so -switching power systems, has allowed the reprogramming of its Pre-Flex motor/inverter controller SoC for EVs, and has incorporated a digital oscilloscope, allowing designers to remotely diagnose and make modi cations.
Pre-Flex ICs have AI algorithms for so switching across all operating voltages, load situations and temperatures, and adjust cycle-by-cycle. Pre-Switch technology delivers 99.57% (peak) and 98.5% (at 5% load) inverter e ciency for e-mobility applications at 100 kHz switching frequency. Deep View, the integrated digital oscilloscope, allows 12 channels and 160 MSPS to analyze switching timing. Recording and exporting traces show system performance, helping in diagnosing issues and taking corrective action.
“Pre-Switch eliminates switching losses and thereby reduces the amount of SiC or IGBTs needed for high e ciency. is substantially improves low load e ciency and runs at 5-10 times higher switching frequencies which improves motor e ciency and reduces DC link capacitor size and cost,” said Bruce Renouard, PreSwitch’s CEO. “To enable engineers to utilize Pre-Flex AI technology, Pre-Switch developed the CleanWave inverter reference system, the PDS-2 development system with Deep View and the remote programming, Pre-Tune dynamometer motor control tuner, a resonant tank design tool and training courses.”
Temperature control is a critical factor during stress and load testing in the development of batteries and other vehicle components. e heat transfer uid (HTF) used in testing is o en a water-ethylene glycol mixture.
To address these applications, thermoregulation specialist Huber has expanded its portfolio to include temperature-control systems designed and tested speci cally for use with water-ethylene glycol over the temperature range of -45° to 95° C for the automotive industry.
Based on Huber’s Unistat technology, which the company developed over 40 years ago, these systems operate with a very low volume of HTF, and feature plate heat exchangers and a sealed uid system. Huber says this results in very short “time to temperature” times, as well as extremely responsive, stable, accurate and repeatable temperature control.
e Unimotive series comprises ve units with up to 35 kW cooling capacity and 24 kW heating capacity. Each model is tted with a magnetically coupled, speed-controlled pump with a maximum ow of 145 l/ min and pressure up to 5.5 Bar.
Unimotive devices can be individually con gured and adapted to various test situations, or integrated into existing test benches. Various sensors, expansion vessels, pumps and data interfaces are available as accessories.
Huber can build custom-designed solutions for demanding applications, for example those requiring high pressures or aggressive uids.
All Unimotive models are operated using a touchscreen controller that supports the most common data communication protocols (including Pro bus, Modbus, TCP, Ethernet, OPC-UA, RS232 and USB), enabling easy integration into automated industrial environments.
NI, formerly known as National Instruments, has launched a new testing solution for battery validation labs. NI’s So ware-De ned Battery Lab covers the entire battery lifecycle from research and development to validation, production, second life and remanufacturing.
e So ware-De ned Battery Lab is designed to support EV manufacturers and battery suppliers. It allows battery validation and data management and analysis of battery data, and it’s designed to be open and exible to scale for global validation testing and adapt to innovations in battery technologies.
e So ware-De ned Battery Lab draws parallels from the concept of So ware-de ned vehicles, which allows engineering teams to continuously improve performance. As battery technologies evolve and scale, companies can accelerate test system development, maximize reuse of battery testing investments, and connect battery data to improve performance through changes to so ware.
“We’re in the nascent stages of the battery revolution,” said Drita Roggenbuck, Senior VP of the Transportation Business Unit at NI. “Companies are faced with driving down battery costs, improving performance, innovating endlessly, and scaling. At a time when new vehicle programs are as short as ever, and battery validation and production must scale immediately and continuously through the end of the decade, NI’s So ware-De ned Battery Lab o ers the step function change needed to improve time to market and battery performance.”
NI’s Battery Test So ware provides battery testing capabilities out of the box, and also allows customization and extensibility through LabVIEW and other common test so ware.
e newly announced NI SystemLink Enterprise so ware is a scalable enterprise solution for managing labs, improving test operations and analyzing test results. It o ers lab management functionality including:
• Test request tracking and scheduling
• Tester status, utilization and health monitoring
• Test so ware management and deployment
• Battery data aggregation, visualization and analytics
NI’s extensive battery cycler portfolio o ers solutions for every phase of battery development. NI’s newest cycler, HPS-17000, provides up to 150 kW of power. NI’s open so ware allows integration with third-party cyclers to increase development e ciency and enable reuse.
e NI battery measurement and control hardware is built on NI’s soware-connected, modular hardware platforms. ese systems can be quickly recon gured and customized to meet rapidly changing test requirements, including integration with third-party components.
Vitesco Technologies has introduced an upgraded version of its electric axle drive platform for main and auxiliary drives that does not use rare earth elements. Vitesco’s fourth-generation Electronics Motor Reducer (EMR4) will be based on a non-permanent magnet rotor. is rotor powers an externally excited synchronous machine (EESM) without rare earths, which decreases rotor costs and eliminates the carbon footprint of mining and processing ores. e company claims that this machine saves a watt-hour of electricity per kilometer since there is no drag from a permanent magnet eld in the rotor, lowering the drive’s power requirements by up to 5% without a mechanical decoupling mechanism.
“ e EESM option requires an additional inverter module to control the coils. Nevertheless, we are really close to an EESM plug-and-play solution,” said Vitesco Technologies Innovation Head Dr. Gerd Rösel.
Piedmont Lithium’s joint venture partner, Sayona Mining, has released a de nitive feasibility study (DFS) for the jointly-owned North American Lithium (NAL) project, and has increased its forecast for the amount of lithium mineral resources at its Moblan Lithium Project. Both projects are located in the province of Québec. e NAL DFS contemplates increased annual spodumene concentrate production averaging 190,000 metric tons per year over a 20-year mine life. e revised production targets, combined with higher spodumene concentrate pricing, resulted in an increase to the net present value for the NAL project compared to the prefeasibility study completed in 2022.
Sayona undertook a strategic review of mineral resources and ore reserves in order to focus on higher-grade open-pit material. Based on the revised block model, certain indicated resources have been reclassi ed as inferred resources. e study contemplates a mine life of 20 years.
Piedmont has an o ake agreement with Sayona Québec to purchase the greater of 113,000 tpy or 50% of the joint venture’s spodumene concentrate production. Piedmont has agreements with LG Chem and Tesla to provide spodumene from NAL beginning in H2 2023. Sayona Québec is undertaking a prefeasibility study to explore downstream production at NAL, and expects results in Q2 2023.
Separately, Sayona has announced a signi cant increase in mineral resources at its 60%-owned Moblan project in northern Québec. Measured and indicated mineral resources at Moblan now total 41.1 million metric tons, making it one of North America’s most signicant spodumene ore bodies.
Schaltbau, a supplier of safety components for DC systems, has designed contactors to meet the charging and driving requirements of 800-volt EVs, which are equipped with two 400-volt battery banks.
e C801 interlock contactor is compact and designed to t the usual installation geometries inside an EV. e contact area has substantial air gaps, allowing for an insulation voltage of 1,000 V. Due to strong contact forces and optimized contact geometry, the contactor can withstand a thermal continuous current of 250 A and a short-time withstand current of 16,000 A during operation.
e contactors only operate while charging at 400 V charging stations, and do not consume power or generate heat when driving or charging at 800 V. e contactor includes a proprietary mechanical interlock system that keeps the connections from closing even if there are extreme shocks of up to 120 g per 20 ms. Schaltbau is also preparing to produce interlock contactors to meet
increasing demand for high-range mid-size vehicles as well as commercial vehicles and buses.
“When driving, the contacts are open,” explains Günther Rott, Director Business Development Automotive of Schaltbau. “ erefore, it is important that the contactor does not close uncontrollably even under high mechanical loads, as may occur during an accident. Were this to happen, the consequence would be a short circuit that would destroy the junction box and probably also the vehicle.”
The Unimotive range is specially designed for applications in the automotive industry. Typical applications include temperature simulations as well as material testing and temperature-dependent stress and load tests for automotive parts and functional components.
Flow measurement and control options
with water-ethylene glycol mixture
The instant availability of maximum torque makes driving even the most economy-oriented EV way more fun than its ICE counterpart, but few would hold the same opinion about the refueling process, especially at fast charge stations with charging cables that rival a Burmese python in size. Wireless charging does do away with wrangling those massive cables, but as regular readers of these articles can probably guess, there are some signi cant trade-o s involved. Still, it does appear that most of the issues are being addressed, so perhaps this will be the year that wireless EV charging nally hits the mainstream.
Wireless EV chargers are portrayed as cutting-edge technology, but the MagneCharge system made by Hughes (a division of GM at the time) was commercially available on EVs way back in the early 1990s . e MagneCharge system employed a paddle-shaped charging head which contained the primary coil. is was inserted into a mating slot on the vehicle which contained the secondary coil. ough one still had to physically handle a cable, power was transferred across an air gap without any exposed contacts, so this was very much a wireless charging system. More speci cally, it was of the magnetically-coupled (aka inductive) type, which is one of the two main types of wireless power transfer systems being pursued these days (the other—to be discussed in much more detail below—utilizes resonant coupling).
An inductive wireless power transfer system consists of (at least) two coils of wire that are usually at spirals in shape and which are placed in very close proximity and in the same plane and axial orientation. An alternating current supplied to one or more primary coils generates a time-varying magnetic eld that induces an alternating current in the secondary coil. If that sounds suspiciously like a transformer to you, that’s because it is—the only di erence is that the primary and secondary are physically separated rather than wound on the same core. It should be noted that minimizing the separation between primary and secondary is a major design driver in proper transformers as it maximizes the amount of coupling between the two sides—ergo, the farther the two coils are apart, the lower the amount of power that can be transferred between them. is is sometimes oversimpli ed as e ciency being inversely proportional to separation distance (air gap), and that isn’t entirely untrue, but it’s more accurate to say that increasing the air gap reduces the amount of power that can be transferred because as the air gap increases, more of
Two main types of wireless power transfer systems are being pursued these days: the inductive type, which is magnetically coupled, and resonantly-coupled systems using electromagnetic fields.
the magnetic eld lines from the primary only travel in a loop through the air back to itself, without ever intersecting the secondary.
In transformer terminology, these orphaned loops of magnetic eld are called leakage, and they give rise to the dreaded leakage inductance, which will store energy received from the source only to send it back a quarter-cycle later (behaving much like a spring). In other words, as the separation between the coils increases, more of the energy that would be transmitted by them instead circulates between the power source and the primary’s leakage inductance, doing no useful work. If there were no resistance present, then this circulating current would have no e ect on e ciency, but in the real (or practical) world there are I2R losses incurred, hence increasing the separation distance does reduce e ciency. One thing to note is that the purely magnetic elds of the inductively-coupled system
(as compared to the electromagnetic elds used by the resonantly-coupled system) aren’t blocked by non-magnetic metals like aluminum, copper, etc, but will induce currents in them, and that will lower the overall transfer e ciency.
e Hughes MagneCharge system aside, which operated at 6.6 kW (and had a very impressive e ciency for its time of 80%), inductively-coupled wireless power transfer systems are typically used at lower power levels and where a low separation distance (less than a few mm) is easy to maintain, especially when minimizing cost is important, since the coupling mechanism really is no more complicated than two coils which can be treated as a regular transformer from the circuit’s perspective.
e Hughes MagneCharge system did have some signi cant safety advantages over conductive charging interconnects such as J1772, CHAdeMO, etc, but it wasn’t much more convenient to use, as you still had to get out of the EV and physically place the charging paddle into a slotted receptacle on the EV to start charging. Arguably not a big deal if the weather is nice (or the charging station is inside a covered garage), but there’s no denying that merely having to park in a speci c (but not too speci c) spot then just tapping a button on a phone app or the EV’s user interface to initiate charging would be far more convenient. Such an arrangement with an inductively-coupled system would require an almost Rube Goldberg-like mechanical contraption to bring the two coils close enough together to e ect power transfer with reasonable e ciency, and to retract the EV-side coil far enough up in the undercarriage to have su cient ground clearance to survive potholes, speed bumps and the like while driving.
As the separation between the coils increases, more of the energy that would be transmitted by them instead circulates between the power source and the primary’s leakage inductance, doing no useful work.Figure 1: Block diagram of an inductive wireless power system
A system that didn’t require the power transmitting and receiving coils to be brought into such close proximity (and that didn’t require such precise positional alignment of them, too) would make it so that xed coils could be used on the ground and on the EV, and that is where the resonantly-coupled approach starts to shine. It is tolerant of a much larger air gap between transmitter and receiver (over 100 times larger—tens of cm can be accommodated), is less picky about alignment between the two, and as a bonus, the magnetic eld from the transmitting coil will naturally be most attracted to the receiving coil, and will drop to a very low level in the absence of a load on the receiving coil, rather than radiating o into free space in all directions at all times, as is the case with the inductively-coupled approach. What’s not to love about resonant coupling, then? Certainly plenty—and more on why below— but the basic issues are that it’s much more complex and far less tolerant of variations in component value. Despite that, resonant coupling still compares favorably to the mechanical contraptions needed to accommodate inductive coupling at a similar power level (on the premise that electronic complexity is usually less costly to implement than mechanical).
Power transfer in the resonantly-coupled system uses electromagnetic elds, the same used by a microwave oven, a radio broadcast station, etc, except that the bulk of the energy is transported by the magnetic eld component, and the electric eld is e ectively out of the picture. is is possible because
the electric and magnetic elds don’t come together to form a proper electromagnetic eld until they have traveled some distance from the antenna. Furthermore, closed loops (like coils) are best at radiating magnetic elds, and are largely ine ective at radiating electric elds (open wires or plates are best for that). Basically, then, as long as the transmitting and receiving coils of the resonantly-coupled system are located within the so-called near eld—loosely de ned as a distance of 1/6 of a wavelength or less, where the wavelength, in meters, is fMHz / 300—power transfer will occur using just the magnetic component of the electromagnetic eld, and little will be diverted into the electric eld. While the circuitry involved in the resonantly-coupled system is far more complex than that of its inductive counterpart, the transmitting/receiving coils might not look that di erent. e main di erence is that, in the resonant system, capacitors are added to each coil to form—no prizes for guessing correctly—resonant LC networks (or tanks in the argot) which will naturally oscillate at a frequency (in Hz) of 1 / (2 * Π * (L * C)^0.5) and have a characteristic impedance of (L / C)^0.5.
Assuming that both LC tanks have fairly similar resonant frequencies (and the separation distance is within the near eld), they will preferentially couple to each other rather than to free space, and will generally ignore other non-metallic objects (as with purely magnetic elds). is e ectively results in power tunneling directly from the transmitting LC tank to the receiving one in the resonantly-coupled system, rather than radiating o in all directions, as would be the case with the electromagnetic elds
of a conventional RF wireless antenna system, or in big loops that follow the same path whether a receiving coil is present or not, as is the case with the purely magnetic elds of the inductively-coupled system.
Another advantage of the resonantly-coupled system over the inductive one is that the LC tanks automatically convert any waveform thrown at them into a pure sine wave, resulting in much lower noise emissions (read: a far easier time getting through EMC compliance testing). And just as LC networks are used to perform so switching in power converters, they can do the same here, greatly reducing switching losses in both the downstream recti er as well as the upstream power converter.
So far the resonantly-coupled system doesn’t seem that much more complicated than the inductive one—just add a capacitor across each power transfer coil and call it a day, right?—but there are numerous headaches that come from resonant operation that might have you thinking that the MagneCharge paddle wasn’t such a bad solution a er all. First, as already mentioned, real-world inductors and capacitors tend to have much looser tolerances on
Power transfer will occur using just the magnetic component of the electromagnetic fi eld, and little will be diverted into the electric fi eld.
value, and both (but especially capacitors with any kind of dielectric besides air or vacuum) will dri in value over time and temperature, so there needs to be some means of automatically tracking the actual resonant frequency of each tank. e usual solution here is a phase-locked loop, or PLL, that tries to maintain a peak in sensed voltage (or current) in the LC tank by adjusting the driving frequency. However, it is critical that the frequency adjustment remain on one side of the peak, otherwise the control loop action will invert (i.e. as the peak value decreases, the frequency adjusts to make it worse, rather than correcting it). Second, resonant LC tanks work best at a xed power level (given by the loaded Q, or the ratio between the load resistance and tank characteristic impedance), as varying the pulse width on the driving side does little to change the power throughput (a side e ect of the resonant LC network turning any waveform applied to it into a sine wave), so if the power level needs to change, either the driving frequency has to change or the driving pulses have to be supplied in bursts. ird, bringing the two LC tanks too close together will paradoxically result in them detuning each other! Basically, designing a resonantly-coupled wireless power transfer system that can be mass-reproduced—i.e. made into a real product—is a Herculean feat, and that probably explains why it is taking so long for such products to hit the market, despite the extremely alluring convenience they promise.
Multiphysics simulation helps in the development of innovative battery technology by providing insight into mechanisms that impact battery operation, safety, and durability. The ability to run virtual experiments based on multiphysics models, from the detailed cell structure to battery pack scale, helps you make accurate predictions of real-world battery performance.
» comsol.com/feature/battery-design-innovation
Construction vehicles are being electri ed at a surprisingly rapid pace, as operators recognize not only the cost savings, but the advantages of silent, emission-free operation. However, the high power requirements of these vehicles mean that vehicle designers face unique technical challenges, especially when it comes to circuit protection.
High-voltage DC current is more dangerous and harder to interrupt than the comparatively sedate 48 volts used in smaller vehicles. Unfortunately, thanks to the fast pace of electri cation and the slow pace of standards bodies, electrical safety standards for heavy vehicles are lagging behind the market.
As the industry gets ahead of the standards, the uncertainty is delaying time to market for many companies, and cutting into pro ts (to say nothing of potentially endangering peoples’ safety).
Circuit protection specialist Littelfuse began its history selling products for the Ford Model T, and it makes circuit protection components for every kind of vehicle imaginable. Geo rey Schwartz, Business Development Manager at Littelfuse Commercial Vehicle Products, told Charged some stories to illustrate the chaotic situation that’s delaying the move to EVs.
Littelfuse has seen designs using 32 V fuses for 600 V systems, and companies using industrial fuses because high-voltage automotive-quali ed fuses aren’t available. When engineers specify components that aren’t automotive-rated, they are then forced to spend time in extensive testing to make sure their vehicles don’t catch re.
Suppliers have to guess at what the eventual standards will look like, and try to ensure that their products will meet the standards when they’re nally published.
Q Charged: So, there’s a lack of standards for vehicles that use higher-voltage electrical architectures?
A Geo Schwartz: Yes. All the standards organizations are running behind. I’m on the SAE Truck and Bus Electrical Systems Committee, and I know we are trying to write 48-volt standards now. We are looking at a few higher-voltage standards, but the real standards, they’re probably three to ve years out. It takes so long to write a standard, for everybody in the industry to come together and come to an agreement. e standards committees just don’t move that fast.
We’re seeing a series of electrical architectures, with one group around smaller equipment at 48 volts, and a medium range—200 to 500 volts—in large equipment and medium-duty trucks. en as you get into larger vehicles—
“
We’re seeing a series of electrical architectures, with one group around smaller equipment at 48 volts, and a medium range—200 to 500 volts—in large equipment and medium-duty trucks.”
trucks, tractors, large construction equipment—that stu ’s all going to 800 volts up to 1,000 volts.
When will they need to go higher than 1,000 volts? I’m pretty convinced that’s a 2035 problem. e EPA requirements are that commercial vehicles will have to be 40% electric by 2035. And there’s 40% of the Class 8 market and the medium-duty market that [drives] under 250 miles a day. With current technology, they can hit those numbers. You can get 250 miles a day even with a full load nowadays, so that technology is there for right now. But the problem is going to come in 2035 when they exhaust that 40%. en you have to look at longer-range vehicles, and that’s when I suspect you’re going to see them go above 1,000 volts, because they have to pack more power into the device.
A couple of things are holding that up right now—number one is the power electronics. Most automotive power electronics are maxed out around 1,200 volts. You’re starting to see some creep up to 1,500, 1,800 volts, but most of them, and most of the volume and a ordable ones, are 1,200 volts and under. ey can’t go much above 800 to 1,000 volts in battery technology with their electronics only at 1,200 volts.
Q Charged: Would you say the biggest standards gap is in safety best practices?
A Geo Schwartz: Yeah, things like what’s the proper spacing of wiring and stu like that. What do you need for gapping in the wiring, and what are the connectors you need at that level? And then there’s interoperability and all those standards that we take for granted in the 12- and 24-volt world. ey don’t really exist in the 800-volt world.
Right now I’m working on a committee where we’re dening the standard for an ePTO (electric power take-o ) connection. We’re talking about the physical connector, but there’s also the communication side of things, the electronic handshaking routine that has to take place—when you plug this thing in, it’s got to acknowledge and say, Okay, I’m connected correctly, and then turn on the power. With the HVIL [high-voltage interlock], you’ve got to turn the power o when you pull the plug out of something.
One of the things that standards organizations do is try and make it about the interface and about the performance rather than the actual design, so that there’s some freedom for companies to nd a base for competition. As long as they are interchangeable, what you do with the rest of it is a competitive advantage.
Q Charged: Do the same standards bodies oversee on-highway stu ?
A Geo Schwartz: Yeah. e SAE committee covers onand o -highway. ere are specialty committees that cover special areas of o -highway, but mostly they kind of count on the truck and bus committee to write the electrical standards, so there are rarely separate standards for those things. And there’s enough [overlap] between those organizations in membership that we share information nicely and we try and work together.
Q Charged: How are vehicle designers dealing with the lack of standards? And what do you recommend to designers right now that are tasked with designing these systems?
A Geo Schwartz: It’s the Wild West. A lot of people out there are running industrial fuses in vehicles. And yeah, they’ll work, but industrial fuses are not built for vehicle-based vibration and shock. ey’re built to go in a building, so they’re just not capable in a lot of cases of maintaining life in a vibration situation, which is typical of a vehicle.
As for designers, nd somebody who knows what they’re doing and work with them. ere are any number of suppliers out there who have the expertise, who are willing to work with you. Talk to them early, bring them on board, make them a partner. ey’ve brought experience in from other people. ey’ve been doing this for a long time.
at’s probably the best advice I can give: Find a supplier partner and bring them in.
e biggest problem with the lack of standards is that it’s hard for suppliers. It’s hard for OEMs to gure out what to
It’s the Wild West. A lot of people out there are running industrial fuses in vehicles. And yeah, they’ll work, but industrial fuses are not built for vehiclebased vibration and shock.
make, and therefore everything is essentially custom. So a lot of this stu ends up costing more because it’s one-o . It’s also very low-volume right now, so that tends to drive the cost up as well. Standards will help drive consistency, and they’ll drive volume improvements and cost improvements.
Q Charged: I imagine it a ects speed to market as well.
A Geo Schwartz: Of course it does, because everything has to be customized for that particular OEM. is one’s doing it a little bit di erently than that one. We do high-voltage PDMs [power distribution modules], and everybody keeps coming in asking for it o the shelf. But nobody wants it o the shelf: “Mine’s a little di erent. Can’t you do something a little bit di erently?”
Q Charged: How is Littelfuse trying to bridge the gap between the demand for products and the lack of standards?
A Geo Schwartz: We’re already out there in the market with all kinds of products, and the standards are well behind. We’re starting to bring components out now that are getting up into the 1,000-volt realm. e testing involved, because the energy levels are so high, just takes time. We are still working on getting our 1,000-volt fuses out. Once you have the design done and you have it in production, there’s about a year’s worth of testing we need to do for every single one of the [voltage] values to get it quali ed.
ere’s a 500-volt standard for fuses right now. ere’s no 1,000-volt standard. So we’ve taken that 500-volt standard that we helped write and we’re extending it up to 1,000 volts. We’re pulling stu in from ISO standards, from OEM standards, and trying to pick worst-case of everything. If we can hit worst-case in everything, we will be able to meet everybody’s standards. at’s kind of what we’re designing to.
Q Charged: I understand you saw a huge variety of electri ed vehicles and industrial equipment at the recent CONEXPO.
A Geo Schwartz: I was surprised—I thought that it was going to be mostly small equipment, but there was a lot of mid-sized to larger equipment that was also going electric, including some really large stu for mining. Probably one of the fastest things out there going electric is underground mining, because one of the big problems is, when you have diesel equipment down in a mine, how do you get all the fumes out?
Small construction equipment is tending to move to 48 volts, for two reasons. Number one, they can get a full day’s work out of a 48-volt battery pack, so they don’t need to go higher. And at 48 volts, they’re below that 60-volt threshold and don’t have to have as much protection and guarding because it’s not considered to be a lethal voltage level.
e other thing is they’ve got a lot of existing infrastructure already built for the material-handling industry.
ere’s a huge number of 48-volt forkli s and things like that and they’re stealing components from those areas to build their products. Forkli s are a pretty high-volume business in our realm. Not like cars, but they make several hundred thousand forkli s a year, easily—maybe worldwide, over a million. at’s a higher-volume product and that tends to drive lower prices, so they’re using those 48volt parts, components and architecture.
We’re seeing more and more movement towards electric in construction, and that’s happening for a couple of reasons. Number one, it’s a lot better, particularly when you’re working indoors or when you’re working in an urban environment. Also, it’s a maintenance issue. For those vehicles, maintenance is key. If your car is not working—oh, that’s a pain, but I’ll use the other car or I’ll take the bus. If your excavator or your loader is not working, you don’t make money that day. So maintenance and uptime is really key and electric vehicles are better for that in this market.
Bobcat recently introduced a completely electric
vehicle. ey even got rid of all the hydraulics. ey’re replacing hydraulic cylinders with electric actuators. e hydraulics in those vehicles are usually the number-one maintenance problem, so they are eliminating one of the biggest problems. You would think they can’t get enough power out of them, but they can. Using screws and gearing they can match hydraulics.
We have been saying that a lot of the big construction equipment wasn’t going to go BEV. e work cycle is longer and tougher, and charging becomes an issue. You can charge a small piece of construction equipment on a mobile charger or a mobile battery, but those bigger pieces of equipment take a lot of power to charge and they’re sitting out in a eld. So I think the small ones are going to go electric fast, but the big ones are going to go electric slower.
One interesting problem that we have in these EVs that you don’t necessarily have in the diesel ones is that because they’re lighter weight, with berglass and all kinds of lightweighting, where do you ground the thing? Grounding becomes a problem, so we’ve actually released a new series of grounding boxes for customers to be able to consolidate ground.
Q Charged: Are you seeing a lot of auxiliary systems being electri ed on those large systems?
A Geo Schwartz: Not really yet. I’m a little surprised. We were expecting the heavy truck market to electrify a whole series of their auxiliaries and take the loads o the motor. What we’ve heard is they’re going to skip that step entirely and go straight to BEV. ere’s a new greenhouse gas requirement on large vehicles for 2027 engines, and California’s adopting that next year. We thought that was going to drive a lot of 48-volt stu , but everything we’re hearing now says they’re going to skip right by that and go pure BEV.
Q Charged: Is there any other commercial o -highway stu that you think is a fast-growing market?
We were expecting the heavy truck market to electrify a whole series of their auxiliaries and take the loads off the motor. What we’ve heard is they’re going to skip that step entirely and go straight to BEV.
A Geo Schwartz: I’ve seen a lot of interest in small farm tractors. I know that Case New Holland has launched an electric tractor, and Monarch is going electric. Particularly for small and specialty farmers where they’re working in tight with the crops. ere’s a company called GUSS that does a fully autonomous sprayer, and now they’re bringing an electric version out as well.
I’ve seen a lot of small equipment, a lot of harvesting assist equipment. ere’s a company called Burro that makes an electric crop hauler. It runs from where the picker is working to a central location—the picker is hand-picking specialty crops, and the Burro is right by his side, he loads it up, so he can just concentrate on picking.
We’re also seeing interest for hybrids based on digestive materials. For instance, a farmer could take all his scraps and put them into a digester, make his own fuel and use that to run a hybrid tractor. Case New Holland brought out a methane-powered tractor that [runs on methane] made from farm waste.
e other thing of course is that drivers love them now, which is fantastic. We hear comments like, “It’s easier on me, less vibration, less noise. I don’t come home smelling like diesel. I don’t come home as worn out and tired.” In the truck market, driver retention is a really big issue, because there’s just not enough truck drivers out there. If they’re not getting treated right, they can move relatively easily, so you want to retain your drivers.
Every one of the major OEMs is launching an electric truck series. e primary customers right now are the ports—Port of Long Beach, Port of Los Angeles—and the ports around the country are usually in urban environments. Transporting goods out of that environment tends to have an overly heavy e ect, particularly on less opportune communities because they’re kind of built around the port, so they’re very sensitive to that pollution.
erefore, a lot of electric and hydrogen vehicles are
being brought into that market quickly. In most cases they’re running from the port, 50 or 100 miles to a warehouse and then running back to the port, back and forth. ey could do three, four runs a day without a problem, without having to recharge. So those vehicles will probably go electric pretty quickly.
e other market that’s probably going to go electric quickly is refuse. Garbage trucks. You’re operating close in neighborhoods, so the quiet is a huge advantage, and you have room to have a pretty good-sized electric actuator on a garbage truck because it’s a bigger vehicle. And also, huge amounts of regenerative braking going on. ey stop, start, stop, start, and because they’re doing that, they’re running that electric motor in a range where it’s very e cient in that low end of the torque band.
Q Charged: In terms of regulations, what are the biggest ones driving the market in the commercial space?
A Geo Schwartz: e MOU is an agreement between California and several other states that are ramping up the requirements for zero-emission commercial vehicles, with the goal to be completely emission-free by 2050. I think it’s gotten up to 17 states total now. at’s for new purchases— the lifetime of a truck is usually at 15 years plus—seven or eight years in the primary market and up to 10 years in the secondary market.
at’s one of the biggest ones, and there’s also a couple of big California regulations. California is shortly going to outlaw the use of diesel engines in transportation refrigeration units. e reefer boxes that are up on trailers or trucks, they’re going to have to go all-electric. Construction equipment, lawn and garden equipment is going electric in California as well. Shortly they’re going to eliminate the ability to buy gas mowers and stu like that.
Now California just actually moved it up 10 years. ey said they want 100% of commercial vehicles to be zero-emissions by 2040. I have doubts whether we could hit that. I think we could hit 50, 60, 70%. But when you get into longer-range vehicles, the problem is still going to be infrastructure.
You think it’s hard to charge a car? ink about how much energy you have to pump into a truck. e Megawatt Charging System standard is intended to charge a Class 8 truck in 30 minutes. It’s capable of up to 2.2 megawatts. It’s a huge water-cooled cable. It’s a lot of power. I think the truck technology is going to be there to do it, but I’m not sure the grid will get built out fast enough to do it on schedule.
Everyone in the EV industry is talking about the IRA and the BIL, two sets of federal regulations that include strong incentives for automakers to establish domestic supply chains for EV raw materials and components. Not everyone is happy about the requirements, and there are a number of issues that need to be considered as the new regulations are nalized. However, bringing mining and processing raw materials closer to the sites of vehicle production is necessary both for reasons of sustainability and national security.
For certain key raw materials, much of the mining and almost all of the processing currently takes place in China, and in other countries that are geographically distant, have environmental or human rights issues, or all three. One of these materials is graphite, which is the main ingredient in EV battery anodes. e few companies that have access to
graphite mines in North America are the belles of the EV ball at the moment. One of these is Westwater Resources, which controls what it says is the second-biggest graphite deposit in the US (the biggest is in a remote region of Alaska).
Westwater holds mineral rights to the Coosa graphite deposit, which is located across 42,000 acres in Alabama. e company is currently building a graphite processing plant in Kellyton, Alabama. e rst phase of plant construction will produce 7,500 metric tons of re ned graphite each year.
We rst met Jon Jacobs back in 2013, when he was working at Wildcat Discovery Technologies, a battery research rm that developed an innovative process to rapidly synthesize and evaluate energy storage materials. Now Jacobs is Chief Commercial O cer at Westwater Resources, and he spoke to Charged about his company’s plans to start supplying graphite anode material in the heart of the Battery Belt.
Q Charged: Graphite’s a hot property these days. Tell us about Westwater’s plans.
A Jon Jacobs: Westwater Resources is positioned to be the only vertically integrated natural graphite supplier in the United States. Prior to my joining Westwater, I was really naive about the importance of graphite and the fact that none of it is currently produced in the US. Much like lithium was ten years ago, graphite is a sleeping giant that is about to get a big awakening. e growing EV market and the IRA are now driving incredible demand for domestically produced graphite.
If you spend time in the battery industry, you’ll nd most of the discussion is about new and promising next-generation materials like silicon anodes or lithium metal. Yet, these technologies still face major technical challenges. Meanwhile, in terms of material by weight, there’s more graphite
in a battery than anything else. Today, over 75% of all the battery graphite comes from China. Unbelievably, none of it currently comes from the US.
Along comes the In ation Reduction Act. It’s amazing what the IRA is driving in terms of new companies and investment. Take Westwater as an example. Westwater transitioned from mining uranium, of all things, to becoming a graphite anode producer—all because of these new trade rules.
Fast forward to today and Westwater is building a graphite plant in Alabama, and people are eager to buy our capacity. How much more are people willing to pay to get US graphite compared to Chinese suppliers? Natural graphite from China sells for about $7 a kilogram, yet companies setting up factories in the US are willing to pay more than that to get graphite domestically if it meets the IRA requirements. is is roughly how the math works: In 2023, 40% of the
critical materials in your battery must be “produced” in the United States or one a few designated free-trade partner countries. “Produced” refers to the percentage of value added during production. By 2027, the critical material requirement will increase to 80%.
Now, if you look at just the materials half of the $7,500 tax credit, there’s $3,750 available, and graphite is on a short list of critical materials, along with lithium, cobalt, nickel and a few others. If you do the math and make some assumptions, it means $550-600 of the total tax credit is attributable just to graphite. For US cars with 80 kWh packs, cell makers should be willing to pay as much as $7 per kilogram more than non-IRA sources just to get anode material from the United States.
Of course, a material supplier like Westwater will need to share the IRA value with the cell maker, the OEM and the end customer, so the real premium will be lower. But without the IRA, it would be di cult for a US company to stand up a facility and compete with China. To be fair, China got most of its battery business o the ground due to government subsidies of its own.
ere’s an additional factor to consider too. e IRA value won’t necessarily be the same at every cell maker, as it’s not a linear calculation. For example, if a cell maker purchases 45% of its battery materials from IRA sources but is still 5% short overall, the company might be willing to pay a lot more to get that nal 5% because that determines whether it gets the entire credit or not.
Q Charged: Tell us about the processing plant Westwater is building in rural Alabama.
A Jon Jacobs: e plant is under construction in east-central Alabama in a town called Kellyton, conveniently located in the growing US Battery Belt. Prior to Westwater, the only major employer in the area was Russell Athletic, a company that makes jerseys and sporting apparel. At one time, Russell employed over 7,000 people in this area. Over the years, however, Russell moved most of its jobs elsewhere, leaving this beautiful part of Alabama in a lurch. I’ve heard as many as half the residents in the a ected area moved away. Fortunately, the battery industry and the IRA are about to change everything, along with some good fortune that one of the battery industry’s most important minerals just happens to exist in that same area. Westwater’s plant will likely employ many of the people nearby. Who knows, maybe we’ll ask Russell to make our uniforms! It’s a
great US story—the government got it right with the IRA, and it’s already generating tangible e ects.
Q Charged: You recently signed a joint development agreement with SK On, a South Korean battery manufacturer that’s operating two EV battery plants in Georgia, and is building several more in the Southeast.
A Jon Jacobs: Yes, and we hope to strike similar JDAs with other cell makers too. Every cell maker, because they’ve been using graphite for 40 years, has their own proprietary twist. at’s what the JDA is about—SK will come into our plant and say, “Okay, for our material, we want you to do this extra thing.” Another cell maker might ask us to do a di erent extra thing. A JDA enables us to openly collaborate with our customers to produce the speci c material they want.
Natural graphite from China sells for about $7 a kilogram, yet companies setting up factories in the US are willing to pay more than that to get graphite domestically if it meets the IRA requirements.
Q Charged: ere’s some controversy around the IRA in Washington. For some reason Joe Manchin’s mad about it, and he was threatening to vote to repeal it.
Jon Jacobs: e main thing I’m hearing is that the rules pertaining to Chinese company involvement aren’t totally clear. SK, LG and SDI announced joint ventures, and that they’re going to build plants in the US, and nobody has an issue with that. Meanwhile, a few Chinese companies want to build plants in the US, but the reply from di erent states is inconsistent. Some say, “No way—I’m not going to support you.” Other states, like Michigan, say, “Your money’s as good as anybody else’s, so you’re welcome here.” ere may not be a consistent response here until the IRA language is fully vetted.
ere was also a long-antici-
As electric vehicle technology evolves, so should your expectations. Our customizable CoolTherm® products help electric vehicles go longer, charge faster and have higher reliability.
Solutions:
▪ Gap Fillers
▪ Potting & Encapsulants
▪ Structural Adhesives
Applications:
▪ Battery Packs
▪ Motors
▪ Charging Systems
CoolTherm
pated update to the IRA language on March 31. An added restriction was placed on things like nickel, cobalt, lithium and graphite, requiring the initial mining to occur outside of China regardless of how much value-added processing occurs later. If interpreted correctly, that’s an added game-changer for Westwater with our rights to the largest graphite deposit in the contiguous US.
Q Charged: Are there going to be enough of these materials that manufacturers can source from places that will meet the requirements?
A Jon Jacobs: at’s tough to predict, but it’s not going to be easy. To put things in perspective, Westwater will produce 7,500 metric tons per year of natural graphite a er our Phase 1 construction is complete. Just one of SK’s plants in Kentucky or Georgia or Tennessee would require roughly that amount of graphite. Although Westwater will increase capacity to over 40,000 MT/year in 2028, there aren’t a lot of other IRA-compliant options available. I believe global EV market growth requires that 6-8 new gigafactories be built every year for the foreseeable future. ese plants are going to require a lot of battery materials from somewhere other than China.
Now, add to that the ratcheting factor of the IRA. In 2024, only 50% of the critical materials need to be IRA-compliant. is then increases 10% each year until it reaches 80% in 2027. We and others intend to boost our capacity over time, but it will require awless execution to keep material supply in line with demand.
Q Charged: Is the post-processing the slow part, or is it actually digging it out of the ground or scraping it o the surface?
A Jon Jacobs: Once graphite is extracted from the ground, it must be puri ed, which usually takes place at the mine location. is can all take a couple days, plus several months to ship it from remote locations around the world to wherever it will be processed. In our case, the resulting feedstock material will be conveniently trucked 30 minutes up the road to our Kellyton processing plant to be converted into battery-grade anode material.
e processing of the feedstock into nished anode material is well understood. e Chinese have been doing this for decades. Although our overall process is similar, we are using what we believe to be superior manufactur-
ing equipment and more sustainable processes, without the use of harmful acids. e basic steps involve reduction of the graphite particle size, turning it into spheres, removing contaminants and coating the surface of the nished material. e overall processing steps also take a couple days. So to answer your question, the two general steps are similar in duration.
Q Charged: How much graphite, and what kinds, go into a cell?
A Jon Jacobs: at’s a good question. In a 60 kWh EV battery pack, there’s roughly 50 kg of graphite. Graphite comes in two avors. ere’s natural graphite, which is what Westwater produces, and there’s arti cial or synthetic graphite, which is made, ironically, from oil re ning by-products. Most batteries today are produced using a blend of natural and arti cial graphite. Overall usage of each type by volume varies from year to year, but it’s roughly 50/50. e downside to arti cial graphite is that it’s nearly double the cost of natural graphite, but companies use it because it can o er cycle life advantages. Like any industry though, cell makers are incentivized to use lower-cost materials. erefore, companies are still nding ways to improve natural graphite, and momentum is arguably in its favor.
Q Charged: Is any of the synthetic graphite produced in the US?
A Jon Jacobs: ere are a few companies ramping up production now, including Novonix and Anovion.
Q Charged: So, all of your direct competitors will import the raw material from somewhere else?
A Jon Jacobs: I suppose that’s true if you’re talking about natural graphite competitors within the US. is is why we view the Coosa deposit as a long-term competitive advan-
The IRA is probably here to stay. It is clearly working to generate investment and jobs across the US.
tage. It reduces graphite feedstock supply risk with the potential to lower costs from vertical integration.
Q Charged: Are there no other deposits anywhere in the US where you could start a mine?
A Jon Jacobs: ere are small deposits in Texas, and I think there is a company that has one up in the Adirondacks. ere’s one deposit larger than ours in Alaska, but it’s likely too expensive given its remote location.
Q Charged: e activity is so great now that I’m starting to think that pressure from the industry will prevent the politicians from reversing the IRA in the future. ere’s so many ribbon-cuttings going on right now, especially in the Battery Belt in the southern states, which presumably would be the people who would overturn it if they get power in a few years.
A Jon Jacobs: I agree the IRA is probably here to stay. It is clearly working to generate investment and jobs across the US. is should appeal to both political parties in a
large number of states, so I don’t think it will go away.
Q Charged: e EU has to come up with some kind of response, right? Otherwise, everything will be made here and shipped to Europe.
A Jon Jacobs: It’s funny—Europe started pumping money into battery infrastructure three or four years ago while the US was doing very little. e IRA has now put the US back into the spotlight. It wouldn’t surprise me if Europe sweetens its own legislation related to EV tax credits to compete with what’s happening here. If they don’t, most new material and cell production investment could go to the US. at said, there’s a lot of production in the EU that’s not going to be stopped due to their head start. Plus, the global battery and EV markets will eventually be big enough to require local supply.
A er 100+ years of auto production, you still see companies throughout the supply chain producing things in all the main regional markets around the world. e transition to EVs is unlikely to change that dynamic once the market matures. But in the near term, it feels like the gold rush!
Construction material provider Holcim will deploy up to 1,000 electric trucks from Volvo by 2030. Deliveries will start in the fourth quarter of 2023. is deal, reportedly the largest commercial order to date for Volvo electric trucks, is part of a wider partnership between Holcim and Volvo Group to deploy electric trucks across Holcim’s operations in Europe between now and 2030.
Both companies are founding members of the First Movers Coalition (FMC), a group of companies that aim to use their purchasing power to create early markets for innovative clean technologies.
“ e net-zero transition requires deep collaboration across value chains,” said Holcim Chairman and CEO Jan Jenisch. “We are excited to be partnering with Volvo to decarbonize our European operations’ logistics with electric eets, advancing our goal to reach 30% of zero-emission heavy-duty truck purchases or contracts by 2030.”
Mercedes-Benz has developed a new purpose-built modular and scalable architecture dubbed Van Electric Architecture (VAN.EA), upon which all its newly developed vans will be based starting from 2026.
e company is planning to reduce its portfolio of van variants by more than 50% compared to its current ICE o erings, while covering the same use cases for customers.
e platform consists of three separate modules: front, center and rear. e front module consists of the electric powertrain and the front axle, and is the same in all VAN.EA variants, as part of an optimized common parts strategy. e center module scales the vehicle length. is is also where the standardized battery case is placed. High-voltage batteries with di erent capacities can be installed within the case. e rear module will be available in two versions: with an electric motor for the all-wheel-drive variants of VAN.EA and without one for the front-wheel drive variants.
”VAN.EA enables us to consolidate our mid-size and large vans down to only one architecture and signi cantly reduce the complexity of our product portfolio,” said Mathias Geisen, Head of Mercedes-Benz Vans.
Canadian materials company Nouveau Monde Graphite (NMG) and Caterpillar have signed agreements to supply NMG’s Matawinie Mine with an integrated solution that includes a zero-emission vehicle eet, supporting infrastructure and services.
e agreements encompass machines such as hydraulic excavators, mining trucks, wheel loaders, dozers and motor graders, as well as charging and energy storage infrastructure and equipment maintenance services.
As part of the agreements, the two companies have mapped the development and testing of equipment and infrastructure at NMG’s Matawinie Mine in Saint-Michel-des-Saints, Québec. Equipment will be progressively replaced with Cat zero-emission machines as they become available.
e two companies have also signed a non-binding memorandum of understanding to advance commercial discussions targeting NMG’s active anode material. A full circular value chain could be established, in which NMG would supply carbon-neutral graphite materials to Caterpillar for the development of its battery supply chain that would serve to electrify heavy vehicles, including NMG’s Matawinie eet.
“Not only will we bene t from Caterpillar’s expertise, products and latest technological developments, but our team will also be sharing insights, testing equipment for further optimization and providing battery materials to support electri cation beyond our mine,” said Eric Desaulniers, founder and CEO of NMG.
Fleet customers represent a lucrative line of business for General Motors. is year, the company reported that GM Fleet achieved its best rst quarter of commercial eet sales since 2006.
In order to better address the rapidly-changing eet market, GM has now brought all of its eet products and services under a new brand called GM Envolve. e new business unit will be headed by VP of Commercial Growth Strategies and Operations Steve Hill.
GM Envolve is “a one-stop customer experience, designed with input from customers and dealers, to make it easier to tap into all the products and services GM has to o er.” GM Envolve will o er “a full program of tailored solutions, providing high-tech management for both ICE and EV commercial eet operations,” and “give business customers more ways to reduce their environmental impact, streamline eet operations and increase driver safety.”
Each large eet customer will be assigned a dedicated account executive to o er coordination and recommendations, “backed by a team of experts to help identify and curate a package of GM’s technologies and innovative solutions for each customer’s business.” A digital platform for customer use is in the pipeline.
GM Envolve is designed to give eets “e cient, uncluttered access” to various GM business units, including BrightDrop, GM Genuine Parts, OnStar Business Solutions (tracking and data analysis), and energy management for EV eets. Consultants will be available to help with upgrading from ICEs to EVs, including such services as telematics, route planning and EV charging.
Among the rst GM Envolve customers are Domino’s, which ordered 800 Chevy Bolt EVs last year, and AutoZone, which plans to order 60 Chevy Bolt EUVs this summer.
“GM Envolve will leverage the complete power of General Motors to o er the best solutions to customers and further reinforce why we’ve increased our eet sales for ve consecutive quarters,” said GM Executive VP Steve Carlisle. “We will bring our customers in to create tailored solutions to meet their unique business challenges.”
e Hyundai Motor Group plans to invest $18 billion in its domestic EV industry by 2030. e funding will be used to increase production and exports and to foster EV-related industries. e Group announced plans to expand its annual EV production in Korea to 1.51 million units and global volume to 3.64 million units by 2030.
To increase domestic EV production, Kia is building a plant to manufacture electric purpose-built vehicles (PBVs), while also expanding existing EV lines to increase production.
Also, the Group will develop a platform for next-generation EVs, expand product lineups, develop core parts and advanced technologies, and establish research facilities. e Group plans to sequentially develop dedicated platforms for each vehicle class under the Integrated Modular Architecture (IMA) system, including the eM platform designed for passenger EVs, which will be introduced in 2025.
In 2030, Hyundai Motor Group expects to have a total lineup of 31 EV models, including models from Hyundai Motor, Kia and Genesis. is year, Kia plans to launch EV9, its three-row electric agship SUV. Hyundai Motor plans to launch the IONIQ 7 in 2024.
e Lagos Metropolitan Area Transport Authority (LAMATA), which serves Africa’s largest city, plans to deploy 12,000 electric buses over the next seven years. e buses will be supplied by Chinese OEM Yutong, and will be assembled locally. Oando Clean Energy Limited (OCEL), a subsidiary of the Nigerian multinational oil company Oando, will provide charging infrastructure.
Yutong’s electric buses are equipped with air conditioning and WiFi. Two pilot vehicles have already been delivered, and OCEL has taken delivery of some charging stations and spare parts. Lagos State is expected to save some $2.6 billion in fuel and maintenance costs.
American bus maker Collins Bus, a subsidiary of REV Group, has introduced its Ford E-Transit Type
A school bus. e new e-bus is now available for orders from Collins Bus dealers.
e bus is built on Ford’s T-350 single-rear-wheel E-Transit cutaway. It is available in two options to accommodate either twelve seated passengers or eight seated and two wheelchair passengers.
e new model, which comes with a 68 kWh battery and an 8-year/100,000-mile warranty, has a narrow-body design, view-out window, one-piece tubular roof bow design, and body and paint warranties.
“Ford and Collins Bus have a long history working together to provide mobility solutions for school systems,” said Ford Pro General Manager Raj Sarkar.
GreenPower Motor Company has received an order for 41 purpose-built Type D BEAST and Type A Nano BEAST electric school buses totaling $15 million from the state of West Virginia. As part of the deal, GreenPower will begin manufacturing electric school buses in the state.
“Since we rst announced our intent to manufacture in West Virginia, we’ve made tremendous progress on our mission to be the leading manufacturer of purpose-built, all-electric school buses,” said Brendan Riley, President of GreenPower. “We look forward to continue providing a positive impact on West Virginia’s economy with clean energy jobs.”
GreenPower took possession of a manufacturing facility in South Charleston in 2022, and has been performing nal assembly and inspection on EV Star Cab & Chassis there as part of its supply agreement with Workhouse Group. Over the next few weeks, GreenPower will begin producing its Nano BEAST Type A electric school bus there, followed by the Type D BEAST.
e BEAST and Nano BEAST have been in pilot operation in several West Virginia counties for some weeks. “Over the course of the 2022-23 school year our BEAST and Nano BEAST have proven their capabilities in cold weather, snowy conditions and mountainous terrain in both rural and urban counties across the state. In short, the GreenPower school buses have performed exactly as we expected them to,” said GreenPower CEO and Chairman Fraser Atkinson.
GreenPower predicts that operation and maintenance costs for its electric school bus will be 70% to 80% less than those of a legacy diesel bus.
GreenPower will increase the number of employees at its West Virginia facility, and expects to reach a head count of 200 by the end of 2024. e company will conduct employee training programs in partnership with BridgeValley Community & Technical College.
“ e fact that our workers will be manufacturing the school buses being purchased by the state that their kids and grandkids will be riding to and from school on brings me great pride,” said Mr. Riley.
Image courtesy of GreenPowerUK-based refuse truck manufacturer Dennis Eagle has announced that Westminster City Council in Greater London, a er extensive trials in 2022, has ordered 40 of the company’s eCollect 27-tonne 6×2 rear-steer vehicles.
e vehicles will be operated by global waste-management company Veolia in partnership with Westminster City Council, which has set a goal of reaching net zero emissions by 2040.
Dennis Eagle launched the eCollect in 2020, and says there are now more than 100 in operation in the UK and Ireland.
Frito-Lay will deploy over 700 electric delivery vehicles in the US by the end of 2023.
e company has already introduced a new electric eet to serve the Dallas-Fort Worth area and recently made its rst third-party shipment as the rst company to contract transport on logistics rm Schneider’s electric truck eet.
“ e introduction of EVs throughout our owned eet and that of our partners is in direct support of our commitment to building a circular and inclusive value chain,” said Laura Maxwell, Senior VP of Supply Chain at PepsiCo Foods North America.
Blue Bird is delivering 60 Vision electric school buses to Broward County Public Schools (BCPS). is represents Blue Bird’s largest e-bus eet sale to date.
Blue Bird’s Vision electric school bus can carry 72 students, and has a range of up to 120 miles.
BCPS is the sixth largest public school system in the US, serving more than 254,000 students and 110,000 adult learners. e agency maintains a bus eet of more than 1,200 vehicles, including 515 Blue Bird buses.
BCPS received a nearly $15-million grant from Florida’s Diesel Emissions Mitigation Program, which is funded by the state’s Volkswagen Settlement and the EPA’s Diesel Emissions Reduction Act. Florida Power & Light is providing the vehicle charging infrastructure.
Blue Bird electric buses come standard with vehicle-to-grid (V2G) capability, which will enable BCPS to coordinate with local utilities to manage vehicle charging and return stored energy back to the grid as needed. V2G programs can lower the overall cost of electric buses for school districts.
“ is project has been in development for several years, and we’re thankful to the Florida Department of Environmental Protection and Florida Power & Light for providing the essential funding and infrastructure to make it possible,” said BCPS Superintendent Dr. Earlean Smiley.
e humble Ohio community of Lordstown has played a dynamic role in EV history. e rst act of the drama was a typical Rust Belt tragedy— shuttered auto plant, lost jobs. e second was a heart-warming resurrection story—plucky startup builds innovative electric pickup. Next came a tawdry tale of a missed opportunity to electrify postal delivery vans, and a told-you-so parable in which credulous investors lost their chips in a SPAC deal. What next?
e latest news from Lordstown is good, as far as it goes: Taiwanese contract manufacturer Foxconn has begun production of MK-V electric tractors for Monarch.
In 2022, struggling EV startup Lordstown Motors sold its manufacturing facility to Foxconn. As part of the deal, the Taiwanese experts are to help bring the automaker’s Endurance pickup into production. Foxconn has also made a deal with Fisker (another company with a highly colorful history) to assemble its planned EV model, the PEAR.
We’ve heard nothing recently about the Endurance or the PEAR, but the electric tractors are real. Monarch says an initial ve units have been assembled and are ready for customer deliveries. According to the companies, MK-V production is on schedule. Foxconn says it is “very pleased with the product quality,” and will now ne-tune its assembly lines and material sourcing as it prepares for full-scale production.
e MK-V can be operated with or without a driver, and is equipped with advanced safety technologies, including collision prevention and human detection, which enables it to stop moving or shut down if it detects a person nearby.
“As a leader in manufacturing some of the world’s most in uential electric and autonomous technologies, Foxconn is the ideal partner for us as we look to rapidly expand production of the MK-V,” said Monarch CEO and co-founder Praveen Penmesta. “Today’s farmers need solutions like the MK-V now that will increase farm pro tability and sustainability.”
JLR announced that its Halewood plant in the UK will become an all-electric production facility. e company will invest £15 billion ($18.9 billion) over the next ve years. Additionally, the company shared that its new platform for medium-size SUVs, Electri ed Modular Architecture, will now be fully electric.
Adrian Mardell, JLR’s CEO, said: “Today I am proud to announce we are accelerating our electri cation path. is investment enables us to be net-zero carbon emissions by 2039.”
JLR also announced that the rst of its three new Jaguar models will be a 4-door GT. e company said it will have a range up to 430 miles (700 km), and a starting price of £100,000. Additionally, it will feature its own architecture, which Jaguar has dubbed JEA. e model is expected to go on sale in selected markets in 2024.
Hydrogen infrastructure system specialist GenH2 has executed an MOU with ZeroAvia to develop liquid hydrogen aviation infrastructure solutions for use at airports.
ZeroAvia is developing a hydrogen-electric aviation powertrain. e company aims to retro t its fuel cell-powered engines to existing xed-wing and rotorcra airframes in order to reduce time to market, and is also partnering with clean-sheet designers. ZeroAvia hopes to earn certi cation of its ZA600, a 600 kW engine for 9-19 seat aircra , as early as 2025, and to certify its ZA2000 engine for up to 80 seat regional turboprops by 2027.
GenH2 o ers hydrogen liquefaction, storage and dispensing systems ranging from 20 kg/day up to 5,000 kg/ day that are capable of working airside as ground support refueling units.
“Today, aviation is the fastest-growing source of greenhouse gas emissions, and without radical change, its share of global climate impact is expected to be more than a quarter of all human activity by 2050,” said Arnab Chatterjee, ZeroAvia’s VP of Infrastructure. “GenH2’s liquefaction capability will further support our mission of demonstrating that hydrogen-electric propulsion is the only way to scale truly clean aviation for commercial use.”
e skies are slowly beginning to clear in the EU, where the most recent quarterly sales data for transit buses shows that diesel-only buses no longer make up a majority of the market.
As the International Council on Clean Transportation explains, city buses (not including coaches and interurban buses) make up about 60% of all heavy-duty passenger vehicle sales. ey tend to have high emissions, and their typical use cases make them prime candidates for electri cation.
e latest milestone was not reached due to a signi cant rise in sales of zero-emission buses—which have hovered around 30% for the last year, according to the ICCT—but rather from increased sales of hybrid buses, which overtook those of diesels this year.
e EU’s Clean Vehicles Directive requires member states to purchase between 24% and 45% “alternatively fueled” buses (i.e. anything other than diesel-only) from August 2021 to December 2025, and half of these need to have zero-emission powertrains. e targets will increase to 33-65% in 2026, so diesel’s days in Europe are clearly numbered.
Several individual countries have set their own targets: ICE bus sales are to be phased out in the Netherlands and Denmark by 2025, in Ireland by 2030, and in Austria by 2032. Major cities are also regulating stinkpots out of existence—the ICCT reports that over half of Europe’s capital cities plan to have only zero-emission buses on their roads by 2040.
e transition is taking place more slowly than many would wish. Hybrid vehicles are playing a strong role in Europe’s largest countries, and an unfortunate amount of investment is going to methane gas engines, especially in France, Spain and Italy. A recent lifecycle analysis carried out by the ICCT found that a natural gas city bus reduces greenhouse gas emissions by 17% compared to a diesel counterpart, whereas a battery-electric bus can deliver a reduction of up to 75%.
Good news: Hydrogen fuel cell buses made up only a tiny percentage of the buses bought in the quarter.
Bad news: Europe still lags far behind China, where zero-emission buses took 91% of the market in 2022.
Battery-electric sedans are a rare breed— that makes Hyundai’s striking Ioniq 6 a strong new entry
Quick, name all the battery-electric sedans for sale in the US—that aren’t Teslas. By our count, there’s only been one: the pricey, luxury Lucid Air.
Now, there’s another: the 2023 Hyundai Ioniq 6 is on sale at your local Hyundai dealer, joining the Ioniq 5 crossover utility and the smaller Kona Electric hatchback. e new Ioniq 6 is built on the same E-GMP underpinnings as its utility sibling, but wears an entirely di erent and strikingly sleeker body.
While the production vehicle isn’t as striking as the Electric Streamliner concept rst shown in January 2022, the arched window line and dropped tail of the Ioniq 6 still turn plenty of heads. Available in rear- or all-wheeldrive versions and three trim levels (SE, SEL and Limited), the new electric sedan starts at $43,000 but can hit $60,000 for a high-spec model.
Many models, one E-GMP
Hyundai’s E-GMP battery-electric platform wins kudos, and rightly so, for its rear-wheel-drive bias and 800-volt battery charging. Today, it’s used under not only the Ioniqs 5 and 6, but sister brand Kia’s EV6 and the luxury Genesis GV60—all e ectively hatchback utilities except for the Ioniq 6 sedan. And that’s just the start: the Kia EV9 three-row electric crossover will break cover later this year, followed by the Hyundai Ioniq 7, a three-row family SUV on the same platform.
Hyundai’s well aware that SUVs now handily outsell sedans in North America. e Ioniq 6 won’t be the brand’s top EV seller—that role falls to the Ioniq 5. Still, it’s a new entry in a category that’s essentially been dominated by one vehicle: the Tesla Model 3.
Hyundai’s compact electric four-door lines up pretty closely against the Model 3. e two cars aren’t dimensionally identical, but they’re the only two batteryelectric sedans on o er below $90,000 or so. It seemed a shame not to let people see them together, so on the March day we drove the Ioniq 6 at a media preview in Phoenix, we rented a Model 3 so we could photograph the pair side by side.
Overall, the Ioniq 6 represents a more comfortable, quieter and more conventional approach to a batteryelectric sedan than the Model 3. e Tesla is undeniably sportier, more BMW-like, and eager to accelerate and carve through corners; the Hyundai is comparatively more relaxed, so er and gentler. It’s hardly an old-
style American luxury car, wallowing on its springs, but many buyers may nd it better balanced and more soothing to drive than the lithe, speedy Tesla.
Which exterior design you prefer is a matter of taste, though midway through its seventh full model year, the Model 3 design has become as common as Toyota Corollas in some precincts. Hyundai’s sleek, arced sedan is fresh and clean, especially from the front, though it gets busy at the rear with a spoiler below the rear window and another at the base of the trunk. Both interrupt the drooping banana shape that makes the car so distinctive. Automotive history fans may see a
Ioniq 6 is a new entry in a battery-electric sedan category that’s essentially been dominated by one vehicle: the Tesla Model 3.
bit of In niti J30 or Mercedes-Benz CLS in its lines, though Hyundai claims the obscure Stout Scarab as a design in uence. But we digress.
Inside, the Ioniq 6’s controls and user interface are relatively intuitive, its graphics are clear and coherent, and it retains actual knobs and buttons for several functions that the Tesla driver controls through the central touchscreen. e Model 3 approach is fairly well known by now: a steering wheel with scroll buttons, stalks behind the wheel, and then just a landscape-oriented central touchscreen on which drivers control virtually every other function.
ere’s a fair amount of hard plastic inside the Ioniq 6, but the patterns and textures bring it up a notch. It took a while to get used to power-window switches on the center console, like a Jeep with removable doors. Hyundai said this was to widen the passenger com-
partment by eliminating switchgear from the inside door panel. (Tesla has window switches right where you expect them: in the armrest.)
For sedans in the same segment, the Ioniq 6 o ers roughly the same battery capacity as the Model 3—but less range, less combined power from its two motors, and less torque.
There’s a fair amount of hard plastic inside the Ioniq 6, but the patterns and textures bring it up a notch.Photos by John Voelcker
e Ioniq 6 price leader is the SE with a smaller 53 kWh Standard Range pack and rear-wheel drive only. It’s rated at 240 miles of range, but o ers a low sticker price of just $42,715, including a mandatory $1,115 delivery fee. Don’t expect to see a lot of these on dealer lots; the vast majority of buyers will go for one of several Long Range models.
A base Ioniq 6 SE with the 77 kWh Long Range battery and rear-wheel drive is EPA-rated at 361 miles on its 18-inch wheels;
add all-wheel drive, and the SE falls to 316 miles. e higher Limited trim adds many more features, along with larger 20-inch wheels, all of which cuts range to 305 miles for RWD, 270 miles with AWD. For comparison, the Tesla Model 3 Long Range we tested, with all-wheel drive and a 75 kWh battery, had a 353-mile rating against our Ioniq 6 Limited AWD range of 270 miles.
As for power, the front and rear motors in the Ioniq 6 are rated at 74 and 165 kilowatts (100 and 221 horsepower) and 446 lb- of torque. e Model 3’s two motors come in at 147 and 188 kW (197 and 252 hp). We couldn’t get an estimated 0-to-60-mph acceleration time for our AWD Ioniq 6, and didn’t have proper testing equipment in our single-day drive to measure it properly, though one car magazine tested it at 4.3 seconds. Tesla quotes a 0-to-60 mph acceleration time of 4.2 seconds for the Model 3 Long Range with dual motors, which felt about right—meaning both are quite fast away from the stoplight for small sedans.
e Hyundai corners at and remains composed, but it’s more isolated from road feel—likely a plus in many drivers’ eyes. It doesn’t particularly invite drivers to toss it through corners, even though it’s perfectly capable of doing just that. It’s a closer analog, perhaps, to the Hyundai Sonata mid-size sedan: a middle-of-the-road sedan entry with the many bene ts of a battery-electric powertrain.
e Tesla is more like a BMW 3 Series, a sport sedan that trades noise suppression and a bit of ride comfort for instantly available performance and roadholding that induces con dence and makes drivers want more. Its controls are considerably heavier than the Hyundai’s—it’s a
As for power, the front and rear motors in the Ioniq 6 are rated at 74 and 165 kilowatts (100 and 221 horsepower) and 446 lb-ft of torque.Photos by John Voelcker
car to be driven. Each approach is valid for its intended audience—neither car has anything to apologize for. ey’re just two interpretations of how a car should feel to its driver.
Behind the wheel, Hyundai requires drivers who want onepedal operation to pull back the le steering-wheel paddle to invoke the i-Pedal function—every single time the car is turned on. at’s annoying when other EVs, including the Chevrolet Bolt EV, retain the setting through multiple power cycles. Strong regenerative braking and one-pedal driving are the default on the Tesla.
e Ioniq 6’s front seats are comfortable and supportive for drivers of virtually any size, but that falling roo ine exacts a penalty on rear-seat headroom—just as it does on trunk space. Still, outside of taxi and Uber duty, most mid-size sedans we see on the road have precisely one person in them, so perhaps rear-seat accommodations simply aren’t that important.
Whither Hyundai, whither Tesla?
e Ioniq 6 is another proof point for the idea that Hyundai-Kia is one to watch in the EV battle. It looks entirely di erent than its Ioniq 5 sibling— you might not know the two are from the same maker. You’d certainly never know they had the same underpinnings—at least until you sat behind the wheel, and saw the family twin 12-inch digital displays side by side, and the identical infotainment graphics.
But the E-GMP platform, with its ability to fast-charge up to 235 kW (under optimal circumstances), and the speed at which models that use it are being rolled out, suggests that the company understands the design and important features of EVs better than some competitors.
Whether Hyundai understands the presently dire state of non-Tesla public fast charging is a di erent topic. e Ioniq 6 comes with three years of unlimited fast charging on the Electrify America network, which may perversely encourage buyers—even those who can charge at home—to overuse public DC fast charging stations. at’s not good for the car’s batteries, or for the drivers who genuinely need fast charging stations to complete their road trips. en there’s the unpredictable and unreliable nature of the half-dozen public fast charging networks, a topic Hyundai execs were notably uninterested in discussing. Tesla’s advantage on that front is unquestioned, and was recently underscored by deals in which Ford, GM and Rivian EVs will be able to use the Tesla Supercharger network. Hyundai has nothing comparable to o er at the moment.
Still, the Hyundai Ioniq 6 is to be welcomed as an electric car, not an SUV. It’s handsome, pleasant to drive, o ers versions with signi cant range, and provides a competitor of sorts to the all-butubiquitous Tesla Model 3. For that combination of attributes, Hyundai deserves a hand.
Note: A more detailed comparison of the Hyundai Ioniq 6 and Tesla Model 3 can be found in e Autopian: “I Rented a Tesla Model 3 To Test Against e New Hyundai Ioniq 6. Here’s How ey Compare.”
Hyundai provided airfare, lodging and meals to enable Charged to bring you this rst-person report.
The Ioniq 6 is another proof point for the idea that Hyundai-Kia is one to watch in the EV battle.Photos by John Voelcker
Korea-headquartered EV charger maker SK Signet has opened its rst US EV charger manufacturing facility in Plano, Texas.
e company projects the plant’s production capacity of its range of chargers, from standalones to power cabinets supporting multiple dispensers, at more than 10,000 units per year. e facility will also host R&D, manufacture EV charger power modules, conduct charger testing with automakers, and develop EV charging so ware and rmware.
SK Signet’s fastest V2 charger, which is slated to begin production at the Texas facility later this year, provides a maximum output of 400 kW.
“ e company’s new state-of-the-art facility will not only create new manufacturing jobs for Texans, but will advance critical EV infrastructure for our state and the nation,” said Texas Governor Greg Abbott, who recently signed a $200-per-year tax on EVs into law.
Electrify Commercial, the Electrify America business unit that provides EV charging solutions to businesses, plans to deploy 20 EV charging stations in Utah for local utility Rocky Mountain Power. e project will include more than 80 individual chargers at 15 stations in the Salt Lake City area and 5 stations in surrounding regions.
Electrify Commercial will provide charging equipment, installation, networking and ongoing operations and maintenance.
Each station will have a minimum of 4 chargers, with charging speeds up to 350 kW. Rocky Mountain Power will set pricing, and customers will be able to access charging through the Electrify America mobile app. e rst of the charging stations are expected to open in 2024 in Salt Lake City, the Wasatch Valley Front and Moab.
“Salt Lake City is the top city in the US to own an electric vehicle, making it more important than ever to provide accessible charging in the region and in other parts of Utah,” said James Campbell, Director of Innovation and Sustainability at Rocky Mountain Power. “Electrify Commercial will play an important role in helping us achieve our electri cation goals and enable seamless EV travel throughout the state of Utah.”
Israel-headquartered energy technology company SolarEdge recently debuted its bidirectional DC EV charger, which is expected to be available in the second half of 2024.
e charger is compatible with 400 V and 800 V powertrains, and will enable solar-powered vehicle-to-home and vehicle-to-grid functionalities. It will allow charging at up to 24 kW by simultaneously drawing from the PV array, the home battery and the grid.
SolarEdge says its ONE optimization system will apply algorithms to calculate dynamic utility prices and autonomously charge the battery. It will also discharge battery power back to the grid, enabling homeowners to receive compensation from electricity suppliers during demand response events.
e EV battery will be able to function as a home onor o -grid battery storage solution with up to 50 kWh of capacity for backup use during power outages.
Versinetic, a UK smart charging consultancy, has developed a so ware stack solution that allows EV charging manufacturers to produce ISO 15118-compliant charging infrastructure.
e ISO 15118 protocol de nes vehicle-charging station communication.
Versinetic licenses its new ISO 15118 so ware stack as part of its modular EV charging solutions. Versinetic’s MantaRay control board, which supports AC and DC chargers, runs the so ware. Versinetic’s Charging Blox are product and service modules that can be customized to build a comprehensive EV charging station solution. ese are o ered under three models:
• Design concept—consulting, feasibility studies, evaluation kit;
• Solution design—Versinetic hardware and so ware;
• Supply options—license, buy direct or construct under license (for huge numbers), or non-recurring engineering.
“Accommodating ISO 15118 in our products is another part of Versinetic’s roadmap to play an integral part in the electri cation of our roads,” said Dunstan Power, MD at Versinetic. “We strive to bring expertise and exibility with our modular EV charging products that reduce time to market for EV charging providers and enable them to ensure their EV chargers are future-proofed.”
e New York City DOT and New York Power Authority (NYPA) have agreed to create up to 13 fast charging hubs at municipal parking facilities across the city, and each will feature roughly 50 charging plugs.
Once installed, these chargers will bring the city closer to achieving the Adams Administration’s goal of all New Yorkers living within 2.5 miles of a fast charger by 2035. ey will also help to advance Mayor Eric Adams’s administration’s plan to transition more than 100,000 for-hire vehicles to zero emissions by 2030 and help to achieve New York State’s target that all new vehicles sold in the state be zero-emissions by 2035.
“Our administration has set ambitious goals to electrify all Uber and Ly trips and ensure every New Yorker lives within 2.5 miles of a fast charger,” Adams said.
“ ese new hubs are sited in areas where many for-hire drivers live and work, and they will boost fast charging availability right at the time the city’s for-hire EV eet is expanding,” added Taxi and Limousine Commissioner David Do.
Motor manufacturer Cummins, and fast charger maker Heliox are cooperating to sell and service EV chargers in North America. e companies will bring a mobile 50 kW DC charger and a stationary 180 kW DC charging system to market.
e Mobile 50 is designed to plug into 480 V AC wall sockets, and can be used anywhere there is a compatible power source. Its portable design does not require xed installation.
e Flex 180 solution provides up to three dispensers capable of static, sequential and dynamic charging for optimal exibility for eet customers. e companies will o er both plug and pantograph options for transit bus customers.
Both EV charger products are available through Cummins’s North American distribution network. Cummins Sales and Service North America will provide repairs and planned maintenance at its over 180 service locations.
“We have a history of building innovative partnerships that combine strengths to create incremental value for our customers. Our relationship with EV charging partners builds on this legacy,” said Zach Gillen, General Manager of Cummins Sales and Service North America. “Our collaboration with Heliox will deliver a reliable solution to support eet customers in reaching their sustainability and emissions goals.”
Volvo has invested in bidirectional EV charging startup dcbel. e automaker’s venture capital rm, Volvo Cars Tech Fund, will support dcbel’s R&D and commercialization e orts for its home energy system.
dcbel’s r16 Home Energy Station will be a “renewable energy ecosystem” that features bidirectional EV charging capabilities and a smart home energy management system. e system can be integrated with roo op photovoltaic panels, and supports charging two EVs simultaneously.
Energy from an EV’s battery can be used to power a home during an outage, to save on utility costs during peak hours, or (theoretically) to earn money from the local utility for providing grid services.
dcbel’s operating system, Orchestrate OS, “synchronizes with a home’s solar power generation and stationary battery storage, and calculates the best ways to use, store or sell home energy every ve minutes. Homeowners maintain complete visibility and control over their energy through their smartphone and other connected devices.”
“Home energy management systems will play a vital role as we move towards bidirectionality of electric vehicles,” said Alexander Petrofski, CEO of Volvo Cars Tech Fund. “Rising energy prices coupled with frequent blackouts are challenges faced by consumers today, and our investment in dcbel and their technology can help alleviate those challenges for our customers.”
Volvo has said that its upcoming EX90 will be the brand’s rst EV with bidirectional charging capability.
Scania has successfully installed and tested a pilot Megawatt Charging System from ABB E-mobility. Deploying this high-power charging solution could enable operators to halve the charging time for heavy-duty vehicles, says Scania.
Scania calls the testing, which was done to prove the technical viability of high-current charging, a rst important step towards a future system, which will result in the progressive deployment of high-power MCS chargers, starting with current levels of 1,500 amps and eventually delivering the full MCS scope of up to 3,000 amps.
Scania and ABB E-mobility have both been instrumental in developing MCS in collaboration with CharIN (the MCS standard is expected to be nalized in 2024).
Scania calls MCS technology “critical” for long-haul electric trucks, as both driving time and resting time for drivers are regulated by law. In some jurisdictions, a commercial vehicle can be driven for a maximum of 4.5 hours before the driver needs to take a 45-minute break. During this time, the truck needs to add enough energy to the battery to operate for another 4.5 hours. Due to the size of the batteries, fast, high-power charging is essential.
“We see momentum for electric transport, and our goal is that 50 percent of all vehicles we sell annually by 2030 are electric,” says Fredrik Allard, Head of E-mobility at Scania. “To achieve this goal will require infrastructure, and MCS is a crucial piece of the puzzle.”
Scania is now o ering trucks with the MCS pre-standard connector to customers with speci c needs, and production is set to begin in 2024. ABB E-mobility will introduce the next iteration of its MCS technology in late 2024 or early 2025.
France-based electrical equipment maker Legrand has expanded into the EV charging market with the launch of the Legrand Networked Level 2 Commercial Electrical Vehicle Charger, designed for such commercial applications as o ces, parking garages, multi-unit residential buildings and vehicle eets.
e 48 A (11.5 kW) Level 2 networked charger comes factory-con gured with customizable charging-management subscription so ware from American EV charging company AmpUp, providing real-time monitoring and remote diagnostics.
e integrated Legrand-AmpUp product is now available to US customers.
“Our partnership with AmpUp was an easy choice— we are excited to bring a di erentiated and comprehensive charging solution,” said Legrand President Ravi Ramanathan.
Multimodal transportation provider Schneider National has completed an electric charging depot at its South El Monte Intermodal Operations Center in Southern California. e depot will power the company’s battery-electric truck eet, which will include nearly 100 Freightliner eCascadias by year’s end.
e 4,900-square-foot charging site, which was designed and built in cooperation with Black & Veatch, features 16 350 kW dual-plug chargers, allowing the carrier to charge 32 trucks simultaneously. Schneider says its eCascadias will be able to charge up to 80% within 90 minutes.
Schneider’s facility is centrally located within the metro Los Angeles area, adjacent to major highways—numerous customers have facilities within a 50-mile radius. Schneider is already using its new eCascadia electric trucks, each of which has a range of approximately 220 miles, to make deliveries for Frito-Lay and Goodyear.
“Schneider decided to lead the way by building our own depot in South El Monte,” said Schneider CEO Mark Rourke. “It was important to develop onsite charging because it is the most e cient solution to power our growing electric eet. With the infrastructure de ciency, we found that we needed to collaborate with a wide array of experts to see our vision come to fruition.”
JETSI, an electric truck project jointly funded by the California Air Resources Board and the California Energy Commission, awarded the project $27 million. Additional funding was provided by the South Coast Air Quality Management District, the Port of Los Angeles and Southern California Edison. Building the depot “would not have been possible without our funding and grant agencies,” said Rourke.
Schneider worked alongside Daimler Truck North America (DTNA) as the eCascadia evolved, piloting a truck for six months in 2019-2020 through Freightliner’s Customer Experience eet. Feedback from Schneider drivers and the equipment team led to the production of today’s eCascadia.
InCharge Energy, a provider of turnkey eet electri cation services, has launched a new portfolio of bidirectional DC fast chargers. e new ICE-22 V2X, ICE-44 V2X and ICE-66 V2X chargers are aimed at eet operators, and are designed to optimize operations and increase cost e ciencies while supporting grid stability, and to enable eets to qualify for grant funds that include a vehicle-to-grid (V2G) compatibility requirement.
A er performing extensive interoperability testing at its Engineering and Ful llment Center, InCharge has veri ed that its solution enables eet managers to charge any bidirectional-capable EV at any ICE V2X charging station.
e suite of InCharge V2X chargers includes three options, with di erent power outputs:
• ICE-22 V2X is intended for eets needing sequential charging, such as those with long dwell times without time-of-use tari s, and is useful for discharging multiple vehicles back-to-back.
• ICE-44 V2X is best for eets that need to maximize charging with simultaneous and sequential charging or discharging of two vehicles at a time.
• ICE-66 V2X is aimed at eets that have high daily utilization and may need to charge up quickly or feed energy back to a building or facility to shave utility costs.
e bidirectional functionality of the InCharge V2X chargers is controlled by the V2X add-on of InControl, the charging management system from InCharge Energy. Using an OpenAPI architecture developed speci cally for large eets, the proprietary InControl platform allows eet managers to operate, monitor and maintain their EV charging infrastructure, and to integrate it into their existing so ware systems.
EV charger manufacturer
Wattzilla has introduced a new family of UL-listed SAE J3068 3-phase Level 2 EV chargers. e new chargers are available in single, dual and quad con gurations, each capable of simultaneously delivering 44 kW of 400 VAC 3-phase power (63 A per phase) on each output cord.
Not all EV chargers on the market are UL-listed, but this certi cation is an important indicator that a product meets the highest safety standards.
e Wattzilla Uno-3P, Duo-3P and Quadzilla-3P are designed for high-power charging of trucks, buses and other medium- and heavy-duty EVs.
All three models are suitable for interior or exterior use. Each features a type 4X 316 stainless steel enclosure for protection from the elements, a gold-plated proprietary circuit board for high corrosion resistance, a multi-color LCD display, and the requisite number of 25-foot cables with J3068 Mennekes couplers.
All are rated for temperatures from -35° C to 50° C, and come with a 39-month standard warranty. An extended warranty is also available.
e Quadzilla Four Vehicle 3-Phase provides up to 63 amps per phase (approximately 44 kW) to four vehicles simultaneously. It can be wall- or pole-mounted, and comes standard with a pole mounting kit and a cable management system that holds all four couplers securely when not in use. It requires four 80-amp, 3-phase protected branch circuits, and is priced at $39,995.
e WattZilla DUO Dual 3-Phase delivers up to 63 amps per phase (44 kW) to two vehicles at a time. It’s available in wall-mounted or exterior pole-mounted styles, and has an optional cable management system. It requires two 80-amp, 3-phase protected branch circuits. Pricing starts at $19,995.
e WattZilla UNO 3-Phase cranks out 63 A per phase to a single vehicle. It’s available in wall-mounted or exterior pole-mounted styles, and has an optional cable management system. It requires a single 80-amp, 3-phase protected branch circuit. Prices start at $9,995.
Medium- and heavy-duty vehicles make up a small fraction of the vehicles on the road, but they generate a disproportionate amount of pollution. erefore, electrifying them is critical to reducing emissions. Furthermore, the case for electric trucks and buses would seem to be an easy one to make. Unlike individual car owners, eet operators know exactly how many miles their vehicles travel, and they aren’t likely to be swayed by questions of styling or coolness factors—if you can demonstrate that an EV will save them money, then you should be able to make a sale.
In the real world, things haven’t been that simple. Here at Charged, we’ve been covering the commercial EV market for a decade. For some (not all) use cases, the economic advantages of going electric have been clear for a long time, and yet we’ve seen a dozen EV manufacturers
go bust while trying to address the commercial market, while eet operators continue to buy diesel vehicles, which continue to belch out clouds of oily black smoke.
A er many discussions with players in the commercial EV eld, we realized that the problem was proving the performance of EVs. Saving money is important, but reliability is mission-critical, and eet operators were unwilling to get serious about going electric until they had tested EVs in years-long pilot projects.
Well, that phase of the transition is over. Commercial EVs have been on the job for years now, at dozens of companies, in just about every conceivable use case, and they’ve
proven that they can do the job better, quieter, more safely and above all, cheaper. Upfront costs are steadily approaching parity with legacy vehicles, purchase incentives are available, and new programs at the levels of federal (IRA, BIL), state (California’s ACT and ACF) and local (city zero-emission zones) government are driving (some would say “coercing”) companies to move forward quickly. However, the electric road ahead is not exactly clear. ere are several roadblocks on the way to an electried trucking system, some of them obvious and some far less so.
Rustam Kocher has been a pioneer in the commercial EV eld. When Charged rst spoke with him in 2021, he was the Charging Infrastructure Lead at Daimler Trucks North America, and also the Chair of CharIN’s Megawatt Charging System (MCS) task force. He later served as Transportation Electri cation Manager at Portland
General Electric, so he’s worked both sides of the electric fence. Now nominally retired and living in Portugal, he remains active in the infrastructure space as a consultant, and closely follows the development of the EV charging ecosystem. If you want to stay up on developments in the commercial EV space, you could do worse than to follow Rustam’s LinkedIn feed.
Q Charged: You recently wrote, “Commercial vehicle battery packs are tough to source.” Lots of eets will be placing orders for heavy-duty EVs over the next few years. Is the supply of battery packs going to be a bottleneck?
A Rustam Kocher: I think it’s going to be an issue for any company that has a large battery pack. Tesla, for instance: if you look at their battery pack in the Semi, it’s roughly 800 kWh, and you’ve got 74 kWh on a Model 3, which means you could make roughly ten Model 3 battery packs with the same number of cells as you’d need for one
Semi. So, Tesla can make more margin selling ten Model 3s than they can on one Semi.
Every company is going to be faced with that issue, whether or not they make light-duty and medium- and heavy-duty EVs, because the battery manufacturers are also going to look at quantity and volume, and if they can sell at a higher volume to light-duty and consumer vehicles, then they’ll be less interested in providing packs for larger EVs.
It’s easier to sell to the light-duty market. It’s less time and e ort. If you’re CATL, you can sell in mass quantities to GM and Ford. Supplying to Volvo Trucks or Daimler Trucks or whoever is more burdensome.
Also, the demands for medium- and heavy-duty battery packs are much more complex. In a commercial vehicle, you have a lot more forces in play, such as G-forces on a truck, that you have to test for. For commercial vehicles, the cells have to be able to perform at a di erent level.
For example, the kingpin that the truck smacks onto when the driver backs up to pick up a trailer, the G-force in that transaction is signi cant. But that’s also where the
You could make roughly ten Model 3 battery packs with the same number of cells as you’d need for one Semi.
battery pack sits, so that battery pack has to be mounted in such a way that when that truck backs up and hits the kingpin and grabs the trailer, it doesn’t jar it and cause shorting issues or whatever else over the long-term life of the battery.
Everything on a commercial vehicle has to be more rugged. Most commercial trucks are engineered for 1.2 million miles, so the engineering that goes into making those vehicles be able to perform and last that long has to apply to the battery pack as well. So, it’s a technical challenge and it’s a lot of cells.
When we were rst starting o at Daimler Truck, trying
to nd a battery cell supplier that would build us a pack that was good in the truck was di cult. Your supplier pool is restricted to who can make what you want and who wants to make what you want, so you have to deal with a smaller number of suppliers. e more suppliers you have, the more competition you have, which means the pricing and performance from those suppliers are going to be better. If you’ve got a limited supplier pool, they’re going to be less inclined to give you a good price for good performance.
Q Charged: You’ve also said that heavy-duty charging is going to be a huge hurdle.
A Rustam Kocher: It is. I was a big part of building the rst-of-its-kind—at least in the Western world that we knew of—heavy-duty charging site in Portland, Oregon. It’s called Electric Island.
You’re not going to be able to pull a Class 8 truck up to a consumer charging station and charge it towing the trailer. It won’t work. We’re going to need purpose-built sites, and we [decided to] build one so we could show people what it would look like.
Electric Island did what we hoped it would do, which was to kick o a movement towards knowing what was possible and what needed to be done. If you don’t build something like that, people can’t refer to it. What Tesla did with their Supercharger network was really di cult because no one else had ever done anything like that. ey thought through all those problems: Where should the charge port be? How long should the cable be? How should the vehicle interact with the charger? All those things. And they came up with a pretty bulletproof solution.
What we wanted to do with Electric Island was play with all those things. In fact, the code name for it internally was “the sandbox,” because we wanted to be able to build up a sandcastle and learn from that process and knock it down and build another one. e site was built with maximum exibility so that we could change things, swap out chargers, move things around and learn from the process of installing battery electric storage or putting solar on the site or what a megawatt charging unit would do under full power in partnership with the utility. What happens when we plug in 1.2-megawatt chargers? Will the lights all dim?
Portland General Electric was also involved with the West Coast Clean Transit Corridor (WCCC), which is a movement towards getting truck and bus charging stations like Electric Island built from Vancouver down to San Diego so
Everything on a commercial vehicle has to be more rugged. Most commercial trucks are engineered for 1.2 million miles.
that you could move goods and freight all up and down the West coast, at 50-mile intervals. [ is project is currently at the stage of conducting grid readiness assessments.]
What we did, again, was try and show what’s possible, and what needed to be done in order to enable goods movement and usage of battery-electric trucks. So we set out to show the industry what needed to be done so that the Flying Js, the Chevrons, the BPs of the world would understand that this needs to be built and that they had some support in doing so.
e utilities did all the desk reviews, they evaluated each of the sites generally and said, “Okay, it’s going to be this much on upgrades and this much time. We built it out in historical growth segments so that people would know if they’re going to build a site there, how long it would take and what it would take to get a site to 3.2 or 12 MW.
Q Charged: A couple of companies are building big commercial charging hubs—WattEV (I know you serve on their advisory board) and Terawatt. What’s di erent about their business model?
A Rustam Kocher: ere’s also a couple more out there building charging hubs for trucks. ere’s the partnership between Daimler and BlackRock, called Greenlane, and Forum Mobility, which is building a charging network for drayage trucks.
WattEV saw the need and they moved prior to the market growth. Power to them for seeing it, understanding it, and being willing to be a rst mover. Terawatt as well. I’m excited for both of them to be successful—we need more. We need a dozen companies that are willing to do this. We need Love’s, we need Flying J, we need Pilot, we need all of the current eet fuel and service providers to move to providing electricity for medium and heavy trucks and buses. If we’re going to hit the numbers we need to hit for eet adoption, we need as many places for those vehicles to recharge as possible.
WattEV’s rst site is in Bakers eld. ey’re building a massive site with onsite generation, solar+storage, which is important within the Megawatt Charging System. Megawatt charging is going to have really high demand charges [fees that utilities charge if peak demand exceeds a certain level] unless you have some way to mitigate those peaks. And having stationary storage on site will be important for that. ey’ve also got a site at the Port of Long Beach and a couple others in the LA area. ose will be public-facing
truck-charging sites similar to Electric Island. But then they did something interesting. ey said, “We’re going to build new sites and there’s simply not enough trucks on the road today for us to get the volume we need for the site to be pro table.” And they recognize that there’s a lot of small eets that serve drayage in and of the ports of Long Beach and LA that are served by owner-operator eets that only have a few trucks. ose guys don’t have the wherewithal to nance a battery-electric truck that costs twice as much as a diesel truck, and they’re usually buying third- or fourth-owner diesels anyway, that are super-cheap. So WattEV is going to o er truck-as-aservice. ey will own, maintain and insure the trucks, and then the owner-operators can rent them on a daily, weekly or monthly basis. WattEV will also provide the charging for those trucks, so it’s a way to allow some of these smaller eets that serve freight in and out the ports to be able to comply with the California regulations so they can stay in business and keep operating cleanly. And it generates ow through the WattEV site so that they get a consistent number of trucks coming through. Because the atter your demand curve is, the lower your power costs are from the utility. If you have a really peaky and spiky demand, your power costs can be really high because utilities don’t like
that, and they charge accordingly. ey want a nice solid demand line, so if you can keep a site active as much as possible, then you’ll have lower overall power costs.
Q Charged: Tell us more about issues with the utilities and how that can be a bottleneck.
A Rustam Kocher: Public utilities are there to serve the public—whether they’re investor-owned, co-ops, cityowned, whatever, they’re there to serve the ratepayer. When your home was built or when the business next to you was built, they went to the utility and said, “I need a hookup to the grid.” ey didn’t have to pay extra for that
We need a dozen companies that are willing to do this. We need Love’s, we need Flying J, we need Pilot, we need all of them.
hookup if it wasn’t exceptional—if it wasn’t very far to where they needed to get hooked up, that cost was essentially free.
It was free to the builder, but it wasn’t free to the utility. What they do is they rate-base that work. In order to get half a megawatt to the supermarket down the street, they had to trench, they had to make the connection, they had to make sure they had enough generation, they had to serve that site. at cost is spread among all ratepayers for that utility. at’s an accepted practice for utilities because that’s what a utility has done over the last hundred years.
What hasn’t normally been done is transportation electri cation work—what’s on the utility side of the EV. So if I’m Tesla or Electrify America, or a truck eet that wants to have an electri ed depot, and I go to Southern California Edison, and I say, “I need an interconnection to grid for this transportation electri cation site,” there’s no stipulation that says that that work should be o set by the ratepayer, so that cost is typically born by whoever’s building the site, which gets expensive. If Tesla needs to come in and build a charging site, they’ve got to pay for the grid connection.
California has passed Assembly Bill 841, [signed into law in 2020] which says that transportation electri cation must be treated just the same as building construction. So now that utility-side work can be done in a rate-based manner, which means that the individual site builder doesn’t have to pay for that work out of their own pocket, which is what needs to happen everywhere.
e way that you can spread that cost to the ratepayer for transportation electri cation sites is important, and it needs to be done with every publicly-owned utility across the nation. e problem is those laws are all state-based and every state has to make that change at the level of the utility commission.
Q Charged: It’s not just the cost—time can also be a big factor. As someone pointed out to me, if you’re building a factory and it takes two years to get your utility connection, that’s okay, because the factory’s going to take two years to build anyway, but a charging site can be built much more quickly.
A Rustam Kocher: I told this story over and over to the utilities every chance I got. It’s like gravity has changed for the utility industry. From the time of the rst utilities until today, everything took a certain amount of time. If they needed to make an interconnection because a building
was going to be built, they had 18 to 24 months, because you don’t build a building faster than that. Gravity always worked in a certain way—you always had this much time to do whatever needed to be done. Today, Sysco could order trucks from Tesla or Daimler and get electric trucks in a month or two, and they can be connecting temporary charging solutions to their warehouse when the trucks arrive. Utilities don’t respond to grid upgrades and interconnection upgrades in two months. ey just don’t operate that quickly. ey never have, they’ve never needed to. Well, suddenly gravity is heavier. A lot heavier.
Q Charged: I’ve been seeing articles from trucking industry groups that say things like, “Don’t get us wrong, we love EVs, but it needs to be a nice smooth, gradual transition,” by which they mean that there needs to be minimal government regulation. An o cial from the American Trucking Associations (ATA) recently made a speech in front of the US Congress, which contained a number of incorrect statements about EVs. Are we going to see a lot of resistance to electri cation from the trucking industry?
A Rustam Kocher: Yes. Any change is hard. And this industry is very, very old-school, very, very conservative. You’ll see pushback from them until TCO becomes positive operating the vehicles. Once your total cost of ownership is lower with a zero-emission vehicle, then that’s a spreadsheet decision. en I can plug that into a business plan and say, “I can o er lower freight rates than Joe down the road, who’s operating diesel trucks, because his cost per mile is more expensive.” Once that happens, then your adoption curve skyrockets. It turns into a hockey stick, which we’re already seeing with passenger cars. And the commercial vehicle hockey stick will be more
The trucking industry is very, very old-school, very, very conservative. You’ll see pushback from them until TCO becomes positive operating the vehicles.
pronounced, because it is a spreadsheet decision. Nobody buys a commercial truck because it looks good. ey buy to make money.
Q Charged: When do you see the TCO clearly becoming better?
A Rustam Kocher: My guess for commercial trucks is the early 2030s, but there’s going to be some binary decisions that eets are going to have to make before then. For instance, in states that have adopted the Advanced Clean Trucks regulation [15 US states at last count], you have to hit certain emissions benchmarks. You’re either operating by hitting those benchmarks with ZEVs or you’re not, so your choice is operate or not operate. And yes, you may have slightly higher costs because you’re forced to operate ZEV trucks as per regulation. And then in Europe, some of the major city centers have created zero-emission zones, so if you want to deliver to Starbucks within Paris, you’d better have an electric truck.
Q Charged: Early 2030s? Is it really going to take that long?
A Rustam Kocher: It depends on a couple of things. I’m watching battery prices, I’m watching component prices, I’m watching the tick-tock of new models coming to market, from gen one to gen two, to gen three to gen four. I call that a “tick-tock,” like what Intel does with the speed of their chips. So, how quickly the OEMs go through their iterations and learn and equip new products, new battery packs, new chemistries, those sorts of things.
You’re already seeing di erent (LFP) batteries on the Tesla Semi, which is interesting. So now they think maybe they don’t need a 500-mile range, maybe they can get by with 300. Well, that helps the OEMs out there that can just barely reach 300. ere’s a lot of use cases for 300mile trucks out there, so let’s do that with LFP batteries.
Iron phosphate batteries are great because they’re durable, they’re cheap. ey’re a little heavy and they’re not quite as energy-dense as some of the other chemistries, but they’re a good t for commercial use because of their durability.
As the industry is able to go through these iterations and get some serious production trucks out there, learning from failure and iterating will make the products better. All these OEMs have had a really slow iteration cycle in the past. Typically, from model to model, it was about eight years, which is just fantastically slow in today’s BEV world. Now they’re down to roughly two, and I think they’re probably going to have to get down to about a year.
It’s going to be a big li for the industry. ey won’t like it because they want to validate everything. ey never want to put something out on the road that hasn’t been fully validated, but in some cases, they’re going to have to do virtual simulation instead of on-road validation.
Q Charged: ere’s another bottleneck. Fleets don’t want to go electric at scale until they’ve done pilots for two or three years. Do you think that timeframe is going to get condensed?
A Rustam Kocher: It will be arti cially constricted by the ACT. ey won’t have any choice. And so they’ll choose OEMs that they trust and move forward. Whether that’s Volvo, Freightliner, PACCAR or Navistar, they have relationships with those OEMs and so they’re going to trust them to build a vehicle that will perform under the conditions that they need it to perform. Tesla’s going to have trouble breaking into the market. Nikola I wouldn’t expect to be around much longer, but other companies like Motiv and Proterra hopefully will have carved out enough of a niche to stand on their own two feet.
Q Charged: ese articles about “sensible regulations” and “smooth transitions” tend to say a lot about hydrogen, CNG and e-fuels. Is there a real danger that the industry will go down one of those dead-end roads?
A Rustam Kocher: ere is. I am quite worried about hydrogen sucking some of the oxygen and funds out of the room. To me, hydrogen is a way that the oil and gas industry can stay relevant. What are they good at? ey’re good at pumping things out of the ground, storing it, re ning it, piping it or trucking it to a place, compressing it or putting into the tank and then dispens-
MCS should put a bullet in hydrogen because the only thing that they have going for them is speed of refueling.
ing it. Hydrogen ts all those things really well. But it doesn’t work. It’s not e cient. It’s extremely expensive. It’s technologically almost impossible to do it safely. Big Oil’s got a lot of resources and money to push this narrative and you see it all day, all the time. When we look at the federal funding for charging and whatnot, they always have hydrogen in there at a similar amount of money as BEV. ere’s no need for it. ere are almost no hydrogen vehicles out there because they cost so much more per mile to run.
at’s why I love the global e ort to standardize the Megawatt Charging System, and hopefully Tesla will come on board with the rest of the industry. MCS should put a bullet in hydrogen because the only thing that they have going for them is speed of refueling. With MCS it’s the same speed. In fact, it might be faster, so hydrogen can go pound salt.
Batteries are only going one way. Gravimetric density is improving, volumetric density is improving, charging speed is improving, and all those curves are heading the right way. None of them are slowing down, so we know that batteries are on an improvement curve that will continue. Solid-state batteries can charge almost instantly. StoreDot has those organic-chemistry batteries, which can charge super-quick. So if you can get your Megawatt Charging System and a big StoreDot battery, we can charge it in maybe 12 minutes, 15 minutes.
new technology, whether it’s hydrogen or batteries?” And he literally laughed and said, “Diesel is the drivetrain for the foreseeable future, period, end of statement.”
And I made it my focus for the rest of my time to agitate for electri cation because I felt that they were missing the boat. I started a newsletter internally about electri cation in the industry, and I sent it to the CEO and the board. And then I got the opportunity to join the e-mobility group and the rest is history.
Q Charged: So you were one of the pro-EV partisans, agitators...
A Rustam Kocher: ...lobbing Molotov cocktails over the wall.
Q Charged: Which of the big OEMs are the ones to bet on to lead in the electric brave new world?
Q Charged: It has long seemed to me that within every automaker there are pro-EV and anti-EV factions eternally contending for the mastery. Is that the case with the commercial vehicle makers too?
A Rustam Kocher: Even more so. When I started at Daimler Trucks, a member of the board came by to visit Portland from Germany. As the new hire, I got to ask them a question—this was 2012. I said, “What is the plan for the decline of the diesel engine and the switch over to
A Rustam Kocher: I’ve really been impressed with Volvo Trucks. What they’ve done in electri cation, both in the European market and the US market, has been tremendous. ere’s still internal factions there, but they seem to be moving very quickly in the right direction. e eCascadia by Freightliner [a US subsidiary of Daimler] is a fantastic product, I’m excited to see more of those get produced out of the factory in Portland and get on the road. e Traton Group [a subsidiary of Volkswagen], is doing great work primarily in Europe, as is Daimler Truck Germany. ey’re more regulation-forced because they’ve got some pretty strict deadlines that are coming up for truck electri cation within the European Union. ey’re really under the gun, so most of the major truck manufacturers are pushing hard to meet those regulations, because otherwise the nes are really, really expensive—in the billions of dollars. Tesla, obviously, they’ve got a great product. We talk about gen two, gen three with the OEMs right now and maybe PACCAR and Navistar are on gen one, gen two. Tesla is on gen ve because they built that truck from the ground up to be electric, which none of the major OEMs have yet. ey’ll get there, but honestly Tesla is that many more jumps ahead. Whether or not they can keep their truck intact, maintain it and build the trust within the industry is a good question—we’ll see. I hope they can. I’ve never worked with smarter people. I’ve never worked with a more agile company than when I was working with Tesla on the Megawatt Charging System
Tesla is on gen fi ve because they built that truck from the ground up to be electric, which none of the major OEMs have yet.By Charles Morris
The term “game-changing” gets thrown around a lot in the EV eld, but if there’s any new technology that really does deserve to be described this way (as California Governor Gavin Newsom recently did), it’s bidirectional charging.
Going bi adds several ni y new bene ts to driving electric. It turns an EV into a mobile battery that can be used to provide backup power to a home or business, and to provide services to the electrical grid, generating revenue for the vehicle owner and potentially o setting a signi cant part of the purchase price of the vehicle.
What’s more, bidirectional charging is no hypothetical future technology—it’s here now, and it’s being used around the world in pilot projects and a few commercial-scale programs. A handful of bidirectional-capable EVs are available today, and automakers are quickly implementing the technology.
In just a few years, every new EV, on both the consumer and commercial sides, is likely to be bi.
Charged spoke with Nuvve CEO Gregory Poilasne about the various V2G projects that his company is working on around the world, and his recent testimony before the California legislature, which is considering a bill that would require all EVs sold in the state to be bi-capable by 2027.
Q Charged: We’ve been covering your company for several years. As Nuvve is one of the pioneers of bidirectional charging, I imagine you can explain the bene ts as well as anyone. What did you tell the folks in Sacramento?
A Gregory Poilasne: In April, I went in front of the Energy Committee and the Transportation Committee of the California Senate. is bill authored by Senator Nancy Skinner is called SB 233, and it would require electric vehicles to have bidirectional capabilities by 2027. Initially, the bill also required the infrastructure—the charging stations—to be bidirectional, but then they decided to split the two. e idea is that having vehicles with bidirectional capabilities creates an environment where innovators like Nuvve can develop business models. Bidirectional EVs would be enough to accelerate adoption of bidirectional services. is would naturally drive more bidirectional charging stations like ours, and all the required hardware to support vehicle-to-grid services and more.
e bill doesn’t say how the bidirectional capability needs to be integrated. You could do V2G through the DC port of the vehicle—this is what we are doing with school buses here in California, where our charging station converts AC to DC and then connects to the DC port of the vehicle to provide power. en it takes the DC from the bus or car, and converts it back to AC to provide power for the grid. at’s one way. is implementation is actually pretty simple. It’s purely a so ware upgrade, and standardization is already in place. e ISO 15118-20 standard enables bidirectional communication between the charging station and the vehicle, and with OCPP 2.0.1, permission is granted to go through the DC port. It's also possible to do V2G through an AC port. In that case, you need to have an onboard bidirectional charger. at means the charger inside the vehicle can convert AC to DC to power the battery and take DC from the battery and convert it back to AC for export to the grid. Your charging station is a lot simpler in this
case—it’s basically just replacing diodes with transistors to make it bidirectional from an AC perspective.
V2G through an AC port solution requires a little bit more work on the vehicle side, whereas V2G through the DC port really requires no work on the vehicle if you have ISO 15118-20 implemented.
Q Charged: Does the bill refer to both of those options or does it leave it open?
A Gregory Poilasne: e bill is agnostic. e bill is just saying the vehicles have to have bidirectional capabilities. My point to the Senate committee was that DC implemen-
The idea is that having vehicles with bidirectional capabilities creates an environment where innovators like Nuvve can develop business models.
tation inside the vehicle is pretty much no cost, it’s just having the right so ware, because people are, like, “Oh, it’s going to make the vehicle more expensive.” Also, it doesn’t a ect the rules that the OEMs might be building around the battery warranty. We’ve been working with Nissan for many years now, and the only rules that we have with Nissan are that we cannot do V2G when the charge level is above 95% or below 30%. Between 30 and 95% we can do V2G without any e ect on the battery warranty.
e case that I made for the Senate is that bidirectional capabilities, with the right V2G business model, can reduce the total cost of ownership of an EV, and therefore make EVs more a ordable. It’s not just for the high end—even the Nissan LEAF has bidirectional capabilities today. In a pilot project in Denmark that has been running for over 7 years, we’re generating about $220 per month from grid services. at’s about two thirds of the leasing cost of a LEAF nowadays.
e other piece is understanding why bidirectional vehicles and vehicle-to-grid are essential to our clean energy future in California. More and more renewable energy is
being added to the grid, but the distribution system has to be designed for the peaks. When you mix EVs and renewable generation, the peaks are going to get even bigger. So, you need to reinforce the distribution system for peaks that might be occurring less than 5% of the time, and therefore the cost of energy is going to go up for everybody, even people that cannot a ord an EV, because the EV increases the volatility of the system.
e idea of vehicle-to-grid is that you are storing energy at the end of the distribution system, so you can absorb those peaks. You can bring the peak as close as possible to the average. Now you’re making a fully-optimized use of the infrastructure and therefore the cost of energy actually might go down for everybody.
I think those are the two most important messages: total cost of ownership and energy cost equity. To me, those are the two critical pieces of why vehicle-to-grid is essential. We are thinking that by 2030 we’re going to have eight million EVs in California. Eight million EVs on 10-kilowatt charging station, that’s 80 gigawatts, that’s 80 nuclear reactors. It’s gigantic.
Q Charged: And it’s particularly important in California. Some months ago, they had rolling blackouts and they were asking EV owners to avoid charging at peak times. Of course, the anti-EV crowd picked up on that. How could V2G address that problem?
A Gregory Poilasne: We actually participated during the heat wave. We saw the largest peak that the California grid ever reached 52 gigawatts. One of the programs we participated in is called the Emergency Load Reduction
Program, which is a demand response program in which you can also discharge to the grid. A regular demand response program, you go down to zero and then that’s it. With the ELRP, we get paid $2 per kilowatt-hour, and we can feed back to the grid. at means we can bring the meter negative.
Last year, we only had about six buses that were connected at Cajon Valley Union School District, so we had a few tens of kilowatts of capacity that we were able to dispatch. is year, we now have close to one megawatt of capacity across three di erent school districts. I think we have 22 or 24 buses in the San Diego area, and we have another deployment underway in the Los Angeles Uni ed School District, where we are initially deploying 24 as well. We are in the process of commissioning those charging stations right now.
Discharging during those peak hours when you have a heat wave, that’s really essential to balance the grid so that when you have this heavy usage we are able to compensate without using spinning reserve. When we had that peak last year, we brought down the load to 52 gigawatts, but everything was turned on—methane gas generators, gasoline generators, everything. From a CO2 footprint perspective, that was really bad.
Q Charged: Does SB 233 address commercial vehicles?
A Gregory Poilasne: It’s all EVs. I know that there are some areas in the heavy-duty piece where they want CARB [the California Air Resources Board] to be involved with it. But buses, school buses, all those things will de nitely be a part of it.
Q Charged: Does the bill include any mandates for utilities?
A Gregory Poilasne: You can take this very complex issue and try to solve all the problems at the same time, or you can do it step by step. Senator Skinner has decided to go step by step. e rst step is bidirectional vehicles. en, with that, you can provide a business model where if you own a home, you can discharge your battery when the cost of energy is the highest, and you can also use the vehicle to power your house if the grid is down. at would drive the business around bidirectional charging stations.
en the second step is to work with the utilities to be able to do grid services, which we are already doing today.
e Emergency Load Reduction Program is part of that. And then you have another ruling called FERC 2222. FERC [the Federal Energy Regulatory Commission] is the federal organization that regulates the independent system operators. FERC 2222 is saying that any behindthe-meter storage solution needs to be able to access the spot market, including ancillary services like frequency regulation, which are essential services to keep the grid balanced. is is opening the door to resources such as V2G participating in the spot market. is regulation is in process because there is some complexity in how it gets implemented. Some of it relates to the energy going in and out at the consumer meter level and, therefore, the PSCs [state utility regulators] have to be involved with that, because the other thing that FERC says is that this market access needs to be fair. at means if you buy retail and you sell wholesale at your meter, it hurts your business case. You need to
If you convert all of LA Unified school bus fleet to electric school buses, it’s 108 megawatts. That’s significant.
come up with a net metering business model. e utilities are like, “But you are still using my infrastructure so I need to be compensated for that.”
ose are some of the negotiations that are underway right now between di erent parties involved with the rollout of FERC 2222. But in places like Delaware or in PJM territory, which covers a very large percentage of the US population, this is getting implemented right now.
Q Charged: Do you think SB 233 has a good chance of being signed into law?
A Gregory Poilasne: It’s a great question. Obviously, the OEMs don’t like when there’s a mandate, so that’s why some are pushing back, but even the people that are pushing back are saying, “Yeah, we need to get there but we are not ready to do it right now.” We expect that there will be some special requests for case-by-case accommodations to implement it. [Editor’s Note: As of this writing, the bill has passed the Appropriation Committee, and been referred to the Transportation and Utilities committees. Mr. Poilasne now tells us that it looks “very close” to becoming law.]
Q Charged: You provide Nuvve-branded chargers. Do you make those chargers yourself, or are you collaborating with other manufacturers?
A Gregory Poilasne: We have an AC charging station that we rolled out that came from our relationship with the University of Delaware. It’s bidirectional, but only with vehicles that have an onboard bidirectional charger. at’s our product. On the light-duty side we are working with ABB and Wallbox. ose are two of the charging stations we have deployed mostly in Europe at this point. We’ve got some others that we have not announced yet. On the DC side, we are rolling out a charging station right now with Rhombus.
Q Charged: Does Nuvve provide just V2G implementation, or do you also o er a comprehensive eet charging-as-a-service solution?
A Gregory Poilasne: At the core, we are a technology company and a grid service company using EVs to provide those grid services. Now, there are certain segments where we provide a full CPO type of service, which is what we are doing in the school bus space. Where we are working with school districts, we are providing them with charging stations and maintenance. We are here to bring the right people to provide installation, and in some cases, we are also the intermediary to help them nance those vehicles at an attractive cost. ose districts are tax-exempt organizations, therefore they have access to attractive loans. We see ourselves as the trusted advisor to the school districts as they go through the installation process, and then in the long run, providing grid services, which also includes monetizing the carbon o sets.
Q Charged: Are school districts your main customers at this point?
A Gregory Poilasne: In the US, yes. Many including San Diego Uni ed and LA Uni ed. LA Uni ed is the second-largest school bus eet in the US; they have around 1,800 diesel school buses. If you convert all of those to electric school buses, it’s 108 megawatts. at’s signi cant. Now, in Europe we have some partners like Circle K. ey are headquartered in Laval, Quebec and they own 17,000 gas stations around the world.
Q Charged: School buses are generally considered to be an ideal use case for V2G. What are the pros and cons of some other use cases?
A Gregory Poilasne: I think the only really bad one is fast chargers on the freeway, because you are not there to discharge. You want to go back on the road as fast as possible, otherwise your kids are going crazy. is is not suitable for bidirectional applications, but there is value in providing unidirectional services.
On-the-road charging is an environment that is expensive, so if you have the ability to use that very large capacity in order to provide some type of grid service without impacting the end consumer too much, this is very attractive. We’ve been working with Circle K on deploying our technology in Norway and Denmark, to provide grid services that only increase the charge time for the end user by 30 seconds to a minute.
e grid services include FCR-D, or Frequency Containment Reserve for Disturbances, which is a frequencycontrolled response that happens only in extreme cases where there is a short but signi cant disturbance in the frequency of the electrical current. Basically, we would stop charging for 30 seconds or a minute and then restart, and hopefully, the grid is stable again.
ere’s another service called FFR, which is a very fastresponding service—in the area of a tenth of a second. We are starting with Norway and Denmark, then we’ll expand across all of the Nordics. Now, they’re also deploying a lot of charging stations here in the US, and they’re also interested in looking at what other grid services we can provide. e issue with the US is that the grid is not as advanced as it is in Europe, and especially in the Nordics, so the system is not always able to send us the right signal in order to help keep the grid balanced.
e good business cases are vehicles that leave in the morning from the depot, do whatever they have to do and come back in the evening. Very o en they’ll stay parked 14 hours a day, and also during the weekend. In Denmark, we’ve done all those light-duty eets. We have some utility vehicles, some municipal vehicles, some private eets.
e transit bus use case is not clear, because sometimes they are just a few hours at the depot, but not all the buses are coming late in the evening and leaving early in the
morning. When you drive by a transit bus depot, you see a lot of buses that are parked maybe for many hours. en the question is: What is the cost of doing V2G from an infrastructure perspective, and therefore does the business case work? As the cost of the charging session goes down, deploying universal bidirectional infrastructure makes a lot of sense.
Another interesting business case is electri ed trailers. When you have a truck with a big trailer, if the truck comes with, let’s say, 500 miles of range, when you put a trailer behind it, now all of a sudden you have 150 miles of range. But if you have a battery in the trailer, the primary purpose of the battery could be to provide functionality—if it’s a refrigerated trailer, maybe the battery powers the fridge. But if you put one or two sets of motors in the wheels, now the trailer can also provide some of its own traction, and therefore, reduce the amount of energy that the tractor needs in order to pull the trailer. [Food distribution giant] Sysco just announced that they were deploying some of those trailers. We have some similar projects in Europe, where we are actually implementing V2G.
Now think about a logistics center. Maybe this is a food place where you have some fridges and maybe some ovens, a lot of loads. And those trailers are usually parked for a pretty large amount of time. While they’re parked, obviously you’re going to charge them, but they have plenty of time to provide some grid services. is could be saving on the cost of the energy for the local site while also providing those grid services. Municipal vehicles are another interesting business case. You drive by a heavy-duty utility vehicle parking lot, and they’re parked most of the time. ere are a lot of cases where bidirectional capabilities can be very viable because the vehicles are parked. For certain periods of time, they might be parked 100% of the time for a few months, like school buses during the summer. ose are some of the good use cases. Anything that is overnight, even in-city charging, V2G is great.
I think residential to me is the top. You might have home solar, a battery, maybe you can already interface all of that together. Your car becomes an extension of your home battery. Your home battery might be 15 kWh, but your car is 150 kWh. It’s a big increase.
Q Charged: Is the Wallbox Quasar the only residential bidirectional charger available at the moment?
A Gregory Poilasne: ere’s a product called dcbel. ey are just nishing certi cation right now. ABB has a 10-kilowatt bidirectional charger. We are deploying that in Denmark.
Q Charged: Is there anything pending in Europe that’s comparable to the California SB 233 bill?
A Gregory Poilasne: Not at this point, but the OEMs over there are very aggressive on the subject. BMW was involved with the V2G pilot of the University of Delaware many years ago. Volkswagen has been working on it. PSA has been working on it. Kia/Hyundai will be launching bidirectional-capable vehicles. No, there’s a lot of activity there, but not at the regulatory level.
I think everybody’s going to keep a close eye on what’s going on in California, because if it goes through, the whole US and the whole world most likely will go this way. Maybe excluding Asia, but the Western world will go bidirectional because the OEMs will build one car for all those markets.
Q Charged: Are the OEMs already moving in that direction without the need for regulation?
A Gregory Poilasne: ey just don’t like to be pushed to do something, but they are already there. e California Energy Commission is working on an interoperability test center. If all the vehicles have bidirectional capabilities, what happens when you plug one into charging station A? What happens when you plug it into charging station B? You want to have a site where the vehicles can be tested. One, you can make sure that the bidirectional capabilities are working, but two, you also want to understand some of the characteristics of the response of that control so that you understand what type of services you can use them for.
I think everybody’s going to keep a close eye on what’s going on in California, because if it goes through, the whole US and the whole world most likely will go this way.
For more info about advertising visit: www.ChargedEVs.com/Advertise
Articles about EVs in the mainstream press invariably mention the need for more public charging infrastructure. ose with an anti-EV slant spin this grain of truth into an insurmountable obstacle, but even those that are neutral or positive-leaning o en assume that we’ll need astonishing numbers of public chargers.
In 2017, a USB auto analyst triggered howls of hilarity when he wrote that Tesla would need to add 30,000 Superchargers at a cost of $8 billion “to match the convenience of the US gas infrastructure.” ( e gentleman also predicted that Tesla would not make any pro t from its then-new Model 3.)
Incredibly, such uninformed views still pervade the press. To give just one example, a recent piece in the New York Times stated that “experts” say that public chargers will need to become as ubiquitous as gas stations are today. Respected news sources regularly make similar pronouncements.
I don’t know how these folks de ne “experts,” but I regularly interview CEOs of charging providers and EVSE manufacturers, and while everyone agrees that more (and more importantly, better) public charging is required, no one I’ve spoken to sees EV charging as analogous to the gas station experience.
As I’ve o en noted, people tend to see every new technology through the lens of the old, and that’s natural. Most of us have spent our lives making periodic stops at gas stations to ll up, and until you’ve owned an EV, it’s hard to understand that this model is history.
e US DOE estimates that 80% of charging takes place at home or at the workplace. Of course, this gure just tells us about current charging needs, and at this point most EV owners are a uent suburban dwellers. As EV adoption spreads, the need for public charging is likely to grow. We don’t know what percentage of refueling sessions will need to take place at public chargers in the electric future, but we do know that, for gas vehicles, it will always be 100%, whereas for EVs, it will be a fraction of that.
As EV owners know (but so many writers don’t), many EV drivers will never need to use a public charger. You can count your favorite pundit among that number. I o en visit public chargers as a journalistic duty, but I’ve never needed to use one, because I charge at home, and I don’t make long trips in my EV.
ere are two main use cases that require public charging. One is long-distance travel. e Great American Road Trip requires widespread access to fast, dependable charging, and while the necessary network is rapidly being built out, more will be needed. However, most drivers will need
By Charles Morristo use highway charging only occasionally, and some not at all. Meaningful stats are hard to come by, but by most accounts, only about 5% of automobile trips in the US are for more than 30 miles.
e second situation that calls for public charging is the Plight of the Drivewayless. Millions of urban denizens lack driveways, or even assigned parking spaces, so they cannot install chargers at home. Workplace charging can serve some of these poor souls, but not all—city dwellers o en take public transport to work, and use their cars for shopping trips and weekend outings.
We’ve seen many proposed solutions for the Drivewayless, ranging from sensible to dubious to downright nutty. I don’t know what the urban charging landscape is going to look like, but I am con dent that it will not involve anything similar to a gas station. Some imagine that urban drivers will pay regular visits to charging hubs, where they’ll sit and wait to charge (an acquaintance of mine proposed that such hubs should feature stages for live music).
is isn’t going to happen. In our society, convenience is next to godliness, and a gadget that saves us the ve minutes it takes to check into a hotel, or the three seconds it takes to stick a credit card into a slot, is hailed as a breakthrough. Can anyone really believe that American consumers will sit and wait to charge for half an hour?
On the highway, waiting to charge is no great inconvenience, because the stations are on the way, and most human bodies need to make a pit stop every 200 miles or so anyway (some commercial drivers are required to do so). But driving to a “charging hub” and sitting around a couple of times a week? People won’t do it.
To get a realistic idea of what urban charging will look like, look at the few cities where EVs make up a large percentage of vehicles. In Oslo, Amsterdam and, increasingly, London, on-street parking areas and public garages are liberally provided with chargers. You park, you charge. No sci- gadgets needed, and no heavy li ing for utilities, as these areas already have electrical service for street lighting. On my last visit to Oslo, I saw lots of EVs charging, but I did not see anyone waiting around at a charging hub.
Cities need lots more on-street chargers, they need to be well-designed to t into streetscapes without clutter, and they need to be smart, so utilities can manage charging times to help stabilize the grid. ere are a lot of rich opportunities for innovative companies in the charging space, but turning gas stations into charging hubs is not one of them.
As EV owners know (but so many writers don’t), many EV drivers will never need to use a public charger.