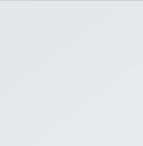

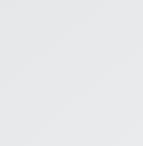



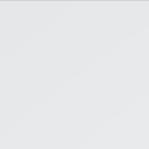

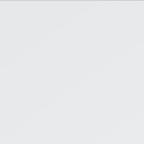





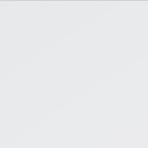

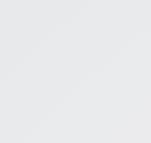













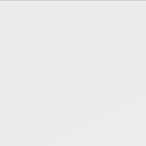


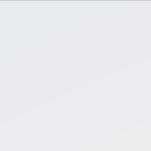
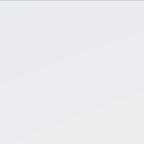


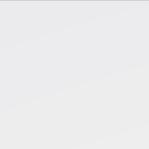
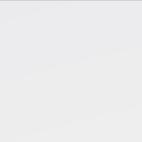




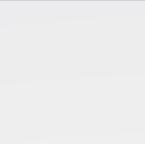

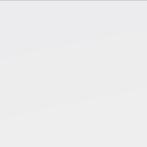

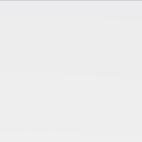

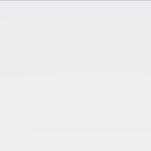

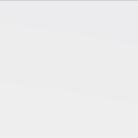











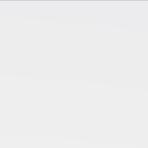


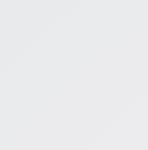






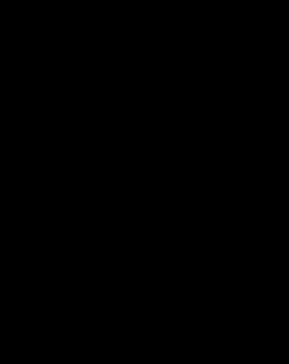


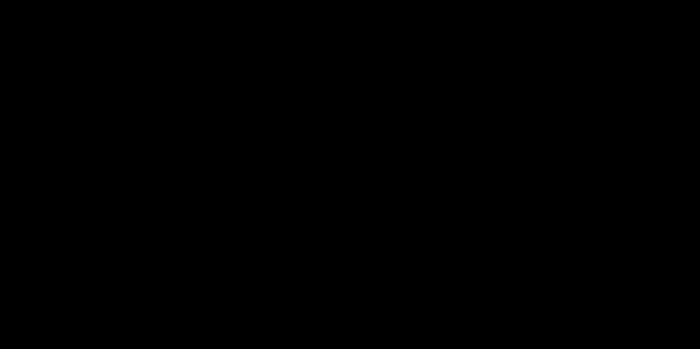

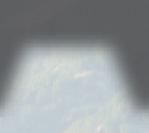
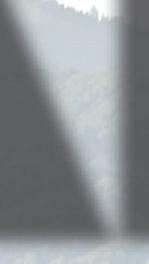

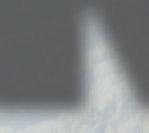
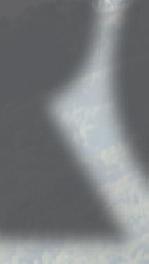

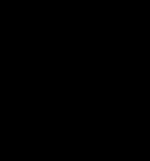
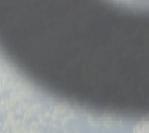
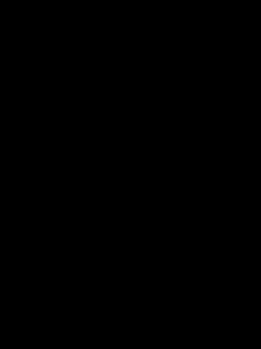
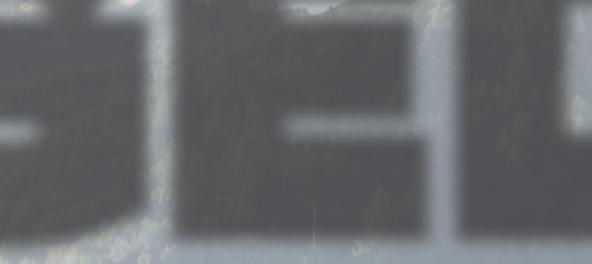










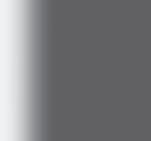
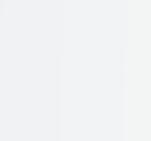
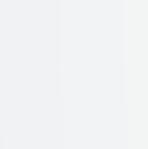
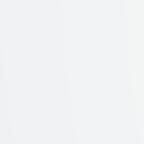
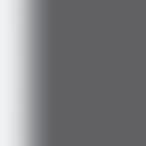

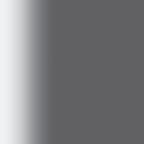
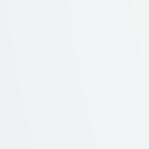
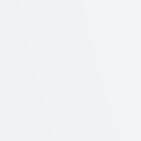
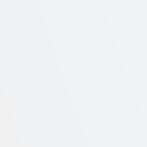
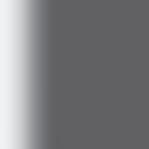
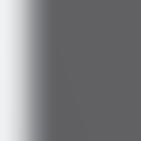
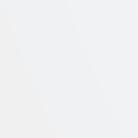
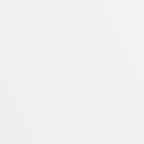

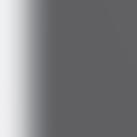
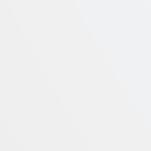
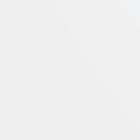
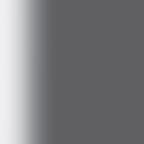
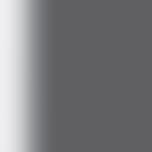
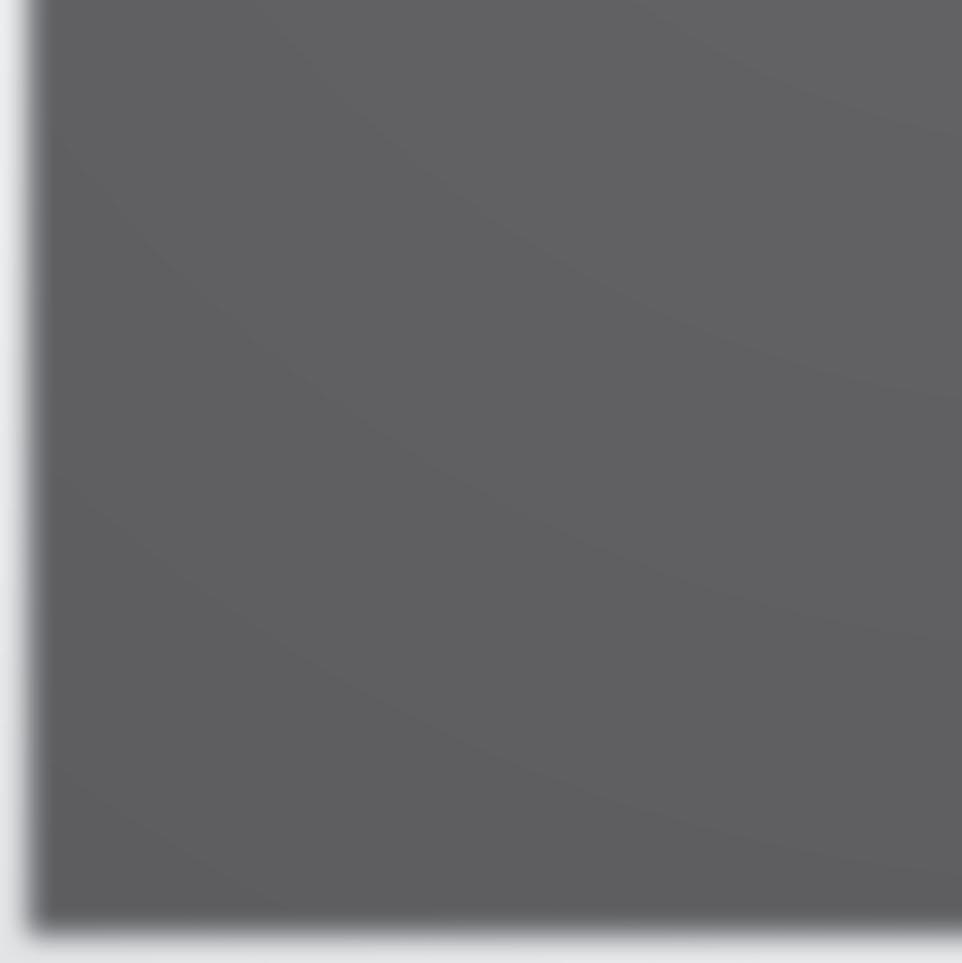

Battery cell, module and pack level charge/discharge cycle testing solutions designed to provide high accuracy measurement with advanced features. Regenerative systems recycle energy sourced by the battery back to the channels in the system or to the grid.
Battery simulation for testing battery connected devices in all applications to confirm if the device under test in performing as intended. Battery state is simulated which eliminates waiting for the charge/discharge of an actual battery. Real time test results include voltage, current, power, SOC%, charge/discharge state and capacity.
To learn more about our Battery Test Solutions visit chromausa.com
DOE allocates $50 million to help suppliers adapt factories for the EV supply chain
Modine introduces EVantage electric compressors and valves for commercial EVs
Cyclic Materials and SYNETIQ partner to recycle rare earth elements from motors
TDK extends inductor range for automotive and industrial uses
NGen invests $29.7 million in five new Canadian EV manufacturing projects
Able Electropolishing enhances its analytic and testing capabilities
ZF Aftermarket introduces electric axle drive repair kits
Paraclete Energy achieves cost-effective silicon anode materials
Hönle and bdtronic develop process for curing sealants for battery controllers
Wright Electric receives $3.34-million grant for ultra-lightweight aircraft batteries
NOVONIX and CBMM sign joint agreement focused on nickel-based cathodes
Arcadium Lithium buys Li-Metal IP and assets
Freudenberg Sealing Technologies launches new product lines for prismatic cells
Logistics firm DSV orders 300 electric semi-trucks from Volvo
Stellantis partner Leapmotor ships its first batch of EVs from China to Europe
Peterbilt 579EV trucks join Universal Logistics fleet
Saudia to buy up to 100 eVTOL jets from Lilium
CASE debuts new 580EV electric backhoe loader
Monarch Tractor raises $133 million in Series C funding for electric tractor
Two Greek cities order 89 electric waste-collection trucks from FUSO Europe
One way to reduce parking costs for property owners—give residents a free EV
Tesla scores a $5-million order from Baltimore for a fleet of EVs
Ford Pro provides free EV chargers to California businesses
South Pasadena, California completely electrifies its police fleet
GM BrightDrop division to be merged into Chevrolet
Munich Airport to deploy 14 Goldhofer electric aircraft tractors
Are Chinese electric buses exempt from European EV tariffs?
Indian firm Exicom to acquire charger manufacturer Tritium
SparkCharge to integrate Pioneer Power’s e-Boost mobile off-grid EV charger
US government awards $521 million in EV charging grants
Los Angeles expands streetlight EV charging program
California incubator launches repair training center for EV chargers
Terbine introduces new digital twin for EV charging networks
Generac makes $35-million investment in Wallbox Chargers
New study finds fleet owners more satisfied with EVs than legacy ICE vehicles
3V Infrastructure launches to offer EV charging at long-dwell properties
SAE International publishes new standard for wireless light-duty EV charging
EVgo pursues several initiatives to improve public EV charging reliability
ENROUTE data sharing to improve efficiency of heavy-duty EV charging
Beam Global acquires power electronics manufacturer Telcom
Uber hires former Tesla Head of Charging Rebecca Tinucci
Publisher Senior Editor
Technology Editor
Segment Leaders
Christian Ruoff
Charles Morris
Jeffrey Jenkins
Joel Franke
Mark Rogers
Greg Schulz
Graphic Designers
Tomislav Vrdoljak
Contributing Writers
Jeffrey Jenkins
Charles Morris
Christian Ruoff
Jonathan Spira
John Voelcker
Cover Image Courtesy of
Special Thanks to
For Letters to the Editor, Article Submissions, & Advertising Inquiries Contact: Info@ChargedEVs.com
American Honda Motor Co., Inc
Kelly Ruoff
Sebastien Bourgeois
ETHICS STATEMENT AND COVERAGE POLICY AS THE LEADING EV INDUSTRY PUBLICATION, CHARGED ELECTRIC VEHICLES MAGAZINE OFTEN COVERS, AND ACCEPTS CONTRIBUTIONS FROM, COMPANIES THAT ADVERTISE IN OUR MEDIA PORTFOLIO. HOWEVER, THE CONTENT WE CHOOSE TO PUBLISH PASSES ONLY TWO TESTS: (1) TO THE BEST OF OUR KNOWLEDGE THE INFORMATION IS ACCURATE, AND (2) IT MEETS THE INTERESTS OF OUR READERSHIP. WE DO NOT ACCEPT PAYMENT FOR EDITORIAL CONTENT, AND THE OPINIONS EXPRESSED BY OUR EDITORS AND WRITERS ARE IN NO WAY AFFECTED BY A COMPANY’S PAST, CURRENT, OR POTENTIAL ADVERTISEMENTS. FURTHERMORE, WE OFTEN ACCEPT ARTICLES AUTHORED BY “INDUSTRY INSIDERS,” IN WHICH CASE THE AUTHOR’S CURRENT EMPLOYMENT, OR RELATIONSHIP TO THE EV INDUSTRY, IS CLEARLY CITED. IF YOU DISAGREE WITH ANY OPINION EXPRESSED IN THE CHARGED MEDIA PORTFOLIO AND/OR WISH TO WRITE ABOUT YOUR PARTICULAR VIEW OF THE INDUSTRY, PLEASE CONTACT US AT CONTENT@CHARGEDEVS.COM. REPRINTING IN WHOLE OR PART IS FORBIDDEN EXPECT BY PERMISSION OF CHARGED ELECTRIC VEHICLES MAGAZINE.
The new CXT-ICM3SA series of Inverter Control Modules forms the heart of CISSOID’s modular inverter platform, leveraging the ultra-fast OLEA® T222 Field Programmable Control Unit by Silicon Mobility.
Based on CISSOID’s CXT-PLA3S series of Intelligent Power Modules and HADES2 gate driver chipset, they are supporting the OLEA® APP - T222 INVERTER software for fast development of electric motor drive trains. OLEA OLEA
3-phase 1200V 340-550A SiC power module
Integrated gate driver board
Dual ARM® Cortex-R5F in lockstep
Advanced Motor Event Control (AMEC®) unit
Real-time actuator & sensor control and processing
T222 processor & software ISO26262 ASIL-D and AUTOSAR 4.3 certified
Less complaining, more educating
A year ago, the media was reporting that the EV dream had gone poof—sales were slowing (belated correction: the rate of growth had slowed). In our last issue, I wrote that the global auto industry is about to be radically reshaped—and possibly not to the advantage of “Western” legacy automakers. Now these trends are starting to converge—spooked by slower sales growth, some automakers are adjusting their plans in ways that bode ill for their future competitiveness.
Sales projections are a big deal because building cars requires coordinating every link in an extremely complex supply chain. Automakers need to predict future demand as precisely as they can, and adjust production accordingly— producing too many or too few of a particular model or component can translate to millions in losses (a sin that Wall Street will promptly punish).
Are Ford and GM (and more recently, Volvo) mistaken to roll back their EV timelines every time they see a dip in sales (and especially, to trumpet such moves in the media)? VW also announced it was considering closing some auto plants in Germany for the rst time in the company’s history, citing di culties in the electric transition as a cause.
Yes, it’s bad to have an oversupply of EVs, but there’s a critical marketing aspect to this—consumers want to buy what others are buying, and corporate kvetching about slow sales can quickly become a self-ful lling prophecy.
Legacy automakers are caught in e Innovator’s Dilemma—with the advantage of a huge brand and customer base but high expectations of yearly sales. Unless they nail the execution, transitioning to all-in on EVs could mean short-term revenue (and job) losses. But there are a couple of things governments and companies could do to boost EV sales, and save our auto industries before the Chinese come in and buy up the remnants at the bankruptcy sale.
First, it’s proven that government support and smart policies will drive sales. EVs are still more expensive to buy upfront than legacy vehicles, and skeptical consumers need a push. Germany abruptly ended its EV purchase subsidies at the end of 2023, and EV sales dropped by 16% in the rst half of 2024. (As we went to press, the German government—spooked by VW’s threat of plant closures—had just agreed to a new set of EV tax breaks.)
Second, the relentless anti-EV campaigns are hitting their marks. Recent surveys have found that substantial numbers of non-EV drivers believe the endlessly-repeated myths. And the anecdotal evidence is overwhelming— everyday acquaintances forward me anti-EV talking points li ed straight from the sewers of social media. e single most valuable thing automakers could do to boost EV sales (assuming they want to) would be to mount a massive public education campaign, not only for potential customers, but for their dealers too. Sales slowdowns, real or feared, may be a topic in Detroit and Wolfsburg, but the outlook from the engineers with their boots on the ground designing the next generation of EVs is overwhelmingly optimistic. Our inboxes over ow with pitches to report on innovations that promise to drastically optimize EV systems to improve quality and performance while reducing costs. For examples, see our articles on e-fuses (page 22) and dry electrode coating technology (page 28). On the infrastructure front, some stubborn logjams are being cleared. Paired Power (page 64) and itselectric (page 72) are addressing very di erent markets, but both aim to bring EV charging to places and segments where it wasn’t practical before, while cutting the delays in setting up new utility service.
And, while we may be hard on the world’s giant automakers, they are moving forward. Honda has introduced an exciting new EV to the US market, and John Voelcker gives you an in-depth look at it on page 46.
Christian Ruoff | Publisher EVs are here. Try to keep up.
e DOE’s O ce of Manufacturing and Energy Supply Chains (MESC) has announced $50 million in grants for six states with signi cant automotive workforces to help small- and medium-sized suppliers adapt their manufacturing facilities to serve the EV supply chain.
e announcement on state allocations follows an April 2024 Request for Information, seeking input on state/federal partnerships that could enable federal funding to reach automotive suppliers embarking on the transition to serve electri ed vehicle supply chains. Eligible states must have a workforce at least 0.5% of which is in the automotive sector. Under these criteria, six states are eligible: Michigan, Ohio, Indiana, Kentucky, Tennessee and Illinois.
DOE has also announced $1.5 million in selections across three teams of technical assistance providers under the Industrial Training and Assessment Center (ITAC) program. e teams from Purdue University, the University of Michigan and the University of Illinois will help create a Small Supplier EV Transition Playbook, to help ICE suppliers navigate the transition to EVs.
“Under President Biden and Vice President Harris’s leadership, America’s auto communities and the workforces they support nally have the tools they need to compete and thrive in the 21st-century clean energy economy,” said Secretary of Energy Jennifer M. Granholm. “By helping states and manufacturers navigate the emerging EV manufacturing industry, today’s announcements will help ensure that the workforces that de ned America’s auto sector for the last 100 years will have the opportunity to shape the next 100 years.”
US thermal-management technology company Modine has announced the availability of its EVantage electric compressor and valve product lines designed for the cooling of battery and power electronics and air conditioning of passenger cabins in heavy-duty commercial EVs.
e EVantage High Voltage Electric Compressor, engineered to adapt to 12 V and 24 V systems, conditions the coolant owing to the battery pack or the air for the cabin HVAC system. EVantage 3-Way Coolant Valves, also suitable for 12 V and 24 V systems, feature three 28 mm ports to channel coolant to battery packs, power electronics, motors and other vehicle subsystems. Both components are IP67-rated.
“Our goal was to design a suite of products to keep commercial EVs on the road through long days and extreme conditions,” said Gina Maria Bonini, VP and General Manager of Advanced ermal Systems at Modine. “ e Modine EVantage electric components are proven to withstand the most unforgiving conditions through rigorous testing.”
Canada-headquartered metals recycler Cyclic Materials has signed a collaboration agreement with SYNETIQ, a UK-headquartered vehicle salvage and recycling company, for the recycling of end-of-life electric motors containing rare earth elements.
e motors to be supplied by SYNETIQ include hybrid and EV drive motors, as well as auxiliary motors found in all vehicles.
To help meet North American demand for domestic sources of mixed rare earth oxide, Cyclic Materials recently opened its Hub100 commercial demonstration plant in Kingston, Ontario, which employs the company’s proprietary hydrometallurgical technology, REEPure.
Cyclic’s Mag-Cycle and REEPure technologies separate magnets from products such as electric motors and then convert them into mixed rare earth oxides, cobalt-nickel hydroxides and other raw materials. Cyclic will process feedstock from SYNETIQ with Mag-Cycle and send it to the Hub100 plant for processing using REEPure technology.
“ is agreement represents a notable step forward in our mission to advance sustainable solutions for rare earth recycling to drive the circular economy forward across the globe,” said Patrick Nee, Senior VP of Strategic Partnerships and co-founder of Cyclic Materials.
Japanese electronics company TDK Electronics has extended its ERU27M series of SMD high current at wire inductors comprising an isolated alloy powder core and at wire helical winding.
e series of four variants is designed to meet the demand for higher power densities and currents in automotive and industrial applications, by using an alloy powder core material that exhibits a so er saturation characteristic than the core material used previously.
Designed for rated currents from 36 A to 48 A, these surface-mountable components cover a range of inductance values from 2.3 µH to 8.5 µH. DC resistances are as low as 0.68 mΩ to 1.66 mΩ. e at wire winding enables the components to have compact dimensions of 27.1 mm x 25.55 mm. e height ranges from 14.1 mm to 16.4 mm. e inductors are designed for operating temperatures from -40° C to 150° C.
e four new AEC-Q200-quali ed energy storage chokes provide magnetic shielding and robust construction incorporating a third pin that is not electrically connected. ey can be used in DC-DC converters, voltage regulator modules and point-of-load (POL) converters in the automotive sector, as well as in solar converters.
TDK Electronics can change certain production parameters to help customers optimize space and cost or provide fully customized designs.
VISIT BOOTH 3600!
SCHULER NORTH AMERICA 7145 Commerce Blvd. Canton, MI | 48187, USA
Phone +1 734-207-7200 www.schulergroup.com
CONTACT US: marketing.information@schulergroup.com
· Latest battery cell production technology for laboratories, pilot plants, and gigafactories.
· Equipment for central processes: battery cell assembly, formation, and testing of cells, modules, and packs.
· System solutions for the production of prismatic and cylindrical battery cell housings.
· NEW calender developed for the upstream electrode production process step.
Manufacturing innovation cluster Next Generation
Manufacturing Canada (NGen) is investing C$40 million ($29.7 million) in ve new advanced manufacturing projects involving 10 companies under its Electric Vehicle Manufacturing Value Chain Program.
Two of the bene ciaries are battery materials developer Nano One Materials and professional services company Worley Chemetics, which together will receive C$2.8 million.
Nano One is developing the process to produce more streamlined, less expensive and less energy-intensive cathode active materials (CAM) for lithium-ion batteries.
Nano One and Worley plan to use the NGen funding to advance their existing strategic alliance to develop, market and sell CAM facility packages. e two companies plan to produce equipment—tanks, reactors, furnaces and kilns—for Nano One’s One-Pot cathode technology process at Worley’s alloy fabrication shop in Pickering, Ontario.
e process engineering design package will include intellectual property rights, ow sheets, detailed engineering, operational know-how, and proprietary equipment including reactors and kiln components, which will be supported by NGen.
Chemetics will support Nano One in identifying the best materials and fabrication methods for the equipment required, as well as engineering and delivering the technology.
“NGen backing Worley Chemetics’ collaboration with Nano One will accelerate the commercial trajectory of the One-Pot process,” said Laura Leonard, Worley’s Group President of Technology Solutions. “ e fastest path to net zero is to standardize or, as we are doing with Nano One, design one, build many.”
Able Electropolishing has acquired new in-house laboratory equipment that brings signi cantly enhanced analytic and testing capabilities.
Electropolishing removes surface imperfections that can compromise mission-critical metal parts used in the automotive, semiconductor and many other industries. Able’s new equipment is designed to further improve the precision and e ectiveness of electropolishing for improving the nish, t and function of critical metal parts made from metal alloys, including stainless steel, aluminum and titanium.
“ e Keyence VK-X3000 3D Surface Pro ler and Keyence VHX-X1 Digital Microscope enable a level of metal surface nish inspection and analysis that provides a high-tech look into electropolishing’s ability to eliminate microcracks, burrs and other surface defects that are invisible to the naked eye,” says the company.
e Keyence VK-X3000 3D Surface Pro ler uses a triple-scan approach, including laser confocal scanning, focus variation and white light interferometry, to perform high-accuracy measurements and analyses, with a resolution of 0.01 nm.
e Keyence VHX-X1 Digital Microscope delivers high-resolution imaging and measurement functions. It features lighting and imaging modes that enhance surface details for a wide range of imaging and analysis capabilities, including metallurgical analysis.
Able Electropolishing is ISO 9001- and ISO 13485-certi ed, and complies with the electropolishing standards ASTM B912, ASTM F86 and ISO 15730.
Automotive a ermarket provider ZF A ermarket, a division of German automotive systems manufacturer ZF Friedrichshafen, has introduced to the US and Canadian markets 25 new kits for performing 25 di erent repair tasks on electric axle drives.
Among 45 new products that the company has recently released in North America, the kits, which contain all needed spare parts and fastening elements, allow independent repair shops to perform such tasks as replacing leaking coolant connections, repairing defective parking locks, changing speed or temperature sensors, and replacing drive sha s, all without removing the electric axle drive.
“Repair shops are seeing more electric cars, and need spare parts to service them. As one of the leading producers of electric drives worldwide, ZF is now making its products available to the independent a ermarket in our region,” said Mark Cali, Head of Independent A ermarket, USC, for ZF A ermarket.
Paraclete Energy, a producer of silicon-based anode materials for the EV and battery markets, has reached a cost of $35/kWh for its SILO Silicon anode materials—below the typical cost of $53/kWh for lithium iron phosphate (LFP) batteries using graphite anodes.
Paraclete Energy’s silicon anode materials o er speci c energy of over 520 Wh/kg, exceeding that of traditional graphite anodes, according to the company. is allows batteries to deliver more energy for longer periods of time.
Paraclete Energy’s distributed manufacturing model enables the production of anode materials near or at customers’ sites, increasing production e ciency and reducing costs.
“ e recent decline in LFP battery prices underscores the industry’s commitment to a ordability and sustainability,” said Je Norris, CEO of Paraclete Energy. “Our SILO Silicon anode technology serves as a proxy for cost-e ective and high-performance energy storage for the rapid adoption of electric vehicles and renewable energy solutions.”
German mechanical engineering company bdtronic and German UV specialist Hönle have created an inline, vestep process for dispensing and curing liquid sealants known as Cured-In-Place-Gaskets (CIPGs) for battery cell module controllers.
In the rst step of the process, the component contours are pretreated with atmospheric pressure plasma to improve the adhesion of the sealant. In the second and third steps, the highly-viscous CIPG is applied in contours. In the fourth step, the sealants are cured using a Hönle UV curing system. Finally, the nished part is inspected for quality and consistency.
e process was developed for a customer that required a production volume of 6,000 battery sensors every 24 hours, requiring one part to be produced every 13 seconds. Hönle’s testing showed that the sealing compound polymerized in the broadband spectrum of UVA and UVC, and required an unusually high UV dose.
Hönle identi ed its UVAPRINT curing module as the optimal curing system for this material, as its Cold-Mirror technology prevents the temperature on the substrate from rising too high despite the high intensity. e components pass through three UVAPRINT modules to receive a full cure before the sensors move to step ve for optical inspection.
“To achieve the best possible process, it is essential to work closely with the customer and all involved technology providers from the very beginning. We need to understand the requirements and collaboratively develop their technical implementation,” explains Fabian Tremmel, Head of Engineering Dispensing at bdtronic.
Wright Electric, a US developer of ultra-lightweight motors, generators and batteries for the aerospace and military sectors, along with its partners, which include NASA, DOE and DOD, has been awarded a $3.34-million grant from the FAA’s Fueling Aviation’s Sustainable Transition (FAST) program.
e funding will be used to develop a new class of batteries for large electric aircra accommodating 100+ passengers—the segment of the aerospace industry that accounts for more than 90% of its carbon emissions. e R&D program’s objective is to make such aircra a possibility by developing lithium-sulfur batteries that hold roughly three times more energy per pound than lithium-ion batteries.
“When Wright Electric was founded in 2016 the idea of a battery that would allow aircra to y regional routes with reserves seemed like a fantasy to most people. Now, we are one of several companies with a viable path toward a technology that will enable regional aircra ights entirely on battery power,” said Wright CEO Je Engler.
COMSOL Multiphysics®
Multiphysics simulation helps in the development of innovative battery technology by providing insight into mechanisms that impact battery operation, safety, and durability. The ability to run virtual experiments based on multiphysics models, from the detailed cell structure to battery pack scale, helps you make accurate predictions of real-world battery performance.
» comsol.com/feature/battery-design-innovation
Battery materials and technology company NOVONIX and niobium specialist CBMM have signed a joint development agreement focused on nickel-based cathode materials.
Under the agreement, NOVONIX will use its patented all-dry, zero-waste synthesis process to synthesize, test and analyze cathode active materials (CAM), which will incorporate CBMM’s suite of niobium products.
NOVONIX will use its cathode pilot line to characterize the materials’ physical and electrochemical performance, including building full-scale pouch cells for benchmark evaluation. CBMM will provide various materials, which will be used to demonstrate optimal performance with NOVONIX’s cathode powders.
NOVONIX was recently granted a patent for its alldry, zero-waste cathode synthesis technology in Japan.
e company continues to produce various grades of mid- and high-nickel cathode material to speci cations of potential commercialization partners, and has begun sampling these pilot-scale materials.
“CBMM’s experience with niobium products allows us to explore the use of important additives to improve the stability and durability of our materials,” said Dr. Chris Burns, CEO of NOVONIX. “Our agreement with CBMM advances NOVONIX’s strategy to form strong partnerships to demonstrate and commercialize our all-dry, zero-waste cathode synthesis technology.”
CBMM has invested $80 million to establish its rst industrial-scale niobium oxide re ning facility, with the intent of providing battery makers with niobium. e use of niobium oxide has been shown to improve the cycle life of NMC cathode materials, and CBMM expects it to be a key material in CAM production. Before the end of 2024, CBMM aims to begin production at the new facility, which has a capacity of the 3,000 metric tons per year.
Arcadium Lithium has acquired the lithium metal business of Li-Metal in an $11-million all-cash deal that includes the company’s intellectual property and physical assets related to lithium metal production, including a pilot production facility in Ontario, Canada.
e acquisition is expected to provide a safer, lower cost and more sustainable process for lithium metal production using various grades of lithium carbonate feedstock, which Arcadium produces in Argentina. ese new capabilities will complement the company’s process technologies for producing lithium metal at its Bessemer City site in North Carolina, using concentrated lithium chloride from its Güemes facility in Salta, Argentina.
Arcadium uses lithium metal to manufacture lithium specialty products, including high-purity lithium metal (HPM) and LIOVIX, a printable lithium metal formulation for primary battery applications and next-generation batteries. Arcadium also processes lithium metal into butyllithium, which is used to manufacture lightweight tires, among other applications.
“ e ability to produce lithium metal from lithium carbonate will give us additional exibility to utilize our vertically integrated network of assets while reducing the need for third-party lithium metal,” said Paul Graves, CEO of Arcadium Lithium. “ is will further enhance the competitiveness of our butyllithium and lithium specialty chemicals business and help us create the scale needed to meet the growing demand for next-generation battery materials developed from lithium metal.”
Germany-headquartered Freudenberg Sealing Technologies has introduced cell caps and nonwoven cell stack envelopes for prismatic battery cells.
e battery cell envelopes use nonwoven materials that wrap the cell stack and, like conventional lms, protect it during assembly and provide electrical insulation. Nonwoven envelopes consist of a ber network forming an ultra-homogeneous pore structure. e bers are surface-treated for permanent electrolyte wettability to reduce the risk of entrapping gas bubbles as the cell is lled, and to help to keep the cell stack wetted over its lifetime.
Nonwoven materials lled with electrolyte also o er improved heat management within the cell compared to conventional foils, owing to the resulting higher thermal conductivity, according to the company.
e custom-designed cell caps, developed in collaboration with cell manufacturers, are tested to be gas-tight and to maintain this capacity throughout the battery’s cycle life. is optimizes performance in a range of operating conditions, minimizes the risk of gas leakage and increases safety. e cell caps also have strong mechanical resistance to peak loads and fatigue. ey are compatible with various electrolytes, coolants and gases, enabling integration into di erent EV systems.
Luma eld’s new Battery Analysis Module is designed to enhance the safety and quality of batteries by providing automated tools for identifying and characterizing common manufacturing defects in batteries.
e module provides automated tools for measuring anode overhang distance, detecting debris and contaminants, assessing can integrity, and identifying common defects such as layer delamination. It also tracks these attributes over time, giving manufacturing managers real-time insights into quality issues as they develop.
Luma eld’s Battery Analysis Module is the latest addition to Voyager, the company’s cloud-based so ware for analyzing industrial X-ray Computed Tomography (CT) scans. Voyager is seamlessly integrated with Luma eld’s CT scanners—the o ce-friendly Neptune scanner and the automated, line-ready Triton inspection solution. e Battery Analysis Module may also be used with legacy CT systems through Uplink, which allows CT data from any scanner to be visualized, analyzed and shared in Voyager.
“Batteries need to be nearly awless to avoid catastrophic failures, and traditional quality control tools can’t look deeply enough to nd every defect. Industrial CT is the best all-purpose inspection tool for batteries, and our Battery Analysis Module gives engineers the tools they need not only to catch aws in real time, but also to track quality trends and ne-tune their processes,” said Eduardo Torrealba, co-founder and CEO of Lumaeld.
e Battery Analysis Module will be available to select partners this fall, and to all customers in early 2025.
By Jeffrey Jenkins
An old saw often uttered by an electrical engineer (or their hapless techs) when an electronic device releases its magic smoke goes something like this: “The transistor bravely sacrificed itself to protect the fuse.”
is is a succinct way of saying that conventional fuses (and most types of circuit breakers) shouldn’t be counted on to protect a downstream load from complete destruction in the event of a fault, but only to (hopefully!) prevent a re from overheated wiring, sparking, etc.
is regrettable shortcoming is mostly due to physics and economics: a conventional fuse or thermal circuit breaker will take about 1,000 to 10,000 times too long to protect most semiconductor devices from overcurrent even when the latter are grossly over-sized (i.e. cost way more than is economically justi able). Specialized circuit breakers that combine a fast-acting magnetic trip along with the conventional thermal one can allow for less over-sizing of the downstream semiconductors, but they themselves are much more expensive devices, so once again this seems economically questionable. To truly protect the downstream semiconductor devices from short-circuit faults without su ering from nuisance tripping during normal operating conditions requires an overcurrent protective device that responds to severe overcurrents in 1 to 10 microseconds while still maintaining a more conventional fuse response
Microchip’s Silicon Carbide E-Fuse demonstrator is available in six variants for 400–800 V battery systems.
to moderate overcurrents, which is precisely what an electronic fuse can do—and potentially at a competitive cost to the specialized magnetic-thermal circuit breaker, especially if it allows the use of more rationally-rated semiconductors.
To better understand the pros and cons of electronic fuses, a review of conventional fuse and circuit breaker technology is in order. All fuses essentially rely on the melting of a fusible element to break the circuit during overcurrent conditions. e amount of time required is inversely proportional to the degree of overcurrent. Since the heating of the fusible element is the result of I2R losses, a doubling of current should result in a quartering of the time to blow (that is, following a square law). Indeed, fuses are most o en characterized by I2t curves as a shorthand way of expressing the energy required to rupture the fusible element by leaving out the resistance, R, in the energy equation of I2R over a given time, t Various tricks can be used to modify this current vs time behavior—particularly in lengthening the time that moderate overcurrents can be tolerated without unduly compromising the response to shorts—but at higher overcurrents the amount of time required for a fuse to
open tends to an asymptotic minimum (due to the need for the molten metal to actually fall far enough away to break the circuit). Furthermore, if the fuse must break a DC circuit above 50 V or so, an arc will be developed as the fusible link melts, prolonging the amount of time that current will be allowed through it (albeit with a voltage drop across said arc). is arcing problem becomes increasingly di cult to manage with open-circuit DC voltage (it’s less of an issue for AC, because of the periodic returning to 0 V), to the point that some form of forced arc quenching is required above 300 VDC or so (by surrounding the fusible element with quartz sand, or spring loading it, etc).
ermal circuit breakers also rely on I2R heating to trip, but this occurs via the heating of a bimetallic strip that causes it to bend. Inexpensive thermal circuit breakers that aren’t expected to trip more than a few times in their operational life will utilize the bimetallic strip directly to move the current-carrying contacts apart (via self-heating of the strip from load current), but more robust designs—and especially at higher currents—will use a separate heater coil around the strip which will itself actuate a toggling mechanism so that there is a
snap-action response upon reaching the critical trip temperature, rather than a more gradual movement which would encourage arcing. e toggle mechanism allows for either a bistable action, meaning it is stable in either the closed or open (tripped) positions, or a monostable action, meaning it will automatically return to the closed position a er the bimetallic strip has cooled down. Regardless of the speci c design of a thermal circuit breaker, it will su er from some downsides that don’t a ict the simpler fuse (or not to the same degree, anyway). For one thing, it will take far longer to respond to a severe overload or short-circuit than a fuse of the same nominal current rating. For another, the trip current (or the time delay before tripping occurs) will be more sensitive to the ambient temperature, because the temperature rise needed to operate the bimetallic strip must necessarily be limited so as not to create the very re hazard it is supposed to prevent.
ermal-magnetic circuit breakers address the excessive delay in responding to severe overloads that is characteristic of purely thermal circuit breakers by passing the load current through a solenoid—that is, a linear coil of wire around a moving ferromagnetic plunger—which can independently operate the toggling mechanism. e magnetic force developed by a solenoid is proportional to the current owing through it, so the higher the load current, the more forcefully (and therefore faster) its plunger will move. e magnetic-hydraulic circuit breaker addresses the sensitivity of trip current to ambient temperature by replacing the bimetallic strip with a viscous uid that the solenoid plunger must operate against. is preserves the relatively slow response to moderate overloads typical of the thermal circuit breaker with the faster response to short-circuits achieved by the magnetically-actuated mechanism.
e aforementioned shortcomings of conventional fuse and circuit breaker designs can be addressed by going with an electronic solution—that is, by using a semiconductor switch to interrupt the circuit in the event of a fault condition—giving rise to what is popularly called an electronic fuse, or e-fuse for short (though it would be more accurate to describe it as an electronic circuit breaker). E-fuses can not only respond far faster to an overcurrent fault, they can also implement current vs time behaviors that would be impractical (or impossible) with conventional technologies, as well as protect against additional hazards such as overvoltage, over- and
E-fuses can not only respond far faster to an overcurrent fault, they can also implement current vs time behaviors that would be impractical (or impossible) with conventional technologies.
under-temperature, etc, at little to no extra cost (i.e. with a few more components or additional lines of code). Furthermore, e-fuses may cost less than conventional electromechanical circuit breakers of similar current interrupt rating (though, admittedly, they compare less favorably to conventional fuses in this regard).
e simplest implementation of an e-fuse is a current-measuring circuit feeding a comparator that controls a semiconductor switch. At operating voltages up to about 50 V and maximum currents up to about 20 A, the current measuring circuit will typically be a resistive shunt that is wired in series with the negative line (aka the low side), whose voltage drop is multiplied by an opamp-based di erential ampli er with a modest amount of gain (2x to 10x is typical here) so as not to incur too high of a power loss in the shunt. At higher voltages and/ or currents, a current measuring circuit based on a Hall e ect current sensor (or a competing technology, such as giant magnetoresistance) will be more attractive, because there is no I2R loss as incurred by a shunt, and galvanic isolation is automatically provided. Either way, the output of the current-measuring circuit will be compared to a reference voltage by a comparator, which itself can be implemented with an analog IC (such as the venerable LM331 from Texas Instruments), though it’s probably more common to use a microcontroller IC these days, especially if other protective functions are to be implemented. A key requirement for the comparator function is that it have hysteresis, or slightly di erent turn-on and turn-o thresholds, to prevent oscillation when the load current is near the overcurrent trip point.
e output of the comparator will likely be unable to directly drive the semiconductor switch, so some form of gate driver circuit or IC will be required, but this could merely be a complementary pair of bipolar transistors wired in the classic push-pull con guration. e semiconductor switch is most commonly either a
Lightweight construction with long-fiber reinforced polyamides
Tailor-made products for cooling systems
Flame-protected polyamides
High-performance polyamides from EMS-GRIVORY are not only predestined in cars with classic combustion engines, they are also excellently suited for electromobility applications.
This applies to both classic lightweight design applications and structural parts as well as thermal management or components for high-voltage onboard power systems.
single low-side MOSFET (for blocking current ow in one direction—i.e. only discharge, from the perspective of a battery), or two MOSFETs wired source-to-source (for bidirectional blocking). is latter con guration is commonly used in the BMS for Li-ion batteries (which, a er all, incorporates all of the functions of an e-fuse, in addition to its cell monitoring and balancing duties).
At higher voltages, it is more usual to put the switch in the high side (i.e. the positive line) and use either an isolated or level-shi ing gate driver to control it, especially when the negative line must be earth grounded for safety reasons. One key requirement for the semiconductor switch is that it must be able to withstand a higher peak current (or, more correctly, have a higher fusing energy I2t again) than the device it is protecting; a less obvious requirement is that the impedance of the upstream power source not be so low as to make it impossible for the e-fuse’s switch to survive a hard short downstream. Note that this latter requirement also applies to conventional circuit breakers and fuses, but is far easier to meet with devices that don’t rely on active semiconductors. is implies that the switch(es) in the e-fuse will be bee er, and therefore more expensive, than the semiconductor devices it is supposed to protect, which would be economically questionable if not for the e-fuse’s extended protection capabilities and much faster response speed.
Finally, e-fuses obviously require power to operate, and if the voltage of the upstream energy source isn’t directly usable by the e-fuse circuitry (in the range of 3 V to 30 V, say) then some type of DC-DC converter will also be needed, adding to the overall cost while decreasing reliability. is also means that an e-fuse can’t directly replace an existing conventional fuse or circuit breaker, as it needs another wire back to the power source to complete its supply circuit (though this is typically easy to retro t).
It is important to note that there are some power circuit topologies in which no external fuse will be able to protect its semiconductor devices from failure, regardless of fuse technology or how fast it can open. e most common example of such are the switches in a 3-phase inverter, as they are immediately preceded by a capacitor wired directly across the supply rails. is capacitor essentially presents a very low-impedance voltage source to the switches, which means it will deliver a very high peak current to them in the event of
A less obvious requirement for the semiconductor switch is that the impedance of the upstream power source not be so low as to make it impossible for the e-fuse’s switch to survive a hard short downstream.
An e-fuse proof of concept for high voltage 800 V automotive applications developed by Asahi Kasei Microdevices Corporation and Silicon Austria Labs GmbH.
a fault such as overlapping conduction of both switches in a bridge leg or a turn-to-turn short in the windings of the motor. e only good solution for protecting the switches which are directly fed by a voltage source is active current-limiting at the individual switch level (aka pulse-by-pulse current limiting). Another situation in which an e-fuse might fare poorly—especially in comparison to its conventional counterparts—is when subjected to a severe voltage spike, such as from a nearby indirect lightning strike. is is mainly because passive electrical (fuses) or electromechanical (circuit breakers) devices tend to be far more rugged than their electronic counterparts (e-fuses). In conclusion, e-fuses aren’t a panacea, and they won’t save you from bad design decisions and component choices in the power circuits they are supposed to protect, but they could reduce overall warranty and technical support costs, while possibly costing less up front, so they’re de nitely worth considering.
The dry electrode coating process has the potential to enable the production of better, greener, more cost-effective batteries. It relies on advanced fl uoropolymer binders with Tefl on™
By Charles Morris
For a few years now, Charged has been reporting on how dry electrode coating processes have the potential to revolutionize battery production by eliminating the use of hazardous, environmentally harmful solvents. Taking the solvents out of the process can translate to big savings in cost and oor space in the factory—and the dry coating process can also enable designers to improve battery performance.
e dry electrode coating process relies on the use of special binders that can form an electrode coating without being dissolved in a solvent, such as uoropolymer binders with Te on™ from specialty chemical company Chemours.
To learn about the advantages of the dry coating process, and how companies are meeting the challenges involved in scaling the technology up from pilot to production scale, Charged spoke with Tejas Upasani, Global EV Technology Manager at Chemours.
A Tejas Upasani: We like to call Chemours “a startup company with 200 years of history.” We spun out of DuPont in 2015, and we have leading brands in various industries, including semiconductors and automotive. Under our Advanced Performance Materials business, we have brands you might recognize, such as Te on™, Na on™ and Viton™.
Now we are experiencing growth in our products in a brand-new eld—the dry electrode coating process—and I’m really excited to see how Chemours can support the scale-up of this new application.
Q Charged: Can you walk us through the basic advantages of the dry electrode coating process versus the traditional wet slurry-based process?
A Tejas Upasani: e dry coating process is a novel way of manufacturing cathode and anode electrodes in lithium batteries.
In the traditional wet slurry process, we have the active ingredients, we have the conductive additives, and we use a particular binder which needs to be dissolved in a solvent. Once all these ingredients are mixed together, we create what is called a slurry. at slurry has to be coated onto a current collector. At that point, the func-
In the dry process, many of the ingredients remain the same—similar active materials, similar conductive additives. What really changes is the binder.
tion of the solvent is done, so we dry o the solvent and we get a nice coating on the current collector.
In the dry process, many of the ingredients remain the same—similar active materials, similar conductive additives. What really changes is the binder. In this case, we’ll be using advanced uoropolymer binders with Te on™ which, because of its unique properties, doesn’t need to be dissolved in any solvent. It can form the coating as it goes through the processing steps through a process called brillation, which basically forms the entire coating on the current collector.
Why is the dry process advantageous over the wet slurry process? We can look at this from three di erent angles. One is that it is much more environmentally friendly. e wet slurry process uses NMP [N-Methylpyrrolidone], which is a hazardous solvent. In order to get rid of
the solvent in the wet slurry process, it has to go through a series of ovens. If there is no need for the solvent, then the hazards associated with the solvent are removed.
e second part is production costs. If you look at how much space is required for the wet slurry process, by some estimates, it’s 10 times the space compared to the dry process, so there’s a tremendous amount of savings of oor space that can be achieved with the dry process.
e third aspect is that it enables better performance of the batteries. With the dry process, we can make
thicker electrodes, which can help with improving power density.
Advanced uoropolymer binders from Chemours are really at the heart and center of that process.
Q Charged: Is this something that could help to reduce charging times?
A Tejas Upasani: It potentially could. ere’s a lot of testing that is being done right now, comparing the wet
But as it stands right now, we are seeing the entire spectrum—lab, pilot, pre-production, production—of adoption of the dry electrode process.
slurry process and the dry process. If you are able to go to a higher loading with the dry electrode process—say, all the way to 8 or 9 milliamp-hours per square centimeter—we can see competitive or higher charging rates compared to a normal loading of the wet slurry process, which is about 3 to 4 milliamp-hours per square centimeter now. Much of this work is done at lab scale or pilot scale, but as the technology matures and we start seeing better process technologies, these can be realized in real-life scenarios as well.
Q Charged: Is dry electrode coating currently in production?
A Tejas Upasani: We are in the early stages of the development process. Some industry players are at production scale. For example, on Battery Day in 2020, Tesla announced that they wanted to produce their 4680 cells in a dry electrode process. And on Investor Day in 2023, the company announced that they had successfully implemented commercial production of the dry electrode process. PowerCo, a subsidiary of Volkswagen, has announced that they will deploy and commercialize the dry electrode process at many di erent locations. LG Energy Solutions has announced similar plans.
We think that cell manufacturers and OEMs in the next two to ve years are going to be in di erent stages. Some are going to be at pilot scale. Others are going to advance into production scale. But as it stands right now, we are seeing the entire spectrum—lab, pilot, pre-production, production—of adoption of the dry electrode process.
Q Charged: Are there any major technical hurdles that we still need to get past before this can be widely adopted?
A Tejas Upasani: Certainly there are hurdles. Everybody’s trying to develop the process, and they’re trying to make sure that the correct mixing and calendaring can be done in order to create a uniform structure. Some of the technical hurdles have to do with binders and the dry electrode processes enabled through understanding the bril network of PTFE [polytetra uoroethylene]. e use of PTFE and the resultant bril network has been understood for decades, and we, as inventors of PTFE, have invested a lot of science behind understanding the bril network, but it generally has been applied to industries where PTFE is the dominant component in the application. As an example, if you look at your standard plumber’s
On the cathode side, generally PTFE is oxidatively very stable...it’s a very promising application. On the anode side there might be reductive stability challenges associated with traditional PTFE, and so using traditional PTFEs might not be the optimum solution.
tape (Te on™ tape), it utilizes exactly the same principle of brillation. at’s why you can pull it in one direction easily, but in the transverse direction, you can just break it apart.
It’s the same in this application—we’re trying to control the brillation through the mixing process and through the calendaring process. Chemours has invested heavily in developing various types of advanced uoropolymer binders with PTFE. ese have a range of di erent molecular weights and di erent polymer architectures, and all of these are intended to enable the proper brillation characteristics within the electrode process.
Traditional PTFE may have challenges on the anode side. On the cathode side, generally PTFE is oxidatively very stable. One of the advantages is that you can go to higher voltages and it still is stable at higher-voltage applications. So, on the cathode side, it’s a very promising application.
On the anode side there might be reductive stability challenges associated with traditional PTFE, and so using traditional PTFEs might not be the optimum solution. at’s one of the reasons why we are developing a lot of di erent products and trying to understand the mechanism of why traditional PTFE is not stable on the anode side. And once we understand that mechanism, how do we solve that? ere’s a tremendous amount of work going on internally and with our external partners as well to try and understand and solve these hurdles.
Q Charged: One of the challenges is adhesion. e dry material has to bond to the electrode surface, but the at surface and lack of texture can make that di cult.
A Tejas Upasani: e industry right now is using what we call carbon-coated current collectors. ey have certain coatings on the current collectors, and when the dry process lms are made, those get laminated onto that carbon-coated current collector.
at’s the solution that the industry has at this point, and it’s working fairly well in both anode and cathode processes. Now, if we wanted to directly laminate the lm onto the current collector without any carbon coating, then that’s a little bit of a problem, and we are working on it right now.
We are looking at ways that we can alter the chemistry of the polymers themselves in order to get better adhesion to the current collectors. If we were able to directly laminate onto the current collector, why have this carbon coating? Eliminating the coating reduces the cost. I think that might come, but right now the focus is on scaling up the technology with coated current collectors.
Q Charged: e process needs to reduce the amount of binder and other inactive material to a similar level as that of wet coating, but this can be expensive and hard to scale up.
A Tejas Upasani: Yeah. Certain cell chemistries require increasing the amount of inactive material, especially on the cathode side, whereas there are some cell chemistries where we are looking at binder loadings of less than 2%, and in some cases even less than 1%.
So, it’s already being worked on, trying to reduce the amount of inactive materials. It does require a lot of process optimization because, as you can imagine, the small amount of binder is holding up the entire powder chemistry. So, a lot of process technology, along with the
We are looking at ways that we can alter the chemistry of the polymers themselves in order to get better adhesion to the current collectors. If we were able to directly laminate onto the current collector, why have this carbon coating?
material enhancements that we are doing in developing new materials and coming up with di erent polymer chemistries, is going to enable even further reductions of the amount of inactive materials.
Q Charged: Another challenge is uniformity—the dry coating mixture needs to be uniform across large areas of the battery electrodes.
A Tejas Upasani: I don’t think uniformity challenges are necessarily restricted to the dry coating process. ere are methods that have been developed in the wet slurry process to understand that the viscosity is right or the solids content is right, and that will help us to understand that the uniformity of the slurry is also good. In the dry process, it’s similar, except that we are dealing with all the powders. ere are analytical methods and tools that are being developed in order to verify that these powders are mixed correctly—the active materials, carbon black and binders, they need to be mixed really homogeneously. Once the mixing is done homogeneously, the beauty of the dry electrode process is that, once it is laminated onto the current collector, the coating process is done. You don’t have any movement or settling of the ingredients. In a wet slurry process, if you were to make a thick electrode, as the solvent is drying o , these ingredients may start to settle during the drying process.
Q Charged: So, your company would partner with the manufacturer to determine the ideal mix.
A Tejas Upasani: Yes. And throughout our history, we have looked at application development. is is what we have done at Chemours for decades. We don’t want to just say to the customers, “Here’s a material, use it.” We don’t want to say that we are just a supplier. We don’t want to stop there. We want to make sure that we contribute to the success of our customers as well. ere are methods available to understand the mixing homogeneity, which are very R&D-based, and we are doing some of that work, but if someone is doing this on a production basis at a manufacturing site, they are not going to have time to take a sample, go into the R&D lab and wait for days in order to get the results. So, when we
Once the mixing is done homogeneously, the beauty of the dry electrode process is that, once it is laminated onto the current collector, the coating process is done. You don’t have any movement or settling of the ingredients.
are developing these methods internally, we are trying to develop a method which is going to be in line with production characterization and analysis.
Q Charged: Can you tell us about your advanced uoropolymer binders with Te on PTFE?
A Tejas Upasani: Understanding the brillation characteristics is really the key in enabling the dry electrode process. We have a spectrum of di erent products, which are available to be applied in a batch mixing process, or in a continuous mixing process. Not all of our customers are going to use the exact same way of manufacturing it, so trying to tailor our products to their needs is the key.
And given that we have tried all di erent sorts of chemistries for our advanced uoropolymer binder products, it’s easier for us to understand what exactly is going to a ect the brillation characteristics, and consequently the mechanical properties of these materials.
Also, Chemours is the only uoropolymer manufacturer who has manufacturing sites in all three major regions—the US, Europe and Asia/Paci c. When we think about a scenario where the manufacturing is going to be scaled up to a production scale, we have the exibility of having the products being made at di erent locations and supporting our customers with the same quality, the same safety standards and same standards applied to responsible manufacturing.
Q Charged: We’ve heard about some proposed regulations in Europe around PFAS that could impact PTFE. What impact would this have on dry electrode coating?
A Tejas Upasani: I’m glad that you asked the question, because sometimes it is the elephant in the room when we are talking with our industry partners.
We at Chemours firmly believe that our fluoropolymers can be manufactured responsibly, and we are in favor of industry-wide national regulations and testing requirements, which are based on science and facts—data-driven regulations and testing methods, we are completely in favor of that.
We spend a lot of time, money and resources in identifying the sources of emissions from manufacturing uoropolymers, and installing abatement systems in order to control those emissions. We are also engaging heavily in trying to develop alternate manufacturing technologies. All of these are steps that we are taking in order to meet the needs of potential regulation.
If we look at the EU regulations, particularly, it’s not necessarily con ned to PTFE. PVDF, which is a uoropolymer used in the wet slurry process, could also be potentially impacted by the same regulations.
Fluoropolymers in general are essential to lithium-ion batteries, and they’re essential for us to transition to a clean energy environment. So, we want to be partners in the regulation to make sure that the regulations address the concerns, and that these products are manufactured in a responsible way, and we are committed to doing both things.
Global logistics rm DSV has ordered 300 electric semi-trucks from Volvo Trucks. e deal represents one of Volvo’s largest orders to date for heavy-duty electric trucks, but it’s just a toe in the water for DSV, which operates a eet of 20,000 trucks. ( e company’s order from Volvo also includes 500 legacy fossil fuel-powered trucks.)
DSV plans to take delivery of the trucks between Q4 of 2024 and the end of 2025, and will deploy them throughout its European operations. e company aims to eld 2,000 electric trucks by 2030.
“I’m very proud to deepen the partnership we have with DSV,” said Volvo Trucks President Roger Alm. “ is order is proof of their trust in our company, and shows that zero-exhaust emissions transport is a viable solution here and now.”
“As a global leader in logistics, we must try to stay at the forefront of the green transition, and this agreement is a fantastic example of how new technologies can be brought to market at scale to make them more accessible for our customers,” said Søren Schmidt, CEO of DSV Road.
DSV’s order will bring Volvo Trucks’ global sales of electric Class 8 trucks to around 4,000 units. e company boasts a 50% market share of electric trucks in Europe, and a 44% share of electric trucks in the US.
In response to the advent of cheap Chinese EVs, the US and EU have instituted various measures to favor domestically manufactured vehicles—including, most recently, steep new tari s. It remains to be seen what the longterm results of these policies will be, but the westward seepage of Chinese-made vehicles continues.
Leapmotor International, a 51/49 joint venture between Stellantis and Chinese automaker Leapmotor, shipped its rst batch of Leapmotor vehicles—C10 SUVs and T03 cars—from Shanghai to European ports this month.
e Leapmotor T03 is “a small ve-door, A-segment urban commuter car” that features 265 km of range (WLTP). e C10 is a ve-seat SUV that comes in both battery-electric vehicle and plug-in hybrid versions.
“ e shipment of Leapmotor C10 and T03 vehicles to Europe this month is a landmark moment in the partnership between Stellantis and Leapmotor,” said Stellantis CEO Carlos Tavares. “Relying on Stellantis’s strong business assets in Europe and the hard work of our companies’ teams on guaranteeing product innovation and quality, I strongly believe that Leapmotor’s electric vehicles will be widely accepted by European customers.”
“China is the biggest and most competitive EV market in the world, and our products have proved their value by being acclaimed by the local customers,” said Leapmotor founder and CEO Zhu Jiangming. “ e C10 and T03 models are designed to meet the high standards of global customers, and we are con dent that the collaboration between Stellantis and Leapmotor will drive signi cant growth for both companies.”
e Leapmotor International JV had 200 retail outlets in Europe at the end of 2024, and plans to increase that number to 500 by 2026. e company also plans to expand its reach to the Middle East, Africa, Asia/Paci c and South American regions in late 2024.
Universal Logistics, an intercontinental transportation and logistics rm that operates in the US, Mexico, Canada and Colombia, has added the Peterbilt Model 579EV truck to its eet in southern California, where it will be used for intermodal logistics.
Designed for regional-haul applications, the Peterbilt Model 579EV features a battery-electric system that the company says provides e cient operation and lower overall maintenance compared to legacy diesel trucks.
e 85-year-old company states that the 579EV “is ideal for regional haul and drayage applications, in part because the frequent starts and stops engage the regenerative braking.”
e Model 579EV’s day-cab con guration features a drive system that uses the energy stored in large packs of
lithium iron phosphate batteries. It went into production in 2021 along with two other all-electric motor lines, the Class 8 520EV low-cab COE and the Class 7 220EV COE (cab over engine).
In 2021, Peterbilt announced that the Model 579EV had become the rst electric Class 8 truck to reach the summit of Pikes Peak.
bdtronic is expert in dispensing 1K and 2K materials, plasma pre-treatment, the unique joining method heat staking as well as impregnation and powder coating processes for electric motors.
Saudi Arabian airline operator Saudia Group has signed a binding sales agreement to purchase 50 Lilium Jets from German electric aircra manufacturer Lilium, and has an option to purchase 50 more.
e sales agreement follows a memorandum of understanding the two companies signed in October 2022. e agreement includes a schedule of deposit and pre-delivery payments, a timeline of future deliveries, guarantees on aircra performance, and provisions on spare parts, maintenance and repairs. e companies also intend to sign a Lilium POWER ON agreement for aircra eet maintenance and support services.
e jets will provide rst- and last-leg connections into Saudia’s regional hubs and new point-to-point city connections, such as Jeddah to Makkah, which could reduce regional travel times by up to 90%. Saudia expects to receive the rst jets in 2026. ey will feature large, premium cabins with capacity for up to six passengers plus luggage.
Saudia will support Lilium in its certi cation process with the General Authority of Civil Aviation (GACA), Saudi Arabia’s aviation regulatory agency.
Lilium has a pipeline of 106 rm orders and reservations, 76 options, and roughly 600 aircra under MOU.
“ e Middle East is a priority for Lilium, and Saudi Arabia will be a very large and exciting market for electric, high-speed regional air mobility. Our partnership will combine Saudia Group’s signi cant market knowledge with our unique eVTOL technology to transform premium air travel in the GCC region,” said Klaus Roewe, CEO of Lilium.
CASE Construction Equipment has developed a production version of the 580EV electric backhoe loader. CASE’s next-generation EV o ers a zero-emission, lownoise solution suitable for work in urban centers or other environments where noise and emissions are an issue, while delivering other EV advantages such as instant torque, lower fuel costs and less maintenance.
e new CASE 580EV electric backhoe loader o ers the same dimensional loading and digging speci cations and delivers the same breakout forces as the company’s 4WD, 97 hp CASE 580SN diesel model. It also o ers new features, including an 8-inch color display, air conditioning, and adjustable four-corner, multicolored LED strobe lights.
Powered by a 400-volt, 71 kWh battery pack that’s charged with a standard Level 2 J1772 connector, the new electric backhoe loader is designed to deliver up to eight hours of operational run time on a single charge, depending on the application. e battery platform uses a thermal management system with system-speci c cooling circuits to help maintain performance in hot or cold conditions.
e four-wheel-drive 580EV uses two independent electric motors for the PowerDrive transmission and hydraulic pumps feeding the loader, backhoe and steering systems to minimize energy consumption and improve performance in loading applications.
CASE’s electric backhoe loader will soon be followed by the commercial availability of two additional EVs: the CX25EV 2.5-metric ton mini-excavator and the CL36EV 3.6-metric ton compact wheel loader. e new models will expand CASE’s EV lineup to ve models, including the previously launched CX15EV electric mini excavator and the SL22EV small articulated loader.
Monarch Tractor, creator of the MK-V electric tractor, has raised $133 million in a Series C funding round co-led by Astanor and the HH-CTBC Partnership, with additional support from At One Ventures, PMV and e Welvaartsfonds.
Monarch will use the new funds to further develop its AI product o ering and expand its operational footprint domestically and globally, while enabling its path to pro tability.
To date, Monarch has raised over $220 million, and has expanded into various agricultural markets such as vineyards, dairy, berries, orchards and land management across 12 states and 3 countries.
In 2022, Monarch released a fully electric, driver-optional smart tractor, the MK-V. Since then, customers have deployed over 400 MK-V tractors.
e cities of Athens and essaloniki in Greece have ordered 89 FUSO eCanter trucks from Portugal-headquartered truck maker FUSO, which is owned by Daimler Truck, for waste collection in their metropolitan areas.
Forty of the trucks are expected to be deployed in November, and the rest will be delivered over the course of 2025.
e trucks are con gured with bodies and rotating drum compaction technology from Greek refuse-collection equipment manufacturer Kaoussis. e li system is compatible with two-wheeled waste bins of 80- to 390-liter capacity, and features integrated diagnostic monitoring from specialized vehicle equipment manufacturer Terberg, which is based in the Netherlands. e 8.55-tonne vehicles have a battery capacity of 82.6 kWh and a range of up to 140 km.
“ anks to its compact dimensions and high chassis load-bearing capacity, the electric eCanter is ideally suited for waste disposal companies that operate in narrow streets,” said Florian Schulz, Head of Sales, Marketing and Customer Services at FUSO Europe.
In our car-obsessed society, providing parking is a major expense for business and property owners. e Delmanor Aurora retirement home near Toronto has found an innovative way to reduce the number of parking spaces it provides to residents, while still allowing them to drive as much as they need to.
In collaboration with EV rideshare technology company Kite Mobility, Delmanor Aurora, which is owned by condominium developer Tridel, provides EVs for the use of residents who volunteer to give up their personal vehicles (and the parking spaces they require).
Participating residents at Aurora have access to an electric Volvo XC40, free of charge, whenever they need to run an errand, or simply feel like taking a ride.
“Real estate developers are struggling with costs, and one of the largest CapEx items that they encounter is parking infrastructure—digging several layers down in the middle of a city or building new surface parking lots,” Kite Mobility CEO Scott MacWilliam told Forbes. “ e idea here is that Kite gives them the ability to reduce or remove parking infrastructure, so some of the CapEx savings there goes to fund these programs.”
At an estimated cost to developers of $100,000 per parking space in a structure, by eliminating an entire oor containing 300 to 400 spaces, a developer could save as much as $30 million to $40 million, according to MacWilliam. “ at would fund the Kite mobility hub and enough EVs (30 to 40) for those without cars, or that don’t want parking spaces.”
Ford’s commercial division, Ford Pro, is supplying its Smart Charging Bundle to businesses in California—one of the largest commercial eet markets in the US—under a new initiative to help make it easier for companies to add EVs to their eets.
e bundle o ers a complimentary Ford Pro Level 2 48 A charger or a Level 2 80 A charger for depot and workplace charging to businesses subscribed to Ford Pro Charging so ware.
e o ering is designed to help businesses improve their operations and reduce upfront and ongoing EV charging costs. e new automated demand-to-grid response function in Ford Pro’s Charging So ware reacts to grid events in California such as high local demand by automatically pausing charging, alerting the customer, and resuming charging when the event is over. is can help reduce the load on the power grid, reducing the risk of brownouts and blackouts.
Ford Pro will manage the enrollment process for customers in grid demand-response programs that manage grid capacity, energy programs, and emergency load programs as well as the Low Carbon Fuel Standard (LCFS) carbon credits program.
“California is an EV pioneer, and new regulations aim to accelerate businesses’ electric transition,” said Ted Cannis, Ford Pro CEO. “We’re here to do the heavy li ing and help companies navigate the complexities of electri cation, helping them be more productive and e cient as they add EVs to their eet.”
e South Pasadena Police Department has completely replaced its gasoline-powered vehicles with EVs. e city’s eet of 20 new Teslas will rely on a bank of 34 new EV chargers installed at South Pasadena City Hall. As part of the project, the City Hall, Police Station and Fire Station buildings will be backed up by a solar PV system with battery storage, adding power resilience in the event of an outage.
e transition is expected to save about $4,000 per year per vehicle on energy costs, and to provide additional savings on maintenance. Overall, the city expects the operational cost of EVs to be around half the per-mile cost of legacy vehicles.
Replacing gas-burning police and other public safety vehicles with EVs can deliver more emissions reductions than replacing other vehicles, a city spokesperson said. Police vehicles typically idle more than others when ocers make tra c stops or respond to emergency calls.
Enterprise Fleet Management assisted the city in acquiring 10 Tesla Model Ys for patrol vehicles and 10 Tesla Model 3s for detective and administrative duties.
e cars were up- tted for police use through Unplugged Performance’s UP.FIT division.
“We’ve had the pleasure of developing best-in-class next-generation police vehicles alongside the great team at South Pasadena Police Department,” said Unplugged Performance CEO Ben Sha er. “As a result, 20 turnkey UP.FIT Tesla Model Y Pursuit and UP.FIT Tesla Model
3 Administrative vehicles have been produced to replace the full eet of aging ICE vehicles.”
General Motors is merging its BrightDrop division, which designs and manufactures light electric commercial vehicles, into Chevrolet, in order to leverage the latter’s sales and service network.
BrightDrop was founded by GM in 2021. Chevrolet was founded 112 years ago in 1911.
e move is intended to provide commercial customers with greater convenience when it comes to eet maintenance and acquisition, by making the Chevrolet BrightDrop vehicles available through select Chevrolet dealerships.
e Chevrolet BrightDrop, formerly known as the BrightDrop Zevo, is an electric delivery van that was unveiled at the 2021 Consumer Electronics Show. e van is available in two models, namely the larger BrightDrop 600 (originally the Zevo 600) and the smaller BrightDrop 400 (formerly the Zevo 400).
“With the addition of BrightDrop to the Chevrolet lineup, we are combining advanced EV technology with the dependability and widespread accessibility that only Chevrolet can o er,” said Scott Bell, Vice President of the Chevrolet division. “ is move strengthens our EV o erings and rea rms our role as a leading commercial brand that enables businesses large and small to get work done.”
BrightDrop EVs o er a GM-estimated 272 miles (438 km) of city and highway driving and incorporate a variety of driver-assistance features including pedestrian detection, automatic emergency braking and a rearview camera. e vehicle features has parking assistance and may be locked, unlocked or started remotely.
An unusual feature built into every BrightDrop van is that the steering wheel and seat are equipped with haptic technology, which can alert the driver of potential hazards through vibration.
While the Zevo name will disappear, the BrightDrop name will continue under Chevrolet’s stewardship. GM builds BrightDrop EVs at a plant in Ingersoll, Ontario that’s capable of turning out 50,000 vehicles per year.
Airport ground support equipment (GSE) presents a perfect use case for EVs. e specialty vehicles that service aircra on the ground travel short distances, and can conveniently charge right on the airport apron.
Goldhofer, a German-headquartered global provider of specialty vehicles, unveiled an electric version of its AST-2 towbarless aircra tow tractor (aka Phoenix E) in 2019. Now EFM, which provides ground support at Munich Airport, has ordered 14 of Goldhofer’s Phoenix E battery-electric tow tractors.
is EV is a beast—it can wrestle aircra of up to 352 tons into position at towing speeds of up to 32 km/h. e Phoenix E boasts the same tractive power, maneuverability and reliability as the legacy diesel version, and o ers lower operating costs and longer maintenance cycles.
e Phoenix E features a 220 kW direct-drive motor and a modular 700 V lithium-ion battery system. Each module has a capacity of 40 kWh, and a vehicle can be equipped with up to six modules for a total capacity of 240 kWh. e Phoenix E supports CCS Type 1, CCS Type 2 and GB/T charging at rates of up to 22 kW AC or up to 150 kW DC.
EFM’s 14 Phoenix E tractors are expected to be delivered and in operation by 2028.
“ is latest investment in Goldhofer equipment is a further milestone for future-proof ground handling by EFM at Munich Airport,” says EFM Managing Director Jörg Abel. “As a pioneer in the eld of zero-emission ground support, our goal is to make ground support t for a sustainable future.”
e EU has joined the US in imposing substantial new tari s on EVs built in China. In June, the EU announced import tari s on Chinese EVs ranging from 17.4% to 38.1%. e rationale behind the new tari s is that the Chinese government has unfairly subsidized its auto industry, enabling Chinese automakers to sell EVs at prices European brands can’t match.
However, one important category of EVs—electric buses—appears to be exempt from the new tari s. As Mika Takahashi, Technology Analyst at IDTechEx, explained in a recent article, the European Commission, in a statement setting out the aims of the anti-subsidy investigation, de nes the product subject to the tari s as a battery-electric vehicle designed for the transport of 9 or fewer passengers. In other words, the EU will only investigate anti-subsidy claims for vehicles that carry 9 people or less.
Ironically, the market share of Chinese electric buses in Europe is far higher than that of Chinese electric cars. e European Commission estimates that Chinese electric cars made up 8% of the market in 2023. According to IDTechEx’s research, Chinese manufacturers accounted for 28% of the European electric bus market in 2023.
As Charged readers know, electric buses are on a roll. IDTechEx tells us that 2023 was the strongest year yet for e-buses in Europe—over 5,000 were sold in the EU and the UK. (However, this is a small fraction of the number sold in China).
Some European bus OEMs are selling their own EVs, but others are behind the curve. According to IDTechEx, some major OEMs did not bring electric buses into production until 2019. Considering the growing market, the comparative lack of domestic competition, and overcapacity at Chinese factories, Europe is a land of opportunity for Chinese electric bus brands.
Meanwhile, Chinese companies are gearing up to produce buses in Europe. BYD has established a factory in Hungary. Battery supplier CATL is also building a plant in Hungary, from which bus-maker Yutong plans to procure modules.
# L E V S 2 4
As it did in previous decades, Honda has used another maker’s car to enter a new US segment.
By John Voelcker
Honda is o en known as the world’s largest maker of internal combustion engines—more than 14 million of them a year. It sells those engines in a variety of containers, from home generators and lawn mowers to ATVs and automobiles. Over the years, the company has pioneered a number of advanced powertrain technologies, including both natural gas and hydrogen fuel cell vehicles.
None of those were battery-electric vehicles, however. at le Honda severely behind in the global race toward long-range electric vehicles that Tesla kicked o in 2012 with its Model S. Since then, in North America, Honda has sold two pure EVs in tiny numbers: the 20132014 Honda Fit EV (82 miles of EPA range) and the 20172019 Honda Clarity Electric midsize sedan (89 miles of range). Both were purely compliance cars.
Now, nally, Japan’s third-largest automaker (and perhaps that country’s most Americanized car brand) is selling a real EV. It’s the 2024 Honda Prologue, a
midsize crossover utility with roughly the footprint of Honda’s midsize two-row, gasoline-powered Passport. A spacious ve-seat utility vehicle, it’s EPA-rated at 273 to 296 miles of range.
Data since sales started in March suggests that the Prologue has done well for Honda—more than 5,400 were sold in August 2024 (the most recent month before this article closed). A Honda exec told Charged in February he was con dent they’d receive 40,000 Prologues from the factory in Ramos Arizpe, Mexico, during calendar 2024.
It’s worth noting that the Prologue presently carries heavy incentives, from the federal $7,500 pointof-purchase rebate to Honda’s own internal spi s. As Electrek recently said, “With up to $14,250 in incentives, the Honda Prologue can be even cheaper to lease than a Civic, despite costing nearly double.”
Honda did a deal with GM to develop its own electric SUV, the Prologue, on Blazer EV underpinnings.
e secret to this remarkable debut lies in a deal announced back in 2020 between Honda and General Motors. GM planned to roll out a variety of vehicles based on its Ultium architecture, from the luxury Cadillac Lyriq through the rock-climbing GMC Hummer EV to the mass-market compact Chevrolet Equinox EV. A core vehicle within those plans was the midsize Chevy Blazer EV—which shares structural dimensions and body hard points with the more upmarket Lyriq.
Honda did a deal with GM to develop its own electric SUV, the Prologue, on Blazer EV underpinnings. GM would build the car for Honda alongside the Chevy in its Ramos Arizpe plant. Honda would also develop an upmarket Acura ZDX crossover on the same platform—that one would be built by GM at the
While the battery sizes, body hard points, and other core characteristics remain common between the Blazer EV and Prologue, Honda made several revisions to give the Prologue more of a Honda feel.
Lyriq assembly plant in Spring Hill, Tennessee.
While the battery sizes, body hard points, and other core characteristics remain common between the Blazer EV and the Prologue, Honda made several revisions to give the Prologue more of a Honda feel. For one thing, it declined a rear-wheel-drive version, o ering the Prologue only with front- or all-wheel drive, to preserve the expected on-road behavior from a brand that has never sold a four-seat, rear-wheel-drive car in the US.
Another tweak was multiple re nements to the multilink suspension, front and rear, to give the Prologue more of a sporty feel on the road. Finally, the Prologue o ers both Android Auto and Apple CarPlay as standard. at compares to GM’s new EV lineup, which includes 8 years of free Google Maps navigation, but doesn’t mirror phones using either operating system. Instead, GM-branded Ultium EVs give buyers 3 years of App Access free—a er which that capability alone costs them $14.99 per month, for the ability to do what they used to do for free on their phones. How that will play out remains to be seen; clearly Honda didn’t want to run that risk.
In both a January media drive through California’s Napa Valley and an August week in upstate New York with a Prologue test car, we came away with the same impressions: Honda is selling a pleasant, large, spacious midsize EV crossover.
Powertrain specs for the Prologue are similar to those of its GM counterparts. All versions are powered by an 85 kWh battery pack under the cabin oor. In the all-wheeldrive version with two motors, Honda quotes power of up to 212 kW (288 hp) and 333 lb- of torque. e base frontwheel-drive model is rated at 155 kW (212 hp) and 236 lb- . at provides enough acceleration and cruising to keep up with almost any form of tra c a family is
A few peculiar aspects likely reflect the combination of fixed GM architecture underneath with Honda’s approach to controls and information layout. For instance, there’s no front trunk.
likely to encounter. Steering is somewhat vague, and the Prologue is a happier vehicle on wide, at suburban arteries than being tossed through curving, irregular canyon roads. Its one-pedal driving is exceptionally well-executed, with standard and strong levels available (also none at all). Drivers of other EV brands will notice that the Prologue accelerates more deliberately than the hair-trigger thrust of some other makes.
Honda said it tuned accelerator response and other characteristics to make the Prologue feel “more like a Honda,” but you won’t nd many similarities to the light, tossable Civic compact sedan in this SUV of 5,000 pounds or more. Here, the goal was interior space, comfort and battery range more than performance.
A few peculiar aspects likely re ect the combination of xed GM architecture underneath with Honda’s approach to controls and information layout. For instance, there’s no front trunk, which seems like a major lost opportunity in a lowish SUV with a long hood designed to mimic the proportions of an SUV with a big engine up front.
Honda laudably kept hard controls—knobs and buttons— for a majority of the vehicle functions. Its center console has large cupholders for big bottles or smaller co ee cups, lower storage, an upper tray, and space for your phone. But compared to the crisply executed cabin of a Civic, the materials—Honda surface styling over GM underpinnings—can seem a bit chaotic or un nished.
ree trim levels are o ered: a base EX, a midlevel Touring, and a top-of-the-line Elite. All share identical propulsion systems, whether front- or all-wheel drive (a $3,000 option on EX and Touring, standard on Elite). ey are di erentiated mostly by trim and appearance items and technology features.
Pricing starts at $48,795 for the EX in FWD form; the AWD EX at $51,795 may be the best value for many buy-
ers. A top-trim Prologue Elite—which adds niceties like perforated leather upholstery, heated and cooled front seats and heated wheel, 21-inch wheels, a head-up display, and even an AC outlet for rear passengers—comes in at just below the crucial $60,000 mark: $59,295. All prices include Honda’s mandatory $1,395 delivery fee. We expect the Prologue to nd takers fairly easily among its customers who are EV-curious but would never consider a domestic brand—and may have been underwhelmed by the Toyota bZ4X.
So how’s the Honda-GM partnership working out? e Honda Prologue and Acura ZDX are presentable,
We expect the Prologue to find takers fairly easily among its customers who are EV-curious but would never consider a domestic brand—and may have been underwhelmed by the Toyota bZ4X.
In October 2023 Honda canceled plans for a previously announced second GM partnership to develop less costly, more affordable EVs using next-gen technology.
competent and competitive. But that may not have been enough. A er 12 to 18 months of GM delay in getting its Ultium vehicles into series production—through an inability to scale up the automated assembly of battery modules using new equipment—in October 2023 Honda canceled plans for a previously-announced second GM partnership to develop less costly, more a ordable EVs using next-gen technology.
Just three months later, Honda announced that its rst vehicles on an internally developed Honda 0 Series platform will hit the market in 2026, earlier than previously expected. Prototypes shown include a sleek Saloon (aka sedan) and a more boxy Space-Hub van/SUV. e series was developed using three precepts, said Honda: thin, light and wise. In Asia and Europe, the company has had its subcompoact Honda e three-door hatchback on sale for a few years. But with likely US range under 200 miles and a smaller size than most Americans would consider, that vehicle was never intended for North America.
Meanwhile, the Prologue and ZDX will represent Honda in the mainstream sector for EVs in north America.
ey’ll likely run at least through 2028—with GM underpinnings, built by GM in its own factories.
Honda’s deal to jump into a new segment using another automaker’s products shouldn’t be all that surprising. Students of auto industry history will recall that Honda rebadged an Isuzu Trooper as the Acura SLX, while Honda in turn provided Isuzu with an early generation of the Odyssey minivan—which Isuzu relabeled an Oasis and sold for the 1996 through 1999 model years. e minivan didn’t help the smaller Japanese company, which exited passenger cars in 1993 and the US market altogether in January 2009. It seems safe to suggest GM probably won’t su er that fate.
Honda provided airfare, lodging and meals to enable Charged to bring you this rst-person report.
Australian DC fast charger manufacturer Tritium has been acquired by the Indian power management solutions company Exicom, which sells a range of AC and DC EV chargers in 15 countries.
e acquisition adds Tritium’s manufacturing facility in Tennessee and its engineering center in Brisbane, Australia to Exicom’s existing presence in Asia. “ e acquisition expands Exicom’s global reach and ampli es its commitment to research and development to drive innovation in this growing industry,” says Exicom.
“ is acquisition is in line with Exicom’s strategic vision to be a key contributor to the world of tomorrow by enabling an emission-free future for mobility,” said Exicom CEO Anant Nahata. “Exicom and Tritium have complementary sales and product footprints, and have each established leadership in their respective regions. We look forward to working with Tritium’s employees, customers, partners and other stakeholders to grow the business further and provide faster, more reliable charging experiences to EV users across the globe.”
Pioneer Power Solutions, a manufacturer, distributor and servicer of specialty electrical transmission, distribution and on-site power generation equipment, is collaborating with mobile charging provider SparkCharge to integrate Pioneer’s e-Boost mobile o -grid EV charger into SparkCharge’s mobile battery energy storage systems.
Pioneer has agreed to deliver up to 12 e-Boost rental units over the next 12 months, beginning in the fourth quarter of 2024. Pioneer will receive a per-kilowatt-hour usage fee in addition to a monthly rental fee. e two companies have also agreed to develop units that will combine Pioneer’s e-Boost platform with SparkCharge’s mobile battery technology for marketing as a chargingas-a-service o ering to selected large eet customers.
“Customers, especially eets, o en struggle with getting access to robust grid power in their EV transformation,” said Joshua Aviv, founder and CEO of SparkCharge. “A unifying charging hub can provide a single source for all vehicle types to charge without a major investment in proprietary platforms and costly infrastructure.”
e Biden-Harris Administration has awarded $521 million in grants to build out EV charging infrastructure across 29 states, two Federally Recognized Tribes and the District of Columbia (DC), including the deployment of more than 9,200 charging ports, the US Department of Energy has announced.
e grants are made possible through the Bipartisan Infrastructure Law’s $2.5-billion Charging and Fueling Infrastructure (CFI) Discretionary Grant Program and a 10% set-aside from the National Electric Vehicle Infrastructure (NEVI) Formula Program. ese programs have spurred private investments in charging infrastructure.
e nancing will be split into two categories: $321 million will be allocated to 41 projects that expand charging infrastructure within communities; and $200 million will go towards 10 fast-charging projects that will build out the national charging network along designated Alternative Fuel Corridors. is new infrastructure provides EV charging for light-, medium- and heavy-duty vehicles along designated highways, Interstates and major roadways.
e Federal Highway Administration (FHWA) received requests from 277 applicants for a combined $2.1 billion in project nancing. is funding round expands the total number of states with an awarded CFI project to 38, in addition to DC and Puerto Rico.
Since the start of the Administration, the number of publicly available EV chargers has doubled to over 192,000 ports, and around 1,000 new public chargers are being installed each week.
“As we build out the EV charging network on our highways, we are also investing in local communities, rural, urban and tribal alike. e grants are a critical part of ensuring every American can nd a charger as easily as a gas station, which will decrease pollution from our roadways, lower costs for families, and help people get to where they need to go e ciently,” said Polly Trottenberg, US Deputy Secretary of Transportation.
e city of Los Angeles has been making it easier for EV drivers to nd a charger by taking advantage of its streetlight poles. e necessary electric infrastructure is already in place, and the Los Angeles Bureau of Street Lighting has been tasked by the mayor’s o ce to install 10,000 EV chargers on the poles while replacing existing bulbs with energy-e cient ones.
e city has already installed over 750 chargers, and the Bureau of Street Lighting is now expanding the e ort with a project that will use technology from AmpUp, a charging so ware provider that specializes in shared charging networks, and EVSE, a provider of retractable-cable EV charging stations.
e Bureau of Street Lighting oversees a fairly complex lighting infrastructure that includes over 220,000 light poles. Because the switch to more energy-e cient LED bulbs reduces each street light’s demand for electricity, it frees up capacity for other uses, including EV charging. e new chargers bolt right into the existing street light infrastructure’s 240 V electrical service.
e chargers, AmpUp said, are installed 10 feet (3.05 m) above grade, reducing their exposure to vandalism, vehicular damage, tripping hazards and cable damage. Each charger’s 25-foot (7.6 m) cable descends upon activation and retracts when the driver unplugs it from the vehicle.
e streetlight pole-mounted EV chargers are an ideal solution for inner-city environments where space is at a premium, said Dean Spacht, Vice President of Sales and Marketing at EVSE. “Pole-mounted chargers make EV charging more accessible to a broader population, including those living in multi-unit dwellings or areas where traditional charging stations are scarce.”
e Los Angeles Cleantech Incubator, a business management organization that focuses on assisting startups involved in the eld of clean energy, and ChargeHelp, a maker of maintenance and repair dispatch technology for out-of-service EV charging stations, have created a multi-manufacturer reliability training hub for EV chargers.
e facility, which recently opened, is located in South Los Angeles on the Los Angeles Department of Water and Power’s La Kretz Innovation Campus. It will o er dozens of EV chargers and related equipment for electric vehicle support equipment (EVSE) charger reliability training. LADWP has supported the buildout of the hub with the installation of electrical upgrades needed to power the chargers.
“By launching the rst brand-agnostic training site in the nation in South Los Angeles, we are not only addressing the technical needs of the EV industry but also empowering local communities with valuable skills and job opportunities,” ChargeHelp CEO Kameale Terry said.
To create the facility, incubator management secured funding from the state of California with the assistance of Congresswoman Sydney Kamlager-Dove.
e training hub will operate for three years, during which it will o er training and teach technicians how to conduct non-electrical diagnostics and perform maintenance and non-electrical repairs to EV chargers. A LACI representative said that most charger repair work involves updating rmware or so ware or resetting the WiFi connection.
Quali ed training providers that need a training facility will be eligible to use the hub as well.
US-based Terbine has launched its Mission Control system for EV infrastructure to provide monitoring and management of complex, multi-vendor charging networks.
Combined with the company’s cloud-based Charging Network Management Platform (CNMP), Mission Control is designed to make operating and maintaining charging systems more straightforward by giving network operators automatic detection, diagnosis and remedies for eld problems.
Terbine Mission Control uses machine learning to predict when faults are likely to occur and issue alerts to system operators. It is linked with IBM’s Maximo asset and maintenance management platform to enable charging operators to issue trouble tickets, pre-order parts and dispatch service technicians.
Mission Control models the locations and types of individual chargers, along with onsite battery storage units, physical and cyber security monitors, plus the service records of all network components. It can integrate feeds from vehicles, weather stations, eet logistics systems and other elements of EV operations to create a comprehensive view of charging network health. Operators can zoom into a region and look at the real-time status of charging network elements.
“Getting EV charging up to enterprise standards requires a top-down, well-architected approach and sophisticated monitoring,” said David Knight, Terbine CEO. “Ensuring high uptime and dependability is critical to mainstream consumers and eet operators adopting electric vehicles, as it was with cellular networks and many other technological evolutions.”
Barcelona-headquartered EV charger manufacturer Wallbox Chargers has secured a $45-million investment from multiple investors.
Lead investor Generac Power Systems, a major manufacturer of home standby and backup generation systems, will use the investment to reinforce its ongoing partnership with Wallbox. Generac has over 8,000 authorized installers, and Wallbox chargers can be integrated with other Generac energy management systems.
Wallbox said the investment will strengthen its balance sheet and provide additional capital that will allow it to manufacture more chargers.
e latest investment, which is Generac’s second in Wallbox, “further accelerates our Powering a Smarter World enterprise strategy,” the Waukesha, Wisconsin company’s CEO, Aaron Jagdfeld, said. “Our strategic alliance provides Generac and our distribution partners deeper access to Wallbox’s technology and will enable deeper integration of Wallbox EV chargers into our residential and C&I energy ecosystem.”
In December 2024, Paolo Campinoti, a Generac Executive Vice President, was appointed to Wallbox’s board of directors.
New study finds fleet owners more satisfied with EVs than legacy ICE vehicles
A new report by Cox Automotive called e Future of Fleets: Path to EV Adoption found that, compared to ICE vehicles, EVs had higher scores among eet owners on key metrics such as “overall satisfaction,” “cost of ownership” and “vehicle usage and capabilities.”
Conducted in Q1 2024, the survey collected data from eet decision-makers in various regions of the US, across di ering eet sizes. Data shows that 14% of eets presently operate EVs, and that 87% of decision-makers expect to see EVs in their eets within the next ve years.
“ e EV is much larger than just the retail story,” said Zo Rahim, Senior Manager of Research and Market Intelligence at Cox Automotive. “In many ways, electric vehicles can be an ideal solution for eet operations, which o en have set routes of known distances, vehicles that routinely overnight in the same location, and operations that prioritize the cost of ownership.”
Cox’s research indicates that awareness of eet EV incentives is high among operators. Barriers to EV adoption in the eet business include high acquisition cost and inadequate charging infrastructure.
Lower maintenance costs are o en cited as a bene t of going electric. Surprisingly, Cox’s survey results indicate that EVs have a slightly higher frequency of service compared to ICE vehicles. Nonetheless, 48% of respondents said they are more satis ed with their EVs when it comes to service (27% said they are more satis ed with their ICEs, and 24% see no di erence).
e most regularly serviced items among EV eet owners are wear-and-tear items such as tires and brakes.
Among Cox’s respondents— eet operators who run both powertrain types—EVs have the highest “overall satisfaction” and “total costs of ownership” satisfaction scores. EVs also edged out ICEs in terms of “ability to complete the business purpose” and “vehicle usage and capability.”
“ ere are certainly challenges in shi ing a business away from traditional ICE powertrains, but if owners and operators are generally satis ed with the outcome and see tangible savings, EV adoption could certainly accelerate through the end of the decade,” said Rahim.
EV charging rm 3V Infrastructure has been formed in the US, with a mission to build and operate Level 2 EV chargers in long-dwell properties such as multifamily housing and hotels, reducing costs for real estate portfolio owners and managers.
e company has a funding commitment of up to $40 million from an a liate of Greenbacker Capital Management.
While there is a strong focus from private and public funding sources on building DC fast chargers at centralized public locations, mirroring a gas station model, most Level 2 chargers are currently located at single-family homes, limiting access for drivers living in multifamily properties, the company said.
3V is prioritizing work with real estate portfolio owners and managers that have portfolios of more than 20 sites, in order to deploy projects broadly and rapidly.
“3V Infrastructure is focused on an overlooked and underfunded asset class of EV infrastructure: Level 2 chargers at long-dwell properties,” said Aubrey Gunnels, the company’s co-founder and CEO. “Consumer behavior and market signals indicate that drivers want to charge their vehicles the way they charge their cell phones—when they’re at rest for extended periods of time.”
SAE International has published a new wireless charging standard for light-duty EVs. SAE Standard J2954, Wireless Power Transfer (WPT) for Light-Duty Plug-in/ Electric Vehicles and Alignment Methodology describes wireless power transfer at up to 11 kW with e ciency of up to 93 percent.
According to the SAE Wireless Power Taskforce, this new standard enables consistent alignment in an exact parking spot, using the Di erential Inductive Positioning System (DIPS). DIPS technology was tested extensively in the lab and eld with light-duty vehicles.
DIPS is a low-intensity magnetic eld generated from the ground assembly with multiple coils that can be evaluated by the vehicle assembly for positioning. Ground and Vehicle WPT assembly manufacturers can develop and test their systems according to this interoperability speci cation.
One feature of the DIPS system is that the vehicle assembly seamlessly recognizes multiple ground assemblies and pairs automatically. e system is designed to enable precise alignment in all weather conditions.
“With the great teamwork of the SAE Wireless Power Taskforce together with the DIPS Team, wireless charging with SAE J2954 Standard has become the rst standardized automatic charging technology,” said Dr. Mike Böttigheimer of MAHLE, a member of the SAE J2954 Taskforce. “ is step marks a signi cant breakthrough towards achieving scalability and mass production of wireless charging systems.”
“ e next models of light-duty EVs can reap the bene ts of automated wireless charging with alignment,” said Dr. Andreas Wendt, co-chair of the Dynamic Power Transfer subteam and Director of Electreon Germany.
“What is coming next is dynamic wireless power transfer, where DIPS could play a similar role in alignment. With this disruptive technology, electric vehicles could charge while in motion.”
e SAE WPT Taskforce is also specifying high-power wireless charging for heavy-duty vehicles at up to 500 kW for its upcoming recommended practice SAE J2954/2.
Fast charging provider EVgo has announced several signi cant enhancements to its network. e company is not only upgrading existing charging stations and adding new ones—it has undertaken several initiatives to improve reliability and customer service.
“EVgo’s new performance monitoring tool, so ware updates, and ongoing equipment replacement and upgrade e orts are just some of the ways we are future-proo ng our fast charging network,” said President Dennis Kish.
Since the start of 2022, EVgo has upgraded, replaced or decommissioned legacy equipment at more than 500 stalls across 20 states. e company plans to replace legacy equipment with the most advanced models, installing higher-power chargers where possible, at up to 150 additional EVgo owned stalls in 2024. e network has more than doubled the number of stalls served by 350 kW chargers over the last year.
Several initiatives are also underway to improve reliability and expedite repairs.
EVgo’s new Canary Model is “a powerful performance monitoring tool designed to automatically identify and analyze patterns and support diagnostics, augmenting EVgo’s maintenance responses with data from actual charging sessions.”
EVgo’s charger so ware now includes around-theclock cable signal monitoring. If a cable signal is lost for any reason, the company is automatically noti ed within seconds.
EVgo has upgraded charger antennae across its network, and says it was able to reduce internet connectivity downtime by almost half in the rst two quarters of this year.
EVgo says it has reduced the mean time to repair chargers by 67% since the rst quarter of 2023. e focus on reliability appears to be delivering results: EVgo says that, since January 2023, it has seen a significant reduction in the percentage of charging sessions requiring call center assistance, as more customers are successfully powering up on their rst try.
ENROUTE project uses data sharing to improve efficiency of heavy-duty EV charging
e E cient Network for Road-freight Optimisation, Utilisation and Transfer of Energy (ENROUTE) project of Innovate UK, a nondepartmental public body that serves as the UK’s innovation agency, is spearheading an initiative to enhance the operational e ciency of the charging of electric heavy goods vehicles (eHGVs).
Addressing the need for scalable and e cient transition to low-carbon freight operations, ENROUTE focuses on real-time data sharing to facilitate improved decision-making and eet e ciency.
e project consortium’s members are logistics company Welch’s Transport, transport technologies company Syselek, and the University of Cambridge. Its primary goals include mapping the existing landscape to identify data-sharing opportunities, building a business case outlining the economic and environmental bene ts of sharing data, and implementing a proof of concept to showcase the approach’s practical viability. e project employs anonymization techniques and security measures to ensure that all participant data remains secure and con dential.
“ rough the ENROUTE project, we are setting a new standard in logistics innovation,” said Chris Welch, Managing Director of Welch’s Transport. “Our commitment to integrating cutting-edge data-sharing technology not only enhances operational e ciencies but also signicantly advances our sustainability goals.”
Beam Global, the maker of an innovative solar-powered o -grid EV charging solution, has acquired Belgrade-based Telcom, which engineers and manufactures specialized power electronics, including inverters, charge controllers, power supplies and LED lighting.
e acquisition of Telcom will enable Beam to replace third-party power electronic components with in-house engineered and manufactured solutions.
Beam says its suite of products, which currently rely upon power electronics components provided by outside vendors, will be enhanced by the replacement of those components with proprietary, tailored solutions. Telcom, now Beam Europe’s power electronics team, will be tasked with creating bespoke solutions to replace third-party products, enabling Beam Global to create products with lower failure rates while reducing costs.
Beam Global also intends to support Telcom in growing its current legacy business. e companies believe that there are signi cant opportunities to cross-sell Beam’s energy storage and renewable energy products to Telcom’s existing client base.
“Beam Global’s unique suite of products have equally unique power electronics requirements,” said Beam CEO Desmond Wheatley. “Until now our talented engineering team has found ways to make o -the-shelf components perform tasks which they are capable of, but were not necessarily designed for, resulting in increased costs and complexities within our products. e acquisition of Telcom continues our strategy of vertical integration and market expansion which we started with AllCell batteries in 2022 and Amiga’s streetlight and other capabilities in 2023. I believe our products will become more powerful, more reliable and less expensive to make.”
When Tesla’s CEO red the company’s entire 500-person Supercharging team earlier this year, EV pundits predicted that most of these highly-skilled pros would soon be snapped up by other companies. In the event, some were rehired by Tesla, and others have moved on to greener pastures, including seven-year Tesla veteran Edward Noseworthy, who joined New York-based rideshare/ charging provider Revel in May.
More recently, Rebecca Tinucci, Tesla’s former Head of Charging, joined rideshare giant Uber, where she will lead the electri cation of the company’s ride-hailing eet.
Ms. Tinucci served in several leading roles in Tesla’s charging team over the last six years, and led the team for the last two. Tinucci’s team built a global DC fast charging network that is widely considered to be the gold standard for public charging. Tinucci oversaw the opening of Tesla’s formerly walled garden to non-Tesla EV drivers, negotiating deals with carmakers such as Rivian, Ford and GM.
In her new role as Uber’s Global Head of Sustainability, Tinucci will oversee the company’s transition to a zero-emissions platform, Bloomberg reports. Uber aims to make all of its rides and deliveries with zero-emission vehicles by 2040. In Q1 2024, Uber said 8.2% of rideshare miles in the US and Canada, and 9% in Europe, were driven in zero-emission vehicles.
Tinucci’s experience “will be an incredible asset to our team at Uber,” Andrew Macdonald, the exec in charge of the company’s ride-hailing business and Tinucci’s new boss, said in a message to employees.
“Electric vehicles, autonomy and robotics hold the potential to substantially reduce our collective emissions,” Tinucci said. “Uber is poised to be an accelerator in this transition.”
Paired Power’s EV chargers let customers mix and match solar, storage and grid power.
By Charles Morris
s eet operators know (or soon nd out), deploying EV charging infrastructure involves much more than buying some chargers and running some conduit. Obtaining adequate power at a site is o en a challenge, and it almost always takes a long time. At sites with limited or no grid power, plugging EV chargers into the grid may be impossible— but that doesn’t mean you can’t get your EVs charged.
AAt Charged, we’ve spoken with a lot of companies that are o ering solutions and/or workarounds for these problems—these usually involve some mix of onsite generation (almost always PV solar), battery bu ering or storage, and charging management. ese solutions go by the collective name of microgrids.
Microgrids o er other advantages: partially decoupling from the grid can help eet operators avoid expensive utility demand charges, ensure that they’re charging with mostly green energy, and o er a backup power source in case of a power outage.
Paired Power o ers a pair of microgrid-based products, each addressing a di erent market. PairTree is an o -grid EV charger featuring a pop-up solar canopy, a 42.4 kWh energy storage system, and one or two Level 2 5.3 kW EV chargers. It’s designed to be set up in just one day. PairFleet is a larger, scalable system that o ers battery capacity from 5 to 85 kWh and Level 2 charging at up to 15.3 kW. It can serve eets of just about any size, and can be set up in a few days.
To learn more about microgrid-based charging, Charged spoke with Paired Power CEO Tom McCalmont.
Q Charged: What’s the di erence between PairTree and PairFleet?
A Tom McCalmont: PairTree is the product we’ve been selling for about a year, which is a pop-up solar canopy that can be a fully o -grid power source, or can be grid-connected. It’s really a microgrid, and has a small footprint.
Our PairFleet scales that up to a much bigger system, so it can include more solar, more storage, more EV chargers, but it works on the same basic concept of a microgrid.
We think of it as an EV charger rst, but it’s not necessarily only an EV charger. Like any microgrid, it has the capability of being a power source, so you could use it, for example, for emergency power, or for V2B applications.
Solar trackers were common when solar was expensive, but now that solar panels are inexpensive, the maintenance for the motors that move the panels is not a good idea. We took a different approach, using bifacial panels to get similar energy yields.
Q Charged: We’ve spoken in the past with a couple of companies that do o -grid solar-powered EV chargers. Perhaps you’re familiar with Beam. What di erentiates your product from theirs?
A Tom McCalmont: Beam’s product is more comparable to our PairTree, but the di erences are many. One is that they have a tracker mechanism, and trackers su er from a
lot of disadvantages. They were common 15 years ago when solar was expensive, but now that solar panels are inexpensive, the maintenance for having motors that move the panels is not a particularly good idea—for a lot of systems that you see in the field, the motors are frozen in a certain position, either because they failed, or they haven’t been maintained and lubricated.
We took a different approach. We said, “Let’s try to get the energy yields that you can get from a tracker from bifacial panels.” Bifacial panels capture reflected light from the pavement, in addition to light on the top surface of the panels. No moving parts, no motors, no maintenance, but you get about the same energy yield, so our PairTree struc-
ture actually has a little more energy yield than Beam’s structure does, but without the maintenance burden.
The other thing that I think a lot of people miss is that off-grid works in some applications—places like parks and beaches where you don’t have any grid at all—but there are a lot more places where you have a little bit of grid power, for example a parking lot that has a lighting circuit. A lot of parking lots have been converted to LED lights, and during that conversion, the electricity draw on that circuit was decreased, because the LEDs use less current, so you have a little excess capacity in that circuit, and if you tie into that, now you can cover things like cloudy days or rainy days much better.
If you have a system that’s completely o -grid, you have a bunch of rainy days, and your battery gets depleted, well, now you can’t charge any cars. We think that’s a disadvantage to the o -grid approach that we’ve overcome— we like situations where we can tie into a little bit of grid.
e other thing we think is important is that you need control of the chargers, so you have control of the energy ows—from the sun, from the battery, from the grid, to the load. You have to manage all of that carefully, and you have to have intimate control of the charger to be able to do a good job of that. We can use third-party chargers, but we prefer to use our own, because it gives us tighter control of the energy ows.
We have a relationship with EV Connect, and with LITEON, so we can use standard commercial chargers in addition to our own. But there’s an advantage in terms of management. We’ve invested a lot in the so ware, too. We have a very comprehensive so ware stack for energy management, and that is really, in my view, critical to a successful microgrid. Our in-house developed so ware allows control of all the elements in the microgrid, so I can con gure it for control of solar, storage, the grid and the chargers—all four—and decide how I want to allocate that energy ow.
ere are di erent ways you might choose to charge a number of vehicles, depending on the available energy that you have in the system. One method is by priority: “I want to give the most current that I can give to the vehicles that are present.” Another is what we call shared power: “I want to share the available power I have equally across all the vehicles that are present.”
Customers can also do things like set their own priorities. Maybe certain classes of vehicles need more during the day. Maybe they’re used for emergency services, or you want to prioritize people who live in apartment buildings, because they don’t have access to home charging, versus people who do have access to home charging. Having an energy management system allows us to have that kind of exibility, that kind of control to work with the site host to deliver exactly the charging scenarios that their vehicle population requires.
Q Charged: Tell me about the chargers. You manufacture them?
A Tom McCalmont: We do. It’s our own design, and we make it here in the United States. When we started
the company, because I came out of the solar industry, in our early life our vision was around DC charging, and our rst product delivered direct DC charging from solar to the vehicle. We patented that, and we still sell that type of system today.
However, as you know, standards in the DC world are more problematic, which is one reason we’ve taken a little bit of a step back from that. ere are many DC interfaces: there’s CHAdeMO, there’s Tesla, there’s CCS, there are all these di erent DC variations, so trying to please everyone becomes harder. When we realized that, we developed our AC charger, and it couples nicely
We analyze a customer’s energy needs. How much do you need, and where are you going to get it? How much solar, how much grid, how much battery storage? All those capabilities are encompassed in PairFleet, our offering for large commercial customers.
with batteries. But we still have the DC technology. We did V2G way before anybody else, so we know there’s potential in making use of that at some point. As V2X capabilities become more available in vehicles, it’ll allow us to use that technology we’ve already developed.
Q Charged: Tell us more about your new product, PairFleet.
A Tom McCalmont: PairFleet takes the same basic system, the same components as PairTree, but allows the customer to scale that up to a much larger scenario. Typically, that larger solar array will be a traditional solar canopy, not a pop-up canopy, with solar panels on a steel rack, potentially more storage, and supporting many more vehicles. We call it PairFleet, but, for us, a eet is any collection of EVs that need simultaneous charging—for example, daytime workplace charging for employee vehicles is really a eet, as is a collection of service vehicles that are charged at night.
In our energy management system, we allow you to de ne your eet, so for example you can say, “I have 100 vehicles, 50 of them are Teslas, 30 of them are Chevy Volts, and 10 of them are E-Transit vans,” and you can de ne the di erent levels of range required by the di erent vehicle categories. How many miles do they drive in a day? What do they need in a day in terms of replenishment? What hours during the day will they be available to charge? We have a whole eet de nition component to our so ware.
en based on that, we can analyze a customer’s energy needs. What do you need in terms of energy, and where are you going to get that energy? How much solar do you need? Do you have an available grid connection? If so, what capacity is it? Is it 3-phase or single-phase? What voltage is available? How many amps? Is there a bene t to having some battery storage? For example, maybe you have a time-of-use rate schedule—power is cheaper at night, so you can charge the battery storage at night, and then deliver that energy in the daytime.
All of those capabilities are encompassed in PairFleet. We’re selling that to large commercial customers, who have a eet charging problem. e existing electric grid is not big enough to fully electrify transportation. As we electrify more and more transportation, there simply is not enough grid power to meet the need, and so microgrids that are augmented by solar are going to be crucial to meeting that demand.
Q Charged: With PairFleet, are there minimum and maximum numbers of vehicles?
A Tom McCalmont: With our design so ware, we can basically accommodate any size. We have a separate program we use for analysis. We call that Pairiscope, and we use it to analyze, “How many vehicles are you trying to charge? How many miles do you need? When do you need the miles? What are the miles per kilowatt-hour each vehicle requires?” en based on those inputs, “How much solar do I need, or have space for? How much battery do I need, or have? How much grid power do I need or have available?” We put all that together to build the solution.
Q Charged: So, when you have a potential customer, it sounds like you have to do a good bit of research and consultation before you make a proposal.
A Tom McCalmont: Yeah. We try to analyze their specific situation. We have all the components. We know we have solutions that are well-integrated, that will meet their needs, and they’re also very scalable, so we can design a solution that is perfect for them.
Q Charged: I’ve heard from a number of people that the problem is o en not so much not having enough power, but not having the right kind of power. For example, many DC chargers require 480-volt 3-phase
We recognize there’s a big market for [fast charging], but we think the more prevalent form of charging is going to be topping up wherever you might be—retail, workplace, school, home.
power, which isn’t available everywhere. But with your product, it sounds like that’s not much of an issue.
A Tom McCalmont: at’s right. We select the inverter or transformer combination to accommodate whatever grid power happens to be available—it could be 480 3-phase, 208 3-phase, 240 volt. Any of those, we can accommodate.
However, we’re not so focused on DC fast charging. We recognize there’s a big market for that, but we think the more prevalent form of charging is going to be daily range replenishment, just topping up wherever you might be—retail, workplace, school, home. If you look at the EV market, overall, much more charging is done in those kinds of facilities than is done at DC fast chargers.
Q Charged: What stage would you say Paired Power is at right now as a company?
A Tom McCalmont: I still think of us as a startup, but we’re a little bit older than many startup companies. e rst target market we addressed was workplace charging. Well, during the pandemic, nobody was at their workplace anymore, so that was when we developed PairTree— we said, “ is is a perfect opportunity to innovate and develop something completely new.”
en as that became nished, we realized, “We really have a microgrid here, let’s take this up to a much bigger level.” at’s what we’ve now done with PairFleet, because the problem of limited grid capacity and large numbers of vehicles that need charging is really becoming pronounced now. We’re still self-funded. e founders have funded the company to date, but we are considering raising an A round now to really scale, and take the company to a larger size and ramp up production to meet our order book.
Q Charged: What can you tell me about some of your existing customers?
A Tom McCalmont: ey fall broadly into a few di erent categories. Certainly, agriculture is one, and PairTree has had a lot of interest in di erent agricultural applications. e grid connection is typically horrible on a farm. Most farms are at the end of a distribution line, so having a solution that’s either o -grid or microgrid can make use of the existing grid capacity that’s available there. We’ve seen interest at wineries. We have a system at Gallo Farms that’s used for their cheese factory operation.
We have several systems for large commercial customers. A lot of those were built a few years ago using our rst product, direct solar to vehicle, so these are big commercial companies—Intuit, for example. Some of those customers are now considering upgrading to our PairFleet solution. Some of these commercial campuses have maybe 3,000 employees, with as many as 1,000 of them driving EVs now, and so they’re trying to gure out, “How do I get enough infrastructure in place to help support my employees, and support cleaner commutes?” It’s di cult to do that with grid power alone.
We have done some data centers. Data centers use so much energy, they want something that’s solar-augmented, so they can provide EV charging without having any impact on their load.
We’re talking to cities. We actually have a bunch of PairTrees being installed this summer. e city of Davis, California is putting two in. We just sold a system in South Carolina to a commercial product company. We have a system running for the Delaware National Guard—that’s a military installation. ere are several other cities pending as well. Our home city of Campbell has purchased one, and that’ll be installed in a few weeks. We have a local university that’s bought some PairTrees that’ll be installed this summer. ey’re using those to charge service vehicles, like golf carts for campus use, rather than cars.
Grid expansion cannot keep pace with EV growth today. That’s not our problem.
Meet PairFleet–An advanced microgrid EV charging system.
Work within your grid capacity. Get more power with our solution. Learn more today.
By Charles Morris
For the last few years, the EV industry has been agonizing over the problem of providing charging for urban drivers who depend on on-street parking, and have no possibility of installing chargers at their homes. EV journalists, including your favorite, have spilled much virtual ink over what once seemed an intractable issue that threatened to hobble the EV transition.
Nowadays however, a visit to some of the world’s most electri ed cities makes the solution plain: lots and lots of curbside public chargers. In Europe, Oslo, Amsterdam and London t this description, as do several Chinese cities. e US is just starting to catch on to the potential of curbside charging, and this presents opportunities for North American operators to learn from what is and isn’t working in Europe.
e eld of public EV charging is divided into several categories—curbside charging is not the same as destination charging, workplace charging or highway fast charging. Successfully deploying curbside charging requires creative ways of thinking about the hardware, the business model, and the supply of electrical power, as Nathan King, co-founder and CEO of curbside pioneer itselectric, explained to Charged
Q Charged: I’m keen on curbside at the moment, because I just got back from London, where I saw lots of EVs, and lots of curbside chargers. Your company focuses on curbside charging, and you approach things di erently from the typical charge point operator. For one thing, you use a behind-the-meter power connection for your chargers.
Nathan King: at’s de nitely one of the things we are doing di erently. I would say most of the companies that are operating as curbside charging networks are based on a direct-to-utility connection.
Also, in North America, we haven’t really seen a network operator come to the curbside charging space. Where you do see curbside charging in North America, it’s based on an OEM model where the companies are selling the chargers to a utility or to a municipality, which then owns and operates them. What we’re trying to do is to bring the network operator model to the US, but skip some of the permitting di culty that you encounter when you’re trying to connect directly to a utility main.
In North America, we haven’t really seen a network operator come to the curbside charging space. The Level 2 charging industry really is based on an OEM model.
Q Charged: So the ChargePoints and the EVgos of the world aren’t doing curbside charging?
Nathan King: Well, you will occasionally see a ChargePoint charger in the roadway. ere’s actually a handful in the District of Columbia. But in that case, DC is procuring the chargers and installing them. New York City also has some chargers on the curbside. ose were made by a Canadian company called Flo, which sold the chargers to the city for them to operate.
e Level 2 charging industry in North America really is based on an OEM model. Companies like ChargePoint and Blink build the chargers, and try to get them procured by cities. en the cities or the utilities have to gure out how to own and operate those chargers. We take the logistics of doing the installations and operation away from cities and utilities, and we earn revenue from the chargers ourselves. So, we’re not actually selling chargers, we’re installing and operating them.
is is how it’s being done in the EU and the UK. We’re trying to bring this owner/operator model to the US, and
curbside is an area where that model is possible because there’s really high utilization potential. If you put a charger in, for example, a supermarket parking lot, you won’t expect 24/7 use of that charger because people are doing opportunity charging. Maybe they’re plugged in for one or two hours while shopping. For a Level 2 charger, that’s not a ton of power that’s being transferred over those couple of hours. But when you put a charger on the curbside, that charger can be used by people who live in that neighborhood and park their cars on the street overnight every day. So now you have 24/7 availability to hundreds or thousands of vehicles that park within walking distance of that charger, and you see high utilization.
Q Charged: It may be a subtle distinction, but how would you de ne the di erence between curbside charging and plain old public charging?
Our chargers are installed on publicly owned property.
Property owners earn revenue from providing EV charging to their community, but they don’t have to worry about managing the parking spots.
Nathan King: e other term we sometimes use is rightof-way charging. e distinction is that our chargers in all cases are going to be installed on publicly owned property. ink about somebody’s sidewalk in front of their building. e city owns and manages the rights to that sidewalk and the parking spot that’s next to the sidewalk. However, property owners have certain rights and responsibilities for that frontage. You’ve got to shovel the snow in the winter, and you’ve got to pick up your trash. On the other hand, property owners can take advantage of their sidewalk frontage in various ways. In some cases, commercial properties install their own lighting. Here in the Northeast, people sometimes install electric snow melting systems underneath their sidewalks. Because you have that frontage, you can make improvements to it that are permitted by the city.
So, there’s a bit of a gray area when it comes to property owners’ relationship to their sidewalks, and that lets us take out a permit from the city on behalf of the property owner to install an EV charger. We always have to have permission from the city to operate. But we’re also working with the property owner for them to supply the power.
e other thing that’s interesting about this right-of-way charging model is that the parking space itself is managed by the city. One of the issues that we see in places like apartments, condos, workplace charging, is that the property owner becomes responsible for enforcing EV charging at that spot. For example, if you’re a supermarket and an ICE vehicle parks in front of that charger, do you tow the vehicle? Or do you just let it sit there and annoy your EV driver customers? ere are other things as well, like determining pricing structure and overstay fees, that can add operational complexity for a private property owner. What we’re unlocking is a model where property owners are able to earn a little bit of revenue from providing EV charging to their community, but they don’t have to worry about managing the parking spots, since those parking spots are managed and maintained by the city. Our chargers are installed on publicly owned property. Property owners earn revenue from providing EV charging to their community, but they don’t have to worry about managing the parking spots.
Q Charged: You o er a turnkey service. You procure the hardware, do the installation, and handle billing and maintenance. Do you do that in-house, or do you contract with other companies?
Nathan King: We’re a fairly lean team in terms of our operations, and a lot of what we do is subcontracted out. Even larger companies like Tesla or Electrify America, they may have some electricians on sta , but by and large, the design and installation work is being done by subcontractors. We’re doing the same thing.
Q Charged: Tell me about the charging station itself. Does somebody build those for you to your speci cations?
Nathan King: at’s right. We saw the need to have a dedicated curbside charging hardware in North America. In the
EU, curbside charging is based on a bring-your-own-cable or a detachable cable model. We don’t have that in the US. Generally speaking, when you encounter a charger, it’s going to have a cable attached to it. e untethered cable makes a lot of sense for curbside for a couple of di erent reasons, and that’s why we invested in our own design. You can’t go and buy an untethered cable that works in the US right now.
Q Charged: I’m surprised. Is there really not a single company that sells those in the US?
Nathan King: We were surprised too. And right now, we are rst and only. I’ll tick through the advantages. e rst is that it presents a smaller, cleaner, compact design. We won an RFP in Boston, and part of the reason that we won is because of the design of the charger. Boston has very narrow streets. ere’s not a lot of room on the sidewalk. Finding a piece of hardware that ts within the urban landscape and doesn’t take up too much space, that’s a very important consideration. e detachable cable allows you to do that. Once you add a cable, you then have to gure out how to manage it. What you might see in a parking garage is a little hook where you expect drivers to loop the charger, or a little receptacle for drivers to plug it back in. Sometimes people just mic drop the charger and it gets le on the ground. On curbside installations, you see cable management systems that keep the cable li ed up o the ground. is adds bulk and complexity, and it doesn’t always work.
e other thing is the repair and replacement of the cable. On the West Coast, we see a lot of issues with copper the . People think that there’s a lot of copper and that it’s easy to get out of these cords. And it’s actually really hard to replace those cables once they’re cut from the charger. You may have to recommission the charger. You can’t just replace the cable. You’ve got to do a series of tests to make sure the cable’s functioning properly. It’s expensive, and there’s also downtime while you’re waiting for the charger to be prepared. With our system, the drivers keep their cables with them, so there’s less opportunity for people to vandalize the cable. en if it does happen, we’re not rolling a truck, we’re not waiting for replacement parts to arrive—we just send that driver another cable.
e third advantage is our exibility in charging standards. Everything is shi ing over to the J3400 (NACS) standard, but we still have around a million cars with the J1772 charging inlet, including cars that are being sold this
year. We give the driver the charging cable that ts their charging inlet. Drivers don’t need an adapter, and we don’t need to worry about coming back to these chargers in two or three years and replacing them with an NACS connector. We’re future-proofed on this charging standard.
Q Charged: What kind of plug is it where your cable plugs into the charger?
Nathan King: e port on the charging post itself is a universal non-proprietary standard—it’s a J3068, the same standard that’s being used in the EU and the UK. We will be interoperable with the existing technology that’s currently functioning in the US, and we expect if anybody else develops a detachable cable charger in North America, then they’ll also use J3068. Just to make it clear, when you get a charging cable from itselectric, it’ll also work with other detachable-cable chargers.
Q Charged: Who makes the chargers for you?
Nathan King: It’s a company called Gyre9, based in Connecticut. ey have their own line of EV chargers that they manufacture and sell. ey also do prototyping and product development, so they were really a great partner for us. We didn’t see any charger in the North American market that o ered the right design to scale this up, so we designed our own charger. It’s completely Build America/ Buy America-compliant.
Q Charged: Another innovative thing you’re doing is sidestepping some of the hassle of dealing with utilities by submetering. Can you really do an end run around the utility like that?
Nathan King: e short answer is: typically, yes. Every utility has di erent arrangements for how they manage what they call a franchise. A utility has special permission to build underground lines and have them powered. Now, when we go into a new municipality, one of the rst things we do as due diligence is to validate our plans with the utilities we’re working with. It’s a dialogue and it’s a process, but generally speaking, wherever we currently have deployment plans, we’ve spoken with the utility and gotten their buy-in for what we’re trying to do. ere are di erent ways that we’re going to do it. In some
Even with fairly low utilization, it’s anywhere from $800 to $1,000 a year that the property owner is receiving in passive income.
cases, we may work with the utility to get a dedicated meter with our own account. We’re just putting a new meter next to the existing meter that goes to the house or the commercial property. We have a lot of homeowners right now that we’re talking to, but we’re also working with commercial properties, multifamily buildings. We’d love to further expand into institutional property owners like schools and universities. So, sometimes we will have a meter that is dedicated for the single charger, or maybe two chargers that we’re attaching to it. And sometimes we’ll just nd spare capacity on the existing house panel and tap into that, and we work out a way to reimburse the property owner for the power we pull. As part of our hardware package, we have a revenue-grade submeter, as any publicly accessible Level 2 charger has, that tracks the power that we’re pulling. We always know how much power is going through our charger, and then we can reimburse the property owner for their utility bill.
Sometimes one way has advantages over another, but in all cases, we’re handling the installation, the permits, and once the charger goes live, we track the power that we’re using, reimburse the property owner and also share some of the revenue. And even with fairly low utilization, it’s anywhere from $800 to $1,000 a year that the property owner is receiving in passive income.
Q Charged: Can you tell me how the revenue breaks down?
Nathan King: Probably about half the revenue will go back to the utility. e price for drivers depends on the city. For example, in Boston, the cost per kilowatt-hour is quite high, so that’ll be re ected in the price we’re expecting drivers to pay. In the Midwest and Detroit, the cost per kWh is much lower. When we think about our pricing model, we set a couple of benchmarks for ourselves. We always want to have
a per-kilowatt-hour price that’s competitive compared to DC fast charging, and a cost per mile below the price of gas. e cost to install a Level 2 charger on a curbside is orders of magnitude less than installing a DC fast charger, so we don’t have that same capital investment that the DC fast charging companies have. Power is also less expensive because we’re not faced with demand charges.
Q Charged: Give me a quick history of the company.
Nathan King: We’re about three years old. My background is in what we call technical architecture— guring out how to work with contractors, how to get permits from the city, how to get power connected to your buildings—which
I enjoyed in some weird way. e city of New York was actually my client on two di erent projects.
During the pandemic, my family decided we needed a car. We live in Brooklyn, and we don’t have a driveway, so our car would be parked on the street, but there was nowhere for me to conveniently charge it.
at was true three years ago. It’s still true today. e closest place for me to charge was a private parking garage a mile away, and I would’ve had to pay for the parking, and the charging on top of that. It’s very expensive. So, we bought a gas car. And throughout 2020 I was thinking about this as a problem. ere’s about 40 million vehicles in the US that park on city streets. If we are going to make this EV transition happen, how are we going to deal with this part of the market?
e aha moment was looking out my window and thinking, Why couldn’t I just toss a cord out, connect it to my building and plug my car in? en I thought, what if I could make money from other drivers paying me for charging? e thing that I had going for me was all this experience in permitting things with cities, dealing with contractors, and three years later, here I am.
Q Charged: How many charging sites do you have up and running at the moment?
Nathan King: We have three in Brooklyn and four in Detroit. We are looking to install another up to 200 chargers in seven cities over the next 12 months. Our recent fundraising is supporting that activity. We have a couple of other smaller cities that we are looking to deploy in, but in terms of major metropolitan areas, it’s Boston, Alexandria, Detroit, Jersey City and Los Angeles. We’re also looking at a pilot opportunity in San Francisco.
Q Charged: It sounds like you’re on the verge of moving from the pilot stage into the scale-up phase.
Nathan King: Yeah. Earlier this year we announced that we had secured UL certi cations for the charger. at’s a very important step in providing public charging. And between the RFPs that we’ve won and the grant money that we’re getting, our investment is really allowing us to build up our team and start to get these chargers in the ground.
Q Charged: One more question, which I ask everybody. Why is the reliability of public chargers so abysmal?
Nathan King: Yeah, how do I not give you a 25-minute dissertation on this? I can call out design, but I think I’ve already talked about that enough, so I’ll call out the business model. Public Level 2 charging in the US is mostly a model in which property owners buy chargers from charger manufacturers and operate them themselves. But I think the right model for Level 2 charging is for the company that makes the charger to be the company that owns and operates it.
You’re then incentivized to design a charger that’s built to last, because your revenue is not based on making the sale. It’s based on earning continuous revenue—and that revenue goes down as soon as that charger stops working. Cities and utilities are experimenting with curbside charging, but ultimately they don’t want to be managing networks of thousands of EV chargers. It’s not what they do. Somehow we need to create accountability for the company that builds the charger to make sure that that charger stays up and running.
By Charles Morris
hen I started writing about EVs a decade ago, I was enamored of e Vehicles (especially the supermodern, super-fast kind), and tended to think of e Infrastructure as boring—and so it is, for us suburban driveway owners, who simply plug in our EVs when we return home, and forget about them until we unplug and get back in the driver’s seat. But as EVs have proliferated, we’ve come to understand that there are di erent charging scenarios that need to be served in di erent ways. Observing startup companies emerge to address the di erent market opportunities is anything but boring.
e di erences among the various avors of charging don’t have so much to do with the charging stations themselves, although there are some slightly di erent requirements. No, it’s the use cases, and the corresponding business models, that o er so much variety, and the fascinating part is that the industry is still guring these out.
We have learned a couple of important lessons. For one, EV chargers are not simply a replacement for gas pumps— we all sco ed at the self-appointed expert who opined that all the world’s gas stations would need to be replaced by fast chargers. For another, site selection is critical—underutilized public chargers, installed early in the transition, litter the landscape, and more than a few have already been ripped and replaced (or not replaced).
Installing the right charger for the right job, and monitoring and maintaining it, are the keys to delivering a good experience to users—and hopefully some pro t to owners. Here are some common use cases, with suggestions for best practices.
• Highway fast chargers. ese need to be covered and well-lighted, with rest rooms and restaurants nearby, they need to support Plug & Charge, and most important, they need to work. Battery storage and/or on-site solar can help avoid demand charges.
• Urban charging hubs. I’m skeptical about these—they may have a role to play, but consumers aren’t going to wait around to charge on a regular basis. Curbside charging is a better solution for cities.
• Home charger. Keep it simple, keep it cheap, and avoid expensive panel upgrades (there are several ways).
• Workplace charging. e chargers themselves can be simple, but you’ll need a charge management system to balance loads and keep track of usage. In some cases, Level 1 may work just as well as Level 2, and allow more chargers to be installed.
• Public destination charger. Suitable for hotels, airports, parking garages and other long-dwell locations. As above, Level 1 may be an option. At hotels and other businesses, sta need to be trained to help customers and deal with ICE-holers.
• Public opportunity charger. Suitable for shopping centers, dining districts, etc. Good site selection and ease of use are the keys to success. ese recoup their costs by attracting EV drivers to businesses (and, some hope, from on-screen ads). Drivers won’t pay for this kind of charging, and if they have to download proprietary apps, fool with logins and passwords, etc, they won’t use them at all.
• Curbside charger. ese serve urban dwellers who rely on on-street parking. ey need to be compact and simple, with a detachable cable. In some cases they can utilize existing power sources (e.g. streetlamps). See our article on itselectric, page 72.
• Semi-portable on/o -grid charger. Obviously suitable for o -grid locations (parks) or temporary applications (events, disaster relief), but also worth looking into for any location where fast setup and/or minimal grid usage is a priority. Beam Global and Paired Power (page 64) target these markets.
• Mobile emergency charger. Contrary to popular belief, EV drivers do not constantly run out of charge, but it does happen. ese are mounted on trucks, AAA-style.
• Mobile concierge charger. Skeptical about these. Rolling a truck to charge someone’s EV in a garage is going to be expensive, but some high-powered, highly-paid exec types may be happy to pay.
A eet might use DC fast chargers, Level 2 chargers, or a combination of both—it all depends on the use case, and there are many. Fleet charging tends to be divided into depot charging (long-dwell) and en route (fast top-up) charging. A eet infrastructure strategy is likely to include battery storage and on-site generation, and it may include cutting-edge technologies such as wireless (handy for some transit use cases) and/or V2G (a possible revenue source for school bus eets).
In any case, your rst step should be bringing in expert help. A lot of eets have spent a lot of money before guring this out. A common mistake is overestimating the power you’ll need, and getting bogged down in trying to get utility interconnects hooked up. A good eet charging provider will analyze your needs, install appropriate hardware, and deploy a comprehensive energy management system. (You’ll nd several companies pro led in previous issues of Charged.)
We shift into higher gear for your success: our innovative cables, wires and adhesive tapes stand for a safe future of electromobility. Discover our products:
Coroplast Tape
• Thermal Management
• Avoiding of Thermal Propagation
• Sealing and Insulation
Coroflex
• HV Cables with outstanding sealing properties
• Free of PCB and talcum
• Actively coolable HV Cables for smaller diameters with highest performance