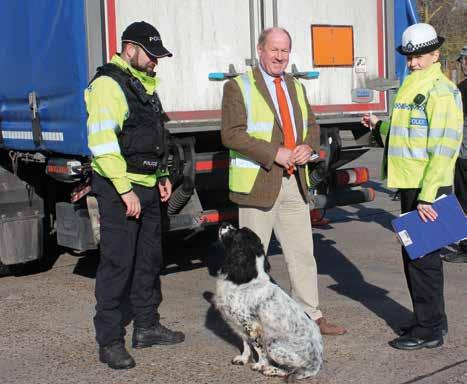
12 minute read
Same enforcement issues at VCA
from HCB October 2019
PLUS ÇA CHANGE
CONFERENCE REPORT • VCA KEEPS THE UK AND IRISH DG COMMUNITY UP TO DATE WITH DEVELOPMENTS BUT THIS YEAR’S SEMINAR HAD SOME DEPRESSINGLY FAMILIAR STORIES TO TELL
THE ANNUAL DANGEROUS goods seminar organised by the Vehicle Certification Agency (VCA) on behalf of the UK Department for Transport (DfT), provides an excellent opportunity for dangerous goods safety advisers (DGSAs), trainers and others involved in compliance with the transport regulations to hear about the latest and upcoming changes to those rules. It also helps to highlight issues with compliance and enforcement, as well as external issues that are impacting the business.
So it was, then, that at this year’s 34th annual VCA Dangerous Goods Seminar, held at the Daventry Court Hotel this past 4 and 5 June, delegates were treated to the usual updates on UK, European and international regulations from an expert panel of speakers, including a number from DfT’s Dangerous Goods Division, as detailed in the first part of this report on the event (HCB September 2019, page 56).
It was apparent to regular delegates that DfT has not only hired a new team of younger people to take the Division forward, but also that the leadership are more than happy to give them their head when it comes to representing the UK at international fora and to present the results of those meetings to attendees at the VCA seminar.
WORDS FROM THE OLDIES Bearing in mind the arrival of some newer faces among both regulators and the regulated, HCB’s editor-in-chief Peter Mackay gave a lively presentation, outlining his belief that, as older members of the dangerous goods community retire or die off, it is important that the lessons that have been learned the hard way over the past decades are not forgotten.
Readers who follow Peter’s weekly video presentations will be aware of this conversation, which at the VCA seminar covered such events as the explosion aboard the chemical tanker Stolt Valor, the process mishaps at Flixborough and Seveso in the 1970s, the horrific road tanker explosion outside the Los Alfaques campsite near Tarragona, and of course the fire aboard the containership MSC Flaminia in 2012. In each case, someone made a decision that led to loss of life, whether to save time or money or due to ignorance or the willingness to take a chance. Peter quoted Warren Buffett, saying: “It’s good to learn from your mistakes; it’s better to learn from other people’s mistakes.”
Bringing things back closer to home, Phil Lapczuk, operations enforcement manager at the Driver and Vehicle Standards Agency (DVSA), gave his regular update on roadside enforcement activity, which is just one element of the Agency’s remit to improve safety for all road users. DVSA inspects around 1 per cent of all dangerous goods vehicles; in the year to end March 2019 that amounted to 1,715 vehicles, of which 581 inspections revealed infringements of the regulations, leading to 384 prohibitions.
Load securing is a big issue “and not going away,” Phil said, just has he has done over and over again. What has changed is that DVSA now has the power to levy on-the-spot fines. But most prohibitions are driver-related and again the situation has not improved. Why is this? Is training adequate? Does it deliver competence? DVSA is now considering the introduction of fines for intervention, something that the Health & Safety Executive already has at its disposal.
EYES IN THE SKIES Continuing with the theme of enforcement, Keith White, acting head of VCA’s Dangerous Goods Office, summarised the situation in airfreight. There had been a significant reduction in incidents and events over the past 50 or so years, he said, but that trend has now levelled out; further improvements will need a new approach.
The UK Civil Aviation Authority (CAA) is working on improving its ability to manage oversight of safety risks and to allocate resources to those areas with the greatest potential to enhance safety, and to increase the effectiveness of its safety regulation activities and projects. The aim of the work is to establish a system of performance-based oversight and regulation, although there are concerns about the ability of CAA to undertake the work given its apparent lack of resources.
Terry Harvey, a police officer with the Suffolk Constabulary and, since late 2018, chair of the National Carriage of Dangerous Goods Practitioners Forum, explained what the Forum does and the role of the police in enforcing the transport regulations. Across the UK there are two national check weeks each year, when every police area concentrates on looking at vehicles carrying dangerous goods; police officers trained specifically in dangerous goods regulations also conduct random checks throughout the year. Each police area should have a DGSA to oversee activities and to provide assistance and advice; the level of training currently varies but the Forum has created a national training package to help ensure standards are maintained nationally.
As with Phil Lapczuk’s presentation, it was somewhat depressing to hear from Terry that the main problems police come across are the same old issues: fire extinguishers that are inaccessible, empty or out of date; old or inadequate instructions in writing; inaccurate documentation; and missing vehicle equipment or personal protective equipment. Terry also showed some images that illustrated the often creative ways hauliers use to display orange-coloured plates.
BOXED IN Another attention-grabbing presentation came from Kevin Dougherty, director of operations at Air Sea Containers, one of the event’s sponsors, who began by pointing out that “you can pull someone off the street and have them packaging dangerous goods for air transport in three days”. His presentation sought to convince the audience that three days of training is not enough to explain the intricacies of the regulations for the proper packaging of dangerous goods, particularly in light of the statistic he quoted that 70 per cent of shipments in 4GV boxes are not properly prepared.
Kevin gave delegates a thorough explanation of what the UN packaging mark means, how packagings are tested and what the test report says. He pointed them towards the text just above the signature at the bottom of the test report, which says: “The use of packaging methods, components, materials or dimensions other than those specified herein shall invalidate any approval based on these tests.”
What this means is that any packaging, such as a 4GV box, used to transport dangerous goods must be in exactly the form it was in when it was tested; this includes inner containers and methods of closure. There are, though, some exceptions to this. Some outer packagings/large packagings have been successfully tested using different types of inner packaging, which provides some flexibility; in addition, fewer inner packagings may be used, providing that sufficient cushioning is used to fill the void space; further, alternative inner packagings may be used, providing they are of equivalent or smaller size and made of a material of equal or greater strength, or have smaller openings.
Users need to be careful, though. Kevin described some common misconceptions that can lead to invalidation of the test: users cannot remove the buffer partitions, use alternative cushioning material, change the tape or taping method, or exceed the weight capacity.
Packaging manufacturers also have responsibilities under the regulations. In particular, paragraph 6.1.1.5 in the UN Model Regulations states: “Manufacturers and subsequent distributors of UN packagings shall provide information regarding procedures to be followed to prepare packages before shipment.”
Air Sea Containers is taking proactive steps to make sure its packagings are used properly. Kevin explained a new programme: Stop Know Do. This urges users to Stop before they buy packagings and make sure they Know what their requirements are under the various transport obligations. Air Sea Containers is also adding QR codes to all its packagings, providing easy access to assembly and closure instructions.
BACK TO BATTERIES A number of other presentations at the VCA seminar offered advice and pointers to staying »
REGULATORS ARE STRUGGLING TO CONTINUE TO
IMPROVE THE SAFETY RECORD IN AIR CARGO TRANSPORT
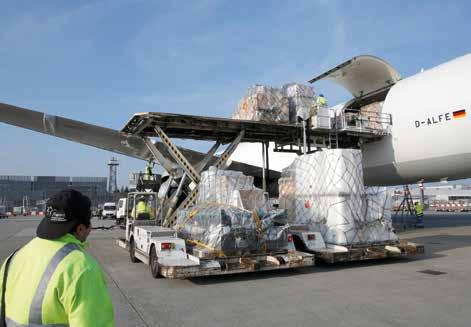
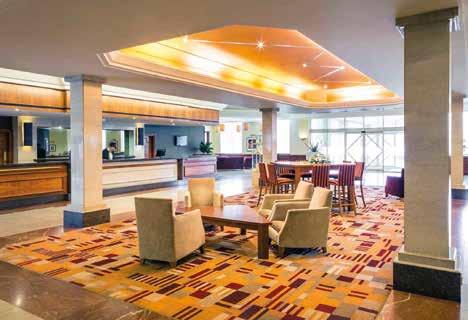
in compliance and away from accidents. Alex McCulloch, dangerous goods manager at UPS International and a member of the International Air Transport Association’s (IATA) Dangerous Goods Board (DGB), provided an insight into how UPS is dealing with the threats posed by lithium batteries in airfreight.
UPS has decided to use fire-resistant unit load devices (ULDs), manufactured from fibre-reinforced plastics panels that are able to withstand fires at temperatures of 650˚C for at least four hours. This gives aircrew sufficient time to get safely down on the ground. UPS began deploying these ULDs in 2015 and now has some 18,000 in use out of a total ULD inventory of more than 42,000 units. The rest are due to be replaced as soon as possible.
Alex reported that ULD manufacturers are continuing to improve their units in areas such as fire detection and suppression. UPS’s own tests demonstrate that these fireresistant ULDs can mitigate gas build-up and contain a lithium battery fire. The latest ULDs being deployed are lighter and stronger than earlier models.
UPS has also used fibreglass blankets as fire-resistant covers for palletised cargo. These are similarly designed and tested to withstand fires for at least four hours.
UPS has taken a broad approach to the lithium battery threat. Since 2017 all shipments of lithium batteries under UN 3480 or 3090 must move as fully regulated; this provides visibility of all shipments within the UPS system. It has put in place programmes to formalise the relationship with small package shippers and for shippers of lithium metal batteries. Shipments are segregated aboard aircraft to prevent propagation of any fire to combustible material.
Alex had plenty of advice for shippers. Make sure you know the regulations and ensure your people are trained; observe the 30 per cent state of charge for UN 3480 shipments; and keep up to date, as the rules change frequently. Shippers should beware of counterfeit batteries and confirm the UN 38.3 test reports. And use the IATA guidance document on lithium batteries, which is freely available on the IATA website.
Sticking with lithium batteries, Keith White returned to the podium at the end of the seminar to bring the story up to the present day. He noted that there are two active work streams: the work by SAE International at the behest of the International Civil Aviation Organisation (ICAO) to develop a performancebased packaging standard to support the safe shipment of lithium batteries as cargo on aircraft, and an intersessional working group of the UN Sub-committee of Experts that is attempting to refine the classification of lithium batteries along hazard-based lines.
SAE started work in 2015 with the aim of completing the project in 2016 but, three years on, it has still not been finished. Keith said he felt the membership of the project team was too wide, which has taken up time and has also resulted in vested interests having a say. There are still plenty of questions to be answered and thus it has been hard to get a draft text on which to vote. The next meeting of the SAE group was due to take place in July, with little hope of a resolution.
The UN intersessional working group has made more progress and will be hoping to finalise a text during the current regulatory
TOP: THE DAVENTRY COURT HOTEL PLAYS ANNUAL HOST TO

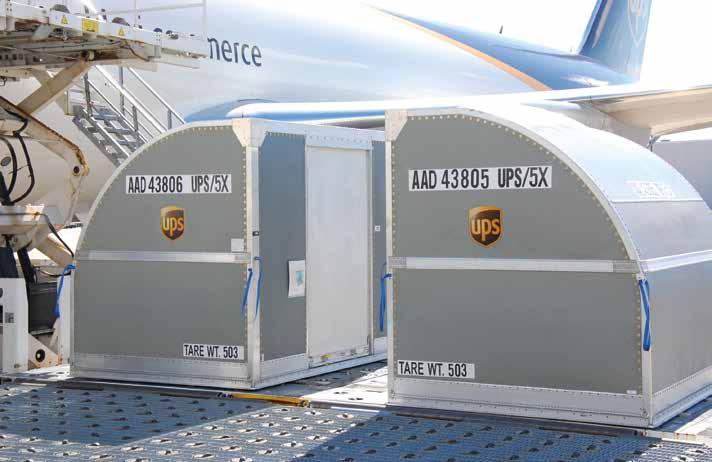
biennium (i.e. by December 2020). It has already discussed the use of packaging as mitigation in the event of a lithium battery incident, and a way of classifying batteries in division, similar to the approach used for Class 1 explosives. The UK had submitted proposals to the UN Sub-committee for its July 2019 session that sought to add tests to Chapters 6.1 and 6.6 of the Model Regulations for articles that may evolve excessive heat during transport – this would apply to oxygen generators as well as lithium batteries – to ensure that packagings used for such articles are able to contain the effects of a heating event without loss of structural integrity and without flames propagating outside the packaging.
LET’S GET ONLINE Also speaking about air transport was Paul Horner, formerly with IATA but now director of Dangerous Goods Safety Group (UK), who discussed the move from paper to digital processes in the sector. The current documentation process is linear and complex and, given the availability of reliable tools, it seems sensible to move to digital platforms, he said. IATA has already moved into the space, developing an electronic dangerous goods declaration (e-DGD) that has been avidly adopted by airlines.
The digital platform supporting e-DGD allows all parties to a shipment to have visibility of the necessary documentation; this includes the shipper and consignee, any freight forwarder, the airline involved, ground handling agents and any transit airports. Paul’s presentation was eagerly received by the audience, who were excited by the development.
Also speaking on the topic of digitisation was Munmohan Malli, strategic business manager of the Frameworks and Engagement Team in DfT’s Dangerous Goods Division, who explained what was happening with the European Telematics Working Group set up to look at the use of e-documents in terms of the transport of dangerous goods. So far the work has been led by Germany, France and Italy, he noted, and these countries have run some pilot projects. A broader pilot project is planned for the third quarter.
The European plan expects a voluntary system that will provide a live e-document that will show only what is on a vehicle at any point, which will certainly be of use in milkround deliveries. It will also give authorities more visibility over what’s being carried on their roads.
There was some confusion among the audience as to who will benefit from this idea, with many of the opinion that business is doing very well and going ahead with implementing its own digitised telematics systems.
The other presentation of note came from Ziyad Akhlaq from DfT, who had drawn the short straw and was asked to explain what Brexit will mean for the dangerous goods sector. But, as things have moved on a lot since then, his words are now obsolete. Perhaps next year’s VCA Dangerous Goods Seminar will be able to give a definitive answer – or perhaps not. It will be worth keeping an eye on the VCA website - www.vehicle-certification-agency.gov.uk – for all the latest. HCB