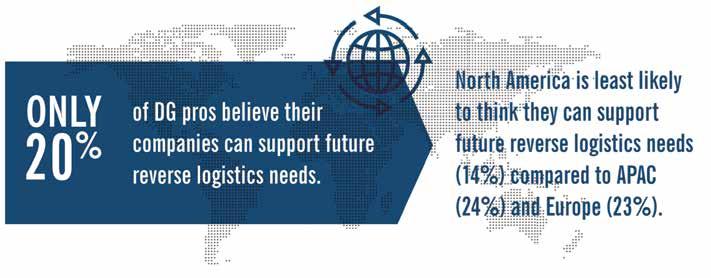
6 minute read
Labelmaster survey identifies gaps
from HCB October 2019
FIXING A HOLE
SURVEY • UNDERSTANDING THE GAPS THAT EXIST IN A COMPANY’S DG SUPPLY CHAIN IS THE FIRST STEP TO BEING ABLE TO PLUG THEM, SAYS LABELMASTER VICE-PRESIDENT ROB FINN
THE GROWTH OF e-commerce, coupled with the supply chain evolution, has made moving dangerous goods (DG) in a safe and compliant manner more important than ever. Unfortunately, several key gaps exist within organisations’ processes and infrastructure that make maintaining a reliable hazmat supply chain challenging.
This much was evident in the report of the 2019 Global Dangerous Goods Confidence Outlook survey, conducted by Labelmaster, IATA and HCB to gain insights into how organisations around the world approach DG shipping and handling, and the challenges they face.
The results found that DG professionals continue to find compliance challenging and time-consuming, and desire additional support from their companies in order to better ensure compliance, support future operational needs and gain greater business value from the supply chain. Overall, budget constraints, lack of adequate technology, lack of seniorlevel executive risk awareness, and resource constraints all contribute to this sentiment.
LACKING IN CONFIDENCE The supply chain has a great impact on an organisation’s overall business performance and managing DG safely and compliantly as part of the supply chain adds a greater level of complexity. Given this, how do DG pros feel about the value of their supply chains?
According to the 2019 survey, two-thirds of respondents have confidence that the investment their company makes to support DG compliance can meet current needs; however, 21 per cent said that it does not meet current needs and only 13 per cent believe their current investment can support future needs.
The lack of confidence many DG pros have in their organisation’s supply chain is partly the result of specific gaps within their operations and infrastructure, and partly due to specific gaps within the global hazmat supply chain itself.
The continued growth of e-commerce has brought with it challenges for companies, including increased reverse logistics activity. In fact, independent research suggests that 30 per cent of products ordered online are returned.
This onslaught of return deliveries – both consumers returning to stores and stores returning to manufacturers and distributors – has created a challenging reverse logistics environment. And it is compounded by the fact that many products being purchased and returned online contain hazardous components, such as lithium batteries, medical devices, laptops, varnishes, paints, cosmetics and other items.
Unfortunately, many DG pros are not confident in their organisation’s ability to manage this process. Overall, only one in five DG pros believes their company can support future reverse logistics needs, with those in North America the least confident (14 per cent), compared to 24 per cent in Asia-Pacific and 23 per cent in Europe.
Developing a strong reverse logistics process for hazardous products requires a thoughtful, proactive approach. This begins with a clear understanding of how reverse
THE 2019 DG CONFIDENCE OUTLOOK SURVEY REVEALED
SOME TELLING DIFFERENCES IN THE ABILITY OF DG
PROFESSIONALS TO DO THEIR JOB, GIVEN THE LEVEL
OF SUPPORT THEY RECIEVE AND THE TECHNOLOGY
logistics and returns impact the supply chain and the overall health of the company. It then extends to identifying the impact that a mismanaged process could have on customer perception and brand reputation, followed by a determination of more streamlined ways to marry efficiency with safety in order to achieve positive change.
CLARITY OF THOUGHT The supply chain is becoming increasingly data-driven, making access to and communication of timely and accurate master data imperative. Unfortunately, data accuracy, completeness and reliability remain challenging for DG pros. This is reflected in both the centralised data stored and communicated across companies’ supply chains, and in the data quality and accuracy they receive from upstream supply chain partners.
One key reason for organisations’ inability to achieve data collection and transparency is the use of limited and disparate technology across the supply chain. While technology has continued to advance and is critical to the supply chain, more than half of DG pros – 55 per cent - still rely on manual processes for shipping DG. Manual processes are wrought with inefficiencies, including the inability to validate shipments against the latest regulations, and an overall slowing of shipping time.
But simply using technology is not a guaranteed fix for DG management and compliance challenges. In many cases, DG pros believe that using their company’s existing systems, such as ERP and WMS, are not particularly effective or relevant in terms of DG functionality.
Technology can significantly improve the efficiency, accuracy and compliance of shipping dangerous goods. But every company is different, so it’s not a ‘one size fits all’ approach. It’s about using the right technology and getting the most out of it.
DG shippers need to understand the functionality of their systems, know how these systems integrate into the DG supply chain, and then identify gaps in their infrastructure and processes. This will help improve compliance while providing greater transparency, both internally and with supply chain partners.
MIND THE GAPS While some supply chain issues have to do with internal process or infrastructure gaps, others have to do with the risk associated with partners. In fact, 71 per cent of survey respondents wish their supply chain partners were as compliant as their own company.
While this often comes as a result of the manufacturers, retailers or distributors they do business with not having adequate resources or training to handle and ship DG properly, in some cases this comes about as a result of risk transfer with carriers.
In fact, 42 per cent of survey respondents agree that the carelessness with which carriers handle or transport DG is a significant problem for their business, though this sentiment varies based according to region, with those in North America (30 per cent) and Europe (41 per cent) less likely to suffer compared to their counterparts in Asia Pacific (58 per cent), Africa and Middle East (53 per cent) or South America (80 per cent).
Although DG pros feel that their carriers share part of the responsibility for hazmat supply chain gaps, they also point to regulators for the complexities of hazmat supply chain management. When asked, “If you had the opportunity to influence regulatory bodies who define the DG shipping rules, which of these ideas would you be most in favor of?”, half of respondents indicated “develop one core set of requirements that are common to all regulatory bodies and then have annexes for all modes” as their top choice.
THREE TRIBES In order to successfully navigate an increasingly complex and dynamic hazmat supply chain landscape, organisations need to overcome these supply chain gaps. Unfortunately, this can be extremely difficult as many companies lack the resources and processes required to meet current supply chain needs, and few have the budget and infrastructure necessary to address future requirements.
Labelmaster identified three distinct groups based on attitudes and behavioral responses revealed in this year’s survey – basically compliant, safely compliant and competitively compliant – with each facing unique challenges. The group an organisation falls into based on its attitude toward, and approach to, compliance directly impacts the level of confidence a DG pro has in ensuring enterprise-wide compliance.
Regardless of which type of organisation they work for, DG pros still desire more resources in order to increase DG confidence and deliver real business value. However, the specific gaps that need to be addressed, and how they influence management into providing additional support, varies.
Understanding which group fits their company can help DG pros develop a practical framework for prioritising resource needs and making compliance a competitive advantage that drives revenue, improves supply chain performance, reduces risk and enables better customer service.
To learn more about these groups, the gaps that exist within the DG supply chain and ideas for how to improve DG compliance within your organisation, download the full report at www. labelmaster.com/dg-confidence-outlook/. HCB
