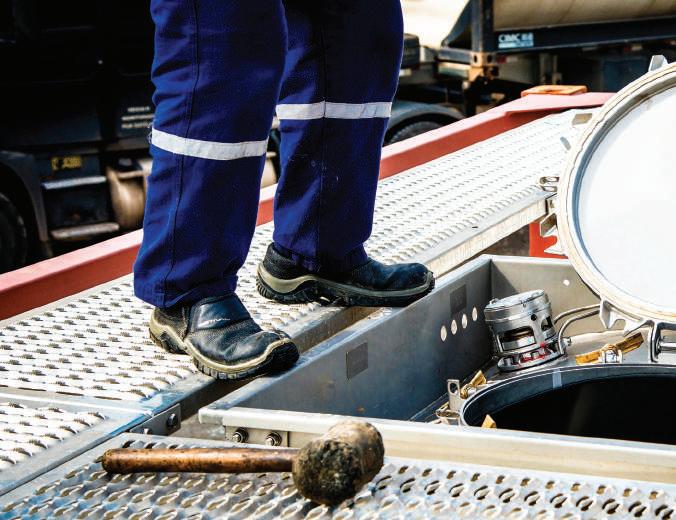
5 minute read
ITCO appeals for PFAS
SAVE OUR SEALS
PFAS • THE TANK CONTAINER INDUSTRY IS ALARMED AT THE PROSPECT OF HAVING TO ADAPT TO DIFFERENT SEALING MATERIALS AND IS CALLING ON REGULATORY AUTHORITIES TO RE-THINK THEIR STANCE
INDUSTRY IS WAKING up to the problems that might be caused should authorities in Europe and North America introduce a ban on products containing perfluoroalkyl and polyfluoroalkyl substances, collectively known as PFAS, due to their persistent effects on the environment and human health. PFAS are widely used in everyday items and, in some industrial applications, perform a critical function that will be very difficult to replicate. One of those applications is in sealing elements, which employ PFAS as they are effective over a wide temperature range and offer excellent chemical resistance. In tank containers, for instance, PFAS material can be found in seals and gaskets in the valves, outlets and manlids. The International Tank Container Organisation (ITCO) is taking the threat of the disappearance of PFAS materials seriously and has published a case study to press its claim that, in terms of sealing element materials, PFAS must be designated as ‘materials of essential use’.
CRUCIAL ROLE Tank containers are designed according to stringent regulations, not only those that govern the transport of dangerous goods (IMDG Code, ADR, 49 CFR, etc) but also ISO standards, the ASTM Pressure Vessel Code and, potentially, other national regulations. Those regulations specify that tanks must be able to contain their product over certain temperature and pressure ranges, so all the equipment fitted to tanks needs to be able to meet those limits. Seals and gaskets are, therefore, critical to meeting the regulations, which exist to ensure the safety of life and protection of the environment by mandating proper containment of the lading under the expected conditions of transport, as well as during an accident.
Metallic valves and other equipment use sealing elements, manufactured of substances such as polytetrafluoroethylene (PTFE), fluorinated ethylene propylene (FEP) or perfluoroalkoxy alkane (PFA), each of which falls under the heading of ‘PFAS’. Gaskets are usually manufactured from compressed non-asbestos fibre (CNAF) and fitted with a PTFE envelope to align with the sealing face. For manlids and other access hatch seals, a PTFE sheaf bonded to a nitrile core or braided polypropylene yarn impregnated with PTFE is used.
Tank containers must be designed to transport a wide range of chemicals, which requires the sealing elements to be compatible over the range. This is achieved by currently manufactured PFAS sealing materials. Similarly, valves are manufactured to meet the required temperature range of -40°C to +200°C (those for cryogenic gases must work down to -150°C) and the sealing elements must also perform over this range.
Sealing elements must also be durable and capable of withstanding a degree of handling damage. In addition, sealing materials should not absorb the substances being transported.
In today’s industry, sealing materials that are manufactured from or include PFAS achieve all of these demands and have been shown to be safe and effective. Moreover, ITCO points out that the materials used are in solid milled and cut form, which does not shred and degrade into particles that could detrimentally affect the environment. The total volume of valves and gaskets used by the tank container sector over the course of a year is estimated at some 230 tonnes.
WHAT’S THE ALTERNATIVE? There are no alternative materials that provide the crucial performance range achieved by existing specified solid state PFAS sealing elements, ITCO stresses. Some of the non-PFAS alternatives that have been researched could be economically beneficial except that the operational cost resulting from risk of leakage from an inferior material would by far exceed any saving. Furthermore, alternative materials are technically unsuitable in many required applications and therefore are not feasible alternatives.
For instance, ultra-high molecular weight polyethylene (UHMW-PE) has been investigated, as it has good resistance to wear and impact, is highly resistant to corrosive chemicals and is relatively low-cost. However, its temperature range is limited, with a maximum of 135°C, and its chemical resistance falls at high temperatures. It cannot therefore be seen as a direct replacement for existing sealing materials; furthermore, as with all alternative materials, it would have to undergo extensive type testing and field testing before use.
PVC has too narrow a temperature range to be considered and is itself regarded as a substance of very high concern, so can be discounted. Polypropylene has a slightly wider temperature range but still not sufficient to meet the needs of the tank container sector. Some silicone grades have a temperature range of -55°C to +300°C and can be used within sealing elements in certain applications but are not resistant to many of the chemicals transported, including most solvents and hydrochloric and hydrofluoric acids. The lack of hardness also restricts the use of these material for some sealing elements. Elastomeric compounds such as silicone, nitrile and neoprene, can also be regarded as bio-accumulative and toxic to the environment.
In addition to these issues, the use of any alternatives to current sealing materials would inevitably reduce effectiveness, opening up the environment and personnel to contamination with potentially hazardous substances; further, they would need to be replaced more frequently, again potentially exposing workers to additional risks.
Ultimately, a restriction on the use of PFAS in sealing materials will result in a higher level of risk than currently prevails and ITCO calls on regulatory bodies to ensure that PFAS may continue to be used. www.itco.org
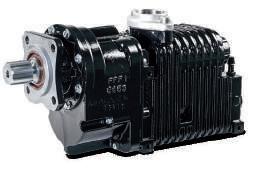
The Mouvex® B200 Flow Control oil-free screw compressor delivers high flow rates in a rugged design that’s lighter than competitive models. The “plug-and-play” installation requires no drive shaft, as well as no mounting bracket and is fully coated for corrosion resistance. The B200 delivers all of this with a 3 year warranty.
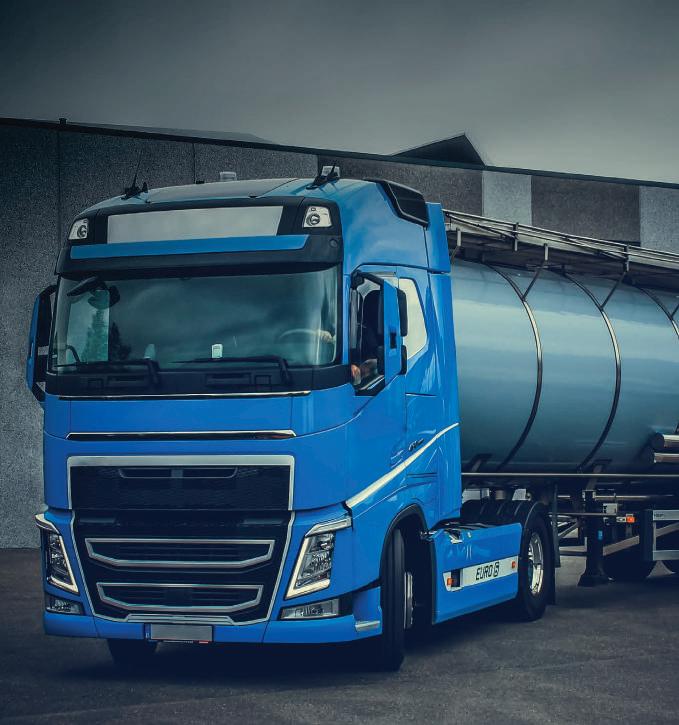
See how much faster you can unload:
mouvex.com/B200
ZI la Plaine des Isles, 2 rue des Caillottes F-89000 Auxerre, France +33 (0) 3 86 49 86 30
mouvex.com | contact.mouvex@psgdover.com