Los ladrillos en la construcción industrializada
Vicente Sarrablo, Catedrático de Construcciones Arquitectónicas en la Universidad Internacional de CataluñaUna de las características de la arcilla cocida como material de construcción es que se ha utilizado desde los más remotos orígenes de la tecnología. La revolución, aún en marcha, es la de incoporar la manufactura off-site en sistemas de fachada que siguen teniendo el material cerámico como responsable de la “cara vista”.
Vicente Sarrablo analiza en este artículo la técnica industrializada con ladrillo hoy en día, tanto dentro como fuera de España.
Asistimos actualmente a un protagonismo creciente de la construcción industrializada, un modelo de edificación en el que los sistemas constructivos que forman parte del edificio se fabrican en taller y se transportan a obra para ensamblarlos en su ubicación definitiva. Esta manufactura off-site de la construcción requiere de una industria lo suficientemente desarrollada para que resulte un gran avance. Cuando se alcanza resultan evidentes las numerosas ventajas que la industrialización aporta relacionadas con la sostenibilidad y los aspectos ambientales, económicos y sociales. Así, además de su importante velocidad y reducción de los plazos de ejecución en obra, se consiguen reducir los residuos, se alcanza un mayor control de costes y un mayor ahorro de energía y emisiones de CO2, desciende la siniestralidad laboral y, por último, permite la estabilización de puestos de trabajo junto a una mejora de la conciliación familiar de los operarios, cuestión que ha logrado que por primera vez se vea una verdadera integración de la mujer en la industria de la construcción más allá de los tradicionales puestos administrativos que ocupaba.
El hormigón, el acero y, sobre todo últimamente, la madera son materiales que han avanzado mucho su desarrollo en este campo. El hormigón se ha refinado y se ha aligerado cada vez más en los paneles modulares y la madera (con paneles de CLT) está batiendo récords de edificación industrializada en altura.
Frente a estos materiales, la prefabricación de los cerramientos con acabado de fábrica de ladrillo ha recibido una menor atención en el pasado. Quizás porque se han asociado en exceso los ladrillos con la albañilería, con la construcción in situ colocada pieza a pieza, y porque la imagen del ladrillo evoca masa, espesor, peso, todo lo contrario de lo que proporciona la técnica industrializada.
Sin embargo, los paneles prefabricados con acabados latericios ya hace tiempo que existen en el mercado (fig. 1), aunque más en el internacional, especialmente en aquellos países con industrias potentes y mayores necesidades de industrialización de la construcción debidas a requerimientos climáticos y/o económicos. En nuestro país empiezan a destacar algunos fabricantes que pueden ofrecer respuestas industrializadas para los problemas de la construcción actual que ya han comenzado a generar arquitecturas interesantes.
En la casuística de componer paneles de gran tamaño con pequeñas piezas de ladrillo se dan varios tipos de estrategias industrializadas de las que destacaremos las cuatro principales: los paneles ligeros de plaquetas cerámicas, los paneles de hormigón con acabado de fábrica de ladrillo, los muros prefabricados de fábrica de ladrillo y los tejidos cerámicos.
Panel ligero de plaquetas cerámicas
Su concepto parte de utilizar la apariencia superficial de un muro de fábrica de ladrillo aprovechando tan sólo sus dos últimos centímetros exteriores por lo que este tipo de paneles presentan un espesor muy reducido y unos formatos y pesos manejables por los operarios sin necesidad de grúas. Su presentación sustituye entonces los ladrillos por plaquetas cerámicas que se fijan en seco o con adhesivos sobre chapas metálicas, paneles de plástico o planchas de aislantes térmicos.
El antecedente de este sistema son las mathematical tile usadas en Inglaterra en los siglos XVIII y XIX. Esta antigua técnica permitía levantar recintos livianos que aparentaban pesadas paredes de ladrillo claveteando las piezas cerámicas de manera solapada sobre un panel de madera y con un rejuntado posterior. Las piezas cerámicas funcionaban, más que como un ladrillo, como una teja de cubierta, en un patrón parcialmente superpuesto para expulsar el agua de lluvia. Su parte inferior, la parte destinada a ser visible cuando se completa el mosaico, era más gruesa mientras que la sección superior se deslizaba debajo de la teja superpuesta de arriba y quedaba oculta. En la esquina superior presentaba un hueco para insertar el clavo que las sujetaba al soporte de madera (fig. 2).
El diseño de las actualmente llamadas brick tiles no ha variado mucho respecto de aquellas, salvo que ya no se solapan porque confían la impermeabilidad al panel que las soporta. Y si bien existen diferentes variantes que colocan las plaquetas una a una y que después se deben rejuntar con morteros in situ, la verdadera industrialización la presentan aquellas en las que el panel llega a obra con las plaquetas ya incorporadas y rejuntadas desde el taller

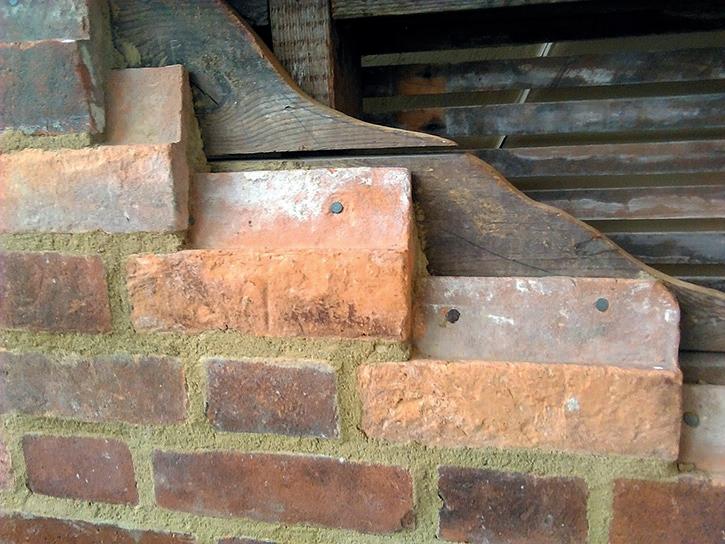

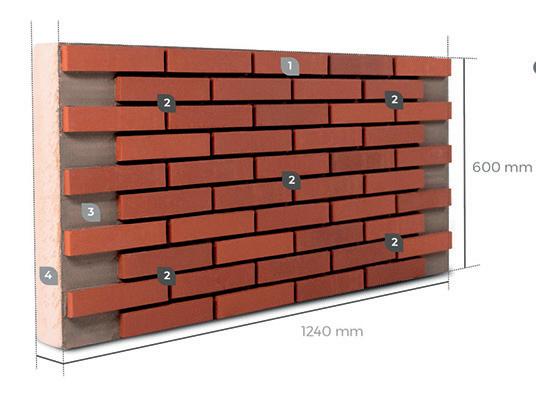
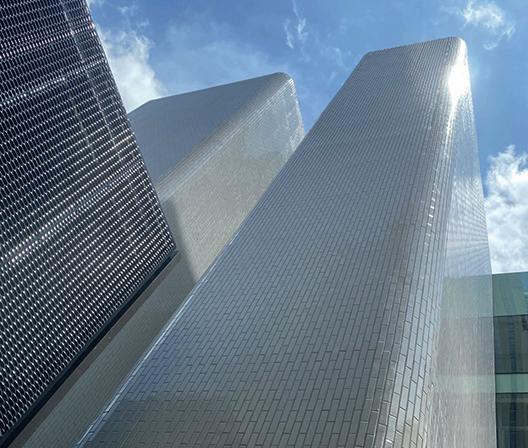
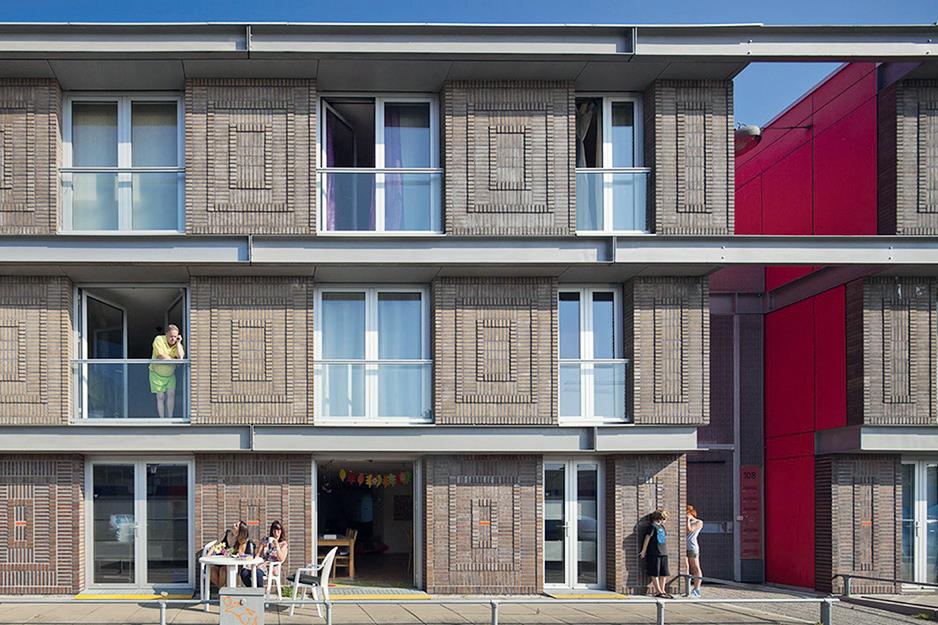
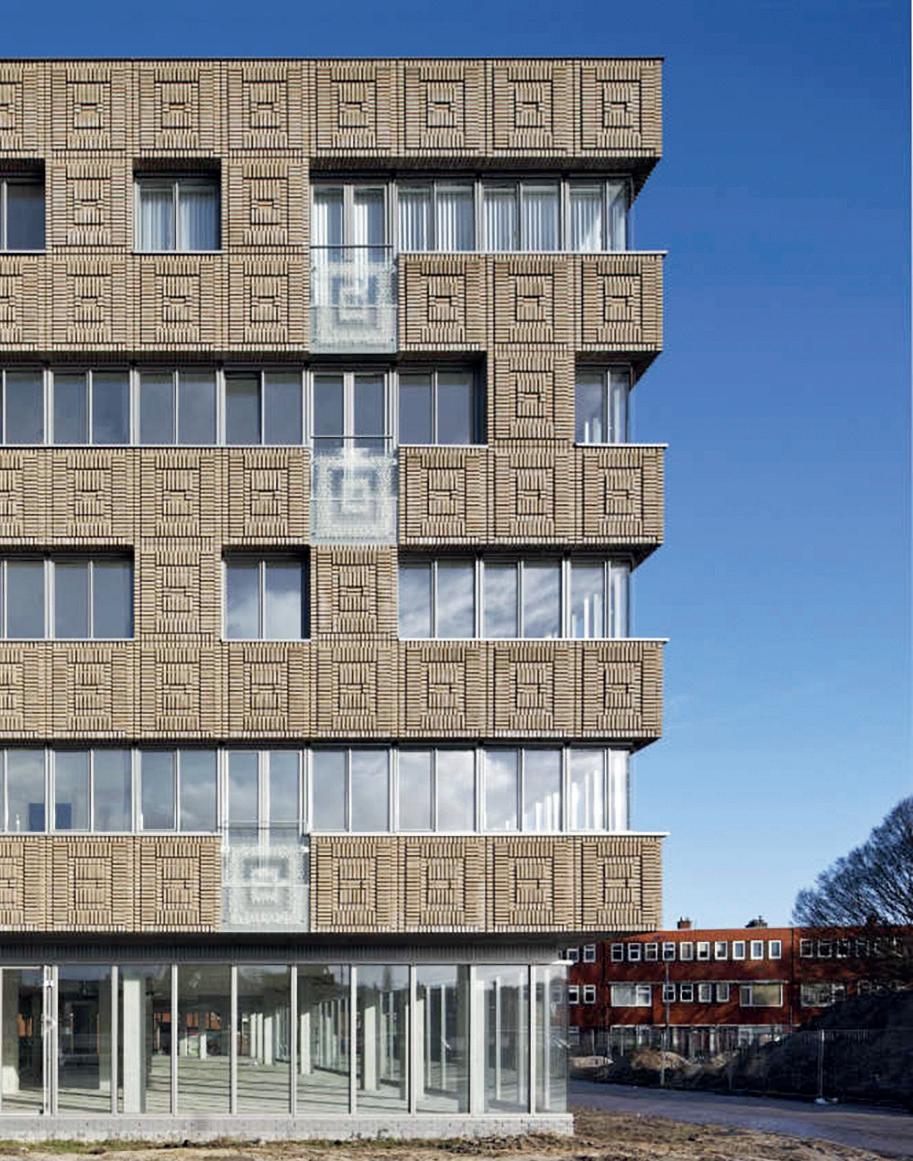
1 Construcción con panel prefabricado en 1961 y 1964, Barrio Darnytsia, Kiev, Ucrania. Fotografía de Tsentral’nyi derzhavnyi kinofotofonoarkhiv Ukrainy im. G.S. Pshenychnogo, publicada en Kateryna Malaia, A Unit of Homemaking: The Prefabricated Panel and Domestic Architecture in the Late Soviet Union
2 Mathematical tiles, en el Bourne Hall Museum, Ewell, fotografía de Lord Belbury (CC)
3 Termoklinker, de La Paloma cerámicas
4 Hospital de Paitilla, TASH arquitectos
5 Molde en silicona para el replanteo de plaquetas en panel
6 Residencia en Zootermeer, Marlies Rohmer Architecture & Urbanism. Fotografía de Rob ‘t Hart
7 Centro multifuncional en Ámsterdam, Marlies Rohmer Architecture & Urbanism
8 Intense city, Marlies Rohmer Architecture & Urbanism. Fotografía de René de Wit
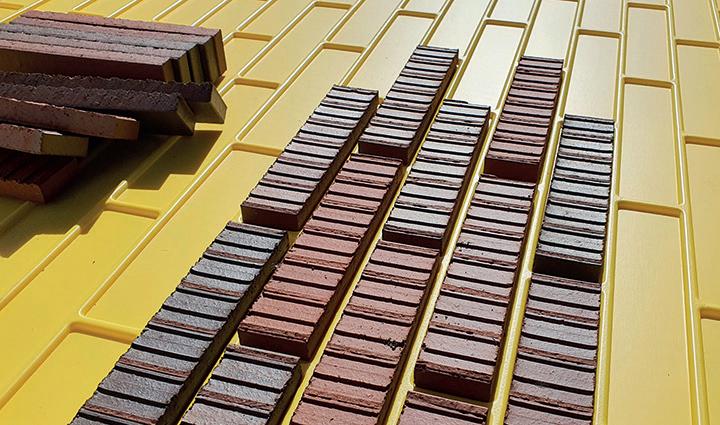

de producción. Además, en los últimos tiempos se ha aprovechado para incorporar aislantes térmicos detrás de las plaquetas. Con ello pueden presentarse como sistemas de aislamiento térmico por el exterior (SATE) con un acabado cerámico que puede competir aportando mayor durabilidad que los convencionales rematados con mortero.
En España, los fabricantes de ladrillo del Grupo La Paloma lideran este tipo de sistemas industrializados con su producto Termoklinker® (fig. 3), un panel aislante de XPS con acabado de plaquetas cerámicas (también se le nombra como veture o prefabricated units for external wall insulation), con el que ya se han realizado importantes obras como la reforma de la fachada del Hospital Paitilla en Panamá, de los arquitectos TASH & Partners. En esta obra se afrontó la rehabilitación energética del hospital en sus enormes machones opacos de fachada suplementando sobre estos las planchas de Termoklinker® con una disposición vertical de sus plaquetas blancas esmaltadas que acentuaban las esquinas curvadas de los volúmenes tratados (fig. 4)
Paneles de hormigón con acabado de fábrica de ladrillo
Los paneles prefabricados de hormigón armado presentan multitud de acabados y los que aquí trataremos son los que muestran incrustaciones de ladrillos, ladrillos de poco espesor o plaquetas cerámicas como las vistas en el anterior punto. Los formatos de estos paneles deben alinearse con las dimensiones de los ladrillos, con un grosor del hormigón convencional de unos 20 cm más el de las piezas cerámicas. Su peso obliga a un uso de grúas para manejarlos.
Su conformación en taller se consigue, en primer lugar, colocando los ladrillos boca abajo en el molde dispuesto según el patrón requerido en plantilla, estándar o diseñado por el arquitecto. Estas plantillas se utilizan comúnmente para mantener los ladrillos en su posición, con una separación de unos 10 mm para las juntas de mortero (fig. 5) Los paneles tridimensionales pueden necesitar un medio adicional para sostener los ladrillos hasta que el hormigón se haya curado. Después se posicionan las barras de armado, los cáncamos de elevación y los soportes de fijación y, finalmente, se vierte el hormigón.
Una vez que el hormigón ha alcanzado la resistencia requerida, se golpea el molde y se voltea el panel. A continuación, se limpia la fábrica de ladrillo y, en su caso, se rejuntan las juntas de mortero. La variante con plaquetas ofrece una opción que permite rellenar previamente las juntas de mortero por detrás de las plaquetas antes de verter el hormigón. Los anchos de las juntas entre paneles suelen ser mayores que las juntas de mortero y están determinados por las tolerancias necesarias para la fabricación, la contracción del hormigón, la expansión térmica y la instalación. Por lo general, estas no exceden los 20 mm y se rellenan con un sellador después de la instalación. Para reducir su visibilidad en fachada se puede usar un sello espolvoreado en el que la junta se frota con polvo de mortero para anular el brillo del sellador y proporcionar una mejor consistencia visual.
El principal reto para los arquitectos que usan estos paneles de gran tamaño es básicamente de composición: se debe evitar o minimizar la repetitividad o la monotonía de sus superficies. Las estrategias para conseguir interesantes ritmos, colores y texturas pueden ser muy variadas, y en este menester el acabado con ladrillos ayuda mucho.
En Europa, una de las pioneras en activar estas composiciones fue la arquitecta holandesa Marlies Rohmer en edificios como la residencia para jóvenes en Zootermeer (2004), donde diseñó los paños ciegos entre vidrieras con un panel prefabricado sándwich que proponía una singular fig. ra latericia de rectángulos concéntricos (fig. 6). A partir de este primer ensayo, en los años siguientes realizó numerosas obras caracterizadas por diversas siluetas geométricas con ladrillos en relieve como el centro multifuncional en Ámsterdam en 2009 (fig. 7), la Intense City de Groningen en 2010 (fig. 8), la Escuela Het Meervoud en 2013 (fig. 9) o la Escuela en Houthavens en 2015 (fig. 10). Todas ellas en armonía con la arquitectura histórica holandesa construida con ladrillos desde el siglo XIX.

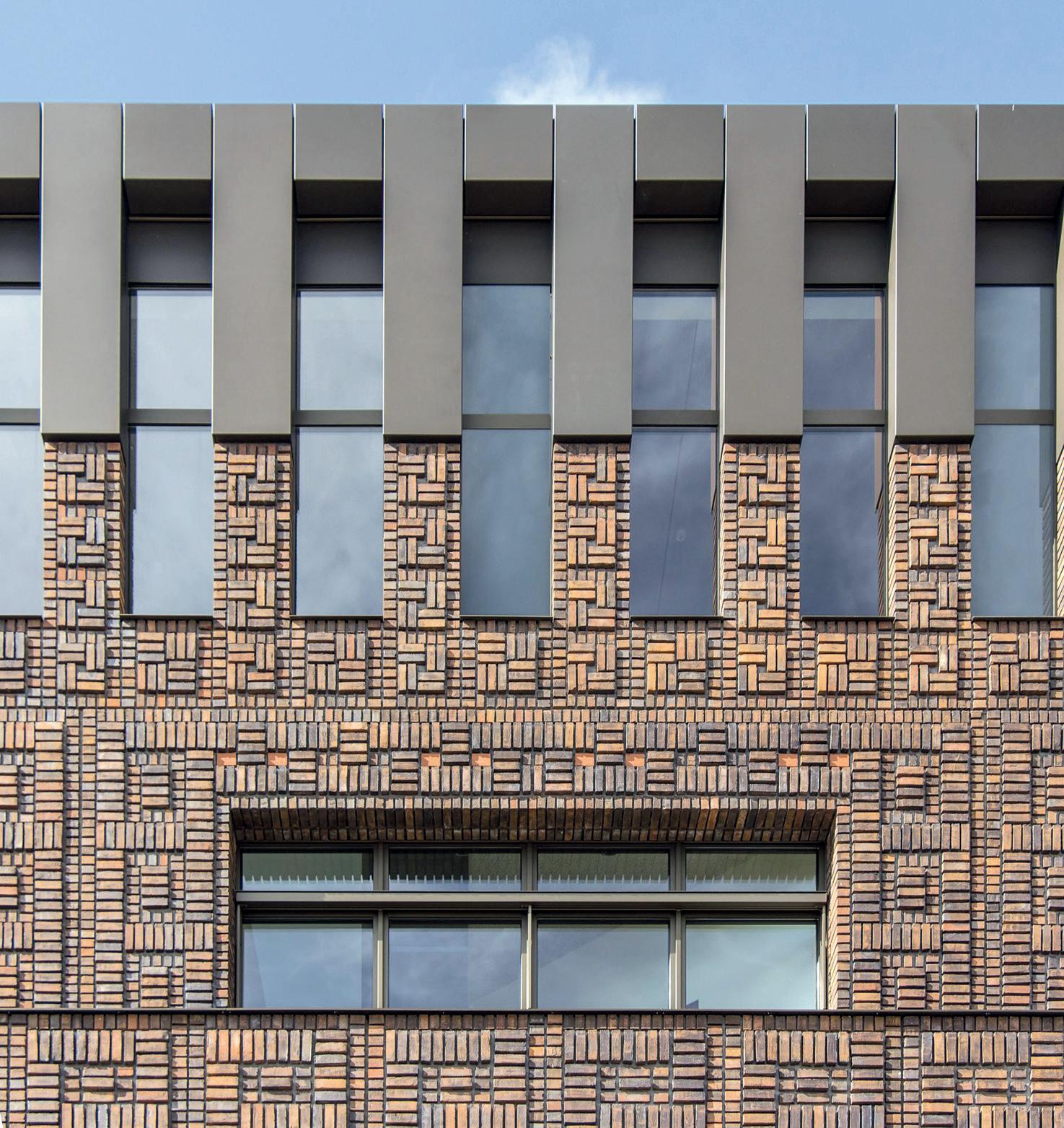
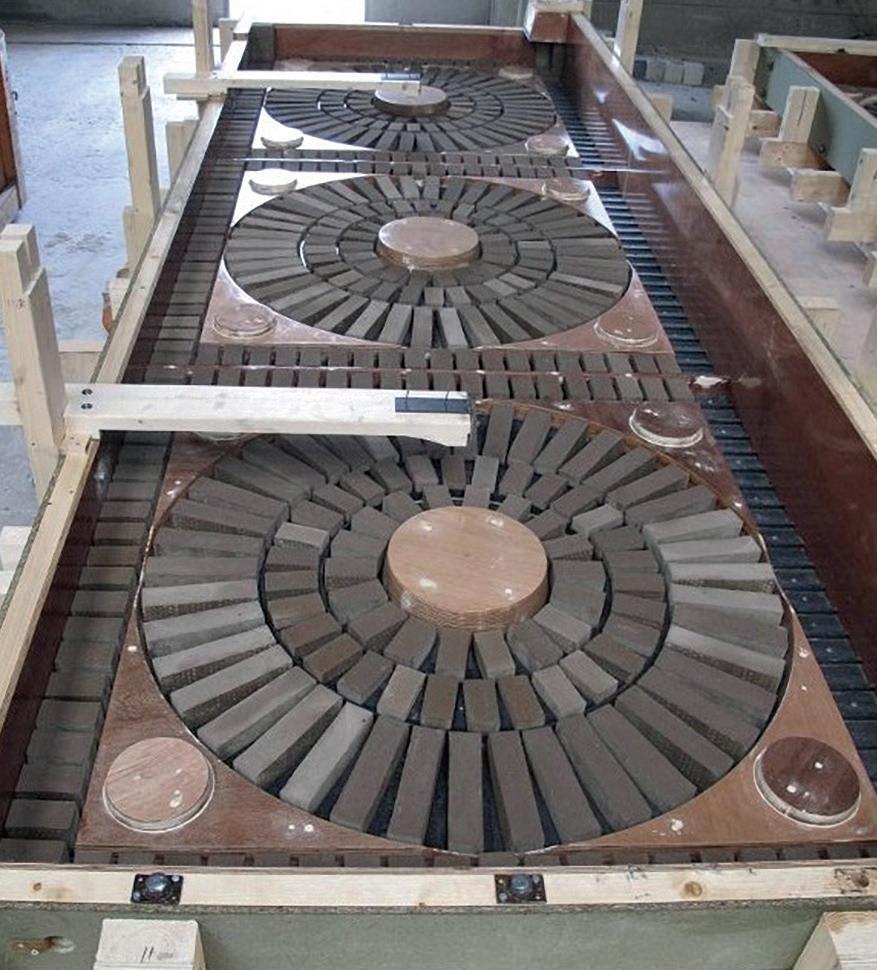

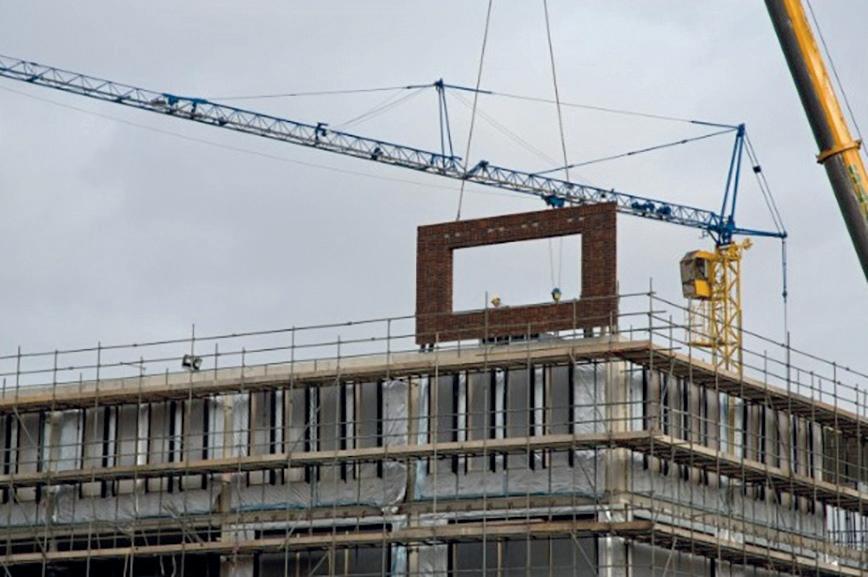


9 Escuela Het Meervoud, Marlies Rohmer Architecture & Urbanism. Fotografía de Thea van den Heuvel Fotografie / DAPh
10 Escuela en Houthavens, Marlies Rohmer Architecture & Urbanism
11 Bloque residencial Noordstrook, Dick van Gameren y Mecanoo architecten
12 Nimbus house, CF Moller Architects
13 Danish Meat Research Institute, CF Moller Architects
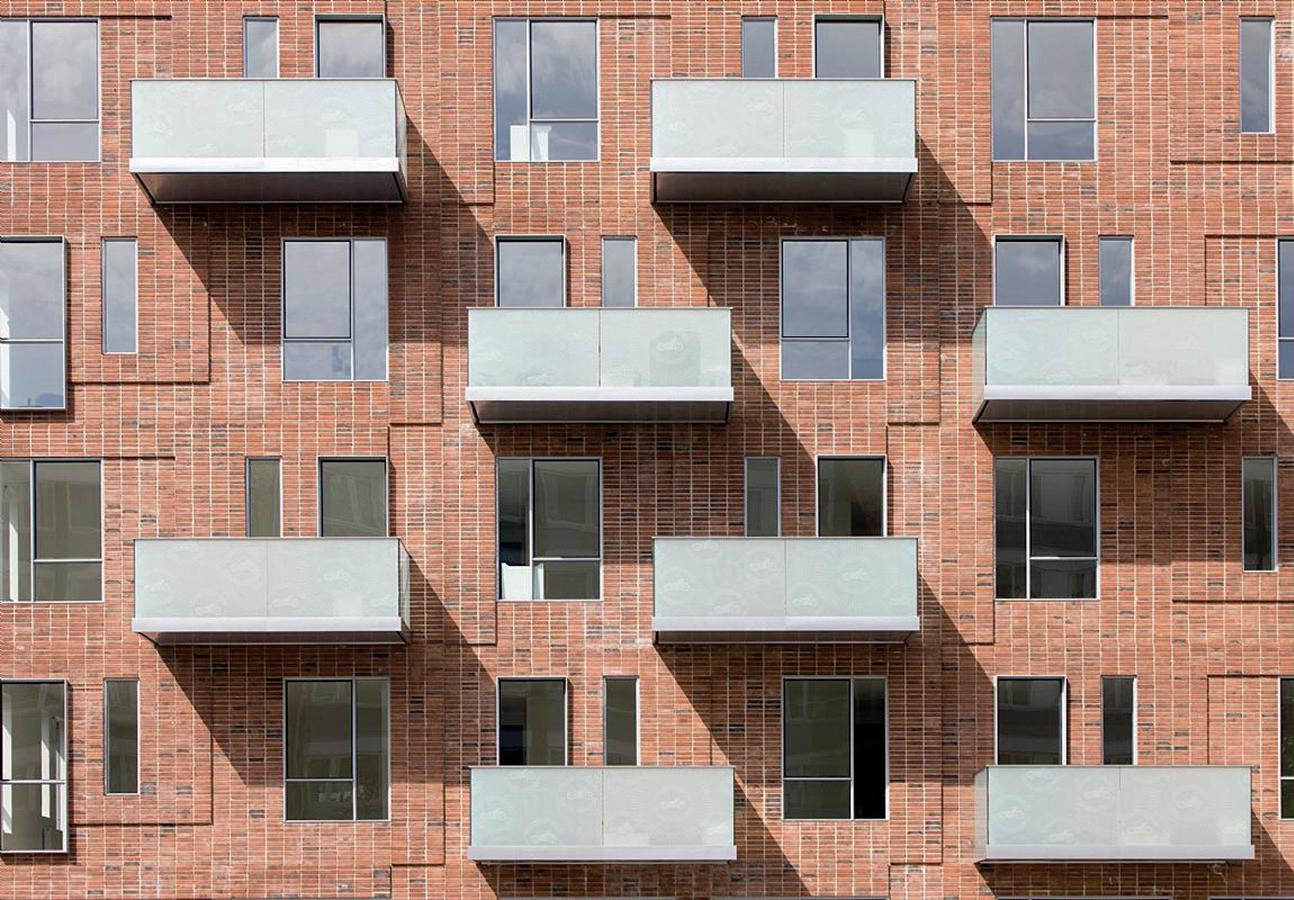
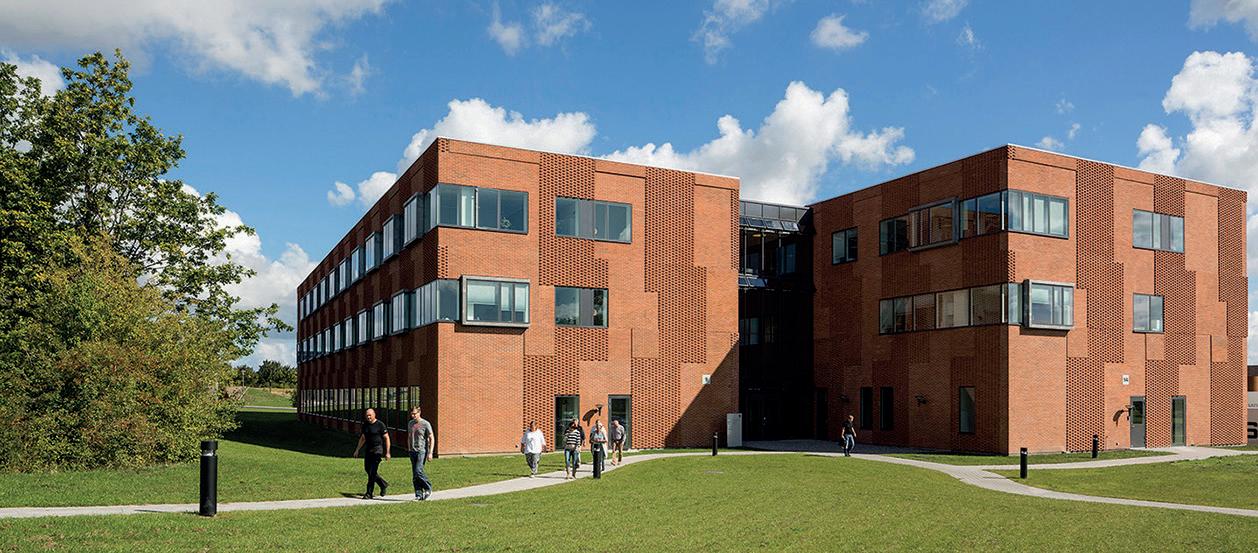
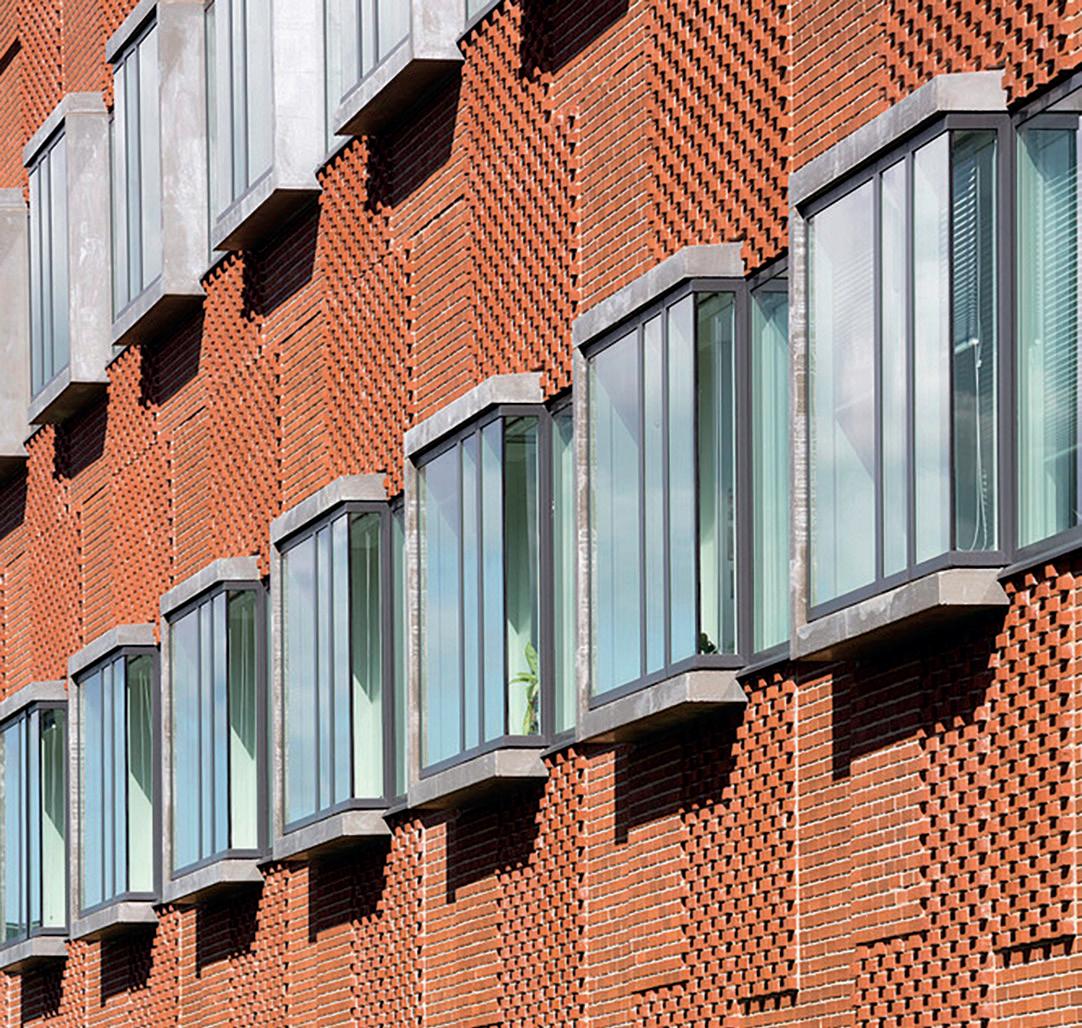
En el mismo país, en 2009, los arquitectos Dick van Gameren y Mecanoo aprovecharon la fachada de un bloque residencial en Ámsterdam para proponer un llamativo patchwork de paneles que evocaban unos tapices textiles con variadas texturas coloridas (fig. 11)
También en Dinamarca se consiguieron interesantes juegos compositivos en las experimentaciones de CF Møller Architects para la Nimbus House en Frederiksberg de 2008 (fig. 12) y el Danish Meat Research Institute de 2014 cerca de Copenhague (fig. 13), donde en ambos casos, para evitar la repetitividad monótona que podrían producir las juntas selladas entre paneles, se desarrolló un nuevo tipo de panel de hormigón en el que los ladrillos del paramento varían en profundidad y crean un juego de desplazamientos que arrojan sombras variables sobre las juntas, rompiendo su ritmo visual.
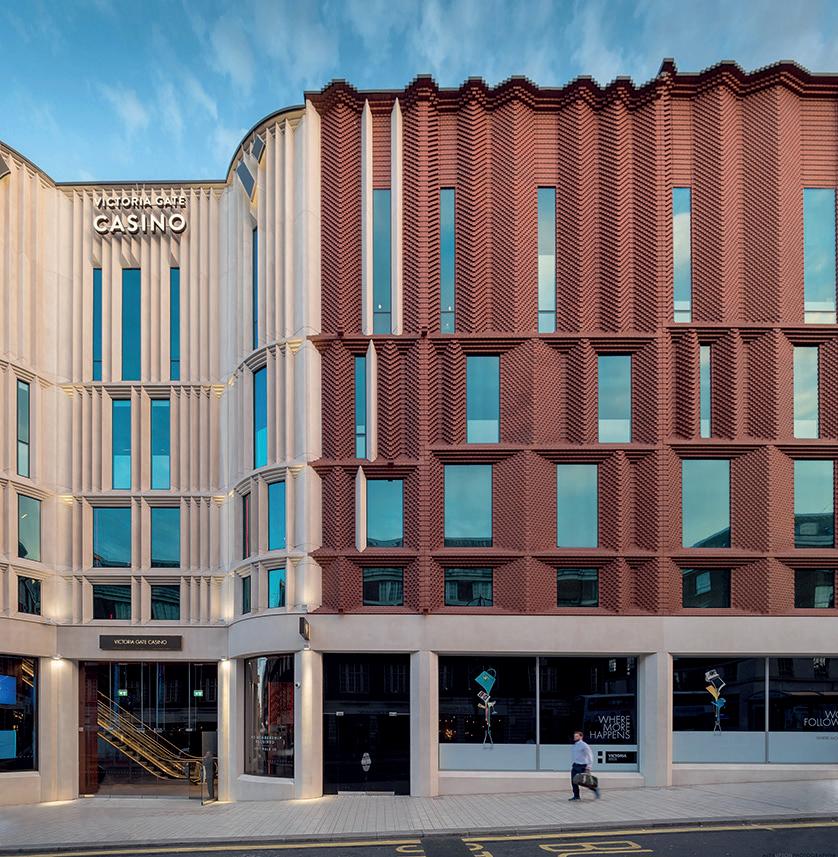


Otra estrategia consiste en la manipulación del panel con propuestas volumétricas que quiebran la planimetría convencional del prefabricado. En Inglaterra tenemos dos ejemplos interesantes: el Victoria Gate Arcades en Leeds, de ACME architects (fig. 14), que en 2016 propuso una atrevida composición muy vibrada en base a unos paneles prismáticos triangulares que buscan el recuerdo de las telas de la tradición textil de Leeds; y el edificio residencial Garden Falls en Londres que los arquitectos de TP Bennet diseñaron en 2017 (fig. 15), cuyo desafío era contextualizar el diseño de una fachada contemporánea de nueve pisos frente a una media luna de casas georgianas catalogadas. También con un trabajo volumétrico que rinde homenaje a las fachadas de su vecindario encontramos en Nueva York la Mulberry House de Shop architects de 2013 (fig. 16)
Y como último hallazgo, se ha llegado a demostrar que no solamente el hormigón armado puede ser el material de soporte de los ladrillos. Coincidiendo con el interés por la construcción industrializada con paneles de madera, que ha supuesto un reto sobre qué acabados deben tener para resistir el envejecimiento que producen los rayos UVA en climas con fuerte radiación solar, como en Australia, se han desarrollado paneles de CLT con acabado de ladrillo que a su vez se fijaban sobre estructuras de CLT. Es el caso de los edificios de la Universidad Nacional de Australia en Canberra, diseñados por BVN architects en 2019 (fig. 17), el primer caso en el país en instalar el innovador sistema de grandes paneles con pesos de 75 a 125 kg/m2, muy inferiores a los realizados con hormigón, y una velocidad de colocación de 200 m2 por día.
En nuestro país, hasta ahora se habían conocido pocos casos relevantes. En el número 45 de esta revista se publicó la sede administrativa del SESCAM en Toledo, de Pardo + Tapia arquitectos, construida en 2009, que presentaba una composición interesante de paneles para la planta baja de este edificio. Pero recientemente, en este año 2022, se ha inaugurado en Barcelona el Hotel Antigua Casa Buenavista, de TdB arquitectos (fig. 18), que usa en los techos de su planta baja paneles prefabricados y abovedados con acabado cerámico de Flexbrick®, aprovechando la investigación que estos arquitectos ya realizaron en 2015 en la vivienda piloto del resort PGA en Caldes de Malavella (publicado en el nº 58 de Conarquitectura). El ejemplo de estas obras y la aparición de nuevos productores de paneles como Insupanel® y MAPS® (de Cerámica Malpesa), que logra un panel con aislante que pesa 50Kg/m2 con 12 cm de espesor (fig. 19), pueden incentivar nuevos e imaginativos desarrollos en este campo
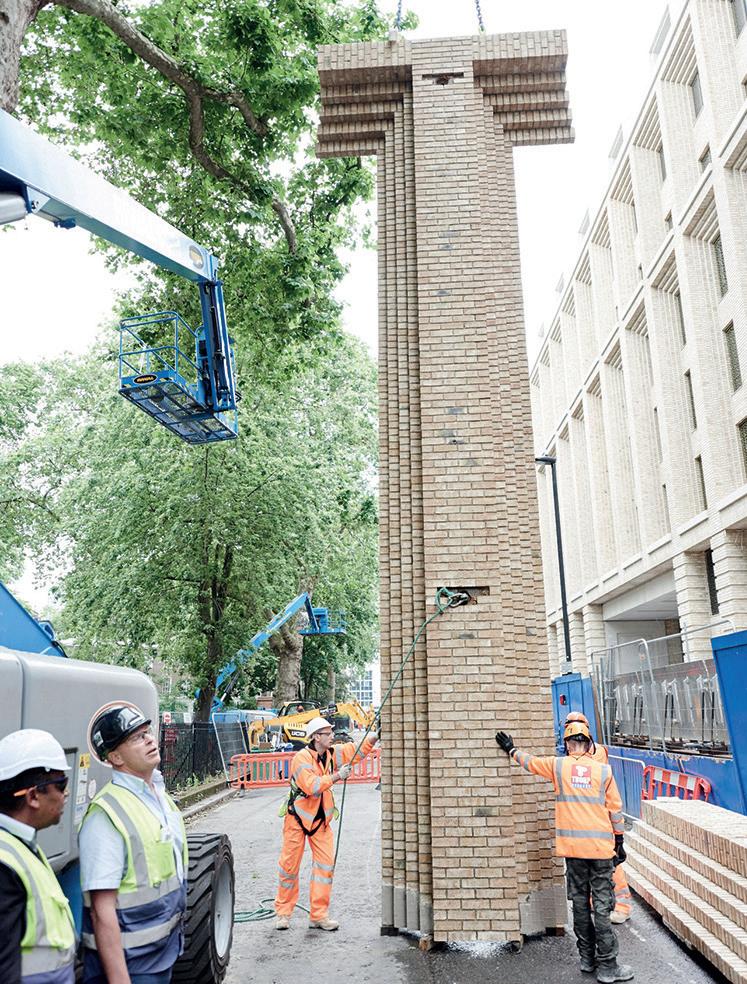

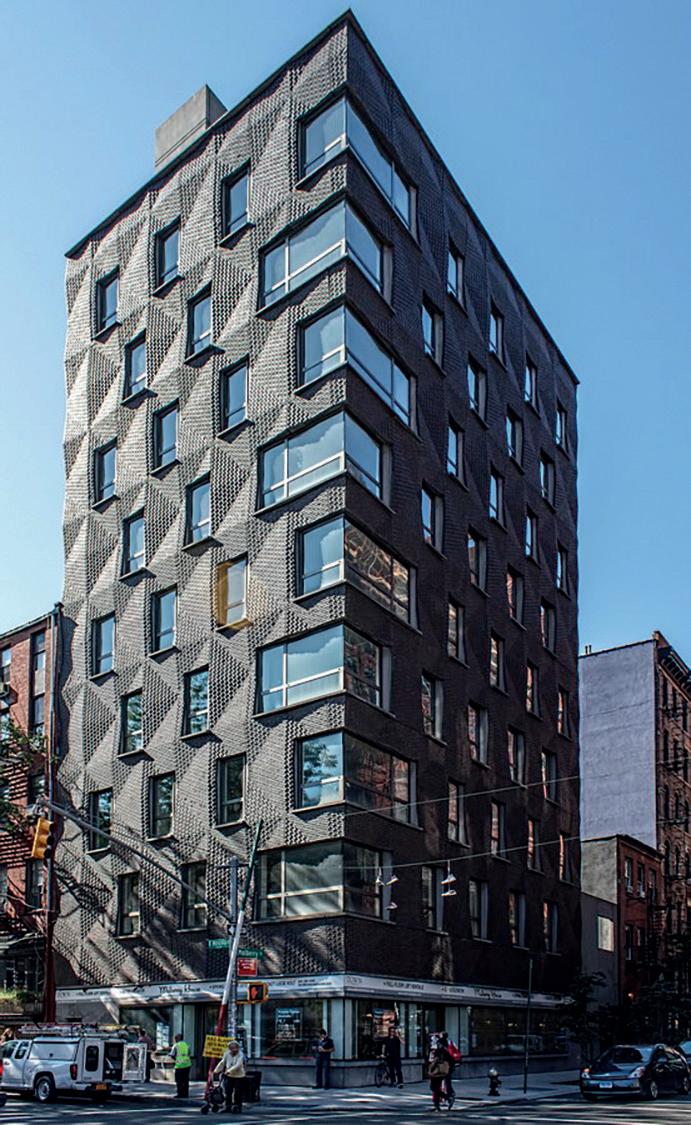
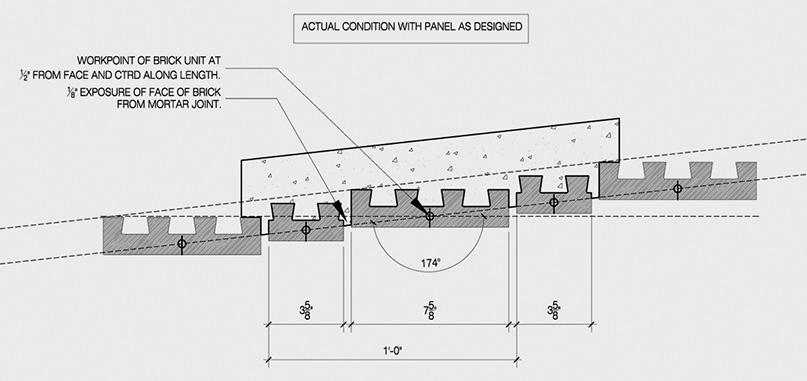

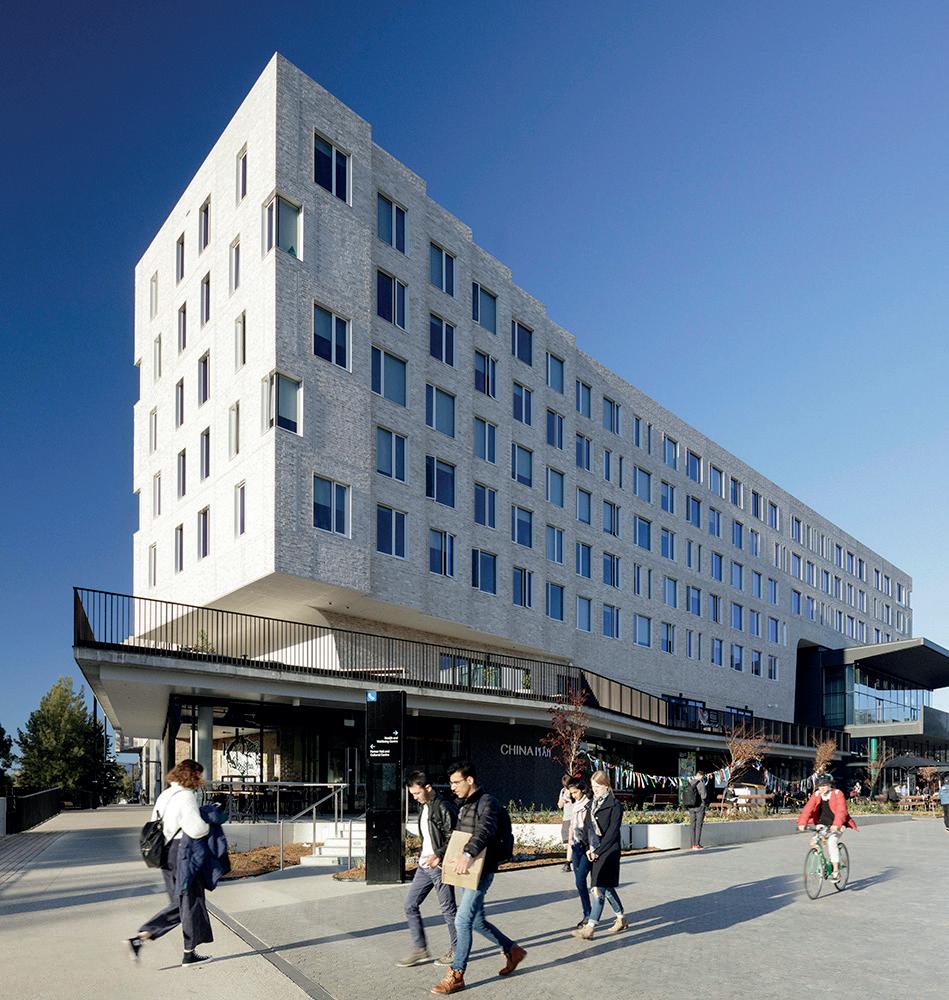
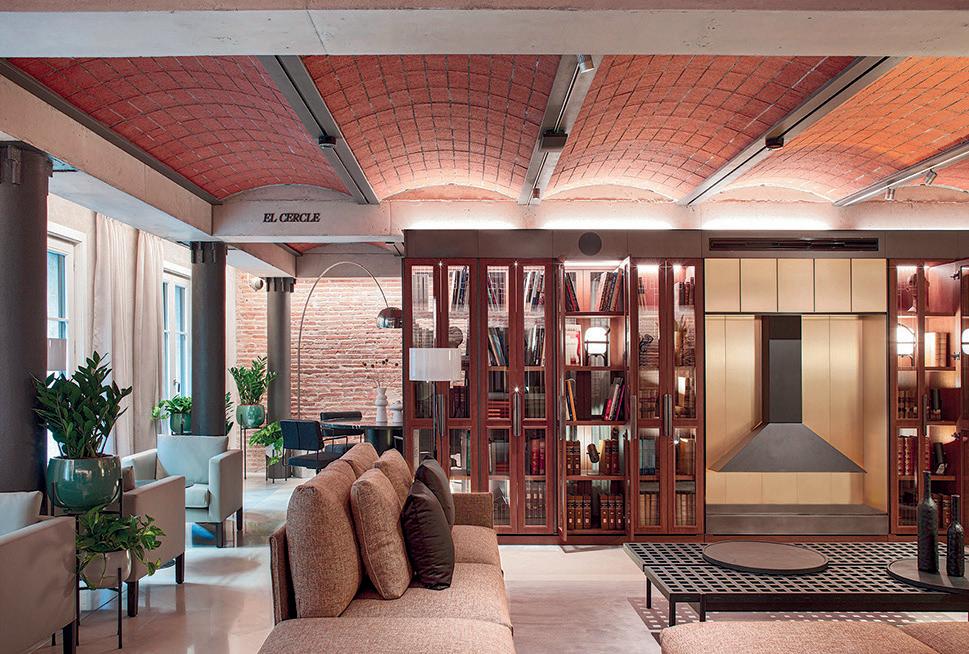
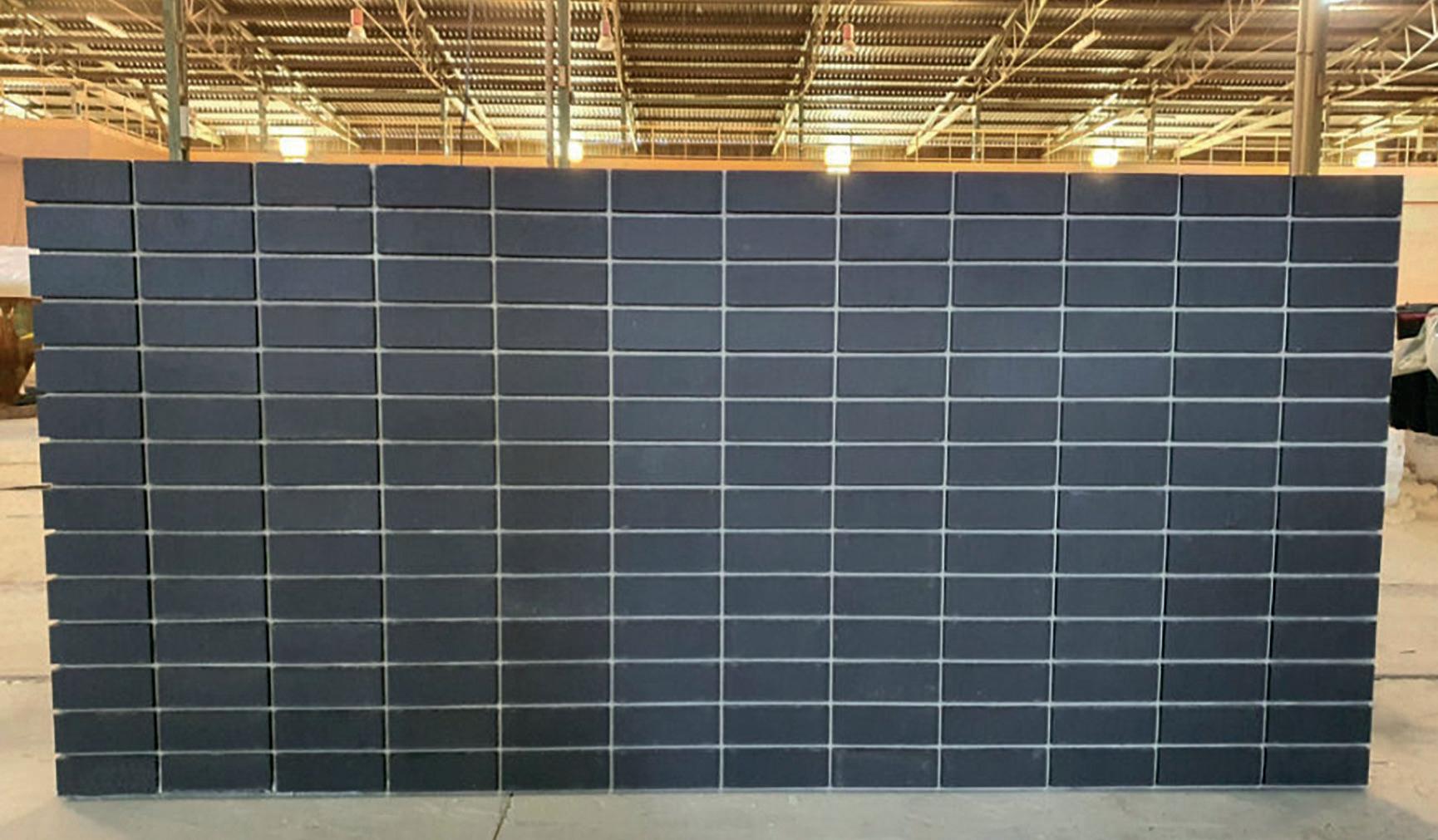
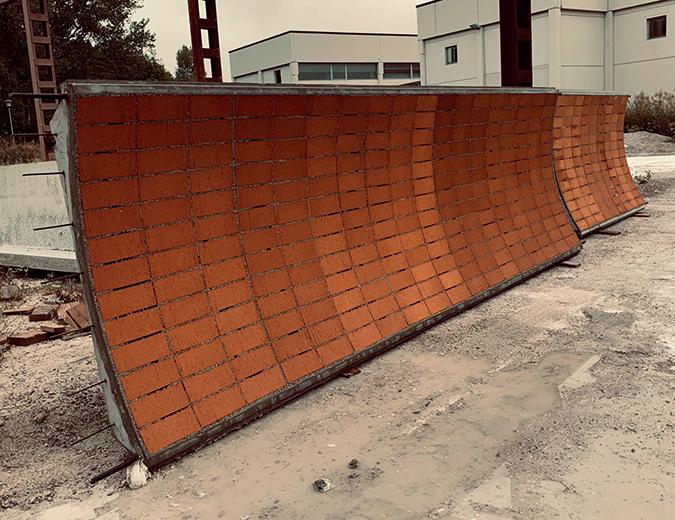
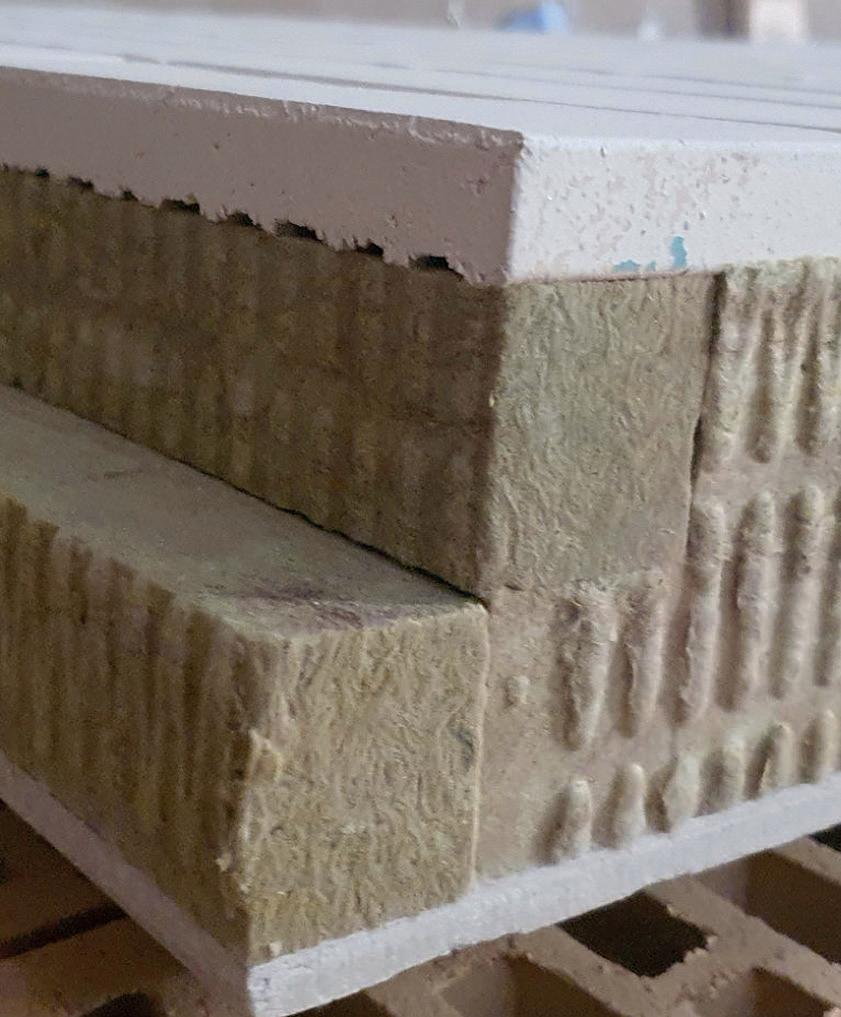
Muros prefabricados de fábrica de ladrillo
A diferencia del punto anterior, en este caso no se requiere un soporte posterior de hormigón, metálico o de CLT para sujetar a los ladrillos, sino que se aprovecha la propia capacidad resistente de la fábrica de ladrillos que pueden ejecutarse en una nave industrial para instalarlos en obra como un panel prefabricado. En algunos casos, los muros pueden incorporar armaduras de acero de refuerzo que soporten las flexotracciones del izado cuando se manejan con grúa (fig. 20). La construcción de estos muros en taller puede realizarse: 1) verticalmente como en una obra con albañiles que usan plomadas y cordeles a nivel; 2) inclinados ligeramente y apoyados sobre un tablero que hace la función de plantilla para los tendeles de ladrillos, lo que simplifica la prefabricación por no requerir ni plomadas ni cordeles; 3) horizontalmente sobre mesas de encofrado como en los paneles de hormigón y que no requiere de albañiles u operarios especializados, la ejecución puede realizarse con peones.
El siguiente paso ha consistido en sustituir a estos operarios por robots capaces de ejecutar complejos aparejos que resultarían lentos o caros de realizar por una mano de obra especializada: una albañilería sofisticada sin albañiles. El caso más avanzado en este tipo de industrialización es el que han conseguido Gramazio & Kohler en la ETH de Zurich robotizando el proceso de prefabricado de los muros que envuelven la bodega en Fläsch (Suiza), diseñada en 2006 por los arquitectos Bearth & Deplazes (fig. 21). En esta obra, el diseño peculiar de la fachada de ladrillos es creado por un robot industrial que sigue unos patrones pre-programados. Con estos se posicionan los ladrillos de tal manera que generan unas sombras con las que se obtiene una imagen abstracta tridimensional de objetos esféricos de gran tamaño inspirados en la imagen de un cesto lleno de uvas. Fabio Gramazio y Mathias Kohler han seguido investigando en este terreno, consiguiendo realizar varias obras más (fig. 22) y abriendo puertas a mayores logros como la ejecución de muros con drones.


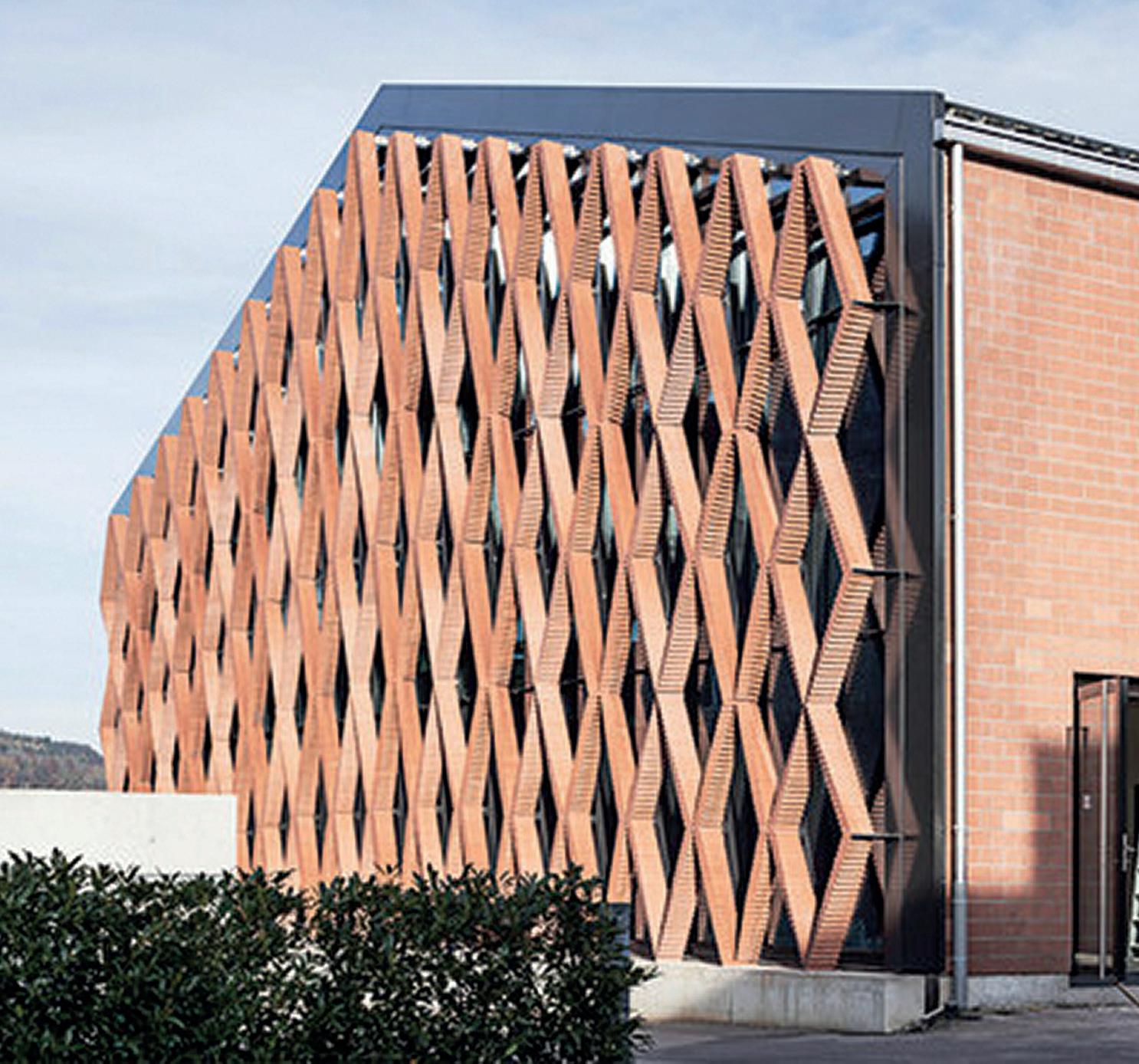
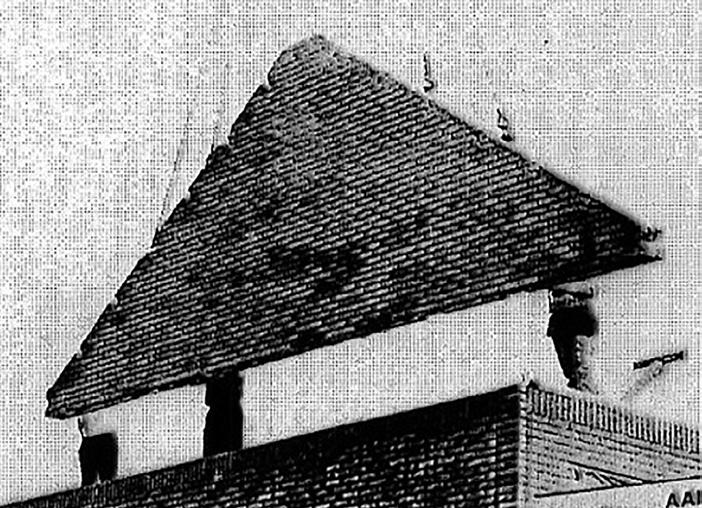

20
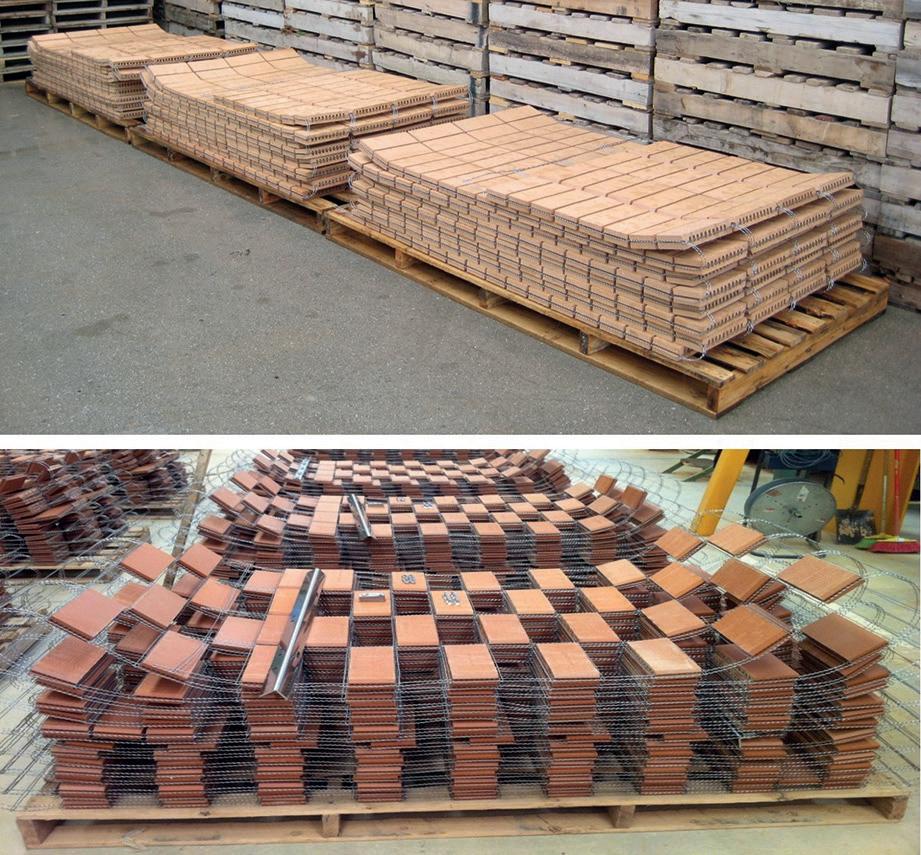
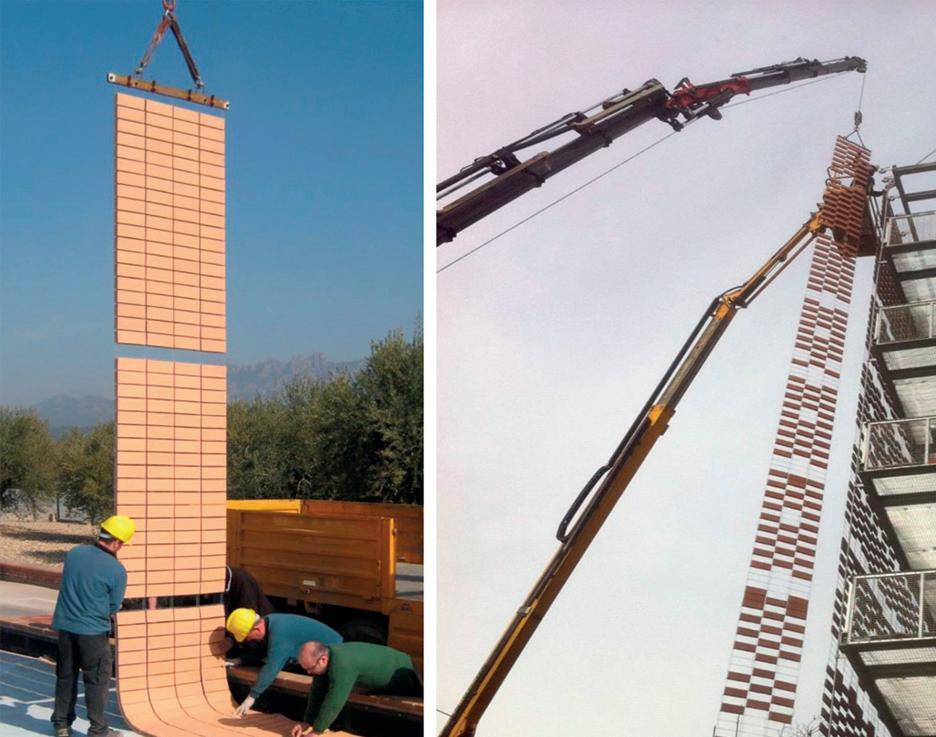
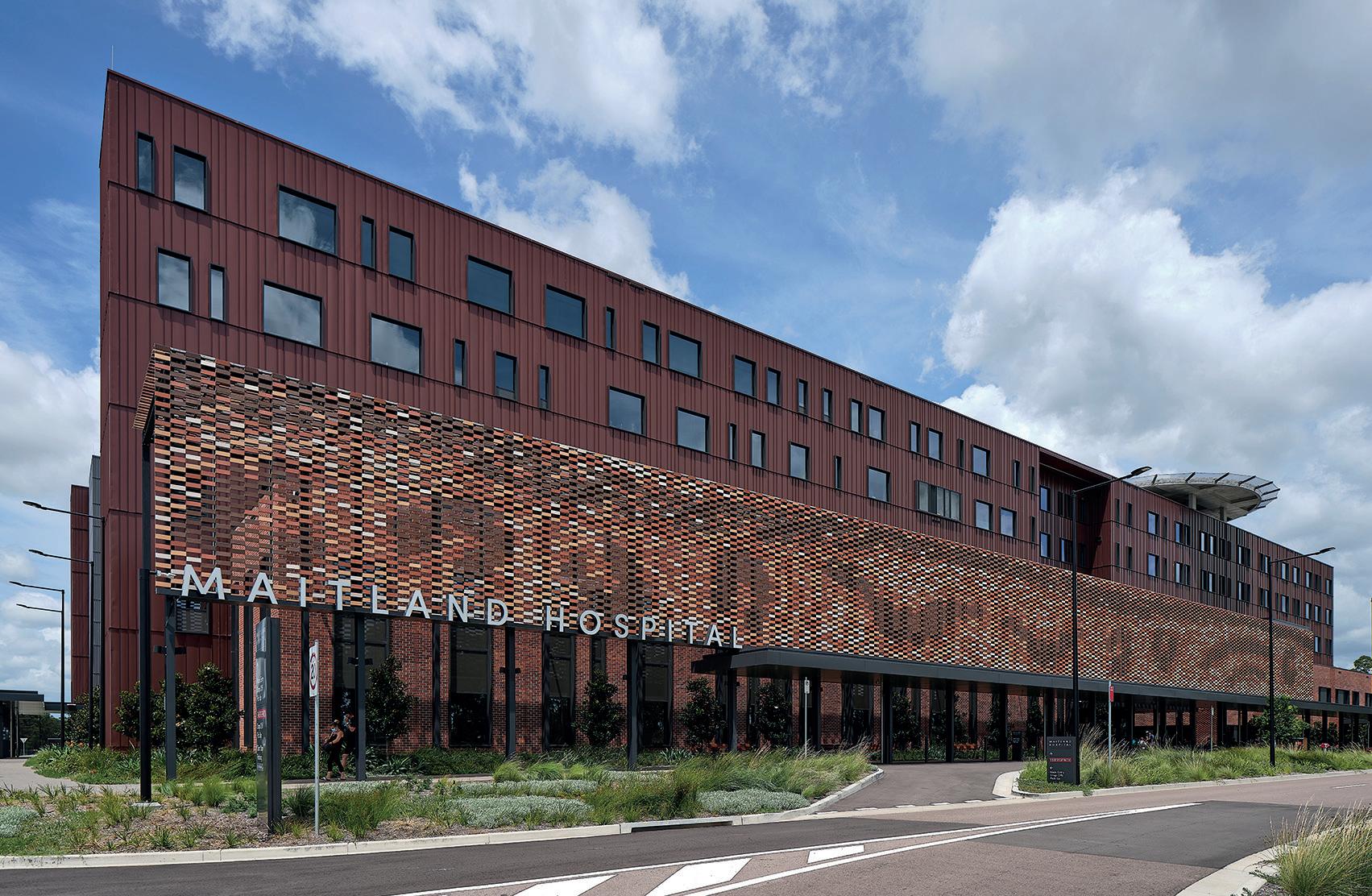

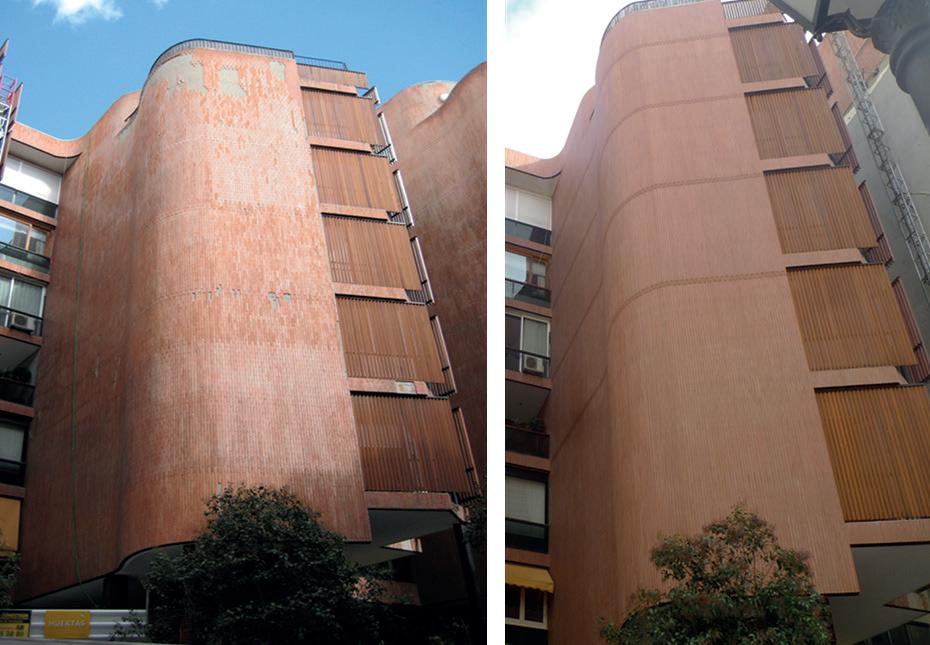
Tejidos cerámicos Flexbrick®
En esta última variante de industrialización con ladrillos los paneles ya no son rígidos sino flexibles. Y más que de paneles hablamos de tejidos para revestir en seco, sin hormigones ni morteros, en los que los ladrillos se presentan con su tabla vista confinados dentro de una malla de alambre de acero. La peculiaridad flexible de los tejidos Flexbrick® tanto les permite plegarse en palets, ventaja que ahorra espacio de transporte y almacenado (fig. 23), como adaptarse a cualquier curvatura que se precise en obra. Una vez llegan los palets a la obra, estos se despliegan con un izado de grúa y se pueden colgar como una cortina en un paramento de fachada o se pueden depositar como una alfombra sobre una cubierta o un pavimento (fig. 24)
23 Plegado del tejido Flexbrick en palets e izado para puesta en obra
24 Izado con grúa del tejido Flexbrick para depositado sobre pavimento
25 Pérgola de Flexbrick en el Nuevo Hospital Maitland, BVN architects. Fotografía de Martin Siegner
26 Rehabilitación con Flexbrick del edifico Girasol de Coderch por el Estudio Galante (antes y después). Fotografía del autor
Lanzado por Cerámica Malpesa y Piera Ecocerámica desde el mercado español en el año 2011, actualmente este sistema se coloca en todo el mundo, incluidas obras en Australia como la recientemente concluida pérgola de entrada para el nuevo hospital Maitland en Nueva Gales del Sur, de BVN architects (fig. 25). Estos arquitectos eligieron para el umbráculo, que protege a los visitantes del inclemente sol australiano, unos atractivos tonos cromáticos que evocan la cultura de los indígenas de la zona.
Si bien la mayoría de las aplicaciones de Flexbrick® son colgantes o depositadas, últimamente se ha desarrollado una variante adherida al cerramiento soporte que permite usarla como solución SATE. En el número 70 de Conarquitectura se escribe un artículo sobre ello y se presenta esta aplicación con el ejemplo del edificio Girasol, diseñado por Coderch, que contó con una magnífica rehabilitación del Estudio Galante mediante este sistema (fig. 26).