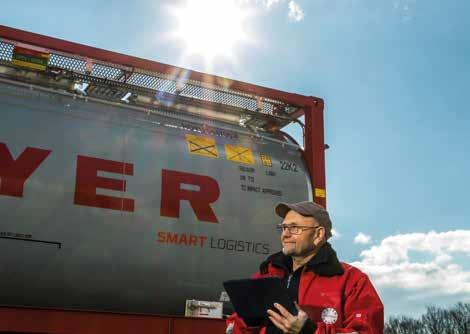
4 minute read
Hoyer rolls out smart tanks
from HCB October 2019
SENSOR SENSIBILITY
DIGITISATION • HOYER CONTINUES TO ROLL OUT THE SMART TANK CONCEPT ACROSS ITS FLEET, AND IS ALSO FOCUSING ON REDUCING THE ENVIRONMENTAL IMPACT OF ITS TRANSPORT OPERATIONS
IT WAS IN May 2017 that Hoyer began digitising its tank container fleet, launching the Smart Tank concept in response to client expectations and the growing availability of the appropriate technology. Rolling out the Smart Tank concept across the Hoyer tank container fleet, which currently numbers 40,347 tanks, has been a massive task but the company reports that more than a third – some 15,000 – tanks are now equipped.
Hoyer describes the digital transformation of its fleet as “the centrepiece of the intelligently networked logistics management”. The sensors fitted to the tank containers continuously measure important set parameters, with information and warning systems and its own online portal ensuring optimum load monitoring and a variety of analysis options.
“We are happy to announce that more than 15,000 tanks are equipped smart already,” says Stephanie Burtscher, communications manager at Hoyer. “Our plan is to equip further tank containers until the end the year. By the end of 2019 we aim to have fitted approximately 22,000 containers.”
One issue for Hoyer is the challenge of updating a fleet of this size, operating around the world. However, Burtscher explains, the fitting of the sensors is taking place at more than 30 locations worldwide. “The majority of the equipping is being undertaken internally by Cotac,” she says. It is expected to take up to three years to finish the task.
GET YOUR DATA HERE The technology being installed includes a sensor that will be attached to the heating conductor to accurately measure the heating or cooling system temperature, a sensor determining location via GPS and GSM, a non-intrusive sensor to measure product temperature and a sensor for measuring pressure. “Furthermore,” Burtscher adds, “we are working on the ability to measure the filling level inside the tank.”
Additionally, the sensors can be adjusted accordingly to suit clients, meaning critical upper or lower violation limit triggers can be altered depending on a tank’s contents. If this is not the first time that a particular cargo has been in transport to a particular destination, the data collected on previous journeys can be used to optimise logistic processes.
Data collected by the sensors can be seen – almost in real time – through Smart Portal, which has been optimised for both desktop and mobile devices and can be mapped in the customer’s own IT system via interfaces. One of the main benefits of Smart Portal is that it simplifies operational monitoring and control of logistics processes, ultimately eliminating the need to manually create and update complex summary tables.
“Smart technology reports deviations in critical load values, thus guaranteeing even greater safety, security and product quality from loading to discharge,” says Burtscher. “With our technology we focus on controlling the products in order to ensure safety and quality. In combination with information and warning systems and its online portal, Smart Tank ensures optimum control of load and predictive analysis options.”
With the addition of Smart Portal, fleet management has attained a new level that includes detailed information about fleet status. Accurate documentation of idle or turnaround times can be used to increase the fleet’s utilisation rate and avoid empty repositioning. Smart Tank and Smart Portal can therefore make logistics not only more cost-efficient but also more environmentally friendly.
Burtscher concludes by saying: “Smart Logistics is the future-oriented continuation of our quest for transparency, reliability, quality, safety and security in a dynamic market and competition.”
LESS IS MORE Continuing on the theme of environmentally friendly developments, Hoyer has enlarged its fleet with a number of LNG- and CNG-fuelled vehicles. Hoyer currently operates seven CNG-
fuelled vehicles and the two new LNG-fuelled vehicles will assist attaining emission targets of reducing CO2 by 25 per cent per tonne/km by 2020. The new vehicles produce 15 per cent less CO2 and 60 per cent less nitrogen oxides, offer drastic noise reduction and use 15 per cent less fuel than a comparative diesel counterpart, even those with Euro 6 low-emission engines that currently make up 96 per cent of the trucks used by Hoyer in Germany.
“As experts in transporting gases liquefied under pressure and cryogenically, we ensure gases of all kinds are transported safely and smoothly on a daily basis,” says Thomas Hüttemann, managing director of Hoyer’s Gaslog business unit. “The growing LNG market has an especially positive effect on the balance sheet of our business. Not only transporting these alternative energy sources but also driving with them ourselves immediately was therefore a logical consequence for us.”
Hoyer is also investigating using electrically powered cars to reduce its environmental impact. However, the market does not yet offer any adequate solutions for heavy trucks of the kind required by Hoyer. Furthermore, the fact that a service station network for alternative energies equipped to handle these vehicles is not yet available in many countries represents an additional obstacle. HCB www.hoyer-group.com
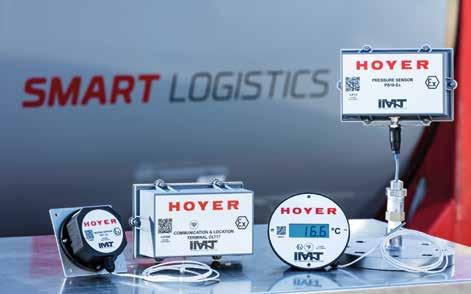
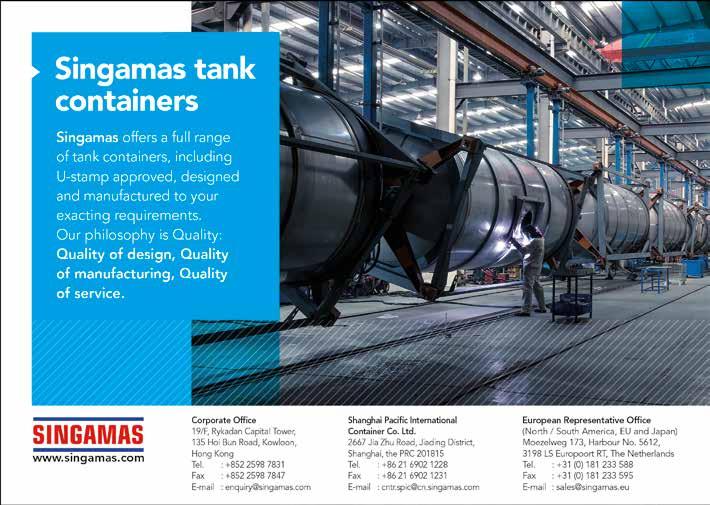