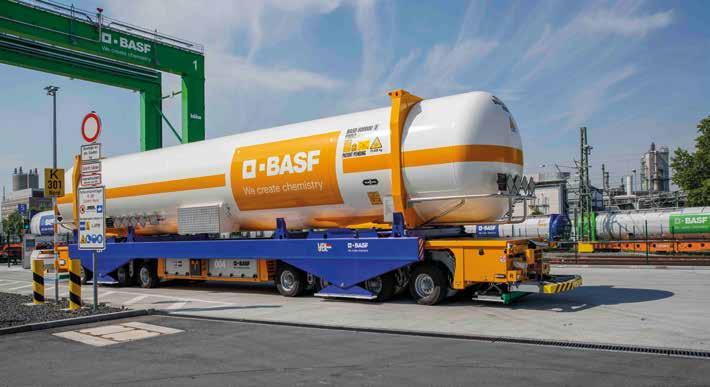
8 minute read
Van Hool’s jumbo tanks for BASF
from HCB October 2019
BIGGER IS BETTER
DESIGN • JOINT WORK BY VAN HOOL AND BASF TO DEVELOP LARGE TANK CONTAINERS FOR IN-PLANT AND RAIL APPLICATIONS IS CONTINUING AND MOVING FROM LIQUIDS TO GAS TRANSPORT
BELGIAN TANK CONTAINER specialist Van Hool is in the final throes of developing a 52foot tank container capable of handling a wide range of gases. The work is the latest element in a multi-year project that began with the realisation by BASF that in-plant logistics at its massive Ludwigshafen chemical production site in Germany were constrained by the reliance on rail tanks to move product from the main rail terminal around the plant to various loading/unloading points.
It was quickly realised that the simple action of decoupling the tank from the bogie would remove much of the inefficiency being experienced. However, BASF could not give up the size advantage of rail tanks and needed something much larger than any tank container yet built.
“The design began two or three years ago at the BASF Ludwigshafen factory, based on liquid tankers,” explains Kris Dobbelaere, sales and business developer at Van Hool. “BASF found there was a lot of inefficiency surrounding internal transport with the existing rail tank cars.” Separating the tank from the bogie not only removed that inefficiency but also opened up new possibilities for tank design and construction, bogie design (including the use of autonomous vehicles) and the use of the tanks for product storage.
“The tank containers are built in cooperation with BASF, but initially began as a new logistics concept formed by BASF and we were asked to take part i n a joint development. There is a joint patent on the design of the tank container,” Dobbelaere says. TO FIT THE FRAME To meet the needs of the Ludwigshafen site, the initial work concentrated on tanks for liquids and only more recently has moved on to the more specific challenges posed by a tank for pressurised gases, although the basic design parameters remain the same. BASF needed to replicate the tank car in terms of its size and maximum gross weight (75 tonnes), but to do so in the form of a tank container that could be removed from the bogie and be stacked six high.
“With these parameters in place, we were able to begin designing the tanks and the frames that could gain approval for ADR/ RID and more,” says Dobbelaere. The newly developed gas tanks are based on those same principles but are adapted in order to handle eight specific gases moved at Ludwigshafen. “Although the products did not need a working pressure above 10 bar, for safety reasons we decided to design a 27-bar tank. This provides extended possibilities for the future,” says Dobbelaere.
Although the design was inspired by the in-plant needs at Ludwigshafen, BASF quickly started to think about how the new tanks could be used to move product between plants, which raised a whole new »
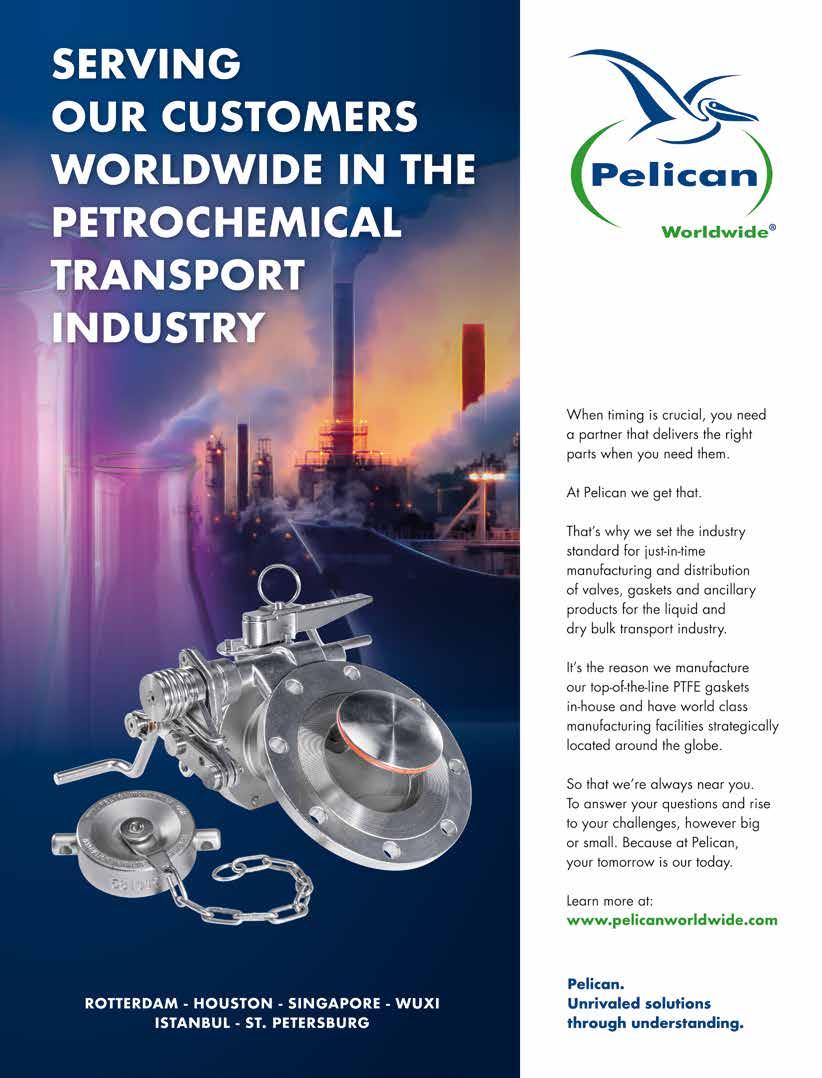
set of considerations. “During the process another limitation was having to achieve the G1 Profile to ensure safe passage through bridges, tunnels and other structures,” adds Frank Bolte of Van Hool’s commercial sales department. “The tanks can be built to other specifications [outside of G1], but they will then be limited to the rails they are able to use.”
WITHIN THE RULES Dobbelaere explains some of the engineering challenges Van Hool faced in the development of the new BASF-class tanks: “The frame design is very specific to be able to cope with the increased weights when considering the stacking ability from a static point of view, but also from a dynamic point of view when thinking about the daily operations on rail. There were several designs for the new frame that drew on our decades of experience in building for rail. The design that satisfied the parameters best was then built and thoroughly tested.
“The process involved in designing and approving a new tank container takes years before actually becoming traffic,” Dobbelaere continues. “Fortunately, as international legislation surrounding tank containers is very clearly explained, therefore, within those limitations, it speeds up optimising and modifying designs. The question of designing the new gas container was brought to us at the end of 2018 and the first prototype was present during the Transport Logistic fair in Munich [June 2019].
“We have planned the designs for dangerous goods within the existing regulations,” continues Dobbelaere. This has had an impact on the equipment of the tanks as the provisions in RID for rail tank cars differ from those for demountable tanks. “There was close cooperation with the authorities on this project so every party will learn and further develop from this, possibly leading to changes in regulations,” he says.
The sheer size of the tanks means that there is little potential for them to be used on the road, although they may be moved empty by road in order to get to maintenance or cleaning depots. They are also moved by road within the Ludwigshafen site and Van Hool designed a skeletal to move empty tanks. “BASF has also decided to have an automated guided vehicle that is able to handle these tanks,” says Dobbelaere. “We have extra safety features added to provide more stability for the vehicles when considering on-site movements.”
“It is possible for the tanks to be carried by road via the skeletals, but it’s not the core aim as there is a maximum allowed weight,” adds Dobbelaere. “There is no use in using a tank this large with only 20 m3 of product in it; that removes the advantage it was designed for.”
FINDING A MARKET These new tank designs do not stand in isolation. Their size limits their applicability to large-volume product flows, which means they are not suitable for supplying end users. Rather, they are designed for in-plant logistics, storage and B2B business within the chemical sector. The advantage of the new system is that no significant investment will be needed to handle the new tanks. For example, reach stackers able to handle 75-tonne containers are available in the market.
“Chemical companies like BASF and logistics frontrunners see the advantages of the new system compared to conventional rail tank cars. They are already building up a new intermodal network with terminals in Antwerp, Hamm, Ludwigshafen, Schwarzheide and Tarragona able to handle 75-tonne containers – a new segment in intermodal traffic across Europe has been born and is growing,” says Dobbelaere.
Van Hool believes that the financial savings offered by the new equipment will far outweigh the level of investment needed and that it will prove to be cost-effective. “The main purpose of this type of equipment is to improve and change the rail logistics related to tank transport, specifically for the big flows of chemical commodities,” says Dobbelaere. The new tanks will increase flexibility and the speed of loading and unloading compared to using rail tank cars, and it is the users of such tank cars that will be the target audience for the new tanks.
However, convincing what is a rather conservative industry of the benefits of change may not be so straightforward. “During the first presentation of the liquid tank containers of this style [in 2017], the very conservative rail market was sceptical,” recalls Dobbelaere. “Within the last two years, we have seen a big change in vision and mentality towards the products. Whereas the majority were sceptical two years ago, ideas are now being created where these tanks will have their applications.”
Despite the warmer reception in recent months, Bolte explains: “The drawback is that this concept will only work if the infrastructure is available. This could take some time.”
“However, we also received a lot of queries from port authorities about how this type of equipment can be developed further,” adds Dobbelaere. “There have also been conversations with a wider range of businesses about how they can adapt facilities to handle things such as cleaning and so on.”
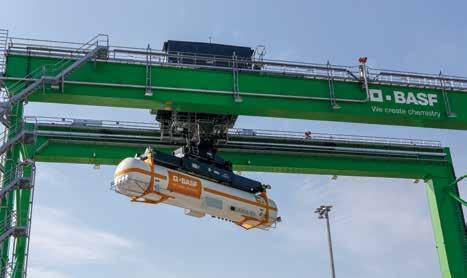
There is clearly interest in this equipment, it just requires planning and, perhaps, a couple of larger businesses to take the first steps.
“We’re looking at facilities across Europe,” says Bolte. “In the future, eastern European facilities would be well suited for transport into Russia, China and Asia and vice versa. Additionally, one of the challenges being examined for future possibilities is combining this particular traffic flow with deep sea traffic.”
“Although this equipment is called a ‘container’, we aren’t really focusing on the container market itself,” concludes Dobbelaere. “This is more about the development of rail tank cars, which is the market we are aiming to tackle. There are further developments in the pipeline for this series of projects, but we cannot say more. This type of development is only experienced perhaps once every five years, so it is of great importance, particularly as it is a new design. It’s rare to have this form of project as it’s not just the development of one specific item, but the whole package around it, making it far more complex.”
The gas tank container is currently receiving the final approvals and terminals are finalising infrastructure alterations to be able to start using them soon, perhaps even within the WORK BY BASF AND VAN HOOL HAS CREATED A WHOLE next six months. HCB NEW CONCEPT FOR MOVING LIQUIDS AND GASES www.vanhool.be
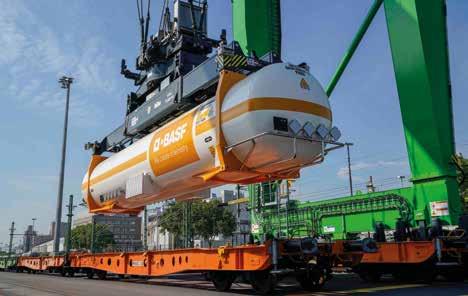

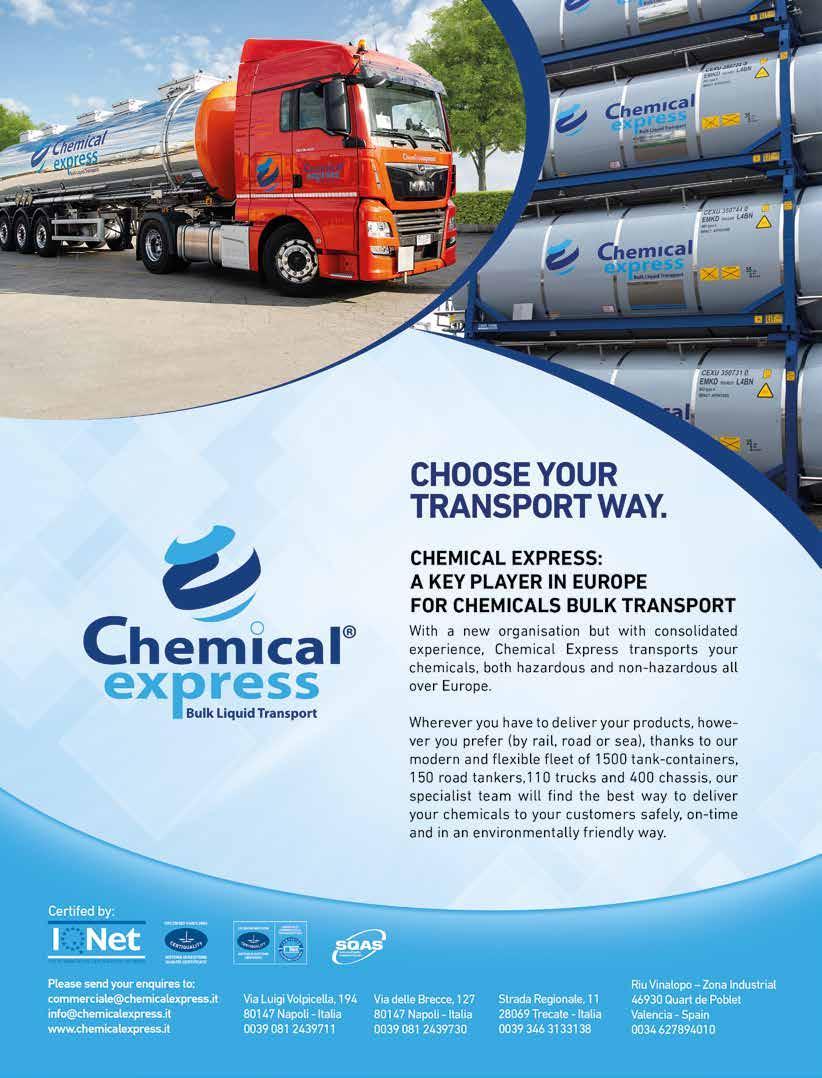