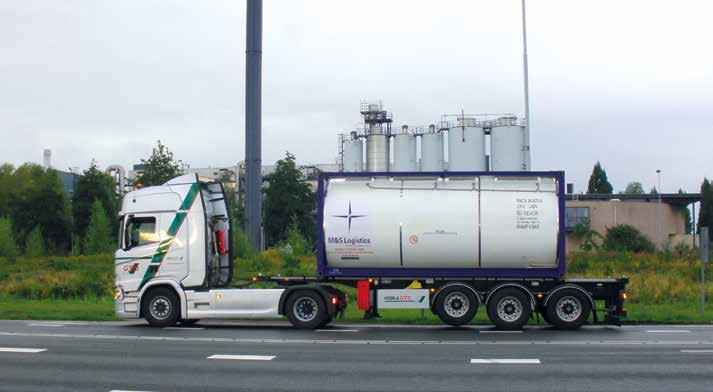
4 minute read
M&S’s view of the market
from HCB October 2019
STATE OF PLAY
BUSINESS • IN HIS REGULAR ANNUAL REVIEW OF THE TANK CONTAINER SECTOR, DAVID KEW OF M&S LOGISTICS REPORTS ON SOME THREATS TO SAFETY AND SECURITY
THE PAST YEAR has highlighted some unwelcome trends in the global tank container industry, a sector that has become increasingly important in the worldwide trade in liquid chemicals but one that is as open to external risk as any other. Its customers search for ever greater cost reductions and alternatives, while macroeconomic and geopolitical machinations make it ever harder for tank container operators to plan for continued business success.
Recent expansion of the tank container fleet has been founded at least in part by low prices for newbuild tanks offered by manufacturers in China. But that has its downside. “There has been an increase in the number of start-up logistic service providers who, having got their hands on some tank containers, start operating without consideration of proper procedures or a regard for the safety of the operations, never mind the acquiring of sufficient and fit for purpose insurance,” says David Kew, managing director of M&S Logistics.
That has had a knock-on effect, with existing players in the market having to cut costs to compete. “Even among established providers, there has been cost cutting where technology is used to reduce human overheads, resulting in a loss of expertise in handling hazardous cargoes.”
FEEL THE SQUEEZE On a broader basis, the current global market conditions have been putting pressure on margins both for chemical manufacturers and their logistics service providers (LSPs). “Unfortunately, the last decade has seen this at the cost of safety and integrity of the supply chain,” Kew says. “This downward pressure has led to some producers and suppliers cutting corners. We have seen an increase in the mis-declaration of cargoes and in some cases a reduction in the inclusion of inhibitors and stabilisers.”
That loss of expertise, already pinpointed by other voices in the tank container sector, puts the excellent safety reputation of tank container at risk. There has already been a reported increase in the number of cases where pitting corrosion has affected the internal surfaces of tanks – which, being made of stainless steel, are impervious to most forms of corrosion.
But more significantly, there have been some high-profile containership fires, not least the MSC Flaminia incident in 2012, which is thought to have been caused by the improper handling of divinyl benzene. Kew also points to a number of others, including those involving the containerships Eugen Maersk (2013), Hansa Brandenburg (2013), APL Austria (2017), MSC Daniela (2017) and
Maersk Honam (2018), in which fires broke out due to the improper handling of improperly declared dangerous goods.
One outcome of these incidents has been greater regulation, most recently the imposition of new restrictions and provisions for the carriage of polymerising substances, including special provision 386 in Amendment 38-16 of the International Maritime Dangerous Goods (IMDG) Code.
BIN THE BAG Kew is keen to stress the environmental credentials of tank containers, especially in contrast to other, competing methods of moving liquids in bulk. In a world where there is a growing momentum towards the circular economy’s mantra of ‘re-use, recycle, remanufacture’, a stainless steel tank with more than 20 years’ worth of life in it avoids many of the issues that apply to short-life or single-use packagings.
What’s more, tank containers have been shown to be highly resistant to damage. Even during the disastrous explosion and fire in the port of Tianjin in 2015, tanks that were caught up in the incident kept their integrity, despite serious damage to the frame and cladding. The chemicals in those tanks were ruined by the high temperatures, but they did not leak.
That level of performance is in sharp contrast to the flexitank, which has become increasingly popular for the movement of nonhazardous goods. But these are merely large plastic bags, most of which are incinerated or sent to landfill after a single trip and suffer regularly from leaks in transit. “With the state of the environment and the global push to reduce single use plastics,” says Kew, “the question has to be asked if the perceived savings are worth it?”
Kew is adamant that chemical shippers and their LSPs should not be derailed by financial headwinds. “While there is a need to build more sustainable partnerships both from a safety and environmental standpoint, we know global growth is slow and we’re heading for still more tough times,” he says.
“While margins remain under pressure and we all continue to strive for reduced costs, we would do well to remember the words of the English writer and economic mind, John Ruskin: ‘The common law of Business Balance prohibits paying a little and getting a lot. If you deal with the lowest bidder, it is well to add something for the risk you run, and if you do that you will have enough to pay for something better’.” HCB www.mslogisticsltd.com
PROPERLY LOOKED AFTER AND OPERATED, TANK
CONTAINERS OFFER THE SAFEST AND MOST COST-
EFFECTIVE MEANS OF MOVING LIQUID CHEMICALS IN BULK
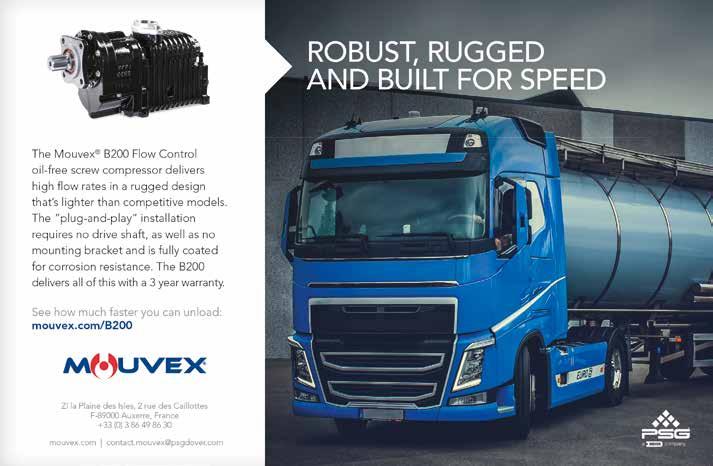