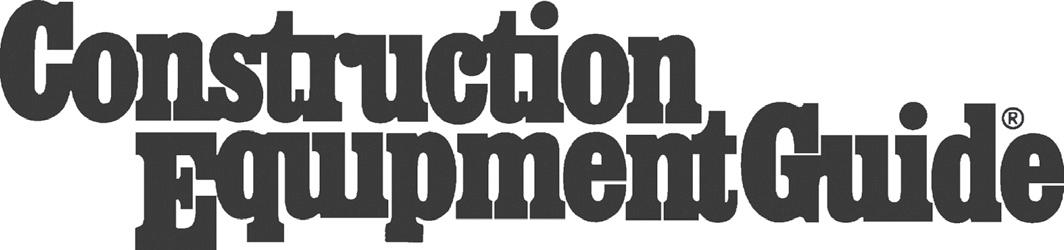
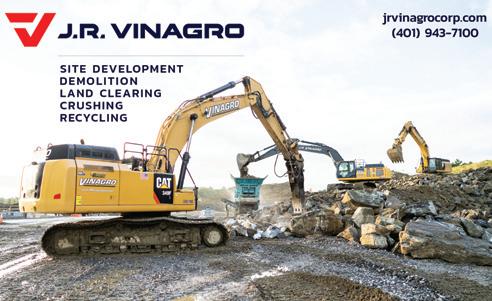
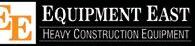
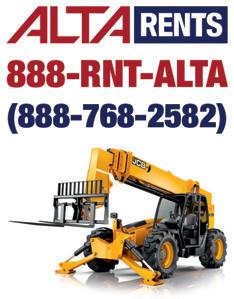




In the rolling hills of Chelsea, Vt., Ben Canonica has built more than just a construction company. He has cultivated a life story rooted in hard work, ingenuity and a deep respect for nature and tradition. Canonica Landworks, the business he founded, is a reflection of this journey — a blend of modern machinery and old-world values.
Before he was a business owner, Canonica was a farmhand, immersed in the gritty reality of agricultural life.
“After college, I worked on a bunch of farms and got into working with draft horses,” he said. “There’s something
incredibly rewarding about working with these animals. You train them, and they train you.”
It wasn’t just a job; it was a way of life that shaped his character. Draft horse logging — an age-old practice of using horses to haul timber — was both a novelty and a necessity for Canonica. It offered a low-impact alternative to modern logging equipment and created a bond between man and animal that no machine could replicate.
Killington, Vt.’s largest ski resort has seen a lot of recent changes. Just last September, the resort was sold for an undisclosed sum to a group of private investors, many with local ties.
Prior to that, in 2023, Great Gulf, a Canadian developer, paid $43 million to purchase 1,095 acres of land, including land and development rights at the base of the Killington mountain with hopes to do what many other developers have tried and failed to do — build a ski village in Killington with new condominiums, homes, shops, restaurants and what Great Gulf is calling the largest “ski beach” in the eastern United States.
The proposed mountain village that Great Gulf currently calls “LiveKillington” will center on 45 acres around the Snow Shed and Rams Head base areas. Great Gulf Killington expects to release finalized designs and begin the permit process later this year.
But the idea of a ski village at Killington has been around for decades, according to a Dec. 31 report from Vermont Public Radio.
Even Preston Smith, who opened Killington in the late 1950s, had some village designs made in the 1960s. Over the years, however, all the various plans ended up falling
SENNEBOGEN, in kee philosophy to maxim created UPTIME Kits
eping with their mize uptime, has Whether you are a service technician i road, these kits have need for every service and PM task in one p created to save you t Managing hundreds o parts, from belts and and special tools bec single part number to n-house or on the everything you e, maintenance place. They were ime and money. of related service d nuts to O-Rings omes easy with a o order and stock
They are:
• Easy to order and ea t d t stock asy to s l
components and too
• Ideal for stocking se and trucks
Choose from the follo
• Central lubrication
• Preventive mainte
• O-Ring kits
• Electrical service k
• Hydraulic service k And the best thing is in stock and ready to built to match your m and series. Count on in-house. For more in UPTIME Kits, scan th s that these kits, go, are custommachine model SENNEBOGEN nformation on he QR code.
Hydraulic service k :kits shops ols ervice owing kits system kits nance service kits its kits
NO North our in parts com with customers maxim commitment h about more Read ontract Demolition C st in parts repair the have virtu and I machine another in If back. to front every come t a have They echnician machine, wntim warehouse. American ready-to-ship of inventories plete for uptime izes aftersale Machine” he “Beyond our ow , Bloomfield Hills, MI or quickly. back unit the g I k they Since do no lose ally bring just [they] situation, a have I over go to month a once through wntime… ock. get theSENNEBOGEN
Since planning and public outreach began in 2017, the voter-approved $28 million Winooski Main Street Revitalization Project, just north of Burlington, Vt., successfully completed its first construction season on Dec. 17 after getting under way back in April.
With work paused until spring 2025, the detour on Weaver Street has been taken down and two-way traffic is restored on Main Street after pavement and line striping were installed, making travel and parking in the area easier to navigate over the winter.
Crews from Wilton, N.Y.-based Kubricky-Jointa Lime LLC were able to get a sizable amount of work done in 2024, including replacing a majority of the town’s 100-year-old water and sewer lines, upgrading gas lines and stormwater systems, installing conduit duct banks and beginning reconstruction of the Main Street roadway between Spring Street and the railroad bridge near Maple Street.
A news release on the city’s website noted that Winooski’s project staff also were kept busy working all last summer on the effort.
“We appreciate the contractors and construction crew members whose efforts led to the successful, on-time, and under-budget
completion of this labor-intensive phase,” the press release noted. “We also appreciate the public information team which assists the city with all important communication efforts.”
Hopes are that the Winooski Main Street Revitalization project will be wrapped up over the 2026 summer season.
In the meantime, independent utility work will continue to occur periodically in the project area over the next few months, according to the city, but will have little to no impact on traffic.
When major construction restarts following the end of the cold, winter months, the focus will be on reconstructing Main Street itself and adding sidewalks, curbs, streetlights and landscaping.
Additionally, crews also will complete upgrades to the water and sewer lines between Tigan Street and the Winooski/Colchester town line, as well as stormwater systems and conduits in the northern half of the project area.
The city promised to share project updates prior to the beginning of next year’s construction, and residents and visitors are
encouraged to sign up for these updates on Winooski’s municipal website.
“The city of Winooski sincerely thanks our businesses, residents and visitors for your patience and understanding while this critical municipal infrastructure project continues,” said City Manager Elaine Wang. “While we all look forward to the long-term benefits, we know that the short-term disruption has been difficult for many.”
Wang noted that Winooski is planning to coordinate with marketing specialists to launch a campaign this winter, “informed by many people, including our business community and local stakeholders.”
“The city, downtown Winooski and the Winooski Working Communities Challenge Initiative held over 30 meetings with financial institutions, government agencies, and business counseling providers to explore options for loans, grants, donations and other support,” she explained. “Input was also gathered from [other Vermont] communities with similar projects, including Middlebury, Brandon and Burlington.
“You can see [online] what we’d like the marketing firm to do by viewing the request for proposals. Thank you to the Vermont Community Foundation for the $25,000 grant to support this work,” Wang said.
Plans are still under way to construct a $4.13 billion sustainable aviation fuel facility at the former Loring Air Force Base in Limestone, Maine, according to its developers.
In 2022, Washington, D.C.-based DG Fuels announced its intentions to build on 1,240 acres of property at the Loring Commerce Center, creating 2,300 jobs during construction and 650 jobs once production begins, reported The County, an online news hub of Maine’s Aroostook County.
Loring was one of two locations, including one in Louisiana, where DG Fuels leaders said they wanted to produce zero to low carbon jet fuel for airports across the United States.
The Maine aviation fuel facility is one of several large projects expected to revive economic development at the Commerce Center, including a more than $55 million potato chip plant projected to bring 75 initial jobs to the region, and other aerospace and technology ventures.
DG Fuels has since announced plans for other facilities in Moorehead, Minn., and in Phelps County, Neb., but remains committed to getting Loring’s plant up and running, noted company CEO Michael Darcy.
“[Loring] is part of an overall strategic plan to move the needle on sustainable aviation fuel,” he explained Nov. 15.
The company currently expects to break ground on the Loring facility in 2026, Darcy said, with construction expected to take close to five years. It will last a little longer because DG Fuels has chosen to go with a stick-built model rather than the modular process that will occur in Louisiana and at other sites.
A modular process would entail workers hauling large, fabricated building materials to the construction site, but no such fabrication facility exists close enough to Loring, Darcy explained. That means fabrication will need to occur on site, which will add more time to the building effort.
“It wouldn’t be feasible to haul 500 tons of modular materials up and down the roads in northern Maine,” he said.
DG Fuels is counting on a renewed interest in environmentally sustainable products as it looks to build large-scale production facilities across the United States.
To that end, the company’s large invest-
ment in the Loring facility will include reviving an underground pipeline that once transported jet fuel from the Maine coastal town of Searsport to Loring Air Force Base. If successful, DG Fuels would use the pipeline to send 33,500 barrels, equivalent to 557,500 gal. of jet fuel, from Loring to Searsport daily for shipment to airports along the northeastern United States.
Additionally, DG Fuels expects to produce 190 million gal. of jet fuel at Loring every year using 1.7 million tons of wood biomass that would be transferred to the plant via local rail lines, and then passed throughout the Loring facility, Darcy said. Six biomass gasifiers on site would use heat, steam, and oxygen to convert biomass to hydrogen without needing combustion.
“On the outside, it will look a lot like a refinery,” he told The County. “[The facility] will be a series of industrial buildings with a series of pipes going from one thing to another.”
Recent investigations of harmful PFAS, also known as “forever chemicals” near Loring’s vacant airport properties have not posed problems for DG Fuels’ project, the company said. To avoid potential contamination, DG Fuels decided to move its
planned facility from its original 30 acres to another 30-acre plot farther from the airport, noted Darcy.
“We’ve been working with the Air Force on this and it’s been made clear that any [PFAS] remediation they’ll need to do won’t interfere with our ability to operate,” he elaborated.
DG Fuels also is partnering with Green 4 Maine, which currently owns 450 acres at Loring but not the DG Fuels property, to house construction employees at 750 renovated apartment units nearby.
Minnesota, along with Maine and Nebraska, are among 10 locations DG Fuels has had its eyes on for new facilities, according to Twin Cities Business. Construction there is expected to last four years, with production starting around 2030.
The company’s $5 billion investment in the Minnesota production plant is designed to employ 650 people and produce 193 million gallons of sustainable fuel every year. And in August, DG Fuels stated that it was looking to build the proposed Nebraska facility with the same price tag, fuel production capacity, and timeframe as the Minnesota plant.
A new year brings a newly renovated section of Copley Square Park in Boston. Mayor Michelle Wu’s office had earlier announced that a portion of the downtown park would reopen Jan. 1 in the northeast triangle between Boylston Street and Trinity Church after more than a year of work.
The rest of the project is still undergoing construction with the city spending about $16.9 million to make the park more enticing and accessible for more visitors.
The newly unveiled section of Copley Square has been shuttered for renovations that started in July 2023. The remainder of the park is slated to reopen later in the winter and spring of this year, according to the mayor’s news release.
WES Construction Corp. in nearby Halifax, Mass., is the general contractor working on the park’s upgrades.
“Copley Square is one of the most iconic parks in Boston, offering vibrancy and open space in an area that welcomes visitors and residents alike,” Wu said. “We’re excited to ring in the New Year by opening a newly renovated piece of this historic park, with the rest of the park’s re-opening to follow soon after.”
City of Boston map
The improvements to Copley Square Park include renovations to the park’s fountain; the addition of shaded groves with seating around the fountain; a raised grove that protects trees; seating and shading at the park’s bus stop; and upgrades to the plaza connecting Dartmouth Street and the Boston Public Library’s McKim Building, the city’s project website noted.
The improvements include renovations to the park’s fountain, the addition of shaded groves with seating around the fountain, a raised grove that protects trees, seating and shading at the park’s bus stop, and upgrades to the plaza connecting Dartmouth Street and the Boston Public Library’s McKim Building, the city’s project website noted. MassLive.com reported that since November, work has paused on the fountain exterior to focus on the plaza and the raised grove areas, which are scheduled to open later this month or in February. Additionally, the area with the fountain is due to open in June.
Copley Square Park’s tortoise and hare statues also have been placed back in the area.
Last year, city officials moved the First Night Boston celebration for New Year’s Eve 2023 from Copley Square Park to City Hall Plaza during the renovations.
Massachusetts just received some federal money that will help protect wildlife from being hit by cars.
The U.S. Department of Transportation’s
Federal Highway Administration (FHWA) announced a $1.7 million grant award to the Massachusetts Department of Transportation (MassDOT) “to fund pre-construction activities for a wildlife crossing project along the Appalachian Trail over Interstate 90 in the western part of the state,” according to a news release.
The Bay State is one of 16 grant recipients to receive funding for wildlife crossing projects nationwide.
The rest of the project is still undergoing construction with the city spending about $16.9 million to make the park more enticing.
“Too many Americans are injured or killed each year in crashes involving cars and wildlife, especially in rural areas — which is why our department created the first-ever program dedicated to crossings that make roads and highways safer for both humans and wildlife,” Transportation Secretary Pete Buttigieg said in a written statement.
“With funding made possible by the Bipartisan Infrastructure Law, the projects moving forward in 16 states will reduce collisions between drivers and wildlife, create places for wildlife to safely move over and under highways, and help preserve American life and property,” he added.
The $1.7 million grant awarded to MassDOT includes replacing an existing
bridge crossing near the small town of Becket in an area with a high number of vehicle collisions with deer, according to the USDOT.
Separate and distinct areas for wildlife, pedestrians and hikers will be offered as part of the I-90 Mass Pike Appalachian Trail Pedestrian-Wildlife Shared Use Crossing project and include fencing to help funnel wildlife to the crossings, the Fall River Herald News reported Jan. 1.
A federal study found that wildlife crossing structures with fencing have been shown to reduce motorist collisions involving wildlife by up to 97 percent.
Nationwide, the USDOT said that there are more than one million crashes involving wildlife each year in the United States, and collisions with large animals result in about
200 human deaths and 26,000 injuries annually. These accidents also cost the public more than $10 billion a year.
Funding for the construction of the animal crossings in western Massachusetts is available through the Wildlife Crossings Pilot Program, a new grant program that was created by President Biden’s 2021 Bipartisan Infrastructure Law. “The purpose of the Wildlife Crossings Pilot Program is to improve safety for motorists and wildlife by reducing vehicle collisions with wildlife while also improving habitat connectivity and supporting the survival of threatened or endangered species,” noted a USDOT news release.
Additionally, the grant supports studies and “projects that construct wildlife crossings over and below busy roads, add fencing to direct animals to the crossings and monitor performance of crossing systems.”
Overall, the law makes a total of $350 million available over five years to the different states with crossing projects. Oregon, North Carolina and Idaho have received the largest grants, with each being over $20 million.
When you need to move dirt and rock quickly, you need our R 936 crawler excavator. Advanced electronics let drive components work together efficiently to save fuel. Sensor-guided controls give you speed, precision and power. And robust cast steel components stand up to the toughest environments. It's all built to last with exclusive Liebherr components.
We haven't compromised on anything; why should you?
Life took a turn when Canonica and his wife purchased a raw piece of land in Vermont.
“We bought the property and needed to do a lot of site work,” Canonica said.
Rather than hiring out, he decided to handle the tasks himself, renting small equipment and learning as he went. What began as a personal project quickly grew into a fledgling business.
Since age 12, Canonica had a landscaping business that he ran through high school, doing various projects with a farm tractor that had a backhoe attachment, before buying his first piece of equipment, a Case 480 backhoe. During this time, he also worked for other landscapers and contractors learning necessary skills to build on.
During college, he spent a summer working for Modern Continental on the Big Dig in Boston, a great experience in knowing that the city was not where he wanted to spend my time, he said.
“I spent another summer working for the USFWS in northern New York rebuilding wet lands in old agriculture fields, and this is where I began to realize I could combine my education with my enjoyment for running equipment.”
Immediately after college, he was introduced to working with draft horses on a farm in Colorado, where he did all aspects of farming with the horses.
“With college loans soon coming due, I realized I needed some steady income to settle my debts while I made a plan for my future endeavors,” he said. “My high school was getting renovated and they were looking for heavy equipment operators. I had very little experience but did have the necessary hoisting license to run equipment in Massachusetts. I learned a lot doing all the aspects of site work on numerous school renovations, and then worked for a few contractors doing residential site work, before moving to Vermont.”
“I enjoyed running equipment and found it was a reasonable way to make a living,” Canonica said.
Slowly but steadily, he expanded his offerings, from trail work to excavation projects, carving out a niche in the local
In floodplain restoration, Canonica advocates for giving rivers room to breathe. Removing outdated berms and dams has become a critical part of his work, allowing rivers to flow naturally and mitigate future flood risks.
community.
Despite the shift from draft horses to heavy machinery, Canonica’s roots were never far from his mind. His company logo prominently features a horseshoe, a nod to the early days when his horses were his partners in labor.
“My wife asked if I wanted to keep the horseshoe in the logo since I wasn’t using horses as much anymore,” he said. “But for me, it’s a symbol of where I started and a way to honor that chapter of my life.
“About a year ago, I had to put my team down,” he added. “I had one mare for 19 years. She wasn’t just an animal; she was a partner. We built our farm together.”
Today, Canonica Landworks thrives as a modern construction company, but its heart remains deeply tied to the land. In the winters, Canonica still turns to low-impact logging, a quiet homage to his beginnings. As for draft horses, he hasn’t ruled them out for the future.
“Maybe at a different time in my life, I’ll have horses again,” he said.
Tropical Storm Irene in 2011 created a turning point for Canonica. The storm’s devastation left rivers altered and banks eroded, calling for urgent and innovative restoration efforts. For Canonica, this wasn’t just a call to action — it was an opportunity to merge his engineering expertise with his love for running heavy equipment.
Canonica equipped his first two excavators with Engcon technology; his approach to equipment is rooted in practicality and vision.
“When I realized how much time I could save with Engcon’s EC oil system, it just clicked,” he said.
The ability to switch between attachments seamlessly
see CANONICA page 16
-Wing to Wing is 120 inches
-The box is 112 inches wide
-The deck is 78 by 78
-Mesh size is ¾ inch
-12 Hp Honda Engine
-Offered in both Black and Red
-6,000 lbs. electric jacks
-Can screen up to 45 yards an hour
-Limited Screens Available!!
-Must pick up in Yarmouth, Maine a family-owned company located in Fort Kent, ME. We take pride in our craftsmanship and look forward to doing business with you! Call the office at (207) 834-5751 to discuss further details!
from page 12
revolutionized his workflow, especially on complex projects like dam removals.
Canonica’s work with river restoration is where his technical skills truly shine. After the immediate chaos of Irene, he began projects that ranged from repairing eroded banks to reconstructing entire miles of river. Using innovative techniques like root wads — large sections of trees embedded in riverbanks — Canonica learned to balance natural and engineered solutions.
“Root wads not only stabilize the banks but also create habitats and reduce downstream energy impacts,” he said.
His approach extends beyond immediate repairs. In floodplain restoration, Canonica advocates for giving rivers room to move. Removing outdated berms and dams has become a critical part of his work, allowing rivers to flow naturally and mitigate future flood risks.
The challenges of environmental work evolve, and so does Canonica’s expertise. From ash borer outbreaks to the maintenance of small-town waterways, his work is as much about preparing for tomorrow as it is about fixing today. For Canonica, every project is a step toward harmony between human needs and the environment.
For Canonica, the Mecalac wasn’t just a purchase; it was an investment in versatility and efficiency. “In the northern states, excavators are often parked for months due to weather,” he said. “But I realized that with the Mecalac, I could run it year-round.”
Canonica’s ingenuity didn’t stop with the Mecalac itself. He developed custom solutions, like cross chains for rubber tracks, to navigate frozen ground and snow — a necessity in Vermont winters. This adaptability extended to his embrace of tilt rotators, devices that further enhance the versatility of excavators. Now, each of his three excavators boasts its own tilt rotator, a testament to his commitment to staying ahead of the curve.
The journey with Mecalac wasn’t without its challenges. The machines were relatively new to the U.S. market, but the collaborative relationship with Lorusso and support from Mecalac’s team, including a factory representative from France, ensured that these hurdles were overcome.
“We worked through a lot of challenges together,” Canonica said. “It’s been a solid relationship.”
Canonica’s first encounter with Mecalac machines came around 2016-2017, a time when its presence in the United States was virtually nonexistent. At the time, Canonica was juggling multiple machines — an excavator, a small forwarder, and occasionally renting skid steers or mini-excavators to fill in the gaps.
When Canonica stumbled upon Mecalac’s 10MCR model, an excavator skid steer hybrid, his curiosity was piqued. It wasn’t just a machine; it was a potential solution to his problem.
“I realized I wouldn’t have to rent a skid steer or a miniexcavator anymore,” Canonica said. “And I wondered if I could even use it as a forwarder for logging.”
This realization set off a cascade of research and conversations, including one with a user in the UK who shared insights about using the 8MCR model with a forestry trailer.
Armed with newfound confidence and a clear vision, Canonica sold his forwarder and invested in the first 10MCR sold in the United States through his equipment dealer: Lorusso Heavy Equipment in Walpole, Mass.
For Canonica, the Mecalac wasn’t just a purchase; it was an investment in versatility and efficiency.
“In the northern states, excavators are often parked for months due to weather,” he said. “But I realized that with the Mecalac, I could run it yearround.”
This year-round utility quickly offset the machine’s premium cost, providing returns far beyond what traditional equipment could offer.
The Mecalac’s ability to adapt to a variety of tasks has been a game-changer for Canonica Landworks. With its compact design, powerful reach and ability to switch seamlessly between roles as a skid steer, excavator and forwarder, the machine proved invaluable for challenging projects. Canonica recounted moments where the Mecalac’s unique capabilities shone, such as grading over a fence or loading a tri-axle truck without moving its tracks.
“It’s even better than just an excavator or skid steer,” he said. “You’re not trapped in a box, and the visibility is fantastic.”
Today, Canonica operates a fleet of Mecalac machines, including the MCR (Mecalac’s mini-excavator hybrid and MWR (Mecalac’s compact wheeled excavator) models, which he describes as indispensable partners in his projects.
“The MCR’s tracks make it perfect for Vermont’s steep and slippery terrain,” he said, “but the MWR’s wheels offer speed and comfort when I need to cover long distances. Each machine plays a specific role, and together, they’re invaluable.”
One of his current projects — a stone arch bridge spanning a picturesque ravine — showcases the utility of this machinery. While the MCR remains stationed at the construction site, stabilizing and navigating the soft ground, the MWR is used to transport materials like concrete blocks and steel beams from a storage yard half a mile away.
“The wheeled machine’s efficiency is unmatched for this kind of task,” Canonica said. “It’s set up to do everything I need and more.”
For Canonica, Landworks is more than a job; it’s a craft. His projects often combine modern engineering with timeless techniques. The stone arch bridge, for example, is being constructed in phases, starting with a temporary steel bridge for access. Once complete, it will stand as a testament to both his vision and the region’s storied traditions.
“We’re blending old-world craftsmanship with modern tools,” Canonica said. “It’s about respecting the land while enhancing it.”
Canonica reflected on the seasonal rhythm of his work. Autumn in Vermont demands preparation, when he is focused on ensuring his equipment and projects are ready for winter. Despite the challenges, it’s clear that Canonica thrives on the complexity of his work.
“I love what I do,” he said. “Every project is a new puzzle, and I’m fortunate to have the tools and support to solve them.” CEG
(All photos courtesy of Canonica Landworks.)
KILLINGTON from page 1
through.
Today, though, despite some hiccups and delays, local officials feel a lot more confident that it is finally going to happen. They point to a combination of town investment and Great Gulf’s plans and corporate portfolio.
The town of Killington has invested some $80 million into improving local infrastructure. Additionally, officials are installing a new municipal water supply system and improving the roads — all to lay the foundation for the high-density development that would be part of a new ski village.
Town and resort officials say there is a lot riding on getting the village plans right, starting with the first phase, which has been designed to include approximately 720 residential units, made up of a mix of ski-in skiout condos, duplexes, and single-family homes, as well as a large new base lodge, and 110,000 sq. ft. of retail and dining space.
Great Gulf Killington CEO Michael Sneyd also noted that his firm plans to develop walking and biking trails, fitness centers, spas and a wooded amphitheater.
In addition, he told Vermont Public that plans call for the creation of an extra-long “ski beach” running over the Killington access road. A ski beach is a flat area of snow that makes it easier for skiers to get around and provides areas to relax and picnic.
Depending on how long the local and state permit process takes, construction on the first phase could begin in 2026.
The previous owner of the land, SP Land Company, did receive Act 250 approval for a ski village they wanted to build on the property. Observers including Jim Haff, the Killington town select board chair and zoning commissioner, believe that may make it easier for Great Gulf to go through the process.
Great Gulf took the older existing village plans and hired Safdie Architects, a Somerville, Mass.-based architectural design firm, to improve upon them.
“And they came back with a new master plan for the village that had half a dozen significant improvements,” Sneyd said in speaking with Vermont Public.
That included shifting Killington Road, having one ski lodge instead of two, building walkways around the pond, and keeping the village retail area car- and bus-free, he added.
Killington town officials were expecting to be well into the local review and permit process by now, but Great Gulf — which is part of the group of investors that purchased the ski resort itself in September — recently announced that they were delaying things for a year.
Mike Solimano, president and general manager of Killington Resort and Pico Mountain, said after looking at Great Gulf’s new base lodge plans, they asked the developer to make the building larger and change some elements. He noted that his group learned a lot building their Peak Lodge and new Killington base lodge.
“This village is going to be around for 100 years. We want to make sure we get it right,” Solimano explained to Vermont Public. “Sometimes when you have architects working on things, you know, they’re working on aesthetics and not really functionality of the lodge. So, I think that’s where a lot of the kind of give and take is, and how operationally is the building working, you know, especially from a food and beverage standpoint.”
Eventually, Sneyd believes Great Gulf Killington can potentially build up to 2,300 residential units with a projected investment of about $3 billion.
“That … construction investment is going to generate 3,800 construction jobs in Vermont over a 25-year period,” he said.
“And then once the village is built in Year 10, the hospitality side takes over the whole property, the management, the rental, the hospitality — and we project 1,500 hospitality jobs. Those would be permanent jobs going forward.”
Finding enough people to build and staff the village — and locate places for them to live — is a big issue under consideration.
Town officials in Killington have already bought a 70-acre piece of land for workforce housing, and once water and sewer are connected, will work with the developer to construct 250 to 350 units made up of a mix of apartments, duplexes and single-family homes.
Sneyd told Vermont Public that he also has met with Rutland, Vt., Mayor Michael Doenges to look at possibly developing worker housing in that city, a 16-mi. drive west from Killington.