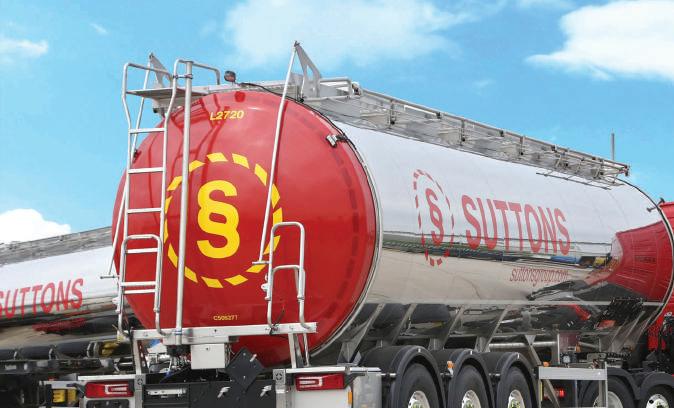
3 minute read
How Suttons has managed
COPING IN A CRISIS
STRATEGY • SUTTONS INTERNATIONAL REPORTS HOW IT HAS FACED UP TO THE RECENT TURBULENCE IN GLOBAL SUPPLY CHAINS, WITH THE FOCUS VERY MUCH ON ITS PEOPLE
THE COVID-19 PANDEMIC , extreme climate events, Brexit and many other unusual events have resulted in unprecedented issues for logistics providers, adding complexity to what they do and impacting the very basis of their business: moving chemicals in bulk from A to B.
Drivers are a crucial element of the chemical logistics supply chain. They are highly trained and use a specialised skillset to safely complete the first and last steps of any delivery at customer plants either loading or discharging tanks. But the Covid pandemic had a major impact on driver availability – an issue that has been building across the entire haulage community for many years but has now been brought to a head.
A reduction in capacity across all sectors of the driver population has occurred due to driving no longer being seen a job of choice within the workforce. This has been compounded by the impact of Covid, which saw many existing drivers move out of the chemical industry and into consumer-facing driving roles such as home delivery.
Recruiting new drivers into the industry has been a challenge. Increasing driver wages is the most obvious first step that most hauliers took. Suttons went above and beyond that by improving working conditions for its drivers, investing in the fleet by adding the latest models of Volvo FH trucks, which provide greater comfort, and introducing in-cab technology to streamline drivers’ jobs and letting them focus on what they want to do: drive.
PRESSURE OFF Another major issue the European logistics industry is currently facing is the new customs requirements that were introduced following Brexit. This has led to additional transit times across the industry adding three or four days to the movement of goods between the UK and EU. New measures and protocols also require more time and effort from operators and planners to address.
Additional transit times have caused capacity issues in terminals, which are rapidly filling up due to the longer clearing time for tanks and containers. This has naturally led to a backlog of tank availability across the entire supply chain.
Suttons introduced a number of new processes and ways of working, including the recruitment of an entirely new customs team, to support its operations. It has established EDI links with customers and customs partners in Europe to ensure product and customs requirement information is accessible instantaneously for all members of the supply chain. This automates certain customs processes and reduces the manhours the team spend on this task.
Suttons has also been pro-active in sourcing additional storage capacity outside of busy terminals and port areas to address the extended transit times. Finally, it has been offering customers, who are experiencing plant shutdowns as a result of the delays at ports and terminals, alternative storage solutions, to help offset disruption to their operation.
“While there was no easy solution to the increased hurdles that Brexit introduced, by pro-actively introducing a new team of customs agents into the business, sourcing additional storage spaces in the event of backlogs at ports, and offering our customers access to our tanks in the event of emergency plant shutdowns, we have mitigated the brunt of the problems caused by Brexit, and have adapted to the new normal,” the company states. “The key to overcoming factors outside our control, and to continuously provide great customer service, is adaptability and communication. Not only with our customers, but internally, with colleagues and drivers, and externally with our partners and suppliers in the supply chain.” www.suttonsgroup.com
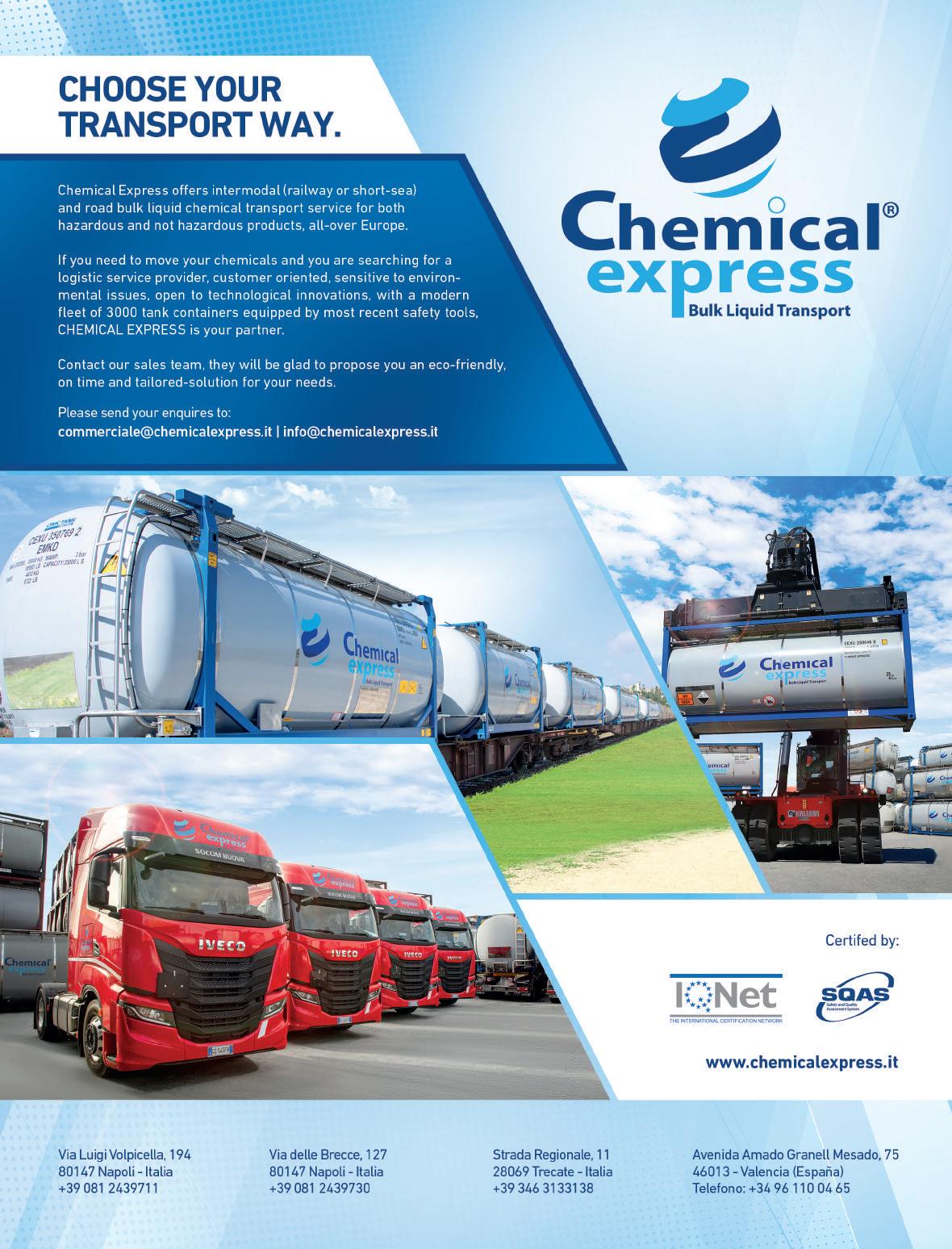