
3 minute read
Schütz expands reconditioning capacity
BIG IN BRAZIL
RECONDITIONING • THE WORLD OF INDUSTRIAL PACKAGING IS NO STRANGER TO THE CIRCULAR ECONOMY CONCEPT. SCHÜTZ VASITEX IS EXPANDING ITS CAPABILITIES IN BRAZIL
EXTENSIVE INVESTMENT OVER recent months has doubled reconditioning capacity at Schütz Vasitex, the Brazilian wing of industrial packaging giant Schütz, based in BonsucessoGuarulhos near São Paulo. The work not only involved the expansion of the site itself but also optimisation of internal logistics, the production of high-quality HDPE recyclate from used inner bottles of composite intermediate bulk containers (IBCs), reprocessing of steel cages and base plates of IBCs and the loading of reconditioned containers. All this is helped by the Schütz Ticket Service, which ensures the return of used IBCs.
In addition, a new automated three-layer blow-moulding machine is used to produce new inner bottles, which are fitted into reconditioned cages and returned to the market as Recobulk IBCs.
Schütz notes that the site, which is certified according to ISO 14001 and OHSAS 18001, is also the only facility in Brazil so far to be authorised by the country’s environmental authorities to recycle unrinsed, contaminated agrochemical packaging. Another part of its operations is to produce F1 RECO tight-head drums, manufactured from 100 per cent recycled materials. This too has been recognised by the Brazilian National Institute of Metrology, Standardisation and Industrial Quality as complying with national regulations and safety standards.
THE RIGHT PACKAGING The investment allows Schütz Vasitex to pool its most important reconditioning and recycling activities, expand its capacities for sustainable packaging and increase flexibility and supply security for its customers in one of South America’s most important industrial regions. The reconditioning plant also complements production of new IBCs, plastics drums and canisters at the Schütz Vasitex headquarters, located some 3 km away.
“The investment in this comprehensive plant expansion in Brazil is in line with our strategy of responding to the current requirements of customers from a wide range of industries around the world,” says Schütz. “Schütz Vasitex offers the right packaging solution for every application. The company supplies the markets with its comprehensive product portfolio of IBCs, drums and a wide range of different types of canisters.
“As an added bonus: Schütz Ticket Service unites the advantages of a manufacturer-led, environmentally friendly collection system for empty containers and their subsequent processing in state-of-the-art facilities.”
DOUBLE WALLS Schütz has also been working on improving the safety of its IBCs used in the food supply chain, adding an integrated liner that ensures maximum purity; this is also suitable for industrial users who have particular cleanliness and hygiene requirements. The new ‘Dualprotect’ system is used in the Ecobulk IBC to complement the Foodcert and Cleancert labels.
Liners are pre-installed at the factory and IBCs are UN-approved for use with dangerous goods. The liner is welded to the container’s outlet valve and consists of a high-quality LDPE film that includes an ethylene vinyl
SCHÜTZ IS INVESTING HEAVILY IN NEW
alcohol (EVOH) permeation barrier. Used in conjunction with the standard inner bottle, this provides double leakage protection. Together with an additional mantle, the filling product is almost hermetically sealed, effectively preventing a skin from forming on the product and removing the need for a nitrogen blanket. For use in the food, pharmaceutical and personal care sectors, the liner and outlet valve can be gammaradiated for additional hygiene protection.
Liners are adapted for specific filling products and applications. The IBCs can be filled via the outlet valve, eliminating the need for a large top opening, or through the top opening using a special hose attached to the liner. In such cases, a filling lance is not necessarily required.
If necessary, the liner can be replaced by the user. Schütz has produced an extensive video to help with this process, as well as to explain the other novel features in the design, available at www.schuetz.net/instructions.
When removing the liner from below through the outlet opening, the outlet valve should be closed. The liner can then be pulled out together with the valve, which is welded to it. If the liner is being removed from the top, the outlet valve and adapter flange must first be pulled out of the IBC slightly and the liner sealed with a cable tie. This prevents product leakage when the foil is cut between the valve and the cable tie. The IBC is then tilted backwards and the liner is pulled out through the filling opening.
In keeping with Schütz’s commitment to sustainability, these new Dualprotect IBCs can be returned through the Schütz Ticket Service for environmentally friendly reconditioning after use. www.schuetz.net
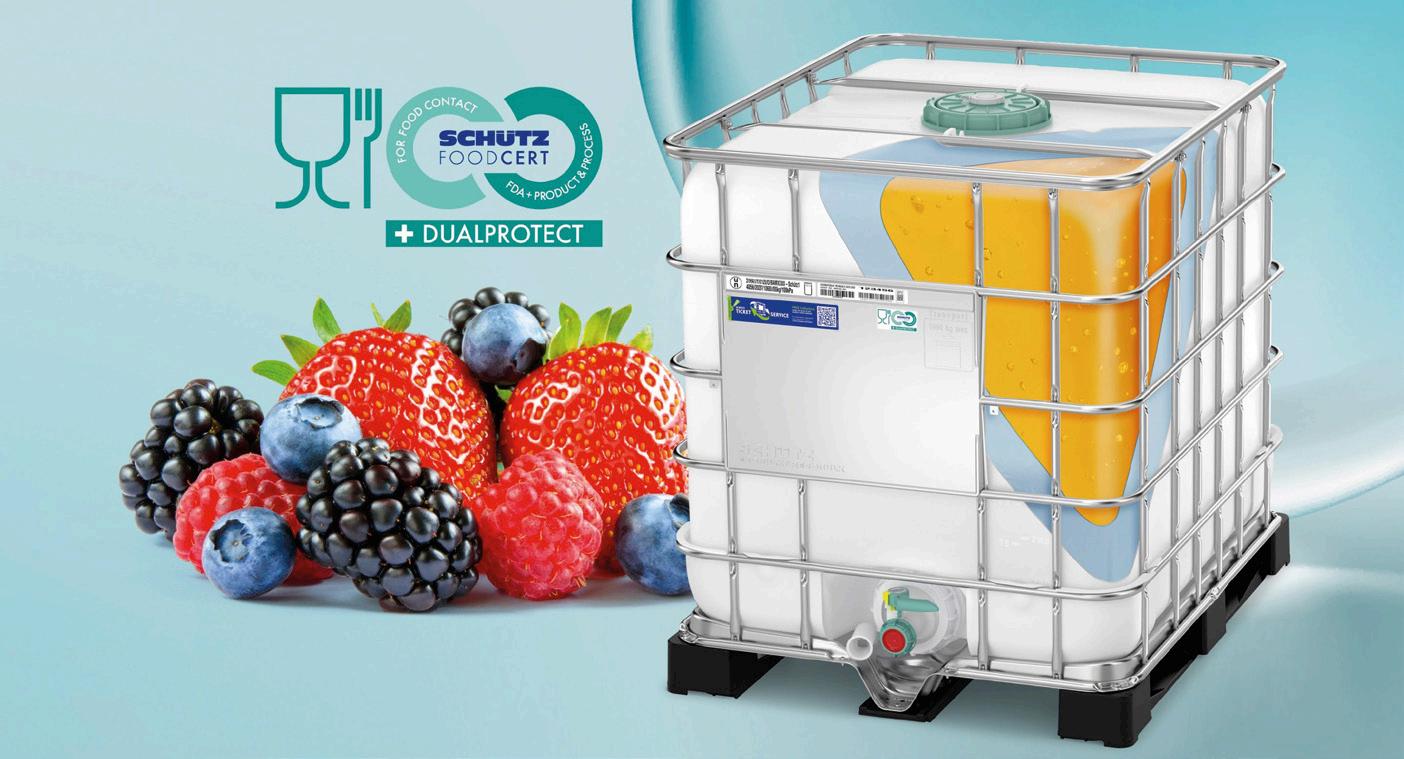
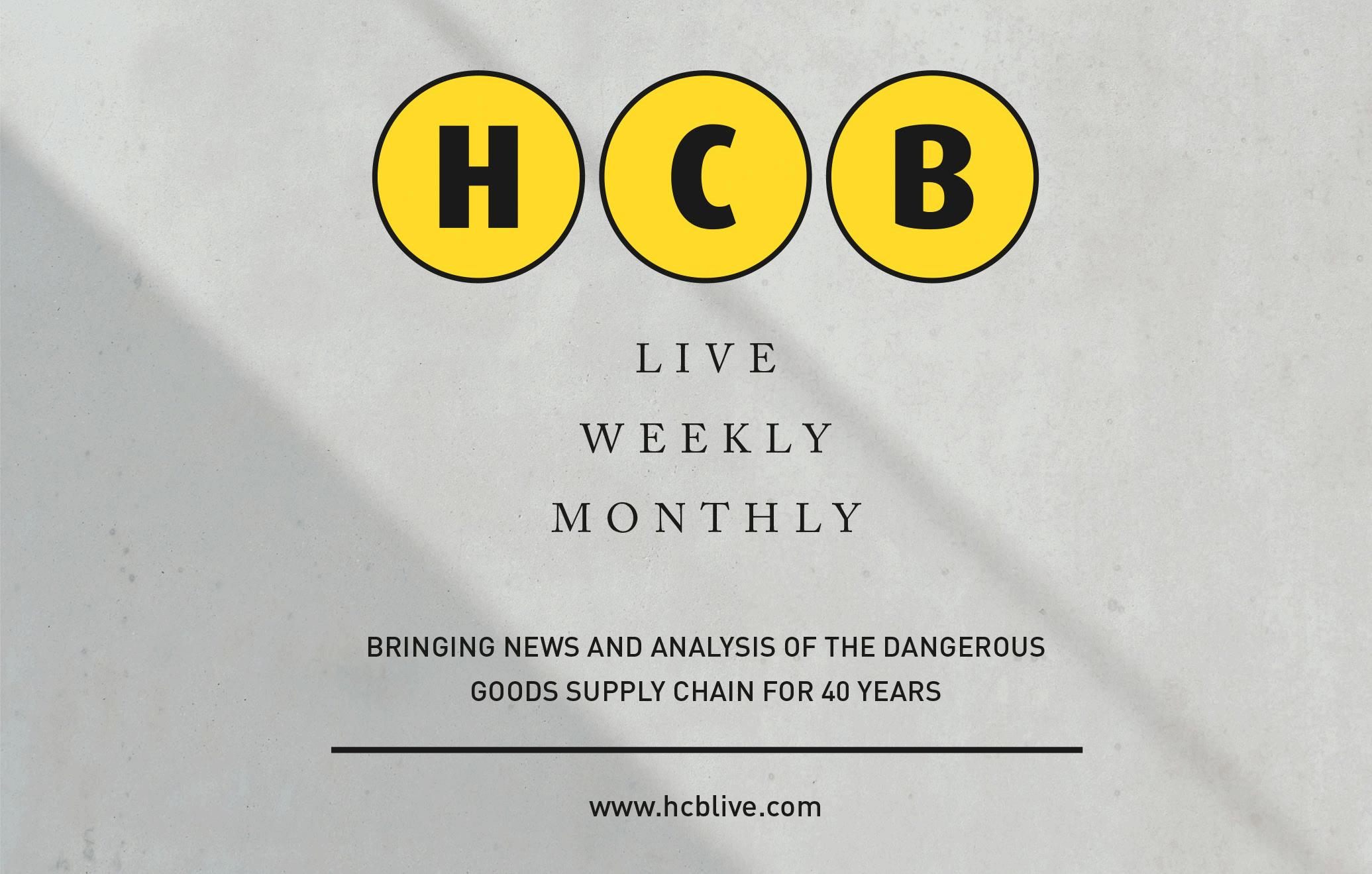
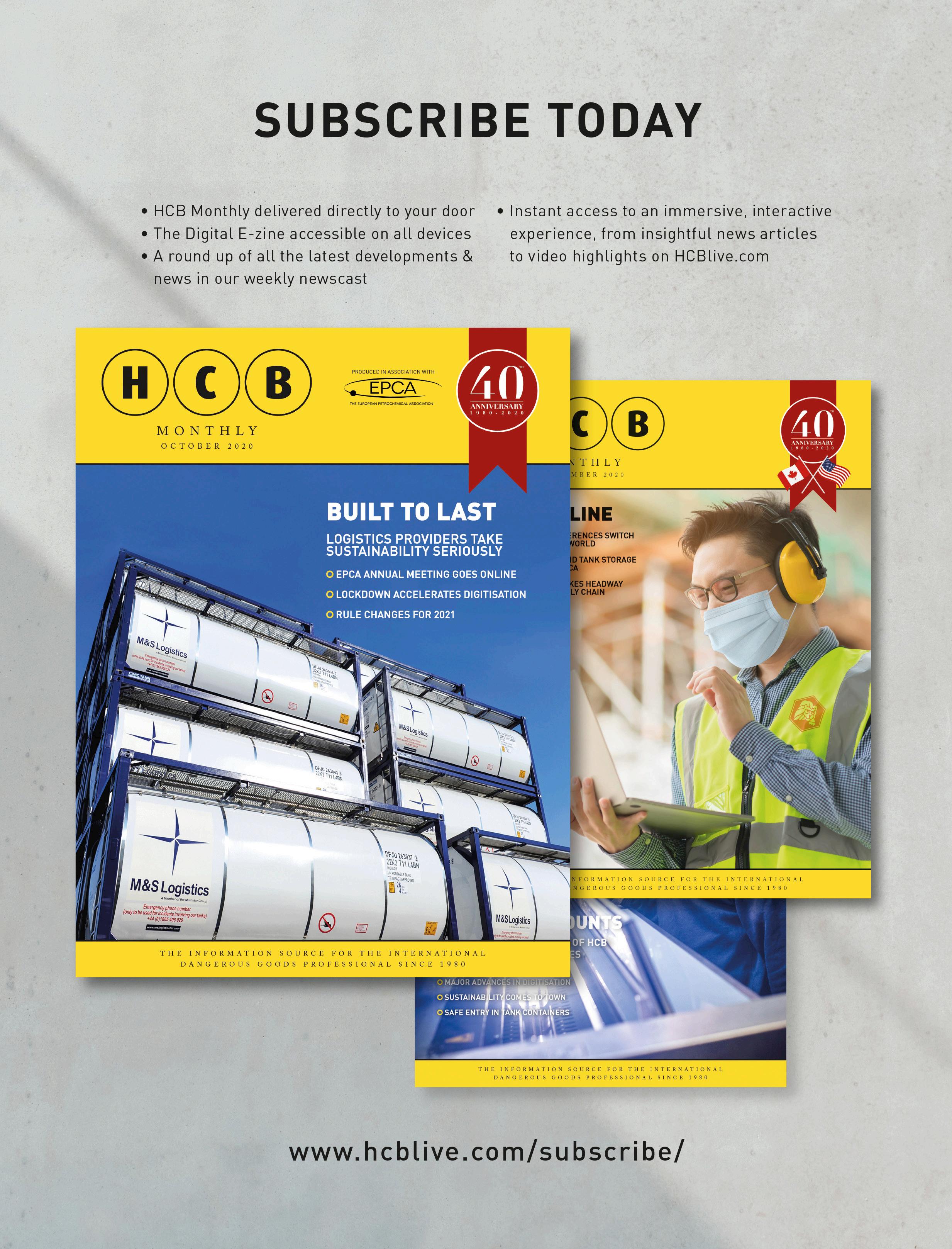