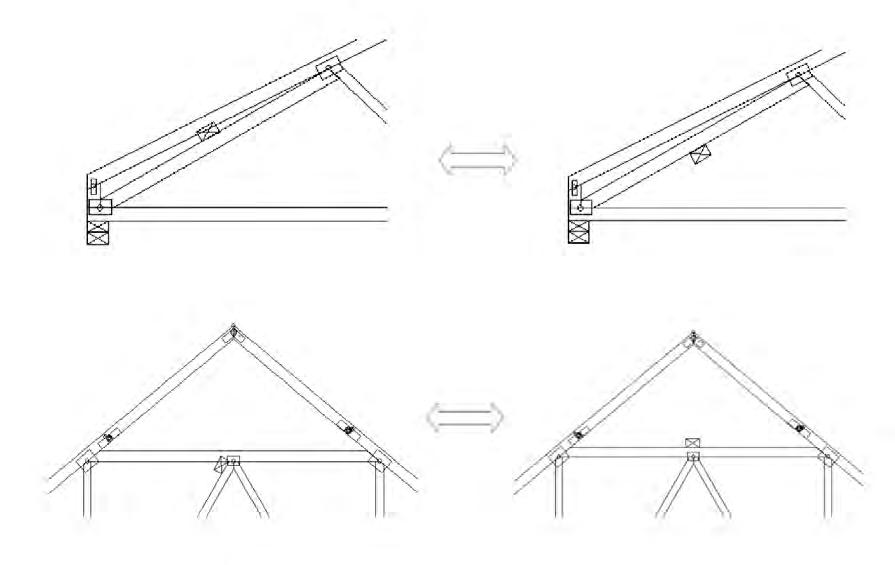
4 minute read
Bracing on Truss Design Drawings
Trusses are designed as individual components to resist the in-plane stresses resulting from the loads applied in the same in-plane direction. To resist out of plane forces, adequate bracing/restraint is required. In absence of designed temporary and permanent bracing plans, BCSI (Building Component Safety Information) is the industry bracing guideline that framers must follow.
Lateral Bracing/Restraint keeps the compression members of the truss from out of plane buckling due to applied loads shown on the Truss Design Drawing. Per ANSI/TPI 1 (National Design Standard for Metal Plate Connected Wood Truss Construction), it is the responsibility of the truss designer to provide required permanent individual truss member restraint location.
Bracing on the truss design drawing is denoted by the symbol " x ". Truss design drawings show the bracing to be located on a side of the member needing bracing/restraint. The actual application of the bracing, whether on the top edge of the member or on the bottom edge of the member, is not important. What is critical is the specific location (i.e., midpoint of the web member) of the bracing/ restraint and the number of rows. If the brace/restraint cannot physically be placed on the side of the member as the drawings show, then place it on the member at the same location except attach it to the opposite edge as shown below.
In some instances, interior webs or end verticals are braced by attaching approved sheathing to their edge such as the collar tie of an attic truss. When this is done, it should no longer be required to attach continuous lateral bracing in addition to the sheathing to the same member as shown below.
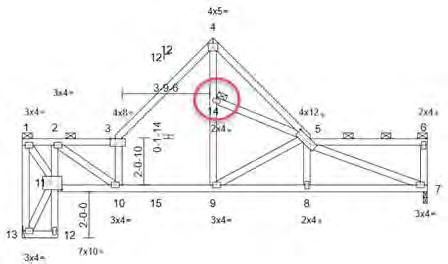

Truss top and bottom chord members shall be braced/restrained. If top and bottom chords are not sheathed, the truss design drawing shows the maximum unbraced length of the chords. Please note web-to-chord and chord-to-chord connections are always considered braced at those connections due to the continuous lateral bracing of the chords, web-to-web connections aren’t considered braced without the addition of a joint brace. Joint braces are not always feasible and are sometimes overlooked in the field. Care should be taken when designing web-to-web connections to ensure that buckling potential of webs will be resisted appropriately. The image below shows an example of this scenario.
For additional information, or if you have questions, please contact the MiTek Engineering department.
MISC.
Electrical Supply: 110 VAC
Motor: 1/4 HP, 110 VAC, Linear Actuator
Highly Accurate: +/- .010 Inches
Stop Rail: 2 x 4 x 1/4 Aluminum Extrusion

Stops: Jig Bored Steel
Stop Blocks: Machine Billet Aluminum
Internal Components: Hardened, Ground and Polished Steel and Billet Aluminum
Dimensions:
Length: 5 feet (60”) to 60 feet (720”)
Height: 12 inches
Depth: 12 inches
If you are looking for the fastest, most consistent way to measure and cut your product, then the Hain Measuring System (MEA) is your answer. The MEA changes from one length t any length instantly, up to 60’, without changing the operator’s position on the line. It is also highly accurate (+/- .010) and quickly moves from one length to the next in seconds. The MEA is designed for quick and easy setup and is simple to use. Even a first time user will be productive with little or no training required. It can adapt to any saw and can be mounted to any surface so that you can integrate the MEA with your existing setup. The MEA is versatile allowing “left” or “right” handed operation and measurement in “feet and inches” or “inches” depending on your preference. The MEA is also available in a “Skid Mounted” version.
HAINCOMPANY
6125 Enterprise Drive, Unit 9 | Diamond Springs, CA 95619 530.295.8068 | sales@thehaincompany.com
Used 2015 Woodrunner Lumber Retrieval System
The WoodRunner WR-2 lumber retrieval system seeks and retrieves the exact boards needed to cut. The core of the system is a trolley with an automated picking head. The trolley moves back and forth on a runway truss positioned over lumber carts while the picking head’s laser scans below. After locating the specific piece of lumber needed, the picking head uses a powerful vacuum to hold the board while moving it to the infeed deck.
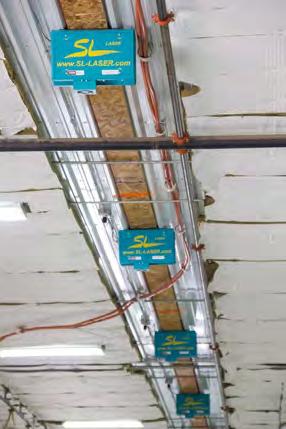
Call for Price
Eide Integrated Systems, LLC 612-521-9193 www.eidemachinery.com
New SL Laser Projection System
New, laser projection system from SL Laser. Projects roof truss, floor truss and wall panel design images accurately onto building surface, for faster setup and fabrication times. Each laser head provides 21' projection length (@15 foot ceiling heights). Includes system computer, cables, mounting hardware for attachment to customer's structure, factory installation, training and choice of green or red laser. Works with each connector plate manufacturer's design software. Modular nature of the laser heads allows for easy, future expansion of system length. 120 volt, 1 phase. FOB NC Wood Tech Systems 765-751-9990 www.woodtechsystems.com www.woodtechsystems.com
The
S erving the S tructural B uilding c omponent S i ndu S try
Purchased but never installed. Manual (x, y) movements, powered vertical movement. 15-ft wide bridge x 23 ft long x 14 ft height. Hoist moves at 16 feet per minute, includes pendant control, chain container and centering strap to minimize the need to reach for the control pendant. Last 3 photos show current condition & status. Other photos are of matching crane frame with hoist in place. 115 volt, 1 phase electrical required.
$16,690 FOB NV Wood Tech Systems 765-751-9990 www.woodtechsystems.com
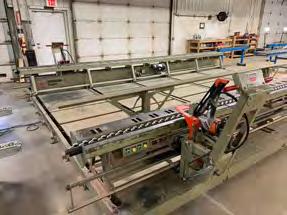
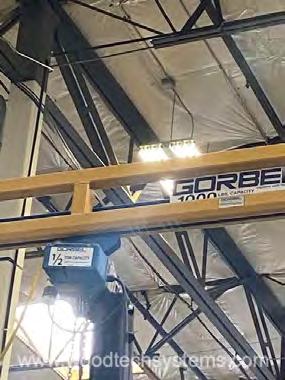
The Generation 3 Framing Table has adjustable 20’ long walls, with wall heights from 6’9” to 14’3”. Studs are placed between color-coded stud locators. With just a push of a button, the width adjustment clamp is activated to clamp and square all components. The Generation 3 Framer features a wider table top, designed with the framer in mind. Our new Anti-Slip Surface that allows the operator to work on a comfortable and safe surface. Call for Price Eide Integrated Systems, LLC 612-521-9193 www.eidemachinery.com
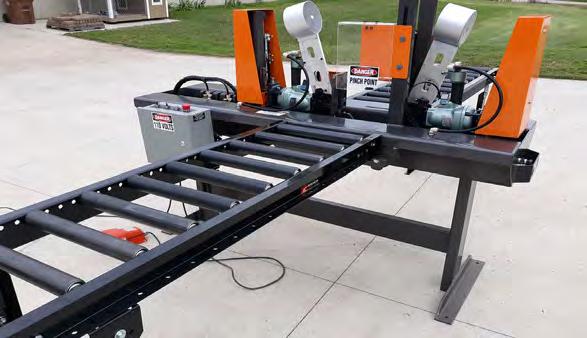
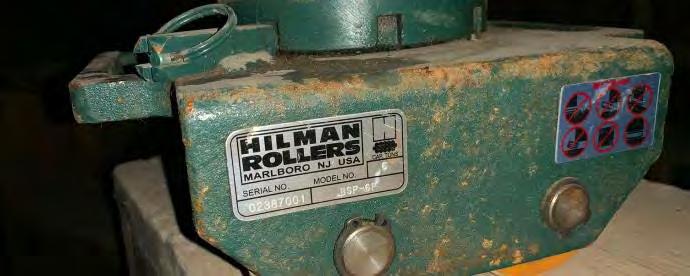
By Simpson Strong-Tie Staff