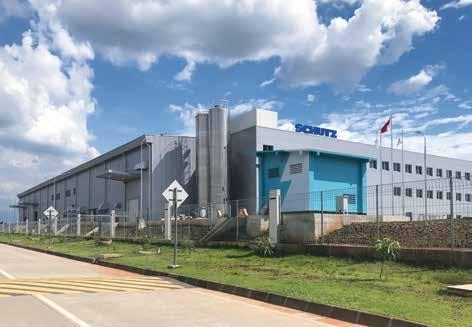
2 minute read
Schütz adds to capabilities
from HCB October 2019
PERFECTING PRODUCTION
MANUFACTURING • SCHÜTZ CONTINUES TO EXPAND AND UPGRADE ITS SITES AROUND THE GLOBE TO COPE WITH INCREASING DEMAND FOR STEEL DRUMS AND IBCS
GLOBAL INDUSTRIAL PACKAGING giant Schütz has had a presence in Indonesia since 2005, starting with a small sales office in Jakarta before opening its first Indonesian production plant in Karawang in 2013. This past June, Schütz opened a new, high-tech facility at the Karawang site (below), located 50 km east of Jakarta, designed to ensure customers receive optimal supplies, improve supply security and boost operational efficiency – essential when working across a nation of 17,000 islands.
The latest investment at the site had added a fully automatic, state-of-the-art extrusion blow moulding unit for the manufacture of intermediate bulk containers (IBCs). This new installation can produce productspecific pieces, such as inner bottles for the EX-protected line; a new grid welding unit; and a new ultra-modern IBC assembly line, meaning that Ecobulk MX and SX models can be produced here to supply the Indonesian market. All products created in Karawang will comply with FSSC 22000.
One of the major benefits of the new facility for Schütz and its clients is a greater level of automation, resulting in significantly shorter cycle times. The plant layout was specifically designed to provide optimal process chains and efficient internal logistics to capitalise on the shorter cycle times. Furthermore, operating a significantly larger warehouse provides more flexible solutions for customers.
Looking to the future, there are plans for the Karawang plant to have equipment for Schütz’s Reco line installed, enabling the reconditioning of IBCs as a part of the Schütz ticket service.
CLASSIC CONTAINER While demand for IBCs is developing rapidly, especially in emerging economies, Schütz reports that “steel drums are still a preferred method” across several areas of the chemical industry due to their “specific properties and universal applicability”.
To provide users with the highest quality steel drums and ensure efficient supply, Schütz has been investing in new equipment at its existing steel drum plants and expanding global steel drum production. This expansion is providing customers with a steady supply of standard and specialised products, including corrugated steel tight-head and corrugated steel open-head drums varying in size (216.5 to 250 litres for tight-head drums and 210 to 230 litres for open-head drums) and thickness (0.8 mm to 1.2 mm).
In Germany, Schütz has replaced the coating line at its Selters plant to meet new standards and to improve production quality, capacity and flexibility. New lines for bung closures, screen printing, shell moulding and fully automatic palletisation were also put into operation. This allows customers to specify how they want their new drums consigned – they can, for instance, be held in place with plastics straps, machine cord or stretch film. In addition, the Selters plant has received a new folding machine and a sophisticated helium leak testing system.
Meanwhile, in the US, Schütz has been producing steel drums in Houston, Texas, since 2016. This has been further expanded by the development of Schütz ELSA – a Mexican subsidiary that produces a wide range of product variants for the local market, following the acquisition of Envases y Laminados in 2018. Schütz ELSA also produces smaller models with a capacity of 30 litres and higher. These drums can be delivered uncoated or coated, individually or palletised as required. HCB www.schuetz.ne