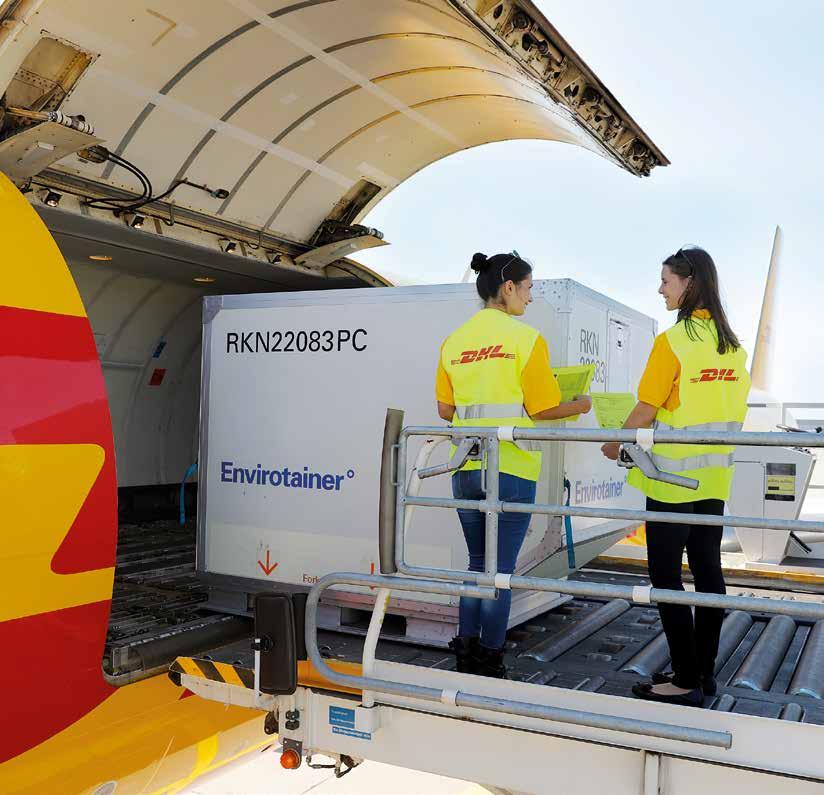
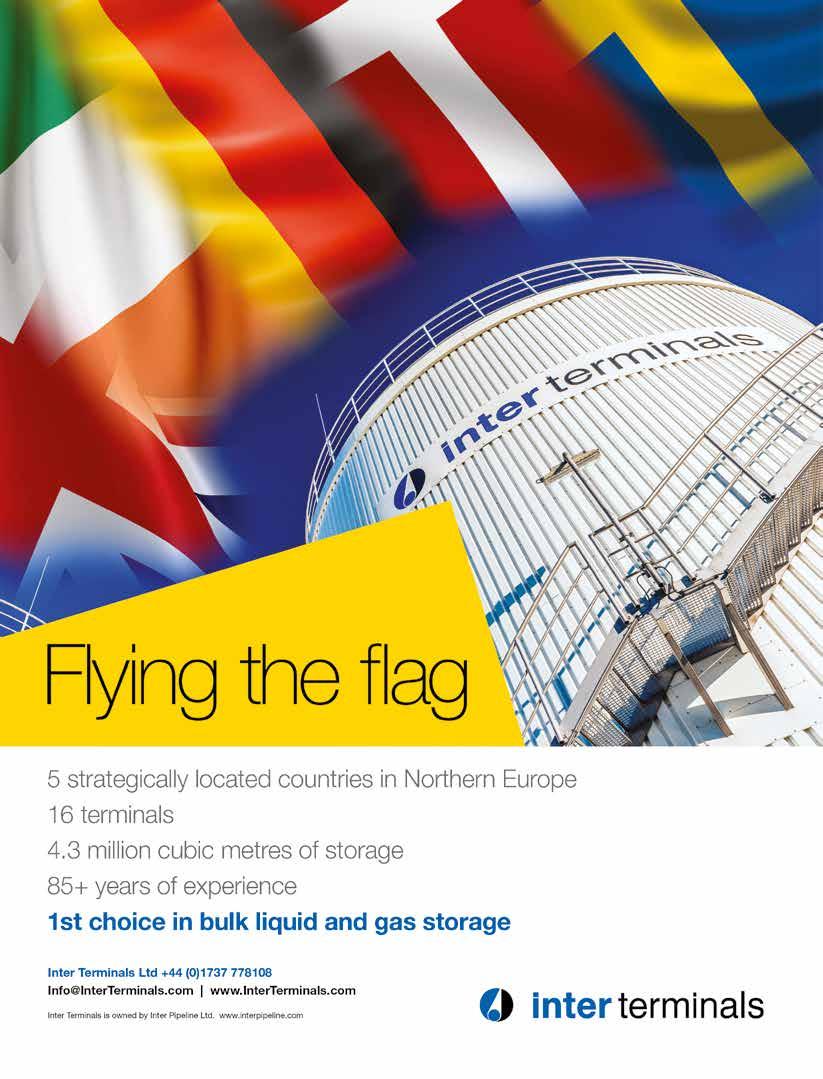
When Hazardous Cargo Bulletin was first published, way back in 1980, one of the first things we had to do was to define just what we meant by ‘hazardous cargo’. It seems fairly obvious: these are goods that, during transport, present a hazard. We could stretch it a little, as most of those goods are also hazardous during handling and storage.
The simplest way to define the universe of ‘hazardous cargo’ is to look at the goods (substances, articles, mixtures, etc) defined by the UN as ‘dangerous’. Those initially presented one or more of the three main hazards: flammability, toxicity and corrosivity, or the other two biggies, explosives and radioactives. You could add to that list those that are not explosive themselves but can explode or catch fire – such as gases under pressure, certain substances that develop hazardous properties when in contact with water, organic peroxides, and so on. In the 60 years since it was first formulated, the UN Dangerous Goods List has multiplied; ‘miscellaneous’ hazards cover a wide range of products, not least lithium batteries and those goods that present a hazard to the aquatic or wider environment.
Then there are those goods that present hazards in the workplace or in the home – ‘supply and use’, to use the official lingo. Since the arrival of GHS and its globally harmonised (stop tittering) approach to the classification of hazards in these applications, supply and use considerations have become more significant, especially for those with responsibilities in terms of hazard communication.
In this issue we take our remit a step further and take a look at the pharmaceutical supply chain. Some pharmaceutical products and their active ingredients do certainly present a hazard (usually toxicity, occasionally radioactivity) that can, in
certain transport scenarios, see them regulated as dangerous goods. More generally, though, they demand a similar level of care to high-hazard chemicals, particularly in area such as temperature control, security and traceability.
As a result, the pharmaceutical supply chain mirrors the speciality chemicals supply chain, with the involvement of very similar players. We have, for instance, noted in recent years a trend towards the design of warehouses that have separate temperature-controlled zones, some dedicated to temperaturesensitive chemicals and some to pharmaceuticals. Many of the larger transport companies that undertake the distribution of packaged chemicals do a similar job in the pharma sector.
More interestingly for our regular readership, perhaps, the distribution of pharmaceuticals sits at the leading edge of emerging trends. Pharmaceuticals tend to be comparatively high-value products and their supply chain can be time- as well as temperature-sensitive. As such, not only consignors but also their logistics partners are keen to adopt new technologies and services that can enhance the reliability of the supply chain and maintain the quality of the goods being moved.
Pharmaceutical shippers make special use of the air mode and readers from other sectors may well be interested to consider how they could leverage new ideas for temperature control during air transport and for dedicated handling on the ground.
Increasing use of battery technologies in all manner of articles, together with the ever-expanding Dangerous Goods List, may one day mean that HCB can justifiably cover every item in the world. For now, though, we are content with this limited expansion of our scope.
Peter MackayCargo Media Ltd
Marlborough House 298 Regents Park Road, London N3 2SZ www.hcblive.com
Peter Mackay
Email: peter.mackay@hcblive.com
Tel: +44 (0) 7769 685 085
Stephen Mitchell
Email: stephen.mitchell@hcblive.com
Tel: +44 (0) 20 8371 4045
Brian Dixon
Designer Natalie Clay Commercial Managing Director
Samuel Ford
Email: samuel.ford@hcblive.com Tel: +44 (0)20 8371 4035
Commercial Manager
Ben Newall
Email: ben.newall@hcblive.com Tel: +44 (0) 208 371 4036
Production Coordinator
Sam Hearne
Email: sam.hearne@hcblive.com Tel: +44 (0) 208 371 4041
HCB Monthly is published by Cargo Media Ltd. While the information and articles in HCB are published in good faith and every effort is made to check accuracy, readers should verify facts and statements directly with official sources before acting upon them, as the publisher can accept no responsibility in this respect.
Letter from the Editor 01
Learning by Training 04
30 Years Ago 05
View from the Porch Swing 06
The third party
Keeping tabs on medicines 08
In-flight service
Latest ideas on temperature control 10
Flying down to Rio World Courier connects South America 14
Standard setter
Bolloré pursues IATA CEIV Pharma 15
Know your onions
Latest data logger from Onset 16
Liner trades
Latest cold chain trucks from Krone 18
The heritage factor
Brenntag expands worldwide 20
Turnaround time
Univar reports recovery 22
News bulletin – chemical distribution 24
A family affair
Huktra acquired by H Essers 26
Swift and secure
Emergency shutdown by Wiegel 28
Platform alteration
Imperial standardises systems 30
Turbocharged results
XPO enjoys boom year 32
Pick the bud
BDP expands in Africa 34
News bulletin – tanks and logistics 36
Irrational behaviour
Still building chemical tankers 38
Major chemical tanker fleets 40
The transfer window opens Team kick-starts consolidation 44
Riverboat shuffle
Kirby acquires Higman fleet 46
Cover the Waterfront
More interest in methanol-fuelled ships 47 News bulletin – chemical tankers 48
Training courses 50 Conference diary 53
Incident Log 54
Open the box
Sharing container inspection results 56
Excuse your dust Newson Gale on dust hazard management 58 News bulletin – safety 60
The long march begins Moving China’s chemical industry 61 Don’t get side-tracked
Working towards RID 2019 62
Get it right and win
Labelmaster promotes the DG professional 68 Change brings challenge
Looking forward to COSTHA meeting 70
Not otherwise specified 72
Annual LPG tanker fleet survey
What’s new in telematics
New ideas in trailers
Latest from the UN regulators
Last month the StocExpo Conference and Exhibition took place in Rotterdam, Holland. An impressive number of internationally operating companies, organisations and people related to the bulk liquids storage industry attended this important yearly event. What I wrote two years ago on the future of bulk liquid storage business, I‘d like to share with you today.
I developed a method to research future trends, predictions on longevity or continuity of industrial sectors and wrote and presented these trends as I do believe we have arrived at a tipping point. Bulk liquids storage is a part of - and dependent on - a hydrocarbon-based economy consuming non-renewable fossil fuels. When I am asking the question; does this industry harm the environment, social cohesion or human and non-human life, I cannot say “no”. Sure, the products we all use made from these fuels and chemicals improve our luxurious lifestyles, but are they sustainable? You can answer this rhetorical question yourself.
When we cooperate and endeavour to phase out products and industries that are harmful or as we called them ‘negatively interdependent’ (benefiting some at the cost of others) and replace them with non-harmful ones, we can create a sustainable range of products that are so-called ‘positively interdependent’ (they benefit everyone). I can therefore see a future energy storage industry storing harvested solar, wind, water, hydrogen or geothermal energy, but also, perhaps even more importantly, to store, ship and distribute (via tank farms and pipeline networks) drinking water.
Investment in guaranteed drinking water supply chains will benefit the continuity of daily, global business. Drinking water should not be made into a commodity, because the value of availability of drinking water for every one on this planet would reduce revolts, risks or conflict. Prevention of such costs would pay amply for needed investments. According to the World Health Organisation (WHO), the yield in drinking water supply investments would be between 10 and 3,000 per cent! I foresee a function for existing oil or chemical storage companies to also become drinking water storage and supply terminals with dedicated pipelines, pumps, jetties and storage tanks for water.
Such an initiative will not be coming from governments but can be organised by the industry itself. When one acts as a systems thinker, all you have to do is use ‘ALL’ information to build a resilient storage industry which is able to stand the test of time. Perhaps we should change the current definition of sustainability into ‘standing the test of time’.
What we now can observe, not only in the storage industry, but in all industries, political and economic linear systems, is that they often overlook the need of future generations. This modus operandi won’t stand the test of time. We would have phase out our harmful business models and adjust them into new, non-harmful, sustainable ways. The awareness, knowledge and skills are here. Let’s use them in cooperation and let’s share the profits equally.
This is the latest in a series of articles by Arend van Campen, founder of TankTerminalTraining. More information on the company’s activities can be found at www.tankterminaltraining.com. Those interested in responding personally can contact him directly at arendvc@tankterminaltraining.com.
By the standards of the day, the April 1988 issue of HCB was a bumper event, weighing in at 106 pages and featuring plenty of full-colour advertisements. As is still the case, much of the coverage was designed to tempt interested new readers picking up a copy at one or other of the various trade shows and conferences lined up for the second quarter, but the size of the issue also had a lot to do with the sheer amount of regulatory and industry news there was to report.
Some months earlier we had waded inadvertently into issues surrounding the regulation of the transport of dangerous goods by air and in the April issue Andy Altemos felt compelled to write from the US to confirm that the Federal Aviation Administration would not – and as far as he was concerned never would - consider the IATA Dangerous Goods Regulations to have any legal basis.
There was a lot of coverage of tank containers in the April 1988 issue, with a strong focus on the growing penetration of this relatively new mode of transport in the North American market. But the market was about to be confused by the US Department of Transportation’s (DOT) plans to harmonise more closely with the UN Orange Book – albeit partly on the basis of “if you do what I do then we’ll be harmonised”.
In particular, European tank container operators were somewhat alarmed at the amendments to the UN provisions that the US was considering in order to help it achieve harmonisation. One of those, for instance, was that Class 2 should be sub-divided so as to recognise the very different hazards posed by flammable, non-flammable and toxic gases, respectively. That seems quite sensible today (as, indeed, do several other changes) but it was somewhat alarming for tank
container operators, who felt that the legal basis upon which they had planned their tank investments was about to be shifted.
The US view was that its own specifications for ‘bulk packagings’ – tank cars, cargo tank motor vehicles and tank containers – had evolved in a haphazard fashion and that it was probably about time that they were straightened out. The International Maritime Dangerous Goods (IMDG) Code had also developed its own approach to the specification and stowage/segregation of tank containers, and it would take many more years before the various systems could be fully aligned.
Another element of DOT’s harmonisation project was to be the new ‘performance-oriented packaging’ standards, or POPs, which are to a large extent still with US industry today. Thirty years ago we had an article on the new UK quality assurance standard BS 5750 (‘BS’ referring to ‘British Standard’ rather than to a term more widely used in the US). This standard was designed in part to ensure regular testing of “a company’s ability to consistently manufacture products to a defined specification”.
Such consistency is a fundamental assumption of the process, still in place today, of design approval of packagings (as well as larger containers) for dangerous goods. BS 5750 required (and still does) that a manufacturer’s management and quality assurance procedures be kept up to date and be followed and that such procedures should be audited.
In a way, BS 5750 was the forerunner of today’s ever-expanding list of safety, quality, environmental protection and process safety management standards.
Once upon a time, for a couple years, I was a single dad. It was exhilarating work most of the time. I really like my kids. They were (and are) interesting people, starting from when they were very young. Even chores weren’t so bad. We chatted about pre-school, my work, or third grade while I prepared dinner. They read to me while I folded clothes. We grocery shopped together, creating menus on the fly. And of course, fun time was fun.
But every once in a while, I needed a little help. Sometimes, I could do adult-only work after their bedtime, like paying bills. But getting a bad cold or the flu was inconvenient at best, and bringing home a project from work sometimes required my full concentration before their bedtime.
Television and recorded children’s movies were my salvation. I could plop my children down in front of the electronic entertainment for a couple minutes and, voila, they’d be hooked on the Power Rangers or The Lion King for as long as I napped or worked.
It was easy and magical. So easy, in fact, that sometimes it required a thoughtful, concerted effort to avoid overusing it. I wanted to be the one to raise my children, not to have
Disney do it for me. TV and VCR needed to be my tools, not a substitute for me.
Electronic tools are quite helpful to me at work these days, too. At some point, I’ll transcribe these words from ink on paper into my laptop, wave my magic wand, er, um, uh…, hit the magic SEND button, and this column will instantaneously appear a quarter of the way around the world. Pretty cool, and quite helpful.
Pretty pictures on PowerPoint and projectors assist me in getting points across during training courses. During those courses, less and less time is spent on documentation because electronic tools, such as software packages, sequence, format, send, and print bills, manifests and declarations. Classifications are stored in electronic memories somewhere, instead of in binders and paper mSDSs. My smarter-than-i-am phone even has an app with comprehensive emergency response information, which I suppose makes my phone WISER-than-i-am, too.
In warehouses, Artificial Intelligence (AI) allows unmanned lift trucks (forklifts) and robotic arms to retrieve stuff from shelves and put it onto conveyance systems, which then package the stuff up and mark it without
human intervention. We have some incredible tools to help with compliance.
Do I think someday AI, robots, software, conveyors, and automated assembly lines will do it all for us, all of the DG functions, without a human being for miles around?
Someday? Some day? Heck, that day was supposed to have been in our past already. About a decade ago, I interviewed for a job where the expectation was that I’d lead them into a human-less DG warehouse. I gave them a list of reasons why it couldn’t be done yet, but that I could get them 80–90% of the way there. They didn’t want to hire anyone who ‘accepted failure as his starting point’ and I didn’t want to take a job that would measure my performance against an unachievable standard. So we mutually parted. But, I keep thinking about those objections, and as DG software gets more sophisticated, wondering about how close we could be to a human-less DG warehouse.
• There are two major problems with transport classifications. Some Section 14s are flat out wrong. And some classifications, mainly 9 and 6.1 (although technically 2.3 also) include subjective criteria. Each re-shipper of a DG/HazMat is independently responsible for arriving at a compliant transport classification, even if the manufacturer or upstream distributor got it wrong.
CAN’T: How do we expect a computer to determine a subjective transport classification? How do we expect a computer to fix incoming classification errors?
CAN: Use OCR (Optical Character Recognition) to scan SDSs and use the same algorithms that a human classifier uses. Just as one example: methemoglobinemia (chocolate blood) and cyanosis (blue lips) are sufficient warnings for many classifiers to subjectively put a material into 6.1, and a computer could use the same reasoning.
• I have a photo of a specialty organic solid in three different bottles, two round glass and one square plastic, yet all are the same product in the same grade in the same quantity with the same SKU number. One of the round glass bottles is fuller than the other.
CAN’T: How does one choose just one UNspecification box-based packaging system if the inner container is sometimes short and sometimes tall, sometimes glass and sometimes plastic, sometimes round and sometimes square? A human being has to look at each particular inner, and choose from among several different, potentially appropriate packaging systems.
CAN: With some sort of optical scanning (maybe laser?) visualization and measuring system, a computer could examine the inner packagings, and be programmed to choose packaging systems appropriately. And even easier, how about a loose fillbased V-box system?
• Some products can occasionally have more than one accurate, specific, and compliant transport classification. One example includes products that can legally be offered for shipment by air as ID8000, Consumer Commodity, or as fully regulated. Another example includes materials that don’t have to be Environmentally Hazardous Substances (EHS) in the USA but are allowed to be treated as EHS if a shipper wants to.
CAN’T: In addition to the intrinsic properties of the products and the potential uses of the products, a person needs to consider how much is being shipped, by which mode, and to where, before the most efficient/effective classification can be chosen.
CAN: Of course, a computer system could always default to the most restrictive (fully regulated), but this isn’t always the most cost-effective. So why not program the computer/AI with the same algorithm for decision making that a human uses in the same situation?
• Some products come pre-packaged and pending an inspection for damage can be re-shipped in that same packaging.
CAN’T: A human being needs to look over the package for dents, tears, stains, damage, deterioration, signs of leakage, and so forth.
CAN: Rather than the cost-ineffective approach of re-packing everything, cameras and lasers can do the inspections, comparing dimensions (such as dents in drums or crushed corners on boxes) with pre-programmed standards of acceptability.
While they’re at it, the color-detecting imaging tools could verify the compliance of the marks and labels, too.
• Many packages suitable for surface transport are non-compliant for air transport. How is one to know whether the inner packagings are air compliant?
CAN’T: Heck, people still screw this one up all the time. But, often, a phone call to the original manufacturer can answer questions about use of cushioning, presence or absence of absorbent, and inner containers of liquids meeting the pressure test or not.
is to have marks and labels either applied or removed at the destination seaport, depending upon which direction the product is moving.
CAN: Create a standing arrangement with various destination seaports to ‘fix’ the types of incoming shipments that cause problems, and then for each new problem order have the warehouses’ automated systems send to the affected seaport a pre-written email template with the shipment details filled in.
• Drone deliveries?
CAN: Re-pack all air shipments of liquids (not necessarily solids), or forbid all liquids from air transport, and/or flag these upon receipt to have a peon human in some remote location make the phone call to the original manufacturer before any air orders are accepted. The results of the phone call would be stored in an accessible DG database.
• Some products are compliant in one classification in one country, but noncompliant when they arrive at another country, with no one classification suitable in both countries. Some examples include Combustible Liquids to and from the US, and other examples include materials that react with water to release toxic gas but have no other regulated hazards.
CAN’T: People screw this one up all the time, too. But the most common fix for IBCs or portable tanks of Combustible Liquids
I can’t believe you went there. Don’t go there. At least not now. Maybe in some future column. Many of the reasons why we CAN’T have human-free shipping operations are capable of being turned into reasons we CAN, if only we have the right e-tools. And though we already have some problems that people have difficulty handling, such as multiple classifications and different packaging requirements for air, we’ll either get those ironed out (hopefully sooner rather than later, especially 4.3 ≠ 4.3 worldwide), or we’ll just apply the same pattern of thinking (decision trees) that a person would use, to the new electronic tools. And I’m sure we’ll continue to develop new e-tools for DG, but they’ll be phased in as costs allow, just as the cost of using e-babysitting tools is factored into how frequently and how often they are used. It’s easier to measure the costs of DG e-tools though, as they are primarily monetary. For child-rearing, the costs of using those e-tools may not be apparent until long after they’ve been over-used. Eventually, prices will drop and I most certainly can envision a time when almost all of the DG shipping functions will be performed by robots and other e-tools. How fast that happens, I’m not sure, but it is happening.
That’s way different than e-tools to occupy children, though, because as a grandparent I’m as opposed to their overuse as I was when I was a mere parent.
This is the latest in a series of musings from the porch swing of Gene Sanders, principal of Tampa-based WE Train Consulting; telephone: (+1 813) 855 3855; email gene@wetrainconsulting.com.
“I CAN ENVISION A TIME WHEN ALMOST ALL DG SHIPPING FUNCTIONS WILL BE PERFORMED BY ROBOTS”
JUST AFTER THE end of World War II an American pulp western writer, Holly Martins, was called to war-ravaged Vienna by his old pal Harry Lime, with offers of a job. Arriving in the city, Martins discovered that Lime had been killed in a road accident and that his body had just been taken for burial.
Those who know Carol Reed’s 1949 movie The Third Man, scripted by Graham Greene, will know what happens next (spoiler alert for those who don’t): it emerges that Lime has been involved in a racket, obtaining penicillin – in short supply outside of military hospitals – and selling it on in diluted (and therefore useless) form.
The film is well worth seeing today, not least for its cinematography, and its theme is also still relevant. While racketeering in medicines was a likely feature of a divided and rubble-strewn city at the start of the Cold War, it remains a problem. Indeed, according to pharmaceutical logistics specialist H Essers, counterfeit medicines are an increasing issue around the world.
In order to prevent fake pharmaceuticals getting on to their domestic markets, more than 55 countries are now developing or implementing requirements for ‘serialisation’, which involves the assignment of unique identifying numbers of individual packages.
In the EU, for instance, serialisation will have to be implemented by 9 February 2019 – less than a year away. The US has a phased programme taking place between 2015 and 2023.
Given the complexity of the rules and procedures, compliance with serialisation requirements is likely to be a challenging process for pharmaceutical manufacturers. H Essers recommends involving logistics service providers at an early stage of the implementation effort; indeed, in some cases it may be possible to hand off the entire process to a specialised logistics provider, which can also handle the communication with the EU data hub.
“Working with a logistics service provider as a serialisation partner will help to not only alleviate some of the complexity of the task at hand, but also transform serialisation from a costly ‘cash out’ process into a tool generating added value and effectiveness in the supply chain,” says H Essers. Many third-party logistics providers (3PLs) will have similar experience in the tobacco and food sectors and already have in place information management systems that can be adapted to the pharmaceuticals supply chain. A similar approach is also being taken in the movement of explosives and precursors.
It has been estimated that the EU Falsified Medicines Directive (2011/62/EU) will cost the pharmaceuticals industry up to €5bn in terms of the implementation of serialisation and the use of anti-tampering systems.
Industry estimates that prices to the consumer will rise by between 30 and 60 per cent.
And those figures relate only to intra-EU operations. Manufacturers supplying other markets will face the complexity of dealing with different measures being applied by other countries, with different deadlines.
According to H Essers, the industry in Europe has been slow to respond. Some have pointed out that the measures are unnecessary, since counterfeit medicines hardly ever find their way into the legal supply chain. The problem lies with online
sales from outside the region, an issue that is not tackled by the Directive. Furthermore, developing a compliance programme involves cross-functional collaboration, which is an additional hurdle in rapid response.
“Manufacturers tend to look at serialisation from a production point of view,” H Essers says. “This seems a logical reaction since serialisation will have an impact on the production and packaging processes. But they neglect the fact that it will also impact the logistics processes. Serialised products will add a new level of complexity to warehouse and inventory management. This is why manufacturers should also determine the serialisation-readiness of their 3PLs.”
Involving logistics partners early in the process also opens up new opportunities. The pharmaceutical industry fears that serialisation will be a cost burden with no added value. Experience in the other sectors shows the opposite. Serialisation can generate benefits on many levels in the supply chain, since the unique identifier allows for better traceability.
In most of the cases, 3PLs should be involved to smoothe and improve the supply chain downstream, i.e. after production and packaging. Many 3PLs have experience in packaging and labelling but involving them in the off-site packaging of big batches is not advised. Outsourcing the packaging of the main production lines is in most cases counterproductive, as there is an additional transport cost. It increases the risks and implies higher insurance costs.
Ideally, packaging and tamper-proofing should occur during the production process. Nevertheless, there are other cases in which outsourcing to a 3PL can prove highly valuable. As the deadline of February 2019 approaches, many manufacturers will concentrate their efforts on their main products in order to
be ready on time and to prevent inventory interruptions. In the industry, many fear that less current medicines will have to be withdrawn temporarily or definitively from production because the serialisation deadline cannot be met.
Logistics service providers specialised in the pharmaceutical supply chain can provide a solution to prevent this. Some 3PLs are already serialisation-compliant. They can take over the serialisation, packaging and tamperproofing for smaller batches, exceptions handling and rush orders. Being compliant, they are authorised to communicate with the data hub, alleviating the pressure on manufacturers. They can order serial numbers, communicate those that have been used, generate the 2D-matrixes, and so on.
Manufacturers do, though, need to verify that their 3PL partners are properly certificated. Computer systems must be GXP approved and they have to comply with Good Manufacturing Practices (GMP). This is essential if they are to perform certain activities, such as repacking or printing matrix codes on the packagings.
While engaging a 3PL to help meet the 2019 deadline will be a boon in the short term, H Essers believes that such an approach will offer bigger benefits further along. The use of unique identification numbers, for instance, will allow supply chains to become more transparent, enabling better quality control and risk management. If an incident occurs, such as a temperature deviation, the consequences can be limited. When the cold chain is monitored from start to end, the place and time of the deviation are determined with accuracy.
In the longer term, manufacturers will be able to involve their 3PL in more fields impacted by serialisation, for instance in late product differentiation or even ‘make to order’ products. In the future, it will even be possible to add further data to the unique serial number, accelerating the possibility of introducing blockchain technology.
Putting this all together, H Essers says, will transform the costs of compliance into added value for pharmaceutical manufacturers and their partners.
CHALLENGES FOR
TAKING THE SUPPLY CHAIN OVERALL, COULD WELL DELIVER BENEFITS FOR THE INDUSTRY AND ITS DOWNSTREAM PARTNERS
TP3 Global’s approach is to create a multilayered blanket that maintains freight within predefined temperature limits for extended periods during breaks in the supply chain. It is also water-resistant and can provide protection against theft.
THE PHARMACEUTICAL SUPPLY chain makes wide use of airfreight to get goods to end markets as quickly as possible. But it also places great demands on the supply chain to ensure that those goods get to the market in good condition. Not only are the goods involved often high-value consignments, they also often require temperature control during transport.
As such, a widespread industry has developed, offering an increasing array of solutions for cold chain shippers such as pharmaceutical manufacturers and their logistics service providers (LSPs). Those solutions display some very different approaches to temperature control, while
solutions providers have also been busy of late signing agreements with some major cargo airlines.
“Breaks in the cold chain are a serious issue for the pharmaceutical supply chain, with valuable stock often sitting on the tarmac for hours at a time,” says Peter Lockett, director at TP3 Global, which manufactures the globally recognised SilverSkin™ thermal protection blanket.
To address this critical problem, TP3 Global has introduced SilverQuilt™, a higherperforming, multimodal thermal protection that achieves superior temperature protection for valuable, sensitive cargo such as controlled room temperature (15°C to 25°C) pharmaceuticals. “With the introduction of SilverQuilt, pharma manufacturers can take a balanced approach, matching cost-effective protection with well managed supply chains,” Lockett says.
“Our existing products, such as SilverSkin, have achieved a solid reputation in the market, being tested, approved and now used by many of the world’s leading pharmaceutical manufacturers,” adds Lockett. “SilverQuilt is the next logical step to support customers looking to protect controlled room temperature (CRT) freight with a high-performance cover solution with tighter control limits. The higher performance enables customers to consider the combination of controlled lanes and thermal covers for +2oC to +8oC shipments, which was not possible with lower performance thermal covers.”
Before its official launch, SilverQuilt underwent an extensive R&D process at TP3 Global’s technical centre in Redditch, UK. The material passed multiple assessments, including hot and cold environmental chamber testing, virtual cold chain simulation and thermal resistance (R-value) testing.
“The launch of SilverQuilt arrives at an exciting time for our business, as we continue global expansion and further establish
AIRFREIGHT • TEMPERATURE CONTROL DURING AIR TRANSPORT IS CRUCIAL IN THE PHARMA SUPPLY CHAIN. NEW SOLUTIONS ARE HELPING ENSURE GOODS ARE DELIVERED IN PRIME CONDITION
ourselves as one of the leading providers of thermal protection solutions,” Lockett says. “The additional launch of the TP3 Global Technical Centre this year has increased our capacity to test materials beyond the identification of an R-value. The data this facility provides will support customer decisions on which insulation materials suit certain lanes, support them in taking a riskbased approach towards GDP and provide documented evidence for quality assurance and best practice.”
TP3 Global has recently been acquired by Softbox, a leading global innovator and provider of cold chain packaging systems for the pharmaceuticals industry. The combined portfolio of industry-leading passive temperature control packaging systems and thermal protection products reinforces both companies’ ability to support their customers’ requirements for cold chain supply solutions, Softbox says.
CSafe Global, a leading expert in cold chain solutions has over the past six months received approval for its new temperaturecontrolled RAP container from both the European Aviation Safety Agency (EASA) and the US Federal Aviation Administration (FAA). The new container expands CSafe’s range of active and passive cold chain solutions, providing greater opportunities for
pharmaceutical and life-science companies to ship their temperature-sensitive goods around the globe.
The CSafe RAP container uses innovative heating and compressor-driven cooling technologies, together with advanced ThermoCor vacuum insulation panels (VIPs).
These features eliminate the risks to payloads associated with extreme ambient temperature conditions and long-duration shipments. The CSafe RAP active container system takes advantage of the proven performance and capabilities of the well-established CSafe RKN in order to remove the operational and environmental challenges encountered with global temperature-controlled shipments.
The CSafe RAP can maintain constant payload temperatures of between -30°C and +54°C; it also has a maximum payload volume of 6.7 m3, capable of accommodating up to four US or five Euro pallets.
Germany-based va-Q-tec, meanwhile, is expanding its footprint into North America, investing several million dollars in a new 20,000-ft² (1,860-m2) headquarters and operations facility in Langhorne, Pennsylvania. The new site will, the company says, become an innovation centre that will showcase its latest products, while also acting as a hub for its rental and repair station for small box containers. The facility will also have the capacity to produce 2,000 boxes and 50 to 100 containers per week.
“The investment in this new facility is a testament to our commitment to grow the business and expand our footprint in North America,” says va-Q-tec’s CEO Dr Joachim Kuhn. “After careful consideration, Langhorne is the perfect location for us - right in the heart of the healthcare cluster, close to several major airport hubs and with easy access to major roads across the country and in close proximity to the pharmaceutical centres in Boston and Durham, NC.”
Christopher J Storch, head of global sales, adds: “We want to offer our current and future customers the best solutions for their temperature-controlled logistics needs. By opening the new facility, we are not only strengthening our position in the US, it also puts us in a better place to accompany the growth of the pharmaceutical industry, in which 27 of the top 50 bestselling pharmaceutical products will require temperature-controlled transportation and handling by 2020.”
As part of va-Q-tec’s growth plans, it has hired Sandy Richwalski as managing director, North America. It also plans to create up to 20 new jobs in the medium term to service the US business.
Elsewhere, va-Q-tec has announced a global cooperation with Japan Airlines, with the aim of offering extended availability of passive thermal containers to one of the largest pharmaceutical markets in Asia.
“We are proud to announce Japan Airlines, a high-class airfreight company, as a strong partner for temperaturecontrolled pharma shipments,” says Takehiro Takasaki, country manager at va-Q-tec Japan. “The cooperation increases the network in Japan tremendously.”
Sook Yoo, head of business development, Asia at va-Q-tec, adds: “We pursue a strong growth strategy in the Asia-Pacific region. »
Besides the establishment of a subsidiary in Japan and the Japanese network station for operating cold chain supply transports, the cooperation with Japan Airlines is one important accomplishment for reaching our ambitious objectives in Japan.”
Va-Q-tec offers high-quality transport containers that provide temperature-controlled solutions for six temperature ranges from -70°C to +25°C in five sizes, taking up to two US pallets inside. These passive thermal containers allow for constant temperature control for five days without using external energy sources. “Currently, there is no other controlled and proven system out there that can reach this level of performance without external sources,” the company says.
Another Germany-based provider, DoKaSch Temperature Solutions, is also looking at expanding its market via a tie-up with an airline, having signed a master agreement with Ethiopian Cargo & Logistics Services (Ethiopian Airlines) for the supply of climate-controlled Opticooler unit load devices (ULDs). “We are very glad to offer our customers a highly reliable packaging solution to transport temperature-sensitive
shipments with DoKaSch’s Opticooler,” says Ethiopian Airlines managing director Fitsum Abady. “In this fast-growing and strongly competitive market, it is important that we offer our customers the best packaging solution for their sensitive cargo.”
Africa’s largest cargo terminal was recently inaugurated at Addis Ababa Airport, Ethiopian Airlines’ main hub, DoKaSch notes, stating that “the inauguration of this [stateof-the-art] cargo terminal, fitted with the latest technology and compartmentalised temperature-controlled storage facilities, will enhance the handling of temperature-sensitive cargo shipments, such as pharmaceuticals”.
Moreover, the new deal means that the airline can now use Opticoolers, which are equipped with battery-powered cooling compressors and heaters as well as a selfregulating temperature control, “to fly these goods through the hub of the airline to and from Africa”.
“Ethiopian Airlines is the most successful African carrier and their hub in Addis Ababa [is developing] very positively regarding cargo handling,” says DoKaSch managing director Andreas Seitz. “Therefore, we are very pleased
that we could expand our African network by signing [this] master agreement with Ethiopian Airlines.”
The Opticooler ULD is one of a range of temperature-controlled containers offered by DoKaSch, its main selling point being the lack of a consumable coolant such as dry ice. The Opticooler RAP is a large-capacity unit, with space for five euro pallets or four CP-1 pallets. It offers quadruple redundancy on all critical components and can control temperature within a 3°C range anywhere between +2°C and +30°C. It has an “extremely large battery capacity,” according to DoKaSch, which can be charged in under six hours and operate independently for 100 hours. If the battery runs low, the unit can be connected to mains power to continue operation.
DoKaSch also highlights the continuous manipulation-proof capture and storage of key metrics, using a system certified by TÜV Germany, via an onboard CPU. Data can be displayed or printed for quality assurance purposes. Alarms are triggered in the event of faults or non-compliant events, such as the doors being opened.
The smaller Opticooler RKN offers many of the same features but has a capacity of one euro or CP-1 pallet and triple-redundant components. Like the larger RAP version, the RKN is ruggedised to help cope with the sorts of rough handling expected during loading onto and unloading from aircraft. All essential components are positioned in such a way as to shield them from external impacts.
Other models from DoKaSch do not use compressors but dry ice for cooling and electric power for heating. The Unicooler has a temperature range of -20°C to +30°C, with permanent temperature monitoring and data recording. The Icecooler is a highly insulated version with no heating and specifically designed for pharmaceutical transport. Both the Unicooler and Icecooler are available in the same RAP and RKN sizes as the Opticooler. HCB www.tp3global.com www.softboxsystems.com www.csafeglobal.com www.va-q-tec.com www.dokasch-ts.com
WORLD COURIER AND MVD Free Airport, located in Montevideo, Uruguay, have formed a partnership that promises to greatly enhance pharmaceutical distribution throughout Latin America. MVD Free Airport was identified by World Courier as a key partner to provide a traceable, specialised and cost-effective entry point for Latin American distribution.
“World Courier has long identified the necessity to enhance and improve the distribution of pharmaceutical products in emerging markets,” says Marcos Lacués, branch manager of World Courier Uruguay. “[It] has been undergoing an arduous due diligence to ensure our key partners in every region are up to global World Courier standards.
“We’ve been familiarised with MVD Free Airport, its organisational culture, as well as its specific pharma experience, and together understood that our capabilities complemented each other perfectly,” Lacués continues. “After the construction of the pharma hub facilities, it became clear that the benefits presented to Uruguay and the LatAm region via a mutual collaboration would have a huge impact on our customers and the pharma sector in general.”
World Courier and MVD Free Airport have symbolised this collaborative spirit with the implementation of the first Standard Operating Procedure (SOP) designed for specific material handling, storage and shipment dispatching for Brazil-bound specialty products, ensuring that every task is performed ‘the World Courier way’.
The partnership will further provide significant operational optimisations and customer-
centric improvements, Lacués states: “With the globalisation of the supply chain and the identification of the main commercial opportunities primarily in emerging markets, pharma organisations are facing key challenges that need to be addressed. This includes optimising longhauls, centralising distribution for leaner stock management, and standardising lastmile delivery taking into account regional and local contexts.”
Customers will have access to optimally designed transport conditions, alongside a tax-free regime that allows for the performance of packaging and latecustomisation activities. World Courier’s global expertise will provide pharma organisations with a straightforward solution to regional distribution. “This is especially the case for time- and temperature-sensitive materials and high-value products, which is where the partnership between MVD Free
Airport and World Courier becomes a vital necessity for customers.” says Lacués.
The joint venture aims to deliver significant benefits for customers. By centralising stocks and postponing customisation activities, pharma organisations will be able to reduce stock-outs, enable rapid replenishments, minimise excess inventory at final destinations, and significantly reduce supply lead times. This will all be undertaken while ensuring its inbound/outbound logistics and storage and handling will be up to par with demanding pharma service level standards.
World Courier has also announced that in January 2018 it achieved Good Distribution Practice (GDP) certification across its 140 offices worldwide. DQS, a leading certification body for management systems worldwide, awarded the certification following a sixmonth long evaluation process covering transport, handling and storage processes. Those processes were tested against the EU GDP Guidelines, US Pharmacopeia and the World Health Organisation (WHO) DGP guidelines.
World Courier says it is the first logistics company to attain global GDP certification against three GDP standards. “As a company that’s committed to ensuring end-to-end product safety, we are proud to be the first specialty logistics provider to achieve this GDP-certification on such a global scale,” World Courier president Sam Herbert says. HCB www.worldcourier.com mvdfreeairport.com
BOLLORÉ LOGISTICS KOREA has become the first transport and logistics company in South Korea to independently achieve certification according to the International Air Transport Association (IATA) as a Centre of Excellence for Independent Validators in Pharmaceutical Logistics (CEIV Pharma).
The certification is a globally recognised and standardised certification for healthcare airfreight shipments. It aims to ensure that all air cargo industry operators are trained on the proper cold chain handling of those pharmaceutical products that require temperature control.
Bolloré Logistics Korea began the certification process in the third quarter of 2015. “The CEIV committee has worked with dedication to bring the internal processes to required expectations,” the company says. Certification was finalised on 31 January 2018.
“We are proud to be the first CEIV Pharma logistics company independently certified in Korea,” says Thibault Janssens, managing director of Bolloré Logistics Korea. “The certification reinforces our commitment to provide the highest standards of professionalism in handling the
transportation of high-value pharmaceutical products under strict temperature and timesensitive conditions.”
The CEIV Pharma certification will allow Bolloré Logistics Korea to have a competitive and strategic advantage in the local healthcare logistics market with a stronger, more competitive and enhanced air cargo service, Bolloré says.
“This is a new success which shows our commitment to achieve the highest international quality standard in the global pharmaceutical supply chain for its customers, by continually improving our processes and infrastructures to be compliant with IATA CEIV Pharma standards,” it adds. “With Australia, Singapore and now South Korea certified, the aim of Bolloré Logistics is to deploy this action throughout its global network with ongoing certifications on other sites in the Asia-Pacific region such as in Hong Kong and Japan.”
IATA created the CEIV Pharma standard in 2015. It aims to set the industrial standard for air cargo supply chain in pharmaceutical handling excellence. It addresses industry’s need for more safety, security, compliance and efficiency, by the creation of a globally consistent and recognised pharmaceutical product handling certification. CEIV Pharma
encompasses, or even supersedes, many of the existing pharmaceutical standards and guidelines, such as IATA Temperature Control Regulations (TCR), EU Good Distribution Practices (EU GDP), World Health Organisation (WHO) Annex 5 and the US Pharmacopeia standards.
The CEIV Pharma standard is a response to what IATA says is “the alarming decline of air cargo’s market share of global pharmaceutical product transport”.
“The industry identified a need to build a network of certified pharmaceutical trade lanes that meet consistent standards and assure product integrity,” IATA explains. “As a result, IATA has taken a leading role in supporting the air transport industry to comply with pharmaceutical manufacturers’ requirements. By establishing a common baseline from existing regulations and standards, this certification ensures international and national compliance to safeguard product integrity while addressing specific air cargo needs.”
Bolloré Logistics says that the certification is recognition of its excellent quality management system as well as the expertise of its specialised teams in each of its offices. These make it “a major player in the supply chain of pharmaceutical products”. HCB www.bollore-logistics.com
CERTIFICATION • WITH ITS STRONG FOCUS ON PHARMACEUTICALS, BOLLORÉ IS ACTIVELY PURSUING IATA CEIV PHARMA RECOGNITION ACROSS ITS ASIA-PACIFIC NETWORKBOLLORÉ SEES SOUTH KOREA AS AN IMPORTANT ELEMENT IN ITS ASIAN PHARMA SUPPLY CHAIN
ONSET, A WORLD leader in data loggers, is expanding its InTemp range of pharmaceutical cold chain management products with the launch of the InTemp CX Gateway.
The new CX Gateway, priced at $250, enables real-time notifications of temperature excursions, with alerts sent via email or text when loggers are in range. This allows for any corrective actions to be taken quickly and efficiently. Rapid responses will ensure the integrity of vaccines, regardless of whether they are stored in a facility, or have arrived at their in-transit destination.
The InTemp CX400 and CX500 series temperature loggers link to InTempConnect, Onset’s cloud-based data warehousing service. Users only have to place the CX Gateway within 30 metres of one or more of the loggers and connect it to the internet via wifi or ethernet. If an excursion occurs, an update is sent to InTempConnect, which is then able to alert a user-defined group via text message or email.
In addition to this, the CX Gateway can automate the process of downloading data from one or more InTemp loggers that are within range at fixed intervals, or on arrival of shipments. This process increases efficiency and eliminates the need to remove the loggers to download the required data. It also prevents missed downloads of critical vaccine storage temperature data.
“Too often, hospitals, clinics and companies in the distribution chain have had to choose between affordable vaccine storage data monitoring solutions that require manual uploads or wifi alternatives that are both complex and expensive,” says Paul DellaVilla, product marketing engineer for Onset. “With the
addition of our InTemp CX Gateway, we are harnessing mobile and cloud technology to bring unprecedented ease of use and cost-effectiveness to automating data downloads and real-time alerts. In doing so, we’re making it easier than ever for customers to gain the anytime, anywhere insights needed to ensure the integrity of their vaccines.”
The CX Gateway is modernising pharmaceutical cold chain monitoring, Onset says. As an affordable and highly accessible alternative to manually driven pharmaceutical cold chain monitoring solutions, the CX Gateway can achieve greater accuracy and is less susceptible to
error. Organisations such as vaccine clinics, hospitals and pharmaceutical manufacturers will be able to reduce demands on staff and resources after adoption of the Gateway.
CX500 and CX400 Bluetooth-enabled loggers offer a cost-effective alternative to GPS-based solutions. With no need to open refrigeration units or packages, the loggers are able to automatically transmit data about temperature conditions while eliminating any risk of compromising the environment.
InTemp CX400 loggers have been designed specifically to meet all the requirements of the Centers for Disease Control and Prevention (CVC) Vaccines for Children programme. All InTemp products also comply with Title 21 CFR Part 11, which requires that electronic records and electronic signatures are trustworthy and reliable.
The free Intemp mobile app enables easy and efficient logger setup, reducing staff training and workload. Authorised users are able to view data that has been uploaded to a dedicated account on the InTempConnect data warehousing service. Users will also be able to check logger status, set alarms and create reports from a smartphone or tablet. Using a mobile app enables data analysis from a centralised location provides a vehicle for two-way communications. HCB www.onsetcomp.com/intemp
IRELAND-BASED RAY Moran International Transport, which celebrated its 20th anniversary last year, is in the midst of a significant expansion of its capacity for groupage loads and pharmaceuticals. To help it on its way, it turned to Germany’s Krone and its range of specialised and curtainsider trailers.
“We started with one Krone trailer to see how things were,” says owner Ray Moran, “and soon realised that the combination of build quality and loading flexibility were good reasons to add some more. Accordingly, we now have one Cool Liner ‘Duoplex’ refrigerated trailer, four Dry Liner box trailers and five Profi
Liner curtainsiders, all of which come into their own for specific aspects of our operation.”
The Cool Liner trailer is fitted with Krone’s new Isowall moveable bulkhead. It was manufactured at Krone’s Lübtheen plant in Germany and is, Krone says, ideal for mixed temperature loads. The newly designed balancer system, combined with a locking lever at the top of the bulkhead, allows the Isowall to easily open, close and manoeuvre along the trailer. Additionally, due to the vertical movement of the bulkhead while opening and closing, there are no extra components required for vacuum ventilation. The bulkhead is also magnetically held in place when stowed on the roof, which eliminates the requirement for secondary locking systems or risk of fork lift obstruction. “When in use, the Isowall can be positioned
hard up against the load for added security and better use of load space,” says Moran. “It’s lightweight and very easy to move along the trailer.”
Germany’s Medicinal Product Act is very specific about the conditions required for the storage and transport of pharmaceutical products, stating for example: “Raw materials, compounds and end products as well as samples must be stored in such a way that quality is not adversely affected and that mix-ups are avoided. Critical parameters concerning the storage and transportation must be checked and recorded so that compliance with the requirements can be confirmed. [...] The storage containers and the internal transport containers must be designed so that the quality of their contents is not affected.”
Krone’s Cool Liner Pharma provides an exact model of how these legal requirements can be met. This is verified by Pharmaserv as well as the European Institute for Pharma Logistics (EIPL). Krone’s pharmaceutical trailers are certified by Pharmaserv at the Lübtheen production plant, after functional tests lasting several days. Krone’s telematics systems fitted to Cool Liner trailers take input from numerous data loggers placed in pre-defined positions in the vehicle superstructure to provide continuous monitoring of the temperature data and thereby a homogeneous temperature distribution in the superstructure.
The Cool Liner also received the EIPL certificate, which is proof of its quality at the interface between the pharmaceutical industry and its logistics partners.
Krone offers the pharmaceuticals-certified Cool Liner with a variety of equipment options. The trailer body is available with side walls of 60 mm or 45 mm thickness. The fridge units can be installed for single or multi-temperature operation. The Carrier Vector 1950 T as well as Thermo King SLXe 400 and SLXe Spectrum are available (each with optional remote evaporators). HCB www.krone-trailer.com
GERMANY’S BRENNTAG HAS begun construction of a new multi-million-pound distribution facility in the north-east of England. Located within Sunderland’s Turbine Business Park and due for completion by the end of this year, the new facility will include 370 m2 of office space, a 1,400-m2 warehouse with dedicated high-bay storage for both life and material science speciality ingredients, and bulk storage facilities for inorganic products. Set to be the new home of the Brenntag Newcastle team and situated next to the main A1 and A19 arterial routes, the 13,400-m2 site, Brenntag says, will also feature “extensive mixing and blending capabilities and will effectively be the hub for the north-east of England, servicing both the current customer base and the wider Brenntag network”.
“Firstly, it makes me very proud to be able to offer our loyal, hardworking colleagues a much-improved working environment, which is richly deserved,” says Shaun Myers, Brenntag UK & Ireland’s business services director. “We have a fantastic heritage of servicing the north-east and Cumbria and are extremely pleased that we will be able to expand our service offering to the region through our brand-new facilities. This major investment signifies our strategic intent to further enhance the efficiency of our infrastructure, geographical reach and added value capabilities in the core markets we serve. At the heart of our Service Excellence programme is the ability to easily access the full range of services you’d expect from a global leader through local servicing and representation, again the new facilities will only go to enhancing these values.”
Meanwhile, as part of its ongoing commitment to safety, Brenntag UK & Ireland reports that it has issued its drivers with new personal protective equipment (PPE). “The new uniforms have been designed for greater visibility, instant recognition, improved weather proofing and better all-round comfort for our drivers –the key features being the result of the direct feedback of our driver team,” the company says. “Our drivers are the public face of Brenntag; given the significance of the role, it was fitting that the launch of the new PPE was accompanied by the new Driver’s Charter (developed by the team) and a Mission, Vision and Standards Card.”
But it’s not just in Britain where Brenntag has been busy of late, with the chemical distribution giant also reporting that it has now officially opened an expanded Service and Application Center (SAC) and new mixing and blending facility at its Brenntag Thailand Operations Complex on the outskirts of Bangkok. The threestorey SAC, it reveals, not only encompasses existing facilities but also features ten applications laboratories focused on particular industrial needs, such as food, agriculture, home and personal care and textiles, among others.
“Standing at more than 1,000 m2, the extended SAC is conveniently connected to the existing SAC via an internal walkway on the third floor, which is fully dedicated to the Food & Beverage Application Center, where the technical team, for example, can do full preparation and processing for bakery, beverage, confectionery, dairy and meat applications,” Brenntag reports.
The second floor is occupied by a large, fully equipped conference room as well as laboratories for general, biotech, water treatment and agricultural applications. Rounding things off, the ground floor houses, inter alia, an analytical and quality control lab equipped with its own special reagents room designed for easy access to the nearby mixing and blending plant. “Thailand is a strategic market for Brenntag in the [Asia-Pacific] region,” the company states. “It has set the highest standards for operational excellence and considers quality as vital for all of its customers and supplier partners.”
“This extension and renovation of our Application Development facility and new mixing and blending plant,” says Brenntag Thailand’s managing director Flemming Soederquist, “clearly demonstrates that Brenntag is committed to all its corporate values and value proposition of distributing quality products and services for all stakeholders and, simultaneously, strengthening personal and environmental safety.”
Elsewhere in Asia, Brenntag has signed a new deal with Neste for the distribution of its premium-grade Nexbase™ Group III base oils across Greater China, a move that builds on an ongoing 20-year collaboration between the two companies. “We are pleased to have Brenntag as our new distributor for Nexbase Group III base oils in Greater China,” says Peter Zonneveld, Neste’s vice-president of sales, Europe. “We are confident that Brenntag meets the high quality, reliability and compliance expectations we have for our Nexbase Group III base oils deliveries in China.”
Used primarily as high-performance engine oils and industrial lubricants, Nexbase stocks, Neste says, boast “high oxidation stability, low evaporation, excellent low-temperature
fluidity and extremely low sulphur content”. Commenting on the news, Liu Hua of Brenntag Shanghai Enterprises Management states: “It’s a great pleasure being appointed as distributor of Nexbase Group III base oils for Greater China. This is a great step forward for Brenntag China to enlarge its business into the lubricants industry. As a professional chemical distributor, we are confident of providing efficient services for this industry in Greater China by working closely with Neste.”
In other news, Brenntag-owned Multisol reports that Kevin Williams has stepped down as managing director after 22 years at the helm. “On behalf of everyone at Multisol, we thank Kevin for his significant contribution and loyalty and wish him well in the future,” says CEO David Hopkinson. “Kevin is extremely well known and respected in our industry and he has played a major part in Multisol’s success over the last 22 years, developing both the business and defining relationships with many key suppliers across Europe, including Infineum, Chevron, Neste and Petro Canada. With his extensive knowledge and experience, we are delighted that Kevin will continue to support the business in his new consultancy role.”
Williams will be succeeded in the post by Kevin Wright, who, the company says, “grew up in Northern Ireland, where he studied mechanical engineering followed by a postgraduate MA in marketing”. After beginning his career at Short Bros, Wright moved to Shell International, holding a number of engineering, technical, sales and senior management posts, including automotive lubricants manager for the UK and Ireland. In more recent years, his roles have included the implementation of “a ground-breaking” Sales Excellence Business programme across the Europe, Middle East and Africa (EMEA) region and the design and deployment of an award-winning Technical Sales Capability programme for Shell’s global distributor B2B network. He will now work closely with his fellow Multisol directors across the wider European business “to lead the development and delivery of the business sales strategy across the UK and EMEA region”. HCB www.brenntag.com www.multisolgroup.com
UNIVAR HAS CLOSED its 2017 books with a net income of $119.8m from net sales worth almost $8.3bn. This compares to a prioryear net loss of $68.4m from net sales of just under $8.1bn. Meanwhile, for the fourth quarter, the company achieved a net income of $27m, up from a net loss of $59.2m this time last year, from sales worth $2bn, themselves up 8.1 per cent year-on-year from $1.8bn.
“2017 was a pivotal year as we significantly advanced our transformation,” says outgoing chairman and CEO Steve Newlin.
“We considerably improved our execution and returned Univar to growth, increasing our momentum with each quarter of the year. Our strategic initiatives of Commercial Greatness, Operational Excellence and One Univar are strengthening our organisation and I am confident that David Jukes [Newlin’s successor as CEO] is the best leader to advance Univar’s transformation to achieve our 2019 and 2021 growth targets.”
“We exited 2017 with higher profitability, solid cash flow and a much stronger balance sheet,”
adds executive vice-president and CFO Carl Lukach. “This enables us to deploy capital to targeted growth investments in our people, operations and technology, while continuing to reduce our leverage and earn a superior return on capital for our shareholders.”
Breaking these figures down geographically, Univar reveals that in the fourth quarter of last year its operations in the US increased sales by 4.2 per cent to surpass the $1.1bn mark. At the same time, US adjusted EBITDA rose 10.7 per cent to reach $86.7m and in so doing racked up a fourth consecutive quarter of growth. Across the border in Canada, sales were up 12.3 per cent, going from $242.1m to $271.9m, concurrent with a 13.3 per cent increase in adjusted EBITDA, which came in at $28.1m as a result, the company says, of “higher average selling prices, improved sales force execution, strong operating expense management and the benefit of a stronger Canadian dollar”.
Meanwhile, in Europe, the Middle East and Africa, a similarly rosy picture emerged. In addition to upping sales by 16.9 per cent from $394.4m to $460.9m, the company also saw its adjusted EBITDA increase 13.1 per cent, from $28.9m to $32.7m, thanks “to improvements in sales force execution, growth in Focused Industries and Industrial Specialties, higher average selling prices [and] a stronger euro”. Adjusted EBITDA from the company’s Rest of World operations, however, remained flat at $7.8m, despite a 5 per cent increase in sales, which rose from $91.7m to $96.3m. “Higher average selling prices and mix improvement were offset by lower volume, which was the result of continued shortages of certain products in Latin America and softness in local economic conditions,” Univar reports, noting that “growth in Brazil and increased profitability in Asia Pacific was offset by softness in Mexico”.
Looking to the future, the company says that it “expects to capitalise on the positive growth momentum it created in 2017”. As a result, it anticipates finishing 2018 with “mid-single digit revenue growth reflecting improvements in sales force
execution, higher win/loss ratios and new supplier authorisations”, while delivering “low double-digit percent growth in adjusted EBITDA”.
In terms of new supplier authorisations, Univar has been pretty busy of late, inking a wealth of contracts, such as that with The Chemours Company for the exclusive distribution of hydrochloric acid produced at the latter firm’s Parkersburg plant in West Virginia. With a total market of over 5m tonnes, hydrochloric acid, Univar says, is widely used in a number of industrial applications, including pH control for water treatment processes, steel manufacturing and oil and gas drilling. As a result of this agreement, Univar will bring “this important product closer to its customers in these markets, shortening the supply chain and improving service response times”.
“Customers will benefit from Chemours’ and Univar’s shared safety culture and focus on productivity and efficiency to help manage their cost to serve,” says Jerry Panock,
Univar’s vice-president of growth in the basic chemicals segment. “Additionally, it will help provide customers with a competitive and long-term supply of hydrochloric acid critical to their operations.”
Univar has also expanded its relationship with Dow to include the exclusive distribution of Ucon™ fluids and lubricants across North America. “Univar and Dow have enjoyed a strong relationship that spans approximately 75 years of serving customers in a wide variety of industries,” says Brian Jurcak, Univar’s vice-president of product management. “Dow’s global leadership, reputation for quality and their commitment to growth in key end markets creates tremendous value. Pair that with Univar’s industry knowhow and value-added services, including excellent technical and laboratory support, as well as formulation proficiency, and we can now deliver an exceptional experience for our customers.”
“The combination of Univar and [Univar-owned e-distributor] ChemPoint representing this product line offers Dow market-leading capabilities to help drive our growth,” adds Andrew Larson, Dow’s North America market manager. “Customers across North America, in key end market segments, such as industrial lubricants and metalworking fluids, will benefit from
Univar’s extensive supply chain network, commitment to customer success and leading digital technology.”
Meanwhile, Univar has also signed an agreement with ABITEC for the distribution of its Capmul®, Captex®, Caprol®, Acconon®, Sterotex®, Nutri Sperse®, Hyrdo-Kote® and Pureco® product lines across Canada. “In the pharmaceutical market, these products are used for a wide array of applications, including solubilisation, emulsification and lubrication to improve drug delivery and enhance bioavailability,” Univar explains, adding that they also have “a number of health applications” within the nutraceutical sector, such as in the fields of sports nutrition and performance and weight management. As a result of this new deal, Univar continues, will now be able to expand its speciality portfolio “to provide customers with important and relevant solutions that will help to overcome some of the most intricate formulating issues facing the pharmaceutical and nutraceutical industries today”.
“We are excited to collaborate with ABITEC, which further enhances our portfolio of highly functional ingredients for the pharmaceutical and nutraceutical industries, both of which we have identified as strategic growth industries for Univar,” says Willy St Cyr, Univar’s vice-president of product and industry development.
“ABITEC’s superior product portfolio coupled with Univar’s technical expertise will help provide customers with next-generation solutions to today’s most complex formulation challenges.”
“ABITEC is pleased to embark on this partnership with Univar to market and distribute ABITEC’s highly functional line of pharmaceutical and nutraceutical excipients throughout Canada,” adds ABITEC’s technical business director Dr John Tillotson. “Univar has a long-standing reputation for their strong capabilities in the technical distribution of highly-functional products in the market and this relationship offers strong support for ABITEC’s business and growth in Canada.” HCB www.univar.com
UK-headquartered 2M Holdings has acquired Franken-Kosmetik-Chemiehandel, a privately held distributor of specialty chemicals based in Nürnberg, Germany. “2M is seeking opportunities to expand its footprint into mainland Europe,” says 2M founder, chairman and CEO Mottie Kessler. “The acquisition of FrankenChemie represents such an event.
“FrankenChemie’s dedicated and experienced team, the ability to support customers with an application laboratory and just-in-time deliveries in the right pack size are FrankenChemie’s strengths. 2M will now build on these strengths and invest to provide customers and suppliers an even better offering. We are therefore very excited about this acquisition,” Kessler adds.
With its prime location and its excellent reputation, FrankenChemie, 2M reports, “is a perfect fit” with the acquired business, distributing a wide range of products to the personal care, home care and food ingredients sectors within Germany as well as other European countries. Moreover, FrankenChemie’s “market-sector focus and product range” is highly aligned with that of Surfachem, one of 2M’s largest companies. Indeed, both companies list Evonik as a major supplier, leading Joerg Prante, Evonik’s key account manager and sales manager for central Europe and Sub-Saharan Africa, to state: “Having a long history with 2M
and Surfachem, we are delighted to see 2M and FrankenChemie come together.”
This is certainly not the first time that 2M has acquired operations in Germany, having for example taken control of Düsseldorf-based CE-O2 Trockeneis, a long-standing producer and supplier of dry ice to customers from the food, catering and life science industries, in April 2017. “When we acquire a business, our objective is to buy a good business and help it to grow and become excellent,” Kessler asserts. “An added benefit is when we can use it as a stepping stone to add product lines which support our suppliers and new customers.”
Established in 2004, Runcorn-headquartered 2M describes itself as “a portfolio of strong brand chemical distribution and related chemical services companies of samples management, storage and blending”. In addition to Surfachem, these companies also include Banner Chemicals, MP Storage & Blending, Packed Chlorine, SampleRite UK, SampleRite China, CE-O2 and Stowlin Croftshaw. Operating locations across the UK, Ireland, Germany, Poland, the Benelux countries and Scandinavia as well as China and Brazil, 2M exports to more than 90 countries worldwide, specialising in the supply of solvents, speciality chemicals and surfactants to customers drawn from the automotive, coatings, emission reduction, oilfield and refineries, flavours and fragrances, personal care, household, industrial and precision cleaning and pharmaceuticals industries among others. www.2m-holdings.com
US-based Hawkins has announced a third-quarter net income of $17.1m, up from $3.6m this time last year, from sales worth $118.1m, themselves up 5.1 per cent year-on-year from $112.4m. For the first nine months of the year, Hawkins reported a net income of $28.2m and sales totalling $377.2m. This compares to respective prior-year figures of $18.3m and $365m.
“During the third quarter, we were pleased to see stabilisation in raw material costs and increased selling prices for our products,” says president and CEO Patrick Hawkins. “Both our Industrial and Water Treatment segments had continued year-over-year revenue growth, with the year-over-year decline in Industrial gross profit dollars being much less than in each of the first two quarters of the year.”
“In our Health and Nutrition segment, sales and margins of distributed products continued to grow; however, reduced sales of manufactured products negatively impacted the overall results,” he continues. “We are addressing these shortfalls by eliminating inefficiencies and focusing on plant core competencies. In addition, we are making a leadership change and Dan Stauber, who has more than 30 years’ experience with this business, will be re-assuming leadership of the Stauber organisation as the vice-president of Health and Nutrition.”
“Fiscal 2018 has been a challenging year with raw material cost increases and competitive pressures limiting our ability to pass the full
increase onto our customers, but it has resulted in the entire organisation continuing to be very cost-focused while ensuring we deliver best-in-class service to our customers,” Hawkins states. “This is having a direct, positive impact on our results of operations. Last quarter, I stated that our results were negatively impacted by investments we had made to facilitate future growth in all parts of our company and to comply with increased customer and regulatory requirements. Those incremental investments are behind us and our quarter- and year-to-date selling, general and administrative expenses were lower than the same period in the previous year. In addition, our operational overhead costs, while still higher year-over-year, were significantly lower on a comparative basis than the first two quarters of fiscal 2018.” www.hawkinsinc.com
France-headquartered Safic-Alcan has been named as the exclusive distributor of Ajinomoto OmniChem’s full range of amino acid-based personal care ingredients across Portugal, the Czech Republic, Slovakia, Hungary Romania and Bulgaria. The agreement, Safic-Alcan notes, includes such trademarked lines as Amisoft®,
Amilite®, CAE®, Amisafe®, Ajidew®, Prodew® and Eldew®, a range of “natural and eco-friendly substitutes for conventional non-biodegradable ingredients”.
“We are happy to have been selected by Ajinomoto OmniChem and to represent a key player in the cosmetics industry,” says Safic-Alcan CEO Philippe Combette. “This new partnership will allow us to better serve our customers in the dedicated territories by distributing natural and brand-new unique ingredients that are highly complementary to Safic-Alcan’s portfolio and which enable us to develop innovative solutions driven by our customers’ needs.”
www.safic-alcan.com
Germany’s Bodo Möller Chemie has opened a new UK subsidiary. Based in Manchester and led by Thomas McCarthy, the new entity will initially focus on the sale of coatings products across the UK and Ireland, with further products added at a later date. “The UK is one of the largest economies in Europe and is therefore an attractive market for us,” says Bodo managing director Jürgen Rietschle, “The coating industry accounts for a large proportion of British exports to Europe and the rest of the world.”
“I am delighted to have the opportunity to represent Bodo Möller Chemie here in Britain and abroad,” McCarthy states. “It is an exciting role as part of a global team, which has already made a name for itself for expert and solution-focused distribution.” www.bm-chemie.com
Germany’s Velox has signed an exclusive deal with Life Material Technologies for the distribution of antimicrobial additives and treatments for the plastics, coatings and textile industries across Germany, Austria, Switzerland, the Benelux countries and the Nordic region.
“With this new partnership, Velox is extending its existing antimicrobial portfolio and is able to address new target markets for compounding, extrusion and injection-moulding applications,” says Velox product manager Stefan Rokitta. “Life has price-competitive solutions with regard to the currently increasing demand for antimicrobial technologies delivering not only reliable inhibition of bacteria and odour, but also colour as well as temperature stability.”
www.velox.com
BELGIUM-BASED LOGISTICS company H Essers has acquired compatriot tank container operator Huktra NV. The transaction, H Essers says, is “entirely in line with the further expansion of its strategic market segment in the chemical industry”.
Headquartered in Zeebrugge, Huktra has a fleet of 897 tank containers for all types of chemicals and last year achieved a turnover of some €50m. It has roughly 50 employees at its offices in Belgium, Italy, Spain and the UK and its own 20,000-m2 maintenance
centre in Zeebrugge. Current managers Gerd and Tim van Poucke, the second generation to lead the family-owned business, will remain with the firm.
“After the strong growth Huktra has recorded in the past years, it is now time for the next step,” say Gerd and Tim.
“Thanks to the takeover by a strong, industrial player such as H Essers, Huktra will be able to keep growing in the coming years and to further develop our expertise.”
H Essers’ CEO, Gert Bervoets, also looks forward with confidence: “The takeover of Huktra is entirely in line with our strategy to offer our clients the best possible synchromodal solutions. Combining different modes of transportation in an intelligent way is
the future, because it offers an answer to current challenges in the field of mobility and the environment. But most of all, synchromodality offers a new interpretation for the management of transportation flows. This approach not only makes them more efficient, but also more advantageous and sustainable. A win-win situation for all parties involved: customers, logistics service providers, and our entire society.”
The acquisition of Huktra also provides H Essers with a footprint in new territories, Spain and the UK, meaning it now has 71 offices in 17 countries. “At a national level, the takeover seamlessly connects to the construction of our trimodal chemical site, H Essers Dry Port Genk,” says Bervoets, “and to our recent investments in the upgrade of our site in Wilrijk, with its tank container terminal and state-of the art filling installation. This enables us to continuously improve our all-in solutions for our chemicals customers.”
Furthermore, the Zeebrugge location is, H Essers says, “an enormous strategic asset” when it comes to serving European and intercontinental destinations through intermodal transport. Huktra’s specialisation in three market segments – liquid bulk, dry bulk and powders – also expands H Essers’ customer base with such leading names in the chemical industry as BASF, Eastman and Repsol.
At the operational level, though, few changes are expected. “Huktra is a family business with the same values and standards as H Essers. We are all on the same page,” says Bervoets. “Moreover, just like H Essers, Huktra is committed to safety and quality, including a constant renewal of their materials and installations, which means that their approach and operation also meet the highest standards and strictest values. We eagerly look forward to welcoming our new colleagues to the warm H Essers family and continue building our future together.”
The parties have not disclosed the terms of the deal, which is subject to the usual registration procedure with the EU Competition Commission. HCB www.essers.com www.huktra.com
“PERFORMING ALL ACTIVITIES as safely and efficiently as possible in the shortest time”. From week to week, this sums up the greatest challenge to Gerard Weijers who, as the director/owner of G Weijers Internationale Transporten, must always accommodate the driving hours regulations.
Since 2007, G Weijers has specialised in intermodal goods transport in conformity with ADR. In order to make loading and discharging of tank containers as safe and
efficient as possible, Weijers has equipped his tanks with a special combination, namely a B200 Mouvex compressor, a 2” membrane pump and a Lodar remote control from Wiegel Transport Equipment. By means of this remote control, the operator may shut down all on-board systems from a distance by the push of a button.
According to industry bodies, some 80 per cent of all accidents during dangerous goods road transport in Europe occur during loading
and discharging. In the US too it is an issue: a recent tragic accident with one fatality occurred because the truck driver was unable to reach his vehicle’s shutdown button in time while the flammable content of his tank container leaked out. Thanks to the chosen solution of G Weijers, from now on the driver may remotely operate his vehicle or even perform a shutdown.
G Weijers can transport any suitable liquids in a tank container, such as various types of oil and juices, as well as liquids for the pharmaceutical and chemical industries. One of the main products that the company is currently carrying for the pharmaceutical industry is intestinal mucus.
Intestinal mucus is used as a base ingredient for the production of blood thinners and blood thinning pills. The substance is picked up at 52 meat processing plants in the Benelux region each week.
Weijers explains: “The production of these types of drugs requires great volumes of intestinal mucus, since a single full container only results in 200 to 250 kg of usable substance. For quite some time now, we have provided intermodal transport of this product from northern Europe to Spain. Our company drops a full product container at a transfer terminal in Antwerp. Subsequently, the container is shipped by rail to southern Spain. On location, a new full container from our client in southern Spain is picked up, which then needs to be delivered to a final destination in northern Europe. Any railway strike necessitates us to keep on trucking all the way to the final destination. Given the limited shelf life of intestinal mucus, it must always be delivered within a designated number of days.”
Particularly with the transport of limited shelf-life products, such as intestinal mucus and food products, loading and discharging them as quickly and as efficiently as possible is essential. Within this context, driver safety and the safety of others must not be ignored. From a safety perspective, Weijers is always looking for the latest innovations in the above-mentioned field. Hence, he had his truck for loading and discharging of tank
containers fitted out with the latest B200 Mouvex compressor complete with an air cooler. The equipment includes a compact industrial Lodar remote control from Wiegel Transport Equipment, approved for use with ADR transports.
Werner Kromdijk, technology advisor at Wiegel Transport Equipment, explains: “What convinced us was the enormous air capacity of this 26.5 kg, compact screw compressor, since it enables the driver to force the full content out of the tank container in a relatively short amount of time.” During loading as well as discharging, the compressor may also be used to operate the 2” on-board membrane pump in order to suction the intestinal mucus from a silo.“
At first, the remote control with six functions only served to switch the pump and air cooler on and off. Yet there were two more buttons that had no designated function. In consultation with Gerard Weijers, it was decided to use these two buttons for starting and shutting
down the entire vehicle. Since the remote control can operate both the vehicle as well as the on-board equipment from a safe distance (up to 300 metres), the driver and/or operator are no longer exposed to the risk of physical injury in case of a broken hose or worse.
As soon as product loading is completed, the pump may be simply shut off by using the remote control. Even the vehicle engine may be started remotely, so the driver can immediately drive away. Interestingly enough, the remote control unit may also be equipped with an optional Texas Instrument chip, so it is prepared for broadcasting as well as receiving at some future point in time. This feature is useful within the context of the developments towards Industry 4.0.”
On average, G Weijers loads a tank twice a day, with a clean between loads, five days a week. Compared to the traditional vane compressor used before, the substantially lighter screw compressor can result in a 25 to 35 per cent time saving on discharge, or a fuel saving of 3 to 4 litres per delivery. A full load can now be discharged in less than 40 minutes, which – together with time savings realised by the use of the remote control unit - results in a significant lower cost all round. In addition, this much more eco-friendly configuration results in lower CO2 emissions and a much safer operating environment for the truck driver during loading and discharging.
Wiegel Transport Equipment has operated from its base in Moerdijk, the Netherlands, since 2012. Its own workshop handles truck conversions to customer specifications. Success in its home market prompted an expansion into Germany, where Wiegel Transport Equipment GmbH also obtained the official distributorship for Mouvex and Blackmer in 2016. In March 2017
Wiegel added exclusive distributorship of Unibloc pumps for the Benelux, Germany, Switzerland and Austria.
General manager Joris Adelaar explains Wiegel’s strategy: “With our organisation, we want to organically grow into the role of ‘systems integrator’ in Europe or focus on strategic takeovers fitting within our organisational philosophy. The recent takeover of the workshop activities of the German silo transporter DWS fits within this framework. DWS will continue these activities from now on under the name of Wiegel Transport Equipment GmbH. With this second site in the German city of Lorsch, Wiegel is focusing on the German market with a team of experts with many years of experience in the sale of components, the construction of complete systems, as well as their maintenance and repairs.
“The main thing for us as an organisation is that our clients are able to reduce their vehicles’ CO2 emissions with Wiegel’s components,” Adelaar adds. “Moreover, by expanding our product range, we are responding to current market developments in the transport world. These include being more energy efficient, providing more compact solutions, lower fuel consumption, better deployability, more flexibility, a lower weight, and a more efficient use of space in conjunction with simple maintenance. Naturally, it is important that our products are safe to operate. In short, it is a continuous quest for innovative products that may require a substantial initial investment. This is quite acceptable, provided that the return in investment over a couple of years remains strong.” HCB www.gweijers.com www.wiegel.eu
The new CarLo system, due to be implemented in full during 2019, covers all aspects of transport management. This includes planning and controlling, tracking and telematics, order management and invoicing and accounting, for all modes of transport.
system aims to minimise manual work, while integrating with clients’ operations and bosting efficiency.
The CarLo system is able to quickly handle large volumes of data, which will allow Imperial Logistics to improve service delivery for clients. Citing the example of one major client in the automotive industry, Lütjann explains: “Imperial Logistics has to handle between 10 and 15 thousand orders within tight time frames on this client’s behalf on a daily basis. In this kind of situation, you need extremely powerful software. Another benefit of CarLo is the availability of status interfaces, which are essential when working in the automobile sector.”
The group has achieved increases in productivity within weeks of implementing with new system, Doug Vela, CIO of Imperial Logistics South Africa, reports. He adds that the new system allows subcontractors to be easily connected to CarLo through interfaces with many other transport management systems, while drivers connect to the ‘InTouch’ telematics system embedded in CarLo, allowing them to generate reports. CarLo’s advanced web-based platform ensures the synchronisation of data in real time and aims to reduce logistics costs and eliminate transmission errors.
“[Customers] will have better access to information through real-time tracking,” explains Michael Lütjann, CIO of Imperial Logistics. “Client service will be enhanced by extended reporting and augmented analytics capabilities that encompass orders, shipments, vehicles and drivers.”
In addition, Lütjann says, implementation of the CarLo system will deliver financial benefits, including “optimal management of cost and revenue, transaction auditability from start to finish and a clear view of profit and loss”.
IMPERIAL LOGISTICS HAS begun rolling out a standardised transport management system (TMS) for its road transport operations throughout Europe and Africa. The company has opted for the CarLo TMS from Soloplan as a method of streamlining its transport operations.
“The switch in the individual business divisions has already been completed in Johannesburg, Stellenbosch and Durban,” continues Lütjann. “The first German and Polish business locations in the general cargo and liquid sections of the Road business unit are due to follow during the first and second quarters of this year.” The new management
CarLo is replacing a number of different TMSs currently in use at Imperial Logistics. The aim is to have standard, comparable, highly automated processes for planning, invoicing, monitoring, electronic documentation and archiving. Imperial Logistics is also planning to involve subcontractors via a web portal and an app, and to make use of a reporting function for clients. The new TMS will be integrated in the existing systems in the IT landscape like ERP, DMS or telematics systems via various interfaces with other programmes. They include different processes from operations like fleet management, price quotations (price information), planning the use of personnel and key performance indicators (KPIs).
CarLo is expected to be rolled out at all the group’s business locations globally over the next two years, to approximately 2,000 users. HCB www.imperial-international.com
THE SIZE OF IMPERIAL LOGISTICS NEEDS A SERIOUS TRANSPORT MANAGEMENT
IT BELIEVES IT HAS FOUND THE ANSWER FOR ITS INTERNATIONAL NEEDS
US-HEADQUARTERED XPO Logistics has posted a 2017 net income of $360.2m, more than four times the $84.5 achieved in 2016, from revenues worth nearly $15.4bn, themselves up from $14.6bn. Meanwhile, for the company’s fourth quarter, net income also rose significantly, coming in at $207.1m from $32.1m a year ago, with revenues increasing over the period from $3.7bn to just under $4.2bn.
“I’m pleased that we beat fourth-quarter expectations for revenue, EPS, adjusted EBITDA, cash flow from operations and free cash flow,” says chairman and CEO Bradley Jacobs. “We generated outsized organic revenue growth of 10.4 per cent, led by gains in freight brokerage, last mile and contract logistics.”
“In our transportation segment, we grew freight brokerage revenue by 33 per cent and increased net revenue margin in a tight market,” he continues. “Our North American less-than-truckload unit increased operating income by 44 per cent year-over-year and improved its adjusted operating ratio to 89.9 per cent — the best fourth quarter ratio in 12 years. We expect to improve the ratio by another 100 to 200 basis points in 2018. Globally, in both transportation and logistics, we capitalised on a strong economy in every country where we operate.”
“We’ve entered 2018 with a global sales pipeline of $3.2bn, following a record $2.8bn of new business signed in 2017,” Jacobs states. “We expect to increase adjusted EBITDA by at least another 17 per cent and deliver about $625m of free cash flow this year, while investing heavily in technology and sales force effectiveness.”
Breaking these figures down, the company reveals that its Transportation segment finished the fourth quarter with an operating income of $132.8m, up from $84.0m 12 months ago, from revenues totalling $2.7bn, themselves up from $2.3bn. The Logistics division also saw its operating income grow, rising from $51.2m to $60.3m, concurrent with an increase in revenues, which came in at nearly $1.6bn from $1.4bn thanks largely to strong demand for contract logistics.
XPO also had much to celebrate in Europe, where it closed its full-year 2017 books with revenues of approximately $7bn, an increase of 5.5 per cent on 2016’s showing. “We delivered solid revenue growth of 7.6 per cent at a constant exchange rate in 2017, reflecting our commitment to superior customer service and our substantial investments in salesforce effectiveness,” says XPO Logistics Europe CEO Malcolm Wilson. “Our focus on data analysis enabled us to anticipate customer needs during the holiday peak and adapt quickly, particularly with e-fulfilment.”
In other news, XPO has launched WMx, which it describes as a “new cloud-based, mobile software platform” that enables the “rapid deployment and integration of automation and robotics at a fraction of traditional start-up times”. WMx, it continues, “creates a single solution for warehouse integration by combining key supply chain elements into one versatile application”. As such, customers can benefit “from unified order management, maximum configurability and intuitive dashboard tools that analyse trends and guide decision-making”.
Furthermore, WMx’s multilingual capabilities “synchronise XPO’s warehouse operations worldwide, giving multinational customers a consistent, global supply chain experience”.
“Our WMx platform is the future of warehouse management,” says XPO’s chief operating officer Troy Cooper. “It turbocharges our operations through greater connectivity, brings innovations on line more rapidly than ever before and supports distributed order management for greater efficiency in multisite and multi-channel environments.” HCB www.xpo.com
FINANCIALS • XPO LOGISTICS ENJOYED A BOOM YEAR IN 2017, WITH PLENTY OF ORGANIC GROWTH. IT IS NOW IMPLEMENTING A NEW WAREHOUSE MANAGEMENT TOOL TO KEEP THINGS MOVING
US-HEADQUARTERED BDP International has opened new offices in the Kenyan cities of Nairobi and Mombasa, bringing its number of global locations to 147. “BDP’s new presence in Kenya serves to provide a more comprehensive scope of logistics services to clients in East Africa. With a youthful, budding population, dynamic private sector, highly skilled workforce and advanced infrastructure, Kenya plays a pivotal role in the region’s industry,” the company says.
Among other things, the new locations will offer air and ocean freight forwarding, customs brokerage, regulatory and compliance services, overland and multimodal transport, project logistics, warehousing, domestic distribution and consultancy services. Operations in Kenya will be led by country manager Timothy Muya, who will be based in Nairobi, with the seaport location in Mombasa serving as a gateway for ocean cargo destined for Kenya, Uganda, Rwanda, the Democratic Republic of Congo and South Sudan.
“BDP is proud to announce the opening of our newest locations in Kenya, marking not only the expansion of our presence in East Africa, but our global network of streamlined international coverage,” says BDP chairman and CEO Richard J Bolte, Jr. “The Kenya offices will play a pivotal role in accommodating the diverse needs of clients located in multiple countries across the region.”
Meanwhile, in other news, BDP has been named by the Ethisphere Institute (EI) as one of the 2018 World’s Most Ethical Companies. This is the third time BDP has been recognised in this way by the EI and is one of only two such honourees in the logistics industry.
“The World’s Most Ethical Companies assessment is based upon the Ethisphere Institute’s Ethics Quotient® (EQ) framework, which offers a quantitative way to assess a company’s performance in an objective, consistent and standardised manner,” BDP explains, noting that “the information collected provides a comprehensive sampling of definitive criteria of core competencies”.
Scores, it continues, are generated in five key categories: ethics and compliance; corporate citizenship and responsibility; culture of ethics; governance; and leadership,
innovation and reputation. “All companies that participate in the assessment process receive their scores, providing them with valuable insights into how they stack up against leading organisations,” it says.
Commenting on the news, Bolte states: “The bottom line is, everything we do at BDP we do with the highest ethical standards in mind. It’s about remaining committed to responsible practices in our daily operations across the globe. We are honoured to be recognised as an industry leader in this field for the third time.”
“We pride ourselves in the ethics programme at BDP International and recognise the tremendous impact it has on our employees and the daily operations of the business,” adds BDP chief legal officer Catherine Muldoon. “This recognition by Ethisphere speaks to the mindset of integrity that drives our culture.”
“While the discourse around the world changed profoundly in 2017, a stronger voice emerged,” says EI CEO Timothy Erblich. “Global corporations operating with a common rule of law are now society’s strongest force to improve the human condition. This year we saw companies increasingly finding their voice. The World’s Most Ethical Companies in particular continued to show exemplary leadership. I congratulate everyone at BDP International for being recognised as one of the World’s Most Ethical Companies.” HCB www.bdpinternational.com
Nexiot has expanded its Digital Logistics platform with the integration of a Blockchaintype distributed ledger function. Data held in the ledger can include a date and time stamp, making the information legally binding and adding a valuable layer of accountability to goods in transit.
“This Blockchain technology also opens the door to the introduction of Smart Digital Contracts,” says marketing and sales director Daniel MacGregor. “Our sensors have already established a new level of accuracy for contract stipulations of location and location-based events. These can now be linked to confirm terms and fulfilment of contracts.”
Switzerland-based Nexiot, which last year signed a deal to equip all of VTG’s European rail fleet with its smart sensors, processed more
than 100m data points in January 2018 alone. Use of Blockchain concepts will allow those data points to be used to verify contract execution, from automated demurrage and insurance claims to excess mileage recharges.
“Our unique combination of zeromaintenance hardware, with mobile app support, digital documents on board, and the enriched data capabilities of a flexible, robust management platform, provides the base to add these Distributed Ledger capabilities,” says MacGregor. “By 2019, it is estimated that 20 per cent of all IoT deployments will have basic levels of Blockchain services and this development promises to deliver a long overdue layer of services to enhance quality in logistics.” nexiot.ch
Suttons Tankers has acquired the business of Bullard Ltd, which specialises in the transport of wastes and fuels in road tankers and is based in Sheffield, UK. Simon Bullard, who founded the firm in 1993, will remain active in a key management role, Suttons says.
“This was a natural evolution with a known player in the market and is beneficial to both parties,” says Michael Cundy, managing director of Suttons Tankers. “We already have the largest shared-user chemical fleet in the UK and this acquisition allows us to focus on one of our key strategic sectors for growth. Our UK network also adds flexibility and capacity to Bullard’s customers and will deliver improved service and capability.”
“In this market, flexibility is key and the scale and infrastructure that Suttons offers is a real benefit to my customers and allows us to be responsive to the increased demand for our services,” Bullard adds. www.suttonsgroup.com
VTG has reported revenues of €1.01bn for 2017, up 2.8 per cent on the previous year. All three divisions contributed to the growth, with capacity utilisation in its Railcar division reaching 92.2 per cent, the highest level since the end of 2008. Adjusted EBITDA was up by 2.4 per cent year-on-year, though one-off charges resulted in a slight fall to €343.4m.
“We are very satisfied with the way business developed overall in 2017. The positive economic climate and investments to expand our business are now bearing fruit,” says Dr Heiko Fischer, chairman of the executive board of VTG AG. “The fourth quarter of 2017 was the strongest in the entire financial year, which lays a solid foundation for the future. In 2018, we expect to see further positive development in revenue and EBITDA. Another focus of our activities will be the Nacco transaction, which we hope to close in the second half of the year.” Excluding any likely impact from the Nacco deal, VTG anticipates 2018 EBITDA being in the €340m to €370m range.
Revenue from VTG’s tank container business in 2017 was flat at €157.3m and EBITDA was essentially unchanged at €11.3m. VTG observes that rising transport volumes were offset by lower freight rates.
www.vtg.com
WINCANTON FULL OF FUEL Wincanton has extended its contract with Phillips 66 to provide delivery services for ground fuels and LPG in the UK. The contract will see the provision of 31 tankers delivering fuel from Phillips 66’s depots in Immingham, Stockton-On-Tees and Kingsbury to Jetbranded forecourts and commercial customers across the UK. Under the same agreement, Wincanton last year made more than 20,000 deliveries for Phillips 66, amounting to some 772m litres of fuel.
“Having worked with Phillips 66 since 2002, we know and understand the needs of the business and its customers,” says Wincanton’s director of energy, industrial and transport Jonathan Shortis. “This contract extension represents the next phase of our working relationship as their largest delivery partner in the UK.”
Wincanton has also boosted its EnergyLink operation with the appointment of David Hauff as general manager. EnergyLink was founded in 2016 with the aim of supporting the ground fuels, aviation and bitumen markets to achieve lower distribution costs, through a flexible and scalable delivery solution.
“It is an exciting time to be working in the fuel distribution market. Customers are demanding a more innovative approach to the services we provide and, as such, we are ensuring that we are at the forefront of driving this transformation across the fuel supply chain, whilst ensuring safety remains our top priority,” Hauff says. “The recent £5m investment that Wincanton has made in terms of assets is a clear indication of its aspiration to provide a best in class service.”
“We are seeing considerable demand in the market for cost-effective and flexible fuel delivery capability and EnergyLink is set up to meet this demand head on,” Shortis explains.
“EnergyLink is a fundamental part of Wincanton’s wider energy business and David’s
appointment demonstrates both our commitment and investment in this area.” www.wincanton.co.uk
Hoyer Petrolog has signed an agreement with World Fuel Services to provide aviation fuel transport services in Scotland. Under the deal, Hoyer will deliver fuel to airports in Edinburgh, Glasgow and Aberdeen, as well as Newcastle, south of the border, from the Grangemouth oil terminal. The contract, which starts on 1 May, will involve four vehicles and 13 drivers and will be worth £1.5m a year to Hoyer.
Elsewhere in the Hoyer Group, Dr Philip Nölling has taken over as CFO as from 1 February, replacing Gerd Peters. He has previously held the same post at the Hermes Logistik Gruppe and DPD.
“Not only are we convinced by the specialist know-how of Dr Nölling, we have also gained the impression that he understands the requirements that Hoyer as a family business asks of a CFO, and that he will identify with our values and exemplify them,” says Thomas Hoyer, chairman of the advisory board. www.hoyer-group.com
David Morrow has been appointed vicepresident of international business development at Heil Trailer International. He will focus on expanding Heil’s business in Asia, through its regional headquarters in Thailand. Morrow has been in the sector for more than 25 years, lately as regional sales manager for Wabash National Tank Trailer. He is returning to Heil, where he worked from 1993 to 2006 in sales, product management and technical service roles.
“We are excited to welcome David back to the Heil Trailer team and are confident he will help us continue to grow our international presence,” says Doug Chapple, CEO of Heil parent EnTrans International. “His role was previously held by John Snodgrass, who will be working closely with David throughout the transition. We thank John for his dedication to building the Heil Trailer brand internationally over the last 20+ years. He will remain with the company, serving key accounts.”
www.heiltrailer.com
THE CHEMICAL TANKER market has been going through another of its seemingly endless series of downturns in recent years. It has been ten years now since the financial crises of 2008/9 ripped up trade forecasts that had been confidently predicated on the promise of continued demand growth, driven not least by China and emerging markets in Asia.
The ability of any tanker sector to respond to a changing market is limited not least by the time it takes for market signals to have an influence on the size of the fleet. Contracting for new tonnage takes about two years to deliver capacity into the fleet (perhaps three years when shipyards are busy), by which time the market is likely to have changed. If the contracting owner is lucky, the market may have developed in a predictable way; if unlucky, and the market has taken a nosedive, difficult decisions may have to be made.
Such was the case after the 2008 crash: plenty of orders for new ships placed in the more confident mid-2000s were still to be delivered, yet demand had slumped. There were a number of high-profile casualties in the aftermath – not least Eitzen Chemical – and other tanker operators are still working through the impact of the necessary restructuring.
It has taken a decade for shipowners and analysts to begin to think about a recovery, but we are not there yet. Drewry Shipping Consultants says that global chemical trade volumes grew by just over 4 per cent in 2017, with tonne-mile seaborne trade increasing by nearly 5 per cent.
At the same time, the global chemicalcapable tanker fleet expanded by 3.9 per cent compared to 2016. On the face of things, that
would indicate a slight tightening in the market that could be expected to be reflected in higher earnings. However, the chemical tanker fleet is a slippery thing to pin down and, in light of a weak market for clean petroleum products (CPP), many product/chemical tankers swung into the easy chemicals and vegoil trades. Drewry estimates that there were 18 per cent more vessels operating in this sector in 2017 than 2016.
“The fleet trading in chemicals has expanded more than demand and will continue to so in 2018,” says Hu Qing, Drewry’s lead analyst for chemical shipping. “Apart from the fact that deliveries of new ships will outpace scrapping, it is also the case that the average size of the new vessels scheduled for delivery are larger than the vessels they are replacing. We therefore expect timecharter rates to come under increasing pressure.”
Increasing self-sufficiency in base chemicals in Asian countries is a definite threat to long-haul chemical trades, says Drewry. Overall tonnemile demand is predicted to increase by just 1.6 per cent this year on the back of dwindling long-haul growth.
Odfjell, one of the leading chemical tanker operators, has a slightly different view. Trade in
the core cargoes for chemical tankers –including vegoils and other non-chemical products – rose by an annual average of 3 per cent from 212m tonnes in 2012 to 240m tonnes in 2017, it says. Odfjell expects that growth to accelerate in the near term, averaging 4 per cent per year to hit 266m tonnes in 2020.
Of that 26m tonnes of new exports, the US and the Middle East are forecast to account for some 18m tonnes, with the new trades focusing on methanol (which could support further newbuilding of specialised tankers), ethylene glycol and xylenes, the latter stemming mainly from the Middle East.
Over the same historical period, Odfjell says, the total chemical tanker fleet grew by 33 per cent, from 66m dwt in 2012 to 88m dwt in 2017. Fleet growth has been particularly rapid in the past two years but has focused on IMO II/III product/chemical tankers designed to operate primarily in the CPP sector. The low cost of upgrading product tanker newbuildings to handle easy chemicals and vegoils has encouraged many of the major product tanker operators – several of which are now backed by investment funds – to do so, resulting in a sharp increase in the size of the swing fleet.
Odfjell expects fleet growth to be tempered over the near term, with average annual growth of 3.6 per cent in the core fleet and – importantly – only 1.9 per cent in the swing fleet. Both of those figures are below anticipated levels of demand growth, indicating a move towards a better balance between vessel supply and demand. Should the growth in trade volumes have a disproportionately large element of long-haul trade – as Odfjell thinks likely – then the move back towards balance will be faster, although Odfjell agrees with Drewry that China’s move towards self-sufficiency in some commodity products could impact this outlook.
In summary, Odfjell says it continues to believe that chemical tanker markets will improve towards the end of this year but that no significant improvement can be expected until 2019.
In a rational market faced with such conditions, it would be expected that all players would take similar decisions and their combined actions would put the market back towards balance. However, the chemical tanker market remains astonishingly fragmented, as HCB’s annual survey of chemical tanker fleets on the following three pages demonstrates.
It is not just that there are so many different players, they also have divergent interests. There are a handful of major specialised
players in the core market, many at least partly in private hands, often led by founding family members. There is another layer of specialised regional players, subject to a smaller selection of market forces, alongside an array of more local operators, many of which have links to domestic downstream interests.
All of these have different financial expectations, as do those (mostly newer) players in the market that are backed by institutional investors. Their behaviour at different points in the market cycle varies, as do their approaches to the investment cycle.
As a result, it seems, for every operator with an eye on leading consolidation in the market – as evidenced most recently by Team Tankers’ planned acquisition of Laurin Maritime and Anglo-Atlantic Steamship – there is another in the throes of divesting assets. The latest example of that is Nordic Shipping, which has over the past year passed on the Crystal Nordic joint venture to Essberger Tankers and offloaded its Herning Shipping subsidiary to a new venture headed by former chemical tanker stalwart Axel C Eitzen.
It is apparent that, however gloomy market conditions are for the market as a whole, there is always a buyer available, if the price is right and the potential returns sufficient to meet current financing demands. HCB
INCREASING SELFSUFFICIENCY IN BASE CHEMICALS IN ASIAN COUNTRIES IS A THREAT TO LONG-HAUL CHEMICAL TRADES
No of vessels Total
ABC Maritime 11 126,914 22
Ace Quantum Chemical Tankers 21 413,303 92
Ace Tankers 20 345,509 58 27 15
Akar Group 4 59,766
Akbasoglu/Trans Ka Tankers 7 50,156 49
43,600 9
12
Alliance Maritime 21 285,400 88 12 10
Älvtank 2 34,550 100 32,600 12
Amoretti Armatori 11 148,559 7 82
15
Antares Naviera 6 93,705 9
Ardmore Shipping 27 1,202,791 100 6
Asahi Tanker 8 111,844 10
Avin International 32 n/a Bahri 31 1,430,698 10
Bergshav 5 72,983 13
Berlian Laju Tanker 5 41,487 50 24 26 24 Bernhard Schulte 11 207,000 8 Beisktas Shipping 10 91,436 10 Blue Lines Shipping 5 243,682 10
Blystad Group 17 365,987 27 69 4 9
Borealis Maritime 14 150,300 11 42 17 30 12
Bryggen Shipping International 9 366,130 15 46 18 21 6
BW Chemical Tankers 11 221,551 79,600 7
Calisa 4 148,816 100 12
Capital Ship Management 27 1,212,615 100 9 Caribe Tankers 5 54,600 100 13 Carl Büttner 7 139,266 78 22 13 Champion Tankers 21 991,797 100 15 Chembulk Tankers 27 610,761 100 13 Chemfleet 22 203,198 yes yes 10 Chemmariner Shipping 5 33,471 14 Chemnav Shipmanagement 4 52,000 25 75 10 Chemship 12 173,173 100 12
Consolidated Marine 12 632,350 4 Crystal Nordic (d) 15 98,240 100 15
D’Alesio Group 7 83,009 100 10
D’Amico International Shipping 39 1,807,695 250,000 8
Daitoh Trading 11 168,480 100 9
De Poli Tankers 8 125,705 100 14
Dong-A Tanker 7 113,284 100 6 Düzgit Group 5 41,529 100 8 Eastern Pacific 6 119,469 100 10
Ektank 4 58,093 100 37,200 15
Elbana di Navigazione 6 48,926 59 41 14 Elcano 4 58,285 22 78 8 Empire Chemical Tankers 3 43,835 100 12
Essberger Tankers 22 135,737 94 6 15
Fairfield Chemical Carriers 29 624,998 100 225,600 6 Finaval 4 202,329 100 10 Finbeta 5 52,085 100 19
No
Flumar 3 88,623 42 58 14
Formosa Plastics Marine 16 712,016 11
Fortune Marine 12 95,551 80 20 14 Furetank Rederi 20 330,534 86 9 5 196,700 12 German Tanker Shipping 5 203,442 12 Gestioni Armatoriali 3 142,900 11
Gothia Tanker Alliance 35 440,785 91 4 5 217296 13 Gotland Tankers 6 291,276 9 Gulf Ship Management 5 229,834 9 Hamburger Lloyd 4 32,668 100 11
Hansa Tankers 27 609,414 100 6 Hassel Shipping (Stolt) 8 262,429 2
Heung-A Shipping 19 140,198 95 5 9 Histria Shipmanagement 11 451,000 10
Iino Chemical 40 1,316,884 65 35 11 Iver Ships 9 363,151 100 14 JX Shipping 23 263,866 100 11 Kaptanoglu Shipmanagement 6 69,651 29 71 9 Knutsen OAS Shipping 5 85,384 20 40 40 11 Koyo Kaiun 17 335,745 80 20 11 KSS Line 8 35,502 92 8 3,500 10
Latvian Shipping 16 778,156 100 11 Laurin Maritime 15 710,479 100 9 Lomar Shipping 7 84,715 100 12 Marida Tankers (Womar) 9 117,556 55 45 10 Marinvest 5 184,577 100 14 Marnavi 11 123,533 100 18 Medcare Shipping 2 80,000 12 Mediterranea di Navigazione 7 142,863 14 57 29 15 Millenia Maritime 7 302,000 100 10 MISC Bhd 13 385,817 8
Mitsubishi Chemical Logistics 24 61,963
MOL Chemical Tankers 55 1,384,148 100 10 Motia Cia di Nav 9 346,533 100 12
MT Maritime 20 448,586 100 113,300 10 Naviera Transoceánica 5 195,100 100 16 Navigazione Montanari 16 627,732 100 14 Navig8 Chemicals 81 2,526,218 11 28 49(a) 12 392,000 5 Navios Maritime Acquisition 19 903,724 7
Nordic Tankers 46 615,257 47 15 3 35 11 Norstar Shipping 13 175,730 11 North Sea Tankers 9 62,070 10 90 10 NYK Stolt Tankers 5 146,614 38,000 17
Ocean Tankers 4 66,594 100 6
Odfjell Tankers 84 2,519,724 80 516,057 11
Offen Tankers 29 1,213,400 9 Petro-Nav 3 19,218 100 8 Rigel Schiffahrts 12 234,630 92 8 10 Rigel Shipping Canada 3 31,533 100 25
Saehan Marine 6 62,805 1000 20 SCF Group 5 252,850 100 10 Sea Pioneer Shipping 4 201,500 100 7
SEA-Tankers 13 147,003 100 13
Seabulk Tankers 3 145,980 100 31
Seatrans Chemical Tankers 12 124,306 97 3(c) 16
Serromah Shipping 10 151,892 100 10 Shanghai Huitong Shipping 5 22,951 9
Shokuyu Tanker (b) 17 139,331 82 18 9
Sinbad Chartering 7 82,577 100 16
Sinochem-Stolt Tankers 9 36,049 10
Sirius Shipping 10 74,213 62 38 16,000 12
Stella Navigation 7 298,504 16
Stena Weco 49 1,921,863 98,800 6
Stolt-Nielsen Inter-Asia Service 3 11,541 17
Stolt-Nielsen Inter-Caribbean Services 5 53,775 13
Stolt-Nielsen Inter-Europe Service 16 83,744 18
Stolt NYK Asia-Pacific Service 13 158,367 10
Stolt Tankers Joint Service 61 2,067,406 14
Streamline Tankers 9 115,853 100 12
Swede Chem Tankers 4 24,150 49 32 13
Tarbit Shipping 3 55,950 89 13
Tatsumi Marine 17 274,291 100 9
Team Tankers International 36 639,941 22 58 18 2 12
Terntank Shipping 12 158,072 55 45 11
Thun Tankers 15 102,808 100 135,796 14
Torlak Shipping 3 21,107 100 10
Tradewind Tankers 3 28,600 100 10
Transmarine Tankers 3 19,138 100 17
Tune Chemical Tankers 17 214,794 52 48 10 Ultratank (b) 17 345,000 7
Uni-Tankers 17 150,444 29 71 11
Unibaltic 8 56,702 58 18
United Arab Chemical Carriers 24 1,228,259 76 9 15 10
Utkilen Shipping 19 213,929 99,300 17 Uyeno Transtech 11 13,712
Varkan Group 3 11,624 33 67 15
Viken Shipping 2 25,600 13
Waterfront Shipping 28 1,143,117 1 99 10 Westfal-Larsen 8 375,645 100 7
Womar Tanker Stainless Pool 23 461,134 100 79,600 6
Woolim Shipping 21 155,683
Yamane Shipping (b) 18 128,685 95 5 9
Yilmar Shipping 10 87,406 10
Zenith Ship Management 28 1,314,908 6
Zodiac Maritime 11 240,740 100 6
Interline coating
international fleet only
Teflon coating
now part of Essberger Tankers
TEAM TANKERS INTERNATIONAL has agreed to acquire all of the outstanding shares in both Laurin Shipping AB and AngloAtlantic Steamship Company Ltd for a total price of some $206m. The deal will expand Team Tankers’ chemical and product tanker fleet from 37 to 52 ships.
“We have communicated to the market the need for consolidation in the chemical tanker industry,” says Hans Feringa, CEO of Team Tankers. “As a first step towards further consolidation, we are pleased to announce this combination with Laurin Shipping and Anglo-Atlantic. Team Tankers will
benefit greatly from Laurin Shipping’s deep relationships, years of experience and AngloAtlantic’s contracted cargo coverage. We believe that the current level of asset prices in the shipping cycle provides a favourable point of entry for this investment.”
In addition to adding ten medium-range (MR) tankers to the Team Tankers owned fleet, the transactions are expected to deliver significant operational synergies.
“The combination of platforms is expected to result in overhead savings that will reduce the company’s administrative costs on a per ship day basis,” Team Tanker says. “Further, Team Tankers gains access to Laurin Shipping’s inhouse technical management expertise which should lead to enhanced operational control of the company’s fleet resulting in high-quality service to the company’s customers. On the commercial operating front, Laurin Shipping’s
dense Atlantic basin cargo network fits well with Team Tankers’ historical strength in trans-Pacific chemical transportation.”
In addition, the acquisition of Anglo-Atlantic “secures a critical mass of sophisticated MRs and a broad portfolio of contracts of affreightment which, combined with Team Tankers’ deep-sea chemical transportation expertise, will create a leading player in the long-haul transportation of chemical and clean petroleum product cargoes,” the company adds.
Mikael Laurin, CEO of Laurin Maritime, says: “We are excited to join forces with a leading listed chemical tanker operator. The combination of the three companies will create a focused and integrated entity with ample muscle to make the most of future market opportunities.”
The transactions are subject to the usual conditions but are expected to close by 6 April. The full list of assets includes:
• Laurin Shipping itself, with its current fleet of 15 MRs in the 45,000 dwt to 50,000 dwt range and its commercial and technical operation teams
• Anglo-Atlantic itself, with six owned, three bareboat-chartered and six time-chartered MR tankers
• The newbuilding Tosca, completed on 2 February, and
• The expected purchase in May 2018 of the three MRs currently under bareboat charter to Anglo-Atlantic with purchase options attached.
Financing for the deals is expected to come from Team Tankers’ cash on hand and a new $220m secured credit facility that will refinance existing debts of Laurin and Anglo-Atlantic.
Laurin Shipping is a privately owned company based in Sweden, engaged in the full-service operation of sophisticated MR tankers capable of handling clean petroleum products and chemicals.
Anglo-Atlantic is a privately owned company incorporated in the Isle of Man and active in the ownership and chartering of tankers. Its board of directors includes Ulrika Laurin, CEO of Laurin Shipping. HCB www.teamtankers.com www.laurinmaritime.com
of seven years, and is one of the younger fleets in the industry. With an average age of eight years, the addition of Higman’s towboats to Kirby’s horsepower profile will allow us to avoid significant future capital outlays for new towboats.
and workforce early retirement charges,” Grzebinski explains. “Earnings from operations were stronger than anticipated, primarily as a result of a significant increase in product and service demand across our entire distribution and services segment. In our marine transportation segment, continued high utilisation and demand in our inland market were partially offset by ongoing weakness in our coastal business.”
KIRBY CORPORATION HAS acquired Higman Marine and its affiliate companies for approximately $419m in cash. The acquisition, financed through additional borrowings, is expected to close in the first quarter of 2018.
Higman’s fleet consists of 159 inland tank barges with a total capacity of 4.8m barrels and 75 inland towboats. It operates along the Mississippi River system and Gulf Intracoastal Waterway, and carries petrochemicals, refined petroleum products, crude oil, natural gas condensate and black oil for global integrated oil companies.
“The acquisition of Higman and its young fleet of well-maintained inland tank barges and towboats is an excellent fit with Kirby’s operations,” says David Grzebinski, Kirby’s president and CEO. “Higman’s inland fleet of 30,000-barrel tank barges, approximately 80 per cent of which are clean and 20 per cent heated black oil vessels, has an average age
“Overall, as the inland market begins its recovery, the timing of the Higman acquisition is ideal as it will further upgrade our fleet and ultimately allow Kirby to emerge from the downturn larger, more efficient, and better able to serve our customers,” Grzebinski adds. “As the cycle improves, and we realise the benefits of integration efficiencies and synergies, this acquisition will improve the earnings potential for Kirby in the future.”
That market cycle is illustrated in Kirby Corp’s financial results for 2017. Revenues from the marine transportation division were down 10 per cent at $1.32bn, although consolidated earnings rose 25 per cent to $2.21bn on the back of strong demand for the group’s land-based and maritime distribution and services operations.
Kirby’s marine transportation division generated an operating income of $136.0m for the year, down down 47 per cent on the year, with its operating margin sliced from 17.5 per cent to 10.3 per cent.
“Our [fourth quarter] earnings were impacted by a sizeable one-time benefit related to US tax reform, as well as impairment, severance
Kirby reports higher demand for inland barge transport of petrochemicals and crude oil during the latter part of 2017, although demand for refined products transport was slightly weaker. Operations were challenged by weather and lock delays along the Gulf Intracoastal and also low water levels on the Ohio River. Market conditions in the coastal market are, though, weaker, with more barges moving from term contracts to the spot market.
“In summary, after a long couple of years, we are clearly starting to see improving market fundamentals in many of our businesses,” Grzebinski continues. “Throughout the downturn, Kirby has taken thoughtful and strategic steps to position itself to excel when our core markets rebound. In marine transportation, we have rationalised our cost structures, retired older equipment, and acquired excess industry capacity, ultimately giving Kirby the youngest and most efficient marine fleet in its history. We are excited about capitalising on these efforts as we move into 2018, while continuing to pursue acquisition opportunities as they arise, particularly in the inland marine transportation industry.” HCB kirbycorp.com
INLAND BARGING • AS THE MARKET FOR COASTAL TANKING CONTINUES TO WEAKEN, MARKET LEADER KIRBY CORP IS CONCENTRATING ON ITS INLAND FLEET AND HAS MADE A SIGNIFICANT ACQUISITION
WATERFRONT SHIPPING (WFS), a wholly owned subsidiary of leading methanol producer Methanex and a leading operator of dedicated methanol carriers, has ordered four additional 49,000-dwt tankers for delivery in 2019.
The contract, placed in collaboration with Marinvest and Skagerack Invest, Iino Kaiun Kaisha, Mitsui & Co and MYK, follows on from seven similar tankers delivered in 2016. Those ships featured the innovative ME-LGI two-stroke dual-fuel engines developed by MAN B&W, which use methanol as an alternative fuel to regular marine bunkers. The partners have again gone to MAN B&W for the latest newbuildings.
“Since this dual-fuel engine entered the market in 2016, its price has dropped considerably, which makes it an even more attractive propulsion option,” says René Sejer Laursen, promotion manager at MAN Diesel & Turbo. “Allied with its environmental credentials and convenience of use when employing methanol as a fuel, we are confident the ME-LGI will continue its promising progress.”
As a safe, biodegradable and cleanburning fuel, methanol is a promising alternative marine fuel that can meet new and existing environmental regulations from the International Maritime Organisation (IMO) that require vessels to decrease emissions of sulphur oxide and nitrogen oxides. By using methanol rather than conventional marine
fuel, the new tankers produce significantly fewer emissions than conventional vessels.
The four new vessels will be built in South Korea at Hyundai Mipo Dockyard, where several of the first generation of methanolfuelled vessels were built. WFS will charter the four vessels to replace older vessels and support growing demand for methanol around the world. Two of the vessels will be owned in a joint venture between WFS and Marinvest, one will be owned by NYK and the fourth will be owned in a joint venture between Iino and Mitsui & Co.
“We have been very pleased by the performance of the vessels delivered in 2016 and excited to be investing in another two,” says Patrik Mossberg, chairman of Marinvest. “Our overall focus in the development of the
dual-fuel system concept has been safety and engine reliability. We have found the technology for handling methanol is well developed and offers a safe dual-fuel solution for low-flashpoint liquid fuels.”
Ryuichi Osonoe, director and managing executive officer of Iino, adds: “With the growing demand for cleaner marine fuels to meet more stringent emission regulations, we’re seeking ways to reduce our environmental footprint. Investing in the next generation of fuels is one way we’ll continue to meet regulations while maintaining the efficiency of our operations.”
“It’s been great working with MAN and our shipping partners who are as committed as we are in advancing sustainable clean marine technology,” says Paul Hexter, president of Waterfront Shipping. “Our seven methanolfuelled vessels have been operating safely and reliably since 2016, and we expect these new vessels to benefit from ongoing technological advances that will continue to optimise performance and efficiency. We are proud to see 40 per cent of our fleet powered by methanol-fuel technology in the coming year.”
WFS currently operates the world’s largest oceangoing fleet of methanol carriers, with 28 modern tankers ranging from 3,000 dwt to 50,000 dwt. HCB www.wfs-cl.com www.marinvest.se www.corporate.man.eu
Herning Shipping has been sold to a newly established Norwegian shipping company, ANE Shipping, a partnership between Axel C Eitzen’s Camillo Eitzen & Co, Castel and Seahorse Maritime. Herning will be renamed Christiana Shipping and headquartered in Copenhagen with Axel C Eitzen as CEO.
“I am very pleased with the establishment of our new company and with the acquisition of a well-respected and competent team from Herning Shipping,” Eitzen says. “I look forward to further building on Herning Shipping’s strong relations with existing and potential customers, and to develop a solid foundation for future business.”
Herning Shipping operates a fleet of 19 chemical tankers, 12 of them owned, in the 3,000 to 11,000 dwt size range. It trades primarily in northern Europe and West Africa. Herning has been part of the Nordic Tankers group since 2012, following the acquisition of Nordic by investment company Triton.
The deal comes less than a month after Nordic Tankers and its partner Embarcadero Maritime sold the Crystal Nordic stainless steel chemical tanker operation to John T Essberger.
Crystal Nordic was formed in 2015 to combine Nordic Tankers’ stainless steel fleet with Crystal Pool and currently operates 14 tankers of between 4,000 dwt and 12,000 dwt, primarily in northern Europe. Essberger Tankers currently has a fleet of 23 tankers. The parties have agreed not to disclose the terms of the deal.
Per Sylvester Jensen, chairman of Crystal Nordic, says: “We are of the opinion that John T Essberger will be a very good owner of Crystal Nordic and thus enhance the service and flexibility offered to customers.”
www.nordictankers.com
Marnavi has established a new venture in which Simest, part of Cassa Depositi e Prestiti
(CDP), has taken a 45 per cent share. The move is aimed at investing in chemical parcel tankers to help upgrade and renew the Marnavi fleet. The plan is to have new parcel tankers built that will offer greater trading flexibility and fuel efficiency, while meeting the latest restrictions on environmental emissions.
“This will allow Marnavi to acquire a more competitive positioning on the international market, particularly in the Mediterranean and northern Europe,” Simest says.
Following the agreement, Marnavi is reported to have ordered a 15,000-dwt newbuilding at Wuchang Shipbuilding for 2019 delivery.
Simest and CDP support the international development of Italian businesses, using soft loans, export credit support and equity investments. www.marnavi.it
North Sea Tankers (NST) is adding five vessels to its fleet this year. Two have already arrived: the sisterships Habip Bayrak and Haci Fatma Ana, both 8,400-dwt chemical tankers featuring MarineLine-coated cargo tanks and built in 2010/2011.
Also due to join the fleet are Eviapetrol V (7,000 dwt, 2007, MarineLine-coated) and two stainless steel carriers: SC Chengdu and SC Chongquing (9,200 dwt, 2010/11).
“Our new capacity will further enable us to serve our COA partners with a wider range of alternatives, by adding to our developed trade structures,” the company says. The size and characteristics of the new ships makes them highly suitable for employment on NST’s established trades to and from the western Mediterranean. www.northseatankers.com
AVIC Dingheng has laid the keel for the first of two 7,999-dwt oil/chemical tankers ordered by Sirius Shipping in 2016. The Ice Class 1A tankers (below) are due for delivery later this year.
The Evolution-class ships have been designed specifically to meet customers’ demands for low-maintenance, fuel-efficient and high-performance tankers to operate in harsh weather conditions. On delivery, the first vessel will go on timecharter to Esso Norway. www.siriusshipping.eu
AIRSAFE TRANSPORT TRAINING PO Box 347 Cloverdale, WA 6985, Australia
T (+61 8) 9277 6968 www.airsafe.com.au
Dangerous Goods by Air –Acceptance
• May 2-4 – Melbourne
• May 9-11 – Sydney
• May 15-17 – Perth
• May 30-June 1 – Adelaide
Dangerous Goods by Air –Refresher
• May 1 – Melbourne
• May 8 – Sydney
• May 9 – Perth
• May 24 – Perth
• May 29 – Adelaide
• June 6 – Perth
AMSA Full Acceptance
• April 30 – Melbourne
• May 7 – Sydney
• May 28 – Adelaide
• June 11 – Brisbane
Dangerous Goods by Road
• May 22 – Perth
AUSTRALIAN FEDERATION OF INTERNATIONAL FORWARDERS
Westfield Office Tower, Suite 403, Level 3, 152 Bunnerong Road Eastgardens, NSW 2036 Australia
T (+61 2) 9314 3055 www.afif.asn.au
Dangerous Goods Acceptance (Air)
• May 8-10 – Brisbane
• May 8-10 – Sydney
• May 15-17 – Melbourne
• June 5-7 – Sydney
Dangerous Goods Recertification (Air)
• May 7 – Brisbane
• May 7 – Sydney
• May 14 – Melbourne
• June 4 – Sydney
Dangerous Goods Awareness (Air)
• May 24 – Melbourne
Dangerous Goods by Sea –
Full Acceptance
• April 30-May 1 – Sydney
• May 22-23 – Melbourne
• June 19-20 – Brisbane
Shipping Lithium Batteries by Air
• May 21 – Melbourne
• June 14 – Sydney
BARRY TRAINING SERVICES
Sully Moors Road Sully CF64 5RP, UK
T (+44 1446) 743 913 www.barrytrainingservices.co.uk
ADR – Initial
• May 21-25 – Barry
ADR – Refresher
• May 14-16 – Barry
CAMEON PO Box 17345 Edinburgh EH12 1DJ, UK
T (+44 131) 334 1929 www.cameon.com
Dangerous Goods Safety Adviser (DGSA)
• June 4-8 – Manchester
Dangerous Goods by Air
• April 16-18 – Manchester
Dangerous Goods by Air –Revalidation
• May 18 – Manchester
Dangerous Goods by Road and Sea
• May 15-17 – Manchester
Dangerous Goods by Road –Upgrade
• April 19 – Manchester
Dangerous Goods by Sea –Upgrade
• April 20 – Manchester
CLASS 7 LTD 9 Irk Vale Drive Chadderton Oldham OL1 2TW, UK
T (+44 161) 628 6677 www.class7.co.uk
RamMaster Level 1 – Foundation
• June 12 – Oldham
RamMaster Level 2 – Road Consignment and Transport
• June 13-14 – Oldham
RamMaster Level 2 – Rail Consignment & Transport
• June 26 – Oldham
RamMaster Level 2 – Radioactive Material Classification
• June 28 – Oldham
DANGEROUS GOODS ADVISORY COUNCIL 7501 Greenway Center Drive, Suite 760 Greenbelt, MD 20770, USA
T (+1 202) 289 4550 www.dgac.org Multi-Modal Transportation –Initial
• May 7-11 – Houston
• June 11-15 – Las Vegas Multi-Modal Transportation –Recurrent
• June 7-8 – Las Vegas
DANGEROUS GOODS COUNCIL PO Box 7325 York, PA 17404, USA
T (+1 717) 848 8840 www.hazshipper.com
49 CFR & International AirCertification
• May 7-9 – Baltimore
• May 21-23 – Raleigh
• June 11-13 – Cleveland
• July 16-18 – Houston
49 CFR – Certification
• May 7-8 – Baltimore
• May 21-22 – Raleigh
• June 11-12 – Cleveland
• July 16-17 – Houston
International Air – Recertification
• May 9 – Baltimore
• May 23 – Raleigh
• June 13 – Cleveland
• July 18 – Houston
DANGO TRAINING SERVICES 169 Affric Road
Glenrothes KY7 6XA, UK T (+44 1592) 748234 www.dangerousgoodstrainingdts. co.uk
Dangerous Goods by Air
• April 23-25 – Aberdeen
• May 7-9 – Aberdeen
• May 21-23 – Aberdeen
• June 4-6 – Aberdeen
Dangerous Goods by Sea
• April 19-20 – Aberdeen
• April 26-27 – Aberdeen
• May 10-11 – Aberdeen
• May 24-25 – Aberdeen
• June 7-8 – Aberdeen
DGI TRAINING CENTER
1060 El Camino Real, Suite B, Redwood City, CA 94063-1645, USA T (+1 650) 306 8450 www.dgitraining.com
IATA Initial Plus
• May 8-10 – Chicago
IATA Initial
May 8-9 – Chicago
June 6-7 – Denver
June 12-13 – San Francisco
June 20-21 – Los Angeles
IATA Recurrent
April 30 – Seattle
May 7 – Chicago
May 16 – Minneapolis
June 4 – Denver
June 11 – San Francisco
June 18 – Los Angeles
IMDG Recurrent
May 2 – San Antonio
May 2 – Seattle
May 18 – Minneapolis
July 18 – Atlanta
Ground Transportation (49 CFR) Initial
April 23-24 – Chicago
May 7-8 – San Antonio
May 21-22 – Seattle
June 25-26 – Orlando
Ground Transportation (49 CFR) Recurrent
May 1 – San Antonio
May 1 – Seattle
• May 17 – Minneapolis
• June 5 – Denver
• June 19 – Los Angeles
Multimodal Initial (49 CFR/IATA/IMDG)
• May 7-11 – San Antonio
• May 21-25 – Seattle
• June 25-29 – Orlando
Multimodal Recurrent (49 CFR/IATA/IMDG)
• April 30-May 2 – San Antonio
• April 30-May 2 – Seattle
• May 16-18 – Minneapolis
Ground/Air Shipping - Initial (49 CFR/IATA)
• June 6-8 – Denver
• June 20-22 – Los Angeles
Radioactive Materials (Multimodal)
• April 25-26 – Chicago
DGM TRAINING INSTITUTE
1813 Greens Road Houston, TX 77032, USA
T (+1 281) 821 0500 www.dgm-usa.com
IATA/ICAO Dangerous Goods by Air – Initial
• April 23-25 – Dallas
• May 7-9 – Atlanta
• May 7-9 – Houston
• June 4-6 – Houston
• June 11-13 – Atlanta
• June 18-21 – Miami
IMDG Code - Initial
• April 23-24 – Atlanta
• April 23-24 – Houston
• May 30-31 – Houston 49 CFR Dangerous Goods by Road – Initial
• May 2-3 – Houston
• May 21-22 – Atlanta
Transporting Batteries
• April 26 – Houston
• June 22 – Houston
ENGINEERING EQUIPMENT & MATERIALS USERS ASSOCIATION (EEMUA)
2nd floor, 16 Black Friars Lane London EC4V 6EB, UK
T (+44 20) 7488 0801
TankAssessor
• May 14-18 – Manchester
• June 4-8 – Antwerp
FREMANTLE TRAINING & TRANSPORT
Rathmore Road
Torquay, Devon TQ2 6NY, UK
T (+44 1803) 293344 www.fremantletraining.co.uk
ADR Driver Training
• May 14-18 – Bristol
• June 4-8 – Plymouth
ADR Driver Training – Tanks & Class 3 Refresher
• April 23-24 – Bristol
• April 25-26 – Plymouth
• June 25-26 – Bristol
GLOBAL TRANSPORT TRAINING
54 Norristown Road
Blue Bell, PA 19422, USA
T (+1 215) 283 0983 www.gttstraining.com
Multi-Modal - IATA/IMDG/DOT 49 CFR – Initial
• April 23-27 – Dallas
• April 30-May 4 – Cincinnati
• April 30-May 4 – Philadelphia
• May 7-11 – Chicago
• May 7-11 – Fairfax, VA
• May 14-18 – San Francisco
• May 14-18 – Portland, OR
• May 21-25 – Houston
• June 4-8 – Atlanta
• June 11-15 – Los Angeles
• June 18-22 – Newark
GULF CENTRE FOR AVIATION STUDIES (GCAS)
PO Box 94449
Abu Dhabi, UAE
T (+971 2) 494 2355 www.gcas.ae
IATA DGR - Category 6 – Initial
• April 22-29 – Abu Dhabi
• May 13-20 – Abu Dhabi
HAZARDOUS MATERIALS
COMPLIANCE
11380 NW 34th Street Doral, FL 33178, USA
T (+1 305) 471 0561 www.hazmatcom.com
Multimodal General Awareness
• April 25 – Miami
• May 16 – Miami
• June 20 – Miami
IATA Air Initial
• April 17-19 – Miami
• May 1-3 – Miami
• June 12-14 – Miami
IATA Air Recurrent
• April 24 – Miami
• May 15 – Miami
• June 19 – Miami
IMDG Ocean Initial
• May 9-10 – Miami
• June 6-7 – Miami
IMDG Ocean Recurrent
• April 26 – Miami
• May 17 – Miami
• June 21 – Miami
Lithium Batteries (IATA/IMDG)
• May 8 – Miami
• June 5 – Miami
HAZMAT TRAINING SCHOOL SINGAPORE
146A Changi Road
Singapore 419726
T (+65) 6542 5539
www.haz-mat-training.com
IATA Dangerous Goods Regulations (Initial)
• May 7-11 – Singapore
IATA Dangerous Goods Regulations (Recurrent)
• April 18-19 – Singapore
• May 10-11 – Singapore
IATA Dangerous Goods Regulations (Awareness)
• May 7 – Singapore
IMDG Code Dangerous Goods By Sea
• April 16-17 – Singapore
• June 26-27 – Singapore
Chemical Safety Awareness
• May 17 – Singapore
SCDF Hazmat Transport Driver Permit
• May 16 – Singapore
• June 25 – Singapore
INTERNATIONAL AIR TRANSPORT ASSOCIATION
800 Place Victoria, PO Box 113
Montreal H4Z 1M1 Quebec, Canada
T (+1 514) 874 0202
www.iata.org/training
Dangerous Goods Regulations (DGR) – Shippers and Packers –
Cat 1 and 2
• May 2-4 – Singapore
Dangerous Goods Regulations (DGR) – Initial, Category 6
• April 16-20 – Brussels
• May 6-10 – Amman
• May 7-11 – Miami
• June 4-8 – Singapore
• June 18-22 – Geneva
Dangerous Goods Regulations (DGR) – Recurrent, Category 6
• April 24-26 – Stockholm
• May 23-25 – Geneva
• May 30-June 1 – Singapore
• June 20-22 – Miami
Dangerous Goods Regulations (DGR) – Instructor Refresher
• May 2-4 – Geneva
• June 27-29 – Miami
Professional Skills for DGR
Instructors – Categories 1,2,3,6
• April 23-27 – Geneva
• June 11-15 – Miami
Instructional Techniques for DGR (for categories 4, 5, 7, 8, 9, 10, 11, 12)
• April 16-20 – Geneva
• May 14-18 – Miami
• June 18-22 – Singapore
DGR for Auditors and Inspectors
• June 25-29 – Geneva
Shipping Lithium Batteries by Air
• May 15-16 – Moscow
Infectious Substances Transport
• May 30-June 1 – Singapore
LION TECHNOLOGY
570 Lafayette Road Sparta, NJ 07871-3447, USA T (+1 888) 546 6511 www.lion.com
Multimodal Hazmat Shipper Certification (49 CFR/IATA/IMDG)
• April 24-27 – Kansas City
• May 1-4 – Chicago
• May 7-10 – St Louis
• June 5-8 – Cleveland
• June 5-8 – Houston
• June 11-14 – Pittsburgh
• June 11-14 – Dallas
• June 18-21 – Detroit
• June 19-22 – Cincinnati
Hazmat Ground Shipper Certification - Recurrent
• April 25 – Sparta, NJ
Managing Hazardous Waste in New York
• June 4 – Buffalo
• June 6 – Syracuse
• June 8 – White Plains
• June 11 – Rochester
• June 13 – Albany
• June 15 – Long Island
Industrial & Hazardous Waste in Texas
• May 4 – Dallas
• May 9 – Houston
Complete Environmental Regulations
• May 10-11 – Pittsburgh
OILSPILL RESPONSE TRAINING
Lower William Street Southampton SO14 5QE, UK
T (+44 23) 8033 1551 www.oilspillresponsetraining.com
Oil Spill Clearance –
On-Scene Commander (IMO Level 2)
• May 7-11 – Singapore
• June 18-22 – Southampton
On-Scene Commander – AsiaPacific (IMO Level 2)
• May 22-24 – Vietnam
• June 5-8 – Port Moresby Oil Spill Operator –First Responder
• May 2 - Southampton
ROADSAFE EUROPE
Unit 006, Solent Business Centre Millbrook Road West Southampton SO15 0HW, UK
T (+44 23) 8070 2576 www.roadsafeeurope.com
ADR Initial
• April 23-27 – Southampton
• May 21-25 – Southampton
• June 18-22 – Southampton
ADR Refresher
• April 30-May 2 – Southampton
• May 30-June 1 – Southampton
Dangerous Goods Safety Adviser
• June 4-8 – Southampton
Security and Emergency Response Training Center PO Box 11130 Pueblo, CO 81001, USA
T (+1 719) 584 0584 sertc.org
HazMat/WMD Technician for Surface Transportation
• June 4-15 – Pueblo
Tank Car Specialist
• May 21-25 – Pueblo
• June 18-22 – Pueblo Intermodal Specialist
• May 7-9 – Pueblo
• June 18-20 – Pueblo
Leadership & Management of Surface Transportation Incidents
• June 11-15 – Pueblo Highway Emergency Response Specialist
• April 23-27 – Pueblo
• April 30-May 4 – Pueblo
• May 14-18 – Pueblo
• June 11-15 – Pueblo
Tactical Hazardous Materials Operations for Surface Transportation
• April 16-20 – Pueblo Crude-by-Rail Response
• April 23-25 – Pueblo
• May 1-3 – Pueblo
• May 15-17 – Pueblo Transportation Container Loading and Unloading Emergency Response
• April 25-27 – Pueblo
• May 8-10 – Pueblo
UPS 55 Glenlake Parkway NW Atlanta, GA 30328, USA
T (+1 800) 634 5656 www.upshazmatseminars.com
49CFR & IATA Dangerous
Goods Seminar
• May 15-17 – Chicago
49CFR Dangerous Goods Seminar
• May 15-16 – Chicago
WARSASH MARITIME ACADEMY Newtown Road, Warsash Southampton SO31 9ZL, UK
T (+44 1489) 556216 www.warsashacademy.co.uk
Basic Oil and Chemical Tanker Cargo Operations
• May 14-15 – Southampton
• June 18-19 – Southampton
Advanced Oil Tanker Cargo Operations
• April 23-27 – Southampton
Basic Liquefied Gas Tanker Cargo Operations
• May 14-15 – Southampton
• June 18-19 – Southampton
Advanced Liquefied Gas Tanker Cargo Operations
• May 7-11 – Southampton
• June 11-15 – Southampton
Advanced Chemical Tanker Cargo Operations
• June 18-22 – Southampton
APRIL 10-12, MONTREUX
Conference on the end-to-end pharmaceutical supply chain logipharmaeu.wbresearch.com
APRIL 15-17, TORONTO
70th annual conference and exhibition of the National Tank Truck Carriers www.tanktruck.org/meetings/
APRIL 15-20, OTTAWA
18th conference of the Chief Inspectors of Explosives, alongside EPP Working Group of IGUS riskom.com.au/index.php/explosives/ international-conference
APRIL 16-19, BARCELONA
Sixth meeting on custody transfer and process metering efmws.eu
APRIL 18-19, LIVERPOOL
Annual exhibition for the fuel distribution sector in the UK and Ireland www.fpsshow.co.uk
APRIL 21-25, ORLANDO
Biannual meeting of the Society of Chemical Hazard Communication www.schc.org/meetings
APRIL 22-25, WESTON, FL
Annual forum and expo of the Council on Safe Transportation of Hazardous Articles www.costha.com
APRIL 24-26, BIRMINGHAM
Annual commercial vehicle exhibition cvshow.com/
APRIL 25-26, MUMBAI
Exhibition for the fine and speciality chemicals sectors, incorporating ChemLogistics India www.chemspecindia.com
China LNG & Gas International
APRIL 25-26, BEIJING
Fourth annual conference on LNG developments in China chinalngsummit.com/
Multimodal 2018
MAY 1-3, BIRMINGHAM
Eleventh annual exhibition for the supply chain management and logistics sectors www.multimodal.org.uk
GPCA Supply Chain Conference
MAY 8-10, DUBAI
10th annual meeting of logistics professionals in the Gulf Petrochemicals and Chemicals Association www.gpcasupplychain.com
FLNG Global
MAY 14-15, AMSTERDAM
13th annual meeting on floating LNG technologies finance.knect365.com/flng/
MAY 14-17, AMSTERDAM
24th annual conference on natural gas and LNG in Europe energy.knect365.com/flame-conference/
MAY 15-16, ROTTERDAM
Inaugural exhibition and networking event tankstorageconnect.com/
Hazards28
MAY 15-17, EDINBURGH
Conference and exhibition on best practice in chemical and process safety www.icheme.org/hazards28
UNITI Expo
MAY 15-17, STUTTGART
Third European convention for the retail petroleum sector www.uniti-expo.de
MAY 16-18, SHANGHAI
Eighth international exhibition for logistics,
telematics and transport www.transportlogistic-china.com
MAY 22-23, HOUSTON
Conference on opportunities in US LNG, LPG and ethane exports energy.knect365.com/gas-trading-shippingamericas/
MAY 22-24, AMSTERDAM
Conference on small-scale LNG applications www.lngfuelssummit.com
MAY 22-25, SAN ANTONIO
Annual conference on improving reliability in the petrochemical and refining industry www.AFPM.org
MAY 23-24, STRATFORD-UPON-AVON
11th annual conference for hazmat specialists the-ncec.com/en/emergency-response/ hazmat-event
MAY 31-JUNE 1, MONACO
Europe’s biggest event for the regional and global LPG sectors www.aegpl2018.com/
JUNE 4-6, NICE
Annual meeting of the European Association of Chemical Distributors www.fecc-congress.com
JUNE 6-7, DAVENTRY
33rd annual regulatory update conference www.dft.gov.uk/vca/dangerousgoods/dangerousgoods-seminar.asp
JUNE 11-13, HOUSTON
38th annual operating conference and trade show of the International Liquid Terminals Association www.ilta.org
Date Location Vehicle Type Substance Details Source
3/1/18 nr Lancaster, vacuum tanker waste oil Septic tank truck with waste gasoline and water exploded at salvage business, reportedly as it was thawing WSYX Ohio, US inside a building during cold weather; two people suffered burn injuries; tanker was used by Hazmat crew
5/1/18 Tarrant, rail tank car sulphuric Tank car with sulphuric acid was said to have “split in half” at CSX railyard; Birmingham Fire & Rescue WBMA Alabama, US acid attended scene but were told by CSX that they were not needed; CSX said no risk to public or waterways
9/1/18 Dai Loc, road tankers ethanol Fire broke out during loading of two road tankers at Dai Tan ethanol plant; series of explosions heard as fire SGGPO Quang Nam, Vietnam spread to alcohol store rooms; workers prevented fire from reaching bulk storage tank; under investigation
10/1/18 Mpigi, road tanker fuel Fuel tanker overturned trying to avoid head-on collision with truck carrying charcoal and bananas; both Xinhua Uganda vehicles were caught in explosion; traffic blocked for several hours; three people severely injured
12/1/18 Pori, truck sulphuric Truck overturned on major highway in western Finland, spilling “several hundred litres” of sulphuric acid; RSOE Finland acid highway closed for several hours until equipment arrived to salvage truck; driver slightly hurt
12/1/18 Medipally, road tankers fuel Two laden road tankers caught fire at repair shop in Hyderabad district; later emerged that the owner and Times of Telangana, India tanker drivers were pilfering fuel; 16 people injured, one dying later of burns; nearby buildings damaged India
13/1/18 Sarina, road tanker molasses Two brothers died while cleaning molasses tank at Vella Haulage; those who died were owners of the facility; ABC Qld, Australia last cargo believed to be ‘superflow’, a sugar cane by-product, and urea; WHSQ investigating
15/1/18 Magodo, road tanker LPG Massive fire broke out at Second Coming gas plant, reportedly after gas leaking from a tanker was ignited Channels Lagos, Nigeria by spark from exhaust of passing vehicle; at least two people believed to have died, others injured TV
15/1/18 Katearagi, road tanker fuel Road tanker and Hiace bus were involved in head-on collision on Bida-Minna road; crash led to fire, which This Day Niger, Nigeria destroyed both vehicles; bus driver and 15 passengers were trapped and died in fire
18/1/18 Salt Lake City, road tanker gasoline Double tank truck exploded on I-15, causing highway to be closed for hours; driver suspected brake fire led KUTV Utah, US to blast; no injuries reported; Utah Air National Guard attended with fire tenders, foam
19/1/18 Chicalim, road tanker ammonia Road tanker overturned on Vasco-Panji highway, leaking ammonia; some 300 nearby homes evacuated; India Goa. India two people needed hospital treatment; roads closed during response Today
20/1/18 Toktogul, road tanker gasoline Driver lost control of tanker on Bishkek-Osh road, crashing into Chychkan River; one killed, two hurt in RSOE Jalalabad, Kyrgyzstan accident; much of 38-tonne gasoline cargo leaked to river, causing extensive fish kill
22/1/18 Port Coquitlam, road tanker ethanol Tank truck with ethanol collided with rail engine in CP rail yard, causing rupture in cargo tank; spilling Canadian BC, Canada ethanol exploded, caught fire; fire was allowed to burn out; no injuries reported Press
23/1/18 Hubli, truck LPG Truck with 204 cylinders of Bharat Gas collided with another truck on highway; cylinders immediately Times of Karnataka, India exploded, preventing responders getting close enough to tackle blaze; driver, cleaner of LPG truck fled India
25/1/18 Imperial, truck paint Truck ran off road into ravine at hairpin turn on Old Lemay Ferry Road; load included some 4,000 gal My Leader Missouri, US (15,000 litres) oil-based paint in tins; some diesel leaked; paint had to be removed before rig was recovered Paper
27/1/18 Willingdon Island, road tanker ammonia 14 people were taken ill after ammonia leaked as tanker was being filled at Fertilizers & Chemicals The Kerala, India Travancore plant near Kochi; tanker was nearly full when leak started; responders quickly plugged leak Hindu
29/1/18 Kiamuringa, road tanker tar Tanker with hot tar being used in road construction caught fire, injuring two workers on the vehicle; others Nairobi Eastern, Kenya ran for safety; witnesses said fuel pipe burst and leaking tar ignited News
30/1/18 Quincy, freight train adipic acid Seven cars of eight-car CSX train derailed, some overturning and spilling adipic acid; spill initially thought to Tallahassee Florida, US be hazardous but later emerged that it was in solid form; witnesses said train was going too fast Democrat
30/1/18 Tulsa, truck peroxide Tractor-trailer with load of organic peroxide overturned on ramp from OK-11 to I-244, spilling some of its Tulsa Oklahoma, US cargo; all lanes of highway closed as a precaution; nearby businesses evacuated World
31/1/18 nr Truckee, road tanker fuel Tank truck was in collision with pickup on highway near crest of Sierra Nevada; both drivers killed in crash; AP California, US fuel caught fire, with high flames preventing responders attacking the fire; blaze did not spread
31/1/18 Monroe county, road tanker diesel Tank truck with “thousands of gallons” of diesel overturned on Highway 87, reportedly after driver fell asleep; WGXA Georgia, US spilling diesel reached nearby Rum Creek; EPA and state environmental agencies in attendance
2/2/18 nr Hayden, road tanker jet fuel Tank truck with 6,700 gal (25 m3) jet fuel rolled over as it turned off US 40 heading for Yampa Valley airport; Steamboat Colorado, US some 100 gal fuel spilled to culvert under highway; leak plugged, culvert dammed, driver cited Today
4/1/18 Gramercy, barge fuel oil Some 2,500 gal (9,500 litres) fuel oil spilled to Mississippi River during loading of barge at Apex Oil terminal; TimesLouisiana, US eight boats with skimmers, booms deployed; air quality being monitored Picayune
7/1/18 East China Sea Sanchi condensate Tanker (164,150 dwt, 2008), with 136,000 t condensate, caught fire after collision with bulker CF Crystal Reuters some 160 nm off Shanghai; fire burned for a week before wreck sank; all hands lost; beaches oiled in Japan
15/1/18 Suez Canal Ethane Opal ethane LEG tanker (87,000 m3, 2017), reportedly on maiden voyage from US to India, collided with two ferries, FleetMon grounded near Ismaila after losing steering in southbound passage; hull was breached; no report of cargo loss
17/1/18 Kandla, Genessa diesel Fire broke out aboard tanker (46,200 dwt, 2000), moored off Deendayal with 30,000 t diesel; all 26 crew ANI Gujarat, India were rescued, one dying later of injuries; ICG dealt with fire; cause of blaze not known
31/1/18 Pyongtaek, Passat
VLGC (83,000 m3, 2015) was involved in collision with anchored New Confidence at outer anchorage; Avance South Korea gas ship suffered hull damage but no reports of cargo loss; no injuries Gas
Date Location Plant type Substance Details Source
2/1/18 Edo state, pipeline natural gas Rupture, fire on NNPC-owned Escravos-Lagos gas line shut supplies to six power plants, Bloomberg Nigeria tripping national grid; half of country’s electricity supply down; cause of blaze unknown as yet
4/1/18 Kranskop, W Cape munitions sulphuric Rupture on pipe on storage tank with oleum at Rheinmetall Denel Munition plant leaked acid, causing cloud ENCA South Africa plant acid of noxious fumes; more than 300 people evacuated; spilt acid neutralised with lime; cloud dispersed
8/1/18 Saint John, pipeline butane Rupture on line carrying butane from Canaport LNG terminal to Irving Oil refinery caused evacuations, Global NB, Canada road closures; Irving cited unspecified “operational issue”; no injuries reported News
9/1/18 Baumgarten, gas terminal natural gas One worker was killed, 18 more injured by explosion at main gas hub; cause of blast not yet known; LNG Austria outage caused gas shortage across Europe as plant is main entry point for Russian supplies World
9/1/18 Bulan, diesel “Thousands of gallons” of diesel spilled to creek in Perry County; nature of accident unknown but WYMT Kentucky, US reports identified Trumbo Oil; no fish kill reported; nearest water intake a long way down river
11/1/18 Ejere, pipeline natural gas Second explosion within two weeks on Escravos-Lagos gas line, this time in Warri region; Vanguard Delta, Nigeria residents panicked, fearing Boko Haram attack; no indication as to cause or impact on power supplies
11/1/18 Montevideo, chemical grease Explosion at Lanco plant, which refines vegoils, reportedly during chemical reaction; one worker missing, El Uruguay plant 10 others injured; plant said to be lacking fire certificate; 80 tonnes grease in warehouse burned Observador
13/1/18 Termoli, chemical oil Fire broke out in large oil tank outside Fis chemical plant in industrial area; rapid response prevented Il Giornale Molise, Italy plant blaze from spreading to chemical storage area; no injuries reported del Molise
14/1/18 Geismar, pipeline natural gas Gas line between IMTT terminal and BASF plant ruptured, causing explosion, fire; roads closed during TimesLouisiana, US response; residents warned to avoid the area but no evacuations necessary Picayune
20/1/18 New Delhi, warehouse fireworks At least 17 people were killed when fire broke out in illegal firecracker storage unit in Bawana area; RSOE India some 50 workers were trapped in building; cause of the fire under investigation; owner arrested
20/1/18 Waterbury, factory hydraulic Some 6,000 gal (22.7 m3) hydraulic oil leaked from tank at Somers Thin Strip Co plant due to ball valve Fox61 Connecticut, US oil failure; sheen spotted on Naugatuck River; booms deployed to absorb leak
29/1/18 Mojkovac, armaments munitions Two people were badly hurt by explosion in Tara weapons factory; cause of blast not immediately clear; AP Montenegro factory Tara has suffered two other explosions since 2014
29/1/18 Cranston, electroplating chemicals Fire broke out in ProSys Finishing plant after end of business; fire crews knew there were chemicals WPRI Rhode I, US plant involved but lack of information hampered response; 14 firefighters needed hospital attention
30/1/18 nr White Lake, oilwell crude oil Nearly 1,300 gal (4,900 litres) crude oil spilled from Peak Operating oil production facility in wetlands area; AP Louisiana, US USCG monitoring cleanup; area is being used to repopulate whooping cranes
31/1/18 Indore, chemical chemicals Massive fire broke out at PC Petrochemical factory, cause unknown; several explosions heard as flames Times of MP, India plant spread to chemicals in store; responders unable to ascertain if anyone was hurt; building destroyed India
2/2/18 nr Hayden, road tanker jet fuel Tank truck with 6,700 gal (25 m3) jet fuel rolled over as it turned off US 40 heading for Yampa Valley airport; Steamboat Colorado, US some 100 gal fuel spilled to culvert under highway; leak plugged, culvert dammed, driver cited Today
Unless the container is physically opened and inspected by the shipping line or the authorities then it is impossible to know if the cargo is completely safe for transport.
Before the cargo is loaded on a ship, shipping lines will make extra checks to determine if any bookings could be undeclared DG. Hapag Lloyd, for instance, uses a tool called Cargo Patrol it has developed specifically to search bookings for possible issues.
If the cargo is declared as DG then shipping lines can use tools such as Hazcheck, from Exis Technologies, to check if the declared cargo complies with the International Maritime Dangerous Goods (IMDG) Code and other local rules and restrictions. Exis works with nine of the top ten container lines.
IT IS ESTIMATED that up to 10 per cent of all containers contain dangerous goods; that means that the new generation of ultra-large containerships can be carrying more than 1,000 boxes with dangerous goods (DG) on any given voyage.
Ocean carriers have to undertake a significant number of complex but critical checks on each DG consignment, for each leg of a vessel’s voyage.
• Most lines restrict or prohibit certain classes of DG (particularly explosives, radioactive materials and some organic peroxides in reefer containers) so the booking line needs to know if any partner line that may be involved in the voyage will accept the box or boxes.
• Detailed stowage requirements (such as on deck only, away from accommodation, or away from sources of heat) mean that suitable space is finite.
• Many ports and individual container terminals have strict rules on the classes of DG that can be loaded, unloaded or transhipped, or even present on board while the ship is in port. Significant disruption can ensue if the ‘wrong’ DG is aboard a ship. Shipping lines carry out these checks to ensure the cargo is safe to carry to protect the crew, vessels and the environment; safety of life and cargo and at sea is paramount.
Of course, the checks listed above assume that the shipper has properly declared the cargo as DG in the first place. In most cases shippers do try to do this but mistakes can be made due to lack of competence; unfortunately in some cases there is wilful mis-declaration to save costs or time. In other cases the cargo may have been properly declared, but when it comes to packing and stowing the cargo in the container the correct procedures may not have been used.
The final option is then to physically inspect selected bookings/containers before they are loaded to check if cargo is declared correctly and packed/stowed.
On average over the last ten years, fewer than 60,000 containers have been inspected each year by the reporting Competent Authorities. According to data from the TT Club, based on reports from four countries, deficiencies are on average found in about 15 per cent of containers.
Cargo surveyors who inspect containers prior to loading on behalf of container lines include, for example: Port Supervisor, which has averaged a 17 per cent rejection rate in the 25,000 containers it has inspected over the past five years; 12 per cent were serious enough to stop the shipment; and National Cargo Bureau (NCB), which has carried out more than 30,000 inspections in the last 12 months with a 9 per cent failure rate.
Most cases of non-compliance by these two bodies related to declared dangerous goods.
There are a variety of reasons for rejection: leaks, documentation, segregation, placarding/ marking - which is the most common problem - and packing/stowage issues.
With 10 million-plus DG containers shipped per annum (a broad estimate), then at a 9 per cent failure rate it is easy to see the size of the issue.
The inspection process takes time and costs money so not every declared DG container is inspected; indeed, not every container line has the same regime. Nevertheless, the number of inspections is increasing. It is becoming clear that it would be valuable to have a database to record and analyse the findings so that the data can be used to address issues with the appropriate parties.
Exis Technologies has been working with the two container inspection companies, NCB and Port Supervisor Rotterdam, to develop a new container inspection system in line with customer requirements. Earlier this year Exis announced the launch of Hazcheck Inspections, a web-based database and access portal for inspection companies to plan and enter details of cargo inspections completed on behalf of container or vessel operators.
The solution allows the container or vessel operator to log in with secure access and view or download inspection results and/or analytics. Consistent data is recorded and reported regardless of where and who records the inspection result. Non-confidential analytics data can be shared with partners and third parties to help influence policy with respect to the shipment of dangerous goods by sea.
Operators have the option to send cargo details to the inspection company so they can plan containers to select for inspection. Pre-entered planned data can be re-used when the inspections details are recorded.
The benefits of Hazcheck Inspections include reporting inspections into a common database, consistent reporting and analysis of data. Operators have the option to share non-confidential data with partners and third parties, such as the Cargo Incident Notification System (CINS).
Bob Ahlborn, NCB’s New York-based vice-president, liner activities, comments:
“We are happy to be working alongside Exis Technologies on this exciting project. This is a ground-breaking system which we are confident will improve the accuracy and timeliness of information that container inspection companies like NCB and shipping lines will be able to use to improve safety of life and cargo at sea”.
Founded in 1952, NCB is a non-profit organisation headquartered in New York and operating nationally across the US; its sole mission is promoting the safety of life and cargo at sea. NCB has been working closely with Exis Technologies to develop the Hazcheck Inspections specification, including
the user interface and the type of data that a DG container inspection needs to focus on and collect.
Port Supervisor BV started activities in 2011 as an independent company providing specialised services for the shipping, port logistics and insurance industries. Its core business includes risk services, hazardous cargo management and surveys involved in the handling, packing, storage, warehousing, transhipment and carriage of hazardous and general cargoes.
Port Supervisor gave important input to the Hazcheck Inspections specification relating to the pre-planning of inspections prior to cargo loading on vessels and how the planning links to the recording of the actual inspections.
John Verhoeckx, principal of Port Supervisor, points out: “Exis is not only an IT developer but also has an in-depth knowledge of the shipment of dangerous goods. Combined with Port Supervisor’s experience of container cargo inspection, we have been able to design a database that will help to improve the safe shipment of cargo.”
With two major companies on board the database has had a kick start but the next challenge is to encourage other similar companies to help build up a database of activity and DG declaration issues on a global basis. HCB www.hazcheck.com
“HAZCHECK INSPECTIONS ALLOWS THE CONTAINER OR VESSEL OWNER TO VIEW INSPECTION REPORTS AND ANALYTICS”
PNEUMATIC TRANSPORT SYSTEMS represent the heart of any granular bulk material handling system in many industries today. Being an efficient method of transporting granular material, such systems allow for quick movement of powders between processes, enabling companies to keep up with ever-growing demands on production.
However, such processes are not without their risks. When the product being processed is considered combustible and has an appreciable portion of fine material, the potential for an explosion increases dramatically. Fine powders with low minimum ignition energies (MIE) will regularly reach the minimum explosive concentration (MEC) along the conveying system and may be at risk of combustion by several
sources of ignition. One such ignition source is electrostatic discharge.
Pneumatic conveying systems have the ability to generate vast quantities of electrostatic charge via the movement of product through the plant equipment. The most common method of electrostatic charging on such process operations is tribo-electrification, which is simply the contact and separation of the powder with the walls of the processing equipment, the powder molecules itself or other factors that can cause charging, like surface contaminants.
In one recent incident a process operator working on a pneumatic conveying system heard a crackling noise when powdered
material was being transported between the classifier and the loading hopper.
During investigation of the noise, the operator came into contact with a section of the duct and received a significant static shock. Although the operator was unharmed, the severity of the incident warranted a full system shutdown to investigate how static charges had been able to accumulate on a particular section of ducting.
During the inspection the duct was examined and it was identified that the section of duct was not suitably grounded. When tested it was found the duct had a resistance path back to ground well in excess of 1011 Ω, exceeding the recommended resistance of less than 10 Ω for metal plant items in good contact with ground, as stated in IEC 60079-32-1:2013 Explosive atmospheres
Part 32-1: Electrostatic hazards, guidance.
Further inspection found that the unusually high resistance was a result of a single grounding clip that had not been properly installed after a clean-down operation.
Consequently, the piping between the two ducts acted as an isolated conductor resulting in the generation and subsequent accumulation of charge. The lack of continuity to ground meant that the charge could not be dissipated, allowing an excessively high voltage potential to develop on the duct that eventually discharged onto the operator.
Given the high rate of charge generation and spark discharge by a poorly fitted grounding clip, a review of grounding and bonding of all metallic parts was carried out. The inspection scrutinised the grounding and bonding integrity of all equipment units, all sections of ducts, bags and cages in the bag filters. As a result many deficiencies were found and swiftly rectified.
The nature of a powder processing operation means that the generation of static electricity is to be expected in all parts of the system because of the movement of the particles through equipment. Therefore, regular maintenance is required to stop material from clogging up the machinery. Regular disassembly for cleaning and maintenance can result
in bonding connections being missed or not made correctly when the equipment is reassembled. Vibration and corrosion may also degrade assembly connections.
Fortunately in this particular scenario, a larger scale incident was avoided by the luck of the operator. If the isolated ducting had not been found the outcome could have been very different. A static discharge in the right place through a combustible atmosphere along any section of ducting could have resulted in a significant ignition incident, putting the lives of employees and plant assets at risk.
The most effective way of ensuring that complex equipment used in powder processing operations cannot accumulate static electricity is to provide a dedicated static grounding solution that is capable of monitoring the ground connection to components at risk of isolation. Such a solution should also be able to prevent the flow of product and alert personnel to a potential hazard should a component lose its connection to ground. This is especially important if the ground connection point to the equipment is not readily visible or is not easily accessible, as was the case with the grounding clips mentioned in this scenario.
It is highly plausible that charge accumulation on an isolated ducting section had resulted from a misplaced grounding clip multiple times during previous operations without a visible electrostatic ignition incident ever occurring. Without a flammable/ combustible atmosphere being present in the spark gap when such a discharge occurs, frequent discharges could have gone unnoticed. This is a common feature of process operations that have suffered from the consequences of a fire or explosion caused by static electricity.
The first place to start is to determine why electrostatic charge was ‘permitted’ to accumulate on the section of ducting. In this case the loss of continuity resulted
in the section being electrically isolated from the general mass of ground. Had the section been connected to a true ground, charge would not have accumulated on its surface. Instead, excess electrostatic charges would simply have found their way to ground. In accordance with industry guidelines like NFPA 77 and IEC 60079-32-1, the isolated section (in this case the length of ducting) should have had continuity through to a verified ground with a resistance of 10 Ω or less.
In the example shown opposite, the system is configured to ground 7 sections of ducting (1 – 7) and a drum (8). Each channel is individually monitored back to ground to a resistance of less than 10 Ω and interlocked with the control equipment responsible for the flow of product. All monitored channels including the drum (1 – 8) need to have a path to ground (via bonding straps or grounding clamp) before the system will go permissive and allow the operation and flow of product to commence.
Powder processing equipment presents more of a challenge than standard applications as there are metal parts making up larger assemblies that can be electrically isolated from each other. The risk of removable sections becoming isolated conductors will occur if:
1. Each section does not have a sufficiently low path to ground to safely dissipate charge.
2. The correct reassembly of equipment after cleaning between operations and regular examination of bonding straps between the metal pipework and duct sections by plant personnel is not routinely carried out.
The Earth-Rite® MULTIPOINT II system solves these problems by ensuring that all parts of the equipment have continuity through to ground with a resistance connection of less than 10 Ω. The reliance on human intervention to perform regular resistance checks is alleviated due to the monitoring and interlocking capabilities of the Earth-Rite MULTIPOINT II.
If a loss of continuity between one of the ducting sections to the verified earth occurs, the system will go non-permissive and the operation will cease. The system only permits the product transfer process when the ground loop resistance of each utilised channel is less than 10 Ω, as recommended in the various international standards. The system has cCSAus, ATEX and IECEx approval for use in hazardous atmospheres and meets all current EC directives. HCB
* This article was prepared by James Grimshaw of Newson Gale; the company stresses that the incident referred to was referenced from a third-party source. Further information on the risks described and systems provided to resolve them can be found at www.newson-gale.co.uk
The UK’s COMAH Strategic Forum, a high-level industry/regulator group working to improve major accident hazard management and raise safety standards across industry, has published a document outlining how it achieves collaboration between trade bodies, authorities and union groups. Such collaboration has proved very useful in helping all sides to understand the issues behind recent highhazard incidents and to identify the changes that need to be made to operating practices, regulations and industry standards.
The Forum hopes that the document will provide a roadmap for other national and international bodies dealing with similar issues. The document can be downloaded from the Forum’s page on the Health & Safety Executive (HSE) website, webcommunities.hse.gov.uk/ connect.ti/COMAHSF.
The UK P&I Club has published a revised edition of its useful guidance document, Book it right, pack it tight. The revision reflects Amendment 38-16 of the IMDG Code and also condenses previous editions into one volume.
The document follows the process a dangerous goods consignment goes through, from classification, through booking, packing and loading on board the ship. The document can help all employees involved in the maritime supply chain to ensure that consignments arrive at the destination without injury to people, damage to property or harm to the environment. A downloadable version is available on the Club’s website. www.ukpandi.com/
The UK P&I Club has also highlighted an incident of liquid cargo contamination caused by tank washing while a tanker vessel was partially loaded. The expensive mistake happened when a hose carrying cleaning water was incorrectly
connected to a tank loaded with cargo due to be discharged at a subsequent port call.
The Club says that tank cleaning operations should always be carried out in strict compliance with documented shipboard procedures and guidelines and that a responsible officer should double-check the setting up of hoses, pipelines and valves involved in such operations.
The International Tank Container Organisation (ITCO) has launched a revised version of its tank container e-learning course, originally introduced at the end of 2016. The new version, developed like its predecessor by Exis Technologies, reflects feedback from customers during 2017.
“The ITCO e-learning programme provides measurable learning on the safe, competent and efficient use of tank containers, offering general awareness about the operation of portable tanks as prescribed by the International Maritime Dangerous Goods (IMDG) Code. In addition,
it gives users the knowledge to progress to function-specific training,” says Exis.
The e-learning course has been developed for use by all those involved in the sector, including shippers, tanker container operators and lessors, depot service providers, surveyors and carriers. It provides a firm grounding for those who need more advanced training, as well as general awareness for those who are not directly involved with tank containers.
The course consists of four modules: the tank container industry; components of the tank; regulations; and tank operations and depot services. Each module is divided into elements and there are tests at the end of each element to check that the student is developing a good understanding as the course progresses. Courses can also be set up on a course administrator system for in-house management of training on a local, regional or global basis.
Further information on the course, as well as details about purchasing and set-up options, can be found at www.tankcontainer-elearning.com.
The migration requirement follows a series of explosions at a container storage in the port of Tianjin in 2015 that caused 173 fatalities and injured hundreds more.
CHINA’S MINISTRY OF Industry and Information has clarified its plans to require enterprises handling hazardous chemicals (HC) across the country to migrate to designated industrial zones in accordance with the Guiding Proposal set out in December 2017. As is usual, implementation of the migration plan has been devolved to provincial and municipal authorities, which makes it difficult to track the exact status of the migration around the country.
The plan requires that all local government and district-levels design and outline a plan for migration. Individual plans must consist of specific goals, an implementation schedule, method of organisation, responsibilities sharing and budget. The plan must also detail the settlement of employees and any safe execution measures required for the migration, all within the one-month deadline set out by the national government.
The Guiding Proposal was based on three national surveys covering a total of 957 migration projects valued at a total of RMB 754bn ($120bn) at the end of 2016.
The size of the migration is staggering: in Jiangsu province alone there are 7,372 HC enterprises that will have to relocate. Authorities estimate that half of them will have moved by 2020. Jiangsu has identified 56 petrochemical industry zones, of which 24 are located in eight major cities on the provinces’ rivers.
In December 2017, Hubei and Shandong provinces and the Tianjin municipal government all laid out plans to migrate their HC enterprises to designated areas. Shandong province approved a management method that details the contents and conditions for authorising specialised chemical industrial zones. It stipulated the standards and regulations of examination and testing, with particular focus on the management of pesticides, paints, water treatment agents and biochemicals.
Local administrations in Anhui province have approved policies on property and land allocation in order to facilitate migration. Incoming companies will be required to use the land as authorised for at least five years after which it may be transferred to another business also involved in HC operations, including logistics providers.
According to statistics released by the Chemical Industrial Zone Committee, only 8 per cent of chemical industrial zones are classified as super-large or large. Some of these zones are at the beginning stages of construction, with others not far behind.
There is assistance available for those that will be affected by the migration requirement. The Federation of Petro Oils and Chemistry released a report on 13 December 2017, China Investment Promotion of Chemicals
Industry – A Guideline of Entry and Investment of Chemicals Industrial Zones Projects, which focuses on industrial policies, economic and technical specifications, energy saving, environmental analysis and safety evaluation.
This coming September, the migration plan will also be on the agenda at China International Hazardous Chemical Industry Expo (HCC China), China’s only dedicated trade exhibition and conference for hazardous chemicals manufacturers, packaging and storage, transport and the risk-control management community. To find out more about HCC China, go to http://hcchina.org/en/index.aspx. HCB
CHINA • THE TIANJIN EXPLOSION IN 2015
HIGHLIGHTED AN URGENT NEED TO MOVE HIGH-HAZARD FACILITIES TO SPECIFIC LOCATIONS; THAT WILL INVOLVE A MASSIVE MIGRATION IN A SHORT SPACE OF TIME
The representative of the International Union of Railways (UIC) was asked to provide the NHM codes for the substances that have been added in Table B at the next session.
THE RID COMMITTEE of Experts’ standing working group held its eighth session in Utrecht, the Netherlands, from 20 to 24 November 2017. Its main task was to review the amendments adopted by the earlier Joint Meeting of RID/ADR/ADN experts and to transpose them into the 2019 text of RID, which regulates the transport of dangerous goods by rail in Europe and neighbouring regions.
The meeting was attended by representatives of 22 RID Contracting Parties and Russia, which is a member state of the Intergovernmental Organisation for
International Carriage by Rail (OTIF) but does not apply RID. Also in attendance were the European Commission (EC), the EU Agency for Railways (ERA), the Organisation for Cooperation between Railways (OSJD) and four non-governmental organisations. The meeting was chaired by Caroline Bailleux (Belgium) with Colin Bonnet (Switzerland) as vice-chair.
The Secretariat had prepared a document listing the texts adopted by the Joint Meeting during 2016 and 2017 and by the standing working group at its November 2016 meeting.
A few errors were noticed and corrected.
A few matters remained to be finalised by the Joint Meeting and these were left in square brackets for the time being.
Russia pointed out that the introductory text of 6.2.4.1 refers to “standards”, whereas at the beginning of the table there is a reference to three European Community directives dating to 1984, which are presumably no longer applicable. Indeed, as the EC representative confirmed, these have been superseded by the Transportable Pressure Equipment Directive (TPED), 2010/35/EU. As the same text is found in ADR, Russia was asked to submit a proposal to the Joint Meeting.
The Secretariat presented another document, this containing the changes adopted by WP.15 at its session earlier in the month (HCB March 2018, page 78). In order to maintain modal harmonisation between RID and ADR, it would be necessary to adopt those relevant to rail transport into RID. This was done, with a few minor changes. The UIC representative said a proposal would be submitted for the next session to include a reference to the relevant EN standard in the footnote to 7.5.7.1. It was agreed that the transitional provision in 1.6.3.3.1 should be deleted.
RAIL • WITH MUCH OF THEIR WORK ALREADY DONE BY THE JOINT MEETING, RID’S STANDING WORKING GROUP GOT ON WITH SORTING OUT THE FINER DETAILS OF THE 2019 TEXT
A third document from the Secretariat contained proposed corrections to the 2017 edition of RID. Those substantive corrections applicable to the English text are:
• In 1.4.2.1.1(e), “empty uncleaned wagons and bulk containers” is replaced by “empty uncleaned wagons and containers for carriage in bulk”
• In Table A of Chapter 3.2, “V8” is deleted from column (16) against UN 1185; “368” is added in column (6) against UN 2908; “325” is inserted instead of “336” in column (6) against UN 2913; and “326” is inserted instead of “336” in column (6) against UN 3326
• In the last paragraph of 5.2.1.9.2, “or suitable contrasting background” is added after “black on white”
• In 5.4.3.4, on the third page of the ‘Instructions in writing according to RID’, the heading of column (2) is replaced with “Hazard characteristics” and that of column (3) is replaced with “Additional guidance”
• In 7.5.11, CW 31 is amended to read: Wagons or large containers in which substances of this Class have been carried as full loads, or small containers in which these substances have been carried, shall be checked, after unloading, for any residues of the load.
The International Union of Wagon Keepers (UIP) sought amendment of the text of 6.8.2.1.23 adopted for the 2019 edition. This change states that the competent authority or a body designated by the competent authority must verify and confirm the ability not only of the manufacturer but also of the maintenance or repair shop to perform welding operations. UIP felt that this should be extended to inspection bodies according to 6.8.2.4.5.
The standing working group did not share this concern, particularly as the amended text does not limit the role to the competent authority that issued the design type approval. Further, as 6.8.2.1.23 applies only to newbuild wagons, 6.8.2.4.5 is not relevant. The UIP representative was invited to consider the comments made and, if the issue is to be pursued, it should be taken to the informal working group on the testing and certification of tanks, due to meet in mid-December 2017.
Russia has a problem with the references to “ECE” regulations in the new special provision 392 as this abbreviation can also (in Russian translation) refer to the Eurasian Economic Commission, whose members are Armenia, Belarus, Kazakhstan, Kyrgyzstan and Russia. As ‘ECE Regulation’ is a standard term used in various places in the modal regulations and other legal provisions, Russia was asked to take the issue to the UN Sub-committee of Experts on the Transport of Dangerous Goods (TDG).
The Secretariat asked for the working group’s view on an apparent conflict between special provision 319, packing instruction P650 and special provision CE 14 for carriage in express parcels, relating to the carriage of UN 3373 biological substance, category B, packed with dry ice. In particular, P650 requires the primary and secondary packagings to maintain their integrity at the temperature at which the refrigerant is used, while CE 14 says that substances that have to be carried at a specific temperature cannot be forwarded as express parcels.
The standing working group was of the view that such substances may be moved as express parcels, as the coolant used is there to ensure biological integrity rather than to ensure safety during transport.
UIC returned to the issue of the provision of information to the infrastructure manager in cases involving the transport of dangerous goods in limited quantities. Depending on the arrangement of a particular consignment, the infrastructure manager may have no information at all. UIC proposed that a transport document should be provided when limited quantities are being carried, or that the UN numbers should be shown on the transport document.
The working group preferred the first option, especially as this would correspond to the provisions of the International Maritime Dangerous Goods (IMDG) Code and to the UN Model Regulations. However, some questioned why UIC had not considered the interests of consignors or the emergency services alongside those of carriers. In any »
event, the proposal should in the first instance be put before the Joint Meeting and UIC was advised to substantiate its argument that the requirements of 1.4.3.6 are not sufficient.
A paper from Sweden prompted discussion of two points: the placarding of wagons containing dangerous goods in limited quantities along with other dangerous goods; and the provisions for protective distances in 7.5.3, which are influenced by the placarding. Sweden felt that the current placarding requirements can mislead emergency responders, by not giving notice of all the hazards present, and that perhaps the approach in ADR, which uses a generic orange-coloured plate, would help.
The standing working group felt some sympathy with the idea but it was of the view that this was another matter that should go to the Joint Meeting first. As to amending the separation provisions, the working group admitted that the current system is not totally
satisfactory but felt that the more complicated system proposed by Sweden could lead to an increase in the number of shunting movements, hence increasing risk in the transport operation. A new proposal may be presented to the next session.
Italy presented the result of an informal working group that had met in Milan in late October 2017 to develop checklists for the filling and emptying of tank-wagons for the carriage of gases, analogous to those already in place for the carriage of liquids. Italy has been leading this topic ever since the fatal explosion of a tank wagon carrying LPG in Viareggio in June 2009.
The standing working group adopted the checklists and they will be made available on the OTIF website. Notes will be added to 1.4.3.3 (for fillers) and 1.4.3.7.1 (for unloaders) to direct dutyholders to the checklists.
The new checklists for gas tank-wagons in fact go further than those already in place for liquids and the working group agreed to expand those in a similar manner. The Netherlands will lead a working group, which was due to meet at the end of February 2018 to undertake the necessary work.
STANDARDS IS CAUSING PROBLEMS
“TARGETED CHECKS ON GAS TANK-WAGONS IN AUSTRIA IN 2015 AND 2016 FOUND SERIOUS DEFECTS IN THE CLOSING DEVICES OF MORE THAN 10 PER CENT OF THEM”
Austria reported that, during 2015 and 2016, targeted checks had been carried out on gas tank-wagons that may continue to be used under the transitional provisions 1.6.3.3.2 to 1.6.3.3.5. Serious defects had been found in the closing devices of more than 10 per cent of those wagons checked. Austria called for the duration of the transitional provisions in 1.6.3.3.4 and 1.6.3.3.5 to be limited to 31 December 2021.
The standing working group was of the opinion that the defects being found were a result of a failure of participants to comply with the safety obligations in Chapter 1.4 and that shortening the duration of the transitional provisions would not resolve the problem.
On the other hand, the working group felt that increasing the number of checks on gas tankwagons across all Contracting Parties would be useful. There also needs to be greater dialogue between states and market players. It invited all states and industry organisations to report at the next session on the measures being taken already, after which a decision will be taken as to how best to proceed.
The Secretariat proposed deletion of the hazard identification number ‘90’ from column (20) in Table A of Chapter 3.2 against UN 3166 and 3171. This is to avoid contradiction with special provision 666. The working group agreed.
The Secretariat had also noticed that, since 1.1.3.3(b) and (c) were deleted in the 2017 text, there is no longer a need to reference 1.1.3.3 in 1.1.3.8, so that reference too was deleted. UIC informed the standing working group that UIC leaflet 201, referenced in Chapter 1.11 of RID, was in the process of being converted into an ‘International Railway Solution’, IRS 20201. This will be submitted to the next session so that the reference can be updated.
UIC leaflet 471-3 O is also currently being converted. The content of point 5 in this leaflet, referenced in 1.4.2.2.1 of RID, is not being modified. However, the reference in that paragraph will need to be updated; again, this will be presented at the next session.
Poland queried whether wooden pallets may be used for the stowage of organic peroxides and whether there is a need to clarify special
provision CW 24/CV 24. There is also some difference in the allocation of those special provisions between ADR and RID. Delegates saw no problem in using wooden pallets – after all, if the dangerous goods are not on wooden pallets they may well be on the wooden floor of a container. However, it seemed that this was another issue that should be taken to the Joint Meeting, which could also look at the differences in ADR and RID.
Also remitted to the Joint Meeting were another Polish query, on the qualification of welding procedures, and a proposal from Russia to delete the derogation for the lithium battery label (model 9A) in 5.2.2.2.1.3.
Readers may recall that Russia had refused to adopt the 2017 amendments to RID into SMGS Annex 2, on the basis that they included references to EU directives and EN standards, over which neither Russia nor some other OSJD states (including China, Mongolia and Tajikistan) have any influence.
The Secretariat informed the standing working group that no progress had been made on this problem over the past year and it seemed inevitable that the same situation would be faced when the 2019 text of RID comes into force. Latvia reported that there have been problems in the Baltic states with the transport of engines, since they are carried as dangerous goods under RID 2017 but are exempt under SMGS Annex 2.
Russia now reported that it was prepared to adopt the 2017 text of RID, except for the references to EU directives and EN standards. Once official translations of the new standards are available, it will carry out analysis in conjunction with the Russian Federal Agency for Technical Regulation and Metrology (Rosstandart). The Russian representative also stated that, given the transcontinental nature of rail transport, it would be more appropriate to use globally applicable ISO standards in the text of SMGS Annex 2.
The OTIF Secretariat reminded the meeting that closer harmonisation between RID and SMGS Annex 2 was something that the UN Economic Commission for Europe’s (ECE) Inland Transport Committee had been seeking for some years; it was OTIF’s attention to »
bring the current unsatisfactory situation to the notice of the Committee.
Germany informed the standing working group of an incident involving a tank container carrying liquid waste that was found to be leaking from the bottom valve during a random inspection at Offenburg station in October 2016. Further investigation found that the information in the transport document and the marking on the tank container were incorrect, and there were other serious defects in the tank itself. Switzerland reported that similar defects had been found on a tank container belonging to the same Italian operator during an inspection in Basel.
Both representatives stressed that no new provisions were needed but that the incidents highlighted the need to ensure that existing provisions are being observed.
The Netherlands reported on an incident at the Kijfhoek marshalling yard near Zwijndrecht in January 2011, when a tank wagon with ethanol caught fire. Information needed by the emergency services concerning the contents of other nearby tank wagons was not immediately available and it only emerged later that there were some empty, uncleaned LPG tank wagons in close proximity.
An investigation was undertaken into the registration of dangerous goods wagons at the marshalling yard, which found that accurate information is regularly unavailable. ProRail, the Dutch infrastructure manager, is now applying new technologies to automatically track freight wagons. The Belgian representative reported that a similar system is now in use in the country.
Belgium also notified the standing working group of an incident in Antwerp during hump shunting. One tank wagon with isobutane (UN 1055) had been severely damaged as a result of the buffers over-riding, although there were no leaks.
Another incident reported by the Netherlands involved two tank-wagons carrying 1,2-dichloropropane (UN 1279) last October; leaks had been discovered, caused by rust particles in the valve and damage to the ball valve and Teflon seals. This seemed to be a problem that could happen at any time but, it was hoped, the new checklists for gas tank-wagons could help resolve it.
The representative of Switzerland discussed an issue that has become a problem for shippers and carriers: the additional riskreduction measures imposed in the country on
rail shipments of chlorine. The presentation explained that the measures, contained in Common Declaration II, had been agreed by the chemical industry, the Swiss Federal Railways (SBB), the Association of Freight Carriers, the Federal Office of Transport and the Federal Office for the Environment, and so have broad support within the country.
The measures include the use of tankwagons with enhanced safety features, speed and route restrictions, and greater oversight by the authorities. In the future, a design study will be undertaken with a view to developing a new generation of chlorine tank-wagons and it is possible that funding will be arranged to enable the production of chlorine locally and obviate the need to transport it in large volumes.
UIC noted that, while these measures are voluntary and relate to local interests, they can effectively be imposed on foreign suppliers. UIC felt that the measures should be notified in accordance with Chapter 1.9. The ERA representative said that the provisions of RID should guarantee safe transport and, in principle at least, additional measures should not be necessary. If the Swiss government feels that RID does not fully address safety in the transport of chlorine, then this should be put to the standing working group. If the safety of chlorine transport were to be called into question, then the same could apply to other very dangerous substances.
The representative of the Netherlands said that, in that country, the entire supply chain is taken into account; the aim is to avoid transport as much as possible by manufacturing chlorine near the point of use. Indeed, the European Chemical Industry Council (Cefic) representative reported that the Dutch government has made funds available to allow industry to build chlorine production plants, although he said that the level of demand in Switzerland is probably too low to make this a viable option.
Overall, the mood of the standing working group was that national variations from the
provisions of RID are to be avoided wherever possible. On a similar topic, UIC presented studies that the body has undertaken on national requirements that apply in addition to RID. This work is continuing and will be communicated to the standing working group. ERA reminded the meeting that the definition of ‘national rule’ is very clear and that EU member states must inform the European Commission of any such rules. ERA felt that UIC presentation may be misleading, as some of the variations noted do not meet that definition. However, it was agreed that reducing national rules is a priority within the EU.
Switzerland provided information on a new 40-foot tank container developed by BASF and the Belgian tank container manufacturer van Hool (HCB June 2017, page 46). These tank containers have a capacity of up to 73,500 litres and a payload of 66 tonnes. The load capacity is therefore equivalent to two conventional tank-containers or one bogie tank-wagon. The representative of Switzerland raised various questions in connection with the consequences of this new technological development for safety in the carriage of dangerous goods.
It so happened that Dr Bieker from BASF was at the meeting as part of the Cefic delegation. He explained that the tank containers in question have tank codes L4BH and L4DH; 50 are currently being built with a calculation pressure of 10 bar. The will be used for substances for which a calculation pressure of 4 bar is prescribed. The new tankcontainers are being carried on new wagons, of which around 150 are planned; they will be fitted with crash-buffers and devices to protect against the over-riding of buffers. They are not fitted with surge plates as they will be carried either filled to at least 80 per cent or empty and uncleaned.
Within the context of Responsible Care, BASF is applying special provisions TE 22 and TE 25 to carriage in these tank-containers. The Austrian representative felt that was all well and good but that it cannot be assumed that other users would be so assiduous. In addition, both Germany and UIP noted that there has been a lot of market interest in
these new tanks and it would be a good idea to clarify the legal position as soon as possible.
The standing working group agreed to hold detailed technical discussions at the working group on tank and vehicle technology, due to take place at the end of January in Hamburg. Part of those discussions would be a comparison of the current provisions applicable to tank-containers and tank-wagons. It might prove desirable to draw up a list of questions to be put before the Joint Meeting.
The ERA representative said that a risk analysis would have to be carried out before any of the measures so far applied on a voluntary basis by BASF were included in the text of RID.
In its new regular slot, ERA had been invited to give an update on developments. Of particular interest was the work on derailment detectors, after the first edition of new ERA guidelines had been presented at the previous session of the standing working group. The European Commission had asked ERA to give priority to developing the necessary specifications and gave it a 2020 date for the work. This drew some criticism from the standing working group, with the Swiss representative reminding the working group that the RIC Committee of Experts’ working group on derailment detection had planned that this work would be carried out in 2017/18.
ERA explained that its activities are determined by the European Commission and that it had been asked to give priority to activities necessary for the implementation of the fourth Railway package. On the upside, the request did clearly indicate the need to work on derailment detection.
The ninth session of the RID standing working group will take place in Berne, Switzerland from 28 to 30 May 2018; the RID Committee of Experts will meet at the end of that session to approve the amendments that will appear in the 2019 edition of RID. HCB will provide a list of those amendments once they have been finalised.
The tenth session of the standing working group will take place in Poland in the week beginning 19 November 2018. HCB
THOSE RESPONSIBLE FOR dangerous goods (DG) and hazardous materials (hazmat) compliance recognise the inherent business value in investing in resources, technology and training that support compliance and enable them to do their jobs more efficiently and effectively. They also recognise that having the tools necessary to ensure compliance (and to do so efficiently) is more critical than ever as the number of dangerous items continues to grow and shipping regulations become increasingly complex.
Unfortunately, that view is not always shared by executive leadership within an organisation – which is demonstrated by the level of investment (or lack thereof) in resource allocation, budget ownership, infrastructure and training.
While some DG professionals feel they have adequate tools in place, the majority do not believe their existing infrastructure and training programmes have the ability to quickly adapt to instruction and process changes across their supply chain. This sentiment was evident in Labelmaster and HCB’s 2017 Global Dangerous Goods Confidence Outlook, conducted to gain insights from DG pros around the world. Survey results showed that there is a general lack of confidence in their organisations’ ability to meet
changing compliance mandates, with the key barriers being:
• Continued reliance on manual processes: Despite the latest technology innovations, many shippers still rely on manual processes to handle DG compliance. In fact, more than one-quarter of survey respondents are still doing everything manually – including searching through regulatory publications for guidance on packaging, labels, marks and documentation, as well as manually maintaining classifications for products and parts that qualify as hazmat.
• Resource reallocation: As companies look to cut costs and gain resource efficiency, many seem to identify DG compliance as one area where roles can be combined in order to save money. In fact, 39 per cent of survey respondents believed their increased compliance responsibility is due to cost-cutting measures. Additionally, 56 per cent have or expect the role of DG compliance to be combined with other roles within their organisation.
• Insufficient infrastructure and training: 33 per cent of those surveyed were not confident that their current infrastructure and training can adapt to the changing needs of the business. This is in part due to the fact that many organisations view training as a ‘necessary evil’ and are simply doing just enough to comply with applicable training regulations. In fact, nearly half of those surveyed said their training is conducted solely to meet regulatory requirements. Likewise, 48 per cent said they DO NOT believe their current training regimen adds real business value.
• Lack of awareness among leadership: There remains a real lack of awareness among leadership – not only regarding what those responsible for DG compliance actually do, but also about how a forwardthinking hazmat shipping function can drive business growth. Case in point: more than one third of all survey respondents agreed that their supervisors are unaware of exactly what they do.
Asking for additional resources when you may not even be on the executive leadership’s radar is difficult to say the least, but it is important
DANGEROUS GOODS PROFESSIONALS NEED TO SHOUT ABOUT WHAT THEY DO - WHICH IS TO BOTH SAVE AND MAKE THEIR COMPANY MONEY
in order to be able to establish a true culture of compliance throughout an organisation. Those responsible for DG compliance need to elevate the conversation with executive leadership and make a real business case for why resources, compliance technology and advanced training are not only necessary but critical to the organisation. But how is that done?
The first step is to recognise (and define) the true financial impact of a safe and compliant organisation – going well beyond simply the fear of a fine.
Corporate leadership cares about profitability and growth. That’s why it is critical to connect DG compliance to revenue, profitability and operational costs. Demonstrate how better management of the DG shipping process can improve operational efficiency and reduce the chances of stopped shipments, which in turn can lead to a faster supply chain, improved customer satisfaction, a competitive advantage, and ultimately drive more revenue. But just as important as showing the positive financial impact of compliance is showing the negative impact of non-compliance, which includes fines or, in the event of disaster, damage liability, increased insurance costs and more.
Try this: if your supervisor granted your wish and increased your operating budget by 25 per cent, what would you be able to do for the company?
• Reduce the cost to process a DG shipment
• Reduce the time it takes to manually record and track DG shipments
• Accelerate the time it takes to process a DG shipment from order to final delivery
• Reduce the time it takes to research the latest regulations for a specific shipment
• Acquire new customers faster with increased DG awareness among the sales organisation
• Reduce insurance costs tied to hazmat shipments
• Add revenue by getting items through the supply chain (and to end users) faster
• Reduce the costs of onboarding a new customer who ships DG
• Reduce fines, penalties and researching costs related to stopped shipments
• Increase awareness and consistency of DG
process, rules and policies
• Reduce the cost of DG training records and documentation tracking
• Better manage and stay up-to-date on carrier variations
• Better manage employee DG training records and documentation
• Reduce training cost per person.
The cost of a stopped shipment is more than just a fine. When a hazmat shipment is stopped for failing to meet shipping regulations (whether it is due to incorrect packaging and shipping papers, wrong markings and labels, or some other mistake), it ends up stuck in customs, on the tarmac, or at a port until a way can be found to make it compliant. These mistakes cost businesses millions of dollars in fees, expenses and lost revenue. Additionally, stopped shipments can cause late customer deliveries, which can lead to additional fines and penalties from customers themselves, and can permanently damage customer relationships.
While DG pros know that non-compliance can lead to more than just a fine, company leadership may not. Shipping hazardous goods is a high-risk business and has the potential to impact public safety and, as a result, brand equity. Show leadership what is actually at stake, including potential brand damage, if the necessary steps to ensure the safe, compliant movement of your goods are not taken. And if a company isn’t easy to work with when it comes to handling DG, customers will likely find a company that is.
By making hazmat compliance a priority and investing in forward-thinking technology, shippers can be confident that their operations teams, suppliers, distributors and partners are all fully compliant with the latest rules and regulations and can better position their companies for success. DG pros know this, but it needs to be clearly communicated to corporate leadership in a way that they can understand and that appeals to their priorities for the business.
Consider what data and proof points would help them truly see that DG compliance
equates to so much more than the mere cost of doing business or an avoidance of fines. Show them how compliance can ultimately impact whether the organisation experiences delayed shipments that negatively impact customer service and brand equity. By making a real business case, DG pros can better position themselves to get the resources, advanced technology and training they need to effectively do their jobs – and ultimately improve the business. HCB
*Pia Jala is vice-president of operations at Labelmaster; more information on Labelmaster’s work can be found at www.labelmaster.com.
Labelmaster has once again teamed up with HCB and has brought IATA on board as well, to carry out another survey of DG professionals; survey forms will be circulated soon – make sure your voice is heard by taking part.
CHANGE BRINGS CHALLENGE
Organisation (ICAO) Technical Instructions for the Safe Transportation of Dangerous Goods by Air are amended to review and include the changes in each revision of the UN Model Regulations. The European Agreement Concerning the International Carriage of Dangerous Goods by Road (ADR) also generally adopts the UN amendments. All countries are encouraged to use the current revision of the UN Model Regulations as the harmonised regulatory guideline for developing countryspecific domestic regulations for the transport of dangerous goods.
THE EXPLOSION OF e-commerce shipments and rapid changes in distribution systems make it more and more important for the regulators to be aware of those system changes and what they mean to the continuing efficacy of the dangerous goods transportation regulations. The e-commerce evolution also means that global companies make more diverse ground shipments within hundreds of countries with access to on-line acquirement of a myriad of products.
Transportation professionals are well aware of the impact of an uninterrupted and consistent global supply chain as a critical component of competition within the global
marketplace. Harmonisation is a key to enhanced regulatory compliance and effective risk minimisation in all modes of transport through all geographies.
The introduction of new products resulting from scientific innovation and consumer demand, such as energy storage systems, revolutionary vehicle design and production, as well as alternative fuels, have resulted in amendments within the UN Model Regulations, including the introduction of numerous new UN identification numbers and recognised proper shipping names. The modal regulations codified in the International Maritime Dangerous Goods (IMDG) Code and the International Civil Aviation
In 2017, Canada updated its domestic transport regulations to align with the 19th edition of the UN Model Regulations. Previously it had used the 12th revised edition – a fourteen-year leap. A nice feature that was also incorporated was the ‘dynamic’ or ambulatory reference. This allows for the use of UN numbers and proper shipping names that may have been adopted in international regulations but may not have been formally adopted by Canada.
In 2017, Brazil also moved from the 12th edition of the UN regulations to the 19th edition and it looks as if Argentina might also be considering significant updates.
Following the Tianjin disaster in China, it was discovered that national regulations for ground transport did not align with the UN Model Regulations; in particular, limited quantity shipments were not recognised. This is currently in the process of being changed. In addition, Australia is currently reviewing its ground transport regulations.
Competent authorities continue to review and modify approvals and permits and ask industry to provide data to justify regulatory relief or alternative packaging. With the rapid advance of technology it becomes more and more difficult for regulators to keep informed of changes and for industry to understand what type of data to provide and when. The importance of representative trade organisations in this process cannot be overstated.
In the US, the Pipeline and Hazardous Materials Safety Administration (PHMSA), an agency of the US Department of Transportation, is responsible for regulating transportation by all modes and the Hazardous Materials Regulations (HMR) appear in Title 49 of the Code of Federal Regulations. The HMR are regularly updated, through the established proposal and comment process, to take account of technical developments and to maintain, where possible, international harmonisation.
However, the current US Administration set out in a Presidential Executive Order a restriction that means that any proposed new regulation must result in the rescinding of two existing regulations. While this provision might be beneficial in some aspects of governmental control, it is more difficult to apply to hazardous materials transportation, where the regulations are primarily related to safety.
Thus, while PHMSA is moving towards its long-time goal of international harmonisation,
it is carefully examining the application of the Executive Order. The Council on Safe Transportation of Hazardous Articles (COSTHA) has been working closely with PHMSA to provide positive comments on recent proposals to incorporate the latest amendments in the UN Model Regulations into the next revision of 49 CFR to ensure ongoing harmonisation.
With all of the changes outline above, collaboration is increasingly important. COSTHA, the Institute of Manufacturers of Explosives (IME) and the Sporting Arms and Ammunition Manufacturers’ Institute (SAAMI) have formed an Explosives Council and are working with PHMSA on some critical issues.
COSTHA is working with regulators from several countries and looks forward to hearing from Brazil, China and the UK at its annual forum, scheduled for April 22 to 25 in Weston, Florida. In addition, it looks forward to seeing proposed rulemakings from PHMSA to incorporate the round of globally harmonised changes from the UN Model Regulations and hearing from PHMSA leadership about upcoming initiatives.
COSTHA’s ultimate goal is ‘Overcoming Global Challenges’ – the theme of this year’s annual forum - and promoting international, intermodal, and domestic dangerous goods transportation safety while enhancing the efficient operations of the global supply chain, so vital to the business interests of its members. HCB
This article was prepared by John V Currie, COSTHA administrator and chief technical officer. More information on COSTHA’s Annual Forum can be found at www.costha.com.
Here on the Back Page we are well known for our juvenile sense of humour, so when a story came through from Brazil in January that a fire had destroyed a storage area full of chemical toilets our antennae twitched.
According to the local fire services, fire broke out in a storage tank at the depot in Retiro, Salvador. We are not quite sure what was in the storage tank, nor do we wish to think about it too long. But the fire spread and destroyed around 500 “pieces of equipment” and three trucks. Fire crews concentrated on preventing the blaze from spreading to the biscuit factory next door, as they needed something to go with their coffee when they got back to the fire station. Well, we assume so.
But the story is a salutary reminder that a chemical toilet does, indeed, contain chemicals. And clearly they are flammable. Ponder on that next time you’re queuing to use one.
More news has come to us about the dangers inherent in cleaning products – which is why the Back Page lives among filth. In fact, two stories in two days from the US in January contained remarkable similarities.
In the first incident, two people evacuated their home in Cornville, Arizona after pouring an acid-based drain cleaner down the drain. Evidently it reacted with something else in the drain, generating a cloud of toxic fumes that filled the house. The product in question is readily available over the counter and the two residents said they had used it before.
The very next day, one man was killed and a woman hospitalised after attempting to clear a drain in Grand Tower, Illinois. The pair
used a mixture of bleach and a commercial drain cleaner, which reacted even before the mixture could be poured down the drain.
And the moral is: if your drain is blocked, call a professional.
The press in the US regularly carries stories of evacuations and emergency response activities caused by the presence of white powder, the latest cropping up in Chattanooga, Tennessee at the end of February.
The Chattanooga Area Food bank was evacuated after three “suspicious packages” containing a white, powdery substance were received. CEO Gina Crumbliss picks up the story: “When I opened one of them, a white powder spilled out and I saw a box labelled ‘baking soda’. We immediately implemented our internal safety and security protocol and called the Chattanooga Police Department.”
Police and fire crews conducted a full evacuation and investigation. All three packets were tested; hazmat crews determined that the contents of each was indeed 99.9 per cent sodium bicarbonate, aka baking soda.
As it happens, here on the Back Page baking soda is the only cleaning product we trust. It gets caked-on grease off pans in a jiffy and does a good job of keeping the oven clean. You can also clean your teeth with it, and it’s the best anti-indigestion remedy going. Come to think of it, it’s probably the least dangerous chemical we keep under the sink.
But it is a chemical, and we have to be on our guard against chemicals. The same day as the food bank was evacuated, a jail in Urbana, Illinois was evacuated after an inmate was said to have brought in a “potential chemical substance”.