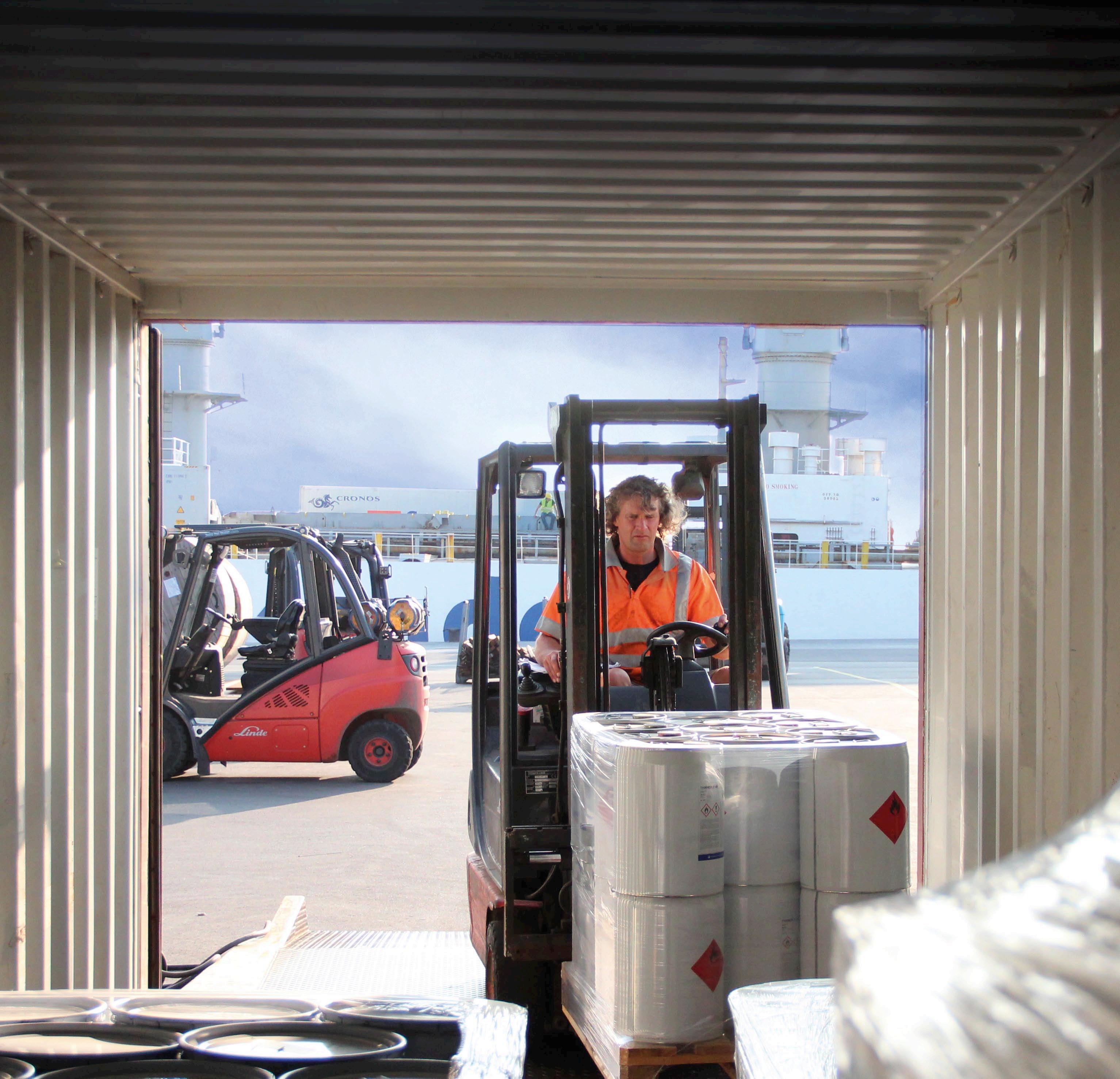
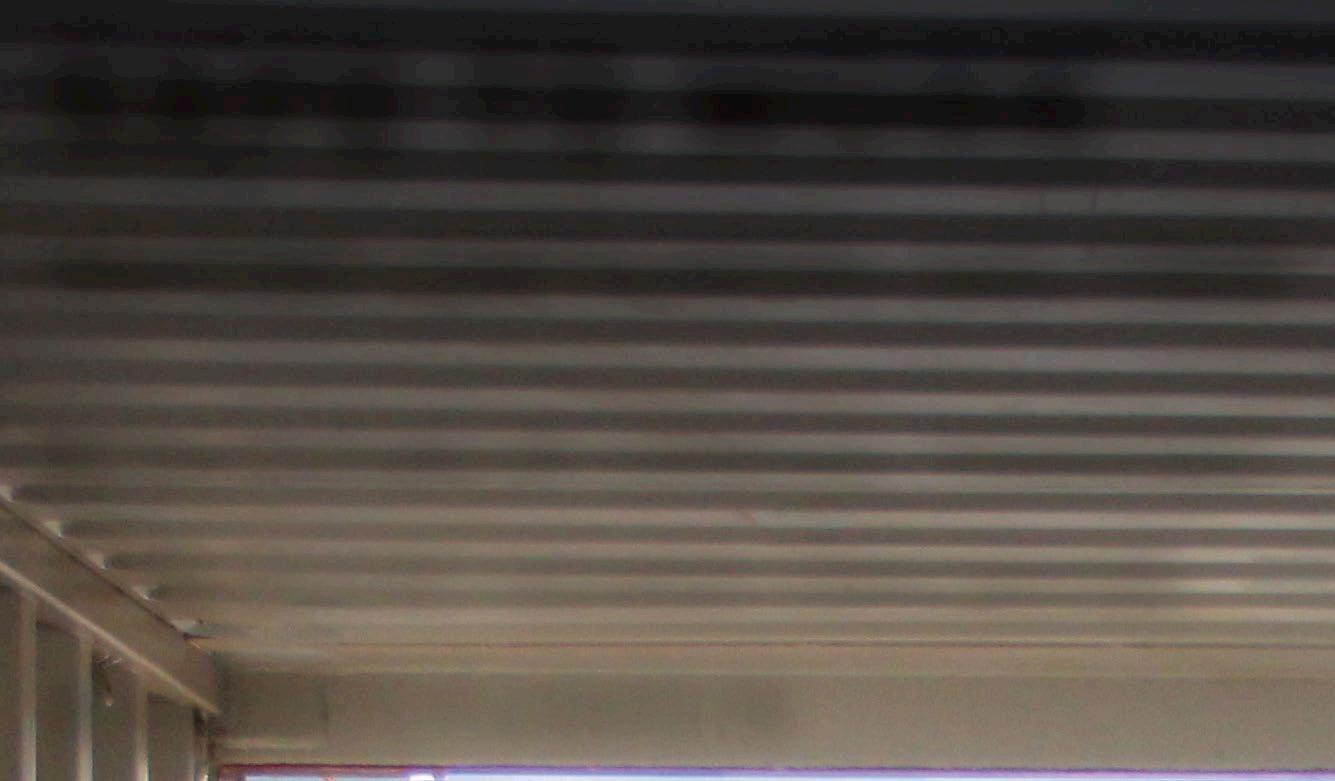
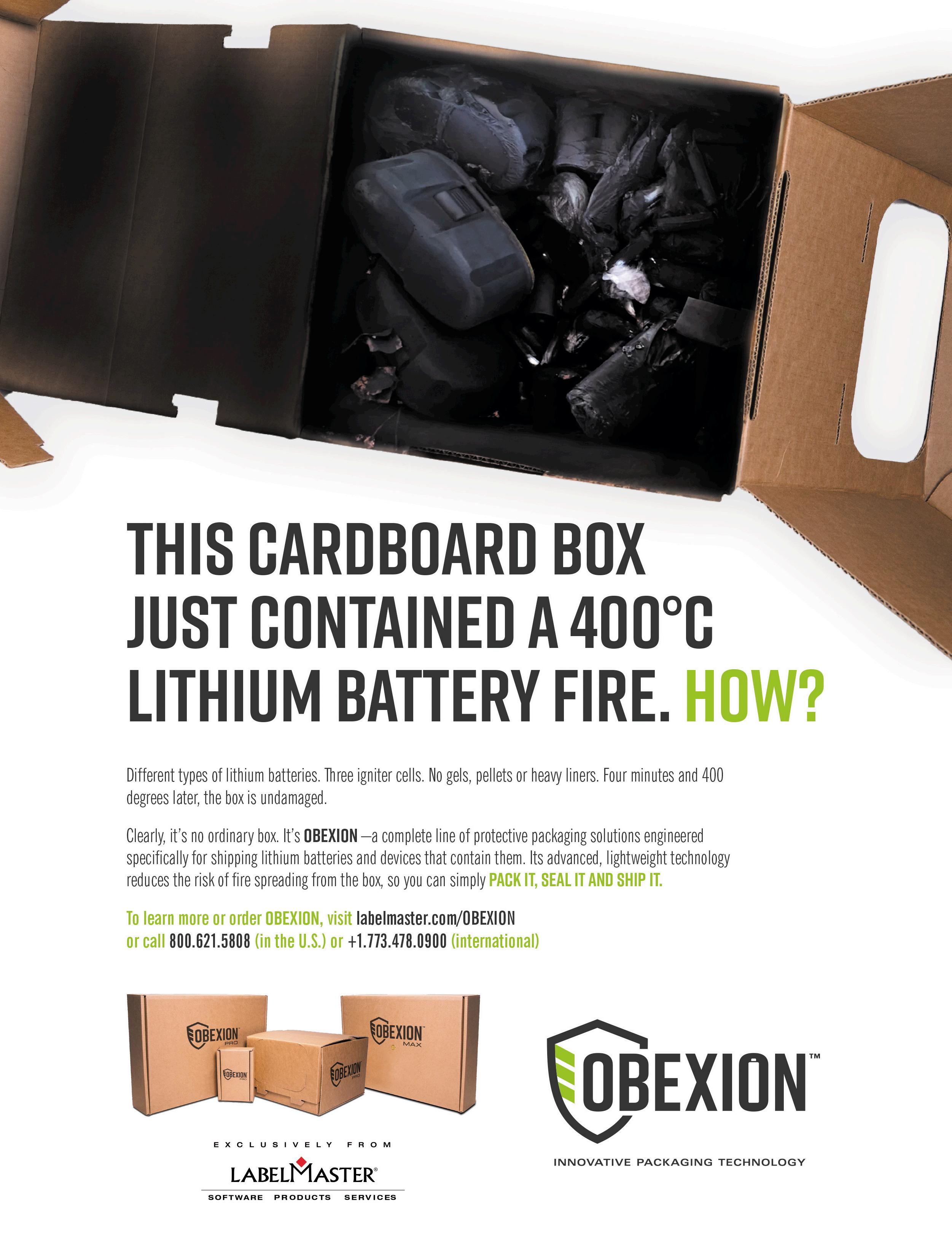
A grandfather of mine spent much of his life working in the transport industry. He reckoned it was safer than going down the pits and, while he would have preferred a career in one of the professions, he didn’t have the Latin for it.
In those days, many companies with large needs for transport services ran their own truck fleets. Independent transport firms might have had some contract work but a lot of their business involved spot loads.
One of my grandfather’s sons, an uncle of mine, followed him into the haulage trade, although by then he reckoned to be in the business of ‘distribution’ rather than ‘transport’. That reflected the trend among consumer-facing industries towards outsourcing their transport needs (and the labour issues that went along with them).
And his two sons – my cousins – also followed their dad into haulage, although they now call themselves ‘logistics experts’. And they spend a lot of their time not just organising transport but also looking for greater efficiencies in the overall business of transporting goods by road around Europe.
Which makes me wonder: if their kids go into the business, what will they call themselves? One thing is for sure: they will spend most of their time in front of a screen rather than behind the wheel of a truck. By the time the fourth generation gets involved, there will certainly be widespread use of autonomous vehicles in the freight industry – much of the technology is already in place, as HCB has reported over the past year or so, and regulations and insurance issues will surely get sorted out. Which might be fortunate, given the difficulty of attracting new drivers to the business.
And the transport sector is not immune to the trend
towards the automation of all sorts of jobs, with computer algorithms and robotics likely to replace many traditional roles (even, I have heard it whispered, magazine editors) in the next couple of decades.
New technologies are arriving in the freight transport industry at an ever-faster rate; in this issue alone, for instance, we cover the roll-out of a telematics solution by Swiss Railways to improve the operation and maintenance of its wagon fleet, the impending introduction of an electronic version of the European Cleaning Document (ECD) in the tank cleaning sector, the increasing penetration of electronic versions of IATA’s regulatory and guidance publications, and the use of e-learning tools by container lines to undertake the immense task of training their employees on the IMDG Code. Also worthy of note is the decision by chemical distributor DKSH to give a place on the board to its chief information officer, recognising the competitive advantage its software investments provide it in the current market.
Probably the biggest problem facing transport companies (or logistics service providers, if you prefer) today, both in Europe and North America, is attracting and retaining drivers. In the future, their biggest problem is likely to be attracting and retaining enough young talent to develop and implement the new technologies that will be, to a very large extent, running the business.
That means transport companies need to start thinking now about the skills that they will need and, perhaps more crucially, the image the industry presents to young people. It might be time to smarten up!
I think my grandfather would have been happy with that.
Peter MackayCargo Media Ltd
Marlborough House 298 Regents Park Road, London N3 2SZ www.hcblive.com
Peter Mackay
Email: peter.mackay@hcblive.com
Tel: +44 (0) 7769 685 085
Stephen Mitchell
Email: stephen.mitchell@hcblive.com Tel: +44 (0) 20 8371 4045
Brian Dixon
Designer Natalie Clay Commercial Managing Director
Samuel Ford
Email: samuel.ford@hcblive.com Tel: +44 (0)20 8371 4035
Ben Newall
Email: ben.newall@hcblive.com Tel: +44 (0) 208 371 4036
Sam Hearne
Email: sam.hearne@hcblive.com Tel: +44 (0) 208 371 4041
VOLUME 39 • NUMBER 02
HCB Monthly is published by Cargo Media Ltd. While the information and articles in HCB are published in good faith and every effort is made to check accuracy, readers should verify facts and statements directly with official sources before acting upon them, as the publisher can accept no responsibility in this respect.
ISSN 2059-5735
Letter from the Editor 1
30 Years Ago 4
The View from the Porch Swing 6
Build high, sell low Tank container fleet keeps growing 9
Behind the wheel ECTA addresses transport problems 10
Generation game Bertschi plans succession 15
Ask the expert Orbit on electronic VMI 16
First and last Safety is paramount for H Essers 18
The gas man cometh EWS on need for gas measurement 20
Talk to the tank
Implico copes with legacy issues 22
The live rail Savvy connects Swiss railways 24
Keep dry in Duisburg Greiwing invests in bulk handling 25
Safe and secure
BDP focuses on cyber threats 26
News bulletin – tanks & logistics 28
Out of the clouds
IATA goes electric 30
Cool flyings
Jettainer’s cool chain service 32
News bulletin – DG by air 33
Shopping spree Brenntag opens its wallet 34
Geared for growth
Azelis consolidates US business 36
Safic-Alcan heads into specialities 38
Univar expands in personal care 39
Committed to the west Nexeo strengthens oil links 41
News bulletin – chemical distribution 42
Training courses 44
Learning by training 48 Trained to comply MSC does IMDG online 51
Conference diary 52
SAFETY Incident Log 54
A bad connection CSB on unloading hazards 56 Click and collect Pharox leads on database management 58 News bulletin – safety 59
Go your own way
Struggle to harmonise the rules 60
Off-road trails
Germany enforces modal shift 68
On the road again Labeline plans for 2019 update 70
Not otherwise specified 72
Bulk liquids storage market update
Annual IBC manufacturing survey
Focus on chemical distribution in Asia
Latest moves in gas shipping
Sometimes when we look back at what we were writing about thirty years ago, one cannot help but feel a sense of sorrow at the hours of wasted effort that went into developing new regulatory provisions that, however sensible they might have seemed at the time, have since been superseded.
That was surely the case back in February 1988, when HCB reported on the outcome of the December 1987 meeting of IMO’s Marine Environment Protection Committee (MEPC), where a longstanding logjam over the selection of marine pollutants under the IMDG Code had at last been cleared. One outcome of that was the agreement of the new mark for marine pollutants: the ‘fish and chips’ triangle.
The concept of identifying marine pollutants has stuck with us but there are constant discussions about specific aspects and substances and, for some reason we fail to recall, the mark was eventually declared unsuitable and replaced with the rather more apocalyptic ‘dead fish and tree’ mark now in use.
During 1987 MEPC, in cooperation with the CDG Sub-committee, had gone a long way to establishing the ground rules for the new Annex III to Marpol but it was clear from the February 1988 issue that there was still work to do to get Annex II fully adopted – and some of its provisions are still not fully in place even now. An interesting piece by HH ‘Curly’ Cail looked at the number of legislative changes that the UK was having to make and the operational arrangements that needed to be put in place at the ship/shore interface.
The February 1988 issue was something of a regulatory smorgasbord, morphing in the turn of a page from the IMDG Code and the IBC and BCH Codes to the latest amendments to the tank provisions in ADR and RID. This took the form of two pages of changes arranged by Marginal – how happy we should all be that we do not have to wrestle with those any longer!
Following that, regular contributor HJK reported on the steady progress being made in the revision of ADR and RID, not least in terms of coping with the need to regulate those new-fangled IBCs. Perhaps irked by the fact that he only had three pages’ worth of contribution in this issue, HJK also sent a letter, warning against the possibility that the European Commission would meddle in the well established system of regulating dangerous goods in transport. That is an idea that cropped up every so often and was normally headed off at the pass; HJK felt that the Commission was prone to confusing regulations for transport with those for supply and use, something that is less likely since the agreement of GHS.
The final item in the February 1988 issue, again on the subject of regulations, was another letter, this from Kaye Warner, head of the Dangerous Goods Section at the UK Civil Aviation Authority. She wanted to alert readers to the fact that a couple of new entries in the Dangerous Goods List in the latest IATA DGR (ID 8035 and 8036, Extracts) did not appear in the ICAO Technical Instructions; anyone using those entries would therefore be in contravention of national legislation and subject to legal penalties.
There are lots of ways to define risk. Most, if not all of the ways involve incorporating the probability of something bad happening. Some of the ways also incorporate assessment of the potential consequences should the something bad actually happen. The defining of risk, and the actual calculations of risk, can be interesting topics, and relevant ones, too. Safety regulations sometimes demand that those regulated assess risks and design programs and procedures to lessen risk. But for all the variants of risk and its application, one thing is quite clear. Risk and hazard are different things.
Transport regulations recently regained an appreciation for the distinction between hazard and risk, and are tightening up their usage of the terms. For example, we’ll no longer have subsidiary risks, but instead subsidiary hazards. This makes some sense, as, roughly speaking, hazards are the bad properties of things (materials, goods) and risks are the likelihood and consequences of those bad properties
causing problems. And transport regulations generally require that those regulated assign hazards, but leave the risk assessment to the regulators.
The US Department of Transportation is good at making clear the differences in roles. Shippers are to determine hazards by applying objective (usually) criteria to what they want to have transported. The Secretary of Transportation determines what is reasonable or unreasonable risk by setting those criteria, and by determining how much packaging/containment and hazard communication each hazardous material requires.
Shippers do not get to decide what an acceptable level of risk is for a liquid that may catch fire easily, and do not get to determine which flash points and boiling points get treated as dangerous. Instead, shippers identify hazards by measuring FPs and BPs, and applying them to the regulatory criteria, and the packaging and/or quantity limits applicable to those ignitable liquids have been pre-determined by the
regulators. Because a PG I material poses a greater risk than a PG III material, stronger packaging must be used. A shipper does not have the freedom to make their own risk determination and decide that PG III packaging will be fine for a PG I material.
All this does make it easier to train on DG regulations. Less decision-making, and more ‘just follow the rules’ simplifies things somewhat. More importantly, though, it makes the outcomes much more uniform, and likelier to be safe.
Recently though, at conferences, meetings, summits, and symposia, I’ve been hearing more discussion of putting transportation riskassessment tools in the hands of the regulated. Proponents argue that excellent tools, properly applied by caring, competent personnel, will reduce risk for everyone. Maybe I’m lazy, or maybe just jaded, but I’m not in favor of moving risk assessment out of the realm of the regulators, into the hands of the regulated.
I once worked for a company that was undergoing a lengthy and ponderous merger. As some milepost in the process was passed, we were finally allowed to reach out to our counterparts in the other company. Only we couldn’t find their DG compliance folks. Our waste department found their waste department. Our air emissions group found their air emissions group. But no DG to DG connection was possible. Why not? Their company had made a conscious decision not to have a DG compliance person, because paying occasional fines was cheaper in $, €, ¥, £, than paying a person to oversee compliance was. And truly, they did pay fines on a regular basis, just not huge ones.
Do we really want that company, whose economic assessment of safety and compliance was no more sophisticated than ‘fines versus salary’ to have authority to make decisions about aviation-related transport risk, no matter how sophisticated the risk-assessment tools we can provide them are? Shouldn’t they already have earned our distrust? What makes us think they’d even try to use the tools?
And there’s the radioactive banana to consider. Or more accurately, consider the man who raged about small amounts of radioactivity. After his company took over my company (neither of us actually owned the multi-billiondollar companies), he was beyond irritated that we complied with the excepted package of radioactive materials regulations, and worse, seemed to expect him to do so, also. Showing him the regulations didn’t help, and showing him how many of our suppliers complied didn’t help. Each just seemed to raise his blood pressure. And eventually he exploded.
“This banana is radioactive! And this apple is radioactive”, he shouted. (Yes, it had started as a lunch meeting.) “And you’re radioactive, and I’m radioactive, and everything’s radioactive”, he raged. “I do the risk assessment for this company, and I’ve evaluated these ionizing smoke detectors, and I’ve assessed these anti-static devices, and their risk is minimal, absolutely minimal. We will not waste our time nor resources complying with these asinine regulations. I make the risk decisions now, I am the authority here, and we will NOT be treating these materials as regulated in any way”, he concluded.
Nothing helped. Even our most gifted diplomat couldn’t convince him to even temporarily comply while we offered to seek to have the regulations changed or to get a waiver. And there was too much of a higher level turf war going on for our VP to have his VP even listen to our complaint. So, the new combined company didn’t comply. Well, that’s not entirely true. Our old company divisions complied whenever we could do so behind his back. And eventually I voted with my feet, and got the heck out of there.
Do we really want companies undergoing high level territorial disputes to be given the responsibility to make transportation risk management decisions when they might be too ‘otherwise occupied’ to do so? Do we want each insecure, corporate risk manager to use her or his ‘common sense’ to decide which level of low risk is equivalent to no risk?
Yes, I’m radioactive, and so is that damn banana. But we’re at background level, and those ionizing smoke detectors are significantly above background. If the DG regulations continue to tell us exactly how far above background an acceptable risk is, anyone who makes even a half-hearted attempt can probably safely comply. But if we leave it in the hands of the regulated community to determine how far above background an acceptable risk is, the accountants and the political animals and self-righteous egotists will be making unsafe decisions for all the wrong reasons, placing lots of us in jeopardy, no matter how wonderful the available risk-assessment tools are.
Attention: Regulators! Yes, I can determine what a reasonable risk is, but I’m asking you not to let me decide. Don’t let any individual person or company decide. Let’s all do it together during the rule-making processes, and then enshrine those group decisions in ironclad regulations. That is essentially what we try to do now, and although what we do now may not be perfect, it could be so much worse.
P.S. I ate that radioactive banana.
This is the latest in a series of musings from the porch swing of Gene Sanders, principal of Tampa-based WE Train Consulting; telephone: (+1 813) 855 3855; email gene@wetrainconsulting.com.
“SHIPPERS DO NOT GET TO DECIDE WHAT AN ACCEPTABLE LEVEL OF RISK IS FOR A LIQUID THAT MAY CATCH FIRE EASILY”
tank containers that had been held in depots and manufacturers’ plant last year are entering service.”
Tank container output could rise further this year. Lee notes that a number of new manufacturing plants are due to open in China and eastern Europe during 2018, although he has not yet been able to determine the size and quality of these new facilities.
GLOBAL OUTPUT OF new tank containers in 2017 is estimated at 48,500 units, according to Reg Lee, who has been tracking fleet developments for many years. Lee’s sources among tank producers indicate that the five main Chinese manufacturers built 40,100 new tanks, with another 5,400 coming from South Africa.
These figures suggest an increase both in output and in the overall tank container fleet of nearly 10 per cent over the course of the year. “However,” Lee points out, “this was achieved not to meet market demand but rather by the tank container manufacturers in Asia dropping prices again to another all-time low just to keep their factories employed.”
Such low prices have had a significant impact: they have encouraged new players to enter the tank leasing sector; they have encouraged a number of small trucking companies to replace older tank trucks with tank containers; and they have discouraged the refurbishment of older tanks.
“The remanufacturing and major refurbishing of older tanks has almost stopped completely during the year because of the very low price of new-built tank containers being made available in the marketplace,” Lee says.
Lee, who collates the data separately from his role as president of The International Tank Container Organisation (ITCO), also reckons that between 3,500 and 4,000 tanks
were scrapped last year. Few were scrapped as a result of manufacturing faults, which pushed up the number in 2016, but many were tanks with a smaller capacity than is now common, making them less attractive in the market.
Despite this avalanche of new tank container capacity, Lee believes that the over-capacity that has bedevilled the sector in recent years is beginning to give way. “Over the last six months we have seen a big increase in the requirement for tank containers and seen customers agreeing to pay a more realistic freight for their services,” he says.
“We are now experiencing the previous over-supply situation being reversed and
Part of Lee’s remit at ITCO is to promote the use of tank containers, especially in emerging markets. “I believe it is important to demonstrate that the tank container market continues to grow,” he says.
“The Asian market will continue to be the driving force behind much of this growth as efforts continue to improve the transport infrastructure. Added to this, local authorities in Asia are now enforcing laws on waste disposal and closing cleaning depots that do not meet the new regulations. Authorities in Shanghai have shut down several facilities in the last year because they did not conform to regulations and I hope that other Asian countries continue this practice.”
Further data on tank container manufacturing and the fleet sizes of the world’s major operators and lessors will be included in ITCO’s annual Tank Container Survey, which is expected to be published by the end of February. HCB
MANUFACTURING • OUTPUT OF NEW TANK CONTAINERS ROSE AGAIN LAST YEAR, WITH INDICATIONS THAT THE GLOBAL FLEET GREW BY ALMOST TEN PER CENT ON THE BACK OF LOW PRICES
itself with road transport.
Indeed, the first presentation of the day, from Bernhard Kunz, CEO of Hupac, addressed the current and future challenges to the use of intermodal transport – especially rail transport – for the chemical industry within the EU. Or, to put it another way, as Kunz began his presentation, “Is rail freight traffic in Europe at risk?”
FOR ONE DAY each year, Europe’s chemical transport leaders gather in Düsseldorf for the annual meeting of the European Chemical Transport Association (ECTA). There is official work to be done and also time to sit and eat with colleagues and old friends in a convivial atmosphere.
There is also a conference, which takes up the larger part of the day between breakfast and cocktails. And it was this as much as anything that attracted some 130 delegates to ECTA’s 2017 annual meeting on 23 November. Those delegates represented both the chemical industry and its transport and
logistics providers, helping deliver a provoking and productive day.
The event also marked the 20th year of ECTA’s existence – a remarkable achievement, especially considering the doubts expressed as to the need for such an organisation when the subject was first discussed more than two decades ago, as Andreas Zink, director of LKW Walter and ECTA’s president, recalled in his introduction.
The transport of chemicals in Europe is these days a multimodal business. Industry has responded to political pressure to remove as much freight as possible – not least dangerous goods freight – from the roads and onto rail, intermodal waterways and shortsea shipping routes. Therefore, ECTA does not just concern
Hupac was founded 50 years ago so has plenty of experience in the ups and downs of the intermodal road/rail business. Nevertheless, Kunz said, 2017 was “a black year for rail” and a year that highlighted vulnerabilities within the current rail industry structure.
Hupac’s aim since its formation has been to invest in its own intermodal terminals and its own rolling stock. This is, Kunz said, “the only way to guarantee independence”. In the decades since, rail freight volumes have grown strongly, especially since deregulation in 2002.
However, the economic and financial crash in 2008 hit the sector hard; volumes dropped by around 25 per cent, with a consequent knock-on effect on investment in infrastructure. This led to problems on the rails, with lower profits hindering the »
EUROPE • CHEMICAL PRODUCERS ARE NOT ALWAYS UP TO SPEED ON THE CHALLENGES THEIR LOGISTICS PARTNERS FACE.
THOSE THAT ATTENDED ECTA’S ANNUAL MEETING LEARNED A LOT
sector’s ability to recover to the necessary level of investment. In turn, that led to poorer performance and lower customer satisfaction.
More recently, the pace of infrastructure investment has picked up again but, Kunz said, that has also led to disruption. The system has “no room to breathe”, he said, meaning that any engineering work inevitably causes delays.
The period since 2008 has also been characterised by consolidation, with many small operators being taken over. Nonetheless, in Germany it is still the case that 43 per cent of freight on the rails (and 60 per cent of that moving intermodally) is carried by private operators.
There has been a lot of work on the northsouth corridor during 2017, Kunz reported, but that investment has not been well coordinated, which led to a reduction in effective capacity. Then in August, groundwater broke into a new rail tunnel under construction near Rastatt, Germany, on the main line from Karlsruhe to Basel. The line had to be completely closed –unfortunately other main lines between Germany and Switzerland were also closed for engineering work.
As it happened, the impact was not at first a problem – this was the middle of holiday season and there was less traffic on the line. However, instead of being repaired in a week or two, as might normally have been expected, the track was out of action for two months.
What this event showed, Kunz said, is that DB Net, the German infrastructure manager, clearly has a national focus and is oblivious to the importance of international rail corridors. “Infrastructure managers need to improve their risk management,” he said. “Construction work needs to be coordinated on an international basis, with the involvement of transport ministries.” Basically, he said, there is a need for overall, international control of the European rail network.
The Rastatt incident also highlighted the language problem. Train drivers are required to be able to speak the local language, so normal trains could not simply be re-routed through France – the drivers did not speak French!
Assuming the lessons of Rastatt can be learned, the future of railfreight in Europe looks bright, Kunz said. There is a broad commitment to grow intermodal freight volumes and a lot of money is coming in. A move to longer trains will help further.
But he also sounded a warning: the cost of low quality is high; there needs to be a middle way between lower prices and higher quality and business associations have a role to play in navigating that path.
“Rastatt was an alarm,” Kunz concluded. “It needs a response. We don’t want it to happen again.”
An opportunity to look outside the particular needs of the chemical industry was provided by Christophe Leclercq and René Horsch, managers in the IKEA Group’s global transport department. Effective logistics is essential to IKEA’s market position and, ECTA hoped, their perspective would give some insightful lessons for its members.
Horsch explained, for instance, that IKEA is committed to decarbonisation; one element of that is greater use of intermodal transport – mainly road/rail. The share of multimodal transport in IKEA’s overall mix has increased from 9 per cent in 2011 to around 20 per cent in 2017 and, he said, it will reach 40 per cent in Europe in 2019.
IKEA has also changed its approach to the market, switching to what Horsch called a “collaborative network approach”. Rather than engaging in competitive tendering, the company opened dialogues with a portfolio of carriers, sharing information on its international flows and inviting comments and ideas. This approach aims to identify strategic logistics partners that can help develop the network and achieve the decarbonisation targets that IKEA has set itself.
This process has, Horsch said, already generated some surprising results, not least the potential offered by shortsea shipping. The connections are already there and in some major sourcing areas (especially Poland, Lithuania and Romania) are better than other multimodal options.
Horsch also said that he had been surprised by the extent and capability of telematics solutions now being offered to the market, up to and including machine learning capabilities.
IKEA is now experiencing better reliability in multimodal transport, Horsch concluded, but it needs to monitor performance and manage
its stakeholders. The company is, for instance, finding that private rail operators are more reliable and flexible than state-owned firms.
Peter Devos, joint managing director of ECTA, introduced an important work project – the digitalisation of the European Cleaning Document (ECD). Around four million ECDs are generated each year and, at four copies each, that is an awful lot of paper. But it is not just about saving trees – digitising ECDs will lead to better accuracy, better security, better data quality and easier distribution of the documents between those who need to have the information.
ECTA has been involved in the project alongside the European Federation of Tank Cleaning Organisations (EFTCO) and Essenscia, the Belgian chemical industry association. Although the concept of the ‘e-ECD’ is “not rocket science,” according to Devos, the number of parties involved has meant that it has taken a lot of organisation to get this far.
Those involved in the project identified a number of hurdles, not lease data ownership. As a result, the system has been designed
on a ‘pass-through’ basis, with concentrated access into the system but decentralised data within it.
A pilot project is expected to start in the first quarter of 2018. If the concept is proven, further investment will be necessary to allow full roll-out to start later in the year –ECTA itself needs to find €120,000 and both Essenscia and EFTCO are going to provide similar amounts. Devos estimated that it will take four years for the e-ECD to have complete coverage – there are more than 600 companies involved across Europe.
But Devos was clear that projects such as this are inevitable and he sees e-ECD as a first step towards the digitisation of all safety systems in the chemical transport chain.
That inevitability was echoed after lunch by Lars Nennhaus, head of corporate development at Duisport, who spoke about the ‘Startport’, an innovation hub for supply chains opened in October 2017. The aim of the hub will be to develop tailor-made solutions for various industry sectors, including chemicals, by leveraging IT capabilities and cooperative and collaborative agreements.
A regular aspect of the ECTA annual meeting is its discussion of Responsible Care issues and the Safety and Quality Assessment for Sustainability (SQAS) system, a key element in benchmarking Responsible Care performance in chemical logistics operations. Luc Renier,
EU transport safety and security leader at The Dow Chemical Company, explained that, while logistics service providers (LSPs) may initially see SQAS audits as a burden on their time, the results can provide the basis of an improvement plan.
LSPs can even structure their management systems along the lines of the SQAS questionnaires, which not only provides a rational basis but also makes life easier the next time an auditor pays a visit.
But shippers can also use SQAS audit results for their own ends, as Dow does, Renier explained. It uses SQAS data to help it define its relationships with its carriers – not only their head office but any depots and subcontractors that may be involved in handling Dow product.
Renier then introduced the big word: ‘sustainability’. How can SQAS play a part in a company’s assessment of its own sustainability? Renier explained that the best companies will, if not now then very soon, have to benchmark their environmental footprint against the benefit that their activities create. This will in due course inevitably involve the public reporting of emissions – future ‘licences to operate’ will be founded on this basis.
SQAS as an audit system is constantly evolving and it seems that, before too long, its questionnaires will have to address sustainability issues. How that will happen is open to question – and that question generated a lot of discussion among the audience, without much in the way of conclusion. Happily, the European Chemical Industry Council (Cefic), which manages the SQAS programme, will be starting a more formal dialogue on the topic.
More on the topic of SQAS came from Evert de Jong, joint managing director at ECTA and its Responsible Care coordinator. He reported that the SQAS questionnaires are to be revised in the first half of 2018, based at least in part on feedback from ECTA members. “Feel free to comment,” he urged delegates.
De Jong then looked in more detail at an ever-present problem: lost-time injuries (LTIs). The number of LTIs at loading sites and during transport has been falling for some time but there has been no »
corresponding improvement at unloading sites. Indeed, he reported, in 2017 two ECTA members stopped deliveries to particular sites because of their lack of action to remedy unsafe conditions. This indicates the seriousness of the situation, de Jong said: carriers do not often refuse work.
One ECTA member has calculated that drivers are five times more likely to suffer an LTI at unloading sites than during transit or at the loading site. There is, therefore, a need to focus on working conditions at (some) unloading sites. ECTA would like to have more data from its members on this issue, where there is clearly more work to be done.
De Jong moved on to the vexed issue of carbon dioxide calculation methodology. The established key performance indicator (KPI) reporting system is to be revised in light of
comments made at a Cefic-led meeting in May 2017.
The last session focused squarely on road carriers’ number one problem: the availability of drivers – or, rather, the lack of them. This is not a new issue, said Bernhard Haidacher, director of LKW Walter and a committee member of ECTA; the problem was being discussed in 2006, before the sudden economic downturn in 2008 masked the issue. But it is now getting worse.
There are a number of factors involved, Haidacher said. Increasing economic activity means there is more demand for drivers across all industries and the chemicals sector has to compete for them. The rise of internet shopping means there has been a rapid increase in home deliveries and many drivers have been tempted away from heavy, long-haul business into the cosier world of local distribution. There are regulatory inefficiencies too: working time restrictions
mean drivers can do less, especially if their ‘active’ time is taken up by road congestion, in-plant delays and increased border controls.
Cefic and ECTA have now introduced an initiative on driver shortages, looking for ideas to ameliorate the problem. Suggestions have been made to harmonise driver training programmes and to harmonise legislation across the EU, both of which would permit greater labour mobility. Action is needed on behaviour at loading and unloading sites. And there is talk of setting up a fund to attract young drivers.
A subsequent panel discussion, moderated by HCB’s editor-in-chief Peter Mackay, talked through some of these ideas in greater detail, but it was apparent from the very lively discussion among delegates that there is plenty of disagreement, not least on who will have to pay for all this. Doubtless this will be a subject of interest at this year’s ECTA annual meeting, details of which will be made available later in the year on the Association’s website, www.ecta.com. HCB
THE BERTSCHI GROUP has appointed Jan Arnet as its new CEO, with effect from 1 August 2018. He will take the place vacated by HansJörg Bertschi, the majority shareholder in the Switzerland-based firm, who is also chairman of the board.
After 30 years in the company, the past 24 of which have seen him act as chairman and CEO, Hans-Jörg has deemed it time to broaden the management base of the firm. He will stay on as executive chairman of the board of directors.
Arnet, who is 44, joined Bertschi in 2003 as assistant to the group management. In 2004 he was named as chief financial officer of Bertschi’s newly acquired subsidiary, Nordic Bulkers, based in Gothenburg, Sweden. He became CEO of the unit a year later. In 2009 he turned his attention to leading Bertschi’s market entry into the Middle East, where it now has an office in Dubai, before being appointed group CFO in 2011. Since 2013, Arnet has been heading Bertschi’s largest business unit, Liquids Logistics Europe.
“My decision to withdraw from the operational management of the company is the result of careful consideration within the board of directors and the family,” says Hans-Jörg Bertschi. “We firmly believe that this is the right step at the right time for the company, its customers and its staff.
Digitalisation and expanding markets are major challenges for the chemical logistics industry. “A broader management team will
help Bertschi stay ahead in this fast-changing environment,” he continues. “As executive chairman of the board, I will continue to work on a full-time basis and focus on the Group’s strategy and innovation projects on Group level.”
The move is also seen as an important step in securing a long-term succession plan. “We want the Bertschi Group to remain a family business,” says Hans-Jörg. “Alongside the second generation of the family, represented by my sister Brigitta BernerBertschi and myself, already three members of the third generation are currently working in first management positions within the company. Our third generation can see itself taking over the company management at a later point in time.”
The move also opens up an opportunity for a new leader to take over the Liquids Logistics Europe unit and that role will go to Santiago Gonzalez, currently head of the Bertschi subsidiaries in Spain and Portugal. Gonzalez has been with Bertschi for eight years and has more than 15 years’ experience in European liquid chemical logistics.
These management changes come at a time of growth in the group, which has expanded steadily over the past decades, not least since it launched its globalisation strategy in 2012. More than one-third of its revenues are now generated outside Europe. Group turnover increased by more than 20 per cent last year to some SFr 900m ($937m), despite the prolonged interruption in rail services on the north-south corridor in Germany due to the problems at Rastatt.
“Our prospects for 2018 are promising,” says Hans-Jörg Bertschi. “In order to meet the growing demand of our customers, we have once more decided [to make] substantial investments in expanding our logistics capacities in Europa and globally. Digitalising our business processes is another important focus for the Group in 2018.” HCB www.bertschi.com
HCB: In light of the ongoing process of digitalisation and the application of the Internet of Things, cognitive computing and blockchain concepts, what does vendor managed inventory (VMI) offer industry?
SS: Those technologies we see as ‘disruptive’ are not only on the horizon, they are here – right now and everywhere. Cognitive computing and software robots - and not forgetting blockchain – are just a few of the technologies that require a change in thinking and will redefine IT strategies.
However, disruption is defined as an innovation that creates a new market by providing a different set of values, which ultimately overtakes an existing market. In any change of this nature, responsible analytics
will identify what stays as a constant function.
The function of the industrial supply chain will stay the same - it is not foreseeable that one will be able to e-mail chemical products - as the functionality; the tools and the associated processes will not. That means that the interaction with the real physical world will also be a condito sine qua non –indispensable. Those stable functions will lead to a migration path which nevertheless will be steep and cliffy.
Will VMI as a value-adding concept make this transition?
Orbit Logistics is one of the leading international providers of inventory management solutions such as Vendor
Managed Inventory (VMI) and Supply Chain Management (SCM). The company also offers add-on solutions that automatically manage consigned inventory at customers’ locations.
Right from the beginning back in 2003, Orbit Logistics provided cloud hosting technologies and Infrastructure as a Service (IaaS) as well as Software as a Service (SaaS), helping customers decrease their expenses by reducing assets and therefore increase productivity. Our solutions are available in the cloud, so connectivity, visualisation, and customised web portals are part of our ecosystem. This helps the company to provide services of interoperability, reliable data security, and end-to-end visibility for all partners along the supply chain.
The company’s VMI system delivers inventory monitoring on site, using measurement technologies like radar for capturing bulk goods and radio frequency identification (RFID) and bar codes for packaged goods.
So are the benefits of VMI still the same? Will IoT and blockchain supersede or complement existing approaches?
VMI allows suppliers a deep insight into the supply chain, providing visibility of inventory levels in real time along with historic values. This enables demand sensing, aggregation, planning and decisionmaking when needed. Orbit Logistics also facilitates the client with a planning system, based on their consumption pattern, that creates production forecasts and allows automatic planning and execution of order placement.
Owing to these implementations, trading partners gain complete visibility along with a reduction in unscheduled or
unplanned production stops. In the light of the increased dynamics, complexity and ongoing globalisation of the supply chain ecosystem, these capabilities lead to increased efficiency and ultimately improved security of supply.
At the same time we also empower organisations with electronic messaging, along with a fully integrated solution in terms of ‘procurement to pay’ (P2P) and ‘order to cash’ (OTC).
Forging ahead, Orbit Logistics will launch a Supply Chain Finance Solution. This will adopt proven Blockchain technology based on the Ethereum network technology, known as Quorum. Combining physical signals (Proof of Existence and Quantity) with solutions as provided from Santander Group for tokenisation and de-tokenisation of Fiat money will provide a migration path for what is called paradigm change or disruption.
Ultimately the message is: ‘The king is dead, long live the king!’. HCB
*Dipl Ing Silvio Stephan is CEO and vicepresident of marketing at Orbit Logistics AG, based in Switzerland. The company’s operational headquarters are in Leverkusen, Germany and it also has offices in France, the US, Brazil and Mexico and a partner network in south-east Asia. More information on Orbit’s supply chain management systems can be found at www.orbitlog.com.
AS A COMPANY offering a wide range of dangerous goods transport, storage and logistics services, safety remains “a top priority” with Genk-headquartered H Essers. “In the world of logistics and transport, safety is something that cannot be discussed afterwards; human lives are at stake,” the company says. “Hence, H Essers focuses on the safety of its employees and visitors day in, day out. From the driver with the forklift truck in the warehouse to the management at the corporate headquarters, everybody is involved. We achieve this level of involvement, for example, by implementing lean manufacturing in the workspace, emergency exercises and safety days.”
“An organisation the size of H Essers needs a good structure to ensure that everything runs smoothly and to achieve optimal results. That is why, for some time now, we have been in the process of implementing the 5S programme, focusing on order and cleanliness to decrease wastage, to discover deviations faster and to involve everyone in the continuous process of improvement,” it continues, explaining that the five Ss in question stand for Sort, Set in order, Shine, Standardising and Sustain. “By reducing and avoiding wastage, we can also save on operational costs,” the company states.
“The next step is the implementation of the safety aspect,” it says, explaining that this,
among other things, includes the adoption of easy-to-understand guidelines for all staff; safety rules for visitors and third parties; clear evacuation plans at every entrance; and regular equipment checks. “In short,” the company states, “nothing is left to chance.”
“In order to keep the 5S+Safety philosophy alive, we have created a quarterly 5S Award, which goes to the [company location] with the highest scores on the different aspects of 5S+Safety. The actions and initiatives taken regarding safety, order in the workspace and visual management have led to fantastic results and have set the standard for best-inclass logistics,” H Essers reports, explaining that the staff at each winning location is rewarded with “something delicious of their choice”. In this way, it says, “we keep our employees motivated and safe”.
But there’s more to it than just that. “To make sure that procedures are mastered by everyone and that everyone is familiar with the procedures and knows what to do when push comes to shove, we regularly organise emergency exercises at [our] different sites,” the company says. For example, this past October the company’s tank cleaning depot in Tessenderlo in the Belgian province of Limburg ran a ‘save a man from a tank’ exercise in conjunction with the local fire brigade.
“The purpose of the exercise was to be able to react adequately if someone falls into a bulk trailer and cannot get out by himself. Both our employees and the firefighters, who had never before performed such an exercise, learned a lot from the experience, so much so that we decided to organise a similar emergency exercise every year from now on. After all, you can never be too prepared,” the company says.
Founded in 1928, H Essers currently employs a staff of 5,400 across a network of nearly 70 locations spanning 15 European countries. Serving customers from the chemicals, pharmaceuticals, healthcare and high-quality goods sectors, it boasts nearly 1m m2 of warehouse space coupled with a fleet of around 1,500 trucks and more than 3,000 trailers.
Moreover, the company, which closed its 2016 books with a turnover of €571m, continues to enhance its network and offering, most recently expanding its 33,000 m2 warehouse near the Romanian capital of Bucharest with a further 5,000 m2 of dangerous goods storage space and an additional 5,000 m2 of pharma storage. What’s more, the company has also purchased another 160,000 m2 of land at the same location to accommodate future growth, bringing the site’s total area to 260,000 m2
Executed over a period of five months at a cost of around €7m, the expansion work, the company says, “involved the strictest security standards”. Consequently, “the warehouse is not only earthquake proof in accordance with the highest standards, [but] the high Seveso storage room is also equipped with foam sprinklers and complete leak retention”. Furthermore, H Essers also maintains “a specialised fire team” that is “permanently present” at the site.
Over the past 12 months, H Essers has also “invested heavily” in upgrading its site in Wilrijk, near Antwerp. “We started with the launch of a new warehouse for highly flammable products and the construction of a state-of-the-art filling installation for filling intermediate bulk containers (IBCs) or tanks with chemicals with a high degree of viscosity,” the company reports. However, to offer customers “integrated solutions”, H Essers has also now added a tank container terminal “for the storage and heating of hazardous liquids”.
“To enable the filling of viscous products, the tank containers are heated at the tank terminal until they have reached the right processing temperature,” the company says. The installation can offer heating via steam, electricity or water as needed. “In addition, the procedures follow the highest standards
regarding safety, quality and the environment.
The semi-automatic filling installation was designed following the ISOPA guidelines and has a capacity of 45,000 tonnes annually,” it continues.
“The site stores, among other things, polyols and isocyanates and raw materials used for the production of insulation materials. Just like other raw materials, these materials can both be stored in the warehouse and processed with the filling installation,” it says. “H Essers continues to invest considerably in this chemical logistics site which, thanks to its excellent location relative to the port of Antwerp, remains highly coveted by chemical producers.”
Meanwhile, at the other end of the equation, H Essers has also signed a five-year contract to provide pharmaceuticals producer Fagron with various logistics services, including fine picking and fine packing, in Winterslag, near
Genk. “The fact that we can store and deliver both hazardous and non-hazardous goods offers great added value to this client,” says business unit manager Benjamin Hermans.
“Over the past few months we have worked hard to align all the procedures,” he continues. “During workshops with the client, we worked out their needs to subsequently transform [them] into processes for the organisation of our warehouse management system. More specifically, this entails that the products of Fagron or their suppliers are delivered to our warehouse in Winterslag.”
“There, we check both quantity and quality. Subsequently, we stock the goods, both physically and in our warehouse management system. Once the goods are stocked, Fagron can send us their clients’ orders. These are then completely picked, packed and shipped by us,” Hermans says, noting that all inbound and outbound movements “are linked to the client’s [IT] system”. HCB www.essers.com
ESSERS IS KEEN
RECOGNISE ITS EMPLOYEES
TOWARDS SAFETY IN
OPERATIONS
LIKE THE ROMANIAN
(ABOVE) THAT ARE LEADING THE WAY IN APPLYING IT SYSTEMS TO ENHANCE EFFICIENCY
AT LEAST ONE in ten of all the freight containers arriving in European ports is unsafe to enter, according to Marcel van den Brink, country manager, Netherlands for the EWS Group. And he is well placed to say: EWS is one of the largest players in the fast-growing market for gas measurement services related to incoming containers.
The problem first came to light about ten years ago, when Dutch customs officers started falling sick during container inspections at ports and terminals. At first authorities suspected that they were being overcome by fumigants in the boxes but, after investigation, it emerged that containers can harbour a wide range of gases or toxic vapours. These are generated either by
the cargo itself – commonly solvents, detergents or other compounds used in the manufacture of the goods – or by new paint or flooring within the containers.
Indeed, as van den Brink explains, less than 10 per cent of the affected boxes show signs of over-enthusiastic fumigation.
The Dutch government took the matter seriously and introduced provisions, primarily under the Health & Safety Act (Arbowet), that amongst other things require companies handling import containers to have gas inspection services in place as part of their overall risk assessment. EWS was well placed to step in, as the Netherlands-based company has had some 40 years’ experience with fumigation services.
The issue has also been recognised in France, Germany, Belgium and the UK, as well as elsewhere in Europe, and van den Brink says that EWS has begun to get inquiries
from the US. EWS has facilities across Europe, including two in the UK – at Bicester and Birmingham – with a third currently being planned.
That expansion is being driven by a growing awareness on the part of major importers, including retailers of the size of Ikea, Amazon, Lidl and others, of the risks posed not only to customs inspectors and terminal personnel but to their own employees. If not properly handled in the first instance, gas concentrations can rise again during the transport movement between the terminal and the distribution centre.
The range of gases found inside containers is remarkably broad and so EWS’s engineers have at their disposal a similarly wide range of gas detection equipment. This must be used before the door is opened and has to be able to detect the concentration of asphyxiants, toxic gases and other volatile organic compounds, and to measure whether the gas concentration exceeds the lower exposure limits. Some of the contaminants are carcinogenic, neurotoxic or teratogenic in very low concentrations and the acceptance levels can vary in different countries, so the EWS engineers have to be experts in dealing with detailed technical specifications.
Once a container has been identified as being a danger, it has to be ventilated to bring the gas concentration down to safe limits. In some cases, such as with high concentrations of carbon monoxide or carbon dioxide or low oxygen level, it is usually enough just to leave the doors open for a while.
Where less volatile vapours or gases are concerned, the gas concentration can rise quickly again after the container doors are closed. In such cases, forced ventilation will be required. EWS has a choice of systems for this purpose, including its patented ventilation doors. Depending on the nature of the gas in the box, it may be necessary to capture the vented gases in a filter system.
It is important to remember that, under the relevant legislation, companies are required to have procedures in place covering the planning for and delivery of gas measurement services. EWS knows these procedures well so is ideally placed to help. HCB www.ews-group.com
INTERNATIONAL SOFTWARE AND consulting company Implico has launched a new, more powerful tool enabling its customers to connect legacy field technology with the OpenTAS terminal management system. The new TCP-X-Unit is capable of simultaneously converting signals from three serial-linked field devices for OpenTAS.
In addition, Implico says, the solution represents yet another step toward the Internet of Things as users are able to monitor data throughput from anywhere and view the information sent most recently by the field devices.
The problem the TCP-X-Unit seeks to solve is the communication gap between legacy hardware and modern software, which makes it impossible for legacy field devices connected via serial links to communicate directly with the OpenTAS terminal management system. This usually requires an additional computer to convert the loading hardware’s legacy signals for the OpenTAS software.
The TCP-X-Unit is a new, compact solution from Implico that considerably simplifies the previously required hardware environment.
The complete solution comprises a suite that includes the powerful Matrix-504 microcomputer and suitable software developed by Implico especially for OpenTAS
connectivity. Except for this pocket-sized computer, no further hardware is required for the connection. The TCP-X-Unit converts the field device’s RS-232 signal into a TCP/ IP signal and transmits it to the OpenTAS automation processes via Ethernet protocol.
Furthermore, the TCP-X-Unit is significantly more powerful than its predecessor. “The computer has three ports instead of just one and can therefore control up to three peripheral devices simultaneously,” says Frank Petersen, head of OpenTAS Automation at Implico. This reduces the need for control hardware, simplifying the IT landscape and lowering total cost of ownership. “The box’s modern processor is also able to handle more data in a given time than the predecessor model,” Petersen adds.
Since the TCP-X-Unit is equipped with a web service for remote access, the solution also represents yet another step toward the Internet of Things. The web service makes it possible to manage, configure, update or start the microcomputer remotely via a web browser.
“The solution’s set of useful features includes data throughput remote monitoring and the ability to display the most recently sent and received information,” continues Petersen.
Should a TCP-X-Unit fail, it can easily be replaced by a low-cost backup device. Local staff do not require any specific IT knowledge to replace the box. After replacement, the preconfigured backup device is set to the failed unit’s IP address and restarted. The unit then automatically receives all the required settings and protocol information from OpenTAS and is available for use immediately. This minimises downtime and ensures a continuous and stable loading process.
OpenTAS automates the storage and transport of hydrocarbons at refineries, tank farms, and service station networks and is one of the high-performance IT solutions offered by Hamburg-headquartered Implico Group. Implico is a Microsoft Gold Partner, a Software Development Partner of SAP and a member of the Oracle PartnerNetwork. Founded in 1983, it now employs around 200 people in Germany, Malaysia, Romania and the US. HCB www.implico.com
LOADING • OLDER HARDWARE AND MODERN SOFTWARE OFTEN DO NOT SPEAK THE SAME LANGUAGE. IMPLICO HAS COME UP WITH A SOLUTION FOR ITS TERMINAL MANAGEMENT SYSTEM
SCHWEIZERISCHE BUNDESBAHNEN (SBB) had come to realise that it could optimise the operation and maintenance of its rail wagon fleet and last year issued an invitation to tender for a suitable telematics system. The tender stipulated that hardware and software with a minimum lifecycle of seven years was required for its ‘GPS rail vehicles – HW and portal solution’ project.
SAVVY® Telematic Systems AG offered a telematics system solution based on innovative hardware and software technologies tailored to SBB’s needs and was awarded the contract in mid-August 2017. Work on the track maintenance trains, switch engines and ten other vehicle types belonging to the SBB infrastructure began in October 2017.
To enable cost-efficient software operations, SBB required a ‘Software as a Service’ (SaaS) solution that also enables flexible user management, mobile access, personalised data visualisation and ad-hoc evaluations. “It was clear from the requirements that they were looking for a highly flexible and innovative system with which SBB would be able to achieve an excellent position both in the short and long term,” explains SAVVY’s CEO Aida Kaeser. “We are proud that we have more than exceeded the expectations and can offer SBB a highly automated future-proof solution which we very much look forward to expanding into a strategic collaboration.”
During the first phase of the project, SAVVY will equip 250 SBB railroad wagons with high-
performance SAVVY FleetTrac telematics units; in the second phase, up to 500 more railroad wagons will follow. The data gathered from the hardware is automated and brought together in the SAVVY Synergy Portal, the central management platform.
In accordance with SBB’s tender documents, all SAVVY Synergy Portal users should be in the 3- to 4-digit range and access distributed among approximately 50 different user groups. This allows SBB to always have access to reliable, consistent operating data and position information.
Thanks to the manufacturer-independence and high connectivity of SAVVY hardware and software, SBB infrastructure is also able to consolidate the telematics systems currently in use. Last but not least, the consistent data collected from a central location is automatically available for other business applications or effective evaluations. SAVVY
technology’s consistent data management and openness support SBB infrastructure in continuing to effectively develop its fleet management processes and the forwardlooking services based on them.
“SAVVY Synergy Enterprise Portal business intelligence has been proven to ensure a high degree of efficiency in different telematics and IT infrastructures, and across systems,” Kaeser says. “In this context, portal systems are not emergency solutions that have to compensate the lack of interface standards. Their openness makes it possible to integrate the existing components worldwide to form a comprehensive solution. And their flexibility ensures that telematics infrastructures are future-proof. Because, regardless of the future path of logistics in relation to Industry 4.0 and smart devices, our open collaboration platform, SAVVY Synergy Portal, will always be at the forefront.”
The SAVVY solution creates a basis with which SBB infrastructure is able to both continue to optimise the transparency and productivity of its fleet management for dayto-day operations but also to develop forwardlooking services tailored to the needs of its internal customers. HCB www.savvy-telematics.com
TELEMATICS • SWISS FEDERAL RAILWAYS AND SAVVY TELEMATIC SYSTEMS HAVE STRUCK A LONG-TERM PARTNERSHIP TO IMPROVE FLEET PRODUCTIVITY
GREIWING HAS FORMALLY commissioned a new warehouse in Duisburg. The 7,500m2 site offers 3,000 pallet spaces in a mobile rack as well as a 1,300-m2 packing area.
The €5.5m project was completed in only eight months but that is only the tip of the iceberg, as Jürgen Greiwing, managing director, explains: “The short construction time does not reflect the effort that we had to carry out for this project. The upstream emission control approval process was particularly complex. Among other things, this demanded the participation of the public and public authorities. In this context, for example, we held a public hearing in the spring of 2016 in the Duisburg Rheinhausen-Halle.”
The new warehouse, which has created 14 new jobs, will be mainly used for the storage of barium chloride in flexible intermediate bulk containers (FIBCs). Up to 3,000 tonnes of the product will be held at the site.
Planning for the new site also involved extensive design work, especially in respect of worker protection. “In order to be on the safe side here, we not only fulfilled all the regulations but partly voluntarily went beyond that,” explains Jürgen Greiwing. For example, the extinguishing water retention system has a significantly greater volume than was required. “In this respect, we have done everything we can to ensure that the facility cannot negatively affect either the environment or nearby residents.”
Barium chloride arrives at the warehouse exclusively in FIBCs in shipping containers, which are picked up from the Duisburg Intermodal Terminal (DIT), immediately adjacent to the warehouse. A small sample of around 500 g is taken from each batch, with the work performed in a special room equipped with high-grade ventilation and filtration systems.
Goods are dispatched in closed box trailers, using only Greiwing-owned vehicles. Transport is undertaken using specified routes that avoid residential areas in Duisburg and the neighbouring region.
“We have gained a lot of experience dealing with hazardous substances in the past and
have acquired a great deal of expertise in this field,” says Jürgen Greiwing. “Of course, we are very pleased that we can now make full use of this know-how at our Logport location.”
Last year Greiwing made additional investments in its Logport site, adding a new 45-tonne gantry crane and a container tilting platform to expand its range of services, particularly in the handling of pourable dry bulk products.
Furthermore, Jürgen Greiwing points out, the ability to provide a link between sea and land routes is important to many of the firm’s customers. “With the Port of Duisburg and a direct connection to the Duisburg Intermodal Terminal, we have found the optimum location for these services in Logport,” he says. “However, in order to be able to respond to the different conditions of the goods recipient, the last transport section usually takes place with one of our 200 silo vehicles.”
The tilting platform allow goods to be transferred from containers equipped with in-liners directly into silo tankers. The Logport site is also equipped with facilities for packing dry bulk products into smaller packagings for transport by container. HCB www.greiwing.de
US-HEADQUARTERED BDP has opened a new office location in Copenhagen, Denmark, bringing its total number of locations around the world to 145. The Copenhagen office, the company says, “is positioned strategically, catering to operations in Denmark while creating an accessible channel of service to clients based in Sweden’s southern tip [and] offering ocean and air import and export services, customs clearance, project logistics, ground transport and warehousing and distribution”.
BDP’s operations in Denmark will be headed up by newly appointed country manager Kenneth Werther. “Due to the healthy business climate of the region, the Copenhagen site is equipped to implement a
full scope of logistics services, with emphasis placed on air, ocean and solution selling for customers in the chemical, petrochemical, healthcare, energy, retail and automotive sectors,” the company reports.
“BDP is proud to announce the Copenhagen office as the newest addition to our global network and newest initiative in our collective mission to provide streamlined, international coverage,” says chairman and CEO Richard J Bolte, Jr. “The Copenhagen location expands our range of operations to better accommodate clients in Denmark and Sweden. As we strengthen our presence at this intersection of two vibrant markets, we plan to implement our full scope of logistics services at a regional and global level.”
Meanwhile over in cyberspace, BDP has unveiled a revamped corporate website.
Among other things, the new-look site features simplified navigation menus; an enhanced list of BDP’s global office locations; direct links to the company’s Smart Suite® visibility tools; and the BDP Blog, “a companyrun news and content hub” that provides “the latest information on industry happenings” as well as company events and developments.
“Social media and other mobile technologies have created smart consumers who want a company’s value proposition at their fingertips,” Bolte says. “Our new website delivers a functional interface for customers to learn about our organisation’s services and presents an aesthetic redesign commensurate to our industry expertise.”
The news comes shortly after the company achieved ISO 27001 certification – which it describes as “the strictest standard of information security” – to ensure its global import and export customers benefit from the highest levels of data protection. “BDP’s clients require assurance that their data is secure and private and that is exactly what we provide,” Bolte asserts. “The ISO 27001 certification is a major step toward protecting the confidentiality and integrity of customer and company information.”
A “stringent certification for information security controls”, ISO 27001, BDP says, guarantees “first-class standards for the identification, prevention and management of security risks”. To attain certification, the company first had to invest in an information security management system that was then subjected to an independent assessment by global standards company DQS. Importantly, the ISO 27001 certification, the company continues, covers all of its “online and vendor management services”, viz Tietan, BDPSmart, Cognos, Impax and DMS.
“The certification process requires an auditable, comprehensive, international framework for the implementation of an Information Security Management System (ISMS), which is a suite of processes and procedures concerning risks management of information security factors,” BDP says. “The ISMS incorporates widely recognised best practices for information security management into the organisation’s operations.” HCB www.bdpinternational.com
VLS Group has taken over the warehousing and logistics activities of Lanxess at its Rhein-Chemie business unit in Mannheim, Germany. VLS is now handling warehousing of raw materials and finished goods as well as internal transport.
“We are pleased to expand our activities in Germany with an additional location,” says Thomas Brakmann, general director of VLS-Group Germany. “It highlights our growth ambitions in Germany and contributes complementary to our existing chemical logistics, warehousing and transport management activities at Frankfurt am Main, Düsseldorf, Belgium and in the Netherlands.”
The deal adds 19,000 m3 of warehouse storage space to VLS’s existing capacity in the Rhein/Main region. VLS will also take on 23 Lanxess employees. www.vls-group.com
Hoyer has transferred its Foodlog operations in Bulgaria and Hungary to H&H Foodlog,
a joint venture established last November with H&S Group. Hoyer holds 49 per cent of H&H, which covers only European operations and does not incorporate Hoyer’s international and deepsea logistics operations in the foodgrade sector.
Hoyer says the latest move is a “logical wstep” to expand the cooperation with H&S. “We have already achieved a great deal in the first two months since the founding of H&H Foodlog,” says Adwin Verhoeks, the company’s managing director. “We look forward to further expansion of the cooperation.”
Ortwin Nast, CEO of the Hoyer Group, adds: “We are very pleased with the first results initially obtained. We are confident we have taken the right decision for a positive development of the liquid foodstuffs transport business.” www.hoyer-group.com
VTG has opened a new branch office for its wagon hire business in Trelleborg, Sweden, taking over responsibility for Scandinavia from
VTG Rail Europe’s headquarters in Hamburg. This office had been supported by Nordic Rail Logistics (NRL) and Danish agent Ib Pallesen. “Successful cooperation between VTG Rail Europe and NRL and Ib Pallesen over the past years has strengthened our presence in the Scandinavian rail freight market. This positive development has prompted us to expand our activities in Scandinavia even further,” says Sven Wellbrock, managing director of VTG Rail Europe. “The new office, with the well-established local contact network in Sweden, will help us in aligning ourselves even more closely with the requirements of the Scandinavian market.”
VTG has also established a new mobile services base in Hamburg, which will improve the mobile rail car service and maintenance operations of Waggonwerk Brühl. “The digital future of the wagon hire business will increasingly require mobile, flexible and foresighted operations to be performed directly on wagons and on tracks. Consequentially, ongoing network expansion measures in the form of additional service support centres are scheduled for 2018,” says Wellbrock.
VTG has also relocated its VTG Rail Europe and VTG Rail Logistics offices in Vienna to a common office. The move is designed to facilitate cross-disciplinary copperation and offer faster integrated rail transport solutions. www.vtg.com
Singapore’s GKE has established G-Chem, a new 65:35 joint venture with Kleio OneSolution that will provide dangerous goods warehousing, drumming and logistics services for packed and bulk chemicals.
“This joint venture will further strengthen the group’s hazardous chemical storage and logistics capabilities – [broadening] our range of services and [transforming] the group into a one-stop integrated chemical storage and logistics service provider to serve both the
chemical and pharmaceutical sectors in Singapore,” says GKE CEO Neo Cheow Hui. “We believe the horizontal expansion within the specialised chemicals space will augment growth in our core warehousing and logistics business.”
The two partners will invest S$460,000 ($350,000) in order to acquire four explosionproof drum filling machines and as initial working capital. G-Chem will operate from one of GKE’s existing warehouses in Pioneer Walk, Singapore, under the management of Lin Duanliang. www.gke.com.sg
Albatross Tank-Leasing has appointed Martin Peploe as its vice-president, Americas to head up its New Orleans office. Peploe is well known in the tank container industry, having previously worked for Sea Containers, ICL, TransOcean and TPI.
Albatross CEO Christoph Schoeler says: “We are very pleased that Martin is on board with Albatross and we believe his addition to our group illustrates our commitment to bring quality differentiation and customer-centric
excellence to our enterprise. This new American focus is an exciting development as it is a very important region for our future development.”
Albatross was formed in 2016 as a subsidiary of Sinochem International Logistics. It currently controls a varied fleet of more than 17,000 tank containers, including temperature-controlled and lined tanks and swap bodies. albatross-tanks.de
Nijhof-Wassink has added 50 new tank containers to its chemical logistics division, which will be used primarily on transports from the Benelux countries and Poland. The company runs nine trains per week from Pernis to various depots in Poland.
Nijhof-Wassink says the new tanks are configured to offer maximum payload and are bottom-operated to avoid the need to work at height. www.nijhof-wassink.com
Van den Bosch has invested in 42 new low-weight Renault trucks, which will be used with its liquid and dry bulk tankers and tank containers in Europe. The Euro 6 Renault Truck T delivers what Van den Bosch calls a “favourable cost price per kilometre” and, with its lightweight construction, will allow vehicles to carry a higher payload.
“We have tested the Renault Truck T extensively and it left a very positive impression,” says Rico Daandels, CEO of Van den Bosch. “We are reinforcing our lightweight strategy in the European bulk transport market with this investment. The use of lightweight equipment, such as trucks, containers and chassis, results in a higher payload, enabling the transport of more product volume.”
Last year, the fleet was extended with 40-ft silo containers, 40-ft silo tipper chassis and lightweight 20-ft liquid chassis. Investments were also made in connectivity, by equipping all trucks with a Trimble board computer and by providing a Trimble application to subcontractors.
www.vandenbosch.com
Suttons Tankers has won a 2017 Roadworthiness Award from the UK Freight Transport Association (FTA). The award recognises high standards in the firm’s fleet of vehicles and trailers and its control of safety-related defects.
“Within the measures that the FTA has, Suttons is consistently at the leading edge of roadworthiness and I’m delighted to present this prestigious award,” says FTA’s senior contract manager, Eric Higham.
“As the UK’s largest bulk chemical logistics company, we are delighted to receive this award,” adds Michael Cundy, managing director of Suttons Tankers. “We believe that we have exemplary standards of roadworthiness and vehicle maintenance which are well above industry averages, and this award backs up that view. Our team, particularly the drivers and technicians, makes an exceptional contribution to maintain our excellent safety record and this award is testament to that.”
www.suttonsgroup.com
WHEN HCB STOPPED off in Geneva last October to pay a visit to the offices of the International Air Transport Association (IATA), we were quite surprised to see the lack of paperwork sitting on people’s desks. After all, if there is one thing we all know about the ability of computers to fulfil the promise of the ‘paperless office’ it is that computers generate much more paper than humans ever can.
But, as we spoke to James Wyatt, IATA’s assistant director of dangerous goods publications, it became apparent that the paper-free environment in which he works mirrors a move towards greater use of online and electronic versions of IATA’s publications.
Indeed, at the time of our visit Wyatt was hard at work on the Electronic Flight Bag (eFB), a reference tool for flight crews that includes a condensed version of IATA’s Dangerous Goods
Regulations (DGR). This is proving very popular, he said, with Emirates airline being the first major customer. Helicopters and military operators are also very interested in this product.
Indeed, Wyatt said, publications are increasingly moving to electronic formats; including IATA’s Lithium Battery Shipping Guidelines, which draw out the relevant provisions in the DGR and present them in a user-friendly way for shippers that may often not be au fait with the DGR themselves.
That customer demand for electronic and online publications is strong should come as no surprise. Use of electronic editions not only saves time, it increases efficiency and regulatory compliance while also reducing
errors. In this respect IATA is no different to any other information provider.
Acceptance personnel can look forward to great things from another current project, DG AutoCheck, the aim of which is to reduce the burden of repetitive work and increase efficiency – and, most important of all, safety. After all, the current paper checklist for acceptance personnel has 53 questions for each shipper’s declaration (DGD)
In this new system, each DGD can be sent electronically to DG AutoCheck or can be scanned and read by optical character recognition (OCR) software. The DGD data is then verified against the DGR, providing the checker with an output of the check and an image of the package(s) or overpack(s) to support the physical check, including labelling and marking, of the shipment itself.
One benefit of doing this electronically, as DG AutoCheck is based on the XML version of the DGR, is that it automatically
IATA IS WORKING ON PROJECTS THAT AIM TO MAKE SURE SHIPMENTS ARE COMPLIANT BEFORE ARRIVAL AT THE AIRCRAFT
updated with the latest information on all regulatory items, including State and operator variations, further reducing the chances of goods being held up in the transport chain. This does, though, depend on the identity of all parties in the chain –the State of origin and destination as well as the carrier – being known.
“Industry is crying out for this,” said Paul Horner, manager of IATA’s dangerous goods standards. He believes that the system will reduce errors, halve the time taken to check documentation and give acceptance personnel more time to focus on problem shipments. It will, though, require users to perform a full manual check of a certain proportion of DGDs, to ensure that the competence of the acceptance checker is maintained.
DG AutoCheck is in final development and will be thoroughly tested in a pilot programme involving airlines, freight forwarders and
ground handlers. Formal rollout is planned for the second half of this year.
Moving towards electronic publications is all part of a broader project at IATA, known as ‘Simplifying the Business’ or StB for short. This has six elements, of which one is the electronic air waybill (e-AWB), and takes what is described as a ‘family of approaches’ across the organisation.
One of the six elements is the Air Cargo Incident Database (ACID), a project currently being explored. IATA wants to understand its members’ needs, opinions and concerns before progressing further. There is, Horner said, clearly an appetite for a single global database of air incidents but there are the usual worries about publication of such details deterring the reporting of them – it has to be anonymous. It also has to be easy to use if it is to be of value to those involved in the airfreight business.
But having the real information available, in a form that can be interrogated, would improve the management of safety.
“Today everything is based on perceptions,” Horner said; there is a need for real data. Interestingly, the initial focus of work to develop ACID will concentrate on dangerous goods incidents.
Another current project is already making a change in the use of IATA documents: the IATA Desktop Reader. This is free to download and installed on any computer running Windows and allows all IATA documents to be opened in a single application. The possibility is now also there for mobile applications such as iOS and Android. HCB
Further information on IATA’s electronic publications can be found on its website at www.iata.org/publications-online. To learn more about the DGR, go to www.iata.org/dgr.
LUFTHANSA-OWNED JETTAINER has expanded its product portfolio to include “a special service for temperature-controlled ULDs”. Dubbed Cool Management, the new service includes the leasing, management and positioning as well as monitoring of units. “With this,” it says, “Jettainer is facilitating this complex process, which includes the coordination of many parties, for their customers.”
“The transport of temperature-sensitive goods via air freight requires precise planning and implementation. Starting with the sender via the shipper and the airline all the way to the owner of the specialised reefer-containers, everyone has to work together in a coordinated manner. Thus, the complexity and also the risk potential for the delicate freight is respectively high. The ULD management is especially important in this case,” Jettainer says.
Jettainer’s new service, it asserts, “increases the efficiency between all involved parties of the supply chain”. Furthermore, it also “reduces the costs that can arise” through positioning, overcapacities or other inefficiencies. Additionally, in order to cater to the customers’ individual needs, Jettainer also offers the Cool Management service in different models, which differ in the scope of the offered services.
“We are transferring our long-standing knowhow of worldwide ULD management to our new Cool Management service in the area of temperature-sensitive transports,” says Martin Kraemer, Jettainer’s head of marketing and PR. “This way, we are serving our customers’ need for an easy, reliable organisation of these transports and are simultaneously closing the gap in the management of complete ULD fleets.”
One company that has been quick to make full use of the service is Lufthansa Cargo. “We very much appreciate the excellence of service provided by Jettainer, as well as its constant push for innovation,”
says Lufthansa Cargo’s global handling performance manager Marcus Bezold. “That is why we are certain to now have the best solution for temperature-sensitive goods. The new service by Jettainer will help us to reduce [the] holding time of units, which will reduce our costs for the leasing of additional ULDs.”
Meanwhile, Jettainer has also up-scaled its services at Abu Dhabi International Airport with the opening of a new Centre of Excellence for the management of temperature-sensitive air freight, a move that the company believes will help it “boost the efficiency of its services between all parties” along the supply chain. “We have implemented Cool Management at the express request of our customers,” says Jettainer’s managing director Carsten Hernig.
“Temperature-sensitive goods, like pharmaceuticals, need highly specialised containers. The management of these expensive containers is a complex part of the ULD management. Mistakes could cause massive financial losses and reputational damages,” he continues. “However, the airlines have a demand for cool management. Therefore, we have developed the Centre of Expertise in Abu Dhabi, where the specialised knowledge concerning cool ULDs is focused. Due to the increasing market for pharmaceuticals, we are optimistic about further developing the Cool Management service in future.”
Describing itself as “the global market leader in outsourcing solutions for ULD management,” Jettainer operates a global fleet of around 100,000 ULDs and maintains a station network encompassing some 500 airports around the globe. “Jettainer is the oldest, best established and most experienced ULD management firm in the market, with stable and unchanged ownership,” it states. “Our mother company, a global cargo airline, provides a solid background in the market and enables Jettainer to be perfectly settled in a true air cargo and airline background.” HCB www.jettainer.com
ULDS • JETTAINER HAS WIDENED ITS SERVICE OFFERING WITH A FULL-SERVICE PACKAGE FOR THE MOVEMENT OF TEMPERATURE-SENSITIVE GOODS BY AIR
Saudi Arabia’s Saudia Cargo has signed a master agreement with Germany’s DoKaSch Temperature Solutions to use the latter firm’s RKN and RAP Opticooler unit load devices (ULDs) for the transport of temperaturesensitive goods.
“We are very pleased to offer our customers a highly reliable packaging solution to transport temperature-sensitive shipments with DoKaSch Opticoolers,” says Saudia Cargo’s Adel Elshazly. “Especially pharmaceuticals must be kept within strict temperature tolerances throughout the entire supply chain, regardless of the ambient conditions, which are a challenge in particular in our region.”
“We are pleased that Saudia Cargo will be joining our global airline network,” adds DoKaSch managing director Andreas Seitz. “Saudia Cargo is a very important partner in many aspects. Not only do they have one of the world’s most modern aircraft fleets, but Jeddah is a very important trading hub for us as well. Now our containers are accessible much easier in the Middle East, Asia and Africa.”
The Opticooler, DoKaSch says, “is especially designed for extreme climatic conditions”.
As such, it is able keep cargo “well within a temperature range of 2°C to 8°C or 15°C to 25°C even when it comes to high temperatures up to 50°C”, something which is “quite common in Saudi Arabia and the surrounding regions”. Indeed, the company asserts, the Opticooler “is the most adequate and reliable packaging solution for temperature-sensitive pharmaceuticals”. www.dokasch.com www.saudiacargo.com
Aviapartner, “one of the leading independent providers of ground handling services across 37 airports in six European countries”, has opened its second Pharma Hub at Brussels Airport. Intended to “support the growth of customer volumes and [its] long-term commitment to operating in Brussels”, the new Pharma Hub 2 development represents Aviapartner’s second investment in pharma-specific facilities in Belgium in recent months.
“The second hub increases Aviapartner’s total handling capacity to 3,400 m2 dedicated to pharma only. The new premier site ensures we provide our customers the confidence that
their sensitive pharmaceutical products are handled to the exacting time and temperature standards required,” the company says, noting that together its Pharma Hubs 1 and 2 are expected to handle some 15,000 tonnes “of the world’s most high profile pharma products annually”.
www.aviapartner.aero
UK-based Air Sea Containers has further expanded its extensive range of dangerous goods packagings with the launch of 4DV plywood boxes for non-specific inner packagings. “Our 4DV boxes offer a rigid outer packaging for the shipment of dangerous goods and are a popular choice for shippers wishing to use their own containers,” the company says, explaining that the new range “allows for dangerous goods to be shipped up to a maximum gross weight of 280 kg” per unit.
Available in a variety of standard sizes as well as bespoke dimensions, the 4DV plywood boxes are delivered flat and can be “easily assembled onsite as and when needed” using a locking tongue method, meaning no screws or nails are required. In addition to assembly instructions, all the company’s 4DV boxes are supplied with plastics liner bags. “Vermiculite, supplied separately, will also be required to provide cushioning for inner packagings during transport,” the company says, reporting that it will be happy to help shippers calculate just how much vermiculite they will need to void space within each packed consignment.
A specialist in the manufacture and supply of UN-approved packagings for the transport of dangerous goods by air, road and sea, the Merseyside-based company can readily furnish shippers with more than 700 different off-the-shelf products. These range from drums and 4G boxes to numerous inner packagings, hazard warning labels and various packaging accessories.
www.air-sea.co.uk
BRENNTAG HAS SIGNED an agreement to enter into a majority 65:35 joint venture with India’s Raj Petro Specialities (RPS) as part of a deal that will see it acquiring the remaining 35 per cent of shares after a period of five years. Jointly headquartered in Mumbai and Chennai, RPS distributes its own-blended brands of petroleum-related products to a diverse array of customer industries across India as well as other countries within Asia-Pacific, Africa and the Middle East and expects to finish its current financial year with total sales worth approximately €180m.
“For Brenntag, the acquisition of Raj is
brands,” adds Henri Nejade, Brenntag Management Board member and AsiaPacific CEO. “Its facilities are strategically placed [in] the west and southeast of India in proximity to major ports, offering blending and repackaging capabilities as well as a strong application development team. The cooperation offers Brenntag diverse potential for synergies and future growth.”
“We are delighted to partner Brenntag, a global leader in chemical distribution,” RPS states. “Through this joint venture, Raj Petro can integrate into Brenntag’s global platform of products, suppliers, customers and bestin-class industry practices and fully leverage on the synergies to emerge as one of the fastest growing specialty petroleum products companies in South Asia.”
Further west, Brenntag has entered into an agreement to acquire Colombia’s Conquímica. Headquartered in Medellín, the company primarily distributes industrial and speciality chemicals to the local coatings, food and cleaning industries. Operating four warehouses located within the country’s main economic areas, it expects to close its 2017 books with sales of around €40m. “Conquímica is an attractive investment to extend our geographic coverage and distribution network in Colombia,” says Brenntag’s Latin America CEO Germán Torres. “The company’s broad product portfolio and well-developed infrastructure complements Brenntag’s offerings to customers in important focus industries.”
a further step into the Indian chemical distribution market, which is the seventh largest globally for chemicals and third largest for lubricants,” says Brenntag CEO Steven Holland. “Raj’s existing product portfolio and market presence, capability of its infrastructure and strategic locations make it a compelling investment target to expand our footprint not only in India, but also in other Asian-Pacific countries, in Africa and the Middle East.”
“Raj has the widest product portfolio among its national competitors and a strong market presence with its own blended
“Conquímica,” adds Anthony Gerace, Brenntag’s managing director, mergers and acquisitions, “is a strategic fit strengthening Brenntag’s footprint in Colombia. Combining Conquímica’s product portfolio with Brenntag’s existing market reach and expertise will greatly benefit our customers across the Colombian market.”
Back in its home territory of Europe, Brenntag has also signed an agreement to acquire Portugal’s Comércio e Indústria Química (Quimitécnica). With 2016 sales of around €37m, Quimitécnica provides a wide range of products and blends as well as logistics and storage services to customers
across Portugal, northern Spain and several African countries, commanding what Brenntag describes as “a strong position in the markets for industrial chemicals, water treatment, pulp and paper and specialty chemicals”.
“With a wide product range targeting various industry segments and six strategically located sites offering customised logistics services and inventory management, Quimitécnica serves as an excellent platform to expand and diversify our distribution activities in Portugal and Spain,” Gerace reports.
Commenting on the news, Karsten Beckmann, Brenntag Management Board member and Europe, Middle East and Africa (EMEA) CEO, states: “The acquisition of Quimitécnica is an excellent strategic fit to Brenntag’s existing distribution activities in Iberia as we gain access to key customer industries in Portugal and in the area of the north of Spain. We thus expand our valueadded service offerings to our regional customers and suppliers.”
At the same time, Brenntag has become BASF’s exclusive distribution partner for the Zetag® and Magnafloc® lines of polyelectrolytes across the UK and Ireland following its acquisition of the water treatment businesses of CCP Gransden and CCP Gransden (Ireland).
“The acquisition of the CCP water solutions business is a great complementary fit to our water treatment business in the UK and Ireland as this now means we can offer the full range of BASF polyelectrolyte flocculants across the entire territory,” says Brenntag UK & Ireland’s chief operating officer Richard Ward. “CCP has a very strong reputation in the sector and I am delighted to welcome Stephen Gallagher and Christopher Murphy, the former CCP technical and sales staff, to the Brenntag Group.”
“The BASF range of flocculants fits perfectly within the Brenntag product portfolio and market sector focus,” adds CCP managing director Jim Erskine. “Brenntag has a very wide water treatment product offering, which will complement the range that CCP has been marketing for many years. I am pleased that the technical sales team from CCP will transfer to Brenntag as this will offer continuity to our customers.”
Sticking with the UK, Brenntag has also expanded its presence on the country’s food and nutrition market through the acquisition of A1 Cake Mixes and Kluman and Balter.
Focused on the distribution of chemicals and ingredients to the local bakery sector, these two companies command combined annual sales of around €87m. “With this acquisition, Brenntag UK & Ireland will significantly strengthen its footprint in the country’s very attractive food and nutrition sector, [which] is one of our focus industries in EMEA,” Beckmann says. “The companies provide value-added services that perfectly complement Brenntag’s proposition to customers, including new product development and technical competence and support based on deep insight in market requirements and trends.”
“The UK bakery ingredients and cake mixes market,” Gerace notes, “is expected to continue to grow, benefiting from positive consumer trends, such as increasing demand for gluten-, lactose- or other free-from goods. In addition, the companies focus on higher value products and channels like artisanal bakers, in-store bakeries and foodservice thus creating further growth potential.”
Meanwhile on the contracts front, Brenntag has become Kronos’ exclusive western European distribution partner for speciality titanium dioxide grades for the food, pharma, cosmetics and animal nutrition sectors.
“This is a great addition to our existing product portfolio and it further deepens and strengthens our global business relationship with Kronos,” says Brenntag’s EMEA chief operating officer Uwe Schültke. “Our excellent market expertise, long-term experience and great customer proximity will ease the sales and marketing of Kronos products.”
“We are very excited to enter into this new partnership with Brenntag for the distribution of our food, pharma and cosmetics line,” adds Kronos Europe president Jean-Pierre Gravel.
“We are confident that this collaboration will help us grow the business through increased market exposure and provide improved service to customers on technical, regulatory and commercial aspects.” HCB www.brenntag.com
AZELIS HAS OPENED a state-of-the-art 1,200-m2 office facility in Cincinnati, Ohio that will function as both the new headquarters of the company’s US coatings, adhesives, sealants and elastomers (CASE) business and the new corporate office of its GMZ subsidiary. As such, the new office will house more than 40 employees, including the Azelis CASE US leadership team, led by managing director Dan Gruber, and the CASE supply chain team. “Our overall commitment and growth in this sector warranted expanding resources,” Gruber explains. “The new CASE headquarters will allow us to have a more centralised and efficient supplier experience.”
“The opening of our new US CASE headquarters is an important milestone for us as we continue our evolution and maturation as the market-leading speciality chemical distributor,” says Frank Bergonzi, Azelis CEO and president, Americas. “This location, along with [Azelis-owned] Ribelin’s corporate office in Garland, Texas will service as Azelis CASE centres of excellence and are designed to encourage employee engagement, collaboration and productivity.”
Commenting on the news, GMZ general manager Tom Wells states: “GMZ has been
rapidly growing as a result of collaborating with our principals to provide the leading portfolio of products, as well as executing on our corporate strategy of providing unparalleled customer and technical support to our more than 2,000 customers to help them win and grow in their markets. All of our employees are very excited about the new office as we had outgrown our previous space. This new facility affords us the ability to continue to expand and will enhance our ability to attract top-notch talent, ultimately for the benefit of our customers and principals.”
Meanwhile on the management front, Azelis Americas has named Al Pearce as its new group principal manager. In this new role, the company says, Pearce “will interface domestically and globally with strategic suppliers and coordinate activities internally with Azelis colleagues” across the planet.
“This is a milestone for Azelis and Al is a great addition to our team,” Bergonzi states. “This newly created position adds a key component to our business model. We are fortunate to have Al join us as he brings a tremendous
amount of experience and knowledge in specialty chemicals.”
The news come shortly after Jesse Kreider was named general manager of Azelis-owned Ross Organic. Having served as the company’s vice-president of sales and strategy for the past three years, he will now take on responsibility for the company’s overall operations. Kreider will report directly to Tim Dooling, Azelis Americas’ managing director, personal care/home care, who states: “We are ecstatic to have Jesse in this role and his continued success in positioning Ross as one of the leading specialty personal care distributors in the US.”
Meanwhile, Azelis has further added to its trophy cabinet by scooping the Laura Marshall Memorial Award for Innovation at the recent SCS Formulate exhibition in Coventry, UK. The company landed the gong for its Maskerade product, which it describes as “a customisable, biodegradable face mask” made from a coldprocess pectin derived from citrus peel.
“We are delighted to win the Laura Marshall Memorial Award for product innovation as we were up against strong leading companies in our industry who had submitted fantastic entries,” says Terry Yeates, Azelis’ regional business manager, personal care. “This award win highlights how as a team Azelis ‘connects the dots’, translating market trends and customer needs into award-winning formulations.” HCB www.azelis.com
With our origins in chemical logistics, leading chemical companies rely on Odyssey to move their products around the world safely, cost-efficiently and on time. The Odyssey team has in-depth knowledge of the unique chemical transportation environment. Safety is our priority and we make it our business to stay abreast of the ever-changing regulations governing transport of hazardous and non-hazardous products. Our global multimodal freight network of over $2 billion and robust Odyssey Global Logistics PlatformSM deliver supply chain efficiencies that enable cost optimization and control across all modes of chemical transportation.
For more information on our Global Chemical Solutions, please visit www.odysseylogistics.com/industries/chemicals or call 855.412.0200.
FRANCE’S SAFIC-ALCAN has acquired Biochimex, a compatriot distributor of active pharmaceutical ingredients (APIs) and excipients to customers across Europe and the Maghreb. Moreover, Biochimex, Safic-Alcan says, “is also and above all [a] supplier of sterile active ingredients, a technically superior category of ingredients complementary to the Safic-Alcan portfolio and with which an important synergy is expected”. Founded in 1982, Biochimex
employs a staff of 10 and expects a 2017 turnover of around €10m, of which 80 per cent is forecast to come from export sales.
Following its acquisition, the company will remain independent. It will also retain its current staff, although Bernard Goldenberg and Agnès Goldenberg will step down from their roles as CEO and general manager. They will be replaced, respectively, by Safic-Alcan CEO Philippe Combette and Jose Lora, development director of Safic-Alcan’s life sciences division.
“I am particularly enthusiastic about this agreement,” Bernard Goldenberg says. “It should allow Biochimex to accelerate its development thanks to the international market knowledge of Safic-Alcan, its important international purchasing structure, its knowhow, its strong responsiveness to the emerging needs of its customers and the expertise of its sales engineers.”
“The acquisition of Biochimex is in line with Safic-Alcan’s growth strategy,” Combette states. “This acquisition will enable us to accelerate our international development, particularly in the Maghreb, to expand our product portfolio and to consolidate our relationships with our suppliers.”
In similar news, Safic-Alcan’s UK arm has also acquired Techform Fine Chemicals. Serving customers from the construction sector within the UK and Ireland, Techform produces and distributes a wide range of polymers, thickeners, accelerators, retarders, shrinkage compensators, defoamers, air entrainers, plasticisers and binders, as well as a speciality additives portfolio under its own private label brand.
“The acquisition of Techform will enable us to strengthen our footprint in the construction sector and widen our group expertise in this field,” says Yann Lissillour, Safic-Alcan’s director of mergers and acquisitions.
“As part of our overall [coatings, adhesives, sealants and elastomers (CASE)] strategy,” Combette states, “we see this acquisition as a stepping stone in the UK market and we look forward to further building on this additional expertise within Safic-Alcan.”
“This [acquisition] fits well and will ensure future growth,” adds Techform director Mike Strong. “I will also continue in a consultancy role to support customers and suppliers during the transition.”
Over in Turkey meanwhile, Safic-Alcan’s Interplast subsidiary has signed a contract with Clariant for the distribution of pigments and pigment preparations to the local coatings sector. Among other things, SaficAlcan says, this includes “high-performance pigments, dyes, preparations and services to meet the demands of decorative, automotive, general industrial, wood, powder, marine and protective coatings”.
“Clariant’s deep experience and knowhow in the sector have also made its products unique for successful technical performance and quality,” it states. “Besides its products, Clariant also supports its services through global technical service centres and production centres. We believe Interplast will be a perfect partner for Clariant that will further improve our footprint and our offering [to the Turkish] coatings market.”
Headquartered in Paris-La Défense, SaficAlcan has a presence across Europe, Turkey, China, the US and Mexico; it closed its 2016 books with sales worth €508m. HCB www.safic-alcan.com
UNIVAR’S WHOLLY OWNED subsidiaries in Sweden and Norway have completed their joint acquisition of Kemetyl Industrial Chemicals, a division of the Kemetyl Group that commands annual sales of approximately $30m. “With the successful closing of this acquisition, Univar will enhance its brand, expand its leading position in the pharmaceutical market and strengthen its expertise in water treatment in the Nordic region,” says Univar chairman and CEO Steve Newlin. “Both our companies have deep experience and key competencies in the life sciences market.”
Kemetyl’s offices in Sweden and Norway, Univar says, “will continue to operate as usual while the integration process is completed”, with a total of 15 employees from both locations now transferring to the Univar payroll. “Kemetyl Industrial Chemicals is a natural extension of Univar’s existing strong market presence in [Europe, the Middle East and Africa (EMEA)],” says Kemetyl Group board chairman Ketil Stave. “Our industrial customers will see tremendous benefit from Univar’s outstanding service, market intelligence and distribution network.”
In other news, Univar has signed an exclusive agreement for the distribution of Cargill’s
personal care portfolio across the EMEA region. The range, Univar says, offers “many solutions with unique benefits to formulators looking to create consumer products that can be eco-labelled and certified”, with the portfolio including “patented, nature-derived texturising agents, such as Actigum™ VSX 20 and Satiagel™ VPC 512”.
“Working with Cargill Beauty gives us the ability to continue our commitment to sustainability by expanding our nature-derived portfolio and deliver unsurpassed value to our personal care customers who demand environmentally-conscious ingredients,” says Matthew Ottaway, Univar’s vice-president of focused industries, EMEA. “Coupled with Univar’s personal care expertise and market analysis, we can offer an attractive package of sustainable, nature-inspired products and value-added services. These services include illustrative formulations and technical assistance that help our existing and future customers meet ever-growing consumer demands for more natural ingredients and real perceived product benefits.”
“With Univar, we have found a leading distributor who can really open doors for Cargill,” adds Cargill Beauty’s general manager Tony Jaillot. “The company
brings great expertise in sales, marketing, formulation and communication and a vision that fits perfectly with Cargill Beauty’s strategy. This agreement provides a solid foundation to bring our unique and differentiated nature-derived, label-friendly and highly functional offering to the global personal care market.”
Meanwhile, Mark Fisher has been named as the new president of Univar USA. A former US Navy aviator with a master’s degree from San Diego State University, Fisher brings with him more than 15 years of strategic sales and operations experience within the telecoms, pharmaceutical and healthcare distribution sectors. He joins Univar from Owens & Minor, a US-based healthcare distribution and medical supply company, where his most recent role as vice-president and general manager, clinical and procedural solutions saw him taking on responsibility for the company’s US medical kitting and packaging business.
Commenting on the appointment, Univar president and chief operating officer David Jukes states: “Mark is a highly driven, resultsoriented executive and has a long track record of commercial, operational and leadership success. He will play a pivotal role at Univar as we continue the transformation of our US business to deliver consistent growth by capturing and promoting the superior value Univar provides our customers and supplier partners.” HCB www.univar.com
offering “durable sealing solutions that are attractive for a variety of market segments, including automotive and household and consumer products”.
“The addition of Santoprene TPVs complements Nexeo’s portfolio of products sold into the wire and cable market and provides our customers an even broader range of flexible, high-quality materials from a leading producer of engineered thermoplastics,” says Shawn Williams, Nexeo’s senior vice-president of plastics.
“This agreement serves as an example of the strong relationship that we already share with ExxonMobil across a broad range of markets.”
US-HEADQUARTERED NEXEO Solutions has signed an agreement with Equilon Enterprises (doing business as Shell Oil Products US) to purchase approximately 32,400 m2 of land that it currently leases from Shell in Carson, California. “Contemporaneously, with the closing of the sale of land, Nexeo Solutions and Shell will execute a new service agreement,” Nexeo says, adding that it has also finalised a new products supply agreement with Shell Chemical to support this long-term relationship. These agreements, it continues, secure Nexeo’s ability “to operate long-term from
its current facility” and expand access to additional storage capacity on the property.
“This investment affirms our commitment to the West Coast region,” says Dan Matheny, Nexeo’s vice-president, industrial markets.
“I’m excited the service agreement will give us the opportunity to grow in the West Coast region beyond our current capability.”
Nexeo has also expanded its business relationship with ExxonMobil to include the distribution of Santoprene TPVs to customers from the North American wire and cable market. “Santoprene TPV materials are high-performance elastomers which combine the characteristics of vulcanised rubber with the processing ease of thermoplastics,” Nexeo says. This, it continues, enables “manufacturing flexibility, ease of processing and durability in a wide range of end-use applications”, with these particular TPVs
Meanwhile on the financial front, Nexeo reports that it has entered into an amendment to its Term Loan Credit Facility. The amendment, it says, “reflects a 50-basis points reduction in the interest rate to LIBOR plus 3.25 per cent from LIBOR plus 3.75 per cent and provides a prepayment premium equal to 1 per cent of the amount of the term loan applicable to certain repricing transactions occurring on or prior to 12 months from the effective date of the amendment”. Moreover, it continues, the amendment “will result in an estimated $3.2m reduction to the company’s annual cash interest expense for each of the next five years, while all other terms remain unchanged”.
The news comes shortly after Nexeo closed its 2017 books with a net income of $14.4m, up from a net loss of $8.4m in 2016. At the same time, the company’s sales and operating revenues more than tripled, rising from just under $1.1bn to reach a new figure of $3.6bn.
Established in 2011 following the spin-off of Ashland’s distribution business, Texasheadquartered Nexeo commands a portfolio of more than 22,000 products sourced from over 1,300 principals worldwide. Operating a network of 170 locations around the globe, its services more 26,700 customers from “a broad cross section of industries”, including the chemical manufacturing, oil and gas, coatings, adhesives, paints, personal care, automotive and healthcare sectors among others. HCB www.nexeosolutions.com
LeBaronBrown Industries has acquired a majority interest in American International Chemical (AIC), a Massachusetts-based distributor of speciality chemicals and ingredients to the North American food, pharma, personal care, biotech and industrial sectors. “The investment puts AIC in the best position for future growth, building upon the success of our dedicated AIC team,” says AIC president Mike Schrage, who will continue to manage the business that he founded in 1972. “We are excited about our future and the partnership with LeBaronBrown.”
Commenting on the news, LeBaronBrown co-founders Simon Brown and Matt LeBaron state: “We are thrilled by the addition of AIC to the LeBaronBrown platform. The company’s high-quality, multi-decade performance history and reputation as a premier specialty chemical and ingredients provider made it an ideal choice. We look forward to the opportunity to provide resources and support to the existing management team to fuel continued growth.”
Headquartered in New York, LeBaronBrown describes itself as “a private investment firm with a multi-decade orientation and a strategy to bring capital and resources to company management teams to enable growth over a multi-decade period”. This past June it acquired a majority shareholding in Charkit Chemical, a Connecticut-based chemicals distributor with a focus on the personal care, pharmaceutical, industrial, nutritional, metal and water treatment industries among others.
“We’re excited about the vision for Charkit’s future and thrilled to be partners with LeBaronBrown,” says Charkit president and founder Charlie Hinnant. “The investment in our company recognises the hard work our management team has put into successfully building Charkit over the last 35 years and also recognises the tremendous opportunities for growth that lie ahead for us.”
“Charlie and the team at Charkit have built a superb company over time,” LeBaron and Brown assert. “We are delighted at the opportunity to partner with Charkit and provide resources to support the ongoing
growth of the company. Building on the company’s operating excellence, we will be actively seeking complementary acquisitions in the specialty chemical distribution industry.” www.lebaronbrown.com www.aicma.com www.charkit.com
Texas-headquartered Vinmar has acquired a 90 per cent controlling stake in Turkish speciality chemicals distributor Veser Kimyevi Maddeler (VKM). Commanding annual revenues of around $50m, VKM operates four warehouses in Istanbul, Izmir and Adana and lists among its principals such companies as BASF, Huntsman, Kolb, Clariant and Givaudan. Having “built a strong distribution presence in polymers” across Europe and the US, Vinmar reports that it is currently “looking to build its capacity in the chemicals business” and thus describes the VKM acquisition as “an important step in expanding [its] product and market segment diversification.” www.vinmar.com
US private equity firm High Road Capital Partners has completed its acquisition of U-C Coatings, a distributor of speciality coatings and sealants to the North American wood and lumber markets. “U-C Coatings, with its market leadership in wood protection, is ideally positioned for expansion,” says High Road partner Jeffrey Goodrich. “Wood protection practices are progressively being adopted both in North America and other wood-producing regions. In addition, exports of North American hardwoods are growing. We see an immediate opportunity to expand U-C Coatings’ distribution globally.” www.highroadcap.com www.uccoatings.com
Caldic Thailand has signed an agreement with BASF for the local distribution of polyisobutene (PIB). “BASF is the global leader in PIB with over 70 years of experience in the manufacturing of PIB and in the understanding of its properties,” Caldic says. “PIB can be used in a wide range of applications in the Thai market, such as lube oils and greases, adhesive and sealants, medical tapes [and] mouse traps.” Netherlands-headquartered Caldic operates more than 40 sites across 17 countries. In terms of its south-east Asian operations, it last year named Nguyen Dinh Phung as the managing director of Caldic Vietnam. “Phung shares Caldic’s innovative and customer-focused
vision and with his appointment we are confident about the continuation and expansion of the Caldic Vietnam business,” it says. www.caldic.com
US-headquartered Horn has signed a deal with Brazil’s Nanovetores Technology for the nationwide distribution of aqueous-based microencapsulated active ingredients for the personal care and cosmetics industries. “There’s a big demand for clean label companies like Nanovetores in the US, where we are seeing a continually growing market of environmentallyconscience consumers,” says Horn Care Elements vice-president Chris Lesko. “Cindy Zhang, senior application scientist at Horn, has developed numerous formulas validating the efficacy and easy-to-work-with claims from Nanovetores. We are confident other formulators and chemists will also be impressed with the formulation-friendly characteristics of these actives. We have great expectations for the success of Nanovetores as Horn’s technical sales team introduces the unique technologies to formulation chemists throughout the US.” www.ethorn.com
BODO GOES FOR GROWTH Germany’s Bodo Möller Chemie has announced plans to finish 2018 with a turnover in excess of €100m for the first time in its history. Moreover, the company hopes to boost this to beyond €150m within five years, having embarked on “a massive expansion of its presence around the globe” and notched up sales increases of 20 per cent since 2015. Much of this future growth, the company reports, is set to come from such emerging new markets as e-mobility and 3D-printing.
“Not only in the US, but also in Asia and Europe, electric vehicles are gaining more and more importance and have different demands on production,” the company says. “We are in a very good position to further expand our worldwide business,” says CEO Frank Haug. “The need for specialised knowhow in the use of adhesives and sealants is growing. In addition to the application knowledge, our concept also provides the products and we perform an important role for the industry as a solution provider.” www.bm-chemie.com
Gordon Kropp and Stephen Coburn have joined US chemical distributor Sea-Land Chemical as supply chain analyst and customer service specialist, respectively. “At Sea-Land, the mission to provide an exceptional experience for our customers and business partners is engrained in our culture and has been for over 50 years,” says company president Jennifer Alstadt. “Gordon and Stephen bring industry-specific expertise that strengthens our commitment to these core values and delivering on customer promises. We are excited to have these two join our customer service and supply chain teams.” www.sealandchem.com
Switzerland’s DKSH reports that its chief information officer (CIO) Michael Hutab (below) now been made a member of the company’s group management team. “Our integrated and centralised IT platform has provided DKSH with a key competitive advantage for many years,” says CEO Stefan P Butz. “The appointment of Michael Hutab to the group management team highlights the importance that we place on digitisation. Over the past two years, we have come to appreciate Michael Hutab as a highly professional and pragmatic CIO. As a member of the group management team, he will continue to play a decisive role in the implementation of our group strategy.” www.dksh.com
AIRSAFE TRANSPORT TRAINING PO Box 347 Cloverdale, WA 6985, Australia
T (+61 8) 9277 6968 www.airsafe.com.au
Dangerous Goods by Air –Acceptance
• February 20-22 – Perth
• March 6-8 – Perth
• March 19-21 – Darwin
• March 21-23 – Adelaide
Dangerous Goods by Air –Refresher
• February 27 – Perth
• March 13 – Brisbane
• March 13 – Perth
• March 20 – Adelaide
• March 22 – Darwin
• March 28 – Perth
AMSA Full Acceptance
• March 12 – Brisbane
• March 19 – Adelaide
• March 23 – Darwin
BARRY TRAINING SERVICES
Sully Moors Road Sully CF64 5RP, UK
T (+44 1446) 743 913 www.barrytrainingservices.co.uk
ADR – Initial
• March 19-23 – Barry ADR – Refresher
• March 12-14 – Barry
CAMEON PO Box 17345 Edinburgh EH12 1DJ, UK T (+44 131) 334 1929 www.cameon.com
Dangerous Goods Safety Adviser (DGSA)
• February 26-March 2 –Manchester
Dangerous Goods by Air
• April 16-18 – Manchester
Dangerous Goods by Road –Upgrade
• April 19 – Manchester
Dangerous Goods by Sea –Upgrade
• April 20 – Manchester
DANGEROUS GOODS COUNCIL PO Box 7325 York, PA 17404, USA T (+1 717) 848 8840 www.hazshipper.com
49 CFR & International AirCertification
• March 12-14 – Atlanta
• April 9-11 – Newark
• April 16-18 – Madison
49 CFR – Certification
• March 12-13 – Atlanta
• April 9-10 – Newark
• April 16-17 – Madison
International Air – Recertification
• March 14 – Atlanta
• April 11 – Newark
• April 18 – Madison
DANGO TRAINING SERVICES
169 Affric Road Glenrothes KY7 6XA, UK T (+44 1592) 748234 www.dangerousgoodstrainingdts. co.uk
Dangerous Goods by Air
• February 19-21 – Aberdeen
• March 5-7 – Aberdeen
• March 12-14 – Aberdeen
• March 19-21 – Aberdeen
• April 9-11 – Aberdeen
Dangerous Goods by Sea
• February 22-23 – Aberdeen
• March 8-9 – Aberdeen
• March 15-16 – Aberdeen
• March 22-23 – Aberdeen
• April 12-13 – Aberdeen
DGI TRAINING CENTER
1060 El Camino Real, Suite B Redwood City, CA 94063-1645, USA
T (+1 650) 306 8450 www.dgitraining.com
IATA Initial
• February 28-March 1 –Philadelphia
• March 6-7 – Chicago
• March 21-22 – San Francisco
• April 4-5 – Atlanta
IATA Recurrent
• February 26 – Philadelphia
• March 5 – Chicago
• March 19 – San Francisco
• March 26 – Los Angeles
• April 3 – Atlanta
IMDG Recurrent
• March 28 – Los Angeles
• April 18 – Detroit
Ground Transportation (49 CFR) Initial
• March 12-13 – Las Vegas
• April 9-10 – Los Angeles Ground Transportation (49 CFR) Recurrent
• February 27 – Philadelphia
• March 20 – San Francisco
• March 27 – Los Angeles
• April 17 – Detroit Multimodal Initial (49 CFR/IATA/IMDG)
• March 12-16 – Las Vegas
• April 9-13 – Los Angeles Multimodal Recurrent (49 CFR/ IATA/IMDG)
• March 26-28 – Los Angeles
• April 16-18 – Detroit Ground/Air Shipping - Initial (49 CFR/IATA)
• February 28-March 2 –Philadelphia
• March 21-23 – San Francisco Ground/Air Shipping - Recurrent (49 CFR/IATA)
• February 26-27 – Philadelphia
• March 19-20 – San Francisco
• March 26-27 – Los Angeles
• April 16-17 – Detroit
DGM TRAINING INSTITUTE 1813 Greens Road Houston, TX 77032, USA T (+1 281) 821 0500 www.dgm-usa.com
IATA/ICAO Dangerous Goods by Air – Initial
• March 5-7 – Houston
• March 12-14 – Atlanta
• March 19-21 – Miami
• April 9-11 – Atlanta IATA/ICAO Dangerous Goods by Air – Recurrent
• March 8-9 – Houston
• May 10-11 – Houston
• March 13-14 – Atlanta
• April 10-11 – Atlanta
• April 9-12 – Houston
IMDG Code - Initial
• February 19-20 – Atlanta
• March 19-20 – Houston
• April 23-24 – Atlanta
• April 23-24 – Houston
IMDG Code – Recurrent
• February 20 – Atlanta
• March 21 – Houston
• April 24 – Atlanta
• April 25 – Houston
49 CFR Dangerous Goods by Road – Initial
• March 26-27 – Houston
49 CFR Dangerous Goods by Road – Recurrent
• March 28 – Houston
Multi-Modal (Air, Road and Sea)
– Initial
• February 19-22 – Houston
• March 12-15 – Houston
• April 16-19 – Houston Transporting Radioactives
• April 12 – Houston Transporting Batteries
• April 26 – Houston
General Awareness
• March 19 – Atlanta
2nd floor, 16 Black Friars Lane London EC4V 6EB, UK T (+44 20) 7488 0801
TankAssessor
• February 19-23 – Rotterdam
• March 5-9 – Hannover
• March 19-23 – Pérouges TankIntro
• April 9-10 – London
FREMANTLE TRAINING & TRANSPORT Rathmore Lodge Rathmore Road Torquay, Devon TQ2 6NY, UK T (+44 1803) 293344
www.fremantletraining.co.uk ADR Driver Training
• March 12-16 – Bristol
• March 19-23 – Plymouth
ADR Driver Training – Tanks & Class 3 Refresher
• April 23-24 – Bristol
• April 25-26 – Plymouth
GLOBAL TRANSPORT TRAINING
54 Norristown Road Blue Bell, PA 19422, USA
T (+1 215) 283 0983 www.gttstraining.com
Multi-Modal - IATA/IMDG/DOT 49 CFR – Initial
• February 26-March 2 –Baltimore
• February 26-March 2 –Houston
• March 5-9 – Atlanta
• March 12-16 – Indianapolis
• March 12-16 – Los Angeles
• March 19-23 – Newark
• March 26-30 – Miami
• April 2-6 – Boston
• April 9-13 – New York
GULF CENTRE FOR AVIATION STUDIES (GCAS)
PO Box 94449
Abu Dhabi, UAE T (+971 2) 494 2355 www.gcas.ae
IATA DGR - Category 6 – Initial
• April 22-29 – Abu Dhabi
Dangerous Goods RegulationsCategory 6 – Recurrent
• March 26-29 – Abu Dhabi
11380 NW 34th Street
Doral, FL 33178, USA
T (+1 305) 471 0561 www.hazmatcom.com
Multimodal General Awareness
• February 21 – Miami
• March 21 – Miami
IATA Air Initial
• March 6-8 – Miami
• April 17-19 – Miami
IATA Air Recurrent
• February 20 – Miami
• March 13 – Miami
IMDG Ocean Initial
• March 14-15 – Miami
• April 11-12 – Miami
IMDG Ocean Recurrent
• February 22 – Miami
• March 22 – Miami
Lithium Batteries (IATA/IMDG)
• March 20 – Miami
12 Kimball Hill Road Hudson, NH 03051-3915, USA
T (+1 603) 882 1112
www.hazmateam.com
US DOT (49 CFR) Ground Transportation – Initial
• April 4-6 – Hudson
US DOT (49 CFR) Ground Transportation – Intermediate Refresher
• March 20-30 – Hudson
US DOT (49 CFR) Ground Transportation – Advanced Refresher
• February 22 – Hudson
• April 10 – Hudson
DOT Manifesting and Function Specific (49 CFR) Ground Transportation
• March 14 – Hudson
International Air Shipping –Initial
• March 6-8 – Hudson International Air Shipping –Refresher
• February 26-27 – Hudson
• April 23-24 – Hudson
Water Transportation of Dangerous Goods (IMDG) – Initial
• March 1-2 – Hudson
OSHA Emergency Response Operations – Initial/Refresher
• March 27 – Hudson
OSHA Emergency Response Technician – Initial
• March 19-21 – Hudson
OSHA/EPA Emergency Response – Initial
• March 19-23 – Hudson
Confined Space Entrant/ Attendant
• April 16 – Hudson
Confined Space Rescue
• April 17 – Hudson
SINGAPORE
146A Changi Road Singapore 419726
T (+65) 6542 5539 www.haz-mat-training.com
IATA Dangerous Goods Regulations (Initial)
• March 19-23 – Singapore
IATA Dangerous Goods Regulations (Recurrent)
• March 1-2 – Singapore
• March 22-23 – Singapore
• April 18-19 – Singapore
IATA Dangerous Goods Regulations (Awareness)
• March 19 – Singapore
IMDG Code Dangerous Goods By Sea
• February 27-28 – Singapore
• April 16-17 – Singapore
Chemical Safety Awareness
• March 29 – Singapore
SCDF Hazmat Transport Driver Permit
• March 28 – Singapore
• April 11 – Singapore
TRANSPORT ASSOCIATION
800 Place Victoria, PO Box 113 Montreal H4Z 1M1 Quebec, Canada.
T (+1 514) 874 0202 www.iata.org/training
Dangerous Goods Regulations (DGR) – Initial, Category 6
• April 2-6 – Lagos
• April 2-6 – Singapore
• April 9-13 – Geneva
• April 16-20 – Brussels
Dangerous Goods Regulations (DGR) – Recurrent, Category 6
• February 27-March 1 – Rome
• March 26-28 – Amsterdam
• April 24-26 – Stockholm
Dangerous Goods Regulations (DGR) – Instructor Refresher
• February 28-March 2 – London
• April 4-6 – Singapore
Professional Skills for DGR Instructors – Categories 1,2,3,6
• February 26-March 2 – Miami
• March 19-23 – Singapore
• April 23-27 – Geneva Instructional Techniques for DGR (for categories 4, 5, 7, 8, 9, 10, 11, 12)
• February 19-23 – Rome
• April 16-20 – Geneva
Shipping Lithium Batteries by Air
• February 26-27 – Singapore
• March 27-28 – Miami
LION TECHNOLOGY
570 Lafayette Road Sparta, NJ 07871-3447, USA
T (+1 888) 546 6511 www.lion.com
Multimodal Hazmat Shipper Certification (49 CFR/IATA/IMDG)
• February 20-23 – Charlotte
• March 6-9 – Houston
• April 10-13 – Los Angeles
• April 10-13 – Las Vegas
• April 16-19 – Denver
Hazmat Ground Shipper Certification (49 CFR)
• February 20-21 – Charlotte
• February 26-27 – Nashville
• March 6-7 – Houston
• March 14-15 – Dallas
• March 19-20 – Little Rock
• April 10-11 – Los Angeles
• April 10-11 – Las Vegas
• April 16-17 – Sacramento
• April 16-17 – Denver
Hazmat Ground Shipper Certification - Recurrent
• April 25 – Sparta, NJ
Hazmat Air Shipper Certification (IATA)
• February 22 – Charlotte
• February 28 – Nashville
• March 8 – Houston
• March 16 – Dallas
• April 12 – Los Angeles
• April 12 – Las Vegas
• April 18 – Denver
Hazmat Vessel Shipper Certification (IMDG)
• February 23 – Charlotte
• March 9 – Houston
• April 13 – Los Angeles
• April 13 – Las Vegas
• April 19 – Denver
Hazardous Waste in California
• April 9-10 – San Diego
• April 12-13 – Ontario
• April 16-17 – San Jose
• April 19-20 – Sacramento
Complete Environmental Regulations
• March 5-6 – Sparta, NJ
• March 15-16 – Salt Lake City
Blackwell Drive
Springwood Industrial Estate Braintree, Essex CM7 2QJ, UK
T (+44 1376) 552999
www.novadata.co.uk
ADR Core, Packages
• March 12-15 – Braintree
• April 9-12 – Braintree
ADR Core, Packages & Tanks
• March 12-16 – Braintree
• April 9-13 – Braintree
ADR Tanks Add-On Course
• March 15 – Braintree
• April 12 – Braintree
Lower William Street Southampton SO14 5QE, UK
T (+44 23) 8033 1551
www.oilspillresponsetraining.com
Oil Spill Clearance –
On-Scene Commander (IMO Level 2)
• March 19-23 – Singapore
• April 9-13 – Southampton
On-Scene Commander – AsiaPacific (IMO Level 2)
• April 10-12 – Hong Kong
• April 17-19 – Bandar Seri
Begawan
On-Scene Commander –Americas (IMO Level 2)
• February 26-March 2 –Fort Lauderdale
Oil Spill Response Management (IMO Level 3)
• February 26-March 1 –Singapore
• March 5-8 – Southampton
Oil Spill Response Refresher (IMO 1 to 3)
• April 4 – Southampton
Unit 006, Solent Business Centre
Millbrook Road West Southampton SO15 0HW, UK T (+44 23) 8070 2576 www.roadsafeeurope.com
ADR Initial
• March 19-23 – Southampton
• April 23-27 – Southampton
ADR Refresher
• March 5-7 – Southampton
• April 4-6 – Southampton
9 Langley House
Wheatcroft Business Mark Landmere Lane, Edwalton Nottingham NG12 4DG, UK T (+44 115) 965 1888
www.safeware-int.com
Transport of Dangerous Goods Awareness
• March 7 – Nottingham
EU Chemical Regulatory Compliance in a Nutshell
• March 8 – Nottingham
GHS Professional Refresher
• April 11 – Nottingham
TECHNOLOGY CENTER Security and Emergency Response Training Center PO Box 11130 Pueblo, CO 81001, USA T (+1 719) 584 0584 sertc.org
HazMat/WMD Technician for Surface Transportation
• March 5-16 – Pueblo
Tank Car Specialist
• February 26-March 2 – Pueblo
• March 19-23 – Pueblo
• April 2-6 – Pueblo
• April 16-20 – Pueblo Tank Car Specialist – Advanced
• March 26-30 – Pueblo
Crude-by-Rail Response
• March 6-8 – Pueblo
• March 20-22 – Pueblo
• March 27-29 – Pueblo
• April 3-5 – Pueblo Transportation Container Loading and Unloading Emergency Response
• April 25-27 – Pueblo Highway Emergency
• March 5-9 – Pueblo
• March 19-23 – Pueblo
Highway Emergency Response Specialist – Advanced
• March 26-30 – Pueblo
Leadership & Management of Surface Transportation Incidents
• March 12-16 – Pueblo
Tactical Hazardous Materials Operations for Surface Transportation
• April 16-20 – Pueblo UPS
55 Glenlake Parkway NW Atlanta, GA 30328, USA
T (+1 800) 634 5656
www.upshazmatseminars.com
49 CFR & IATA Dangerous Goods Seminar
• March 6-8 – San Diego
49 CFR Dangerous Goods Seminar
• March 6-7 – San Diego
• April 4-5 – Edison, NJ Lithium Batteries
• February 21-22 – San Antonio
The World Economic Forum (WEF) meeting in Davos, Switzerland was held last month for the 45th time. Its slogan is: ‘improving the state of the world’. This is not an easy task, because improving what is created fundamentally wrong makes, in my humble opinion, things ‘wronger’.
Over the course of a week, top politicians - even the President of the USA, Donald Trump attended - and a mixed crowd of business people, celebrities, NGO executives and journalists were there to talk about what to do to ensure economic growth can be ‘inclusive’. But what do they mean by inclusive growth? And why is growth necessary? I shall try to explain this from a systems, scientific viewpoint.
Growth in organisms, people, plants or animals, is possible from the beginning of life’s conception to a certain age and then decline starts to change growth into decay, because the energy stored in life is needed to feed new forms of organisms in order to continue life. Growth is therefore limited by time. Growth is necessary to create the ability for organisms to ensure survival of a species. On the top of growth, an organism is able to procreate, produce seeds to ensure the sustainability and continuity of life through offspring.
In systems science we speak about a realm of life which we find between and within borders of functionality, i.e. between order and chaos and which can only be sustained by constant learning and adaptation. At this time we observe that the economic and financial systems that we have created contradict this natural method to sustain life. In fact they are driving systems into chaos because they refuse to learn and adapt.
Inclusive growth is impossible because these man-made systems cause exactly the opposite. We see that in our economies and
financial sectors where the income gap is growing and causing an ‘exclusive’ growth, only for those who can take advantage of our so-called linear economic system. Inclusive growth can be called a linear solution that has to fit a linear financial system, which can only thrive in separation but not in inclusion of everyone and everything.
Therefore I believe that our world leaders are looking in the wrong places and have politicised business, which leads to an increased number of states and countries being run by oligarchs who are getting less interested in including the people. In fact, they are afraid of opposition and therefore information that contradicts their noninclusive agenda is negated or suppressed.
Conclusion: inclusive growth is an oxymoron. Growth always needs to be balanced by decline to sustain life on earth. Our linear economic and financial systems do not fit in a universe which is non-linear. So, I hope that our leaders, celebrities and everyone involved will read this column and start using new sciences such as cybernetics and use systems thinking. We must understand ‘relationships’, ‘interdependence’ and ‘feedback that needs to be fed back into living systems in order to learn’. We can then change the WEF objective into ‘inclusive balance’.
This is the latest in a series of articles by Arend van Campen, founder of TankTerminalTraining. More information on the company’s activities can be found at www.tankterminaltraining.com. Those interested in responding personally can contact him directly at arendvc@tankterminaltraining.com.
Shipping and storing (petro)chemical products requires top-notch quality assurance. It is absolutely essential to ensure the quality, safety and sustainability of every single step in the logistical chain. Which in turn requires reliable inspection data and robust assessment procedures.
But can quality assurance also be easy and straightforward?
At Pharox, we are fully focused on delivering the most efficient and user-friendly quality assurance and vetting database solutions. The result? A proven track record in fully managed end-to-end solutions, for some of the biggest names in the industry.
Find out more at www.pharoxassurance.com
Pharox =
• industry expertise and a full focus on assurance and vetting database solutions
• fully managed end-to-end solutions: from design, development and implementation to hosting, maintenance and support
• secure, user-friendly access to reliable and up-to-date inspection data
(MSC), a world leader in global container shipping, has implemented IMDG Code e-learning as a core element in its global training programme to ensure its staff are up to date with the International Maritime Dangerous Goods (IMDG) Code.
MSC, a privately owned, global organisation operating a network of over 480 offices in 150 countries, employs a team of more than 60,000 people. Its fleet of 460 container vessels has an aggregate capacity of some 2.75m TEU and the company’s extensive network of sailing schedules spans 200 routes, calling at 315 ports. This enables MSC to deliver all types of cargo, safely and
swiftly, almost anywhere in the world. Among its many cargo specialisms, MSC is a highly experienced expert in the carriage of packaged chemicals.
MSC staff in offices around the globe have first-hand experience of local requirements and regulations regarding chemicals/ dangerous goods in ports worldwide. Their focus is on ensuring that the highest level of safety and environmental standards are met. MSC also has a specialist chemical support department based at its home port in Antwerp, Belgium. It is this department that ensures shipments meet the stringent compliance requirements of the IMDG Code, and it provides any necessary contingency plans en route.
Specialist chemists ensure the chemical cargo (and the box it sits next to) is stowed and shipped in keeping with the necessary legal and safety requirements.
MSC was looking for an IMDG Code training solution that could be rolled out globally across its network of offices. The company purchased the SCORM version of IMDG Code e-learning to allow students to train using the company’s learning management system. The project team implemented the Amendment 37-14 version last year and will be implementing the Amendment 38-16 training programme over the next few months.
For several years, MSC has been using Exis Technologies’ Hazcheck compliance system to check shipments against the IMDG Code. It was perhaps natural that it should opt for the IMDG Code e-learning system developed by Exis Technologies in collaboration with the International Maritime Organisation (IMO). The program is now used by six of the ten largest container lines.
This program utilises a wide range of the IMDG Code e-learning courses available, to ensure that staff are receiving the most appropriate training for their job role. In MSC’s case these include the 49 CFR training module, which ensures staff understand the different provisions relating to packaged dangerous goods being shipped into and out of the US.
To date, the company has successfully trained 21,000 people working across the worldwide MSC network. This includes agents, fleet operators and terminals.
Dirk Vande Velde, corporate senior director for MSC Chemical Transports, has been working closely with Exis Technologies to implement IMDG Code compliance solutions for many years. He comments: “For some time now, we have been working very closely with Exis to replace our existing training with the Exis Dangerous Cargo training across our global network. We have been really pleased with how the relationship has developed, how well they have understood the complex needs of our business, and how their specific training tools have performed in terms of our requirements. We look forward to continuing the implementation of the current training programme.” HCB
Further information about IMDG Code e-learning is available from www.imdge-learning.com.
FEBRUARY 20-22, LONDON
Annual week of meetings, lunches, conferences and seminars in London www.ipweek.co.uk/_nocache
FEBRUARY 25-27, HAMBURG
34th annual conference on dangerous goods transport (German language) www.ecomed-storck.de/Veranstaltungen/34Internationale-Gefahrgut-Tage-HamburgVeranstaltung-Hamburg-25-27-02-2018.html
FEBRUARY 28-MARCH 1, RUNCORN Conference and exhibition on hazardous area operations www.hazardexonthenet.net/event. aspx?EventID=4724
MARCH 4-6, TAMPA
Bi-annual meeting and tradeshow of the Petroleum Packaging Council www.ppcouncil.org/upcoming-meetings.php
MARCH 7-8, LISBON
Summit on developments in the regional LPG market www.wplgroup.com/aci/event/lpg-europesummit/
MARCH 11-13, NEW ORLEANS
AFPM’s annual meeting for refiners and marketers www.afpm.org
MARCH 13-15, DALLAS 12th global conference on air cargo www.iata.org/events/wcs/pages/index.aspx
MARCH 13-15, SÃO PAULO
International exhibition on intermodal logistics,
cargo transport and international trade, focusing on Latin America www.intermodal.com.br/en
MARCH 13-15, LONDON
Triennial conference and exhibition for the European oil spill response sector www.interspill.org
MARCH 14-15, CAPE TOWN
Conference on the prospects for LPG market growth in Africa www.argusmedia.com/events/argus-events/ europe/argus-africa-lpg/home/
MARCH 15-16, SYDNEY
Conference and workshops on business continuity issues www.marcusevans-conferences-australian.com
MARCH 19-21, MELBOURNE
Workshop on optimising dangerous goods management processes www.marcusevans-conferences-australian.com
MARCH 20-22, SHANGHAI
Fifth annual exhibition for the Asian intermodal sector www.intermodal-asia.com
MARCH 20-22, AMSTERDAM
Chemical supply chain and logistics conference logichem.wbresearch.com/
MARCH 20-22, ROTTERDAM
The main annual exhibition and conference for the European tank terminal industry www.easyfairs.com/stocexpo-europe-2018/ stocexpo-europe-2018/
MARCH 20-23, PARIS
Annual transport event, including Dangerous Goods Logistics Pavilion www.sitl.eu/en/Home/
World LNG Series: Americas Summit
MARCH 20-23, HOUSTON
16th annual convention for LNG buyers and sellers lngamericas.cwclng.com
MARCH 22, NORTHAMPTON
Annual AGM and seminar of the British Association of Dangerous Goods Professionals www.badgp.org/event-2685411
MARCH 25-27, SAN ANTONIO
AFPM’s annual International Petrochemical Conference www.AFPM.org
MARCH 26-29, KUWAIT
Sixth annual meeting on crisis resilience in the Middle East crisisandriskmanagement.iqpc.ae/ NISTM
MARCH 27-29, ORLANDO
National Institute for Storage Tank Management’s 20th annual international aboveground storage tank conference and trade show www.nistm.org
APRIL 4-5, PROVIDENCE, RI
Meeting for code coordinators and others subject to Responsible Distribution www.nacd.com/meetings/workshops/
APRIL 8-12, PORTLAND, OREGON
Meeting for industry, regulators and enforcers to improve commercial vehicle safety cvsa.org/eventpage/events/cvsa-workshop/
APRIL 15-17, TORONTO
70th annual conference and exhibition of the National Tank Truck Carriers www.tanktruck.org/meetings/
Date Location Vehicle Type Substance Details Source
1/11/17 Lumberton, truck acid, base Tractor-trailer overturned on I-95, cause unknown; crash caused leak of hydrofluoric acid, sodium hypochlorite WRAL N Carolina, US as well as diesel fuel; spilt product reacted, causing chemical cloud; no evacuations necessary
2/11/17 Ottumwa, road tanker phosphoric Tank truck with 8,000 gal (30 m3) phosacid rolled on Highway 63, causing spill; local hazmat team were on Ottumwa Iowa, US acid training day at Iowa DPS but arrived back in time to organise offloading of remaining acid Courier
3/11/17 Port Everglades, road tanker
Worker at tank repair facility was badly injured when tanker exploded as he was repairing faulty valve; WPLG Florida, US state fire marshal investigating cause
6/11/17 Meacham, truck corrosive Driver lost control of truck on icy road surface on I-84; truck hit median, rolled over, spilling load of KTVZ Oregon, US tetramethyl ammonium hydroxide; half-mile exclusion zone imposed; road closed for eight hours
7/11/17 Baton Rouge, tank container MAO Leak of methylaluminoxane from tank container caused fire at Albemarle Process Development site; WAFB Louisiana, US leak stopped, fire extinguished within 15 minutes; no off-site impact; investigation underway
8/11/17 Bhavnagar, road tanker naphtha Road tanker with “naphtha chemical” collided head-on with bus on Bhavnagar-Ahmedabad highway; Times of Gujarat, India tanker caught fire, exploded; five killed, including two on tanker; ten others injured India
9/11/17 Daqing, road tanker oil Road tanker caught fire on expressway, apparently after leak ignited; responders found 100-metre spill, CBS Heilongjiang, China also on fire; blaze extinguished in 30 minutes without injury
9/11/17 Manchester, road tanker propane Car collided with propane tanker making home delivery, causing fire and explosion; tanker driver pulled car AP New York, US driver from burning vehicle; car driver suffered severe burns; fire department extinguished blaze
9/11/17 New Enterprise, road tanker fuel Bedford Valley Petroleum tank truck ran off road, rolled over; some 800 gal (3,000 litres) of 2,100-gal load WJAC Pennsylvania, US leaked into creek leading to reservoir; cleanup expected to take two weeks
12/11/17 Lubudi, freight train fuel 13-car oil train running from Lubumbashi to Luena derailed, plunged into ravine, catching fire; at least 33 The Lualaba, DR Congo people illegally riding on train died, many more injured National
13/11/17 Cornville, road tanker heating oil Dead River Oil tank truck rolled over after driver lost control; some 1,000 gal (3,800 litres) No 2 home central Maine, US heating oil leaked near stream; booms, absorbent pads deployed; remaining cargo transferred maine.com
14/11/17 Obodore, road tanker gasoline Road tanker overturned, spilling gasoline and trapping scores of people in nearby homes; other residents Daily Lagos, Nigeria erected barriers to stop traffic and prevent ignition of spill Trust
17/11/17 nr Pagoh, road tanker diesel Road tanker with 32 m3 diesel overturned on North South Expressway, causing major disruption during The Star Johor, Malaysia cleanup of spill; authorities blamed brake failure; sawdust applied to soak up spill; remaining fuel transferred (KL)
22/11/17 Annawan, road tanker ethanol Tank truck with ethanol crashed on I-80, spilling some 8,000 gal (30 m3); vehicle caught fire, KWQC Illinois, US prompting closure of road; cleanup expected to take seven days; no injuries reported
24/11/17 nr Owerri, road tanker kerosene Road tanker overturned, exploded on Njaba bridge after rolling backwards on incline; fire engulfed bus Nigeria Imo, Nigeria behind tanker; at least 30 people killed in inferno; other reports suggested collision Today
27/11/17 Lakeland, freight train sulphur Nine cars of CSX train derailed, four with molten sulphur; some leaked, caught fire; shelter-in-place advised ABC Florida, US during response by local hazmat and fire teams and CSX personnel
1/12/17 Melbourne,
ON THE MORNING of 21 October 2016 a driver from Harcros Chemicals arrived at the MGPI Processing facility in Atchison, Kansas with a load of 30 per cent sulphuric acid. He was met by an MGPI employee, who unlocked the cam lever dust cap from the sulphuric acid fill line. The MGPI employee then returned to the control building while the driver connected his hose to the line and began to discharge his cargo.
Within a few minutes a cloud of greenishyellow gas started pouring from the site’s sodium hypochlorite tank; three MGPI employees in the control room and the driver were all affected by the fumes and had to flee the area.
Investigation by the US Chemical Safety Board (CSB) found that the driver had hooked the hose up to an adjacent fill line, the dust cap of which was unsecured; this resulted in 4,000 gal (15,000 litres) of sulphuric acid being discharged into a tank containing 5,850 gal (22,150 litres) of sodium hypochlorite, causing a reaction that generated chlorine gas and other compounds.
As a result of the incident, nearly 150 people needed medical attention and six had to spend days in hospital.
On the face of it, this might seem like a classic ‘human factors’ incident: miscommunication between the site employee and the driver left the driver to choose between two available fill lines. Why did the site employee not stay to check that the operation was being carried out correctly? Why did the driver not check to see which of the two available lines was the right one? Why had someone left the second dust cap
unlocked? Or, as CSB found, why had the dust cap on the sodium hypochlorite line not been replaced? It had a missing split ring, which meant it could not be secured by a padlock.
In recent years, CSB’s investigations have repeatedly highlighted examples where systems and procedure have been designed in such a way to allow accidents to happen through human error. At the MGPI plant, the two fill lines were only 18 inches (45 cm) apart yet they were not identified in any way that would enable the driver to tell which line to connect to. Indeed, the plant had three other fill lines (for acetic anhydride, propylene oxide and sodium hydroxide) at the same point and none of these was immediately identifiable.
CSB’s investigation into the MGPI incident resulted in recommendations to both MGPI and Harcros Chemicals, as well as the Atchison County Department of Emergency Management. CSB recommends that MGPI evaluate the chemical transfer equipment at its site and install appropriate engineering safeguards to prevent and mitigate an unintended chemical reaction, release or spill during bulk unloading. The recommendation is equally applicable to any facility accepting bulk deliveries of differing chemicals:
“Where feasible, install safeguards, such as alarms and interlocks, to prevent personnel
from opening the incorrect chemical transfer valves during deliveries. In addition, install mitigation measures to automatically shut down the transfer of chemicals into the facility based on process deviations or abnormal conditions (e.g. pressure, temperature, flow or level indications; gas detection).”
CSB also recommends that Harcros Chemicals establish a refresher training programme to ensure that its drivers know where to find the various emergency shut-off devices on their tank truck, when to use them and their respective effectiveness in stopping the flow of chemicals during an emergency.
CSB was also concerned that the driver involved in the MGPI incident was not equipped with (or did not have time to put on) appropriate protective equipment. Harcros was asked to evaluate the respiratory hazards associated with chemical unloading at customer sites.
Similarly, CSB recommended that MGPI commission an independent engineering evaluation of the building at the site of the incident and its ventilation system and to evaluate whether design changes and controls are needed to protect occupants in the event of an external chemical release. The Board was concerned that chlorine gas had entered the building and that those inside were unable to access emergency respirators.
CSB was also concerned at the level of response provided by Atchison County Department of Emergency Management; its list of recommendations also encouraged the Department to improve the extent of training and coordination with businesses handling hazardous materials. Its recommendations note that grants are available through the Hazardous Materials Emergency Preparedness (HMEP) programme to help fund training and pre-planning activities.
Other key lessons for fixed facilities to emerge from the incident, CSB says, are:
• The need to apply the hierarchy of controls when evaluating safeguards to prevent inadvertent mixing of incompatible chemicals
• The need to ensure that fill lines for incompatible materials are physically
separate, ideally with acids and bases being unloaded in separate areas
• The benefits of working with chemical distributors to select hose couplings and fill line connectors with uniquely shaped or colour-coded fittings for each class of chemical
• The benefits of working with chemical distributors to develop agreed procedures for unloading and emergency operations, particularly in terms of clearly defining responsibilities.
“Delivery and unloading operations may be perceived as simple compared to other processes at chemical facilities, but because these activities can involve large quantities of chemicals, the consequences of an incident can be severe,” says CSB chair Vanessa Allen Sutherland. “Our case study on the MGPI incident stresses that facilities must pay careful attention to the design and operation of chemical transfer equipment to prevent similar events.”
According to a study by the National Association of Chemical Distributors (NACD), more than 39.9m tonnes of product were delivered to customers every 8.4 seconds in 2016 – resulting in many opportunities for incidents like the one at MGPI to occur.
“Because these deliveries are so common,
CSB strongly urges the managers of facilities and distributors to review and adopt the key lessons from our case study, and work together to prevent future incidents like the one at MGPI,” Sutherland adds.
According to incident data provided by the Pipeline and Hazardous Materials Safety Administration (PHMSA), unloading incidents involving hose connections to incorrect tanks happen frequently. Most often these involve compatible materials and result in tank overfills. Nevertheless, PHMSA has identified eight incidents similar to that at the MGPI site since 2014, which resulted in a total of 44 injuries and the evacuation of nearly 850 people. Indeed, PHMSA investigated a very similar incident in 2015 in Holly Hill, Florida, when sodium hypochlorite was delivered into a sulphuric acid tank.
Clearly the incident at the MGPI Processing plant was far from unique. CSB’s investigation and recommendations therefore have much wider relevance. As part of CSB’s efforts to spread awareness of the issues it has prepared a safety video, Mixed Connection: Toxic Result, featuring an animation of the incident and interviews with CSB and PHMSA personnel. The video is freely available via YouTube and on the CSB website at www.csb.gov/videos/ mixed-connection-toxic-result/. HCB
(CDI) provides over 70 multinational chemical companies with reliable inspection data on oil and gas tankers, terminals and logistic services providers, using three separate assessment database systems. These are based on extensive assessments by accredited inspectors, which may take up to five days and which cover a vast range of details.
“However, as good as our data is, it’s only going to be of use if it’s available 24/7”, says CDI general manager Captain Howard Snaith. “Our members conduct round-the-clock activity in all major ports around the world. They rely on our data for fast and reliable risk assessments.” Which in turn depends on a robust database, capable of handling large volumes of requests from hundreds of users with different requirements and access rights.”
Over the years, CDI has found Pharox Assurance to be a partner capable of delivering end-to-end solutions with high availability rates and user-friendly, accessible formats. “The first database they built for us focused on terminals and packed cargo. We were so pleased with their performance that we decided to transfer our existing CDI-M database to Pharox as well,” Snaith says.
This decision wasn’t taken lightly, as Snaith emphasises: “Transferring an existing database containing thousands of active inspection reports, users, access rights and project files is a huge task, with a lot of potential for things to go wrong. And we
couldn’t afford any downtime - the transition had to be 100 per cent flawless.”
Despite the complexity of the task, CDI was willing to invest in the transition because “we wanted an enhanced, more user-friendly database and a high availability rate. Which is exactly what Pharox delivered. They developed a quick, slick and user-friendly interface and have consistently provided an extremely high level of availability and security,” says Snaith.
Over the years, CDI and Pharox Assurance have continued to work together, for example
on regular updates. “We are in a constant process of review and improvement, which is made easier by the fact that Pharox is fully focused on this type of solution,” Snaith adds.
“It’s very efficient to work with a partner with an insider’s knowledge of the chemical industry. Pharox is quick to grasp what we need and is often able to point to similar solutions they have developed for other clients. It makes life a lot easier for us.”
Pharox Assurance not only provides this service for CDI but also for those who have to use the CDI database, as well as the Oil Companies International Marine Forum (OCIMF) SIRE and TMSA databases. It can provide database systems for companies that need to manage their vessel vetting programmes and all those that rely on health, safety and quality integrity. It also provides interfaces to allow internal vetting systems to integrate CDI Marine and Terminals and SIRE/TMSA database interfaces. “This way it is possible to collect report information from the [inspection] database systems and use them in your own proprietary system,” Pharox says. HCB www.pharoxassurance.com
The Chemical Distribution Institute (CDI) has published a new book, Chemical Tanker Operations for the STCW Advanced Training Course. The culmination of almost three years’ work, the publication is a comprehensive guide to chemical tanker cargo operations and an essential reference point for serving officers, chemical tanker ship operators and managers, as well as those undertaking advanced training as required by the STCW Convention.
“CDI’s members felt it was essential to draw upon their collective expertise to produce a guide that would not only support the continuity of practical knowledge within the wider chemical tanker industry, but assist candidates studying for the Advanced Training for Chemical Tanker Cargo Operations (STCW) course,” says CDI general manager
Captain Howard Snaith.
The book is written both as an aide-memoire for service officers and managers and as a consolidated study guide for those undertaking advanced training for chemical tanker operations. It covers chemical tanker design and construction, the various applicable regulations, safety issues,
pollution response, cargo handling equipment and practices, cargo compatibility, ballast water systems and wall wash testing.
The book is priced at £225 for hard copies and £75 for the student e-book version. It is available via Witherby Publishing; full details can be found at www.witherbyseamanship.com/ chemical-tanker-operations-for-the-stcwadvanced-training-course.html.
The Cargo Incident Notification System (CINS) and the International Group of P&I Clubs have published an updated version of their Guidelines for the Carriage of Calcium Hypochlorite in Containers. This third edition includes updated references to package limits and gives greater clarity in its application.
“The Guidelines can essentially be considered ‘IMDG Code-Plus’ precautions, insofar as they include selected provisions from the IMDG Code plus additional precautions, consistent with the science basis established in 1999,” says CINS. The new version can be downloaded from the CINS website, www.cinsnet.com.
The Steel Tank Institute (STI) has published revised editions of its standards SP001 on the inspection of aboveground storage tanks (ASTs) and SP031 on the repair of shopfabricated ASTs. The new editions include information on the inspection of asphalt tanks, steel diked tanks and concrete-encased shop-fabricated tanks. There are also revisions to the monthly and annual checklists and the safety considerations and welding sections of the standards.
STI’s SP001 certification classes, due to be held over the course of the year, will reference the revised standards. Full information can be found on the STI website, www.steeltank.com.
Transport Canada has circulated a guidance document – You’re Not Alone! – that gives advice to local emergency planners, firefighters, paramedics and the police concerning rail incidents involving flammable liquids. The document is adapted from guidance prepared by the International Association of Fire Chiefs (IAFC) for the Renewable Fuels Association, which has agreed to its wider dissemination to communities in Canada. The online document can be accessed via the Transport Canada website at www.tc.gc.ca/eng/tdg/safetymenu-1318.html.
The total volume of oil lost to the environment from tanker incidents last year was some 7,000 tonnes, according to the annual tanker oil spill survey by the International Tanker Owners Pollution Federation (ITOPF). There were only two incidents in which more than 700 tonnes was lost, and four ‘medium’ spills of between 7 and 700 tonnes.
The figures for 2018 will be higher, given the loss of the tanker Sanchi with 1m bbl of condensate in the East China Sea last month.
THE AUTUMN 2017 session of the Joint Meeting of the Joint Meeting of the RID Committee of Experts and the Working Party on the Transport of Dangerous Goods (WP15) of the UN Economic Commission for Europe (ECE) was held in Geneva from 19 to 29 September. It was chaired by Claude Pfauvadel (France) with Helmut Rein (Germany) as vice-chair.
The meeting was attended by representatives of 22 states, an observer from the Democratic Republic of Congo, the European Commission, the EU Agency for Railways (ERA), the Central
Commission for the Navigation of the Rhine (CCNR), the Organisation for Cooperation between Railways (OSJD) and 11 nongovernmental organisations.
The main task of the meeting was to discuss and, insofar as was possible, agree the multimodal changes to the regulations to enter into force on 1 January 2019, with the usual six-month transition period to 1 July 2019. Those changes will then need to be discussed and adopted by the respective bodies responsible for the RID (rail), ADR (road) and ADN (inland waterway) regulations. Those regulations apply throughout the EU, in a number of non-EU European countries and in various other states. ADR is also being observed by an increasing range of countries outside Europe as a model for their domestic legislation.
As is customary, proposals relating to the transport of dangerous goods in tanks were remitted to a working group that met alongside the plenary under the chairmanship of Arne Bale (UK).
The secretariat highlighted an item in the report of the Ad Hoc Working Group on the Harmonisation of RID/ADR/ADN with the UN Recommendations, which suggested adding a portable tank special provision corresponding to TP10 for the carriage of bromine. This was agreed: TU43 An empty uncleaned tank may be offered for carriage after the date of expiry of the last inspection of the lining for a period not to exceed three months beyond this date for the purposes of performing the next inspection of the lining prior to refilling (see special provision TT2 in 6.8.4 (d)).
“TU43” is added in column (13) of Table A in 3.2 against UN 1744 bromine. This is also referenced in special provision TT2 in 6.8.4(d).
Special provision TU42 had previously been added to prevent the carriage of substances that react violently with aluminium alloy in tanks with a protective lining or shell made of such alloys. Russia proposed extending its applicability to another UN number but an
MULTIMODAL • REGULATORY HARMONISATION STILL PROVES ELUSIVE, AS THE AUTUMN 2017 JOINT MEETING EXEMPLIFIED. RID, ADR AND ADN WILL STILL DIFFER FROM THE UN MODEL
informal document from Belgium felt that a new approach using classification criteria for corrosivity rather than a pH value was needed. It was agreed that a special working group should be set up to pursue this idea but, in the meantime, it was also felt that the Russian proposal should be allowed; as a result, TU42 is added in column (13) of Table A in 3.2 against UN 3266 corrosive liquid, basic, inorganic, nos for both PG II and III.
Belgium asked for an extension of the transitional measures for the carriage of substances to which TU42 applies. It felt that the cut-off date of 2022 now appears to be too soon for industry and proposed 2033 instead. Others felt this was too long and a compromise was reached, settling on 31 December 2026 as the new cut-off.
An official submission from Belgium proposed to extend the requirement for entering the actual holding time in the transport document to portable tanks as it is already applicable to tank containers and tank-wagons carrying refrigerated liquefied gases. While there was broad support for the idea, it was felt that this should be passed up
the chain to the UN Sub-committee of Experts on the Transport of Dangerous Goods (TDG).
The UK had continued to lead work through an informal group on the inspection and certification of tanks; this work followed the discovery that a significant number of road tankers imported into the UK had been approved by a body not authorised to do so. However, the ongoing work raised a number of concerns, not least from representatives of the rail industry, which felt that the system under RID works well as it stands. There were other problems relating to the legal position of the various parties in the supply chain under EU law.
It did not prove possible to discuss all the points raised in the UK’s paper, and the informal working group was planning to reconvene in December 2017 so further submissions under this topic are inevitable.
However, the group did agree to amend the first two sentences of the first paragraph of 6.8.2.1.23 to read:
The ability of the manufacturer, or the maintenance or repair shop, to perform welding operations shall be verified and »
confirmed by either the competent authority or by the body designated by this authority.
A weld quality assurance system shall be operated by the manufacturer or the maintenance or repair shop.
At the spring 2017 meeting there had been discussion of the position under the regulations of tanks that are designed with a concave section in the barrel. It was accepted that the current text leaves room for interpretation and that some modification was needed. Since then an informal working group had met to discuss the issue, although its conclusions were not well received, and the Netherlands arrived with an alternative proposal. This garnered more support but it will require standard EN 13094 to be amended. For the time being, the proposal has been adopted in square brackets. It consists of additional sentences at the end of footnote 2 to 6.8.2.1.18:
However the cross section of shells according to 6.8.2.1.14 a) may contain recesses or protrusions such as sumps, cut-outs or recessed manhole constructions. They may be constructed of flat or shaped (concave or convex) sheet metal. Dents
and other unintended deformations shall not be regarded as recesses or protrusions
In an informal document the UK proposed including within the regulations a model tank plate, rather than leaving this to a standard. The idea was well received, on the condition that it should apply only to new tanks. Various other specifications were agreed. The UK was invited to submit a revised proposal at a future session.
Germany suggested that the use of austenitic-ferritic (Duplex) stainless steels should be recognised in 8.6.5.1.2(a). The working group was happy with the idea and added a new indent to the sub-paragraph. However, the specification that such steels may be used for cargoes at a temperature of -40˚C remains in square brackets as it needs to be checked: some delegates thought that refrigerated carbon dioxide is carried at a lower temperature. A reference to austeniticferritic stainless steel is also added at the end of the second indent to 6.8.5.2.1.
The Netherlands raised the question of standard EN 14596 on emergency pressure relief valves. It had been decided in 2005
not to reference the standard as it appeared to allow significant leakages in the event of a tank vehicle overturning. The standard has since been revised and the Working Group on Standards was now considering whether to insert a reference to it in ADR. The Netherlands was of the opinion that this should not happen, which was supported by other experts. The Working Group on Standards (see below) agreed.
The Netherlands also raised the question of the marking of tank codes on fibre-reinforced plastics (FRP) tanks. The experts recognised that some amendment of the current text was necessary and the Netherlands will return with a formal proposal.
The secretariat proposed the deletion of a number of transitional measures that have now expired. Most of those were agreed, although 1.6.3.16 and 1.6.4.18 were retained so as to provide clarity on why the tank record of tanks constructed before 1 January 2007 may not be complete.
France queried the marking of tanks with the date of initial inspection. The group’s consensus was that the date of the first hydraulic pressure test sets the start of the life of a tank and determines which version of the regulations apply to it. However, the date of the initial leakproofness test, which could be some time later, is preferable in determining the date of periodic and intermediate inspections. This topic will be considered in conjunction with work on the tank plate.
Referring to intermediate inspections on LPG road tankers, the UK was keen to build a body of evidence on the checking of safety valves and the option to use EN 14334 as an alternative. The UK is hoping that inspection bodies and industry will undertake a test programme, the results of which will be shared. In the meantime, the issue would be brought to the attention of the Working Group on Standards.
France asked if any experts had experienced problems with the electronic
documents and electronic signatures in relation to inspections. The general feeling is that there is no problem with their use but, as it applies to other types of document, the issue should be brought to the attention of the plenary session. The Joint Meeting felt there is a potential problem, as not all electronic signatures have the same level of security. The assurance level must be sufficient to fulfil the requirements of ISO 17020.
The Working Group on Standards met during lunch breaks to discuss reports from the European Committee for Standardisation (CEN) on progress with relevant standards.
As a general rule, when a new version of a standard is introduced, a two-year transitional period is allowed. The Working Group agreed that it would be worth having a similar system for new standards. In effect, that would mean that newly referenced standards would become mandatory with the next edition of the regulations; for instance, those appearing for the first time in the 2019 edition will become mandatory on 1 January 2021. A formal proposal to amend standards already adopted for the 2019 will be made at the spring 2018 Joint Meeting.
The Working Group noted that there is a difference in the approach to periodic inspection of safety valves in EN 12972:2007 and EN 14334:2014, particularly in respect of what constitutes a “check of the
satisfactory operation” of the valves. The Group could not state that either approach is incorrect but felt that the work proposed by the UK (see above) might provide useful evidence for further discussion.
The Working Group supported CEN’s proposal to limit the scope of EN 12245, following Denmark’s report on accidents involving LPG cylinders constructed in accordance with EN 12245:2002. Given that LPG cylinders are adequately covered by EN 14427:2014, it was felt that the versions of EN 12245 referenced in RID/ADR should be accompanied by a Note forbidding their application to LPG cylinders. A decision on this will be made at the next session.
A number of updated standards were adopted for Chapter 6 of ADR/RID:
EN ISO 17871:2015 + A1 [2018] on the specification and type testing of quick-release valves for gas cylinders, with the existing reference to EN ISO 17871:2015 no longer applicable after 31 December 2020;
EN 13807:2017 on the design, manufacture, identification and testing of battery vehicles and multiple-element gas containers, with the existing reference to EN 13807:2003 no longer applicable after 31 December 2020;
EN 13317 [2018] on manhole cover assemblies for tanks for the transport of dangerous goods, with the existing reference to EN 13317:2002 + A1:2006 no longer applicable after 31 December 2020;
EN 1440:2016 + A1:[2018] (except Annex C) on the periodic inspection of traditional welded and brazed steel LPG cylinders, with the existing reference to EN 1440:2016 (except Annex C) no longer applicable after 31 December 2020 and references to earlier versions of EN 1440, EN 14912 and EN ISO 11623 deleted;
EN 16728:2016 + A1:[2018] (except clause 3.5, Annex F and Annex G), on the periodic inspection of transportable refillable LPG cylinders other than those of traditional welded and brazed steel, with the existing reference to EN 16728:2016 no longer applicable after 31 December 2020.
The secretariat provided the Joint Meeting with an exhaustive report on the results of »
the April 2017 meeting of the Ad Hoc Working Group on the Harmonisation of RID/ADR/ ADN with the UN Recommendations on the Transport of Dangerous Goods, which included a 53-page document containing proposed amendments taken from the 20th revised edition of the UN Recommendations.
The Joint Meeting considered each of these proposals in turn and adopted the changes, subject to some editorial modifications.
The most significant of these include:
(a) rationalisation of the use of the terms ‘risk’ and ‘hazard’ throughout the regulations
(b) addition of a new sub-section 2.1.4.3 on samples of energetic materials for testing purposes
(c) insertion of a new section 2.1.5 on the classification of articles as ‘articles containing dangerous goods, nos’, with the renumbering of the existing 2.1.5 as 2.1.6
(d) amendments to 2.2.1.1.7 relating to flash composition and the appropriate testing methods
(e) changes in 2.2.51 relating to the classification of ammonium nitrate fertilisers
(f) replacement of the existing text of section 2.2.8 on Class 8 corrosive substances with a completely new text (some of which is different to that in the UN Recommendations)
(g) the following new entries are added to the Dangerous Goods List:
• UN 3535 toxic solid, flammable, inorganic, nos
• UN 3536 lithium batteries installed in cargo transport unit
• UN 3537 articles containing flammable gas, nos
• UN 3538 articles containing nonflammable, non-toxic gas, nos
• UN 3539 articles containing toxic gas, nos
• UN 3540 articles containing flammable liquid, nos
• UN 3541 articles containing flammable solid, nos
• UN 3542 articles containing a substance liable to spontaneous combustion, nos
• UN 3543 articles containing a substance which emits flammable gas in contact with water, nos
• UN 3544 articles containing oxidising substance, nos
• UN 3545 articles containing organic peroxide, nos
• UN 3546 articles containing toxic substance, nos
• UN 3547 articles containing corrosive substance, nos
• UN 3548 articles containing miscellaneous dangerous goods, nos
(h) substantive changes in special provisions 188, 251, 307 and 376
(i) new special provisions 193 (ammonium nitrate fertilisers), 301 (machinery or apparatus containing dangerous goods), 387 (lithium batteries), 388 (vehicles powered by flammable liquid or gas or fuel cells), 389 (lithium batteries installed in a cargo transport unit), 392 (fuel gas containment systems), 671 (chemical kits and first aid kits), 672 (machinery and apparatus) and 673 (RID only, applicable to the new entries for articles containing dangerous goods)
(j) new special packing provisions PP94 and PP95 added in packing instruction P520, relating to energetic samples
(k) new packing instructions P006 (for UN 3537 to 3548), P907 (for UN 3363) and P911 (for damaged or defective cells or batteries) (l) substantive changes in packing
instructions IBC520, LP902, LP903 and LP904 (m) new packing instructions LP03 (for UN 3537 to 3548), LP905 (for pre-production prototypes and small production runs of lithium cells and batteries) and LP906 (for damaged or defective cells or batteries) (n) addition of provision for large salvage packagings
(o) a new sub-section 5.2.2.2.1.12 with special provisions for the labelling of articles containing dangerous goods (p) amendments to the specimen labels in 5.2.2.2.2 (q) addition of provisions for bulk containers, especially in Chapter 5.3
(r) several additions and revisions to the standards referenced in Chapter 6.2 (s) amendments to the IBC testing provisions in Chapter 6.5, and (t) a new 7.1.7 on special provisions for the carriage of self-reactive substances stabilised by temperature control.
In the process of agreeing these amendments, a number of questions emerged. Russia queried the meaning of ‘energetic substances’ and whether a definition should be added in 1.2.1. That question will be taken to the UN TDG Sub-committee.
With the terms ‘risk’ and ‘hazard’ having been rationalised, it was noticed that, in 2.1.4.3.1(b), the terminology used to describe packing groups in the English text uses the word ‘hazard’, whereas the more usual terminology for packing groups uses ‘danger’. The same problem does not exist in the French text, which is the reference version for ADR, but it seemed worth bringing this to the attention of the UN TDG Sub-committee.
Now that all provisions concerning the classification of ammonium nitrate fertilisers
have been consolidated in section 39 in the Manual of Tests and Criteria, some details in special provision 307 have been deleted. This has presented a problem for such material not accepted for carriage, as mentioned in the 13th indent of 2.2.51.2.2. Sweden offered some amended text but this did not achieve a consensus. It is likely that this will be another issue to go back to the UN TDG Sub-committee.
In plenary, there was extensive discussion of the new provisions for ammonium nitrate fertilisers. It was noted that the current provisions in RID/ADR/ADN are more restrictive than those in the UN Recommendations and the conditions imposed for maritime and air carriage. On the basis of a presentation by Fertilizers Europe, it was decided that this is not a problem.
The text of the new special provision 389 in the UN Recommendations was also deemed to be unclear, as it could be interpreted as applying to a container carrying batteries, whereas it is meant to apply to containers fitted with batteries, which are being used as mobile power sources in remote locations. The Joint Meeting amended the UN text and will inform the UN TDG Sub-committee.
The new special provision 392 has effectively replaced the existing special provision 660 in RID/ADR/ADN. The Working Group felt it appropriate, therefore, that 392 be assigned to all those UN numbers to which 660 is currently assigned. This includes UN 1972, to which 660 is not assigned in the UN Recommendations. The Working Group also noted that ECE regulation No 110 has been amended to cover LNG-fuelled vehicles, meaning the table in SP 392(a) should be amended. These issues will be brought to the attention of the UN TDG Sub-committee.
Germany proposed extending the scope of SP 392 to cover non-flammable and non-toxic gases (groups A and O), recognising the needs of the automobile industry. Many felt that this was an issue that should be taken to the UN TDG Sub-committee in the first instance but the German representative stressed that it was a matter of urgency for industry. It was eventually agreed to insert new text but only for group A gases; this was done by amending special provision 660 to read: »
For the carriage of fuel gas containment systems designed and approved to be fitted in motor vehicles containing this gas the provisions of sub-section 4.1.4.1 and Chapter 6.2 [ADN: of ADR] need not be applied when carried for disposal, recycling, repair, inspection, maintenance or from where they are manufactured to a vehicle assembly plant, provided the conditions described in special provision 392 are met. This also applies for mixtures of gases subject to special provision 392 and gases of group A subject to this special provision.
The Working Group also foresaw issues with practical implementation of the new provisions for the transport of articles containing dangerous goods. In particular, the position of UN 3363 is difficult, since dangerous goods in machinery or apparatus are not currently subject to RID/ADR/ADN by dint of 1.1.3.1(b). In plenary, the Joint Meeting decided to delete 1.1.3.1(b) and to assign special provision 301 to UN 3363, deleting the last sentence concerning exemptions
that can be made by the competent authority. Conditions for such exemptions will now be consolidated in SP 672. A four-year transition has been allowed for 1.1.3.1(b).
The Working Group will also seek clarification about the placarding of cargo transport units (CTUs) containing lithium batteries. RID/ADR/ADN (and the IMDG Code) currently require CTUs with lithium batteries of UN 3090, 3091, 3480 or 3481 to bear the placard corresponding to label model No 9, not No 9A, although the text in the UN Recommendations is not clear. Similarly, SP 389 indicates that CTUs shipped under the new UN 3536 entry should carry a No 9 placard.
There was also discussion about the labelling and placarding of articles that contain both dangerous goods and lithium batteries; 1.1.3.1(b) allows the hazard presented by the batteries to be not communicated but this hazard is not represented by other labels. It was felt that the UN Recommendations are not clear on how to deal with this. A proposal
from Germany and Sweden was deemed acceptable, resulting in the amendment of 5.2.2.1.12.1 to read:
Packages containing articles or articles carried unpackaged shall bear labels according to 5.2.2.1 reflecting the hazards established according to 2.1.5, except that for articles that in addition contain lithium batteries, a lithium battery mark or a label conforming to model No. 9A is not required.
The Working Group noted that the new provisions in Chapter 7.1 on temperature control during transport reflect to a large extent the provisions already found in special provisions V8 and S4 of ADR. Some work may be needed to streamline the provisions, but this will be left to WP15 since it only affects ADR. HCB
The second part of this two-part report on the autumn 2017 Joint Meeting in next month’s HCB Monthly will cover ongoing and new proposals for amending RID/ADR/ADN, questions of interpretation and reports from informal working groups.
(PG II) or more;
• UN 1093, 1099, 1100, 1131 and 1921 (Class 3), PG I, in tanks of 3,000 litres or more;
• Desensitised explosives of UN Nos 3364, 3365, 3367 and 3379, Division 4.1, in packaged form with a net mass of 1,000 kg or more;
• UN 3394, Division 4.2 in tanks of 3,000 litres or more;
GERMANY IS PERHAPS unique in that the requirement to promote a modal shift away from road in goods transport is enshrined in legislation. In fact, a rule in place since 1970 means that shippers and carriers must, wherever possible, use rail or inland waterway transport for certain dangerous goods and, when using road transport, must stick to motorways unless there is no alternative.
The regulation applies to both domestic and international transport. Therefore, shippers, carriers and all others with a responsibility under the regulatory provisions must be aware of the requirements if their goods are to be exported to, imported from or transited through Germany.
Germany’s Ordinance on the Transport of Dangerous Goods by Road, Rail and Inland Waterways (Gefahrgutverordnung Strasse, Eisenbahn und Binnenschaft – GGVSEB) was updated in March 2017 and an English translation was made available later in
the year. The revision has extended the range of dangerous goods covered by the requirements and updated the costs for determination of routing.
The specific provisions can be found in GGVSEB Section 35, Modal Shift. Section 35b specifies those dangerous goods to which the provisions apply. These are:
• Explosives of Divisions 1.1 and 1.2 in packaged form with a net explosive mass of 1,000 kg or more;
• Explosives of Division 1.5 in tanks or packaged form with a net explosive mass of 1,000 kg or more;
• Flammable gases of Class 2 in tanks with a net mass of 9,000 kg or more;
• Toxic gases of Class 2 in tanks with a net mass of 1,000 kg or more;
• Flammable liquids of Class 3, PG I or II in tanks of 3,000 litres (PG I) or 6,000 litres
• UN 1928 and 3399 (Division 4.3) in tanks of 3,000 litres or more;
• UN 1745, 1746, 1873 and 2015 oxidising liquids, PG I only (Division 5.1), in tanks of 3,000 litres or more;
• Toxic liquids (Division 6.1), PG I only, in tanks of 3,000 litres or more; and
• UN 1052, 1739, 1744, 1777, 1790, 1829 and 2699 corrosive liquids (Class 8), PG I only, in tanks of 3,000 litres or more.
It is assumed that dangerous goods included in this list will be carried by rail or inland waterway if the transport distance is more than 200 km and there are suitable facilities at either end of the transport (rail siding, barge dock).
Multimodal transport (ie including a road leg) will be allowed if the total transport distance is more than 400 km and the larger part of that distance is covered by rail or inland transport.
There are some exemptions. The modal shift required by the provisions does not apply, for instance, if the distance by rail or inland waterway is more than twice the
DOMESTIC RULES MEANS THAT SHIPPERS NEED TO BE CAREFUL HOW THEIR DANGEROUS GOODS ARE BEING CARRIED
actual distance by road. Other exemptions are listed in Section 35c, applicable to specific dangerous goods or to specific types of tank.
GGVSEB Section 35a sets out the requirements for dangerous goods listed in Section 35b when transported by road. The basic requirement is that they shall move only on motorways, except when the use of motorways is excluded or restricted by provisions of the Road Traffic Regulations (Strassenverkehrs-Ordnung) or Holiday Traffic Regulations (Ferienreiseverordnung), or when the distance that would be covered by using motorways is more than twice as long as the route by alternative suitable roads.
There are, though, costs involved. In order to confirm that a shift from road to rail or inland waterway is not possible a certificate must be obtained from the Federal Railway Authority or Waterways and Shipping Agency at a cost of up to €250 per confirmation. A determination of non-motorway routeing must be obtained from the relevant local authority (each Land has its own legislation) at a cost of up to €1,000.
Failure to observe any of the provisions can result in a penalty of €800.
Those with a responsibility under GGVSEB need to examine the complex provisions closely to see how they apply to them and what options they have for avoiding them, bearing in mind the potential cost to do so. HCB
HCB is grateful to Norbert Müller, global dangerous goods coordinator at Schenker AG in Essen, Germany for his invaluable help in producing this article. He can be contacted by email at norbert.mueller@dbschenker.com.
HCB LIKES TO think that it plays an important role in the dangerous goods business. So, when we were approached during our (belated) 35th birthday party in London in February 2016 by Labeline International, a long-time friend of the magazine, with an idea for a series of update seminars, we were all ears. After all, Labeline has more than 25 years’ experience in the regulatory compliance business and has been the leading reseller of IATA’s Dangerous Goods Regulations for each of the past nine years.
The idea was, as all good ideas are, relatively simple: Labeline would – with help from HCB – organise a short series of seminars around the UK just ahead of the arrival of the revised regulations at the start of 2017. And so the idea of the Labeline/HCB ‘Biennial Roadshow’ was born.
Nearly 200 people attended each of the first three events, which took place in November 2016 at Heathrow, East Midlands and Aberdeen. Delegates came from a wide spectrum of the industry and included shipper
and transport employees as well as trainers, dangerous goods safety advisers (DGSAs) and other interested persons. Delegates also came from further afield than expected, with visitors from across Europe and the US.
They were attracted not just by the subject matter but by the calibre of speakers that had been lined up. They included Jeff Hart OBE, former chair of the UN Sub-committee of Experts on the Transport of Dangerous Goods, who since his retirement from his position as head of the Dangerous Goods Division at the UK Department for Transport (DfT) now sits in at meetings of the International Maritime Organisation (IMO) on behalf of the Dangerous Goods Advisory Council (DGAC).
Also on the stage was Geoff Leach, who for many years was chair of the Dangerous Goods Panel at the International Civil Aviation Organisation (ICAO) and, since leaving the UK Civil Aviation Authority, now runs his own consultancy and training company. Jeff and Geoff have developed a highly informative and, at times, humorous double act, the better to get the regulatory message over to the audience.
They and other presenters, including representatives of the International Air Transport Association (IATA), Currie Associates, Exis Technologies, DGOffice and others, provided not only an update on the incoming regulatory changes but also delved into the background and the process by which regulations are developed. That gave delegates an insight and, hopefully, helped them understand why they are being asked to do what they are.
There was also an interesting presentation by response organisation Braemar Howells, which brought along one of its mobile emergency response vehicles and offered delegates a look at its contents during the coffee and lunch breaks.
THE LABELINE/HCB BIENNIAL ROADSHOW NOT ONLY PROVIDES A REGULATORY UPDATE BUT ALSO GIVES DELEGATES A CLOSE LOOK AT THE PRODUCTS AND SERVICES AVAILABLE TO HELP THEM
Keith Kingham, managing director at Labeline, expresses his pleasure with how things went. “The response to this first event and its concept with the visitor feedback was tremendous and very positive for a future event.” Cliff Collie of Petrofac Training Services, for instance, said of the Aberdeen event: “Thank you for organising such a wellrun Roadshow. I certainly found it worthwhile and it is definitely a ‘must attend’ for anyone in the industry.”
“The quality of the speakers was extremely important to us and we were delighted that all those who we asked to present were able to do so,” Kingham adds. “Their commitment boosted the credibility of the Roadshow. The clear message that delegates took away was that all those involved in the classification, packing or shipping of dangerous goods should familiarise themselves with the latest versions of the regulations.”
Indeed, across the three events the feedback forms indicated a 90 per cent satisfaction rating, giving Labeline the confidence to think about organising the next Biennial Roadshow.
So, with the next round of regulatory revisions due to appear at the start of 2019, the next Biennial Roadshow will kick off in November 2018. This year there will be two events: one in Heathrow on 13 November and one near Manchester Airport on 15 November. The venues have been chosen not only for their accessibility near major transport hubs but also for the quality of the facilities available at the hotel venues.
Labeline has been putting a lot of thought into the conference programme as well and has made a few tweaks. Kingham and his colleagues, who have seen plenty of events like this in their years, have addressed the problem that often besets modal presentations on regulatory changes. Given that all the modal rulebooks derive ultimately from the UN Model Regulations, each biennial change to the regulations tends to see very similar amendments adopted by each of the modes; when conferences cover each of the modes, there is often a lot of repetition in the successive presentations.
At this year’s Biennial events, delegates will not have to sit through that repetition; rather, the various modal knowledge leaders will sit in a panel, led by HCB’s editor-inchief, Peter Mackay, and discuss the various amendments derived from the UN Model Regulations and how they are being applied in ADR/RID, the IMDG Code and the ICAO Technical Instructions (and IATA Dangerous Goods Regulations).
That panel is likely to feature Jeff and Geoff once more, along with Richard Masters, well
known in the UK dangerous goods sphere, talking about road and HCB columnist and chair of the Dangerous Goods Trainers Association (DGTA) Gene Sanders bringing news of developments in the US.
In addition, there will be talks on additional requirements for exports to the US, the role of safety data sheets (SDSs) in transport classification, what enforcement agencies are looking for and, of course, the ever-changing regulations for lithium batteries.
The one-day events are structured so as to provide plenty of time for attendees to talk to the experts and there will also be a small exhibition area so delegates can take a look at the tools available to help them do their job. Naturally, there will be a comprehensive and useful delegate pack to take home.
Full details remain to be finalised but those interested in attending might want to make a note of the dates in their diary and register their interest by emailing sales@labeline. com. More information will be available via the Labeline website as the year goes on and will be also disseminated through HCB. HCB www.labeline.com
Over the years, a number of readers – many, but by no means all of them American – have asked us why so many of the stories reported here on the back page involve dumb things happening in America. Our response is normally simple and diplomatic: the US has a vibrant local press network and efficient news aggregators that bring such stories to our attention.
Then again, there is a trend, especially in the more rural parts of the country, for safety oversight to be lacking; there are also plenty of pretty dumb individuals with access to the sorts of material that will end them up on this page.
There is also our old friend, the ‘disgruntled former employee’, who turned up again last month in a story from Orange County, Florida. As reported by local NBC affiliate WESH, employees of a medical business turned up to work one Friday morning to find an unknown substance all over the inside of the building. Intervention by the local hazmat crew determined this unknown substance to be cooking oil.
We understand that some younger people find nothing unusual in spraying cooking oil on their frying pans using oil specifically packaged to be delivered in this way. One cannot help but wonder whether a cooking oil aerosol mist would be flammable. Perhaps someone has already tried…
On the other coast, five children were hurt by a washing incident at the Palm Desert YMCA in January. The children, all under five years old, had to be taken to hospital after washing their hands, which started to burn.
It emerged that a janitor at the facility had accidentally put a harsh cleaning compound,
marketed as Ecotemp Ultra Klene, in the hand soap dispensers. Well, local reports said it was accidental – who are we to assume?
Just for the record, Ecotemp Ultra Klene, an Ecolab product, uses sodium hydroxide as its active ingredient and is “reserved for industrial and professional use”. Under GHS it is classified in Category 1A for skin corrosion; for transport it is UN 1824, Class 8, PG II.
In this incident, its use seems far from professional. On the other hand, the incident supports toddlers’ opposition to washing.
Finally, a story that takes us back to Florida and the small town of Leesburg, near Orlando, where the coroner’s office was closed for several days in December after it was contaminated by mercury.
The incident began when locals spotted what they thought might be human bones in the water near a boat ramp in nearby Silver Springs. Alongside the bones were antlers, beads and a pot. We let Lindsey Bayer, director of operations at the district Medical Examiner’s office, take over the story:
“They came into the office and when they started cleaning the pot and the beads and all the voodoo stuff, they found the mercury. That’s when we called hazmat.” Lucky old hazmat…
The material was thought to be related to the practice of Santeria, a Caribbean religion derived from the West African religion of Yoruba.
“They do use mercury in their rituals, despite the fact that it’s poisonous, but I believe we’ve found the bones to be of no forensic evidence,” Bayer said. “It’s not like somebody’s running around killing people and using them in a ritual.”