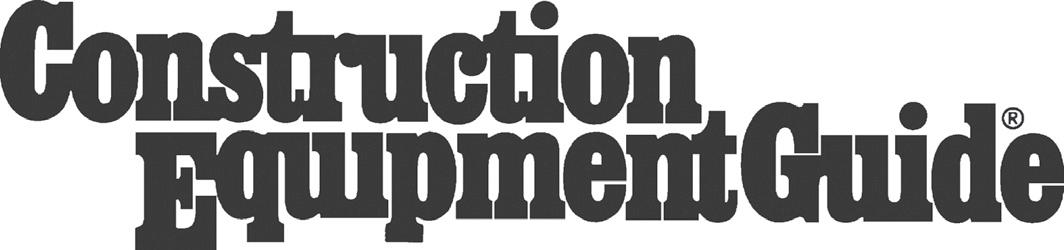
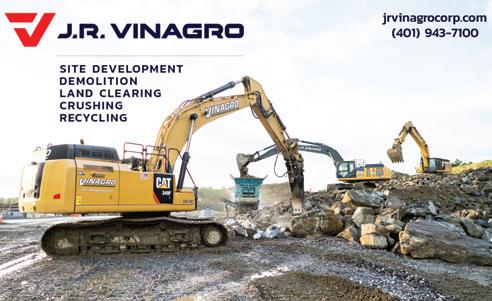
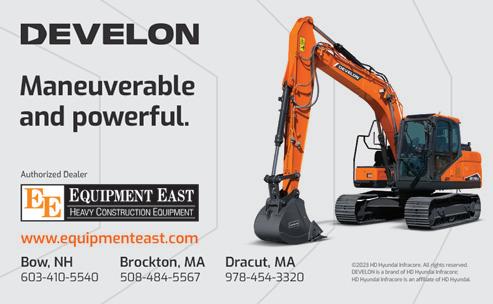
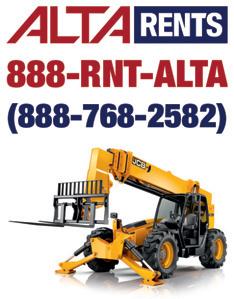
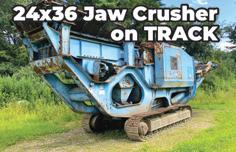
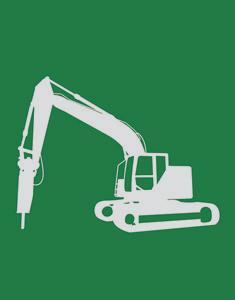
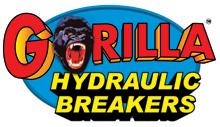



Mizzy Construction, a large site development contractor based in Plainville, Conn., was founded in 1988. But the name goes back a lot farther, to company president Stanley Mierzejewski’s father.
Mierzejewski, who said his last name is “too big to fit on a truck,” chose to use his late father’s nickname as his company’s name.
“His friends all just called him ‘Mizzy’ because Mierzejewski was just too much. I lost my dad when I was six years old, and I named the company after him,” Mierzejewski said.
The company provides a vast array of services, including site clearing, erosion control, drainage, utility installation, excavation, paving, concrete work, paver installation, landscaping and many other services. It prides itself on embracing technology and staying ahead of the curve, which typically translates into lowering the cost of projects during a time when keeping costs under control can be particularly challenging.
The firm has a reputation of being able to confidently tackle major projects and, when needed, to use its vast
resources to solve problems quickly and offer engineering suggestions along the way. Mizzy also prides itself on the expertise of its employees, with each of its project managers being required to have either a bachelor’s degree in construction management or civil engineering. The company has on staff two Connecticut licensed professional engineers. When asked how he got his start in the construction industry, Mierzejewski said, “When I was a kid riding around with my mom in the car, if I saw construction equipment, I made
SENNEBOGEN, in kee philosophy to maxim created UPTIME Kits
n-house or on the everything you e, maintenance place. They were ime and money. of related service d nuts to O-Rings omes easy with a o order and stock
eping with their mize uptime, has Whether you are a service technician i road, these kits have need for every service and PM task in one p created to save you t Managing hundreds o parts, from belts and and special tools bec single part number to
They are:
• Easy to order and ea t d t
components and too
stock asy to s l
• Ideal for stocking se and trucks
Choose from the follo
• Central lubrication
• Preventive mainte
• O-Ring kits
:kits
• Hydraulic
service
• Electrical service k Hydraulic service k
shops ols ervice owing kits system kits nance service kits its kits
k
And the best thing is in stock and ready to built to match your m and series. Count on
s that these kits, go, are custommachine model
SENNEBOGEN
nformation on he QR code.
dow NO
come t a have They echnician machine,
If back. to front every
ontract Demolition C st in parts repair the have virtu and I machine another in
wntim warehouse. American ready-to-ship of inventories plete for uptime izes
they Since do no lose ally
over go to month a once through wntime… ock. get
quickly. back unit the g I k
, Bloomfield Hills, MI or
North our in parts com with customers maxim commitment h about more Read
rain e • T ervic ts • S Par
to
bring just [they] situation, a have I theSENNEBOGEN y-t t act OGEN f tor ained technicians tr ned tec cians
machine” the “beyond ng Cost Total lower and its of life the out
a more Learn 2-6351 ) 29 (800 ongmead ast L E oa er R 1 Shak 25 yle t.ww our to commitment our w bout (800 Berli 1980 28 A 010 , M ow d om omers requipment.c cust 52-4473 ) 3 0 7 in, CT 0603 urnpike 0 Berlin T sennebogeen-na.com/beyond-the--machine
her pull over and let me watch. I had an absolute fascination with construction and construction equipment from as far back as I can remember.
“I got a job with a local construction company right out of high school as a laborer, then advanced into a truck driver & then an equipment operator. At the same time, I went
to college, got my education and with the experience I was getting on the job site, combined with my education, I ended up a project manager. After numerous years of hard work I ultimately ended up being an officer of the company.
“An opportunity came my way when a friend of mine who was associated with the telephone company presented to me the
chance to do some of their construction work. To get started, I rented a mid-sized dozer and a 200- and 270-sized excavator, along with a wheel loader and dirt roller. Shortly after starting to work for the telephone company, we landed a project building a big subdivision. So, between the two of them we were off to a good start.
“Business was booming for the phone
company. They were diversifying into the wireless market and there was a high demand for the construction of cell towers. Having a steady flow of business from a good anchor account put us in a position to expand aggressively into other markets. It wasn’t long before, we were doing a lot of commercial excavation and foundation work as well as utility installations … really any type of project that involved excavation or site work.”
Approximately 10 years after the founding of Mizzy Construction, Mierzejewski found himself at a turning point. He had been taking a conservative approach to the management of his firm, being very careful not to grow too fast and not shying away from turning away work if he felt that it would press them too hard to accomplish the projects. Around the year 2000, he decided to change direction.
“We actively started to pursue new business. I hired new people and made it a point to hire good management level people whenever possible. I wanted to get away from being in the position that I had to be hands-on with every project we were involved in, and instead have quality people on staff to handle the projects and letting me get more involved in the big picture. As an example, right now we have four project
see MIZZY page 8
managers. That gives us a great deal of flexibility and the opportunity to grow in different directions.”
Mizzy Construction is currently involved in numerous site development projects throughout the state of Connecticut. The company also does a fair amount of business with local municipalities, CTDOT, and for major utility companies throughout the state.
“We have specialized crews to do work for the area utility companies. We currently have approximately 85 employees. Our equipment inventory is extensive. We have over 40 excavators just to give you an example, not to mention all of the other categories of equipment that we have.”
Mierzejewski has a very traditional approach to equipment ownership. He very rarely rents equipment, and he typically does not want to purchase a piece of equipment that’s been owned or operated by someone else. When he buys, it is typically a machine with zero hours.
“We just bought two new machines to replace two machines that had 20,000 and 18,000 hours on them, respectively. The expenditures for maintenance on buying used machines versus what a brand-new machine costs and the reduced amount of maintenance that you put into a new machine, there is no savings buying used. Buy new machines, properly maintain them and run them until there is very little life in them, that is an approach that just works for us.”
Over the years Mierzejewski has converted a significant amount of his fleet to John Deere machines.
“As you start increasing your investment in a dealership, relationships also come into play. Originally, at W.I. Clark [Connecticut’s John Deere dealer], I worked very closely with Ray Tripodina. Ray took great care of us and eventually retired, at which point I started working with Matt LaDuke. It doesn’t seem possible, but that was 15 years ago. That relationship has continued to grow as Matt demonstrated a keen ability to match up the right equipment for our needs, make sure we are getting properly serviced and resolve problems whenever they arise.
“Buying new equipment from a dealership is just about the same experience no matter where you go. It’s what happens afterwards that makes the difference. When the machine goes down, do they understand what that is costing you? How quickly do they return your phone call? Do they walk through your door with the part you need? If they don’t have the part, do they get you another machine to keep you going?
“Those are all the things that Matt has
continued to bring to the table since he became our representative. We’ve worked together so long it’s now beyond just the equipment. We occasionally grab lunch together, but now we [also] go boating and fishing together.
Mierzejewski and his fishing team regularly goes fishing for big fish, shark and tuna. A few years ago, they caught a 559 lb. Tiger shark off the coast of Long Island in
Montauk to bring home the trophy in one of the tournaments they had entered. In fact, in the 12 years they have entered they’ve won it three times.
Mierzejewski may still not be sure if it was the quality of the fishing, the great service or the great machines, but today almost without exception every machine he buys is a John Deere —excavators, haul trucks, loaders, skid steers, backhoes, graders and
dozers.
“There’s no reason for me to look anywhere else. W.I. Clark’s service and parts support was right there every time I needed them. If it can’t be fixed or part can't be found, I’ve got a replacement machine to use until the problem is resolved,” Mierzejewski said.
For more information, visit www.wiclark.com and www.mizzyconstruction.com. CEG
(All photographs in this article are Copyright 2024 Construction Equipment Guide. All Rights Reserved, except where noted.)
Keri Caron has joined Monroe Tractor’s Westborough, Mass., location as an equipment sales representative.
Caron brings a wealth of knowledge with her extensive experience in real estate, trade contracting and her philanthropic work. She will be responsible for selling and supporting Monroe’s full line of Case construction equipment and Case IHagriculture equipment in Massachusetts’ Northern Middlesex County.
“I’m thrilled to be joining Westborough’s team. I look forward to meeting and building strong relationships and assisting customers with our wide selection of equipment,” said Caron.
“We are excited to welcome Keri and her expertise in customer service. I am confident she will approach her role with a consultative and customer-centric mindset. Keri is an effective communicator, trustworthy and eager to meet the needs of our customers,” said Dan Duhn, Westborough branch manager.
The developers of Northeastern University’s new Roux Institute campus on the Portland, Maine, waterfront have released their latest plans to account for sea level rise, storm surge and other impacts from climate change at the site of the former B&M Baked Bean factory.
The existing pier, for example, will be replaced and made higher, Tim Mansfield, an architect with CambridgeSeven in Cambridge, Mass., told the Portland Planning Board Feb. 13.
“The pier itself is elevated to a [12.8-ft.] elevation, which is approximately 3 ft. higher than it is today,” he explained.
“We’re starting to accommodate already for coastal storms.”
The former cannery building will be converted to office space, but the developers acknowledged the first floor of the old factory will be vulnerable to flooding, reported Maine Public Radio, and nonessential services, such as indoor bike storage, will be located there.
The latest plans for the first phase of the project call for a 238,000-sq.-ft. academic building, a parking garage with 625 spaces, and a daycare center that would serve 50 children.
The first blueprints to build the graduate campus and research center began about a year before the Roux Institute in Portland was announced in January 2020, along with a $100 million gift from technology entrepreneur and Maine native David Roux and his wife, Barbara.
They joined with Boston’s Northeastern University to ignite their vision of a Portland-based hub to educate generations of talent for the digital and life sciences sectors and create innovative ideas through research.
The university noted in an earlier news release that the integrated Roux Institute campus plan would include a variety of buildings to be developed in phases as the center grows. Among the buildings are academic spaces for learning and research, new business and startup incubation space, and collaborative facilities for Roux’s partners.
In response to demand, the development will also include housing to support Roux’s students, faculty and staff.
“The people who are working in the institute — the learners, the partners, the researchers and the entrepreneurs — need a campus that’s integrated and that can meet their needs for constant collaboration and convenience,” Chris Mallett, Roux’s chief administrative officer, told the Portland Planning Board in 2022. “That’s how we believe change and innovation happens: By connecting people with one another.
“We’re excited about the plan because we think it gives us the best prospects to do just that — and also to attract experts from around the world to join us at the Roux Institute campus and participate in the process.”
Mansfield explained in 2022 that the proposed campus is designed around four principles:
• A connection to the waterfront, Portland, and the world. The plans include three public acres of waterfront parkland and a restoration of the historic bean factory, which ended production in 2021. Land on the edge of the campus has been reserved for a potential freeway exit in case the growth of the institute results in traffic that exceeds expectations.
• Places to gather. The center of the campus will be a pedestrian zone with a bike path that circles the site, while other features include a public cafe, seating along the waterfront and a dock. The two tallest buildings, which have been relocated to the center of campus, will serve as hotel and campus housing (the latter of which may be available for rent to the general public based on student demand).
• A sustainable and resilient campus. Roux has developed a sustainable charter that includes seawater heat exchange, green roofs, and geothermal energy.
• An integrated landscape. The campus will make use of stone, granite, brick, copper and other materials that have traditionally defined Maine’s largest city.
“We’re reclaiming a wasteland of tarmac and industrial buildings,” Mansfield added. “This is an opportunity to create a landscape that’s welcome to all, that supports the diversity of activities, and feels like it’s part of Portland.”
In addition, much of the site will be restored to its natural state while the rest of the property is geared to driving the institute’s mission to empower the tech industry in Maine.
Roux Institute is currently housed 2 mi. away from the new site on the shores of Portland’s Casco Bay in 44,000 sq. ft. of space operated by WEX, a founding corporate partner of the research center.
The Institute for Digital Engineering and Life Sciences (IDEALS), a nonprofit formed to create a permanent site for the Roux, announced in 2021 that it had purchased the new waterfront property. IDEALS will finance and manage construction of the new campus before ownership is transferred to Northeastern.
Although the majority of residents in the area are supportive of the new project, neighbors close to the proposed site of the Roux campus told Maine Public Radio that they are concerned about traffic and parking in the area, particularly when school lets out in the afternoons.
The station learned from city planners and developers that the Maine Department of Transportation (MaineDOT) will conduct a traffic study of the area around the proposed campus and will consider a possible off-ramp from Interstate 295 to the site.
The new plans also call for a METRO bus stop on campus as well as a new park, and pedestrian and bike pathways along the waterfront.
“Connection to the city’s most prominent trails is a massive asset in the Roux campus, and as a runner, a stroller pusher, and a paddler, I’m just super excited for the access to the perimeter trail,” said Nick Littlefield, one of several Portland residents who applauded the plans for public pedestrian access.
Roux Institute’s developers also said they are considering off-site park-and-ride options with a shuttle to and from the campus.
The Portland Planning Board is expected to host additional workshops on the Roux Institute’s proposals, Maine Public Radio noted Feb. 14.
Two months after a propane truck explosion damaged a Vermont Highway 14 bridge near the town of Irasburg early last December, federal agencies have now stepped up to help fund its repairs.
U.S. Transportation Secretary Pete Buttigieg announced Feb. 13 that the Federal Highway Administration (FHWA) made $1.2 million in “quick release” emergency relief funding immediately available to Vermont to get a new bridge built as fast as possible. Vt. 14 is an important north-south route in the northern part of the state.
“We know how important this bridge is to the people of Vermont,” Buttigieg said in a news release. “The BidenHarris administration is making these federal emergency funds available to help restore travel on this critical route as quickly and safely as possible.”
Officials with the Vermont Agency of Transportation (VTrans) told MyChamplainValley.com that they are pleased to receive the grant which will be used to pay for more than a third of the replacement project, slated to cost about $3 million.
With the federal money in hand, VTrans officials said the bridge construction is now expected to be completed, with cars driving across the structure, in mid to late April.
Early on Dec. 4, a propane truck crashed into the Vt. 14 bridge before landing in the Black River and bursting into flames. The driver was okay, but the bridge itself was not, as firefighters were unable to extinguish the blaze until the evening of Dec. 5. During that time, and fed by the tanker’s propane, the fire slowly ate away at the structure until it was totally destroyed.
Since then, traffic has been rerouted to Vt. 58 and U.S. Highway 5, adding about a 4-mi. detour between Irasburg and Coventry as well as other nearby towns in Vermont’s Northern Kingdom.
Crews from VTrans had already gotten to work to repair the bridge before the department even knew if it would receive relief money from the FHWA.
“There wasn’t a whole lot we could salvage from the previous bridge, so this is a brand-new bridge,” noted Jeremy Reed, the state agency’s chief engineer. “We’re certainly not in any way slow walking this; rather, we’ve done everything we can to expedite the reconstruction of this bridge.”
He added that the quick-release funds are certainly appreciated because it means “we don’t have to encumber other [state] funds while we wait for the construction to conclude.”
“Vermont residents and businesses are experiencing disruptions to their daily lives that often result in additional cost and delay,” noted FHWA Administrator Shailen Bhatt. “It’s imperative that we get this bridge back up and running again soon.”
FHWA’s Emergency Relief program provides funding to states, territories, tribes and federal land management agencies for highways and bridges damaged by natural disasters or catastrophic external events. Its “quick release” emergency funds are an initial installment of monies to help restore essential transportation.
Additional funds needed to repair the bridge damage in Vermont will continue to be supported by the federal agency’s program, FHWA officials said.