

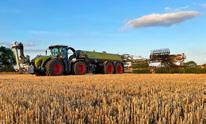
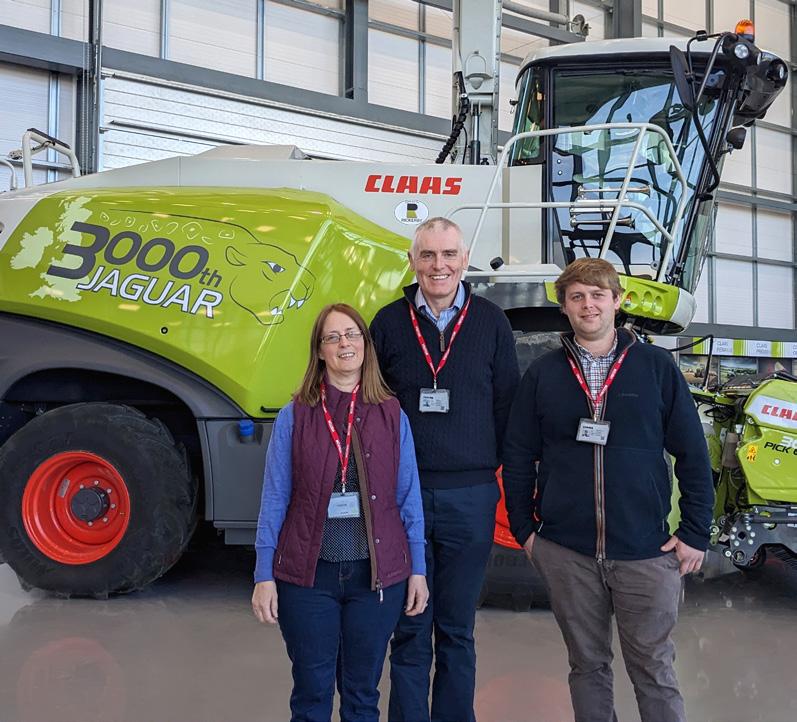
Stronger modular rollers.
Larger tyre options.
The CLAAS ROLLANT 540 features the latest generation of rollers with 15 reinforced rollers, 50-mm drive stubs and extra-robust ball bearings for perfectly formed silage bales and optimum crop flow. Quality is not expensive, it’s priceless.
3 years / 30,000 bales warranty available. Terms and Conditions apply.
Contact your dealer for more information or visit claas.co.uk
Despite the difficult trading conditions experienced during the 2022 financial year, CLAAS was able to increase sales by 2.7% to a new high of €4.9 billion (previous year: €4.8 billion). However, earnings before taxes dropped 53% to €166.3 million due to impairments in Eastern Europe as a result of geopolitical changes and disrupted supply chains.
“The year 2022 has challenged us in every respect. In this difficult mix, we have shown how resilient our business model is. We delivered and proved with a lot of personal commitment that we can measure up to our vision of making customers the best in their field. We have delivered 100% on our harvest promise to our customers. For this, all employees and distribution partners deserve my thanks,” says CEO Thomas Böck.
Despite significant supply-side disruptions and the warrelated slowdown in Eastern Europe, a combination of the strong harvest year and beneficial financing conditions helped maintain demand, especially in North America.
CLAAS has always maintained a high R&D spend and 2022 was no exception with a record €279 million invested in product development. A further €130 million was also spent on the expansion of its global sales and production network, including work to modernise the main plant in Harsewinkel, in addition to the further infrastructure development at Bad Saulgau and Le Mans.
Employee numbers in the CLAAS Group also rose to 12,116 people worldwide, of whom approximately 50.4% are outside of Germany, with 792 apprentices also employed, of which 493 are in Germany.
Last autumn saw the new LEXION range pick up two awards. At SIMA in France the LEXION was awarded with a Farm Machine Award in the combine category, while in America it was named as ‘The Coolest German Thing made in the USA”.
Each year, at the alternating SIMA and Agritechnica shows, a jury of international journalists decide on a number of Farm Machine awards for outstanding innovations in agricultural engineering in various categories, with the LEXION winning the combine category in the awards announced at SIMA in November.
Meanwhile in America, each year in their annual Business Awards, the German American Chambers of Commerce recognize outstanding achievements in the German-American business community. A particular focus is placed on competences in the areas of innovation, services, economic development and social commitment.
Following an online vote in which over 5,000 votes were cast, the LEXION, which in America has been assembled at the CLAAS factory in Omaha for 25 years, was named as ‘The Coolest German Thing made in the USA’. The award, which was presented by Comcast, was made to CLAAS at the annual German American Business Awards that were held in Chicago.
For 2023 a number of new innovations have been introduced on the LEXION range, including a larger cab with a rotating driver’s seat, the new CEMIS 1200 terminal with the new GPS PILOT, performance and crop flow optimization, larger grain tanks and optional additional equipment such as a pivoting spout for the grain tank discharge auger or the variable steering ratio DYNAMIC STEERING. New CEMOS functionalities are available for process optimization in terms of productivity and efficiency. A new model, the LEXION 8600, has also been added to the product range.
Established in 1999 by Helmut Claas, the CLAAS Foundation annually awards a total of €50,000 to students from agricultural and engineering facilities around Europe, in recognition of their outstanding final theses. This year’s awards saw the work of three students from Harper Adams University being recognised. Four annual Helmut Claas Scholarships are awarded, with the 2022 third prize being awarded to Richard Geary for his thesis entitled “Maize Belongs to the Farmer, Not the Field” which investigates the optimisation of harvesting technology and earned him a grant of €4,800 towards his annual fees.
In addition to the Scholarships, the Foundation also awards four Bonus Awards that are each worth €1,500. One of these was awarded to John David Kendal Morgan, who received the prize in the category of Technical Solutions to Improve Animal Welfare. His thesis explored the development of a low-cost imaging system to analyse the behaviour of poultry in small Kenyan pens. In the category of Improved Nutrient Management for Food Production, James Patrick Nicol Shaw was also awarded a Bonus Prize for his thesis investigating the mechanical durability of digestate pellets.
Since 1951, in early October of every year, the streets of Clarholz-Sundern near Harsewinkel come alive for the annual Harvest Festival Procession. Amongst the various floats in last year’s Procession was this unique 1:1.7 scale model of an original XERION created using grains from seven different cereals, which was made by a local firm of float builders to celebrate the tractor’s 25th anniversary.
The basic frame of the model was built from chipboard. This was then covered in some 427,588 grains that were sprinkled onto wood glue, with a further 5,372 ears of wheat fixed using a hot glue gun. Other materials used included metal, acrylic glass, wood and rubber for the tyres. Working on average four days a week for five weeks, in all it took the team of nine builders some 250 hours to construct the model, which is now to be found on display in the Technoparc at Harsewinkel.
In 2022 CLAAS UK employees were busy holding charity fundraising events for a number of local and national charities, and by the end of the year they raised over £20,000, which is a fantastic result.
The fund raising events included a football match between CLAAS EASTERN and MANNS, while diets were momentarily forgotten when a ‘Bake Off’ was held at Saxham in which staff members baked and brought in their favourite cakes, which were then judged by those who bought and ate them.
Engineering teams at CLAAS have been looking at how lightweight construction techniques, using lighter, stronger materials and specialist bonding technology, originally developed and used within the automotive industry, can be adapted and used to help reduce machine weight and compaction.
“We can find inspiration from the automotive manufacturers’ lightweight solutions, but it would be difficult to simply transfer their ideas due to the different requirements and, above all, different quantities,” explains Markus Pellmann from the CLAAS selfpropelled machinery division. But adopting the basic rules – the right material in the right place, the right joining technology in the right environment and all of this integrated in the right lightweight construction concept – does get closer to lightweight construction solutions for agricultural machinery.
The first area in which lightweight construction techniques have been applied is for the manufacture of the preparation floor for the TRION and LEXION. A concept has been developed that involves the use of a thinner, but stronger, sheet material that has resulted in a reduction in weight compared to the usual design. The preparation floors are manufactured using robots that automatically apply the thermosetting structural adhesives or use resistance spot welding technology to connect the thinner and stronger sheets.
The engineering teams at Harsewinkel are now in charge of sharing this experience of lightweight construction with other CLAAS factories and for other developments. The team includes developers and production planners from different locations who coordinate lightweight solutions. This team will support the next lightweight solution, which will be implemented for the ORBIS maize header manufactured at Bad Saulgau.
The winners of the annual Christmas Draw nominated a charity of their choice to donate any winning prize money to and a Christmas jumper day was also organised. In addition, collections were taken at Dinner Dances held by CLAAS UK, CLAAS EASTERN and CLAAS WESTERN, and also at the annual CLAAS UK Dealer Awards Dinner and the CLAAS Pensioners Lunch.
The local and national charities to which donations have been made include:
The CLAAS Ukraine Family Appeal/UNICEF, the DEC Ukraine Humanitarian Appeal, RABI (Royal Agricultural Benevolent Fund), Children with Cancer, St Nicholas Hospice (local to CUK), the Royal British Legion (poppy appeal) and MIND for their World Mental Health Day.
As anyone who has had the builders in will know, getting them to work to a strict timescale can be a challenge. Yet last autumn, construction teams at Harsewinkel rose to the task of creating the world’s most modern combine assembly plant in just 22 weeks.
With up to 150,000 individual parts, combine harvesters are some of the most complex agricultural machines to be built, and the wide range of options and specifications make planning and assembly a particular challenge.
With parts of the main combine assembly hall, with its two production lines in the heart of the Harsewinkel site, dating back to the 1950s, the size and complexity of today’s combines meant that the combine production facility was at its limit. For instance, with ceiling heights ranging from just 4.2m up to 6.0m, during testing it was impossible to open the grain tank lids to ensure they were functioning properly.
The launch of the new TRION range in 2021 with its wide range of models and specifications meant that a complete rethink was necessary if CLAAS was to achieve the flexibility and efficiency of production it was looking to achieve.
The solution was the €44 million SynPro 2020 project which in the space of just 22 weeks saw the old production halls and assembly lines completely demolished and replaced by a new 14m high hall with a floor space of 15,000m2. LED lighting provides bright, almost naturally illuminated workplaces, no matter the time of day.
A new 6-tonne ventilation system circulates 80,000 m3 of indoor air per hour, creating a pleasant working environment all year round. The new hall alone saves around 470 tonnes of CO2 per year thanks to efficient energy management, excellent insulation and LED lighting.
The old assembly lines have been replaced by a single new assembly line, on which both LEXION and TRION combines and up to 30 different variants can be built at a rate of up to 28 machines a day in a single shift.
As they are assembled, each combine harvester is carried down the line on electric automated guided vehicles (AGVs) capable of carrying up to 20 tonnes. The main line is fed from each side by a series of sub-assembly lines which deliver the required parts and modules, such as the threshing and separation systems which are assembled adjacent to the main hall, on a just in time basis managed by a cutting edge IT system.
The final stage are six ultra-modern test bays used to perform the first comprehensive quality controls, but also the important initial commissioning of the machines. They run through all the mechanical, hydraulic and electrical functions to check
for flawless working order – and even test electronic features such as CEMOS, CEBIS, CEMIS 1200 with GPS PILOT and TELEMATICS.
By using the latest production and logistics technologies, this enables two model ranges incorporating an unprecedented variety of specifications and options to be assembled on just one line, in the world’s most modern, state-of-the-art production plant.
More information on the new combine assembly plant at Harsewinkel can be found at: www.excellence-harsewinkel.claas.com
The long established Irish family dealership KELLYS has been awarded with the prestigious CLAAS UK ‘Dealer of the Year’ award for 2022.
The award recognises the high overall level of performance by the company in three key areas: Finance, Dealer Performance and Customer Feedback.
Based at Borris in Co. Carlow, Ireland with a second branch at Abbeyleix in Co. Laois, KELLYS was established in 1957 and has been a CLAAS dealer for many years, serving the Midlands of Ireland from the Irish Sea across to the Atlantic.
In making the award, the judging team not only assesses a dealership’s overall performance, but the performance of each of its individual branches.
The award also reflects the results of the Customer Feedback Survey and KELLYS scored well in this category too, underlining their commitment to their customer base and the first class customer care service they provide.
The announcement and presentation of the ‘Dealer of the Year’ award to Maurice Kelly, was made at the CLAAS Dealer Council meeting, held at the CLAAS UK headquarters at Saxham, Suffolk.
Established in 1997, the CLAAS factory at Törökszentmiklós in the south east of Hungary is the home of CLAAS combine cutterbars and the ORBIS maize header.
Employing over 800 people the Törökszentmiklós factory is the largest manufacturer of agricultural machinery in Hungary, and last year saw the major milestone of the 100,000th combine cutterbar to roll off the production line.
The most recent addition to the CLAAS combine cutterbar range is the CONVIO and CONVIO FLEX draper type header, and such is its popularity and sales success, it is expected that record numbers will be manufactured this year with over 1,000 units leaving the factory.
Introduced in 2019 and available in five working widths from 7.7m up to 13.8m, the CONVIO and CONVIO FLEX can be used with both the LEXION and the TRION. With its ability to significantly increase output, especially on higher capacity LEXION, 55% of all LEXION 8000/7000 models sold in the UK are now specified with a CONVIO or CONVIO FLEX cutterbar, while across all LEXION and TRION combines sold they account for 40%.
New developments for the JAGUAR range for 2023 include an update to the optional hydraulic pickup drive for the JAGUAR 900 which now features a new automatic ground speed adjustment system. Meanwhile, a change in engine has given the JAGUAR 840 a significant increase in power and torque while both the JAGUAR 900 and 800 are the latest CLAAS machines to feature the new CEMIS 1200 terminal with GPS PILOT.
Introduced in 2021, the optional hydraulic drive for the reel of the PICK UP, enables the speed of the reel to be varied automatically relative to the ground speed, independently to the intake auger. This has now been further developed so that the speed of the PICK UP is automatically adjusted at a ground speed above 5 km/h. If the ground speed or the set chop length is changed, the speeds of the pick-up reel and intake auger are automatically matched to the prevailing conditions. This results in an even more consistent crop flow, especially where there are frequent and significant changes in swath thickness. If necessary, both speeds can also be adjusted manually from the cab by the operator. This has the benefit that crop feed is even more precise, resulting in a more consistent crop flow through the forager, especially when operating under varying conditions. Also new is the automatic chain lubrication for the left-side drive of the intake auger and pick-up reel.
A change of engine in the JAGUAR 840 to the larger MercedesBenz OM 471 LA 12.8 litre Stage V six-cylinder engine already used in the JAGUAR 850 means that power output for the smallest forage harvester in the CLAAS range is increased by 27 hp. This takes the maximum output to 435 hp at 1,600 rpm and makes significantly greater torque reserves available, although the excellent diesel consumption per tonne of throughput remains the same despite the increase in displacement.
The JAGUAR 900 and 800 are also the latest machines in the CLAAS range to be equipped with the new CEMIS 1200 terminal with the newly developed GPS PILOT.
As well as representing an alternative to the row sensor when harvesting maize with the ORBIS and the CAM PILOT when harvesting grass, this automated steering system can be used when harvesting whole crop silage or other types of forage crops. The CEMIS 1200 has a 12-inch screen that provides a 2D and 3D display with a splittable screen, as well as online task management and documentation with data export by means of TELEMATICS or USB stick.
Another new development is the two-stage activation of AUTO PILOT / GPS PILOT and CEMOS AUTO PERFORMANCE or CRUISE PILOT. After turning and entering the next track, the operator first activates the steering system at the touch of a button and accelerates up to the speed at which the machine is able to make optimal use of the available power. A second push of the button on the CMOTION lever, CEMOS AUTO PERFORMANCE or CRUISE PILOT - depending on the system fitted – then takes automatic control of the ground speed. This enables faster adjustment to the set engine speed, the most efficient power level and a suitable ground speed. If the pushbutton is pressed down somewhat longer; both functions are activated simultaneously as usual.
Eight years after it was launched, CLAAS’ industrial division based in Paderborn recently manufactured the 10,000th EQ stepless transmission. Designed specifically for the ARION 600 and 500 ranges, the EQ200 was introduced in 2015 and was followed two years later by the EQ220 which is used in the ARION 660, and set new standards for infinitely variable transmissions.
A key feature of the EQ200/220 mechanical-hydraulic power split transmission is its simple design with an automatic change between its two driving ranges. This enables the operator to accelerate under maximum load right the way through from 0-50kph without losing speed or torque. To conserve fuel, at 50kph the engine speed is reduced to just 1500rpm and when it comes to stopping, the tractor can be stopped and held in powered zero mode, even on a slope.
In operation, the operator has the option of either accelerator pedal, CMOTION or manual modes. In the first two modes the transmission is controlled using the accelerator pedal or CMOTION, and engine speed and transmission ratio are adjusted automatically and the operator can switch mode on the move. In manual mode the operator selects the engine speed and ratio. The EQ200/220 transmission comprises of two multi-plate clutches, a stepped planetary transmission and two wide angle
hydrostatic units with the ability to change function to allow the transmission to automatically change range. This provides smooth acceleration under load right the way through the speed range from 0 to 50kph without any interruption in tractive power, combined with high, constant efficiency at any speed. In addition, once the tractor reaches 50kph, for even greater economy engine revs are reduced to just 1500rpm.
In order to achieve this seamless change in range, as the tractor accelerates, the rotational speeds of the clutch shafts come closer and closer until they reach the same speed and align. As they align and become perfectly synchronised, the transmission automatically changes from the lower to the higher speed ratio. At the same time, the characteristics of the two wide-angle hydrostatic pumps also change, with the unit that was pumping changing function to being a motor, and the unit that was the motor becoming a pump.
Designed and manufactured by CLAAS Industrietechnik, the EQ is assembled following a computer-guided ‘zero defect’ strategy where not only is the transmission thoroughly tried and dynamometer tested, but it is manufactured in an environment where cleanliness limits are down to one micrometer, which compares to a human hair which is 17 to 180 micrometers wide.
Building on the success of the EQ transmission, the signing of a new strategic agreement between CLAAS and the SDF Group for the joint development of CVT transmissions for tractors will see the ongoing development of the EQ200 and 210 transmissions, in addition to the new EQ260 for higher horsepower tractors.
Yield maps do not just provide a record of past performance. With the simple addition of further information they can also play a key role in unlocking the future potential of fields.
Yield mapping is now virtually standard on today’s combines, but many users are not making the most of this beneficial technology, despite it being easier than ever to make a move to variable rate applications to boost yields and quality.
“Many people, I believe, may still not be utilising all the benefits that ‘precision farming’ has to offer as they are still apprehensive about using the technology,” states Edward Miller, CLAAS Smart Farming Product Manager.
“Precision farming is not complex. It may use some sophisticated technology, but that technology has been designed for ease of use. Most CLAAS combines have TELEMATICS fitted. If you have a QUANTIMETER as well, then you have the ability to yield map,” he explains.
TELEMATICS, available for all CLAAS combines, automates mapping. This means operators don’t need to create and transfer maps – that’s all done automatically.
During harvesting, yield monitor information is transferred via TELEMATICS to servers in Germany. The resulting yield maps can be accessed either via the CLAAS TELEMATICS webpage, or via a ‘Cloud API’ (Application Programming Interface). Essentially this allows the customer to access their data in the farm management software of their choice.
The data is transferred in the industry standard ISOXML format. In the UK, the Cloud is linked to Omnia (Hutchinsons), Gatekeeper and MySoyl – the most commonly used software and service providers.
So, now we’ve got a yield map, what can we do with it? “We need some more information to turn it into a useful tool,” says Edward. “I would start with your own local knowledge. We all know where the bad patches are in fields, the places that never yield. You will be carrying this around in your head.
“But do you really know the cause? Is the low yield along the hedge really rabbit damage, or is it deep seated compaction? You can’t see things like nutrient deficiencies or pH imbalances, so the next step is to invest in some soil testing – the more the better. “Most farms will already have a soil texture map – and this is what shows its potential. Be sure to invest in tests on all the main contributors to yield – nutrients, organic matter, P & K levels, Ph levels, and soil N content,” he explains.
Armed with this information, it’s now possible to compare the soil map results with the yield maps and make plans to create variable rate applications.
“In reality a lot of farms are already doing is – without any digital maps or controls. For example, most people only apply lime to where they know it’s needed, others will manually adjust seed rates while drilling and some even vary PGRs to match the growing crops.
“With the digital maps, this can now be done automatically using a ‘prescription map.’ We sometimes encounter another common stumbling block here though, as not everyone is familiar with how to create these maps,” says Edward. Most soil testing services, will not only provide a soil analysis map, but also create the prescription map as well. Thanks to the industry standard ISO XML format, these maps are not only compatible with most commonly used farm management software, but also variable rate equipment.
Operation of modern fertiliser spreaders, sprayers and drills now comply with the ISO 11783 standard. This is another, incredibly useful industry standard, which provides ‘plug n play’ connectivity, enabling any compliant terminal to operate all compatible implements.
You literally plug the implement into the ISO socket on the tractor and its operating menu appears on the tractor terminal, such as the CLAAS CEMIS 1200. At the same time any instructions/maps loaded into the terminal will automatically control the implement.
Transferring the prescription map (‘task’) is just as easy, either using CLAAS TELEMATICS or on a standard USB memory stick. All the operator needs to do is to receive the ‘task’ on the terminal and select ‘play’.
The implement will automatically start and stop, as well as apply the correct rate in the defined areas. At the same time it records an ‘as applied map’ which provides proof of the job and rates for record keeping, if required. You now also have a treatment plan you can compare with the next season’s yield map to check the effectiveness of your variable treatment – nicely completing the circle.
“One problem we encounter when discussing precision farming is the actual word precision,” says Edward. “Many farmers translate this into meaning tiny adjustments all the across the field, but it’s not.
“It’s really about improving consistency and just applying things more accurately than before. It certainly doesn’t need to involve precision down to 1m or even a section on a sprayer,” he says. Rate adjustments are usually set in ‘zones’ matching specific soil types, quite large areas that require a different treatment to the whole field or adjoining zones. The actual resolution (or accuracy) will be determined by the width of the applicator’s section control set-up.
Seed rates are often the first to be varied, because many farms are already matching this to the soil type and quality, changing this manually on the drill’s terminal. Simply switching this to having this done automatically, according to the map, is an easy win.
“Correct plant populations, more even germination and a regular canopy size will provide the consistency that makes future applications much easier and more effective through the growing season,” adds Edward.
Fertiliser is an obvious target for variable rate treatments, particularly now after the enormous cost increases. “Variable rates are not, however, about saving fertiliser but optimising its use with correct targeting,” explains Edward. “There are plenty of advisers and service providers that will do this for you and even provide the application map. An ISObus terminal will automatically control the application as well as produce the application map for record keeping.”
• Yield mapping can be a good starting point to highlight the lower yielding areas of the farm
• Soil sampling and testing is vital to identify any areas where the soil requires improvement
• Base fertilisers, lime, and trace element requirements can all be mapped by soil sampling
• Variable rate nitrogen is based on the current crop’s growth. This is usually monitored with satellite imagery
• Variable seed rate is mainly based on soil type and expected germination rates
• The application map loaded on the terminal in the tractor controls the rate of application
• After harvest the yield map will show the improvements that you have made to yield compared to previous years
Users have often commented on how fuel efficient their ARION 400 tractors are. This has now also been confirmed in the latest DLG PowerMix tests on an ARION 470 HEXASHIFT conducted for Profi, where in a range of tests fuel savings of up to 16.1% below the average for tractors in this class were achieved.
As with all tractors in the ARION 400 range, the ARION 470 is powered by a 4.5 litre FPT Stage V engine. Maximum power output for the 470 is 145hp with 631Nm of torque that is held over a wide engine speed range. In addition, it also features the CLAAS POWER MANAGEMENT (CPM) electronic control system which delivers an additional 10hp for PTO and transport work.
In their PowerMix tests, the DLG subject tractors to 14 test cycles to simulate various loads on the tractor and the resulting fuel and AdBlue consumption, power output and efficiency.
The initial results on the PTO dynanometer showed that the ARION 470 is not only powerful, but also economical at the same time. Up to 144.25 hp of the boosted 155 hp power output was available at the PTO – an excellent value. The maximum torque of 600 Nm and a 34 percent increase in torque were also impressive. The tractor consumed only 242 g/kWh (at nominal speed) or 224 g/kWh (at maximum output) of diesel plus 25 g/kWh AdBlue each – which according to Profi are top values.
In the practical PowerMix tests, where various field work operations are simulated on the test bench, fuel consumption was 270 g/kWh plus 21 g/kWh AdBlue, which was almost 3% below the average of all tractors measured so far.
It was in the tests replicating heavy and medium-heavy draft work with ploughs and cultivators that the ARION 470 started to show its true colours consuming around 6 percent less than the average. Despite the low power-to-weight ratio of just 37.51 kg/hp, the ARION 470 converts a particularly large amount of engine power into tractive power. Thanks to the outstanding traction, it achieves an impressive maximum tractive power of 133.38 hp - which is significantly more than many heavier tractors in this performance class can offer.
However, it was in the transport tests where the ARION 470 and its HEXASHIFT transmission really excelled. The 6-speed power shift HEXASHIFT transmission on the ARION 470 has a top speed of 40kph at just 1,660 rpm. The benefit of this was obvious in the transport test where the fuel consumption value was just 351 g/ kWh (plus 32 g/kWh AdBlue), which is a massive 16.1 percent below the average!
The full test report is due to be published in the June issue of Profi, which is due out in early May.
Find
out
The ARION 400, Stage V offers: 85-155 hp
Intelligent operator assistance systems
Smart data management
Efficient connectivity
Exceptional cab comfort
It was 20 years ago that on 23rd February 2003, Helmut Claas signed the agreement to acquire a majority stake in Renault Agriculture, the tractor division of the Renault Group. Since then, CLAAS has gradually consolidated its position as a full system provider on the international stage and invested both in the development of the product line, but also in the creation of one of the world’s most advanced tractor production facilities.
The agreement signalled a reshuffling of the cards in the global agricultural machinery sector, but was also the largest acquisition in the company’s history. The agreement to initially take a majority share in Renault Agriculture with a full buy-out to be completed four years later, was signed by Helmut Claas and Renault S.A board member Patrick Faure on the eve of the SIMA tradeshow in Paris.
Following the signing, on 1 October the factory in Le Mans began switching the colour scheme from Renault Orange to Seed Green and from 1 November 2003 all models for new and emerging markets rolled off the assembly line in CLAAS corporate colours.
Work on the development of the AXION 800 large tractor started in late 2003 and barely three years later, the new tractor was added to the CLAAS sales range. This marked the first step in the gradual replacement of the Le Mans product portfolio: over time, the CELTIS, ARES and ATLES were replaced by the ARION and AXION – product names which ushered in a new era.
The development of the ARION and AXION tractor range has also seen the introduction of numerous award-winning innovations, including:
The large, high-contrast CEBIS terminal for the AXION and later also the ARION 500 and 600 series
The PANORAMIC cab for the ARION 400
TELEMATICS for fleet management
The AXION TERRA TRAC, which was the first half-track tractor with full suspension
CEMOS, the market-leading self-learning, dialogue-based operator assistance and process optimisation system for the ARION and AXION CMATIC
CLAAS tractors from Le Mans have also set new standards for efficiency. In 2013 the DLG Test Centre tested the 416 hp AXION 950 on behalf of the farm machinery journal Profi and measured a record-breaking pulling power of 242 kW – making it the world’s most powerful standard tractor! In the DLG PowerMix test the tractor beat the average of all tractors tested before by a whopping 15.6% with a fuel consumption of just 249 g/kWh.
But product research and development is not the only focus of investment. Since 2003, CLAAS has invested more than 80 million Euros in the construction of state-of-the-art production facilities and ergonomic workstations. The largest and most important of these was the CLAAS Forth initiative launched in 2020 and the redevelopment of the Le Mans factory, which is now one of the most up-to-date in the world, deploying
driverless transport systems and artificial intelligence (AI) in logistics. A new visitor centre modelled on the Technoparc in Harsewinkel recently opened there too.
Spring 2019 saw the 150,000th CLAAS standard tractor leave the Le Mans production line and it is expected that the 200,000th will be reached this year.
Today CLAAS Tractor in Le Mans produces more than 60 different models that are exported to 80 countries around the world. These range from 75 to 445 hp, from simple tractors for markets with less stringent emissions standards such as Turkmenistan or Africa to the high-volume ARION 400 mainly for the European market and the AXION 900 TERRA TRAC hightech large tractor for the global market.
23 February 2003
CLAAS signs agreement to purchase majority share of Renault Agriculture.
1 October 2003
Roll-out of the first Seed Green CLAAS standard tractors from Le Mans.
1 November 2003
All tractors now produced in CLAAS colours.
9 – 15 November 2003
CLAAS exhibits full range of tractors at Agritechnica ranging from CELTIS, ARES and ATLES to XERION.
2006
Launch of the AXION 800 series with HEXASHIFT semi powershift transmission and CEBIS terminal.
2007
Launch of the ARION 500 and 600 series available with a CMATIC CVT as an alternative to the HEXASHIFT powershift transmission.
2008
Acquisition of the Renault tractor division complete.
2008 – 2010
Installation of new cab pre-assembly and new paint shop.
February 2011
New AXION 900 with CMOTION multifunction control lever.
2012
Launch of new ARION 500 and ARION 600 series.
2013
The AXION 950 sets a new pulling power record for standard tractors of 242 kW.
November 2013
Premiere of the ARION 500/600 CMATIC with EQ200 continuously variable transmission.
2014
Launch of the new ARION 400 series with PANORAMIC cab.
November 2017
Agritechnica silver medal for the AXION 900 TERRA TRAC and CEMOS for Tractors, the first self-learning, dialoguebased operator assistance and process optimisation system.
Spring 2019
The 150,000th tractor rolls off the production line in Le Mans.
From 2019
The CLAAS FORTH investment programme leading to the opening of the “factory of the future” in May 2021.
2021
The AXION 960 CMATIC with CEMOS wins Sustainable Tractor of the Year.
September 2022
The new CENTRAL ACADEMY opens in Le Mans.
Farming a stone’s throw from the north Norfolk coast, the Harrison family have a broad range of cropping and consequently need a tractor fleet to suit a wide range of different roles.
CLAAS machines have long formed the backbone of the business and in the last five years the move to stepless CMATIC transmissions has brought greater efficiency to the operation.
“We’ve run CLAAS tractors for decades and before that had Renaults, so we’ve got a long history with Le Mans-built machines,” explains Matthew Harrison.
“We like them for their robust build, comfort and reliability. But crucially from a financial point of view they stack up. Each time we look at anything else the price to change is significantly more than a CLAAS.
“More important than any of that is the back-up we get from our dealer – MANNS. Our relationship with them is really strong, from the storemen through to the sales guys and fitters.
“If we have a problem we know we can pick up the phone at any time – evenings or weekends – and someone will be on hand to help us. And, if the issue can’t be sorted straight away they’ve
“Our 2017 AXION 870 was our first CVT tractor and it changed everything about the way our machinery is operated. It’s our main drilling tractor and for that it is perfect – you just set your target speed, adjust the engine droop settings to suit the terrain and soil conditions and let the CMATIC gearbox sort the rest out. Then if you need to tweak things as you’re going along it’s simple.
“Our second CMATIC tractor was our 930. Its operator is very focused on getting the most out of the machine and is constantly fiddling with the settings to fine tune it. The stepless CVT box means you’re able to find the optimum balance between output and fuel use – ultimately we’re covering more acres in a day while burning less diesel.
“Our most recent addition is an ARION 660 CMATIC. It’s responsible for the lion’s share of the potato work – de-stoning, planting and harvesting. There was never any question that it would be anything other than a CVT – the stepless transmission means you’re always going at the right pace.
“We have a couple of tractors with HEXASHIFT powershift gearboxes and they’re perfectly good as all-rounders – real stalwarts for transport work. But you’d never do as good a job with them in the field as you would with our CMATIC tractors.”
LG Harrison and Son near Blakeney, north Norfolk
Farmed area
810 ha
Machinery
AXION 930, 870, 810
ARION 660 and 630
CLAAS LEXION 750TT
Livestock
50 x Sussex suckler cows plus followers
Cropping
Spring barley 240 ha, Winter wheat 120 ha, Winter barley 135 ha, OSR 50 ha, Sugar beet 70 ha, Potatoes 60 ha - Remainder in permanent pasture and land under HLS conservation schemes
Staff
Matthew and Philip Harrison plus another 3 full-timers.
You’d never do as good a job with a HEXASHIFT in the field as you would with our CMATIC tractors.
“I have known Maurice Kelly from KELLYS of Borris for a long time and there is a lot of trust there. They have a great deal of experience with the products they are selling and with their scale will never see you stuck.
“We have run various CLAAS combines for a good few years, so CLAAS tractors were certainly worth a look. I needed something that was value for money as this tractor would be staying on its narrow wheels all year round pulling a trailed fertiliser spreader and sprayer, the other two tractors would do the heavy work.”
So in 2015 the first CLAAS tractor – an ARION 650 HEXASHIFT–arrived on the farm and has performed admirably. When it came to replacing one of the other more powerful tractors, the decision was an easy one – another CLAAS and the first AXION,
When it came to getting a third tractor to meet an expanding workload, Carlow grower John Foley decided to see what his local CLAAS dealer had to offer. The main duties for the new tractor would be spraying and spreading fertiliser on the arable enterprise, while two other tractors would tackle the cultivations and drilling as well as the bulk of the haulage work.
“The tractor practically drives itself!”
John Foley & Sons
an 870 with CMATIC stepless transmission. This has since been joined by another 870 to pull the wider cultivators and drill that demanded more power.
“The CMATIC transmission just adds to the comfort, reducing the stress and workload. You never have to think about changing gears as the tractor is constantly doing this for itself. I just set the target speed and it runs to the maximum pre-set engine revs which I tend to set at 1,900 to 1,950 rpm.
“The ease of use has to be the biggest benefit of the CMATIC box and you are always running at the right speed. Even with different operators, the tractor always works the way you want it to and you can change the ranges and settings while the tractor is under load.
“Working together, the CVT gearbox and GPS auto-steer mean less fatigue allowing the quality of work and implement settings to become your primary focus – the tractor practically drives itself.”
The experience of owning and running the CVT-equipped 870 meant there was no debate when it came to changing the business’ powershift ARION 650. Earlier this year it was replaced by an AXION 830, also fitted with a stepless CMATIC
box. Partnered with a new, larger 6,000-litre sprayer and a bulk spreader which can hold up to 10 tonnes of fertiliser, it is now always on top of the job.
“The smoothness of the CMATIC transmission has already proved to be a real benefit when spreading fertiliser, as it smoothly slows down when approaching the headland giving the spreader time to maintain the rate and the same when returning back to work. I can easily flick between range one for the headland turn and range two when back in work and get quickly back up to 16 km/hr.”
All three AXION tractors have the CEBIS terminal, the newest 830 with the touchscreen version. The ISObus-compatible display is also used to operate the spreader and sprayer, with the application map shown on the larger S10 terminal and the machine controls on the CEBIS screen.
“Both screens are just so intuitive to use with little prompts to help you – you don’t need to read the manual to operate these tractors. I can easily assign the different functions to the F-keys so I never have to take my hand off the CMOTION joystick.
“With all three tractors now running similar controls, you get to know how to operate them to get the best of their abilities.”
“We’ve seen how CLAAS tractors have really moved with the times. Each one we’ve had has been nicer again. With little changes and improvements, they are just getting better all the time.”
“You shouldn’t be married to one service provider, but it is hard to beat CLAAS machines and the service from KELLYS of Borris.”
Farranafreney Farming Ltd, Leighlinbridge, Co. Carlow
Machinery
2 x AXION 870 CMATIC
1x AXION 830 CMATIC LEXION 7400
Cropping
Winter wheat, Winter and Spring barley, Oats, OSR, Spring beans
Staff
John Foley, brother Tom Foley and William Walsh at peak times.
The ease of use has to be the biggest benefit of the CMATIC box.
John Foley
Central to this has been the arrival of a 445hp CLAAS AXION 960 TERRA TRAC. Where previously heavily intensive cultivation practices necessitated well in excess of 540hp and tractors with a track at each corner, the lower draft requirements of the new regime allowed the contract farming business to look at other options.
While a number of tractors were considered, the company settled on an AXION 960 TT for its ability to put power to the ground in an efficient way.
“We felt the combination of wheels up front and tracks at the rear offered the best of all worlds, particularly when it came to running costs,” explains farms director James Green.
“We aim to keep our kit a decent amount of time to extract maximum financial value out of it but to do that we have to closely examine running costs – four-track machines have proved costly of late although we are still running one for the really heavy work.
“We have a fair bit of steeply rolling ground and plenty of heavy clay so traction is king. And of course moving to strip-till drilling means we have to be ever more aware of surface and sub-soil compaction.
“The CLAAS TERRA TRAC system is about the most reliable on the market – we’ve run with them on our combines for a long time and they’re pretty much bomb-proof – that gave us all the confidence we needed.”
“We’ve never run CLAAS tractors before but the back-up we get from MANNS at Market Harborough on the combines was enough to convince us. We have total confidence that we’ll be properly looked after by the Parts, Service and Sales departments.
“We took a six-year warranty and, having clocked 1700 hours in 18 months, the 960 hasn’t had a spanner on it.”
CLAAS TERRA TRAC system is about the most reliable on the market.
James Green
A move away from conventional crop establishment techniques towards a strip-tillage regime has seen a massive reduction in the horsepower required and diesel used at Conant Farming in Rutland.James Green and Michael Gardner
“Despite being 100hp less than my last tractor, the AXION pulls like a train. Even on our banks it doesn’t struggle with a 12m cultivator,” says operator Michael Gardner.
“And when it comes to traction it feels unstoppable – one of the first times I went out with it I forgot to put it in four-wheel-drive and it was a couple of hours before I realised. It just cruised on up our banks without scrabbling.
“Most of the time it’s hitched up to our 6m strip-till drill which barely ever makes it murmur. Having the stepless transmission makes it so much more adaptable – all the time I’m working in the field I run it in ‘Eco’ mode so the engine’s burbling along at 1600-1700rpm. I can switch to ‘Power’ and run at higher revs but I’ve never found it necessary.
“The transmission works out the revs required to keep going at the speed I set – even in tough spots I just let it get on and do its own thing.”
“While the intelligence of the gearbox undoubtedly adds to the AXION’s efficiency, it’s the weight saving that I believe is making the biggest difference,” says James.
“It is over 10 tonnes lighter than our four-track tractors. Not hauling all that extra weight about has had a massive impact on fuel use – we’re using between 15-20% less diesel than before.”
“I’ve got CLAAS’ S10 screen and RTK-corrected GPS steering which is so much easier to set-up and use than the system I had before,” says Michael. “Connected via iPad, it integrates seamlessly with SOYL’s system for variable rate drilling.”
“With our land shared between five estates spread across Rutland, Leicestershire and Northamptonshire we’re sometimes having to travel up to 18 miles.
“The AXION is an absolute pleasure on the road - the cab is so much quieter and more comfortable than our articulated machines. Having suspension on the front axle, under the cab and in the tracks, it doesn’t rock about and rides so much better.”
“The AXION 960’s performance has given us a lot of confidence in CLAAS tractors which we probably wouldn’t have considered before,” says James.
“We want machines that will do a decent stint with us without giving trouble. If the AXION continues with its current reliability we’ll certainly be looking at CLAAS seriously when it comes to changing our other tractors in the future.”
The Conant Farming Company, Lyndon near Oakham, Rutland
Farmed area
2,836 ha
Cropping
Winter wheat 1,234 ha, winter barley 396 ha, oilseed rape 416 ha, spring barley 39 ha, spring wheat 332 ha, spring beans 419 ha
Staff
Six full-timers plus one other part-time
Machinery
LEXION 8800 TT and 8900 TT
AXION 960 TT
SCORPION 7044
“The ability to work within any tramline width is a great advantage when it comes to compaction and working in growing crops,” says Tom. “There is no getting away from the fact that farmers see it as a big machine. But both the tanker and the XERION are fitted with 900 wide tyres, plus the weight is spread over four axles, so they are often surprised by how little damage it does.
Contract and share farming around 800ha of cereals based at Finedon in Northamptonshire, Tom Banks relies totally on digestate for all his wheat, barley, rye and oilseed rape nutritional needs, sourced from two local AD plants that take in food waste. In addition he also has application contracts with a further two AD plants near Oxford, from which digestate is spread on farms mainly within a five mile radius.
Central to the whole operation is a XERION 4200 bought in 2021, paired with a 28m3, tandem axle Kaweco swan-neck tanker, fitted with a 36 metre Vogelsang dribble bar boom with automatic section control and front-mounted turbo-filler.
In a season lasting from March to early October, the XERION/ Kaweco combination will apply in the region of 100,000 tonnes of digestate. Supported by a fleet of four nurse tankers, while the combination has the capacity to spread around 2,000 m3 a day, for planning the average is nearer 1,000 to allow for moves and delays.
“Because the plants mainly run on food waste, the higher protein in the substrate results in a digestate that is higher in nitrogen and trace elements. The digestate is almost the equivalent of a 10/5/5 depending on feedstock, so is a well-rounded product that has certainly added a lot of potassium back into the ground. Over the five years that we have been using digestate, we have seen soil indices rise from zero or even minus in some places, to plus three or four,” explains Tom, who adds that financially over his wheat acreage alone, the digestate has saved around £300400/ha in just nitrogen.
Tom and his team of drivers have all been impressed by how easy the XERION and Kaweco tanker are to operate, helped by the fact that everything is interlinked using ISOBus. This makes it easy to set-up and operate the tanker and boom via the S10 terminal and F functions on the CMOTION control, along with the GPS steering and, points out Tom, avoids having numerous terminals mounted in the cab.
For optimum flexibility, the Vogelsang boom can be used within any tramline width from 24 up to the full 36 metres, while the 16 sections with auto stop/start section managed by the section control function within the S10 terminal, ensure precise application.
“The ability to travel is important and in a normal season we realistically only have about 100 to 120 days when we can spread, so it is important that we can maximise output. Although it was expensive, I had autolube fitted to the tanker, which saves a lot of time, so the operator only really has to maintain the XERION and clean out the macerators. Having the filling system on the front of the XERION makes things much easier, and with a fill rate of 12,000 litres a minute, it takes minimal time whether we are filling from tankers or lagoons.”
While a tractor and tanker combination were always Tom’s favoured choice, he did also look at the option of running a self-propelled machine. “The benefit of the XERION and Kaweco tanker option is that if we want to upgrade the tanker in the future it’s very easy to just replace that element, while the XERION will always have a value as a tractor, and having the extra axles helps spread the load.
“The XERION is a fantastic machine to operate. It’s very comfortable and the visibility from the cab is excellent. Also, I like the fact that it has an all mechanical drive. Because there is little power loss, both the traction and fuel economy are superb. Reliability has been excellent and the old 2012 XERION 3800 that it replaced, which we used for primary cultivations and drilling, was just the same.
“All in all the combination of the XERION 4200 and Kaweco tanker makes it a fantastic bit of machinery for our operation. Despite its size, due to its manoeuvrability it’s surprising where it can get in, and because everything is interlinked it is just so streamlined and easy to operate.”
With the massive rises in compound fertiliser cost over the past year, the use of digestate has not only proved a massive financial benefit to Banks Farming, saving them in the region of £200,000, but also proved an invaluable aid for overall soil fertility and health.
I like the fact that the XERION has an all mechanical drive. Because there is little power loss, both the traction and fuel economy are superb.
Tom Banks
Carrying out silaging services throughout the length and breadth of the picturesque Warfe Valley, contracting outfit Brian Darnbrook runs all the way from Skipton to Harrogate and as far as York for maize work.
“We’ve had JAGUAR foragers ever since we started chopping in 2008,” says Guy Darnbrook.
“Our first new machine, a JAGUAR 860, arrived in 2013. We then stepped up to the 900 series in 2018 with a JAGUAR 950 model, which we replaced with another 950 this year.
“The 950 matches our customers well, taking into account clamp capacity, the number of trailers required and staff availability. It is a forager we can get all of the performance out of all of the time, not wasting any unnecessary horsepower as you might with bigger machines. Our new LINER 4800 rake really helps us with this. Being able to rake up three, four or five rows, it brings the best out of the forager in all conditions - it’s a very good combination.”
“We specified our new 950 with CLAAS’ QUANTIMETER yield monitoring and NIR sensing technology. We had a few customers enquire about being able to get this information from the forager and now it is a service which provides a good selling point for our business,” explains Guy.
The first customers that used the service reported back that the figures from the spout-mounted NIR sensor are very close to their in-clamp analysis.
Guy Darnbroook
“The first customers that used the service reported back that the figures from the spout-mounted NIR sensor are very close to their in-clamp analysis. Of particular interest are the dry matter and protein content numbers, which gives them an early heads-up as to their silage quality, from which they can start planning their rations. It’s also a good indicator if anything needs sorting out in the field, such as mole hills that can often cause contamination.
“As for the yield information from the QUANTIMETER, this really comes into its own when we are clearing maize, as it allows us to chop the right amount for the wagons which are hauling it away. When we are chopping for multiple customers in one field, it also makes it a lot more accurate for us to gauge how much we have harvested. It is early days with the system but so far we are pleased with it and our customers say it is accurate.”
“You just can’t beat the ease of maintenance on a JAGUAR 900 series - the swing out feed rollers make getting at the chopping cylinder so simple,” says Guy.
“They are also easy to operate, reliable, parts are readily available and the backup from RICKERBY is brilliant. While they are not our closest CLAAS dealer, they offer great service for the grass kit and are always just a phone call away.
“I believe the JAGUAR 950 is the ultimate grass machine - it’s the right size and the right price, offering a good balance of value for money and performance.”
Brian Darnbrook, near Ilkely, West Yorkshire Services
Silaging
Round and Square Baling
Muck Spreading
Slurry Tanking
Ploughing
Re-Seeding
Staff
Full time staff: Guy Darnbrook, his father Brian, son Robert, nephew Aston and operators Jamie Garnett (forager driver) and Richard Wallace (buckrake driver)
Part time staff: Up to seven extra people during the busy months
JAGUAR
With over 500 mouths to feed the Prichard family know the importance of making decent quality silage. To that end they’ve run their own forager for the last 32 years and last season took delivery of a brand-spanking new JAGUAR 840.
“Our old 2008-plate 850 had done 13 seasons and was just tremendous,” says Clive.
“In all that time it had nothing other than wearing parts – not one major mechanical breakdown. But going into its 14th year we felt we were pushing our luck and so we decided to change for a new 840.”
“On paper the 840 is a good match for the 850 on power – in fact I’d say it’s got a good bit more go in it. In truth it could do
the performance data and jobs lists. Having the additive dosing system integrated into the system means it’s straightforward to access and adjust – it is incredibly accurate.
“The new armrest is clearly designed by someone who has spent hours in the seat – little things like having the radio controls at your fingertips makes a big difference.”
“Compared to the conventional roller mill in our previous forager, we find the SHREDLAGE cracker tends to shatter the grain rather than cracking them.
“Its ability to let long fibres pass through without overloading the cracker means we’re able to run with longer chop lengths to maximise our milk solids. And critically there are no untouched grains – it’s doing a far better job than before.”
“Having had four-wheel-drive on our old 850 we would never have gone back. To say it gets you out of trouble isn’t quite true – we rarely ever come close to getting stuck, even with the wet conditions we often get here in South Wales.
“For hill-climbing it’s just brilliant, there’s no scrabbling”.
“Without doubt we are CLAAS men through-and-through and run a fleet of tractors as well as a TUCANO combine and the JAGUAR. That’s all down to the relationship we have with our dealer RIVERLEA,” says Clive.
CH Prichard and Son near Raglan, Monmouthshire
Farmed area
263 ha
Cropping
Winter wheat 28 ha, Winter barley 12 ha, Winter oats 12 ha, Forage maize 49 ha, Potatoes 2 ha, Short-term grass leys 28 ha - Remainder in long-term grass
Livestock
200 milking cows plus 300 followers (replacements and beef crosses taken through to finishing)
double the acreage we’re doing each season but because it’s never pushed it doesn’t clock silly hours and therefore it should do a good ten years plus with us.”
“The whole machine runs so much quieter than the old 850 and you really notice that up in the cab.
“The new CEBIS touchscreen makes it so much simpler to tweak settings on the move and it’s now so much easier to monitor all
Staff
Clive and Rob Prichard plus another two full-timers and a further two at busy times
Machinery
Forager CLAAS JAGUAR 840
Tractors CLAAS ARION 630, 530, 440, 410 and ARES 657
Handler CLAAS SCORPION 736
Combine CLAAS TUCANO 420 with 5.4m header
Based near Blackpool the contracting business W J Sanderson was started by Mr Sanderson senior back in 1952. Today the business is run by Mr Sanderson’s two sons Andrew and William, and it remains a full family concern.
The Sandersons’ first CLAAS forager, a new 62 trailed machine arrived on farm in 1980. This was followed closely by their first CLAAS self propelled forager, a second-hand JAGUAR 682.
Through the 1980s the family ran foragers from various manufacturers, before deciding to return to their roots with CLAAS, and they’ve never looked back. The relationship with their local dealer RICKERBY has been key to this long term return to CLAAS.
Now on their thirteenth JAGUAR, Andrew prefers to ‘skip’ the unlucky number thirteen, and counts his current machine as his twelfth – he’s run twelve self propelled foragers and one drag forager. His next new CLAAS self propelled forager he’ll count as his fourteenth – so missing out the ominous number thirteen!
(On another ‘numbers’ note, Andrew is also very influenced by the number 23. Born on the 23rd, his wife was born on the 23rd, engaged on the 23rd and married on the 24th (the 23rd was a Friday), Andrew’s latest forager has a 23 plate – he may not be superstitious but knows it will be hard for him to part with that particular machine.)
The backup is superb, as is the Parts availability, to keep us moving in the field as quickly as possible.
Andrew Sanderson
We asked Andrew what are the stand out features of a CLAAS forager to him. “A few things really” he commented, but reliability of the machines came top of his list.
“All machines break down at some point” he stated, “but the backup is superb, as is the Parts availability, to keep us moving in the field as quickly as possible”.
“Our latest machine came with the improvements to the cab with the new armrest and joystick, both of which I find really easy to use. I’m also impressed with how quiet the cab is now. Also the PREMIUM LINE wear liners we have had fitted in the last couple of machines have lasted really well and I wouldn’t think of not having it on future foragers as it keeps the machines’ running costs down.
“We feel like part of the family somehow, that we as customers really matter.” states Andrew.
“Resale values of the machines are very good and the product itself is just so reliable. That’s all to do with back up, parts, service, right through to the guys in the workshop.”
“Our relationship with our dealer feels like being part of a larger family. I had a problem with one of the harvesters, RICKERBY called Dean Cottey (CUK Product Manager, Foragers and Green Harvest) to discuss the issues we were having, and Dean turned up at the farm. I was so impressed with that level of attention and that he himself came out to see me.”
Andrew, his wife Susan and their son Robert were recently invited to the CLAAS headquarters at Saxham, to celebrate the sale of the 3,000th JAGUAR in the UK and Ireland to Andrew. The JAGUAR 880 had been given a unique special edition 3,000th ‘wrap’, which the family were delighted with. They also received a 1:32 scale model of the forager with the same unique wrap.
A great day was enjoyed by all, including the local RICKERBY Field Sales Manager Rob Bell and everyone agreed the new Saxham headquarters were “superb!”
Bought during the 2022 silage season, initially to boost mowing capacity, such is the output from a set of non-conditioner CLAAS DISCO 8500 Contour triple mowers that the rig now handles the lion’s share of contractor RM Simpson’s 800 ha mowing workload.
Based at East Bierley, Bradford, contractor RM Simpson offers a wide range of contracting services, covering West and South Yorkshire. Their diverse customer base, which includes dairy, beef, sheep, arable and equine customers, can see them travel up 50 miles from their base. On top of this, they also contract farm 120 ha for a local estate.
“We originally started running CLAAS mowers about eight years ago and after a spell of trying other makes we soon came back to the CLAAS machines - we wouldn’t have anything else now,” explains operator Harry Fairbank. “As well as their good performance, they are very well made and we get great backup from our dealer, CLAAS EASTERN at Wilberfoss.
“Up until the arrival of the non-conditioner mowers, we relied on a pair of front and rear mounted DISCO 3200 conditioner mowers. However, with all the foraging and baling last year, we were struggling to keep up. That’s when we decided to increase capacity with a set of non-conditioner triple mowers - a DISCO MOVE 3200F on the front and a DISCO 8500 Contour on the back.
For us, they have boosted capacity, saved time and diesel, and reduced maintenance.
“As well as looking for greater capacity, we went for nonconditioner mowers for a number of reasons,” says Harry. “For starters, we didn’t want to buy something that would then need a bigger tractor to run. By going wider with the new mowers, but not having conditioners, it means we can use the tractors we already have and keep the ability to swap the tractors between the mowers.”
“As we’ve found, it takes about the same amount of power to run a set of non-conditioner triple mowers as it does just a set of front and rear conditioner machines,” says Harry. “For the triples, 180 to 200hp is a good match - 230hp is on top of the job. And because you are mowing 50% more using the same power, fuel use per acre is also less.
“Throughput of the triple mowers is very good - I can mow up 20kph on good land, which sees about 6.5 ha per hour comfortably mown, compared to 4.5 to 4,8 ha per hour with the front and rear conditioner mowers.
“All of our CLAAS mowers offer good contour following, which is great for coping with rough land. In particular, the new suspended-type DISCO MOVE front mowers follow the ground much better compared to our previous push-types.
“Cut quality is excellent and they tackle laid grass very well. Likewise, they can handle a wide variety of grasses, from big stalky, singe-cut crops, to short, multi-cut silage.
“For delicate crops where you want the leaf intact, the nonconditioner triples have proven useful for this, and I was able to leave a long stubble height of five inches. You could easily see this being useful for mowing crops like lucern.
“Firstly, non-conditioner mowers are just so simple - there’s no conditioner to maintain, there’s less shafts to grease, you’re less likely to damage them from foreign objects and you don’t get stone damage to the hoods. They are also relatively light - they don’t feel like a big lump on the tractor.
“Like all of our CLAAS mowers, they are quick to set-up - orange markers enable you to quickly and accurately get your linkage height right. Bed pressure is hydraulically adjusted - you actually need a little less with the non-conditioner mowers, because they are lighter.
“Quick release blades make them easy to swap, and there’s lots of blade storage on the machines. Bed access to the non-conditioner rear mowers is good, as the guards in front of and behind the beds can be folded up. And the mowers can be stored in the shed folded up, saving floor space.
“In all, these new non-conditioner mowers have been brilliant. We’ll definitely be looking at another pair, possibly larger, when it comes time to trade them in.
“For us, they have boosted capacity, saved time and diesel, and reduced maintenance.”
RM Simpson, East Bierley, Bradford Services
Grassland applications
Tillage applications
Contract farming
Gritting
Forestry
Staff
Six full time and up to 10 part time
CLAAS History
DISCO 8500 CONTOUR (non-conditioner) ‘butterfly’ mower
DISCO MOVE 3200F (non-conditioner) front mower
DISCO 3200C CONTOUR (conditioner) rear mower
DISCO MOVE 3200FC (conditioner) rear mower
2 x LINER 2800 twin-rotor rakes
LINER 4800 four-rotor rake
2 x JAGUAR 870 foragers
DIRECT DISC 520 whole crop header
ORBIS 750 maize header
Complimenting his long-standing recycling business and successful egg production enterprise, which produces 6,000 eggs per day, Phil farms 52 ha on the outskirts of Manchester, rearing 150-head of cattle and 100 sheep.
“When I bought the baler, there was no question that it was going to be anything other than a CLAAS machine, simply based on the great service that I get from my dealer, RICKERBY, now with a depot at Burscough,” explains Phil.
“Producing about 1,200 bales per season, I’ll be the first to admit that buying my own combi-baler is a bit of a luxury for this size of business. But it does mean we can go baling exactly when we want to. And when you cost it out compared to the price of using a contractor over a period of time, the numbers do stack up.”
Phil’s baler is specified as a ‘film on film’ machine, which applies film wrap in the bale chamber rather than net. “This means we can keep film use down – only applying two and a half layers in the chamber and another four layers on the wrapping table. But crucially, the bales keep really well with excellent bale quality and no spoilage. It also means we have only one type of plastic waste to deal with.”
Bales produced are like bricks, says Phil. “In our first year using the baler, the bales were actually too hard for our diet feeder to handle. As such, we lowered the chamber pressure in the second year, from 180bar to 120bar, which makes an ideal bale for the diet feeder, while maintaining their shape throughout winter with good square shoulders.”
Operator Rhys Woodward adds: “After two seasons of use, the baler has been reliable. In good conditions, it can produce about 40 bales per hour.
“The wrapping table easily keeps up with the throughput of the baler and is not upset by any of the hills that we have to work on. To prevent bales from rolling away, the baler is also fitted with a ‘kicker’ that puts the bales on their ends.”
For the last two seasons, the baler had been paired with a CLAAS ARION 650, which handled it comfortably, says Rhys. “This year (2023), it will be used with an ARION 660 CMATIC, which should be good for achieving the ideal baling speed.”
One of the baler’s stand-out features is its Maximum Pressure System, which sees three of the chamber’s rollers swing into the chamber, says Rhys. “This helps get the bale formed initially, then keeps pressure applied to the bale to get good bale density.
“Everything we bale for ourselves is chopped - mainly using all of the baler’s 25 knives. This produces a very dense bale, but is easy to feed out. If conditions get too dry, we will then switch to using 12 or 13 knives - simply selected via the control box.
“To prevent the bale from ‘bursting’ when feeding out, the baler also has a good feature whereby the knives automatically retract when the bale is nearly complete, leaving the outer part of the bale unchopped.”
Phil concludes: “Overall, I’m very pleased with the baler - it does a great job, produces dense bales with no waste, keeps wrap costs down and has lots of capacity.”
Middleton, Manchester
Farmed area
52 ha
Livestock
150 beef cattle
100 sheep
Staff
20 across all businesses
CLAAS History
ARION 660 CMATIC tractor
ARION 630 tractor with loader
DISCO 3200FC PROFIL front mower
DISCO 3200C CONTOUR rear mower
VOLTO 52 tedder
Taking control of his own baling operation, livestock farmer Phil Dickinson bought his first combi-baler in 2021 in the form of a CLAAS 455 UNIWRAP. And already the investment is paying dividends, not least financially, but also in the quality of the bales being produced, he says.
It does a great job, produces dense bales with no waste, keeps wrap costs down and has lots of capacity.
Rhys Woodward
Based at Micheldever Station in Hampshire, with two further stores at Membury on the Berkshire Downs and Shrewton near Salisbury, the Micheldever complex comprises of two on-floor stores holding 12,000 tonnes and 44 bins, giving them a total nominal wheat capacity of 63,000 tonnes. Serving 100 members, typically wheat accounts for about half of the total stored each year, followed by malting barley, oats then beans.
A ‘70-plate SCORPION 746 VARIPOWER is the latest in a long line of SCORPION handlers to be operated by the company, sourced through local dealer OLIVERS just a few miles down the road near Winchester. Powered by a 143hp Deutz engine with DYNAMIC POWER and 240 bar load sensing hydraulic system, the SCORPION has a maximum load capacity of 4.6 tonnes and can lift to 7.03m.
“We tend to change the SCORPION handlers about every four to five years, by which time they will have only done about 2,500 hours, and with each machine we have seen an improvement.
We certainly don’t test the machine to its limits. It doesn’t do any pulling or digging, just loading grain, so they make a good buy for someone and our last SCORPION is now on a local dairy farm,” says Store Manager Bill Fife.
“During harvest when grain is coming in, even though the store is very busy, the SCORPION is fairly quiet and mainly used to just move around a large vacuum or IBCs, or to just finish filling the stores. However, once we start emptying the flat stores, that’s when we need the SCORPION to perform reliably and to be there when we need it.”
Bill adds that the load-sensing hydraulics ensure that there is always plenty of hydraulic power available and makes operating the SCORPION very smooth. This, combined with the SMART LOADING function which allows the operator to pre-set loading height, makes loading and manoeuvring in and out of the stores straightforward and has enabled him to load up to 20 lorries in a morning when necessary.
“The SCORPION gives us the capability to shift a lot of grain off the floors very quickly and to load lorries in no time. This is important because at times we could have a boat load of 2-3,000 tonnes going out of Southampton, which means that we will need to load 70 to 80 lorries in a couple of days. Also, if the market comes right or, if like last year, we start running short of space, we may suddenly have perhaps 8,000 tonnes that needs to be loaded out.
“Compared to the original handlers of 10 to 15 years ago the new Liebherr built SCORPION machines are very capable and the cab and operator environment is superb. There are three drivers who mainly load the lorries, plus a couple of extras, so having the colour coding in the cab makes the controls very self-explanatory and easy to operate. Even though it was never a problem with our older machines, it’s noticeable that the new 746 feels far more stable. Also the grill has been redesigned so that the upward visibility is far better, plus the air conditioning unit is very efficient. Apart from one machine that had overheating problems due to the dust, which was quickly sorted out, reliability has always been good and OLIVERS are always quick to sort out anything we need.”
SCORPION machines
are very capable and the cab and operator environment is superb.
Bill Fife
Farming 1,200ha spread over six main holdings in what Laurence Matthews describes as prime commuter belt near Dorking in Surrey, having the two SCORPION handlers reduces the need to move machines around on what are often very busy and congested roads.
“The SCORPION handlers are on the go constantly and I work on the basis that each machine will do at least 1,000 hours a year. We have around 500 cattle spread over the six farms, plus three grain store sites, so there is no way that we could run just one telehandler.
“We have a large number of attachments which for both efficiency and safety when on the road, are left at each farm. Also during the autumn when we are handling grain but also muck spreading, it means that we can have a dedicated machine for each job. Some of the attachments date back to when we ran Matbros so each SCORPION is always specified with a Matbro headstock, which I still think is a very simple and brilliant system.”
In addition to the cattle, which includes a suckler herd of Belted Galloways that are used for conservation grazing on the North Downs, the farm, which is within the Surrey Hills AONB, also
Early March saw EDG Matthews take delivery of two new SCORPION 741 VARIPOWER telescopic handlers, making these the fourth pair of SCORPION machines to be run by the company over the past 12 years.The 500 cattle on the farm include a suckler herd of Belted Galloways for conservation grazing Laurence Matthews
grows a wide range of cereal and forage crops, plus a large area is managed under stewardship and HLS schemes.
The policy is to renew the handlers, which are contract hired through OLIVERS at Petworth, every three years. The two new SCORPION 741s, which have a maximum lift capacity of 4.1 tonnes with a lift height of 6.93 and are powered by a 143hp Deutz engine, replaced a pair of 736s, which in turn superseded two 7035s.
“Because of the amount of work they do, I need a machine that is both reliable and will do what it is supposed to do. But allied to that is the knowledge that if there is a problem that there is the service and reliable back-up to ensure that we are not left in the lurch,” states Laurence. “By contract hiring, this means I know exactly what each machine is costing me and the only additional costs are insurance and fuel, which is also monitored so I have an accurate running cost.
“In these days of dealer consolidation it is important to me that I have the confidence and reassurance that the support and service will be there when I need it. That is the reason we have run CLAAS combines for so many years, and have a new TRION MONTANA arriving for this year, but also now buy all our tractors
and the handlers from OLIVERS and Southern Harvesters before them. It’s all about the relationship we have with the dealership. But having said that if I wasn’t happy with the SCORPION they wouldn’t be here.
“Physically the SCORPION 741 is the ideal size as we have a complete range of buildings and size, and by replacing them on a regular basis this ensures that they are kept new and fresh, and keeps everyone happy.”
The SCORPION handlers are on the go constantly and I work on the basis that each machine will do at least 1,000 hours a year.
Laurence Matthews