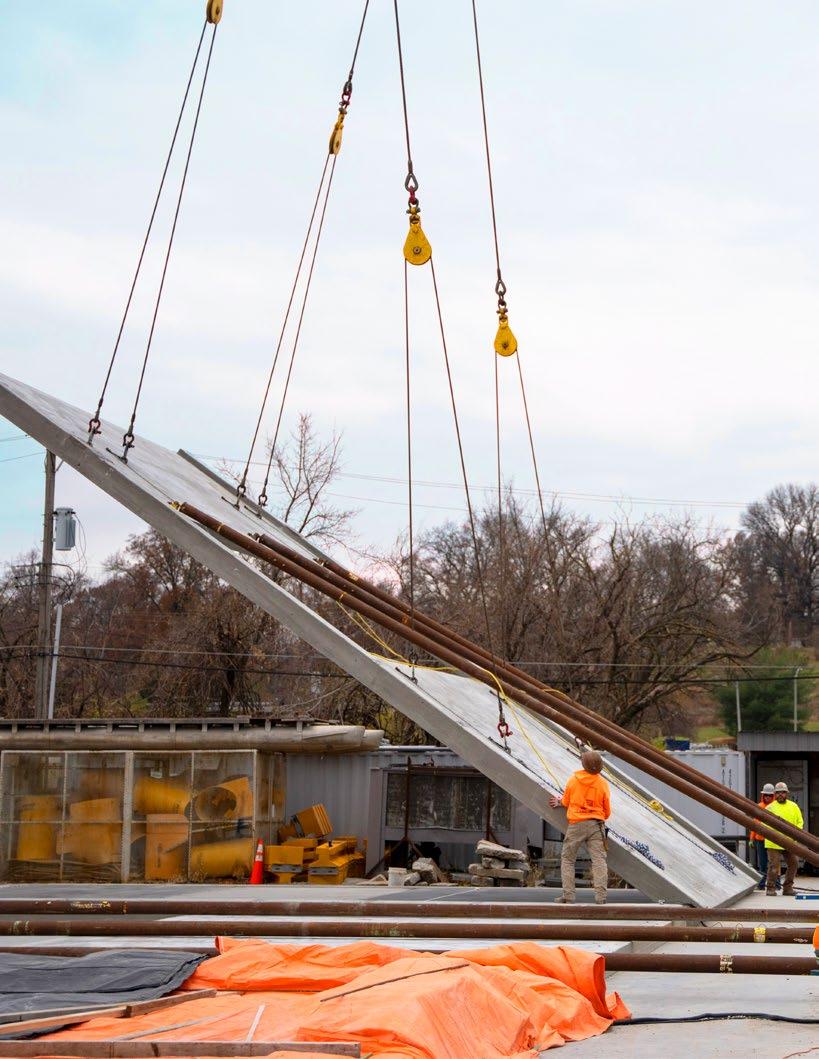
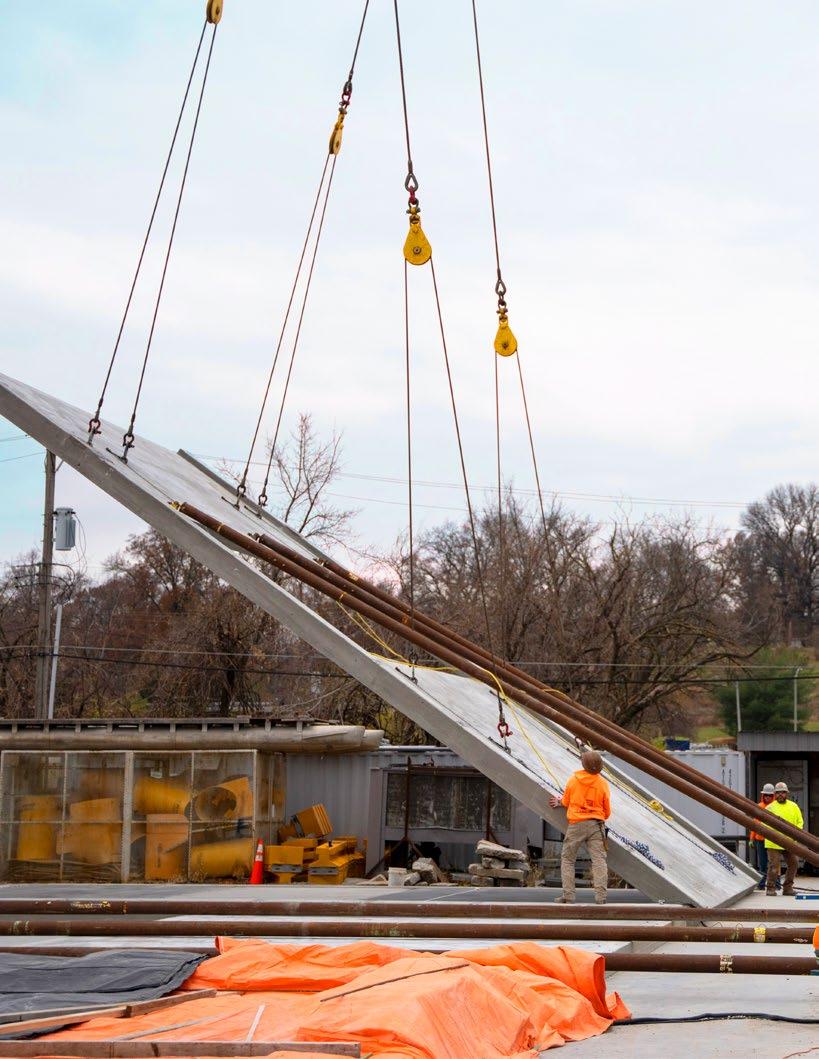
I. Executive Summary
In November 2023, a team consisting of representatives from Clayco Construction, Concrete Strategies (CSI), Wiss Janney Elstner (WJE), a confidential data & web services client, Ozinga Concrete, and Kienstra Concrete cast three experimental concrete tilt-wall panels to compare performance between common and innovative concrete mixes, each of which achieves varying levels of embodied carbon reduction when compared to industry average benchmarks and mixes with higher portland cement contents. This work was partially funded by the client and various research/NGO groups: Breakthrough Energy Foundation and Climate Works Foundation.
THE GOAL WAS TO PROVE THE APPLICABILITY OF LOW-CARBON CONCRETE MIXES FOR USE IN FAST-TRACK TILTWALL CONSTRUCTION. Tilt-wall construction is typically schedule-driven; the use of high early-strength concrete mixes to facilitate “tilting” or erecting of the wall panels within an aggressive construction schedule is often necessary. Wall panels are typically tilted 5-7 days after pouring, but sometimes as early as three days. Conversely, the use of Supplemental Cementitious Materials (SCMs) in lowcarbon concrete mix design many times will extend the traditional strength gain curve of traditional portland cement mixes.
Three panels were constructed in the Concrete Strategies’ St. Louis test yard. They were built to a design provided by The client, representing a typical Data Center wall design.
CEMENT TYPES FOR CONCRETE MIXES EVALUATED
Type
Baseline NRMCA V3.2, Great Lakes Region
type 1L cement, Holcim St. Genevieve Plant
Panel 2
Panel 3
RESULTS
cement - 25% blast furnace slag, 75% type 1L cement, Holcim St. Genevieve Plant
Proprietary blended 1157 cement mix 1
All three mix designs were able to be pumped, placed and finished in the field. Panels 1 and 2 attained adequate compressive and flexural strength to facilitate erection on day 3. Although panel 3 demonstrated adequate strength gain on day 3 when laboratory cured at room temperature, the cold temperatures during the pour retarded the strength gain for this specific mix. Panel 3 attained strength on day 7 and was erected on day 8.
MAIN TAKEAWAYS
• Panel 2 represents the successful use of a high-early strength mix with approximately 40% embodied carbon reduction versus the NRMCA 3.2 baseline. This mix can be implemented successfully on construction sites in all weather conditions and gain adequate strength to facilitate 3-day erection.
• Panel 3 is a mix that will aggressively reduce embodied carbon by 64% and could be implemented on the client's construction sites in warmer temperatures. Further testing will be completed to determine applicable temperature ranges.
NEXT STEPS
• Perform further testing to isolate applicable temperature ranges for 1157 mix designs in varied domestic climate locations.
• Produce matrix outlining mix proportions and carbon reduction vs. applicable temperature ranges.
• Further education/training for placing and finishing crews on low-carbon mix designs.
II. Introduction
This report details procedures followed in the field to facilitate the construction of the three experimental concrete tilt-wall panels. Information will be given on quality control procedures, material verification, finishing equipment/methodologies, and curing methods. Pour conditions, erection procedures, and observations from laborers involved in the placement, finishing, and erection of the panels are included. Preparation of samples sent to the lab for testing will be described.
BACKGROUND
In the summer of 2023, Ozinga concrete approached Clayco construction with an opportunity to partner with the not-forprofit climate group Breakthrough Energy to assist in “eliminating barriers associated with the implementation of low-carbon concrete mixes.” Clayco construction and its in-house concrete subsidiary Concrete Strategies (CSI) expressed interest in investigating what it felt was the largest barrier to low-carbon mixes: high early-strength gain. Clayco then approached the in-house Data Center design team for this confidential client, to gauge interest in piloting lower-carbon mix design. Climate Works Foundation also engaged at this point, in support of The client and their review, and in collaboration with the Breakthrough Energy Foundation team. Ozinga had recently tweaked the formulation of a proprietary blended cement (formed to ASTM 1157 standards) and had begun to test its performance in foundation and slabs. CSI offered the use of its concrete test panel yards in St. Louis to cast and erect full-height tilt wall panels to gather data on the suitability of the 1157 blended cement for use in tilt-wall construction.
THE CLIENT'S CHARGE TO GROUP
“Our company constantly seeks new concrete technologies which can help reduce our embodied carbon. Beyond materials commercially available at scale today, we realize the need to develop materials which provide further embodied carbon reductions in both the near-term and long-term. We are committed to partnering with contractors and suppliers to develop innovative materials and providing opportunities to further our progress toward net zero.” - Sr. Sustainability Engineer, Confidential Data and Web Services Client
ORGANIZATIONS INVOLVED:
Clayco
Large general contractor with a large industrial portfolio
Concrete Strategies
In-house concrete placement and erection subsidiary of Clayco
Wiss, Janney, Elstner (WJE)
Forensic engineering firm & Laboratory testing partner
SCI Engineering, Inc.
Laboratory testing partner
Ozinga Concrete
Ready-mix supplier (supplier of mix for Panel 3)
Kienstra Concrete
Ready-mix supplier (supplier of mix for Panels 1 and 2)
Breakthrough Energy Foundation
Technical guidance and material science inputs to testing program and report.
Climate Works Foundation
Technical guidance and engineering review inputs to testing program and report.
III.Mix Designs and Preliminary Laboratory Testing
The group agreed to test and compare three separate mixes, all at a compressive strength (f’c) level of 5,000psi. Mix parameters are as shown below in Table 1. Beyond pouring and erecting the panels, the group wanted to assess constructability aspects of the 1157 mix in the field.
Widespread implementation of mix designs is equally driven by constructability and engineering parameters. The ability of crews to place and finish elements in a timely manner is often overlooked but will make-or-break the use of mixes that perform well in laboratory settings. A key goal was to take statements from the pumping and finishing crews to document any additional effort or techniques needed to place and finish the 1157 mix in addition to the two other mixes.
As the third mix was a proprietary cement blend from Ozinga (Chicago-based) and the testing was to be performed in St. Louis, it was determined Ozinga needed a local counterpart in
the St. Louis market to procure and batch ingredients for panels 1, 2, and the non-cement ingredients for panel 3.
CSI chose to engage Kienstra ready mix as the local partner. On the day of the pour, Ozinga quality managers worked handin-hand with Kienstra staff to ensure mix proportions were correct. It is notable that two companies who are often in direct competition with one another worked together to further lowcarbon concrete knowledge.
In the St. Louis market, ASTM Type I/II Cement was fully replaced by ASTM Type IL cement in 2023. Therefore, Type IL is regarded as the “baseline” for this testing. It is critical to note the 1L cement in these mixes comes from the Holcim St. Genevieve plant. Cement from this Holcim plant delivers roughly 25% less embodied carbon than industry average due to the regional electricity grid's utilization of renewable energy sources and this plant's modern and efficient operations.
Prior to field activity, Wiss Janney Elstner (WJE) performed laboratory testing on the mix designs. Two main goals were accomplished via laboratory testing:
• Establish maturity curve of 1157 mix.
• Establish compressive and flexural strength gain baselines in laboratory settings.
These results are documented and interpreted in the accompanying engineering report. It is important to note that in the laboratory setting at ambient temperatures, all three mix designs were able to achieve the dual lifting criteria within a threeday window.
IV. Panel Design Criteria
V. Lifting Design/Criteria
Concrete Strategies employed Leviat/Meadow Burke to perform lifting analyses on the typical panel designs to determine dual lifting criteria of compression strength and flexural strength. Many design and construction teams rely solely on compressive strength criteria. Concrete Strategies/Clayco recognize the maximum bending stress a panel will experience is during erection, and thus evaluate both criteria as a matter of course on all projects.
A further reason to use these dual criteria when testing experimental mixes is to provide an additional data stream with which to evaluate performance.
AS THE INDUSTRY VEERS AWAY FROM TRADITIONAL MIXES IN SEARCH OF LOWER-CARBON SOLUTIONS, TRADITIONAL CRITERIA AND RULES OF THUMB ASSOCIATED WITH PORTLAND CEMENT DESIGNS MAY NEED TO BE RE-EVALUATED.
LIFTING CRITERIA PER REPORT (TABLE 3)
These parameters were to be demonstrated via laboratory testing at SCI lab in St. Louis with samples collected in the field during the pour.
In addition to laboratory data, Bluetooth-enabled maturity sensors were to be installed within the panels themselves to provide insitu feedback on strength gain in the field. These sensors provide temperature data of the panels as they cure, which are then evaluated against the maturity curve to give real-time strength gain feedback.
As discussed in later sections, the data provided via these sensors would become key in evaluating the prescribed lifting criteria.
(Right) White wire and device SmartrockTM in-situ maturity sensor installed within panel. Smaller blue wires are for strain gages to measure stress levels within panel during erection process.
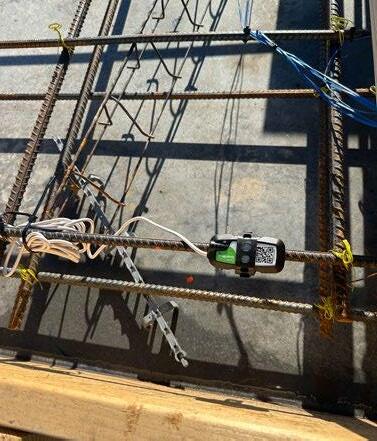
VI. Construction Schedule & Supplemental Materials
Concrete Strategies followed the below schedule in forming the casting slabs and test panels:
Oct. 25-30: Grading and set formwork for casting slabs
Oct 31: Pour strip footing for tilt panels to erect on
Nov. 15: Pour casting slabs
Nov. 13-Nov 14: Build forms for tilt panels
Nov. 15-Nov. 17: Install Rebar, lifting lugs
Nov. 20-Nov. 21: WJE Engineers apply panel instrumentation
CASTING SLAB/FORMWORK INFORMATION
Panel Layout
Based off the client's and MeadowBurke/Leviat drawings
Material for Formwork (2”x10”x16’) (2”x12”x16’) Lumber White Wood, (1”x2”x8’) Lumber Furring Strip, Nails, Nox Crete Select Joint Tape, 3 ½ gal. Sprayer Viton, Nox Crete Bond Breaker
Strip Footing 4000 PSI SR(Stone/Rock) NO AIR
Casting Slab Mix 3000 PSI SR(Stone/Rock) AIR
Rebar Layout
Subbed to American Steel Fab. not from the client
Pump Length 46 M
Link to pump truck parameters: https://concretestrategies. com/2023/03/46m-kcp-concrete-pump-rental
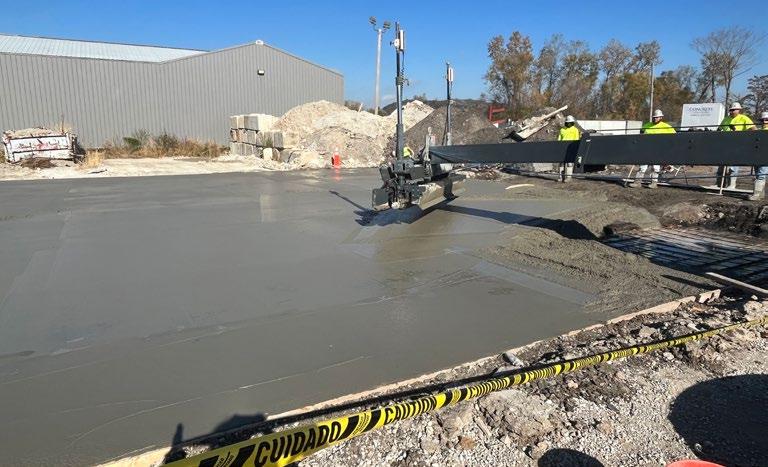
Casting slab placement.
VII. Test Panel QA/QC
There were two different inspections used for the tilt-up panels. The first was a pre-pour inspection. This inspection covered all of the formwork, rebar, openings and general dimensions of the panel. It also covered the location and type of all the lifting and bracing inserts. The second inspection was a “Day of Pour” Inspection. This inspection is intended to make sure that the crew
Prior to pouring the panels, the following QA/QC checks

is ready to pour and understands the plan as well as making sure the proper equipment such as vibrators, come-alongs, vibra-strikes etc. are all on site and functioning as well as having backups if needed. Other items were also checked such as truck/pump access, mix designs verification, checking weather conditions and making sure that any last minute issues like cleaning forms and clearing ice/water were addressed.

Scoping
Details
Auditor Samuel Klucker
Questions 1.
3.
4.
VIII. Laboratory Testing Plan
CSI worked with SCI Laboratories in St. Louis to test various concrete properties.
• Compression tests were performed in the lab on cylinder samples according to ASTM C39
• Flexural tests were performed in the lab on beam samples according to ASTM C78 (third-point methodology)
• Air content was tested in the both the lab and field according to ASTM C231
• Slump was tested in the field according to ASTM C143
• 15 cylinder and 7 beam samples were cured in the field.
• 5 cylinder and 0 beam samples were cured in the lab.
Field Curing Methodology: Panels were cured with WR Meadows 100 Clear Cure.
Lab Curing Methodology: Done per ASTM C31. For initial curing, the specimens were placed in a temperature controlled curing box.
These parameters were to be demonstrated via laboratory testing at SCI lab in St. Louis with samples collected in the field during the pour.
In addition to laboratory data, Bluetooth-enabled maturity sensors were to be installed within the panels themselves to provide insitu feedback on strength gain in the field. These sensors provide temperature data of the panels as they cure, which are then evaluated against the maturity curve to give real-time strength gain feedback.
As discussed in later sections, the data provided via these sensors would become key in evaluating the prescribed lifting criteria.
TESTING DAYS
Beams (Panels 1 & 2)
Beams (Panel 3)
*Note: All 28 day actions & testing were performed on day 29 (12/26) due to the holiday.
†Note: Panel 3 only.
While further discussed in the WJE Engineering report, compression strength cylinders for panel 3– both field and laboratory cured – exhibited results that did not correspond with the in-situ maturity sensors. It was discussed in detail with the team and surmised that the cylinder samples were adversely affected by cold temperatures during their collection. Although all applicable ASTM procedures were followed, the cold temperatures and relative small size of the cylinders in comparison to the overall mass of the wall panels provided inconsistent test results.

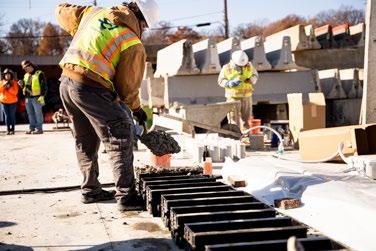
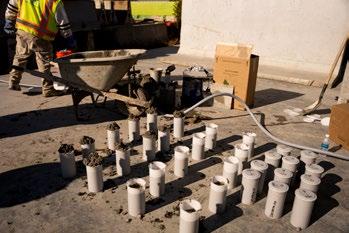
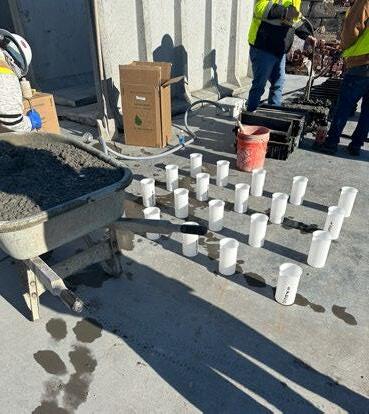
IX. Test Pour Conditions
On the day of the pour, conditions were cold and cloudy. Temperatures varied from roughly 37°F during the first pour to 45°F during the third pour. There was not a significant wind chill effect, with wind chill temperatures 1-2° colder than ambient temperature. The humidity was roughly 50%.
Concrete Strategies used several monitors to assess weather conditions and the necessity of cold-weather concreting procedures.
Device Name
PRO - 2730842
Device Model and Serial Number 5200L, 2730842
Session Name
Session - Nov 27, 2023 9:50:16 AM
Start Nov 27, 2023 / 9:50:16 AM
End Nov 27, 2023 / 10:22:52 AM
Duration 00:32:35
Logging Rate 5 seconds
Location Description
Location Address
Location Coordinates Notes Enter Notes
Session Statistics
X. Panel Concrete Placement, Finishing
&
Curing
Pump truck was a 46M KCI pump. Panel 1, as the “control” panel, was considered the baseline. It was mixed to roughly an 8” slump and was very workable in the field.
Approximate finishing time for each panel (from end of placement to final pass):
• Panel 1: 3 hrs
• Panel 2: 3 hrs, 10 mins
• Panel 3: 3 hrs, 30 mins+*
*Notes: The finishing crew was unable to put power trowels on Panel 3 by the time the sun was setting, so the decision was made to finish by hand and get blankets on to avoid losing heat. Actual final set time was in excess of the value noted.
The ASTM 1157 mix had an initial "false chemical set" once the concrete stopped moving out of the pump hose. It stiffened to the point where it was difficult to move by hand, but could be brought back with mechanical energy (i.e. vibrators or vibrascreed).
PANEL 1 PHOTOS
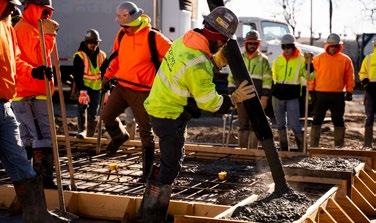
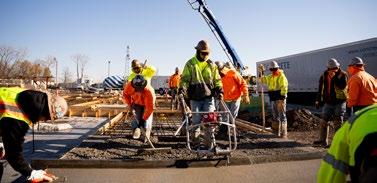
Finishing equipment utilized included:
• Bull floats
• 4’ power trowel machines, walk-behind type
• Hand Trowels (magnesium & steel)
• Vibrastrike
• Vibrator
CONSTRUCTION PROCESS COMPARISON
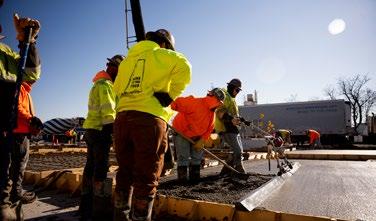
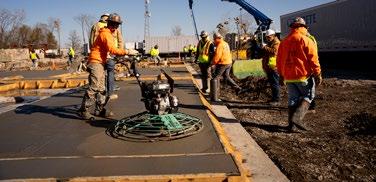
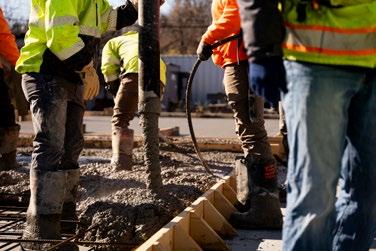
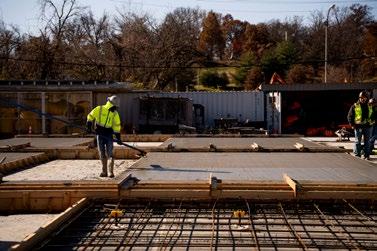
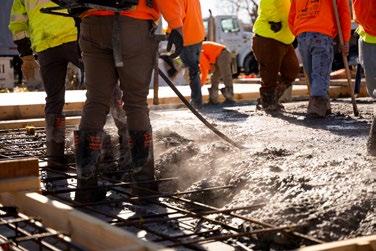
The following observations were noted for Panel 2:
“25% mix acted similar to standard. Placed, finished and cured the same. Less cracking that straight cement.”
“25% was not bad – placed and finished like straight cement.”
“25% mix gave the crew a bit extra time to finish, which was good. Still set and finished within a reasonable time.”
“A bit sticky and harder to finish.”
Concrete washout area demonstrating color difference between Panels 1 & 2 (darker) and Panel 3 (lighter).
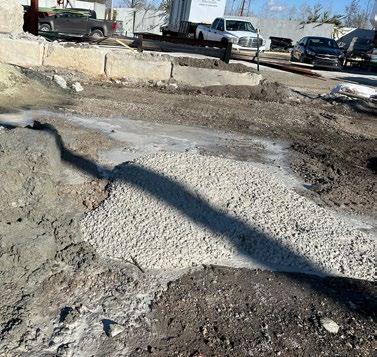
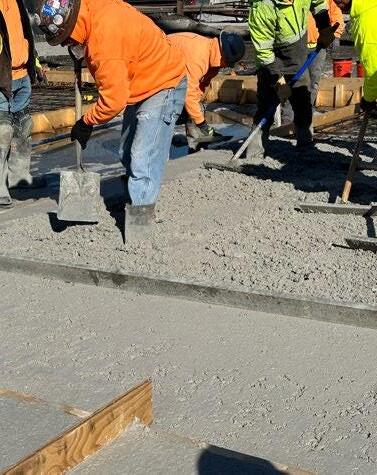
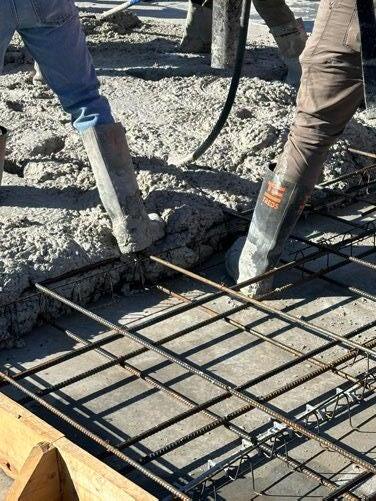
The following observations were noted for Panel 3:
“Difficult to place and finish”
“Very dry mix”
“Didn’t “mag up”” (It was hard on top but soft inside)
“Once you used the VibraStrike, it finished well. You need to keep it moving.”
“Would need more moisture to work well in the field.”
“Finished well – final product looked good. Difficult to pour, move around and place.”
“Seemed to set up hard on top but was soft underneath. Top inch was hard but you could put a dent in it.”
“Seemed to be about a 4” slump. Would need 6” slump at least to place and finish. Hard to move around.”
XI. Erection QA/QC
Concrete Strategies used a 350 ton hydraulic crane to erect the tilt panels.
Per the Critical pick plan, the total weight to be lifted on each pick, including blocks, rigging, and cables, was roughly 124,000lbs (65 tons).
The crane capacity at 45’ is 144,000lbs, making this a critical pick at 86% capacity.
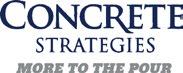
CRITICAL LIFT PLAN
-U
&
RE -C AST P ANELS
Project Name: AWS test panels
Project Location: St. Louis MO
Contractor: Concrete Strategies
Engineer: Leviat
Job No.:
Start Date: 11/30/23
Duration: 1 day Responsible for planning and conducting the hoisting operation Number of Days
Identity of Engineer or Engineering Firm, if required
Crane Owner: Barnhart
Primary Contact:
NOTE: The Information Source section must be completed to provide verification and documentation of each weight listed OR the Critical Lift Plan will NOT be acceptable.
Prior to erecting the panels, the following QA/QC procedures were followed:
• Rigging inspections
• Critical Lift plan was written and approved
• Rigging inspections
• Both compressive and flexural strengths were verified
• Lifting and bracing embed locations were checked, cleaned and prepped for use
• Braces were attached
• Crane radius and dimensions were verified
• All-hands Critical Lift Safety meeting was held
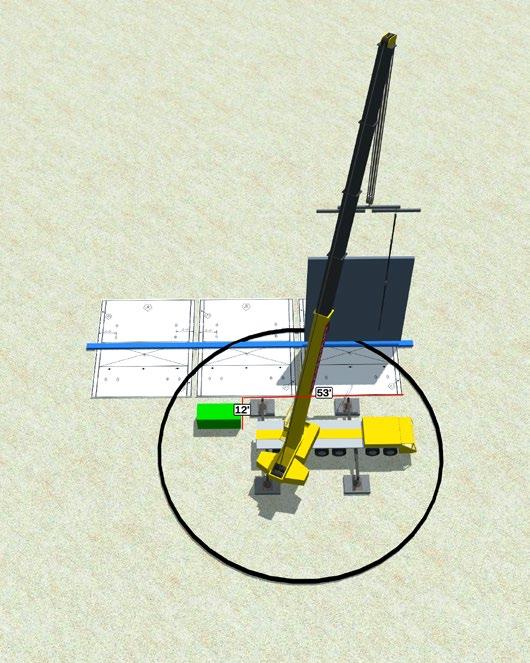
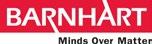
XII. Erection Field Notes
Panels 1 and 2 attained compression and flexural criteria in two days, and were erected on day 3 - Thursday, November 30. Notably, this represents the successful use of a 25% SCM mix attaining adequate strength to erect in a 3-day time-frame, even in cold weather conditions. As discussed in the Introduction, project teams have been hesitant to incorporate SCMs in schedule critical elements. This result provides the client an immediately implementable option.
In laboratory conditions, Panel 3 attained the necessary properties to facilitate erection within three days. The colder temperatures retarded the strength gain of this particular mix. Inconsistencies with laboratory break results led the team to ultimately consider data from the in-situ maturity sensors as well as a core of the in-place panel to verify compression strength. Considering all the data in aggregate, Panel 3 attained adequate compression and flexural strength to erect on day 7. It was ultimately erected on day 8 (Tuesday, December 5).
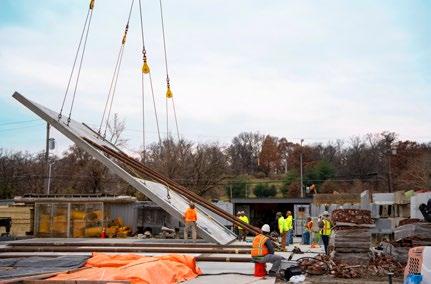
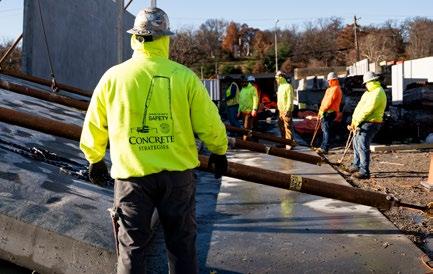
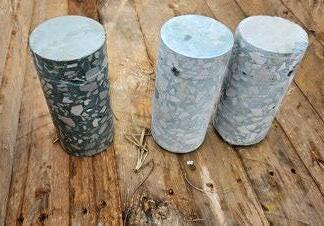
were taken from each panel to verify
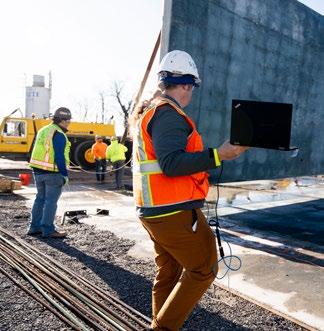
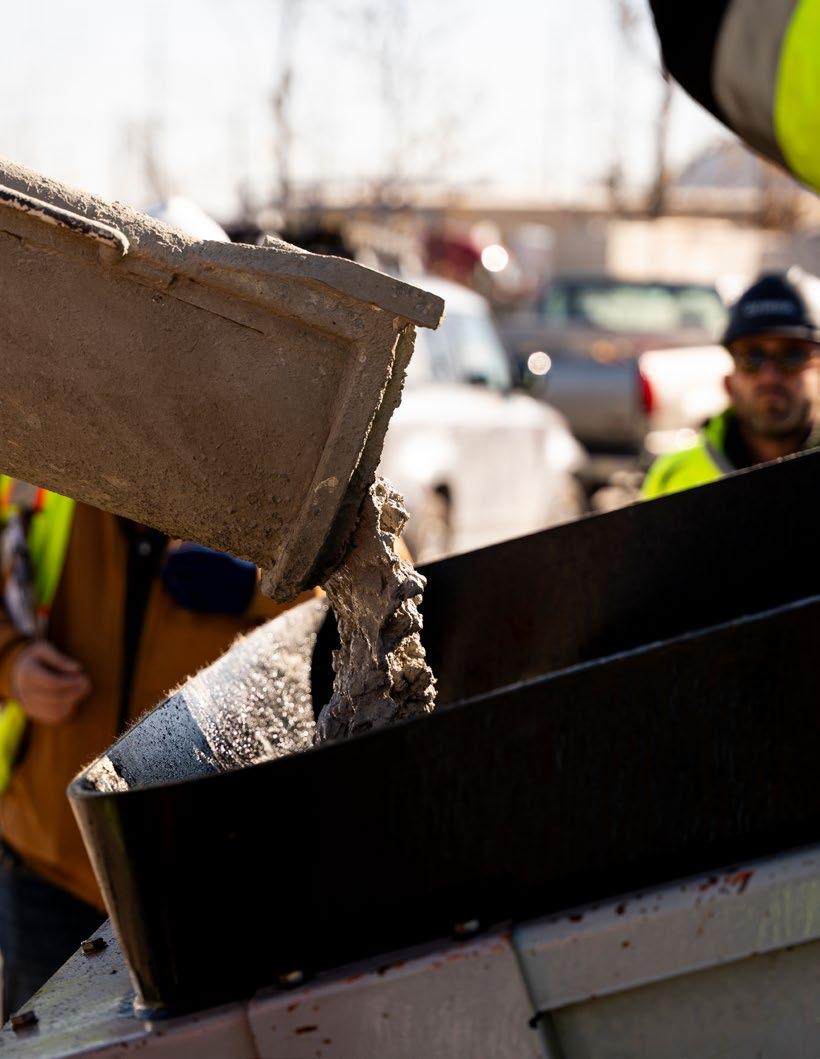
CONTACT KYLE KAMMER, P.E. Director of Quality KammerK@concretestrategies.com 816.797.4456 ERIKA WINTERS-DOWNEY, S.E., LEED AP BD+C Director of Sustainable Structures WintersDowneyE@theljc.com 816.501.8844