


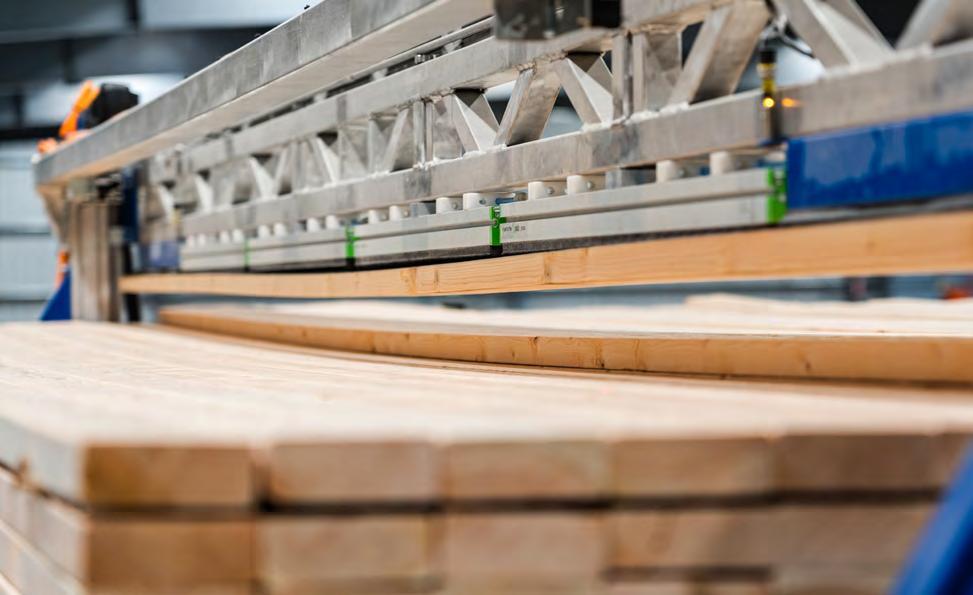
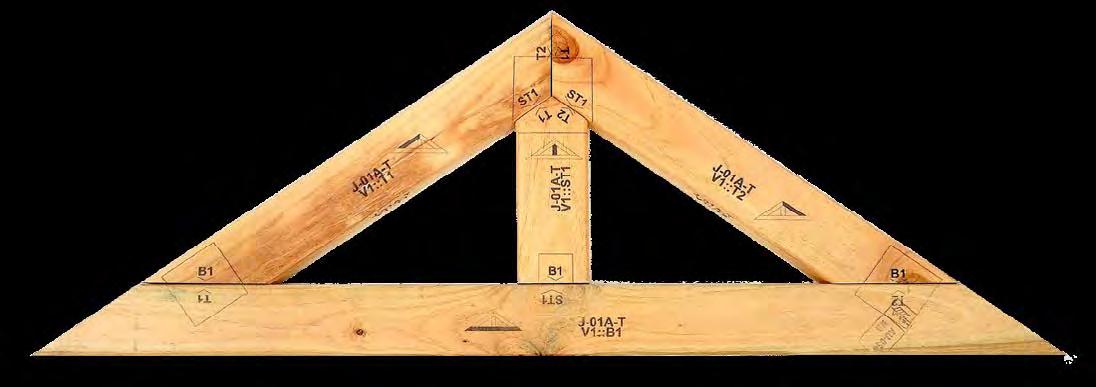
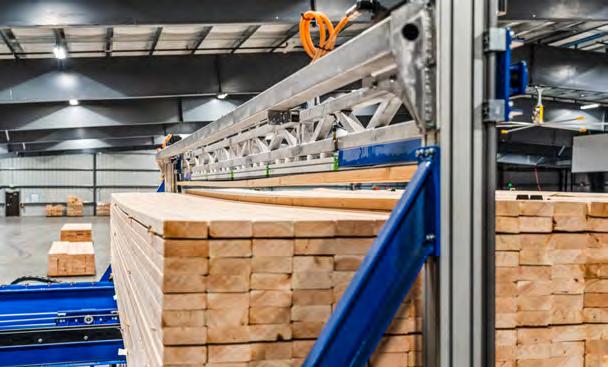
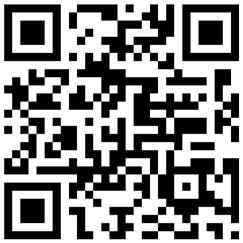
6
Anna Stamm – Advertiser Forum: Fall is for Follow-Up
Joe Kannapell: The Development of the Truss Plate, Part III: The Ingenuity of Carol Sanford and Cal Jureit
Wendy Boyd – Spida USA: BCMC 2022—What an Awesome Event
Todd Drummond Consulting, LLC: Including Meaningful Process Improvement on Your Capital Investment Checklist
Glenn Traylor: Are You Counting Your Teeth Correctly?
Tracy Roe – Eagle Metal: Perseverance and Success in the Components Industry
Edmond Lim, P.Eng. –LimTek Solutions: The Most Automated, Most Toured Truss Plant
A dverti $ er Component 72 77 80 86 90 95 98 103 106 122
Rob Bellian – Vekta: A Model of a Show at BCMC
Eide Machinery Sales Team: From Minneapolis to Columbus with Eide
Tim Kassa – Panels Plus: Going Platinum at BCMC with Panels Plus
Rod Wasserman – Wasserman & Associates: Displaying Our Family Pride at the Show
Steve Shrader – Hundegger USA: Getting Started with CNC Automation
Carl Villella – Acceptance Leasing: Added Value From Your Funding Source
MSR Lumber Producers Council: Because Good Ingredients Matter
Thomas McAnally – From the Road: The Best Laid Plans
Geordie Secord – The JobLine: Are We Selling Trusses or Lumber?
Michael Fagan – A-1 Industries: Building a 100-Year Company
Craig Webb – Webb Analytics: LBM’s Pace of Deals Hasn’t Slowed But Fewer Yards Are Involved
Randy Shackelford – Simpson
Strongtie: Hurricane Andrew — a 30-Year-Old Learning Experience
Joe Kannapell – The Last Word: The First Trade Show
From plans, to walls, to panels, and everything above. Introducing a new level of design tools, built from the ground up.
31,121
17,86,87
48,100
22,68
8,56
4,42,88
17,31,45,66,97
36,112
13,97
15,78
9,27,39,80,87
28,44,50
12,141
30,55,64,72
13,97
14,94,122,128
1,18,19,46,70,74
9,37,93,99
17,41,45,49,59,61,95,98,109,113
32,110
16,24
38,108,144
2,60,96
7,21,27,53,57,59,62,71,75,76, 77,85,101,105,109
49,89
21,23,29,37,39,40,41,47,49,53,54,55,57,58,59,61, 63,65,69,71,75,79,84,85,87,109,111
Thomas McAnally twm@componentadvertiser.org
Anna L. Stamm 800-289-5627 x 3 anna@componentadvertiser.org
Via e-mail subscription Download PDF or Read on line at www.componentadvertiser.com
News of Interest and Advertising inquiries can be submitted to: anna@componentadvertiser.org An Open Forum for many sources.
Deadline 20th of each month. Articles, Trade Names, and Logos are the property of their respective owner or creator unless otherwise noted
Disclaimer: We reserve the right to refuse any advertisement or material that we deem not in the interest of the industry or the Advertiser. Permission to use content is the responsibility of the contributor including permissions to use any likeness of persons.
The Advertiser is provided “As Is” including typographical errors, omissions, and mistakes both intentional and unintentional. Believe it at your own risk! 30,55,64,72 Copyright 2008-2022
Component Manufacturing
The Advertiser 411 Walnut Street #12250 Green Cove Springs, FL. 32043 no reproduction in whole or in part without
from the
advertiser
Archive Copies Available On Line www.componentadvertiser.com
As a follow-up to last month’s article, September is for Celebrating, I’ve realized that October should be the sequel. Indeed, as you’ll see from this month’s authors, there are many reasons to regard October as the perfect month for follow-up.
By all accounts, BCMC 2022 in Columbus last month was outstanding! Wendy Boyd from Spida describes it as “awesome” in her article. Tracy Roe from Eagle calls it “the best BCMC in almost two decades.” In the eyes of Rob Bellian of Vekta, it was a “bumper year,” and Tim Kaasa at Panels Plus had many “encouraging” conversations. The team from Eide Machinery thanks everyone for visiting both of their booths, and Rod Wasserman from Wasserman & Associates reminds us all how our industry is like a big extended family.
If you were fortunate enough to attend the show last month, be sure to prioritize your following up with the friends and colleagues you saw there or missed seeing there! Whether you have new business to conduct or simply want to catch up and stay in touch, October presents your best opportunities to do so before we begin the rapid approach into the holiday season.
Now that it is officially fall, it’s also time to consider the things we have intende d to accomplish “before the end of the year.” We all know that Thanksgiving and Christmas always arrive much more quickly than we think they will, immediately followed by the new year. Do you have a mental list of things you’ve been expecting to accomplish in 2022? Are there a few more goals to attain or targets to hit? Whether we’ll be relieved that 2022 is ending or sorry to bid it adieu, we have one quarter of 2022 left—let’s see if we can make the most of it!
• Automated (Truss Design Software Download) or SemiAutomated (Touch Screen Entry) Operation
• All Movements are Computer & PLC Controlled
• Comprehensive Setup Screens
Display Each Piece with Setup Data
• 22” x 40 Tooth Blade on PAE Cut 1 or 2 Boards up to 20’ (2 Second Plunge Cut)
• Cut Chords, Webs, Rafters, Wedges & Stair Stringers
• Cut Long Scarfs by MultiPlunging
• Servo Positioning on Infeed, Angle & Outfeed Pusher
• Over Travel Protection
• Ink Jet Printer
• Lumber Optimization Program
• Belt Waste Conveyor
• 480 Volt / 3 Phase / 60 Amp
• Includes 5 Day Onsite Installation & Training
• Optional Monet DeSauw Live Deck, Bunk Feeder & Incline Belt Waste Conveyor
FOB MO
Call For Pricing
• Touch Screen User Interface with Backup Mechanical Controls
• 3 Operating Modes: Auto, SemiAuto & Manual
• All 20 Axes of Movements are Computer & PLC Controlled
• Comprehensive Setup Screens
Display Each Piece with Setup Data
• Anti-Collision & Optimizing Programming
• Auto Calibration Productivity & Time Tracking
• Maintenance Diagnostics
• Variable Speed Conveyor (0-50 Flights per Minute)with Powered Hold Downs
• (1) 30” x 80 Tooth Blade (27 3/4” Scarf on PAE)
• (4) 16” x 40 Tooth Blades (13 1/2” Scarf on Centerline)
• Pneumatic Blade Brakes on all 5 Blades
• 16 1/2” to 20’ Length Capacity (11” Minimum on Square End Blocks)
• Vibrating Waste Conveyor Under Saw
• 480 Volt / 3 Phase
• Includes 4 Day Onsite Installation & Training
• Add $2,900 for Extra Set of Blades
• Optional Live Deck, Label Printer, Ink Jet Printer, Catcher Display & Incline Belt Waste Conveyor.
CarolSanford’s invention didn’t equal Cal Jureit’s, but he made up for it with his head start and his aggressive marketing. Sanford had filed for his patent in March 1954, two years ahead of Jureit’s September 1956 filing, and had a plate design that was relatively simple to mass produce. Though his plate required extensive hand nailing, it was the best wood connector available at the time and an instant hit. By July 1958, Sanford was operating a huge stamping plant and had developed extensive engineering manuals, declaring on their covers that his company was “The World Leader in Roof Truss Connectors.” This claim was undoubtedly true, as Sanford had no real competition until Jureit entered the scene.
Cal Jureit engineered his own business startup with thoughtful aplomb. Before going to market with a product that he knew was better than Sanford’s, he spent a year of R&D perfecting it, drawing from his years running a testing lab. This involved “one-off” fabrication of multiple plate configurations and running dozens of tests. With the data collected, Jureit was able to determine optimal tooth size and arrangement, and the necessity of increasing the plate thickness from 16 gauge to 14 gauge. Finally, with design in hand, he was unable to find an existing stamping facility capable of producing it, as Miami lacked heavy industry. So, he invested further time and effort recruiting manufacturing talent and outfitting a suitable building. And by 1958, Jureit was ready to stake his claim in the truss plate market.
Perhaps Sanford felt the competition was growing and realized he needed to distinguish his plate from Jureit’s, as these 1958 product listings from American Builder Magazine seem to imply. Sanford indicates “Semi-Nailed” in the headline without any mention of the extensive hand-nailing effort required. He seems to hang his hat on the “1,000 lbs. (jigging) pressure” and “each joint placed under 50 tons of pressure” without acknowledging that the truss must be flipped, back-plated, and nailed before being “moved to a roller table.”
Contrarily, Jureit’s promotions immediately seized on his trump card, headlining that the “Gang-Nail plate eliminates hand nailing altogether.” Then, he compounded that advantage by stating that both top and bottom plates are applied while the truss is in the jig.
While both of these listings gloss over the machinery needed to apply their products, this determination was underway. Sanford alluded to a roller table and a vertical press with 50 tons of pressure at each joint, while Jureit referenced a moveable table that rolls through a vertical beam-type press that can simultaneously press two or more truss joints. Jureit was the first to submit a patent application for a vertical press. Two years later, in 1962, Sanford patented a system with a vertical press with finish roller.
Another factor that was not apparent from the early ads, but would eventually be a game changer, was the dramatic difference in the steel makeup of their plates: Sanford’s 20 gauge plate was half the weight and half the cost of Jureit’s 14 gauge plate.
Next Month: Competition Intensifies
Since 1970, Joe Kannapell has worked as programmer, Chief Engineer, Marketing Manager, and Sales VP for MiTek, plus 7 years at truss plants, retiring at the end of 2020.
1995 Koskovich Auto Omni
Component Saw
1995 Koskovich Auto Omni saw, S/N
AO950056 4-blade automated saw includes [1] 29 inch blade and [3] 19 inch blades.
Includes scrap incline. Fully automated setup with full power length and all axis angulation, single sided setup from operator console, 2×3 through 2×12, 12 degree minimum angle to -71.6 maximum angle.
20’ to 2′-4” @ 90°/90°, includes owner ’s manual and any available spare parts including [6] spare blades. 208/240/480 volt, 3 phase, 100 Amp, and 120 volt, 1 phase electrical, 100 Amp electrical required, 90 psi air.
$14,990 FOB SD Wood Tech Systems 765-751-9990
www.woodtechsystems.com
Safety Speed Manufacturing Model 7400 XL Panel Saw
Safety Speed Manufacturing, model 7400 XL*, vertical panel saw, 3 HP induction motor, 64 inch crosscut, 2 1/8" maximum thickness, accuracy within 0.005 inches, 13 foot long welded steel frame with integrated stand and linear V-guides, enclosed counterweight system, adjustable vertical and horizontal rules. Quick changes from vertical to horizontal cutting. Includes machined aluminum material rollers, hold down bar, wheels, quick stop gauges and material hold downs. Dust collection ready. Options available include digital readouts for vertical cuts, automated length measuring, laser guide, stop bar, vacuum and midway fence. 208-230/460 volt, 3 phase electrical (208-230 single phase, 2 HP power optional +$100.00).
$13,149 Base, FOB MN.
Wood Tech Systems 765-751-9990
www.woodtechsystems.com
a blending of excellent services and products, with answers that work...!©
Not producing the results you need or want – getting conflicting info about what to do and the equipment and the systems you may need?
Before you Buy - Ask yourself –do I need a salesman or a guide?
If you want an Independent Guide that has your bottom-line results as the #1 priority, Call Me. If the salesman will do - we'll talk later...
Also, don't let Financing Deals influence your best solution. FitzGroup can arrange – Zero down & No payments for 90 Days!
Please be assured that your investment with any of our selected partners will not cost one penny more with the Fitzgerald Group as your purchasing contact. In addition, you will receive the full advantage of our Partner Relationships and Services NOT offered elsewhere.
RFitzgerald@FitzGroup.com 719.528.5445
www.FitzGroup.com
Used Razer S5 Linear Saw
S5 Razer saw modules configured for either left-to-right cutting and/or “Z” shaped layout. AIT auto infeed tables. Vekta user interface software complete with the full version of the optimization algorithms.
Stack cutting and side by side cutting
Contact for Pricing
Eide Integrated Systems, LLC 612-521-9193
www.eidemachinery.com
– One person rafter cutter can make single or double compound cuts and simple cuts on either end of the rafter. Features twin H.D. Milwaukee worm-drive circular saws, 10’ infeed conveyor, turntable system allows for precise angle cuts and easy set-up, 120 volt, 1 phase, 90 psi air required.
$2,990, FOB WA.
Wood Tech Systems 765-751-9990
www.woodtechsystems.com
•
•
SpeedCut Speed Rafter Cutter Saw SpeedCut model SRC, Speed Rafter CutterMeeting production goals is easier when you can rely on people who understand your business. Our service pros at Simpson Strong-Tie are ready to listen and offer solutions to strengthen your organization. System integration and team collaboration are easy with our open-platform software. And whether your team is in the office, on the production line or at the jobsite, we’re here every step of the way to provide technical support and expert training — so you can stay on track and get the job done.
Let our team support and train yours. Visit go.strongtie.com/componentsolutions or call (800) 999-5099 today.
The Most Advanced and Up to Date Lean Process and Industrial Engineering Methods to Significantly Improve:
√ Productivity
√ Quality
√ Employee Issues
√ Net Profits
All Areas - Manufacturing, Sales, Design, and Admin.
Cost Savings and Net Profit Gains that Usually take Months or Years, Can be Accomplished in Weeks or Months with TDC
“I’ve been reading Todd’s articles for the last few years and have been intrigued by his view of productivity measures, so I decided to hire him to learn more about his philosophy. It was an investment well spent because I not only learned a completely different way to view labor metrics, but I came out of it with a completely different mindset on pricing, scheduling, and staffing. I highly recommend Todd’s services to take your company to the next level. The most valuable information you can get is the information you don’t know you need.”
Shane Soule, President Bremen, IN
Dozens of clients provided written testimonials on the TDC website.
a show together is no easy feat—organization on this scale doesn’t just happen, rather it takes months and months of planning to have it evolve from planning to a show. Spida is grateful to SBCA for the outstanding event that was BCMC 2022.
What a throwback to BCMCs of old! When the doors opened, there were scores of customers just waiting to come in and see old and new faces and all the Exhibitors had to offer Every attendee came through the door with a huge amount of energy and so many had a specific piece or pieces of equipment in mind to complement their factory and increase their market share.
Spida was able to introduce our new salesmen to the world of BCMC and they were shocked at the attendance and then the spectacle of the Spida Machinery booth machinery demonstrations first-hand. Our newcomers, Bill, Dan and Mike, were in 7th heaven attending to loads of questions and enquiries on the machinery at hand. Tony, our long-standing salesman in Texas, was smiling and shaking so many familiar hands that he said it was just like old home week: “So many friends and faces I haven’t seen for a while, so good to be back doing BCMC.” We also brought our Aussie and New Zealand staff to the booth—what a great way to introduce some of them to the USA!!
Spida again showcased our Wall Framing Line with Sheather, Build Table, and Wall Extruder. Lots of great conversation was had on our Raked Frame Extruder that’s in the market now, making raking and common walls with ease. Our PieceMaker was showcased in its finest form and the interest was outstanding. With so many customers watching our linear saw doing its best to cut the most amazing cuts from long and short length lumber, I even saw some of our customers take bits of lumber as souvenirs from the linear saw outfeed.
This year I was privileged to talk at the Women in Construction forum. It was an honor to sit and talk amongst my peers about how to engage women into this exciting career. Thank you to all those people who came and talked to me afterwards about their mothers’, sisters’, and wives’ journey and to those who now aspire to bring their daughters to work with them. I was in awe of the ladies who spoke on the stage with me, they are outstanding women with fascinating stories to tell.
Spida would like to thank everyone who came to say hello to us at the booth. We also would like to thank everyone involved in bringing BCMC 2022 to fruition and all those who we are engaged with in quoting and machinery supply. We had a blast and planning is already underway for a bigger and better show next year!!!
See you in Indianapolis, IN next September for BCMC 2023!
Price: $209,000
FOB: MN
Don’t just do it, nail it. It’s a brand new day in wall-panel production, with a whole new way of doing things better.
Terminailer®, a revolutionary, event-driven, nailing machine that completely defies any preconceived notions about sub-component assembly
Terminailer all but shatters the stereotypical myth that subcomponent equipment is essentially peripheral – unimportant. And it does so by quickly and accurately driving far more framing nails in your wall panel jobs than ever before. Whether in your shop or in the field, one operator sets the pace for production and quality And that reduces labor costs and other aspects of overhead.
Terminailer is an event-driven, sub-component assembler that will quickly and accurately drive 30% to 70% of the framing nails in any wall panel job. In your shop or in the field, one operator sets the pace for production and quality. The Terminailer functions independent of design software, requires zero set-up time when switching between any configuration, and requires no special operator training.
The Terminailer is easy to move around the shop so it’s location can evolve as your shop evolves. With all of the nailing occurring in the closed main chamber, nail injuries and nail location miss-fires are eliminated, making your plant that much safer.
With nearly ten years of development from people that know machinery it is assembled to exacting standards, well supported, and it is easily maintained with shelf-item parts. Terminailer: vetted, tested, and ready to drive maximum productivity for you. Be sure to check out our videos below for a quick review of this revolutionary machine!
PARTS & COMPUTER
• Used Servo Star CR10251 (3 Available) -$1,100 Each
• Used Servo Star CR06251 (3 Available) - $1,100 Each
• Used Servo Star Master Controller MCSS-08-6410-004 - $4,000
• Used ALS Windows XP Computer - $1,500
• All Parts - $10,900
• Used parts were removed in "working condition" from the ALS 276 during a saw upgrade
FOB AL Wasserman & Associates 800-382-0329
www.wasserman-associates.com
2002 Koskovich Auto Omni 5-Blade Component Saw 2002 Koskovich Auto Omni component saw, 5-blade automated saw includes [3] 20 inch blades, [1] 30 inch blade, [1] 12 inch blade and shaker waste conveyor with factory side pans. Fully automated setup with full power length and all axis angulation, single-sided setup from operator console, 2×3 through 2×12 and 4×2, 20’ to 9” @ 90°/90°, Exair cabinet coolers, remote monitor, no spares.
In operation until Aug. ’21. 208/240/480 volt, 3 phase, 100 Amp saw electrical required. 120 volt, 1 phase PC electrical required.
$13,970 NOW $9,997 FOB OH
Wood Tech Systems 765-751-9990 www.woodtechsystems.com
The L-M Verticut 2000 is a true Precision End Trim (PET) saw that is capable of holding a 1/16th accuracy all day long. Made in the USA, the V2k comes equipped with a 15 HP 460/230 volt High-E three phase TEFC motor driving a Double ended Premium “Stellite” inlaid saw bar with a spring loaded chain tensioner and an automatic oiler to lubricate the .404 pitch custom profile semi chisel saw chain.
Rather than a single pivot-point, the saw assembly is mounted on a mandrel box that is guided by cam followers on a steel frame that is raised and lowered by a hydraulic cylinder. A console with the saw controls moves with the saw assembly along a track positioned using a manual “V” wheel geared drive or optional Hydraulic drive
Safety Speed Manufacturing model 7000, vertical panel
saw, 3 HP induction motor, 64 inch crosscut, 2 inch maximum thickness, accuracy within 1/64th of an inch, 10 foot welded steel frame with integrated stand and linear V-guides, enclosed counterweight system, adjustable vertical and horizontal rules. Quick changes from vertical to horizontal cutting. Includes machined aluminum material rollers, hold down bar, wheels, quick stop gauges and material hold downs. Dust collection ready. Options available include lower frame extensions, digital readouts, laser guide, stop bar, vacuum and midway fence. 208-230/460 volt, 3 phase electrical (208-230 single phase, 2 HP power optional +$100.00). $9,332 Base, FOB MN.
765-751-9990
The V2k is unlike other imported systems that are basically a Portable Yard Saw on a cutting rack with a best cutting accuracy of +/- 1/8″ (meaning up to ¼” accuracy variance between units of lumber). The V2k from L-M provides +/- 40 thousands, assuring consistent PET precision from unit to unit.
Another advantage L-M has over the competition is their commitment to personal service with unlimited phone assistance and technical help. Their team has traveled the country working on crosscut saws for many years and they know their equipment inside and out. L-M is a familyowned business that prides themselves in doing the job right and building long term relationship that is vital to their business: “Built to last as long as our customers since 1946”.
765-751-9990
www.woodtechsystems.com
Timeand time again, TDC has witnessed too many companies spending millions on capital investments to achieve marginal improvements while others spend far less and achieve spectacular results. It may feel obvious that adding a saw or auto-puck table will significantly enhance output, but the reality often falls far short of the promised results. It is far easier for many to risk spending millions on new equipment and buildings, but an investment of a few thousand for formal training in proper process enhancement has been deemed a step too far. Why is investing in meaningful process improvement not part of every company’s yearly checklist?
One might be asking, what is meaningful process improvement? Well, process improvement covers all processes that happen within any company. For example, HR, manufacturing, design, sales, admin, and capital improvement discussions are all part of the process improvement umbrella. Process improvement is at the heart of the continuous improvement philosophy embedded in successful lean manufacturing. For a fraction of the millions spent on capital improvements, the investment in process improvement can be measured in the hundreds of thousands, if not millions. What would the return for your company be for a 3-point gain in net profits year after year? Just FYI, a 3-point increase is a very low bar.
Employer HR practices. Time and time again, many are stating that finding enough talented and dependable employees is becoming a growing problem. That statement is far more accurate than most understand. More people will be leaving the workforce for the foreseeable future than coming into it. In the US, it will be 400k fewer new workers per year for the next nine years. As a percentage, Canada’s demographics are even worse. (Source: Peter Zeihan, The Trade Breakdown | Upfront Summit 2020)
Todd DrummondLean manufacturing has two sides to the proverbial coin. One is lean tools, such as 5S and Just-In-Time, and the other side of the proverbial coin is that it requires excellent employee and management practice. Without good employee and management practices, lean manufacturing will fall apart. Over the coming decade, the companies that survive and prosper will only be those with strong and healthy HR management practices. Employees will have far better bargaining strength when choosing who to offer their services as an employee. Talented and skilled individuals will have multiple offers from multiple companies to make their choice.
Case Study for HR Process Improvement. During our lean training, TDC spends considerable time explaining best practices of HR and management principles. One client, who must remain confidential, had chronic turnover and vacancies in a very prosperous area with an extremely low unemployment rate. While their competitors were experiencing healthy net profits, they struggled to break even. Fast forward three years later, while implementing best practices for HR and management, and with no investment in new equipment, the company has virtually no turnover or vacancies. Their net profits are now among the high percentage of their peers. HR and management practices are part of process improvement and need to be remedied too. The best practices of HR and management principles are just as important as any new equipment.
With so many areas included under the meaningful process improvement umbrella, all of them cannot be covered in this article.
The one thing that needs to be mentioned – the most significant barrier to implementing or investing in a formal process improvement program is pride or ego.
Case Study for Manufacturing Process Improvement. One client brought me into their location without his co-owner’s consent.
His partner could not believe that he did not think that they were undoubtedly the experts. They certainly did not need an outsider coming into their location to point out what the consultant believed were areas of deficiencies and how they could make improvements.
He thought they already knew where they needed improvement and did not need anyone explaining what they already knew. Long story short, each day spent showed just how many areas where they could make adjustments and improve, and that both owners had blind spots. It was a typical case of not knowing what you do not know. The services’ cost was paid back within the first hour on location. The returns garnered by the better practices in every department kept filling their bank account every month, just like an investment in new equipment. Yet this investment was not even close to what new equipment cost. Client quote: “Damn Drummond, you are certainly a straight shooter and a hell of a cheap investment for the return. I like how you work.”
TDC is Now Scheduling the Fall and Winter Months for New Consultations. The team of TDC is your best source for learning about proven and practical lean manufacturing best practices combined with industrial engineering principles to keep your company at the leading edge of competitiveness. No one is better at providing your team with proven results for process improvement of employee practices, pricing, truss labor estimation, and so many other best-in-class practices. TDC’s tailored solutions are for the client’s specific needs. Go beyond the typical software and equipment vendor recommendations for your operations and do what many have dared to do. Embrace the Drummond Method, and your company can experience cost savings, and net profit gains that usually take months or years can be accomplished in weeks or months, resulting in an average of 3 to 6 point net profit gains for CMs. All areas are addressed, not just the manufacturing. Please do not take my word for TDC’s services, though. Read the public testimonials many current and past clients with decades of expertise and experience have been willing to give: https://todd-drummond.com/testimonials/.
Website: www.todd-drummond.com
Phone (USA): 603-748-1051
E-mail: todd@todd-drummond.com Copyrights © 2022
Driven
Conveyor
• Rea Ink Jet Printer (does not work)
• 24' Capacity Outfeed Table
• 6 Arm Storage Deck (adjacent to saw outfeed table)
• Waste Conveyor (under saw, parts to the rear)
• Excludes Incline Waste Conveyor
• A/C System for Control Cabinet
• 480 Volt / 3 Phase
• Saw will need a tune up when installed at buyers location for 100% cutting accuracy
• Video available upon request
One month after installing a Double Lumber PickLine to feed two TCT Linear Saws:
"We are getting 3,000 to 5,000 bdft more each saw, than we were getting before the install.
We have shut down one Cybersaw and one TCT chord saw.
This equals about 3 less people 10 hours, and 2 less forklifts 10 hours.
Overall, it is a major improvement to our operation. We hope to have the chance to run it two shifts to further accelerate the payback.”
Tom Hollinshed, Ownermode,
powered movements,
network
depths and internal brakes are standard. Options include enhanced servo controls featuring autocalibration, catcher's display and either shaker or belt scrap conveyor and incline. 440 volt, 3 phase
The Panels Plus 3-Table Line is also known as a Full Production Line. It has the largest footprint and the highest production output in comparison to the other system lines. The 3-Table Line frames and sheathes wall panels. This production line consists of a Framing Station, Squaring Station, Sheathing Station, Subcomponent Tables and Roller Conveyors.
and
ProCut™ UC Linear Saw Series offers many variations to suit your plant and
line. Let
design a system for
The truss industry relies on 3rd party quality assurance services to provide random visits to review the plants Quality Assurance program along with their operations. If your plant needs to comply with the IRC, IBC and to those who depend on solid, experienced QA expertise, we ask you to consider selecting Timber Products Inspection, Inc. (TP) as your choice for 3rd party inspections.
Proudly serving the forest products industry for over 50 years, TP brings the expertise you need to ensure your business is successful. As a responsible partner, TP delivers to clients, employees, and the industries we serve the confidence to drive value through the effective use of our diverse professional team.
TP would like to welcome the following authorized agents to our inspection team, each of whom have many years of experience in the truss industry!
• Al Coffman
Jean Hart
Curt Holler
Chuck Ray
Glenn Traylor
Elliot Wilson
If you have questions about how you can make this selection, please contact your authorized agent above or Glenn Traylor at 919-280-5905 or trusguy@gmail.com.
https://www.tpinspection.com/ https://www.tpinspection.com/auditing-services/truss
Onoccasion, we are required to utilize a detailed tooth count to qualify a connection on a metal plate connected wood truss. Fortunately, we have several tools that can assist us. My June article, “Which is Better: Plate Placement Method or Tooth Count Method?”, includes a point-by-point comparison of two of these tools, showing how neither is the perfect solution for all situations. In addition, we should include two more items on this list of tools for counting teeth:
1. Plate Placement Method (PPM) – Critical plate inspection template
a. This is generated by the plate manufacturer’s software
b. Software settings allow any or all plates to be generated
a. Available to SBCA members at no charge for the software
b. Utilizes electronic devices with camera and wireless connection to connect to your system database
a. This is generated by the plate manufacturer’s software
b. A compilation of connectors, with 4, 6, or 8 per page that can printed to accompany the job
4. A combination of PPM and TCM.
Except for TCM, these tools consider the conditions and requirements that must be followed. It is built into the software. Sometimes, it’s up to an old-fashioned tooth count to make the determination, but there are several rules that need to be understood. Based on a recent inspection challenge conducted at BCMC 2022 in Columbus, it was observed that many in the industry may not be aware of this particular rule that is dictated in part by the American Wood Council’s National Design Specification® (NDS®) for Wood Construction
Let us look at a typical example. In this analysis, we are not going to consider defects in the plated area.
In the first photo, a particular joint is illustrated. Teeth are counted for each member considering all teeth in the web member. This is a simple process – but that does not automatically make it a correct process.
As we apply the NDS® rule reflected in ANSI/TPI 1–2014, 3.7.7.2.2 Ineffective Teeth End and Edge Distances, the second photo shows the actual effective teeth. The NDS® rule dictates that lumber within ½” of the end of the member and lumber within ¼” of the edge of the lumber (the margins shown with the orange lines) cannot be counted as effective.
Thus, the table demonstrates the difference between simply counting ALL teeth versus counting effective teeth. When the teeth located in the ½” end distance and the ¼” edge distance are eliminated from the count, the reduction can be striking. The percentages will differ from case to case, but in this example the result varies from roughly 60% to 70%.
When it comes down to which teeth to count when you’re counting, TCM is the most precise method. With TCM, you can verify the effective tooth holding with your own eyes. As long as you take into account the edge and end distance considerations, TCM will prevail over PPM in this challenge.
An ANSI/TPI 1 3rd Party Quality Assurance Authorized Agent covering the Southeastern United States, Glenn Traylor is an independent consultant with almost four decades of experience in the structural building components industry. Glenn serves as a trainer-evaluator-auditor covering sales, design, PM, QA, customer service, and production elements of the truss industry. He also provides project management specifically pertaining to structural building components, including on-site inspections and ANSI/TPI 1 compliance assessments. Glenn provides new plant and retrofit designs, equipment evaluations, ROI, capacity analysis, and CPM analysis.
Glenn TraylorStructural Building Components Industry Consultant http://www.linkedin.com/in/glenntraylor
Don’t Forget!
Saw it in the
Hardened, Ground and Polished Steel and Billet
Length: 5 feet (60”) to 60 feet (720”)
Height: 12 inches Depth: 12 inches
If you are looking for the fastest, most consistent way to measure and cut your product, then the Hain Measuring System (MEA) is your answer. The MEA changes from one length t any length instantly, up to 60’, without changing the operator’s position on the line. It is also highly accurate (+/- .010) and quickly moves from one length to the next in seconds. The MEA is designed for quick and easy setup and is simple to use. Even a first time user will be productive with little or no training required. It can adapt to any saw and can be mounted to any surface so that you can integrate the MEA with your existing setup. The MEA is versatile allowing “left” or “right” handed operation and measurement in “feet and inches” or “inches” depending on your preference. The MEA is also available in a “Skid Mounted” version.
The Spida Apollo saw with Automation is a computerized, pull-arm type saw used for cutting either wood truss components or wall panel cutting and represents the lowest-cost way to add an automated single-blade saw to your operation. Features include angle cutting from 10 to 170 degrees, 36 inch scarf cuts, patented variable stroke limiter for safety, solid frame and arm design, 17 inch industrial touch screen with enclosure, 7.5 HP motor, plug and play wiring making installations easier and includes cowls for adding a dust extraction system.
Available options include software is available for both trusses and wall panel cutting, laser guide showing exactly the path of the blade before the blade moves, Safe Grip™ Clamp for cutting smaller pieces, clamping table, Plate Marker template providing automated set up for marking joint locations (studs, sub-component locations, etc.) on top/bottom plates, Chop Saw Table for adding another saw for miter/compound or end cuts, prior to feeding the Spida Apollo saw, Portable Dust Extractor and spare blades.
Saw is available in 240 volt, 20A or 460 volt, 15A 3 phase electrical. Computer requires 110 volt, 1 phase, 20A.
Wall Heights:
Wall Lengths: 16', 20'
Pre-Stage Area: 16', 20' or
The new field-tested Triad PreStage Framing Table, designed and built with customer input, can bring increased productivity to your panel shop.
Triad's exclusive and unique design merges a pre- layout material-staging area with a fast and efficient framing station -- into a single unit that can assist with rapid throughput in your plant.
A powerful, built-in continuous track system lifts and conveys components and material to framers and then the finished panels to your next station.
Initial customer field production, from a Texas plant, has shown an average of 3600 linear feet per day (8 hr shift) of framed walls in their facility!
(matches wall length)
to change without notice
New, DeRobo linear saw by Monet organizes "fill" boards to increase optimization of each board, can produce unlimited scarf cuts, cuts 1 or 2 boards at a time and cuts webs, chords, wedges, rafters and open-stair stringers. Works with all major connector plate manufacturer's software. Features include 22 inch blade, left-to-right feed direction standard, lumber push and pull grippers for more accuracy, ink marking on the 1 1/2" face of the incoming boards and small piece capture and delivery to the front of the saw for easy access. Infeed deck and bunk feed are shown as options only. 480 volt, 3phase. Call for pricing, FOB MO.
765-751-9990
www.woodtechsystems.com
New Square 1 Rolsplicer, splices 2"x3", 2"x4" and 2"x6" lumber with a 3 to 4 second cycle time. Presses the lumber together prior to imbedding plates. Embeds plate lengths up to 19 inches. Features two, recessed, simultaneous-activation buttons, guarded motor and sprockets, external lubrication points, 3 HP motor and a footprint of 59" long x 42" wide. Optional 20' infeed and 10' outfeed conveyor available. 480 volt, 3 phase electrical. Other voltages available.
765-751-9990
www.woodtechsystems.com
2002 Auto Omni 5 blade automated component saw includes shaker waste conveyor with factory side pans, [3] 20 inch blades, [1] 30 inch blade and [1] 12 inch blade. Fully automated setup with full power length and all axis angulation, single sided setup from operator console, 2×3 through 2×12, 22’ to 3′ @ 90°/90°, and spare blades. 208/240/480 volt, 3 phase, 100 Amp and 120 vac, 90 Amp electrical required.
Price: $19,990 FOB PA
Wood Tech Systems 765-751-9990
www.woodtechsystems.com
2008 Alpine PF 90 wall panel cutting and marking syste m. 3.5″ x 12″ m aximum cutting profile, Inkjet option, cuts to 16 ft long. From the OEM’s literature, “Effortlessly handles two of the most critical and difficult processes in any wall panel operation – plate cutting and panel layout. At the rate of 1,000 linear feet per hour or more, uses data from the design software and accurately marks stud, cripple and jack locations, job and panel number, subcomponent and window/door locations, and even sheathing locations on both top and bottom plates simultaneously with ink-jet printing.
MORE INFORMATION HERE
$8,499 FOB NY
Wood Tech Systems 765-751-9990
www.woodtechsystems.com
Safety Speed Manufacturing model 6400 vertical panel saw, 3 HP worm drive motor, 64 inch crosscut, 1 3/4" inch maximum thickness, accuracy within 1/64th of an inch, 10 foot welded steel frame with integrated stand and linear V-guides, enclosed counterweight system, adjustable vertical and horizontal rules. Quick changes from vertical to horizontal cutting. Includes machined aluminum material rollers, hold down bar, wheels, quick stop gauges and material hold downs. Dust collection ready. Options available include lower frame extensions, digital readouts, laser guide, stop bar, vacuum and midway fence. 120 volt. Starting at $5,169 FOB MN.
765-751-9990
www.woodtechsystems.com
765-751-9990
Havingjust returned from the best BCMC in almost two decades, I want to share some reflection. Our industry was deemed essential during the pandemic, and we outperformed many other sectors. Demand for wood components continued to stay strong through it all.
Today, defeating the odds of recession has strengthened and enhanced our industry. Now more than ever we are coming together as one and displaying perseverance, drive, and dedication like no other. As we continue to soar above the facts and percentage of our declining economic affairs, the future is what we remain focused on.
BCMC 2022 attendance was within reach of record breaking. Attaining such an accomplishment has proven to everyone that this industry is valued and capable. The wood component industry expansion has conquered the diminished recession that our country has entered. Focusing on the future, and staying true to who we are, has set us apart and the world is taking notice.
The demand in our industry continues to rise, as we continue to showcase how essential we are. With the statistics of our economy working against us, the push for our industry remains in our favor. As we remain hopeful, we look forward to surpassing the projections of attendance and growth in the years to come. Our industry is changing and shaping this world as well as the young minds that are patterned closely behind. Reframing the world’s perspective on our industry allows us to represent ourselves as a part of the future. This gives us the opportunity to adjust the world viewpoints.
BCMC has presented endless possibilities within our industry that help us secure success and advancement. As we progress, we will prevail sustaining gratitude and gratefulness. Thank you for those who attended, bravo to those who were recognized with awards, and most of all congratulations for all those involved in this industry. This is an exciting time to be in such a close-knit and friendly business. We are proud to be a part of it.
thick,
reduce noise, dust, and improve operator safety; automated via downloaded sheathing cutting files from wall design software. Includes 8 foot long idler infeed conveyor and outfeed conveyor with pop-up skate wheels, (1) spare blade and all available spare parts. 220v/440v, 3phase electrical saw, 120v, 1 phase electrical PC. 100 PSI at 14 CFM
3″. Fully enclosed
angulation axis of movement for cutting and
(both faces, one edge).
Ph, spare blade. The WoodRunner Air Pick automated lumber retrieval system includes a single picking head with 10 bunks and 2 magazines. Includes manuals, all available spare parts and spare servo cards, and WoodRunner software source code. Available March 2022.
Safety Speed Manufacturing, model 7400 XL*, vertical panel saw, 3 HP induction motor, 64 inch crosscut, 2 1/8" maximum thickness, accuracy within 0.005 inches, 13 foot long welded steel frame with integrated stand and linear V-guides, enclosed counterweight system, adjustable vertical and horizontal rules. Quick changes from vertical to horizontal cutting. Includes machined aluminum material rollers, hold down bar, wheels, quick stop gauges and material hold downs. Dust collection ready. Options available include digital readouts for vertical cuts, automated length measuring, laser guide, stop bar, vacuum and midway fence. 208-230/460 volt, 3 phase electrical (208-230 single phase, 2 HP power optional +$100.00).
765-751-9990
www.woodtechsystems.com
Since 2006, we've been helping businesses of all kinds build their online presence. We make websites and software for the construction industry to empower companies to reach a wider customer base and engage their audiences. Companies all around the world work with us to make websites and apps that people actually want to use. Reach out to Wolf X Machina if you're a business and you want a website that actually drives results.
www.wolfxmachina.com info@wolfxmachina.com
Highly confidential position, Regional Manager opportunity. Experience with operations in the $20-50M range. Responsible for all areas of Truss and Wall Panel Manufacturing operations, safety, inventory control, delivery, and customer service at 3 locations producing $10-15M each. The facilities produce Roof and Floor Trusses.
Compensation $100k+ base range plus substantial bonus based on your performance. Very competitive benefits package. Relocation package is negotiable if not in the region. Please inquire to discuss details. Strictly Confidential! Let's talk to see if this is a perfect opportunity for you.
visit: www.thejobline.com email: mail@thejobline.com
Monet DeWall 90/90 wall panel marking saw is a computer numeric controlled wall panel saw with touch screen user interface. Cuts and marks up to 2 boards at a time using 2x4 through 2x8 or cuts and marks one board at a time. Call for pricing, FOB MO
765-751-9990
www.woodtechsystems.com
In my humble opinion, since 2014, United Truss of Innisfil, Ontario, Canada has unofficially held the titles of “The most automated truss plant” in North America and “The most visited truss plant in North America.” United Truss was the un-named but featured truss plant in my May 2022 article, “Debunking the ‘Automation Takes Too Much Space’ Myth.”
Edmond Lim, P.Eng. LimTek Solutions Inc.
United Truss has been visited by a “Who’s Who” of the US truss industry, including ProBuild, Builders FirstSource, 84 Lumber, USLBM, S.R. Sloan, Ridgway Roof Truss and Toll Integrated Systems, just to drop a few names that made the trip to United to see how they Feed the Beast! In Canada, it is easier to ask who has not yet visited United Truss. As mentioned in last month’s article, “Incremental CapEx ROI and Plant Tours," United Truss is a textbook study just like R&K. United Truss started with a fully loaded RetroC automatically fed lumber from a Lumber PickLine to auto-fill carts which funded future investments and optimized investments in table automation. United Truss will tell you that they could not have achieved their goals if they did not invest in material handling and sawing first — yes, they knew how they were going to Feed the Beast!
United Truss incorporates traditional truss plant automation, such as automated saws to cut the lumber, auto jigging to set up the truss perimeters, and overhead lasers to help position the truss plates. Traditional automation is not why people come to visit United Truss. People come to see the efficiency and simplicity of United Truss cutting lumber for multiple jigs with just one human picking lumber and one human saw operator with auto-fill lumber carts which is all part of their
complete in line lean manufacturing system. The collated lumber and collated truss plates (per joint) arrive at the tables organized for left and right of truss, which results in an average of 2–3 minutes per truss build time, optimizing United’s investment in traditional truss building automation.
For United Truss, this is a standardized day-in and day-out of 2–3 minute per truss, not just for a run of benchmark trusses as described in Joe Kannapell’s November 2020 article, “60 Years of Machines, Part XII: Best of Both.” Material has to arrive in front of the truss build tables organized so that truss builders just keep building trusses, not wasting time and energy finding and/or sorting material for every truss.
Truss plants are the original off-site construction component manufacturers. The sheer volume and size of trusses, along with the variability of lumber and complexity of truss shapes, is just beginning to be addressed on scale with industrial robotics. Interestingly and economically, with all of United’s automation they do not need full-time maintenance personnel, and trusses can be produced at volume and complexity with just one lumber picker, one sawyer, three truss builders, and one forklift operator. To produce even more trusses, all they need to do is add truss builders (if and when they can find them!).
When hosting visitors, Allan Inglis likes to praise the significant reduction in paperwork and the ease of cross-training, especially when businesses just can’t find people. To David Sandke, it is the continued operatingcost savings that have funded annual CapEx improvement projects that have enabled them to continue to look after their loyal and growing customers.
What’s next for United Truss? Ed DeBiasio has already approved a building addition to put the entire Lumber PickLine under roof. Ed has a vision and he continues to implement a profitable plan.
We at Enventek and LimTek are proud that Ed DeBiasio relied on us to help him and his team execute his plan. We are grateful for United’s continual hospitality of hosting plant tours that have resulted in many additional sales for us and we would like to take this opportunity to thank Allan, David, and Ed! On behalf of Larry Dalson, Dave Dalson, and myself, thank you, and it was nice to catch up with everyone at BCMC this year.
2006 Alpine AutoMill SC, model 348B, five-blade component saw Servo controlled computerized saw sets up in 2 to 19 seconds and downloads from a network or by using a touch screen for ease of operation. Five-head automated component saw works in both automated (downloading files) and semi-automated control via touchscreen input. It has 23 axes of automated movement, enhanced diagnostics, and auto management reporting. The SC cuts from 9″ 90/90 blocks to 2′-6″ to 20′-0″ long angled material, in sizes ranging from 2×3″ through 2×12″, and 4-angle floor webs from 3′-4″. Includes [3] 18″, [1] 20″ and [1] 32″ blades with air brakes, under-saw shaker conveyor and a scrap incline conveyor. Includes owner’s manual, all available spare blades and all available spare parts. 480v/ 60Hz/ 3 phase electrical required. $69,997
765-751-9990
www.woodtechsystems.com
New, Monet five-head, floor truss web saw, cuts 4-angle, 4x2 floor truss webs from 16 inches and 90-90 blocks from 12 inches to four foot long maximum length. Features 10-board magazine feed, powered, fixed-quadrant angulation, manual carriage standard, shaker-pan scrap conveyor with short incline conveyor and cut-off blade. Option for longer carriage length, single-sided setup (shown in pictures, but not standard), dust hood and horizontal scrap conveyor 480 volt, 3 phase. Call for pricing, FOB MO.
765-751-9990
www.woodtechsystems.com
The Light Gauge Steel Sheathing Station offers flexibility in wall height, sheathing thickness, and screw spacing and screws sheathing to steel wall panels to ensure quality panels every time.
This model can be stand-alone or integrated into a full production line.
Various sizes and configurations are available.
• Ergonomic working height
• Single person operation
• Flexibility with fastener spacing
• Fastens consistently and accurately
1-866-726-7587
of mind
unique “uni-body” construction creates a ridged machine that does a final press of the connector plates for complete embedment into lumber, saving wear on your floor assembly machine. 12” diameter rolls, 7 1/2 HP motor, 80# chain, 114 FPM speed, emergency photoelectric shut-off, chain and sprocket guards, integrated brake. Available options include: other roller widths, Heavy-Duty upgrade, gear motor drive, and soft start controls. 480 volt, 3 phase electrical. Other voltages
Designed for high-volume floor truss web output with even greater safety, the Monet DeSauw FWA-500 AC (for “automated controls”) offers the very latest in operator-friendly saw technology. Perfect for manufacturers running floor trusses in large volumes with variable web design, the 500 AC features automation for all blades, including the fixed cut-off blade for minimal waste. And without any need to open the saw motor cabinets, except for periodic service, you’ll benefit from enhanced safety as well. You might say that with the fully automated FWA-500 AC, Monet DeSauw has set a new standard. Again. Contact us today to discuss how this exceptional machine can positively impact your production goals.
Wood
visit: www.thejobline.com
email: twm@thejobline.com
STRICTLY CONFIDENTIAL!
Model HVS, Two Unit, 2-Zone, 14’ Horzontal Stacking System. Two lifting units (one master and one slave) with integral electrics. A truss sensing system consisting of adjustable laser sensors mounted on slide rails. One indoor electric control enclosure & panel w/PLC and manual controls. A stacker-conveyor interface package comprised of (1) mounted 3-push button enclosure and (1) remotely mounted 2-push button enclosure (pause/ emergncy stop). Hand-held Wampfler Remote Control System. 8 stacking rails and 4 stripping posts. Stack 1 5/8” thick x 14’ tall trusses up to 30 high. Stack a truss in approximately 40 seconds (cycle time). Stack up to 55’ or longer trusses on each side of the conveyor with minor assistance for truss sag, shorter lengths can be stacked unassisted. Excludes 77’ Walk Through Conveyor System. Two systems available at $25,000 NOW $19,900 Each. FOB NE. Wasserman & Associates 800-382-0329
www.wasserman-associates.com
•
•
•
•
•
from
• Truss Flip-Over
• Side or End Ejectors
• Bui lt-In Camber
Clamping on Both Sides
• Air Cylinders Under Table
• 2 Contr ol Valves
Clamping
•
Control Vlave
Diameter
• 10 HP / 3 Phase Gear Motor
• Front & Rear Emergency Shut-Off
• Joystick Control
• 2' per Second Travel Speed
800-382-0329 | www.wasserman-associates.com
General Manager
Must
P&L management experience in $10-15M range of Roof and Floor Truss manufacturing facilities. Produces components for Tract, Single Family Custom, Small-Medium Multifamily, and Mega-Multifamily projects. Responsible for Sales, Design, Production, P&L. Long time facility with potential for more output.
Compensation: $100k+- base, bonus potential to match base if metrics are met. Base is based on skills and experience. Relocation assistance available. Benefits details are available to qualified applicants.
Give
800-289-JOBS (5627)
visit: www.thejobline.com
email: mail@thejobline.com
New table-guided (NO rail) gantry system by Spida, side-eject or end-eject options, with continuous production tables built to length. Available in steel, plastic or combination table top options. Can be fabricated to receive automated jigging such as “Wizard” brand. 24″ diameter gantry heads feature raised operator platform, heavy-duty steel roll with 4″ shaft, baffles and heavy-duty spherical bearings, dual 7.5 HP braking gear motors for a total of 15 HP, easy adjusting bogie wheel assemblies, safety bars, Wampfler “finger safe”, under-table-mounted electrical supply and optional soft start drive. Spida can provide the combination of powered transfer rolls, sloping ejectors, receivers, idler conveyors and powered conveyors required to meet your configuration needs. 440 volt, 3 phase electrical. Other voltages available. FOB IN.
765-751-9990
2007 Clark Industries Horizontal Truss StackerBy
all accounts, it was a bumper year for BCMC 2022, and we were glad to see the significant increase in interest from not only attendees but also exhibitors across the industry
We appreciated the number of enquiries we had on our Direct Delivery Solution and there was significant interest in our PackFeeder solution too. To help everyone visualize how our systems can help improve their company processes, we even brought a 3D model for hands-on discussions.
The winner of the Dundee Style Genuine Croc Akubra Hat was (drumroll, please) — Steve Strom of The Truss Company in Eugene, OR.
Pictured here with me and Ryan Burtenshaw is Aaron Bahner, our GM of US Operations, modeling the hat before the drawing.
Thank you to everyone who visited the Vekta booth at BCMC Columbus. Thanks so much for stopping by, we really enjoyed the conversation and we promise to bring more hats next time!
2007 VIKING 16' X
WITH SHEATHING BRIDGE
• 16' x 12' Squaring Table with Powered Width Adjustment & Powered Chain Conveyor
• Wall Panel Lengths up to 16', Wall Panel Heights from 4'-0" to 12'-2"
• Swing Gates at Both Ends of Squaring Table
• Automated Field & Edge Nailing Driving by Panel Pro Event Software & Your Programmed Nailing Patterns
• Simple Touchscreen Controls
• 2 Tool Carriages for Sheathing Nailing with Tilt Function for Seams
• 2 Paslode Nail Guns with High Load Coil Tray
• Auto Sheathing Bridge Return
• Includes 4 Pallets of Magnum Coil Nails (2 3/8 x .113)
• 480 Volt / 3 Phase $29,900 FOB KS. Wasserman & Associates 800-382-0329
www.wasserman-associates.com
2021 Triad Router Bridge & Portion of V-Track
2021 Triad Routing Bridge with approximately (20) feet of v-track. Fits over tables that build up to 12′ nominal he ight wall panels. Includes powered automatic bridge return, powered vertical router movement, manual fine adjustment wheel, manual vertical router travel with chain drive and (1) Milwaukee router, catalog #5625-20 120 volt, 1 phase, 15 Amp electrical required. No table included. $28,970 NOW $12,000 FOB BC Wood Tech Systems 765-751-9990
www.woodtechsystems.com
FOB: MN
IBS Tool Bridge & Router Bridge IBS multi-tool bridge with (24) tool stations. Bridge features auto-return, button controls and laser guide mount. Fits up to 12′ nominal rail centers. IBS router bridge features (1) router, laser guide mount and lever-switch button controls. Fits up to 12′ nominal rail centers Sold as a pair Includes all available floor mounted, v-rail. Both bridges missing laser sub-assembly. 120vac, 120psi air. $15,975 FOB UT Wood Tech Systems 765-751-9990
www.woodtechsystems.com
New Panels Plus floor framing machine, supports the structural members creating floor sections from 2" x 6" LVL through 2" x 10" to 2" x 12" dimensional lumber, 20" deep wood floor trusses or engineered wood / I-joists. Standard footprint of floor panels (cassettes) up to 12' wide x 45' long. Table consists of a fixed section and a track-guided, moveable section controlled by either a foot switch or push-buttons.
twm@thejobline.com
New Wall Panel Lift
• 8'
• 1,000 Lb
• Weight: 120 Lbs
• Excludes: Electric Hoist & Freestanding Bridge Crane $1,850 FOB NE Wasserman & Associates 800-382-0329
www.wasserman-associates.com
Includes a series of color-coded locator pins at 16", 19.2 and 24" on-center spacing and clamping with squaring feature including foot pedal control. The locators individually flip down if a joist comes out on top of them. After the floor is complete and unclamped, the floor section can be raised up on skate-wheel conveyors and rolled out or lifted off the table using an overhead crane. Table height is 24.5", OAL 45.5 ft, OAW 14.5 ft. 120 volt, 1 phase, 15 Amp electrical required. 90 to 120 PSIG at 15 CFM air required.
2016 Triad exterior and interior wall panel lines with conveyors and terminal stations. Builds 2×4 and 2×6 walls up to 16’ in length with wall heights from 6’-9” to 10’-2” and includes Component Nailer model FTN and panel lift model XPL1000:
Exterior line includes (2) sets of Rough Opening Assembly tables model RO-CAT, framing table model Gen II with manual nail-gun tool dollies each side & stud locators at 16” and 24” o.c., squaring and sheathing table model Gen II with staple & routing combo bridge & side shift for seams @ 3” & 6” o.c. fasteners, top & bottom plate gun mounts for 6” o.c. fasteners, auto stop & tilt features, (3) 10 ft skatewheel conveyors, (4) 20 ft x 36″ roller conveyors and (4) powered infeed conveyors with chain track.
Interior line includes Rough Opening Assembly table model RO-CAT, framing table model Diamond Quad with manual nail-gun tool dollies each side, pop-up rollers & stud locators at 16” and 24” o.c., (2) 10 ft skatewheel conveyors, (4) 20 ft x 36″ roller conveyors.
System sold for over $223,000 new. Sold as one system only. 110 volt, 1 phase electrical required. 100 PSI air required.
Used Triad wall assembly equipment includes 16 ft x 12′-3″ max height framing station, model G2, with (2) two-tool dollies, squaring/ sheathing combo table, model G2 SH-SQ, with multi-tool mount nailing bridge and separate manual-drive router bridge, quantity of (6) 10 ft long x 2 ft wide idler roller conveyors with (4) legs, and Triad model FTCN component nailing station with four Hitachi NR83A nail tools.
Framer includes 16″ and 24″ color-coded stud locators, pop-up skate wheel conveyors, tool dollies have two tool mounts each (no tools) and powered height adjustment. Sheathing bridge includes joy-stick controls, tool offset, tool tilt, laser guide, power return and mounts for up to (23) Hitachi nail tools. Router and all available spare parts included. 120 volt, 1 phase, 30 Amp electrical required. 100 PSI air required.
765-751-9990
www.woodtechsystems.com
Wall Panel Work-Station (Green)
Custom fabricated, heavy-duty table ideal for producing rough openings, rake-walls, even interior walls. Table features a squaring lip, double-row pneumatic liftouts, duplex 110v outlet for hand tools.
Table dimensions: 16’ 4 1/2” long, 9’ 5” wide, 30 1/2” high.
$9,490 FOB KY
Wood Tech Systems 765-751-9990
www.woodtechsystems.com
Wall Panel Work-Station (Blue)
Custom fabricated, heavy-duty table ideal for producing rough openings, rake-walls, even interior walls. Table features a squaring lip, double-row pneumatic liftouts, duplex 110v outlet for hand tools.
Table dimensions: 17’ 8 3/4” long, 9’ 5” wide, 25 1/2” high.
$9,490 FOB KY
Wood Tech Systems 765-751-9990
www.woodtechsystems.com
New Component Table with Skatewheel Conveyors
Lift & Extend Skatewheel Conveyors. 10' x 10' Work Area with Squaring Lip. Gun Holster & Nail Tray.
$11,900 FOB NE
Wasserman & Associates 800-382-0329
www.wasserman-associates.com
Triad model PSRB Sheathing/Routing bridge builds minimum 3′ 9″ and maximum 12′ 3″ walls. includes: staple/nail bridge (no tools included) with auto return, 24 tool mounts, Porter-Cable Router, laser sight & joystick control. Bridge only, no table included. 120v, 100 PSI air required.
$8,490
Wood Tech Systems 765-751-9990
www.woodtechsystems.com
Consider Panels Plus wall panel assembly equipment for manufacturers of wood or steel wall panels, floor-panels, and related framing components. Panels Plus is an employee owned, ISO certified, manufacturing company that builds state-of-the-art equipment featuring durable construction, with fit and finish second to none in the structural building component industry The referenced base framing table allows you to assemble from 7-12 foot wall heights, at industry standard 16 foot lengths, at a working height of 29 to 32 inches. This framer design includes controls at each end of table, squaring stops and pneumatic clamping for consistent wall panel quality. Frames 2x4 or 2 x 6 walls, with color-coded, steel stud locators at 16 and 24 inches O.C. spacing. Includes pop-up skate wheels for easy transfer of completed wall frame. Framing table can be configured to receive wall framing light bars, other options include custom buildable wall heights, lengths and auto-indexing of optional 2 or 3 tool carriages.
Additionally from Panels Plus are sheathing tables with features that include foot pedal control at squaring end of table, with squaring stops, roller conveyors at both sides, single pendant controls for bridge, tool spacing at 6 inch centers with 3 inch bridge shift for offset nailing. Tool bridges can accommodate from 2 x 4 to 2 x 8 walls, with seam tilt being standard equipment Panels Plus Tool Bridges are available with single beam or dual beam design for two different tool mounts on one bridge. Squaring stations, sub-component tables, conveyors and panel lifts are also available to complete the configuration of the wall panel assembly line. Price includes factory installation and training. 50 CFM at 120 psi air. 120 or 230 volt, 1 phase electrical.
765-751-9990
IBS/Comsoft Wall Panel Light Bars
Reconditioned dual 16’ foot long light bars, includes spare light board. Light bars are compatible with all light-bar equipped or ready IBS/Comsoft, Panels Plus, etc. wall panel equipment driven by ITW (IBS) or other compatible design software. 110 volt, single phase electrical. $18,890 NOW $16,550 FOB MN.
Wood Tech Systems 765-751-9990
www.woodtechsystems.com 765-751-9990
New Spida fully-automated CNC controlled sheathing station, fastens sheathing to wood frame wall panels from 2×3″ to 2×8″ nominal, in wall heights from 7′ to 12′. Straightens studs from the underside of the panel prior to firing fasteners. Fixed bridge fires fasteners into sheathing as wall panel passes under bridge. Works with tools firing up to 3 1/2″ nails. Features touch-screen controls, (4) high-speed nail tools, automated tilting of tools at seams and powered transfer of panels. Approximate size is 18 ft wide x 27 ft long. 230 / 460 volt, 3 phase electrical required. 100 PSI at 28 CFM.
www.woodtechsystems.com
Thanks
for the awesome show! We’ve just returned to Minneapolis after attending BCMC 2022 in Columbus – and we can’t thank you enough for visiting our booths and reminding us of all the terrific people who work in this great industry.
Over the past 95 years, our company has grown and expanded to keep pace with the everchanging woodworking and fabricating industries. We were pleased to bring our best equipment to this year’s tradeshow. We featured our WizardPDS®. This automated perimeter definition system is what gives our tables their speed, accuracy, and setup efficiency.
Add as much or as little WizardPDS® automation as you need. It can be used for the entire table line or a 40’ section to capture the bulk of your schedule.
New table installations and/or retrofit table systems for existing lines are available.
Eide Machinery’s New Product Booth displayed our Universal™ Table and Machinery Exchange Program. The Universal™ Table is designed exclusively for adding to and extending WizardPDS® Automation to your existing table line, even discontinued models.
Our Machinery Exchange Program offers complete upgrade and reconditioning services for your existing truss manufacturing equipment. It can add years of life to older or discontinued lines, and our warranty on exchanged equipment meets or exceeds the original OEM warranty. Everything mechanical is new – including the controls, electrical, and drive systems. You can keep your old machine working until your new machine arrives, and installation and operator training is available for any equipment exchange.
In addition, we brought the ProCut™. This linear saw series is configurable to any assembly line and provides a safe, accurate way to cut your lumber – while keeping your materials moving on your line.
If we saw you in person at the show, thank you for stopping by! If you were unable attend, please contact us to hear more about what we brought to the show…and what we can bring to your plant to improve your material handling, cutting, jigging, and more. In business since 1927, we’ve learned many things about what our customers want and need.
You’re welcome to visit us the next time you’re in Minneapolis, or you can call us anytime at 612-521-9193. See you in Indianapolis for BCMC 2023!
Drive your truss plant into a
company, and
ITW Company,
future.
of Design,
teamed together to bring you the latest in
solutions. Solutions that increase your plant’s production
while helping solve labor concerns and improve employee safety. Contact your local Alpine Sales Representative to learn more.
60
Triad in 2021. Maximum panel height clearance 12′-3″.
for (3) tool mounts along
middle beam, top & bottom plate tool mounts, tilt-tool option, joy-stick controls, power bridge return, e-stop button, all available Paslode tool mounts, manual and all available spare parts. 120 volt, 1 phase electrical required. 100 PSI air required.
765-751-9990
Triad squaring table with two bridges and one Viking power conveyor. Either bridge fits on the squaring table. Builds from 6′-9″ to 12′-3″ tall wall panels to 16′-0″ long. Triad squaring table, model G2SHSQ, has powered clamp / unclamp controls on either end of the fixed side of table.
Triad nailing bridge, model PSTT, has (24) tool mount locations with Paslode tool mounts, auto return and bottom plate laser sight mount. Changed by owner from staple tools to nail tools. Router bridge is manual travel. Viking powered conveyor 23 ft long with support platforms alongside both chains. Forward powered drive only. Foot pedal controls for drive motors. 120 volt, 1 phase electrical required. 100 PSI air required.
765-751-9990
2016 Triad wall assembly equipment, model Diamond Quad Framer, Panel Nailer Bridge and Flow Thru Nailer. Builds from 6′-9″ to 9′-3″ panel heights to 16′-0″ long. Framer includes power height adjustment, (4) Hitachi nail tools, squaring stops, manual dollies and parking sections. Nailing bridge includes (18) Hitachi nail tools, laser pointer, 3″ tool shift function and plate fire. Flow Thru Nailer includes (4) Hitachi nail tools. Handle bar router and all available skatewheel conveyors are included. 120 volt, 1 phase electrical required. 100 PSI at 10 CFM air required at nail bridge and Flow Thru Nailer.
www.woodtechsystems.com
The2022 BCMC show was a very good one for Panels Plus. Our Platinum Series Automated Sheathing Station was a big hit, with a steady stream of people coming into the booth to ask questions about it or get a demo. In fact, the equipment at the show never made it back to our manufacturing facility in Minnesota—it went directly from Columbus to one of our customers.
One of the highlights every year at BCMC is getting to see old friends and current customers as well. Panels Plus has been exhibiting at the show for nearly 20 years and we have been very fortunate to work with so many great people. We always enjoy getting to see so many of them during the show.
It was encouraging to have so many conversations with builders that are expecting to grow their business. You can’t turn on the news without hearing reports of an economic slowdown, but the vast majority of people we spoke with at BCMC expressed optimism about the health of their business. Panels Plus is pleased to play a role in helping so many builders achieve their business goals.
Thanks to everyone who stopped to see us at the show, and here’s to a great 2023 and beyond!
Saw it in the
tool dollies builds
to 16 ft
from 4 ft to 12 ft in height with 2×3″ through 2×8″ material. The framer clamps and squares components with push button activation before nailing. The trident tool dollies use a single tool per dolly and can be set up to accommodate the nail spacing and quantity of nails. Pop-up skate wheel conveyors assist with moving the wall or components. 110 volt, 1 phase electrical required.
The concept of the Spida Extruder is to bring materials to a central location as the product is extended or “extruded” to create the framed wall panel. A single operator in one central location, feeds the studs and sub-components in-between the plates, while the Extruder does the nailing. The Extruder features (4) servo-controlled, indexing, bracket-mounted tools that can be coil or stick fed, hands-free clamping of plates and is adjustable for wall heights starting from 5’-11”, with options to build walls to 12‘3”, from 2×4″ to 2×8″ lumber.
An option is available to add an intermediate tool mount, for fastening blocking between studs, a notoriously slow process in wall panelization that usually reduces production. The Extruder design makes this connection much easier for the operator, keeping your wall production high.
The support stations are adjacent to the Extruder and operators at those stations build the sub-component openings, sub-assemblies (like ladders) which are conveyed to the central operator’s station, where they are dropped and nailed into the panel in sequence.
Conveyors and transfer tables of various configurations are used to bring the parts to the Extruder. Each design takes advantage of curved or raised conveyors to efficiently bring materials to the Extruder and fit within your plant’s material flow in the most efficient way possible.
Once the wall panel is framed, it proceeds by conveyor to a squaring station and a sheathing station for completion. Here too, the sheathing is fastened as the panel passes by the sheathing bridge with its’ (4) four, high-speed tools. There are options for router bridges and automated ply loading. The Spida Sheather is a fully automated, CNC machine that features touch screen controls and tilt nailing at seams.
Over ten years in development and use in Australia and Asia, there are now several locations using the Extruder here in North America. A typical system can be installed in about (5) hours thanks to the modular, “plug-and-play” design of the Spida wall equipment. 120 volt, 1 phase, 15 Amp electrical required and 110 PSI air @ 6 CFM required for each Extruder and Sheather station.
Wasserman & Associates is proud to be a small family-owned company, and we’re equally proud to be a member of this structural building components industry family. Every fall, attending the BCMC show is like a family reunion – so many old friends and family come together in one location to swap stories and share advice. We wouldn’t miss it!
At our booth in Columbus this year, we emphasized how we always strive to personally address your needs. Wasserman & Associates is a representative for new truss, wall panel, stair, door, and finger jointing equipment, and we also offer the option of used or reconditioned equipment.
In particular, our booth emphasized how we can assist with all your wall panel manu facturing needs. On display was the Single Tool Programmable Panel Bridge. Even though it wasn’t dis played with the complete framing table, attendees were able to get a good sense of its capabilities and ease of use.
When you’re looking for reasonably priced equipment with long-term reliability and performance as well as installation support, call us at 800-382-0329 or sales@wasserman-associates.com. As a partner in your equipment selection process, we promote the equipment that best suits your individual requirements, not the equipment that optimizes our commission. Partnering with Wasserman & Associates will result in competitive pricing, support before and after the sale, and the care that you deserve. After all, you’re part of the family!
Developed in a commercial wall panel production facility this is the remarkable ProStack, fully automated wall panel stacker. The ProStack relieves your build team from creating a stack of wall panels and keeps them building walls instead. Stacks 2×4 through 2×8 walls up to 20′ in length and up to 12 feet in height. The ProStack automatically centers each layer including multiple wall segments on the same layer, and the ability to “create” fork lift pockets for ease of loading in your yard or on the build site. (Please see video for more.) 208 volt, 3 phase, 45.3 full Amp load electrical required. No air required. Footprint is 26′-5″L x 19′-3″W.
Here are some of the features of the ProStack Wall Panel Stacker:
• Wall Length Max – 20’
• Wall Height Range – 8’ to 12’
• Material 2×4″ through 2×8″
• Total Weight capacity – 6,000 lbs.
• Total stack Height Max – 6’
• This unit stacks on-center
• System is able to stack on center layers that have multiple wall segments
• Siemens
• Full manual override controls via HMI
• Speed – 45-60 seconds per
2016 Triad exterior and interior wall panel lines with conveyors and terminal stations. Builds 2×4 and 2×6 walls up to 16’ in length with wall heights from 6’-9” to 10’-2” and includes Component Nailer model FTN and panel lift model XPL1000:
Exterior line includes (2) sets of Rough Opening Assembly tables model RO-CAT, framing table model Gen II with manual nail-gun tool dollies each side & stud locators at 16” and 24” o.c., squaring and sheathing table model Gen II with staple & routing combo bridge & side shift for seams @ 3” & 6” o.c. fasteners, top & bottom plate gun mounts for 6” o.c. fasteners, auto stop & tilt features, (3) 10 ft skatewheel conveyors, (4) 20 ft x 36″ roller conveyors and (4) powered infeed conveyors with chain track.
Interior line includes Rough Opening Assembly table model RO-CAT, framing table model Diamond Quad with manual nail-gun tool dollies each side, pop-up rollers & stud locators at 16” and 24” o.c., (2) 10 ft skatewheel conveyors, (4) 20 ft x 36″ roller conveyors.
System sold for over $223,000 new. Sold as one system only. 110 volt, 1 phase electrical required. 100 PSI air required.
Ah,‘tis the season. Sure, you traditionally hear that expression around wintertime, but we’re talking about a different season altogether: BCMC Season! Which means Shopping Season!
It’s that season when CMs start to study automation and equipment that gains automation. Whether you’ve been sitting on the thought for a while, or the demand is pressing on your mind, or labor issues have forced the thought, you likely go to BCMC or read “Component Advertiser” because you’ve been thinking about adding automation to your process. So to get started, you want to learn more about automation in the CM industry.
If you and I haven’t met before: we are Hundegger, an automated CNC wood saw manufacturer that distributes Hundegger CNC wood saws around the world. Hundegger has around 500 employees. Hundegger has customers in 59 countries and have delivered more than 6,000 machines. Hundegger is commonly considered the world market leader for CNC-controlled joinery machines.
Being in the wood CNC machine industry for 40+ years, we’ve picked up some nuggets of knowledge regarding CNC component saws. Having installed 6,000+ CNC machines in the wood construction industry, we’ve seen more than our fair share of automation innovations in material handling, manufacturing work flow, lumber optimization, future flexibility, greater production capacity, reduced labor requirements, and dramatic improvements in lumber yield, all designed to improve the bottom-line.
So even if you decide to get a saw that is not a Hundegger, that’s a-okay: after all, TRUE CNC saws aren’t the best fit for everyone. We’ll feel like we’ve done our job if you are able to make a more informed decision that does not keep you up at night wondering if you made a wrong decision.
This leads us to why we’re here today—we’d like to give you the 411 on CNC saws and automation: their pros and cons, the basics of what to expect from the CNC processes, the infrastructure, installation and cost, and maintenance. If these topics seem up your alley, then let’s go!
Computer numerical control (CNC) is a process for automating control of saws, drills, and milling tools through the use of software embedded in a microcomputer on the saw.
With CNC, each component is computer programed. Usually the program is written in an international standard language called G-code, which is stored in and executed by a microcomputer attached to the machine. The programing contains the instructions and parameters of the cutting tools, the feed rate of materials, and the positioning and speed of the tool’s components. This is why CNC machines have gained a prominent place in the manufacturing industry. Now more than ever, companies use CNC technologies to maximize productivity and automate their process.
Computer-aided design (CAD) is the use of computer-based software to design. CAD (BIM or component design) software is frequently used by engineers and designers. CAD software can be used to create twodimensional (2D) drawings or three-dimensional (3D) models.
Computer-aided manufacturing (CAM) systems import geometry data from various design/BIM models and convert that data into “tool paths” (the motions that the tip of a cutting tool follows on its way to producing the desired geometry of the truss part) for a CNC saw.
Most CAM (BIM or component design) software systems are designed to be machine independent, allowing users to program their parts regardless of what equipment they will be cut on. In the wood truss component manufacturing industry, there are a few additional nuances (to be discussed).
While CAD and CAM systems are very stimulating (to some people, anyway), there is an equally significant piece of the software trail. It covers the gap between the computer-generated “tool paths” as the CNC saw’s cutting tool produces the desired geometry. It’s called the “post processor” or “post” for short. Although it’s not as graphically interesting as CAD or CAM, there’s a lot more to the post than meets the eye. Understanding those capabilities can help your production and automation goal. Post processor software converts tool paths into CNC programs that can be read by a machine’s controller in a safe, consistent, and predictable manner. There are two types of post processors: open and closed.
CAD / CAMAt some level, a wood component CAM software is included in your truss design software. If you can design in CAD/BIM and the geometric cutting data can be transferred to your saw, you have a CAM conversion going on and there is some post processing occurring. If you are authorized to see and customize the post, you have a “open” post. If you are not authorized to see the post, it’s called a “closed” post.
Open or closed—why does it matter? Well, it depends on what more you intend to do. If you want fixed simplicity, then closed is fine. You’ll have the level of performance that’s been advertised and you don’t have to worry about making changes. But, if you think you’ll be interested in customization options, then you want open. With open post systems, you can have the software customized to fit your specific requests, and you won’t be limited to pre-determined tool paths. Vendors, resellers, and users can continue to make modifications and collaborate with other equipment by customizing the automation process over years as a business grows and the needs of the manufacturing process evolve.
Advanced posts can create additional functionality for their equipment even when the desired routines are not supported in the CAM system itself. For example, there already is enough data available in today’s CAD files to drive robots! The developers of open post processors have created a specialized module to drive a wide variety of six-axis robots. Think of it like this: if the data is in the CAD/BIM design program file, then you can use the CAM system and an open post processor to program a CNC machine to its full capability This is the difference between a CNC saw and automation.
Production manufacturing requires a high level of visibility to maximize efficiency. The CNC/CAD/CAM allows you to track your jobs with CAM “post processing.” With non-CNC equipment and generic or closed CNC post processors, you may get what you need, but you’re often stuck manually modifying software and equipment to get it to match up with your methodology and preferences. With open custom-developed CNC posts, you get much more. You can add or modify your preferences and practices into the post itself, allowing you to focus on designing your best tool paths or adding more automation equipment, such as infeed automation, tool changing robots, and production delivery systems.
Having more control over your project with this advanced technology leads to fewer errors, therefore resulting in faster production cycles and minimal revisions needed.
Don’t Forget! You Saw it in the
Machine automation started as a revolutionary innovation in the manufacturing industry. I still get calls today from CMs who say, “Hey Steve, we’re looking at automating our business and so we need a quote on your CNC saw.”
Hopefully, if you are still with me, you’re realizing a CNC saw does not mean you are magically “automated.” Once programmed properly, the right CNC milling machine can process multiple parts at a high level of precision. This can be done in a closed environment, a one-stop shop, meeting your basic production needs. Or, it can be done in an open environment, which makes a CNC machine a prime candidate for automating a plant.
Today’s CNC software platforms give CMs more than just end-to-end visibility and control of your manufacturing operations. They also let you use the generated data to implement improvements and move your business into the future. The right operating software optimizes production, improves flexibility, and boosts speed-to-market, giving you visibility and control over all of your processes. Combining the right CAD/BIM and CAM to automate the right CNC manufacturing process has been adopted and implemented by manufacturers globally.
With increased efficiency, CMs are able to take on larger and more complex jobs with less effort and less stress. With the right CAD/CAM, the right CNC machines can help stimulate the optimizing and processing of the model and help further your customization and your automation needs!
If we took the time to say everything there is to say about CAD/CAM/CNC, we’d be here all day. But if there’s one thing you take away from this article, let it be this: we truly believe a CNC saw is a great step at achieving automation in wood component manufacturing. Scratch that: the right CNC saw combined with the right CAD/design software and the right CAM/post processing can provide just about everything from “just what you need” to “more than you imagined.”
Of course I’ll have a lot more to say about CNC saws, but we’ll cover those topics on another day. If you’d like to learn more or jump ahead, just contact me directly or visit the Hundegger website.
With a Terminailer XP, it takes only one person to drive between 30% and 70% of the framing nails in any given job . And all this nailing is done within a secure enclosure, so your people are protected from costly nailing injuries while eliminating literally millions of repetitive motions ( 4,001,398 repetitive motions to be exact , judging from the total nail count tallied recently on a two year-old Terminailer XP).
That’s a lot of nails successfully installed to be sure, and a lot of debilitating repetition your workers’ hands are spared, without any complicated training, software or lengthy setup time required.
Developed by people who know wall panel production, Terminailer XP boasts multiple repeat buyers, 20-plus machines performing exceptionally in the field and tens of millions of nails installed. Thoroughly field-proven, Terminailer is ready to drive greater productivity for you. Contact us today for more information.
2003 JDH TRUSSMASTER SIDE-
10,000 Lb Tandem Axles (Dual Wheels). 26,000 GVWR. Deliver Trusses Vertically. Stretch from 18' to 38'. Raise Loads Hydraulically. Air Brakes. $6,900 FOB CA
Wasserman & Associates 800-382-0329
www.wasserman-associates.com
1995 Pines 45' Chip Trailer
• Modified by LMI TENN
• 8" Floor Cross Members
• Reinforced Roof
• 22.5 Tubeless Tires
• Sl iding Tandem Axle (for weight distribution) (FOB PA) $9,900 Wasserman & Associates 800-382-0329
www.wasserman-associates.com
Step Deck Roller Trailer
40'-0" Lower Deck, 12'-6" Upper Deck Hydraulic Tilt on Lower Deck
Lower Deck has 3 Split Load Lifts
Roller Locks (upper & lower decks)
GVWR: 37,000 KG (81,400 LB)
Air Ride Suspension
Tires & Brakes are Good Winches & Straps
Price in US Dollars
$30,000 NOW $25,500 FOB ON
Wasserman & Associates 800-382-0329
www.wasserman-associates.com
1987 Barnes Pole Trailer
1987 Barnes pole trailer, model RTY. Carries trusses peak down, with spans from 28’6″ to 46′-0″. Includes bolster arms
It’s important to explore your options when considering the financing of your business equipment. There are a number of financing companies out there, as well as local banks, and it’s likely that the rates and additional interest charges will differ.
Do you go with the lowest rate? Think about the whole picture before you jump at what might seem to be the least expensive financing. The whole picture includes any interim interest payment, how difficult the application process is, is the lender filing a blanket lien on the business, are yearly financial statements required, and does the lender restrict you from seeking other funding?
Consider a few other things: How flexible is your lender? Can you borrow for both new AND used equipment?
We invite you to consider the advantages that we provide of being able to call your funder and getting a live person on the other end of the phone to respond to your questions. Responses answered by a seasoned professional who knows the equipment, the vendors, the necessary procedures to get the equipment into your hands as quickly as possible.
Not every deal falls neatly into place. We work with you, on a personal level, to obtain what is needed to get an approval. We go the extra mile to get the best rate for you with the best terms.
It isn’t by coincidence that a large part of our business is from repeat customers. Individual small business owners and large corporations alike recognize the advantage of a funding source that works WITH them and not against them.
We are Acceptance Leasing and Financing Service, Inc. We’re proud to be celebrating our 30th anniversary in business this year. Established in 1992, we pride ourselves on our Certified Leasing and Financing Professional designation. We are a member of SBCA and a frequent attendee of the BCMC tradeshow. We can provide financing for any new and, regardless of age, used equipment.
We invite you to call us at 412 262-3225 to see how we can help you.
Our swivel casters are precision built with perfectly aligned raceways. All cold-form parts are made to exacting tolerances from heavy-gauge steel, and are hardened for severe service and long wear. Series B-4 carts include four casters, one at each corner, to prevent "tri-cycling" of long lumber loads.
Adapts to Any Saw. Left or Right Hand Operation. Feet & Inches System (Stops at 12” Centers) or Inches System (Stops at 10” Centers). Motor: 1/4 HP Linear Actuator (110 Volt). Stop Rail: 2 x 4 x 1/4” Aluminum Extrusion. Stops: Jig Bored Steel. Stop Blocks: Machine Billet Aluminum. Optional Lengths from 5’ to 60’. Optional Gang Stop. Add $890 per 10’ Section of Heavy Duty Roller Conveyor with Stands $7,890
Wasserman & Associates 800-382-0329
www.wasserman-associates.com
Since 2006, we've been helping businesses of all kinds build their online presence. We make websites and software for the construction industry to empower companies to reach a wider customer base and engage their audiences. Companies all around the world work with us to make websites and apps that people actually want to use. Reach out to Wolf X Machina if you're a business and you want a website that actually drives results.
WOLF X MACHINA
www.wolfxmachina.com info@wolfxmachina.com
2748
3248
3260
3660
3672
4072
3696
4896
*Other models and sizes are available on request. FOB NC.
Wood Tech Systems 765-751-9990
www.woodtechsystems.com
Sincethe 1960s, fabricators have used machine stress rated (MSR) lumber of all species to improve the performance and reliability of their engineered components and structures.
Nowadays, you don’t have to look far to find a successful component manufacturer who relies heavily on MSR grades to produce high quality roof trusses, floor trusses, and wall panels. While the reasons to use MSR are numerous, they all boil down to one word: quality
Rigidply Rafters in Richland, Pennsylvania, is a family-owned operation that has been building roof and floor trusses since 1963. President Vernon Shirk says the company has been using MSR in their products for more than 35 years. “It’s really helped our business,” he says. “We know it’s something we can count on. We are providing an engineered product, so MSR is crucial to that.”
Dave Kipp, Purchasing Manager for Structural Component Systems (SCS) in Fremont, Nebraska, agrees. “We’ve been using MSR pretty much since day one when SCS was founded in 1987,” he says. “It’s a crucial element for roof and floor trusses, especially with today’s challenging designs for residential and commercial construction.”
“By using MSR, we reduce the overall fiber required for the design of our products,” says Kipp. “For example, a top chord on a roof truss might require 2x6 if only #2 is available but that can often be replaced with a 2x4 in MSR. Likewise, floor trusses may require more webs if the chords are #2 but using MSR can allow us to reduce the number of webs and/or the size of the connector plates used.”
Clear span flexibility is another benefit of MSR’s consistent strength values enjoyed by companies like Rigidply. “One of our specialties is large span trusses for ag and commercial projects (60-100’ clear span),” explains Shirk. “MSR helps in that part of the business, too. Designers can rely on MSR properties, use full-design strength, and avoid overbuilding.”
Why is MSR key to a quality truss? In contrast to visual grades, machine rated lumber production is centered on measuring the physical properties of each piece of lumber on the line. MSR manufacturers are required to test samples during each shift, and independent third parties audit the entire quality assurance process to confirm conformance with published design values. This testing process verifies that production consistently meets design value requirements even as timber growing practices and environmental conditions change.
The result? Component manufacturers have confidence in MSR’s higher strength values, which in turn provides greater design flexibility This allows truss designers to optimize the lumber in each truss, resulting in a more efficient use of materials and lower installed costs.
The
Steve Szymanski of Drexel Building Systems in Little Chute, Wisconsin, has been involved with truss design for 33+ years and says he wishes more truss designers understood the value of optimization in truss design. “The analogy I like to use is cooking,” he says. “There can be similar recipes for a certain type of dish but it’s the cook who chooses high quality ingredients and uses them in just the right amounts that usually produces the best end product. The same is true when using MSR lumber to optimize truss designs. Because there are more grades to choose from, you can make a more cost-effective truss.”
Szymanski says he often uses a basic floor truss system to illustrate the overall installed cost savings with customers: “I explain that, because we can be confident in the higher design values and deflection properties of MSR, we can often use fewer trusses in the floor system as a whole placing components 19.2 inches on center instead of 16. Less lineal footage of product to install means a lower installed cost, while delivering a high performance floor that doesn’t sacrifice loading capacity.”
Consider this example from Szymanski that maximizes the benefits of using MSR lumber in his optimized designs to create a high performance, cost effective product. Shown are two drawings of the same 22’ floor truss: the first truss i s designed with 2x4 SPF No. 2 and the second truss is designed with 2x4 SP 2850F 2.3 MSR lumber.
The 22’ floor truss designed with 2x4 SPF No. 2.
While the drawings are almost identical, the performance that results from Szymanski’s optimization of the design is particularly noteworthy. The floor truss designed with the MSR grade can be spaced 19.2” on center, instead of the tradition 16” on center, saving the builder one truss for every eight feet of floor system. What’s more, the MSRbuilt system will perform better as the design values of the MSR deliver approximately 23% lower deflection. While these optimized trusses might cost a bit to build due to slightly larger plates and higher quality lumber, overall installed costs will go down as fewer trusses and less framing labor is needed.
The 22’ floor truss designed with 2x4 SP 2850F 2.3 MSR lumber.
Don’t Forget! You Saw it in the
Rigidply’s Engineering Manager agrees that using MSR is key to truss design optimization. “Our designers are always looking to reduce the amount of web lateral bracing required by increasing the lumber grade to our MSR options,” explains Tim Riegel, PE. “Reduced lateral bracing requirements reduces the installed cost and overall amount of lumber needed within a roof system. I think it’s one of the biggest benefits of using MSR lumber.”
Last but not least, wood continues to be one of the most renewable resources for use in a variety of applications. In addition to consistent strength, high quality, and increased flexibility for optimized design, every single piece of MSR lumber can be used to the maximum, which allows component manufacturers to turn inventory faster and reduce waste costs. At the end of the day, the combined benefits of using MSR lumber demonstrate a clear commitment to quality and make the engineered components even more marketable.
The bottom line for those considering a move to using more MSR lumber in trusses? Shirk says, “you know what you’re working with and that broadens your capabilities.”
For more information on common grades of MSR lumber and design values by species, visit the MSRLPC website.
The MSR Lumber Producers Council (MSRLPC) represents the interests of machine stress rated lumber producers in the manufacturing, marketing, promotion, utilization, and technical aspects of MSR and MEL lumber. Suppliers, customers, and professionals may join as Associate members. Members enjoy:
•
•
•
•
“There is no question that the MSR Lumber Producers Council meetings are worth your time to attend. Understanding the MSR market has helped my company grow during these trying times. The information you will receive from the guest speakers and members of the Council is unparalleled!”
—Sean Kelly, Automated Products Inc.
Quincy QT-15 splash lubricated, reciprocating compressor with 120 gallon tank.15HP motor supplies a manufacturer stated 52.5 CFM at 175 PSI. 230v, 3 phase electrical.
$2,990 FOB IN
Wood Tech Systems 765-751-9990
www.woodtechsystems.com
The WoodRunner WR-2 lumber retrieval system seeks and retrieves the exact boards needed to cut. The core of the system is a trolley with an automated picking head. The trolley moves back and forth on a runway truss positioned over lumber carts while the picking head’s laser scans below. After locating the specific piece of lumber needed, the picking head uses a powerful vacuum to hold the board while moving it to the infeed deck.
Call for Price
Eide Integrated Systems, LLC 612-521-9193
www.eidemachinery.com
New, laser projection system from SL Laser. Projects roof truss, floor truss and wall panel design images accurately onto building surface, for faster setup and fabrication times. Each laser head provides 21' projection length (@15 foot ceiling heights). Includes system computer, cables, mounting hardware for attachment to customer's structure, factory installation, training and choice of green or red laser. Works with each connector plate manufacturer's design software. Modular nature of the laser heads allows for easy, future expansion of system length. 120 volt, 1 phase. FOB NC Wood Tech Systems 765-751-9990
www.woodtechsystems.com
2003 Virtek, 3-head system, model LPS-6R, includes PC with monitor and keyboard, PC enclosure, two LPS-6R heads for parts and all available power cords. Projection area of 14′ x 20′ with proper mounting height over work area. Red laser projection. 110 volt, 1 phase electrical.
$9,890 FOB OK
Wood Tech Systems 765-751-9990
www.woodtechsystems.com
The Generation 3 Framing Table has adjustable 20’ long walls, with wall heights from 6’9” to 14’3”. Studs are placed between color-coded stud locators. With just a push of a button, the width adjustment clamp is activated to clamp and square all components. The Generation 3 Framer features a wider table top, designed with the framer in mind. Our new Anti-Slip Surface that allows the operator to work on a comfortable and safe surface.
Call for Price
Eide Integrated Systems, LLC 612-521-9193
www.eidemachinery.com
Electrical Supply:
Accurate:
Stop Rail:
Stops:
Stop Blocks:
Components:
Ground
Polished
5 feet (60”) to 60
12
12
(720”)
If you are looking for the fastest, most consistent way to measure and cut your product, then the Hain Measuring System (MEA) is your answer. The MEA changes from one length t any length instantly, up to 60’, without changing the operator’s position on the line. It is also highly accurate (+/- .010) and quickly moves from one length to the next in seconds. The MEA is designed for quick and easy setup and is simple to use. Even a first time user will be productive with little or no training required. It can adapt to any saw and can be mounted to any surface so that you can integrate the MEA with your existing setup. The MEA is versatile allowing “left” or “right” handed operation and measurement in “feet and inches” or “inches” depending on your preference. The MEA is also available in a “Skid Mounted” version.
As a truss and component manufacturer, you know how tough it can be to coordinate all the resources you need. That’s why Simpson Strong-Tie, a dedicated partner to the construction industry, continues to create new, customer-focused solutions. Our open-platform software can be integrated with your existing systems, making collaboration easier than ever. Now you can design and manage projects while keeping your people, processes and products all connected. And because we’re focused on service and support, you can stay focused on business success.
Open doors with open-platform software. Visit go.strongtie.com/componentsolutions or call (800) 999-5099 today.
Ihadplanned to start writing a series about building a new home and large workshop... but things have not gone as planned. Day one in moving my RV from Florida to southern Indiana to use as our base camp, I had to grab some things out of storage. Searching my large storage slot filled with tools I found what I needed, just behind a portable 12k generator. No problem, I think, just reach over some boxes, drag the generator over a few inches using my right arm, and I am good to go. But something else happened. I felt a pull in my back, which I thought would be just another muscle that would talk to me later, as more and more do every morning. I grabbed the item, closed the storage unit, and went back to the RV.
The next morning, I had a more than usual pain in my back. Even so, we were on the road to Indiana. No back pain would delay our mission, even though that spot would start really talking to me. After two days of bouncing and jarring along our lovely highway system, my right arm was numb with pain shooting down it. Two fingers were numb, and one was, as I say, drunk. The next day, it was bad enough that Beth made me go to the emergency room. After two emergency room visits and one visit to a neurosurgeon, the diagnosis was a severely compressed disk and pinched nerve – all from dragging a stinking generator 6”, which is something I have done for years (decades) without any issues. This was definitely not part of my plan.
So here I sit in southern Indiana, starting two construction projects, a shop and a home, but unable to do physical work. I can hold a measuring tape with my left hand, but no lifting, pulling, nailing, standing for long periods, or motion to aggravate the back. Dang, the idea of all of the processes I wanted to do that now I have to hire out hurts my pride. I could build anything, but not right now and maybe not again depending on what I hear at my next neurosurgeon appointment.
My point is that we guys go through life thinking we are bulletproof. Especially with our construction background, we don’t think about how we may be pushing our limits as we get older. As I tell my kids, life is full of choices and choices have consequences. Beth says I better learn to slow down and leave the tough stuff to the younger generation. Maybe I will, but just a little bit.
Your “recruiter down the hall,” I’ve been recruiting off-site manufacturing industry professionals for 30 years through TheJobLine.com. Contact me for assistance with recruiting assignments or outplacement job search: twm@thejobline.com
Relationships and Services NOT offered elsewhere.
RFitzgerald@FitzGroup.com
✓ New, state-of-the art component manufactoring & material handling systems - by the industry leaders.
✓ Used & Reconditioned machinery. Eide’s warranty on reconditioned equipment meets or exceeds the new machine warranty.
✓ Installation & Operator Training included or available with any equipment purchase.
✓ Table Retrofit and upgrades for Wizard PDS.
✓ Parts & Supplies. Our parts department stocks thousands of parts & supplies for most brands of cutting and pressing systems. Custom and obsolete parts fabrication is our specialty.
✓ Service & Repair. Our service department offers complete repair, rebuilding and retro-fit services; in-house or on-site.
✓ Equipment moving, installation, and operator training services.
✓ Auction Buyers Service; We remove, ship and reinstall your equipment.
✓ Overseas Buyers; We can service and update your purchase as desired, containerize, ship and reinstall the machine in your plant.
Itis common for truss plants to be owned at least in part by a lumber yard. This relationship should, at least in theory, provide for a great business relationship. The lumber yard can focus on relationships with the builders, home owners, and developers knowing that they have a dedicated manufacturing facility ready to service their clients. And the truss plant can focus on manufacturing and delivering quality products, with the knowledge that the lumber yard will act to provide sales and marketing.
Ideally, having common ownership between the lumber and truss divisions provides the cooperation to optimize the opportunity for both entities. The truss plant can design and manufacture value-added components that make the framer’s life easier – and construction faster – while simultaneously providing an increased value product for the lumber yard to sell and generate profit. It’s truly a win-win-win situation.
However, I have witnessed exactly the opposite of this in large operations that own both lumber yards and truss plants. Rather than eagerly welcoming more items to provide as part of the valueadded truss package, the lumber yard actively discouraged the truss plant from providing more than was necessary so that they could maximize lumber sales. In effect, they would rather sell a $50 pair of rafters than a $100 valley truss.
Simple common-place items like valley sets were left to be site-framed. Large areas of the roof layout would be cross-hatched to show over-framing to be done on site by the framer. While the over-framing area on the layout could appear significant, a visit to the job site can quickly reveal that the voids to be site-framed could represent days or weeks of work to the framer filling in the roof lines. I once had the VP of construction for a large, upscale home builder comment that he didn’t care what the cost was in the truss package, he needed more components to help cut down the framing time. He knew that savings on the site labor side, and the benefits of faster closings, would more than offset the additional component costs.
Truss companies spend a significant amount of time developing a 3D CAD model of a building. Once that model is created though, it’s a relatively minor amount of additional work to add in components beyond the basics, and every one of those components will save time in the field. If you are a truss designer, talk to your salespeople, or the associated lumber yard sales staff, about the additional components you could provide that your framers will love, and that may set you
apart from your competitor down the road. Depending on the region you are working in, common add-ins to consider might include:
• Valley sets
• Lay-in gables
• If not lay-in gables, at least drop the flat chords of your step-down hips
• Complete dual pitch corner sets
• Gable end ladders
• Top chord bearing details at beams to eliminate the need to supply and install hangers.
I am sure there are other components that you are supplying – please send me an email to let me know what else I should have on this list.
Yes, your truss quote will have a higher bottom line number than your competition, but time saved on site will more than offset that cost. Salespeople need to educate their customers on the benefits of increasing component use. This was true 30 years ago and, with the skilled labor shortages today only set to get worse in the coming years, it will be even more true tomorrow.
If you want help finding that next perfect component designer or design job in Canada, please contact me. If your work is in the mass timber world anywhere in North America, I’d love to talk to you about connecting you to that next great job or candidate. You can reach me at secord@thejobline.com, or 800-289-5627 ext. 2. I’m also happy to engage at: LinkedIn.com/in/geordiesecord. www.thejobline.com
The Hain Systems Framer (HSF) will help you build square and accurate wall panels for residential or commercial construction applications. It will help you cut building costs by saving time and improving your quality. It’s a reliable, efficient and proven system that features a ruggedly simple design. The HSF is based on a proven design with over 20 years of actual production use and maintenance experience. It comes fully assembled and is designed for portable job site framing or in-plant permanent installation. The table has many optional attachments and will support Mylar Tape wall layout or any other type of layout. The optional gun rails can also be retro-fit to any table.
Dimensions: Length: 5
(60”) to 60
(720”)
12
12
If you are looking for the fastest, most consistent way to measure and cut your product, then the Hain Measuring System (MEA) is your answer. The MEA changes from one length t any length instantly, up to 60’, without changing the operator’s position on the line. It is also highly accurate (+/- .010) and quickly moves from one length to the next in seconds. The MEA is designed for quick and easy setup and is simple to use. Even a first time user will be productive with little or no training required. It can adapt to any saw and can be mounted to any surface so that you can integrate the MEA with your existing setup. The MEA is versatile allowing “left” or “right” handed operation and measurement in “feet and inches” or “inches” depending on your preference. The MEA is also available in a “Skid Mounted” version.
Ace Equipment Vertical Bailer
Ace Equipment model Vertical Bailer, infeed opening 24″ high x 66″ wide, 59 second cycle time, 10 HP pump, 10 GPM at 2,200 psi, 6″ diameter cylinder x 48″ stroke, 37 PSI at pressing platen with 62,000 lbs. pressing pressure. Overall nominal dimensions 6′ wide x 4′ deep x 12′ tall. Controls 120 volt, 1 phase electrical. Bailer 230/460 volt, 3 phase electrical required.
Weight 4,200 lbs.
#4,490 FOB IN
Wood Tech Systems 765-751-9990
www.woodtechsystems.com
6 detection zones to locate missing plates. Horn & zone lights indicate missing plates. 12" to 60" adjustable height from floor 110 Volt / 1 Phase. New control panel switches & lights in 2014. Needs circuit board repair or replacement and new tower light. Includes 4 extra detection zone boxes.
$2,500 NOW $1,500 FOB NE
Wasserman & Associates 800-382-0329
www.wasserman-associates.com
pendant.
&
need
Three (3) 2004 model PD-4 SL laser heads. All three heads are functional but need some repairs before being installed. The heads are also valuable as parts heads for the motherboards and other components. Repair quotes are available upon request.
$11,900 FOB WI
Wood Tech Systems 765-751-9990
www.woodtechsystems.com
OnSeptember 20, A-1 Industries, a leading manufacturer of preengineered wood trusses in the Southeastern United States and the Caribbean, celebrated our 45th anniversary with the launch of a new corporate video and a special day of appreciation for our employees at the Fort Pierce, FL and Bainbridge, GA manufacturing facilities. Whether you had been with the company since the start or were a relatively new hire like me, the day filled you with a sense of pride and appreciation for all that John Herring has accomplished in these past 45 years.
Many CMs know John from his years of involvement in the Structural Building Components Association (SBCA), formerly the Wood Truss Council of America (WTCA), where he served as President in 1990 and was subsequently inducted into the WTCA Hall of Fame in 1999. And now, decades later, John remains an insightful businessman who continues to make his mark on our industry.
As he strives to build A-1 into a 100-year company, it was especially enjoyable to hear him reflect on his humble beginnings. As John himself tells the story:
On September 18, 1977, at 6 am, I first walked into the 600 sq ft office building in Mangonia Park, FL and switched on the light. There was a reception area in front of me, one office to the left, two offices to the right, and one bathroom. So, I thought, ‘OK, I guess we need some furniture.’ I walked down to the end office, which was the smallest, but it had a back door to the outside. This is my office! I can escape to the Shop! I stepped outside and surveyed the yard: approximately 2 acres, with only about one-third paved. A pole barn sat to the left back corner, maybe 10,000 sq ft, and I said, ‘OK, let’s get to work.’
A Clary long cutter saw, a Clary short cutter, a roller press, a 22-flatbed dump truck, a DeWalt radial arm saw, a forklift, and a truckload of lumber all sat in the middle of this building. So, Day One in the history of A-1 was about to begin.
Looking back, I am most amazed at how the industry has changed and grown. I can say without a doubt that A-1’s success is due to its ability to adapt, think ahead, only make promises that we can keep, and be the best. ‘On Time Deliveries Guaranteed’ was our Yellow Pages headline.
Our first hire was a very young lady as our receptionist. We hired her on the spot, and she seemed OK. Of course, I was in the Shop, so I had nothing to do with office matters. After about a week, I read her resume, and I literally broke out laughing. Name, address, home phone (no cell phones at that time), date of birth, sex… I swear, it read ‘NOT TOO OFTEN!’ OMG! I thought, ‘We better start hiring better, or this isn’t going to work!’
So, from the first week in business, I convinced the partners that we should all be involved in hiring and that we should read each resume before hiring. From then on, our mission was to hire good people, intelligent people, honest and hard-working people, and we would have a much better chance of success. History speaks for itself!
From that small location, we moved to a 3.75 acres facility in West Palm Beach, with a larger pole barn, a second smaller barn for saws, and a 1200 sq ft office. We stepped it up big time, so we thought the location was a brilliant one for growth.
Shortly thereafter, I bought out my partners and in 2000, due to an eminent domain by the state threatening our existence, I planned a new concept in truss manufacturing, by taking out steps and making it more efficient and competitive. So, plans were drawn on a napkin: a dream, a vision, and the start of being a 100-year company was formed.
Looking back, I can say the leaps we made with facilities each time were enormous. Yet, it is still the people we call family. It is still the work ethic and our Core Values: Own it, Passionate, Honesty, and Respect, and how we hire and who continue to make up our company. These are the most important aspects of making the goal of a 100-year company.
Today, with the Bainbridge operation and its potential across 80 acres, and the Fort Pierce facility expanded to 27 acres with a new 40,000 sq ft building, the sky is the limit. I am so proud to be on this A-1 TEAM. Yes, TEAM A-1! It is our people that ensure customer satisfaction and make our reputation. Each and every one is equally important and critical to our success. We all want this for the TEAM A-1! 100 YEARS!
On September 20, John did many things to thank us, his employees, for our service to the company. On behalf of the employees, I’d like to give a hearty, “Thank you, John,” right back to him.
the construction supply community has had 97 deals made by 50 buyers. At this same point in 2021, Webb Analytics counted 102 deals by 50 buyers. So much for predictions of a slowdown in M&A in 2022.
What’s different is the size of the deals: A total of 255 yards have changed hands this year vs. 411 by late September 2021. On the other hand, we’ve had more greenfield openings so far this year (127) than by mid-September last year (115). There also have been a few more closures--29 vs. 24.
The most important single deal in recent weeks undoubtedly was Builders FirstSource’s acquisition of Trussway, a components manufacturing giant with six locations, all in hot markets: Houston, Orlando, Denver, Dallas-Fort Worth, Atlanta, and Washington, DC. Trussway ranks 35th on this year’s Construction Supply 150, with an estimated $400 million in revenue in 2021.
Truss manufacturers have been prized targets these past two years, and not just for BFS and the No. 2 lumberyard, US LBM. Just last week, for instance, Tibbetts Lumber acquired D&M Truss in Pensacola, FL.
One of the only rivals to truss manufacturers for desirability is landscaping facilities, a segment where SiteOne Landscape Supply leads the way. On Sept. 1, SiteOne purchased three-unit, Floridabased Stone Plus, and six days later it followed up by acquiring Kaknes Landscape Supply of Naperville, IL. So far this year, SiteOne has made 10 purchases that have landed it 26 facilities.
In other action:
• Ganahl Lumber ventured further north into Los Angeles County by acquiring Northridge (CA) Lumber.
• Big C Lumber bought Delton (MI) Pole Building Supply.
• Kodiak Building Partners acquired Denver-based Western Interior Supply.
• R.P. Lumber grew in Iowa by purchasing Southwest Building Supply of Mount Ayr, IA.
• Southeast Building Supply Interests, a unit of Building Industry Partners, entered Alabama for the first time by purchasing Buettner Bros. Lumber of Cullman.
• Graber Building Supply bought Tuscola (IL) Home Center.
• RoMac Lumber & Supply bought T&D Distribution, which focuses on serving customers in The Villages, FL.
• Former builder Dave Colver bought Piscitello Home Center of Easton, PA.
• US LBM’s Coastal Roofing Supply launched in Tampa, FL, co-locating with another US LBM unit, Rosen Materials.
• ABC Supply opened new branches in Redding, CA; Cheswick, PA;
• SRS Distribution’s Advanced Building Products opened a new facility in Monroe, LA.
• Gillman Home Center opened its doors in Muncie, IN.
• Floor & Decor grew again, opening branches in Maple Grove, MN; Lexington, KY; and Mooresville, NC.
• Port Royal (SC) Ace Hardware opened Sept. 5, while late August saw the closures of Chicago’s Joe Harris Paint & True Value Hardware as well as Biloxi, MS-based Eltzey’s True Value Hardware.
• Valu Home Center revealed it was closing stores in Batavia, Fredonia, and Lakewood, NY, effective Sept. 30.
Webb Analytics is a data and research consultancy that helps executives in construction supply spot the trends, threats, and opportunities that matter most. It’s led by Craig Webb, one of the nation’s best-known industry figures and the former editor-in-chief of ProSales, the construction supply industry’s most honored publication. Aside from the Construction Supply 150, Webb Analytics also produces an annual deals report, consults with dealers, publishes research reports, and speaks at industry events. Contact him at cwebb@webb-analytics.com.
either two
The truss industry relies on 3rd party quality assurance services to provide random visits to review the plants Quality Assurance program along with their operations. If your plant needs to comply with the IRC, IBC and to those who depend on solid, experienced QA expertise, we ask you to consider selecting Timber Products Inspection, Inc. (TP) as your choice for 3rd party inspections.
Proudly serving the forest products industry for over 50 years, TP brings the expertise you need to ensure your business is successful. As a responsible partner, TP delivers to clients, employees, and the industries we serve the confidence to drive value through the effective use of our diverse professional team.
TP would like to welcome the following authorized agents to our inspection team, each of whom have many years of experience in the truss industry!
• Al Coffman
Jean Hart
Curt Holler
Chuck Ray
Glenn Traylor
Elliot Wilson
If you have questions about how you can make this selection, please contact your authorized agent above or Glenn Traylor at 919-280-5905 or trusguy@gmail.com.
https://www.tpinspection.com/ https://www.tpinspection.com/auditing-services/truss
Machinery (BAM) Titan series pre-hung door machine. Designed to produce between 150 and 250 doors per day. Multi-function door machine capable of doors 1′-6″ to 4′-0″ in width, and both 6′-8″ or 8′-0″ door heights. Processes both 1 3/8″ and 1 3/4″ thick door slabs. Machines the door, hinge jamb and strike jamb all at the same time. Capable hinge sizes include 3 1/2″ x 3 1/2″, 4″ x 4″, 4 1/2″ x 4 1/2″ with 5/8″ radius. Cycle time with flush hinge routing is 45 seconds. 10′ long x 7′-6″ wide footprint. Shipping weight 4,000 lbs.
More information Click Here
Price based on configuration 765-751-9990
www.woodtechsystems.com
Automation Machinery (BAM) model 2220, stair wedge saw station automatically produces wood wedges used to lock stair treads and risers into slots cut into the stair stringers…
Builders
Price based on configuration
FOB FL
765-751-9990
www.woodtechsystems.com
TheJobLine.com
Truss Designer. MiTek software. Experience required: 2+ years. Components include: floor trusses, roof trusses and wall panel experience is a plus. Markets include lumber yards, single family, single family custom, and light commercial. Work Schedule: average 40-45 hours a week or more if interested.
Compensation hourly, plus overtime, and base pay from $22 to $28hr+-. ($45k-70's) Yr.+-) depending upon experience, monthly bonus based on production output/errors. Benefits include: Medical, Dental, Vision, retirement programs, and ESOP (Employee Stock Ownership Plan). Relocation is open to negotiation. Low cost of living. EOE (Equal Opportunity Employer). J15235
Not a remote job but who wants to work remote when the office is in Montana?
visit: www.thejobline.com
email: mail@thejobline.com
Our client in Florida is looking for Remote Truss Designer NOW, before the end of the year! Work remote, or in an office location in Florida. They need ONE Basic or Intermediate level Remote Truss Designer. Fantastic benefits, compensation is very competitive, and they use MiTek software. Remote is an option if you have a home office and remote experience, or you can work in office. They may consider someone without remote experience, just depends on the skill level. Fantastic benefits, compensation is very competitive, and they use MiTek software. I can't say more about this opportunity here.
Compensation can be estimated based on your experience and skill 45 hours per week average.
Overtime hours are usually available. Call/email for details
visit: www.thejobline.com
email: mail@thejobline.com
Plant Manager - Truss/Panel J15258 Midwest Operations Manager J15231 Southwest
Truss & Wall Panel Designer J15259 Midwest
Truss Design/Estimating Manager J14171 Texas
Remote Multifamily Truss Designer J15257 REMOTE
Project Manager - Yard/Site/Trans J15256 Southeast
Plant Manager - Truss J15255 Florida
Project Manager J15252 South
Residential Order Tech J15232 South
Truss Designer J15251 South
Truss Designer J15250 South
Remote Multifamily Truss Designer J15249 Southeast or Remote
Remote Truss Designer - J15248 Eastern US
Procurement Manager J15247 Remote or in Texas
Operations Manager - Truss ID: J15230 Southwest Yard/Field Delivery Manager J15240 South
Truss Designer J15239 South or Remote
Truss Designer - Remote (MiTek) J15241 Remote
Truss & Wall Panel Designer J15226 Northeast
Remote Truss Designer - Alpine J15246 Midwest Candidate preferred
Outside Sales - Truss/Panel/EWP J10600 Southern IA
Truss Sales - Truss/Framing Packages J15245 Texas, Louisiana, Oklahoma
General Manager - Truss J15242 Upper Midwest Truss Designer J14164 Florida
Remote Designer - Truss/Panel J14179 KY
Components Package Estimator J15238 Western US
Truss & Wall Panel Designer J15237 Western US
Truss Designer J15235 Montana
Advancement Opportunity to Production Manager J15219 South
Remote Mega-Multifamily Truss Designer J14177 Nation Wide
Remote Multifamily Truss Estimator J15227 USA
Remote Mega-Multifamily Truss Design Manager J15234 Nationwide Mega-Multifamily Project Manager J15229 South/Southeast
Senior Truss Designer J14214 Remote - Central or Eastern time zone preferred
Remote Truss Designer - MiTek J15228 Florida
Senior Designer - Panel/Truss J14181 Midwest
Senior Truss Designer - Truss J13952 South
Senior Design/Design Manager | Alpine J15224 Knoxville, TN
General Manager - Truss J15221 South
Remote Truss Designer - MiTek J15215 Central Florida
Production Manager - Truss/Wall Panel/Shipping/Maintenance J15217 KY
Estimating/Inside Sales ManagerTruss/Panel Mega-Multifamily J15216 South
Outside Sales - Truss J14207 KY, TN, IN
Production Manager - Truss/Panel Midwest J13987
Design Manager - Truss/Panel J14014 Midwest
Remote Mega-Multifamily Design Checker J14187 Remote or in Texas
Senior Designer/Design ManagerPanel/Truss J14186 New England
Senior Multifamily Truss Designer J14117 Colorado
Truss & Wall Panel Designer J14182 Florida
ID: C18459
Remote Wall Panel Designer | Wall Panel Designer
Relocation: Alberta, British Columbia, Ontario
8 Years' experience as a wall panel designer. Uses HSB CAD, AutoCAD, Autodesk Revit. Everything from Single family custom to multifamily and modular.
ID: C10968
Senior Designer - Truss / Part Time
Relocation: Florida, Alabama
Candidate desires to use his career long industry experience to be the best Part Time Remote Designer you have. Prior truss plant owner for 10 years, strong production and operations management background, and JobLine Senior Designer rating in truss design using MiTek software. Also has FASTBeam experience. Products: floor & roof trusses. Markets: Single family custom, multi family, tract and light commercial. Was successful in creating strong teams in production, design and customer service, but the local economy and overwhelming competition was more than he could overcome from a small plant perspective. Degree: BSEE
Compensation: $26hr part time employee or $33 hr 1099
Thom's Notes: I have worked with this candidate as an employer for years. Very strong manager with the ability to combine individual strengths into one team effort. Fair, honest, and customer service oriented. Scored 98
ID: C13419
Truss Designer | Design Manager | Remote Truss Designer | Estimator Relocation: Illinois
20+ years Truss Design experience. Manage estimating and design department. 4-5 employees. Handle all computer and software issues. Assist in network maintenance. Project
coordinator for all multifamily and commercial projects. Train new designers. Schedule final designs for all orders. Assist in sales for 4 million dollar operation.
Past: Established and maintained remote design office. Assisted in adding 2 million dollars to operation along with a sales representative. Managed all communication with main office. Designed all components for local area.
Looking for a position suited for a self-motivated person with a very knowledgeable background in component and housing design industry. Enthusiastic about working for a professional, well organized and establish environment that will allow someone to achieve their fullest potential while adding efficiency and profitability to the operation.
Scored above average using only a Construction Master Calculator. Very fast!
Truss Designer | Wall Panel Designer
Relocation: Arizona, California, Nevada, Utah
Designer, truss and wall panel, MiTek, AutoCAD, iLevel, almost considered a senior designer. In addition to design, was responsible for training new designers. Also has iLevel, Open Joist 2000 experience. Wall panel design experience is in AutoCAD and later in Sapphire. Started in the industry in sales, then wall panel design, added truss, and I-Joist. 7 years' experience in truss design, 3 in wall panel, 10 in I-Joist design. Will consider relocation to indicated areas only. Will consider remote.
$26-28 hr.
Relocation: USA - Eastern Exceptionally dedicated and highly motivated Plant and Production Manager offering a 30-year background in leadership, oversight, and development of high productive environments through coaching and development strategies maximizing profitability, optimizing output, and minimizing operating costs.
Past framer, framing contractor with 14 years' experience in truss and wall panel manufacturing.
MBA, retired veteran.
ID: C18387
Division Manager, VP Operations, President - Truss | Panel | Building Materials | Pro Dealer
Relocation: Arizona, Colorado, Florida, Georgia, Hawaii, Maryland, Texas, USA - South, Virginia, Washington DC, Wisconsin
Executive level manager, VP, President with $1+B P&L responsibility. Lumber, building materials, trusses, wall panels, and CFS background. Inquire to discuss this candidate.
ID: C18449
We’re here when you need help! visit: www.thejobline.com email: mail@thejobline.com
or call Thomas McAnally for Personalized Service
STRICTLY CONFIDENTIAL!
efficient and inexpensive when being constructed in the field. Design complete models in MiTek Sapphire. Design and engineer roof trusses and transfer loads throughout the structure as need. Also design and engineer beams and hangers when necessary.
ID: C18456
Plant/Location/Production Manager - Truss & Panel
Estimator | Designer - Truss, Panel | Prior carpenter Relocation: Ohio, Pennsylvania Prepare and distribute estimates to competing bidders. Calculate labor, time, and material estimated per individual job. Read, analyze, and interpret residential and commercial blueprints. Ensure projects meet the proper building codes and standards for the industry. Communicate with prospective bidders both over the phone and in person. Design and engineer roof trusses, floor trusses, pre-fabricated wall panels, and EWP Gained first-hand experience setting trusses in the field during prior construction job. Design roof systems to be most
Truss Designer | Wall Panel Designer | All Hats Relocation: Arizona Engineered panel and truss design, developed material take off for turnkey build up, worked in coordination with multiple plants and design teams, worked closely with material suppliers on take offs and estimating.
I've worked for decades in the construction industry. Not only in new construction, but additions and remodels as well using innovative designs for added value and to drive down cost. In addition to experience with MiTek, Wallbuilder and other design software packages, I have extensive manual trig/ math skills. I use these to back check questionable loads as well to design from scratch in the field when needed. I have also written
mail@thejobline.com
a plant hemorrhaging money into an extremely profitable facility, earning an 51% ownership stake in the company. I managed all aspects of the company from production and admin to Human Resources, design, and sales. P&L responsible for the financial management of lines of credit, accounting, and analysis. Worked directly with major accounts, trained and supported sales manager and staff. Developed market focus and worked closely with sales manager to support technical and design areas of expertise.
departmental policies, goals, objectives, and procedures, conferred with organization officials, and staff members as necessary
ID: C10853
Remote Design Manager | Remote Offshore Design Project Manager
Relocation: Texas
Relocation: North Carolina
30 year industry veteran, started as a Truss Designer, earned his way to Design Manager over 20+ designers. MiTek - Advanced, AutoCAD proficient. BSCE PE.
Compensation: Open??
tutorials for the training of others and checked other designer's work as a Design Manager at a Panel Plant. All things being equal, I love working in components whether designing, cutting, building or setting components at the site.
ID: C11636
General Manager - Truss Relocation: USA - ALL States, Alabama, Alaska, Arizona, Arkansas, California, Colorado, Conneticut, Delaware, Florida, Georgia, Hawaii, Idaho, Illinois, Indiana, Iowa, Kansas, Kentucky, Louisiana, Maine, Maryland, Massachusetts, Michigan, Minnesota, Mississippi, Missouri, Montana, Nebraska, Nevada, New Hampshire, New Jersey, New Mexico, New York, North Carolina, North Dakota, Ohio, Oklahoma, Oregon, Pennsylvania, Rhode Island, South Carolina, South Dakota, Tennessee, Texas, USA - Eastern, USA - Northwest, USA - South, USA - Southwest, USA - Western, Utah, Vermont, Virginia, Washington, Washington DC, West Virginia, Wisconsin, Wyoming
20+ Years truss industry experience from Design Manager to Owner/GM of a $7M truss manufacturing company. Turned
Organized manufacturing systems and procedures to control costs and quality, oversaw buying to keep costs at a minimum and inventory lean but available. Developed LEAN procedures that minimized labor steps, eliminated duplication between stations, and made sure that safety procedures and reporting requirement were maintained. Overall, I had a hands on role in all areas of the company to make sure it operated efficiently and very profitably Market conditions and competition from larger competitors ultimately required us to close the company.
ID: C18357
Division/Regional Manager, Multiplant Operations Manager - Components & Lumber to Site | Mega Multifamily.
Relocation: Florida, Georgia, North Carolina, South Carolina, Tennessee, Texas, USA - South, Virginia, Arizona, Colorado Oversaw Operations of multiple Component Facilities with annual Sales exceeding $100MM. Assisted with the start-up of three Facilities. Reviewed financial statements, sales and activity reports, and other performance data to measure productivity and goal achievement to determine areas needing cost reduction and program improvement. Established and implemented
Top level Engineering/Design Management candidate, 14+years experience Truss, 4+- Panel experience. Has experience building and integrating offshore design resources with internal design departments and training design managers to better utilize offshore capabilities. Large volume manufacturer experience. MiTek Sapphire design/layout proficient. Too confidential to go into more detail.
Compensation: $120k+
ID: C18430
Truss Designer | Remote Truss Designer
Relocation: USA - South, USASouthwest, USA - ALL States Extensive experience in truss estimating and design. Proficient in designing roof and floor trusses for a variety of projects including: custom homes, track homes, multi-family, mega-multifamily, and light commercial projects. I always get everyone involved with the project like architect, engineers, homeowners, and sales personnel Many times I go to the job site for the convenience of the framer and see what kind of condition or changes they might have; this way we will be working on the same page. Also included in my experience is purchasing material, negotiating contracts, setting up deliveries, steel and cmu detailing for steel columns and beams, with almost 25 years of experience in the construction business. MiTek Sapphire.
ID: C10897
Thom's Notes: PE with Mid Atlantic seals
ID: C14510
Remote Truss Designer Relocation: Florida
20+ Years' experience in truss design. Alpine software but will consider other software if training is provided. Has extensive experience, except MegaMultifamily, but will consider positions that are MMF as long as a learning curve is expected. Scored Senior Designer on JobLine's Design Skills Evaluation, representing the best 5 % of Truss Designers nationwide. Has extensive remote and in office management experience but is looking to step back and focus on design and manage personal results.
Compensation: $30-32 an hour, depending on opportunity, benefits, and job expectations. Not looking to work 50-60 hour a week all year, but will consider high hours on a seasonal basis. Remote only.
ID: C18420
Senior CFS Truss Designer/ Detailer | Wood Senior MegaMultifamily Truss Designer | Design Manager | Checker | Remote or In Office
Relocation: Florida
Currently CFS truss design, but has wood experience. Scored
Available Candidates Design Manager/Senior Designer/PE/Optimizer - Truss/ Panel/EWPSenior Designer in the JobLine
Truss Design Skills Evaluation, that is primarily wood truss focused. Currently an advanced Alpine TrussSteel user, but has used MiTek in the past. Also has AutoCAD, Keymark experience. Projects include $700k MegaMultifamily apartments. Designs/ Layout using Alpine, CAD shop drawings, designs connections and hardware, creates department procedural and standards program, trains new designers.
ID: C18278
General Manager | Operations Manager - Truss/Panel Relocation: Georgia, North Carolina, South Carolina, USAEastern, Virginia, Florida
General Manager over floor and roof truss manufacturing facility producing $15-20M, 110-135 employees. Supply clients in the NC, SC, Eastern TN, and VA markets. Turned around volume, safety, and profitability of a failing plant. 6 Sigma, Lean, BA.
General Manager - Truss/Panel Relocation: Florida, Georgia, North Carolina, South Carolina, USA - Eastern, USA - South, Tennessee, Virginia, West Virginia
I have worked in the residential and multi-family construction industry for 25 yrs. I started as a framer and have held numerous positions throughout my career. I have held a position as a Division Manager for a Wall Panel Facility that was part of a Building Material Supply Company. In this position, I was responsible for total operation of the division including P&L responsibility. I have also been a Department Manager of a Wall Panel Facility at a second Building Material Supply Company. During my career, I have held positions as a Director of Purchasing and a Purchasing Manager for Home Building companies, as well as an Operations Manager at a Soffit & Siding installation company. In
this position, I was responsible for the day to day operations of the company.
ID: C18367
Wall Panel Designer | Remote Wall Panel Designer | MegaMultifamily Relocation: Utah
Remote wall panel design for medium to large scale MF. Remote estimating using MiTek Sapphire to get a more accurate material count. 100,000 - 500,000 sq ft MF projects primarily in the New England Market with the panel plant being in New Brunswick. Also worked on projects in the Arizona, Texas, and California markets.
Compensation: $70's+ (45+hours)
ID: C18365
Intermediate Canadian Remote Truss Designer - Sapphire Relocation: Ontario Remote Truss Designer available.. Currently provides technical support and designs to lumber distributors for roof systems for residential and commercial applications. Provides technical assistance and support to the distribution staff to meet client demands for engineered wood structural applications. Ensures that wood truss fabricators, lumber distributors and specifiers have adhered to established building standards, codes and practices. Maintains extensive knowledge of structural analysis programs such as MiTek SAPPHIRE Structure design software. Analyze/ prepare engineered wood designs and details for Design Engineer review and approval. Generate manufacturing information and quotations for sales team and management. Prepares the job for production. Canadian codes and standards experienced.
ID: C18399
Full or Part Time Lumber Buyer/Logistics
Relocation: Colorado
Personally managed, purchased all lumber products and manage a $100 million spend for this industry leading 6 plant location manufacturer, VMI, contract developer and manager. Responsible for supply, programs, demand cycles, strategic planning, and purchasing excellence. Purchased MRO, machines, trucks, assembly lines, buildings and ongoing CAPEX projects. Team member for new construction projects for plants, 3rd party labor. Products used for construction in North America focused on multifamily engineering products. Direct mill purchasing from major US/Cano vendors.
ID: C15958
Operations/Plant Manager - Millwork | Doors | Ply |
Flooring Relocation: Colorado, Illinois, Indiana, Iowa, Kansas, Kentucky, Minnesota, Missouri, Montana, Nebraska, Nevada, North Carolina, South Dakota, Tennessee, Virginia, Wyoming 30 years' experience starting in production and advancing to multi-plant operations manager. Door experience includes managing three Production Managers and five Production Supervisors, consisting of 300 hourly employees producing 11,000 doors and 10,000 face frames per day. Responsible for the manufacturing functions of all mill operations, five frame component machining cells, three frame assembly operations, four door component machining cells, three door assembly clamps, three door profiling lines, two wide belt sanding lines and specialty machining and assembly cells.
Flooring experience: Responsible for all plant functions including budgeting and P&L. Managed six Department Managers: two Production Departments, Quality Assurance, Materials, Human
We’re here when you need help! visit: www.thejobline.com email: mail@thejobline.com
or call Thomas McAnally for Personalized Service
STRICTLY CONFIDENTIAL!
Resources including SHE, and Plant Engineer/Maintenance Manager including the CI program. Their staffs consist of eleven Supervisors and 330 hourly employees. The door plant operation dries lumber, cuts dimension stock, assembles and sands the doors. The panel plant produces the veneered flat and raised center panels, by cutting engineered wood and veneer from flitch and pressing the veneer to the substrate. Both plants are equipped with finishing lines.
ID: C11638
General Manager/Division Manager - Truss/Panel/EWP/ Lumber
Relocation: Colorado, Conneticut, Delaware, Illinois, Maryland, Massachusetts, Minnesota, New Jersey, New York, Pennsylvania, Wisconsin, North Carolina, Ohio, Indiana, Kentucky, Louisiana, Maine, Michigan, Missouri, Oregon, South Carolina, Virginia, Washington DC, New Hampshire, Vermont
An energetic, out-of-the-box, problem-solving, executive with a science-based holistic approach to manufacturing, building products and other business operations; I am recognized for my vision,
batch fabrication process and continuous production flow Enhanced scheduling system to accurately track production and achieve on-time delivery, established QC metrics, quality assurance and OSHA-approved safety programs. After 2006, helped company downsize and then worked as a consultant for turn around opportunities. Computer literate, Alpine and MiTek experience, Microsoft Office.
ID: C11465
Sales/Operations/ManagementTruss/Panel/Building Materials
16 years of management and leadership experience, and am seeking a management position with a progressive company that offers advancement commensurate to job performance.
ID: C11370
Production/Plant/General Manager - Truss/Panel/Framing Package Relocation: Texas
Relocation: Ohio
business acumen, integrity, work ethic and capability to cultivate durable professional relationships.
Practitioner of “Lean and JIT” manufacturing principles, setting metrics, improving key performance indicators, reducing costs, expanding production capacity and sales – all improving the bottom line. Skilled in business analysis, strategic planning, market and sales development; ability to drive multi-million dollar growth, institute “Best Practices” for small to medium emerging and expanding companies, managing budgets to $ 30M with full P&L accountability and oversight.
20+ Years of truss/panel/EWP
manufacturing and business management experience. In 2006 at the height of residential construction distributed $ 24.0 in Lumber, Architectural Millwork and Windows and $ 8.5 M in manufactured wood components. In this position optimized design and production process, which increased output and reduced labor and material costs. Hired trained and mentored middle management; negotiated union labor contracts. Implemented “Lean and JIT” fabrication procedures; consolidated raw material inventory, implemented
Relocation: USA - ALL States, USA - South 10 years industry experience. Successfully managed operations. Plant production, national sales team, licensed engineers, project managers, CAD designers, erection/installation division and office staff. Significantly increased productivity, sales and profit in all areas. Previously founded a wholesale building material company specifically related to engineered lumber, wood trusses, structural steel, turnkey installation and custom Millwork. Sales in excess of $7 million in less than five years. Successfully negotiated and executed the sale of these companies in 2006.
ID: C11760
Management/Operations/Sales - Building Components, LBM Manufacturing
Relocation: USA - ALL States, Arizona, California, Colorado, Alabama, Florida, Hawaii, Massachusetts, Nevada, New Mexico, North Carolina, New Hampshire, South Carolina
I am an Accomplished Manufacturing and Operations Leader with a history of increasing responsibility. My proven experience covers contractor building materials and manufacturing to the construction and turnkey fields. I have over
20 years' experience. Started in production, advanced to Saw Supervisor, Production Manager, Plant Manager, now General Manager. As General Manager (2 years) operated a $125M truss plant. Tripled output and reduced errors and labor cost. As Plant Manager (4 years), manage all the operation of the manufacturing plant, such as Productivity, logistics, efficiencies, costs. As Production Manager (12 years), manage all the areas of the manufacturing across the plant. Safety, quality control, efficiencies, HR, etc... Software: MiTek, Word, Excel, OptiFrame. Products: R & F Truss, Panel, Framing package. Markets: Single Family, Multifamily, Custom Homes. Bilingual English/Spanish spoken and written. Degree in Industrial Engineering. Compensation: $90's+
ID: C15995
Truss Designer - MiTek Relocation: Florida
Truss Designer. Primary duties: design, layout, optimization, and cutting/production documents. Secondary duties: checking others work. Software used: MiTek and AutoCAD. Component experience includes floor trusses and roof trusses. Market experience includes single family, multi-family, light commercial, and agriculture. My volume was varied depending on projects. 2 years experience, MiTek software.
ID: C13437
Remote Truss Designer | In
If it is big, bad, ugly, or worse, I can handle it. I've done layout and profile work in autocad w/ some home brewed scripting, and ArchiCAD. Custom residential, a few track builders that had 3 base models and many options to track, some multi-family, and large commercial projects. Software: MiTek, AutoCAD, ArchiCAD, Truswal, Simpson, Eagle and others. Quick to pick up new software.
ID: C11856
Designer/Design ManagerTruss/Panel/I-Joist/Stairs/EWP
Relocation: Ohio
18 years Design experience with 3 as a Senior Designer. Primary duties: design, layout, and optimization. Secondary duties: checking others work and repairs. Software used: MiTek Sapphire, Robbins, Keymark, and AutoCAD. Component experience includes floor trusses, roof trusses, wall panels, I-Joists, and hardware. Market experience includes tract, single family, single family custom, multi-family, and agriculture. My volume was varied depending on projects.
ID: C18310
Truss Designer | Estimator
Relocation: Virginia
Responsible for project management/design of commercial design -build projects up to $5 million. Directly manage subcontracted architectural, structural, and mechanical designers/ engineers, develop project estimates and designs utilizing Revit software. Work closely with project superintendents providing technical support while delivering projects within budget and on time. Initiate contact with new clients, answer sales calls, and develop project criteria. Prior Truss Designer a few years back with 2 years MiTek experience.
Available Candidates Office Truss Designer | Design ManagerID: C15678
Remote Truss Designer Relocation: Alberta
I have 25+ years of roof and floor truss design experience, with the last 3 years working as a remote designer using MiTek software.
I also have experience designing engineered wood beams using various software versions. I have acted as a local Mitek software network administrator, trained junior designers and checked their work. I have extensive design experience in mid to larger size custom homes, Multi-Family, Independent Living and small to large Commercial projects and enjoy the challenges these projects bring.
Please inquire if you are interested in learning more about this candidate. Use our Contact Us page, or if you know me, send an email.
ID: C10789
Production Manager/ Supervisor - Truss/Panel Relocation: Minnesota, Iowa, North Dakota, South Dakota, USA - Northwest, Wisconsin
20 years experience. Responsible for all aspects of truss and panel production, inventory, performance reviews. 65 workers, $9M year. WTCA quality control certified.
ID: C18277
Professional Engineer | Engineering ManagerEngineered Wood Products, Components Structural Hardware | Codes & Compliance
Relocation: Maryland, Minnesota, North Carolina, Pennsylvania, South Carolina, USA - Eastern, Virginia, Washington DC
Experienced and successful professional engineering manager with over 25 years experience in improving productivity and resolving structural problems for engineered wood product and truss manufacturers and
developing innovative design software programs. Also skilled in building outstanding teams and relationships among sales, manufacturing, and engineering stakeholders. Highly educated with exceptional employment history & experience.
ID: C18250
Remote Senior Light Gage Steel Truss/Panel Designer. Relocation: Texas
Top level Light Gage Steel Senior Remote Designer with Truss and Panel and well as metal frame commercial project experience. Alpine, Truswal and Keymark experience.
ID: C17230
Remote Wall Panel DesignerSapphire Relocation: Newfoundland My objective is to be part of a team/company and prove I am reliable, show my ability and my willingness to learn! In addition to being a newer wall panel designer, I have learned software such as Mitek Sapphire, Revit 2017, Bluebeam Revu 2016. I have recently done jobs such as designing garages and adding on additions to homes. Jobs I have worked in wall paneling include a massive wall panel job for the US (500,000+ SFT) and designed units for a senior complex. In addition to wall panels...I also add in blocking, windows, doors, etc. I also do bundling and paperwork as well.
ID: C12220
Design/Design Manager - Truss/ EWP/Remote or at Plant
Relocation: Pennsylvania
Remote / Satellite Truss Designer Roof / Floor truss design utilizing Mitek Sapphire design software. Project estimating, including roof system, floor system, and wall panels. Responsible for 100% of quoting and preparations for production for our #2 and #4 clients. Maintained a database for
a major tract builder, producing 5-8 house a week.
Truss & Engineered Wood Products Design Manager / Sales. Oversaw all aspects of Truss & Engineered Wood Products operations and sales. Maintained personal sales accounts, as well as developed new clients. Customer service from the quote stage to production, including verifying sight conditions and field measuring. Produced production drawings and reviewed / corrected design staff, MiTek / Truss Joist software. Responsible for maintaining lumber / plate inventory.
ID: C17191
Remote Truss Designer/Part Time
Relocation: USA - Northwest My objective is to be a part of a Design Team where I can contribute to the success of the company, and establish a career as a remote truss designer. I love the challenge of tough projects, and consider it my job to complete my assigned work ahead of time, and to the best of my ability. I won't quit before the job is done fully and accurately.
In addition to 4 years experience with MiTek truss design software, I have worked in the shop as both a sawyer, and a truss builder, so I have first hand knowledge of how a truss should be designed to save time on the shop end. I also worked in framing and using wall panels. So I have first hand knowledge of how a house actually goes together in the real world, and how trusses layout on framing.
My long term goal is establish myself as a reliable truss designer, and to that end, grow and advance at the same company, based on proving my ability and reliability.
We’re here when you need help! visit: www.thejobline.com email: mail@thejobline.com or call Thomas McAnally for Personalized Service STRICTLY CONFIDENTIAL!
www.TheJobLine.com
October 3 – 4 Future Place Dallas, TX
October 12 – 14 LBM Strategies 2022 Conference Denver, CO
October 12 – 14 LMC 2022 Expo Philadelphia, PA
October 12 – 14 METALCON 2022 Indianapolis, IN
October 17 – 18 Builder Connections Arlington, TX
October 18 – 20 IndustryWeek’s Manufacturing & Technology Show (M&T) Cleveland, OH
October 19 – 21
October 19 – 20
October 27
October 30 –
November 1
November 1 – 3
Southern Forest Products Assoc. (SFPA) Annual Meeting Nashville, TN
West Coast Lumber and Building Material Assoc. (WCLBMA) Annual ConventionSan Diego, CA
Midwest Building Suppliers Assoc. (MBSA) Member Summit Grand Rapids, MI
Specialty Tools and Fastener Distributors Assoc. (STAFDA) 46th Annual Convention & Tradeshow San Diego, CA
Industrialized Wood-Based Construction Conference (IWBC) at Greenbuild International Conference & Expo
San Francisco, CA
November 1 – 3 NAFCD + NBMDA 2022 Annual Convention Chicago, IL
November 1 – 4
November 2 – 4
November 4
November 9 – 11
National Council of Structural Engineers Assoc. (NCSEA) Structural Engineering SummitChicago, IL
Design-Build Conference & Expo Las Vegas, NV
American Lumber Standard Committee (ALSC) Annual Meeting St. Augustine, FL
North American Wholesale Lumber Assoc. (NAWLA) Traders Market Phoenix, AZ
November 10 Mountain States Lumber & Building Material Dealers Assoc. (MSLBMDA) BrewFestDenver, CO
November 10 – 11
November 14 – 16
November 14 – 16
November 14 – 17
American Institute of Building Design (AIBD) Design & Build Fall 2022 online
Affordable Housing Finance (AHF) Live Summit Chicago, IL
University of Texas Building Professional Institute (BPI) of Texas—Central Texas Austin, TX
Lumber Quality Institute (LQI) Lumber Quality Workshop Salem, OR
November 15 WoodWorks Wood Solutions Conference—Vancouver Vancouver, BC
November 24 WoodWorks Wood Solutions Conference—Toronto Toronto, ON
Uncasville,
Dells,
Assoc. (NDRLA) Convention Fargo, ND
Center, MN
January
January
Structural
Assoc. (SBCA) Open Quarterly Meeting
–
Association
February
–
TBA
Builders (NAHB) International Builders Show (IBS) Las Vegas, NV
Lumber Assoc. (NLA) LBM Expo—North
NFBA
St. Cloud, MN
Frame Building Expo Louisville, KY
March 1 LBM Advantage Annual Buying Show Orlando, FL
February 27 –
February 27 –
March 3 EduCode 2023 Conference & Exhibition
February 28 –
March 1
Las Vegas, NV
Northwestern Lumber Assoc. (NLA) LBM Expo—Nebraska La Vista, NE
March 1 Independent Dealers Education Association Services (IDEAS) Show
March 1 – 2
March 2 – 3
Pennsylvania Housing Research Center (PHRC) Housing Conference
Northwestern Lumber Assoc. (NLA) LBM Expo—Iowa
King of Prussia, PA
State College, PA
Des Moines, IA
March 8 – 9 Lean Summit 2023 Tucson, AZ
March 8 – 10 Lumbermens Merchandising Corporation (LMC) Annual Charlotte, NC
March 8 – 10
Southeastern Lumber Manufacturers Assoc. (SLMA) Spring Meeting & Expo Savannah, GA
March 11 – 12 Do it Best Spring Market Orlando, FL
March 12 – 16
Build23: AWCI’s Convention + INTEX Expo
March 13 – 16 AGC–The Construction Assoc. 2023 Annual Convention
March 14 – 18 CONEXPO-CON/AGG 2023 Tradeshow
Las Vegas, NV
Las Vegas, NV
Las Vegas, NV
March 24 – 25 JLC Live New England Providence, RI
March 27 – 29 International Mass Timber Conference Portland, OR
March 28 – 30 Atlantic Builders Convention (ABC) Conference & Expo Atlantic, NJ
APRIL 2023
April 26 – 28 MSR Lumber Producers Council (MSRLPC) Annual Workshop
San Antonio, TX
Don’t see your event? Increase attendance and participation by listing your industry focused events here! E-mail details and event web-link to Anna@componentadvertiser.org. We can’t guarantee space for all events, but all industry related events will be added on a space available and interest to our reader priority.
This August marked the 30th anniversary of the Florida landfall of Hurricane Andrew, one of the most damaging, and influential, hurricanes ever to hit the United States. Hurricane Andrew hit South Florida with Category 5 winds early on the morning of August 24, 1992. Andrew caused damages of $25 billion in Florida, and another billion dollars’ worth when it struck Louisiana as a Category 3 hurricane two days later. This image, from NASA Earth Observatory, shows Andrew on August 23, 24, and 25.
Engineers tend to learn something about wind resistance from every major hurricane, and Andrew was certainly no exception. In this writer’s opinion, the main lessons of Hurricane Andrew were fourfold: (1) proper roof deck nailing, (2) testing of roof coverings for wind resistance, (3) protection of openings from wind-borne debris, and (4) proper construction of gable ends.
Prior to Hurricane Andrew, contractors, inspectors, and designers tended to pay more attention to the fastening at the edges of the roof decking panels, because those fasteners are the ones that determine the shear resistance of the roof diaphragm. However, in a windstorm it’s the fasteners in the interior of the panel that are the more highly stressed in withdrawal, because they’re spaced farther apart. Research conducted by APA, the Engineered Wood Association, in Andrew’s wake showed that the installation of these interior fasteners was more important than previously considered, and that if even one of these is missing or misplaced, it can affect the performance of the entire panel.
Some reports after Andrew observed that the use of staples was inadequate to attach roof decks. Generally nails have been the required method, since Andrew, for fastening roof decking in high-wind regions.
Furthermore, the locations of roof sheathing damage strongly reinforced the importance of using Components and Cladding (C&C) loads to design roof sheathing fastening. After Andrew, prescriptive codes and standards began showing increased nailing requirements, even reducing nail spacing to 4” on center, for nails in panels at roof end zones due to high C&C loads. Most recently, due to even higher C&C roof loads in ASCE 7-16, the wood and fastener industries have collaborated to develop a new type of nail, the roof sheathing ring-shank (RSRS) nail, for use in fastening roof decks. The RSRS nail has rings on the shank to aid in withdrawal resistance, and a larger head to add resistance to nail head pullover.
The FEMA report, Building Performance: Hurricane Andrew in Florida, states “Field observations concluded that the loss of roof cladding was the most pervasive type of damage to buildings in southern Dade County.” Prior to Andrew, test procedures existed for roof coverings, but testing for higher wind speeds was generally not required. For example, at that time, composition shingles were only tested to resist wind speeds of around 64 miles per hour (as this author recalls). Building code philosophy tended to focus on structural performance, not cladding. However, Andrew showed that if roof coverings are removed in a hurricane, the building could be severely damaged by water even if there are no structural failures. Further, roof coverings removed by the wind become windborne debris that can cause failure (or injuries) in surrounding buildings.
From FEMA P-499, Home Builder’s Guide to Coastal Construction.
PHONE: 800-289-5627 FAX: 800-524-4982Read/Subscribe online at www.componentadvertiser.com Don’t Forget! You Saw it in the Adverti$$er October 2022 #14279 Page #123A dverti $ er Component manufaCturing mThe Continued next page Illustration from APA FEA analysis of fasteners on a panel under roof uplift.After Hurricane Andrew, Miami-Dade County became the first jurisdiction to require testing of all roof coverings to higher wind speeds, over the objections of some materials’ manufacturers. Once the requirement was in place in South Florida, manufacturers made tested products available, and the national building codes adopted similar requirements in the following years.
Dr. Joseph Minor, P.E., in his paper “Lessons Learned from Failures of the Building Envelope in Windstorms,” ( Journal of Architectural Engineering, ©ASCE March 2005) states, “As early as 1972, investigators at Texas Tech University observed that windborne debris plays a major role in damaging the building envelope.” Major failures were seen from roof gravel blowing off and damaging nearby buildings in downtown Houston in Hurricane Alicia in 1983.
Codes and standards contained requirements that buildings with openings had to be designed for higher internal pressure. But it was left up to the designer’s judgment to decide what should be considered an “opening.”
However, after Hurricane Andrew it became such an obvious issue that it could no longer be ignored. Two major issues were observed. First, if a window or other opening is broken by debris in a hurricane, it allows wind and water into the building, ruining everything inside, even if there is no structural damage. Second, the opening in the envelope allows the wind to penetrate inside the building, causing a large increase in internal pressure, which can cause structural damage.
Window damage from windborne roof gravel in downtown Houston, from Dr. Minor’s paper.
As a result, Miami-Dade County was the first to add a requirement into their code that openings in the building envelope must be protected from wind-borne debris either by installing tested windows and doors or by adding tested impact protection, such as shutters.
ASCE 7 took more of an incremental approach in their treatment of wind-borne debris. In ASCE 7–93, there were only two conditions for internal pressure: Condition I and Condition II. Condition II is what came to be defined as Partially Enclosed, and required a design to a higher internal pressure where openings in one wall exceeded the openings in the remaining walls. ASCE 7–95 was the first edition to contain wind-borne debris protection requirements. It introduced the definitions of enclosed, open, and partially enclosed buildings that essentially remain today. Table 6-4 contained four cases for internal pressure coefficients: open buildings, partially enclosed buildings, buildings not meeting the other three cases, and buildings meeting a fourth case. This fourth case was defined as buildings sited in hurricane-prone regions, with a windspeed greater than or equal to 110 mph, with glazed openings in the lower 60 feet that were neither designed to resist wind-borne debris nor specifically protected from wind-borne debris impact. Buildings meeting this fourth case had to be designed using the same internal pressures as a partially enclosed building. This was slightly clarified in ASCE 7–98 when the internal pressure coefficients table was reduced back to just open, partially enclosed, and enclosed classifications, and a new section in the text was added stating “Glazing in the lower 60 ft. of Category II, III, or IV buildings sited in wind-borne debris regions shall be impact-resistant glazing or protected with an impact-resistant covering, or such glazing that receives positive external pressure shall be assumed to be openings.” While this addressed the issue of increased internal pressure from damage to openings, it still did not address the issue of having a building loss due to entrance of wind and water through openings. ASCE 7–02 took the final step to where we are today, requiring that openings in buildings located in wind-borne debris regions be protected. It stated, “Glazing in buildings classified as Category II, III or IV (Note 1) located in wind-borne debris regions shall be protected with an impact-resistant covering or be impact-resistant glazing according to the requirements (Note 2) specified in Ref 6-1 and Ref 6-2 referenced herein or other approved test methods and performance criteria.” References 6-1 and 6-2 were ASTM E1886 and ASTM E1996, respectively.
The final major lesson learned from Hurricane Andrew was that gable ends deserved more attention than they had previously been given.
On masonry buildings, the walls may still be standing, but the trusses could still collapse due to loss of support from roof sheathing. On woodframe buildings, entire gable walls may collapse.
After Andrew, new requirements were added to codes requiring that wood-frame gable ends have continuous framing from the floor to the roof (balloon framing). Fastening of roof decking to gable end trusses was increased in prescriptive documents and codes. The wood industry developed details for bracing of gable ends. These two illustrations (in yellow) are taken
from “Hurricane Andrew, Part 2, Wood Building Analysis and Recommendations,” from the National Forest Products Association, November 1992.
These details have now made their way into standards such as the American Wood Council Wood Frame Construction Manual for One- and Two-Family Dwellings (ANSI/AWC WFCM).
Methods were also developed to retrofit existing gable ends to better resist the out-of-plane wind loads from hurricanes. These can now be seen in such documents as Appendix C of the 2021 International Existing Building Code, Section 1704 of the 2020 Florida Building Code, Existing Building, and FEMA P804, Wind Retrofit Guide for Residential Buildings, as shown here.
These are the main areas where codes were improved as a response to Hurricane Andrew, in the opinion of this author. There were surely others. For another take on what was learned from Andrew, see this video of Tim Reinhold, a well-known wind engineer. Thanks to the Insurance Institute for Business and Home Safety for this.
Do you have any recollections or resources to share?
The article, Hurricane Andrew — a 30-Year-Old Learning Experience, appeared first on Simpson Strong-Tie Structural Engineering Blog. To sign-up to receive the Engineering Blog in your inbox, go to seblog.strongtie.com/subscribe
CopyrightDon’t
it in
From State Fund CA.
Each year in the workplace, an estimated 1.7 million workers are injured in assaults and approximately 800 homicides occur. Workplace violence incidents include verbal assault, simple or aggravated assault, robbery, rape and homicide. Anyone can become the victim of a workplace assault, so it is important to know the risk factors.
Factors that increase the risk of workplace violence include contact with the public; the exchange of money; and guarding or delivering valuable property. Other factors include mobile workplaces (cars or trucks); working in high-crime areas, and working late night or early morning hours. Finally, workers that have contact with unstable and volatile persons in health care, social services, and criminal justice settings can be at risk.
If you are at risk for workplace violence, know and follow the safety guards in place at your worksite. Respect requirements for restricted access to the public. Ensure that visitors are screened when entering the workplace and escort them throughout the building. Physical separations like glass walls, partitions, and deep counters can provide distance between you and the public, so use them. Security measures like video cameras, two-way mirrors, and personal or desk panic alarms can help you communicate if you are in distress.
Know and follow the policies for opening and closing your place of business and handling and transporting cash and valuables. Make it a rule to work with a backup employee or enough staff coverage if you will be dealing with a potentially hostile person. Keep possible offensive weapons like sharp or heavy instruments locked away and out of the public eye.
Get training on recognizing and reporting the signs of a disturbed coworker, customer, or member of the public. You should also seek training on handling hostile customers and diffusing violent situations. Immediately report violent incidents and threats to management; often, violent threats can escalate to become violent acts.
When faced with a hostile person, respect their personal space and be aware of your body language, movements, and tone of voice. Stay calm and diffuse the situation. Try to keep a barrier like a desk between yourself and the person, but don’t block yourself into a corner. If there is no barrier available, stand at an angle and 4 to 6 feet from the person; this keeps you at arms length and gives you a means to escape. Have plans should a dangerous situation arise; note exits, phones, and potential defensive weapons. Use physical force as a defense only.
Se estima que cada año 1.7 millones de trabajadores resultan lesionados en su sitio de trabajo por asaltos y que ocurren aproximadamente 800 homicidios. Los incidentes de violencia en el sitio de trabajo incluyen confrontaciones verbales, asaltos simples o agresiones con daños físicos graves, robo, violación y homicidio. Todos podemos ser víctima de la violencia en el trabajo, por lo que es importante estar conscientes de los factores de riesgo.
Los factores que aumentan el riesgo de violencia en el sitio de trabajo incluyen el contacto con el público, el intercambio de dinero, y la vigilancia, resguardo o entrega de artículos de valor. Otros factores incluyen sitios de trabajo móviles (autos o camiones), trabajo en áreas de alto crimen y trabajo tarde por la noche o temprano por la mañana. Por último, los trabajadores que entran en contacto con personas inestables y volubles en el cuidado de la salud, servicios sociales y justicia penal pueden correr riesgos.
Si usted corre el riesgo de ser víctima de la violencia en el sitio de trabajo, conozca y observe los resguardos de seguridad que existen en su sitio de trabajo. Respete los requerimientos de acceso limitado al público. Asegúrese de que los visitantes sean revisados al entrar al sitio de trabajo y actúe usted como escolta por todo el edificio. La separación física, como por medio de paredes o divisiones de vidrio y mostradores anchos pueden proporcionar mayor distancia entre usted y el público; úselos. Medidas de seguridad tales como cámaras de video, espejos falsos o unidireccionales y alarmas de pánico personales o en el escritorio pueden ayudarle a comunicarse si tiene problemas.
Conozca y cumpla las políticas para abrir y cerrar su sitio de trabajo, y para manejar y transportar dinero en efectivo o artículos de valor. Establezca, como regla de trabajo, tener a otro empleado como refuerzo, o suficientes empleados si usted tiene que tratar con una persona potencialmente hostil. Mantenga todas las armas ofensivas potenciales, tales como instrumentos filosos o artículos pesados guardados bajo llave y fuera de la vista del público.
Entrénese sobre cómo reconocer y reportar los indicios de un compañero de trabajo, cliente o integrante del público con trastornos emocionales. Usted también debe recibir entrenamiento sobre cómo tratar a clientes hostiles y calmar situaciones violentas. Reporte de inmediato cualquier incidente de violencia o amenaza contra la gerencia; a menudo las amenazas de violencia pueden intensificarse y convertirse en actos de violencia.
Cuando encare a una persona hostil, respete su espacio personal y esté consciente de su propio lenguaje corporal, movimientos y tono de voz. Permanezca tranquilo y calme la situación. Trate de mantener una barrera física, tal como un escritorio, entre usted y la persona, pero no quede acorralado en una esquina. Si no hay una barrera disponible, párese en ángulo y a unos 4 a 6 pies de la persona; esto le mantiene alejado a más del largo de un brazo y le brinda una vía de escape. Planifique cómo actuar si surge una situación peligrosa; observe las salidas, teléfonos y armas defensivas potenciales. Use la fuerza física sólo como defensa.
The above evaluations and/or recommendations are for general guidance only and should not be relied upon for legal compliance purposes. They are based solely on the information provided to us and relate only to those conditions speci
cally discussed. We do not make any warranty, expressed or implied, that your workplace is safe or healthful or that it complies with all laws, regulations or standards.
PHONE: 800-289-5627
PHONE: 800-289-5627
READ/SUBSCRIBEONLINE AT WWW.COMPONENTADVERTISER.COM
Read/Subscribe online at www.componentadvertiser.com
FAX: 800-524-4982
FAX: 800-524-4982
New hybridized design approach can revolutionize development of future housing
September 12, 2022, Houston, TX — Construction 3D printing is gaining new heights in Texas, as printing begins on the first multistory printed structure in the United States.
HANNAH, PERI 3D Construction, and CIVE, in collaboration with building industry partners, are printing a two-story single-family home that integrates customized architectural design and a resilient structural system that leverages a hybridized construction method.
The 4,000-square foot project showcases the possibilities of 3D printing technology, mass customization and design solutions that integrate conventional construction methods. With a hybridized construction method that combines concrete 3D printing with wood framing, this approach allows the two material systems to be used strategically and aims to increase the applicability of 3D printing in the U.S., where framing is the one of the most common construction techniques. The building design is conceptualized as a series of printed cores that contain functional spaces and stairs. The spatial cores are connected by wood framing to produce an architectural alternation of concrete and framed interiors. The project’s scalable design and construction process is applicable for multifamily housing and mixed-use construction. Using the COBOD BOD2 gantry printer, the project takes advantage of the printer’s modularity for its design layout.
The project is the culmination of a two-year collaborative effort between boundary-pushing design researchers and industry partners. The project is spearheaded by architectural designers and assistant professors at the College of Architecture, Art, and Planning at Cornell University Leslie Lok and Sasa Zivkovic, principals of HANNAH; along with PERI 3D Construction, an internationally leading provider for 3D construction printing, and CIVE, one of the leading engineering and design/build contractors in Houston.
“For the design of the project, we developed a hybrid construction approach that couples innovations in concrete 3D printing with traditional wood framing techniques to create a building system that is structurally efficient, easily replicable, and materially responsive,” said Leslie Lok and Sasa Zivkovic, of HANNAH. “The project also highlights the exciting design potential of mass-customized architectural components to meet homeowner’s needs and to simplify building system integration. These design efforts aim to increase the impact, applicability, sustainability, and cost efficiency of 3D printing for future residential and multi-family buildings in the U.S.”
Collectively, the team has extensive experience in 3D printing. HANNAH is an innovative architectural design practice known for its progressive design solutions, such as demonstrated in the upstate New York Ashen Cabin project, a sustainable building that advances the use of 3D printing concrete and robotic timber construction. PERI 3D Construction has an extensive record of advancing the implementation of 3D printing in building construction. Using COBOD BOD2 printers, PERI has completed six projects in Europe and in the U.S. including the first 3D printed home in Germany and Europe’s largest 3D printed apartment building. CIVE combines structural engineering expertise with bountiful construction experience to create a coordinated workflow.
“We are incredibly proud to not only showcase the possibilities of the BOD2 3D construction printer but also our extensive know-how in planning, engineering and printing on this project, which is the seventh and largest one we printed so far,” said Fabian Meyre-Broetz, CEO of PERI 3D Construction. “We are convinced that it will set new standards from a design as well as printing execution perspective and underlines our role as the forerunner for this new construction technique.”
The project also developed detailed solutions with key building industry partners from construction material to HVAC systems. The team selected Quikrete’s new generation of specially formulated 3D printable concrete for the project. Working with Huntsman Building Solutions and their R&D research team, the building integrates a closed cell foam insulation system. The hybridized construction utilizes Simpson Strong-Tie’s anchoring systems for both 3D printed elements and wood connections. The residential building deploys Toshiba Carrier’s state-of-the art Variable Refrigerant Flow (VRF) technology for an efficient HVAC system that is translatable to larger scale housing and multi family construction.
“Having the opportunity to be the engineers and general contractor for the first multistory 3D printed structure in the U.S. has been an honor,” said Hachem Domloj, CIVE President. “We can see how this technology and our team’s approach is providing the scalability to larger commercial developments. Collectively, we're changing the way our country builds, and paving the way for more affordable housing, higher structural integrity, and faster building capabilities. The possibilities of 3D printing are endless!”
Posted September 19, 2022 on NAHB Now | The News Blog of the National Association of Home Builders Reprinted with permission.
In another sign that the slowdown in the housing market continues, builder sentiment fell for the ninth straight month in September as the combination of elevated interest rates, persistent building material supply chain disruptions and high home prices continue to take a toll on affordability.
Builder confidence in the market for newly built single-family homes fell three points in September to 46, the lowest level since May 2014 with the exception of the spring of 2020, according to the National Association of Home Builders (NAHB)/Wells Fargo Housing Market Index (HMI) released today.
“Buyer traffic is weak in many markets as more consumers remain on the sidelines due to high mortgage rates and home prices that are putting a new home purchase out of financial reach for many households,” said NAHB Chairman Jerry Konter, a home builder and developer from Savannah, Ga. “In another indicator of a weakening market, 24% of builders reported reducing home prices, up from 19% last month.”
“Builder sentiment has declined every month in 2022, and the housing recession shows no signs of abating as builders continue to grapple with elevated construction costs and an aggressive monetary policy from the Federal Reserve that helped pushed mortgage rates above 6% last week, the highest level since 2008,” said NAHB Chief Economist Robert Dietz. “In this soft market, more than half of the builders in our survey reported using incentives to bolster sales, including mortgage rate buydowns, free amenities and price reductions.”
Derived from a monthly survey that NAHB has been conducting for more than 35 years, the NAHB/Wells Fargo HMI gauges builder perceptions of current single-family home sales and sales expectations for the next six months as “good,” “fair” or “poor.” The survey also asks builders to rate traffic of prospective buyers as “high to very high,” “average” or “low to very low.” Scores for each component are then used to calculate a seasonally adjusted index where any number over 50 indicates that more builders view conditions as good than poor.
All three HMI components posted declines in September. Current sales conditions dropped three points to 54, sales expectations in the next six months declined one point to 46 and traffic of prospective buyers fell one point to 31.
Looking at the three-month moving averages for regional HMI scores, the Northeast fell five points to 51, the Midwest dropped five points to 44, the South fell seven points to 56 and the West posted a 10-point decline to 41.
HMI tables can be found at nahb.org/hmi. More information on housing statistics is also available at Housing Economics PLUS (formerly housingeconomics.com).
Posted September 20, 2022 on NAHB Now | The News Blog of the National Association of Home Builders Reprinted with permission.
High mortgage rates and building production bottlenecks continue to act as a drag on the single-family housing market even as overall housing starts posted a double-digit gain in August due to a surge in multifamily production.
Overall housing starts increased 12.2% to a seasonally adjusted annual rate of 1.58 million units in August from a downwardly revised July reading, according to a report from the U.S. Department of Housing and Urban Development and the U.S. Census Bureau.
The August reading of 1.58 million starts is the number of housing units builders would begin if development kept this pace for the next 12 months. Within this overall number, single-family starts increased 3.4% to a 935,000 seasonally adjusted annual rate. Year to date, single-family starts are down 4%. The multifamily sector, which includes apartment buildings and condos, increased 28% to an annualized 640,000 pace.
“Single-family production is running at a weakened pace due elevated mortgage rates and high construction costs that have led to a major slowing of the housing market and exacerbated housing affordability,” said Jerry Konter, chairman of the National Association of Home Builders (NAHB) and a home builder and developer from Savannah, Ga. “The slowdown in the single family market has been reflected in our builder surveys, which have posted declines every month in 2022.”
“Today’s housing starts report is more evidence that the housing recession is deepening for the single-family market, with the pace below 1 million for the last two months,” said Jing Fu, NAHB’s director of forecasting and analysis. “Expected additional tightening of monetary policy from the Federal Reserve, falling builder sentiment and a 15.3% year-over-year decline in single family permits points to further weakening for the housing sector. The one bright spot is multifamily construction, which remains very strong given solid demand for rental housing.”
On a regional and year-to-date basis, combined single-family and multifamily starts are 4.6% higher in the Northeast, 2.4% lower in the Midwest, 5.6% higher in the South and 1.5% lower in the West.
Overall permits decreased 10% to a 1.52 million unit annualized rate in August. Single-family permits decreased 3.5% to an 899,000 unit rate. Multifamily permits decreased 17.9% to an annualized 618,000 pace.
Looking at regional permit data on a year to-date basis, permits are 3.1% lower in the Northeast, 1.2% higher in the Midwest, 1.2% higher in the South and 1.4% lower in the West. The number of apartments under construction (890,000 residences in 2-plus unit properties) is at the highest level since the first quarter of 1974.
Posted September 27, 2022 on NAHB Now | The News Blog of the National Association of Home Builders Reprinted with permission.
A brief decline in mortgage rates helped to boost new home sales in August but sales are expected to move on a downward trend in the months ahead as rates have since moved higher and builder sentiment continues to fall due to declining housing affordability and ongoing supply chain bottlenecks.
Sales of newly built, single-family homes in August increased 28.8% to a 685,000 seasonally adjusted annual rate from an upwardly revised reading in July, according to newly released data by the U.S. Department of Housing and Urban Development and the U.S. Census Bureau. New home sales are down 14% on a year-to date basis despite the August upturn.
“With housing affordability at a more than 10-year low and the Federal Reserve continuing to aggressively raise interest rates to rein in stubbornly high inflation, policymakers must find ways to reduce construction costs that are delaying home projects and putting upward pressure on home prices,” said Jerry Konter, chairman of the National Association of Home Builders (NAHB) and a home builder and developer from Savannah, Ga.
“The sales gain in August reflects that there is clearly sidelined demand for housing, but it is being constrained by rising interest rates that are pricing many potential consumers out of the market, particularly entry level buyers,” said NAHB Chief Economist Robert Dietz. “After a brief lull when mortgage rates fell below 5.3% for much of August, they have since jumped much higher in September and are now approaching 7%. The Fed should take careful note of the weakening of the housing market given the policy lag involved with monetary policy. Housing is a leading indicator of economic conditions.”
A new home sale occurs when a sales contract is signed or a deposit is accepted. The home can be in any stage of construction: not yet started, under construction or completed. In addition to adjusting for seasonal effects, the August reading of 685,000 units is the number of homes that would sell if this pace continued for the next 12 months.
New single family home inventory remained elevated at an 8.1 months’ supply. The count of homes available for sale, 461,000, is up 24.6% over last year. Of this total, only 49,000 of the new home inventory is completed and ready to occupy. The remaining have not started construction or are currently under construction.
Reflecting gains for construction costs, the median new home price in August was $436,800, up 8.2% from a year ago. This is a diminished growth rate as a growing number of builders cut prices due to slackening demand.
Regionally, on a year-to-date basis, new home sales fell in all four regions, down 15.6% in the Northeast, 24.5% in the Midwest, 10.8% in the South and 16.7% in the West.
Strengthens Company’s roof and floor truss value-added products, including a multifamily presence in key high-growth markets
DALLAS, Sept. 01, 2022 Builders FirstSource, Inc., the nation’s largest supplier of structural building products and value-added components and services, today announced it has acquired Trussway, a leading provider of pre-fabricated roof and floor trusses as well as value added building components and services, including for the multifamily sector, with annualized sales of approximately $340 million.
“We are thrilled that Trussway will now be an integral part of Builders FirstSource. Since 1972, Trussway has been a supplier of choice to customers due to its ability to routinely deliver high quality products and services,” said Dave Flitman, President and CEO of Builders FirstSource. “The addition of Trussway expands our footprint with our roof and floor truss offerings, including for multifamily customers, and enhances our valueadded portfolio to better serve our customers and accelerate growth. We are excited to welcome the Trussway team, with its long-standing customer relationships and track record of profitable growth, into the Builders FirstSource family.”
Headquartered in Houston, and with 1,000 employees nationwide, Trussway benefits from customer relationships across the ecosystem of owners, developers, general contractors and framers. Trussway serves more than 340 customer accounts in the U.S., and its average relationship with its top 25 customers is over 10 years. Trussway’s innovative in-house estimating, design and engineering approach will be complementary to BFS, and the Company anticipates it will lead to synergies across its portfolio. As part of the acquisition, Builders FirstSource is adding Trussway’s integrated network of six strategically located manufacturing facilities across the U.S.
“Trussway is honored to be a part of the BFS family,” said Jeff Smith, President and CEO of Trussway. “For 50 years, Trussway associates have worked hard at building this company into a leading truss manufacturer. We look forward to bringing, and building on, our high intensity approach to safety, quality, service, production and customer satisfaction with the BFS Team.”
Headquartered in Dallas, Texas, Builders FirstSource is the largest U.S. supplier of building products, prefabricated components, and value-added services to the professional market segment for new residential construction and repair and remodeling. We provide customers an integrated homebuilding solution, offering manufacturing, supply, delivery and installation of a full range of structural and related building products. We operate in 42 states with approximately 560 locations and have a market presence in 47 of the top 50 and 85 of the top 100 MSA’s, providing geographic diversity and balanced end market exposure. We service customers from strategically located distribution and manufacturing facilities (certain of which are co located) that produce value-added products such as roof and floor trusses, wall panels, stairs, vinyl windows, custom millwork and pre-hung doors. Builders FirstSource also distributes dimensional lumber and lumber sheet goods, millwork, windows, interior and exterior doors, and other building products.
With this acquisition, SBSI grows to 11 lumber and building materials (“LBM”) locations in Alabama, Georgia, North Carolina, South Carolina, and Tennessee, and adds truss manufacturing capability.
August 31 2022 CULLMAN, Ala. (BUSINESS WIRE) Southeast Building Supply Interests (“SBSI”), a platform company of the leading building industry-focused investment firm Building Industry Partners (“BIP”), has acquired Buettner Brothers Lumber Company (“Buettner”). SBSI is led by industry veteran Roger Farmer, and serves local, regional, and national builders and contractors, as well as do-it yourself customers, across five states in the Southeast. Buettner is SBSI’s first location in Alabama and third acquisition of this summer including Wallace Building Supply (Indian Mound, Tennessee) and Haywood Builders Supply (Waynesville, North Carolina).
SBSI is building a best-in-class regional pro dealer organization that is committed to establishing leading human capital management practices. As part of this commitment every SBSI employee, including all Buettner employees, participate in SBSI’s employee equity ownership program.
Roger Farmer, President of SBSI, shared, “I consider Alabama home, and I could not be more excited to acquire our first business in the state. Under John’s [McPhillips] and Jimmy’s [Barnes] leadership Buettner has been a pillar of the Cullman community, and we look forward to continuing in that tradition.”
Jimmy and John jointly added, “We are proud of the business, our employees, and the Cullman community. SBSI is a growth-oriented team and that means that our employees will continue to have tremendous opportunities and that our customers will continue to have a committed local building materials dealer to serve them.”
Cam Sadler, Vice President at BIP, commented, “We see tremendous opportunity in North Alabama. Cullman is a great place to live, and Buettner is well positioned to service a major economic growth corridor."
Nick Massengill, Operating Partner at BIP and SBSI Director, noted, “We are excited to be in Alabama, and we are excited to partner with Buettner employees on this next growth phase. Our employee equity program is designed to reward the hard work that is required to grow a business. Our goal is to create shared prosperity with all of our employees.”
SBSI is actively seeking to invest in lumber and building materials companies in the Southeast and works tirelessly to elevate the employee value proposition at all organizations that join the SBSI family of businesses.
September 14, 2022—Tibbetts Lumber Co. LLC announced it has agreed to acquire Pensacola, Florida based D & M Truss Co. The transaction is expected to close later in 2022. The St. Petersburg, Florida-based multi location building materials supplier's agreement is to acquire all of the assets of the single location, Pensacola, Florida-based roof and floor truss manufacturer.
“Assuming this deal is consummated, D & M Truss’ team and facility are strategic to our existing Florida operations to allow for further growth into Florida’s panhandle, Alabama, and Mississippi; finally propelling us over the Florida state line. D & M gives us a very geographically-significant footprint to complement our existing Central Florida truss production, and the team is experienced, well-disciplined, and extremely respected in the marketplace. This is an exciting growth opportunity and time for us,” stated Kyle Hooker, Tibbetts Lumber’s Executive Chairman.
Tibbetts Lumber’s Director of Human Resources, Rob Hicks, said, “As a people first, growth focused leader in the building materials industry, we are excited to work with the D & M team and bring aboard the exceptionally hardworking and dedicated employees as part of the Tibbetts Lumber family. It’s an amazing opportunity to have their talent and expertise join the team!”
Upon the closing of the transaction, Tibbetts Lumber’s U.S. footprint will increase to 10 locations throughout Florida and its sister company, Cox Lumber Ltd., operates two locations in the Cayman Islands. Tibbetts Lumber’s Vice Chairman and CEO, Russ Hallenbeck, commented, “D & M’s ‘Core Values’ and business model align with ours. If this acquisition closes, it should enhance our ability to serve current key and future customers in the Greater Pensacola area. Servicing customers in the Florida Panhandle solidifies our strategic growth plan in Florida and throughout the Southeastern U.S.”
Tibbetts’ primary business lines include roof and floor trusses, lumber and building materials, interior and exterior doors, millwork and trim, windows, siding, and specialty items for new home construction and remodeling.
Tibbetts Lumber is essentially a rebirth of the former Cox Lumber Co., which was purchased in 1949 by Hooker’s grandfather, Linton N. Tibbetts, OBE, and operated until 2006, when it was acquired by a subsidiary of The Home Depot. Cox Lumber Co. had 28 Florida locations at the time of the sale, and in 2009, Hooker and his family started Tibbetts Lumber Co.
Hooker stated, “After we sold Cox, my grandfather and I felt like fish out of water. We really didn’t know what to do at that point. So, we decided to start Tibbetts Lumber Co. in 2009, and we have hired back over 70 of our former employees who have helped recreate the unique, family and employee-centered, and very special culture that my grandfather Linton, Bob Fehr (former Cox president and director), and Juan Quesada (former Cox and Tibbetts Lumber president and current director of Tibbetts Lumber) created over the course of 57 years. I truly think we have taken that culture and ‘feel of the company’ to an even greater level at Tibbetts Lumber, and we are excited to continue our growth with the expected acquisition of D & M Truss Co. with its similarly embedded culture and product offerings.”
August 31, 2022 There are multiple credits many businesses are eligible for through the federal government for expenses related to or during the COVID-19 pandemic. Below is information about these credits and you can find information about all COVID-19 Economic Relief on the Treasury’s website.
The federal government allows small and mid-size employers, and certain governmental employers, to claim refundable tax credits that reimburse them for the cost of providing paid sick and family leave to their employees due to COVID-19, including leave taken by employees to receive or recover from COVID-19 vaccinations. This applies to qualified sick and family leave wages for leave taken after March 31, 2020.
If your business provided paid leave to employees and you have not yet claimed the credit, you can file amended payroll tax forms to claim the credit and receive your tax refund. You just need to file an amended 941 X payroll tax return to fix underpayments and make a credit refund claim for overpayments. Form 941-X has new line items specifically designated for COVID-19-related corrections. Here is a one-page Fact Sheet on the Paid Leave Credit, and here is another related Fact Sheet.
The Employee Retention Credit is a refundable tax credit against certain employment taxes equal to 50% of the qualified wages an eligible employer paid to employees after March 12, 2020 and before January 1, 2021. This credit was also extended through 2021. Here is a US Treasury Fact Sheet on the Employee Retention Credit
• Use this IRS Article for instructions on how to claim the credit in 2021 as well as in prior years;
• Visit the IRS website or view this FAQ for how to claim the credit;
• Read this IRS article for more information on the credit; and
• Read this IRS article that includes multiple FAQs and information about the extension of this credit by the American Rescue Plan.
• Here is an article that gives advice regarding claiming COVID 19 relief credits, including how long you have to claim the back credits you might not have applied for.
Be wary of companies online who say they will complete these forms and claim the credit for you. They not only charge large percentages of the total refund, but it is a conflict of interest: they have an incentive to increase the amount you receive but are not held accountable, nor must they defend what they filed on your behalf. The IRS has warned for employers to be very careful in selecting an advisor or using a firm to prepare it on an hourly or project basis.
ABMA advocates on behalf of the lumber and building materials (LBM) industry. ABMA represents LBM dealers and associated businesses in Alabama, Connecticut, Delaware, Georgia, Louisiana, Maine, Maryland, Massachusetts, Mississippi, New Hampshire, New Jersey, New York, Oklahoma, Pennsylvania, Rhode Island, Vermont, and Washington, D.C. We work directly with members of Congress, the White House, and federal agencies to impact the legislative and regulatory process as it affects the LBM industry. ABMA is powered by the Northeastern Retail Lumber Association (NRLA) and Construction Suppliers Association (CSA).
PONTE VEDRA BEACH, Fla., September 8, 2022 The US LBM Foundation, the nonprofit organization of US LBM, one of the nation’s largest distributors of specialty building materials, raised $1 million, which will go to multiple charities, including the Gary Sinise Foundation, through the sixth edition of its charity golf tournament, which was held at TPC Sawgrass in Ponte Vedra Beach, Fla. on Sept. 7.
At the event, the US LBM Foundation presented a $300,000 contribution to the Gary Sinise Foundation. The donation will be used to support the Gary Sinise Foundation’s R.I.S.E. (Restoring Independence Supporting Empowerment) program, which builds specially adapted smart homes for severely wounded veterans. Participating in this year’s tournament was retired U.S. Marine Corps Sergeant Nick Kimmel, who lost an arm and both his legs in Afghanistan, and received an adapted smart home from the Gary Sinise Foundation in 2016.
Additional beneficiaries of this year’s event include Puppies & Golf, which advocates for dogs in need of companionship, the Langer Family Foundation, which works to support and strengthen families, and the U.S. Adaptive Golf Alliance, which is focused on inclusion and accessibility in golf for disabled players.
Special guests at this year’s tournament included PGA pro Erik Barnes and US LBM brand ambassadors and pro golfers Bernhard Langer and Nelly Korda. Korda also participated in a conversation about her career hosted by CBS Sports reporter Amanda Balionis-Renner. Joining in the conversation was Sophia Howard, whose father is a US LBM associate, and has been mentored by Korda and recently participated in the USGA Adaptive Open, a showcase for the world’s best golfers with disabilities.
The event concluded with a performance by actor Gary Sinise and his Lt. Dan Band for event attendees and several area veterans. The band is named after Sinise’s character Lt. Dan Taylor in the film “Forrest Gump.”
The US LBM Foundation is registered 501(c)(3) nonprofit organization dedicated to improving the quality of life in communities across the United States. The Foundation was established in 2013 by US LBM, a leader in the building materials industry, to help fulfill the company’s mission of giving back in the communities where it operates. The US LBM Foundation supports causes and organizations through financial and in-kind donations that address critical community challenges, including economic development, housing, health care and human services. For more information, visit uslbmfoundation.org
4Ward Solutions Group www.4wardconsult.com 623-512-6770 ben@4wardconsult.com
Acceptance Leasing & Financing Service, Inc. www.acceptlease.com 412-262-3225 cvillella@acceptlease.com
Acer Inc. www.acerinc.com 507-864-2220 sales@acerinc.com
Alpine www.alpineitw.com 800-521-9790 mschwitter@alpineitw.com
Clark Industries, Inc. www.clark-ind.com 800-743-9727 general@clark-ind.com
Eagle Metal www.eaglemetal.com 800-521-3245 connect@eaglemetal.com
eideintegratedsystems.com 612-521-9193 ext 204 tom@eidemachinery.com
EstiFrame Technologies, Inc. www.estiframe.com 209-576-5000 cgifford@estiframe.com
Fitzgerald Group, LLC www.fitzgroup.com 719-528-5445 rfitzgerald@fitzgroup.com
HOLTEC USA Corporation www.holtecusa.com 813-754-1665 info@holtecusa.com
Hundegger USA www.hundeggerusa.com 435-654-3028 steve@hundeggerusa.com
LimTek Solutions limteksolutions.com 416-888-4457 edmond.lim@limteksolutions.com
MiTek USA www.mitek-us.com 800-325-8075 customerservice@mii.com
Panels Plus www.panplus.com 866-726-7587 tkaasa@panplus.com
Runnion Equipment Company www.runnionequipment.com 708-541-1063 barunnion@runnionequipment.com
Simpson Strong-Tie
www.strongtie.com 800-999-5099 web@strongtie.com
Home
Hain Engineering Services
Company Overview Products Companies We Represent Hain Racing Products
Request Form
Contact Us Mailing List
Used Products
Leasing & Financing Services
About Hain Racing
Spida Machinery USA www.spida.com 866-647-7771 sales@spida.com
The Hain Company www.thehaincompany.com 530-295-8068 sales@thehaincompany.com
TheJobLine.com www.thejobline.com 800-289-5627 mail@thejobline.com
Welcome to The Hain Company's website! Here you will find information about the Hain Company and its line of innovative products that can help streamline your company.
Our products are diversely used throughout the manufacturing industry to speed production and reduce labor costs.
News
Timber Products Inspection www.tpinspection.com 770-922-8000
Todd Drummond Consulting, LLC. www.todd-drummond.com 603-748-1051 todd@todd-drummond.com
Triad | Merrick Machine
www.triadmachines.com 800-568-7423 ext 133 mmcsales@merrickmachine.com
Products
Wolf X Machina www.wolfxmachina.com info@wolfxmachina.com
Wood Tech Systems, Inc. www.woodtechsystems.com 765-751-9990 info@woodtechsystems.com
All Measuring Systems
Hain Systems Framer Sub Component Nailer
Quick Rafter Cutter
Vent Block Drills
Hain Racing Offset Drive
Aluminum Valve Cover
Used Products
Refurbished QRC Refurbished VBD
Refurbished MEA
Refurbished SCN
Refurbished MMEA
Monet Desauw
Anna Stamm anna@componentadvertiser.org 800-289-5627
Component Saws
Floor Web Saw
Material Handling
Used Equipment
Companies We Represent Festool Klaisler Mfg. Corp. The Koskovich Company Monet Desauw Inc.
Mango Tech
All Measuring Systems
Folding Measuring System
New Videos
Vekta USA www.vektausa.com 907-230-8276 info@vektausa.com
The New (JSMEA) or Job Site Measuring System has been released for production.
Folding Measuring System
Overview: About the Hain Company
Wasserman & Associates
Products: Hain System Framer
Measuring System (Includes the ELMH and MMEA)
Folding Measuring System
www.wasserman-associates.com 800-382-0329 sales@wasserman-associates.com
Table Measuring System
Portable Measuring System
Measuring System
Manual Measuring System
Extended Length Material Handler
Both Vent Block Drills
Vent Block Drill
Posted on Friday, September 9th, 2022
The Experienced Truss Designer will prepare truss layouts and cut sheets per architectural and structural plans in a timely and efficient manner and is expected to exhibit our core values both on and off the job. Projecting Respect, Honesty, Owning it, and Passion in everything you do.
Truss Designer 22-0816-1
Posted on Tuesday, August 16, 2022
Employer: Automated Products, Inc.
Automated Products, Inc. has been in the truss business since 1964. We currently have openings in the design department working out of the Marshfield or Verona, WI locations.
Truss designer will be responsible for creating designs pertaining to roof and floor trusses utilizing MiTek Software to meet the needs of the customer.
Truss Designer 22-0816-2
Posted on Tuesday, August 16, 2022
Employer: The Building Center Inc.
The Truss Designer reads residential and commercial plans to design wood trusses for both roof and floor truss systems. The Designer communicates with production teams, customers, and Store Managers to ensure designs are accurate throughout the process.
Attention to detail and knowledge of design software are crucial for success in this position. The successful candidate will have a strong can-do work ethic and a flexible approach to the work at hand. They must be able to discuss the design with customers and to work as a member of a team — all while having a strong belief in the mission and goals of the company.
Lead Designer 22-0811-2
Posted on Thursday, August 11, 2022
ProTec Panel & Truss is looking to add a Lead Designer to our team. The designer will be responsible for the production of detailed shop drawings for component manufacturing using Mitek Software. They will contribute to the Design Team's success by working with team members to check accuracy and assist entry level designers.
Posted on Tuesday, April 26, 2022
Employer: Simple Homes Simple Homes is seeking a highly motivated, experienced draftsperson/component designer to join our architecture and engineering team. This role will primarily be focused on transforming both new and existing designs into detailed fabrication models using the MiTek Sapphire Suite. In addition, this individual will be responsible for the production of detailed construction and shop drawings for component manufacturing (wall panels, floor panels, and roof sections). Last but not least, the individual will have the opportunity to contribute to the development of new designs that are optimized for our unique panelized building system.
At Simple Homes we look for problem solving pros – folks who aren’t afraid to dive in, get their hands dirty, and figure out innovative solutions. As we are an early-stage startup, we need folks who can wear many hats and are energized by a fast-paced and ever-changing work environment. In this role, we also need you to have a passion for VDC and BIM.
Contact: twm@componentadvertiser.org or Call: 800-289-5627
For Rates and Posting, visit our website: www.componentadvertiser.com/Hiring-Zone
The Hiring Zone is operated by The Component Manufacturing Advertiser Magazine. All applications will be sent exclusively to the advertising company.
S the S tructural B uilding c omponent S i ndu SYOU SIMPLY CAN’T AFFORD TO IGNORE THE ADVANTAGES OF THE POSI-STRUT FLOOR TRUSS SYSTEM.
Longer Spans allow design freedom Wide Surface makes attaching the floor deck and ceilings simple
Open Web design creates a service void for ease of access
Top Chord Bearing for reduced hanger cost
Lightweight Construction means joists are easy to handle Increased space to run HVAC and mechanicals due to the metal web design
Factory Manufactured ensures a made to measure quality product
Improved energy efficiency by allowing for insulation over windows and doors
If you’re interested in using Posi-Strut in your next build, talk to your MiTek representative at (314) 851-7306. To learn more about Posi-Strut, visit Mitek-US.com/Posi-Strut
After this year’s BCMC, it’s worth considering how far our industry has progressed since we first went to a trade show. The year was 1958, and the National Association of Home Builders Show (NAHB now IBS) was the only way to reach a national audience. Fortunately, we had one tenacious man, Cal Jureit, to show the world the marvel of his technology. And this first trade show made all the difference.
Jureit had to go on a tear just to get to the Show, optimizing his Gang-Nail design and putting together a complete business in the two preceding years. That included building machine tools, buying stamping presses, and developing truss engineering. At that point, he really hadn’t come up with an economical way to ship his truss plates, or to fabricate trusses. But he had the foresight and confidence in his invention to make the trip, even though when he left for the Show he had only sold $25,000 worth of truss plates.
Jureit had no hesitation about leaving the warmth of Miami for a frost-bitten Chicago in January – he had previously worked two years in Toledo, Ohio. Yet he had to take a full day to get there, flying in a propeller plane (Pan Am flew the first commercial jet flight later that year) and pay about $150, or $1500 in today’s money, for the flight. And likely he took the train to get downtown to the Conrad Hilton Hotel and register at the Show headquarters. From there, he had to take a cab or mount the elevated “L” train platform to get to one of several Show hotels, such as the Summit House shown here.
From there, Jureit would have to find one of the Show annexes, which were each one mile down the L train from the main exhibit floor at the Hilton. He’d then set up his small booth at one of two vintage 1920’s venues: the ballroom of the Summit House Hotel or on the floor of the Black Hawk’s hockey area. Jureit gambled that a few of the 20,000 attendees would find him. After all, it would be easy to miss his small booth in this, the largest trade show in the country, where he’d be dwarfed by the huge displays of U.S. Steel, GE, Kitchen Aid, International Harvester, and the like.
Fortunately, in the years leading up to the Show, builders across the country had begun experimenting with 2x4 trusses in place of rafter framing, spurred on by research at Purdue, U. of Illinois, Michigan State, Virginia Tech, and others. Even entire hip systems resembling today’s had been proven effective when subjected to long-term full scale load tests. Of course, all of these used glued and nailed plywood gussets. One of these builders in South Bend, Indiana, cited in American Builder magazine, used this method. Not specified was whether this approach was practical in the winter months on a muddy jobsite. Thus, the building industry was primed for a much improved, more practical truss technology.
And Cal Jureit delivered it on January 19–23, 1958, in Chicago, even attracting builders from overseas. Jureit described the experience as taking “a tiger by the tail” and this inspired him to spread his technology far and wide, and inadvertently create a raft of competitors. His timing was perhaps perfect, but since then, so has been the timing of the many innovators who come to BCMC, a show aimed specifically to our industry. And consider how easy it is to get to see their innovations today, traveling on jet airplanes or on an Interstate Highway system, both of which didn’t exist in 1958. And walking leisurely to the Show over a bridge from your hotel and seeing everything in a single space in a modern convention center — we’ve certainly come a long way.