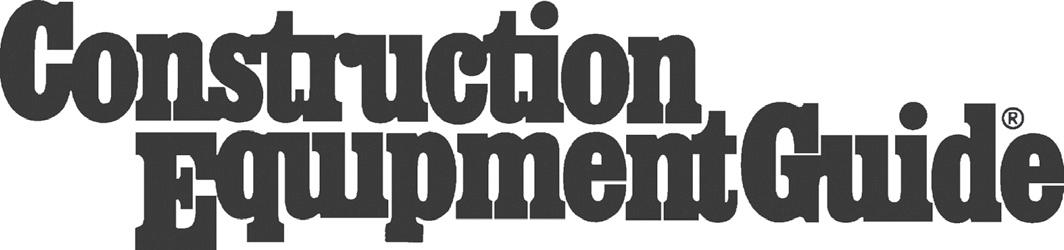
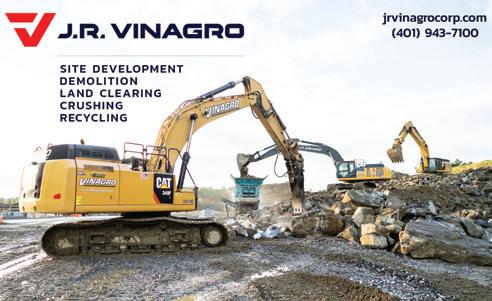
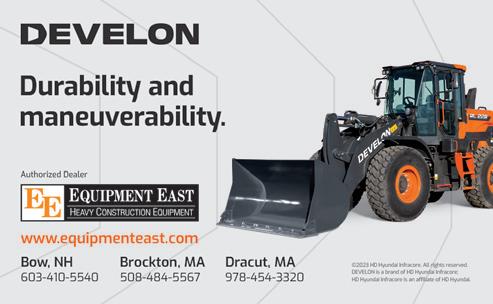

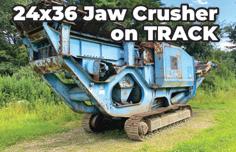
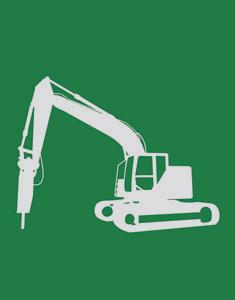
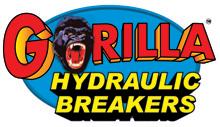
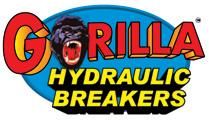


Chadwick-BaRoss Inc. and Thompsonrolec Enterprises LLC (Thompson Equipment), recently announced the appointment of Jeremy Jordan as president of both companies.
“Jeremy’s appointment marks an important chapter in the history of both companies,” said Yedidia Koschitzky, chairman of Chadwick-BaRoss and Thompson Equipment. “His leadership, and deep long-tenured knowledge of the companies for over 30 years, positions us to meet the growing needs of our markets, strengthen our regional focus, and continue the legacy of nearly a century of excellence. We are confident that Jeremy will take these companies to new heights.”
Jordan’s journey with Chadwick-BaRoss started in 1992 as an apprentice in the track shop. Since then, he has risen through the ranks, holding various roles, including shop technician, field service technician, used/rental fleet manager, general manager, sales territory manager and, most recently, vice president of
The effort to replace the westbound Washington Bridge in Providence, R.I., got a major boost Oct. 16 as the state’s U.S. Senate and House representatives in Washington, D.C., joined with Gov. Dan McKee in announcing a $95.6 million Infrastructure for Rebuilding America (INFRA) federal grant for the Rhode Island Department of Transportation (RIDOT).
Together with a previous $125.39 million MEGA grant, awarded by the National Infrastructure Project Assistance program, that the state was awarded in September, Rhode Island has now received the almost $221 million it requested from the federal government to fully fund the bridge project, according to a news release from McKee’s administration.
The new monies are being made available through the Bipartisan Infrastructure Law, which Rhode Island’s two
Democratic U.S. Senators Jack Reed and Sheldon Whitehouse supported and was signed into law by President Joe Biden in 2021, delivering a 50 percent increase in the amount of available funding for INFRA grants.
The additional resources also have helped improve Rhode Island’s roads, bridges, public transportation and water infrastructure over the last three years.
The Washington Bridge, which spans the Seekonk River connecting East Providence to Providence and has a daily traffic volume of 90,000 vehicles, was shut down on Dec. 11, 2023, after RIDOT discovered broken anchor rods that put the bridge at risk of failure.
“Securing this federal investment has been a top priority,” said Reed, a leading member of the Senate Appropriations
SENNEBOGEN, in kee philosophy to maxim created UPTIME Kits
eping with their mize uptime, has Whether you are a service technician i road, these kits have need for every service and PM task in one p created to save you t Managing hundreds o parts, from belts and and special tools bec single part number to n-house or on the everything you e, maintenance place. They were ime and money. of related service d nuts to O-Rings omes easy with a o order and stock
They are:
• Easy to order and ea t d t stock asy to s l
components and too
• Ideal for stocking se and trucks
Choose from the follo
• Central lubrication
• Preventive mainte
• O-Ring kits
• Electrical service k
• Hydraulic service k And the best thing is in stock and ready to built to match your m and series. Count on in-house. For more in UPTIME Kits, scan th s that these kits, go, are custommachine model SENNEBOGEN nformation on he QR code.
Hydraulic service k :kits shops ols ervice owing kits system kits nance service kits its kits
NO North our in parts com with customers maxim commitment h about more Read ontract Demolition C st in parts repair the have virtu and I machine another in If back. to front every come t a have They echnician machine, wntim warehouse. American ready-to-ship of inventories plete for uptime izes aftersale Machine” he “Beyond our ow , Bloomfield Hills, MI or quickly. back unit the g I k they Since do no lose ally bring just [they] situation, a have I over go to month a once through wntime… ock. get theSENNEBOGEN
By Sheila Capetta CEG CORRESPONDENT
Sales Auction Company LLC, established in 2009, held its 15th Annual Fall Sale Oct. 25 and 26, 2024, featuring both a virtual timed auction and a live onsite event at its 8-acre facility located at 55 King Spring Road in Windsor Locks, Conn. The event generated just more than $9 million in sales.
Sales Auction Company has seen significant participation throughout the years with this October event, attracting 1,968 online bidders, offering more than 1,400 items in the timed auction on Oct. 25 using Proxibid. Online purchases amounted to $4.3 million. On Oct. 26, favorable weather and enthusiastic attendees drew more than 1,020 pre-registered and onsite bidders, who competed for 397 items, resulting in $4.7 million in onsite sales.
Crowds gathered at the Windsor Locks facility to browse an extensive selection of equipment, machinery, parts and vehicles. Carlos Garcia, an attendee for eight years, said, “When you buy or sell with Sales, you can do it with confidence.” Many attendees have been loyal customers of the Sales annual auctions for years.
Among the standout items sold were a 2024
Caterpillar D1 crawler dozer for $117,000; a 2017 Rockster R1100DS impact crusher for $82,500; a 2019 Caterpillar 313FL excavator for $79,000; and two 2000 Terex TA40 articulated dumps, each fetching $72,000. A unique highlight was a 1928 Ford Model A from the estate of a local contractor, which sold for $4,500.
This year’s auction also featured two charity items. A
lot of 16 uncut $2 bills sold for $600, benefiting the Shriners Hospital for Children. In addition, a Napoleon Prestige 500 Gas Grill was auctioned for $800, supporting The Dana-Farber Cancer Institute. CEG (All photographs in this article are Copyright 2024 Construction Equipment Guide. All Rights Reserved.)
see AUCTION page 8
challenges. The stro
Equipment East can wepo ng lift capacity and reduce help you dig into your bigg ve r mo e a d tail gest .
AUCTION from page 4
Among the donation items was this lot of 16 uncut $2 bills, which sold for $600 and benefited the Shriners Hospital for Children.
from page 1
Chadwick-BaRoss. His hands-on experience in both technical and managerial positions has equipped him with a unique perspective on the challenges and opportunities within the industry.
Construction Equipment Guide (CEG) recently spoke with Jordan about his new role.
CEG: It’s quite rare in our industry to see someone start at an entrylevel position, work their entire career at the same company, and eventually become president. How does your background contribute to your new role?
Jordan: One of the biggest assets is that I can relate to the team at all levels. When issues come up, I bring relatability and legitimacy because I’ve been there. This background also is valuable on the customer side — I’ve worked in many different departments, so I can speak knowledgeably about all aspects of our business.
This experience has been especially helpful in managing our new Volvo territory in Massachusetts, which we acquired from Woodco. Having been with ChadwickBaRoss for so long and familiar with Volvo, I can help bridge the gap for transitioning customers. I understand both our history and how we handle business, which makes it easier for them to connect with us.
CEG: How does this experience influence your interactions with corporate leaders?
Jordan: It helps tremendously. While serving as vice president, I established relationships at the corporate level, so now as president, I have strong support from them. There’s a deep trust because I’ve been part of this company for so long, which makes the transition to my new role much smoother.
CEG: Some of the roles you’ve held must have changed dramatically over the years. Can you talk about that?
Jordan: Absolutely. It’s been night and day. When I started as an apprentice in the track shop, we were heavily focused on manual repairs, like welding up idlers or doing pin and bushing turns. But now, it’s the opposite — parts are more affordable, and labor is expensive, so the work structure has shifted a lot.
CEG: Were you a Komatsu dealer when you first joined?
Jordan: Yes, the company had been a Komatsu dealer for many years before I started. At that time, we represented Komatsu, Volvo, Link-Belt, JCB, Powerscreen and also Timberjack, until Deere bought them out. We held the Komatsu dealership for a couple of years before it changed.
CEG: What was your first move out of the service department?
Jordan: I spent about six months in the track shop, then two years as a shop tech, followed by five or six years as a road tech. After that, I approached Dave Costanzo, our operations manager at the time, and told him I was ready for a new challenge. I wanted to move into sales, and thankfully, he gave me that opportunity. Dave mentored me, and I’ll always remember his guidance — he knew the industry inside out.
CEG: There’s a sentiment that salesmanship has become less influential in dealership growth. What are your thoughts?
When issues come up, I bring relatability and legitimacy because I’ve been there. This background also is valuable on the customer side…”
Jordan: I partly agree; if you can’t support your customers, you’re in trouble. But I’d still say that salesmanship drives about 60-70 percent of a dealership’s success. Even with top-notch support, you need a strong sales team pushing the equipment into the market. Salesmanship is about being a true partner to your customer, and that relationship still matters a lot.
CEG: Chadwick-BaRoss recently went through a reorganization. Can you elaborate on the changes?
Jordan: We eliminated the general manager (GM) role at each branch, which was often focused on sales. By moving to a north, central and south regional structure, each region now has a director responsible for both sales and product support at a high level, with the primary focus on sales, while a corporate product support manager oversees support. This allows us to focus more on product support and better serve our cus-
Jeremy Jordan
Chadwick-BaRoss/Thompson Equipment
tomers. Steve Bodtman is our corporate product support manager, coming over from the Woodco acquisition. Our directors include Cole Leavitt in the north, Mike Anderson in the south, and Scott Rooney in the central region.
CEG: Chadwick-BaRoss and Thompson Equipment have distinct ways of doing business. How do you see your influence shaping Thompson Equipment?
Jordan: Thompson operates differently than Chadwick-BaRoss, especially in aggregate production. My role is to bridge best practices between the two companies. We’ve started holding weekly meetings with our regional directors and Steve Ferris,
Thompson’s vice president, to discuss top-level strategies. This helps us align better, reduce internal gaps and improve customer service.
CEG: The aggregate division’s motto is, “The more you make, the more you make.” Can you explain what that means?
Jordan: It’s straightforward: the more aggregate our customers produce, the more revenue they generate. We’re here to support that goal.
CEG: How does the sales process for aggregate equipment differ from other machinery?
Jordan: Aggregate sales require a much deeper understanding of production needs. It’s a highly consultative process and involves long buying cycles — sometimes years. Compared to compact equipment sales, which are more transactional, aggregate sales demand a strong trust level due to the significant investments involved.
CEG: What are the biggest challenges you anticipate in your new role?
Jordan: Typical challenges like interest costs and inventory levels persist, but for us, the main focus is shifting our company culture. We’re moving from a top-down approach to a more inclusive one where employees at all levels feel ownership. We believe this will improve customer support and attract top talent, as people want to be part of a company where their input is valued.
CEG: Is hiring skilled technicians still a significant challenge?
Jordan: Yes, it’s a major challenge, though we’ve had some recent success with quality applicants. It’s still our most challenging role to fill, but as the economy softens, we’re hopeful that the pool of available technicians will grow.
CEG: Are you noticing any sales slowdown in the marketplace?
Jordan: It’s more a matter of inventory levels than sales volume. During COVID, if you had inventory, it sold. Now, everyone has inventory, so we’re all competing for the same deals. It’s time to return to solid sales practices.
CEG: Chadwick-BaRoss has grown substantially over the years through expansion and acquisition. Do you expect that to continue?
Jordan: Yes, although likely not at the same pace as in recent years. Our owners have a target in mind, but it depends on the available opportunities within our footprint. CEG
When you need to move dirt and rock quickly, you need our R 936 crawler excavator. Advanced electronics let drive components work together efficiently to save fuel. Sensor-guided controls give you speed, precision and power. And robust cast steel components stand up to the toughest environments. It's all built to last with exclusive Liebherr components.
GRANT from page 1
in federal funding to accelerate progress toward a new bridge that meets capacity and safety needs now and, in the future.”
He added, “[Rhode Island] must put this money to work and keep the public updated with a clear timetable for progress.”
The infusion of INFRA money to demolish the old structure and build a new Washington Bridge “fills in a major missing piece of the funding puzzle to ensure the state can get the job done right,” explained Whitehouse, who helped author the INFRA program as a senior member of the Senate Environment and Public Works Committee. “We will continue to work as a delegation to secure whatever the state needs from the federal government to fix this situation for drivers.”
Demolition of the bridge has already begun, noted McKee’s press release. Last May, RIDOT estimated the price tag for replac-
ing the bridge would include $58.2 million for demolition as well as $368.3 million for the design-build process.
Now, though, the state will pay its demolition contractor another $38.4 million to tear down the piers and beams underneath the westbound lanes of Interstate 195 on the Washington Bridge, according to an agreement inked Oct. 16 and obtained two days later by Rhode Island Current, an independent, nonpartisan digital news site that covers state government and public policy.
The amendment to the existing contract with Warwick, R.I.based Aetna Bridge Co. marks an 84 percent increase over the existing, $45.8 million deal, which only covered the demolition of the superstructure, and not the piers, beams, and footings beneath it. Adding in another $10 million in demolition-related costs not included in the contract, the first phase of the project now totals more than $96 million.
Rhode Island Current reported that state officials originally
planned to keep the substructure beneath the thoroughfare intact for potential reuse in the replacement bridge. However, expert companies brought in to consult on the rebuild plan all said that the aging substructure posed too big a risk — and expense — for a contractor to want to preserve it.
At an Oct. 15 press conference, McKee and RIDOT Director Peter Alviti first revealed the change order with Aetna, expanding its scope of work to include the new substructure demolition.
The company was awarded the initial demolition contract through a competitive solicitation that closed in June. It comes with a Dec. 15, 2025, completion date — nine months later than the end date if Aetna was only in charge of tearing down the main bridge thoroughfare.
In accordance with the typical 80-20 split between federal and state cost shares for infrastructure projects, RIDOT will be responsible for paying $7.7 million of the extra $38.4 million price tag, with the new federal grant funding
covering the remaining share.
Separate from the demolition and rebuild costs for the Washington Bridge, RIDOT also estimated costs of approximately $46 million for emergency expenses, including work to stabilize the old bridge and estimated funding to account for both state and municipal safety and transportation-related expenses.
“Securing a second major federal grant marks another important milestone in our work to build a brand-new Washington Bridge,” McKee said in a statement. “We know that ensuring this complex project, if done right, will take time, but it’s encouraging to see demolition resuming this week, the rebuild bidding process moving forward, and additional federal dollars coming in.”
Prior to its latest INFRA award, Rhode Island previously received grants from the federal
program for a quartet of other construction projects. They include:
• A $60.3 million INFRA grant in 2019 to rebuild the Northbound Providence Viaduct.
• In 2020, $65 million to overhaul R.I. Highway 146.
• An $82.5 million grant in 2022 to upgrade the Pell Bridge.
• Another $81 million award earlier this year to create a “missing move” between I-95 and the state’s Quonset Business Park.
Additionally, the state has now received two MEGA awards to fund the Washington Bridge, totaling $125.39 million. These grants come on top of a $251 million federal Bridge Investment Grant the state’s delegation in Washington secured earlier in 2024 to repair 15 bridges along the I-95 corridor in Providence and Cranston.
In the future, Rhode Island is due to receive a total of $255 million in bridge formula funds over the life of the Bipartisan Infrastructure Law.
T.F. Green International Airport (PVD) in Providence, R.I., will be getting some new interior upgrades and gates in its passenger terminal due to the efforts of the state’s congressional delegation in Washington, D.C.
In an effort to improve operational efficiency, deliver a unified and modern design, and enhance passenger flow and comfort for the traveling public, U.S. Senators Jack Reed and Sheldon Whitehouse and Congressmen Seth Magaziner and Gabe Amo, all Democrats, announced Oct. 24 that the Rhode Island Airport Corporation (RIAC) has been awarded $10 million in federal funding from the Federal Aviation Administration (FAA) to advance renovations and technology upgrades at the airport.
The grant funding was awarded through the FAA’s Airport Terminals Program. Established by the Infrastructure Investment and Jobs Act of 2021, the program provides competitive grants for airport terminal development projects to address older infrastructure at facilities nationwide.
In the case of the Providence airport, the federal monies will be used to modernize PVD’s aging terminal infrastructure to sustain current and future air traffic and passenger demands, drive competition and enhance environmental sustainability and energy effi-
“This federal investment will provide critical funding for our efforts to modernize our airport terminal to be ready for the next three decades.”
Jonathan N. Savage Rhode Island Airport Corp.
Providence and Warwick Convention and Visitors Bureau also supported federal funding to renovate the 30-year-old terminal and allow T. F. Green International Airport to serve the community’s growing needs.
For the past several years, RIAC has been preparing for this new era of growth for PVD through the planning and design of the Terminal Reconfiguration project, which aims to ensure that today’s aging terminal presents the first and best impression of its state to incoming visitors.
ciency, according to a joint new release through Reed’s office.
Among the upgrades due to be made to the Providence terminal are backup power and water overhauls to maintain public safety and minimize travel disruptions, improvements to common interior areas, the expansion of seating capacity, traveler experience enhancements and renovating the interior space in the concourse to introduce a “sense of place” by bringing elements of local architecture inside the building.
The new funding also will improve ADA accessibility across all areas of the terminal,
and upgrade mechanical systems to meet energy efficiency and smart building goals, the news release noted. Making the upgrades will also accommodate additional increased passenger traffic to allow for continued growth and competition at PVD.
“Rhode Island T.F. Green International Airport is an economic engine and the gateway to the Ocean State for many visitors,” explained Reed, a senior member of the Senate Appropriations Committee. “Upgrading the concourse will ensure the airport continues to offer a world-class experience for all and can continue to support a high-volume of traffic.
“This is a forward-looking investment in a crucial piece of public infrastructure,” he continued. “It will strengthen not just the airport, but local businesses, tourism and our economy, as well and help accommodate future growth.”
Whitehouse, Reed’s colleague in the U.S. Senate, added, “Thanks to our Bipartisan Infrastructure Law, more investments are on the way to keep improving one of the best, most user-friendly airports in the country. This federal funding will make the terminal more comfortable so that residents and visitors flying out of T.F. Green can enjoy a better overall experience.”
The original terminal at the Providence airport was constructed in 1993 to support 2.4 million annual enplanements. Today, PVD is on track to exceed that by 1 million passengers over the next five years, and recently announced agreements with several airlines are slated to bring hundreds of new jobs to the airport and connect the airport to even more domestic and international destinations.
As the airport’s operations continue to expand and passenger numbers increase, RIAC seeks funding to reconfigure its terminal to meet this demand.
In addition to advocacy from the state’s federal delegation, Gov. Dan McKee and the
“T.F. Green International Airport is a key part of how Rhode Islanders and our visitors experience memorable moments in our state,” noted Amo. “It’s where we welcome loved ones when they return from a trip and where we send off our community’s heroes when they travel to D.C. for their Honor Flight.”
Jonathan N. Savage, board chair of the Rhode Island Airport Corp., said that since the Bruce Sundlin Terminal at PVD was built, it has had a critical impact on transforming and maintaining the local economy in and around Providence.
“This federal investment will provide critical funding for our efforts to modernize our airport terminal to be ready for the next three decades,” he added. “We are truly grateful for our Congressional delegation’s continued support for Rhode Island’s aviation economy.”
The grant funding was awarded through the FAA’s Airport Terminals Program. Established by the Infrastructure Investment and Jobs Act of 2021, the program provides competitive grants for airport terminal development projects to address older infrastructure at facilities nationwide.
Loved for the features. Trusted for the performance.
Hyundai wheel loaders have the power and performance, not to mention top-notch interiors, accurate onboard weighing system, industry proven drivetrain durability, clear sightlines, and handy tech that make life on the jobsite easier. So you can do more without feeling it. No wonder so many first-time Hyundai users become longtime fans.
The Connecticut Airport Authority (CAA) announced Nov. 4 that $6 million of federal funding has been secured for a major improvement project at Bradley International Airport (BDL) in Windsor Locks, north of Hartford.
The funding will be used for the ongoing construction of an 80,000 sq. ft. inline baggage screening facility behind the Sheraton Hotel, which is one of two construction projects currently underway at BDL. Once complete, baggage will be sent from the airline ticket counters along a mile-long conveyor belt to the new facility for screening.
Current explosive-detection machines located in the terminal lobby will be relocated once the new screening facility is operational, CAA noted in a news release, which will open additional space for current and future airline growth. The facility also will entail the construction of three new gates.
“The CAA is grateful for this new infusion of federal funding as we continue construction on major projects to enhance the passenger experience at Bradley International Airport. We also want to particularly thank Governor [Ned] Lamont, Connecticut’s federal delegation, and the Connecticut Business and Industry Association for working hard to secure this funding,” said CAA Executive Director Kevin A. Dillon.
The designated funding for BDL comes from $970 million in grants from the Federal Aviation Administration’s (FAA) FY25 Airport Terminal Program, which was established by the Bipartisan Infrastructure Law (BIL). Through a competitive grant process, the FAA is providing funds to 125 airports across the country this fiscal year to focus on terminal reconstruction, development, accessibility, energy efficiency and more.
In prior years, the Airport Terminal Program awarded the Hartford airport more than $31 million in grants, which represents a subset of the total $99 million in federal grants that the facility has received for its major terminal enhancement projects. The CAA has successfully applied for funds in each year that the highly competitive grant program has been offered.
“Over the last several years, Bradley has implemented many major improvements that have resulted in this airport being ranked among the best in the nation,” Lamont said. “This funding will enable Bradley to continue making upgrades that will strengthen its reputation as one of the best and most convenient airports available.”
U.S. Sen. Richard Blumenthal, D-Conn., said that he would continue working diligently for even more federal funding for the airport.
“As a frequent flyer — from Bradley back and forth weekly to D.C. — I know very personally what a great airport it is, and how much greater it could be,” he added. “In fact, with this $6 million federal funding boost, it will be on a flight path to become one of the nation’s premier air travel hubs. Streamlined, upgraded and expanded, its services will be speedier and safer than ever.”
The total cost of the inline baggage screening facility project is estimated at $188 million, according to CAA. In addition to the monies secured from the FAA, the airport’s newest upgrade will be funded through a combination of passenger facility charges and airport revenue.
“This $6 million in funding for Bradley International Airport builds on the progress that’s been made to improve passenger experience, modernize baggage screening, expand flight options, and create good-paying jobs” said U.S. Rep. John B. Larson, D1st District. “I am proud to have worked with the delegation to deliver millions of dollars in funding for Bradley through the Bipartisan Infrastructure Law. We will continue to work with our partners at the state, including the CAA, to advance our airport’s infrastructure and ensure a positive experience for travelers.”
Bradley International Airport is New England’s second-largest airport, behind only Boston’s Logan International. Recognized nationally by leading travel publications for its ease of travel, the award-winning Connecticut airport is operated by the CAA, and its operations are entirely selffunded. The airport contributes nearly $3.6 billion to the regional economy.
The CAA was established in 2011 to develop, improve, and operate the Hartfordarea airport, as well as the state’s other five general aviation airports: Danielson, GrotonNew London, Hartford-Brainard, Waterbury-Oxford and Windham. Its board is made up of 11 members with a broad spectrum of experience in aviationrelated and other industries, as well as government. CAA’s goal is to make Connecticut’s airports more attractive to new airlines, bring in new routes and support the state’s overall economic development and
strategy.