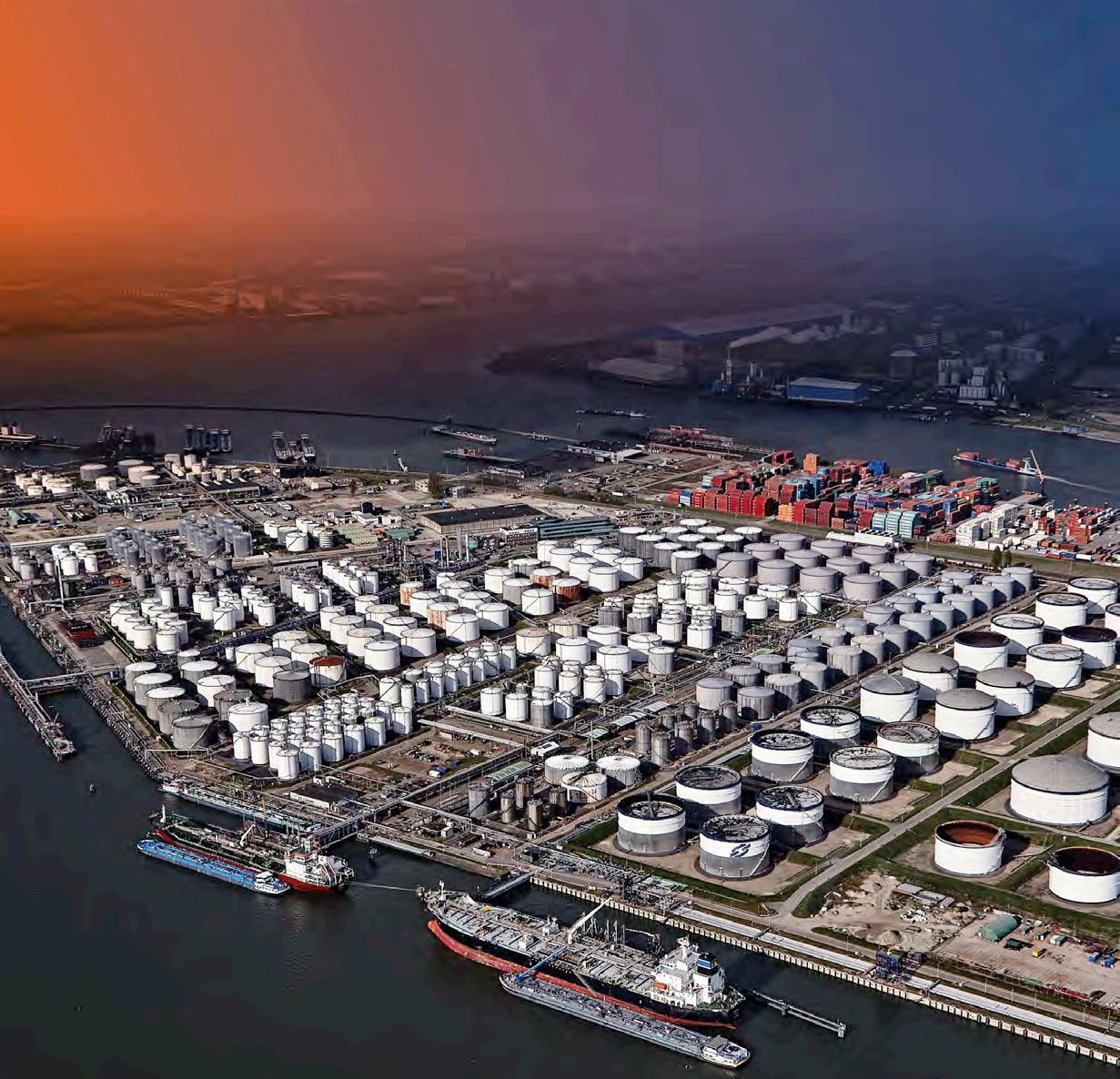
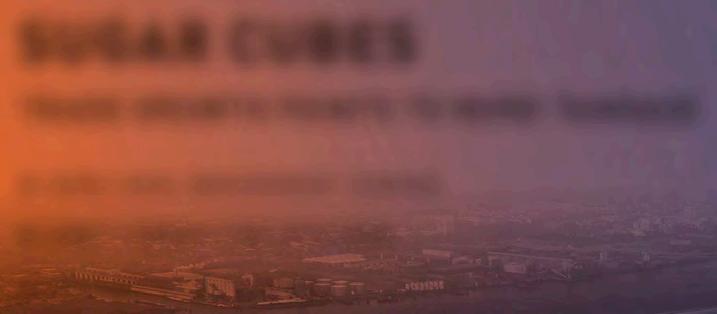
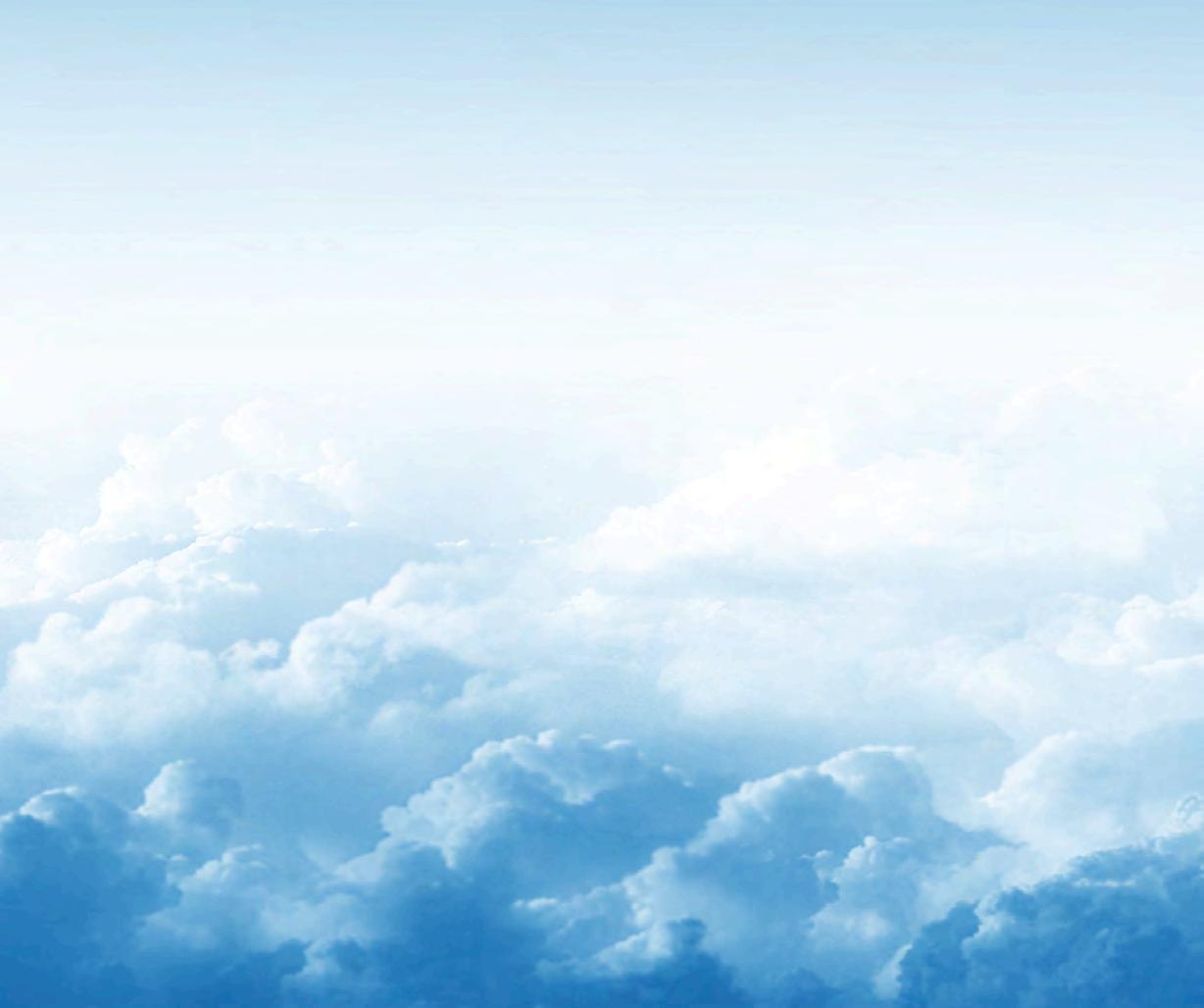


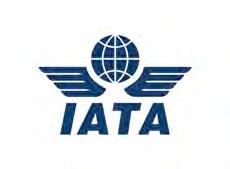
It is common at this time of year to reflect on the events of the past 12 months and to promise to do better in the year to come. That strikes me as a fatuous enterprise: time is always on the move and cannot be put into neat parcels by arbitrary dates.
More to the point, in this increasingly globalised world, 1 January does not mark the start of the year for a large proportion of the world’s population. The date was set by the Romans (of course), who moved the start of their year from 1 March to mark the election of new consuls, and counted their years from that point. But many other cultures still start the year in March or April, to coincide with the first full moon of spring; this is the case throughout south Asia and much of Indochina, while China, Vietnam and Korea mark the new year in late January or February. The Islamic and Jewish new years fall this year in early September.
I was surprised to discover, through that impeccable source, Wikipedia, that the UK did not recognise 1 January as the start of the year until 1752; even then, many communities continued to regard 25 March as the first day, more or less coinciding with the vernal equinox and also marking Lady Day, one of the four days of the year when quarterly rents are due. And it is well known that, until the railways came along, each town set the church clock according to the position of the sun at noon.
So it is odd to think that – despite these cultural differences – pretty much everywhere these days runs on a consistent clock, using the same dates. It we did not, then computers
couldn’t communicate and GPS wouldn’t work. Air travel would be even more of a nightmare than it can already be. It’s only by having a unified approach around the world, using the same language (whether that’s computer code or – for aviation – English) that the machines that run much of our world for us can do their jobs. And as those machines take on a bigger role in organising our lives – Industry 4.0 again – then it will be crucial that they all know how to talk to each other.
It is just the same in the world of dangerous goods (or hazardous materials – we still haven’t managed to straighten that one out). There are global standards and regulations for many international shipments, designed to allow goods – often vital to the consignor – to move seamless around the world by different modes. Those involved in such movements are (or ought to be) well aware of those standards and, by and large, seek to meet them.
Then again, dangerous goods move in large volumes on domestic trades, not least in countries with a large surface area. While the rules for such movements are often not so restrictive, they are gradually changing to come more into line with international standards.
Perhaps those involved only in local transport, when facing changes to the regulations, feel much the same as an 18th century Englishman, asked to change his idea about when the year starts. But such changes are needed if the new, interconnected world is going to work.
Peter MackayIATA’s Dangerous Goods training tackes all regulatory intricacies and propels you to the top of your field. Studies prepare you for the role of quality control spe cialist and operations guru. As a dangerous goods expert, you’ll know how to stay on top of all audits and inspections through a deep understanding of complex regulations and current training methodologies.
Complex regulatory requirements receive in-depth analysis. You’ll learn how to identify weak links in your system, focus on specific hazards such as lithium batteries and infectious substances and know how to effectively implement emergency procedures.
Discover the full industryrecognized curriculum: www.iata.org/training-dgr
Harness the proper skills to be a leader and educator. Not only will you receive the necessary technical and theoretical insight but you’ll also benefit from training that harnesses your communication, presentation and training strengths.
Designed for handling agents, freight operators and anyone interacting with dangerous good in aviation, these programs consist of four courses that can be completed over a three-year period.
Cargo Media Ltd
Marlborough House 298 Regents Park Road, London N3 2SZ www.hcblive.com
Editorial Editor–in–Chief
Peter Mackay
Email: peter.mackay@hcblive.com
Tel: +44 (0) 7769 685 085
Stephen Mitchell
Email: stephen.mitchell@hcblive.com Tel: +44 (0) 20 8371 4045
Brian Dixon
Designer Tiziana Lardieri
Commercial Managing Director
Samuel Ford
Email: samuel.ford@hcblive.com Tel: +44 (0)20 8371 4035
Commercial Manager
Ben Newall
Email: ben.newall@hcblive.com Tel: +44 (0) 208 371 4036
Production Coordinator
Sam Hearne
Email: sam.hearne@hcblive.com Tel: +44 (0) 208 371 4041
VOLUME 39 • NUMBER 01
HCB Monthly is published by Cargo Media Ltd. While the information and articles in HCB are published in good faith and every effort is made to check accuracy, readers should verify facts and statements directly with official sources before acting upon them, as the publisher can accept no responsibility in this respect.
ISSN 2059-5735
Letter from the Editor 1
30 Years Ago 5
The View from the Porch Swing 7
Thinking ahead Vopak predicts tank demand 8
Give them what they want Inter responds to customers 10
All roads lead to Rotterdam HES makes progress on projects 13
News bulletin – storage terminals 15
Take it to the streets Hoyer opens Saudi joint venture 18
Care in the community Talke applies RC in GCC 20
Going up in Chicago Odyssey expands Linden operation 21
Mos’ DEF
Blackmer has the right pumps 22
Shout out on Safety HCC promotes standards in China 24
Build a bigger barge Ineos moves butane by river 26
News bulletin – tanks and logistics 27
And the winners are…
NACD recognises excellence 29
News bulletin – chemical distribution 30
Packaging prognosis
Smithers PIRA anticipates growth 32
Truckloads of growth Greif adds to truck fleet 34
News bulletin – industrial packaging 35
Training courses 36
Learning from training 39
Conference diary 40
SAFETY Incident Log 42
Safe to ship Don’t forget the CTU Code 44
A new chapter
Pyroban prepares for change 46
Roll out the labels
FMS meets 2018 head on 47
Portal for poisons NCEC advises on poison centres 48
Messing about with boats Getting ready for ADN 2019 52
Freight all kinds
Next IMDG amendment nearly done 58 Code corrected
Last-minute corrections to IMDG 62
Calendar of regulatory meetings 63
Not otherwise specified 64
Logistics in Rotterdam
Dangerous goods by air
The latest in telematics
Focus on chemical tankers
Sponsored by Odfjell Terminals
The January 1988 issue of HCB marked a step change in design and layout for the magazine, with bolder colour and glossier paper. Perhaps the increasing number of advertisers were demanding a higher standard of reproduction – though it may just have been that the title had taken on some younger staff with a more modern eye for design.
Whatever, it was a nice chunky start to the year, kicking off with the second part of HJK’s report on the August 1987 meeting of the UN Group of Rapporteurs in Geneva – at the time the Group played a similar role to today’s UN TDG Sub-committee, preparing the amendments for adoption by the parent Committee at the end of the biennium.
While the name of the body may have changed, some of the topics remain the same: in 1987 the IMO was concerned at a lack of consistency in the design of the Class 7 placard – in particular the width of the border around the image. There was also a proposal to amend the packing requirements for Division 6.2 infectious substances and three papers from the USSR on tank containers, one of which wondered if it might not be possible to come up with a code system to describe the type of tank, similar to that used in the IMDG Code.
There was also a lot of discussion of incoming provisions for the testing of reconditioned drums, including one piece from the appropriately named (for a January issue) Vincent Buonanno, ICDR chairman. Indeed, in many ways the new provisions that were taking effect at the end of the 1980s set the framework for those that are
still with us. That included the performance testing of UN-specification packagings, both in Europe and, perhaps more revolutionarily, in the US. Producers of all types of packaging were working out how to comply with incoming rules and how to manage the regulations alongside the quality demands of their customers (and, presumably, the profit demands of their shareholders).
Another hot regulatory topic of the time was the arrival of Annex II to Marpol, which took effect in April 1987. The January 1988 issue carried a report from Rear Admiral Kime of USCG on how the US was approaching the implementation of the new provisions and, just as importantly, their enforcement. He noted that the list of chemicals being carried by sea was growing ever longer, meaning that USCG personnel had to have a deeper understanding of the business, and that there had been something of an increase in the number of older and lower quality chemical tankers calling at US ports. On the upside, he said, there were already more than 70 ports in the US complying with the requirement to provide adequate reception facilities.
Closer to home, we reported on practical difficulties being experienced by industry in applying the new Road Traffic (Carriage of Dangerous Substances in Packages etc) Regulations, which had also come into force in April 1987. In particular, there was confusion over the size and shape of the new orange-coloured plates that had to be affixed to vehicles and how to cover them up at those times when the vehicle was not carrying dangerous goods. It seems simple now but back then it was quite a novelty.
Maybe my first taste came from a bad batch. I’d been so looking forward to a frozen yogurt. I love ice cream, and I love yogurt, so why wouldn’t a frozen yogurt be spectacular? Um, cuz it tasted like curdled, lumpy, sour milk, just smoother and colder. Gross.
Every few years someone would talk me into trying another, but although none tasted exactly the same as that nasty first one, the memories invoked were always so strong I usually had to fight not to spit it out. So, me plus fro yo equaled no go.
Enter the power of free. A fancy new frozen yogurt place opened near us, and as part of the grand opening week, each customer was offered a free one. Wife and kids were excited, so I went along. I could still be the family chauffeur, even if I refused my free fro yo. The place was huge, the set-up elaborate,
and the atmosphere electric. My children were jumping up and down, wide-eyed, as if on a sugar high, before we’d even had a spoonful. Grabbing bowls, my family got creative. A layer of one flavor, a layer of fruit or nuts, followed by another flavor, topped with a scattering of sugary sprinkles or crushed candy.
Finally, the checkout counter where the concoctions were weighed and an exorbitant bill assessed. “But, but, but, …”, I stammered to the cashier, “…these are free”. “Yes”, the cashier wearily explained, “a small, plain, fro yo is free, but your family has vastly exceeded the small size limit, incurred add-on charges for the mixed in fruits and nuts, incurred add-on charges for the luxury-flavored yogurts, and incurred add-on charges for the toppings.” The charges and add-ons together exceeded the amount we paid for an entire
meal the previous time the family had gone out to eat, and this was only dessert, and without dad getting any to boot. I paid. Boy, did I pay.
Discretely complaining to my wife on the way home while the children bounced joyfully around in the back of the minivan, I muttered that I now had two reasons to hate fro yo. (BTW, has there been a competent authority determination on whether it’s fro yo, froyo, or FroYo? Sometimes these fine points elude me.) Wisely, and politely, my wife pointed out that I was still back at only one reason, as my new objection was more about the add-ons than about the fro yo itself. Yeah, I considered, she was probably right. It may be add-ons that I’m not too fond of.
Some transport regulations have add-ons, too. And for a change, I can’t point my finger
at only the US DOT regulations, because the IMDG Code, and others, do the same thing, too. IMO has us add on the words MARINE POLLUTANT to shipping documents and add on a mark to the container when a material is bad for the environment if released. We do these two add-ons whenever the material is already a dangerous good (DG). But, what do we ‘add to’ if the material isn’t otherwise a dangerous good? Well, we make it a DG, throwing it into Class 9, giving it a PSN, PG, and technical name, and then we can add “Marine Pollutant” and the diamondshaped mark.
The USA treats their “hazardous substances” and the letters RQ almost identically. If a hazardous material is also a hazardous substance (which is confusing enough), then the preparer of the shipping papers must add on “RQ” (not just near the basic description, but immediately before or immediately after), and the packer must add on “RQ” near the other required marks and labels. And analogously to the IMDG Codes treatment of Marine Pollutants (MP), the US DOT requires that a hazardous substance that isn’t already a hazardous material be thrown into Class 9 so that the add-ons can be added on.
Long before there were any Proper Shipping Names (PSNs) that began with “Toxic by inhalation…”, the US DOT required that certain ‘inhalation hazards’ have their own add-ons, a practice that continues today. For certain materials that are “toxic by inhalation”, but not for all materials that cause toxicity when inhaled (wow, again, horrendously confusing), we must add on “INHALATION HAZARD” to both the shipping papers and the package marks, and we must add “poison” or “toxic”, and an appropriate HAZARD ZONE to the shipping papers. It’s not enough for a poisonous gas, for example, that it bear a hazard label with a skull-and-crossbones pictogram and a “2” in the bottom corner, those extra words must added on. And, oh yeah, in the US, the hazard label gets a black background added on behind those skullsand-crossed-bones.
Both inside and outside the USA, materials containing extra thermal energy get add-ons, too. Depending upon the physical state at
time of offering, physical state at standard temperature and pressure (STP), flash point, and amount of thermal energy (temperature), the container might get an add-on mark that looks like a thermometer inside a triangle or an add-on mark that says “HOT” inside a diamond outline, and the documents may get verbiage such as “Hot” or “Elevated Temperature” or even “molten” added on. Of course, like the MPs and RQs, if the hot stuff isn’t already a DG, we throw it into a hazard class, usually 9 but possibly 3, and then add on from there.
There are other add-ons, too, such as control and emergency temperatures for certain self-reactives, polymerizing materials, or organic peroxides. There are ‘cryogenic’, ultra-cold warnings for some gases. There are flash point communication requirements when shipping Class 3 by water, and more. And the problem isn’t that these requirements are unreasonable, because they are justified.
It is important that people get adequate warnings to protect themselves. It’s important that emergency responders get readily available information to mitigate dangers when something is or might get free of its containment. It’s just that, well, handling them as add-ons doesn’t seem like it’s necessarily the best or most consistent way to communicate all this information.
This may be better understood if you try to construct a simple spreadsheet for transport classifications. ID#, PSN, technical name(s), Primary Class/Division, Subsidiary Hazards, and Degree of Danger (e.g. PG or category or type) seem like obvious choices for columns, and a nearly complete listing. But then, consider the add-ons. Columns need to be added for Hazard Zones, and for flash point, and for Marine Pollutant, and probably for physical state. But what do you do about things that change classification with size, such as RQ (or self-heating for that matter), or that change classification with temperature at time of offering, such as materials melted to get them into a container that may or may not be elevated temperature depending upon how long after filling the transport journey begins? All of a sudden a simple spreadsheet isn’t so simple any longer.
There’s also a point about consistency in approach that’s both philosophical and practical. Why is an MP sometimes Class 9 and sometimes not? Why can Class 9 be a primary hazard, but not a subsidiary hazard? Why aren’t Hazard Zones treated as the equivalent of “types” (like 5.2 or self-reactive) or “categories” (like 6.2) or “packaging group” (like most DG), and treated as an integral part of the basic classification? Why should Hazard Zone be an add-on, when PG isn’t? Sure, as long as the information gets communicated, we’ve got a decent system, and does it really matter if we’re ‘philosophically consistent’ in how we communicate? Well, how about the practical aspects, not including complicated spreadsheets or databases?
Both individual nations and international modal agencies are grappling with a perception (probably accurate) that DG training isn’t always well understood and applied. Is it possible that a big part of the problem isn’t just the quality of the instruction, the time allotted, and the employer follow-up, but the complexity of the material?
Is it possible that the more simple, the more uniform, the more ‘philosophically consistent’ we are, the more able students in DG courses will be able to understand the system, and more importantly, the better able to consistently apply it they’ll be? Is it possible that if we re-engineered our system a bit to reduce some of the add-ons, it would be more consistent, more understandable, and more consistently applied compliantly?
I don’t like fro yo, but I do really, really like our DG system. It’s the add-ons, though, that give me some pause, whether paying for them on nasty fro yo, or tacking them onto the framework of our basic DG classification and communication system. I can’t do much about the former, but maybe we can all weak the latter, make training simpler, and increase safety by making compliance easier to simply understand.
This is the latest in a series of musings from the porch swing of Gene Sanders, principal of Tampa-based WE Train Consulting; telephone: (+1 813) 855 3855; email gene@wetrainconsulting.com.
AS 2018 OPENED, many operators of bulk liquids storage terminals were experiencing unusually soft market conditions. This was to a great extent the result of product price trends and their effect on trade volumes and the need for intermediate storage in the supply chain. It also marked something of a shift in fortune for terminal operators, who are often insulated from the vagaries of the markets through their position as balancing points for supply and demand.
Royal Vopak, which has the most diverse network of all the major independent terminal operators, has been looking hard at the
markets that provide it with its core business and has concluded that market fundamentals remain strong and that it is well placed to benefit from underlying trends.
That analysis has also confirmed the thinking behind its strategy, developed in 2014, to concentrate on four core terminal types:
– Hub terminals in the US Gulf, ARA region, Middle East and Greater Singapore
– Distribution terminals in locations with significant structural product shortages – Gas terminals
– Industrial terminals integrated with major refining and petrochemical complexes.
As Ismael Mahmud, Vopak’s global chemicals director, explained during a presentation to financial analysts in December 2017, there are five ‘mega-trends’ currently impacting the end markets that Vopak serves, the most significant of which is increasing urbanisation – especially in China. In 1992, little more than 25 per cent of China’s population lived in cities; that proportion increased to 54 per cent in 2017 and is projected to rise to 67 per cent by 2030.
The significant factor here is that urban dwellers in China have annual income around three times that of those living in rural China, a figure that has been remarkably consistent over the years. Greater urbanisation means that personal disposable income – and, thus, consumer spending – will outstrip overall GDP, leading to greater demand for energy and chemical products.
Urbanisation across developing nations, along with demographic trends in mature markets, growing pressure for sustainable
industrial production, geopolitical changes and the impact of disruptive technologies, will drive growth in chemical demand, Mahmud said. Much of this will occur in the polymer supply chain, as emerging economies increase consumption of plastics in end market production.
The outcome of these trends will be increasing imbalances between chemical supply and demand in different regions of the world. Looking specifically at liquid chemicals trade over the next ten years, Vopak anticipates that there will be a significant increase in exports from the Middle East (up by 29 per cent) and North America (up by 500 per cent, albeit from a low base), with small export increases from Latin America and the former Soviet Union. These increases will feed rising import demand, particularly in northeast Asia (up by 90 per cent) and south-east Asia (up by 34 per cent).
Vopak believes that this outlook points in particular to the need for new industrial complexes based both on exports (from feedstock advantaged producers in the Middle East and North America) and imports, primarily in the growing end markets in Asia (especially China and India but also Vietnam, Thailand and Indonesia).
Vopak’s experience in industrial terminals goes back as far as 1973, with the establishment of the Deer Park complex in Texas, and it is currently engaged in development of the Pengerang complex in Malaysia. Mahmud said that this level of experience means Vopak is well placed to take part in any future developments, particularly given its complementary network of hub and distribution terminals.
A similar set of trends is driving the market for petroleum product storage, Hari Dattatreya, Vopak’s global oil director, explained at the same event last month. Despite pressure to reduce hydrocarbon use, oil demand is expected to continue to grow, at least out as far as 2040. While use of natural gas and
renewable sources will increase as a share of the overall energy mix, oil demand will grow in absolute terms in Asia (concentrated in China and India) for use in the petrochemical sector and for transport fuels.
As a result, global imbalances in oil product supply and demand will become more noticeable; as before, rising import demand for clean products in the Asia-Pacific region (and, to a lesser extent, in Latin America and Sub-Saharan Africa) will be met almost entirely by new export streams from North America. Vopak quoted Wood Mackenzie figures that indicate that this trend will be more significant in the ten years after 2020.
Indeed, it is the period after 2020 that holds the most uncertainties. Mature markets are likely to see greater regulatory pressure to decarbonise the energy sector and the International Maritime Organisation’s (IMO) new restrictions on sulphur oxide emissions from ships also take effect in 2020. How vessel operators will respond to those restrictions is as yet unclear: one option is to install scrubbers but this may be too expensive, depending on the cost of alternative fuels and retrofit requirements.
Ships equipped with scrubbers will still be able to burn high-sulphur fuel oil; those without will need to turn to ultra-low sulphur fuel oil, distillates (gasoil or diesel) or, more radically, liquefied gases (LNG, LPG, ethane) or other fuels such as methanol. What this means for terminals supplying marine bunker
fuels is that they will have to be able to segregate and deliver a wider variety of fuels. Many of those terminals are located in hub ports; demand for storage in those ports will also be affected by other changes in regional demand profiles and the competitive position of local refineries. Vopak has a position in all the main hub areas but, as Dattatreya explained, it is facing increasing competition from other players.
Vopak is also keeping its eyes on emerging opportunities in major markets that have a structural fuel supply deficit, where economic growth can lead directly to increasing fuel imports. In the more mature markets, refinery closures can have a significant impact on import requirements, while some developing markets – Mexico, for example - are opening up through privatisation and deregulation, raising opportunities for established terminal operators to play a part in national fuel distribution operations.
Vopak already has a presence in some of those territories and currently has new fuel import/distribution terminals under construction in Brazil and South Africa.
Overall, Vopak says, the market for oil product storage looks likely to remain comparatively soft in the short term but in the long term it will benefit from solid underlying demand. It says there will be new opportunities in the mid- to long term. Vopak also says it will update the financial markets on developments in the second half of 2018. HCB www.vopak.com
INTER TERMINALS IS due to complete the largest organic expansion of its Seal Sands terminal this month. New tanks and pipeline links have been constructed to meet contracted demand for chemical storage at the terminal, adding a total of 27,000 m3 of new capacity.
Seal Sands occupies a prime location on the River Tees in north-east England and provides easy access by road and direct pipeline to the region’s major petrochemical and industrial complexes, as well as excellent sea connections via two jetties.
“The investment at Seal Sands demonstrates Inter Terminals’ commitment to working closely with its customer base to identify and develop solutions for specific product storage and handling requirements,” the company says.
“Our Seal Sands Terminal has developed specialist expertise in storing and handling a wide range of chemicals, many of which have distinct storage requirements,” adds Paul Oseland, commercial director of Inter Terminals. “Recognising that each customer and application is different, Inter Terminals is able to apply its considerable expertise and resources to provide tailored solutions.”
The project at Seal Sands includes the construction of two 7,000-m3 mild steel
tanks with internal floating roofs and a dedicated import pipeline for receiving product into storage by sea. In addition, an existing cross-country pipeline is being redeveloped to allow the direct transfer of stored product to nearby chemical manufacturing plants.
A further three mild steel tanks, with a total capacity of 13,000 m3, have also been built at the terminal, together with interconnecting infrastructure, to enable the export of product by sea and by road via a new tanker loading facility.
The extensive design and build programme at Seal Sands is being project-managed by Inter Terminals’ own engineering division. Offering specialised engineering expertise, the company’s in-house team has a wealth of experience in the design and implementation of projects to construct, upgrade and expand capacity within its own terminals and at customers’ facilities.
Inter Terminals’ latest investment at Seal Sands forms part of a continuous programme of asset integrity management and development across the company’s European storage network to ensure facilities meet the needs of current and future operational capacity.
Elsewhere in that network, Inter Terminals recently completed the construction of six new specialised stainless steel tanks at the Mannheim Terminal complex in Germany, which are now fully operational. The company’s engineers have also been busy recommissioning old tanks and converting others to handle different products as the regional market has changed.
Inter Terminals now has a combined bulk liquid storage capacity of more than 4.3m m3 (27m bbl) at 16 wholly owned multi-product terminals in the UK, Ireland, Germany, Denmark and Sweden. These terminals, the company says, provide comprehensive storage and handling solutions for the oil, chemical, and biofuel markets, complemented with a wide range of services for the general chemical, food, agricultural and pharmaceutical sectors, including the handling and management of technical wastes. HCB www.interterminals.com
HES INTERNATIONAL REPORTS that its Botlek Tank Terminal (BTT) subsidiary, located in the heart of Rotterdam’s chemical cluster, has put 277,000 m3 of new tank storage capacity into service. After this phase of construction, BTT’s tank capacity has now more than doubled to some 490,000 m3
Work is expected to start soon on the next phase of construction, which will add another 130,000 m3 of tank capacity and, in cooperation with the Port of Rotterdam, a jetty capable of handling Suezmax tankers.
“HES International has a longstanding history and a strong track record in providing safe and reliable storage and port infrastructure at key locations in Europe,” says Jan Vogel, CEO. “Our customers are large industrial clients that count on the reliability of our services and appreciate the quality and logistical advantages of our terminals. The realisation of these key infrastructure projects is a central part of this strategy. We are equally excited that we see similar developments and opportunities at most of our other terminals.”
HES International has also acquired the Valt Asphalt Terminal in Botlek, Rotterdam. The terminal, formerly part of a joint venture between Vitol and Sargeant, provides storage, handling and blending services for the European and African
bitumen market. “This acquisition is in line with HES International’s liquid bulk strategy to expand our storage footprint in Europe,” says Paul van Poecke, head of liquid bulk terminals at HES.
“HES International is a reputable market player and we are confident that the terminal’s customers will benefit from their professionalism and the planned enhancements to the terminal,” adds Dan Sargeant, Valt’s CEO.“At Valt we are focusing on optimising the logistical services we provide to our clients worldwide.”
The terminal, located close to HES’s existing Botlek Tank Terminal and adjacent to its European Bulk Services dry bulk facility, has a storage capacity of 30,000 tonnes and a quay capable of handling the largest
dedicated bitumen tankers. HES says it will invest to upgrade the terminal, now renamed HES Botlek Tank Terminal-Bitumen, over the course of 2018 with new tanks and ancillary infrastructure.
Meanwhile, work continues on the new Hartel Tank Terminal at Maasvlakte 1, also in Rotterdam, which is expected onstream early in 2019. HES is planning to build some 1.3m m3 of storage capacity at the site in tanks ranging in size from 5,000 m3 to 50,000 m3, primarily for petroleum products. Blending and additive injection will be offered. The Hartel site will have a quay long enough to accommodate three large or five small seagoing ships, with another nine berths for inland vessels in the Hudson harbour. HES says all product movements will be by vessel, with no road or rail transport involved.
HES International currently has six operating subsidiaries, all based in Rotterdam; three are involved in bulk liquids storage and three in dry bulk terminal operations. As well as Rotterdam, there are liquids terminal operations in Wilhelmshaven (Germany) and Gdynia (Poland); there are also dry bulk operations in Belgium, France, Australia and the US. HES International itself is owned by Riverstone Holdings and The Carlyle Group, following the acquisition of HES Beheer by Hestya Energy in 2014. HCB www.hesinternational.eu
Antwerp Port Authority has agreed to acquire Nationale Maatschappij der Pijpleidingen (NMP) from Ackermans & van Haaren and Electobel. NMP operates 720 km of pipelines, 90 per cent of which serve chemical and petrochemical companies in the port and its hinterland.
“Pipelines are the ideal mode of transport for the chemical industry and oil refining,” explains Port Authority CEO Jacques Vandermeiren. “By giving them access to a pipeline network that is open to all users we gain on at least two fronts: we help to reinforce the presence in the port of this sector which is so important for the economy of Belgium and Flanders, and the many logistics flows in and around the port area are further established in the Antwerp region. Furthermore, pipelines are the most environment-friendly, energy-efficient and safe means of transport.”
NMP was set up in 1978 by the Belgian government in order to coordinate the Belgian pipeline network for transport of petrochemical products. Over the past 40 years it has become
an important link in the cost-efficient logistics chains of many chemical and petrochemical companies in the port.
“O ur cluster companies confirm the importance of pipelines, but the high initial investment cost is frequently a barrier preventing them from actually switching to pipeline transport,” explains Vandermeiren.
“Because we really want to make the modal shift happen, with goods being carried by sustainable transport methods such as rail and barge, as well as by pipeline, not only are we taking over control of this pipeline network but we also seek to harness the know-how and expertise of the NMP personnel to further expand this network.
In this way the present chemical companies and others who come along in future will have an easier transition to pipeline transport, which is the most sustainable option for them.”
www.portofantwerp.com
Vopak has reported third-quarter EBITDA excluding exceptional items of €176.4m,
down from €203.8m for the same period last year. Revenues were down 5 per cent at €312.1m, overall, with declines in all operating divisions except the Americas (other than the US).
The company reports tougher market conditions in Asia as well as unexpected expenses during the quarter, including jetty damage in Singapore. Vopak says it is now expecting full year EBITDA to be about 10 per cent below last year’s €822m, taking account of market dynamics and the effect of terminals divested in 2016.
www.vopak.com
Viva Energy has put into service a 100,000-m3 crude oil storage tank at its Geelong refinery in Victoria, Australia. The tank is the country’s largest and will increase the company’s storage capacity by 40 per cent. It will also increase production capabilities at the refinery and improve fuel supply security in Victoria.
V iva Energy has also added a new jet fuel gantry at the refinery along with a new pumping station to increase pipeline supplies of fuel to Melbourne. It is also planning to install a 25,000-m3 gasoline tank and construct a bitumen export facility. www.vivaenergy.com.au
Mobil Oil New Zealand is to build two new tanks at its fuel terminal in Lyttelton to replace tanks damaged in a landslide in 2014.
“Construction of new tanks will restore fuel storage capacity at our Lyttelton operation, which, along with the Lyttelton-Woolston pipeline and Woolston Terminal, is an important part of the fuel supply chain in the South Island,” says Andrew McNaught, country manager for Mobil.
The new tanks, which will be used to store gasoline and diesel, are due in service in 2019. www.mobil.co.nz
Gibson Energy has posted third-quarter EBITDA of C$48.0m, up from C$45.6m a year ago, and a net loss of C$8.5m, down from a loss of C$30.8m in the previous year. “We continue to deliver strong operations while executing on our strategy to focus on growing our long-term, high quality cash flows within the Infrastructure segment,” says Steve Spaulding, president/CEO.
“During the quarter, Gibsons sanctioned an additional 1.1m bbl of new tankage at the Hardisty Terminal, demonstrating the asset’s commercial competitiveness in a modest oil price environment and providing additional visibility on how the company will continue to grow its Infrastructure segment,” Spaulding adds. The new capacity at the facility in Alberta is expected to be placed into service in third quarter 2019, bringing total capacity up to some 10m bbl.
Gibsons expects to invest between C$115m and C$140m in terminal expansion projects this year, mainly at the Hardisty site, lower than in previous years following major work at the Edmonton terminal. “We continue to expect that we will sanction one to two tanks per year on a run rate basis in a flat oil price environment, but also believe that the company needs to further leverage its existing asset base to drive additional growth,” Spaulding says. www.gibsonenergy.com
TransMontaigne Partners has reached agreement to acquire the Martinez and Richmond terminals in California from Plains All American Pipeline for $275m. The west coast facilities will expand TransMontaigne’s storage and terminalling footprint in the San Francisco Bay area refining complex. The deal was expected to close on or about 1 January 2018.
“ We believe that this transaction strengthens our position as one of the leading refined
products terminalling and transportation service providers in the country,” says Fred Boutin, CEO of TransMontaigne Partners.” Together, the two terminals offer some 5.4m bbl (860,000 m3) of storage capacity for refined products and crude oil in 64 tanks.
TransMontaigne Partners has also reported net earnings for the third quarter of $11.0m, down on the $11.9m recorded a year earlier, although consolidated EBITDA rose from $23.5m to $25.4m. The company achieved another quarter of record revenue of $45.4m, up 11.8 per cent year-on-year. The period also saw completion of the 2m-bbl first phase expansion of its Collins terminal in Mississippi; the company has recently received air permits for a second phase, which will add up to 5m bbl of additional capacity. www.transmontaignepartners.com
Blackline Midstream has acquired SEA-3, which owns a major propane storage and distribution facility in Newington, New Hampshire, from Trammo Inc. The new owners plan to expand rail access at the site “in order to
position SEA-3 as the most flexible and reliable propane supply terminal in the north-east US”.
The facility has a propane storage capacity of 530,000 bbl, rail and truck loading racks, and a marine dock capable of handling oceangoing vessels. In addition, SEA-3 has a fully approved upgrade project which will significantly increase the rail unloading capacity of the terminal giving it access to both domestic and international markets.
Blackline Midstream was formed in November 2017 by Blackline Partners LLC and TPG Sixth Street Partners with the purpose of acquiring and developing oil and gas midstream infrastructure assets. The SEA-3 acquisition is its first investment in the sector. Trammo’s Houston-based team involved in its operation have transferred to Blackline Midstream, which also has an office in Houston, and the SEA-3 terminal personnel will remain in place. “All existing commercial agreements will be carried forward, and customers of the terminal will experience a seamless transition following the acquisition,” says David Herr, who is managing commercial operations at Blackline Midstream. blackline-partners.com
HOYER MIDDLE EAST is currently building a new filling plant in Al-Jubail, Saudi Arabia on an area of around 10,000 m2. On completion later this year, the facility will offer four storage tanks, two blending tanks, two filling lines and a warehouse for palletised goods. The filling plant’s capacity will amount to some 30,000 to 50,000 tonnes per year.
This new investment is the first fruits of a new joint venture established by Hoyer in Saudi Arabia to help expand activities in the Supply Chain Solutions (SCS) division of its Chemilog business unit. Hoyer has acquired a 51 per cent stake in a Saudi-based business, with local partners Petrochem Middle East FZE and Al Fahdah Al Arabia Trading Company holding 24.5 per cent each, which has been named Hoyer Middle East Ltd.
“The joint venture pools the regional and international strengths of the two partners with the core competences of Hoyer as an international logistics company specialising in handling dangerous goods,” Hoyer states.
“Hoyer Middle East will offer extensive blending, filling, bulk storage, quality testing and dispatch processing services, together with warehouse storage of palletised and non-palletised goods,” Ulrich Grätz, global SCS director at Hoyer, elaborates. “We are specialised in handling in dangerous goods and satisfy the highest international environmental, quality and safety standards.”
Menno Douwes Dekker, managing director Middle East & India for Hoyer, adds, “It’s the
first professionally operated off-site blending and filling plant in Saudi Arabia, and therefore very attractive for chemicals producers with international operations. Furthermore, we can also offer international intermodal transport beyond the plant, because we collaborate closely with the Hoyer Business Unit Deep Sea.”
Establishment of the regional joint venture marks continued growth and geographic expansion in Hoyer’s SCS division. SCS now operates at 16 locations in five countries, and has recorded a doubling of its order volume since 2008, making it one of the strongest growing business activities within the Hoyer group.
“SCS scores points through the expertise of the Hoyer group in the logistics and handling of dangerous goods, and brings this know-how into its comprehensive, customer-oriented portfolio of services: on-site and off-site logistics, filling, blending, handling of liquid dangerous goods, dry-bulk logistics, the operation of intermodal and dangerous goods terminals, and planning support for change management projects in plants,” the Hamburgbased company explains. “The utilisation of synergies, efficiency and transparency are important values in this respect.”
So far, SCS’s operations have been largely confined to Europe, so the new Saudi business marks an extension into a new theatre of activity. SCS has more than 450 staff in Europe at a number of logistics facilities, many of them on third-party premises. The division leverages Hoyer’s infrastructure assets to provide them on a needs-oriented basis to its clients.
The Hoyer group as a whole, which was founded in 1946, employs some 6,100 people in more than 115 countries around the world; its assets include some 2,400 trucks, 2,900 road tankers, 37,300 tank containers, 41,200 intermediate bulk containers (IBCs) and numerous logistics facilities, including tank depots, workshops and cleaning stations. HCB www.hoyer-group.com
THE TALKE GROUP has announced that all of its operations in the Middle East are now operating to the standards demanded by the Responsible Care initiative, the global chemical industry’s voluntary scheme. Within the Gulf Cooperation Council (GCC) states, Talke says, it is one of the first chemical logistics providers to do so. Its regional operations are now entitled to use the Responsible Care logo.
A basic principle of the Responsible Care scheme is that companies should voluntarily follow stricter environmental standards than those required by local laws and regulations.
The parent company, Alfred Talke Logistic Services, has been affiliated to the Responsible Care programme since 2009 and, for its part, was one of Germany’s very first chemical logistics providers to join the initiative.
“By implementing Responsible Care standards for our activities in the Gulf, Talke is once again leading the way in promoting safe and environmentally sustainable chemical logistics activities. All around the world, we see responsible treatment of both people and the environment as one of the most important pillars of our business activities,” says Richard Heath, Talke’s director, Middle East & USA.
“Voluntary commitments such as Responsible Care and systems such as SQAS are of particular importance in the
Gulf region, as the statutory provisions there do not cover all fields in detail. In addition, by participating in Responsible Care, we are aiming to raise awareness of environmental matters among other market players and customers, too.”
Indeed, only a couple of years ago Richard Heath played a leading role in developing a pilot project for the Gulf Petrochemicals and Chemicals Association (GPCA) aimed at establishing SQAS standards in the GCC area. That initiative, originally developed by the European Chemical Industry Council (Cefic), is designed to create a uniform set of metrics for assessing logistics companies’ performance in terms of health, safety, security, environment and quality (HSSEQ).
Talke has three joint ventures in the GCC states. It established Aljabr-Talke in 2004 in Saudi Arabia along with its partner Al-Jabr Group; another Saudi company, Sisco, later joined the venture, which is now trading as SA Talke. This company mainly handles polymer granulates and liquid chemicals for industrial customers in Al Jubail.
An Omani joint venture was also established with Al-Jabr Group in 2006, which provides efficient logistics for polymer granulates in the Gulf of Oman area. The newest joint venture in the region, RSA-Talke, was formed in collaboration with RSA Logistics in 2013. This is based around a chemical warehousing facility in the Dubai World Central industrial complex, which offers more than 19,000 pallet spaces for hazardous and non-hazardous materials. It is also well positioned to take advantage of regional and international transport links via the port of Jebel Ali and Dubai’s Al Maktoum International Airport.
Around the world, the Talke Group handles the bulk liquid, dry bulk and palletised transport of chemicals, polymers and other goods using a range of transport assets, including road tankers and tank containers. It also offers warehousing services, packaging, sampling, tank and silo cleaning, clean room drumming and other value-adding services, and operates a container terminal and rail link at Hürth, near Cologne in Germany. HCB www.talke.com
furnishes customers from the chemicals and other industrial sectors with numerous intermodal services, trucking services, managed services, international transportation management and consulting. Meanwhile, its bulk transport businesses provide “safe, reliable and cost-effective service for over-the-road tank truck, ISO tank for domestic and international shipments and rail transfer services”.
Maintaining a presence throughout North America, Europe and Asia, Odyssey operates “in all modes of transport” and is also able to offer its customers access to the Odyssey Global Logistics Platform, which “features a transportation management system that supports the safe, reliable and efficient delivery of client products throughout the world”. At the same time, its Web Integrated Network (WIN™) offers “a scalable technology solution with an accelerated deployment and faster time to value”.
& Technology reports that its Linden Bulk Transportation subsidiary, a specialist provider of chemical logistics services it acquired in 2016, has expanded its bulk transportation footprint in Joliet, Illinois. The new location, it continues, “positions Odyssey to offer its customers additional capacity and services in the greater Chicago and Midwest region”.
“Expanding our footprint and adding to our fleet addresses the capacity shortage issue that’s affecting the entire shipping industry,” says Linden’s chief operating officer Michael Salz. “Additional capacity in this area is a huge benefit to our clients and helps increase our productivity by significantly increasing our loaded miles. This also positions us for organic job growth by adding more drivers.”
Boasting a strategic location in close proximity to Chicago, Milwaukee and Indianapolis, the Joliet facility provides what Odyssey describes as “easy access to all major roadways and railways throughout the region that feed into national routes”. Furthermore, as a part of the expansion, Odyssey is adding new tractors and trailers, as well as relocating current equipment from other regions of the country to supplement the new site.
In addition to being an expansion of Linden’s growing network, the Joliet location will also utilise the onsite services of Quala, North America’s largest independent provider of industrial container cleaning services, including tank trailer, tank container, railcar and intermediate bulk container (IBC) cleaning.
A “global logistics solutions provider with a freight network of over $2bn”, Odyssey
Moreover, this past August Odyssey announced that an affiliate of the Jordan Company, “a middle-market private equity firm that manages funds with original capital commitments in excess of $8bn”, had signed a definitive agreement to become its new majority shareholder. “With the Jordan Company, Odyssey will continue its path of strategic growth, both organically and through acquisitions,” says Odyssey president and CEO Bob Shellman.
“This transaction underscores our consistent focus on providing broader service offerings, a larger transportation network and advanced technology to enhance our global supply chain capabilities,” he continues.
“As we enter this new and exciting phase in our company’s evolution, we thank our loyal customers for their support and our dedicated employees for the contributions that have made Odyssey so successful.”
“The Jordan Company targets partnerships with established and profitable companies like Odyssey,” adds Jordan Company senior partner Brian Higgins. “We are excited to partner with Odyssey’s leadership team and to support their vision for continued growth through investment in services and technologies for their customers.” HCB www.odysseylogistics.com
CHEMICAL DISTRIBUTORS HANDLE all sorts of products and, for a company like Brenntag, in all sorts of volumes. One large-volume product distributed by Brenntag North America is diesel exhaust fluid (DEF) which, although non-hazardous itself, is corrosive to certain metals – notably copper and brass. As such, handling DEF demands care in the choice of materials used in transfer equipment.
DEF is a non-toxic, high-purity solution comprised of 32.5 per cent urea and 67.5 per cent de-ionised water. Using this fluid in dieselpowered vehicles helps to reduce the amount of nitrogen oxides (NOx) emitted into the air by 90 per cent.
“We started delivering DEF in the US in 2009,” says Alan Smith, DEF business director for Brenntag North America. “Since then, we have made significant investments in DEF-dedicated terminals and delivery assets across the US and Canada. We have more than 25 dedicated DEF tankers and around 31 DEF rail locations in the US. These assets make us unique in the DEF space. We have a broad global network with outstanding local execution, allowing us to supply a wide variety of customers, including fleets, distributors, OEMs and truck stops.”
Delivering DEF can be challenging and must be handled by specifically designed equipment and vehicles. DEF is incompatible
with materials such as copper and brass, and can lead to corrosion of these materials. This means that any transport used to haul DEF, as well as all of its wetted components, needs to be made of stainless steel or approved plastics such as high density polyethylene (HDPE). This ensures fluid will not become contaminated by trace quantities of metals during its handling and transfer. The same goes for the pumps used to transfer DEF to and from vehicles.
“The main consideration when choosing a pump for a DEF application is the materials of construction,” says Matthew Sparrow, a DEF mechanical engineer for Brenntag North America. “All materials that come in direct contact with DEF must be compatible to avoid any contamination of the fluid. To ensure that all our equipment is compatible, we follow ISO 22241-3 standards, which describe best practice recommendations and requirements for the handling, transporting and storage of DEF.”
“It is essential to deliver clean, noncontaminated DEF fluid to customers,” adds Smith. “Vehicles using contaminated DEF are in danger of suffering severe damage to their SCR system. A majority of issues encountered stem from material-of-construction issues; either the wrong materials are selected or materials not on the recommended list were not properly tested by a third-party lab.”
Another major issue is downtime and leakage. When DEF dries a white crust will appear. This residue can create havoc on the internal pump components, connectors, seals and anything else that comes into contact with the fluid. Improper design can cause the equipment to lock up or leak, resulting in costly downtime or a messy clean up.
When it came time to select a transport pump capable of interacting positively with DEF during the loading and unloading process, Brenntag North America turned to STX-DEF series sliding vane pumps from Blackmer.
“We use STX-DEF pumps at our terminals to unload railcars, transfer product from one tank to another, and to load and unload tank trucks,”
explains Sparrow. “With the addition of either a bypass line or VFD (variable frequency drive), the STX-DEF pump can also be used to fill drums and totes. In addition, we use Blackmer pumps on our internal DEF tanker fleet to fill customers’ drums, totes and mini-bulk tanks. These pumps are the ideal solution for applications with long runs of piping, when suction hoses and piping need to be stripped dry, or when precise flow rates are desired.”
STX-DEF pumps from Blackmer feature 316 stainless steel construction with external ball bearings, chemical-duty mechanical seals, PTFE elastomers and non-metallic vanes, making them the ideal choice to handle DEF. These features allow STX-DEF pumps to meet the ISO 22241-3 material standards and cleanliness specifications required for DEF-handling applications.
The specific models used by Brenntag North America in its DEF streams offer high-capacity flow rates up to 250 gpm (946 l/min) and pump speeds up to 800 rpm for delivering fast fluid offloading. A 6,000-gallon (22,700-litre) tanker can be unloaded in about 24 minutes using the STX3-DEF pump. For other applications Brenntag uses Blackmer pumps with lower flow rates.
The STX-DEF Series pump’s non-metallic vanes also self-adjust for wear in order to maintain flow rate, while minimising shear and agitation. An adjustable relief valve protects the pump from excessive pressures. The pump has excellent self-priming and dry-run capabilities and maintenance is reduced because internal wear is almost completely limited to the easily replaced sliding vanes, which can be changed out without needing to take the pump out of line.
“Blackmer DEF pumps have an excellent service record,” says Sparrow. “Our facilities have reported less downtime and repair work since installing Blackmer pumps. The wetted
components have long service life, and the housings, gearboxes, motors and frames hold up well in indoor and outdoor applications. Only a handful of pumps have ever needed repairs over the last five years and, thanks to their excellent design, repairs are typically completed in a day or less depending on the availability of parts.”
“Bottom line is Blackmer pumps work extremely well with DEF thanks to their many features and benefits,” Sparrow concludes.
“As Brenntag continues to build its internal infrastructure for DEF, Blackmer pumps will continue to be an essential component. In addition, we also will continue to recommend Blackmer pumps as an approved equipment solution for our customers’ mini-bulk and bulk applications.”
Part of the Germany-based Brenntag group, Brenntag North America, headquartered in Reading, Pennsylvania, is responsible for
providing business-to-business distribution as well as sales and marketing solutions for industrial and specialty chemicals throughout the US and Canada. This responsibility includes managing complex supply chains for both chemical manufacturers and consumers and then streamlining processes to provide market access to thousands of products and services.
Brenntag itself traces its history back to an egg distribution business formed in Berlin in 1874; its move into chemical distribution started after a relocation to Mülheim an der Ruhr, close to the Dutch border, in 1943. Since then the company has grown around the world and now has a global network of more than 530 locations in 74 countries, offers more than 10,000 products, employs more than 14,000 people and serves more than 150,000 customers worldwide. HCB www.brenntag.com www.blackmer.com
CHINA • THE CHEMICAL INDUSTRY LANDSCAPE IN CHINA IS CHANGING RAPIDLY, SPURRED BY REGULATORY DEMAND FOR SAFER OPERATIONS AND REDUCED ENVIRONMENTAL IMPACTS
CHEMICAL MANUFACTURERS AND logistics service providers (LSPs) active in China need to be aware of the changes currently being driven by the 13th five-year plan for hazardous chemicals, which covers the period 2016 to 2020. Jerry Xu, conference organiser for AIT Events, which is to host the Hazardous Chemicals China (HCC) event in Hangzhou in September 2018, explains how the plan is changing the business landscape.
Around 10 million people in China are employed in the chemical industry and its supply chain, working for 19,000 registered chemical producers, 265,000 companies involved in distribution and trade, and a further 5,500 firms specialising in chemical
storage. In recent years the industry has responded to government calls for greater safety, with many companies either shutting up shop or relocating to dedicated chemical industry zones. There has also been significant investment in renovating chemical storage and handling equipment.
Nevertheless, there is some way to go. There are plenty of bottlenecks in the production and distribution sectors, Xu says, and few domestic companies have deployed advanced safety and process safety management systems. While 2015 saw the number of chemical industry accidents fall below 100 for the first time – there were 97 reported accidents involving 157 fatalities –there is clearly room to improve the situation further, and a need to retire outdated facilities.
The 2016-2020 chemical industry plan demands a 10 per cent drop in the number
of accidents and an increase in the amount of research and development work put into safety management in the sector. Xu expects there will be pilot projects to examine how the application of new safety management techniques work in practice and how they can contribute to improving the safety record.
Xu identifies some technologies that Beijing wants industry to focus on: these include gas monitoring, pipeline leak monitoring, control and alarm systems at facilities handling high-hazard chemicals, and safety instrumentation management. Xu also says there will be a focus on information sharing, using online systems to alert supply chain participants to accidents and building an online catalogue of dangerous chemicals. Further, the plan envisages the development of a single platform for supervision and data sharing in the movement of explosives and high-hazard chemicals, based on hazard communication elements.
Finally, a single nationwide centre for accident inspection and analysis will be set up, with the aim of collecting and evaluating accident data and developing warning systems for the chemical and oil pipeline sectors.
What all this means is that there is plenty of opportunity for international firms, already well versed in the provision of safety systems for the chemical industry and its supply chain, to apply their expertise in helping to develop the same levels of safety in industry in China. The HCC event, which will take place in Hangzhou on 5 and 6 September this year, will provide a marketplace to allow them to put that expertise on display.
Xu explains that the HCC event has been designed with this in mind, with separate zones for products and services aimed at the transport and logistics sector; “intelligent planning” in chemical manufacturing; wastewater and gas disposal techniques; intelligent technologies for monitoring and reporting; incident response and rescue; security inspection and occupational health; monitoring and alarm technology and equipment; and industrial repairs and maintenance. HCB
Full information on the event, which is being supported by HCB, can be found at www.hcchina.org.
INEOS HAS SIGNED a contract to partner with Imperial Logistics to design and build the largest butane river barges ever used in Europe. These barges will link the world’s largest butane tank, currently under construction at the Oiltanking Antwerp Gas Terminal (OTAGT) in the Port of Antwerp, Belgium, with the Ineos site in Köln to enable one of the largest crackers in Europe to be supplied with large volumes of butane as well as naphtha as a feedstock.
These new state-of-the-art barges will move about 3,000 tonnes of butane each, which is about three times as much as the current barges move on the Rhine system. The shipyards to build these new barges will be selected in the near future and the barges will be operational in 2019
Hugh Carmichael, director of Ineos Trading & Shipping, says: “This agreement represents a further step in a strategic investment in the future of our naphtha crackers in Köln. The new butane tank in Antwerp and the Imperial butane river barges will provide Ineos with increased flexibility and security of supply that will significantly improve our competitiveness in Europe. It also positions Ineos as a major
player in global LPG markets. We are pleased to work together with Imperial Logistics as a major barge operator in this unique project. Our joint expertise and experience will help make this a successful project.”
Steffen Bauer, COO at Imperial’s Business Unit Shipping, adds: “We are very delighted to be awarded as project partner from Ineos. To design and build the largest butane river barges ever used in Europe is an extraordinary challenge.”
The deal with Imperial marks a continuation of Ineos’s process of investing in supply chain flexibility at its European facilities, supported by similar investment by its supply chain partners. Oiltanking is currently almost doubling capacity at OTAGT, building a 135,000-m3 fully refrigerated tank – Europe’s largest – to receive butane from oceangoing gas carriers of up to VLGC size.
Similarly, LPG tanker operator Evergas has now built eight 27,500-m3 ‘Multigas’ carriers designed to carry ethane from the US to Ineos crackers at Grangemouth, UK and Rafnes, Norway. That supply chain is designed to reap the benefits of low-cost ethane from North American shale gas and improve the competitiveness of Ineos’ European petrochemical manufacturing, but was only enabled by investment in ground-breaking ship technology. That was recognised in September 2017 when Evergas was presented with the Innovation Award at the annual Lloyd’s List Global Awards. A similar level of innovation is likely to be needed in the design and construction of the new barges Imperial will build.
Ineos has 105 manufacturing facilities in 22 countries around the world, employing some 18,500 people. Imperial Logistics, a wholly owned subsidiary of South Africabased Imperial Holdings Ltd, is responsible for coordinating and managing all the group’s international logistics businesses outside Africa. The shipping business unit is part of Imperial Transport Solutions, based in Duisburg, Germany. HCB www.imperial-international.com www.ineos.com www.oiltanking.com
Katoen Natie and its partner Allied are to introduce the SuperTruck concept in Singapore. The SuperTruck design can carry two 40-foot or four 20-foot dry freight or tank containers at a time. The trucks will be used to move product between chemical plants, Katoen Natie’s logistics terminal and local container terminals.
The move follows the introduction of driverless vehicles in depot operations; both innovations are prompted at least in part by the need to address the shortage of drivers in Singapore. Katoen Natie and Allied are working with the Singapore government authorities on the certifications and operational framework for the SuperTruck.
“ We are continuously looking for innovative and new solutions to optimise our logistics operations,” says Koen Cardon, chief executive of Katoen Natie Singapore. “We work with our business partners to introduce new solutions to increase productivity and efficiency. We have been working closely with Allied to implement this SuperTruck concept whereby they have demonstrated entrepreneurship and innovative
thinking. Shortage of drivers is a real challenge in Singapore and we need such innovative solutions to address this.” www.katoennatie.com
The Talke Group has won a five-year contract from Qapco to handle the management of all logistics activities at its production facility in Mesaieed, Qatar. The deal covers warehouse logistics, packing finished products, the administration and provision of spare parts for the petrochemical plants as well as servicing and maintenance of all the logistics equipment within the entire production facility.
The spectrum of chemical and petrochemical substances stored and handled at the Qapco site ranges from hazardous materials of nearly all classes to harmless polyethylene granules of the highest quality, which are prepared for transport.
In addition, Talke is taking over both the loading and unloading of oceangoing vessels with liquid chemicals, gases and finished products and the servicing and maintenance
of heavy dockside equipment, such as straddle carriers and cranes.
Talke and Qapco have been working together since 2008, with their cooperation gradually expanding. “This latest award from Qapco serves both as recognition for our past performance and as an incentive to continue striving to improve still further,” says Richard Heath, Talke’s director, Middle East & USA. “We also see it as further confirmation that our strategy of integrating ourselves into the supply chains of our customers with an explicitly broad spectrum of high-quality and well thought-out services is right.”
www.talke.com
Suttons has won a five-year contract to deliver carbon dioxide for Praxair to customers across the UK. The deal builds on a 13-year business relationship, adding telemetry management to the existing long-term partnership.
“ Working in partnership with Suttons gives Praxair a number of advantages in the market including flexibility which enables us to respond to our customers’ changing needs,” says Mark Patterson, head of commercial and supply chain, UK at Praxair. “Our strong relationship with Suttons further builds on our aligned values of safety, service and flexibility. Suttons’ reputation for these values is well regarded in the industry and, as has already been proved, we are a natural partner to further develop these core values.”
www.suttonsgroup.com
Odyssey Logistics & Technology has announced that its Linden Bulk Transportation subsidiary
has expanded its operations in Joliet, Illinois. The site’s strategic location provides easy access to regional and national highways and railroads. “Expanding our footprint and adding to our fleet addresses the capacity shortage issue that’s affecting the entire shipping industry,” says Linden’s chief operating officer Michael Salz. “Additional capacity in this area is a huge benefit to our clients and helps increase our productivity by significantly increasing our loaded miles.”
Among other things, the Joliet location will now utilise onsite services provided by Quala, which Odyssey describes as “North America’s largest independent provider of industrial container cleaning services, including tank trailer, ISO container, railcar and IBC cleaning”. Linden will also add new tractors and trailers, and will relocate existing equipment from other regional depots. www.odysseylogistics.com
Carsten Taucke has given the board of Imperial Logistics International a year’s notice of his intention to step down as CEO and leave the company at the end of November 2018. “Over the next twelve months, Carsten Taucke will actively continue to lead the company with his typically strong commitment and focus on results in all areas of his responsibility,” says Marius Swanepoel, CEO of the Global Logistics Division at Imperial Logistics. Taucke will also be closely involved in the selection
of his successor and in the handover of his management responsibilities to that successor.
Meanwhile, Christian Berlin has been appointed director of Imperial Logistics’ road business unit, which operates some 600 road tankers in liquid foodstuffs, chemicals and gases service. He succeeds Steffen Bauer, who moved to become COO of Imperial’s shipping business earlier this year. Berlin was previously assistant to the CEO and has also managed the company’s business in China.
In other news, Imperial Logistics has agreed to sell its Schirm contract manufacturing subsidiary to South Africa-based chemicals company AECI Ltd. The deal, which is subject to approval by the authorities in Germany and South Africa, is valued at some €110.5m. Imperial acquired Schirm as part of its takeover of Lehnkering in 2011 but says that the third-party chemical manufacturing operation does not fit into its core business of transport and logistics. As part of the deal, AECI will rent four warehouses adjacent to the Schirm plant at Schönebeck, with a 12-month purchase option.
www.imperial-international.com
DOGGETT THE MAN FOR CLUGSTON Clugston Distribution has appointed Tim Doggett as distribution director. Doggett arrives from Rhenus Logistics, where he was general manager, responsible for sales and operations across the north-west of England.
Bob Vickers, chief executive of the Clugston Group, says of Doggett: “His experience across
a broad range of logistics roles will be vital to the division as we continue to examine ways to further expand our offering to both new and existing customers.”
“I’m proud to have a joined a company with such a strong history within the industry, and particularly in its 80th anniversary year,” adds Doggett. “I am looking forward to working with the team to further develop opportunities for the division and the Group.” www.clugston.co.uk
Greiwing has begun construction of a new €33m logistics centre in Burghausen in southern Bavaria, close to the Austrian border. The 60,000-m2 facility, due to enter into service late in 2018, is designed to offer contract logistics services for major customers at the nearby chemical parks, primarily for polymers and other granular chemicals. Part of one warehouse will eventually be used to handle hazardous and environmentally sensitive chemicals. The facility will be directly connected to the combined transport terminal in Burghausen.
“ The investment in a location in the Bavarian Chemical Triangle is also the result of our strategy of expanding the contract logistics division,” says Jürgen Greiwing, managing partner. “Even today, our services are an integral part of the value chain of many of our customers. And we continue to see potential that we do not want to leave unused.”
www.greiwing.de
recruiting and retaining member companies. She has provided a voice for those whose resources are limited but who fervently believe in the values and ethics of NACD. She’s accomplished this all while tirelessly leading our Membership Advancement and Retention Committee.”
At the same time, David B Garner of Brenntag North America has been awarded an NACD Lifetime Achievement Award. Marking only the sixth time in the Association’s 46-year history that this gong has been given, Garner was honoured with the award after, in NACD’s words, dedicating “his career to enhancing safety through training, mentorship, exercises and drills and incentive programmes as well as the creation of management systems with metrics to demonstrate improvement in safety”.
Additionally, Garner has also spent “countless hours providing NACD staff and peers in the industry with information, guidance and support through regulatory comments, communicating the hard work NACD members perform day in and day out to key stakeholders and advocating for better laws and regulations.”
JOSEPH FISCHMAN AND Andrea Nagle of Chem/Serv have jointly won the US National Association of Chemical Distributors’ (NACD) 2017 Distributor of the Year Award. Recipients of the award, NACD explains, “demonstrate outstanding commitment to the chemical distribution community” and “work steadfastly” on behalf of both the Association and the entire industry.
As well as having served on two NACD standing committees and the NACD Board of Directors, Fischman has hosted site visits with Congressional representatives and members of his local government while also participating in business roundtables with elected officials.
“Joe has played a critical role in advancing NACD’s advocacy efforts over the years,” says NACD president Eric R Byer. “He’s led these efforts with clear vision, passion and dedication by devoting an incredible amount of time and effort to his company and the industry as a whole and we’re proud to present him with this award.”
Nagle, meanwhile, has also served on the Association’s Board of Directors for two years and on a standing committee for nine. Throughout this time, NACD says, she has been “a thoughtful proponent for the role of the small distributor in NACD” as well as helping “to mitigate the challenges for a small distributor to fully participate in the Association”.
“Over the years,” Byer states, “Andi has contributed greatly to the growth of our association programmes targeted at
“Dave is the consummate safety professional,” says Roger Harris, president and CEO of Producers Chemical and a previous recipient of the award. “Over the years, he has taught us what it means to take safety seriously. He’s been a mentor, educator, a resource to some and a role model to everyone. It is my distinct pleasure to present this Lifetime Achievement Award to my trusted friend and colleague, David B Garner.”
All three presentations were made at NACD’s recent 46th Annual Meeting in San Antonio, Texas. Described by NACD as “the premier chemical distribution industry event of the year”, the 2017 meeting saw around 575 attendees “joining together to discuss opportunities for companies to improve business performance, management skills, recruitment and more, while getting in-depth insights into the latest trends and future of the industry”. HCB www.nacd.com
Univar has reached an agreement to acquire Kemetyl Industrial Chemicals (KIC). A division of the Kemetyl Group, KIC, Univar says, commands annual sales of around $30m and “is among the leading distributors of chemical products in the Nordic region”, providing both bulk and speciality chemicals to customers across Sweden and Norway.
“ The Nordic region is at the forefront of global R&D when it comes to life sciences, which makes this agreement a smart and strategic move to build our customer base and enhance our market expertise,” says Univar chairman and CEO Steve Newlin. “This acquisition will allow Univar to expand its leading position in pharma and strengthen its expertise in water treatment.”
“ We are very satisfied with the development of Kemetyl Industrial Chemicals over the past several years,” adds Kemetyl Group board chairman Ketil Stave. “In our ambition to further focus our business around consumer chemicals, this divestiture is a logical step to ensure that our industrial customers continue
to get the level of service and expertise they deserve. It has been a pleasure to work with the Kemetyl Nordic Industry team. I believe there is a tremendous match with Univar’s outstanding service and capabilities and we are convinced that they are in the best position to further develop and grow this business.”
Commenting on the news, Nick Powell, Univar’s EMEA president, states: “This is a great pairing of capabilities that gives Univar the ability to be even more competitive in the European market. The agreement supports our global corporate strategy to pursue market expansion and acquisitions, to continue profitably growing our core business and to accelerate growth by focusing on chosen industry segments. Both companies have deep experience and key competencies within the life sciences market and we welcome this opportunity to expand Univar’s reach within the water treatment sector, allowing us to forge deeper customer relationships.”
Meanwhile on the financial front, Univar and its wholly-owned subsidiary Univar USA have entered into an amended credit agreement
with Bank of America NA and other lenders to provide a new Term B loan facility in an aggregate principal amount of just under $2.3bn. This replaces all of the company’s US dollar loans and $96.3m of euro loans outstanding under its previous credit agreement dated 1 July 2015. “The amended term loan facility reduces the company’s interest rate from LIBOR plus 2.75 per cent to LIBOR plus 2.50 per cent,” Univar says. “This rate will be further reduced to LIBOR plus 2.25 per cent when the company’s total net leverage (total net debt to adjusted EBITDA) falls below 4.0.” www.univar.com
US-headquartered Nexeo Solutions has announced a fiscal 2017 net income of $14.4m from sales and operating revenues worth $3.6bn. This compares to a fiscal 2016 net loss of $8.4m from sales and operating revenues of just under $1.1bn. Meanwhile, for the fourth quarter of the year, it achieved a net income of $13.6m from sales and operating revenues worth $981.7m as opposed to respective prior-year figures of $8.7m and $851.4m.
“I am pleased to report we delivered our third consecutive quarter of double-digit adjusted EBITDA growth,” says president and CEO David Bradley. “Our results are attributable to our team’s commitment to connecting our customers and suppliers utilising our proprietary operating platform which gives us the ability to react in real-time to changing market conditions and provide a unique level of transparency to our partners. We continue to execute well on our strategy and, with the macro-industrial environment showing signs of improvement, we have
good momentum in the business as we enter fiscal year 2018.”
In other news, Nexeo has expanded its partnership with Polynt-Reichhold to represent the latter company’s full range of coating lines across the southern US. The news comes after Polynt-Reichhold announced plans to re-align its coatings distribution networks to regional partners following its creation through the merger of Polynt Composites and Reichhold.
“ We are pleased to represent PolyntReichhold in the market,” says Joey Gullion, Nexeo’s vice-president of specialty chemicals. “This authorisation complements our market-leading product portfolio and is strong validation of our technical capabilities to our customers.”
www.nexeosolutions.com
Brenntag-owned Multisol UK reports that it “has excelled” in its recent BSI Audit for the new ISO 9001:2015 and ISO 14001:2015 standards. Multisol “consistently operates to the highest levels of quality, professionalism, safety, health and environmental management, an ethos demanded of every employee,” the company says, adding that by utilising these skills it is able “to meet and exceed customer expectations” while putting “environmental management at the heart of the business” and providing “the framework for making safety its number one priority”.
Commenting on the news, group compliance manager Mary Hibbs states: “This achievement
further demonstrates our continued commitment to provide excellent quality products and services to maximise value for our customers, minimise waste and improve our energy efficiency.” www.multisolgroup.com
Valtris Specialty Chemicals has named Krahn Chemie as its new distributor for the Santicizer® line of speciality plasticisers across Germany, Poland, the Benelux countries, Switzerland, Slovakia, Hungary, Romania and the Baltic states.
“ Valtris Specialty Chemicals is a renowned manufacturer of products for the field of flexible PVC,” says Krahn’s managing director Axel Sebbesse. “The cooperation completes our extensive portfolio when it comes to highly technical plasticisers. Valtris’ range of phosphate esters will help us [in] providing non-halogen solutions to our customers in line with the new flame retardant norms which are more and more orientated towards low smoke.” www.krahn.eu
Algol Chemicals reports that it recently commissioned an independent research firm to conducted a customer satisfaction survey among a random sample of customers both in its home country of Finland and elsewhere.
“By commissioning an independent research company to conduct the survey, we wanted to obtain honest and constructive feedback
from our customers,” the company says.
“The feedback was gathered by means of both interviews and traditional questionnaires. According to the survey results, [the] majority of [customers] are either satisfied (42 per cent) or very satisfied (48 per cent) [with] our operations in general.”
“ We managed the best in terms of company image, innovativeness of products and services, locality and handling of claims,” it continues.
“We still have some room for improvement with our price-quality ratio, deliveries and communication in general. These will be the topics we’ll be focusing [on] even more in the future.”
www.algolchemicals.com
Germany’s Lehmann & Voss has begun construction of a new laboratory and technical centre at its Hamburg Wandsbek site. The €4.5m development will feature state-of-the-art technical infrastructure and equipment and is expected to open during the first half of 2019 in time for the company’s 125th anniversary.
“Ever since its foundation, Lehmann & Voss has attached great importance to having a high technical expertise available in its business units and market products tailored to the individual customer,” says managing partner Dr Thomas Oehmichen. “With the construction of the new laboratory and technical centre we want to make sure that we maintain and continue to strengthen our leadership position.”
www.lehvoss.de
A NEW MARKET report from Smithers Pira estimates that annual worldwide industrial packaging sales topped $52.7bn by the end in 2017. What’s more, the report, The Future of Industrial Packaging to 2022, forecasts this value to grow across the next five years at an annual rate of 3.2 per cent to reach nearly $61.9bn by 2022. Moreover, while the materials used to produce the main industrial packaging formats, viz sacks, intermediate bulk containers (IBCs), drums, crates and totes, came to around 14.6m tonnes in 2017, the report anticipates this figure to increase at an annual rate of 2.7 per cent across the same period to reach 16.6m tonnes.
Consumption increases, the company says, “will continue to be driven primarily
by the faster-growing transition economies of Asia, central and eastern Europe and Africa, rather than the more mature advanced economies of western Europe, North America and Japan”. However, “despite this impression of stability, complex dynamics are acting to restructure the industrial packaging sector” as a whole.
“Gradual changes along the supply chain that have been brought about by market and technology developments will have implications for the future of industrial packaging formats and markets,” says report author David Platt. “These include 3D printing, the Internet of Things (IoT) and the switch to dimensional weight pricing in the consumer parcel shipping business.”
“A deeper disruption is the increasing automation of industrial shipment chains – part of the broader technology trend
toward Industry 4.0 – including the merging of automation and data exchange in manufacturing technologies, combining cyber-physical systems, the IoT and cloud computing,” he continues. “As a key part of the supply chain, the packaging industry really needs to be aware of what changes in the fourth industrial revolution are likely to be and how these will impact on processes and profits.”
In terms of the particular packagings used by industry, the report notes that flexible intermediate bulk containers (FIBCs) “will register steady growth due to the advantages they offer in terms of efficiency, loading and unloading products”. Overall, however, “rigid industrial packaging containers are forecast to grow at a faster rate than flexible formats”.
Plastics drums in particular “will post above-average gains based on cost and performance advantages” over fibre and steel units. That said, in the industrial packaging sector, “a key concern is the overall protection provided by the packaging, particularly when dealing with the transport of hazardous materials”. Consequently, the degree of substitution from steel to plastic drums for the handling of industrial products “is limited because of safety regulations that apply to various hazardous products”. In instances where this switching is plausible, though, “the relative cost of steel versus plastics remains the principal driver”.
“As the market evolves there will be internal shifts, such as the wider use of [IBCs] and above average demand from key end-use applications, like chemicals and pharmaceuticals,” the company says, adding that the report’s “comprehensive analysis tracks and quantifies these trends by value, volume and packaging units, with unparalleled precision”.
The Future of Industrial Packaging to 2022 includes more than 280 tables and is available from the Smithers Pira website priced £4,500 per copy. HCB www.smitherspira.com
GREIF HAS ANNOUNCED that it is to deploy 3,000 new branded trailers to better serve its customers throughout North America. Commenting on the move, Adam Galliers, Greif’s senior manager, logistics and supply chain, states: “This multi-million-dollar investment is an expression of our commitment to be industrial packaging’s best performing customer service company in the world. These new trailers will provide our customers additional assurance their valued packaging will be protected from contamination and reduce the risk of damage during transit.”
The new fleet, the company asserts, will provide “optimised load capacity by increasing
the number of containers per trailer by 5 to 10 per cent, which reduces the number of trailers on the road”. At the same time, this allows “for safely loading and unloading of the trailers and reducing the man hours needed for customers to unload their shipments”. Furthermore, the “improved fuel efficiency and dependability of the trailers” will be “environmentally beneficial” to customers in terms of reduced emissions.
While new trailers have already begun delivering products to customers, the entire process of replacing the company’s older fleet is expected to take approximately six months. Greif says it will continue to partner with trucking companies to manage all trailers concerned. “Greif strives to deliver on time and in full,” Galliers says. “This new fleet will help to ensure we meet these goals and help our customers be more successful.”
Greif has meanwhile posted a fiscal 2017 net income of $118.6m, up from $74.9m the previous year, from net sales worth just over $3.6bn, themselves up from $3.3bn. For the fourth quarter, the company similarly saw its net income rise from $8.5m 12 months ago to a new figure of $33.3m, while net sales grew over the period from $867.6m to $968.1m. “We continued to make Greif a stronger and more profitable business in 2017, with solid earnings and cash generation,” says president and CEO Pete Watson.
“Our focus on customer service excellence continues to strengthen and we are driving a continuous improvement mindset to create stronger sustainable performance,” Watson states. “Our plans for fiscal 2018 and beyond remain focused on our teams being accountable to execute on our commitments and to deliver superior value to our customers and shareholders.”
In terms of its Rigid Industrial Packaging & Services division, the company finished the fourth quarter with net sales worth $662.5m, an increase on the prior year quarter of $59.6m. “Net sales excluding divestitures and foreign currency translation increased by $52.3m due primarily to an 11.1 per cent increase in selling prices and product mix on our primary products stemming from strategic pricing decisions and increases in index prices,” the company says. Nevertheless, both the segment’s gross profit and operating profit fell over the period, decreasing, respectively, by $12m to $118.9m and by $6m to $24.5m. This, Greif reports, was largely the result of increased raw material prices and the impact of “adverse weather events”.
The company’s Flexible Products & Services arm, which among other things represents the world’s largest producer of flexible intermediate bulk containers (FIBCs), saw its quarterly net sales increase by $7.1m over the period to $76.2m “due primarily to strategic pricing decisions”. Gross profit increased by $0.3m to $12m, while operating profit rose by $3.9m to $0.3m. HCB www.greif.com
Earnest Beardsley, co-founder of Ohioheadquartered North Coast Container (NCC), has been posthumously honoured with a Lifetime Membership Award by the US Industrial Steel Drum Institute (ISDI). Given to long-time members of the steel drum industry in recognition of their service and dedication, the award was presented to Beardsley’s son, Jim Beardsley, current chairman and CEO of NCC. “It is with great honour that I accept this award on behalf of my father,” Beardsley said. “His dedication and entrepreneurial spirit drove him to build a world-class steel drum business and I couldn’t be prouder to follow in his footsteps.”
Earnest Beardsley began his career in 1950 at Ohio Corrugating Company as an hourly employee, later graduating from Youngstown College. Determined to own a steel drum company, he worked his way up at several organisations, including United Steel Services, Cleveland Steel Container and Cortland Container, “cultivating his knowledge of the steel drum industry along the way”. In 1983, Beardsley and his business partner Randy Reed purchased Cortland Container and founded NCC, where he worked until his retirement in 2011.
“Ernie was a pillar in our industry and I am privileged to formally recognise his many accomplishments,” said Kyle Stavig, ISDI chair and CEO of Myers Container. “For five decades, Ernie showed great commitment to his company and the steel drum business. His renowned enthusiasm and contributions will be an example for the next generation of manufacturers that push this industry for generations to come.”
In other news, NCC has also been named as Wacker’s 2017 Supplier of the Year. “I could not be more proud of the NCC family,” Jim Beardsley says. “We are truly honoured and
humbled. Our goal is to always go above and beyond for customers, especially in areas of innovative research and development, quality and continuity. After all, our philosophy is that we work for NCC but our actual employers are our customers.” www.whysteeldrums.org www.ncc-corp.com
US-headquartered Flexicon has unveiled a new Tip-Tite® drum dumper for units with filling volumes of between 115 litres and 200 litres. Designed to facilitate the dust-free transfer of free-flowing solid materials, the system features an elongated discharge cone that mates with the gasketed inlet of low-height receiving vessels. Housed within a three-sided safety enclosure that uses safety-interlocked doors, the drum platform is raised by a single hydraulic cylinder, creating what the company describes as “a dust-tight seal between the rim of a drum and the underside of the discharge cone”.
“ With drum secured in place, a second hydraulic cylinder tips the platform-hood assembly, stopping at a dump angle of 45° with a motion-dampening feature, causing the spout of the discharge cone to mate with a gasketed receiving ring on the lid of a low-height receiving vessel,” Flexicon says. “A pneumatically actuated slide gate at the spout can be opened variably for partial or total discharge at controlled rates and then closed before returning the drum to its original position, with no dust emitted throughout the cycle.”
Available in both stationary and mobile configurations, the new drum dumper can be supplied “in carbon steel with durable industrial finishes, with material contact surfaces of stainless steel or in all-stainless steel finished to food, dairy, pharmaceutical or industrial standards”. At the same time, a diameter adapter can be used to allow for “the safe and dust-tight dumping of smaller-diameter drums”. www.flexicon.com
730 Bridge St West, Unit 3 Waterloo, Ontario N2V 2J4, Canada
T (+1 519) 747 5075
www.acuteservices.com
Transport of Dangerous Goods
• February 8 – Waterloo
• March 27 – Waterloo
Confined Space Entry
• February 22 – Waterloo
Confined Space Rescue
• February 23 – Waterloo
HAZWOPER
• January 30-Feb 2 – Waterloo
• March 20-23 – Waterloo
HAZWOPER Refresher
• March 13 – Waterloo
PO Box 146
Riddell’s Creek, VIC 3431, Australia
T (+61 3) 5428 6077
www.aitac.com.au
Sea Transport of Dangerous Goods
• February 12-13 – Tullamarine
• March 5-6 – Tullamarine
Sea Transport of Dangerous Goods – Recertification
• March 7 – Tullamarine
Air Transport of Dangerous Goods – Acceptance, Initial
• January 22-24 – Tullamarine
• February 19-21 – Tullamarine
• March 26-28 – Tullamarine
Air Transport of Dangerous Goods – Recertification
• January 31 – Tullamarine
• March 8 – Tullamarine
Dangerous Goods Driver Licence
• February 10-11 – Tullamarine
• March 17-18 – Tullamarine
Westfield Office Tower, Suite 403, Level 3, 152 Bunnerong Road Eastgardens, NSW 2036 Australia
T (+61 2) 9314 3055
www.afif.asn.au
Dangerous Goods Acceptance (Air)
• February 6-8 – Sydney
• February 13-15 – Melbourne
• February 20-22 – Brisbane
• March 6-8 – Sydney
• March 13-15 – Melbourne
Dangerous Goods Re-certification (Air)
• January 23 – Brisbane
• January 23 – Melbourne
• February 5 – Sydney
• February 12 – Melbourne
• February 19 – Brisbane
• March 5 – Brisbane
• March 5 – Sydney
• March 12 – Melbourne
Dangerous Goods Awareness (Air)
• February 22 – Sydney
• February 28 – Melbourne
• March 8 – Brisbane
Dangerous Goods by Sea –Full Acceptance
• February 20-21 – Sydney
• February 26-27 – Melbourne
• March 6-7 – Brisbane
• March 20-21 – Sydney
Dangerous Goods by Sea –Recertification
• January 22 – Melbourne
Shipping Lithium Batteries by Air
• March 22 – Sydney
Redfern House, Browells Lane Feltham, Middlesex TW13 7EP, UK
T (+44 20) 8844 3625 www.bifa.org
Dangerous Goods by Air
• February 5-7 – Feltham
• February 7-9 – Glasgow
• February 12-14 – Leeds/Bradford
• February 19-21 – Altrincham
• February 26-28 – Feltham
• March 5-7 – Bournemouth
• March 12-14 – Coventry
• March 19-21 – Bristol
• March 19-21 – Feltham
Dangerous Goods by Air –Revalidation
• February 8-9 – Feltham
• February 8-9 – Glasgow
• February 15-16 – Leeds/Bradford
• February 22-23 – Altrincham
• March 1-2 – Feltham
• March 8-9 – Bournemouth
• March 15-16 – Coventry
• March 22-23 – Bristol
• March 22-23 – Feltham
Infectious Substances by Air
• February 6-7 – Watford
Dangerous Goods by Road
• January 22-24 – Feltham
• February 19-21 – Coventry
• March 12-14 – Altrincham
• March 19-21 – Feltham
Dangerous Goods by Road –Revalidation
• January 23-24 – Feltham
• February 20-21 – Coventry
• March 13-14 – Altrincham
• March 20-21 – Feltham
Dangerous Goods by Sea
• January 25-26 – Feltham
• February 22-23 – Coventry
• March 14-15 – Altrincham
• March 22-23 – Feltham
Dangerous Goods Safety Advisor
• February 26-March 2 – Heathrow
• February 26-March 2 –Manchester
Carriage of Lithium Batteries –All Modes
• February 1-2 – Feltham
Carriage of Lithium Batteries by Air
• February 1 – Feltham
Carriage of Lithium Batteries by Road
• February 2 – Feltham
Carriage of Lithium Batteries by Sea
• February 2 – Feltham
CARGO TRAINING INTERNATIONAL
PO Box 176
Shepperton TW17 8WP, UK
T (+44 1932) 769682
P O Box 580026 Houston, TX 77258-0026, USA
T (+1 281) 333 4672
www.cargotraining.com
Dangerous Goods by Air – ICAO (full course)
• February 7-9 – Glasgow
• February 7-9 – Heathrow
• February 12-14 – Leeds/Bradford
• February 19-21 – Manchester
• February 26-28 – Heathrow
• March 5-7 – Bournemouth
• March 12-14 – Birmingham, UK
• March 19-21 – Bristol
• March 19-21 – Heathrow
Dangerous Goods by Air –Revalidation
• February 8-9 – Glasgow
• February 8-9 – Heathrow
• February 15-16 – Leeds/Bradford
• February 22-23 – Manchester
• March 1-2 – Heathrow
• March 8-9 – Bournemouth
• March 15-16 – Birmingham, UK
• March 22-23 – Bristol
• March 22-23 – Heathrow
Dangerous Goods by Road –ADR (full course)
• January 22-24 – Heathrow
• February 19-21 – Birmingham, UK
• March 12-14 – Manchester
• March 19-21 – Heathrow
Dangerous Goods by Road –Revalidation
• January 23-24 – Heathrow
• February 20-21 – Birmingham, UK
• March 13-14 – Manchester
• March 20-21 – Heathrow
Dangerous Goods by Sea (IMDG)
• January 25-26 – Heathrow
• February 22-23 – Birmingham, UK
• March 15-16 – Manchester
• March 22-23 – Heathrow
Lithium Batteries Multimodal
• February 1-2 – Heathrow
Dangerous Goods Safety Adviser
• February 26-March 2 – Heathrow
• February 26-March 2 –Manchester
Dangerous Goods Safety Adviser (Refresher)
• February 28-March 2 – Heathrow
• February 28-March 2 –Manchester
Diagnostic and Infectious Substances by Air
• February 6 – Elstree
CHEM FREIGHT HONG KONG
Suite 907, Silvercord Tower 2
30 Canton Road, Tsim Sha Tsui Kowloon, Hong Kong
T (+852) 2961 4887 www.chemfreight.com.hk
IATA Basic DG Regulations
• January 22-26 – Kowloon
• February 5-9 – Kowloon
• February 26-March 2 – Kowloon
• March 12-16 – Kowloon
IATA Refresher DG Regulations
• January 29-31 – Kowloon
• February 12-14 – Kowloon
• February 21-23 – Kowloon
• March 5-7 – Kowloon
• March 19-21 – Kowloon
IATA Dangerous Goods Awareness
• February 1 – Kowloon
• March 8 – Kowloon
CHEMICAL HAZARDS
COMMUNICATION SOCIETY
PO Box 899
Oxford OX1 9QG, UK
T (+44 333) 210 2427 www.chcs.org.uk
Transport Labelling and Documentation
• February 1 – Manchester
Introduction to Basic SDS Writing
• March 1 – Manchester
Introduction to European Chemical Regulation
• March 15 – London
An Overview of the Biocidal Products Regulation
• February 7 – Manchester
COGENT
5 Mandarin Court Warrington WA1 1GG, UK.
T (+44 1925) 515 200 www.cogentskills.com
Process Safety Leadership for Senior Executives
• February 13 – Teesside
• March 13 – Cardiff Process Safety Management Foundations
• February 27-28 – NW England
• March 20-21 – Teesside
Process Safety for Operations
• February 20-24 – Holmes Chapel
COMMERCIAL OPERATOR
TRAINING SOLUTIONS
Unit 6, Queensway
Swansea West Business Park Swansea SA5 4DH, UK
T (+44 1792) 587250
www.cotsolutions.co.uk
ADR All Classes and Tanks
• February 12-16 – Swansea
• March 19-23 – Swansea
DANGEROUS GOODS OF AMERICA
10400 NW 33rd Street, Suite 230 Doral, FL 33172, USA
T (+1 305) 871 3313
www.dga4u.com
Initial IATA & HMR Air
• February 5-7 – Doral
• March 5-7 – Doral
Recurrent IATA & HMR
• February 13 – Doral
• March 13 – Doral
IMDG Code & HMR Ocean
• March 12 – Doral
Hermes House, St John’s Road
Tunbridge Wells TN4 9UZ, UK
T (+44 1892) 526171
www.fta.co.uk
Dangerous Goods Safety Adviser
• February 19-23 – Stirling
ADR – Initial
• March 12-16 – Stirling
• March 19-23 – Tunbridge Wells
Dangerous Goods Awareness
• February 12 – Stirling
• March 19 – Leeds
2150 Liberty Drive
Niagara Falls, NY 14304, USA
T (+1 888) 442 9628
88 Lindsay Avenue
Dorval, QC H9P 2T8, Canada
T (+1 888) 977 4834 www.thecompliancecenter.com
Shipping Dangerous Goods by Ground in Canada: Initial
• March 20-21 – Toronto
Shipping Dangerous Goods by Ground in Canada: Refresher
• February 13 – Montreal
• March 13 – Toronto
Shipping Dangerous Goods by Ground in Canada: Initial/Refresher
• February 14 – Vancouver
• March 20 – Vancouver
Shipping Dangerous Goods by Ground in Canada: Drivers & Handlers
• February 5 – Toronto
• February 16 – Vancouver
Shipping Dangerous Goods by Air: Initial
• February 15 – Vancouver
• March 21 – Vancouver
Shipping Dangerous Goods by Air: Refresher
• February 14 – Montreal
• March 14 – Toronto
Shipping Dangerous Goods by Sea using IMDG Code: Initial
• March 13-14 – Montreal
Shipping Dangerous Goods by Sea using IMDG Code: Refresher
• March 15 – Toronto
GHS Classification
• March 21-23 – Toronto
PETER EAST ASSOCIATES
504 Centennial Park Centennial Avenue
Elstree, Herts WD6 3FG, UK
T (+44 20) 8953 6721
www.petereast.com
Carriage of Dangerous Goods by Air – Certification
• January 29-31 – Elstree
• February 5-7 – Heathrow
• February 5-7 – Stansted
• February 12-14 – Luton
• February 19-21 – Southampton
• March 5-7 – Heathrow
• March 12-14 – Northampton
• March 12-14 – Stansted
Carriage of Dangerous Goods by Air – Revalidation
• January 25-26 – Manchester
• February 8 – Heathrow
• February 8-9 – Stansted
• February 15-16 – Luton
• February 22-23 – Heathrow
• February 22-23 – Southampton
• March 8 – Heathrow
• March 15-16 – Northampton
Carriage of Dangerous Goods by Road & Sea
• February 12-14 – Heathrow
• March 5-7 – East Midlands
• March 19-21 – Southampton
Carriage of Radioactive Material by Air
• February 22-23 – Heathrow
Carriage of Lithium Batteries by Air, Road & Sea
• March 12-13 – Elstree
Carriage of Excepted & Limited
Quantities by Air, Road and Sea
• January 24-26 – Elstree
Lancaster Environment Centre,
Lancaster, Lancs LA1 4YQ, UK.
T (+44 1524) 510278
www.thereachcentre.com
• March 14 – Lancaster
Managing REACH for Downstream Users
• March 13 – Lancaster
REACH – IUCLID
• March 15 – Lancaster
Introduction to the Biocidal Product Regulations
• February 6 – Lancaster
Biocidal Product Regulations –Introduction and Authorisation
• February 6 – Lancaster
SAF-T-PAK 17827 – 111 Avenue Edmonton, AB T5S 2X3 Canada
7466 Candlewood Road, Suite E Hanover, MD 21076, USA
T (+1 800) 814 7484 www.saftpak.com
Shipping Division 6.2 Infectious Substances
• February 6 – Rockville, MD
• February 8 – Philadelphia
• February 21 – Denver
• February 22 – Albuquerque
• March 5 – San Diego
• March 8 – San Francisco
• March 12 – Nashville
• March 15 – Atlanta
• March 28 – Raleigh
TANKTERMINAL TRAINING
Schulhausstrasse 11
3932 Visperterminen Switzerland
T (+41 79) 83 71 392
T (+31 6) 5493 1738
www.tankterminaltraining.com
Marine Expeditor and Certification
• February 26-28 – Rotterdam
LNG Marine Terminal Loading Master and Certification
• March 19-21 – Perth
LNG Loss Control Expeditor & Ship/Shore Interface
• March 1-2 – Rotterdam
12 Gleneagles Court, Brighton Road Crawley, West Sussex RH10 6AD, UK
T (+44 1293) 536943 www.trainingteam.co.uk
• February 5-7 – East Midlands
• February 5-7 – Heathrow
• February 12-14 – Gatwick
• February 12-14 – Manchester
• February 12-14 – Newcastle
• February 19-21 – Bristol
• February 19-21 – Glasgow
• March 5-7 – East Midlands
• March 12-14 – Gatwick
• March 12-14 – Manchester
• March 19-21 – Heathrow
Dangerous Goods by Air Revalidation
• February 6-7 – Heathrow
• February 8-9 – East Midlands
• February 13-14 – Gatwick
• February 19-20 – Manchester
• March 5-7 – Glasgow
• March 13-14 – Gatwick
• March 19-20 – Manchester
• March 20-21 – Heathrow
• March 21-22 – East Midlands
Radioactive Materials by Air
• February 15-16 – Gatwick
• March 15-16 – Manchester
• March 22-23 – Heathrow
• January 30-31 – Gatwick
• February 21-22 – Manchester
• March 19-20 – East Midlands
Dangerous Goods by Road
• January 24-25 – Manchester
• February 7-8 – Gatwick
• February 14-15 – East Midlands
• March 7-8 – Newcastle
Dangerous Goods by Road – ‘Top-Up’
• February 9 – Heathrow
• February 16 – Manchester
• February 16 – Newcastle
• February 23 – Bristol
• February 23 – Glasgow
• March 9 – East Midlands
• March 16 – Gatwick
Dangerous Goods by Sea
• February 5-6 – Gatwick
• February 12-13 – East Midlands
• March 5-6 – Newcastle
Dangerous Goods by Sea – ‘Top-Up’
• February 8 – Heathrow
• February 15 – Manchester
• February 15 – Newcastle
• February 22 – Bristol
• February 22 – Glasgow
• March 8 – East Midlands
• March 15 – Gatwick
Combined Dangerous Goods –Air, Road & Sea
• February 5-9 – Heathrow
• February 12-16 – Manchester
• February 12-16 – Newcastle
• February 19-23 – Bristol
• February 19-23 – Glasgow
• March 12-16 – Gatwick
Dangerous Goods Safety Adviser
• February 26-March 2 – Gatwick
• February 26-March 2 – Heathrow
• February 26-March 2 – Manchester
The Legion, Wigshaw Lane Culcheth, Warrington WA3 4LY, UK
T (+44 151) 488 0961
www.transchemtraining.com
ADR Initial
• February 12-16 – Wakefield
• February 19-23 – Warrington
• March 12-16 – Wakefield
• March 19-23 – Warrington
Class 1 Explosives
• January 26 – Warrington
WARSASH MARITIME ACADEMY Newtown Road, Warsash Southampton SO31 9ZL, UK T (+44 1489) 556216
www.warsashacademy.co.uk
Basic Oil and Chemical Tanker Cargo Operations
• February 5-6 – Southampton
• March 19-20 – Southampton
Advanced Oil Tanker Cargo Operations
• February 19-23 – Southampton
Basic Liquefied Gas Tanker Cargo Operations
• February 5-6 – Southampton
• March 19-20 – Southampton
Advanced Liquefied Gas Tanker Cargo Operations
• February 26-March 2 –Southampton
Advanced Chemical Tanker Cargo Operations
• March 5-9 – Southampton
Crude Oil Washing
• February 1 – Southampton Jetty Operations (Petrochemicals)
• January 29-30 – Southampton
As the new year opens before us, I’d like to write a few words about the business we’re in and the sustainability of our industries.
The message of Christmas is peace on earth, but when one looks around, reads the news, follows tweets or spam, our future does not look too bright. We have to work and operate our businesses in an increasingly complex world driven by economic and political ideologies that have little to do with reality.
As a writer and business ethicist I look at the way our industries are only reluctantly changing from negative interdependent, pathdependent production and processes towards positive interdependent ones. But when we look at the vast volume of scientific data that confirms that we won’t survive walking the trodden path, we must change course.
We as hazardous cargo industries could build a cooperative platform, sponsored by all of us, that researches a way out that would benefit us all and our planet. Complexity Theory, Systems Science and Cybernetics are cool tools to be used, but many of us don’t know much about these alternative sciences. Trapped in linear sciences, we not seem to be able to change our deterministic way of thought.
The beauty of Complexity Theory is that it can be quite simple. All we have to acknowledge is the fact that everything we do, say or move is related to something else. We can say: everything is interrelated. What we do is not just simple cause and effect, but cause and complex, non-linear effect, over which we can’t have control. Understanding this basic fact, would perhaps influence our old ways of thought and replace
them with new ones. This would create millions of jobs, because it will re-awaken our incredible and infinite ability to create. Peter Gabriel sang a while ago: ‘All of these buildings, all of these cars were once just a dream in somebody’s head’
Let’s all sit down and contemplate these words for a while. Perhaps we can launch a think tank which endeavours to create long term longevity and sustainability for all we do, make, process or ship, before we are fined for non-compliance.
This would indeed be the challenge for 2018. Many industries have already begun this highly complex journey. What I can do is to write about it and teach this stuff during my management trainings. I mean, we have the awareness, but lack perhaps the courage to pursue or embark on a journey with an unknown destination.
See yourself as Marco Polo or Columbus, traveling and sailing to new lands. These new lands are still there, we don’t have to travel too far. This new world of matter resides within all of us. All we have to do is to use information and our own energy to explore them. This means a journey within ourselves because that is where we will find sustainable solutions.
This is the fourth in a new series of articles by Arend van Campen, founder of TankTerminalTraining. More information on the company’s activities can be found at www.tankterminaltraining.com. Those interested in following up his invitation can contact him directly at arendvc@tankterminaltraining.com.
JANUARY 16-17, GALVESTON
Tenth annual event for the US aboveground tank storage sector www.nistm.org
JANUARY 16-18, HOUSTON Conference on regional and global LPG market developments www.argusmedia.com/events/argus-events/ americas/americas-lpg-summit/home/
JANUARY 25-26, AMSTERDAM
Platts’ 11th annual conference on oil markets for terminal owners, ports, oil traders, financiers and analysts www.platts.com/events/emea/european-oilstorage/index
JANUARY 29-FEBRUARY 2, GARDEN GROVE, CA
Annual conference of the Cooperative Hazardous Materials Enforcement Development (COHMED) programme cvsa.org/eventpage/events/cohmed-conference/ Platts LNG Conference
FEBRUARY 12-13, HOUSTON
17th annual conference on LNG supply/demand, pricing and project development www.platts.com/events/americas/liquefiednatural-gas/index
FEBRUARY 20-22, LONDON
Annual week of meetings, lunches, conferences and seminars in London www.ipweek.co.uk
FEBRUARY 25-27, HAMBURG
34th annual conference on dangerous
goods transport (German language) www.ecomed-storck.de/Veranstaltungen/
FEBRUARY 28-MARCH 1, RUNCORN Conference and exhibition on hazardous area operations www.hazardexonthenet.net/event. aspx?EventID=4724
MARCH 4-6, TAMPA
Bi-annual meeting and tradeshow of the Petroleum Packaging Council www.ppcouncil.org/upcoming-meetings.php
MARCH 7-8, LISBON
Summit on developments in the regional LPG market www.wplgroup.com/aci/event/lpg-europesummit/
MARCH 11-13, NEW ORLEANS
AFPM’s annual meeting for refiners and marketers www.afpm.org
MARCH 13-15, DALLAS
12th global conference on air cargo www.iata.org/events/wcs/pages/index.aspx
Intermodal South America
MARCH 13-15, SÃO PAULO
International exhibition on intermodal logistics, cargo transport and international trade www.intermodal.com.br/en
MARCH 13-15, LONDON
Triennial conference and exhibition for the European oil spill response sector www.interspill.org
MARCH 14-15, CAPE TOWN Conference on the prospects for LPG market growth in Africa
www.argusmedia.com/events/argus-events/ europe/argus-africa-lpg/home/
MARCH 15-16, SYDNEY Conference and workshops on business continuity issues www.marcusevans-conferences-australian.com
MARCH 19-21, MELBOURNE
Workshop on optimising dangerous goods management processes www.marcusevans-conferences-australian.com
MARCH 20-22, SHANGHAI
Fifth annual exhibition for the Asian intermodal sector www.intermodal-asia.com
MARCH 20-22, AMSTERDAM Chemical supply chain and logistics conference http://logichem.wbresearch.com/
MARCH 20-22, ROTTERDAM
The main annual exhibition and conference for the European tank terminal industry www.easyfairs.com/stocexpo-europe-2018/ stocexpo-europe-2018/
Annual AGM and seminar of the British Association of Dangerous Goods Professionals www.badgp.org/event-2685411
MARCH 25-27, SAN ANTONIO
AFPM’s annual International Petrochemical Conference www.AFPM.org
MARCH 27-29, ORLANDO
National Institute for Storage Tank Management’s 20th annual international aboveground storage tank conference and trade show www.nistm.org
6/10/17 Missoula, road tankers gasoline Massive fire broke out at Mountain West Co-op storage area; fire crews arrived to find two tank trucks, both MTN Montana, US reportedly empty, on fire; both were burned out; explosions heard; not clear if fire started in gasoline tankers News
7/10/17 Accra, road tanker LPG Seven killed, 132 injured by explosion in LPG tanker delivering to Mansco filling station at Atomic Junction; Graphic Ghana authorities found evidence of black market activity, out of hours operation; driver, station owner absconded Online
10/10/17 Karusi, road tanker fuel At least 50 people were injured by explosion of fuel tanker after it overturned in central Burundi; blast Xinhua Burundi happened as locals ran to collect spilling fuel
10/10/17 Iroquois county, road tanker gasoline Tank truck ran off Route 54, rolled several times; driver was trapped in cab, later released and hospitalised; Daily Illinois, US substantial gasoline spill was contained; tanker owner helped Illinois EPA clean up site Journal
11/10/17 Townsend, road tanker gasoline Lee Transport tank truck with 8,900 gal (33.7 m3) gasoline crashed on Route 1 after driver lost control; tank WPVI Delaware, US detached from cab, overturned, leaked “steady stream” of gasoline from several ruptures to drainage ditch
12/10/17 Ludvika, freight train “dangerous 10 cars of 36-car freight train derailed, overturned near station in Ludvika; train said to be carrying dangerous The Dalarna, Sweden goods” goods but unclear what they were or whether one car on fire was carrying them; fire was allowed to burn out Local.se
15/10/17 Calgary road tanker jet fuel Some 4,000 litres jet fuel leaked from faulty valve on tank truck at Calgary International Airport; fire crews Calgary Alberta, Canada helped airport personnel contain leak, clean up; spill contained on airport property Herald
16/10/17 Mwanza, road tanker petroleum Rashy fuel tanker carrying unspecified petroleum product overturned shortly after crossing Mwanza River, Nyasa Malawi possibly due to brake failure or other malfunction; spilling fuel was ignited by nearby wildfire; no injuries Times
16/10/17 Obingwa, road tanker gasoline Unmarked road tanker, probably with gasoline, became stuck in “crater” on Aba-Ikot Ekpene road; driver Vanguard Abia, Nigeria got out of cab to look, whereupon tanker exploded; driver fled; several children hurt in nearby school
18/10/17 Kolkata, road tanker jet fuel Road tanker caught fire on apron where aircraft are refuelled at Kolkata’s international airport; no casualties Xinhua W Bengal, India or damage to aircraft reported; operations unaffected; investigation ordered to ascertain cause
18/10/17 Elko, road tanker ammonium Tank truck crashed on I-80, spilling some 51,000 lb (23 tonne) ammonium bisulphite; police closed highway Elko Nevada, US bisulphite in both directions due to inhalation hazard; driver said to have fallen asleep at the wheel Daily
20/10/17 Cudjoe Key, road tanker gasoline, Tank truck collided head on with utility truck on Overseas Highway, spilling significant part of 4,900-gal Miami Florida, US diesel (18.5-m3) mixed fuel load to road, mangroves; one driver hospitalised; highway was closed for several hours Herald
21/10/17 Navi Mumbai, road tanker acetic acid Road tanker overturned on old Mumbai-Pune highway, spilling load of acetic acid to Patalganga River; big Times of Maharashtra, India fish kill downstream; water supply to nearby villages cut off India
21/10/17 Thane, road tanker hydrochloric Tanker driver lost control negotiating turn on Ghodbunder Road at Gaimukh; tanker overturned, spilling Times of Maharashtra, India acid concentrated acid to road, generating fumes; driver fled; responders unaware of nature of load India
22/10/17 nr St Albert, freight train crude oil Around 12 tank cars in CN train derailed north of Edmonton; some cars leaked oil, but no major spill; Global Alberta, Canada nearby residents evacuated News
22/10/17 Jenks, road tanker gasoline Tank truck overturned in Tulsa suburb after driver swerved to avoid car; several hundred gallons fuel spilled, AP Oklahoma, US some reaching storm drain; no impact on nearby Arkansas River
25/10/17 Bareilly, road tanker diesel Road tanker with diesel was struck by passenger express train on manned crossing; tanker said to be speeding; Hindustan UP, India tanker driver killed, 50 passengers hurt; no fire; role of gate man under investigation Times
29/10/17 Cleveland, road tanker fuel SUV was in head-on collision with fuel tanker on I-77; SUV driver killed (may have been his intention); Cleveland. Ohio, US significant fuel spill from tanker; highway closed for several hours for cleanup com
30/10/17 Andover, truck chemicals Fire broke out on tractor-trailer on I-495, apparently due to chemical reaction in load; hazmat team had to Eagle Massachusetts, US wait for fire to be doused before containing leaks; not clear what chemicals were involved Tribune
31/10/17 Toronto, road tankers fuels At least 2 killed, many others injured in 14-vehicle pile-up on Highway 400, apparently after truck rear-ended CBC Ontario, Canada vehicles stopped for another crash; two tank trucks involved; witnesses reported explosions
31/10/17 Harrisburg, rail tank car butadiene Leak of butadiene from faulty valve on rail tank car at Mallard Creek Polymer plant; nearby businesses, WSOC N Carolina, US homes evacuated; hazmat crews monitored air quality; EPA advising operator on preventing similar events
1/11/17 Charikar, road tankers fuels ‘Sticky bomb’ placed on tanker exploded, causing fire to spread to other tankers and a passing bus; at least MENA Parwan, Afghanistan 15 people believed killed, 27 injured; no immediate claim of responsibility
Date Location Vessel Substance Details
3/10/17 off Ulsan, Victoria
Source
Containership (15,300 gt, 2008) collided with chemical tanker (unidentified, as per South Korean rules) Shipwreck South Korea Trader in Onsan approaches; both vessels damaged but no injuries or pollution reported; both berthed at Ulsan Log
3/10/17 off Portugal? MSC London
Fire broke out in two containers aboard containership (15,900 teu, 2014), en route Tanjung Pelepas to FleetMon Rotterdam; fire extinguished by crew before arrival at Maasvlakte; extent of damage, nature of cargo unknown
4/10/17 off Imperial Beach, USS Dewey lube oil Some 700 gal (2,650 litre) lubricating oil spilled from US Navy vessel near mouth of Tijuana River, Ship & California, US apparently due to equipment malfunction; booms deployed; US Navy coordinating with USCG on response Bunker
13/10/17 off Venice, pipeline crude oil At least 16,000 bbl crude oil – double the initial estimate – believed to have leaked from ruptured LLOG Reuters Louisiana, US Exploration pipeline some 40 m south-east of Venice; sheens quickly dissipated, no oil reached shore
19/10/17 Abbenfleth, Bow Guardian propylene Leak of propylene from LPG tanker (9,000 m3, 2008) on River Elbe in Lower Saxony; locals advised to FleetMon NS, Germany shelter in place; faulty pump and/or vent blamed; leak sealed within two hours
19/10/17 Rotterdam, Atlantic coconut oil Fire broke out aboard oil/chemical tanker (36,700 dwt, 2009) berthed at Koole Terminals facility with coconut FleetMon Netherlands Symphony oil from Port Klang; one crewman injured; cause of initial explosion under investigation
19/10/17 Korsakov, Shun Yue 19 flammables Three drums with flammable liquid fell into hold during unloading of containership (6,800 gt, 2011), spilling FleetMon Sakhalin, Russia contents; vessel moved to outer anchorage for cleanup; one report mentioned tank containers
20/10/17 off Port Aransas, Buster crude oil Fire broke out on barge with 130,000 bbl crude oil, reportedly during anchor heaving; two crew died; Maritime Texas, US Bouchard USCG imposed safety zone, deployed booms; some oil washed up on nearby islands Executive
24/10/17 Bruinisse, Hortensia 2 diesel Bunker barge (1,388 dwt) with 1,400 t diesel grounded on Oosterschelde; vessel refloated on rising tide, AD Netherlands moved to Krammersluizen for underwater inspection; no pollution reported
26/10/17 Borssele, Maria Aframax tanker (107,500 dwt, 2012), in cargo from US, grounded on Western Scheldt, possibly following FleetMon Netherlands Bottiglieri mechanical failure; tanker later refloated with tug assistance, anchored for inspection; no pollution reported
Date Location Plant type Substance Details Source
11/10/17 Kertih, oil refinery condensate Fire broke out in condensate tank at Petronas refinery; plant’s fire team helped local brigade extinguish Bernama Terengganu, Malaysia blaze with no reported injuries; Petronas, authorities investigating cause
11/10/17 Izmir, oil refinery naphtha Four contractors killed, two injured during maintenance work on empty naphtha tank at Tupras refinery; Reuters Turkey operator blamed pressure in boiler; four arrested over incident, now subject to official investigation
12/10/17 Brighton, tank battery crude oil Explosion, fire in oil tanks at Great Western facility; second incident in three weeks; blast happened during Denver Colorado, US unloading of “materials”; no injuries reported; fire crews had to turn off natural gas lines before fighting fire Post
17/10/17 Fernie, sports arena ammonia Three people died from exposure to ammonia at Fernie Memorial Arena; nearby residents evacuated; CBC BC, Canada RCMP took control of site; WorkSafe BC investigating cause
17/10/17 El Segundo, oil refinery light oil Significant fire broke out close to storage tanks at Chevron refinery; witnesses reported explosions but operator KABC California, US said these were transformers blowing; fire crews kept tanks cool to prevent spread of fire; pump failure blamed
17/10/17 La Salle county, tank battery crude oil Explosion, fire at Carrizo Oil & Gas property injured two workers; fire crews arrived to find several tanks on KSAT Texas, US fire; blaze allowed to burn out; new tank under construction at time of incident
18/10/17 Balasore, fireworks firecrackers Seven killed, several others badly injured by explosion at unlicensed firecracker unit; blast destroyed building, News Odisha, India factory blew asbestos over area; cause unknown Odisha
18/10/17 nr Columbia, nuclear fuel uranyl One
Westinghouse
at
THE USE OF freight containers revolutionised international transport, allowing all manner of goods to travel seamlessly by all modes virtually anywhere in the world. Yet, despite more than half a century of experience in using containers, accidents still happen regularly, not least during maritime transport.
Those accidents reflect bad practices, mostly on the part of shippers or consolidators: overweight containers, poor securement of cargo within the box or, in the case of dangerous goods, undeclared or misdeclared cargo.
There are many reasons for this situation but much of it is to do with a lack of knowledge on the part of those packing
containers. In particular, it is thought, container stuffers are often unaware of the forces to which containers will be subjected during transport by sea, which are very different to those experienced during rail or road transport.
The result of these failings is often damage to the cargo, with a financial loss to the shipper and disappointment to the consignee, or in worse cases damage to third-party property, personal injuries and environmental damage.
There are tools available to improve matters. A lot of work has been done over the years to try and drive better standards in the containerised chain, culminating in the publication of the Code of Practice for Packing of Cargo Transport Units (the CTU Code) by the International
Maritime Organisation (IMO), International Labour Organisation (ILO) and the UN Economic Commission for Europe (ECE).
Application of the CTU Code appears patchy thus far; while its use is mandatory in certain jurisdictions and for certain goods, and is welcomed by carriers, insurers and regulatory bodies, it would appear that in many parts of the world it is being ignored or, perhaps more likely, is simply unknown.
Industry associations are keen to see the practices explained in the CTU Code get used more widely and have begun efforts to promote it in different fora around the world. At the Intermodal Europe event in Amsterdam in November 2017, for instance, four bodies gave a joint presentation on the Code and the responsibilities it places on the various parties in the transport chain.
The Global Shippers Forum (GSF), ICHCA International, TT Club and the World Shipping Council (WSC) have for some months now been working together to improve safety through a focus on cargo integrity. The specific aim has been to promote wider use of the CTU Code for correct packing and securing of all containers. Improved standards of declaration and handling of dangerous goods are also within the scope of the Code, together with steps to prevent pest contamination, and the provision of
CONTAINERS • THE SAFETY OF CONTAINERISED CARGO IN MARITIME TRANSPORT REMAINS A CONCERN, DESPITE EFFORTS FROM ALL SIDES TO IMPROVE STANDARDS
containers and other equipment that comply with international rules and standards.
The Code calls for effective interaction between the shipper, who is responsible for specifying requirements for the type of equipment suitable for the cargo intended to be carried, and the container operator in providing units that satisfy such requirements, meet applicable safety and manufacturing standards, and are clean. Faulty and badly maintained units may have as serious ramifications as incorrect and deficient packing of cargo inside the units.
“Engagement with governments and industry groups representing the diverse mix of supply chain stakeholders is one of our primary goals,” explained TT Club’s Peregrine Storrs-Fox. “Through communication and understanding of the safety issues comes a wider implementation of the CTU Code
and other best practices aimed at cargo and environmental safety. To this end we urge regulatory and advisory bodies as well as associations to unite with us in spreading the good word.”
The group has been working with IMO for some time, contributing to aspects of the CTU Code and other regulatory recommendations, but there remains an element of concern that governments may not effectively be communicating agreed IMO requirements and advisory information within their jurisdictions. Lars Kjaer of the WSC explained: “We want to make sure that governments as well as industry are promoting the CTU Code and its best practices to all parties in the CTU supply chain around the globe.”
Ultimately, though, it is those that pack containers that have the primary responsibility for ensuring cargo integrity and safety, and those responsibilities are laid out clearly in the CTU Code. Chris Welsh, secretary-general
of GSF said in Amsterdam: “In many modern international supply chains there are multiple ‘hand-offs’ where cargo is passed variously from manufacturers, suppliers, distributors, warehouses, consolidators, forwarders and logistics operators to shipping lines. Ultimately, however, it is the responsibility of the shipper as the party causing the transport of the CTU unit to demand and control compliance with proper packing standards, and to specify the type of equipment needed for the cargo. This is a responsibility clearly set out in the CTU Code. It cannot be negated or ignored irrespective of the complexity of the logistics chain.”
This industry group is seeking to communicate to all stakeholders through governmental and industry events. Progress is being made in increasing awareness of the CTU Code and linking with other organisations to deliver improved safety and sustainability in the international supply chain. HCB
PYROBAN, WHICH DESCRIBES itself as “a worldwide company offering explosionprotection solutions for the materials handling and oil and gas industries”, is now under new ownership after US-headquartered Caterpillar divested its 100 per cent interest. The move opens “an exciting new chapter”, Pyroban says, which will allow it “to realise the full market opportunities” for explosion protection worldwide.
“The Pyroban Materials Handling and Pyropress Instrumentation businesses remain unaffected, but there will be significant opportunities in other areas of the business serving the oil and gas sector,” the company continues. “By operating outside of the Caterpillar distribution model, Pyroban can now work with all engine OEMs and packagers in the oilfield markets, offering explosion-protection engine kits, components and packages.”
In line with all this, Brian Quarendon has been named as the new CEO of the Pyroban Group. Previously CEO of the Industrial Acoustics Company, a private equity-backed provider of noise and acoustic control systems, he joins Pyroban “to support existing management, implement the carve out from Caterpillar and drive growth”. Commenting on his appointment, Quarendon states: “With outstanding engineering expertise, both Pyroban and Pyropress have strong brands and impressive operational capabilities. I am looking forward to partnering with management to take advantage of the great potential which lies ahead.”
Meanwhile, to meet the requirements of the new EU standard for explosion-protected lift truck design, Pyroban has invested in a comprehensive EN1755:2015 change programme. Entitled Safety of industrial trucks. Operation in potentially explosive atmospheres. Use in flammable gas, vapour, mist and dust,
the new EN1755:2015 standard supersedes EN1755:2000 and has been mandatory since November 2017. It affects all new orders for lift trucks that will be used in Zone 1, 2, 21 and 22 areas.
The changes, Pyroban explains, mean that the technical makeup of an ATEX 2014/34/EU truck conversion will now be different. “From an end user’s perspective, the requirements have changed for tyres, seats, batteries and the management of electrical static risks,” the company says. “As a result, end users will need to consider ongoing maintenance requirements thereafter, including service engineering training.”
At the same time, from a manufacturer’s perspective, “the new requirements place significant demands on the safety control systems which form part of the ATEX-compliant explosion-protection solution”. Furthermore, it continues, “the requirements to assess and address non-electrical ignition sources throughout the entire forklift truck has involved a significant level of engineering resource”. Pyroban has thus made “a significant investment creating new solutions and updating many products over a two-year period to ensure its explosion-protection conversions for forklifts” are suitably compliant.
“Supporting the end user and OEM supply chain through these changes is a priority for Pyroban,” says engineering and operations manager Steve Noakes. “To manage risk, it is important that those liable for placing the truck on the market, for approving the conversion in line with EN3691 or responsible for on-site safety and ATEX compliance know about these changes and are confident that their suppliers are ready to meet the new requirements.”
Moreover, Pyroban reports that it is also providing “information and resources” to ensure companies understand how the new EN1755:2015 standard may affect them. For example, in addition to unveiling a dedicated web page focussing on the changes afoot, the company has also now published a White Paper and a new infographic on the matter that can both be freely downloaded from the company’s website. HCB www.pyroban.com
ACQUISITION • PYROBAN IS NOW UNDER NEW OWNERSHIP AS IT PREPARES TO HELP ITS CLIENTS MEET TOUGHER STANDARDS FOR EXPLOSION-PROTECTED INDUSTRIAL MACHINERY
May 2016, a decision that, as managing director Paul Delaloye says, “is working very well”.
It is from here that FMS supplies labels and other consumable to its customer base, which includes not only dangerous goods shippers and other manufacturers but also local authorities, airlines, airfreight agents, packers and the UK Ministry of Defence.
And while labels remain the mainstay of FMS’s business, the start of the year always brings with it new demand from air shippers who need to keep up with the latest rule changes from the International Air Transport Association (IATA). Nor does IATA limit itself to annual changes to the Dangerous Goods Regulations (DGR); FMS also provides the Quick Reference Guide to the DGR, the Lithium Battery Shipping Guidelines, the Temperature Control Regulations, the Perishable Cargo Regulations, the Ground Operations Manual and the Airport Handling Manual, alongside all the specific handling and identification labels and marks that go with them.
In addition, there are IATA-style Dangerous Goods Notes (DGNs) for air shipments as well as standard DGNs and those for sea/road consignments, as well as air waybills, CMR and live animal documentation and certificates for non-restricted articles.
HAZARD COMMUNICATION IS one of the pillars of safety in the transport of dangerous goods; it makes sure that emergency responders have the right information when an accident occurs but also that those handling dangerous goods in the supply chain are aware of what they are dealing with, and how they should package and stow it.
As HCB’s columnist Gene Sanders points out in his View from the Porch Swing this month (see page 6), the elements of hazard communication – through labels, placards, other marks and documentation – involve not just substances’ proper shipping names, UN numbers and class/division but also
such aspects as warnings about elevated temperature, fumigated loads and those that need to be carried in a particular orientation.
Those whose business it is to ship dangerous goods need to be fully kitted out with all the necessary labels, marks and documents that will appear on or accompany their goods in transit. And they also need to have access to up-to-date regulations.
There are plenty of places to get hold of all this material: specialist suppliers are found all over the world, often providing UN-specification packaging and compliance software alongside all the necessary books and labels.
One such supplier is UK-based Freight Merchandising Services (FMS), which has its office and warehouse in Slough, west of London. FMS moved to these new premises in
The list of hazard labels includes those for packagings in 50 mm and 100 mm sizes, placards and container labels in 250 mm and 300 mm sizes, the relatively new pictograms for use under the EU’s Classification, Labelling and Packaging (CLP) Regulation, the new lithium battery warning marks, and those for marine pollutants and limited and excepted quantities.
But, as Gene Sanders pointed out, the list of handling labels goes on and on and includes such items as cargo aircraft only (CAO), orientation arrows (in black and red), dry ice, fragile items, ‘keep away from heat’, ‘keep dry’, cryogenic liquids, magnetised material, ‘do not stack’, ID 8000 consumer commodities, overpack marks, and the specialised ‘permitted in UK domestic mail only ID 8000’ labels.
All these, Delaloye says, are provided as part of a “fast and friendly service” – customers will also get a free poster showing all the labels likely to be seen on a dangerous goods package.
Full details of the FMS product range can be found at www.fmslondon.co.uk.
accept notifications under the upcoming requirements of Annex VIII to CLP. Annex VIII will significantly change requirements for poison centre notification when it is implemented in 2020.
PORTAL. NCEC EXPLAINS HOW
THE EUROPEAN CHEMICALS Agency (ECHA) has voted to create an opt-in poison centre notification portal, which could harmonise how some EU Member States accept notifications to poison centres.
Poison centres are bodies that disseminate the information provided to them under Article 45 of the Classification, Labelling and Packaging (CLP) Regulation to medical professionals or members of the public in the event of poisonings. Businesses must notify information on the hazards and composition
of their mixtures to poison centres in every Member State they operate in.
The portal, which is predicted to have a development cost of €4.2m, will have phased introduction with a final version potentially released in 2020. It aims to provide a centralised platform for companies to notify and disseminate their product information to the relevant poison centres or equivalent appointed bodies.
According to the UK’s National Chemical Emergency Centre (NCEC), a leading provider of poison centre notifications services and member of the ECHA working group, it is likely that the portal will only be able to
In the majority of cases, as from 2020 businesses will need to notify more information on their mixtures to poison centres than is currently required – in some cases going from a simple safety data sheet (SDS) and label submission to full composition under Annex VIII.
Any notification submitted ahead of the introduction of Annex VIII will be valid until 2025, assuming there is no change that would trigger a renotification, such as a change in product identifier or classification.
“To be clear, if your business has mixtures with a health or a physical effect classification on the EU market now it is a legal requirement and an expectation to notify with relevant poison centres immediately,” says Larissa Silver, poison centre consultancy technical manager at NCEC.
The NCEC is one of the only organisations to
POISON CENTRES • ECHA HAS VOTED TO CREATE A ONE-STOP
WILL AFFECT BUSINESSES IN THE EU
have documented notification procedures for the majority of EU Member States. It conducts poison centre notifications on behalf of several global chemical companies – helping to reduce the time and cost for notification and minimise the risk of non-compliance.
“If your product is on the market in the EU then a poison centre could receive medical emergency calls about it, so businesses should be motivated to notify immediately to protect their customers,” Silver explains, “and we are increasingly seeing enforcement actions being taken by poison centres against non-compliant businesses.”
Among the recommendations for the one-stop portal is a searchable database for enforcement authorities to confirm that notifications have been completed and that companies are compliant. The feasibility study for the portal, published in October 2017, also suggests a repurpose of the
IUCLID software, which businesses use to make notifications to ECHA. If implemented, this would constitute a major change to previously communicated plans for poison centre notification, which businesses will need to adapt to.
The portal would also be offered to Member States on an opt-in basis only, meaning Member States will be able to retain their individual notification processes if they choose to. Member States have widely different processes for notification, which can make compliance a complex and time-consuming process.
“A one-stop portal is an exciting proposition and shows that ECHA continuing to enhance the accessibility of critical product information. However, it is important to bear in mind that the recommendation for the portal to be implemented on an opt-in basis means that many Member States - particularly
those with well-established poison centres like Spain - may retain their own notification processes,” Silver warns.
NCEC, part of Ricardo Energy & Environment, has been providing companies and emergency services with emergency response, regulatory compliance and supply chain support for more than 40 years.
It is therefore natural that NCEC should be taking a leading role in helping businesses understand their responsibilities in terms of poison centre notifications, how the changes to the notification landscape will impact industry and what business can do to minimise the administrative burden of notification. Those wishing to discuss their requirements in more detail can email NCEC on ncec@ricardo.com. NCEC is also holding a number of free webinars on the topic this year; the next will be held on 6 March. HCB www.the-ncec.com
THE JOINT MEETING OF Experts on the Regulations annexed to the European Agreement concerning the International Carriage of Dangerous Goods by Inland Waterways (ADN) – the ADN Safety Committee – held its 31st session in Geneva this past 28 to 31 August. The meeting was attended by representatives of 12 of the 18 ADN contracting parties and delegates from the Central Commission for the Navigation of the Rhine (CCNR), the Danube Commission, the EU and nine non-governmental organisations. Before getting on with finalising the text of the 2019 edition of ADN, the experts noted
that corrections to the 2015 and 2017 texts were demed to have been accepted. Those affecting the 2017 text are few in number and editorial in nature.
The Recommended ADN Classification Societies queried the use of the term ‘rapid blocking valve’ and its equivalence in French and German, only the latter of which uses a consistent term throughout ADN. The Safety Committee agreed with the submission and agreed to use “quick closing valve” in English and “vanne à fermeture rapide” in French.
This affects 3.2.3.1, 7.2.2.21 and several references in Part 9. The Recommended ADN Classification Societies were asked to check whether there are other instances of the term.
The Recommended ADN Classification Societies also followed up on discussions at the August 2016 session regarding emergency showers and eye baths. Taking the experts’ comments into account, its paper proposed an expansion of 9.3.x.60 on special equipment and an amendment to 7.2.4.60. The Safety Committee agreed with those changes, which specify that the water used in showers and face baths must be of comparable quality to drinking water; it also adopted a transitional measure that obligates compliance when certificates are renewed after 31 December 2018.
CCNR presented the session with a report on the latest meeting of the informal working group on the training of experts; this was accompanied by another CCNR paper on the catalogue of questions and one from Germany on the specialised knowledge certificate.
The report of the informal working group raised a number of questions, though the Safety Committee did not express an opinion and invited the working group to continue its discussions. Germany’s paper was deemed insufficiently clear and it was invited to submit a new proposal at the next session. The Administrative Committee was invited to approve CCNR’s proposal to update the directive on the use of the catalogue of questions.
Belgium, Germany, Slovakia and Switzerland had all provided statistics on the results of examinations in their countries, which were considered to be extremely useful. The Secretariat was invited to compile a consolidated document, which could be used by all contracting parties. The informal working group was asked to come up with a standard format for the reports to make it easier to collate and circulate the data.
The Danube Commission had been collating the questions used in the safety adviser examinations and had received input from Austria, Bulgaria, Romania, Slovakia and Ukraine; the Danube Commission regretted that similar information had not so far been received from countries not on the Danube.
Nevertheless, on the basis of the information received so far, which related to all three modes of inland transport, it was clear that they had all been developed with reference to their national context and it would be difficult to drawn on those questions to develop a mandatory catalogue of questions. However, the Danube Commission is now planning to set up a working group to put together a catalogue of questions for use as a reference tool for contracting parties. Once guidelines have been drawn up the Safety Committee could decide whether to reference them in 1.8.3.
The Secretariat provided, in five separate documents, details of the amendments adopted by the Joint Meeting of RID/ADR/ADN
experts in 2016 and 2017, as well as those adopted by WP15. The Safety Committee asked the Secretariat to consolidate these into a single document so they can be considered at the next session.
Austria proposed an amendment to question 4 in the checklist in 8.6.3; this includes a reference to 7.1.4.77, which applies only to dry cargo vessels, whereas the checklist applies only to tank vessels. The Safety Committee agreed with the argument, deleting that reference, and also amended the first sentence of the question for clarity.
CCNR presented a very lengthy paper detailing existing and desired changes throughout the text of ADN needed to implement the modified concept for explosion protection onboard inland waterway vessels, as requested at the previous session. Those changes affect most parts of ADN. The Safety Committee adopted the proposals but, with the Dutch representative saying that more time was needed to check the English text, another chance will be given at the next session for a review of all the changes.
Germany followed up on discussions at the previous session with a proposal to add a Note to 8.3.5. The idea was sound but the Safety Committee agreed slightly different wording to that proposed: NOTE: In addition, all other applicable regulations regarding workplace safety and safety of operations must be observed.
CCNR had come, as requested, with a proposal to define ‘barge’ – something surprisingly missing from ADN. However, the Comité Européen pour l’Élaboration de Standards dans le Domaine de Navigation Intérieure (CESNI), established by CCNR in 2015 to draw up common standards in the field of inland navigation, is currently working on technical requirements for vessels and it seemed best to postpone consideration of the CCNR proposal until that work is completed.
Belgium proposed some specific text for 1.16.1.3.1 to limit the use of provisional certificates of approval. The idea drew criticism both from those who felt that the current text is adequate and from others who felt that placing a limit on the validity of provisional certificates could in fact allow non-compliant vessels to operate for nine months. The proposal was withdrawn.
Austria proposed a number of changes to the provisions concerning vapour return, both in the definitions and obligations and in the checklist in 8.6.3. After some discussion and amendment, the proposals were adopted.
In 1.4.3.3(s), “at the crossing-point of the gas discharge pipe or the compensation pipe” is replaced by “at the connecting-point of the vapour return piping and the venting piping”.
In 1.4.3.7.1(j), “at the connecting-point of the gas discharge pipe or the gas return pipe” »
is replaced by “at the connecting-point of the vapour return piping and the venting piping”. Paragraph 1.4.3.7.2 is amended to read: If the unloader makes use of the services of other participants (cleaner, decontamination facility, etc.) or of the pumps of the vessel he shall take appropriate measures to ensure that the requirements of ADN have been complied with.
In question 12.2 of the ADN Checklist in 8.6.3, “at the connection point” is replaced by “at the connecting-point of the vapour return piping and the venting piping”.
The Netherlands will follow this up at the next session with a proposal on the use of vapour return piping for unloading.
Germany felt there is still uncertainty over the application of 7.2.4.9 to transhipment operations and proposed changes to the notes at the end of that paragraph and to 7.2.4.7.2. In addition, it proposed an interpretation of the definition of ‘carriage’ in 1.2.1. With some changes, the proposed amendments were adopted, with 7.2.4.7.2 amended to read: The reception from other vessels of unpackaged oily and greasy liquid wastes resulting from the operation of vessels and the handing over of products for the operation of vessels into the bunkers of other vessels shall not be taken to be loading or unloading within the meaning of 7.2.4.7.1 above or transhipment within the meaning of 7.2.4.9.
A second Note is added to 7.2.4.9: This prohibition also applies to transhipment between supply vessels.
The question of the interpretation of ‘carriage’ was, it was felt, a matter for the Joint Meeting to rule upon.
Germany also sought the harmonisation of the provisions for berthing in 7.1.5.4.1 and 7.2.5.4.1 which, its paper said, should be identical. The Safety Committee agreed and thought the existing text of 7.2.5.4.1 is correct. Germany was invited to prepare a proposal for the next session on that basis.
Austria offered some consequential amendments following on from the replacement at the last session of the term ‘closed container with complete metal walls’ with ‘closed container’. That change had raised some questions – does it, for instance, include containers with a sheeted roof? The Safety Committee agreed with Austria and made what are in effect purely editorial changes in 1.1.3.6.2, 7.1.4.3.4, 7.1.4.4.2 and 7.1.4.14.4.
The Recommended ADN Classification Societies had been asked to look at provisions referencing Class A-60 fire protection in Chapter 9.3; it provided some wording to achieve consistency with the provisions of the International Convention for Safety of Life at Sea (Solas), which was found acceptable.
The Recommended ADN Classification Societies had also spotted that, while
9.3.1.11.2(d) and 9.3.2.11.2(d) prohibit the use of side-struts, there is no equivalent 9.3.3.11.2(d). It was felt that this is an oversight. The Safety Committee agreed and created that paragraph, also making a change to the table of general transitional provisions for tank vessels in 1.6.7.2.2.2.
Another paper from the Recommended ADN Classification Societies sought amendment of 1.15.3.8, which lays out the internal quality systems that classification societies must implement. Its proposal offered more detail on the EN and ISO standards to be applied and on the process of third-party verification. However, several delegations felt that this change could reduce the level of safety. The Societies said they would discuss the matter at their meeting in October 2017 before deciding how to proceed.
The European Barge Union (EBU), the European River-Sea-Transport Union (ERSTU) and the European Skippers Organisation (ESO) had, over the preceding two years, been looking at the provisions on the use of permissible construction materials, which
had been identified as being in need of bringing up to date and being presented in a different format.
The Safety Committee appeared happy with the revised table in 9.3.x.0.3 but asked the organisations to add a line for all types of movable equipment. It also felt there was no need for two new paragraphs proposed for 7.1.2.3 and 7.2.2.3.
Belgium had identified some potential ambiguities in Table C, which its paper said had crept into the 2017 text. The Safety Committee decided to forward the paper to the working group on substances but was concerned that it might not have time to meet and produce specific proposals for correction before the deadline for submissions for the January 2018 session, which would be the last chance to agree amendments for the 2019 text.
Another paper from Belgium referred to 7.1.2.19 and 7.2.2.19, which deal with pushed convoys and side-by-side formation. It felt that it should be made clear that the provisions of those paragraphs do not apply to bunkering and waste collection. Belgium was asked to propose a Note to clarify the matter and also to define ‘side-by-side formation’, taking into account definitions developed by CESNI.
A joint paper from Belgium, the Netherlands and Switzerland laid out necessary amendments to take account of new common standards for the use of firefighting systems using dry aerosol-forming extinguishing agents. The Safety Committee adopted the proposal in principle and several
comments were made on the wording. A new proposal will be made at the next session taking those comments into account and also bearing in mind parallel work being undertaken by CESNI.
The Recommended ADN Classification Societies had noticed that, when 9.3.x.25.10 had been added in the 2017 edition of ADN, following its proposal to address risks involved in the supply of compressed air on deck, mistakes had been made in the final text. The Safety Committee agreed and moved the reference to ‘wheelhouse’ in those paragraphs and also in 9.3.1.40.1 and 9.3.3.40.1.
The European Federation of Tank Storage Associations (Fetsa), with the support of Fuels Europe, EBU and ESO, returned to the topic of product blending onboard inland tankers, which it had raised in an informal document at the previous session. Fetsa’s paper gave more information on how such blending operations are undertaken, the products involved and its ideas for what any regulatory text should cover.
Opinions differed as to whether this is an issue for ADN at all; the onboard blending of product is not a transport issue, for instance, and there may be interactions with other maritime and port regulations and workplace safety and environmental protection legislation. Others said that such practices are not authorised during transport. The other side of the coin, as some experts felt, was that blending operations are taking place in the »
real world and it would be better to regulate them than leave them in a legal vacuum.
In the end, the Safety Committee agreed with Fetsa that an informal working group should be set up to decide whether the existing practice violates the provisions of ADN and to decide which operations could be authorised and under what conditions.
The European Chemical Industry Council (Cefic) had reported in 2016 that, during a process of classification under the EU’s Regulation on classification, labelling and packaging (CLP), ExxonMobil Chemical had identified that tripropylene (UN 2057, PG III) presents an acute aquatic toxicity hazard. Cefic
now returned with a formal proposal to amend the entry in Table C. Meanwhile, Germany had initiated a multilateral agreement, M021, to allow the hazard ‘N1’ to be mentioned on the transport document in place of ‘N3’.
The Safety Committee adopted the proposal to amend the entries in Table C for UN 2057, both PG II and PG III. As to the multilateral agreement, it was noted that it was not yet applicable as there were so far no counter-signatories; moreover, the aim of such agreements is to provide a derogation from the current requirements and not, as in this case, to reflect the use of a more stringent interpretation.
A joint submission by France, the Netherlands and Cefic returned to earlier discussions surrounding a possible amendment to 7.2.4.25.5 on the use of closed cargo tanks. The proposal was deemed acceptable and that paragraph has been amended to read:
The gas/air mixtures released during loading operations shall be returned ashore through a vapour return piping if:
• A closed cargo tank is required according to column (7) of Table C of Chapter 3.2; or
• A closed cargo tank was required for the previous cargo in column (7) of Table C of Chapter 3.2 and before the loading the
concentration of flammable gases of the previous cargo in the cargo tank is above 10% of the LEL or the cargo tank contains toxic gases, corrosive gases (packing group I or II) or gases with CMR-characteristics (Categories 1A or 1B) in a concentration above national accepted exposure levels.
If the substance to be loaded requires explosion protection according to column (17) of Table C of Chapter 3.2, and the use of the vapour return piping is prescribed, the connection of the vapour return piping shall be designed such that the vessel is protected against detonations and the passage of flames from the shore. The protection of the vessel against detonations and the passage of flames from the shore is not required when the cargo tanks are inerted in accordance with 7.2.4.18.
In an informal document, EBU, ESO and ERSTU proposed deleting the last paragraph of 7.2.4.10.1 on the grounds that it is now obsolete. The Safety Committee accepted the argument and deleted the text as proposed.
CCNR had identified inconsistencies in the use of the terms ‘residual cargo’ and ‘cargo residues’ and in the French and German equivalents. The Safety Committee accepted in principle that there is a need for some changes and asked CCNR to make a formal proposal indicating where such changes should be made.
EBU, ESO and ERSTU asked for M017 to be extended for another year; however, there was no support from contracting parties for any extension to the 31 December 2017 expiry date.
The same organisations raised the issue of leaks of dangerous goods from loading arms, which they said cause harm to crew and damage to the environment. They asked for a working group to be set up to look at the problem. The Safety Committee noted the comments but asked Cefic and Fuels Europe to provide evidence to substantiate the problem.
The same organisations also sought amendment of 7.1.4.1, which sets limits
on the volumes of dangerous goods that may be carried, saying that some of those limits seem to have no sensible grounding. The Safety Committee was content to agree to set up a correspondence group but expressed reluctance to the idea of deleting the maximum limits.
A joint paper from Belgium, France and the Netherlands sought establishment of an informal working group to look at the use of membrane tanks on inland vessels for the carriage of LNG. A temporary derogation had been issued for a planned vessel, Argos GL, but due to economic circumstances this vessel was never built. However, there are plans for other vessels and it would be useful to establish the conditions under which membrane tanks could be used on inland vessels and what adjustments to ADN would be necessary to allow their use.
The Safety Committee agreed with the proposal; the informal working group is expected to meet early in 2018 with the aim of submitting a report for the August 2018 session.
Germany presented a report on the outcome of the ninth meeting of the informal working group on substances, which generated a large number of proposals for amendment, most of which were adopted. These involve a lot of changes to Tables A and C, together with additional explanatory text for a number of entries. Consignors and carriers will need to check the final text carefully to see if the products they are moving are affected. The relevant entries are UN Nos 0510, 1120, 1148, 1163, 1188, 1191, 1203, 1206, 1208, 1224, 1229, 1262, 1267, 1268, 1274, 1275, 1280, 1578, 1663, 1664, 1764, 1783, 1863, 1986, 1987, 1989, 1991, 1992, 1993, 2048, 2053, 2057, 2078, 2205, 2259, 2280, 2309, 2357, 2381, 2448, 2485, 2486, 2531, 2618, 2920, 2924, 2929, 2983, 3166, 3171, 3256, 3257, 3271, 3272, 3286, 3295, 3446, 3475, 3494, 3527, 3528, 3529, 3530, 3531, 3532, 3533, 3534, 9001 and 9002.
Some items were left undecided. It had been noticed that the entry for UN 3256 requires an open type N tank vessel with flame arrester; however, column (5) would require carriage in closed cargo tanks. »
A decision on this has been deferred to give industry time to study the question.
The meeting had also noted that substances with more than 10 per cent benzene were not addressed in ADN; the working group proposed the addition of three nos entries but it was aware that this could not be done in time for application under ADN 2017. The Netherlands offered to initiate a multilateral agreement to allow their early application.
The English and Russian versions of ADN currently omit the entry for UN 1208 hexanes; it was agreed that a corrigendum would be issued to put this right.
The Netherlands had asked for a new entry for UN 1288 shale oil, PG II; however, as the Safety Committee noted, the Netherlands had not yet received data from the consignor concerning the product and it was agreed to postpone a decision until the relevant information was forthcoming.
The Netherlands provided a report on the fifth meeting of the informal working group on the degassing of cargo tanks. Again, this document included a significant number of proposals for amendment of ADN, which were all adopted, some with modifications. These included a revision of the definition of
‘toximeter’ and new definitions for ‘degassing’, ‘explosion range’, ‘lower explosion limit (LEL)’, ‘reception facility’ and ‘upper explosion limit (UEL)’.
A new sub-paragraph (k) is added to 1.4.2.2.1: Complete his section of the checklist referred to in 7.2.3.7.2.2 prior to the degassing of empty or unloaded cargo tanks and piping for loading and unloading of a tank vessel to a reception facility.
A new section is added:
1.4.3.8 Reception facility operator
1.4.3.8.1 In the context of 1.4.1, the reception facility operator shall in particular:
(a) Complete his section of the checklist referred to in 7.2.3.7.2.2 prior to the degassing of empty or unloaded cargo tanks and piping for loading and unloading of a tank vessel;
(b) Ascertain that, when prescribed in 7.2.3.7.2.3, there is a flame arrester in the piping of the reception facility which is connected to the degassing vessel, to protect the vessel against detonations and passage of flames from the side of the reception facility.
A new Note is added at the end of 1.8.3.1: This obligation does not apply to reception facility operators.
There are amendments throughout paragraphs 7.1.3.1.3 to 7.1.3.1.7, 7.1.4.12.2
and 7.1.6.12 and a new 7.1.3.16 and 7.2.3.16: All measurements on board the vessel shall be performed by an expert according to 8.2.1.2, unless provided otherwise in the Regulations annexed to ADN. The results of the measurements shall be recorded in writing in the book according to paragraph 8.1.2.1 (g).
In 7.1.6.16, IN01 is amended to read: After loading and unloading of these substances in bulk or unpackaged and before leaving the cargo transfer site, the concentration of flammable gases and vapours given off by the cargo in the accommodation, engine rooms and adjacent holds shall be measured by the loader or unloader or by an expert according to 8.2.1.2 using a gas detector. The results of the measurement shall be recorded in writing.
Before any person enters a hold and prior to unloading, the concentration of flammable gases and vapours given off by the cargo shall be measured by the unloader of the cargo or by an expert according to 8.2.1.2. The results of the measurement shall be recorded in writing.
The hold shall not be entered or unloading started until the concentration of flammable gases and vapours given off by the cargo in the airspace above the cargo is below 50 % of the LEL.
If the concentrations of flammable gases and vapours given off by the cargo is not below 50 % of the LEL safety measures shall be taken immediately by the loader, the unloader or the responsible master.
In Chapter 7.2, 7.2.3.1.5 is amended to read: Before any person enters cargo tanks, the residual cargo tanks, the cargo pump-rooms below deck, cofferdams, double-hull spaces, double bottoms, hold spaces or other confined spaces:
(a) When dangerous substances of Classes 2, 3, 4.1, 6.1, 8 or 9 for which a gas detector is required in column (18) of Table C of Chapter 3.2 are carried on board the vessel, it shall be established, by means of this device that the concentration of flammable gases and vapours
EUROPE’S INLAND WATERWAY FLEET CARRIES ALL MANNER OF GOODS AND PERSONAL EFFECTS AND ADN MUST ADDRESS A WIDE RANGE OF HAZARDS AND OPERATING PRACTICES
given off by the cargo in these cargo tanks, residual cargo tanks, cargo pump-rooms below deck, cofferdams, double-hull spaces, double bottoms, or hold spaces is not more than 50% of the LEL. For the cargo pump-rooms below deck this may be determined by means of the permanent gas detection system;
(b) When dangerous substances of Classes 2, 3, 4.1, 6.1, 8 or 9 for which a toximeter is required in column (18) of Table C of Chapter 3.2 are carried on board the vessel, it shall be established, by means of this device that the cargo tanks, residual cargo tanks, cargo pump-rooms below deck, cofferdams, doublehull spaces, double bottoms or hold spaces do not contain concentration of toxic gases and vapours given off by the cargo which exceeds national accepted exposure levels.
In deviation of 1.1.4.6, more stringent national legislation on the entry into holds shall take precedence over the ADN.
A similar amendment is made to 7.2.3.1.6. The title of 7.2.3.7 is amended to read: “Degassing of empty or unloaded cargo tanks and piping for loading and unloading”. That entire section has been rewritten.
There are also a number of consequential amendments in 7.2.3, 7.2.4 and 7.2.5 and additional provisions in Chapters 8.1 and 8.2.
CCNR provided a report of the 12th meeting of the informal working group on explosion protection of tank vessels, which largely dealt with the use of land-based power by inland vessels carrying dangerous goods. The Safety Committee accepted the group’s conclusions in principle. However, as the necessary amendments had only been made available in German it would be necessary for them to be submitted in an official document for consideration at the next session.
That next session is due to take place in Geneva from 22 to 26 January 2018; its task will be to finalise the draft amendments that will enter into force on 1 January 2019 but, given that the Safety Committee still has to discuss the amendments emanating from the RID/ADR/ADN Joint Meeting as well as all those points carried over from the August 2017 session, it will be a very busy week.
HCB will report back on that meeting in a forthcoming issue and provide a summary of the changes contained in the 2019 text. HCB
THE INTERNATIONAL MARITIME Organisation’s (IMO) Sub-committee on Carriage of Cargoes and Containers (CCC) held its fourth session from 11 to 15 September 2017 in London. The meeting had plenty on its plate, not least the updating of the International Maritime Dangerous Goods (IMDG) Code.
To this end, CCC reviewed the work of the Editorial & Technical (E&T) Group, which had finalised corrections to Amendment 38-16 of the International Maritime Dangerous Goods (IMDG) Code (see page 62) as well as the changes that will appear in the next Amendment, 39-18.
For reference, Amendment 38-16 took mandatory effect on 1 January 2018, though it has been available for use since 1 January 2017. Similarly, those subject to the Code will be able to use Amendment 39-18 as from 1 January 2019 and it will become mandatory on 1 January 2020.
For the most part, CCC agreed the corrections and amendments to the IMDG Code as well as revisions to the Emergency Schedules, subject to a final review by the E&T Group at a meeting held just after the CCC session. The final text of Amendment 39-18 will need to be ratified by the Maritime Safety Committee (MSC) at its 99th session in May 2018; only after that can IMO’s publications department get on with the serious work of laying out the final text for the printers.
CCC’s work on Amendment 39-18 began with a look at the decisions already made, to which some further changes were agreed. To the list of items assigned to Class 9 in 2.9.2.2 was added an entry for UN 3548 Articles containing miscellaneous dangerous goods nos.
The headings in 3.1.4.4 and other references to segregation groups were aligned so that there is no space between ‘SGG’ and the following number (eg SGG1, SGG1a, etc).
The segregation groups for UN 1971 (SGG8) and UN 1908 (SGG5) were confirmed and the square brackets removed from those entries in column (16b) of the Dangerous Goods List.
In packing instruction P403, special packing provision PP31, “, except for solid fused material” was deleted. It is likely that P403 and P410 will need a review at a forthcoming session.
A new definition for IMO type 9 tanks was added in the Note to the transitional provisions for the use of portable tanks at 4.2.0.1:
IMO type 9 tank means a road gas elements vehicle for the transport of compressed gases of class 2 with elements linked to each other by a manifold, permanently attached to a chassis, which is fitted with items of service equipment and structural equipment necessary for the transport of gases. Elements are cylinders, tubes and bundles of cylinders, intended for the transport of gases as defined in 2.2.1.1.
While CCC and the E&T Group had by now adopted most of the amendments in the 20th revised edition of the UN Model Regulations into the new edition of the IMDG Code, following a recent decision by the UN Sub-committee of Experts on the Transport of Dangerous Goods (TDG), reference to a
2-mm line around labels was removed from 5.2.2.2.1.1.2. In 5.3.1.1.2 and 5.3.2.3.1 reference to ‘bulk container’ is inserted after ‘transport units’. The last sentence of the revised 5.4.3.1 was deleted and a textual change was made in 5.4.3.3 for clarity.
Discussion then moved on to a number of new submissions. Many of these were put forward by Germany, whose head of delegation, Gudula Schwann, is chair of the E&T Group and, as from this session, vice-chair of CCC.
The first proposed a clarification in SP 963, which is specific to the maritime mode, that nickel metal hydride (NMH) cells or, whether packed with or contained in equipment, or button cells packed separately, are not subject to the provisions of the IMDG Code. This was accepted, with a change also made in the Dangerous Goods List against UN 3496.
A rather more complex proposal involved the applications of the segregation requirements of SG1 apply to UN 2956; SP 133, which applies to this entry, required a Class 1 label to be applied, although the primary hazard for UN 2956 is Division 4.1. There was some support for the change, although the proposed wording was not thought sufficient. After some work, CCC accepted a revised text for the description in SG1 in 7.2.8:
For packages carrying a subsidiary hazard label of class 1, segregation as for class 1, division 1.3. However, in relation to goods of class 1, segregation as for the primary hazard.
Another issue in respect of segregation had arisen following the recent addition of a Division 6.1 subsidiary hazard for uranium hexafluoride, as explained in papers from Germany and the World Nuclear Transport Institute (WNTI). Again, there was broad support for the changes but further work was needed before an acceptable solution could be found. This involved creation of a new SG78 for UN 2977 and 2978:
Stow “separated longitudinally by an intervening complete compartment or hold from” division 1.1, 1.2 and 1.5.
SG68 was removed from those two entries. For UN 3507, SG77 was amended to read: Segregation as for class 8. However, in relation to class 7, no segregation needs to be applied.
France felt that a change was needed to SP 363, the fourth indent of which is specific to the IMDG Code. It currently includes a requirement to apply a marine pollutant mark of 100 x 100 mm for UN 3530 but the proposal sought the use of a larger, 250 x 250 mm, mark in cases where the engine or machinery involved contains more than 60 litres of fuel and has a capacity of more than 3,000 litres, to be consistent with requirements in the UN Model Regulations for other placards. The US identified a gap in the proposal concerning engines or machinery containing more than 60 litres of fuel but with a capacity of less than 3,000 litres.
Both points were taken into account by the E&T Group, which drew up a new sub-paragraph 10 for SP 363 as part of a larger revision and expansion of that special provisions.
Peru returned with further proposals on the fumigation of cargoes of fish meal, arguing for lower levels of ethoxyquin to be added to and to be residue in cargoes both in packaged and bulk form. Such a move is necessary to comply with EU requirements that will enter into force in 2019. There was support in principle at CCC, leaving the E&T Group with the task of finalising the textual changes.
This was done by revising SP 308 to read: Stabilization of fish meal shall be achieved to prevent spontaneous combustion by effective application of ethoxyquin, BHT (butylated hydroxytoluene) or tocopherols (also used in a blend with rosemary extract) at the time of production. The said application shall occur within twelve months prior to shipment.
Fish scrap or fish meal shall contain at least 50 ppm (mg/kg) of ethoxyquin, 100 ppm (mg/kg) of BHT or 250 ppm (mg/kg) of tocopherol based antioxidant at the time of shipment.
At the suggestion of the Dangerous Goods Advisory Council (DGAC), a note was added: For the transport of fish meal in bulk, see the IMSBC Code.
As a consequence, SP 945 was deleted.
A rather more extensive proposal envisaged the restructuring of section 5.5.2, which deals with fumigated cargo transport units (CTUs). The proposal generated considerable discussion and, in the end, there was little agreement at CCC other than MSC.1/Circ.1361 is in need of revision.
The E&T Group was invited to look at the proposals in more detail. It was evident from the discussions that there is an issue insofar as the IMDG Code is designed to deal with cargo during maritime carriage (other than the relatively recently included provisions for the training of shoreside personnel), whereas issues surrounding the safety of fumigated CTUs relate largely to their handling within container terminals and at their destination. »
To some extent this had been foreseen when 5.5.2 was originally drawn up: it was intended to work as a standalone provision that could be copied for reference by shoreside workers, albeit their safety is normally overseen as part of occupational safety and health regulations within their national jurisdiction.
Further concerns emerged surrounding the potential for those who fumigate cargoes to become dangerous goods shippers, which would mean a requirement for training and legal responsibilities as regards placarding and the completion of a dangerous goods transport document. It was pointed out that some of these concerns apply equally to section 5.5.3 on the use of conditioning treatments in CTUs. It was agreed that the UN TDG Sub-committee should be consulted on this and on the necessity to specify what “adequate ventilation” means in practice.
In the end very few changes were agreed, other than the deletion of 5.5.2.5.2 (with renumbering of the following paragraphs) and the revision of what is now 5.5.2.5.3 to read:
Cargo transport units shall be fumigated in accordance with the requirements determined by the competent authority, to ensure a sufficient
period has elapsed to attain a reasonable uniform gas concentration throughout the cargo in it. Twenty-four hours is normally sufficient for this purpose.
While there was general agreement on the need for MSC.1/Circ.1361 to be revised, there was little agreement on what actually needs to be done. After discussion, interested delegations were invited to make submissions to CCC’s next session.
China proposed a mode-specific special provision to require that batteries, wet, non-spillable, installed in CTUs for the operation of equipment in the CTU, meet similar provisions to those applied to lithium batteries under SP 389. There were questions but few answers at CCC and the E&T Group also failed to reach a consensus. Some felt this was a question for the UN TDG Sub-committee.
The European Chemical Industry Council (Cefic) submitted a proposal building on prior discussions on the transport of battery-vehicles on shortsea vessels. The concept of ‘battery-vehicle’ clearly confused some delegations – this is a concept defined in ADR but largely absent outside Europe. Battery-vehicles are not battery-powered and are not the same as multiple-element gas containers (MEGCs).
Eventually a definition for a new IMO type 9 tank was agreed (see above). After much debate, a new 6.8.3.4 was agreed, with provisions for road gas elements vehicles for compressed gases of class 2 (IMO Type 9). This sub-section includes general provisions (6.8.3.4.1), requirements for design and construction (6.8.3.4.2) and provisions for approval, testing and marking (6.8.3.4.3). The title of Chapter 6.8 was changed to “Provisions for road tank vehicles and road gas elements vehicles”.
A full list of the changes that will appear in Amendment 39-18 to the IMDG Code will appear in an issue of HCB later in the year, once they have been formally adopted.
Aside from IMDG-related issues, CCC also had other matters to discuss. It continued with its work to update the International Maritime Solid
FINAL TEXT OF AMENDMENT 39-18 WILL NEED TO BE RATIFIED BY MSC AT ITS 99TH SESSION IN MAY 2018”
Bulk Cargoes (IMSBC) Code, the next edition of which will be a consolidated version. This is expected to be prepared by the E&T Group at its meeting in the spring of 2018 for final adoption by MSC at its 101st session in 2019.
Draft amendments were agreed to Part A-1 of the International Code of Safety for Ships using Gases or other Low-flashpoint Fuels (IGF Code), relating to protection of the fuel supply for liquefied gas fuel tanks, aimed at preventing explosions. Further progress was also made in developing safety provisions for ships using fuel cells, which will appear in a new Part E in the IGF Code.
CCC also agreed unified interpretations to the IGF Code and the International Code for the Construction and Equipment of Ships Carrying Liquefied Gases in Bulk (IGC Code) relating to testing of high-level alarms and level indicators in the bilge well of tank connection spaces of independent liquefied gas storage tanks.
Also relating to gas ships, discussions continued on the suitability of high-manganese austenitic steel for cryogenic service. It was agreed that draft interim guidelines will be developed for the use of such steels in cryogenic services and a correspondence group was re-established for this purpose.
Two specific hazards were also addressed by CCC. The first involved the carriage of bauxite and CCC was moved to issue new guidance in the form of a revision to CCC.1/Circ.2. As a result of work carried out over the past two years, CCC noted that some bauxite cargoes should be classified as Group A, with a shipping name of ‘bauxite fines’.
During its session CCC finalised draft test procedures for determining the transportable moisture limit (TML) of bauxite cargoes, the draft individual schedule for Group A bauxite and draft amendments to the individual schedule for Group C bauxite. Group A bauxite should be carried in accordance with sub-section 1.3 of the IMSBC Code.
These drafts are expected to be adopted by MSC at its 101st session in 2019 for entry into force on 1 January 2021.
The revised circular invites governments to note that those bauxite cargoes deserving of a Group A classification pose a risk to ships and seafarers and suggests that maritime administrations pass this message on to vessel operators, agents, terminals and others involved in the transport of bauxite by sea.
The second specific hazard addressed during the meeting was ammonium nitratebased fertilisers (non-hazardous), following incidents involving the vessels Purple Beach (in 2015) and Cheshire (in 2017). CCC noted that investigations are not yet complete but felt that the risks inherent in the transport of this cargo in bulk deserved prompt recognition; a new circular CCC.1/Circ.4 was issued.
During the two incidents mentioned, the cargo gave off clouds of toxic gas large enough to envelop the ship, hindering the safe abandonment of the vessels and rescue and firefighting efforts. The circular notes that, during such events, cargo decomposition may continue for several days and result in temperatures within cargo holds of as much as 500˚C. The best protection against such incidents is the early identification of any cargo decomposition through regular monitoring of the cargo throughout the voyage. HCB
USE OF AMENDMENT 38-16 to the International Maritime Dangerous Goods (IMDG) Code became mandatory on 1 January 2018; this version had been available for use since 1 January 2017 but, before it took mandatory effect, the International Maritime Organisation (IMO) made a number of corrections to the text.
The corrigendum affects the English, French and Spanish versions of the IMDG Code. The list of changes is extremely lengthy, although many are minor editorial corrections. However, a significant number make substantive corrections to the text
and all those subject to the provisions of the IMDG Code are advised to look closely to see if their operations will be affected.
Leaving aside spelling mistakes and formatting errors, some of the changes that users should be aware of are summarised in the following paragraphs.
The definition of ‘self-accelerating decomposition temperature (SADT)’ in 1.2.1 is changed to specify that the SADT shall be determined “in accordance with Part II of the Manual of Tests and Criteria”.
In the Dangerous Goods List in Chapter 3.2, “PP40” is deleted from column (9) for all those entries that are not Packing Group II. This affects UN Nos 1396, 1398, 1402, 1403, 1405, 3132 and 3208.
Also in the Dangerous Goods List, there are changes to the spillage and/or fire schedules in column (15). This affects UN Nos 0500, 0501, 1324 and 2735. The following special provisions are added: SP368 to UN 2908, SP325 to UN 2913 and SP326 to UN 3326.
“SW1” is inserted in column (16a) against UN 2383. SG72 now refers more generally to the segregation examples in 7.2.6.3 rather than the example table; as such, SG72 is added in column (16b) for UN Nos 3391 to 3400.
The words “or fuel cells” are deleted from column (17) against UN 3530.
There are textual changes to a number of special provisions. In SP207, “Moulding compounds” is replaced by “Plastic moulding compounds”. A new third paragraph is added to SP225 specifying the types of fire extinguisher covered by the special provision. In SP384, a last sentence is added before the Note:
However, for placarding of cargo transport units, the placard shall correspond to Model No 9.
Changes to the marking and labelling provisions in Chapter 5.2 include a clarification in 5.2.2.2.1.3 that the new lithium battery label (model No 9A) may not include additional text.
A significant error in 5.3.2.0.2 has been rectified: “not more than 65 mm” is replaced by “not less than 65 mm”.
In Chapter 6.5, the last sentence of 6.5.2.1.2 is deleted and 6.5.5.6.4, on provisions for wooden intermediate bulk containers (IBCs) is revised.
In the list of generic and nos proper shipping names in Appendix A, the new UN entries for polymerising substances are moved from generic entries to specific entries. There are also a number of corrections to entries in the alphabetical index. HCB
The full list of corrections to the English, French and Spanish versions of Amendment 38-16 of the IMDG Code can be found in the report of the 28th session of the Editorial & Technical Group of the IMO Sub-committee on Carriage of Cargoes and Containers, E&T 28/WP.1.
Joint meeting of Experts on the Regulations ECE Geneva Jan 22–26 annexed to ADN (WP15/AC2), 32nd session
Administrative Committee of ADN ECE Geneva Jan 26
RID Committee of Experts’ working group on OCTI/ Hamburg Jan 30–31 tank and vehicle technology UIP
Sub-Committee on Pollution Prevention and IMO London Feb 5–9 Response (PPR), 5th session
Temporary Working Group on Annex 2 to OCTI/ Warsaw Feb 13–16 SMGS: Provisions for the Carriage of OSJD Dangerous Goods
Joint meeting of the RID Committee of ECE/OCTI Bern Mar 12–16 Experts and the Working Party on the Transport of Dangerous Goods (WP15)
Dangerous Goods Board, 112th meeting IATA Dallas Mar 19–21
Marine Environment Protection Committee IMO London Apr 9–13 (MEPC), 72nd session
Editorial & Technical Group (IMSBC Code), IMO London Apr 16–20 29th meeting
Working Party on the Transport of Dangerous ECE Geneva May 14–18 Goods (WP15), 104th session
Maritime Safety Committee (MSC), IMO London May 16–25 99th session
RID Committee of Experts’ standing working OCTI Berne May 28–30 group (9th session)
RID Committee of Experts (55th session) OCTI Berne May 30
ECOSOC Sub-committee of Experts on the ECE Geneva Jun 25–Jul 4 Transport of Dangerous Goods (53rd session)
ECOSOC Sub-committee of Experts on the ECE Geneva Jul 4–6 Globally Harmonised System of Classification and Labelling of Chemicals (35th session)
Joint meeting of Experts on the Regulations ECE Geneva Aug 27–31 annexed to ADN (WP15/AC2), 33rd session
Administrative Committee of ADN ECE Geneva Aug 31 Sub-committee on Carriage of Cargoes and IMO London Sep 10–14 Containers (CCC), 5th session
Joint meeting of the RID Committee of ECE/OCTI Geneva Sep 17–21 Experts and the Working Party on the Transport of Dangerous Goods (WP15)
Dangerous Goods Board, 113th meeting IATA * Sep/Oct*
Dangerous Goods Panel (DGP) ICAO * Oct*
Marine Environment Protection Committee IMO London Oct 22–26 (MEPC), 73rd session
Working Party on the Transport of Dangerous ECE Geneva Nov 6–9 Goods (WP15), 105th session
RID Committee of Experts’ standing working OCTI Poland Nov 19–23 group (10th session)
ECOSOC Sub-committee of Experts on the ECE Geneva Nov 26–Dec 4 Transport of Dangerous Goods (54th session)
Maritime Safety Committee (MSC), IMO London Dec 3–7 100th session
ECOSOC Sub-committee of Experts on the ECE Geneva Dec 5–7 Globally Harmonised System of Classification and Labelling of Chemicals (36th session)
ECOSOC Committee of Experts on TDG and ECE Geneva Dec 7 GHS (9th session)
ECE – UN Economic Commission for Europe; IAEA – International Atomic Energy Agency; IATA – International Air Transport Association; ICAO – International Civil Aviation Organisation; IMO – International Maritime Organisation; OCTI – Central Office for International Rail Transport
* Details to be confirmed
GENERAL NOTE: These regulatory authorities are the international organisations responsible for the provisions governing the carriage of dangerous goods by various modes of transport. The list contains the major sessional meetings, together with certain scheduled working group and ad hoc group meetings. HCB will keep readers informed of further relevant meetings as and when they are called.
Too often HCB picks up stories of grisly accidents in developing countries involving a road tanker that has overturned – normally as a result of speeding, bad driving, poor roads or lax vehicle standards. In many cases, poor people living nearby run to collect the free fuel (gasoline, diesel, kerosene or whatever) spilling from the tanker; often someone is smoking while doing so and the vehicle explodes.
Residents of Chickballapur, a modest town in the Indian state of Karnataka, were somewhat more fortunate last month, when a tanker driver lost control of his vehicle and it overturned. On this occasion, though, its cargo was milk and residents rushed to the scene with buckets and jugs to collect the free bounty.
While this was going on, some rescuers pulled the driver and his assistant from the cab, along with three (count ‘em!) other people travelling in the tanker. They were all sent to hospital with minor injuries. According to a report in The Hindu, the tanker was not supposed to be on the road where the accident happened but it appeared that the driver had taken a detour to give a few of his relatives a lift.
We think it unlikely that the driver will still have a job when he gets out of hospital.
We are well used to the process by which beer is turned into water – it happens every night at our local - but scientists at the University of Bristol in the UK claim to have found a more sustainable use for our favourite tipple. A project at the university’s
School of Chemistry has been looking at ways of converting ethanol to butanol –which has a higher energy density and would be a better alternative to ethanol as a biobased transport fuel.
Press reports say that alcoholic drinks are being used to test a process for converting their ethanol into butanol through the use of a catalyst. So far, the results have been good and it seems the technology has the potential to be scaled up for industrial production.
Our sense of alarm at this potential diversion of a chunk of the UK’s beer supplies was fortunately misplaced. It seems that alternative sources of ethanol will be used for industrial-scale production – phew!
Inmates at the Boyd County Detention Center in Kentucky were evacuated one day at the end of November due to a “hazmat situation”, local press reported. One jailer and one inmate needed medical treatment after inhaling chemical fumes, the facility reported.
It all happened when a maintenance worker at the jail was trying to clear a clogged drain; the usual cleaner he used for such operations was clearly not up to the job, so the worker decided to try something stronger.
Regular readers can imagine what happened next: the two chemicals reacted, creating a cloud of noxious vapour. The local hazmat crew had to be called in to flush out the system and decontaminate the booking area. Later the same day, WSAZ News Channel 3 gleefully reported, the facility was given the all clear and “was back open for intakes and releases”. It sounds to us like there had already been plenty of releases.
Employer Cargo Media
Full time
Cargo Media is looking for an enthusiastic, outgoing and self-motivated Deputy Editor to join the dedicated production team for HCB magazine, the world’s leading trade title for dangerous goods professionals. This busy and stimulating role requires an individual who is energetic, meticulous and proactive.
The successful candidate will be required to fulfil a number of editorial duties, including editing, writing, client liaison and project management, as well as representing HCB at industry events around the world.
HCB is a global provider of business-critical information to the dangerous goods industry. With constantly updated reports on every aspect of the dangerous goods supply chain, the monthly title was established in 1980 and has grown to become a leading media partner for key conferences and events around the world.
Today it is the number-one voice on all issues concerning the transport and handling of dangerous goods, delivering ground-breaking data, analytics and information to an international readership of influential individuals and organisations.
In addition to the monthly print magazine, HCB also produces digital content in the form of an e-zine version, a weekly newsletter and a website – www.hcblive.com. The HCB brand also encompasses HCB TV and film-production capabilities.
If
would like to be
for
please send your CV and covering letter to samuel.ford@hcblive.com with “Deputy Editor
in the subject line of your email.