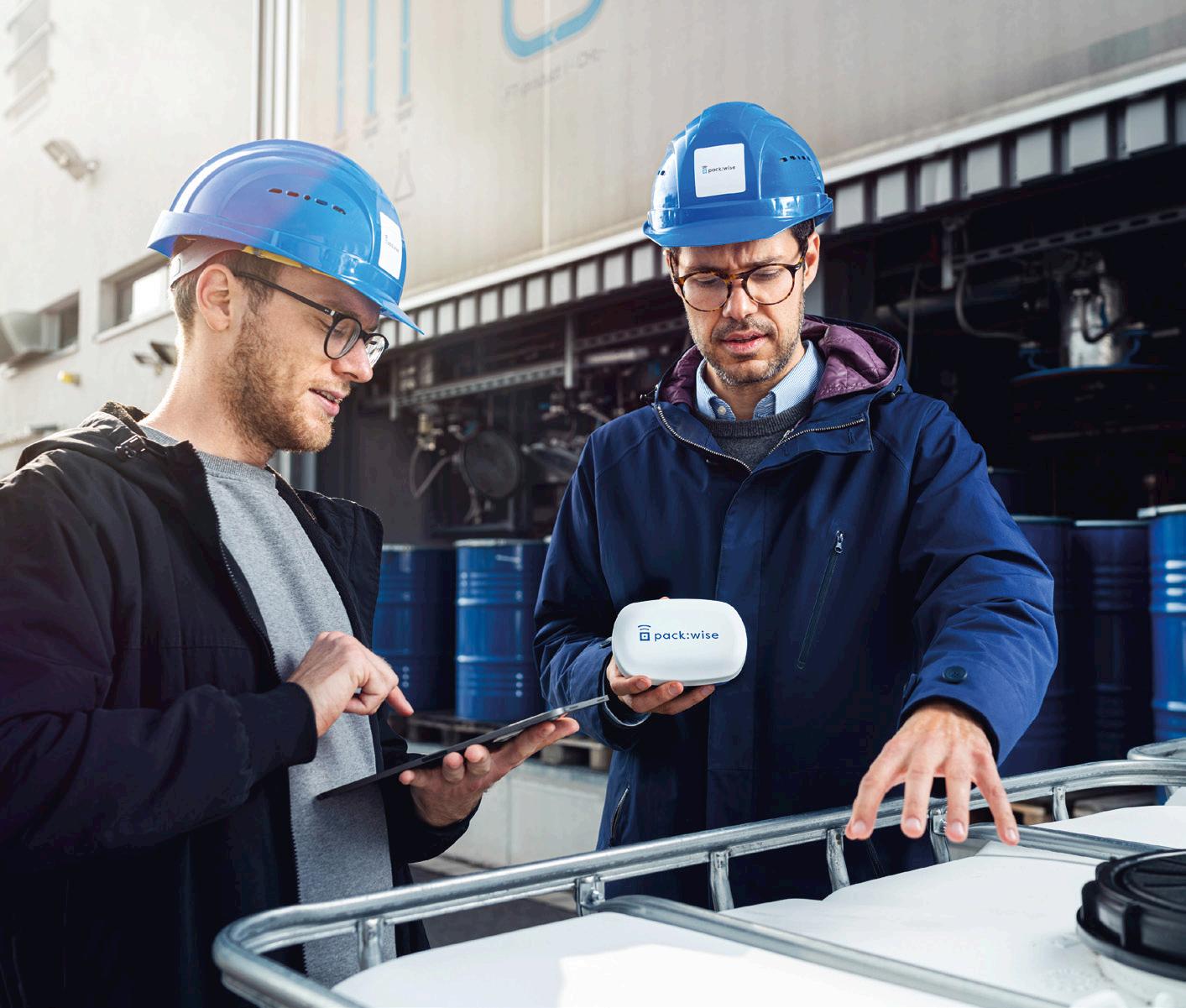
2 minute read
Packwise trials Smart Cap for IBCs
THE CAP FITS
TRACKING • OPTIMISING IBC UTILISATION THROUGH THE APPLICATION OF DIGITAL SYSTEMS HAS COME A STEP CLOSER NOW THAT PACKWISE IS STARTING TRIALS OF ITS SMART CAP
AFTER THREE YEARS of development, Packwise has started trials of its Smart Cap for intermediate bulk containers (IBCs). It has recruited 25 IBC users across Europe to test the device over the next five months, anticipating full-scale production starting in January 2021.
The new hand-sized device is designed to cut costs, improve efficiency and enhance safety and environmental performance for users in the chemical, food and logistics sectors. It provides users with track-andtrace capabilities, automatic re-ordering, automated damage notifications and theft protection by means of a digital alarm. This improves demand forecasting and best-before-date surveillance and helps avoid cross-contamination.
Gesche Weger, CEO of the Dresden-based startup, explains what this means for industry: “There are an estimated 10m IBCs in Germany alone and up to 300m across the globe, meaning the impact of improved logistical capabilities will be huge for the chemical, liquid, and food industries, plus a great benefit for the environment.”
“Smart Cap users are able to increase service levels to their customers because fill levels and overall stock can be observed, monitored and replenished in line with demands while benefitting from optimised distribution and recovery routes,” Weger continues.
HOW IT DOES IT Smart Cap technology reduces the number of IBCs lost in the supply chain, reducing the
THE PACKWISE SMART CAP OFFERS A CLEVER need for more IBC production – a carbonintensive process – while also optimising the logistics chain and thereby saving fuel, storage and idle unit costs.
“Our Smart Cap technology enables businesses to enhance pay-per-consumption business models and makes the whole chain far more transparent by creating a digital twin,” says René Bernhardt, chief technology officer at Packwise. “We have been able to reduce the administrative burden with a greatly improved communication system that can be tailored to each business.”
The container and product data for each user, generated by the sensor in the Smart Cap, is encrypted and transmitted to the Packwise Flow web application where it can be analysed, set to trigger notifications and alarms, and interfaced with existing ERP systems. It creates a digital twin of an IBC showing high-precision sensor data in real time. The platform tells users quickly about any deviation from set parameters and provides calls for action. It visualises and automates processes for various applications in the supply chain.
The Smart Cap can be easily mounted to any type of composite or metal IBC and, once attached, is ready for use to monitor fill level, location, temperature and movement. Once the IBC comes to the end of its life, the Smart Cap can be removed and attached to a new container. The Smart Cap has a battery with a five-year guaranteed life if set at a daily transmission interval.
The initial trial involves 25 businesses in the chemical production, chemical logstics and food logistics sectors in Germany, Switzerland, Austria, the Netherlands and the UK. Packwise envisages beginning production of tens of thousands of Smart Caps in the first half of next year. packwise.de