RESERVOIR LOGS
PLENTY OF ACTION IN STORAGE TERMINAL CONSTRUCTION
TANK CONTAINER FLEET STILL GROWING ALMOST THERE WITH RID/ADR/ADN 2025
PHMSA PLAYS CATCH-UP
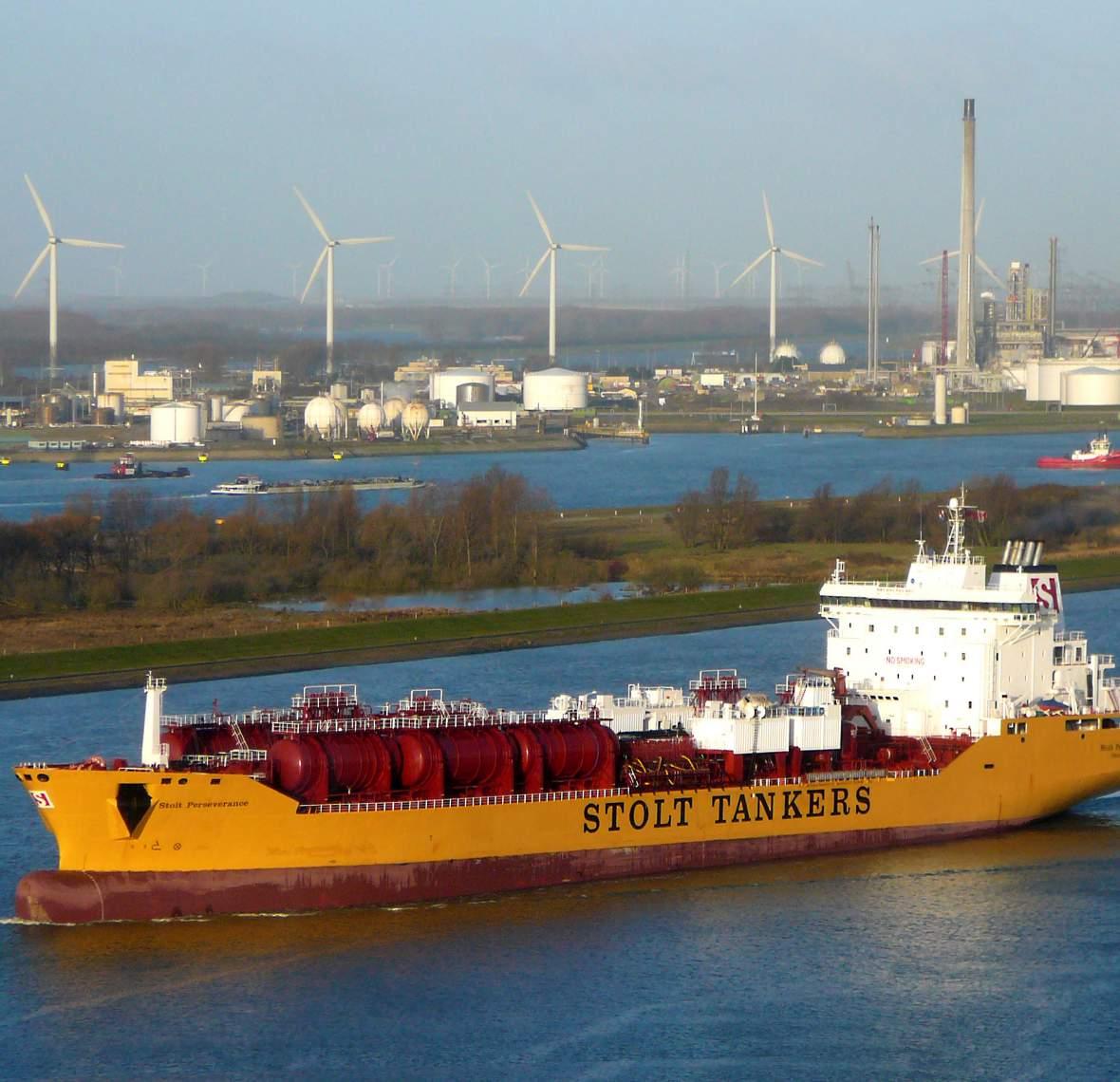
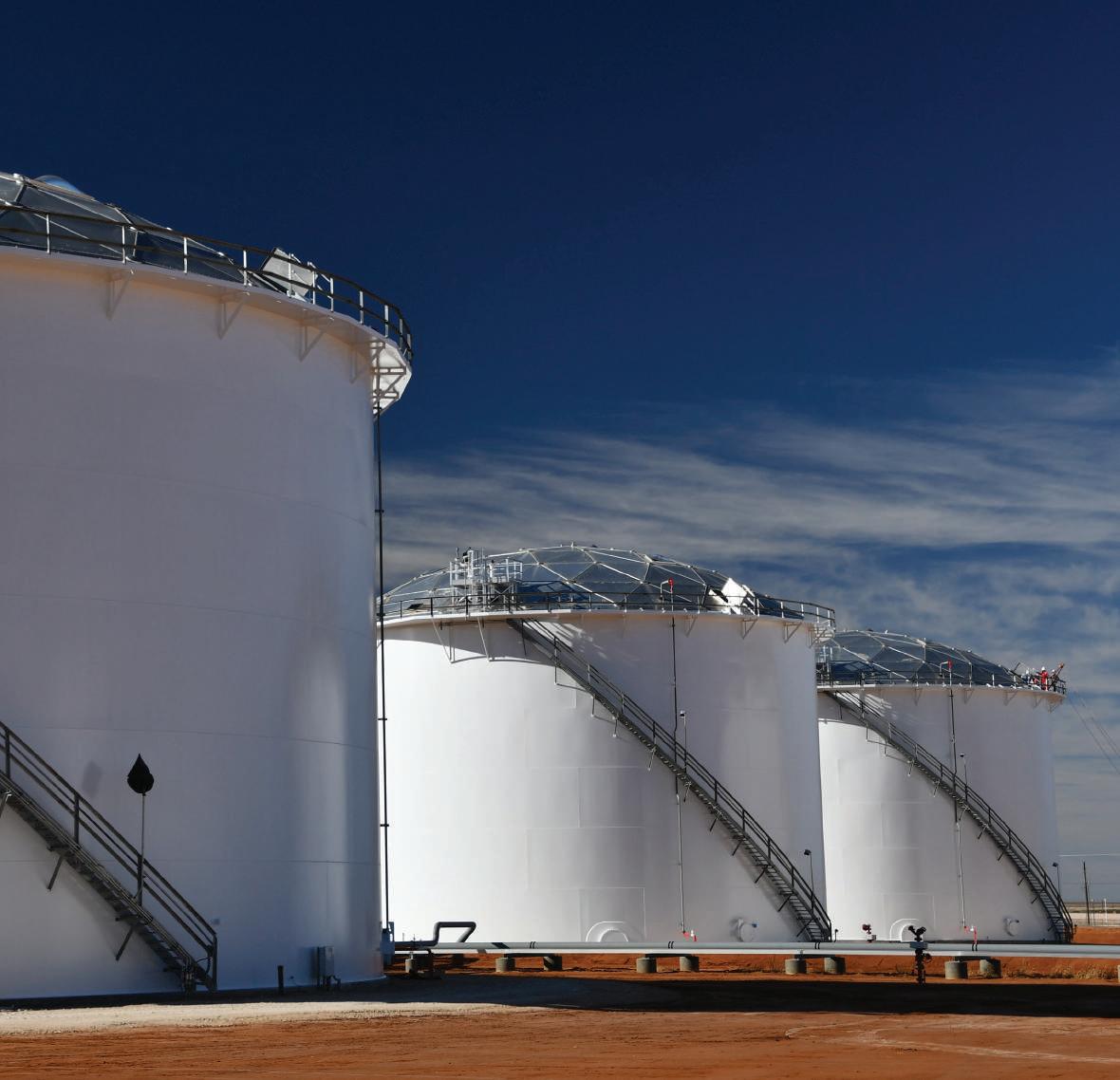
PLENTY OF ACTION IN STORAGE TERMINAL CONSTRUCTION
TANK CONTAINER FLEET STILL GROWING ALMOST THERE WITH RID/ADR/ADN 2025
PHMSA PLAYS CATCH-UP
.
With full visibility of regulatory requirements across 279 jurisdictions.
Regulatory Database gives your team a single, standardised source of information, helping them to:
• Get a comprehensive view of what the regulation says now and how it’s changing
• Reduce risk by eliminating knowledge gaps and out-of-date information
• Save time and resources by dramatically reducing the need for desk research
Joint
GES,
Evos, Cepsa to move sunshine
Managing Editor
Peter Mackay, dgsa
Email: peter.mackay@chemicalwatch.com
Tel: +44 (0) 7769 685 085
Advertising sales
Sarah Smith
Email: sarah.smith@chemicalwatch.com
Tel: +44 (0) 203 603 2113
Publishing Manager
Sarah Thompson
Email: sarah.thompson@chemicalwatch.com
Tel: +44 (0) 20 3603 2103
Greif innovates in Scandinavia
Publishing
Designer
Petya Grozeva
Chief
Chief
• Product for safer products
It is that time of year when companies are releasing their first quarter financial results. These are always of deep interest to shareholders but they also – if read critically - give the broader community a pointer to how wider economic, trade and political factors are playing out. So far this year, the results being announced by players in the distribution, haulage and terminalling sectors have indicated that conditions are returning to something more like what we would call ‘normal’ after the pandemic years and supply chain disruptions caused by problems in the Suez and Panama canals.
This made me wonder what ‘normal’ looks like these days. We have become inured to the idea that business conditions are ‘volatile’ or ‘uncertain’ and we certainly know that supply chains, particularly in a globally connected world, are increasingly ‘complex’. The addition of ‘ambiguous’ takes us back to ‘VUCA’, a term originally developed in the US Army War College in the 1980s – not the first time that military thinking has described or influenced the world of peacetime logistics and probably not the last.
I believe it took some time for VUCA to enter our general vocabulary but I am sure that it predates the Covid pandemic. In fact, I can recall discussions about supply chain complexity during an EPCA Annual Meeting some time in the 2010s, when ‘VUCA’ was offered up as a lens to help understand the often conflicting pressures acting upon global chemical supply chains and, as a result, on the operators active all along those supply chains.
Pre-Covid, the talk was all about increasing globalisation and what that meant for trade, especially in light of the
business imperative to keep inventory as low as possible. We had occasion to question that approach when natural and manmade incidents had caused supply chain interruptions. The grounding off the UK coast of the containership MSC Napoli in 2007 led to automotive plants in South Africa having to close, as their ‘just in time’ supply chains offered no leeway. Hurricane Katrina (2005) had plenty to teach us – for instance, there is no point in keeping emergency stockholdings in the form of crude oil if refinery capacity is going to be closed.
One obvious feature of the past four years has been a willingness to increase inventories, with ‘just in time’ morphing into ‘just in case’. This has been particularly profitable for the tank container business, as tanks provide a relatively costeffective and certainly very flexible way of holding emergency stocks. Tank container operators earned a lot of demurrage income and also found a handy place to put their older, heavier tanks that were not so attractive for transport purposes.
Now that chemical companies and their customers are getting used to the post-pandemic world, those opportunities are evaporating; as ITCO’s annual survey reports (see page 44), scrapping of old tanks has increased now that they are being released from short-term storage duties and the fleet as a whole seems over-supplied. That is translating into a marked reduction in profitability for tank operators, even if the number of consignments is still increasing, although they seem happy with their lot.
China’s increasing self-sufficiency in chemicals is the next thing to worry about. This looks likely to reduce overall trade volumes but might offer opportunities in local transport operations.
Peter MackayTHERE IS ALWAYS a risk, with the benefit of hindsight, in writing an article promising the ‘HGV of the future’ but it was a risk that HCB took in its May 1994 issue. Concern had been building about road tanker safety in the UK, which was experiencing an average of one rollover incident every month. In response, Cambridge University’s Engineering Department and Cranfield University’s Automotive Studies Group got together with some industry sponsors to study truck dynamics and suspension design, with input from new-fangled computer modelling to examine exactly how rollovers happen.
The project had piqued the interest of many, not least Shell Oil UK, and its findings fed directly into a number of innovative systems and practices that, thankfully, have almost removed the risk of tanker rollovers from UK roads. Now, if only those same innovations could be picked up in the US.
Another hostage to fortune in the May 1994 issue was a small item looking at the impending increase in the number of LNG carriers in layup. The problem was in fact caused by Abu Dhabi determining that its gas reserves could support a longer period of LNG exports than had originally been planned, so it had ordered a brand new fleet and announced that the Gotaas-Larsen ships it was relying on would no longer be needed. At the time, it was the general practice for ships to be built against long-term contracts for a specific project – there was no spot market to speak of. And, while there had been talk of the LNG tanker market developing along the lines of the crude oil trades, it was to be several years before owners started investing in speculative vessels. Now the LNG business has been turned upside
down – in 1994 the US was importing LNG, today it is the world’s largest exporter.
Another milestone reached in early 1994 was the end of the 12-month pilot phase of the new Safety and Quality Assessment Scheme (SQAS) developed by the European Chemical Industry Council (Cefic) as one part of a two-pronged approach to promoting continuous improvement in accident prevention and emergency response under the International Chemical Environment (ICE) programme.
P&O Roadtanks, which was in those days one of the largest road tanker operators in the UK, found the SQAS assessment to be quite easy to undergo, especially as it was tied in to its BS 5750 quality assurance certification, but it did provide some pointers to how the SQAS audit could be improved.
April 1994 was another important date in the UK, as it was then that the new Carriage of Dangerous Goods by Road and Rail (Classification, Packaging and Labelling) Regulations came into force as part of the UK’s effort to harmonise its domestic dangerous goods legislation with the provisions of the ADR Agreement. The new regulations imposed additional duties on consignors and replaced the carriage provisions of the Chemicals (Hazard Information and Packaging) Regulations – usually referred to as ‘CHIP’. The supply provisions in CHIP were to be copied into a new ‘CHIP 2’, due to come into effect on 1 January 1995.
This might have been seen as ‘progress’ but, thirty years on, the UK’s civil servants are still busy drawing up provisions to distance UK legislation from those pesky Europeans.
WHAT I DISCOVERED when researching information theory as part of physics is that an information deficit is equivalent to an energy (to do work) deficit. This means that functionality of all living systems, including our industry, depends on the use of real-time, optimal information. The universe and nature work like this too.
I look at the first and second laws of thermodynamics and the newly proposed law by Dr Melvin Vopson of the University of Portsmouth (I interviewed him in person) which he named the second law of information dynamics (infodynamics). This is based on the MassEnergy-Information equivalence principle. We already apply this to our work to boost performance levels dramatically. As you may know, the universe uses minimum but optimal information. This ‘minimum’ is equal to the need for a minimum quantity of energy (maximal efficiency without causing loss or waste). When you apply this, you will gain so-called free energy by the acquisition of information. Entropy is sometimes described as ‘the information we don’t have or don’t use’.
I designed the following equations to measure and predict functionality. I depends on how people understand how nature functions (perception).
¬p(m-(i ≡ e))>r→∆S entropy / disorder / dysfunctionality
¬p: false perception; m: symbol for living systems as matter/mass; i: information; ≡ equivalence symbol; e: energy; r > beyond reality → results in; ∆S: social entropy/disorder or probability of dysfunctionality.
√p(m+(i ≡ e))≤r→J negentropy / order / functionality
√p: correct perception; m: symbol for living systems as matter/mass;
i: information; ≡ equivalence symbol; e: energy; ≤ equal to within r, reality → results in; J: social negentropy/order or probability of functionality.
I then designed so called PPP’s: Performance Probability Patterns of Marine Storage Terminals based on these laws of physics: P(A) Probability Function of Information Deficit (C) = Metaphysical Equation: P(A) C: (i-e) ⇒ ∆S
Probability Function of C due to a lack of information ≡ is equivalent to dissipated (displaced) energy, which is no longer available to do useful work ⇒ implying increased (entropy) disorder (growing ∆S).
Hence: systems that are dependent on a shortage of information, lack of knowledge, unawareness, delays in preventive action, accelerate internal and external (impact) Performance Probability Patterns of dysfunctionality ≡ Entropy.
This may be look a bit odd, but when you read this slowly, I am sure you will understand the significance of this. Anyway I tested them and can demonstrate empirically that it works. Practical uses of the equations were tested empirically in marine storage terminals where the quantity of information prior to and after a loading master training was measured. Quantifying the volumetric growth in information helps industries to detect potential learning and information gaps (loss of energy to function).
This is the latest in a monthly series of articles by Arend van Campen, founder of TankTerminalTraining, who can be contacted at arendvc@ tankterminaltraining.com. More information on the company’s activities can be found at www.tankterminaltraining.com.
We’ll start with two words that seem to do the same job - poisonous and toxic. Then and just for the hell of it, let’s bring on another word - venomous. And while we’re at it let us chuck in the word toxicant in last place. The first three are adjectives that are not interchangeable and they all have different meanings. We’ll give toxicant a run out later.
Let us begin by showing a simple way to explain the difference between venomous creatures and poisonous ones by their bites: If you bite it and you die, it is poisonous; if it bites you and you die, it is venomous.
Anybody with even a passing interest in these matters can tell you that there are three ways that a toxic substance can be administered, namely inhalation (fastest and hardest to protect against), oral (slower and easier to deal with) and dermal (slowest and easiest to stop from working). Anyway, that avenue of thought is probably best left there at least for the purposes of this discussion. Anyone care to discuss albino rats? No? We’ll leave it there then and put it down to me grandstanding like there’s no tomorrow.
But back to the case in point and breaking things down a bit more: to deliver their ‘chemicals’, venomous creatures bite you — they actively inject their deadly mixture into other organisms (such as you) via fangs, spines, stingers, or similar methods of venom delivery. For example, consider Oxyuranus microlepidotus (the inland taipan). This snake is generally believed to have the deadliest venom of any known creature. If this snake bites you, things will go Pete Tong very quickly. A single drop of its venom can kill 100 adult humans. However, the
good news is that this snake is very timid, and so it runs (slithers?) away at a rate of knots rather than come into contact with humans.
Another horrifyingly venomous snake is Dispholidus typus, (the boomslang). The average size of these creatures is 1.0 to 1.6 m (3.2 to 5.2 feet). That’s significant because, while many snakes have fangs and mouths that are too small to pose a danger to humans, this is certainly not the case with the boomslang. These creatures are able to open their jaws more than 170 degrees in order to bite their prey. What’s more, the venom of the boomslang is a hemotoxin. This means that it disables the body’s clotting process. That means the unfortunate victim will likely die as a result of internal and external bleeding unless medical treatment is administered.
Fun fact: boomslang venom is also known to induce internal bleeding in muscle and brain tissues.
If you are looking for a more scientific way to define venomous creatures; a venom is:
A secretion, produced in a specialised gland in one animal and delivered to a target animal through the infliction of a wound ‘regardless of how tiny it could be,’ which contains molecules that disrupt normal physiological or biochemical processes so as to facilitate feeding or defence by the producing animal.
Conversely, poisonous creatures secrete their harmful chemicals (often through their skin). In other words, a poisonous creature can only deliver its toxin if you (or another unwary creature) eats it or
touches it. For example, let’s look at the poison dart frog (from the Dendrobatidae family). These chaps are rather small, measuring in at just 2 inches (5 cm). However, this tiny amphibian has enough poison on board to kill an estimated 20,000 mice (or about 10 adult humans).
Just out of interest, scientists believe that the poison dart frog, like many other poisonous creatures, gets its deadly concoction from its environment. Research suggests that the frog eats insects that carry the poison and that these insects in turn, get their poison from plants.
According to Oxford Dictionaries, “poisonous organism” can be defined rather simply:
An organism that produces toxins that are harmful when the animal or plant is touched or eaten.
Notably, some creatures are poisonous and venomous. Eat one and you will be poisoned and if it stings you, you will not be venomed –you will have been stung (oh all right - poisoned). And as a final point in the discussion of poison and venom, the word ‘poison’ actually has a rather broad definition; it is simply any chemical substance that causes a biological disturbance in other organisms.
So, what about toxicants (and toxin)? Unlike venom and poison, the word ‘toxin’ is not defined by a specific method of delivery. Rather, a toxin has a broader meaning. It is a biologically produced chemical substance that impacts biological functions in other organisms. In this respect, anything that is synthesised is not considered a toxin. Rather, a ‘toxicant’ is a chemical substance that is synthesised/
produced by human activity. In short, toxins and toxicants are narrower definitions for the word ‘poison’.
Keep up at the back, we’re nearly there.
In summary:
• Poisons are any chemical substances that impact biological functions in other organisms.
• Poisonous organisms secrete chemical substances that impact biological functions in other organisms.
• Venomous creatures inject chemical substances that impact biological functions in other organisms.
• Toxins are biologically produced chemical substances that impact biological functions in other organisms.
• Toxicants are synthesised chemical substances that impact biological functions in other organisms.
And there we have it. Are scales falling gently from our eyes? Or is the water still muddy?
It’s decision time and now…
Milord, I rest my case as I lean back in my green leather court chair and puff heartily on my meerschaum…..
This is part of a regular series of articles by Grahame Moody, senior analyst (technical services) of Hazmat Logistics, who can be contacted at sales@hazmatlogistics.co.uk. More information on the company’s activities can be found at www.hazmatlogistics.co.uk.
TWS offers tank containers for liquid products in the chemical and food industries for more than 30 years. Whether you opt proven standards or special requirements –we have the right equipment and develop sophisticated advanced individual solutions with you. With TWS you rent experience, quality and innovation for your success. For more information: E-mail: tws@tws-gmbh.de and web: www.tws-gmbh.de
MULTIMODAL • THE JOINT MEETING’S SPRING SESSION WAS MEANT TO MAKE ONLY MINOR CHANGES TO WHAT HAD ALREADY BEEN AGREED BUT THERE WAS A LOT OF WORK TO BE DONE
THE JOINT MEETING of the RID Committee of Experts and the Working Party on the Transport of Dangerous Goods (WP15) held its spring 2024 session in Bern from 25 to 28 March; the meeting had to be kept to four days because of a public holiday in much of Europe, and it had been decided that this session should not spend time deliberating on any new items – rather, it kept itself largely concerned with revisions to amendments already adopted and some minor changes, with a few items adopted for entry into force in 2027.
The role of the Joint Meeting is to provide a forum for the modal bodies that oversee the three sets of European dangerous goods transport regulations, ADR (road), RID (rail) and ADN (inland waterways); ADR is being used more widely than just in Europe, resulting in non-European countries now attending the meetings of WP15. The aim of this forum is to encourage the harmonisation of the three sets of regulatory provisions, the
better to ensure the seamless multimodal transport of dangerous goods across Europe.
The texts of RID, ADR and ADN that will enter into force on 1 January 2025 are now nearly complete; the Joint Meeting was to be followed by separate sessions of WP15 (for ADR) and the RID Committee of Experts, at the end of which the full list of amendments could be prepared.
The Joint Meeting’s spring session was chaired for the first time by Silvía Garcia Wolfrum, who has stepped up following the retirement of Claude Pfauvadel. The new vice-chair is Soedesh Mahesh (Netherlands). The session was attended by representatives of 22 full member countries (including the US) as well as Zimbabwe, along with the EU Agency for Railways (ERA) and 13 nongovernmental organisations.
The Joint Meeting convened at the headquarters of the Intergovernmental Organisation for International Carriage by Rail (OTIF) in Bern; the session was opened by its
secretary general, Wolfgang Küpper, who is due to retire by the end of the year. As a result, this was his last opportunity to play host to the meeting.
As always, the first item on the agenda was matters relating to transport in tanks; the Working Group on Tanks had met separately at the end of February to discuss matters arising from the autumn 2023 session of the Joint Meeting. Among these was the issue of whether competent authorities that perform inspection activities themselves, rather than rely on approved inspection bodies, should themselves be similarly accredited. The Working Group felt that technical services within the competent authority that performed the activities of approved inspection bodies would require accreditation. It also noted that the designation of bodies to act as the competent authority may create a loophole for inspection bodies not to become accredited. The Working Group suggested an amendment to the already agreed change in 1.8.6.2.1, which will now read:
When the competent authority performs the tasks of the inspection body itself, the competent authority shall comply with the provisions of 1.8.6.3. However, when a competent authority designates an inspection body to act as the competent authority the designated body shall be accredited according to the standard EN ISO/ IEC 17020:2012 (except clause 8.1.3) type A.
The previously adopted amendment to 1.8.6.3.1 remains unchanged:
The requirements above are deemed to be met in the case of accreditation according to the standard EN ISO/IEC 17020:2012 (except clause 8.1.3).
The Working Group followed up on earlier discussions where it was agreed that an intermediate inspection was required when the specified date for such an inspection has passed. However, depending on the time period that the inspection is overdue the owner/operator may decide to have an intermediate or periodic inspection performed. To prevent misinterpretation, the International Union of Wagon Keepers (UIP) suggested some alternative wording.
The Joint Meeting, however, decided that the adopted provision was not a ‘new provision’ but only a clarification; rather than amend the texts, it asked the secretariats to add this clarification to the RID and ADR Interpretations Lists. It also agreed to include a new third paragraph in 6.8.2.4.3 for the 2027 editions of RID/ADR:
If the specified date of the intermediate inspection has passed, an intermediate inspection shall be performed or alternatively a periodic inspection may be performed in accordance with 6.8.2.4.2.
The Working Group examined Spain’s proposal to improve the provisions for filling multiple-element gas containers (MEGCs) in Chapter 4.3; it was felt that, to be fit for purpose, this amendment should also address battery-wagons/battery-vehicles. This was agreed by plenary but, as it was deemed a significant change, it will not be included in the 2025 texts and will be held over to 2027. It will involve a new 4.3.3.2.5:
Prior to filling, the battery-wagons/ batteryvehicles and MEGCs shall be inspected to ensure they are authorized for the gas to be carried and that the applicable provisions of RID/ ADR have been met. The elements of batterywagons/battery-vehicles or MEGCs that are pressure receptacles shall be filled according to the working pressures, filling ratios and filling provisions specified in packing instruction P 200 of 4.1.4.1 for the specific gas being filled into
each element. When battery-wagons/batteryvehicles and MEGCs are filled as a whole or groups of their elements are filled simultaneously, the filling pressure or the load shall not exceed the lowest maximum filling pressure or the lowest maximum load of any single element. Battery-wagons/battery-vehicles and MEGCs shall not be filled above the applicable permissible masses.
The existing 4.3.3.2.5 will be renumbered 4.3.3.2.6, with some consequential amendments in 4.3.3.1.1, 6.8.2.4.1 and 6.8.3.4.2.
Russia proposed amendments to 6.8.2.1.27 (RID/ADR) and 7.5.10 (ADR) relating to tank vehicles for the carriage of UN 1361 Carbon black. Russia pointed out that, for classification under UN 1361, the material should be of animal or vegetable origin; however, most carbon black transported in tanks is derived from hydrocarbon gases and is therefore classified under UN 3190 Self-heating solid, inorganic, nos. As such, the requirements for electrostatic protection may not apply. The Working Group made some observations on Russia’s interpretation and plenary concurred that the matter should be sent up the chain for discussion by the UN Sub-committee of Experts on the Transport of Dangerous Goods (TDG), with proposals for amendments to the Model Regulations.
Spain and the European Industrial Gases Association (EIGA) had raised a problem that has arisen since the TDG Sub-committee changed the wording that must appear on the tank plate from ‘degree of filling’ to ‘maximum allowable mass of gas filled’. While this is in itself not an issue, it will take time for the necessary replacement plates to be sourced and fitted. The Working Group supported the proposal to insert a new transitional measure, akin to that already adopted by the UN TDG Sub-committee. This will appear in the 2025 texts as a new 1.6.4.66:
Portable tanks constructed before 1 January 2027 in accordance with the requirements in
force up to 31 December 2024, but which do not, however, conform to the requirements of 6.7.4.15.1 (i) (iv) applicable as from 1 January 2025 may continue to be used.
The Netherlands proposed waiving the requirement for calculating the actual holding time for tank containers in road transport, as is already done for tank vehicles. Transport operations are usually relatively short and there is a driver present to monitor the tank pressure. The Working Group supported the proposal but felt that the wording offered could be improved. In addition, there were some consequential amendments needed.
The Joint Meeting agreed, and made the following changes for ADR 2025. Firstly, a new paragraph is added to the end of 4.2.3.7.1:
The calculation of the actual holding time may be waived when the whole journey takes place by road only, without trans-shipment onto another vehicle and without intermediate temporary storage. When the calculation of the actual holding time is waived the provisions of 4.2.3.7.2,
4.2.3.7.3 and 4.2.3.8 (e) and (f) shall not apply.
The same text is added at the end of 4.3.3.5, right-hand column, except that the last sentence reads:
When the calculation of the actual holding time is waived the provisions of 4.3.3.6 (e), (f) and (g) shall not apply.
Finally, an additional paragraph is added at the end of 5.4.1.2.2(d):
When the calculation of the actual holding time is waived in accordance with 4.2.3.7.1 or 4.3.3.5 this provision shall not apply;
On a similar note, the International Union of Railways (UIC) followed up on a decision made at the autumn 2023 session of the Joint Meeting to add a new sub-paragraph (h) to 4.3.3.6 designed to prevent the premature activation of pressure relief devices on empty uncleaned tanks for refrigerated liquefied gases. There had been some discussion about clarifying the consignor’s responsibilities in this regard, but no decision was taken. The Working Group was happy with UIC’s solution
and it was confirmed by plenary, resulting in the addition of a new 1.4.2.1.1(f) in the 2025 texts. The version for RID reads:
in the case of tanks carrying refrigerated liquefied gases ensure that the actual holding time is determined or, in the case of empty, uncleaned tanks, ensure that the pressure is sufficiently reduced.
The version for ADR is the same, except that it begins: “In the case of tank-containers and portable tanks carrying refrigerated liquefied gases…”.
UIP queried whether the requirement in RID for tank wagons for gases to be marked with an orange band (as per 5.3.5 and special provision TM6 of 6.8.4) is still useful. There is no similar requirement for tank-vehicles or tank-containers and apparently no desire to introduce one. Some experts in the Working Group were not convinced by the argument and Belgium provided a summary of the
reasons for keeping the orange band mark,
situations. Belgium did note some difficulties with meeting the specifications for the orange colour, but that is another matter that can be
specifications for which differ somewhat in wording of the latter paragraph in particular is
better if it were changed, Germany says. The Working Group concurred, as did plenary, and Each
personnel – General principles, which is referenced in TT8 (RID) and TT11 (ADR) in 6.8.4 as the 2012 edition. The standard is also referenced several times in Chapter 6.2 but undated. Should the 2022 edition now be referenced? The Working Group felt that changing from 2012 to 2022 could result in problems for inspection bodies and offered an alternative solution, removing references to EN ISO 9712 in TT8 and TT11.
The last paragraph of TT8 will, subject to approval by the RID Committee of Experts, now read:
Such magnetic particle inspections shall be performed in accordance with EN 12972:2018 + A1:[2024].
Similarly, the paragraph referencing EN ISO 9712 in TT11 in ADR will be replaced by: Non-destructive checks shall be performed by personnel in accordance with EN 12972:2018 + A1:[2024] or EN 14334:2014.
Finally, the Working Group on Tanks is still dealing with the thorny issue of the dual approval of intermodal tank containers, which the regulators do not like but which seems to be very useful for operators. The International Tank Container Organisation (ITCO) had organised intersessional meetings in November and December 2023, which were well attended, with the aim of developing a list of the problems that could arise if dual approval is no longer permitted.
One problem is the case of portable tanks that are approved in accordance with Chapter 6.7 of the International Maritime Dangerous Goods (IMDG) Code but not approved in an RID/ADR contracting state/party. This can lead to the tank being refused for carriage or filling. The Working Group came up with a proposal to remove the problem, which was accepted in plenary. It involves am amendment to Note 2 under the heading of Chapter 4.2 to read:
Portable tanks and UN MEGCs marked in accordance with the requirements/the applicable provisions of Chapter 6.7 but which
were approved in a State which is not an RID Contracting State / Contracting Party to ADR or approved in accordance with Chapter 6.7 of the IMDG Code may nevertheless be used for carriage under RID/ADR.
CEN provided an update of its work relevant to the transport of dangerous goods, which the Joint Meeting welcomed. The experts also reviewed the report of the Working Group on Standards, which had met early in February. It was agreed to update the references to technical standards in Part 6 as follows.
In 6.2.4.1, in the row for EN 1964-3:2000, ‘Until further notice’ is replaced by ‘Until 31 December 2026’.
In the row for EN 13322-1:2003 + A1:2006’, ‘Until further notice’ is replaced by ‘Between 1 January 2007 and 31 December 2026’. A new row is then added for EN 13322-1:[2024].
In the row for EN ISO 10297:2014 + A1:2017, ‘Until further notice is replaced by ‘Between 1 January 2019 and 31 December 2026’. A new row is then added for EN ISO 10297:[2024].
In the row for EN ISO 17871:2020, ‘Until further notice’ is replaced by ‘Between 1
January 2023 and 31 December 2026’. A new row is then added for EN ISO 17871:2020 + A1:[2024].
In 6.8.2.6.2, in the row for EN 12972:2018, ‘Until further notice’ is replaced by ‘Until 31 December 2026’. A new row is then added for EN 12972:2018 + A1:[2024].
The Joint Meeting reminded CEN the need to confirm to the secretariat by 31 May 2024 at the latest whether those standards for which ‘2024’ remains in square brackets have been published; if they have not appeared, then they cannot be included in the 2025 texts and will have to wait until 2027.
It was also noted that EN 590:2013 + A1:2017, which is referenced in 3.2.1, 4.1.1.21.6 and 9.1.1.2, has been replaced by EN 590:2022. The Working Group on Standards asked for the appropriate experts to be consulted to see if the references can be updated. Some delegates who took the floor preferred to use an undated reference, which they considered sufficient for the purpose of classification.
At the autumn 2023 session, the Working Group on Standards had discussed the value of column (3) in the tables in Chapters 6.2 and 6.8, which is used to show those paragraphs
to which the standards are relevant. There is no equivalent column in the UN Model Regulations and it was felt that perhaps this information was no longer of much use. The Working Group recommended to the Joint Meeting that this column be removed; CEN will come back with a formal proposal to that
The Netherlands raised concerns at the provision in clause 7.3 of EN 1439:2021, which prescribes that refillable LPG cylinders, valves and valve seals shall be checked for leakage and that the admissible leakage rate shall be in any case not higher than 5 g/h. The issue is that this ‘acceptable’ rate of leakage may still allow sufficient gas to escape to cause a fire and explosion risk. The Netherlands said that there have been accidents caused by gas leakages in roofers’ vans and other vehicles. An LPG cylinder leaking at 5 g/h for 36 hours in a closed or poorly ventilated van can result in the lower explosive limit being exceeded. Furthermore, the general provisions of packing instruction P200(1) state that pressure receptacles shall be so closed and leakproof as to prevent escape of the gas or that the closures and equipment are not leaking, which runs counter to clause 7.3 of the standard. The Netherlands asked the Joint Meeting to consider if the leakage rate in
Some delegations reported similar national requirements stipulate a lower limit.
important that those interpretations do not differ. Overall, though, it was stressed that, in general, the provisions of RID/ADR/ADN should be as concise and clear as possible to
There were, though, a couple of requests. Germany sought clarification of 7.1.7.4.2 in
carriage under temperature control, the temperature must be measured by two independent sensors. Does this mean that they need to have separate power sources? Or does it just mean that two temperature measurements at different points of the
Those who took for floor were largely of the opinion that two independent power sources are required, for the purpose of redundancy. Germany will take the issue to the UN TDG Sub-committee and propose a clarification in
UIC reported that the International Railway loading units, which is referenced in footnotes been updated and a third edition published in new edition in the references in RID and ADR. The Joint Meeting agreed and made the
Tel: +44 (0)870 850 50 51
Email: sales@labeline.com
www.labeline.com
interpretation of the regulatory text is normally a task for the respective bodies in charge of RID, ADR and ADN. Nevertheless, for topics with a multimodal applicability, it is
We serve Freight Forwarders, Shippers, Airlines, DCA’s, Port Authorities, Petrochemical industry and the Pharmaceutical industry.
Labeline is one of the world’s leading regulatory services and product providers; we hold comprehensive stocks with a fast worldwide delivery service.
We are one of the very few authorised Multi-mode providers worldwide and described by industry as a pro-active organisation, our name is recommended by many leading authorities and a world class service providers.
Who do you contact for the latest DG compliant labels? IATA, ICAO, ADR, IMDG, RID, DoT Labeline is the leading worldwide “One Stop Dangerous Goods Service” for Air, Sea, Road, and Rail
Since 1st Jan 2023, all UK consignors must have an appointed DGSA.
responsibilities under 1.8.1.1 of ADR, it conducts background checks on drivers and other employees involved in the carriage of dangerous goods. It recommends that employers do the same, by requesting a Disclosure and Barring Service (DBS) check on potential employees’ criminal records.
RID/ADR/ADN do not currently rule on whether staff with a criminal record can be
For a local, professional consultant DGSA, contact Labeline Free worldwide shipping from IATA’s leading international distributor Do you consign Dangerous Goods?
Specialist software for creating compliant DG Documentation
associated with, the carriage of dangerous goods, or whether background checks should be carried out before employing staff. The UK sought the Joint Meeting’s opinion as to
regulation, and was interested to hear what other contracting parties do in this regard.
Most delegations felt that there is no need to expand on the existing security provisions in Chapter 1.10. Furthermore, the issue is
administrative law. Security clearance issues should be dealt with at a national level rather
Tel: +44 (0)870 850 50 51
Email: sales@labeline.com
www.labeline.com
The second part of this two-part report on the Joint Meeting’s spring 2024 session in next month’s HCB will cover new and pending proposals for amendment, reports from other informal working groups, and accidents and risk management.
Worldwide Leading Authorised Distributor
When it’s time to order your DG products and services, Labeline will be your “One Stop Service” Compliant with
Tel: +44 (0)870 850 50 51
Email: sales@labeline.com
www.labeline.com
USA • THE LATE-RUNNING FINAL RULE UNDER HM-215Q IS HERE AT LAST. INDUSTRY DID SPOT SOME ISSUES IN PHMSA’S PROPOSALS, SOME OF WHICH HAVE NOW BEEN REMEDIED
THE US PIPELINE and Hazardous Materials Safety Administration (PHMSA) published its final rule under docket HM-215Q on 10 April; the rulemaking is PHMSA’s biennial update to maintain harmonisation – insofar as it sees fit – with international standards. In this case, the US rule has appeared somewhat behindhand, as the updates to international standards with which it aims to harmonise are those that took effect on 1 January 2023, based largely on the changes in the 22nd revised edition of the UN Model Regulations. The notice of proposed rulemaking under HM--215Q was published in May 2023 (HCB July 2023, page 08) with a comment period that closed at the end of August. PHMSA received 21 sets of comments, mostly supportive of the changes but some asking for further clarification or revisions. This article
will focus first on the comments PHMSA received and the decisions it has made in response.
Firstly, the Household Commercial Products Association (HCPA) and Medical Device Transport Council (MDTC) asked PHMSA to reconsider the definition of ‘aerosol’ in §171.8 so as to align more closely with that used in the UN Model Regulations and the international provisions. PHMSA acknowledged the concerns expressed but, having not included a proposal to amend the definition in the NPRM, it is unable to accede to the accede to the groups’ request. However, PHMSA says, it will continue to evaluate the potential harmonisation of the aerosol definition in conjunction with a petition
from the Consumer Specialty Product Association (CSPA).
PHMSA received a number of comments proposing the incorporation by reference of ISO 18119:2018, which deals with the periodic inspection and testing of seamless steel and aluminium alloy gas cylinders and tubes. The comments noted that this standard has superseded ISO 10461:2005 and ISO 6406:2005, which are currently referenced in the US Hazardous Materials Regulations (HMR) but which will no longer be included in the UN Model Regulations after the end of 2024.
Again, PHMSA said it could see the logic in making the change but it had not included the proposal in the NPRM and it will therefore have to be addressed separately; it has already received petitions from FIBA Technologies and Hazmat Safety Consulting on the issue.
The Institute of Hazardous Materials Management (IHMM) submitted comments recommending that PHMSA introduce a requirement for companies transporting hazardous materials to appoint a certified person, similar to the dangerous goods safety advisor (DGSA) required under ADR, and offered its own accredited professional certifications - Certified Hazardous Materials
Manager (CHMM), Certified Hazardous Materials Practitioner (CHMP) and Certified Dangerous Goods Professional (CDGP) – as possible models.
Once again, PHMSA acknowledged IHMM’s position but, as it did not include any proposals in this regard in the NPRM, it cannot now add any new provisions into the final rule. Such a change would necessitate evaluation by PHMSA’s own subject matter experts and a period for stakeholders to comment. PHMSA encouraged IHMM to submit a petition for rulemaking,
The American Association for Laboratory Accreditation (A2LA), while supporting the proposed amendments in the NPRM, suggested that PHMSA consider taking a further step by recommending that, when testing is required, dutyholders use the services of laboratories approved in accordance with ISO/IEC 17025, so as to help ensure the data generated to show compliance with HMR is developed by accredited bodies.
PHMSA could again not respond to this request in the final rule, since it had not been tested during the comment period. Should it wish to do so, A2LA is free to submit a petition for rulemaking.
The Compressed Gas Association (CGA) and Entegris commented on the proposal to update the reference to the ISO 11117 standard on valve protection caps for gas cylinders from the 2008 edition to the 2019 edition. The NPRM included a proposal for a phase-out date of 31 December 2026 for the old edition. This will cause problems, since industry would have to replace a large number of valve protection caps in a relatively short time, causing an unnecessary economic burden. CGA and Entegris proposed amendments that would permit the continued use of valve protection caps compliant with the 2008 edition.
PHMSA agreed that it was not its intention to require industry to replace all valve protection caps by 31 December 2026; rather, what it wanted was for all new valve protection caps to be compliant with the 2019 edition of the standard by that date, in line with the UN
Model Regulations. As such, PHMSA is revising the text in §173.301b(c)(2)(ii) to more closely align with its original intent.
CGA went further, suggesting that PHMSA modify the regulatory text for all the ISO standards incorporated by reference in §§178.71 and 178.75 to permit the manufacturing of UN cylinders conforming to the ISO standards being replaced until December 31, 2026, to better align the HMR with the intent of the 22nd edition of the UN Model Regulations.
PHMSA concurred that its intent was to closely align with the phaseout language used in the UN Model Regulations and has revised the texts indicated by CGA.
The NPRM included a proposal for a new special provision for UN pressure receptacles containing mixtures of fluorine and inert gases, to allow flexibility in the maximum allowable working pressure (MAWP), in line with the UN Model Regulations. In the NPRM,
PHMSA proposed adding special provision 441 to UN 1045 Fluorine, compressed.
CGA and Entegris pointed out that this is incorrect. Special provision 441 cannot be assigned to UN 1045 as mixtures of fluorine with inert gases containing less than 35 per cent fluorine are not Hazard Zone A gases and there is no scenario under which a gas classified as UN 1045 would be able to qualify for the exception. Instead, special provision should be assigned to nos entries UN 3306, 3156 and 1956, as per the 22nd revised edition of the UN Model Regulations.
Entegris and CGA also noted that the equations for calculation of the MAWP contained several editorial errors, as did the latest amendments in the UN Model Regulations.
PHMSA agreed with the comments made and has not applied special provision 441 to UN 1045. Rather than applying it to the nos entries for compressed gases, however, it has
added a new paragraph (g) to §173.302b, in line with a suggestion from CGA. This sets out the calculation method to determine the MAWP for mixtures of fluorine with nitrogen and mixtures of fluorine with inert gases, largely following the wording proposed for special provision 441 but including editorial corrections suggested by Entegris.
In the NPRM, PHMSA proposed to revise §§178.706(c)(3) and 178.707(c)(3) to allow for the manufacturing of rigid and composite intermediate bulk containers (IBCs) manufactured from recycled plastics, with the approval of the Associate Administrator, consistent with a change adopted in the 22nd revised edition of the UN Model Regulations. In the NPRM, PHMSA proposed including a slight variation from the international provision by requiring prior approval by the Associate Administrator for use of recycled plastics in the construction of IBCs manufactured from recycled plastics.
The Rigid Intermediate Bulk Container Association (RIBCA) disagreed with the proposed requirement for manufacturers to obtain case-by-case approval, arguing that this would be inconsistent with the UN Model Regulations, which allow the use of recycled plastics meeting a specified definition with no need to resort to competent authority approval.
RIBCA also questioned PHMSA’s rationale that approvals are needed due to lack of requirements in HMR for manufacturers to have in place quality assurance programmes, noting that these are already integral to ensuring IBC integrity. Indeed, the performance-oriented packaging requirements in HMR should sufficiently address any safety issues with recycled plastics, as demonstrated by the millions of UN plastic drums and jerricans successfully produced with recycled plastics.
PHMSA acknowledged RIBCA’s comments but said that, by requiring approval by the Associate Administrator, PHMSA would be able to maintain oversight of those procedures
– such as batch testing – that manufacturers will need to use to ensure the quality of recycled plastics used in the manufacture of IBCs. PHMSA’s position is that this is consistent with the intent of the UN Model Regulations.
In addition, PHMSA is currently conducting research to develop an Agency-wide policy on packaging manufactured from recycled plastics. It issued a request for information in April 2023 on how the potential use of recycled plastic resins in the manufacturing of specification packagings may affect hazardous materials transportation safety. It received nine comments in response to that request, which are currently being evaluated. Until this analysis is complete and an Agency-wide policy can be put in place, PHMSA feels it is prudent to leave the requirement for Associate Administrator approval in HMR. PHMSA also noted that it received supportive comments from other respondents to the NPRM.
The remaining proposals contained in the NPRM have been confirmed in the final rule, which takes effect on 10 May 2024. Those proposals included changes to proper shipping names, hazard classes, packing groups, special provisions, packaging authorisations, air transport quantity limitations, and vessel stowage requirements. These amendments are necessary to facilitate the transport of hazardous materials in domestic and international commerce. The final rule also aligns HMR’s requirements with anticipated increases in the volume of lithium batteries transported in interstate commerce from electrification of the transport and other economic sectors.
It is interesting to read the commentary on the rulemaking provided by the US Department of Transportation (DOT). Those working in the hazmat transport sector in the US are generally supportive of PHMSA’s efforts to keep the US regulations in line with those found in the international modal rulebooks – the International Civil Aviation Organisation’s (ICAO) Technical Instructions and the International Maritime Dangerous Goods (IMDG) Code – and requirements in other countries with which US industry trades.
There is, on the other hand, a section of the industry that is active only within the national borders of the US (or even within state borders in many cases) and for which biennial changes to harmonise with international regulations represent an unnecessary burden.
Still, the importance of achieving safety in the transport of hazardous materials means that HMR needs to reflect the latest and most stringent standards, and industry is behind that intent, even if to outsiders it seems that federal agencies are ladling additional regulatory burdens on an already hardpressed business.
Therefore, comments made by US Transportation Secretary Pete Buttigieg need to be seen as addressing an audience outside of the immediate hazardous materials community. Introducing the final rule under HM-215Q, Buttigieg said: “The safe
transportation of hazardous material like batteries and components used in manufacturing is integral to our supply chains and our economy. This new rule improves safety, keeps the US competitive on the global stage, and cuts shipping costs to the benefit of consumers nationwide.”
Similarly, PHMSA Deputy Administrator Tristan Brown said: “This regulatory update actually improves safety and environmental benefits while reducing red tape for businesses. It will also help improve supply chains and reduce prices for everyday Americans.”
PHMSA also has to make the case for the need for regulation. In the preamble to the final rule, it says the rulemaking will improve safety, streamline the transport of essential products — including medical supplies, batteries and components used in manufacturing — and encourage shippers to
package goods more efficiently.
And there is always a sustainability box to be ticked. PHMSA says the final rule will help reduce greenhouse gas emissions and supply chain disruptions by allowing the transport of more goods in fewer trips and aligning hazardous materials regulations requirements with anticipated increases in the volume of lithium batteries transported in domestic and international commerce. The rule also helps lessen the economic disadvantages faced by American companies that, when competing in foreign markets, are forced to comply with different or conflicting requirements or forgo exporting internationally altogether.
The text of the final rule, as published in the Federal Register, can be found online at www. govinfo.gov/content/pkg/FR-2024-04-10/ pdf/2024-06956.pdf.
MARITIME • SHIPPING HAS A DOUBLE ROLE TO PLAY IN MEETING
THE UN SUSTAINABLE
GOALS; IMO IS WORKING HARD TO PUT IN PLACE THE NECESSARY
AS AN AGENCY of the United Nations, the International Maritime Organisation (IMO) is tasked with observing and promoting the implementation of the UN Sustainable Development Goals, with specific reference to the marine environment. As a result, much of the current work of the IMO Marine Environment Protection Committee (MEPC) revolves around the adoption of measures to enhance the protection of the world’s oceans.
Over the past decades, much of that effort has been concentrated on preventing atmospheric pollution from ships, especially near to land and in port, and that programme is continuing, with successive targets for limiting emissions of greenhouse gases and other exhaust emissions. That process marked a step away from MEPC’s traditional
role in protecting the world’s oceans from pollution from cargo spills, tank washings and other noxious substances.
More recently, the focus has swung back to the water, with a higher priority being placed on preventing the inadvertent pollution of the seas by plastics materials, either jetsam such as discarded fishing nets and other plastics garbage, or flotsam in the form of cargo lost overboard, including plastics pellets.
One of the significant agenda items for MEPC’s 81st session, which took place in London this past 18 to 24 March, was to approve the Recommendations for the carriage of plastic pellets by sea in freight containers, developed by the Sub-committees on Pollution Prevention and Response (PPR) and Carriage of Cargoes and Containers (CCC). A circular,
MEPC.1/Circ.909, was adopted, which will act as a short-term measure to reduce the environmental risks associated with the carriage of plastic pellets in packaged form by sea while mandatory instruments are being developed.
The Recommendations developed by PPR and CCC are quite broad in nature, comprising three basic tenets:
• Plastic pellets should be packed in good quality packaging which should be strong enough to withstand the shocks and loadings normally encountered during transport. Packaging should be constructed and closed to prevent any loss of contents which may be caused under normal conditions of transport, by vibration or acceleration forces.
• Transport information should clearly identify those freight containers containing plastic pellets. In addition, the shipper should supplement the cargo information with a special stowage request requiring proper stowage.
• Freight containers containing plastic pellets should be properly stowed and secured to minimise the hazards to the marine environment without impairing the
safety of the ship and persons on board. Specifically, they should be stowed under deck wherever reasonably practicable, or inboard in sheltered areas of exposed decks.
It was an indication of the importance attached to the topic of plastics pollution that MEPC went ahead with its approval, despite the fact that PPR’s 11th session, where the Circular was finally agreed, took place only three weeks prior to the MEPC session; all other matters from that PPR meeting, which come under the broader Action Plan to Address Marine Plastic Litter from Ships, have been held over for discussion at MEPC’s 82nd session later this year.
There were, though, other matters relating to marine litter that were discussed. In particular, MEPC adopted amendments to article V of Protocol 1 of the International Convention for the Prevention of Pollution from Ships (Marpol), which contains provisions concerning reports on incidents involving harmful substances, to add a new requirement for reporting lost containers. Containers lost overboard can be a serious hazard to navigation and safety at sea as well as to the marine environment.
The amendment will add a new paragraph to say that “In case of the loss of freight container(s), the report required by article II (1) (b) shall be made in accordance with the provisions of SOLAS regulations V/31 and V/32”. MEPC’s sister committee, the Maritime Safety Committee (MSC), is due to adopt parallel requirements in Chapter V of the International Convention for the Safety of Life at Sea (SOLAS) at its 108th session this month. These will place a responsibility of the master of every ship involved in the loss of freight container(s) to communicate the particulars of such an incident to ships in the vicinity, to the nearest coastal state and to the flag state. These changes are expected to take effect on 1 January 2026.
IMO has addressed the issue of greenhouse gas (GHG) emissions from ships’ exhausts in two ways: firstly by imposing restrictions on the fuels that can be used, either in specific areas or more widely; and secondly by introducing measures to enhance fuel efficiency. These measures have contributed to a significant reduction in emissions from ships but, in view of the UN Sustainable Development Goals, IMO is looking at how to achieve its aim of achieving net-zero GHG emissions by around 2050.
It is already apparent that there will be no single target but that, in pursuit of the 2023 IMO Strategy on Reduction of GHG Emissions from Ships adopted at MEPC’s previous session in July 2023, there will be a number of steps. These have been sketched out in a draft net-zero framework, which identifies those regulations under Marpol that will need to be added or amended to allow for a new global fuel standard and a new global pricing mechanism for maritime GHG emissions,
which are the 2023 Strategy’s mid-term measures. The fine detail of those measures is still under consideration.
While IMO is clearly going to put in the time to get the next step on the road to net-zero right, the maritime industry itself is having to take something of a gamble on what the end result of IMO’s deliberations will be. New ships ordered today will need to comply at some point in their lifetime with rules that are yet to be written, so it is noticeable that many owners are trying to future-proof newbuildings by specifying that they be able to accommodate alternative fuels or carbon capture technologies.
In the meantime, MEPC has agreed that it should have a comprehensive impact assessment of the proposed medium-term GHG reduction measures available for its next session, which is scheduled to start on 30 September. Before then, a two-day expert workshop will discuss preliminary findings from that impact assessment. A 17th intersessional working group on greenhouse
LITTER HAS BECOME AN EMOTIVE ISSUE AND URGENT ACTION IS BEING TAKEN
gas emissions will also meet and develop draft terms of reference for a fifth IMO GHG study.
MEPC also adopted revised guidelines on lifecycle GHG intensity of marine fuels (the ‘LCA Guidelines’), updating the template for well-to-tank default emissions and adding a new template for tank-to-wake emission factors. Work on this topic will continue, with the Group of Experts on the Scientific Aspects of Marine Pollution (Gesamp) also to take part.
Two new correspondence groups have been established: the first is tasked with developing a work plan for the creation of a regulatory framework for the use of onboard carbon capture systems and to look into tank-to-wake methane and nitrous oxide emissions; the second group will look into social and economic sustainability themes and aspects of marine fuels for possible inclusion in the LCA Guidelines. An existing Working Group on Air Pollution and Energy Efficiency has already discussed onboard carbon capture and storage and will develop a work plan for a regulatory framework. These groups will report back to MEPC next year at its 83rd session.
MEPC approved the report on the fuel oil consumption data submitted to the IMO Ship Fuel Oil Consumption Database (reporting year: 2022). Data was reported by almost 29,000 ships, an increase of more than 800 ships compared to 2021. These ships reported the use of 213m tonnes of fuel, which is just higher than the 212m tonnes reported in 2021. The report on annual carbon intensity and efficiency of the existing fleet provides information on progress towards the at least 40 per cent carbon intensity improvement target to be achieved by 2030, on the basis of both demand-based and supply-based measurement metrics.
MEPC adopted updates to three sets of guidelines, covering: the development of a Ship Energy Efficiency Management Plan (SEEMP); administration verification of ship fuel oil consumption data and operational carbon intensity; and shaft/engine power limitation system to comply with the EEXI requirements and use of a power reserve. It also approved a new procedure for reporting
of uses of a power reserve, and unified interpretations of regulations 2.2.15 and 2.2.18 of Marpol Annex VI.
There was also some work on the sampling of fuel oil to determine compliance with Marpol Annex VI and SOLAS chapter II-2. Marpol requires demonstration of sulfur content while SOLAS relates to the flashpoint of fuel. There is a difference insofar as SOLAS considers ‘oil fuel’, which are generally petroleum products, while Marpol considers ‘fuel oil’, which can be any fuel delivered for use on board. MEPC approved a draft MSC/ MEPC circular, which will now go forward to MSC for approval as an urgent matter; once the new circular enters into effect, the 2009 guidelines (MEPC/182(59)) will be revoked.
In a similar vein, MEPC adopted amendments to Marpol Annex VI as regards the definition of gas fuels along with clarification of fuel sampling and bunker delivery notes for low-flashpoint fuels and gas fuels, as well as other related changes. These amendments are expected to enter into force on 1 August 2025.
The energy transition continues to generate issues for regulators; MEPC is still
struggling with the transport of biofuels by sea. Fuel oil is transported as a Marpol Annex I product on standard tankers; biofuels with a bio content of more than 25 per cent, by contrast, are transported under the terms of Marpol Annex II, requiring chemical tankers (with a limit on parcel size). This poses a challenge to the transport of biofuels, in particular to meet the demand for alternatives to very low sulfur fuel oil.
MEPC referred the matter to the Working Group on the Evaluation of Safety and Pollution Hazards of Chemicals (ESPH) for further consideration at its 30th session this coming October. It is hoped that the experts will be able to point MEPC on the best way forward.
The paragraphs above give a brief insight into some of the decisions taken by MEPC that are likely to be of most relevance to HCB readers. There were, though, plenty of other decisions taken, many relating to the ballast water management convention and its implementation; in addition, MEPC approved new Emission Control Areas (ECAs) for the Norwegian Sea and Canadian Arctic waters. MEPC has also endorsed a draft action plan to address underwater noise from commercial shipping activities, which will be discussed further at the next session.
MARITIME • THE UK IS CLOSE TO ENACTING NEW LEGISLATION COVERING THE TRANSPORT OF DANGEROUS GOODS BY SEA. BY AND LARGE, ITS CONSULTATION WENT SWIMMINGLY
THE UK MARITIME and Coastguard Agency (MCA) reports a largely favourable response to its consultation on the proposed Merchant Shipping (Carriage of Dangerous Goods and Harmful Substances) Regulations 2024. The consultation period ran from 8 December 2023 to 26 January 2024, attracting comments from 17 respondents, and MCA says the consultation was “generally well received”, with no recommendations for any substantial changes to the proposals.
The proposed Regulations would revoke the Merchant Shipping (Dangerous Goods and Marine Pollutants) Regulations 1997, along with a number of other dangerous goods related regulations, and replace them with a single set of regulations to provide a more complete, consolidated and up to date legal framework for the carriage of dangerous goods and harmful substances by sea.
One obvious change will be to include an ambulatory reference so as to allow future amendments to mandatory instruments agreed by the International Maritime Organisation (IMO) to become law into force in the UK as
they enter into force internationally; this is more efficient for UK regulators but also ensures that dutyholders are not faced with misaligned requirements. For instance, it will no longer be necessary for MCA to issue a new Merchant Shipping Notice every two years to reflect changes to the International Maritime Dangerous Goods (IMDG) or International Maritime Bulk Solid Cargoes (IMSBC) Codes.
While respondents were largely in favour of the proposals, there was some concern expressed about the proposed Regulation 12 – requirements in relation to shippers and forwarders. More clarity was urged in respect of the responsibilities of those involved in the transport chain, in particular the shipper/ forwarder/agent’s responsibilities for the stowage and securing of cargo within the cargo transport unit (CTU) and for placarding of CTUs and also with regard to Part 6 of the IMDG Code.
Regulation 12 lists sections of the IMDG Code which apply in each case but does not
reference IMDG Code section 7.3 (packing of goods inside the CTU). Regulation 10 of the proposed 2024 Regulations clearly states that master and owner must comply with all relevant sections of SOLAS Chapter VIII and MARPOL Annex III but there is no equivalent clear application of all relevant sections of the Conventions to shippers and forwarders in regulation 12.
In light of the comments received and in order to ensure that the application of SOLAS Chapter VII and MARPOL Annex III is clear and is unambiguously applied to those with particular responsibilities in the transport chain, policy leads and legal advisors have reviewed the text of regulation 12. Consequently, the text has been amended so as to more closely mirror the text already set out in regulation 10 for master and owner, making the two regulations more consistent in their wording and clearer on the application of the Regulations to shippers/forwarders.
There were some questions as to why the term ‘marine pollutants’, as used in the 1997 Regulations, has been changed to ‘harmful substances’. MCA says the change is to better reflect the terminology used in the Marpol Convention, particularly Annex III.
The UK government now plans to finalise the proposed Regulations and accompanying guidance, incorporating the amendments referred to above, with a view to having the 2024 Regulations laid in draft in May 2024 and, once approved by both Houses, to come into law in June 2024.
The International Air Transport Association (IATA) has issued an addendum to the 65th edition of its Dangerous Goods Regulations, which is in force for the whole of 2024. The addendum largely gathers together a significant number of changes to the operator variations, many of which relate to lithium batteries. There are, though, some significant changes to FedEx’s conditions. There is also one correction in 8.3.4 and updates to the lists of competent authorities and training providers.
The English language version of the addendum can be downloaded at www.iata.org/ contentassets/90f8038b0eea42069554b2f4530f 49ea/dgr_65_addendum_en.pdf. Other language versions are available via www.iata. org/en/programs/cargo/dgr/.
Australia’s National Transport Commission (NTC) has issued two more working group papers as part of its major review of the Australian Dangerous Goods (ADG) Code. The 11th paper presents the draft provisions for the use of tanks, bulk containers and vehicles for dangerous goods transport. These provisions are found in Parts 4, 6 and 9 of the draft code, along with some administrative matters in Part 1. NTC sought stakeholders’ views on the proposals, and in particular on 27 specific questions.
The 12th working group paper covers requirements for vehicle crews, equipment, operation and documentation. This will form Part 8 of the future code, combining existing provisions in the ADG Code with relevant elements of ADR. Again, NTC sought stakeholders’ views, with 20 questions designed to generate feedback from the regulated industries.
The latest papers, together with the draft parts of the new ADG Code currently
available, can all be found at www.ntc.gov.au/ transport-reform/ntc-projects/comprehensivereview-australian-dangerous-goods-code.
The US Environmental Protection Agency (EPA) has published its final rule that will require some facilities to develop response plans for a worst-case discharge of hazardous substances (or threat thereof), to include discharges resulting from adverse weather conditions. The Hazardous Substances Facility Response Plans rule, which falls under the Clean Water Act (CWA), applies to facilities that could reasonably be expected to cause substantial harm to the environment, based on their location. These include facilities with a maximum onsite quantity of a CWA hazardous substance that meets or exceeds threshold quantities, located within a 0.5-mile radius of navigable water or conveyance to navigable water, and that meets one or more substantial harm criteria.
The new rule has drawn criticism from industry. Eric R Byer, president/CEO of the Alliance for Chemical Distribution (ACD), describes the final rule as “needlessly broad in scope and deeply flawed” and says that it duplicates many of the requirements already finalised in the Risk Management Program.
“This rulemaking, compounded with additional onerous regulations coming from the Biden Administration, place businesses of all sizes at a significant disadvantage at a time when they are navigating high inflation rates and labour costs in a sluggish economy,” Byer says. “The EPA’s justification for this heavy-handed oversight does not demonstrate the need, as facilities are already required to comply with existing regulations that meet the same objective.”
EPA’s recent changes to the Risk Management Program (RMP), which drew sharp criticism from industry in the US, is facing a further challenge in Congress. Texas Representative Dan Crenshaw has introduced a Congressional Review Act Joint Resolution to
repeal the changes, which industry sees as unnecessarily burdensome.
Not surprisingly, this move has been welcomed by industry associations. Eric R Byer said: “ACD applauds Representative Crenshaw for standing with the chemical distribution industry and recognizing the current effectiveness of the RMP program. Despite countless objections from industry stakeholders, including ACD, the EPA finalized its rulemaking without demonstrating the need for these sweeping and counterproductive changes.
“It is imperative that the US House of Representatives pass this resolution without delay, and the US Senate follow with similar action. ACD wholeheartedly opposes the amendments to the RMP rule and applauds Congressman Crenshaw’s action to reverse them.”
The US Federal Railroad Administration (FRA) has published its final rule establishing minimum safety requirements for the size of train crews. The rule aims to ensure that trains are adequately staffed for their intended
operation and railroads have appropriate safeguards in place for safe train operations whenever using a one-person train crew.
The rule includes specific requirements for trains carrying certain types and quantities of hazardous materials that have been determined to pose the highest risk during transport, both from a safety and security standpoint, although there are some exceptions for existing operations and for Class II and III railroads.
FRA says the rule responds to some “troubling trends” over the past decade, including a 41 per cent increase in accidents caused by human factors; ensuring that a second crewmember is onboard can help avoid many of those errors. The final rule will take effect on 10 June. Its full text can be downloaded from the FRA website at https:// railroads.dot.gov/elibrary/49-cfr-part-218-traincrew-size-safety-requirements.
France has initiated a new multilateral special agreement under ADR, M356, to provide conditions for the carriage in bulk of waste contaminated with free asbestos (UN 2212 and
2590). The agreement anticipates an amendment agreed for the 2025 edition of ADR; as such, it is scheduled to expire on 31 December 2024. Germany is so far the only other country to have counter-signed the agreement, meaning it can now be used in France and Germany and in cross-border transport between the two countries.
The UK Health & Safety Executive (HSE) has issued a safety notice to alert industry to the proper classification of thermites and articles containing thermite. HSE says it has noticed that thermite is often being classified as Division 4.1 or as non-dangerous, while the correct classification is in Class 1, in accordance with ADR and the GB Carriage of Dangerous Goods Regulations.
In addition, the manufacture and storage of thermites and articles containing thermite are subject to the Explosives Regulations 2014 and they are also subject to the requirements for placing on the market contained in the Pyrotechnic Articles Safety Regulations 2015. Full information on the manufacture, storage and transport of thermites can be found on the HSE website at www.hse.gov.uk/explosives/ manufacture-storage-carriage-of-thermites.htm.
The Canadian General Standards Board (CGSB) has published a new edition of CAN/ CGSB-43.151, which deals with the packaging, handling, offering for transport and transport of Class 1 explosives. The 2024 edition of the standard will now be incorporated by reference in Canada’s Transportation of Dangerous Goods Regulations (TDGR) and stakeholders will be expected to comply within six months.
The new edition includes a number of updates to keep in step with international provisions; in addition, there are new requirements on the reuse of packagings and the use of partially filled packagings, updated decontamination requirements and a new provision to prohibit the use of lightweight IBCs for the transport of Class 1 explosives.
EXPANSIONS
• TERMINAL OPERATORS HAVE PLENTY OF WORK
TO DO IF THEY ARE TO BE IN A POSITION TO ENABLE THE ENERGY TRANSITION, BUT A LOT OF PROGRESS IS BEING MADE
FOR THE BEST part of a century, the bulk liquids storage terminal industry has played a pivotal role in the global energy market; it has enjoyed a similar position in the petrochemical industry since the 1950s too. Terminals do more than just offer a place to transfer product between modes of transport; they provide flexibility in long supply chains, buffering volumes to allow demand to be met, regardless of the pace of production.
As the world goes through its current phase of transition in the use of energy and, perhaps to a lesser extent, chemicals, terminals can offer the same services to make the movement of alternative fuels more efficient. After all, the areas of consumption of these new fuels are very much the same as those for traditional fuels.
This much has been apparent for a few years, as this annual review of terminal investment activity has shown. But it is also apparent that the pace of investment has picked up, despite the uncertainties that surround not just the routes that will be taken on the road to decarbonisation but also the wider geopolitical and economic environment. Terminal operators have to make a choice on the basis of the best information they can get, so as to be able to develop the sorts of facilities that will be required in the future – especially as larger projects will have a payback period measured in decades rather than years.
For some projects, the work is easier. Where existing fossil fuels are being challenged by drop-in alternatives such as
biodiesel (or even ‘e-fuels’, though there has not been much activity in that area this year), it may be enough to renew piping so as to ensure an effective separation between grades. Mass balance approaches may even make this redundant. On the other hand, building a global infrastructure for the production of renewable hydrogen and its delivery to market, whether as liquefied hydrogen, ammonia or a liquid organic hydrogen carrier (LOHC), will take a lot of money. It is noticeable that the projects such as these that are underway at present depend on long-term commitment by offtakers and, in many cases, the regulatory and financial support of governments or local authorities (including port authorities).
As a result, this year’s review of terminal construction and expansion activity is as long as ever. And we should not ignore the fact that there are plenty of projects that involve traditional fuels and crude oil. This review does not normally consider LNG terminals, since that has long been a very specific industry, but as the transition moves forward there are plenty of developments linking LNG and hydrogen, as the cryogenic technologies employed are similar.
Gibson Energy, Alberta
Gibson Energy is to build another two 435,000-bbl (70,000-m3) tanks at its Edmonton Terminal, underpinned by a 15-year take-orpay contract agreement with Cenovus Energy. Together with a similar tank already in development, this will add 1.3m bbl of new capacity by the end of 2024, giving the site a total capacity of some 3.0m bbl.
“Gibson is very pleased with the sanction of two new tanks at our Edmonton Terminal, which will further increase our high-quality, long-term infrastructure revenues and drive continued distributable cash flow per share growth,” says Steve Spaulding, president/CEO.
Vopak, British Columbia
AltaGas and Vopak have agreed to further evaluate the development of a large-scale LPG and bulk liquids terminal on Ridley Island in British Columbia, Canada. The projected Ridley Island Energy Export Facility (REEF) will sit adjacent to the existing Ridley Island Propane Export Terminal (RIPET) that the two partners commissioned in 2019, and will be used to facilitate the export of LPGs, methanol and other bulk liquids. Key approvals and permits are already in place for the construction of storage tanks, jetties and other infrastructure on the 77-ha site.
“We are excited to build on our success with AltaGas in Prince Rupert,” says Dick Richelle, Vopak CEO. “Our goal is to create together with partners high quality critical infrastructure for vital products. The strategic location of Prince Rupert, with the shortest shipping distances between North America and Asia, has the potential to increase the trade between Canada and the Asia Pacific region. REEF fits very well within Vopak’s strategic pillar to grow in gas and industrial infrastructure. We look forward to further collaboration with First Nations rights holders and key stakeholders to make this project a reality.”
Vopak, California
Vopak finalised the repurposing of 22 storage tanks at its Los Angeles terminal to offer 148,000 m3 (39m gal) of tankage for renewable fuels, including sustainable aviation fuel (SAF) and renewable diesel, this past October. Vopak
Los Angeles has a long-term agreement for this storage infrastructure with Neste, the world’s leading producer of SAF, renewable diesel and renewable feedstock solutions for various polymers and chemicals industry uses.
“Neste is fully committed to supporting the energy transition in the US as well as globally via working closely together with partners to increase the availability of our renewable fuels. Our cooperation with Vopak shows how repurposing existing fuel distribution infrastructure can accelerate the much needed transition to renewable energy,” says Annika Tibbe, acting president of Neste US.
The Vopak Los Angeles Terminal is strategically located in the Port of Los Angeles and is well-connected for logistics via various modes of transport, including vessel, barge, truck, pipeline and rail. The repurposed storage capacity at the terminal significantly increases the availability and accessibility of Neste’s renewable fuels at critical hubs in the
Los Angeles area, such as SAF for airlines at the Los Angeles International Airport (LAX) and surrounding airports, and renewable diesel for fuelling stations serving road transport.
IMTT has announced plans to consolidate existing bulk liquids storage operations at its Bayonne site in New Jersey to free up some 130 acres (52.6 ha) of waterfront land for redevelopment. IMTT says the move will allow it to serve its bulk customers more efficiently and attract additional economic opportunities to the Bayonne area. There will be some reduction in storage capacity but, IMTT says, the terminal will continue to be the largest in the New York Harbor area.
“We are pleased to announce that IMTT is consolidating a portion of the Bayonne terminal and embarking on a transformational development process for the eastern portion of the property. This will allow us to continue
providing high-quality storage and logistics services on the west side of our property and pursue sustainable development opportunities on the east side,” says Carlin Conner, IMTT’s chairman/CEO. “IMTT has proudly been operating in Bayonne for nearly four decades and we are committed to continuing to provide the safe and dependable services our storage and logistics customers rely on, while also preparing the east side of our property for commercial activity that will support growth in the community for years to come. We are eager to work with the city of Bayonne, the state of New Jersey and other various stakeholders on a plan that will provide significant economic and environmental benefits to Bayonne and the broader New York metropolitan area.”
Kinder Morgan commissioned the renewable feedstock storage and logistics hub at its Harvey facility in Louisiana last year; the site serves as a US hub for Neste.
Kinder Morgan has also started work on a planned $52m project to create a renewable diesel and SAF feedstock storage and logistics facility at its Geismar River Terminal in Louisiana; the new capacity, which will include heated tankage, is supported by a long-term customer commitment and is expected to be in service in fourth quarter 2024.
Enterprise Products Partners has put the first phase of its Texas Western (TW) Products System into service, with the start of truck loading operations at its new Permian terminal in Gaines County, Texas, this past March (above). The terminal has some 900,000 bbl of storage capacity for gasoline and diesel and truck loading capacity of 10,000 bpd. Enterprise expects that the rest of the system, which includes terminals in New Mexico and Colorado, to be in service later in the first half of this year.
“Once completed, the TW Products System will provide supply reliability and diversity to
the historically underserved gasoline and diesel markets in the southwest United States,” says AJ ‘Jim’ Teague, co-CEO of Enterprise’s general partner. “By repurposing segments of our integrated Gulf Coast midstream network, which features access to the largest refining complex in the US, representing more than 4.5m bpd of capacity, the TW Products System will provide retailers access to alternative sources of refined products, which should result in lower fuel prices for consumers in West Texas, New Mexico, Colorado and Utah.”
Enterprise has also received a deepwater port licence from the US Maritime Administration (Marad), enabling it to move forward with the development of the planned Sea Port Oil Terminal (SPOT) offshore crude oil loading terminal. The offshore platform will be located some 30 nm off the coast of Brazoria County, Texas in 115 feet (35 metres) of water and will be capable of loading 2m bbl per day. The plan includes construction of dual 36-inch bi-directional pipelines to connect the platform to the planned Oyster Creek crude oil terminal some 10 miles inland.
Use of SPOT will obviate the need for offshore loading of VLCCs by ship-to-ship transfer from smaller tankers, significantly reducing crude oil vapour and other greenhouse gas emissions, Enterprise says. “With US exports of crude oil at 4m bpd, SPOT offers a more environmentally friendly, safe, efficient and cost-effective way to deliver crude oil to global markets,” says Teague.
Howard Energy Partners (HEP) last year completed a significant expansion of its Port Arthur terminal to support Diamond Green Diesel’s new renewable diesel production facility at the nearby Valero refinery. The work included a new dock, which has opened up capacity for third-party shippers. In addition, HEP has commissioned new infrastructure to handle refinery-grade and polymer-grade propylene, included pressurised storage, rail transloading spots and associated pipelines to connect the terminal to a nearby major chemical production plant.
HEP’s Port Arthur terminal now offers almost 2m bbl (318,000 m3) of tank storage
capacity, 16 miles (26 km) of rail track served by two railroads, three barge docks, two deepwater docks capable of handling Panamax vessels, and pipeline connections to local refineries and industrial plants.
During the third quarter of 2023, Kinder Morgan commissioned a new 30,000-bbl (4,770-m3) butane sphere at its Pasadena terminal, helping meet growing butane demand for in-tank gasoline blending.
Odfjell Terminals US has completed the new Bay 13 at its Houston site, adding nine new tanks with a combined capacity of 32,400 m3 to increase the site’s overall capacity by 9 per cent to more than 410,000 m3. The new tank bay includes a combination of stainless steel and carbon steel tanks, designed specifically for the storage of specialty chemicals. Each tank has been engineered with positive pressure systems and full automation, underscoring Odfjell Terminals’ dedication to minimising emissions and environmental impact.
“As we continue to invest in our assets, we are proud to have developed a new tank bay that will set the standard for our business with state of the art automation and controls with enhanced operating flexibility that prioritises both environmental sustainability and operational efficiency,” says John Blanchard, CEO of Odfjell Terminals US.
Odfjell Terminals Houston has further growth potential at an undeveloped plot known as ‘The Point’, which has direct access to the Gulf of Mexico, avoiding the congested Houston Ship Channel. There is the possibility, depending on demand, for the construction of some 140,000 m3 of new tankage together with two jetties for chemical tankers of up to 45,000 dwt.
Stolthaven Terminals has confirmed an expansion and upgrade programme for its US terminals to meet its customers’ growing needs for specialist storage and handling services. The work will include increasingly automated operations, additional specialist services for customers and the installation of
new tanks, which will significantly increase Stolthaven Terminals’ current total US storage capacity of 954,491 m3
Guy Bessant, president of Stolthaven Terminals, says: “We are pleased to be able to expand our US operations and enhance our offering to customers, especially given fluctuating market conditions. We remain committed to meeting the needs of our customers in the bulk liquid and gas industry, so we are continuing to invest in our state-ofthe-art storage and handling services for these products. At the same time, we are exploring new opportunities for value-add services, both for the storage of chemicals and to support the green-energy transition.”
Oiltanking, Brazil
Oiltanking Logística Brasil last year established a joint venture with Grupo Edson Queiroz and Copa Energia to develop a greenfield LPG terminal in Suape, Pernambuco to meet LPG import demand in the north-eastern states of Brazil. The planned terminal will be the largest refrigerated onshore LPG storage facility in the country and the only one capable of handling fully laden very large gas carriers (VLGCs). Development of the project is subject to
anti-trust approvals; if it goes ahead as planned, operations are expected to begin in first quarter 2026.
Ultracargo, Brazil
Ultracargo is expanding operations in the north of Brazil, where it is currently planning an expansion of the Itaqui terminal and has started work on construction of a new facility in Palmeirante, Tocantins. The two sites will be linked by rail.
Excavation work at Palmeirante started in January and the terminal is expected to be completed by September with operations starting in early 2025. It will have 12 tanks for the storage of gasoline, diesel and ethanol, with a total capacity of 23,000 m3. The Palmeirante terminal will receive and ship product by road and rail, facilitating the delivery of fuels in the states of Maranhão, Tocantins, Pará and Mato Grosso.
“By building another terminal, we are continuing the strategy of transforming Ultracargo into a company of integrated logistics solutions, connecting the Brazilian coast to the interior of the country. The rail connection will ensure more safety and sustainability to the transport of liquid bulk, and is in line with our expectation of offering
more efficient options to our customers”, says Ultracargo’s executive director of operations and engineering, Leopoldo Gimenes.
Odfjell has expansion projects in hand at its related terminals in South America, with 22,000 m3 of new carbon steel tankage due in service at the Terquim terminal in Mejillones, Chile during the first half of this year. Granel, its Brazilian affiliate, also has expansions underway at its terminals in Rio Grande and Santos.
ADPO is currently working on a new tank pit at its site in Kallo, Belgium, where it will install 23 new storage tanks with a total capacity of 8,100 m3; the small tanks will be used for the storage of liquid fine chemicals for use in the healthcare and life sciences markets. The new tank pit TP 26 is being built on the plot of a former warehouse, now demolished, next to the recently completed tank pit 25.
“The demand for extra storage is high due to the increased import traffic,” says Filip De Dycker, managing director of ADPO. “The high energy prices and wage costs in Europe have put the European process industry at a competitive disadvantage. The production cost is currently cheaper in America, Asia and the Middle East. Because the raw materials –which are normally transported directly between the factory and the downstream user in Europe – are now mainly imported, additional tank storage is required.”
It is expected that TP 26 will be put into service early in 2024.
ITC Rubis began construction of tank pit 7 at its Antwerp terminal this past September. The new pit will add nearly 40,000 m3 of new tank capacity in carbon and stainless steel storage capacity, as well as a new liquid loading station for rail tanks and road tankers.
LBC Tank Terminals is expanding its Antwerp site and will build 28 new tanks to add some 80,000 m3 of new capacity along with new loading stations for road tankers and rail tank
cars. The new tankage will be dedicated to the efficient storage of base oils and chemicals to meet growing demand.
“With high energy prices, chemicals production in north-western Europe is under increasing competitive pressure, while Middle Eastern and US-based producers have an advantage with access to lower priced feedstock,” says Erik Kleine, general manager Europe at LBC. “We see a healthy and consistent growth in import of base oils and chemicals into Europe, where Antwerp is a prime location for these growing product flows.”
The project is expected to be completed and in operation in the fourth quarter of 2025.
Noord Natie’s executive board has approved the next expansion projects at its Antwerp terminal. Tank pit R will be dedicated to the storage of base oils and specialty chemicals in a series of tanks of 2,500 and 3,000 m3 capacity, with a total capacity of 27,500 m3. The tanks will be linked by dedicated lines to jetties and truck loading racks and may be equipped with vapour return, heating or
insulation, depending on customer demand. Tank pit R is due in service in the first quarter of 2025.
The news came shortly after commissioning of six duplex stainless steel tanks in the new tank pit U in November 2023, adding some 36,000 m3 in new capacity.
Noord Natie also has further potential expansion projects in hand, which could take total capacity at the site to close to 580,000 m3 by 2027.
The planned Hanseatic Energy Hub (HEH) is ready to move forward, following a final investment decision by its partners and after concluding the permitting phase. The founding partners, Partners Group, Enagás, Dow and the Buss Group have now successfully secured financing and awarded the construction contract to Técnicas Reunidas and its partners, FCC and Enka. Enagás has also increased its shareholding to 15 per cent and will be the site operator.
The future-flexible energy hub will be built at the Stade Industrial Park, near Hamburg,
and is expected to involve an investment of around €1bn. HEH is due to be commissioned in 2027 and will initially serve as an import location for LNG, synthetic natural gas and liquefied bio-methane; in this phase it will replace the existing floating storage and regasification unit at the port. Subsequently, it is expected that HEH will be used for the import of green ammonia.
Mabanaft is progressing its plan to establish a large-scale terminal for green energy alongside the Blumensand terminal of its subsidiary, Oiltanking Deutschland, in Hamburg. The plan was kicked off in late 2022 when Mabanaft signed an agreement with Air Products, which is planning to build a plant for the production and handling of hydrogen, for which imported green ammonia will be the feedstock.
Since then, Mabanaft has been through a voluntary hearing to establish the scope of works, and in February this year successfully completed the so-called scoping meeting, initiated by Hamburg’s Authority for Environment, Climate, Energy and Agriculture (BUKEA), in the run-up to the approval procedure for the construction of the terminal.
“Our planned ammonia import terminal on our land in the Port of Hamburg has the
potential to bring significant quantities of energy products to Hamburg that can support the energy transition,” says Philipp Kroeppels, director of new energy at Mabanaft. “A voluntary environmental impact assessment along the way is very important to us. We are now getting ready to officially initiate the permit process.”
Advario has managed to gain a foothold in the crowded Rotterdam port space through an agreement to acquire a plot of land in the Botlek area from Aluminium & Chemie. The site will provide Advario with the opportunity to develop, build and operate a bulk liquids storage terminal designed to help its customers and partners successfully transition to cleaner energy.
“We are very pleased to have secured this strategic location in the Port of Rotterdam,” says Bas Verkooijen, Advario’s CEO. “This is another important step in the delivery of our long-term strategy to play a frontrunner role in supporting the energy transition. The site’s strategic location, ample size, and waterfront access offer us an excellent opportunity to enter one of the leading energy and chemical hubs in Europe. Advario looks to develop a new and future-
focused storage terminal in close cooperation with our customers, industrial partners, and the Port of Rotterdam.”
Aluchemie will now prepare the site for handover by demolishing and removing all above- and underground structures and remediating the soil. It is aiming to finish this work by the end of 2025, after which Advario will begin construction on its terminal for future fuels.
This past December, Evos signed a letter of intent with Value Cargo, sister company of Value Maritime, which operates the Filtree onboard carbon dioxide capture technology. At present, Value Group uses tank containers to store the captured CO2 before it is delivered to horticultural users in the Netherlands; it is now looking for a central location in Rotterdam where it can receive, store, treat and redeliver that CO2 as the market develops.
Under the terms of the LOI, Evos will build two 2,000-m3 storage tanks for absorption liquids to accommodate Value Carbon’s growing needs. The Evos terminal in Rotterdam enjoys an advantageous proximity to Rotterdam Shortsea Terminal (RST) in the Eemshaven and deepsea terminals at the Maasvlakte. It is strategically positioned next to CO2 infrastructure, with ready access to essential steam and electricity supplies. The surrounding area hosts a cluster of experts specialising in CO2 processing, providing valuable support for the purification, liquefaction and storage of CO2, all key to realising the growth of Value Carbon.
“This partnership is a promising development that will help both Value Carbon and Evos work towards our shared sustainability goals,” says Rolf Bakker of Value Carbon. “Having a central location such as this, where the entire process of treatment, storage and redelivery can take place, offers a considerable boost in efficiency, especially
Also in this issue, we explore the value of life cycle assessments, the new Bulk Storage Terminal Technician Apprenticeship and the many initiatives that are taking place in the bulk storage and energy infrastructure sector.
Tank storage provides an essential interface between sea, road, rail and pipeline logistics.
Insight is published by the Tank Storage Association, the voice of the UK’s bulk storage and energy infrastructure sector.
To contact the editorial team, please email info@ tankstorage.org.uk
TSA Insight Team
Davidson, Jamie Walker, Nunzia Florio
CONNECT WITH US
@UK_TSA
Tank Storage Association
TSA
@uk_tsa
CONTACT
Tank Storage Association
Devonshire Business Centre Works Road
Letchworth Garden City Herts. SG6 1GJ
United Kingdom
Telephone: 01462 488232
TSA has used reasonable endevours to ensure that the information provided in this magazine is accurate and up to date. TSA disclaims all liability to the maximum extent permitted by law in relation to the magazine and does not give any warranties (including any statutory ones) in relation to its content. Any copying, redistribution or republication of the TSA magazine(s), or the content thereof, for commercial gain is strictly prohibited unless permission is sought in writing from TSA. Claims by advertisers within this magazine are not necessarily those endorsed by TSA. TSA acknowledges all trademarks and licensees.
Welcome to the summer issue of Insight. There has been a strong focus on energy sustainability, security and affordability, as well as on policy to tackle the “energy trilemma”. For example, the Energy Act 2023 aims to deliver a cleaner, more affordable, and more secure energy system that is fit for the future. It covers a wide range of areas from oil and gas to nuclear, as well as nuclear fusion, hydrogen, carbon capture and storage and renewable energy. In addition, the UK’s first critical imports and supply chain strategy aims to build resilient supply chains and safeguard critical imports. In this issue of Insight, we explore latest developments as well as the many innovations and initiatives that are taking place in the bulk storage and energy infrastructure sector as it seizes opportunities ahead. I hope you enjoy this new edition of the magazine and don’t forget to follow us on social media.
Tank Storage Associa on Peter04
Training for new fuel tanker drivers - good practice
The DFDF strongly supports the recruitment of new drivers and recognises the critical need for extensive training and assessment of potential newcomers.
06 The bulk storage and energy infrastructure sector: in conversation with Peter Davidson
There has been a strong focus on energy sustainability, security and affordability, as well as on policy to tackle the “energy trilemma”.
09 Government announces consultation on the introduction of a UK CBAM
A new consultation is seeking views on a carbon border adjustment mechanism.
10 Adapting to climate change
The Chemical and Downstream Oil Industries Forum (CDOIF) has recently published a key guide on adapting to climate change.
12 Inherent sustainability: the value of life cycle assessments
A thorough LCA will help you to determine a product or process’s environmental impacts, from extraction of raw materials to disposal.
15 UK Government rolls out British Industry Supercharger
New measures will cut network charges and provide exemptions from electricity costs for firms in sectors like steel, metals, chemicals, cement, glass and paper
16 Introducing the new Bulk Storage Terminal Technician Apprenticeship
The new apprenticeship standard has been hand-built by the sector to address the specific demands of bulk storage operations.
19 Teamwork Security and Training Services
Ltd. celebrate their 20th anniversary
Teamwork Security and Training Services Ltd. is now the leading ISPS consultancy and training firm in the UK, delivering its services to a large number of UK and international ports.
20 UM Terminals makes multi-million pound investment in Liverpool terminal
UM Terminals has made a multi-million pound investment in one of its key strategic terminals.
22 The risk assessment toolbox – do you know everything you need?
RAS explores some of the tools to consider when it comes to performing a risk assessment of your operation.
24 Enhancing sustainability in industrial operations and maintenance
Innovative emissions reduction, degassing and VRU back-up services for a wide range of applications and industries.
TThe DFDF strongly supports the recruitment of new drivers and recognises the critical need for extensive training and assessment of potential newcomers.
he Downstream Fuel Distribution Forum (DFDF) was established in 2012 to provide a collaborative platform for the discussion and resolution of issues relating to health and safety as well as training in the downstream fuel industry. Its membership ranges from hauliers, to trade associations, government departments - namely the Department for Transport and the Department for Energy Security and Net Zero - and trade unions.
As part of its early collaborative work, in 2014, the DFDF launched the Petroleum Driver Passport (PDP) Scheme, a voluntary industry scheme, supported by government, designed to ensure that all tanker drivers in the UK are trained and assessed to a consistent standard in loading, transporting and offloading petroleum fuel products from road tankers. Ten years on from its launch, over 11,000 tanker drivers in the UK hold a PDP card demonstrating to terminal operators, hauliers, customers and the wider public that they have been trained to the same consistently high and externally
verified standard in all aspects of tanker driving from pre-vehicle checks to loading, driving and discharging.
The fuel distribution sector is reliant on competent drivers. As it looks to the future and to making the most of opportunities ahead in terms of existing and new fuel products, the sector will need to address both immediate and future skills shortages by attracting, training and retaining new tanker drivers. Indeed, against the backdrop of a high proportion of the workforce set to retire in the short to medium term who will take with them critical skills, knowledge and experience, as well as competition for talent more widely, the sector must act now if it is to secure a resilient workforce for tomorrow.
The DFDF strongly supports the recruitment of new drivers and recognises the critical need for extensive training and assessment of potential newcomers prior to them being able to work unsupervised. In this context, the DFDF is clear that the provision of good quality induction and training will not only help to maintain high standards of safety in the industry but also boost the attraction of the sector to new recruits. In order to aid this process, the DFDF has recently consulted with its haulier members to provide some good practice advice on the training and assessment of new drivers with no previous fuels experience.
The good practice advice is clear
in that new drivers must hold the appropriate class of driving licence and ADR. As part of their training, new drivers will also need to pass their written and practical PDP assessments. DFDF further recommends that the initial preemployment assessment includes a driving assessment as well as an interview stage to ascertain whether the person demonstrates the required attributes to be a tanker driver.
The next step would be for the employer to provide the new starter with a training period with a fuels specific driver trainer. This should include in-depth classroom theory, vehicle and trailer familiarisation, terminal inductions, as well as familiarisation in loading and unloading. Before progressing any further, new drivers should have successfully completed this initial training period. The recommendation is that this is followed by a further period of training/supervision by a driver trainer, with the new driver initially only observing, before progressing to completing loading and delivery workloads under strict supervision, with the new driver gaining experience and confidence at delivery sites. During this period, time needs to be allowed for a driver trainer to coach and assess the driver for safe and efficient driving and slow speed maneuvering.
When the driver trainer/driver coach deems the new driver competent, the new driver needs to take and
pass their written and practical PDP assessments. No unsupervised work should take place until the new driver has passed a full assessment and is able to demonstrate the ability to work to a safe standard aligned with industry and the employer company’s own standards, and holds all the necessary qualifications, including PDP. Finally, to be able to load unsupervised at a terminal, the new driver will be required to be signed off as competent, typically by demonstrating the ability to load three loads at the terminal in question.
For those new drivers joining retail, to gain the experience of forecourt delivery’s and locations, they will be required to deliver safely by having a Site Specific Risk Assessment (SSRA) for that Petroleum Filling Station (PFS), and by being aware of ACoP L133 and the Dangerous Substances and Explosive Atmospheres Regulations (DSEAR).
Most crucially, it is noted that employers should work on the basis that the training period may need to be extended depending on feedback from the driver trainer, and also taking into account the new driver’s own feedback/confidence.
Another important aspect is that of ensuring that new drivers feel welcomed and supported, especially during their first six months. Employers could consider the establishment of formal mentoring programmes with experienced staff members i.e. buddy
up a new driver with a Driver Mentor/ Coach once they have completed their PDP practical and terminal pass out.
As ever, ongoing follow-up and assessment is vital to maintain standards. As part of the PDP Scheme, all drivers will be required to take a practical assessment and classroom refresher training every year. Additional good practice could include: ongoing periodic training; spot checks; sending out a new starter out with a trainer for a day after a few weeks of running solo as a proactive attempt to address any issues that may have crept in before these become habits; write to new drivers to flag the risks associated with the job becoming unconscious, with a reference to the conscious competence models that are out there.
The DFDF is committed to continuing to provide a platform for the discussion of training in the downstream fuel industry and the important work of attracting, training and retaining the next generation of tanker drivers. This good practice advice is testament to this commitment, and the high priority being given to supporting the provision of good quality induction and training for new drivers.
For more information, please visit www.pdpassport.com
TThere has been a strong focus on energy sustainability, security and affordability, as well as on policy to tackle the “energy trilemma”.
Peter Davidson, Chief Executive, Tank Storage Associationhe Tank Storage Association (TSA) represents the interests of over 70 member companies engaged in bulk storage, energy infrastructure and the provision of products and services to the sector. Collectively, its members operate 309 terminals and distribution hubs in the UK and have over 11 million cubic metres of storage capacity in the United Kingdom (UK) and Republic of Ireland (ROI). TSA’s members provide and support an essential interface between sea, road, rail and pipeline logistics for many different substances including transport and heating fuels, chemicals, animal feed and foodstuffs.
Most recently, the “energy trilemma” of security, affordability and sustainability has come into sharper focus owing to recent shifts across energy markets and in the wider geopolitical landscape. There has been a strong focus on energy sustainability, security and affordability, as well as on policy to tackle the “energy trilemma”. For example, the Energy Act 2023 is described by the government as the
“largest piece of energy legislation in a generation”,1 and aims to deliver “a cleaner, more affordable and more secure energy system that is fit for the future.”2 It covers a wide range of areas from oil and gas to nuclear, as well as nuclear fusion, hydrogen, carbon capture and storage and renewable energy.
Part 12 of the Act, which came into force on 11 January 2024 and is aimed at addressing matters around energy security of supply, gives the Secretary of State for Energy Security and Net Zero new key powers, including powers to impose obligations on companies to take such actions as thought necessary to ensure the resilience of supply and continuity of certain core fuels. It also creates a duty on core fuel sector participants to report a notifiable incident,3 such as an incident which affects their relevant activities or assets in such a way as to create a significant risk of or cause, disruption to or failure of the continuity of core fuel supply. Core fuels are defined as crude oil based fuels and renewable transport fuels4 and core fuel sector activities are defined as activities such as storing oil or renewable transport fuel; handling oil or renewable transport fuel; the carriage of oil or renewable transport fuel by sea or inland water; transporting oil or renewable transport fuel by road or rail; conveying oil or renewable transport fuel by pipes; processing or producing oil or renewable transport fuel (whether by refining, blending or otherwise).5
The Act further sets out the thresholds specifying whom the statutory duty to report an incident applies to. The thresholds specify that the measure applies to operators or facility owners with an annual capacity over 500,000 tonnes.6 A facility owner is defined as the owner of a pipeline, terminal, or other facility or infrastructure which is used, or any part of which is used, for the purposes of core fuel sector activities. Guidance on the duty to report as well as on financial assistance powers have been published on 18 January 2024 and can be found on the UK Government’s website.
But there is more. Part 4 of the Act covers new technology. For example, the Act notes that the Secretary of State must carry out a public consultation, hosted by the Department for Transport, on the options for designing and implementing a Sustainable Aviation Fuel (SAF) revenue certainty scheme7 in order to secure consistent fuel supply. This mechanism is set to be introduced by the end of 20268 and will run in parallel with a mandate requiring 10% of fuel supply to be SAF by 2030 rising to 75% in 2050.
The Act further states that a report to Parliament on the progress made towards the development of a sustainable aviation fuel revenue certainty scheme will have to be laid within 18 months from 26 October 2023.9 And Part 2 of the Act covers carbon dioxide capture, storage etc. and hydrogen production, transport
and storage. The Energy Act 2023 also contains many other provisions in areas such as heat and energy efficiency, electricity and gas sector governance, nuclear, offshore wind and upstream oil and gas.
The UK government has also published its first critical imports and supply chain strategy aimed at building resilient supply chains and safeguarding critical imports. The new critical imports and supply chain strategy,10 which was published on 17 January 2024, focuses on the reliable access to the critical imports and goods needed now and in the future. The strategy defines critical imports as “those goods imported into the UK which are critical to the UK security and prosperity”, further noting that “this primarily refers to goods which are essential for the operation of the UK’s designated Critical National Infrastructure (CNI) sectors and / or to the success of the government’s five growth sectors”.
CNI currently encompasses the energy, chemicals, transport, civil, nuclear, communications, defence, emergency services, finance, food, government, health, space and water sectors. The five growth sectors, as set out by the Chancellor of the Exchequer in January 2023, are creative industries, digital technology, green industries, life sciences and advanced manufacturing. A new Critical Imports Council is also expected to be set up shortly to bring together businesses in critical and
growth sectors and government to identify risks to critical imports and develop an action plan.
Against this backdrop, the Tank Storage Association continues to highlight the central role terminals play in the supply security and resilience of the products that are critical to our daily lives. It will continue to work with the government and key stakeholders to help to deliver on the opportunities and innovative solutions that will support the achievement of the UK’s climate neutrality targets, shining a light on the proactive steps the sector is taking to open up new possibilities.
Good leadership is key to safe operations. Tell us more.
The TSA is committed to ensuring that safety lessons and best practice are shared across the sector wherever possible, and our dedicated Safety, Health and Environment (SHE) committee is key to achieving this. I recently watched a BBC documentary titled The Space Shuttle that Fell to Earth which explores the events leading up to the failure on re-entry of the Columbia shuttle in 2003 and the loss of all seven astronauts. What was of most concern was that many of the failures that led to the accident were due to poor management decisions and leadership. The documentary highlighted several areas of particular concern: a management hierarchy that did not encourage the sharing of concerns and potential issues; silo working which did not promote
cooperation between teams; schedule and cost influencing decisions that could have an impact on safety; not reacting to the small things, such as the loss of insulation from the main fuel tank, when this was indicating a much larger potential risk; and not spending the time to get the data that would prove or disprove that those small things could actually result in something big. But there were many more.
Many sectors have a defining moment – when an accident or incident forces them to change how they think. For the UK’s tank storage sector that was the Buncefield explosion and fires of 2005. For the past 15 years, I have done something every day that relates to the recommendations arising from that incident and it is still at the forefront of many of the activities that we engage in at the TSA. It is incredibly important that those lessons are not lost. Of course, the TSA is involved in many activities, from net zero to cyber security, but our core focus remains safety. It is our number one priority: if we cannot protect our people, the environment and our assets we have no business. Watching the documentary brought home to me that all businesses that have the potential to harm people and the environment have the same challenges and can learn the same lessons. It doesn’t matter if you make red widgets or send people into space, the fundamentals of managing risk, and importantly leadership in safety, are the same.
The TSA, for example, also leads the COMAH Strategic Forum’s Leadership Working Group, which has published several articles including Managing
the risks that can destroy your business and Learning lessons from leadership interventions. The TSA has also published its own commitment to good major hazard leadership. All these publications refer to the original Process Safety Leadership Group’s Principles of Process Safety Leadership These principles are as relevant today as they were when published in 2009 in response to Buncefield incident.
I would encourage anyone to watch the documentary on the Columbia shuttle disaster. I hope it inspires and educates those in our sector and beyond as it did me, whilst reaffirming why safety should be our number one priority.
1. The Rt Hon Claire Coutinho MP, Department for Energy Security and Net Zero, Press Release, ‘New laws passed to bolster energy security and deliver net zero’, 26 October 2023
2. Energy Bill Summary Impact Assessment, April 2023
3. Energy Act 2023, s. 276
4. Ibid., s. 268(4)
5. Ibid., s. 268(2)(a)-(f)
6. Ibid., s. 274(2)(a)-(c)
7. Energy Act 2023, s. 158
8. Department for Transport, Revenue certainty mechanism for SAF: delivery plan, 4 September 2023
9. Energy Act 2023, s. 158(5)
10. Department for Business and Trade, UK critical imports and supply chains strategy, 17 January 2024 Author
Peter Davidson is TSA’s Chief Executive Officer and is responsible for all aspects of advocacy and lobbying on behalf of the sector, and for promoting process safety leadership, helping members achieve excellence in this area and work toward becoming high reliability organisations. Peter works in close collaboration with the UK Government and Regulators and is a leading member of a number of cross-industry committees, Process Safety groups and the Federation of European Tank Storage Associations.
The Tank Storage Association (TSA) is an industry based organisation whose members are engaged in the storage of bulk liquids and the provision of products and services to the sector. TSA members support an essential interface between sea, road, rail and pipeline logistics for a diverse range of essential products, including transport and heating fuels, chemicals, animal feed and foodstuffs. They provide the infrastructure required to import, store, blend and export liquid products essential to our daily lives.
Decarbonising the UK’s industry is a core part of the government’s plan to achieve net zero. The UK is committed to reduce greenhouse gas (GHG) emissions by at least 100% on 1990 levels or achieve net zero by 2050 under the Climate Change Act 2008, to reduce its GHG emissions by at least 68% on 1990 levels by 2030 under its updated Nationally Determined Contribution under the Paris Agreement, and has introduced legally binding carbon budgets that place a restriction on the total amount of GHGs the UK can emit.
However, there is concern that efforts could be undermined by ‘carbon leakage’, which is the movement of production and associated emissions from one country to another due to different levels of decarbonisation effort through carbon pricing and climate regulation.
Against this backdrop, in 2023, the Department for Energy Security and Net Zero and HM Treasury consulted on the risk of carbon leakage and a range of potential mitigation measures in a consultation titled ‘Addressing carbon leakage risk to support decarbonisation’. The consultation sought views on the nature and extent of carbon leakage risk to UK industry and potential design and implications of a potential Carbon Border Adjustment Mechanism (CBAM) in the UK. After considering the information gathered as part of
the consultation, on 18th December 2023, the government published its response and announced that it would introduce a UK CBAM from 1st January 2027 on imports of certain carbon-intensive goods from the following sectors: aluminium, cement, ceramics, fertilisers, glass, hydrogen, and iron and steel. In addition, it announced the intention to work with industry to establish voluntary product standards that businesses could choose to adopt to help promote their low carbon products to consumers, and to develop an embodied emissions reporting framework that could serve future carbon leakage and decarbonisation policies. These measures will be subject to technical consultation in 2024.
Meanwhile, on 21st March 2024, HM Treasury and HM Revenue & Customs launched a consultation seeking views on proposals for the design and administration of the UK CBAM. The consultation will close on 13th June 2024. The UK CBAM will apply both to the import of ‘complex goods’ and ‘precursor goods’. It will be a charge on the emissions embodied in relevant imports into the UK that take place on or after 1st January 2027 (not payable until after the end of an accounting period).
The consultation can be found on the UK government’s website.
The Chemical and Downstream Oil Industries Forum (CDOIF) has recently published a key guide on adapting to climate change.
Many businesses are vulnerable to severe weather conditions and other climate change impacts. While flooding is the most common and widespread natural hazard event that occurs in the UK, other natural hazards, including storms and high winds, lightning, cold weather, extreme heat, tidal surge, and sea level rise can all impact a business, causing disruption to operations or harm to people and the environment.
With many Control of Major Accident Hazards (COMAH) regulated businesses, and several sites designated as Critical National Infrastructure, understanding the risks of climate change on the terminals sector is critical. However, conducting risk assessments in this area can be challenging. To address these concerns, the Chemical and Downstream Oil Industries Forum (CDOIF) has recently published a key guide for operators of sites on adapting to climate change.
The guidance provides a step-by-step process to help operators understand
potential risks and the ways in which these can be mitigated.
When considering climate change, businesses should have regard to both mitigation and adaption. Mitigation refers to the implementation of measures within the business to reduce the sources of greenhouse emissions (or by introducing technologies to absorb them) and it is fundamental to help in achieving net zero ambitions. Adaption means understanding climatic changes and adjusting business practices and processes accordingly to minimise potential impacts. While these two concepts can be considered separately, businesses that integrate both can often develop a more resilient and robust approach.
Process safety leadership methodologies have been encouraged for some time, and these principles should also be adopted for climate change. These include ensuring that senior management teams understand the concepts of climate change and their responsibilities to both mitigate and adapt. Furthermore, they should ensure appropriate policies and plans are in place, that these are funded and resourced, and that there are mechanisms to provide assurance that these policies are being implemented.
An adaptive management approach to risk assessment, as part of a wider management system, should promote
a cycle of continuous improvement. At the beginning of the cycle, businesses should seek to carry out a major accident hazard identification and evaluation process – determining what the potential major accident hazards are and evaluating whether they are relevant to the business. This will include industrial accidents that can been caused by a natural event, often exacerbated by climate change – commonly referred to as Natural Hazards Triggering Technological Accidents (NaTechs).
Common NaTech characteristics include existing control measures that are not designed for present and future environmental extremes, events that have a wide geographical impact – for example those that result in large areas of disruption to power, communications and supply chains - and multiple simultaneous major accidents brought about by a single event, such as a tidal surge.
For equipment that may be susceptible to NaTechs, a risk assessment should first evaluate available detailed data, such as meteorological, flood and coastal risk, river flow, sea level, temperature, fire risk and geological data. Also, topographical, general arrangement, equipment data, design parameters, vulnerabilities, and site maps / general arrangement drawings relevant for weather related threats and climate change impacts should be assessed. A risk analysis, using all data, can be carried out to determine
whether the equipment under review remains within the safe operating envelope or if there is increasing risk of failure with the potential to lead to an increasing major accident hazard risk. This analysis should compare present day and potential future risk (people and environment) to tolerability criteria.
A proportionate sensitivity analysis of the risk assessment should be carried out. This is especially important where climate change influenced risks are high and risks may not remain tolerable in the future. Using data from a wider range of climate projections can help to improve understanding of how climate impacts may change with different future scenarios and, in turn, what that might mean for the site’s vulnerability and major accident risk.
Following the risk assessment and sensitivity analysis, an As Low As Reasonably Practicable (ALARP) demonstration can be made. If present day risks are not deemed to be ALARP, then further risk reduction measures should be appraised to find those control measures that are reasonably practicable to implement. Where future risks may not be deemed to remain ALARP due to changing weather threats and climate impacts, appropriate management or other relevant measures to ensure risk will remain ALARP, both until the next review point and over the installation’s lifetime, should be considered.
Those measures identified as part of the ALARP demonstration can be planned (at an appropriate time), adopted and implemented as required, to ensure major accident hazard risk is ALARP both in the present and as predicted in the future. Implementation of adaption plansto put in place measures to ensure major accident hazard risk is ALARP - should be monitored and reviewed. This should include an assessment of any changes in knowledge, such as emerging climate predictions or weather changes that could impact the original assessment. Appropriate metrics should be shared with senior management teams to ensure that they understand the process and progress of adaption plans, can resource and fund them appropriately and consider the potential impacts of other decisions made.
The published CDOIF guidance, Adapting to Climate Change, provides extensive information on adaptive management approaches to climate risks, together with worked examples and other resources. References are also provided to other sources of information, including ISO 14090 which is the international standard detailing the principles, requirements and guidelines for adaptation for climate change.
All CDOIF publications are currently hosted on the Process Safety Forum’s website which can be accessed at www.p-s-f2.org.uk
OA thorough LCA will help you to determine a product or process’s environmental impacts, from extraction of raw materials to disposal.
ne of the first principles involved in making inherently sustainable decisions is carrying out a Life Cycle Assessment (LCA); a thorough LCA will help you to determine a product or process’s environmental impacts, from extraction of raw materials to disposal. This should be considered early in the development of a project and should also be carried out during any options assessments.
For businesses looking to explore LCAs and the benefits they can deliver, the article below shares more details about concept, practice, and project examples.
Owing to the rise in incorrect environmental claims and ‘green washing’, in recent times LCAs have garnered a lot of attention in the press and public, having mostly been the domain of academia previously. These controversies highlight the importance of adopting robust, proven approaches to LCAs. But what is an LCA?
In our day-to-day lives, most of us try
to reduce our impact on the planet –however, we have limited foresight of unforeseen consequences across the lifecycle of the products we use. For example, you could buy an electric car in hopes of reducing carbon emissions from the use of the car, but the manufacturing stage of the batteries involves mining minerals that cause pollution and could be sourced unethically. Similarly, you could switch to a plant-based diet to better the environment but eat much more soy, which is imported from overseas.
An LCA study in these instances would empower you with the knowledge to make more reasoned and ultimately sustainable choices. It does this by quantifying the environmental (and sometimes social) impacts of a product or service across its entire lifetime, usually against multiple criteria.
Each LCA study is unique and tailored to the client’s objectives, which affect the scope of the LCA. For instance, one might choose to adopt a ‘cradle to grave approach’ which assesses all stages from raw material to disposal. The most comprehensive approach would be ‘cradle to cradle’ which assess all life-cycle stages, up to the point of re-use, meaning the entire environmental impact of the product is revealed.
For those seeking a more simple and cost-effective approach, a ‘cradle to gate’ outlook should be adopted,
this measures the impacts from the raw material extraction stage to the manufacturer’s gate.
The scope is not the only defining feature of an LCA, as the type of LCA will dictate the number of requirements the LCA will have. An LCA conducted for internal purposes will have less stringent requirements than one used for external communications, which should adhere to International Organisation for Standardisation (ISO) standards 14040 and 14044 as best practice. ISO 14040 sets out the key features and phases of the LCA including scope, inventory analysis, an assessment of the environmental impacts and interpretation of results.
The requirements of the phases themselves are set out in ISO 14044. LCAs used for marketing purposes will have to follow further ISO sub standards which set out guidelines and definitions for environmental claims regarding products / services, to ensure transparent methodology and reporting.
changes that organisations make.
LCAs are a powerful tool that have a diverse range of applications and can be used to inform decision making in industry government and non-government bodies alike.
Some clients, for instance, may use the results to make comparative claims about the benefits of their products –e.g. being ‘green’ or ‘environmentally friendly’. These claims serve not only to differentiate their products in the marketplace but also to communicate their commitment to sustainability to consumers and stakeholders. More recently, it’s a baseline that most consumers expect them to meet. Through transparent and credible data-driven comparisons, businesses can effectively showcase the environmental benefits of their products and reinforce their brand’s position as a leader in sustainable practices.
improves environmental performance but can also enhance operational efficiency, reduce costs, and enhance brand reputation as a responsible steward of the environment. Moreover, by continually monitoring and reassessing these hot spots over time, companies can continue to adapt and evolve their sustainability strategies to address emerging challenges and opportunities in their supply chains and operations. Alternatively, stakeholders (including investors, consumers, and community groups) increasingly demand transparency and accountability regarding environmental performance. LCAs serve as a robust mechanism for generating credible data and insights in response to these requests.
What are LCAs used for?
While LCAs can’t see into all the details of each decision in everyday life, at a higher level they can help to understand the bigger picture and make more informed decisions on
Other clients may wish to identify the ‘hot spots’ in their life cycle, so that interventions can be made to eliminate or reduce negative impacts. This targeted approach not only
In general, LCAs can aid in supporting regulatory compliance. Many industries and regions of the world have, or are in the process of, bringing in specific regulations that mandate or encourage the LCAs for products or supply chain processes. For example, Environmental Product Declarations (EPDs) are standardised documents that provide transparent and verified information about the environmental impacts of a product throughout its lifecycle. Many countries and regions have developed EPD programs that encourage or require LCAs for certain product categories, such as construction materials or waste packaging.
How can SLR help?
Tank storage sites are often associated
with environmental concerns due to the nature of the substances they store. This, paired with the energy demand of industrial operations, has led operators in pursuit of methods to reduce the carbon footprint of their facilities. One avenue that could potentially be achieved is integrating Solar Photovoltaic (PV), including on spare land and bund walls. There is even the option of flexible PV cells on tank roofs – assuming appropriate electrical and explosion risks have been assessed.
Solar PV has minimal environmental impacts during use, but its impact during manufacture, installation and at end-of-life can prove challenging.
A firm that regularly invests in solar PV farm developments commissioned SLR to investigate these life cycle impacts across numerous environmental criteria.
SLR’s LCA team has practical experience in delivering studies on an extremely wide range of products, technologies, and services. We understand the reputational risks and benefits, and that there is no ‘one size fits all’ approach for LCA, so each project is carefully tailored during commissioning to ensure we deliver on your specific goals, as efficiently as possible.
As part of this project, we gathered data from the client’s preferred technology provider, concerning the quantities of materials used, the manufacturing and installation burdens, and the activities to keep the farm operational during its lifetime. We also anticipated what might happen to the farm’s materials at end of life. All this information was compiled into a life cycle inventory of the materials, energy, emissions, and
wastes associated with the lifetime operation of the facility.
SLR then applied its LCA databases to convert the flows into environmental impacts and compared them against the likely counterfactual impacts from UK grid electricity generated over the same period.
Our analysis delivered two key findings for our investment client:
• Firstly, they learnt the truth about the impacts of their solar power in comparison to UK grid electricity.
• Secondly, they discovered what aspects of the life cycle were causing the biggest impacts, enabling their technology provider to target improvements.
LCAs represent more than just a methodological tool, they embody a commitment to sustainable practices and informed decision-making. As businesses navigate an increasingly complex landscape of environmental challenges and opportunities, the value of LCAs in guiding responsible action and optimising resource use, as well as mitigating risks, cannot be overstated.
Get in touch to see how SLR’s LCA team can support your sustainability objectives. For more information, please visit www.slrconsulting.com
Authors
Euan Munro (Energy Transition Lead – Europe) and Becca Shaikh (Process Engineer).
On 23rd February 2023, the UK government announced the British Industry Supercharger (BIS), a set of measures aimed at making Britain’s strategic Energy Intensive Industries (EIIs) more competitive across Europe, tackle the challenge of indirect carbon leakage and the risk of that the policy costs imposed on EIIs could lead to the displacement of production, and associated emissions.
The BIS underwent a consultation by the Department for Business and Trade from June to August 2023 and responses represented the views of over 2000 organisations, when taking into account bodies who answered on behalf of multiple members. Following the consultation, the government announced its intention to take forward measures to compensate EIIs for a portion of their network charges.
In April 2024, the government launched the BIS ‘to bring energy costs for key industries in line with other major economies, levelling the playing field for UK businesses’.
The government advises that ‘support will be made available to sectors particularly exposed to the high cost of electricity including steel, metals, chemicals, cement, glass and paper, and is expected to be worth between £320 million - £410 million in total savings to UK businesses’ in 2025. According to the government,
the British Industry Supercharger’s measures will fully exempt eligible firms from certain costs linked to renewable energy policies, including the small-scale Feed in Tariff, Contracts for Difference and the Renewables Obligation, as well as GB Capacity Market costs.
The government notes that ‘there will also be a 60% reduction in network charges, defined as the costs industrial users pay for their electricity supply’. According to the government, taken together, this support is expected to be worth around £24 to £31 per Megawatt Hour to the industry on average.
The BIS measures build on the Energy Security Strategy, published in April 2022, which committed government to taking action to address the UK’s industrial electricity prices, which are higher than those of other comparable countries. It will also form a key part of the government’s wider plans to seize on the potential of new green industries.
More information on the announcement can be found on the UK government’s website.
This new
apprenticeship
standard has been hand-built by the sector to address the specific demands of bulk storage operations.
The bulk storage sector is the cornerstone of the global supply chain. And, here at Reynolds Training, we’d argue that process safety and technical training is the cornerstone of our sector.
Therefore, it’s a great privilege to confirm that we have been embedded within a trail blazing group (along with our good friends at the TSA, its wide range of members and Cogent) formulating the Bulk Storage Terminal Technician Apprenticeship (aka ‘BSTT’).
This new Apprenticeship Standard has been hand-built by the sector to address the specific demands of bulk storage operations, with an eye on the constantly shifting landscape of digital transformation and energy transition. As such, we think this new apprenticeship standard is a significant step towards enhancing the skills, safety and professionalism of those operators at the sharp end of our vital industry.
Isn’t there already a Bulk Storage
Well, yes and no! We at Reynolds Training have been proud to help pioneer the introduction of the first purpose-built apprenticeship into our sector, but this was as a Level 3 Specialism aligned to an existing apprenticeship - namely the Science and Manufacturing Technician Apprenticeship with Bulk Liquid Terminal Technician Specialism (which, let’s face it, is quite a mouthful).
This new Standard doesn’t in any way reduce the value of the training those apprentices received. Indeed, those who have followed this route are true pioneers for the sector. We have always felt that it was important that the crucial role our sector plays would be more fairly recognised and reflected by having our own specific apprenticeship route.
Now we do!
Understanding the BSTT Apprenticeship
The BSTT apprenticeship is designed to equip operators with the essential knowledge, skills and behaviours required by the bulk storage industry now and moving forward into a future of energy transition. The apprenticeship aims to cultivate a deep understanding of operational excellence, underpinned with safety protocols, technical understanding and environmental compliance, ensuring that technicians are wellprepared to support the sector’s evolving needs as well as empowering them with the skills to keep learning
and improving so they can expect to benefit from a lifelong career in our sector, whichever direction energy transition ultimately takes us.
As national and international efforts to tackle climate change by reducing carbon emissions become ever more important, the bulk storage sector will continue to grow in the coming years. From helping to unlock the potential of hydrogen, to the scale up of sustainable biofuels, the industry will have a key role to play in energy transition.
- IfATE’s standard-in-development for ‘L3: Bulk Storage Terminal Technician’
As outlined in the IfATE development document, the BSTT apprenticeship underscores the strategic importance of bulk storage terminals in maintaining supply chain continuity and supporting national infrastructure. With many terminals designated as critical infrastructure, the need for a specialised, well-trained workforce is self-evident.
This apprenticeship responds to that need by providing a structured pathway to develop the competencies required to manage and mitigate the unique risks associated with bulk storage operations.
A key improvement of the BSTT apprenticeship over previous training standards is its focused approach. Prior standards, which broadly covered science and manufacturing disciplines, only tangentially addressed bulk storage.
The BSTT apprenticeship, however, offers a dedicated pathway, supported by a curriculum that is directly relevant to our sector. This specificity ensures that apprentices are not only trained in basic interchangeable skills but are also proficient in the specialised tasks and responsibilities unique to bulk storage terminals.
The development of the BSTT apprenticeship was spearheaded by the Trailblazer Group, comprising industry leaders, associations and employers from across the sector. This collaborative effort ensured that the apprenticeship standard was informed by real-world insights and current industry practices, as well as focusing on the transitional aspects of future fuels. By involving those who are intimately familiar with the sector’s challenges and opportunities, the Trailblazer Group has been instrumental in crafting an apprenticeship that is both comprehensive and forward-looking.
With an anticipated rollout in September 2024 (subject to any temporary delay predicated by possible events in Westminster,
obviously) we think that the rollout of this new Apprenticeship Standard is a call to action for employers - there has quite literally never been a better time to take on apprentices and cultivate a highly skilled workforce poised to tackle the challenges of today and tomorrow. By integrating the new BSTT apprenticeship into your workforce development strategy, you can enhance your operational capabilities, take an important step towards futureproofing your business and contribute to the sector’s sustained growth and resilience and along with that the resilience of UK PLC.
As we explained in our three-part series of blogs called ‘The Apprentice Process’ (still available for you to read at reynoldstraining.com), by investing in apprenticeships you can ensure your operations are
supported by professionals who are not only technically proficient but also deeply versed in the industry’s best practices and emerging trends. You can also leverage the money you are likely already paying into The Apprenticeship Levy in order to offset the cost of training your apprentices.
You can also read the TSA’s take on this important issue - just Google ‘TSA Apprenticeships’ to download and read the excellent guide the TSA published on this very subject.
It isn’t too late to recruit apprentices for the September 2024 cohort. If you’d like to know more, just get in touch with us at Reynolds Training, we’d be only too happy to talk you through the process and explain the benefits to your business.
The new and improved Bulk Storage Terminal Technician apprenticeship represents a watershed moment for our sector, in that it demonstrates recognition of the fundamental role we play in the infrastructure of our society and the strategic assets that are part of this. It also heralds a wider understanding and acceptance of the ongoing importance of energy transition to our culture, and the crucial role our sector will play in that.
For employers, the time to act is now - to recruit apprentices under this new standard and to invest in the future of your operation and the bulk storage sector at large. The BSTT apprenticeship is more than just a program; it’s a pathway to ensuring that the bulk storage sector remains competitive, safe, efficient and profitable for decades to come.
Teamwork Security and Training Services Ltd. are thrilled to be celebrating their 20th Anniversary this year. Established in May 2004, Teamwork Security and Training Services Ltd. was formed in response to the demand for Port Facility Security Officer training following the introduction of the ISPS (International Ship and Port Facility Security) Code under amendments to the 1974 SOLAS Convention.
Since its inception the business has grown from a one-man business to a thriving team of 8 plus - with a number of professional consultants on its books - and is now the leading ISPS consultancy and training firm in the UK, delivering its services to a large number of UK and international ports.
Teamwork Security and Training Services Ltd. delivers complete ISPS support to its clients, including audits, ISPS compliance, security exercises, as well as Wharf Approval and ADR support packages and provides a high-level security guarding service to Port Facilities. They also deliver training and are approved by the Department for Transport to deliver Port Facility Security Officer and refresher courses along with Harbour Master’s investigators courses, staff Security Awareness and Search Training courses, consistent with the latest Port Facility Security Instructions as issued by the DfT.
Paul Symons, Managing Director, commented: “We are delighted to be celebrating our 20th Anniversary. Chris Amos, who set up the business in 2004, made a significant impact entering the market and since then, the business has grown from strength to strength. It’s an honour to deliver our services to a significant percentage of UK Ports and we look forward to continuing to nourish and build those relationships over the next 20 years.”
For more information, visit: www.teamwork-security.co.uk
Email enqs@teamwork-security.co.uk or call 01647 221544
UM Terminals has made a multi-million pound investment in one of its key strategic terminals.
UM Terminals has made a multi-million pound investment in one of its key strategic terminals.
The investment has been focussed on the company’s Regent Road terminal in Liverpool, which is also home to its head office.
The improvements at Regent Road form part of UM Terminals’ strategic growth plan to ensure the breadth of product expertise, bulk liquid storage capability, value-added services and sustainability credentials remain industry-leading.
The investment, which has taken place in recent months, was also an important part of the onboarding of new customers, ensuring that the business was able to meet their specific requirements. A number of tanks at Regent Road have been upgraded to keep up with the demand for storage in the Liverpool area.
One major enhancement at Regent Road has seen the introduction of dual dock loading with customers now able to load
and discharge cargo at Huskisson Dock and Canada Dock, reducing delays due to congested shipping berths.
The investment has also supported UM Terminals’ expansion into a broader range of products which now includes chemicals, industrial oils, vegetable oils, fertiliser and key growth areas of biofuels and biofuel feedstocks.
The company is also underway transferring across to low carbon tank heating technology, part of the wider UM Group’s sustainability strategy.
This investment includes the introduction of industrial ground and water source heat pumps to support the reduction in its carbon footprint in line with various UK and international requirements.
Phil McEvoy, Managing Director of UM Terminals, said: “Regent Road is a key strategic terminal and this multimillion pound investment will ensure that it will continue to meet and exceed the expectations of existing and new customers. We talk a lot about how we are willing to invest in the right opportunities to ensure the facilities and services we provide match our customers’ requirements. We pride ourselves on the quick turnaround from customer enquiry to product in tank, finding the right solutions to meet their varied logistical challenges. This significant investment at Regent Road covers four key bases – meeting the needs of our customers, including new ones we are onboarding, ensuring our capabilities are the best they can be, having the right capacity and
meeting our sustainability obligations.”
UM Terminals currently has a limited amount of storage available at Regent Road.
The company has six further terminals located in Liverpool, Hull and Portbury, all strategically situated to meet the logistical opportunities and challenges facing its customers. Value-added services include biofuel feedstock pre-treatment, blending, water dilution, product packing, HMRC bonded warehouse and COMAH compliance.
Further investment in recent months has been made in enhancing engineering and IT capabilities.
It means the business can now manage over 80 per cent of its asset integrity
inspections and assessments in-house, while the investment in IT has included the development of its own bespoke software package that can manage all aspects of task management of integrity inspections.
The software package provides mobile working for UM’s technicians so that data can be inputted live into the system, while integrity performance KPIs are also updated and can be viewed in real-time in dashboard format.
The company has also increased its project team to enhance its ability to solve complex problems for customers through engineering design and quick turnaround of projects. This has been of pivotal importance in the successful onboarding recently of several new customers.
UM Terminals is also tireless in its commitment to health and safety best practice with the company this month winning a Silver Award in the Achievement category of The Royal Society for the Prevention of Accidents (RoSPA) Health and Safety Awards.
The awards, now in their 68th year, are among the most prized in the health and safety industry, attracting over 2,000 entries from more than 50 countries.
UM Terminals is part of the United Molasses Group. The Group’s other services include the international trading of molasses and the sales and distribution of molasses.
For more information, please visit www.umterminals.co.uk
HRAS explores some of the tools to consider when it comes to performing a risk assessment of your operation.
osted by the TSA in London earlier this month, Carolyn Nicholls and Andy Stanley of R A S Limited (RAS) facilitated a special Risk Assessment Workshop which brought together a diverse range of people from member organisations of the TSA. In addition to looking at the fundamentals of risk assessment (why risk assessment is important), and its key ingredients (the right people, the right time, and the right process), the importance of using the right risk assessment tools was explored in detail.
There are numerous risk assessment tools available, ranging from qualitative (subjective) methods through to fully quantified (formal and systematic using measurable, objective data) methods. To avoid confusion over which tools are appropriate, the concept behind each tool needs to be understood and a clear idea of why the risk assessment is being conducted is needed. So, where do you start? The following are some of the tools Carolyn and Andy touched upon during the workshop.
Hazard Identification
Hazard identification is the bedrock of risk assessment and should be repeated throughout the plant life cycle. It can take the form of a specific study, or through the review and collation of existing studies. The key is to ensure a proper understanding of what the hazards are so that they can be managed, and it is important that these are reviewed as minor changes can creep in which alter the underpinning understanding in older studies. The input of a multidisciplinary team with the right level of knowledge and experience (process, mechanical design, and operations as a minimum) is also vital as different perspectives allow us to see different problems and solutions, and during our discussions we review and consider hazardous inventory, plant layout, PFDs and P&IDs, and design specifications.
There are many HAZID tools available; one well known technique is the Hazard and Operability (HAZOP) Study, but this isn’t the only one and others may be more appropriate at different stages of the lifecycle, or if we need to understand particular issues; for example, a Failure Mode and Effects Analysis (FMEA) Study can be conducted to drill down to the component level of a system.
It is important to remember that if the hazard identification techniques used are incorrect, or the quality of the study is poor, then subsequent risk analyses, assessments and decisions
made based on those early studies are of equally low quality, and you cannot be sure that your risks are appropriately managed. It is also important to keep in mind that risk criteria are not used at this stage as the sole purpose of hazard identification is to identify what can go wrong and not to assess risk. Considering risk at this stage can dilute the effectiveness of the hazard identification process as it leads to distraction.
The Risk Assessment
There are a substantial number of tools to draw upon when assessing the risk of the hazards identified in the Hazard Identification studies. But first, let’s look at the definition of risk; what does it actually mean?
The Institution of Chemical Engineers (IChemE) defines risk as, ‘The likelihood of a specified undesired event occurring within a specified period or in specified circumstances. It may be either a frequency (the number of specified events occurring in unit time) or a probability, (the probability of a specified event following a prior event), depending on circumstances.’ The willingness to live with risk, or ‘Tolerability of Risk’ can be estimated by comparing to tolerability criteria. This is a potential minefield as the criteria used must be appropriate for the type of risk calculated. The main criteria available to us is for Individual Risk, which is meant for cumulative risk, from all hazards that exist at the facility. However, many risk analyses will have
calculated a different type of risk, so we are not comparing apples with apples, but is the idea of comparing to risk criteria itself a distraction? We conduct a risk assessment to ensure understanding and satisfy ourselves that we have taken appropriate risk reduction measures; are numbers always needed to do that?
A Layer of Protection Analysis (LOPA) is a type of semi-quantified analysis that systematically considers the reliability of protective layers in place in a system to mitigate the chance of a catastrophic event. This technique can help answer questions such as, are there enough independent layers of protection against an undesirable event? Are layers of protection reliable enough? Can the risk be tolerated (if we set limits)? What is the best way to further reduce risk? What is the required reliability of instrumented systems?
An Occupied Buildings Risk Assessment (OBRA) is a type of risk assessment used to assess the risk from hazards (including fires, explosions, and toxic releases) at a site, to determine whether the risk to a building’s occupants is tolerable and, ultimately, whether the buildings on a site are providing suitable protection for the people working in them. It can be used as a standalone risk assessment, or integrated into further risk assessments, and can be semi-quantified or fully quantified depending on the level of rigour required.
In the UK, the law requires us to demonstrate that we have reduced risk to As Low As Reasonably Practicable (ALARP). We believe a specific ALARP workshop is required to do this justice. Using existing safeguards as a starting point, additional measures for risk reduction are sought based on inherent safety, prevention, control, and mitigation measures. Similar to a HAZID or HAZOP Study in its need for a multidisciplinary team, an ALARP Demonstration Workshop is held to focus on evaluating risk drivers (taking key contributors from risk analysis); developing a thorough list of ‘what more could be done’ using guidewords and prompts; considering wider generic issues; evaluating the potential risk reduction achieved by the proposed measures; developing a quantified assessment of risk reduction benefit if it cannot be assessed by judgement alone; and proposing a concise list of improvement measures for implementation. Once the measures are identified they are assessed to determine whether they are practical to implement.
Hopefully, this gives a flavour of the workshop and, indeed, some of the tools to consider when it comes to performing a risk assessment of your operation. There are, however, many more which may be more suitable to your operation so if you need any help, advice, or just want to ask a question, please reach out to Carolyn or Andy via www.ras.ltd.uk.
SInnovative emissions reduction, degassing and VRU back-up services for a wide range of applications and industries.
David Wendel, Managing Director ENDEGS GmbH, Managing Director & CCO ETS Group GmbHustainability and environmental protection accompany us daily, the awareness for these important topics has grown significantly over the last years and it is necessary to pay even more attention to them in the near future. Everyone can contribute to enhanced environmental protection – in case of industrial operations and maintenance, sustainability is of special importance as the industrial sector still produces a high amount of greenhouse gas (GHG) emissions, foremost of all carbon dioxide (CO2) and methane (CH 4 ) as well as their precursors, the volatile organic compounds (VOC). These emissions are created in many industrial processes – such as loading and unloading procedures or commissioning and decommissioning – and are dangerous to both the environment and the human health when emitted untreated into the air. Thus, treating and reducing industrial emissions contributes to more sustainability and environmental protection. Emission treatment and reduction is as broadly diversified as industrial processes in itself.
ENDEGS and SIS as part of the ETS Group offer a wide range of versatile and innovative emission treatment services for many different industries.
all products
The technology fleet of the ETS Group companies consists of about 50 mobile vapor combustion units that are perfectly suited for degassing and VRU back-up deployments. The units can be transported on trailers and are therefore highly flexible as they can be deployed in a short time and can be used directly on-site at the customer’s facility. With availability in five combustion capacities – with 3, 4, 5, 10 and 20 MW –, the mobile incinerators are suited for different applications and can combust all kinds of gases, gas mixtures and vapors with an efficiency of more than 99.99%. In the combustion process, neither open flame nor odor develop – ETS Group mobile emissions reduction projects are sustainable and environmentally-friendly.
The units are compact and, thanks to very short execution processes, highly flexible and easily adaptable. They are equipped with everything required for emissions reduction and degassing such as piping, power generators or flame arresters, tank and the entire support gas facility. ETS Group customers can trust in a transparent and efficient process as well as in the highest quality standards on the market. As daily operations can continue as usual and without
disruption during our work, ETS Group clients save time and money.
Wide range of applications and industries
Our mobile vapor combustion units are ideally suited for a wide range of different applications, products and substances. Our customers work in different industries – for example oil and gas, chemical and petrochemical, marine, shipping and logistics and food and fertilizer – and use our services for the following applications.
Our mobile vapor combustion units can be applied for the degassing of all types of components that are used in industrial facilities – for example tanks, containers, pipelines, rail cars, barges, ships or vessels. With our European patent, we also offer the degassing of vacuum trucks. In the Port of Duisburg, we have established a permanent site for the degassing of vessels and barges in the world’s biggest inland port, creating the first possibility for environmentallyfriendly degassing in shipping on the River Rhine in Germany. For this, we have also achieved important changes in regulations.
ETS Group mobile emission treatment solutions are designed to destroy all pollutants in the explosion groups IIA, IIB and IIC, from hydrocarbon solvents and vapors to hydrogencontaining vapors. Our units are for example perfectly suited to work with petrol, crude oil, hydrogen, methane,
ammonia, propylene, butane, benzene, naphtha, slop, meaylene, n-hexane and many more products.
Nowadays, mobile degassing has become a standard. That is why we always aim at improving our services and technologies and give everything to fulfill the wishes of our customers – if they work with a product or have individual requirements that our current technologies are not suited for, we do everything we can to make it possible thanks to our innovative processes and strengths that have been recognized as we were named one of the most innovative mediumsized companies in Germany for the last three years in a row.
Many industrial facilities such as refineries, loading terminals or storage tank terminals can only operate when a stationary system for the treatment of the developing emissions is in place. The most common system for this is a vapor recovery unit (VRU). When a VRU needs to be shut down due to maintenance or failure, the whole facility can no longer operate until the VRU is back online and running.
To avoid downtimes of the entire facility, our mobile vapor combustion units can also be used for the temporary replacement of VRUs during downtimes due to maintenance or repair. This way, operations can continue as usual, saving customers valuable time and
money.
We also offer our services and technologies during turnarounds and shutdowns. During maintenance work and revision in production and process facilities, our technologies can ensure the safety of employees, external workers and surrounding neighbourhoods from hazardous gases and vapors.
One of our largest projects to date involved the degassing of several columns, heat exchangers, decanters and liquid tanks during a major refinery turnaround in Germany. Besides piping with a total length of 1.9 kilometres, we have also deployed three of our mobile vapor combustion units for this project. With two units with a combustion capacity of 10 MW and one 5 MW unit, we have used a total combustion power of 25 MW for the refinery turnaround project. The project lasted for about two and a half months, the operations in the refinery went on undisturbed and without any long downtime during our deployment.
When handling substances like liquefied gases under pressure that are highly flammable and pose a high risk of explosion, the components containing these substances – for example LNG, ammonia, hydrogen or liquid gas – must be purged. As reactions such as oxidation can lead to deflagration or explosion inside
the tank, unwanted substances like oxygen must be displaced from the tank. This is achieved by purging and inerting – adding an inert gas that does not react with other substances. For purging and inerting components, we use our mobile vaporizer with nitrogen tanks. Thus, working with liquefied gases under pressure is a safe process. Our mobile nitrogen vaporizer can also be combined with our vapor combustion units – purging and inerting are also advantageous for degassing as the gas or liquid can be pressed out of the component with an inert gas as a medium and fed into the combustion chamber, where it is combusted in an environmentallyfriendly manner.
Manual tank cleaning is a dangerous task as workers are – despite
extensive safety gear – exposed to the hazardous ATEX Zone 0. With the remote-controlled ATEX Zone 0 robot, that the ETS Group offers as a rental service, industrial tanks can be cleaned from a safe distance in a cabin via two joysticks and a monitor showing every movement of the robot in real-time. Due to its small size and mobility, the robot can be used in many industries and for a wide range of materials. Thus, the ATEX Zone 0 robot increases occupational health and safety.
As we are not only looking at the rough cleaning of the tank and want to make the entire cleaning process safe and emissions-free, the robot can be combined with a mobile vapor combustion nit to clean the tank before the robot starts its work. After the remote-controlled rough
cleaning of the tank is finished by the robot, manual tank cleaning can start – as mobile vapor combustion unit and ATEX Zone 0 robot have done a thorough job, the concentration of VOC in the tank is low and cleaning employees only need to wear a respiratory mask with filter while removing the small of material still remaining in the tank.
We also offer the degassing of suction tanks with our European patent. As the hazardous materials are pumped into the suction truck from the tank, they create dangerous gas concentrations. Instead of just releasing these into the atmosphere – a common but harmful practice – we burn them off with a combustion rate of more than 99,99 % with our combustion unit.
For more information, please contact: David Wendel, Managing Director ENDEGS, Managing Director & CCO ETS Group, at d.wendel@e-t-s-group. com
Find out more at www.endegs.com and www.s-i-s.com
Author
David Wendel, Managing Director ENDEGS GmbH, Managing Director SIS GmbH, Managing Director & CCO ETS Group
given the strategic nature of the location, with easy access to road, rail and water for redelivery. As such, this move represents a significant step forward for storage and re-use of carbon.”
Impala, Netherlands
Impala Terminals Group acquired the unfinished Hartel Tank Terminal from HES in November 2023; it now plans to complete the facility, to be renamed Impala Energy Infrastructure Netherlands, by the end of 2025. The finished terminal will have a total capacity of some 1.3m m3 for liquid energy products. The high specification and connectivity of the terminal will provide maximum flexibility for the users of the facility. Importantly, the terminal will be capable of storing a variety of biofuel products, helping to facilitate the energy transition for the region.
Work on the new terminal had been put on hold at the end of 2022 following delays caused by the Covid-19 pandemic, which increased costs.
“This is an excellent development for Impala, particularly as it will provide our strategic customers with a strong and sustainable asset located within the Port of
Rotterdam in the major trading hub of ARA,” said Sjoerd Bazen, CEO of Impala Energy Infrastructure, at the time of the transaction. “We look forward to developing our business in the region in collaboration with different stakeholders and specifically the Port of Rotterdam Authority.”
The deal was also seen as significant by the port itself, with Boudewijn Siemons, CEO of the Port of Rotterdam Authority, saying: “The Port Authority Rotterdam is pleased that Impala has purchased the terminal asset and that construction work will be completed. With this transaction, the company is making a lasting commitment to the port and is adding a brand-new facility for storing a wide range of bulk liquid energy products. This provides a new future for the terminal after a bankruptcy that has been difficult for all parties concerned, particularly the employees.”
Koole, Netherlands
Koole Tankstorage Botlek is planning to construct a second distillation tower at its site by the end of 2024, to increase production capacity for sustainable aviation fuel (SAF) by the distillation of hydrotreated vegetable oil (HVO).
“With this project we will increase our production capacity from 130,000 tonnes to
almost half a million tons of SAF feedstock per year. All of that simply here in the Botlek,” says Jeroen Kensmil, team leader for the petroleum industrial distillation (PID) unit at the terminal.
Koole Terminals has also lined up another major customer for its planned green ammonia terminal in Rotterdam, signing a letter of intent with Hyphen Hydrogen Energy. Namibia-based Hyphen has, over the past year, lined up a number of MoUs with potential customers in Europe and is targeting the supply of up to 750,000 tpa beginning in 2028.
LBC, Netherlands
LBC Tank Terminal is to expand its Rotterdam terminal, adding 98,000 m3 of new tankage to take overall capacity to 280,000 m3 by first quarter 2026. This will be the third phase of development of the site, which has already seen new berths, loading bays and tankage added.
“As we move into the next phase, I am excited about the opportunities ahead of us,” says Erik Kleine, general manager, Europe at LBC. “The commitment and hard work of our team has been the driving force behind our journey thus far, and I take immense pride in our achievements. LBC Rotterdam’s growth is a testament to the collective success of dedicated team players enthusiastic about our role in shaping a more sustainable future, and I look forward to the continued progress on this important path.”
LBC Tank Terminal has also begun a collaboration with Shell Chemicals for the storage of pyrolysis oil derived from waste plastics at the Rotterdam terminal. “Shell is excited to start this collaboration with LBC; the five-year agreement supports our strategy to supply our customers with more circular chemicals and to help the development of a viable plastic circular economy in Europe”, says Liz Allen, general manager of Shell Chemicals Business Management Northwest Europe. “This dedicated storage will help grow the market for pyrolysis oil by delivering much needed capacity which will enable Shell to aggregate and process pyrolysis oil from multiple suppliers and improve value chain flexibility.”
Frank Erkelens, CEO of LBC Tank Terminals, adds: “This collaboration reiterates LBC’s dedication to making impact by driving
positive change within the industry. Storage solutions play a crucial role in advancing and supporting long-term growth in the circular chemicals value chain, and we look forward to combining forces with Shell in making significant progress towards achieving a carbon-neutral future.”
LBC had earlier signed a similar partnership with Vitol, which is planning to supply pyrolysis oil to the local petrochemical industry.
Vesta Terminals has appointed Proton Ventures to complete FEED work on the re-purposing of two 30,000-m3 ammonia storage tanks at its facility in Vlissingen, the Netherlands. The work forms part of a larger plan to refurbish and expand the existing terminal with the aim of creating the first green ammonia hub in north-west Europe. This will include installation of infrastructure for loading and unloading VLGCs, rail tank cars and barges as well as a cracker to convert green ammonia back to hydrogen and links to the Dutch hydrogen pipeline network. A second phase is envisaged that would double capacity.
“As Vesta, we are proud to push forward this project,” says Daan Schutte, CCO of Vesta Terminals. “With the help of Proton Ventures, we are taking important steps towards being a frontrunner in the renewable energy transition.”
Vopak commissioned 16 new storage tanks at its Vlaardingen terminal in Rotterdam in second quarter 2023, adding 64,000 m3 of capacity for waste-based feedstocks for the production of biodiesel and sustainable aviation fuel (SAF) under a long-term deal with Shell, which will use the feedstocks at its new biorefinery to produce SAF and renewable diesel.
Vopak Terminal Vlaardingen is strategically located in the Port of Rotterdam and is well-connected for logistics via vessels, barges,
trucks, and trains. The terminal has extensive experience in storing products such as used cooking oil and tallow. Work began on the €90m project to repurpose part of the terminal for waste-based feedstocks began in 2021. Vopak says the project is in line with its strategic goal “to accelerate towards new energy by developing infrastructure solutions that support customers and society in decarbonisation”.
Inter Terminals Sweden has put a carbon fibre unit into service at its facility in Malmö, reducing the emission of vapours from the handling and storage of bitumen at the site.
“This is an investment that we have chosen to make together with our customers in order to prevent and reduce the risk of any odour in the immediate area around Inter Terminals’ terminal in Malmö that may arise in connection with the handling of bitumen,” says Jonas Taserud, technical manager at Inter Terminals Sweden.
Inter Terminals Sweden is also expanding its aviation fuel facility in the Port of Gävle by converting tanks from conventional fossil heating oil storage to a blending and storage facility for Sustainable Aviation Fuel (SAF), in
collaboration with the Scandinavian airline SAS, which has an ambitious target for SAF use by 2030. The new tankage will be ready for operation this summer.
“Our demand for SAF is significant, but there is a need for investments throughout the entire value chain to enable us to transition to more sustainable flights,” says Ann-Sofie Hörlin, had of sustainability at SAS. “That’s why it’s important for us to partner up and have a proactive approach to ensure a sufficient and efficient SAF value chain. SAS use of SAF today is low in comparison to our future demand and needs to increase significantly as the usages of SAF directly correlates with lower flight emissions.”
Navigator Terminals has signed an MoU with Alfanar, a global developer of renewables projects, envisaging the development of the North Tees rail terminal for the receipt, storage and handling of up to 1m tonnes of non-recyclable waste feedstocks for Alfanar’s Lighthouse Green Fuels plant at Port Clarence, which will produce the UK’s first sustainable aviation fuel (SAF) from waste; the plan includes an SAF handling terminal at the
CONSTRUCTION
HUB IS
PRODUCTS
North Tees dockside. Construction of the Lighthouse plant is due to start this year with the unit coming onstream in 2028; it is projected to produce around 10 per cent of the UK’s SAF target in 2030.
Navigator Terminals’ North Tees complex is a road fuel and crude oil storage facility with the region’s only deep-water jetty designed for petrochemicals, direct pipeline connections to the North Sea and modern rail distribution facilities. Finished SAF will be exported via ship at the North Tees waterside complex. SAF may also be exported via rail or truck at Navigator’s inland North Tees rail terminal.
“Navigator Terminals is committed to playing a leading role in delivering net zero for the UK; as the UK’s leading transport, storage and handling experts, we operate a network of strategically located terminals,” says Jason Hornsby, CEO of Navigator Terminals. “We have supported Alfanar’s progress in its thinking around the Lighthouse SAF project for over 12 months and now are pleased to announce our formal partnership.”
Stolthaven Terminals has completed renovation and upgrade work on the jetty at its Dagenham facility in the UK. Work started in 2022, with the aim of improving discharge rates and turnaround times for vessels, enhancing safety and reducing environmental impact and, ultimately, delivering a superior service to customers. The main jetty structure was completed in October 2022 and the final engineering and mechanical work was finalised in the first quarter this year.
Steve Walker, general manager of the Dagenham terminal, says: “This is a major milestone for Dagenham and for Stolthaven Terminals. It has been a great team effort to coordinate this project and keep the berth operational for our customers during these complex works.”
Alkion, Portugal
Alkion Terminal Lisbon began handling bitumen in April 2023, in response to an expression of interest by an existing customer. Bitumen is an important product, as an essential material for road construction,
repairs and civil works. The bitumen that is being stored at Alkion Terminal Lisbon is used all across Portugal.
“Bitumen must be stored at a high temperature, otherwise it will turn solid inside of the tank,” notes terminal manager Diogo Godinho. “We keep the bitumen at a temperature of more or less 160°C,” which means that bitumen storage requires specific infrastructure. “We invested in a new loading bay, thermal insulation of the tanks, heating equipment and new reception and expedition lines among other things.”
Alkion Terminal Lisbon is now looking into making the new bitumen storage location more sustainable: “We generate energy with solar panels at the terminal. We are currently looking into the option of powering our bitumen heaters, which currently run on propane, with electricity, meaning we could run them with the energy we generate ourselves. This would lower our CO2 emissions as well as being more cost effective, which adds value for our customers.”
Exolum has been appointed by the Port Authority of Gijón in north-west Spain to manage the 67,000-m3 bulk liquids storage
terminal at La Osa pier. The 15-year contract also involves Exolum investing €3m to connect the site to its own terminal in the port, and to modernise and adapt the infrastructure to provide a wider range of logistics services. This will focus in particular with the energy transition and decarbonisation.
The port’s terminal has 12 tanks plus a service station, with extensive vessel, road tanker and, eventually, train interconnection options. The port of Gijón is a key location for logistics operations owing to the quantity and quality of its connections with the region’s industrial hub, and the contract gives Exolum an opportunity to invest in a larger number of tanks to transport and store new energy vectors, such as biofuel, eco-fuel, hydrogen, ammonia and methanol.
“At Exolum, we are committed to investing in Spain and, particularly, to developing logistics investments at ports that support the energy transition,” says Jorge Guillén, Exolum’s Spain Region Lead. “The port of Gijón, therefore, represents a great opportunity to develop a larger volume of logistics operations and to boost the diversification of our business, thus expanding our services to new energy vectors that are
relevant for the modernisation, competitiveness and sustainability of the industrial infrastructure in Asturias.”
Vopak, China
Vopak has agreed to go forward with a 20,000-m3 expansion of the Haiteng terminal in China, along with new pipeline connections to its customer’s cracker; this project is underpinned by a 20-year commercial agreement and is due for commissioning in second quarter 2026.
Stolthaven, Taiwan
Work is underway on the Stolthaven Revivegen Kaohsiung Terminal (SHRVK) in Kaohsiung, a joint venture between Stolthaven Terminals and Revivegen Environmental Technology. The terminal, due to be commissioned this year, is designed to meet growing customer demand for high-quality bulk liquid storage in the region and to introduce more international trade to Taiwan. It can also help support the transition to more sustainable energy and fuel alternatives, including ammonia for local power generation and green methanol for greener marine bunker fuel.
The first phase of development includes a logistics facility with warehousing and drumming facilities, to be followed by the first
48,000 m3 of tank storage. Further tank construction will form a subsequent phase.
“Ultimately, SHRVK will be a one stop shop for customers, providing integrated storage, drumming, warehousing, and distribution solutions for chemical and bulk specialty liquid customers,” says Mark Lim, commercial manager of Stolthaven Singapore and business development manager, Asia.
BW, India
BW LPG has signed a joint venture agreement with Confidence Petroleum to establish a 50/50 company, BW Confidence Enterprise, to develop and operate an onshore LPG import terminal in Jawaharlal Nehru Port in Navi Mumbai, India. The joint venture will collaborate with BW LPG’s international trading operation and with its India shipping subsidiary.
As part of the deal, BW LPG will invest some $30m in Confidence Petroleum through an allotment of shares, giving BW LPG an 8.5 per cent shareholding in Confidence; BW LPG has an option to increase its shareholding. The capital injection will assist Confidence in its planned expansion of downstream assets, which currently number some 60 LPG bottling and blending plants and more than 200 autogas fuelling stations.
“These agreements represent a significant
milestone in our commitment to grow in India, and underscore our confidence in the potential of the domestic LPG market as well as our JV partners,” says Kristian Sørensen, CEO of BW LPG. “We have generated strong and stable returns from our Indian subsidiary, and we are ready to advance our growth trajectory along the value chain, to generate even better returns for our shareholders.”
Dialog Group Bhd began work on expanding its third terminal at Tanjung Langsat in March 2023; the new tankage will offer some 24,000 m3 of capacity for sustainable and renewable fuel products. The development is Dialog’s response to growing investor interest in low-carbon fuel alternatives; the company says that bulk fuel storage terminals have an opportunity to become principal facilitators of the energy transition by helping to develop new low-carbon lines of products and services.
Dialog Terminals Langsat 3 currently offers some 205,000 m3 of capacity, serving short to medium-term energy traders and multinational companies storing energy products. It is located adjacent to Dialog’s other two terminals at Tanjung Langsat and the new tankage is expected to handle raw materials such as cooking oil, tallow, pyrolysis oil and palm oil mill effluent, as well as biodiesel containing used cooking oil methyl ester (UCOME) and fatty acids methyl ester (FAME).
“This is just the first step in Dialog Terminals Langsat 3’s plan to create an ecosystem for renewable fuels with potential plans in the future to include integration and collaboration with pre-treatment or hydrotreat plants, thereby creating synergy to blend renewable and conventional fuel,” says Tan Sri Dr Ngau Boon Keat, executive chairman of Dialog Group.
The new tankage is due for completion by the end of this year.
JPTT (Jurong Port Tank Terminals) completed phase 2 expansion of its site in Singapore in second quarter 2023, taking total capacity to some 580,000 m3 for clean petroleum products. The work involved construction of three new tank pits, adding 330,000 m3 of
Investment. In other words, you get out what you put in.
Fort Vale has always had the attitude of ‘the best product, at the best price, using the best materials’and we apply it to our own infrastructure, as well as our future planning.
The skeleton of a building you see above may not look much at present, but when completed will play an important part in our day-to-day operations. The new building will primarily be used for final assembly and testing - we’ll also be moving R&D and despatch there - this means we can free up space in our main building to focus on the key areas of machine shop and fabrication.
This will improve efficiency and increase capacity, meaning we can keep thinking ahead, making products built to last, and doing all that on one site. It means we can be agile, resilient and above all, effective.
Not every company can do this. Not every company is Fort Vale.
®
capacity, along with an upgrade to the terminal’s infrastructure. All tankage at the site has now been fully leased, JPTT says.
“The expansion of our state-of-the-art liquid bulk terminal is a significant milestone,” says Francis Nyan, JPTT chairman. “Since starting operations in 2019, JPTT has supported the needs of our customers in the clean petroleum trading market and fortified Singapore’s position as a global energy and chemicals hub. With our partner Advario, we remain confident that JPTT’s expansion strengthens the integrated terminal network and enhances our overall value offering to the market, leveraging each other’s expertise and length of experience.”
JPTT is a 60/40 joint venture between Jurong Port and Advario.
Vopak, Singapore
Vopak commissioned 40,000 m3 of tankage at its Sebarok terminal in Singapore, dedicated to blending biofuels into marine fuels, in February this year. The work, which is underpinned by a customer commitment, also involved the conversion of existing pipework. The Sebarok terminal is close to Singapore’s eastern anchorage, where a lot of bunkering takes place.
“Our vision for Sebarok terminal is to be a sustainable multi-fuels hub to strengthen Singapore’s position as the top bunkering hub,” says Rob Boudestijn, president of Vopak’s Singapore business unit. “As a storage and critical infrastructure services provider, this development can facilitate the entry of more biofuels companies to diversify the supply chain for marine biofuels and accelerate the decarbonisation of the shipping industry.”
The Sebarok terminal now has a total capacity of 1.34m m3 across 83 tanks.
Impala, Australia
Impala Terminals has formally inaugurated its first energy import, storage and distribution terminal in Australia. The Kwinana Bay site in Western Australia, which has been operating since October 2022, offers 225,000 m3 of storage capacity in 11 liquids and one butane tank, and has an express lane for diesel loadings to road tankers. It is currently handling diesel and gasoline, with butane for blending, supported by an anchor customer.
“We are very excited to be here, not only as an asset owner and operator, but also as a company committed to further investing into Western Australia infrastructure,” says Sjoerd
Bazen, CEO of Impala Terminals Energy Infrastructure. “We have been impressed by the support and collaboration with the local government, the Fremantle Port Authority and other key stakeholders and look forward to building on these relationships.”
Stolthaven, Australia
Stolthaven Terminals last year signed an MoU with the Port of Melbourne and a number of shipping companies to explore the commercial feasibility of setting up a green methanol bunkering hub in the port, using green methanol shipped from plants in Victoria and Tasmania.
“Stolthaven Terminals is pleased to support this project – as well as many others worldwide – that enable the transition to greener energy alternatives,” says Ben Serong, general manager of Stolthaven Terminals in Australia. “The scope of activities involved under this MoU will evolve as the collaboration progresses and the parties develop a clearer understanding of how our respective expertise can be combined on this potential project.”
“Decarbonisation of the maritime industry is really gaining pace,” adds Saul Cannon, CEO of the Port of Melbourne. “As Australia’s largest container port with around 3,000 ships visiting annually, it makes sense that we look at ways to work together with customers, service providers and producers to understand the needs of the market.”
Stolthaven, New Zealand
Stolthaven Terminals last year commissioned two new 8,100-m3 storage tanks at its Mount Manganui site in New Zealand (left). The tanks were built to store very low sulphur fuel oil (VLSFO) for one of its customers and were built by Culham Engineering in Whangarei. The tanks were delivered to Mount Manganui by sea, involving a five-day, 290-nautical mile trip.
Stolthaven’s customer plans to use the IMO 2020-compliant VLSFO to replace heavy fuel oil bunkering at the nearby Port of Tauranga. “The Mount Maunganui terminal is perfectly located to serve the port,” say Brent Metson, general manager of the Mount Manganui terminal.
RESULTS • VOPAK HAS POSTED IMPROVED RESULTS FOR THE FIRST QUARTER, DESPITE A SLIGHT DROP IN REVENUES. IT IS CARRYING ON WITH PLANS TO MEET THE ENERGY TRANSITION HEAD-ON
VOPAK HAS POSTED first quarter revenues of €328.2m, down from €361.8m for the same period last year. Net profit was up 3 per cent at €105.8m and adjusted EBITDA, excluding exceptional items, rose by 1.3 per cent to €297.8m. The company refers to these figures as “strong” and has adjusted its forecast for the year as a whole upwards, projecting proportional EBITDA of €1.14bn to €1.18bn, compared to €1.08bn for the full year 2023 (adjusted for divestments over the past year).
CEO Dick Richelle says of the results: “In the first quarter of 2024, we continued to
deliver on our strategy to improve our financial and sustainability performance, to grow our business in industrial and gas terminals, and to accelerate towards new energies and sustainable feedstocks. The demand for our infrastructure services remained robust, resulting in an increased proportional occupancy of 93 per cent. Oil and gas markets were strong, driven by a higher demand for energy, and rerouting of supply chains. Chemical markets remain under pressure, having a limited impact on our chemical distribution terminals so far, while
industrial terminals maintained solid results, backed by long-term take-or-pay contracts.”
Vopak reports that its joint venture in India, Aegis Vopak Terminals, has acquired a new terminal in Mangalore, which is well connected to marine and road infrastructure. The site has a current tank storage capacity of 44,000 m3 with another 11,000 m3 under construction and space for further expansion.
Following Vopak’s three-pronged strategy to ‘improve, grow and accelerate’, the company put in place repurposed infrastructure at its Sebarok terminal in Singapore in February, designed to allow for the blending of biofuels into marine fuels. Later this year it expects to put similar upgrades into service at its terminals in Alemoa, Brazil, which will be expanded by 30,000 m3, and at Vlaardingen in the Netherlands, which will increase capacity by some 34,000 m3
Investment is also being targeted at growing Vopak’s presence in gas infrastructure, with good progress in development of a new LPG export project in British Columbia, Canada. In South Africa, Vopak and its partner Transnet have been appointed to design, develop, build, finance, operate and maintain an LNG import terminal in Richards Bay; market interest is currently being gauged prior to a final investment decision being made.
An interesting development for Vopak is its move into electricity in the US; it reports that its terminals at Long Beach, Los Angeles and Corpus Christi and the Vopak Exolum Houston (formerly Vopak Moda Houston) terminal have all been running on 100 per cent green electricity since the start of this year; as of the end of 2023, renewable energy accounted for 66 per cent of its global energy consumption. In February Vopak announced a €9m investment in new infrastructure for energy storage in Texas, which will involve the installation and operation of two standalone lithium ion battery energy storage systems (BESS) near Houston. “This is an important development in executing Vopak’s strategy to accelerate towards new energies,” the company says.
www.vopak.com
EVOS HAS SIGNED an agreement with Cepsa for the storage of green methanol at the Evos storage facilities in Algeciras and Rotterdam. The partnership, which also provides for the storage of green ammonia at Evos’ facilities in Algeciras, opens up a logistics link for the transport of green hydrogen products between key strategic ports in Spain and the Netherlands. Cepsa and Evos will also jointly study logistics for biofuels (including sustainable aviation fuel - SAF), renewable fuel from non-biological origin and hydrogen carriers, such as Liquid Organic Hydrogen Carriers (LOHCs), in other terminals of the Evos network in north-west Europe, including Amsterdam.
“As Evos extends its reach within the Green Import Corridors of Northwest Europe and propels the growth of our Algeciras terminal in Spain, we are pleased to join forces with Cepsa to provide essential infrastructure to accelerate
the energy transition,” says Harry Deans, CEO of Evos. “This collaboration will pave the way for a south-north corridor for green hydrogen products, aligning seamlessly with the strategy for our eight terminals, located in key strategic ports, to lead the energy transition in partnership with our clients.”
This focus on the ‘Green Import Corridors’ involves the storage and handling of green hydrogen derivatives and renewable fuels, especially in the ARA ports. Meanwhile in Spain, Evos is progressing the expansion of its Algeciras terminal as a renewable export hub. Across all Evos terminals, infrastructure for green bunker fuels, such as green ammonia and green methanol, is undergoing development.
Already a key part of Evos’ portfolio, the storage and handling of SAF will expand further in coming years. Collaborating with partners, Evos aims to pioneer an integrated
terminal concept, with nearby green fuels production facilities, to enhance carbon reductions and to augment the Energy Transition.
Cepsa is currently developing a green methanol plant in Huelva that aims to reach an estimated annual production capacity of 300,000 tonnes, involving an investment of up to €1bn. The plant forms part of the Andalusian Green Hydrogen Valley that Cepsa is developing alongside other partners, which will also entail two green hydrogen plants with a total capacity of 2 GW and a green ammonia plant with an annual production capacity of up to 750,000 tonnes. In addition, Cepsa has started building a second-generation biofuels plant in Huelva as part of a joint venture with Bio-Oils that will create the largest facility of its kind in southern Europe with the capacity to flexibly produce 500,000 tonnes of SAF and renewable diesel annually.
“Through strategic partnerships, Cepsa is building a network of green molecule supply stretching from Spain to northern Europe,” says Maarten Wetselaar, CEO of Cepsa. “This alliance with Evos provides crucial storage infrastructure which will enable the flow of green methanol produced in southern Spain into northern Europe, reinforcing the viability of our large-scale green hydrogen projects.
Last year, we announced the development of one of the largest green methanol projects in Europe as part of our Andalusian Green Hydrogen Valley, and this new partnership provides us with the end-to-end solution to bring these green molecules to our customers in north-west Europe as we support decarbonisation efforts across the continent.”
Cepsa already has a partnership with the Port of Rotterdam to establish a green hydrogen corridor from the Port of Algeciras and also has agreements with ACE Terminal for the storage of green ammonia in Rotterdam and with Dutch company Gasunie that guarantees access to its green hydrogen transport network, which will connect with European industrial clusters in the Netherlands, Germany and Belgium as part of the Delta Corridor project. www.cepsa.com evos.eu
HYDROGEN • SUPPLY CHAINS FOR NEW ENERGIES WILL NEED TO BE BUILT FROM SCRATCH. GES AND PROVARIS ARE LEVERATING THEIR DIFFERENT SKILL SETS TO BRING COMPRESSED HYDROGEN TO ROTTERDAM
GLOBAL ENERGY STORAGE (GES) and Provaris Energy have agreed a collaboration to develop a gaseous hydrogen import facility at the terminal currently being built by GES in Rotterdam to import refrigerated ammonia and compressed hydrogen. The multi-client, multi-product terminal will ship product out by barge, rail, truck and Gasunie’s HyNetwork hydrogen grid.
Under the collaboration, GES and Provaris will complete a comprehensive prefeasibility study to demonstrate the technical and economic viability of berthing and unloading of Provaris’ H2Neo compressed hydrogen carriers. Activities will also include the joint marketing of the proposed facility where Provaris will be responsible for the transport of the hydrogen in the H2Neo carriers and GES responsible for the discharge and injection into the hydrogen grid.
“This collaboration with Provaris showcases the types of partnerships that GES is pursuing
to facilitate the energy transition through our contribution with storage and logistics solutions, at Rotterdam as well as other existing and future locations,” says Peter Vucins, CEO of GES. “I welcome the opportunity to work closely with Provaris to develop a cost competitive import solution for Rotterdam and European energy customers.”
Both parties have a shared belief that the GES terminal in Rotterdam is an ideal site for bulk scale import of green hydrogen given the early connection to the HyNetwork grid for gaseous supply to industrial users in the Port of Rotterdam and key industrials users in Europe. The project also rests on the opportunities provided by the compressed hydrogen vessels designed by Provaris, as well as the potential for it to be able to supply green hydrogen from Norway, where it has a collaboration agreement with Gen2 Energy.
“We are delighted to be collaborating with GES on a world-first terminal for bulk scale import of gaseous hydrogen that can accelerate the availability of green molecules for industrial users,” says Martin Carolan, managing director and CEO of Provaris Energy. “GES has a global network and track record of terminal assets and is demonstrating leadership in the development of a bulk terminal for hydrogen and derivatives for Europe. We look forward to the outcomes of this collaboration which can accelerate the delivery of ambitious import volumes required for the European market and support export projects under development based on the Provaris approach to the simple and energy efficient marine transport of hydrogen.”
There is, though, much work to be done. Over the course of this year, GES and Provaris plan to complete prefeasibility level studies focused on the jetty facilities to discharge the H2Neo carrier, along with scavenging compression, storage, HyNetwork grid connection, risk and safety, emissions, and other permitting and environmental considerations. Provaris, an Australia-based company developing a portfolio of integrated green hydrogen projects in Asia and Europe, is meanwhile completing construction and testing of its prototype cargo tank, with final construction approval from Class anticipated in mid-2024.
www.gesgroup.global
www.provaris.energy
NEW ENERGIES • OF ALL THE COUNTRIES IN SOUTHERN EUROPE, SPAIN IS PROGRESSING FASTEST IN DEVELOPING A RENEWABLE ENERGY SECTOR. MEDITERRANEAN SUNSHINE IS FUELLING EXOLUM
LAST MONTH, EXOLUM organised a one-day seminar on renewable hydrogen and sustainable mobility, in collaboration with Funseam, the Foundation for Sustainable Energy and Environment in Spain. As elsewhere in Europe, the prospects for a rapid transition to renewable energy in industrial and transport applications rest on the availability of the necessary infrastructure to supply renewable energy to the places it is needed – something that Exolum, with its roots as Spain’s state hydrocarbon logistics firm, is keen to establish.
The seminar, which was organised around four round-table discussions, kicked off with an official welcome speech given by Rosa García, Exolum’s chairwoman, who highlighted the importance of hydrogen as a solution to help decarbonise sectors that are difficult to electrify, such as energy-intensive industries and heavy-duty mobility. She also pointed out, however, that significant
challenges lie ahead, such as the regulatory and tax framework, the creation of new demand and technological developments, which must be addressed to ensure the success of green hydrogen.
The first round table, moderated by Joan Batalla, managing director of Funseam, addressed the perspectives for the deployment of green hydrogen in Spain. High-profile participants such as Pedro Casero of the Aragonesa del Hidrógeno Foundation, and Eduardo Sañudo, general manager of Vopak Terquimsa, expressed their views on the potential of green hydrogen to become a key element for the integration of renewable energies in the electricity grid and as a means of decarbonising the industrial and transport sectors. The speakers stressed the fact that the sector is going through a cautious period, during which it is important to be realistic about project perspectives, as well as the need to scale and develop
technologies and to implement the logistics chain as a key factor
FOCUS ON HYDROGEN
Hydrogen’s contribution to the decarbonisation of mobility was the focal point of the second discussion at the event, led by Patricia Prieto, Exolum’s hydrogen project developer. Participants included leaders in the automotive, shipping and oil industries, such as José López Tafall from the Spanish Association of Automobile and Truck Manufacturers, Elena Seco from the Spanish Shipowners’ Association, Andreu Puñet from the Spanish Association of Petroleum Product Operators, and Eugenia Sillero from Gasnam, who discussed the opportunities and challenges of adopting green hydrogen in the different means of transport, as well as the need for a clear, stable regulatory framework that favours the profitability and competitiveness of ongoing projects.
The third round table of the day, moderated by Eduardo Cembrano, manager of the Energy Industry Area of the Spanish Centre for Information and Business Creation (CIRCE), focused on the role of innovation and technology in the achievement of sustainable mobility. Emilio Nieto, from the National Hydrogen Centre (CNH), José María Sánchez Hervás from the Research Centre for Energy, Environment and Technology (CIEMAT), Ekain Fernández, in charge of H2 Technologies at TECNALIA, and María Retuerto, researcher at the Spanish National Research Council (CSIC), discussed emerging technologies in green hydrogen and their transformative potential for the transport sector, as well as the role of industrial research and development in the process. In this regard, they stressed the importance of training hydrogen experts to enable the development of the technologies required for implementation of this process.
Hydrogen development as an element of corporate strategy was the topic of the last discussion at the event, led by Antonio Pérez-Collar, president of Alicante’s Hydrogen Valley (VAHIA). Speakers included Maribel Rodríguez, Repsol’s hydrogen business development manager, Olivia Infantes, Cepsa’s manager of hydrogen regulatory affairs, David Álvaro, Airbus national engineering and
accessible solutions based on innovation and reducing CO2 emissions while enabling the use of currently existing infrastructure and vehicles.
transport sustainable aviation fuel (SAF) by hydrant, which reduces carbon dioxide emissions by 80 per cent.”
technology representative, and Rafael Calvera, chairman of Calvera Hydrogen. They talked about the opportunity that green hydrogen poses for companies in their decarbonisation journey and highlighted Spain’s excellent position to lead renewable hydrogen production.
Closing the event, Jorge Lanza, CEO of Exolum, emphasised the sector’s current situation: “We are going through a cautious and realistic phase, but this should not dampen our enthusiasm,” he said, also stressing the need to effectively promote collaboration between the public and private sectors and among companies. “Now is the time to develop hydrogen for mobility. There are many challenges ahead, but what’s most important is to get started.”
Lanza was also asked to talk about the energy transition at the Wake Up Spain! event last month, where he stressed the importance of alternative fuels and the efficiency of combustion engines in the energy transition process. In the face of the challenges of decarbonisation in the maritime, aviation and heavy goods transport sectors, Lanza pointed out the strategic role played by eco-fuels that offer
“Last year we began operating the first and, for the moment, only hydrogen station in the Madrid region,” Lanza said. “We aim to provide hydrogen transport and storage services. For this reason, we have also entered the hydrogen market in the US, the world leader in adapting those supply chains”, he added, while also emphasising the possibilities offered by ammonia. Exolum kicked off 2024 by purchasing a 50 per cent stake in the largest ammonia storage, import and export terminal in the US, located on the Houston Channel, now named Vopak Exolum Houston. “We strive to be a relevant player in this transition by developing and operating the infrastructure required by these new energy solutions,” stated Lanza.
Exolum has plenty of other initiatives underway in alternative fuels, as Lonza explained: “Our pipelines already transport HVO (pure biodiesel) and we are implementing pilot projects for hydrogen transport through liquid carriers, which increase safety because they are neither flammable nor toxic. This is an emerging technology that we are already promoting this year. We are also adapting our terminals at the main ports. At the Madrid and Barcelona airports we can store and
Lanza noted several key milestones in the company’s international expansion over the past few months. For example, Exolum has secured the contract for the operation and maintenance of the fuel supply facilities at Paris-Charles de Gaulle airport and is currently developing a green hydrogen production plant and refuelling station at its Riverside terminal.
More recently, Exolum has been appointed by the Port Authority of Gijón in north-west Spain to manage the 67,000-m3 bulk liquids storage terminal at La Osa pier. The 15-year contract also involves Exolum investing €3m to connect the site to its own terminal in the port, and to modernise and adapt the infrastructure to provide a wider range of logistics services. This will focus in particular on the energy transition and decarbonisation and the contract gives Exolum an opportunity to invest in a larger number of tanks to transport and store new energy vectors, such as biofuel, eco-fuel, hydrogen, ammonia and methanol.
“At Exolum, we are committed to investing in Spain and, particularly, to developing logistics investments at ports that support the energy transition,” says Jorge Guillén, Exolum’s Spain Region Lead. exolum.com
Enterprise Products Partners has received a deepwater port licence from the US Maritime Administration (Marad), enabling it to move forward with the development of the planned Sea Port Oil Terminal (SPOT) offshore crude oil loading terminal. The offshore platform will be located some 30 nm off the coast of Brazoria County, Texas in 115 feet (35 metres) of water and will be capable of loading 2m bbl per day. The plan includes construction of dual 36-inch bi-directional pipelines to connect the platform to the planned Oyster Creek crude oil terminal some 10 miles inland.
Use of SPOT will obviate the need for offshore loading of VLCCs by ship-to-ship transfer from smaller tankers, significantly reducing crude oil vapour and other greenhouse gas emissions, Enterprise says. “With US exports of crude oil at 4m bpd, SPOT offers a more environmentally friendly, safe, efficient and cost-effective way to deliver crude oil to global markets,” says AJ ‘Jim’ Teague, co-CEO of Enterprise’s general partner. www.enterpriseproducts.com
Global Partners has acquired four bulk liquids terminals in north-east US from Gulf Oil for a
price of $212.3m. The four sites, in Chelsea, MA, New Haven, CT, Linden, NJ and Woodbury, NJ, together offer some 3.0m bbl of shell capacity, expanding Global Partners’ ability to store and distribute gasoline, distillates and ethanol. The move aligns with Global’s strategy to acquire and invest in assets that allow the partnership to leverage scale from its integrated network in high-demand markets.
“This acquisition further delivers on our commitment to strategic growth and our ability to identify and capitalise on assets that leverage our growing network,” says Eric Slifka, president/CEO of Global Partners. “We are happy to finalise this acquisition and welcome these terminals into our growing network. These assets will strengthen our existing operations and provide us with new opportunities to serve our customers and enhance our competitive advantage.”
www.globalp.com
CST Industries, which specialises in dome roofs and storage tanks, has acquired Ostsee Tank Solutions (OTS), which is a leading provider of innovative aluminium domes and covers for tanks. OTS will enhance CST’s ability to deliver exceptional value and service
to customers globally, CST says. OTS is based in Stralsund, on the Baltic coast in northeastern Germany.
“We are thrilled to welcome Ostsee Tank Solutions to the CST Team,” says Jeff Mueller, president/CEO of CST. “This acquisition aligns with our commitment to innovation and customer satisfaction, and we look forward to leveraging our combined strengths to drive growth and success on a global scale.”
“With this acquisition, Ostsee Tank Solutions will gain access to cutting-edge aluminium dome and cover solutions,” adds Thomas Schmidt, managing director of OTS. “These state-of-the-art solutions are designed to meet the evolving needs of customers in various industries worldwide.”
www.cstindustries.com
Moda Midstream II LLC, formed late last year, has secured an equity commitment from EnCap Flatrock Midstream, which had been a major investor in the first Moda Midstream operation. Moda II aims to provide a wide range of independent midstream solutions to refiners, petrochemical manufacturers, producers and marketers of traditional energy, as well as companies developing transition fuels. Moda II is focused on providing safe and reliable last-mile storage and transport solutions with an emphasis on deep-water capabilities.
“I am grateful for the opportunity to once again partner with the EnCap Flatrock team, following the completion of our successful investment together in Moda Midstream LLC,” says Moda II CEO Bo McCall. “We see tremendous opportunity in the market and anticipate leveraging our deep commercial strengths and experience to develop and build superior waterborne terminals.”
“We are excited to partner with the Moda II team and to continue our relationship with a
skilled industry veteran like Bo,” adds EnCap Flatrock Midstream managing partner Gregory C King. “Bo has assembled another strong team with a complementary skill-set and broad range of experience setting up Moda II for the next wave of energy investing. The Moda II team is well-positioned to execute on their strategy, which is primarily focused on development activities along the US Gulf Coast.” www.modamidstream.com
Oiltanking Americas has formed a joint venture with Grupo Edson Queiroz (GEQ) and Copa Energía, OT Gás Nordeste (OTGN), based in the city of Ipojuca in Pernambuco, Brazil. OTGN will develop, build and operate a greenfield LPG terminal with 120,000 m3 of refrigerated storage in Suape.
The project aims to increase the security of LPG supply in the north-east of Brazil by expanding the capacity for local supply and making it possible for independent companies to import gas by fully loaded VLGCs.
Oiltanking Americas, which has a 42.5 per cent share in the venture, will handle terminal operations and commercial aspects. It says a final investment decision will be taken in the first half of 2025, with the terminal expected to begin operations in mid-2027. www.otamerica.com
Petregaz India has inaugurated its new LPG import and storage facility at the Adani port in Krishnapatnam, Andhra Pradesh. The terminal has two 30,410-m3 refrigerated tanks, one each for propane and butane, two 700-m3 mounded tanks, a modern jetty capable of berthing all LPG tankers, two gantries with a total of 16 truck loading pays, and an on-site laboratory. The terminal is designed to handle up to 1.4m tonnes of LPG per year.
“Government-run oil companies can utilise our terminal’s capacity to improve LPG supplies in the hinterland, optimising logistics and strengthening India’s LPG landscape,” says Susheel Raina, CEO of Petregaz India. “This
new facility will also benefit private marketers and bottlers by improving access to LPG in an area of the country historically underdeveloped in terms of LPG infrastructure.” petredec.com
Stolthaven Terminals has reported revenues of $76.8m for the three months to end February, up from $74.0m a year earlier. Storage and throughput revenue rose by 4.6 per cent and volumes rose 10 per cent in a continued tight market. Operating profit rose from $25.1m last year to $28.5m.
“Stolthaven Terminals produced record operating results for the quarter, fully focused on executing the strategy of bringing in higher-margin business,” says Udo Lange, CEO of parent company Stolt-Nielsen. The company expects the tight market to continue, with a return to growth in chemical output and ongoing demand from biofuel feedstocks and other specialty liquids. “We anticipate a flat first half of 2024 with slightly improving earnings during the second half of the year as we continue to optimise our contract portfolio,” the company says.
www.stolt-nielsen.com
Yara Clean Ammonia and Azane have been granted a safety permit by Norway’s Directorate for Civil Protection (DSB) for the
construction of the planned ammonia bunkering facility in Florø. The planned terminal consists of a floating tethered barge with a capacity of 1,000 m3/650 tonnes of ammonia. DSB has allowed for 416 bunkering operations per year. The partners expect many of the customers for the ammonia will be offshore support vessels, which call regularly at ‘Fjord Base’ in Florø. The partners now have to obtain a permit from the local municipality before a final investment decision can be made.
“This marks a milestone for ammonia as a fuel,” says Steinar Kostøl, vice-president, projects and products at Azane. “Now we finally know with certainty the safety zones we will have to operate under when bunkering ammonia. The required safety zones are very encouraging and demonstrate how it will be possible to bunker ammonia in the biggest and busiest ports around the world.”
azanefs.com
Rubis has reached a final agreement with I Squared Capital on the sale of its 55 per cent shareholding in the Rubis Terminal joint venture. This follows consultation with employee representatives and the agreement of the company’s social and economic committee. The sale remains subject to the customary regulatory approvals but is expected to be concluded around the middle of this year. www.rubis-terminal.com
FLEETS • ITCO’S ANNUAL GLOBAL FLEET REPORT SHOWS THAT DEMAND FOR TANK CONTAINERS IS STILL RISING, EVEN IF THE RATE OF INCREASE HAS SLOWED AS SUPPLY CHAINS HAVE NORMALISED
THE TANK CONTAINER business has experienced some sharp ups and downs over the past few years, as volatility and disruption in global liquids supply chains prompted changes to trade patterns and volumes. Many operators did very well financially for a while as tanks were retained by receivers to act as temporary storage, at a time when ‘just-intime’ inventory management gave way to ‘just-in-case’ stockholding. At one time, as much as 15 per cent of the global tank container fleet was held on demurrage, according to the International Tank Container Organisation (ITCO).
Those conditions helped support rapid growth in the global tank container fleet, building on increases in pre-Covid years as shippers were attracted to the flexibility and safety offered by tank containers for the transport of bulk liquids and gases. However, as had been expected, the unwinding of those disruptions in supply chains and the
consequent destocking by cargo owners, coupled with the high rates of growth in previous years, led to something of a cooling down in the business in 2023.
Nevertheless, ITCO calculates that the global fleet grew by 5.8 per cent during 2023 to reach 848,400 tanks in service at the end of
TABLE 1
the year, with some 56,600 new units joining the fleet from manufacturers, mostly from China, compared to 67,865 in 2022. At the same time, ITCO says, the reduction in utilisation by both tank operators and leasing companies has led to more tanks standing idle and also to an increase in the number of ageing tanks being disposed of for, a sharp increase on previous years. Nearly 64,000 tanks owned by leasing companies were said to be idle at the end of 2023, well up on the figure of 36,930 quoted for a year earlier.
ITCO estimates that around 10,000 tanks were retired during 2023. The disposal of old tanks is a relatively new phenomenon; tank
*shipper, military and other Source: ITCO
containers are designed for a working life of 20 to 25 years but, with careful maintenance and, when necessary, repairs, they can easily last longer, as the stainless steel barrel is both hard-wearing and valuable in itself.
More recently, though, ITCO reports that older tanks are being retired because they are wearing out, or they are too heavy compared to newer models and therefore less productive. In its 2024 Global Fleet Survey, ITCO asked members about rates of disposal, which has given it confidence in its estimate. It seems there may also have been some pent-up retirement demand, as older, smaller tanks were used for storage during the pandemicrelated disruption and surging demand.
Another important factor in this equation is the price of new tanks, which depends primarily on the price of stainless steel but also on the manufacturing environment. There have been some changes in China over the past year that made ITCO reluctant to estimate production numbers by manufacturer but it is also clear that prices for new tanks are currently at a high level and may well stay that way for the rest of this year; this will make the remanufacturing of older tanks more attractive.
ITCO’s annual survey draws data from its own membership and also from other known
Source: ITCO
operators and leasing companies, as well as equipment suppliers. ITCO says that there are more than 240 tank operators in the world, the ten largest of which represent just over 50 per cent of the total fleet.
There has been relatively little change in the list of the top ten owners in recent years, though some new players have emerged in Asia. But Stolt Tank Containers (STC) remains the largest in terms of fleet numbers, having now passed the 50,000 figure and having added more than 10,000 tanks over the past four years. Hoyer has also grown in the past two years and is now the only other operator to have more than 40,000 tanks in its fleet.
NewPort retains its third place in the list, despite not having added significantly to its fleet since 2021; the company is now owned by Shanghai-based Gentco Logistics, which also owns Albatross Tank Leasing. Other leading players include the European firms Bertschi, Den Hartogh and Bulkhaul, each of which has been slowly building its fleet. A relative newcomer to the list is Singapore-based E-Way Group, which offers a range of services for liquid cargoes and has rapidly built a 21,000-strong tank container fleet. Also moving fast is Legend Global Logistics, also based in Singapore, which describes itself as a one-stop logistics provider for bulk liquid and dry commodities as well as perishables and general cargo.
In comparison with the tank container operator business, tank container leasing is relatively concentrated, with the ten largest names accounting for around 85 per cent of the lessor-owned fleet. Indeed, ITCO identifies fewer than 40 such companies around the world. Exsif Worldwide remains the largest of them, with more than 70,000 tanks under its control. Chicago-headquartered Exsif is part of Marmon Holdings, which itself is owned by Berskhire Hathaway.
Eurotainer kept its second place in the list of leasing companies this year, though its fleet dropped by 5,000 units; on the other hand, sister company Raffles Lease increased its fleet by 5,000 so between them they still control a larger tank fleet than Exsif. Both are part of Streem, formerly Ermewa Group, which was owned by the French state company SNCF Group until being sold to
EXSIF is one of the world’s largest, and most trusted ISO tank leasing companies for tank container solutions. EXSIF provides reliable and sustainable equipment combined with best-in-class services that enable the global movement of products essential to everyday life. Leverage our 20+ years of experience and expertise serving the tank container industry.
50+ GLOBAL DEPOT PARTNERS
70,000+ TANKS WORLDWIDE CUSTOM
investors Caisse de dépôt et placement du Québec (CDPQ) and DWS Group in October 2021. Streem also owns Demi Container Services, which offers tank repair, refurbishment and inspection services in Rotterdam and Houston.
In general, the major lessors have not added significantly to their fleets over the past year, though GATX-owned Trifleet Leasing and Peacock Container, which was acquired by Arcus Infrastructure Partners in early 2021 and subsequently bought GEM Containers, are both growing gradually.
Speaking about the results of this year’s survey, Paul Gooch, who assumed the role of president of ITCO at the start of the year, says: “The global tank container fleet continues to grow, although at a slightly slower rate in 2023 compared with previous years. This was to be expected, considering the variety of economic and geopolitical headwinds being experienced by the chemical industry, and weakness in global GDP growth.”
The industry also had to reckon with a correction after the record year in 2022, which had been fed by the supply chain disruption resulting from the Covid 19 pandemic. ITCO predicted in its 2023 report that the ramping up of production (mainly in China) to meet short-term demand was likely to result in an over-supply of tanks that would be followed by an adjustment in output. This year’s report appears to indicate that, while that prediction was true, the correction has not been as severe as expected.
As ITCO was preparing its 2024 report, the worsening situation in the Red Sea was forcing some of the major container lines to re-route their sailings via the Cape of Good Hope; ITCO says the impact of this has, so far at least, not been as severe as that experienced during the Covid-19 pandemic, though the added time for vessels to move between the major hubs in Asia and Europe is effectively adding to tank demand.
Despite the slow-down in the growth of the industry, the massive disruption and challenges in the supply chain over the past three years have proved that the tank
container can play a critical role in the ‘just-in-time’ business philosophy of the major end users - the shippers. There is also evidence suggesting that with China becoming increasingly self-sufficient in chemicals, and its demand growth lower than forecast, as well as other factors, there could be a trend away from global supply chains to more local-for-local supply chains, which could present a promising opportunity for tank containers supplying less accessible markets.
As to the future for ITCO itself, Gooch says: “ITCO will continue to drive initiatives supporting safe working practices, environmental best practice, and efficiency improvements through global standards and
digitalisation. But we will be more diverse and inclusive in our approach. We will also focus on expanding our geographical footprintrecognising the need to be more present and active in the Americas, India, and Asia Pacific. The location of our events and agenda content will also reflect this geographical diversity, and the need to leverage technology advances.”
ITCO has organised its regular ITCO Village at the at the upcoming Transport Logistic China event in Shanghai, which takes place from 25 to 27 June; for more information, go to www.transportlogistic-china.com.
ITCO’s 2024 Global Tank Container Fleet Survey can be consulted in full via the ITCO website, www.itco.org.
THE RIGHT TANK FOR THE RIGHT CARGO
safe transportation of hazardous and non-hazardous bulk liquids, gases (including Cryogenics) and bulk powder products.
Seaco offers a modern and diverse tank fleet, suitable for the storage and WHY
• Quality build
• Fully intermodal T11-T75 tank types
• Dedicated technical team support
• Flexible leasing plans
• Customised tank solutions available
• Global network of specialised depots
COMBINED TRANSPORT • THE MODAL SHIFT TO GET FREIGHT OFF THE ROADS HAS LONG BEEN A LYNCHPIN OF EUROPE’S EMISSIONS POLICY BUT, ECTA SAYS, IT IS JUST NOT HAPPENING
EU AUTHORITIES HAVE set tough targets for decarbonisation in all walks of life and business areas; they are enshrined in the Green Deal and the European Commission’s ‘Fit for 55’ document. For the transport sector, it is taken as understood that road is the least sustainable mode of all and that getting freight off the roads and onto rail or inland waterway provides a simple way of reducing the environmental impact of moving product.
The European Chemical Transport Association (ECTA) is worried about how this is playing out; its members – transport service providers to the chemical industry – have been investing in combined transport solutions over the past few decades, the better to enable this modal shift, but recent data suggests that the
modal shift has gone into reverse.
Based on the annual Responsible Care reports submitted by its members, ECTA calculates that the share of shipments using combined transport has fallen consistently over the past five years. In 2019, 47.8 per cent of shipments went entirely by road and 52.2 per cent at least partly by rail; by 2023, road’s share had gone up to 54.6 per cent and rail’s share had fallen to 45.4 per cent.
ECTA says that combined transport is seen as an important enabler of the EU’s Green Deal but, in some major countries, the desired modal shift is going in the wrong direction. The reasons are clear: rail networks lack the capacity needed to handle the additional freight; the punctuality of train operators is not
as good as it needs to be; infrastructure works exacerbate the lack of punctuality and cause further reductions in carrying capacity; all this leads to delays and cancelled trains. Shippers who need reliability are not finding it in the rail sector, ECTA says.
What is worse, ECTA says, is that some countries are actively working against the modal shift. In Germany, for instance, the government has decided to cut subsidies for rail operations in the Route Promotion Act (Trassenförderungsgesetz or ‘Trafög’).
National decisions such as these are in contradiction with EU policy and should be revised, ECTA stresses.
Despite the actual situation, ECTA and its members will continue to invest in combined transport solutions. “We believe that this mode of transport does not only contribute to a reduction of emissions, combined transport also positively contributes to the competitiveness of the European economy and the overall mobility across Europe,” ECTA says. “We trust that the chemical industry players will follow us along this path.”
ECTA has been supportive of recent efforts by the European Commission to amend the Council Directive 92/106/EEC on intermodal transport (the ‘Combined Transport Directive’ or CTD), saying that an update of the support framework will be instrumental in meeting the ambitions of the Green Deal as well as the Sustainable and Smart Mobility Strategy.
However, ECTA has also challenged the proposals, particularly as regards their limiting definition of combined transport, which does not reflect the complexity of international intermodal transport. ECTA says it is inappropriate to regard each individual shipment as a potential ‘combined transport’ operation, since combined transport only works through the aggregation of individual road transport demand on a certain lane and bundling that demand to a train or vessel. “Combined transport is a complex system. Its definition cannot be reduced to an external cost saving target on each individual journey,” ECTA stresses. www.ecta.com
Telematics
Telematics solutions for enhanced product traceability and supply chain management.
Sustainable Solutions
Sustainable solutions for reducing the carbon footprint of ISO tank operations.
Fleet Management
Fleet management services for reduced operational costs.
24/7 Fleet info
24/7 Cloud-based accessibility to fleet information and documentation.
Advice
Expert advice on product compatibility.
With more than 30 years experience in ISO container tank leasing, Peacock offers global availability of standard and special ISO tanks for a wide variety of petrochemicals, liquid food products, bitumen, liquefied gases and cryogenic gases.
Singapore The Netherlands China USA
info@peacock.eu
www.peacockcontainer.com www.tankcontainer-sales.com
LOGISTICS • HGK SHIPPING IS REORGANISING ITS OPERATIONS IN BELGIUM, AFTER SELLING ITS HOLDING IN DGA SHIPPING TO ITS ERSTWHILE PARTNER RHENUS
HGK SHIPPING HAS relaunched its Belgian business under a new name, HGK Logistics Antwerp, following the sale of its 55 per cent shareholding in DGA Shipping to its partner Rhenus. HGK Logistics Antwerp will fulfil customer requirements for inland tanker shipping as well as logistics services in the Port of Antwerp-Bruges, taking account of the major changes taking place at the port in light of the energy transition.
On the one hand, the Port of AntwerpBruges is planning to reorganise its operations at its terminal structures as part of the energy revolution – for example, by providing extensive storage capacity for hydrogen or its derivates. On the other hand, the world’s second largest chemicals port still offers a great deal of potential for hinterland traffic services using inland waterway vessels – and not least for transport services to
top-performing German business regions. HGK Shipping believes there is plenty of growth potential for its new venture in these fields.
“We’re using the sale of our holding in DGA Shipping BV to reorganise our operations and we want to continue to play an important role in an attractive market such as Belgium,” says Steffen Bauer, CEO of HGK Shipping.
“We’re offering our regular customers an extensive range of services for logistics tasks locally and transport services to hinterland destinations from this central hub for European cargo handling.”
“Our new office is a clear expression of our strong commitment both to the Port of Antwerp-Bruges and our aspiration to integrate sustainable supply chains along
inland waterways to and from the major North Sea ports even more strongly into the mix of modes of transport in our business activities within the HGK Group,” Bauer adds.
The new company is being led by joint managing directors Dirk Verstraeten (pictured, right), who has moved over from DGA Shipping, and Simon Lucas (left), who was previously leading the Wijnhoff & Van Gulpen & Larsen (Wijgula) inland tanker operation. Lucas will largely focus now on managing tanker shipping activities while Verstraeten will bring his many years of experience in chemical logistics to bear, especially in those kinds of operations that involve HGK Logistics Antwerp acting as port agent for shipping companies and their customers from around the globe.
Meanwhile, DGA Shipping is now part of Rhenus PartnerShip, where it offers dry bulk, general cargo and project load shipping to all ports on the Rhine system. Rhenus intends to use the acquisition to secure a strong competitive position. “We’ve greatly expanded the DGA business with HGK during the last few years, particularly in the field of chartering. However, there has been and there still is a great deal of potential that we now want to further develop,” says Thomas Maassen, CEO of Rhenus PartnerShip. www.hgk.de
ACQUISITIONS • SINCE ACQUIRING A&R LOGISTICS, NOW RENAMED QUANTIX, IN 2019, WIND POINT PARTNERS HAS INVESTED TO EXPAND ITS OPERATION, WITH TWO DEALS ANNOUNCED IN APRIL
HOUSTON-BASED QUANTIX HAS made 11 acquisitions since it was formed following investment by specialist transport and logistics fund Wind Point Partners. Perhaps the most significant of these was announced at the start of April, when it acquired CLX Logistics, which has more than 25 years’ experience in liquid bulk 3PL services and related activities in North America and Europe. The addition of CLX bolsters Quantix’s existing supply chain service offerings for the chemical industry. Together, the two companies create a platform with more than $2bn in logistics spend and will be one of the largest providers of global chemical logistics services.
“This deal is a significant step for Quantix as a leader in the chemical 3PL market and will bring meaningful value to our customers as we integrate a wide-ranging set of offerings, technology and analytics products into our portfolio,” says Chris Ball, president/CEO of Quantix. “We’re proud to have the CLX team as part of the Quantix family of companies, and congratulate founder J Stephen Hamilton on the exceptional business he has built.”
“The CLX team has created a comprehensive suite of solutions that accent our existing offerings to our valued customers,” adds Konrad Salaber, managing director of Wind Point Partners, owner of
Quantix. “Expanding our 3PL offering by adding liquid capabilities was an important pillar of our value creation plan, and by partnering with CLX we have become one of the largest chemical 3PL companies in our network. We look forward to continuing to deliver a full suite of services to our customers.”
A week after announcing the CLX deal, Quantix took another step in its growth strategy by acquiring Space City Services, which specialises in the transport of hazardous and non-hazardous chemicals and wastes in the US Gulf Coast region. “This acquisition is important for Quantix as we continue to lead the chemical industry in being a comprehensive provider of supply chain solutions for every need,” says Ball. “Space City builds nicely on our portfolio and further expands the ways in which we can provide the best service to customers.”
“We’re thrilled to continue providing our services to our current customers while bringing even more value through Quantix’s powerful suite of transportation, export, packaging and warehousing services,” adds Space City founder Rob Thomas. “Our customers are at the heart of everything we do, and pursuing this next chapter with Quantix means all of our customers benefit from our shared commitment to provide high-quality services and solutions.”
Quantix is now organised in six divisions: 3PL Solutions, where it claims to be the largest chemical-focused 3PL and freight broker in North America; transport services for liquid and dry bulk, packaged goods and intermodal containers; in-plant logistics and resin enhancement services; distribution and warehousing; export/import services in Houston, Charleston and Savannah; and eco-recovery of solid wastes, including transport and disposal.
These two deals will not be the last; Quantix says its acquisition strategy will continue to focus on acquiring companies that provide dry and liquid bulk transportation, warehousing, export and logistics services to producers and distributors of chemicals nationwide. quantixscs.com
TANKS & LOGISTICS
Stolt Tank Containers (STC) has reported revenues of $156.1m for the three months to end February, well down on the $193.9m posted a year ago. Transport revenue fell by 14.2 per cent as a result of lower ocean freight costs but demurrage revenue, which had been at very high levels in recent years in response to supply chain disruptions, dropped by 31.2 per cent. Despite a 22 per cent increase in shipments and an 8.1 per cent increase in STC’s tank fleet over the year, operating profit fell from $39.3m a year ago to $13.3m.
Commenting on the results, Udo Lange, CEO of parent company Stolt-Nielsen, says: “Shipment volumes continued to increase as we hit a record 40,047 shipments during the first quarter – an increase of 22 per cent from the same quarter last year – as we continue to grow our market share. The reductions in margins and demurrage revenue that we experienced during 2023 now seem to have levelled off.”
To counter the recent erosion of margins at STC, the focus has been on increasing volumes and the company expects to see its results stabilising around current levels. In the near term, the restricted transit of the Suez Canal is expected to cause a reduction in freight capacity as customers move to stockpile inventory to counter supply chain disruptions. STC also reports firming demand out of the Americas and south-east Asia, with Chinese exports also picking up.
www.stolttankcontainers.com
Leschaco has opened a new chemical warehouse in Moerdijk, located conveniently between Rotterdam and Antwerp and offering optimal connectivity to the European hinterland. The 29,000-m2 facility offers space for some 45,000 pallets in five sections, four of which are designed for hazardous goods.
“We are happy to further expand Leschaco’s presence in contract logistics with the opening of our newest dangerous goods warehouse,” says Constantin Conrad, CEO of the Leschaco Group. “This strategic facility in Europe enables us to meet the growing demand of our global customers in the region and reinforces our commitment to providing our customers with innovative and tailored supply chain solutions.”
Sebastian Haebler, Head of Global Contract Logistics at Leschaco, emphasises the importance of the new warehouse: “The opening of our newest facility in Moerdijk is another milestone in Leschaco’s commitment to providing its customers with world-class solutions to their logistics challenges. This strategically located warehouse enables us to provide customised support to our global customers across multiple sectors, including chemicals, healthcare, automotive, industrial materials and consumer goods.”
In addition to its operational capabilities, the new ADR warehouse in Moerdijk is also an example of Leschaco’s commitment to
sustainability. The facility is equipped with solar panels on the roof, which cover part of its electricity needs, and incorporates various environmentally friendly measures, including electric underfloor heating, LED lighting and the highest building standards for insulation. In addition, the proximity to the port of Moerdijk enables environmentally friendly transport options such as barge and rail, complemented by e-charging stations for electric vehicles. www.leschaco.com
Rhenus Ireland has opened a new 11,150-m2 warehouse facility in Dublin, significantly expanding storage capacity in the country. The new facility will provide increasingly integrated management of the company’s portfolio services across sectors, including energy management, life sciences and healthcare, industrial, retail, chemicals, food and beverage and automotive, in addition to a wide range of critical local industries.
Declan Sinnott, managing director of
Rhenus Ireland, says: “I am pleased to confirm the opening of our new Dublin facility which is designed to enhance our service offerings and extend the services we deliver to our customers across a wide range of industries. Coupled with our continued investment in our Galway operation earlier this year, the opening of the Dublin facility is yet another statement of our continued commitment to support the Rhenus customers in the Irish market.”
www.rhenus.group
Greiwing has opened a new logistics facility in Rheinmünster, close to the French border in south-west Germany, offering 15,500 pallet spaces for a range of goods. The new location offers shorter transport routes for many existing and potential future customers, having its own rail siding and being close to a Rhine port and regional airports.
Evonik will be a major customer for the new site. Greiwing had previously been handling its products at another site some 30 km away from Evonik’s Rheinmünster plant, which is now
only 500 metres from the new Greiwing facility. Harald Plöchinger, site manager of the Evonik superabsorber plant in Rheinmünster, and Bernd Nahler, Head of Global Logistics, say: “With the new Greiwing logistics centre in the middle of the chemical park in Rheinmünster, we will have short transport routes in the future and this will enable us to simplify processes and have very flexible scope for action between production and logistics.”
www.greiwing.de
Suttons has expanded its fuel distribution fleet with its 100th truck, part of a batch of four Volvo FM units. The new trucks are said to be 10 per cent more fuel-efficient than other units, contributing to a reduction in CO2 emissions, and are also lighter, allowing a higher payload. They are also fitted with Microlise telematics, which monitor driving style, and full outward facing camera systems.
“Our trucks are run day and night so ensuring we can deliver our promise to customers is paramount. Having the latest
specification of trucks, coupled with high performing in-house workshops, ensures we minimise the potential for service delays,” says David Heath, head of fuels at Suttons.
www.suttonsgroup.com
Bertschi has commissioned two additional covered storage halls, each occupying 3,000 m2, at its STR Tank Container Cleaning facility in Schwarzheide in eastern Germany.
Construction began a year ago, with trial operations in the first new hall successfully concluded in February this year. The work responded to escalating demand for covered storage, adding 5,200 spaces to the existing capacity of 8,500 spaces.
www.bertschi.com
Vervaeke is to test the use of a hydrogenfuelled truck, starting in mid-2024. The Belgian carrier is one of five transport firms to take part in the trial of the prototype Mercedes Benz GenH2 truck, which is powered by hydrogen fuel cells. As such power trains are not yet authorised for use with ADR cargoes, the trial will involve the transport of PVC in a silo bulk trailer for Ineos Inovyn, which produces PVC at its Rheinberg plant. Ineos Inovyn also produces green hydrogen at its Antwerp plant.
The new truck uses subcooled liquid hydrogen as the sole fuel, which is used to charge a battery that drives the motors of the drive axle. This is a more advanced technology than using compressed hydrogen and Mercedes Benz and its carrier partners will be monitoring its performance during the one-year trials.
“We are delighted to support these fuel cell customer trials,” says Wouter Bleukx, business director hydrogen at Ineos Inovyn. “Hydrogen is a game-changing source of energy which will transform truck technology and help us reach a net zero future. As both a user and producer of hydrogen, Ineos is in a unique position to support this transition and we are excited to work with Vervaeke.”
www.vervaeke.com
PRODUCTS • ALTHOUGH BUSINESS CONDITIONS HAVE BEEN TOUGH, GREIF CONTINUES TO EXPAND ITS INDUSTRIAL PACKAGING PORTFOLIO, WITH NEW PRODUCTS LAUNCHING IN EUROPE
GREIF HAS PARTNERED with CDF Corporation on a new version of its GCUBE IBC Flex, engineered specifically for transporting highly sensitive and liquid products under sterile conditions. The new unit, which is available in Europe and Scandinavia, features an enhanced aseptic liner developed by CDF Corporation. The advanced Form-Fit™ liner is said to outperform conventional IBC liners, offering superior evacuation capabilities, and its unique design means it opens as a square to fit the internal shape of the IBC and fills automatically.
“We collaborated closely with CDF throughout the development process to
ensure we delivered an upgraded product that meets the exacting needs of our customers,” says Jacob Demen, sales director, Scandinavia at Greif. “We needed to partner with an organisation like ours that prioritises sustainability at its core. Furthermore, our commitment to sustainability is reinforced by our collection and reuse or reconditioning of the entire GCUBE IBC Flex system, including the liner and outer structure, making it an ideal choice for closed-loop operations.”
“The launch aligns with our overarching innovation and investment strategy, which prioritises the development of sustainable solutions that not only enhance customer satisfaction but also uphold product integrity and safety,” adds David Khanna, UK sales director.
CDF Corp has also recently opened a new production line for Form-Fit IBC liners in Germany, expanding its ability to deliver linings for different customer needs.
Greif is currently manufacturing the GCUBE IBC Flex at its sites in Sweden, the Netherlands, the UK and Turkey, with US production slated to start up in the third quarter.
Greif is also planning to expand its jerrycan portfolio in Scandinavia with the introduction of a 10-litre Jerrycan Reinforced (JRC) unit, complementing the existing 20- and 25-litre JRCs. The 10-litre model features a special structure, engineered to enhance stability and facilitate safe stacking, despite being 20 per cent lighter in weight than competing jerrycans on the market.
“Scheduled to launch production in Q3 2024, this innovation not only improves efficiency but also contributes to reducing overall carbon emissions,” the company states.
Greif has reported net income of $67.2m for its first fiscal quarter 2024, to end January, compared to $89.9m a year ago; adjusted EBITDA also fell, from $164.5m to $128.0m, in tough trading conditions.
“Greif once again has produced solid financial results in a challenging operating environment,” says Ole Rosgaard, president/ CEO of Greif. “Our team continues to navigate this extended slow demand environment, while making structural improvements to the business under our Build to Last Strategy. We will continue to focus on controlling what we can control while we invest for the future as we approach closing the Ipackchem acquisition and advance other exciting strategic initiatives.”
In the Global Industrial Packaging segment, net sales were down by $19.2m at $686.6m, primarily due to lower volumes and also lower average selling prices. Gross profit improved by $10.0m to $135.3m as a result of lower raw material costs.
Greif cannot, however, make any firm forecasts for the rest of this year, stating: “Given the deterioration of product demand in the past year and the degree of uncertainty in the forward looking macro-economic environment, we continue to be unable to determine the trajectory of product demand for the remainder of the fiscal year.” www.greif.com
PARTNERSHIP • MAUSER IS CONTINUING TO BUILD ITS GLOBAL PACKAGING PRESENCE, WITH A NEW PARTNERSHIP WITH RIKUTEC AND THE ADDITION OF CONSOLIDATED CONTAINER IN THE US
MAUSER PACKAGING SOLUTIONS has entered into an exclusive partnership with Rikutec Packaging for the global production and promotion of sustainable intermediate bulk container (IBC) solutions. Under the strategic alliance, Mauser will add Rikutec’s IBCs to its project portfolio and together they will launch a heavy-duty 1,000-litre IBC produced with recycled plastics, the new Mauser Poly IBC MT Series.
The Mauser Poly IBC MT is available in different variations to meet the special requirements of many industries and can be equipped with digital IT devices to foster end-to-end supply chain connectivity, providing real-time tracking and tracing, visibility, and risk mitigation. With the integration of real IoT, customers can stay in
touch with their container/product, having around the clock visibility to product fill levels, location, temperature, shock information, as well as technical documentation, manufacturing data, and loop information (number of fillings and returns).
“Mauser Packaging Solutions is excited about the partnership with Rikutec to bring their innovative IBC solutions to our customers,” says Michael Steubing, president, international of Mauser Packaging Solutions.
“Both companies are focused on providing leading edge sustainable product solutions that offer reduction of CO2 emissions to customers, and their product portfolio is a perfect addition to ours. Our mutual commitment to sustainability, digitalisation, and providing customers with new multi-trip
packaging solutions that safeguard their filling goods is a great combination.”
Bodo Richter, president/CEO of the Rikutec Group, adds: “Together, Mauser Packaging Solutions and Rikutec Packaging are determined to make a real difference in the market. Mauser Packaging Solutions’ proven expertise and vast network will be instrumental in making the Mauser Poly IBC MT Series, specially designed for Mauser Packaging Solutions, a familiar sight around the world, paving the way for a more sustainable future with state-of-the-art multi-trip packaging solutions.”
In North America, Mauser Packaging Solutions has acquired “substantially all of the assets” of Consolidated Container Co, a manufacturer, reconditioner and distributor of industrial containers with facilities in Minneapolis and Kansas City, in a deal that is expected to be highly complementary to Mauser’s existing business.
“The acquisition of Consolidated Container complements the Mauser product and service portfolio in many ways and creates tremendous opportunity for our customers, employees, and suppliers,” says David Vergo, president of Mauser’s North America Industrial Packaging segment. “We welcome the Consolidated Container employees to the Mauser family and look forward to their contributions in supporting our mission of providing customers with the highest quality products and the most dependable service.”
“It has been an honour to serve our customers, represent our suppliers, and work with our employees for the past many years,” adds Phillip Dworsky, CEO and co-founder (along with his brother William) of Consolidated Container. “William and I truly appreciate our team’s dedication and commitment to excellence and look forward to the new opportunities that will be created for our valued customers and team members as part of the Mauser organisation.”
Mauser Packaging Solutions, an affiliate of Stone Canyon Industries and headquartered in Oak Brook, Illinois, now has manufacturing locations in 20 countries.
mauserpackaging.com www.rikutec.de
HCB is the number one voice on all issues concerning the transport of dangerous goods. Subscribe today for FREE and stay connected with access to 11 issues per year, our weekly newsletter and premium web content.
Labelmaster’s DGeo Packaging Division has been named as the first premium North American distributor of Dolav’s AkkuGrain plastics shipping containers. Now available as part of Labelmaster’s Obexion protective packaging, Obexion AG offers a safe, simple and cost-effective packaging solution for transporting and storing lithium batteries.
Lighter than other products on the market, these reusable containers are highly durable and can be filled up with as many batteries that fit in the unit, regardless of type or state of charge. These boxes are ADR-compliant, P911 and P908 certified, DOT Special Permit, and TÜV-tested. Designed specifically for lithium batteries, AkkuGrain works by instantly reducing temperatures in case of a thermal runaway, dousing the fire while simultaneously cutting it off from further oxygen and neutralising toxic gases, emitting them from the container as water vapour.
“The lithium battery market continues to grow and our DGeo Packaging Division is committed to offering the widest breadth of products, training, technology and services for shipping and handling lithium batteries,” says John Glaser, director of packaging development at Labelmaster. “Partnering with Dolav to offer AkkuGrain containers as part of our Obexion line of protective packaging allows us to extend our wide range of lithium battery packaging solutions that help businesses ship lithium batteries safely, compliantly and cost-efficiently.”
Labelmaster’s DGeo packaging division has further expanded its portfolio with a range of collapsible wooden crates under the Obexion Max banner. The packagings, developed by Action Wood 360, are designed for use with large-format lithium batteries. They are UN-certified and have a repeatable fastening system that delivers a simple and cost-effective way of transporting large lithium batteries.
“As the leading provider of packaging products and services for the safe and compliant transport of dangerous goods, DGeo continues to expand its offering of UN-certified lithium battery packaging to meet the growing needs of shippers around the world,” says Glaser. “Partnering with Action Wood 360 to offer clippable and reusable wood crates as part of our Obexion line of protective packaging allows us to extend our wide range of lithium battery packaging solutions that help companies ship and handle large batteries simply, safely and efficiently.”
www.labelmaster.com/dgeo
SCHÜTZ
Schütz has begun production of tight-head plastics drums at its new facility in Dahej, India. The new plant is located in the Special Economic Zone in Gujarat and is the company’s first production site in the country.
Initial production includes Schütz’s standard F1 plastics drum, as well as a new model, F2, designed for the Indian market, which has an additional grip ring at the bottom to facilitate manual handling. Schütz is now planning to expand production to include its established MX series of IBCs, as well as a reconditioning line to handle packagings collected under the Schütz Ticket Service.
“Our customers in the region are benefiting in many ways from our investment, which in the first phase has a volume of over €30m,” the company says. “The local production of packaging solutions will significantly reduce transport distances and delivery times; previously we supplied Indian customers from Malaysia. It
will also reduce CO₂ emissions and further increase delivery reliability and flexibility. We are also pleased that the expansion of the sales organisation will further strengthen customer proximity and personal contact.”
www.schuetz.net
Thielmann has agreed the sale of its Ucon business unit to management. Going forward, Thielmann Ucon GmbH will act independently under the new name of Ucon Container System GmbH. Thielmann will continue to produce aseptic and industrial containers as well as pressure vessels; Ucon will focus on the container systems business and cubical containers.
“We wish the new owners of Thielmann Ucon all the best and hope that the team will be successful in their venture,” says Manfred Zurkirch, Thielmann CEO.
uconcs.com
www.thielmann.com
Greif has completed the acquisition of Ipackchem Group, which was announced late last year. Since its formation 35 years ago, Ipackchem has become a leader in the design and manufacture of innovative, highperformance rigid barrier packaging products, which offers an attractive addition to the Greif portfolio.
“Adding Ipackchem to the Greif portfolio is another key step forward in executing our Build to Last strategy and helps unlock significant new capabilities and market opportunities to further grow as a world leader in highperformance small plastic containers and jerrycans,” says Ole Rosgaard, president/CEO of Greif. “Our teams have been planning our integration strategy over the past several months, which we will begin implementing immediately post-closing to drive incremental benefits, support future growth, and capture our targeted $7m of synergies.”
www.greif.com
ILTA
MAY 6-8, HOUSTON
43rd annual operating conference and trade show of the International Liquid Terminals Association
https://ilta2024.ilta.org/
Argus Clean Ammonia Asia
MAY 7-9, TOKYO
Inaugural regional event to discuss opportunities in new fuels
www.argusmedia.com/en/conferences-eventslisting/clean-ammonia-asia
IOSC 2024
MAY 13-16, NEW ORLEANS
Triennial International Oil Spill Conference iosc.org
GPCA Plastics Conference
MAY 13-14, DUBAI
13th GPCA conference on the polymers sector and recycling https://gpca.org.ae/conferences/plastics/
Argus Green Marine Fuels Conference
MAY 14-16, AMSTERDAM
Forum to discuss the path to decarbonising marine fuels
www.argusmedia.com/en/conferences-eventslisting/green-marine-fuels
UNITI Expo
MAY 14-16, STUTTGART
European convention for the retail petroleum sector
www.uniti-expo.de
Bulk Tanker Day
MAY 15, BRISBANE
15th annual road tanker event hosted by the National Bulk Tanker Association www.nbta.com.au/Bulk-Tanker-Day
ChemUK 2024
MAY 15-16, BIRMINGHAM
Supply chain expo and conference for the UK chemical industry www.chemicalukexpo.com/
GPCA Supply Chain Conference
MAY 15-16, DUBAI
15th annual meeting of logistics professionals in the Gulf Petrochemicals and Chemicals Association https://gpca.org.ae/conferences/scc/
Hazmat 2024
MAY 22-23, STRATFORD-UPON-AVON
NCEC’s annual conference for those involved in hazmat response, incident management and crisis management www.ricardo.com/en/news-and-insights/eventsand-webinars/hazmat-2024
Intermodal Asia
MAY 22-24, SHANGHAI
Annual exhibition for the Asian intermodal sector www.intermodal-asia.com
ChemCon Asia
JUNE 3-7, BANGKOK https://chemcon.net/
Posidonia 2024
JUNE 3-7, ATHENS
Biennial exhibition and conference for the global shipping industry www.posidonia-events.com
SIL Barcelona
JUNE 5-7, BARCELONA
Annual international logistics expo and congress www.silbcn.com/en/index.html
IAFC Hazmat Conference
JUNE 5-9, BALTIMORE
Annual international event for response teams www.iafc.org/events/hazmat-conf
Argus Clean Ammonia North America
JUNE 10-12, HOUSTON
Regional event to discuss opportunities in new fuels
www.argusmedia.com/en/conferences-eventslisting/clean-ammonia-north-america
Achema
JUNE 10-14, FRANKFURT
Exhibition and conference for the specialty chemicals sector www.achema.de
Multimodal 2024
JUNE 11-13, BIRMINGHAM
16th annual exhibition for the supply chain management and logistics sectors www.multimodal.org.uk
CO2 Shipping & Terminals
JUNE 18, LONDON
Third one-day event to discuss the emerging CO2 supply chain www.rivieramm.com/events/co2-shipping-andterminals-2024
Chemspec Europe 2024
JUNE 19-20, DÜSSELDORF
International exhibition for fine and speciality chemicals www.chemspeceurope.com
Transport Logistic China
JUNE 25-27, SHANGHAI
Tenth international exhibition for logistics, telematics and transport www.transportlogistic-china.com
2 Packed Days
500+ Leading Exhibitors
Operations & Logistics
Tank Storage Solutions
Plant, Process & Asset Management
Chemicals & Materials Sourcing
100+ Speakers
24/3/24 Coconut Creek, road tanker motor oil Tank truck overturned on Florida Turnpike after collision involving several other vehicles; thousands of WSVN Florida, US gallons of motor oil leaked to road, causing it to be closed for cleanup; one person injured
28/3/24 Park City, road tanker crude oil Fire broke out on tank truck carrying crude oil on US 40; road was closed in both directions during response; TownLift Utah, US not clear what caused fire; responders managed to contain fire without environmental damage
29/3/24 Nebo, road tanker diesel B-double fuel tanker with 50,000 litres diesel exploded on Peak Downs Highway; eyewitness reports suggest Daily Qld, Australia brakes had locked, sparking fire; no damage to nearby farms, no injuries reported; fire allowed to burn out Mercury
30/3/24 Douglas county, road tanker diesel Tank truck crashed into guard rail on I-25 in single-vehicle accident, overturned several times into ditch; Denver Colorado, US driver injured; some 2,500 gal (9,500 litres) diesel cargo spilt; highway closed southbound for cleanup Post
31/3/24 Ganjam, road tanker LPG Gas tanker from Vizag to Khurda overturned when driver lost control; driver seriously hurt; LPG leaked from Times of Odisha, India damaged tank; police closed road; power supply was cut off during response India
2/4/24 Savar, road tanker fuel Fuel tanker overturned, caught fire on Dkaha-Aricha highway; fire spread to four other vehicles; one person MENA Bangladesh died of burns, eight more injured; road closed for several hours FN
6/4/24 Huntington county, road tanker ammonia Responders called to report of ammonia leak at Nutrien Ag Solutions plant found large cloud of anhydrous WANE Indiana, US ammonia coming from double ‘pony’ trailer; one worker died after being exposed to fumes
7/4/24 Haroli, road tanker diesel Road tanker overturned after brakes failed, catching fire and crushing other vehicles; fire spread to nearby NDTV HP, India shops; one person killed, eight others injured
8/4/24 Bhiwadi, road tanker chemicals Fire broke out during unloading of chemicals from road tanker at Yadav Petro Products turpentine factory; Times of Rajasthan, India driver bravely drove burning tanker away from the plant to prevent spread of fire; tanker was burned out India
9/4/24 Bracebridge, road tanker fuel Fire broke out in road tanker with 28,000 litres unspecified fuel on Highway 11; fire started in rear axle, CTV Ontario, Canada spread to trailer; road closed overnight; fire destroyed tanker, damaged road surface; no injuries
15/4/24 nr Durango, road tanker LNG Tank truck with 7,900 gal (30 m3) LNG ran off road, overturned on US 160; at least 80% of load leaked; Durango Colorado, US driver ticketed; road closed for more than eight hours; nearby homes evacuated Herald
16/4/24 Walker county, road tanker oil Tank truck with unidentified oil cargo crashed, overturned at Exit 46 of I-22; driver killed; large fire broke WMTV Alabama, US out, damaging road surface; ALDOT officials unable to determine load or which way tanker was heading
18/4/24 Columbus, truck lithium ion Part of downtown Columbus was evacuated after fire broke out in trailer with lithium batteries, prompting Fire Ohio, US batteries concern about potential for explosion; fire crews managed to bring fire under control in four hours Eng’ing
19/4/24 Orlando, truck muriatic Semi-trailer overturned on SR 417 north-east of Orlando International Airport, after driver over-corrected; click Florida, US acid driver and passenger hospitalised; 12 gal (45 litres) muriatic acid spilt to road; southbound lanes closed orlando
21/4/24 London, freight train creosote CPKCR train suffered fire in five wagons with old railway ties coated in creosote as it travelled towards CBC Ontario, Canada downtown London; crew brought train to a halt in residential area; fire did not reach tank cars with hazmat
22/4/24 Elizabeth, road tanker petroleum Tank truck with unspecified petroleum cargo crashed, caught fire on Routes 1 & 9; no serious injuries; NJ.com New Jersey, US news images showed tanker and SUV on fire; parts of highway closed for response
23/4/24 Pune, road tanker ethanol Road tanker with alcohol from Rajaram Bapu sugar factory overturned on Bengaluru-Mumbai expressway Hindustan Maharashtra, US near Khed Shivapur toll plaza; ethanol spread across road, causing road to be closed; two men injured Times
26/4/24 nr Suhum, road tanker fuel Road tanker with unspecified fuel load caught fire on Kumasi-Accra highway, reportedly due to mechanical Modern Eastern, Ghana fault; driver abandoned tanker; fire crews prevented explosion; no casualties reported Ghana
26/4/24 Eleme, road tanker gasoline Road tanker collided with heavy truck in roadworks on Akpajo-Onne Road; tanker spilled load, burst into Punch Rivers, Nigeria flames; fire spread to dozens of cars; five people confirmed dead, many more injured
26/4/24 Topagac, road tanker LPG Gas tanker collided with truck parked illegally in safety lane on Anatolian Highway; tanker overturned, Özgür Sakarya, Turkey leaked LPG; tanker driver was hurt; fire crews played water on tanker to prevent explosion Kocaeli
26/4/24 McKinley county, freight train propane 35 cars of BNSF train, six with propane, derailed near Arizona state line; residents within two miles ordered CNN New Mexico, US to evacuate; 50-mile stretch of I-40 closed; some propane tank cars caught fire, were allowed to burn off
27/4/24 Gölcük, road tanker gasoline Road tanker overturned in residential area, spilling gasoline; residents evacuated; spilt fuel and firewater DHA Kocaeli, Turkey were collected into IBCs for removal, disposal; cause of crash not clear
6/4/24 Gulf of Mexico Akal-B crude oil At least one worker killed, several others injured when fire broke out on Pemex’s Akal-B oil platform; Splash fire began in pipeline manifold area; most of those hurt were contractors
16/4/24 off Kuchinoshima I, Keoyoung chemicals Chemical tanker (3,970 dwt) from Kemen for Nagoya grounded on reef; hull damaged, causing bunker leak; Marine Japan Pioneer one source identified vessel as sister ship Keoyoung Star, carrying flammable chemicals Traffic
23/4/24 Iskenderun, Minerva unknown Chemical tanker (46,900 dwt, 2008), in cargo, grounded while departing Iskenderun Global terminal; ship Marine Hatay, Turkey Antonia was quickly refloated, moved to Dortyol anchorage; no pollution reported Traffic
1/4/24 Yekaterinaburg, military unknown Explosion, massive fire in Uralmashzavod plant, which manufactures equipment for military and industrial
Ural, Russia factory purposes; not clear how explosion happened; fire spread over 4,500 m2 area; no reports of casualties
3/4/24 Sangareddy, chemical chemicals
At least five people killed by explosion at chemical factory, reportedly in reactor vessel; surrounding area
Telengana, India factory evacuated in case second reactor also exploded; up to ten other workers said to be trapped in rubble
7/4/24 New Taipei City, plastics PP Fire broke out in upper floor of concrete building at Nan Ya Plastics plant, destroying some 300 tonnes
Taiwan factory polypropylene; shelter-in-place advisory over wide area; no injuries reported; cause under investigation
8/4/24 Dera Bassi, chemical solvents Fire broke out in spent solvent recovery unit at Maggo Chemical & Pharmaceutical plant; several explosions
Punjab, India factory reported, possibly due to drums over-pressurising; no casualties reported; police investigating incident
15/4/24 Ogden, chemical nitric acid 200-gal (750-litre) container of nitric acid was punctured at Rochester Midland Corp facility; site staff
New York, US plant brought spill under control until responders arrived; no injuries reported; cause under investigation
16/4/24 nr Edson, pipeline natural gas TC Energy’s Nova Gas transmission line ruptured 40 km north-east of Edson, causing wildfire; all personnel CBC Alberta, Canada evacuated safely; 4.5-km section of line was isolated, shut down; cause of rupture under investigation
Each month seems to bring more stories that illustrate the unknowability of today’s youth. Here’s the latest instalment: ten people, mostly students, were treated for ‘chemical eye exposure’ (presumably that means their eyes were exposed to chemicals, rather than them being exposed to ‘chemical eyes’). They had all been partying at Stages Nightclub on the downtown strip in Kingston, Ontario (do they have ‘downtown strips’ in Canada?) during a ‘foam party’. At these events, foam is sprayed onto the dance floor throughout the night and several feet of foam can accumulate.
Those affected said they had a burning sensation in their eyes; some needed antibiotics to get rid of the infection caused by the foam. One female student said her eyes started burning within an hour of arriving; CBC News rather obligingly avoided naming her, as she said she was concerned that “being associated with drinking in clubs could affect her career prospects”. Back in our day, drinking in clubs was one way to get a job offer.
Anyway, it may be news to us that events such as these go on but they apparently have been around for at least a decade – the American Optometric Association warned in 2013 that the foam could cause eye irritaion, following a report by the US Centers for Disease Control and Prevention about eye injuries sustained at a foam party in Naples, Florida.
Those in the know say that high-quality, hypoallergenic foam does not cause eye irritation, but that it costs more – about C$90 per hour to spray onto the floor – so some venues might be skimping. We just hope that, whatever foam they use, it is PFAS-free.
Speaking of youngsters, around 100,000 Chinook salmon smolts made their escape in March while they were being transported to be released into the Imnaha River in Oregon to boost local stocks and provide sport (once they were a bit older). They were being transported by tank truck (who knew?) when it overturned after skidding on a sharp bend. The Oregon Department of Fish and Wildlife reckoned that 77,000 of the smolts made it as far as the nearby Lookinglass Creek, by flapping across the road, which would lead them to the Grande Ronde River, which feeds into the Snake River and thence to freedom in the Pacific. One might well wonder how the Department managed to count them all – as it happens, some of them were fitted with transponder tags, which gave a good indication of how many perished.
Less fortunate were five poor souls who died last month in Ahmednagar in the Indian state of Maharashtra. According to press reports, a cat had got trapped in an abandoned well that was being used to generate biogas from animal waste. One local man jumped in to rescue the cat, but was overcome by the gases in the old well; another went in to rescue him, and so on. After five of his neighbours were lying unconscious at the bottom of the well, a sixth man went in with a rope tied around him – he too lost consciousness but was hauled out by police and taken to hospital.
There is no word as to the fate of the cat. One life down, eight to go, perhaps.
They say that imitation is the sincerest form of flattery, but we beg to differ.
Fort Vale is the market leader in the design and manufacture of manways, valves and ancillaries for tank containers. All of our equipment, from the largest manlid to the smallest valve seal, is rigorously tested for quality and efficiency. In fact, we manufacture the most extensive range of tank container equipment available in the industry for the diverse requirements of IMDG, ADR and RID.
We also go to enormous lengths to maintain the quality of our equipment - Fort Vale will always supply you with the safest, most durable and reliable OEM seals and gaskets - but we can’t guarantee parts from third-party suppliers.
So don’t let a short term saving cause you a long term problem - stay safe, and accept no substitutes. And join us at the head of the pack.