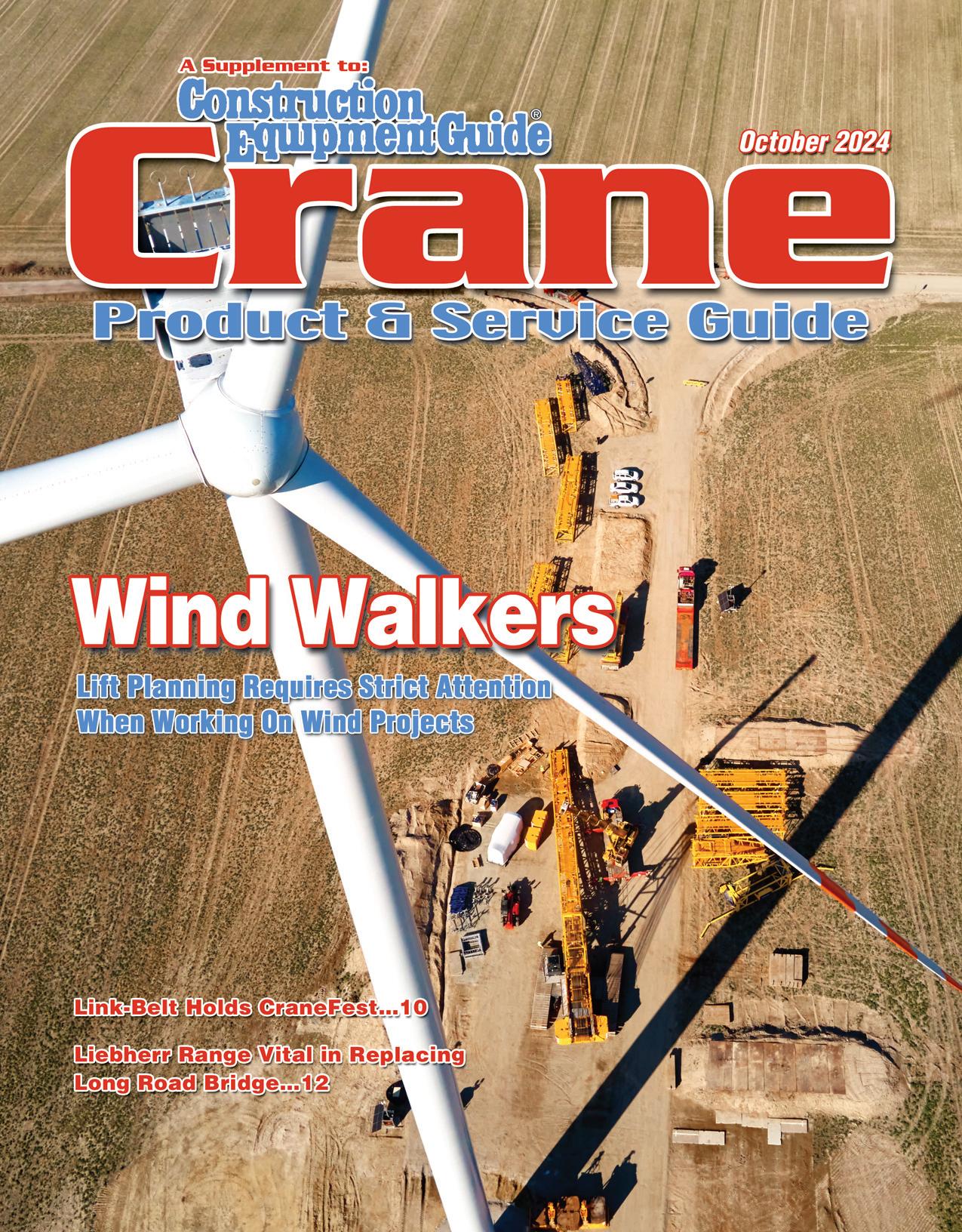
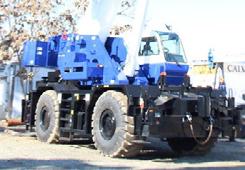
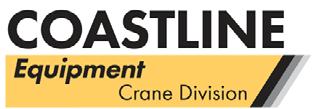
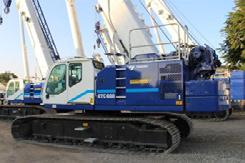
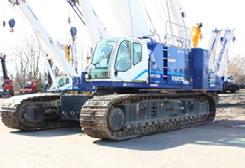
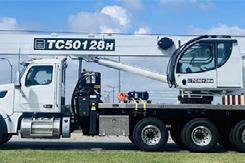
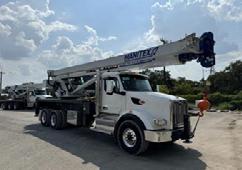
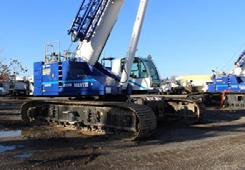
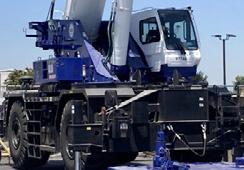

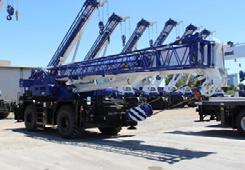
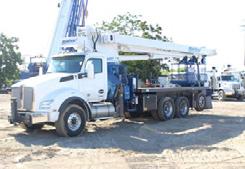
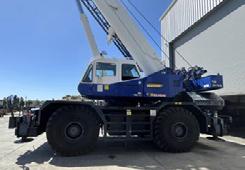
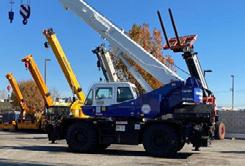
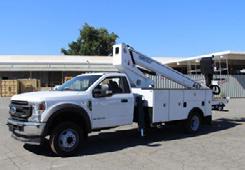
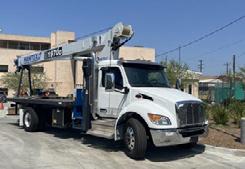
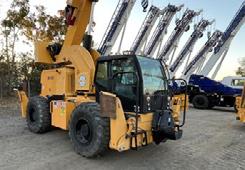
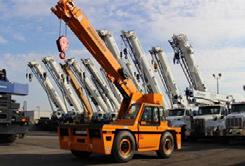
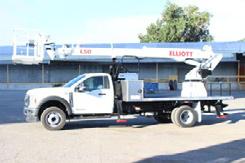
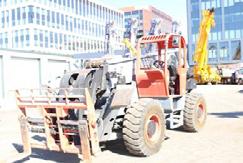
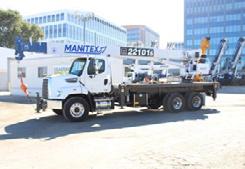
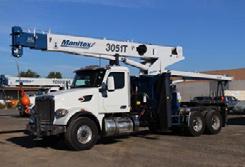


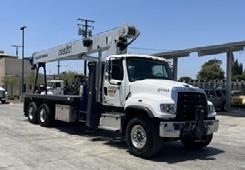
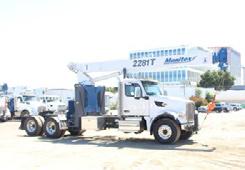

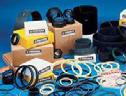




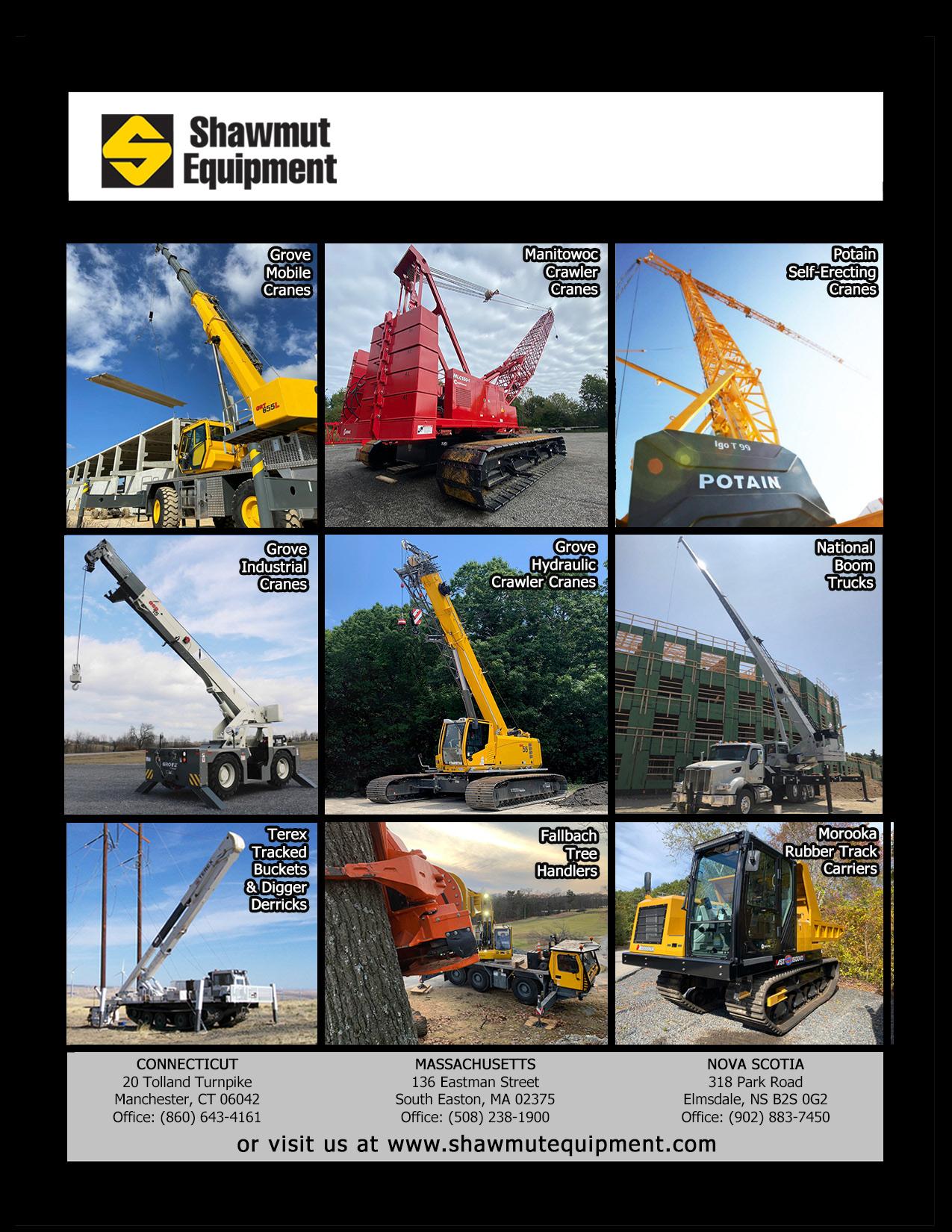


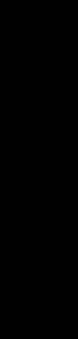
By Lucy Perry CEG CORRESPONDENT
Mobile cranes, especially crawlers and all-terrains, are critical components in wind turbine installation. When it comes to hoisting blades and tower sections into place, cranes provide the lifting capability contractors can’t get with other machines. But there are basic ground rules contractors need to know in planning turbine transport, installation and maintenance.
Poor planning and the wrong team on a wind installation project can result in missed deadlines, unexpected costs or
even damaged components and machines.
Lift planners need to plan for logistics, crane transport and, once on site, ground conditions. With vertical operations, wind conditions are a factor, as well.
Cranes at wind farms are larger, with longer crane booms that are often 300 or more feet in the air, said Hank Dutton of Travelers Insurance.
“Ground conditions are really critical,” said Dutton, senior regional construction specialist of Travelers. “The ground needs to be level within the crane manufacturer’s specifications.”
The surface also must be “strong enough to resist the forces imposed by the crane, which can be greater than the weight of the crane, plus what is being lifted.”
Every lift should be considered a new lift — operators and crews need to resist complacency.
Uneven ground conditions, high winds and other factors can make wind farms especially risky for cranes, he said.
Besides lift planning and operations, wind farm developers and contractors should consider the unique risks of cranes in transit at their site, urged Dutton.
continued on page 8
Alta Equipment Company
www.altaequipment.com
Byron Center, MI (616) 878-7450
New Hudson, MI (248) 356-5200
Flint (Burton), MI (810) 744-4840
Traverse City, MI (231) 943-3700
Detroit, MI (313) 394-1811
Atlantic & Southern Equipment
www.atlanticandsouthern.com
Birmingham, AL (205) 951-6656
Theodore, AL (251) 443-5229
Lake City, GA (404) 361-1100
Midland, NC (704) 731-7272
Central/Eastern, TN (888) 951-6656
General Equipment & Supplies
www.genequip.com
Shakopee, MN (952) 224-1500
Minot, ND (701) 852-0479
Fargo, ND (800) 437-2924
Bismarck, ND (701) 223-9700
Williston, ND (701) 572-0570
Nixon-Egli Equipment Co.
www.nixonegli.com
Ontario, CA (909) 930-1822
Tracy, CA (209) 830-8600
Columbus Equipment Company
www.columbusequipment.com
Columbus (614) 443-6541
Toledo (419) 872-7101
Cincinnati (513) 771-3922
Richfield (330) 659-6681
Cadiz (740) 942-8871
Dayton (937) 879-3154
Massillon (330) 833-2420
Zanesville (740) 455-4036
Piketon (740) 289-3757
Kelly Tractor Co.
Crane & Foundation Equipment
www.kellytractor.com
Clewiston, FL (863) 983-8177
Davie, FL (954) 581-8181
Ft. Myers (239) 693-9233
Mulberry, FL (863) 205-2537
Miami, FL (305) 592-5360
Orlando, FL (407) 568-8055
West Palm Beach, FL (561) 683-1231
Rudd Equipment Company
www.ruddequipment.com
Louisville, KY (800) 283-7833
Corbin, KY (606) 528-9440
Prestonsburg, KY (606) 874-2104
Evansville, IN (812) 867-6661
Ft. Wayne, IN (260) 482-3681
Indianapolis, IN (317) 247-9125
St. Louis, MO (314) 487-8925
Clearfield, PA (814) 765-8500
Leetsdale, PA (412) 741-1731
Nitro, WV (304) 755-7788
Link-Belt Construction Equipment Mid-Atlantic
www.link-beltmidatlantic.com
Ashland, VA (800) 552-3837
Chesapeake, VA (800) 342-3248
Frederick, MD (833) 546-5235
New Castle, DE (302) 501-6900
Transport Equipment Sales
www.tes-inc.net
South Kearny, NJ (973) 589-4100
Wood’s CRW Corp
www.woodscrw.com
Carlisle, PA (717) 795-0700
Central Square, NY (315) 676-2008
Williston, VT (802) 658-1700
North Oxford, MA (508) 499-1950
“From steep mountain-top sites in the northeast to soft ground conditions at farmland sites, crane operators face significant risks when walking cranes from pad to pad.”
With a long history of advising crane company clients, Travelers offers tips on specifically for contractors working in the wind sector.
1. Make sure lift plans reflect wind farm risks.
Create a lift plan that reflects the conditions expected at the site and addresses the crane manufacturer’s limitations and specifications.
“Each site pad has a different set of conditions that needs to be evaluated carefully,” Dutton said. “Review every lift plan with crew members involved, including the crane calculations, ground condition requirements and the associated rigging drawing.”
2. Ensure riggers are trained in specialized rigging.
Rigging-related accidents at wind farms have the potential to create significant damage and cause fatal injuries.
“These are high-risk operations,” said Jay Hurin, a Travelers risk control construction specialist.
Specialized rigging designed to lift long, heavy turbine blades can require additional training. Therefore, it is important to ensure riggers have reviewed the rigging manufacturer’s instructions as well as the rigging drawing as part of the lift plan.
Risks include falling objects and being crushed by heavy equipment. There’s also the potential for costly damage to the crane and the turbine. And “if something goes wrong, these tend to be serious accidents,” Hurin said.
3. Create a plan that addresses the hazards when moving the crane.
The crew involved in relocating a crane between wind turbine pads should follow the site plans, which have generally been developed by engineers.
These plans should address the crane manufacturer’s specs as well as the ground conditions needed to support the crane for the entire travel route.
“Not only can injuries and damages be severe, but so too can delays in the project as turbine blades usually have long manufacturing lead-times,” Dutton said.
4. Monitor weather conditions.
Extreme weather can be especially dangerous at a wind farm installation. Have weather monitoring equipment on site and weather procedures established.
5. Re-evaluate site conditions after severe weather events and site changes.
It’s important to re-evaluate ground conditions after a severe weather event or other changes to site conditions.
“Analyze the conditions at the time that you’re trying to walk the crane,” Dutton said.
Another concern is traction of the crane when coarse aggregate is used for the roadway. The crane’s tracks can start digging up the ground cover as it turns, and conditions can become dangerously unlevel.
“Operators need to understand the crane manufacturer’s level requirements while walking cranes, including front-to-back and side-to-side,” Dutton said.
6. Exercise caution when disassembling a crane.
The large-scale dimensions of wind farms can make distances between pads too great to travel fully erected cranes.
“There is an inherent risk in assembly and disassembly that people need to be aware of,” Dutton said.
Employees can be injured or worse if pins are removed in the wrong order or counterweight is removed too soon.
Transporting a disassembled crane on a truck also requires performing due diligence.
That includes pulling appropriate permits, making sure the load is properly secured and ensuring that drivers are qualified. Contractors should check drivers’ motor vehicle records and confirm that they are properly licensed.
7. Follow road plans for established sites.
When significant maintenance needs to be performed and cranes are brought back on site, it’s important to first establish safe conditions. This can involve replacing access roads and installing crane pads to ensure that soil is stable for transporting and using cranes.
It’s important to have a qualified professional design a road plan that addresses slope, firmness, compaction and levelness for the entire route
“Sometimes that means rebuilding access points across a large site,” Dutton added.
Because transportation and downtime are two of the primary costs of crane operation in wind farm applications, it pays to consider dedicating one crane to the entire project.
8. Have a commitment to safety at all levels.
“There really needs to be support from management, including the site superintendent,” said Dutton. “One bad decision … can lead to a costly accident.”
Creating a culture of safety can help crane operators, spotters and other members of the team feel more empowered, he said.
That encourages employees to report potentially dangerous site conditions that might delay the day’s activities and avert a potential disaster in the long run.
Gerrit van Doornik of Wind Solutions said two of the primary costs of crane operation, especially in wind farm work, are transportation and downtime.
Cranes require dismantling and transporting site to site, which can drive a single day’s rental costs to $50,000 depending on how crane size fits the job.
Van Doornick, president of the turbine parts and services company, told windpowerengineering.com that 20 or more truckloads may be required for transport.
“Each truck can move a load about 600 miles a day, or multiple loads over a shorter distance,” he said. “If a crane needs to move 100 miles, it would likely need a truck to move two to three loads in a day.”
He said that means mobilization costs can add up to almost 50 percent of overall crane cost, even for a single turbine repair. He advised that, on the turbine maintenance side, economies of scale and careful planning are the solution. If a turbine needs major maintenance every five years and the maintenance cycle lasts one week, a single crane could maintain 52 turbines per year.
Van Doornick believes that on a wind farm with many turbines located close together, a crane sourced full-time to that site would cut down on relocation costs.
“Onsite labor downtime can add up as well,” he said. “Once the crane is delivered, it takes a few days to set it up, depending on crane type.”
And when maintenance tasks are completed, it takes another couple days to dismantle and prepare for loading onto trucks to start the process again. Also, the crane team and turbine technician team work on different scopes. When the crane is being assembled, moved or disassembled, the tech team is idle.
This means more crane personnel are needed. Once the crane is ready to work, the technicians are working but fewer people are needed on the crane side.
“This leads to inefficiencies on both teams; up to 40 percent of labor costs can come from idle time,” said van Doornick.
He added cross-training technicians to be proficient in both crane operation and wind turbine maintenance can be an effective way to reduce costs. This cross training also can improve the efficiency of the entire process by eliminating the need for separate technicians for each task.
“Companies can save significantly on recruiting and reduce the number of personnel on site,” he said.
Another plus? Cross-training can improve the overall efficiency of the maintenance process, said van Doornick.
“Having technicians familiar with both cranes and wind turbine communication and coordination can streamline the work and reduce downtime.”
He added for the wind turbine owner, this makes the process far easier because a single contractor can complete each element of the turbine maintenance process.
“However … it requires time and resources to provide the necessary education and ensure that technicians are proficient in both areas,” he cautioned.
Ultimately, cost savings and efficiency make cross-training crane teams a potentially worthwhile investment, said van Doornick. CQ
Link-Belt Cranes held CraneFest 2024 at its world headquarters in Lexington, Ky., Sept. 16 to 20, 2024. The event was held in two-day sessions with representatives of the company’s dealer network, rental houses and end users in attendance to learn about Link-Belt’s historic beginnings, manufacturing capabilities and lineup of world class cranes.
Link-Belt hosted a reception and dinner at Fasig-Tipton, the oldest Thoroughbred auction company. The reception and dinner provided an excellent opportunity for attendees to network with peers and spend time with Link-Belt representatives.
The following day, the Link-Belt executive team welcomed the group with opening remarks followed by a video presentation which outlined Link-Belt’s history, development and accomplishments. Attendees were then bussed to the Link-Belt Company world headquarters for a tour of the manufacturing facility. After the tour, attendees were led to an outdoor staging area for a live presentation of Link-Belt’s full product line.
Link-Belt introduced its new 65-ton (60 t) 65 RT to its rough-terrain product line. The 65 RT includes a four-section, full-power, greaseless main boom (38 to 115 ft. [11.6 to 35 m]) and an optional 35 to 58-ft. (10.7 to 17.7-m) offsetable bi-fold lattice fly that are manufactured in the United States at Link-Belt’s headquarters.
Link-Belt kicked off its 150th anniversary celebration with CraneFest 2024.
The 65 RT features a new hydraulic boom extend system, as well as LED lighting for brighter, more efficient lighting during low-light conditions. The 65 RT also is equipped with a new sixspeed Dana transmission with a remote filter for ease of servicing. The transmission is mounted to a 270-hp Cummins QSB6.7L Tier IV engine.
Following Link-Belt’s presentation of
its crane lineup, CraneFest attendees were treated to lunch, after which they had an opportunity to review the cranes up close while spending time with LinkBelt company representatives for a full run down on each of the models.
CQ
(All photographs in this article are Copyright 2024 Construction Equipment Guide, except where noted. All Rights Reserved.)
The new 65 RT rough-terrain
debuted at CraneFest 2024.
The replacement structure for the eastern half of the bridge is being built next to the existing bridge and is scheduled for completion in 2026.
Liebherr Range Vital in Replacing Long Road Bridge
The replacement of the Rader High Bridge in Schleswig-Holstein is one of the largest bridge modernization projects currently under way in Germany.
The bridge, built back in 1972, spans the Kiel Canal and is part of the A7 motorway. Measuring approximately 4,920 ft. in length, it is Germany’s second-longest steel road bridge and plays an important role in the flow of traffic to and from Denmark and the Scandinavian peninsula.
The bridge is approaching the end of its useful life as a result of high volumes of traffic, meaning that a rebuild and simultaneous widening of lanes has become necessary.
Strong support for this major construction project is being provided by 18 Liebherr cranes from the rental fleet of Friedrich Niemann GmbH & Co. KG, based in Kronshagen near Kiel. Five fast-erecting cranes, two 65 K.1s and three 81 K.1s, are on site to assist with the foundations. The new bridge piers are being built with the help of six 125 EC-B and seven 150 EC-B flat-top cranes.
Conditions on site are responsible for some spectacular crane assemblies. The first crane to arrive on the construction site, a 125 EC-B, was assembled at the end of 2023. Assembly took place in the waters of Lake Borgstedt, where the crane stood on the first pier’s pile cap secured by foundation anchors. This involved working with a Liebherr crawler crane from Nenzing (Austria). The 275.5 ton LR 1250 crawler crane required for the assembly was positioned on a floating platform between the crane site and the ferry used for transporting parts. The flattop crane reached a hook height of 144 ft.
Liebherr Project Department, Rental Fleet Support Planning, Implementation
Assembly in the water: The first crane used for the replacement of the Rader High Bridge was assembled on the new pile cap of the first bridge pier.
foundation anchors; some of them are set in concrete in the water. They are working with a hook height of between 160.7 and 223 ft.
The hydraulic climbing equipment has been provided by the Liebherr Tower Crane Center, the Liebherr partner for special crane hire, crane components and used machines direct from the manufacturer.
Three 125 EC-B cranes also were assembled using the 275.5 ton crawler crane, from its floating platform on the water. The cranes were initially assembled at a height of 98.4 ft. and then climbed to their final hook height of 164 ft. using hydraulic climbing equipment. This allowed them to work some 49 ft. above the height of the roadway.
A 150 EC-B 8 Litronic started off working on the bridge pier on land. But the progression of the site required the crane to be moved to a new location. At the end of June 2024 it was time: the flat-top crane was moved from the north side of the bridge to the next bridge column and reassembled in the water.
The disassembled crane was transported to its new location on a ferry and put back together again with the help of a 242 ton crawler crane on a floating platform. Once assembled, it climbed to a hook height of around 164 ft. and reached a jib length of 131 ft. The crane has the capacity to lift up to 8.8 tons.
Precise planning was required in advance for the use of the cranes, and Liebherr’s own project department for large and special projects (Tower Crane Solutions, TCS) provided valuable support. A major challenge lay in the cranes being assembled by the crawler crane on the floating platform.
As the permissible hook height of the crawler crane on the floating platform was restricted, the assembly height had to be kept as low as possible. However, a certain tower height was also necessary so that the cranes could be climbed. Various options and tower systems were therefore investigated in the run-up to the project in order to find the best solution.
The configuration of the tower combinations was another major issue prior to planning crane operations; it was essential to prevent the towers from colliding with the newly erected bridge piers and any potential tower deformations.
Consequently, the fast-erecting cranes are only partly utilizing their maximum hook height. The two 65 K.1 cranes are in use with their tower retracted as they slew under the bridge, and the three 81 K.1 cranes also are assigned to work under the bridge as well as at maximum height above it. The 13 flat-top cranes are assembled in a free-standing position on crosses and
Weather conditions present an extra challenge during construction work. The Rader High Bridge is closed to empty lorries and cars with trailers from wind force 9 onwards (storms with wind speeds of 46 to 55 mph). If the wind picks up further, it can be closed to all vehicles over 8.2 tons. In the event of a hurricane (wind force 12), the bridge is closed completely. The wind conditions therefore had to be taken into account in the cranes’ static calculations.
The Rader High Bridge is located east of the town of Rensburg, approximately 18.6 mi. from Kiel and around 40 mi. from Flensburg. Traffic currently flows across the Kiel Canal, Rader Island and Borgstedter Enge (part of Borgstedt Lake) on four lanes and two hard shoulders. The bridge’s piers stand both on land and in the water. Three piers are being erected in the water and require a foundation of 131 ft.-deep bored piles.
The new build is happening in two stages with traffic flowing along the existing bridge as well as the Kiel Canal, the world’s busiest man-made waterway. The eastern half of the bridge is being built first, next to the existing bridge, and is expected to be opened to traffic in 2026. Following this, the original bridge will close and be demolished, with the western bridge section being built in its place. The new structure is being widened to six lanes and should be finished in 2031.
continued on page 17
Versalift Midwest LLC
midwest.versalift.com
51761 Danview Technology Court
Shelby Twp., MI 48315 586-991-0054
L & M Truck Sales, Inc. www.lmtrucks.com
4001 E. Boone Ave. Spokane, WA 99202 509-535-4175
Stephenson Equipment www.stephensonequipment.com
Harrisburg, PA 800-325-6455
Philadelphia, PA 800-220-4033
Pittsburgh, PA 800-692-7600
Wilkes-Barre, PA 866-667-6756
Albany, NY 518-357-2200
Syracuse, NY 800-368-6455
Nixon-Egli Equipment Co. www.nixonegli.com
2044 South Vineyard Avenue Ontario, CA 91761 909-930-1822
800 East Grantline Road Tracy, CA 95304
209-830-8600
teamjdc.com
777 Doheny Drive Northville, MI 48167
800-336-4369
Antioch, CA 925-434-0320
Bay Shore, NY 631-416-5070
Cincinnati, OH 513-250-3080
Corona, CA 951-281-2550
Gonzales, LA 225-647-3010
Joliet, IL 815-727-1000
Greenville, SC 864-315-2900
La Porte, TX 281-842-8700
Orlando, FL 407-654-3840
Sulphur, LA 337-607-3260
Westfield, MA 413-642-4000
Twinsburg, OH 330-486-0800
Wharton, NJ 973-206-4300
Whitestown, IN 317-768-2600
Aspen Equipment aspenequipment.com
Minneapolis 9150 Pillsbury Ave. S Bloomington, MN 55420 952-888-2525
Quad Cities 1733 South Stark St. Davenport, IA 52802 563-949-4045
Omaha 11475 S 153rd St. Omaha, NE 68138 402-894-9300
Des Moines 1525 SE Cortina Dr. Ankeny, IA 50021 515-965-1000
Kansas City 1150 SE Hamblen Rd. Ste 2 Lee’s Summit, MO 64081 816-451-1745
The two Liebherr LTM 1750-9.1 all-terrain cranes were configured with 161 ft. of main boom and maximum counterweight.
The challenge: Replace a section of railroad bridge in a close, urban setting — in which you will need to use the remaining tracks to both roll the old bridge section away and roll the replacement section into the work zone.
The solution: a rarely seen heavy lift operation requiring two 900-ton cranes. Plus, they’ll be working side-by-side, but won’t be performing any dual picks.
“This kind of job only happens once or twice a career,” said Chad Rados, project coordinator of ALL Erection & Crane Rental, flagship branch of the ALL Family of Companies, which provided cranes for the job.
The operation happened this summer in Cleveland, Ohio, at the Norfolk Southern
railroad bridge over West Third Street near the city’s downtown. One crane was set up directly on the street below the span, the other in a neighboring empty lot, with the cranes only approximately 25 ft. apart.
“When you’re in the thick of planning the project, you’re thinking about all the little details that lead to a successful lift,” said Zac Kasparek, sales representative of ALL Erection & Crane Rental.
“Then the day came that we’ve got two 900-ton cranes set up and ready to work, and it occurred to me … the fact that we have two cranes of that size mobilized in one area, on the same job, is pretty impressive.”
Both were Liebherr LTM 1750-9.1 allterrain cranes configured with 161 ft. of
main boom and maximum counterweight. The crane on West Third Street, with its boom directly over the replacement area, also was outfitted with Y-guying to bolster boom capacity.
The operation called for the West Third Street crane to single-pick the old bridge section and set it on a flatbed rail car directly east of the now-missing section, on a second set of tracks. A road-rail vehicle (a truck able to drive on train tracks) powered the flatbed to the east, where the second Liebherr LTM 1750 lifted the old section off the flatbed, lowered it to the lot below, then picked up the new replacement bridge section and set it on the flatbed.
The road-rail vehicle next drove the flatbed back to the Third Street crane,
which picked it from the railcar and set it into the gap created by the absence of the old bridge section.
In essence, with the flatbed acting as a gobetween, the two giant cranes formed an assembly line.
Total elapsed time: about seven hours.
The need to use two 900-ton cranes in this manner was prompted by a variety of factors. The top elevation of the bridge was 55 ft. Because of the size of the bridge section, which measured 90 ft. and weighed 243,000 lbs., rigging required a large spreader beam. The narrowness of West Third Street left no room to lay down the old bridge section or the new one, requiring a shift to the adjacent empty lot.
“This is a classic case of the job picking the cranes,” said Rados. “The site logistics told us it was going to have to be two cranes. The limited amount of room and weights of the two pieces made it clear that the two 1750s were the best option.”
It’s unusual to deploy two cranes with such high capacities on a single job. ALL owns three of the units, and pulled these two from branches in Lima, Ohio, and Atlanta.
It took approximately 40 truckloads to deliver both cranes to the deceptively complex job site, and two to three days total to assemble them before and disassemble them afterward. Meanwhile, crane maneuvers all took place within a single seven-hour period in which rail service to the tracks was shut down.
(All photos courtesy of ALL Crane.)
from page 13
The bridge piers for the eastern replacement structure are being erected first. Steel parts for the substructure arrive as 13 ft. long components and are welded together on land to create elements up to 262 ft. in length. These are then pushed along towards the next pier using the incremental launching method, with one increment being one bridge segment. To do this, the piers have to be erected well in advance of the launching process.
Work has started north of the bridge and is progressing southwards towards Lake Borgstedt and across Rader Island in the direction of the Kiel Canal. There also is work under way to the south of the bridge, on the banks of the canal. The construction project is being carried out by a consortium headed by the Swiss construction company Implenia AG together with two Saxonybased companies Plauen Stahl Technologie GmbH and ZSB Zwickauer Sonderstahlbau GmbH.
On June 28, the first bridge segment reached the first pier. This particular segment is 183 ft. long, 46 ft. wide and 19.7 ft. high. Hydraulic presses moved the segment, which weighs several tons, at a speed of 29.5 to 32.8 ft. per hour southwards towards the first pier. The replacement structure will consist of a total of 14 sections, with one advancement planned for every six to seven weeks.
(All photos courtesy of Liebherr.)
sprague Energy is leading a large-scale project to unload and transport massive wind turbine components from vessels and rail off the coast of Searsport, Maine. The company is using a fleet of five Manitowoc crawler cranes to efficiently move components from sea vessels to holding yards and then onto trucks that will take them to various wind energy farms across the state.
The operation, which began in January 2024, employs three Manitowoc MLC150s, one MLC250 and one MLC300 VPCMAXTM, all of which perform up to 30 lifts per day. Loads vary from 267 to 112 tons, and the work is expected to conclude in October 2024.
Maine is set to significantly expand its current onshore wind capacity in the upcoming years. Together, the new wind energy projects will power over 62,000 homes and reduce CO2 emissions equivalent to 50,000 cars annually. Already, 26.19 percent of the state’s installed energy generation capacity comes from wind.
As the energy industry goes through significant changes, Manitowoc and its customers are playing a vital role in enabling this transition with efficient and innovative tools.
Sprague Energy, Shawmut Equipment, and a partnering transportation company are working on the Searsport project together. The process of unloading and moving the parts demands exceptional coordination and precision. Some larger components, like turbine blades, can reach lengths of up to 250 ft. and require two cranes working in tandem to lift them.
“Our Manitowoc cranes work together to lift the windmill’s tower sections, blades, hubs, drives and nacelles,” said
Cameron Giroux, terminal supervisor at Sprague Energy. “Due to the significant distance between pick points on the turbine blades, we are fortunate to be able to exe-
cute two-crane lifts. We rig the components with slings, shackles and hooks, and use a block and tackle at one end to maintain even pressure and prevent twisting of the blades. After that, we use the cranes to stage loads for the next phase.”
The complexity of the work underlines the importance of the precision and control Manitowoc’s Crane Control System (CCS) offers crane operators.
“Manitowoc’s CCS system is designed to improve operator efficiency and accuracy by offering intuitive controls and advanced diagnostics,” said Brennan Seeliger, Manitowoc’s product manager for crawler cranes. “Its user-friendly interface enables efficient operation, reducing the learning curve for operators. Users can harness the precise load monitoring, customizable configurations and automated functions of CCS that enhance job site productivity and reduce the risk of errors. This makes it an invaluable tool for experienced and new crane operators alike.”
Giroux also emphasized how collaboration between Sprague Energy and local Manitowoc dealer Shawmut Equipment has been vital to the project’s success.
“Together, we assessed each component’s specifications — weights, lengths, styles — and matched them with the appropriate cranes. Using the load charts as our baseline, we executed a highly coordinated operations plan that’s proving to be quite successful.”
“We’re managing a continuous flow of components from ship, barge and rail. The logistics are complex, and these cranes are essential for a seamless workflow,” Giroux said. “Without dependable cranes, we’d face significant delays. Fortunately, the Manitowoc cranes have proven reliable, and their performance makes the Manitowoc series — from 100 t to 300 t — our preferred choice when wind turbine components are larger.”
Sprague Operating Resources LLC, founded in 1870, is based in Portsmouth,
N.H. With a 150-year history, the company delivers innovative energy solutions and material handling services to commercial, industrial, wholesale and government customers across the Northeast United States
The NCCCO Foundation announced the launch of a new website, MyCraneCareer.org, an interactive, online resource for prospective professionals and employers in the crane industry.
With predicted shortages of skilled crane operators in the coming decades, fueled by an aging workforce, the website aims to educate about the field and provide engaging resources for individuals to get started in their path toward training, certification and employment. Over the next year, the website will be promoted by a targeted marketing and communications campaign to drive awareness of the potential career opportunities in the field.
“As with all skilled trade jobs, there is a significant need for many more quality people to fill and grow the career pipeline in the crane industry,” said T.J. Cantwell, executive director of NCCCO Foundation.
“The NCCCO Foundation recognized that the crane industry did not have a one-stop online resource that could provide the needed information and tools for individuals to learn about the many varied and amazing careers available. MyCraneCareer.org addresses a critical gap for our industry, and ultimately, we believe that it has the potential to create long-term, positive impact on our nation’s economy.”
and Quebec, Canada. It offers fuel storage, delivery, electricity, material handling, storage, natural gas and solar products and services.
(All photos courtesy of Manitowoc.)
many of the projects that the BIL is designed to fund will likely not be able to be achieved. In the coming decades, thousands of new crane operators will be needed to fulfill the growing demand across the nation.
“The need to develop a quality workforce that can fill the pipeline was the driving force behind the development of MyCraneCareer.org and the accompanying national workforce development campaign for the crane industry,” said Cantwell.
NCCCO photo
MyCraneCareer.org is a site dedicated to educating, engaging and exciting people about career opportunities in the crane industry. Visitors to mycranecareer.org can:
• Watch videos about careers in the crane industry and hear from individuals already working in the industry.
• Take a quick quiz and find out if they’re a good match for the crane industry.
• Learn how to get started in the field.
• Explore the different roles and career pathways.
• Learn more about cranes and the industry.
• Find educational resources.
• Connect to businesses and organizations within the industry.
In 2021, $1.2 trillion of federal funds was allocated by the Bipartisan Infrastructure Law (BIL) to support transportation, energy and climate infrastructure projects. The crane industry is a critical piece of the success of that infrastructure investment. Without cranes, crane operators, riggers, signalpersons and many others,
“We encourage companies and others working in the crane and rigging industry to use mycranecareer.org and its associated resources in their own community outreach and recruitment activities. We want this to be a powerful resource for the entire industry,” Cantwell said.
Courtesy of Historical Construction Equipment Association
Working to preserve the history of the construction equipment that shaped our world . . .
From the mid 1940s until as late as 1960, Hyster Company offered its Hystaway line of shovel, backhoe, crane and dragline attachments for Caterpillar crawler tractors such as this D7.
The Historical Construction Equipment Association (HCEA) is a 501(c)3 non-profit organization dedicated to preserving for public education the history of the construction, dredging and surface mining equipment industries.
Oklahoma City, OK
800-375-3339
Tulsa, OK
918-438-1700
McAlester, OK
918-310-1550
Kansas City, KS
913-850-6300
St. Louis, MO 314-729-0125
Dallas, TX 214-371-7777
Fort Worth, TX
817-378-0600
Abilene, TX 325-692-6334 Waco, TX 254-261-1370
Amarillo, TX 806-373-2826
Lubbock, TX 806-745-2112
Odessa, TX 432-333-7000
www.mgxequipment.com
www.kirby-smith.com Baltimore, MD 443-399-7100
Baton Rouge, LA 225-251-7500
Belle Chasse, LA 504-394-7400
Billings, MT 406-698-6768 Birmingham, AL 205-661-1323 Dallas, TX 972-986-0910
Houston, TX
713-433-6411
Norfolk, VA
757-935-4300
Phoenix, AZ
602-232-0660
Salt Lake City, UT 801-297-8500
Winston-Salem, NC 336-582-7400
www.hoffmanequip.com
Corporate Headquarters Piscataway, NJ 732-752-3600
South Jersey Deptford, NJ 856-227-6400 Long Island Medford, NY 631-207-2900
Mid-Hudson Valley Marlboro, NY 845-236-3000
New York City Bronx, NY 718-822-1180
www.stephensonequipment.com
Corporate Headquarters Harrisburg, PA Harrisburg, PA 800-325-6455 Pittsburgh, PA McDonald, PA 800-692-7600 Philadelphia, PA Prospect, PA 800-220-4033
Wilkes-Barre, PA Pittston, PA 866-667-6756 ALT Sales Corp. Richfield, OH 330-659-2100
Dawes Rigging & Crane Rental Elk Mound, WI 800-943-2277
Kaukauna, WI 800-236-8630
Altaequipment.com
18405 115th Avenue Orland Park, IL 60467 877-399-6430
420 Nolen Drive South Elgin, IL 60177 877-399-6430
613 E Stevenson Road Ottawa, IL 61350 815-587-7610
1035 Wylie Drive Bloomington, IL 61705 888-693-2271
480 Blaine Street Gary, IN 46406 219-240-0268
coastlinecd.com
325 N. 5th Street, Bldg. A Sacramento, CA 95811 916-440-8090
Santa Ana, CA 714-265-6550
Las Vegas, NV 702-399-2700
Meridian, ID 208-888-3337
smequipment.com
14925 South Main Street Houston, TX 77035 713-721-7070
11618 C.F. Hawn Frwy Dallas, TX 75253 214-391-4000
2290 FM 1516 North, Lot 4 San Antonio, TX 78109 210-629-0400
255 S Navigation Blvd, Bldg. B Corpus Christi, TX 78405 361-289-2782
1001 West 3rd Street Big Spring, TX 79720 432-517-4378
9477 North Ridgeway Tulsa, OK 74131 918-224-2000 Sales Office Oklahoma City, OK 405-639-8226
exactcrane.com
Serving Ohio, Michigan, W. Pennsylvania, Kentucky 28985 Ambina Drive Solon, OH 44139 440-349-1999
2728 Rev. Abraham Woods Jr. Blvd. Birmingham, AL 35203 205-278-5438
5215 Wills Road Mobile, AL 36582 251-679-0090
3090 State Hwy 20 Decatur, AL 35601 256-936-5438
empirecrane.com
7021 Performance Drive N. Syracuse, NY 13212 800-342-7575
68 Industrial Blvd. Hanson, MA 02341 800-342-7575
9 Finderne Avenue, Ste 7 Bridgewater, NJ 08807 908-203-0400 craneworks.com
STEPHENSON EQUIPMENT, INC.
www.stephensonequipment.com
Philadelphia, PA
800/220-4033
Harrisburg, PA 800/325-6455
Wilkes-Barre, PA
866/667-6756
Pittsburgh, PA 800/692-7600
Syracuse, NY 800/368-6455
Albany, NY 518/357-2200
KIRBY-SMITH MACHINERY INC.
www.kirby-smith.com
Oklahoma City, OK 405/495-7820
Tulsa, OK 918/438-1700
McAlester, OK 918/310-1550
Kansas City, KS 913/850-6300
St. Louis, MO 314/729-0125
RING POWER CRANE
www.ringpowercrane.com
St. Augustine, FL 904/494-1219
Pompano Beach, FL 954/977-5010
Orlando, FL 407/855-6195
Tampa, FL 813/671-3700
Union City, GA 770/774-7300
Concord, NC
704/795-3636
Aiken, SC 843/818-1954
SHAWMUT EQUIPMENT COMPANY, INC.
www.shawmutequipment.com
20 Tolland Turnpike Manchester, CT 06042 800/829-4161
136 Eastman St. South Easton, MA 02375 877/526-9213
SHAWMUT EQUIPMENT OF CANADA, INC.
318 Park Rd. Elmsdale, NS B2S 0G2 902/883-7450
MGX EQUIPMENT SERVICES, LLC www.mgxequipment.com
Baltimore, MD 443/399-7100
Baton Rouge, LA 225/251-7500
Belle Chasse, LA 504/394-7400
Billings, MT 406/698-6768
Birmingham, AL 205/661-1323
Dallas, TX 972/986-0910
Denver, CO 720/864-9842
Houston, TX 713/433-6411
Norfolk, VA 757/935-4300
Phoenix, AZ 602/232-0660
Salt Lake City, UT 801/297-8500
Winston-Salem, NC 336/582-7400
ROAD MACHINERY & SUPPLIES CO.
www.rmsequipment.com
314 Garfield Avenue Duluth, MN 55802 218/727-8611
315 Hoover Road N. Virginia, MN 55792 218/741-9011
WESTERN PACIFIC CRANE & EQUIPMENT
www.wpcrane.com
8600 Calabash Ave. Fontana, CA 92335 562/286-6618
1500 Madruga Road Lathrop, CA 95330 855/927-2637
275 W. Larch Road Tracy, CA 95304 209/597-3824
3521 Alken Street Bakersfield, CA 93308 855/927-2637
19602 60th Avenue NE Arlington, WA 98223 253/254-7950
91-210 Kalaeloa Blvd. Kapolei, HI 96707 808/682-7263
10680 NW 289th Place, Bldg A North Plains, OR 97133 971/202-4002
6720 Arctic Blvd. Anchorage, AK 99518 855/342-7263
HAYDEN-MURPHY EQUIPMENT COMPANY
www.hayden-murphy.com
9301 E. Bloomington Freeway Minneapolis, MN 55420 952/884-2301 800/352-2757
New Jersey
Headquarters 300 S. Randolphville Rd. Piscataway, NJ 08854
732/752-3600
South Jersey 1330 Hurffville Rd. Deptford, NJ 08096 856/227-6400 New York 1144 Zerega Ave. Bronx, NY 10462 718/822-1180
Valley 1440 Route 9W Marlboro, NY 12542 845/236-3000 Long Island 22 Peconic Ave. Medford, NY 11763 631/207-2900
Pennsylvania Philadelphia Metro Area 120 Gordon Dr. Lionville, PA 19341 610/363-9200