
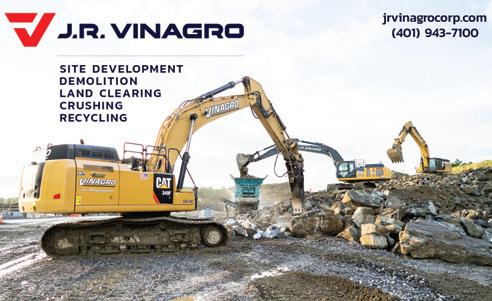
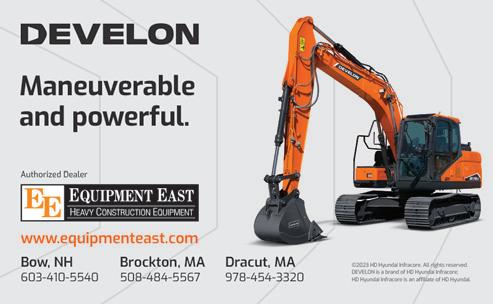


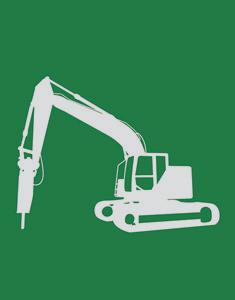

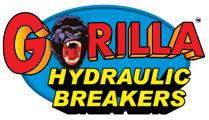


Cole Landscaping is a large residential and commercial landscaping firm headquartered in Rowley, Mass., which serves the north shore region. The projects that it tackles for residential customers include property management; lawn care; plant health care; landscape design; hardscapes; outdoor kitchens; pool and water features; and irrigation.
For commercial customers it is primarily called upon to do landscape design and build; property maintenance; irrigation; and snow removal.
“We look at each customer as a lifelong commitment and relationship,” said Greg Cole, president of Cole
Amtrak will soon begin construction of a new, $1.3 billion Connecticut River Bridge between the towns of Old Saybrook and Old Lyme following the award of a design-bid-build contract to
O&G/Tutor Perini, a joint venture of two major construction firms.
The passenger rail company’s agreement with the building team comes on the heels of recent permit approvals from
SENNEBOGEN, in kee philosophy to maxim created UPTIME Kits
eping with their mize uptime, has Whether you are a service technician i road, these kits have need for every service and PM task in one p created to save you t Managing hundreds o parts, from belts and and special tools bec single part number to n-house or on the everything you e, maintenance place. They were ime and money. of related service d nuts to O-Rings omes easy with a o order and stock
They are:
• Easy to order and ea t d t stock asy to s l
components and too
• Ideal for stocking se and trucks
Choose from the follo
• Central lubrication
• Preventive mainte
• O-Ring kits
• Electrical service k
• Hydraulic service k And the best thing is in stock and ready to built to match your m and series. Count on in-house. For more in UPTIME Kits, scan th s that these kits, go, are custommachine model SENNEBOGEN nformation on he QR code.
Hydraulic service k :kits shops ols ervice owing kits system kits nance service kits its kits
NO North our in parts com with customers maxim commitment h about more Read ontract Demolition C st in parts repair the have virtu and I machine another in If back. to front every come t a have They echnician machine, wntim warehouse. American ready-to-ship of inventories plete for uptime izes aftersale Machine” he “Beyond our ow , Bloomfield Hills, MI or quickly. back unit the g I k they Since do no lose ally bring just [they] situation, a have I over go to month a once through wntime… ock. get theSENNEBOGEN
A year ago, as historic levels of rain fell and rivers jumped their banks in New England, Vermont’s dams felt the full force of the flooding.
At least five small dams failed entirely. Around 50 dams, at least, sustained damage requiring repairs by the state’s Agency of Natural Resources. And at the state’s key flood control dams — Waterbury, East Barre, and Wrightsville — water levels reached record or nearrecord highs, alarming residents who lived downstream.
For Vermonters residing along waterways or beneath dams, July 2023’s historic flooding drew attention to the state’s network of hundreds of dams, many of which are old, decaying or forgotten.
The disaster helped spark a sweeping reappraisal of how the state manages its waterways and the structures built on them.
Now, new legislation as well as an influx of state funding and a suite of new rules are slated to dramatically reshape how Vermont oversees its dams.
“It’s a big deal,” Neil Kamman, the director of the Vermont Department of Environmental Conservation’s (DEC) Water Investment Division, told VTDigger. “The dam safety program is evolving significantly, [and] in a good direction.”
VTDigger noted on July 1 that last year at this time, as torrential rainfall soaked Vermont, water rose precipitously behind the Waterbury, Wrightsville and East Barre dams, the state’s trio of Winooski River flood control barriers.
On July 11, 2023, Montpelier City Manager Bill Fraser took to Facebook to warn, “If water [at Wrightsville] exceeds capacity, the first spillway will release water into the North Branch River. This has never happened since the dam was built so there is no precedent for potential damage. There would be a large amount of water coming into Montpelier which would drastically add to the existing flood damage.”
State officials scrambled to get personnel to monitor the structures, and despite several false alarms and high anxiety in downstream communities, the dams held fast.
“At the end of the day, we’re actually pretty fortunate with how everything performed,” Ben Green, an engineer and section chief for the DEC’s dam safety program, said in a recent interview with VTDigger. “But we had probably more close calls than we should have had.”
In the aftermath of the floods, those close calls came into focus.
In the two weeks following the flooding,
state inspectors — as well as dam safety personnel called in from New York and Massachusetts — assessed nearly 400 such structures across the state, Green told lawmakers in presentations last winter.
Inspectors found that five dams — in Woodbury, Wallingford, Peru, Cabot and Washington — were effectively destroyed. Another 50 dams sustained “notable damage,” according to DEC data. In all, Vermont estimated that 57 dams were overtopped by floodwaters.
At the Wrightsville and East Barre dams, officials recorded record-high water levels, with floodwaters rising to within 10 in. of the Wrightsville Dam’s auxiliary spillway. The Waterbury Dam, meanwhile, recorded its fourth-highest water level on record.
Those findings provided state officials with something of a wake-up call, VTDigger noted.
After hearing testimony about the impact of the flood on Vermont’s dams, Sen. Chris Bray, D-Addison, and chair of the Senate Committee on Natural Resources and Energy, thought, “How do we not have this happen again?” he said.
“We are understaffed, and then the weather is more and more violent, making us more and more susceptible” to flooding, Bray told the online news site. “So how do we build a long-term pathway out of here?”
More Funding, Oversight Needed
In Vermont’s 2024 legislative session, that pathway largely took the form of Act 121, a
sweeping law regulating development near waterways, improving wetlands conservation and strengthening dam safety.
State lawmakers added four positions to the dam safety program and made two others permanent, bringing the total number of state dam safety staff from five to nine — a much-needed boost for the program, officials said.
The legislation also will correct what critics say is an inconsistency in Vermont’s dam oversight system. Currently, the state DEC has jurisdiction over approximately 1,000 dams, while another 21 hydropower dams fall under the purview of the state Public Utility Commission (PUC).
Dozens of others are regulated by federal agencies, including the Federal Energy Regulatory Commission, the U.S. Army Corps of Engineers (USACE) and the National Park Service, among others.
Act 121 will bring the PUC’s dams under the jurisdiction of Vermont’s DEC by 2028, unless they qualify for federal oversight. The change will also standardize two different processes — a disparity that has sometimes caused anxiety for folks living close to the state’s dams.
The Vermont Legislature also added $4 million to the Dam Safety Revolving Loan Fund to fund the removal of dams that could pose a threat to communities downstream.
Previously, Vermont’s dam safety loan fund was much smaller, and could only be tapped in case of emergencies. Act 121, however, allows dam owners to access
money for dam removal or renovation even before it is urgently needed.
Those monies, state officials said, will allow those landowners who might not otherwise have the resources to remove dams to access forgivable state loans to get rid of potentially hazardous structures.
Karina Dailey, a restoration ecologist at the Vermont Natural Resources Council and operator of the nonprofit’s dam removal program, said that in the aftermath of last July’s record rainfall and resulting floods, multiple landowners reached out seeking to get dams off their properties.
Deconstructing dams is not only safer for downstream communities, she explained, it is also a boon for the health of stream ecosystems.
“Certainly, a removed dam is the best dam, in our opinion,” she said in speaking to VTDigger.
Outside of the state Legislature, officials are using other strategies to improve the condition of Vermont’s dams.
For example, the Waterbury Dam is already undergoing a multi-year renovation as part of a collaboration with the USACE to upgrade deteriorating concrete and flood gates. That project, which is currently estimated to cost roughly $80 million, is scheduled for completion in 2029.
Northeastern University in Massachusetts filed detailed plans June 14 with the Boston Planning & Development Agency (BPDA) for its proposed replacement of Matthews Arena on St. Botolph Street.
In addition, the college laid out longerterm plans for a number of other buildings and properties across its campus, including dormitories and lab buildings, that could, if built, dramatically change the look of one stretch of Huntington Avenue in the city.
Universal Hub, an online local news source, reported that what is currently called the “262 St. Botolph Street Multipurpose Athletic Facility,” or MFA, would be able to seat 4,000 fans for hockey games, 5,000 for basketball games and include recreational sports facilities for use by the entire campus, including an indoor turf field and rowing tanks.
According to Northeastern’s project notification form, an auditorium also is proposed, which the school said might even become a place for Boston Public Schools to hold graduations.
Northeastern officials said they looked at renovating or expanding Matthews Arena, built in 1910, but concluded the current building is in such poor structural shape, extensive work would not be feasible.
“The [old] building has consistently had issues with structural stability and fire safety,” the university said in its proposal. “While Northeastern has invested in the facility to address these issues, including most recently installing temporary bracing to mitigate safety concerns associated with differential settlement, the [arena] has been deemed beyond repair. Redevelopment has emerged as the preferred approach from a financial and programmatic perspective, in line with Northeastern’s goals as an institution as well as a community partner.
The university began looking to expand Matthews Arena in 2019, Universal Hub noted.
“As a result of that work, Northeastern discovered the building’s limitations, the gravity of the structural deficiencies [which go back as far as the 1940s], and the implications such an addition would have on the structural integrity of the facility,” the school noted in the BPDA filing. “As a result of those studies, Northeastern proceeded with temporary structural improvements to the existing facility and is proposing redevelopment of the arena with the proposed project.
As designed, a new four-story arena would be topped by solar panels, part of Northeastern’s push to reduce its carbon emissions.
The school hopes to begin demolition of
Northeastern officials said they looked at renovating or expanding Matthews Arena, built in 1910, but concluded the current building is in such poor structural shape, extensive work would not be feasible.
In addition to detailed plans for the arena replacement, Northeastern also filed a proposed 10-year “institutional master plan” that calls for a number of other new buildings across the university campus.
The renderings and plans for these buildings are far less detailed; each will require the university to file a separate, far more detailed project notification form, as well as separate sets of community meetings, before work could begin on them.
Matthews Arena in early 2025, followed immediately by construction on the MFA. Opening ceremonies are tentatively scheduled for the summer of 2028, according to Universal Hub.
The new facility’s construction is currently estimated to cost between $300 million and $350 million.
In its filing, Northeastern University discussed how the new structure, planned to include the planting of 22 new street trees, would fit in with the surrounding area.
The new athletic complex’s design “aims to create a unique building for the campus while responding to the surrounding neighborhood context. The scale of the proposed project is driven by the modern athletic and recreational program requirements, and [its architecture will] break down the building’s massing to create dynamic, inviting and people-centric spaces for building users, guests and the community at large.”
Northeastern also noted that paving
The university began looking to expand Matthews Arena in 2019, Universal Hub noted.
along both St. Botolph and Gainsborough Streets “will relate in style to the existing enhanced streetscape across the street by the New England Conservatory of Music and further north along Gainsborough Street, stitching the project into the fabric of the greater neighborhood.”
Site elements, such as benches, will offer space for gathering and resting, and a high building overhang will offer an all-weather area undercover.
The university plans to support its sustainability goals and provide sustainable space with green infrastructure, it said, such as rain gardens within the street to act as zones for stormwater management. Low maintenance salt tolerant plant material and continuous soil trenches will help to promote successful planting and tree growth.
With the filing, Universal Hub said Northeastern is set to begin a series of required community meetings, both with the general public and with an “impact advisory group” of local residents and business owners appointed by the BPDA, before the Boston agency’s board votes on whether to approve the project.
The college laid out longer-term plans for a number of other buildings and properties across its campus, including dormitories and lab buildings.
These proposals include replacing the nearly 100-year-old Burstein Hall and Rubenstein Hall dormitories between 454 and 464 Huntington Ave., across from the MFA, with a 260-ft. tower that would include not only dorm rooms, but academic spaces and ground-floor retail, with the “unique opportunity to establish itself as a focal point for artistic and cultural activities, serving not only the university population but also the neighboring community,” according to Northeastern.
A 20-story, 1,000-bed dormitory on Forsyth Street at Huntington Avenue also is proposed to replace the five-story White Hall, which the university shut down due to structural problems last August just as the fall semester was ready to begin.
Additionally, Northeastern wants to raze the Cabot Center gym at 400 Huntington Ave. to make way for a 250-ft.-tall “academic, research, and student life building.”
Other future infrastructure projects on the university’s wish list, Universal Hub reported, include:
• The replacement of Northeastern’s Mugar Life Sciences Building and Cullinane Hall, at the opposite side of St. Botolph Street from the arena, with a new 160-ft.-tall research building.
• Replacing a two-story garage at 10 Gainsborough St. with a 150-ft.-high academic building that would become a campus life and recreational hub.
• Constructing a 200-ft.-tall academic and research building at the current site of a century-old building at 70 Forsyth St.
• Demolishing Lake Hall, Meserve Hall, Nightingale Hall, Holmes Hall, and Northeastern’s Power Plant in order to build another new 200-ft.-high structure designed for instructional, research, administrative, and student life spaces.
Northeastern also announced that it hopes to perform major renovations to nine other buildings — including the former Horticultural Hall building at 300 Massachusetts Ave. — that it bought earlier this year.
Sales Auction Company hosted an absolute auction June 20, 2024, exclusive to the family of businesses owned by Peckham Industries, currently celebrating its 100th anniversary.
Over the past 100 years, Peckham Industries has supplied materials, paved roads and worked on construction projects. With more than 30 locations in eastern New York and southern New England, Peckham Industries is well positioned to continue to serve its customers into the next century. The sale, held in Westfield, Mass., included an inventory of more than 250 pieces of equipment that bidders would expect to find from a major aggregate concrete and paving producer and contractor, including 45 pieces of paving, grading and compaction equipment; 13 skid steers; 33 trucks; 20 trailers; 15 wheel loaders and backhoes; and other types of support equipment. CEG
(All photographs in this article are Copyright 2024 Construction Equipment Guide. All Rights Reserved.)
see AUCTION page 12
AUCTION from page 8
Always looking for some good paving equipment are
James Nekludoff, Monroe Tractor equipment sales rep., has transferred to Westborough from the store in South Windsor, Conn., where he also worked as an equipment sales representative.
With 20 years of experience in construction equipment, Nekludoff brings a wealth of industry knowledge to Westborough. He will be responsible for selling and supporting Monroe’s full line of Case construction equipment and Case IH agriculture equipment, Screen Machine and Dynapac in Massachusetts’ Worcester and Franklin counties.
“I am thrilled to be joining Westborough’s team and look forward to offering customers my friendly, transparent and prompt solutions: Never overpromise, but always over-deliver,” said Nekludoff.
“James joins us with an extensive background in construction equipment, and paired with his ability to expedite customer’s needs make him an invaluable addition to our team,” said Dan Duhn, Westborough branch manager.
The Vermont DEC also is in communication with the USACE about making potential improvements to the Wrightsville and East Barre dams. Renovations are being considered that would allow the dams to release water more quickly in order to build capacity ahead of expected rainfall.
That process is still in its preliminary stages, and it is not clear if or when such improvements would take place, VTDigger reported.
And even before last summer’s flooding, Vermont officials were drafting new rules governing dams. New regulations will strengthen the state’s oversight of those water barriers owned by other entities, giving state officials the authority to compel dam owners to inspect and remediate the structures.
“They are a big deal,” explained the DEC’s Kamman.
Once they go fully into effect, he said, “the state will be in a position of saying, ‘Okay owner, your dam was found to be in poor condition. It poses a risk to downstream
residents. It’s not imminent, but it is a significant risk, and you need to do X, Y and Z in order to make this safe.’ That’s enforceable.”
Green, the agency’s dam safety engineer, told lawmakers in the past legislative session that the new rules amounted to a “paradigm shift in terms of how dams are regulated in the state.”
After delays caused both by COVID-19 and last year’s flooding, the regulations are slated to take effect in the summer of 2025.
Vermont officials and lawmakers say the reforms are the result of a need to keep making revisions. Climate change is exacerbating flooding in the Green Mountain State, forcing policymakers to continually adapt to heavier rainfall and more frequent deluges, events that will put further pressure on the state’s dams.
“We’re just living in a different climate,” said Bray, the chair of the Vermont Senate’s Natural Resources and Energy committee. “And we had not adapted our laws and planning practices to keep up with the hazards that we’re facing.”
quality of life as well as the value of their property. We help customers consider every detail of each project with the goal being not only to increase the value of their property, but to also make sure it can be easily maintained.”
Cole Landscaping has embraced technology and the company believes in taking advantage of any new products that can improve its customer service.
“From scheduling customers to managing our fleet using GPS, we rely on technology to be more efficient,” Cole said. “We do our landscape design using the latest software with 3-D models, which provide a realistic view of our proposed project. Our back office uses landscape specific management platforms that allow us to look at any project in real time as needed. We use a software called Aspire that tracks all key customer interactions and then integrates with Google tools and Outlook to help us manage tasks, appointments and e-mail correspondence. We are finding these technology tools to be critical to our future growth and the key to managing customer communication.
going to be hit with a blizzard. With just one day’s notice, I called Ryan [Sears] and he showed up with a JCB 270T, a 74 hp compact track loader with a 2,700-pound load capacity. It was exactly what we needed.
“On short notice, he provided us with a compact track loader that perfectly met our needs. We use it constantly for snow all winter and we use it to load materials throughout the year. The machine is great. It’s easy to get in and out of, gives us great visibility thanks to the single arm boom and great ground speed.
“We work closely with industry-related associations whom we find to be critical to staying on top of industry trends,” he added. “Beyond the relationship with associations, we maintain our competitive edge by attending seminars and trade shows across the country. We are constantly adapting new strategies and solutions to continue to grow and provide our clients with the service they deserve.”
According to Cole, the focus of his company’s 30-year history has been servicing customers on the north shore and becoming experts on the various conditions and circumstances unique to each area.
“We pride ourselves on keeping open and continuous communication with each customer during the entirety of their project,” he said. “We pride ourselves on having sameday response to any questions or concerns a client may have and we are absolutely dedicated to sticking to the agreed upon time frame and budget.”
Employee training also is critical to being able to achieve its goals, along with meeting customers’ expectations.
“Our entire staff meets every week for a team meeting,” Cole said. “Part of each meeting is dedicated to safety and the balance to operational training, such as how to properly trim a hedge or how to operate a skid steer. Safety is of the utmost concern to us. Our employees are family, and we want them to come home every day in the same condition that they left.”
Between the company’s longevity, product knowledge and the dedication of its employees, Cole Landscaping has opportunities to get involved in many unique projects, including a recent pool project in Marblehead where the pool was being installed on a hillside with a 30-degree grade that had to be maintained.
The future is bright for Cole Landscaping. It has projected that by the end of the decade it will have 160 employees and it is currently looking to invest in a second facility to reduce windshield time.
Cole is quick to point out that his employees at times are only as good as the equipment they have access to complete a project. With that in mind, Cole Landscaping has made significant investments in its equipment fleet. The company has purchased six Toro Dingo TX track loaders with vertical lift loader arms, which gives each Dingo a 1,000-lb. capacity for loading and unloading. The vertical lift makes the machine very flexible and able to use attachments such as
augers and vibratory hammers.
“We love our fleet of Dingo machines and use them for many applications, from pulling pipes to loading and unloading trucks,” he said. “We typically have one Dingo machine at each project that we are working on.”
Relationship building and reliability is the key to the company’s growth Cole said his company looks to receive the same from its vendors.
“Alta Equipment, who sold us the Dingo machines, gives us great customer service. Ryan Sears, our sales representative with Alta, understands the work that we do and does everything possible to keep our fleet up and running. But, with the Dingo machines we typically do not need any support. I would highly recommend that anyone in our business own these machines.”
Another machine that Cole Landscaping has purchased from Alta Equipment is a JCB 270T compact track loader.
“About two years ago, I knew we were
“The single arm boom is very important to us from a safety standpoint,” he added. “The loader boom allows for a side door entrance, which means no more climbing over the boom to get into the cab, a great safety innovation. Besides providing a safer environment for our operators, the machine is very stable and very strong.”
Another machine in the Cole Landscaping fleet is a JCB 417-wheel loader, a 2-yd. loader with a 125 hp engine. Cole Landscaping relies on this loader to fill its salters and help with the snow removal needs. One of the key features of the JCB 417 is its quiet motor operation.
“We live in a decibel restricted area,” Cole said. “We cannot have a machine that operates at over 100 decibels. The JCB 417 meets those decibel requirements.”
The most recent JCB purchase from Alta Equipment is a JCB 55Z-1 compact zero tail swing excavator with an operating weight of 12,000 lbs.
“Once again Alta Equipment delivered an awesome machine to us. It has tremendous digging and lift capacity and with the addition of a thumb it has become a very flexible tool for us.”
When asked why Alta Equipment is Cole Landscaping’s equipment supplier of choice, Cole said, “All of the machines are reliable and that’s important. But it’s really the performance of our sales rep that puts it over the top for us. I have his cell number and I am encouraged to call him day or night and, believe me, I do. Every time I have needed him, he has come through.
“I am a very loyal guy, that’s why we service customers the way we do at Cole Landscaping. Because we know that great service will ultimately give us customer loyalty. Alta Equipment and Ryan [Sears] have given us that same excellent level of service.”
For more information, visit www.altg.com and www.colelandscaping.com. CEG
(All photographs in this article are Copyright 2024 Construction Equipment Guide. All Rights Reserved.)
Equipment East, LLC
61 Silva Lane Dracut, MA 01826 978-454-3320
196 Manley Street Brockton, MA 02301 508-484-5567 1474 Route 3A Bow, NH 03304 603-410-5540
www.equipmenteast.com
30 Birch Island Road Webster, MA 01570 508-949-0005
7 Harry’s Way Webster, MA 01570 508-949-0005
1608 John Fitch Blvd South Windsor, CT 06074 860-288-4600
www.barryequipment.com
164 Boston Post Road Orange, CT 06477 203-795-0591 www.fwequip.com
45 Dempsey-Greaves Lane Stillwater, ME 04489
207-827-6193
www.centralequipmentco.com
The new Connecticut River Bridge will improve reliability and reduce delays for Amtrak’s intercity services, the Connecticut Shore Line East commuter service, and freight operators along the Northeast Corridor (NEC), America’s busiest rail corridor.
It will be primarily funded by the Infrastructure Investment & Jobs Act (IIJA), due to a $826.64 million federal grant awarded by the Federal Railroad Administration (FRA); Amtrak and the state of Connecticut will foot the remainder of the project’s cost.
It is but one of several passenger rail improvement efforts in the state, including the Devon Bridge and Walk Bridge replacement projects undertaken by the Connecticut Department of Transportation (CTDOT).
“Today’s milestone brings us one step closer to putting shovels in the ground and kicking off construction for this major project,” Amtrak CEO Stephen Gardner noted in a June 28 news release.
He also expressed his appreciation to the Biden-Harris Administration and the FRA for the funding necessary to advance the project from planning to construction. Additionally, Gardner thanked Connecticut’s two Democratic U.S. senators, Richard Blumenthal and Chris Murphy, along with Gov. Ned Lamont (D), and CTDOT “for their continued support and partnership.”
“The Connecticut River Bridge is an essential part of the busy Northeast Corridor rail line, but in dire need of repair,” Blumenthal said in the news release. “I am thrilled the work to replace this century-old bridge is moving forward — ensuring improved rail service is on the way — and I will keep fighting for federal resources to improve Connecticut’s aging infrastructure.”
In a statement from his office, Murphy added, “Investing in the future of rail in Connecticut is a no-brainer — it makes life easier for travelers and commuters, boosts economic growth, creates good-paying jobs and helps fight the climate crisis. Thanks to funding from the Infrastructure Investment and Jobs Act, this $1.3 billion investment to replace the aging Connecticut River Bridge will keep our railways safe, cut travel times and improve Amtrak’s rail service for Connecticut riders.”
The current 1,500-ft.-long Connecticut River Bridge opened in 1907 and is one of several moveable rail spans along the NEC.
Today, it serves more than 50 daily Amtrak Northeast Regional and Acela trains,
the CTrail Shore Line East service, and various freight trains. However, the unreliability of the aging bridge, due to its failure to open and close consistently, results in cascading delays to rail and maritime traffic.
The O&G/Tutor Perini joint venture will work with Amtrak at the Connecticut River site to construct a new two-track, moveable bridge to replace the existing dual-track structure between Old Saybrook and Old Lyme, located about midway between New York City and Providence, R.I.
• The proposed moveable bridge will be located immediately south of the old span, and feature modern tracks, signals, catenary, power, communication and other supporting rail infrastructure.
• It also is designed to safely support trains moving at a maximum operating speed of 70 mph, a 55 percent increase from today’s maximum speed of 45 mph.
• Maritime navigation and safety in the river also will improve due to additional vertical clearance compared with the existing bridge.
The new bridge design is 100 percent complete, according to Amtrak, and construction is set to begin late this summer or early fall.
The rail service previously awarded a construction management contract to AECOM, which will assist the rail company with management of the construction joint venture, document control, schedule and budget oversight, and community outreach support.
The NEC rail bridge project in Connecticut is key to Amtrak’s vision of a new era of passenger rail, which includes investments into modern trains, stations, tunnels, bridges and other critical infrastructure upgrades to enhance the customer experience, improve safety and reliability, and expand capacity to serve more future customers.
“The new Connecticut River Bridge will serve the entire Northeast Corridor. It will help realize Gov. Ned Lamont’s goal of improved rail connectivity north to Boston and south to Washington, D.C.,” explained CTDOT Commissioner Garrett Eucalitto.
“The new structure, built by Connecticut’s building trades, will improve safety, reliability and increase operating speeds along the line,” he added. “CTDOT is grateful for the continued support of the U.S. Department of Transportation and the Federal Railroad Administration, the advocacy of our congressional delegation, and collaboration of our partners at Amtrak.”