
5 minute read
News bulletin – industrial packaging
from HCB October 2019
NEWS BULLETIN
INDUSTRIAL PACKAGING
SCHÜTZ IMPROVES NORWEGIAN FACILITY
The Schütz plant in Kongsvinger, Norway, some 100 km north-east of Oslo, has finished its latest expansion and modernisation. The production of plastic components has been concentrated and expanded in a newly built 1,200-m2 hall (above). In addition to the preexisting extrusion blow moulding system, a new three-shift layer extrusion blow moulding system has been installed, and inner container production is linked to IBC assembly via new, fully-automated conveyor technology.
Production of plastics pallets has also been relocated to the new hall meaning plastics production is now all under a single roof. The Nordic nations are a vitally important market for Schütz, and have been since its inception, according to Veit Enders, Business Unit Manager EMEA Schütz. The company is now the largest reconditioner of industrial packagings in the region, with the company stating: “The competence displayed by Schütz in reprocessing containers and reusing recovered plastics is a key component of the company’s sustainability strategy.” www.schuetz-packaging.net
GOOD FOR GREIF
Greif’s third quarter results indicate a strong increase compared to the same period in 2018, largely thanks to the Caraustar acquisition, but some sectors have weakened. During the latest quarter, net sales increased by $240.5m to $1.25bn and gross profit increased by $62.3m to $279.4m. Adjusted EBITDA rose by roughly 39 per cent versus the same period in 2018 to $203.8m.
“Greif produced solid third quarter 2019 results despite ongoing market softness and a weakening industrial economy,” says Pete Watson, Greif’s president/CEO. “Third quarter adjusted EBITDA rose by roughly 39 per cent versus the prior year quarter. Our newly acquired Caraustar operations performed better than our original assumptions. However, we faced weaker market demand in our containerboard operations and in certain segments of our rigid industrial packaging business.
“In light of external headwinds, we are implementing additional optimisation measures in parts of our portfolio to lower costs and better navigate challenging market conditions,” Watson adds. “We remain laser-focused on those areas within our control to more profitability serve our customers. I remain highly confident in our long-term plan to drive more sustainable free cash flow, deliver our balance sheet and grow our profits.”
Greif has been working on rebranding nearly 90 former Caraustar facilities in Canada and the US since its acquisition in February 2019. The facilities added to the Greif roster operate within one of four specific units: recycling services, mill group (coated and uncoated paperboard and specialty paperboard products), industrial products group (tubes and cores, construction products, protective packaging, adhesives) and consumer packaging (folding cartons, set-up boxes, packaging services). Greif now has nearly 300 facilities across 43 nations.
In other news, Greif’s GCUBE® with Shield barrier technology is now available throughout North America. Users receive improved product stability, shelf life and operational performance across a range of industries. The innermost layer remains 100 per cent highdensity polyethylene (HDPE), the intermediate layer contains the Shield blend, which reduces the permeation of gases, and the external layer can be customised with colours or antistatic.
Shield technology, introduced last year, is proven to be more efficient than offsite fluorination and is currently the only barrier technology available that is fully recyclable, Greif says. www.greif.com
PROCESSING PESTICIDES
HDPE plastic pesticide containers will now be processed through Mauser Packaging Solutions’ Reidsville, North Carolina facility. The Ag Container Recycling Council (ACRC) certification was granted following a site review to ensure the council’s stringent guidelines for handling and recycling recovered HDPE containers were met.
The Ag Container Recycling Council is a not-for-profit organisation founded in 1992.
The Council promotes and supports programmes in the US related to the collection and recycling of used agricultural crop protection, animal health and specialty pest control product containers. More than 190,000,000 pounds (86m tonnes) of plastics have been recycled through the Council’s recycling programme since its founding. The resulting recycled resin can be used in specific, approved end products such as drain pipes, highway sign posts and utility conduit.
“This certification supports our continued commitment to reducing the amount of waste sent to landfills,” says Jen Kienen, Mauser Packaging director, PCR division. “We continue to look for new ways to close the packaging lifecycle loop and give raw materials a second life.” www.mauserpackaging.com
BERLIN INTO EUROPE
Berlin Packaging has acquired Vincap & Adolfse, a specialist supplier of food and beverage closures and pharmaceutical packaging serving customers in northern Europe from its base in Utrecht, the Netherlands. Vincap & Adolfse will be integrated into Berlin’s Bruni Glass division, based in Milan, Italy.
Paul Devilee and Joost Wurth, owners of Vincap & Adolfse, say they are “excited to become part of the Berlin Packaging family and to embrace our new Bruni Glass colleagues”. www.berlinpackaging.com
CHANGING FORM
Germany-based Jokey Group has decided to change the legal form of its parent plants in Wipperfürth and Gummersbach from a GmbH to a Societas Europaea (SE). The move does not entail any change in the shareholder structure of head office location.
The SE Board of Directors consists of Herbert Kemmerich, chairman and CEO, Ralf Kemmerich, deputy chairman and COO, and Dr Peter Köhler. The SE’s managing directors – CEO Jens Stadter, COO Ralf Kemmerich, CFO Peter Dörmbach and CSO Christof Kölschbach – are responsible for the operative business.
Jokey currently has 15 plants in 12 countries. In addition to its Germany sites, Jokey also has facilities in France, Poland, the Czech Republic, Turkey, Serbia, Belarus and Russia. www.jokey.com
CONSOLIDATING STAVIG
Stavig Group has formed the largest independent manufacturer, reconditioner and recycler of rigid packagings in the US, through the centralisation of support for its four independent packaging solution brands - Myers Container, Container Management Services, General Steel Drum and North Coast Container – under the Stavig Group name.
All current brands will remain in place after the process is complete but will now be connected by the Stavig Group brand to promote to its customers a long-term vision and reliable, redundant capabilities.
Stavig Group, now under its fourth generation of family ownership (below), says it is is creating a sophisticated growth platform for its customers. Stavig Group takes a lifecycle approach to industrial packaging solutions and promotes a strong commitment to continuous improvement and sustainability across all companies. staviggroup.com
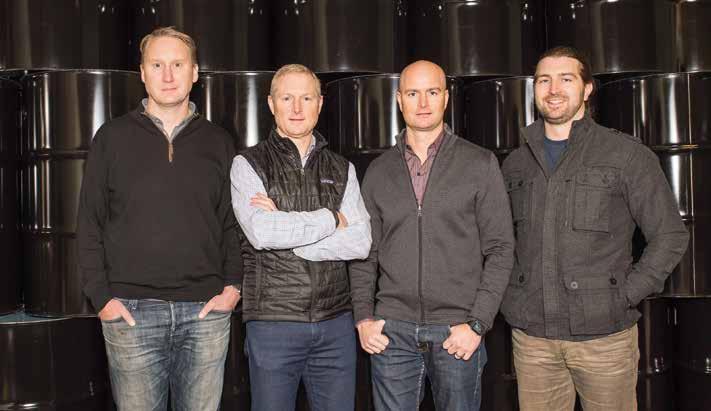