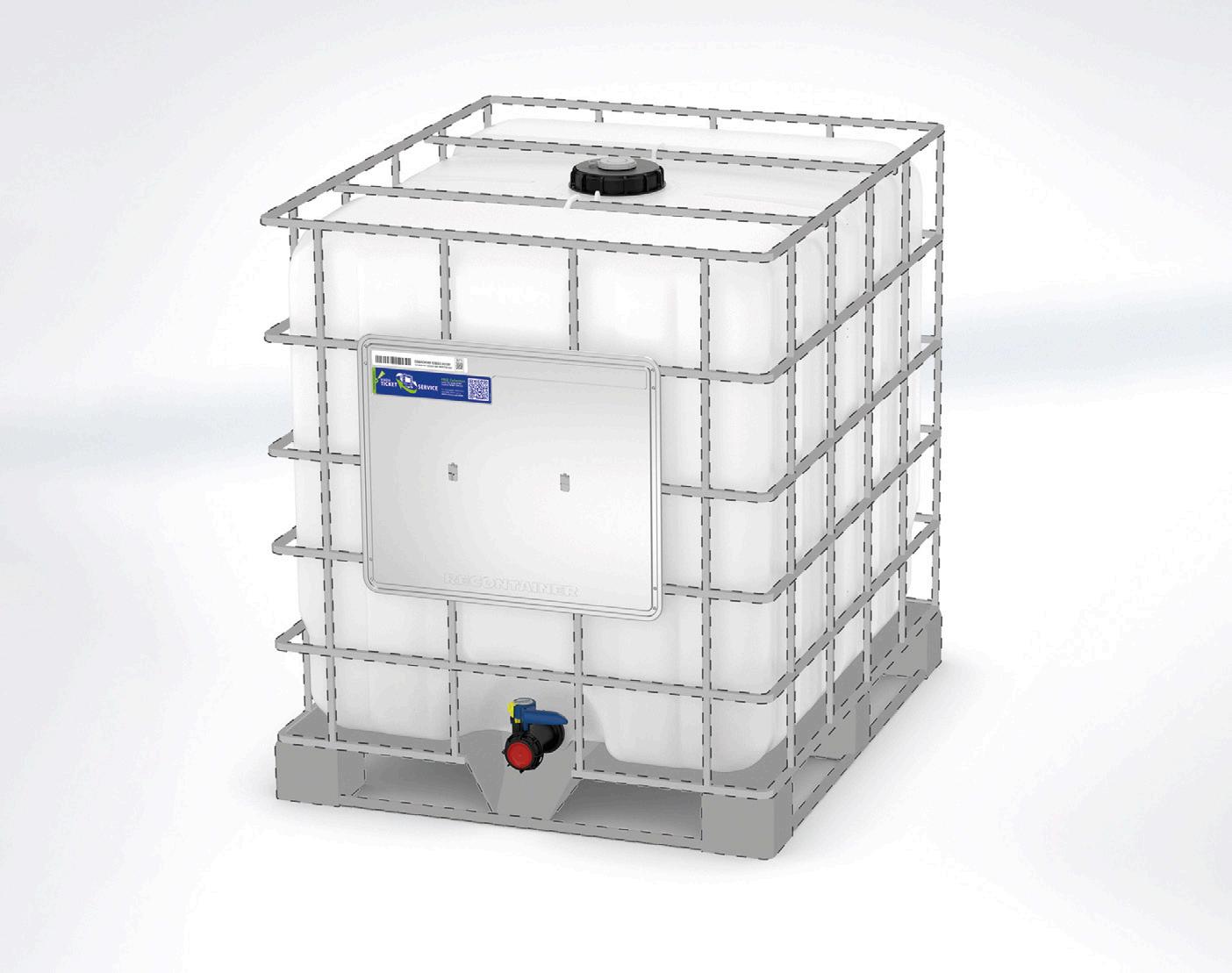
2 minute read
Cross-bottling reconditioning from Schütz
JUST THE TICKET
RECONDITIONING • EXPANDING THE NUMBER OF IBCS THAT CAN BE RECONDITIONED THROUGH CROSS-BOTTLING WILL LEAD TO SUSTAINABILITY GAINS FOR THEIR USERS, SAYS SCHÜTZ
GERMANY-BASED INDUSTRIAL packaging giant Schütz has introduced a new reconditioning service for composite intermediate bulk containers (IBCs) – Recontainer – that allows for cross-bottling. A specially designed replacement inner bottle can fit the frame of any manufacturer’s IBC, meaning that many more IBCs can be reconditioned.
Schütz was one of the pioneers of global IBC reconditioning, first offering the service in 1976 and then in 1980 introducing a fully equipped circular system to collect its used IBCs for return to its 50 production and
SCHÜTZ HAS FOUND A WAY TO RECONDITION THIRD-
PARTY IBCS TO PRODUCE RECOBULK UNITS TO THE
SAME SPECIFICATION AS THOSE MADE FROM ITS service locations around the globe. This Schütz Ticket Service guarantees worldwide collection and has become the largest producer-owned network for the collection and reconditioning of emptied IBCs.
Collected IBCs are fitted with original inner bottles and components produced in a globally standardised, eco-friendly process. The resulting Recobulk IBC is a fully compatible version of the original Ecobulk unit with the same standard specification.
Taking this concept a step further with Recontainer means that cross-bottling of IBCs from other manufacturers also meets the same standards.
HOW IT WORKS Just as with the reconditioning of its own IBCs, the Recontainer process starts with an evaluation of each used IBC, particularly with regard to the last product carried. Schütz has developed a comprehensive database with more than 200,000 evaluated filling products, which it keeps constantly updated. Any residues are removed and properly disposed of. The old inner bottle is removed and recycled in an internal system that generates high-quality HDPE recyclate, which is then used to produce plastic components such as corner protectors and plastics pallets for the remanufactured IBCs.
The grid cage of the old IBC is extensively cleaned and, if necessary, repaired and then fitted with a new universal Schütz inner bottle. This specially developed inner bottle has been technically adapted to fit into the cages of numerous IBC models on the market.
Furthermore, the Recontainer is equipped with a new label plate, which again has been optimised to fit the different grid cages; adhesive residues from old labels are unavoidable on the old label plates when they are only cleaned during the reconditioning process. Further components such as screw caps and discharge valves are replaced with new original parts during the inner bottle replacement process.
“Customers that use the Recontainer can rely on Schütz’s proven standards when using this packaging for their valuable filling products,” Schütz states. “The IBCs are delivered as a single-type standard specification. At the same time Schütz is contributing to the conservation of natural resources through the eco-friendly reconditioning of IBCs from other producers.”
In Covid-19-related news, Schütz has stepped in to help BASF in its ‘Helping Hands’ project to supply hand sanitiser free of charge to hospitals in the Rhein-Neckar region of Germany, supplying every second IBC for the project free of charge. BASF had not produced sanitiser at its Ludwigshafen plant before but had the necessary know-how and some of the raw materials needed. Schütz supplied IBCs meeting the latest safety requirements for sensitive hygiene products and has upped production at its Selters headquarters with additional weekend shifts. The IBCs are collected free of charge from end users by the Schütz Ticket Service and recycled internally as part of the sustainable reconditioning process. www.schuetz.net