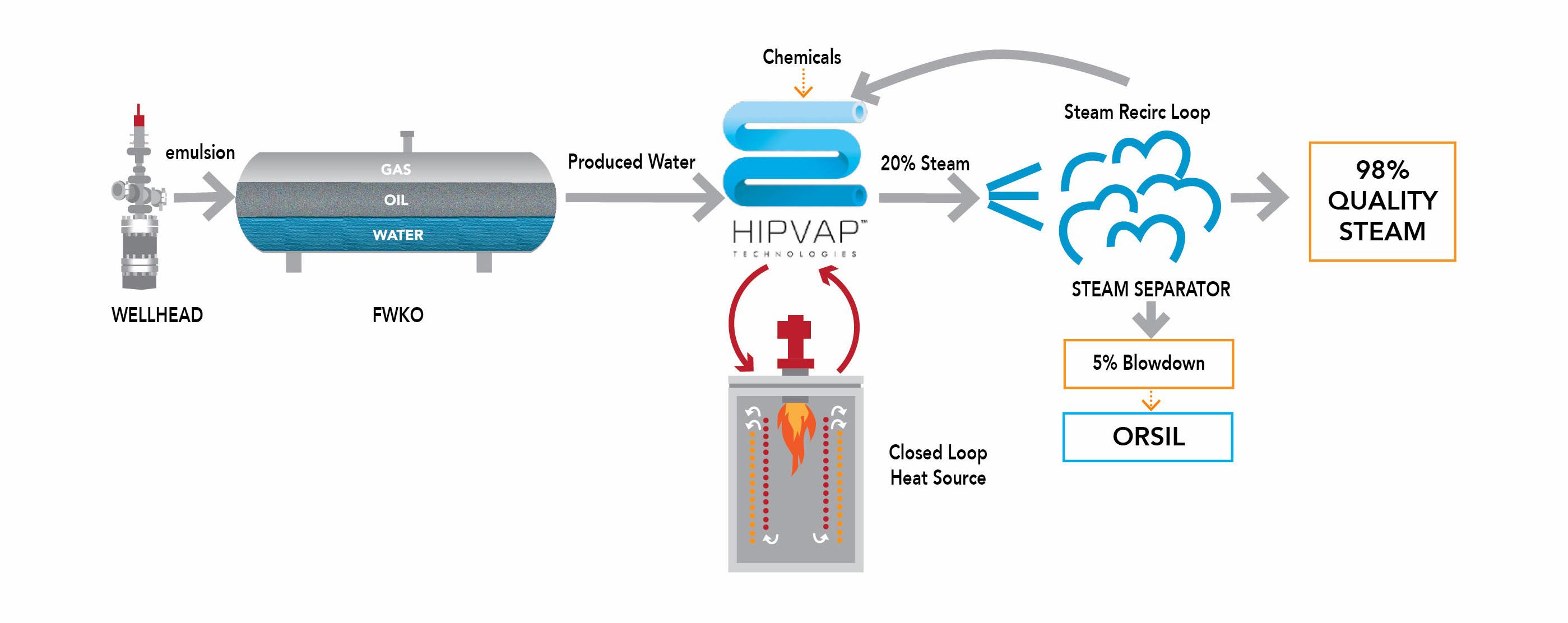
9 minute read
ALBERTA THERMAL OIL SANDS CANACHIEVE COST AND CARBON COMPETITIVENESS
Alberta Thermal Oil Sands can Achieve cost and carbon competitiveness
BY JANE CAVANAGH P.ENG. VP, PRODUCT INNOVATION, SCOVAN
Advertisement
IMPROVED STEAM GENERATION IS NEEDED
The oil sands deliver major economic benefits to Canada, and have a pivotal role in providing a secure and reliable long-term energy supply and raw material feedstock for the world. It’s an understatement to say that, along with this economic and security discussion, a great deal of attention is being paid to oil sands environmental impact. GHGs, tailings ponds, biodiversity, water use, land disturbance, and the boreal forest — virtually everything about oil sands development has an environmental dimension and represents an opportunity for innovative solution integration. Today’s uncertainties in longer-term bitumen prices and GHG emissions costs make it challenging for operating companies to sanction proceeding with thermal oil sands developments – and a key enabler, particularly for small thermal oil sands project sanctions, would be commercialization of
significantly more cost-effective and less GHG-intensive water treatment and steam generation technologies. Enter HipVap. Oil sands production using SAGD (Steam Assisted Gravity Drainage) or CSS (Cyclic Steam Stimulation) technologies requires large quantities of water to generate steam. This steam, after condensing into “The HipVap Indirect Fired water in the oil sands reservoir and returning to the surface with Steam Generator (IFSG) has been conceived as an alternative to currently bitumen, has many impurities. Current technologies used to recycle and treat produced water for steam generation use – Lime Softening/Once Through commercialized steam Steam Generators (OTSG) or Evaporators/Drum Boilers – generation technologies account for a large percentage of SAGD surface facilities which require extensive capital and operating costs at projects where water recycling – and expensive – water treatment.” is employed, and contribute to a severe cost competitiveness issue for Canadian oil sands producers.
Figure 1: HipVap IFSG Process Schematic
The HipVap Indirect Fired Steam Generator (IFSG) has been conceived as an alternative to currently available steam generation technologies which require extensive – and expensive - water treatment. Instead, HipVap generates steam using minimally treated produced water. The HipVap name comes from its concept of high pressure vapourization. HipVap circulates produced water in a loop, where 20% quality steam is generated and circulated to a steam separator, based on the steam generation concept of the Forced Circulation Once Through Steam Generator (FC-OSSG) that has been proven in SAGD operation (but is fed with evaporator water). Key is that that boiler tube heat flux is maintained at relatively low levels, temperatures are relatively low, chelants are added to keep calcium and magnesium in suspension, and the process is operated at a pH where silica remains dissolved. Any scale that forms is mechanically removed on line by a brush system that has been proven on produced water coolers. The circuit is operated on a net basis up to 98% steam quality. Cost Reduction via Technology Integration The HipVap IFSG process integrates a combination of technologies to address the SAGD industry’s cost challenge with respect to boiler feedwater treatment and steam generation. In conventional OTSG operations, 900°C flame is in direct contact with the steel tubes containing the boiler feedwater. In this environment, foulants and scale create an insulating layer on the inside (produced water side) of the boiler tube that impedes heat transfer, leading to hot spots where temperatures can exceed the 600°C maximum allowable temperature of the boiler tube and cause its failure and rupture. These risks with OTSGs are mitigated by intensive water processing to reduce or remove levels of oil, silica, calcium, and magnesium in the boiler feedwater. In contrast, the indirect heating design of the HipVap IFSG ensures the tube heat transfer surfaces do not exceed 325°C, virtually eliminating the incidence of tube failures. A clean heat transfer fluid is heated to 325°C in a fired heater and flowed to tube-in-tube heat exchangers that contain the produced water fed directly from the primary oil/water separator (Free Water Knockout or FWKO) without any additional cooling or contaminant removal treatment. Chemicals are added to maintain scale and foulants to a minimum level on the produced water side, and the process includes a physical tube cleaning system to ensure clean tubes.
Figure 2: HipVap Pilot Module Isometric, 100 tonnes per day steam capacity
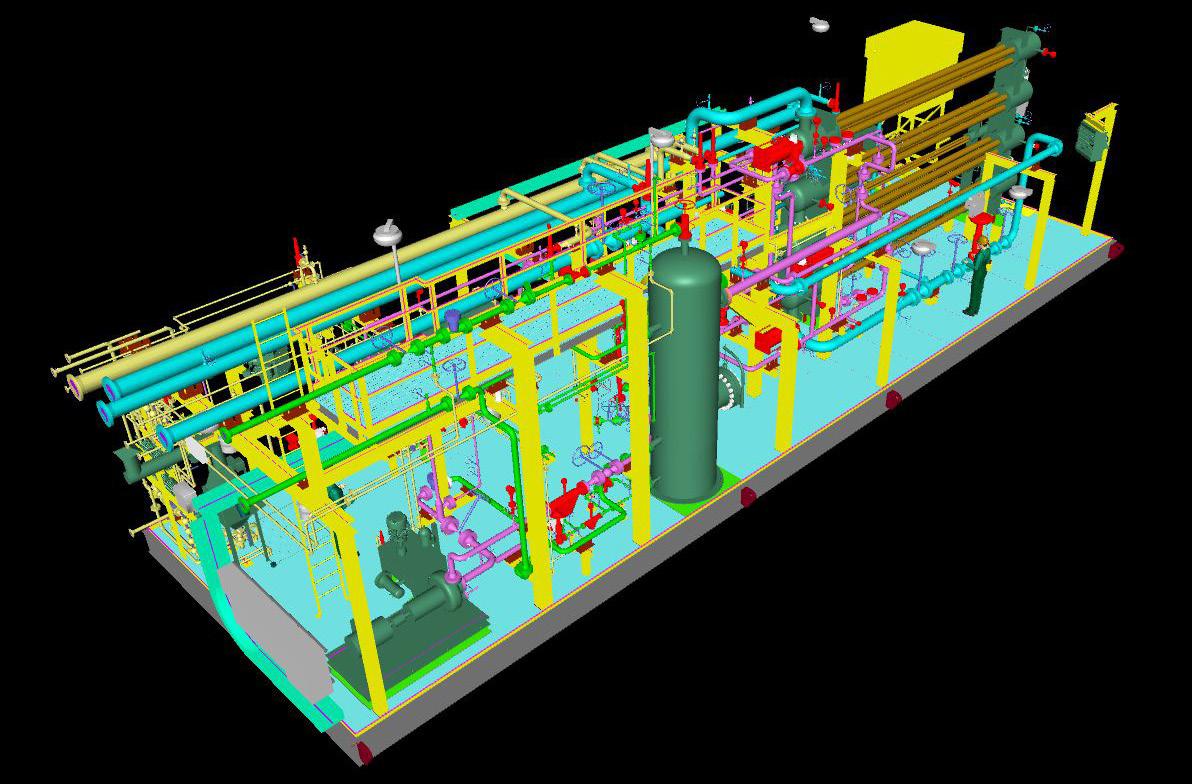
HipVap is designed to effectively maintain clean boiler tubes through the combination of these methods, eliminating the costly components in conventional systems required for produced water cooling and boiler feedwater treatment. The HipVap technology also is resistant to the types of upsets (oil and calcium/magnesium hardness in the feed water) that exacerbate the risk of tube failures in OTSGs. As these systems are maintenance intensive, their removal allows HipVap to deliver operational cost sav-ings, capital costs savings and important improvements to process unit up-time.
Key Process Elements • HipVap eliminates the need for produced water de-oiling and pre-treatment equipment commonly required for current boiler feedwater processing methods, including induced gas flotation units, oil removal filters, after filters, and ion exchange units. ׇ All of these components of current processes normally operate at a temperature of 90°C, requiring coolers to drop the temperature of produced water flowing from the FWKO primary oil separation that normally operates in the range of 110°C to 160°C. These produced water coolers are one of the most maintenance-intensive systems in a SAGD plant. ׇ The IFSG can accept feedwater at any of these temperatures, eliminating the produced water coolers. • Hipvap eliminates the requirement for produced water treatment after de-oiling. ׇ The primary water treatment equipment in typical lime softening/OTSG and evaporator/drum boiler schemes is a major contributor to the capital cost of central processing facilities, is operator intensive, and is a significant source of plant downtime. ׇ Current systems are primarily designed and manufactured outside Canada, introducing potential supply chain and foreign exchange risks. HipVap is being built in Canada. • The IFSG generates steam in an unfired heat exchanger. ׇ The IFSG operates at 20% quality steam per unit to keep its tubes well wetted, and hot oil use mitigates against “hot spots”. ׇ This eliminates the potential for the catastrophic tube failure, which is a risk for OTSGs. • The IFSG heat transfer tubes can be brushed while online or pigged if required. ׇ The IFSG design incorporates an on-line deposit control system (tube brushes). ׇ Although this is a novel deployment of the on-line deposit control system, it’s a proven system that has been successfully operated in other heat exchange applications. • The heat transfer oil is heated in a fired furnace. ׇ Operation of the hot oil heater does not require a First-Class Steam Ticketed Operator. ׇ The ability to operate the HipVap process with Third-Class Steam operators can provide significant labour flexibility and labour cost savings at sites that don’t otherwise require a FirstClass Steam Operator. • The IFSG is completely modular and can be installed on piles in a significantly reduced timeframe when compared to existing SAGD systems. • HipVap’s overall greatly simplified produced water treatment and steam generation process makes it suitable for deployment at small
CPFs and potentially at wellpads. ׇ Wellpad deployments would eliminate the need for surface gathering systems and the large transfer pumps required to circulate fluids between the wellpads and the CPF. ׇ Steam generation located at wellpads also benefits from lower hydraulic losses and a higher overall system efficiency.
Figure 3: HipVap Pilot Module Fabrication, November 2021
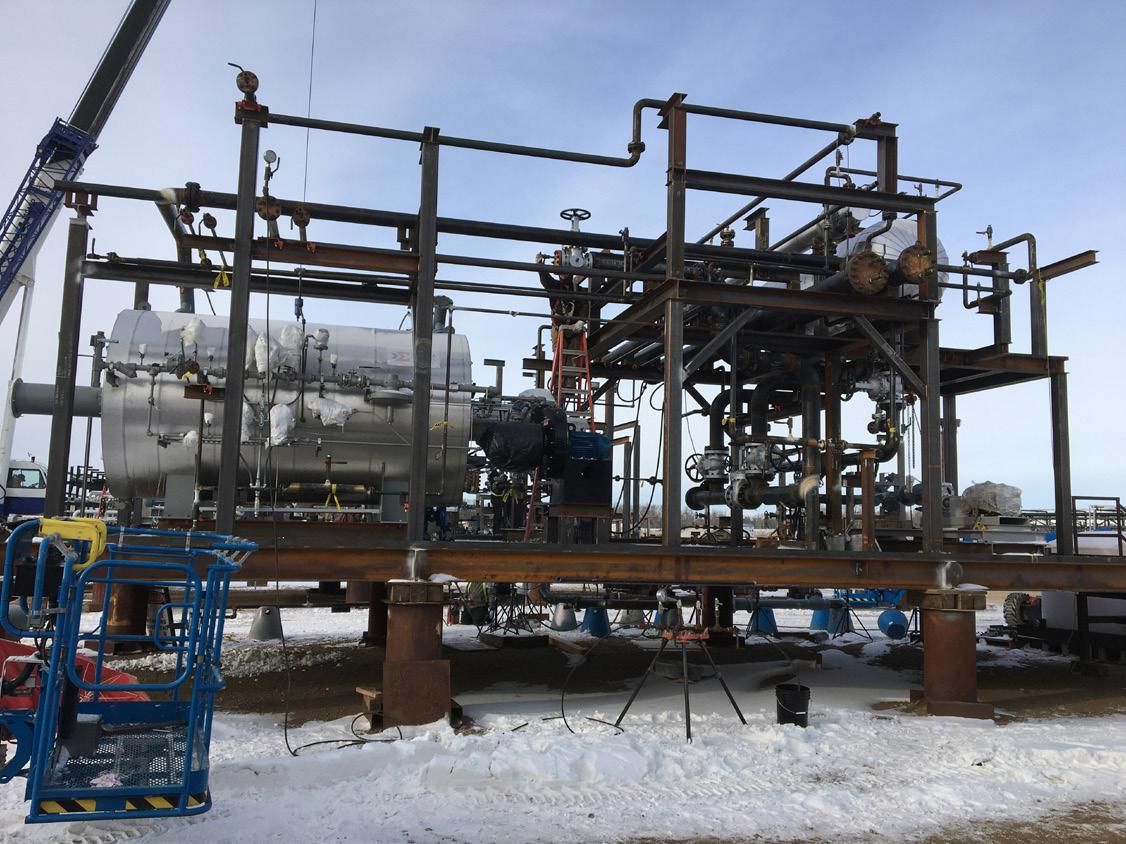
Bottom Lines Based on a typical 33,000 b/d SAGD CPF with a warm lime softener design, current estimates indicate that implementation of the HipVap process will • Reduce CPF capital costs by 24% and non-energy operating costs by 30% • Reduce CPF GHG emissions by 70% • Reduce CPF water consumption and disposal by 35% • Enable alternative pad-based steam generation deployment that further reduces overall project surface footprints (34% reduction in overall land disturbance) • Provide an overall significantly more cost-effective and less GHGintensive water treatment and steam generation technology.
Pathway to Commercialization To advance the HipVap process to commercialization, a commercial field pilot project is currently being conducted at a Strathcona Resources Ltd.-operated SAGD facility near Bonnyville, Alberta. This pilot project is to be commissioned in early 2022, with plans to operate and optimize the HipVap technology during the 2022 calendar year. The pilot has a design capacity of 100 tonnes per day steam. Key pilot elements include: • Increasing HipVap tube size: the commercial pilot tube size is nominal 3” diameter, compared to the bench-scale tube size of 0.75” diameter. • Moving to actual commercial operating environment: the pilot is being fully integrated into an operating SAGD facility. One important aspect will be the continuous processing of produced water from a live operating SAGD facility, compared with batch-processed trucked-in fluids that were used for the bench-scale testing • Proving the on-line brushing system: the pilot will confirm practical on-line cleaning in SAGD produced water operating conditions. The commercial pilot project will also be used to validate other HipVap design parameters, GHG and water usage benefits, and capital cost and operating expense reductions.
Recent TIER funding from Alberta Innovates has allowed HipVap to proceed from bench-scale level to full field piloting. Successful operation of the current HipVap pilot is intended to lead to final optimizations, and rapid deployment of the transformative HipVap technology by the oil sands industry.
HipVap’s contributing partners for the execution phase of this project include Scovan, Gemini Fabrication, Strathcona Resources, Drishya AI Labs, and Orsico. We thank Alberta Innovates for providing TIer (Technology Innovation and emissions reduction) funding on this project. Alberta Innovates’ TIER Economic Recovery Program (Program) consists of a set of “shovel-ready” projects that will accelerate innovation in support of GHG emissions reduction, increase long-term economic competitiveness and stimulate growth in critically important sectors of Alberta’s economy.
Jane Cavanagh P.Eng.
Ms. Cavanagh holds both B.Sc. and M.Sc. degrees in Mechanical Engineering from the University of Saskatchewan. She has 15+ years of experience as an engineer, project manager and new technology champion in Western Canada’s energy industry. In her current role, VP Product Innovation, Scovan Engineering, she oversees the team working to commercialize the HipVap technology.
CHOA Platinum Sponsors
CHOA Gold Sponsors
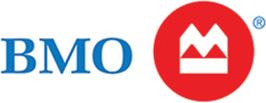
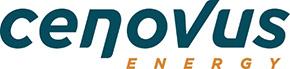

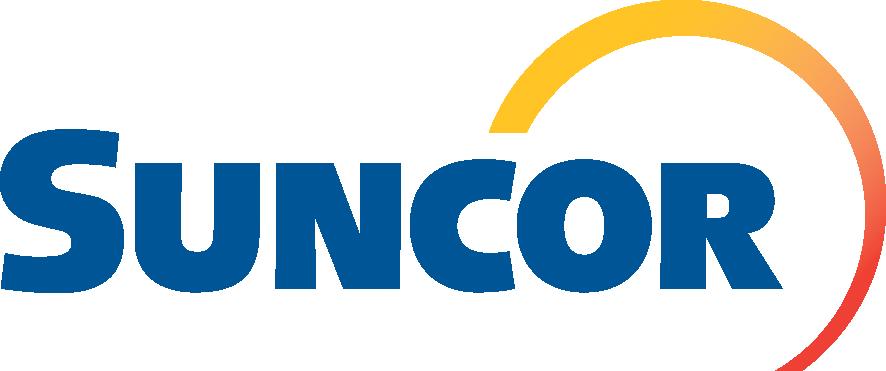
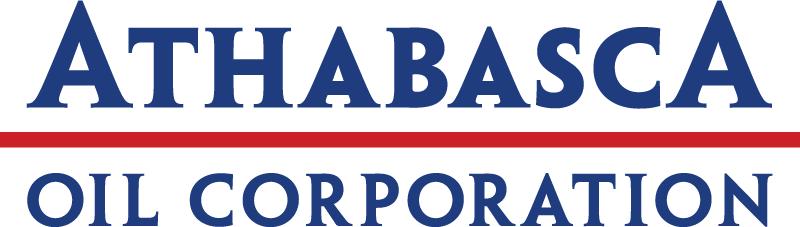
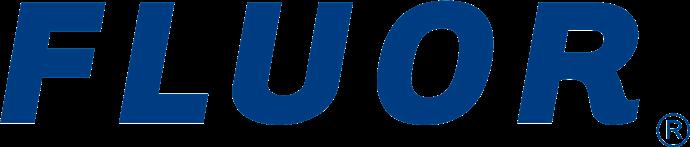
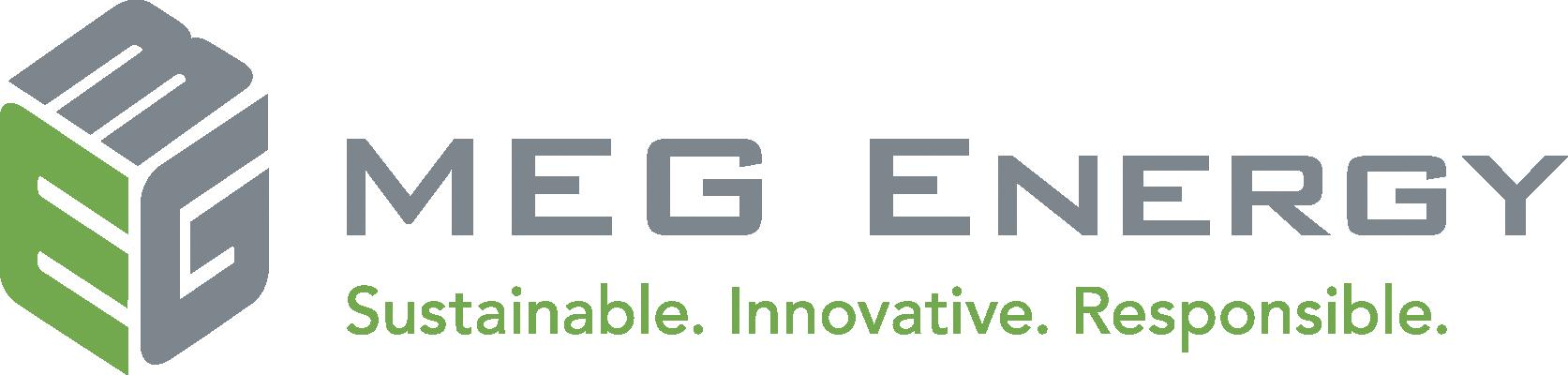
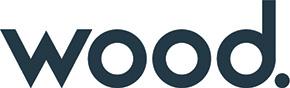
CHOA Silver Sponsors
CHOA Bronze Sponsors
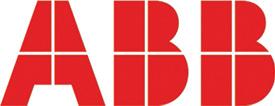
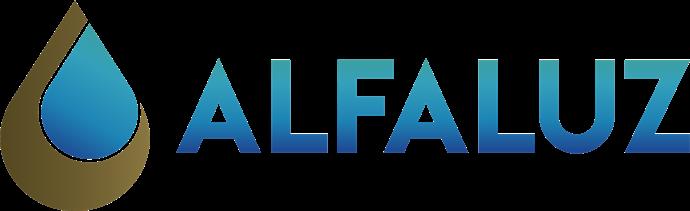
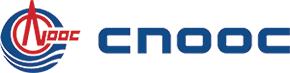
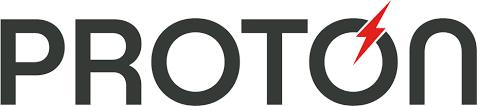
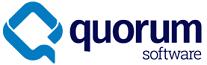
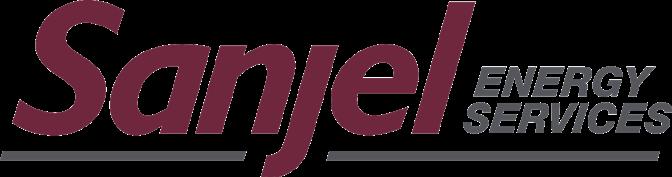
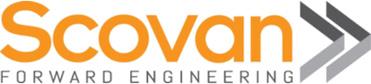


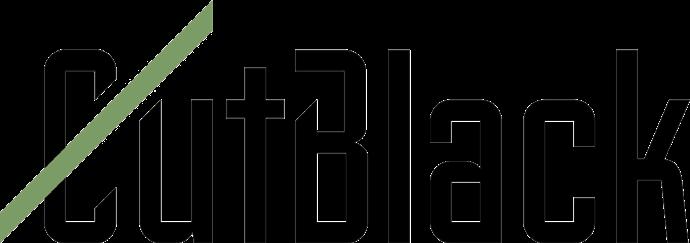
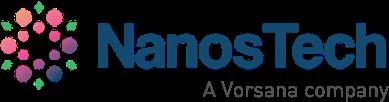